UNIT 5
Cement and Concrete Chemistry
Concrete is most widely used non-metallic material in construction of buildings, dams, bridges, etc. Cement act as a binder substance which is used to harden and help in binding the material together. It is used for binding material like bricks, stones, tile and also used for flooring and plastering purpose. Cement is used for construction work by mixing up of sand and crushed stones. It is a mixture of sand and water which is used in binding bricks together and for plastering purpose. On the basis of chemical composition cement can be classified into 4 different parts:
(i) Natural Cement
(ii) Pozzolana Cement
(iii) Slag Cement
Portland cement used as the basic ingredient of the concrete worldwide. It is the most common type of cement in general use. It is the mixture of calcium silicates and calcium aluminates with small amount of gypsum in it. On mixing the powder of Portland cement with water it gives the hard, stone like mass which resembles like Portland rock this is the reason why it is named as the Portland cement.
Composition of Portland Cement: - Hydraulic cement produced by pulverizing clinkers that consists of calcium silicate, usually containing one or more of the forms of calcium sulfate as a inter ground station. A good sample of Portland cement consists of:
(i) Silica(SiO2) : - 20-24%
(ii) Calcium Oxide : - 60-70%
(iii) Alumina (Al2O3) : - 5-7%
(iv) Magnesia(MgO) : - 2-3%
(v) Ferric Oxide (Fe2O3) : - 1-2.5%
(vi) Sulphur trioxide (SO3) : - 1-1.5%
(vii) Sulphur Oxide : - 1%
(viii) Potassium Oxide (K2O) : - 1%
The raw material which is used for manufacturing of cement contains the following materials:
- Calcareous (chalk consist of limestone)
- Argillaceous (clay consist of silicates of alumina)
Wet Process manufacturing: On using the calcareous as a raw material then chalk must be crushed into minute particles and hence dispersed it in water in a wash mill. Wash mill used to break the solid materials into lumps/slurry. In similar wash mill clay is also broken up and mixed with water. Then this slurry is stored in the silo called as slurry silo where it is consistently stirred. The composition of raw material is checked again and if required corrected by adding clay or chalk materials as per requirement.
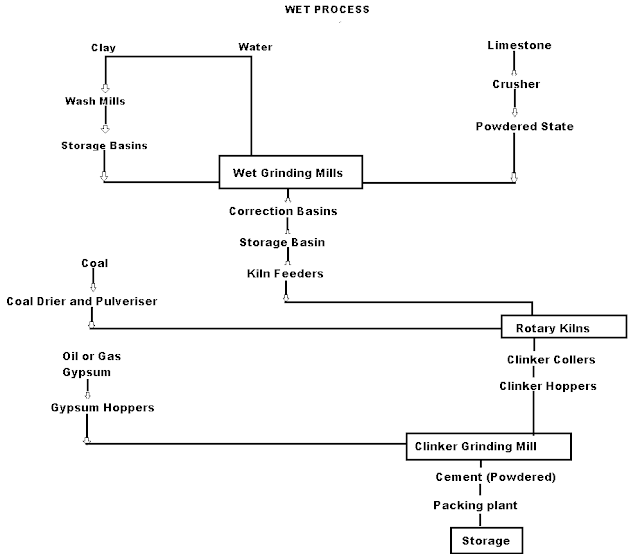
Cement Manufacturing Process Flow Chart
(I) Drying Zones : The raw material in slurry form is directly fed into the kiln which has more amount of water. It is the upper portion of the kiln. In this zone, water is evaporated at temperature 100-400°C.
(ii) Formations of modules: As the slurry gradually descends in the kiln, the carbon di oxide from slurry evaporates and small lumps formed which may be called as modules.
(iii) Burning Zone:- The modules enter in this zone where temperatures is kept about 1400-1500° C. The modules are converted into dark greenish balls and the product obtained in the kiln, known as clinker, is of varying size 5 to 20 mm. The clinkers are very hot when come out from this zone.
(iv) Cooling of Clinkers:- It is used for cool down the clinkers up to about 90°C.
Grinding: The cooled clinkers are finally ground in ball mills or tube mills.
Also, the gypsum is added during grinding about 2-4%. The gypsum acts as a retarder and so allows the cement to mix with sand or aggregate and to be placed in position. i.e. it increases the initial setting time of cement.
Storage and Packing: As cement comes out from grinding mills, it is collected in a hopper and taken in bucket elevator for storage in silos.
The cement from silos is packed by machines in bags. Each bag of cement contains 50 kg or 0.035 m3 of cement.
Dry Process manufacturing: This type of process for manufacturing the cement is available in the places where hard crystalline limestone and shales are available. The advantage of using this type of process is that fuel consumption is low.
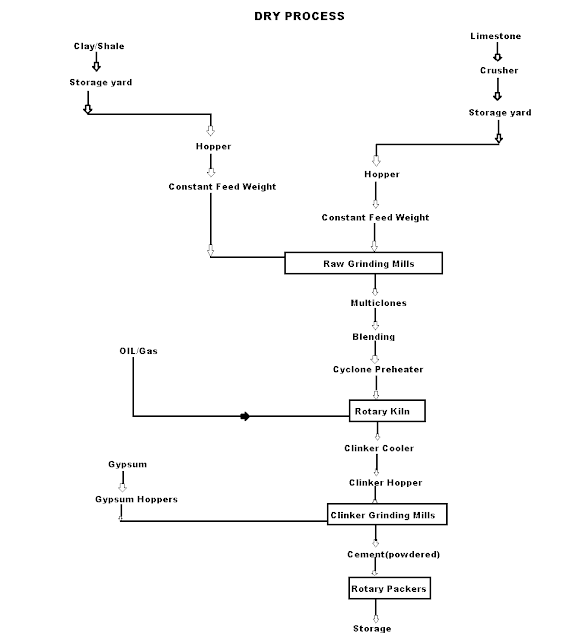
Mixing of Raw Materials: The used raw material undergo the following process:
- Crushing: The raw materials are broken in crushers to small fragments.
- Drying: The crushed materials are dried by heating at a sufficiently high temperature. It may be done in drying kilns.
- Reduction of size: The drying materials are then grinding by using ball mills and tube mills to reduce the size of materials to find powder.
- Mixing in correct proportion: The finely dried materials are mixed in exact proportions. The mixing may be done either mechanically or by pneumatic methods.
Burning and Grinding: In this process, the raw materials mixed, fined and then fed into kiln whereas in the wet process, the raw materials are crushed separately and then directly mixed in correct proportion in the presence of water to make a fine thin paste known as Slurry.
On mixing up of cement with water to form plastic mass then it is called as cement paste. During hydration reaction, gel and crystalline products are formed. The inter-locking of the crystals binds the inert particles of the aggregates into a compact rock like material.
This process comprises of
(i) Setting
(ii) Hardening
Setting is defined as stiffening of the original plastic mass due to initial gel formation while hardening is development of strength, due to crystallization.
The hardening starts after setting as because of gradual progress of crystallization in the interior mass of cement. The strength developed by cement paste at any time depends upon the amount of gel formed and the extent of crystallization. The setting and hardening of cement is due to the formation of inter locking crystals reinforced by rigid gels formed by the hydration and hydrolysis of the constitutional compounds.
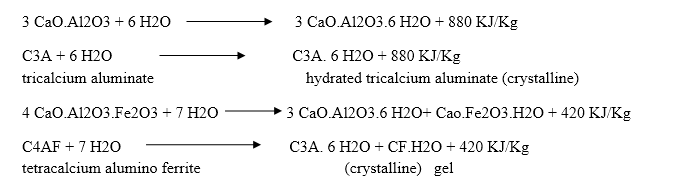
Dicalcium silicate also hydrolyses to tobermonite gel which contributes to initial setting.

Final setting and hardening of cement paste is due to the formation of tobermonite gel and crystallization of calcium hydroxide and hydrated tricalcium aluminate.

During setting and hardening of cement, some amount of heat is liberated due to hydration and hydrolysis reactions. The quantity of heat evolved during hydration of cement is 500 KJ/Kg.
Function of gypsum in cement :-
Tri calcium aluminate combines with water very rapidly.

After the initial setting, the paste becomes soft and the added gypsum retards the dissolution of tri calcium aluminate by forming insoluble calcium sulpho aluminate.
When a reactant A-B reacts; C comes out as the leaving group i.e.; it has taken a place of B or in other words it has substitution reaction. In other words, a substitution reaction is a part of one molecular replaced by other atom or group without causing a change a change in rest of the molecule.
E.g.
A-B + C A-C + B
CH4 + Cl2 CH3Cl + HCl
CH3Cl + Cl2 CH2Cl2 + HCl
CH2Cl2 + Cl2 CHCl3 + HCl
CHCl3 + Cl2 CCl4 + HCl
The substitution reaction may be brought by free radical nucleophilic or electrophilic reagent.
Mechanism:
The substitution reaction may be completed through following steps:
Chain Initiation:
The formation of chlorine free radical took place by the presence of sunlight or ultraviolet rays.
Cl : Cl Clo + Clo
Chain Propagation:
The Cl2 free radical replaces H2 atom forming another free radical which can later again formed Cl2 free radical & thus this chain goes on till all the H2 atoms are reduced by the chlorine.
Clo + H:CH3 HCl + oCH3
oCH3 + Cl:Cl CH3Cl + oCl
oCl + H:CH2Cl HCl + oCH2Cl
oCH2Cl + Cl:Cl CH2Cl2 + oCl
oCl + H:CH2Cl2 HCl + oCHCL2
oCHCL2 + Cl:Cl CHCl3 + oCl
oCl + H:CCl3 HCl + oCCl3
oCCl3 + Cl:Cl CCl4 + oCl
Chain Termination:
When all hydrogen atom are replaced by Cl than finally 2Cl free radical combines & chains terminates to form Cl molecule.
Clo + oCl Cl:Cl
Elimination Reaction:
Elimination reaction is the type of reaction that is mainly used to convert saturated compounds to the unsaturated compounds that is organic compounds which contain single carbon bonds to the compound which features double or triple carbon bonds. It is a chemical reaction where several atoms either pair or groups are removed from a molecule. The removal usually takes place due to the action of acids and bases or action of metals. It can also happen through the process of heating at high temperatures.
Mechanism
The elimination reaction consists of three fundamental events they are:
- C-C pi bond is formed.
- Proton removal.
- There is a breakage in the bond of the leaving group.
Depending on the reaction kinetics, elimination reactions can occur mostly by two mechanisms namely E1 or E2 where E is referred to as elimination and the number represent the molecularity.
E1 Reaction
- This is also called as unimolecular elimination reaction, thereare usually two steps involved – ionization and deprotonation.
- During ionization, there is a formation of carbocation as an intermediate. In deprotonation, a proton is lost by the carbocation.
- This happens in the presence of a base which further leads to the formation of a pi-bond in the molecule.
- In E1, the reaction rate is also proportional to the concentration of the substance to be transformed.
- It exhibits first-order kinetics.

E2 Reaction:
- In an E2 mechanism which refers to bimolecular elimination is basically a one-step mechanism.
- Here, the carbon-hydrogen and carbon-halogen bonds mostly break off to form a new double bond.
- However, in the E2 mechanism, a base is part of the rate-determining step and it has a huge influence on the mechanism.
- The reaction rate is mostly proportional to the concentrations of both the eliminating agent and the substrate.
- It exhibits second-order kinetics.
The E2 mechanism can generally be represented as below. In the below-mentioned representation, B stands for base and X stands for the halogen.
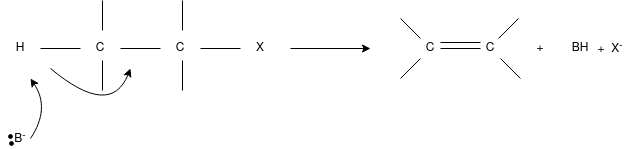
Aspirin:
The chemical name for the Aspirin is Acetylsalicylic acid. It is used as pain killer and fever reducer. Salicylic acid derives from the willow family of plants which were widely used for treating headache. For the preparation of aspirin, the salicylic acid is reacted with the excess acetic anhydride. Phosphoric acid is used for boosting the procedure of reaction. The excess acetic acid will be quenched with the addition of water. The aspirin product is not very soluble in water so the aspirin product will precipitate when water is added. The synthesis reaction of aspirin is shown below:
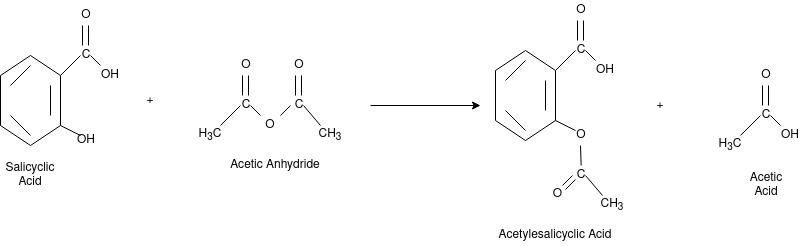
Since acetic acid is very soluble in water, it is easily separated from the aspirin product. The aspirin isolated in this step is the “crude product”. A “purified product” can be obtained through re-crystallization of the crude product in hot ethanol. In this experiment, the crude product will be the desired product. The percent yield of the crude product will be determined for this reaction. The purity of the product will also be analyzed. The product will be analyzed by three different methods: melting point, titration, and spectroscopic assay. C and the melting point range of the salicylic acid. The melting point range of pure aspirin is 138-140 C. If impurities are present in your crude sample, the melting point rangestarting material is 158-161 for your product will be lower than the range of pure aspirin. Also, your melting point range may be greater than 2 degrees.
Paracetamol:
From Phenol:
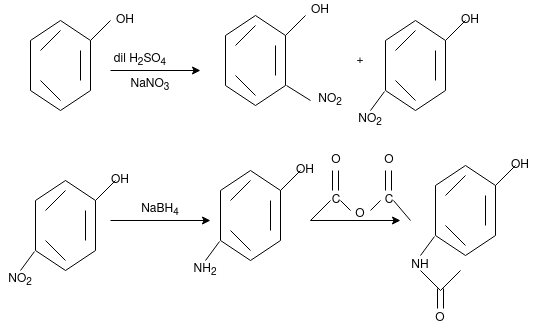
From Para nitro Phenol
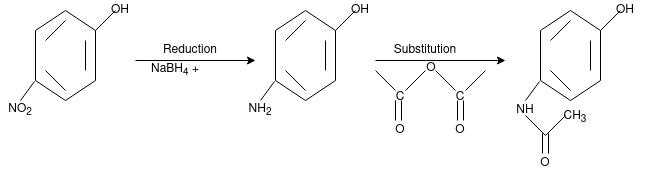