Unit - 1
Concrete
- Concrete is a composite fabric composed of exceptional and coarse combination bonded collectively with a fluid cement (cement paste) that hardens (cures) over time.
- In the past, lime primarily based totally cement binders, consisting of lime putty, have been regularly used however now and again with different hydraulic cements, consisting of a calcium aluminate cement or with Portland cement to shape Portland cement concrete (named for its visible resemblance to Portland stone).
- Many different non-cementitious forms of concrete exist with different techniques of binding combination collectively, together with asphalt concrete with a bitumen binder that is often used for avenue surfaces, and polymer concretes that use polymers as a binder.
- When combination is blended with dry Portland cement and water, the combination bureaucracy a fluid slurry this is without difficulty poured and molded into shape.
- The cement reacts with the water and different elements to shape a difficult matrix that binds the substances collectively right into a long lasting stone-like fabric that has many uses.
- Often, additives (consisting of pozzolans or superplasticizers) are protected with inside the combination to enhance the bodily residences of the moist blend or the completed fabric.
- Most concrete is poured with reinforcing substances (consisting of rebar) embedded to offer tensile strength, yielding bolstered concrete.
- Because concrete cures (which isn't always similar to drying), how concrete is treated after it's miles poured is simply as essential as before.
- Concrete is one of the maximum often used constructing substances.
- Ts utilization worldwide, ton for ton, is two times that of steel, wood, plastics, and aluminum combined. Globally, the ready-blend concrete industry, the biggest section of the concrete market, is projected to exceed $six hundred billion in sales with the aid of using 2025.
- Concrete is wonderful from mortar. Whereas concrete is itself a constructing fabric, mortar is a bonding agent that generally holds bricks, tiles and different masonry devices collectively.
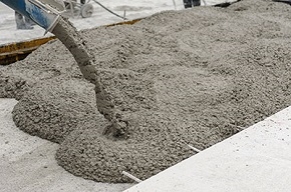
Fig 1: Concrete
Key Takeaways:
- Concrete is a composite fabric composed of exceptional and coarse combination bonded collectively with a fluid cement (cement paste) that hardens (cures) over time.
Plain concrete:
- Plain concrete, additionally referred to as undeniable cement concrete or PCC, is maximum typically used for paving and flooring.
- Made from a combination of cement, combination, and water the special varieties of combination and ratio of substances used will deliver special varieties of cement with barely special homes.
- This is one of the foremost promoting factors of geared up blend concrete as the precise values and varieties of combination may be measured and monitored exactly to offer the traits which are wished with none variance.
- The computerized production procedure limits the capacity of human blunders whilst saving time and resources.
- While there are variations with inside the composition of the concrete maximum undeniable concrete stocks the equal strengths and weaknesses.
- It is rather robust beneath Neath compression even as susceptible beneath Neath anxiety, because of this whilst on a solid, unmoving floor it's miles able to withstanding large quantities of weight.
- However, whilst located beneath Neath anxiety it's miles an awful lot weaker and might frequently crack and buckle.
- This makes it the correct cloth for floor ground layers and offering a strong or even base for strengthened concrete to be constructed onto whilst proscribing its use in large creation projects.
Key Takeaways:
- Made from a combination of cement, combination, and water the special varieties of combination and ratio of substances used will deliver special varieties of cement with barely special homes.
Reinforced concrete:
- Reinforced concrete, or strengthened cement concrete (RCC), is surely very just like PCC in phrases of substances used.
- The one massive distinction in its composition is the addition of metal rebar.
- By casting the moist cement round reinforcing metal bars the consequent composite cloth has an awful lot extra electricity beneath anxiety whilst nonetheless maintaining the homes that make PCC so effective.
- With the concrete retaining its electricity beneath compression and the metal resisting any bending or stretching way to its tensile electricity the RCC is a far extra flexible creation cloth.
- Able to rise up to weight pushing down onto it in addition to any wind stress or moving that outcomes in moderate twists and lines way to the expanded flexural capability of the concrete/metal blend, it's miles an appropriate cloth for taller and heavier homes and for roads and bridges.
- Steel is the maximum not unusual place cloth used for the introduction of rebar because it reacts to very comparable variances in temperature as concrete, that means it'll amplify and settlement with the concrete instead of cracking it from the inside.
Key Takeaways:
- By casting the moist cement round reinforcing metal bars the consequent composite cloth has an awful lot extra electricity beneath anxiety whilst nonetheless maintaining the homes that make PCC so effective.
Steel fiber/Glass fiber-strengthened concrete:
- Steel Fiber Reinforced Concrete (SFRC) is described because the concrete made with hydraulic cement containing high-quality and coarse combination and discontinuous discrete metal fiber.
- In SFRC, lots of small fibers are dispersed and disbursed randomly with inside the concrete for the duration of mixing, and hence enhance concrete homes.
- SFRC is getting used to enhance static and dynamic tensile electricity, strength soaking up capability and higher fatigue electricity.
- Steel fibers are the most powerful typically to be had fiber, and are available special lengths and shapes.
- Steel fires can simplest be used on surfaces which can tolerate or keep away from corrosion and rust stains.
- In a few cases, a metal-fiber floor is confronted with different substances.
- Glass fiber is a less expensive and corrosion-evidence fiber, however now no longer as robust as metal.
- The layout of glass fiber strengthened concrete proceeds from understanding of its fundamental homes beneath tensile, compressive, bending and shears forces, coupled with estimates of conduct beneath secondary loading results along with creep, thermal reaction and moisture movement.
Key Takeaways:
- SFRC is getting used to enhance static and dynamic tensile electricity, strength soaking up capability and higher fatigue electricity.
Light-weight concrete:
- Lightweight concrete is a combination made with light-weight coarse aggregates along with shale, clay, or slate, which provide it its feature low density.
- Structural light-weight concrete has an in-location density of ninety to a hundred and fifteen lb/ft³, while the density of everyday weight concrete stages from a hundred and forty to a hundred and fifty lb/ft³.
- This makes light-weight concrete best for constructing current systems that require minimum move sections with inside the foundation.
- It is being more and more used to construct smooth foundations, and has emerged as a possible opportunity to everyday concrete.
- Nevertheless, a better compressive electricity of 7000 to 10,000 psi may be attained with light-weight concrete.
- However, this can compromise the density of the combination because it calls for the addition of extra pozzolans and water-decreasing admixtures to the concrete.
Key Takeaways:
- Structural light-weight concrete has an in-location density of ninety to a hundred and fifteen lb/ft³, while the density of everyday weight concrete stages from a hundred and forty to a hundred and fifty lb/ft³.
High overall performance concrete:
- Concrete assembly unique combos of overall performance and uniformity necessities that cannot usually be accomplished mechanically the use of traditional parts and everyday mixing, placing, and curing practices.
- High-overall performance concrete (HPC) is concrete that has been designed to be extra-long lasting and, if necessary, more potent than traditional concrete.
- HPC combinations are composed of basically the equal substances as traditional concrete combinations, however the proportions are designed, or engineered, to offer the electricity and sturdiness wished for the structural and environmental necessities of the project.
- High-electricity concrete is described as having a targeted compressive electricity of 8000 psi (fifty-five MPa) or greater.
- The price of 8000 psi (fifty-five MPa) became decided on as it represented a electricity stage at which unique care is needed for manufacturing and checking out of the concrete and at which unique structural layout necessities can be wished.
Key Takeaways:
- HPC combinations are composed of basically the equal substances as traditional concrete combinations, however the proportions are designed, or engineered, to offer the electricity and sturdiness wished for the structural and environmental necessities of the project.
Polymer concrete:
- Polymer concrete is a combination that makes use of a few form of epoxy binder to remedy and harden into location.
- A polyester, vinyl ester, or everyday epoxy combination is frequently used, however polymer concrete may be made with many styles of polymer resins that permit the concrete to be poured or troweled after which hardened.
- It remedies via a chemical response with the polymer cloth.
- Like conventional concrete, it additionally has water, sand and gravel or overwhelmed stone as number one ingredients.
- Polymer concrete gives special blessings relying at the resin used to make it.
- Acrylic binders set right away and provide resistance to weathering, whilst epoxies create a completely robust cloth that shrinks little or no because it remedies.
- Furan resins can face up to excessive temperatures, and polyuria resins can update phenolic or formaldehydes in lots of creation projects.
- Polymer concrete is used for lots styles of specialized creation projects.
- Like different varieties of concrete, it is able to be used to sign up for special additives or to offer a shape or base.
- The cloth is utilized in electric or commercial creation in which the concrete desires to final a long term and be proof against many varieties of corrosion.
Key Takeaways:
- A polyester, vinyl ester, or everyday epoxy combination is frequently used; however, polymer concrete may be made with many styles of polymer resins that permit the concrete to be poured or troweled after which hardened.
Concrete is a commonly used construction material, which is the mixture of cement, sand, aggregate, and admixtures blended with water. Concrete gets hardened with time and gains the strength, and for the best results in a construction of your dream home, mixing of concrete is said to be the most important process. All the ingredients are to be mixed in proper proportion because the properties of concrete like workability, strength, surface finish, and durability of concrete etc. are ensured by the right and proportionate blending.
In the nominal mix concrete, all the ingredients and their proportions are prescribed in the standard specifications. These proportions are specified in the ratio of cement to aggregates for certain strength achievement.
The mix proportions like 1:1.5:3, 1:2:4, 1:3:6 etc. are adopted in nominal mix of concrete without any scientific base, only on the basis on past empirical studies. Thus, it is adopted for ordinary concrete or you can say, the nominal mix is preferred for simpler, relatively unimportant and small concrete works.
As per the ‘Indian Standard- IS 456:2000’, nominal mix concrete may be used for concrete of M20 grade or lower grade such as M5, M7.5, M10, M15.
M 20 is identified as the concrete grade in which, M denotes the Mix and 20 denotes the compressive strength of concrete cube after 28 days of curing in N/mm2. There are various grades of concrete that can be used like M10, M15, M20, M25, M30, etc.
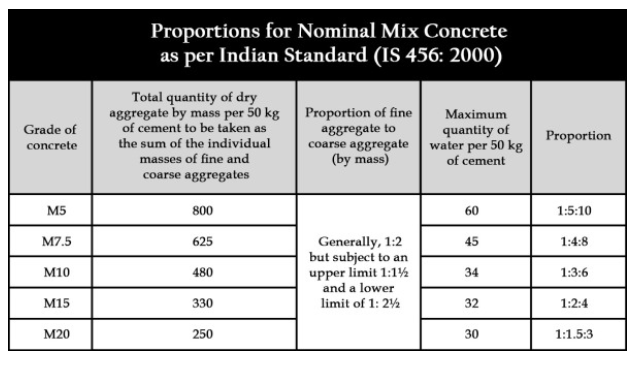
Tests on fresh concrete
Objective
- The word ―workable or concrete used has a broader and deeper meaning than the word alternative that is commonly used freely to make it work. Consistency is a general term that indicates the level of fluid or flow rate.
- Factors that help concrete to have the most effective effect of reducing internal friction that facilitates easy mixing are:
(a) Water content
(b) Mixing Dimensions
(c) Collection Size
(d) Structure Shapes
(e) Spatial Design Design
(f) Placement layout
(g) Use of Admixtures.
- Slump test is the most widely used method of measuring the consistency of concrete that can be used in a laboratory or in the workplace.
- It is not suitable for very wet or very dry concrete. It does not measure all factors that affect performance, nor does it always represent concrete placement.
- Indicates the concrete feature above the drop value. When the concrete slips evenly it is called a true slump. When one part of the lump slips, it is called a shear slump.
- In the event of a shear bend, the slump value is measured as the height difference between the height of the mold and the average amount of shrinkage.
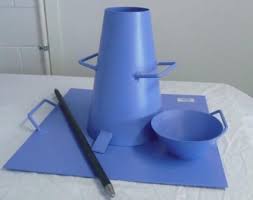
Fig no 2 Slum cone
Procedure
- If this test is performed in the field, a mixed concrete sample will be obtained. In the case of concrete containing a diameter of more than 38 mm, the concrete will be diluted with water by one and a half inches of screen to remove compacted particles larger than 38 mm.
- The inner surface of the mold will be thoroughly cleaned and freed from unwanted moisture and pre-set concrete before testing. The mold will be placed on a smooth, horizontal, strong, and non-abrasive surface, such as a carefully weighed metal table, the mold will be kept firmly in place while filling.
- The mold will be filled in four layers, each about a quarter of the height of the mold. Each layer will be smoothed with twenty-five lashes on the round edge of the lubricating rod. The lashes will be distributed evenly over the section at the cross section of the mold and the second and subsequent layers will fit into the lower layer.
- The bottom layer will be smoothed in the depth of it all. After the upper layer has been coated, the concrete will be flattened and trimmed with a trowel, so that the mold will fill directly.
- After the top layer has been glued, remove the concrete surface by moving and moving the lubricating rod.
- Any mud that may have leaked between the mold and the base plate should be cleaned. The mold will be removed from the concrete immediately by lifting it gently and carefully in a vertical direction. This allows the concrete to drop and the fall will be measured immediately by determining the difference between the height of the mold and that of the highest of the test template.
- The above operation will be performed in a non-vibrating or panic-free environment, and within two minutes after sampling.
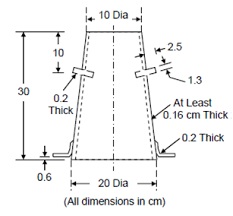
Fig no 3 Dimensions of slum cone
Key takeaways
- Slump test is the most widely used method of measuring the consistency of concrete that can be used in a laboratory or in the workplace.
- It is not suitable for very wet or very dry concrete. It does not measure all factors that affect performance, nor does it always represent concrete placement.
COMPACTION FACTOR
Objective
The compacting factor test is mainly designed for use in the laboratory but can also be used in the field. It is more accurate and sensitive than fall testing and is especially useful for very low-performance concrete mixes and is often used when the concrete will be squeezed by vibration. This method works on bare and ventilated concrete, made of lightweight, standard weight or heavy aggregates with a maximum weight of 38 mm or less but not on open concrete or non-reinforced concrete.
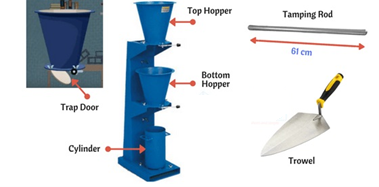
Fig no 4 Compaction factor apparatus
Procedure
- A sample of the test concrete will be gently placed on the upper hopper, using a hand scoop. The hopper will be evenly filled with its edge and the trap door will be opened so that the concrete falls to the ground.
- Some mixes tend to stick to one or both hoppers. When this happens, the concrete can be helped by pushing the rod gently into the concrete from the top. During this process, the cylinder will be covered with tiles.
- As soon as the concrete is out, the cylinder will be exposed, the door to the bottom trap will be opened, and the concrete will be allowed to fall into the cylinder. The remaining concrete over the top of the cylinder will be removed by holding a trowel in each hand, the plane of the belts horizontally, and then moving them simultaneously to each side above the cylinder, at the same time keeping them pressed against the upper edge of the cylinder.
- The outside of the cylinder when it is wiped will be clean. The above work will be done in a place that will not tremble or shake. The weight of the concrete in the container will be determined by the nearest 10 g.
- The remaining concrete over the top of the cylinder will be removed by holding a trowel in each hand, the plane of the belts horizontally, and then moving them simultaneously to each side above the cylinder, at the same time keeping them pressed against the upper edge of the cylinder. The outside of the cylinder when it is wiped will be clean. The whole process will be done in a place where there is no vibration or shock.
- This weight will be known as the weight of the partially bonded concrete. The cylinder will be filled with concrete from the same sample with layers about 5 cm deep, the layers folded tightly
- Or shaken to achieve complete integration.
- The surface of the fully covered concrete will be carefully beaten and weighed above the cylinder. The outside of the cylinder when it is wiped will be clean.
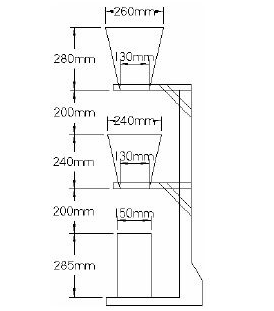
Fig no 5 Dimensions of compaction factor apparatus
Key takeaways
The compacting factor test is mainly designed for use in the laboratory but can also be used in the field. It is more accurate and sensitive than fall testing and is especially useful for very low-performance concrete mixes and is often used when the concrete will be squeezed by vibration. This method works on bare and ventilated concrete, made of lightweight, standard weight or heavy aggregates with a maximum weight of 38 mm or less but not on open concrete or non-reinforced concrete.
VEE BEE CONSISTOMETER AND FLOW TABLE APPARATUS
VEE BEE CONSISTOMETER
Objective
- The performance of the new concrete is a composite material, which incorporates various requirements for stability, mobility, durability, placement and finishing. There are various ways to measure performance.
- Each of them measures only a specific aspect of it and there is no unique test, which measures the performance of concrete completely. This test provides an indication of the flow rate of the newly mixed concrete mix.
- The test measures the concurrent effort required to change a pile of concrete from one concrete to another (e.g., from a circle to a cylindrical) using vibration.
- The amount of effort (called retrieval attempt) is taken as the time in seconds, which is required to complete the change. The results of this experiment are useful when you study the flow of concrete piles made of different amounts of water, cement and different types of composite placement.
- The time required for a full recovery in seconds is taken as a performance measure and is expressed as the Vee-Bee number of seconds.
- This method is suitable for dry concrete. With concrete drop of more than 50mm, reconstruction is so fast that time cannot be measured.
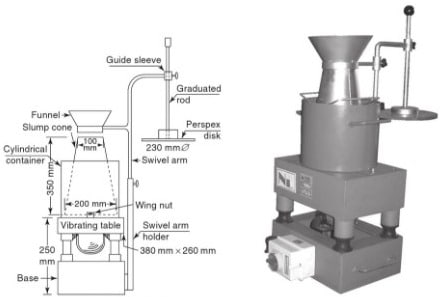
Fig no 6 Vee bee Consistometer Test
Procedure
- Slump test as described in "IS 1199: 1959 Details of Concrete Testing Equipment (Fourth Review). Confirmed- Dis 2013". Is made, inserting a collapsible lump inside a round metal pot of consist meter.
- The glass disk attached to the rotating arm will be moved to the top of the cone in the pot and before the cone is raised, the location of the concrete cone will be identified by fixing the glass disc attached to the arm wrist. The cone will then be lifted and the fall will be marked on the graduating rod by lowering the glass disc over the concrete cone. The electric heater will then light up and the concrete will be allowed to lay in the pot.
- The vibration continues until the point where the concrete shape disappears and the concrete takes on a circular shape. This can be judged by looking at the glass disc from the top disappearing visually.
- As soon as the concrete completely begins to form a circle, the stand clock is turned off. The time required for concrete formation to change from the formation of a collapsing lump into a circle in seconds is known as the Vee Bee Degree.
- This method is best suited for dry concrete with an unmeasured fall value with a Slump Test, but vibration is much stronger than concrete with a fall of more than 50 mm.
FLOW TABLE
Flow tests were performed to measure the performance of the concrete. As the name suggests, in this experiment concrete performance is measured by examining the flow of concrete material. Flow test Easy laboratory test. This test applies to the principal for the general weight loss of concrete and is measured by the flow of concrete. The flow of concrete indicates the performance of the new concrete.
Why flow test of concrete required
Flow tests are used to measure the performance of high or very active concrete, which ultimately indicates a fall. It gives an idea about the quality of concrete in terms of consistency and consistency. This performance test is easy to perform and is best suited for concrete with a high overall size of the joint less than 38 mm.
Flow Test Apparatus
Metal Cone or Mould: Mould is in the form of a frustum of a cone with a base diameter of 250 mm, upper surface diameter of 170 mm and 120 mm height. The mould comes with handles for support.
Flow Table
Trowels
Hand scoop
Scale
Tamping Rod
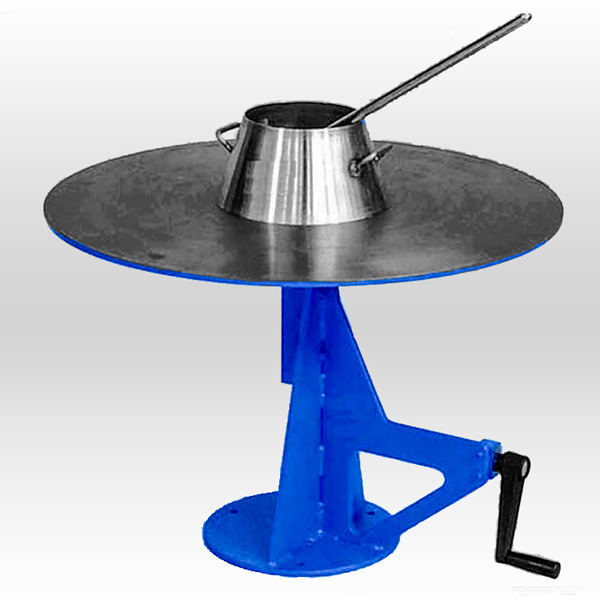
Fig no 7 Flow test apparatus
Procedure
- Clean anything toxic or dusty from the flow table and inside the mold.
- Place the lump on the marked area or in the middle of the flow table.
- Now pour the freshly mixed concrete into the mold in two layers, each layer should be moistened 25 times with a soft stick. If the concrete overflows after stamping and measure with the help of a torch, and the excess concrete should be removed from the table.
- After that, lift the mold upwards and allow the concrete to stand on its own without support.
- After that the table is raised and lowered from 12.5 mm high, 15 times in about 15 seconds.
- Next, measure the width of the concrete spread by about 6 points and write down the scale.
Key takeaways
- The performance of the new concrete is a composite material, which incorporates various requirements for stability, mobility, durability, placement and finishing. There are various ways to measure performance.
- Each of them measures only a specific aspect of it and there is no unique test, which measures the performance of concrete completely. This test provides an indication of the flow rate of the newly mixed concrete mix.
- Flow tests were performed to measure the performance of the concrete. As the name suggests, in this experiment concrete performance is measured by examining the flow of concrete material. Flow test Easy laboratory test. This test applies to the principal for the general weight loss of concrete and is measured by the flow of concrete. The flow of concrete indicates the performance of the new concrete.
Effect of admixture on workability of concrete and optimum dosage of admixture by marsh cone test
Effect of admixture on workability of concrete
- Concrete contains cement, sand, a mixture of water. Anything other than these if added to concrete before or during mixing to convert structures to our desired requirement is called admixtures. The use of admixtures provides certain beneficial effects on concrete such as improved performance, speed or delay of set time, reduction of the amount of water cement, and so on.
- There are two basic types of admixtures available: chemicals and minerals. Admixtures such as fly ash, silicate fume, slag come in the category of mineral admixtures. They are incorporated into concrete to increase performance, improve thermal resistance and alkaline reactions and enable us to reduce cement content.
- Fly ash is a good residue left over from global warming or powdered charcoal. They are all better than cement and contain mainly round glass particles as well as remnants of hematite and magnetite, char and other crystalline layers formed during cooling. The use of fly ash in concrete makes mixing more economical, and improves performance, reduces separation, bleeding and reduces hydration temperatures but also offers natural benefits.
- Silica fire, also known as micro silica. It is available as a product during the production of silicon and ferrosilicon alloys. The particles of silica fire particles are 100 times smaller than cement particles which mean their smoke like cigarettes. Its highly efficient pozzolanic material, which improves concrete structures such as improved durability, bond strength, abrasion resistance, dense concrete leading to reinforcement and rust protection.
- Chemical admixtures are applied to concrete in very small quantities especially for ventilation, reduction of water or cement content, installation of new concrete mixtures or control of concrete set time. These compounds can be widely used as super plasticizers, accelerators, retarders, water reducers and ventilation admixtures.
- Super plasticizers were added to reduce water demand by 15 to 20% without affecting performance leading to high durability and high concrete. Super plasticizers are liner polymers that contain sulfonic acid groups attached to the polymer from time to time. Commercial composition can dissolve melamine - formaldehyde condens- sates, sulfonated naphthalene formaldehyde condensates, and modified lingo sulfonates, derived from polycar- boxylate. The main purpose of super plasticizers is to produce a concrete slope with a very high drop of 175 to 200 mm that can be used effectively on reinforced concrete structures, a decrease in volume depending on the volume, type and timing of good plasticizers (preferably before adding concrete.), Water cement, environment and value of cement.
- Accelerators were added to reduce the setting time of the concrete thus facilitating pre-form removal and are also used in the combination of cold weather. Calcium chloride is the most widely used accelerator in blending. The use of calcium chloride in reinforced concrete can promote the corrosion function of the steel reinforcement. As people become aware of it there is a growing interest in using free chloride.
- Retarders were added to increase the setting time by delaying the hydration of the cement. They are popular in areas with high temperatures combined. Retarders contain organic & inorganic agents. Organic retarders include unrefined calcium, sodium and ammonia salt lignosulfonic acid, hydro carboxylic acid and carbohydrates. Inorganic retardants include lead oxides, zinc, phosphate and magnesium salts. Most retarders work as a water repellent. They are called retarders that reduce water. It is therefore caused by high pressure forces due to the low water content.
- Admixtures reduce the amount of water added to the concrete to achieve a certain effect (fall) at a lower water level. Strong concrete specified for low cement content thus saving cement. Water reducers are widely used in hot weather and assist in pumping. Water-repellent plasticizers are hygroscopic powder, which can inhale air into concrete.
- Ventilation admixtures bring in small concrete bubbles. These air bubbles act as rollers thus improving performance and also work more efficiently in thaw-chilling channels as they provide a stabilizing effect in expanding water where cold weather meets.
- Ventilation admixtures are compatible with most combinations, care should be taken to prevent them from collapsing during mixing.
- In general, the performance of both types of plasticizers depends on the ambient temperature and thus in the summer the amount of plasticizer that will be used to handle the same rate of plastic expansion may be more than the amount that will be used in winter.
- The change in the normal set time within a specific requirement also makes the product dependent on other chemicals and as plasticizers with different nomenclature available in the market.
- CICO Technologies Limited, a 75-year-old Indian company ISO 9001: 2000 supported producing a range of concrete installation admixtures.
- Many RMC companies use CICO admixtures. Further modification is required during the trial. Modification to Plasticizers can meet the needs of any particular client.
Optimum dosage of admixture by marsh cone test
- Admixtures are common and important of modern concrete. Low water content, high efficient, durable and cost-effective cement
- Many desirable properties that can be expected from concrete made of chemical and mineral composites
- Admixture-Cement mixing in concrete is complex combination of chemical and physical equipment independent.
- All combinations in large volumes offer good results when used with cement.
- Cement hydration involves a series of reaction, which is highly dependent on cement composition, water / cement ratio, surface area, particle distribution of size, temperature and integration.
- Admixtures when added in small amounts do that the hydration process is very complex. In recent times, developments in the cement product sector are related to the use of admixtures especially organic polymeric building materials.
- Many species of polymeric organisms known as super plasticizers, are used construction industries to change the way it flows again concrete machinery facilities.
- Among the various species for chemical admixtures, PCE-based admixtures are shown to develop new flow and complex areas of low-grade concrete.
Key takeaways
- Concrete contains cement, sand, a mixture of water. Anything other than these if added to concrete before or during mixing to convert structures to our desired requirement is called admixtures. The use of admixtures provides certain beneficial effects on concrete such as improved performance, speed or delay of set time, reduction of the amount of water cement, and so on.
- Admixtures are common and important of modern concrete. Low water content, high efficient, durable and cost-effective cement
- Many desirable properties that can be expected from concrete made of chemical and mineral composites.
Testing of hardened concrete
- The compression take a look at indicates the exceptional feasible electricity concrete can gain in best conditions.
- The compression take a look at measures concrete electricity withinside the hardened state.
- Field concrete samples are organized, cured and examined consistent with ASTM preferred procedures.
- Specimens are organized from concrete taken from exclusive creation sites.
- Following methods and calculations are used for measuring compressive electricity of cylindrical concrete specimens.
Test Procedure
- Placing the Specimen — The plain (decrease) bearing block is located, with its hardened face up, at the desk of the trying out device without delay beneath the spherically seated (top) bearing block. The bearing faces of the top and decrease bearing blocks are wiped clean and the take a look at specimen is located at the decrease bearing block.
- Zero Verification and Block Seating— previous to trying out the specimen, it's far demonstrated that the weight indicator is ready to zero. If the indicator isn't always well set to zero, it's far adjusted.
- Rate of Loading— the weight is implemented constantly and without shock.
- Standards specify that for trying out machines of the screw type, the shifting head shall tour at a charge of about zero.05in. (1mm)/min while the device is jogging idle .While for hydraulically operated machines, the weight will be implemented at a charge of motion (platen to crosshead measurement) similar to a loading charge at the specimen in the variety of 20 to 50 psi/sec (0.15 to 0.35 M Pa/sec).
- During the software of the primary 1/2 of of the expected loading phase, a better charge of loading is allowed.
- No adjustment is made with inside the charge of motion of the platen at any time at the same time as a specimen is yielding swiftly right away earlier than failure.
- Load is implemented till the specimen fails, and the most load carried via way of means of the specimen all through the take a look at is recorded. The form of failure and the arrival of the concrete also are noted.
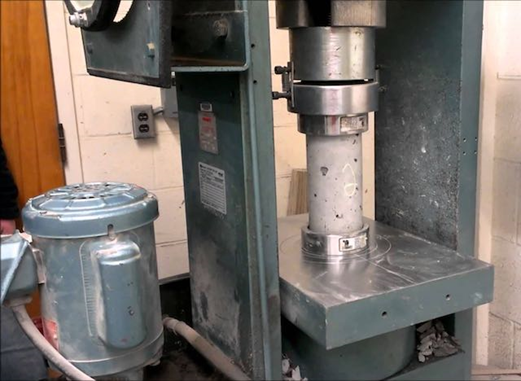
Fig no 8 Compression Testing Machine
Calculations:
Concrete Cylinder Loading Samples Compressive energy of the specimen is calculated through dividing the most load carried through the specimen all through the check with the common cross-sectional area.
Determine and specific the end result to the closest 10 psi (0.1 M Pa).
Key takeaways
The electricity of air-dried cores is on common 14 percentage large than the electricity of soaked cores.
Flexural Strength
Objective:
- To decide the Flexural Strength of Concrete, which comes into play whilst a avenue slab with insufficient sub-grade guide is subjected to wheel masses and / or there are extent modifications because of temperature / shrinking.
Equipment & Apparatus:
- Beam mildew of length 15 x 15x 70 cm (whilst length of mixture is much less than 38 mm) or of length 10 x 10 x 50 cm (whilst length of mixture is much less than 19 mm)
- Tamping bar (forty cm long, weighing 2 kg and tamping phase having length of 25 mm x 25 mm)
- Flexural take a look at gadget– The mattress of the checking out gadget will be furnished with metal rollers, 38 mm in diameter, on which the specimen is to be supported, and those rollers will be so hooked up that the space from centre to centre is 60 cm for 15.0 cm specimens or forty cm for 10.0 cm specimens.
- The load will be implemented via comparable rollers hooked up on the 1/3 factors of the assisting span that is, spaced at 20 or 13.3 cm centre to centre.
- The load will be divided similarly among the 2 loading rollers, and all rollers will be hooked up in this sort of way that the burden is implemented axially and without subjecting the specimen to any torsion stresses or restraints.
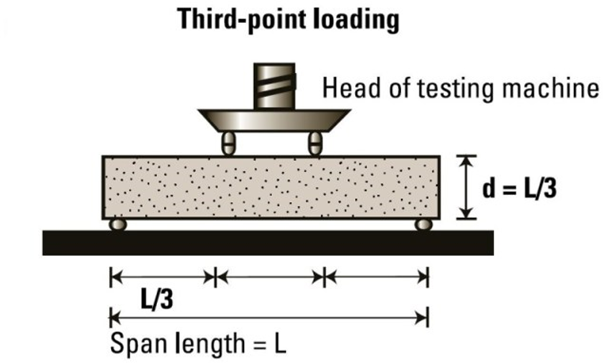
Fig no 9 Flexural testing machine
Procedure:
- Prepare the check specimen via way of means of filling the concrete into the mold in three layers of about identical thickness.
- Tamp every layer 35 instances the use of the tamping bar as distinct above.
- Tamping have to be disbursed uniformly over the whole cross section of the beam mildew and in the course of the intensity of every layer.
- Clean the bearing surfaces of the assisting and loading rollers , and get rid of any free sand or different cloth from the surfaces of the specimen in which they may be to make touch with the rollers.
- Circular rollers synthetic out of metallic having pass phase with diameter 38 mm may be used for presenting assist and loading factors to the specimens.
- The duration of the rollers will be at the least 10 mm greater than the width of the check specimen.
- A general of 4 rollers will be used, 3 out of which will be able to rotating alongside their very own axes.
- The distance among the outer rollers (i.e. span) will be 3d and the gap among the internal rollers will be d.
- The internal rollers will be similarly spaced among the outer rollers, such that the whole gadget is systematic.
- The specimen saved in water will be examined right away on elimination from water; while they may be nevertheless wet.
- The check specimen will be positioned with inside the device efficiently targeted with the longitudinal axis of the specimen at proper angles to the rollers.
- For mould specimens, the mold filling route will be ordinary to the route of loading.
- The load will be implemented at a price of loading of 400 kg/min for the 15.0 cm specimens and at a price of 180 kg/min for the 10.0 cm specimens.
Calculation:
- The Flexural Strength or modulus of rupture (fb) is given via way of means of
- F b = pl/bd2 (while a > 20.0cm for 15.0cm specimen or > 13.0cm for 10cm specimen)
O r
- F b = 3pa/bd2 (while a < 20> 17.zero for 15.0cm specimen or < 13> 11.0cm for 10.0cm specimen.
Where,
a = the gap among the road of fracture and the closer assist, measured at the middle line of the tensile aspect of the specimen
b = width of specimen (cm)
d = failure factor intensity (cm)
l = supported duration (cm)
p = max. Load (kg)
Safety & Precautions:
- Use hand gloves while, protection footwear on the time of check.
- After check transfer off the device.
- Keep all of the uncovered metallic elements greased.
- Keep the manual rods firmly constant to the bottom & pinnacle plate.
- Equipment have to be wiped clean very well earlier than trying out & after trying out.
Key takeaways
1. Beam mildew of length 15 x 15x 70 cm (whilst length of mixture is much less than 38 mm) or of length 10 x 10 x 50 cm (whilst length of mixture is much less than 19 mm)
Indirect Tensile Strength
- Indirect dynamic strength changes were tested from six samples: three dry samples and three samples exposed to water.
- During the indirect strength test, the sample is attached between two load strips and loaded freely at a speed of 50mm / min.
- The maximum load on the crack is measured. The relationship of energy values before and after water storage is determined, and is called the Indirect Tensile Strength Ratio (ITSR).
- Similar to the indirect strength test, a single-axial direct tensile test was initiated to investigate the strength structures of the study. Also, the strength was determined before and after preparing the test sample in the bath water according to EN 12697-12 B.
- The test samples used in this study included prismatic samples of the asphalt compound, as well as rods extracted from the rock and glued together with bitumen film.
- In the testing of dominant asphalt beams, every six beams are cut into slabs of composite asphalt composite (three dry, three wet). Adapters are attached with adhesives to the two parts of the sample surface.
- This is required to load samples into the machine. Strength strength is applied at a speed of 1.5mm / min at a temperature of 15 ° C. After the sample cracking, the strength of the strength is determined from high pressure, and the exact amount of strength strength (DTSR) accordingly.
- Similarly, direct strength testing was also applied to the extruded walls. On the rock covered and glued together the bitumen film.
- The power test is performed with different loading speeds and test temperatures. The broken sample.
- The materials investigated in this study include various types of bitumen (50/70, 70/100), bitumen modified polymer (PmB 40 / 100-65H, PmB 45A), of a wide range of natural materials from adhesive adhesives to adhesive markers. Fine (basalt, Taunusquarzite, limestone, granite, gabbro), and four types of asphalt mixtures (AC 11, AC 16, SMA 11, PA 8).
- Details of the composite, bitumen-aggregate composites, types of asphalt composites and related tests. Preliminary tests have shown that high image quality is very important for reproduction, because both the base installation and the descent frame depend on contrast of the image brightness.
- Therefore, image quality was guaranteed by the introduction of low levels of brightness, contrast, and sharpness of the image as measured by DSA1 software.
- About 10% of the images produced failed to meet these standards and were not included in further analysis. A small number of usable metrics are defined as 30 data points per bit bitumen.
- The data only show slightly different outputs for multiple samples, with the exception of PE6506, and the standard deviation (SD) of the method generally compared the differences between the contact angles of different locations.
- To determine whether communication angles are very different or not, statistical testing methods have been used. The first Shapiro- Wilk test was used for standardized testing. It confirms the general distribution of data. Subsequently, variance analysis (ANOVA), in particular data was subjected to the F test.
- Including all samples tested, the F test rejected the absurd notion that communication angles are very different, i. e. a group of mediators is very different from each other.
- As the mean values of PE6506 deviated significantly from the data of other bitumen, the test was repeated without PE6506. The result shows that in this experiment only PE6506 can be separated from a number of other samples, which can also be separated between them.
- Pendant suction measurements are performed using five bitumen and bitumen precursors. Excess power is measured as a heat function.
- Linear regression analysis can be used in addition to other adjacent conditions because the samples show a very similar pattern at higher temperatures, but a different tendency to deal with lower.
- For example, the two releases include a 95% confidence interval time. Places are very advanced. The results of the addition of all the bitumen studied including error bars, which are found in the external confidence interval.
- The general overlap indicates that this method cannot distinguish between the tested samples. Therefore, the development of testing in relation to rebirth is necessary. The use of small glass slides as a basic model of bitumen-mineral aggregate interface has several advantages.
- First, the surface is perfectly smooth and chemically uniform. Second, the chemical properties of glass are similar to the composition of highly acidic minerals, which usually have a very high content of SiO 2.
- To test the strength of this test, two samples of bitumen (50/70 and 70/100) and a mixture of these bitumen and adherence agent were tested (50/70 + and 70/100 +). New drops of bitumen in the glass gave the same effect to all bitumen.
- After being stored at 70 ° C for 30 minutes, in addition to the bitumen softening points (50/70 and 50/70 +: 48 ° C; 70/100 and 70/100 +: 45 ° C) the results were different. Communication angles are very different from each other. The contact angles of pure bitumen are around 6 ° below the mixtures.
- This means, however, that wettabilities are worse with bitumen containing the input. The final variation of this test was the introduction of static water storage.
Key takeaways
- Indirect dynamic strength changes were tested from six samples: three dry samples and three samples exposed to water.
- During the indirect strength test, the sample is attached between two load strips and loaded freely at a speed of 50mm / min.
Core Test
- Basic concrete testing is the most popular and well-established test method for the compressive strength of hard concrete. Critical concrete testing makes visual inspections of the internal parts of the concrete member also related to strength limitations Portable coring enables the inspection of other reinforced concrete structure structures with solid concrete testing
- In any case, the need to perform basic concrete tests often stems from the failure of concrete cubes / cylinders to get a realistic view of the strength of concrete as it exists in construction materials
Sampling of concrete core
It is very important that basic concrete samples are taken according to the guidelines given below
- Cores should be taken using pieces of diamond-filled spinal cord.
- Cores tested for power structures should have a minimum diameter three times the size design size of a rated set or 50 mm. Whoever is great
- Where possible, cores tested for energy structures should be at least twice their length width
- As far as it is concerned that the reinforcing metal should not be inserted into the spine to be tested for strength. The size, number, and location of the metal reinforcement in the proposed primary area can be determined by using magnetic resonance imaging such as a retrieval meter (cover meter) or by ground-based radar testing or by using a pull-out radar system. If the spine contains a flexible reinforcing steel, a certain effect on the strength should be expected There is a possibility of a decrease in the strength of the concrete slab depending on the position of the steel. This effect is especially important when the metal is very far from the end of the set.
- As far as possible, the foundation pit should penetrate completely into the concrete section. This prevents spinal fractures and facilitates their removal. On the other hand, if drilling is not possible due to the size and configuration of the building in the area where the coring is planned, an additional 50 mm should be bound as a share of potential damage to part of the context.
- One root should not be used to diagnose a specific problem. When cores are taken gain power, a minimum of three characters need to be removed from each location. The amount of concrete strength in the hole should be taken as the benefit of these grains
- Special care needs to be paid when choosing a place for the concrete for standing concrete members such as walls, deep beams, etc. This is due to the differences in high-rise concrete structures due to differences in laying and mixing processes, separation, and bleeding. It is known that in general, the strength of concrete decreases as its height within the placement of membership increases.
- The exact history of structural treatment is often difficult to obtain so the effect of cooling the ammunition is also uncertain. When there is no wet treatment, no power expectations should be expected
- The direction of the ball also affects the strength of the bullets. Horizontally bound cores usually have lower power than direct bound calls,
- When cutting the core, the integrity of the concrete structure in the full section (c / s) is possible is affected to some degree. This feature should be taken into account when selecting a location where the file the core should be taken
Concrete Test procedure
Concrete pieces are usually cut with rotating cutting tools with diamond pieces. The cylinder sample is obtained by concluding its unequal pieces of equal parts, square, and embedded.
Cores are inspected visually to pay attention to the distribution of the composite, the compaction of concrete (non-air visibility), and the presence of metal, etc. The concrete slab should be soaked in water, soaked in melted sulfur so that it ends up parallel to the right angle. It is also tested on a pressure-testing machine in wet conditions in accordance with BIS 1881: Part 4: 1970 or ASTM 42-77.
Use of concrete core sample
- Water or gas leakage
- Chemical analysis
- ASHTO chloride permeability testing
- Determination of strength and resilience
- Depth of concrete installation
- Petro graphic Analysis
Key takeaways
- Cores should be taken using pieces of diamond-filled spinal cord.
- Cores tested for power structures should have a minimum diameter three times the size design size of a rated set or 50 mm. Whoever is great
- Where possible, cores tested for energy structures should be at least twice their length width
Non-Destructive Test - Rebound Hammer
Objective:
- The rebound hammer technique might be used for:
- Assessing the possibly compressive electricity of concrete with the assist of appropriate correlations among rebound index and compressive electricity,
- Assessing the uniformity of concrete,
- Assessing the excellent of the concrete in relation to traditional requirements, and
- Assessing the excellent of 1 detail of concrete when it comes to another.
Principle:
- When the plunger of rebound hammer is pressed in opposition to the floor of the concrete, the spring controlled mass rebounds and the volume of such rebound relies upon up on the floor hardness of concrete.
- The floor hardness and consequently the rebound is taken to be associated with the compressive strength of the concrete.
- The rebound is examine off alongside a graduated scale and is unique as there sure variety or rebound index.
Procedure:
- For trying out, smooth, easy and dry floor is to be selected. If loosely adhering scale is present, this have to be rubbed of with a grinding wheel or stone. Rough surfaces due to incomplete compaction, lack of grout, spalled or tooled surfaces do now no longer deliver dependable outcomes and have to be avoided.
- The factor of effect is to be at the least 20 mm far from any facet or form discontinuity.
- For taking a measurement, the rebound hammer is to be held at proper angles to the floor of the concrete member. The check can as a result be performed horizontally on vertical surfaces or vertically upwards or downwards on horizontal surfaces. If the state of affairs demands, the rebound hammer may be held at intermediate angles additionally, however in every case, the rebound variety may be unique for the equal concrete.
- Rebound hammer check is performed round all of the factors of remark on all on hand faces of the structural detail. Concrete surfaces are very well wiped clean earlier than taking any measurement.
- Around every factor of remark, six readings of rebound indices are taken and common of those readings after deleting outliers as consistent with IS: 8900-1978 turns into the rebound index for the factor of remark.
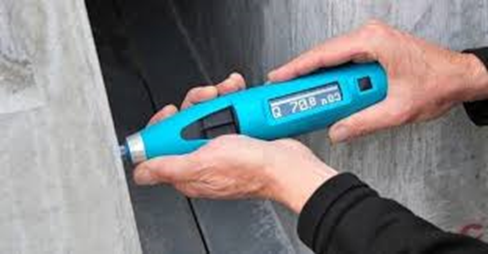
Fig no 10 Showing Rebound Hammer
Interpretation Of Result:
- The rebound hammer technique offers a handy and speedy indication of the compressive energy of concrete via organism appropriate correlation among the rebound index and the compressive energy of concrete. The process of acquiring such correlation is given in 4.2.
- It is likewise mentioned that rebound indices are indicative of compressive energy of concrete to a constrained intensity from the floor. If the concrete in a selected member has inner micro cracking, flaws or heterogeneity throughout the cross-section, rebound hammer indices will now no longer imply the equal.
- As such, the estimation of energy of concrete with the aid of using rebound hammer technique can't be held to be very correct and in all likelihood accuracy of prediction of concrete energy in a shape is ±25 percent.
- If the connection among rebound index and compressive energy may be checked with the aid of using assessments on center samples acquired from the shape or well known specimens made with the equal concrete substances and blend proportion, then the accuracy of consequences and self belief thereon are substantially increased.
Key takeaways
- The rebound is examine off alongside a graduated scale and is unique as there sure variety or rebound index.
Ultrasonic Pulse Velocity
- This take a look at is accomplished to evaluate the nice of concrete with the aid of using ultrasonic pulse pace technique as according to IS: 13311 (Part 1) – 1992. The underlying precept of this take a look at is –
- The technique includes measuring the time of journey of an ultrasonic pulse passing via the concrete being tested. Comparatively better pace is acquired whilst concrete nice is ideal in phrases of density, uniformity, homogeneity etc.
- Procedure to decide energy of hardened concrete with the aid of using Ultrasonic Pulse Velocity:
- Preparing for use: Before switching at the ‘V’ meter, the transducers ought to be linked to the sockets marked “TRAN” And ” REC”.
- The ‘V’ meter can be operated with either:
a) The inner battery,
b) An outside battery or
c) The A.C line.
- Set reference: A reference bar is supplied to test the tool zero. The pulse time for the bar is engraved on it. Apply a smear of grease to the transducer faces earlier than putting it on the other ends of the bar. Adjust the ‘SET REF’ manage till the reference bar transit time is acquired at the tool read-out.
- Range selection: For most accuracy, it's miles endorsed that the 0.1 microsecond variety be decided on for route duration up to 400mm.
- Pulse pace: Having decided the maximum appropriate take a look at factors at the fabric to be tested, make cautious dimension of the route duration ‘L’. Apply couplant to the surfaces of the transducers and press it tough onto the floor of the fabric. Do now no longer flow the transducers whilst a analyzing is being taken, as this could generate noise indicators and mistakes in measurements. Continue keeping the transducers onto the floor of the fabric till a steady analyzing seems at the show, that's the time in microsecond for the ultrasonic pulse to journey the distance ‘L’. The imply price of the show readings ought to be taken whilst the gadgets digit hunts among values.
Pulse pace= (Path duration/Travel time)
- Separation of transducer leads: It is really helpful to save you the 2 transducer leads from getting into near touch with every different whilst the transit time measurements are being taken. If this isn't always accomplished, the receiver lead would possibly pick-up undesirable indicators from the transmitter lead and this will bring about an wrong show of the transit time.
Interpretation of Results:
- The nice of concrete in phrases of uniformity, occurrence or absence of inner flaws, cracks and segregation, etc, Indicative of the extent of expertise employed, can as a consequence be assessed the use of the recommendations given below, that have been advanced for characterizing the nice of concrete in systems in phrases of the ultrasonic pulse pace.
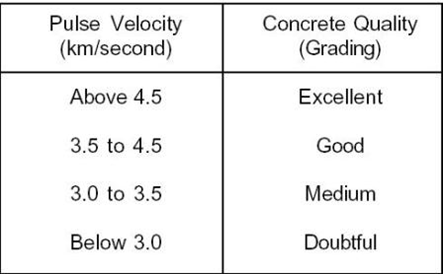
Fig no 11. Table of pulse velocity
Key takeaways
2. Set reference: A reference bar is supplied to test the tool zero. The pulse time for the bar is engraved on it. Apply a smear of grease to the transducer faces earlier than putting it on the other ends of the bar. Adjust the ‘SET REF’ manage till the reference bar transit time is acquired at the tool read-out.
Pullout Test and Impact Echo Test
Pullout Test
The principle
This test is based on the principle that the force required to extract a metal coating embedded in concrete is equal to the strength of the concrete.
Test Process
Remove the insert (shown on the fig tree) embedded in the empty concrete during pouring. When power is required to be determined, power is applied to the embedded end. The power required to issue a meeting is measured.
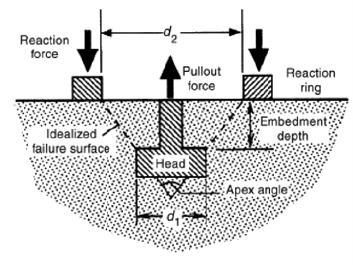
Fig no 12. Pull out the concrete test
Limitations
The steel assembly should be embedded in concrete at the time of pouring so testing may not be carried out in the years to come.
Damage to damaged concrete is required.
Evaluation
- The extraction assembly is pulled by a concrete cone, which is responsible for friction and shaving and the force required to exit is related to the cutting strength of the concrete and not the compressive force.
- The rate of dissipation in the compression force decreases slightly with increasing power level.
- Removal cannot be performed until complete. It is sufficient to insert a fixed power into the embedded pole and if not removed, the supplied power is assumed to exist.
- According to Malhotra, the output test is higher than the Schmidt hammer and the input test because a large volume and depth of concrete are involved in the test. Post-test concrete repairs are also required. The relationship between the force of gravity and gravity is shown in the figure below.
Impact Echo Test
Impact-Echo is a non-destructive exploration method for exploring concrete structures and stone structures. The test uses pressure waves (sound) that are usually made of impact-impact concrete, and to record thinking and emissions from internal errors and other parameters (Echo). Typically, a heartbeat is performed with an effect in one place. The resulting wave of depression is spreading in all directions. In this regard, the generated wave does not have a directional pulse generated by a large transducer (as in the case of ULTRASONIC PULSE VELOCITY). As the reflection reaches in all directions, the test method works well for thin objects, such as piles where the outer boundary directs the wave to the pile. In this particular application, the test is set as the low-level strength test. Learn more about the PILE INTEGRITY TEST.
Concept Behind Impact-Echo Method
The concept of Impact-Echo testing is shown in Figure. The mechanical impact of the concrete surface is used to produce a pressure wave. The production pulse creates a spread across the concrete next to circular waves such as P- and S-waves. Another is the surface wave (R) that moves over.
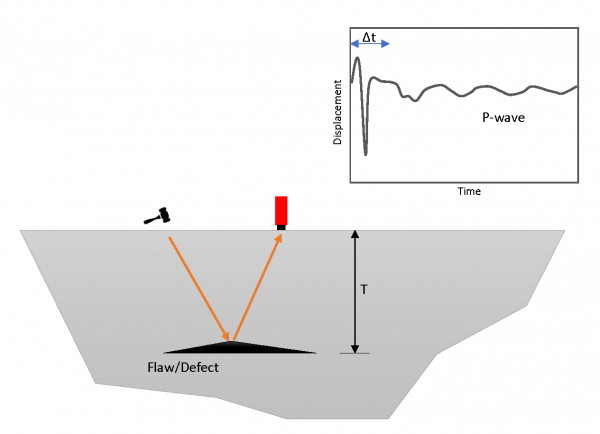
Fig no 13. Impact echo method
As the P- and S waves propagate inside the concrete object, they are indicated by internal interactions (concrete-split, air-concrete, concrete -rebar) or external boundaries. The arrival of these echo in the face causes migration. This migration can be measured by placing a sensitive transducer (which converts the transmission or acceleration of electrical energy). Data is recorded through a data acquisition and data entry system.
Analyses Impact-Echo data
Data analysis can be done in Time Domain, or Frequency Domain. While time domain analysis seems to be the best way to define sensitive data (as in the case of bulk testing), it can be a much more complex approach in the case of small slabs. In these sections, signal analysis in the domain of frequency is popular.
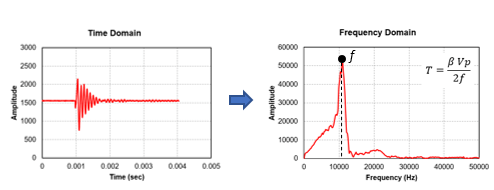
Fig no 14. Analysis of impact echo method
The Fast Fourier transform (FFT) process is used to analyze digital frequency frequency recordings. In this way, the wave form can be represented as a total of sine curves, each with a certain height, frequency and phase shift. According to N. J. Carino. This method is used to calculate the amplitude magnitude of a frequency form, which gives the relative height of the fractional frequencies in the wave form.
Impact-Echo Technique Applications
Impact-Echo is an effective test solution with a variety of applications in assessing the condition of concrete structures. The test can be used to:
1- Measure the thickness of the concrete labs and walls
2- Measure the thickness of the concrete walls and the tunnel line
3- Identify deformities such as delamination in concrete books.
4- Measure the storage condition of concrete, dams, tunnel lamps, sea walls.
Key takeaways
- This test is based on the principle that the force required to extract a metal coating embedded in concrete is equal to the strength of the concrete.
- Impact-Echo is a non-destructive exploration method for exploring concrete structures and stone structures. The test uses pressure waves (sound) that are usually made of impact-impact concrete, and to record thinking and emissions from internal errors and other parameters (Echo).
- Good quality concrete is actually a compact mixture of cement, composite and good mixing with water that mixes into a hard mass due to the chemical action between cement and water.
- Each of the four regions has a specific function. The coarser collection serves as a filler. A good collection fills the gaps between the attachment and the green combination. Cement by contact with water acts as a bond.
- The flow of the mixture is aided by the adhesion of cement, fines to this day, increasingly using mixtures.
- Most of the reinforced concrete materials depend on the care used in all stages of concrete production. The logical separation of concrete ingredients is the core of the mixing design.
- However, it may not guarantee the achievement of the goal of quality workmanship. The purpose of quality control is to ensure the production of concrete of the same power from batch to batch.
- This requires that certain rules be followed in the various stages of concrete production and discussed below. The stages of concrete production are:
1. Batching and measurement of material
2. Mixing
3. Transport
4. Placement
5. Compacting
6. Curing
7. Finishing
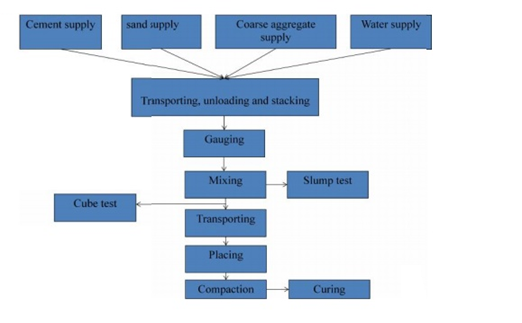
Fig no 15. Manufacturing process of concrete
Batching of material
- For good quality concrete should be used the correct and accurate amount of all ingredients. Combined, cement and water must be measured with an accuracy of 3 percent of batch quantity and admixtures at 5 percent of the total value. There are two most common forms of baking material, batching volume and heavy batching. Factors affecting the choice of baking method by the size of the work, the required production rate, the required batching performance standards. It is recommended for the most important tasks.
a) Volume batching
b) Weight batching
Mixing
1. Hand Mixing
2. Mixing Machine
a) Tilting mixers
b) Non- tilting mixer
c) Reversing Drum mixer
d) Pan type or stirring mixer
e) Transit mixer
f) Charging Mixer and mixing time
The order for the ingredients in the mixer is as follows:
- About 25 percent of the water needed for mixing is initially placed in the mixing tank to prevent any cement attachment to the rings and bottom of the drum. Then the ingredients are extracted in excess. To skip over the loading sequence should be to insert the first half of the coarse cement and then the composite half to be on top of this complete cement and the aggregate to balance. After adding the ingredients to the drum equal volume was introduced. The mixing time is calculated from the total water added to the mixture.
- The speed of the aggregates is usually 15 to 20 per minute. With proper mixing, the number of changes per minute required by the drum is 25 to 30. The mixing time also depends on the mixing capacity
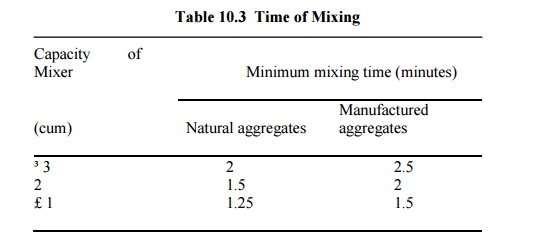
Fig no 16. Table of mixing
- Poor quality of concrete is obtained when mixing time is reduced. On the other hand if the mixing time is extended it is not economical. However, it is found that when the mixing time is extended to 2 minutes the compressive strength of the produced concrete is improved and beyond this time the improvement of the compressive strength is not significant. Prolonged mixing can cause separation. Also, due to the long mixing times water can get in or out and lead to loss of function and energy.
Transporting
The concrete should be moved to the storage area immediately without the loss of homosexuality acquired during mixing. a maximum of 2 hours from mixing time is allowed if trucks have an agitator and 1 hour using trucks without stimulants to move the concrete. And it must be ensured that separation does not occur during travel and placement. The methods used to transport concrete depend on the quality and value of the work, the distance to the placement site, and the location. Some of the concrete delivery methods are below:
a. Mortar pan
b. Wheel barrow
c. Chutes
d. Dumper
e. Bucket and ropeway
f. Belt conveyor
g. Skip and hoist
h. Pumping
Placing
- Achieving quality concrete should be placed very carefully to protect the homosexuality achieved during mixing and to avoid transport segregation. Studies have shown that delays in the installation of concrete results in gaining greater compressive strength as long as the concrete is not sufficiently compacted. In dry mixes in hot weather a delay of half an hour is allowed and in wet mixtures when it is cold it can be a few hours. The various conditions in which concrete is applied are discussed below.
Foundations
- Concrete foundations for walls and columns are provided underground. Before laying concrete on the foundation all open ground, tree roots etc., are removed. If the area is found dry it is made wet so that the soil does not absorb water from the concrete. On the other hand when the foundation bed is wet the water and mud are removed and the cement is sprinkled before laying the concrete.
Beams, columns and slabs
- Before laying the concrete, the forms must be inspected for proper alignment. They should be strong enough to withstand the weight of concrete and construction loads without undue damage. The forms should be light enough to avoid any mud loss that has resulted in concrete mixed with bees. The inside of the forms should be cleaned and oiled before use to avoid any adhesion to the concrete and forms and make it difficult to remove them.
- Concrete should not be discarded but should be placed in a place to protect against discrimination. It should be lowered as high as possible. It should be placed in one place on the formwork and allowed to flow in separate ways to take care of the bee colony.
- The formation of seas should be avoided. Can be tested by preventing concrete thickness by 150-300 mm with r c c function. Laitance, however, if constructed must be removed before laying the next layer of concrete. Several such layers form an elevator, as long as they follow each other fast enough to avoid cold joints. The top of the previous elevator is kept rugged and all the money spent is wiped out before setting the next elevator.
- Firmness should be checked for firmness and clean face. Rust or loose scales if present, are removed with a wire brush. Paint, oil or grease if found should be removed. a small tightening cover should be checked before assembly.
Mass concreting
- Where the concrete will be laid in bulk as a foundation for raft, dam, bridge, pier etc., the concrete is laid in sections of 350-450 mm in diameter. Several such layers arranged in quick succession form an elevator. Before applying the concrete to the next lift, the front elevator area is thoroughly cleaned with water jets and scrubbing with a wire brush. In the case of dams, sand explodes.
- Laitance and lax matter are removed and cement mortar is applied. Where the concrete is subjected to lateral thrust, binding bars or binding stones are provided to form the key between the various layers.
Concreting Highways and Runways
- Concrete is placed in the areas of highway, open road, or floor slabs. First the soil on which the concrete is to be placed is prepared and all loose material and grass are removed etc. The ground is wet and compacted. The subgrades into which the concrete is to be placed should be well mixed and diamond-plated to avoid any moisture loss in the concrete. The concrete is then placed elsewhere. This allows the concrete to pass through enough and the cracks do not grow after that. Concrete is not placed in a pile in one place and then pulled out, instead it is placed in the same size.
Concreting underwater
- Concrete can be placed under water with the help of dumping buckets. The concrete is soaked in water from a water-tight bucket. When you get to the floor the bucket is made open and the concrete is discarded. In this process a certain amount of cement is washed away resulting in a decrease in the strength of the concrete. Another way to make underwater concrete is to fill a bag of cement with a dry or dry mixture of cement and aggregates and lower it into the storage area. The downside to this approach is that the concrete will fill the gaps filled with the bags with the guns.
- A good way to put concrete under water is to use a termie pipe. Concrete is poured into it by a ditch. The lower edge of the pipe is covered with thick ploythene paper, below the pipe in the installation area. Concrete (150-200 mm fall) is poured into the mortar until the entire pipe is filled with cement. The pipe is slightly raised and given a jerk, the polythene metal cover falls off and the concrete is shown. It must be ensured that the end of the pipe stays inside the concrete so that water does not enter the pipe. The pipe is then filled with concrete along the border and the process is repeated to the concrete level above the water level. No reduction is required for underwater concrete as combined with hydrostatic water pressure. Concrete can also be placed under water with the help of pipes and pumps.
Compaction of concrete and curing process of concrete
1) Compaction of concrete
- Concrete should be thoroughly compacted and fully work around the reinforcement and into the corners of the formworks
- Concrete shall be compacted using mechanical vibrators
- Whenever vibration has been applied externally the design of formwork and the deposition of vibrators should receive special consideration to ensure efficient compaction and to avoid sir face blemishes
2) Curing process of concrete
- Curing of concrete is defined as the process of maintaining the moisture and temperature condition of concrete for hydration reaction to the normally so that the concrete develops hardened and properties over time
- The main components which need to be taken care of your heat and time during curing process
- Curing is the process of preventing the loss of moisture from the concrete which maintaining a satisfactory temperature effect
- If the cement has high rate of strain development and if the concrete contains granulated blast furnace and flue Ash then,
- The curing should also prevent the development of high temperature gradients within the concrete
a) Moist curing
- Surface of the concrete shall be kept continuously in Dam or wet condition by covering with the layers of materials like checking Canvas etc.
- It should be kept continuously wet for at least 7 days from the date of placing concrete.
- In case of ordinary Portland cement at least 10 days. Where mineral admixture or blended cement are used.
- The period of curing shall not be less than 10 days for concrete exposed to the dry and hot weather condition.
- In case of concrete where mineral admixture or blended cement are used it is recommended that above minimum period may be extended 14 days.
b) Membrane curing
- Approved curing compounds may be used in place of moist curing with the permission of engineer in charge.
- Search compound shall be applied to all exposed surfaces of the concrete as soon as possible after the concrete has set.
- Impermeable membrane such as polyethylene sheeting covering closely the concrete surface may also be used to provide effective barriers against evaporation.
- For the concrete containing Portland pozzolana cement, Portland slag cement or mineral admixture period of curing may be increased.
NOMINAL MIXES
- In concrete mix concrete, all ingredients and their size are determined by standard definitions. This ratio is specified in the cement ratio to the specific energy gain combination.
- Mixing ratios such as 1: 1.5: 3, 1: 2: 4, 1: 3: 6 etc. They were adopted by mixing concrete without a scientific basis, only on the basis of previous studies of solidarity. Therefore, acceptance of ordinary concrete or not to mention, the mixing of preference is preferred for simple, insignificant and minimal concrete works.
- According to the 'Indian Standard- IS 456: 2000', pre-mixed concrete can be used for M20 grade concrete or lower grade such as M5, M7.5, M10, M15.
Proportion of nominal mix as per Indian Standard
- The volume of composite materials under M20 grade concrete will comply with IS 456: 2000
- According to IS 456: 2000, in the composition of the composition can be adjusted the estimated values if the water level will be increased to overcome the difficulty of laying and density of concrete so that the water level of the cement is maintained as specified.
- Automatic mixing usually consists of volumetric batching. The measurement is usually determined by weight, and in combination it is converted to a volume value, i.e. in the case of one bag of cement, i.e. 50 kg of standard measuring boxes are made on site, at the rate of one bag of cement. These measuring boxes are called box gauges.
Advantages of nominal Mix Concrete
01. A self-proclaimed mix is a pre-determined concrete because the scale is pre-determined.
02. It is easy to do in the construction site.
03. It does not take much time to determine the value because the size is already provided with the standard code.
04. There is no need to find people who have the skills to make concrete mixing name.
Disadvantages of nominal mix concrete
01. The great recurrence of the mix of claims is that, it is based on past experience and studies of art, and has no scientifically proven method.
02. It can create or build well-designed energy unless all other factors such as density, w / c ratio, concrete treatment are strictly adhered to.
03. The amount of water cement is considered by thought and, if left unchecked, sometimes leads to bleeding and separation of the concrete which leads to poor performance and therefore impairs the strength of the concrete.
04. No consideration of composite structures such as classification and quantity of composite items etc.
05. In a word mix, cement content is sometimes used in excess, which increases the total cost of construction.
06. No laboratory tests are performed to ensure the quality of the new concrete.
07. This combination does not consider and evaluates the specific properties of each ingredient. For example, if we take cement as part, the softness of the cement, the quality of the cement and the type of cement, the size and layout of the composite etc. It is usually not counted individually when making this fake assertion mix.
Key takeaways
- In concrete mix concrete, all ingredients and their size are determined by standard definitions. This ratio is specified in the cement ratio to the specific energy gain combination.
- Mixing ratios such as 1: 1.5: 3, 1: 2: 4, 1: 3: 6 etc. They were adopted by mixing concrete without a scientific basis, only on the basis of previous studies of solidarity. Therefore, acceptance of ordinary concrete or not to mention, the mixing of preference is preferred for simple, insignificant and minimal concrete works.
- According to the 'Indian Standard- IS 456: 2000', pre-mixed concrete can be used for M20 grade concrete or lower grade such as M5, M7.5, M10, M15.
Freeze-Thaw Effect:
Concrete is very strong in compression but relatively weak in tension. It can and often does crack. Concrete is also fairly porous and subject to forces that absorb and release water. Absorbed water can freeze within the concrete and cause spalling and cracking.
Chemical Attack:
Chemical attack can occur because concrete is alkaline and chemically reactive. It can be attacked by acids; some alkalis; numerous salt solutions; and organics such as fermenting liquids, sugars, and animal oils, especially if they contain free acids.
Crazing:
This is a network of very small surface cracks usually spreading out over large areas or the entire surface. Crazing is caused by finishing the concrete with bleed water on top. The bleed water is forced down into the surface by the finisher’s trowel. This increases the ratio of water to cement, creating a weak surface layer.
Scaling:
Thin flakes of concrete come loose and flake or peel off the surface. The sizes of the flakes vary, but they usually increase over time and with traffic. Conditions that cause scaling and include freeze/thaw cycles, deicing agents with calcium or sodium chloride, fertilizers containing nitrates, working in bleed water, or improper curing.
Blisters:
These are typically about 1/4 to 1 inch diameter, but it’s not impossible to get 3 to 4 inch blisters. They are not easily seen until they are broken by traffic. Blisters are caused by working and finishing the surface while water or air is still working its way up through the mix to the surface.
Spalling:
Spalling is similar to scaling except large chunks instead of just flakes break loose. This indicates a severe weakness in some parts or the entire project. It is more likely to happen during freeze thaw conditions.
Dusting:
Also known as chalking, this is a fine loose powder caused by the deterioration of a weak surface. Causes of dusting include working in bleed water, improper curing, a bad sand-to-cement ratio, or exposure to carbon monoxide caused by using an unvented heat source to keep a project warm.
Foreign Objects:
Foreign objects can often slip into the form prior to pouring and may not become evident until after the forms are stripped. If fully embedded, the foreign object does not create a coating problem. But a piece of rope on the surface disappearing into the concrete is a problem. It must be removed, usually by chipping, and the concrete must be restored.
Efflorescence:
Efflorescence is more likely to be found on concrete that has been in place for a while. Concrete contains water-soluble salts. As water from the interior of the concrete migrates to the surface and evaporates, salts are deposited on the surface, usually as a white stain. Efflorescence can occur with concrete, brick, or concrete block construction. It can be removed with acid etching. The best way to prevent its recurrence is with adequate waterproofing.
Service / Market Area:
For industrial and commercial flooring projects we work in Michigan cities such as Muskegon, Norton Shores, Newaygo, Traverse City, Big Rapids, etc.
- Many types of admixtures or additives change the performance of a new concrete, either by construction or as a side effect.
- Surfactants such as super plasticizers reduce the attraction between cement and composite particles, allowing compounds that can flow without negative energy and the effects of excess water separation.
- The insertion of internal admixtures of durability / dissolving solids produces internal bubbles of a controlled size that can make it easier to eliminate, although overuse produces an adhesive mix with a different effect.
- The pressure of the concrete is eight times greater than its strength.
- This refers to the established relationship between the compressive strength and the strength of the concrete. In fact there is a close relationship but not a direct relationship.
- The degree of stiffness and pressure is low at high pressures.
- Experimental results also showed that concrete in stress and stress (both direct and indirect tension) is highly correlated but the relationship does not have a direct equation.
- The degree of strength and durability depends on the strength of the concrete.
- Thus, the increase in tensile strength, increases the tensile strength, but the rate of increase in tensile strength decreases steadily.
- The strength of concrete is more sensitive to improper treatment than to compressive strength.
This is possible for two reasons:
(a) The formation of a low-grade gel due to improper treatment.
(b) The formation of multiple shrinking cracks due to improper treatment. The use of pozzolanic materials showed an increase in strength.
- The Central Road Research Institute Delhi has conducted extensive research to build a relationship between the strength and durability of concrete in the construction of concrete roads.
- Based on the research experimental data, CRRI suggested the following relationship between flexural strength and concrete compression strength:
y = 11 x - 3.4
- Where is the compressive strength of MPa concrete and x and its flexibility. This relationship depends on the size of the coarse aggregate. Energy is available to vary in type and quantity of composite.
Relationships are renewed below:
(a) With a crushed stone of 20 mm y = 15.3 x - 9.0
(b) 20 mm Natural Graval y = 14.3 x - 10.4
(c) For 40 mm Crushed Stones y = 9.9 x -5.5
(d) 40 mm Natural Graval y = 9.8 x - 2.5
Key takeaways
The pressure of the concrete is eight times greater than its strength.
This refers to the established relationship between the compressive strength and the strength of the concrete. In fact there is a close relationship but not a direct relationship.
There are three main factors that affect concrete compression results: the specimen size, shape, and friction at its ends. These factors affect the observed phenomena, and they affect each other. This paper aims to review the current knowledge on concrete compression and the effect of size, shape and friction on it. Understanding their effects is essential for a safer design and more effective testing.
- Creep and thinning concrete are the two most visible features of concrete. The shrinkage of concrete, derived from calcium silicate hydrate (C-S-H) in a hardened Portland cement compound (which is responsible for mineral compounds), is quite different from the tilt of metals and polymers.
- Unlike metal cracks, it occurs at all levels of stress and, within the service level of stress, depends on what is stressed if the pore water content remains the same.
- In contrast to the eruption of polymers and metals, it exhibits several months of aging, caused by chemical hardening due to hydration that strengthens the formation of micro-organisms, and age-old aging, resulting in long-term resting of small equal pressure in nano- low CSH formation. When the concrete is completely dry, it does not move, but it is almost impossible to dry the concrete completely without severe cracking.
- Changes in water content in the pore due to dryness or watering processes cause significant changes in the volume of the concrete in non-load-bearing species. They are called shrinkage
- The age-old insect varies logarithmically over time (except for the final asymptotic value), and over normal life spans can receive values 3 to 6 times larger than the initial stretch problem. When deformation formation is abruptly induced and held inconsistently, the movement causes a break in the pressure produced in moderation. After discharge, increased recovery occurs, but in part, due to aging.
- In practice, travel during drying is inseparable from diminishing. The flow rate increases with the rate of change of pore humidity (e.g., vapor pressure associated with the pores). In the size of a small model, the penetration during drying far exceeds the total reduction of load without load and the penetration of the closed-loop template. The difference, called the drying creep or Pickett effect (or pressure-induced decrease), represents a hygro-mechanical between pore changes and pore humidity.
- The drying of the high humidity is mainly due to the pressure pressures on the solid microstructure that measure the increase in capillary tension and the surface tension in the pore walls. At low pore humidity (<75%), the shrinkage is caused by a decrease in the binding pressure across all nano-pores less than 3 nm in diameter, filled with indicated water.
- The chemical processes of Portland cement hydration lead to another type of shrinkage, called automatic shrinkage, which is detected in closed specimens, i.e., without loss of moisture. In part, this is due to changes in chemical volume, but especially energy loss due to the loss of water used by the hydration reaction.
- It achieves only about 5% of the dryness in normal cones, which self-desiccate about 97% of pore humidity. However, it can be equivalent to the reduction of drying in today's high-strength concrete containers with very low cement levels, which can cause the floor to have a humidity of less than 75%.
- The creep comes from calcium silicate hydrate (C-SH) attached to Portland cement. It is caused by slips due to breakage of bonds, by restoration of bonds in nearby areas. C-SH is highly hydrophilic, and has a colloidal microstructure separated from a few nanometers upwards. The paste has a porosity of about 0.4 to 0.55 with a large internal surface, about 500 m2 / cm3. Its main component is tri-calcium silicate hydrate gel (3 CaO · 2 SiO3 · 3 H20, abbreviated C3-S2-H3). The gel forms particles of colloidal size, which are weakly bound by van der Waals forces.
- How it works and modeling is still debated. The structural model in the following scales is not only available but at the moment has a very solid theoretical basis and fits very well with the full range of test data available.
Key takeaways
- Changes in water content in the pore due to dryness or watering processes cause significant changes in the volume of the concrete in non-load-bearing species. They are called shrinkage
- A concrete blend is a mixture of 5 primary factor numerous proportions: cement, water, coarse aggregates, quality aggregates (i.e. sand), And air.
- Additional factors including pozzolana substances and chemical admixtures also can be integrated into the combination positive ideal properties.
- While a concrete blend layout is a system of choosing substances for a concrete aggregate and choosing their proportions.
- When designing a blend, you don't forget the favored power, durability, and workability of the concrete for the venture in question.
- Needless to say, Already-blend manufacturers attempt to locate the suitable proportions of those substances to optimize the concrete mixes and provide their concrete power, durability, workability, and different ideal properties.
- It’s crucial to optimize concrete to make sure the bottom keeping the very best power of your aggregate.
- Concrete blend layout is frequently mistake analysis “cement blend layout.” However, cement is since rely one of the substances of concrete.
- It is a binding substance that let sin concrete to set, harden, and cling to different substances.
- Therefore, it can't and ought to now no longer be used interchangeably with concrete blend layout.
Objective
The following are the objectives of the concrete mix design:
a. Finding the pressure force at a certain distance.
b. Maintain concrete mixing performance throughout the work.
c. By gaining strength.
d. Achieve economy by choosing the right concrete ingredients.
e. Getting the highest yield in a cement bag.
f. Avoid bee contact and bleeding.
g. Compliance with various levels.
h. Reduce concrete damage by proper measurement.
The proportioning of concrete mixes consists of determination of quantities of different concrete-making materials necessary to produce concrete having the desired workability and 28-days compressive strength of concrete for a particular grade of concrete and durability requirements. Emphasis is laid on making the most economical use of available materials so as to produce concrete of required attributes at the minimum cost.
Concrete has to be satisfactory both in fresh and hardened states. The proportioning of concrete mixes is accomplished by the use of certain established relationships from experimental data which provides reasonably accurate guidance for selecting the best combination of ingredients so as to achieve the desired properties of the fresh and hardened concrete. Out of all the physical characteristics of concrete compressive strength is often taken as an index.
- Strength and sturdiness of the concrete blend layout are established upon the subsequent factors:
- Grade designation: Concrete’s power is measured in N/mm2 whilst issue to check after curing in any curing medium. The preference of concrete grade relies upon on its utilization.
- Choice of cement: Cement preference varies relying on utilization. The cement have to be examined for overall performance required with the aid of using their utilization earlier than being examined with inside the layout blend.
- Choice of mixture size: Aggregates wanted for every blend depends upon the bodily houses wanted for the layout. All aggregates need to be nice sized earlier than use.
- Type of water: Any water used for concrete blend layout is to be examined earlier than use to make certain it's far with inside the variety of water required for concrete. Most all consumable water is right for concrete work, however have to nevertheless be examined.
- Water to cement ratio: The ratio of water to cement have to be examined for consistency, preliminary and very last setting, soundness of the cement, workability, hunch of the concrete and compacting factor.
- Workability: This is the degree of ease of blending concrete without segregation or bleeding. It by and large relies upon at the designed hunch of the concrete.
- Durability: This is the degree of the specified power (N/mm2) of any concrete grade after 28 days of curing. Durability have to be manipulate examined on site.
Key takeaways
- Here different type of factors which affects mix proportion are durability, workability, water to cement ratio, type of water, choice of mixture size, choice of cement, grade designation.
The following points highlight five methods of concrete construction. The methods are:
1. American Method of Mix Design
2. Graphic Method of Mix Design
3. Mix Design by Indian Standard Method
4. American Concrete Institute Method of Mix Design
5. Quick Method of Mix Design.
1. The American Way of Mixing Designs:
- The American Concrete Institute (ACI) approach is based on the fact that the given size of a mixture of water content per kilogram of concrete determines the performance of a concrete mix, usually independent of the equilibrium. It is therefore possible to start the mixing formation by selecting the water content in these tables.
- In addition it is also assumed that the maximum volume of the estimated quantity of the total value of the concrete depends only on the maximum size and the combination of good composites.
2. Graphic Method of Mix Design
- This approach was developed by the Road Research Laboratory, London and its detailed procedure is described. Combined composites are supplied and their percentage above the normal working fine collection is 4.75 mm, 2.36 mm, 1.18 mm. 600 microns, 300 microns and 150 microns are used. For the maximum combined size of the allowable size, it says 38 mm, 19 mm, 9.5 mm 4.75 mm, 2.36 mm is used.
3. Assemble Design in a Traditional Indian Way:
- The Indian Bureau of Standards has recommended the concrete construction process in conjunction with the experimental work carried out in national laboratories. The mixing process is provided by IS-10262- 1982. Subsequently no updates have been made to this process , and IS 456-1968 has been updated in 2000. That is why IS 10262-1982 needs to be reviewed as the cement power available to a highly developed country.
Therefore the following changes need to be made:
1. The 28-day capacity for phase A, B, C, D, E & F renewal needs to be reviewed.
2. The relationship between the different strengths of cement and the size of w / c should be re-established.
3. The relationship between 28 days of pressure and w / c ratio should reach a pressure of 80 MPa (800 kg / cm2), if the graph is to be used for high strength concrete.
4. According to the revised IS 456-2000 the usability level is expressed in degradation instead of compacting factor. This change requires new amounts of sand and water content for the use of standard concrete up to 35 M Pa and high strength Concrete over 35 M Pa.
- However in the absence of a review on IS 10262-1982, the existing IS 10262 process is described below as a smart move.
- The IS recommendations for mixing design include the composition of the mixing of self-contained (non-ventilated) concrete of medium and high strength concrete.
The integration method consists of the following:
(a) Water content
(b) Percentage of penalty collections corresponding to the maximum aggregate size of the reference value
(c) The amount of cement water, and
(d) Preservation of penalty collection.
- Water content and percentage of fine aggregate and adjust for any differences in performance. Finally the size of the ingredients per unit of concrete volume is calculated in the form of absolute volume. This method works for both underground pozzolana centers.
- The final amount of compounds selected after the experimental mixing, may require minor adjustments. In the case of fly ash cement, the water content can be reduced by about 3 to 5% and a good portion can be reduced by 2 to 4%.
4. American Concrete Institute Method of Mix Design:
- Although the ACI committee published its mixing method in 1944 and almost all concrete dams using a lot of Indian works were designed using the ACI committee method used at the time of mixing. Since then many improvements have been introduced in a practical way. Here is a discussion of the latest method of constructing concrete mixes based on ACI 211-1 of 1991 manual part-time concrete recommendations.
The ACI committee took the following basic ideas:
1. The new collapsed concrete provided and containing a fully proportional measure of the maximum given size will have a fixed water content, regardless of the w / c ratio and the cement content associated between the maximum range of operating parameters.
2. The maximum stiffness of the coarse aggregate per unit of concrete per unit depends on its maximum size and the correct modulus of the fine compound as shown in table 20.39 taking into account the minimum particle size. The effect of angularity is reflected in the empty content. So angular green joints require more mud than circular joints.
3. Regardless of the compaction methods, even when complete compaction has been achieved, a certain percentage of air remains in the concrete and is proportional to the maximum volume.
Mix Design Process:
For compound design, the following data is required to be collected:
(a) Fineness modulus of selected fines.
(b) The unit has the weight of the selected dry fine.
(c) The gravitational force of coarse and fine aggregate in saturated, dry areas.
(d) Absorption of combined rates and penalties.
(e) The gravitational force of cement.
5. Quick methods Mixing:
- Measuring the initial amount of cement water according to purpose means the actual strength will be to combine it with 28 days of cement strength. Feature strength is found to be better related to 28 days of cement strength than in age. This method will therefore require 28 days to determine the size of the cement and the next 28 days of testing mixing the strength of the concrete. The 28-day strength of the cement can be considered as that provided by the curves
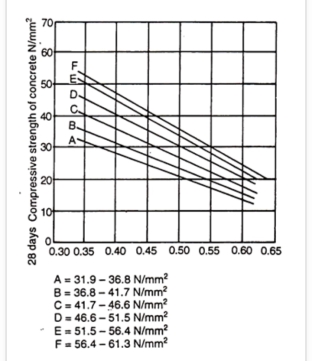
Fig no 17. Graph of compression strength of concrete
- 28 days or 56 days is too long for the contractor to wait for the results of the merger. There is a tendency to use direct mixing without trying experiment mixing. To reduce the time required for the mixing of experiments, the Cement Research Institute of India (CRI) has developed a method called rapid method, in which the compressive strength of cement and cement is obtained using a rapid therapeutic method as discussed in IS 9013-1978. This method reduces the recovery time of experimental compounds from 28 days to only 3 days.
- 28 days of concrete hardening is found to be highly correlated with statistics and rapid strength. Therefore the combination of temptation in line with the target means faster energy than the target means 28 days of energy, with the help of a combination between the two.
- This mixture is obtained independently by the type or characteristics of the cement used i.e. the mixture is not affected by the type of cement used, probably because it affects the fast and normal concrete strength of 28 days equally, so that the result is neutral in comparison. The advantage of each operation is such a combination can be established by the type of building material and assembled to the size to be used.
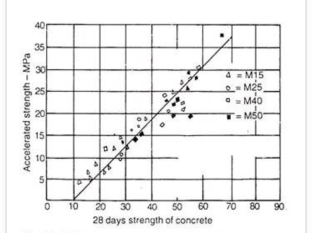
Fig no 18. Strength of concrete vs accelerated strength
- On the other hand, the results of a stable acceleration test in standard cement mortar such as IS 4932-1968 Were not found to be reliable. This problem is overcome by inspecting the cement and quickly and determining its speed.
- The concrete composite concrete or the fastened concrete mixing strength has a w / c value of about 0.35 and the performance is much lower with slump 0 to 10 or compacting factor 0.8 per available cement i.e. (cement in hand).
- The maximum size of the crushed natural compound name should be 10 mm and a good composite should correspond to area II of table 4 of IS-383-1970.
Key takeaways
The following points highlight five methods of concrete construction. The methods are:
1. American Method of Mix Design
2. Graphic Method of Mix Design
3. Mix Design by Indian Standard Method
4. American Concrete Institute Method of Mix Design
5. Quick Method of Mix Design.
The quality of concrete construction on site can be done in three different phases as follows
1. Quality control before integration
2. Quality control during integration
3. Post-construction quality control
STAGE 1 (QUALITY CONTROL BEFORE CONCRETING)
This phase of quality control has two steps.
- Assessment of specification requirements regarding mining, forms, consolidation and embedded repairs etc.
- Control test for concrete ingredients (eg cement, composite and water)
Cement
Cement quality is obtained by performing strength tests of cement cubes. However, with effective control cement:
- It should be tested first and foremost for each source and then tested every once every two months
- It should be protected from moisture
- It should be returned after the last 3 months, if long-term storage is unavoidable
- It should be rejected if a large lump is found in the cement bags.
Aggregate
Concrete composites should be validated at specified values as standard specifications.
The quality of concrete is affected by the various physical and mechanical properties of the composite, namely structure, proportions, durability, gravity and water absorption etc. These composite structures should be tested before using them to produce concrete.
The amount of horror and natural pollution should also be considered.
Sand connections are also an important asset in a number of ways. Provides incorrect results when volume encryption is performed .It increases the amount of water cement which also reduces energy.
With aggregate functional controls:
- They need to be tested once in the beginning to allow the source
- If it is to be checked once or twice daily the moisture content and grant must be made for the combined moisture content.
Water
Water quality should be assessed for needs as defined at the appropriate level. Chemical analysis will be performed to authorize the source. In the event of contamination, it is necessary to store the water for a period of time to allow it to settle. In case of doubt the concrete cubes made of this water are examined. A maximum of 28 days of pressure for at least three cubes or cylinders or a set size, prepared for the proposed water use shall not be less than 90% of the strength between three cubes of the same concrete prepared with distilled water.
STAGE 2 (QUALITY MANAGEMENT DURING CONCRETING)
Careful precaution during concrete is required for all assembly operations such as baking, mixing, transporting, placing, coating and curing. Follow-up safety measures should be taken during concreting operations.
- The concrete mix should be built into the laboratory and the materials to be used on site.
- As far as possible the concrete should be driven by weight. If weight assembly is not possible, volume collection can be allowed with proper monitoring in the presence of the lead engineer.
- During mixing the mixer should be charged in full. Building materials should be fed in the right order. The mixer speed should be from 15 to 20 fluctuations per minute. The mixing time should not be less than 2 minutes in any case. Separation should be avoided when loading concrete into the mixture.
- The performance of concrete is an important material of concrete while concrete is in its new state. Therefore testing of slump or compaction factor should be performed to check the performance of the concrete. About three tests should be performed on every 25 m3 of concrete.
- Care should be taken so that no separation occurs during the concrete transfer.
- Concrete should not be lowered from a height of not more than 1 m. If the height of the drop is more than 1 m chutes should be used.
- To avoid re-release the concrete should be placed in its final position as much as possible.
- Vibrators should be used to connect the concrete. Internal vibrator installation space should not exceed 0.6 m. It should be lightly painted so that no holes are left in the concrete. Vibrator frequency should not be less than 7000 cycles / minutes.
- The treatment should be done over a period of time so that the concrete develops the required strength. Concrete should be covered with hessian as soon as it becomes hard.
- The form function must be aligned with the final form of the form. It should be checked before the start of integration. The inside of the forms should be cleaned and oiled. Forms must be removed after the deadline.
- Concrete should be protected from hot and cold weather at an early age. Concreting should not be performed at temperatures below 4.50C and above 400 In very hot weather water and aggregates should be cooled. Approved quality retards can be used.
- In very cold weather water and aggregates should be heated. Approved quality Accelerators can also be used.
STAGE 3 (QUALITY CONTROL AFTER CONSTRUCTION)
- Once the concrete has been laid and assembled, a pressure test is performed on the tubes made of this concrete. With standard concrete, cubes are made of concrete made in the workplace.
- Reinforced concrete should be considered to be true in size, shape and size as specified in each design. The appearance of the concrete surface should also be checked. Sizes are available in various sizes. Reinforcement should have adequate concrete cover and if reinforcement is visible on the part of the structure, the part should be rejected or appropriate action taken.
Concrete strength is usually obtained by cube or cylinder samples tested within 28 days. In the event that the power received is less than the specified minimum, one or more of the following steps may be taken.
- Load testing and deviation of the deviation and / or difficulty (structural quality can also be obtained by calculating back concrete strength)
- Cutting cores from structures and testing them for strength
- Non-destructive tests such as the Schmidt rebound hammer or ultrasonic pulse velocity test. These tests give a very complex view and are used to find structural similarities.
- Chemical analysis of hard concrete.
Key takeaways
The quality of concrete construction on site can be done in three different phases as follows
1. Quality control before integration
2. Quality control during integration
3. Post-construction quality control
The behavior of the concrete under high temperature values could be affected with several factors. The temperature rate, aggregate type, and stability of the mixture are among the most important factors to be considered under high temperature condition. It is noted that the abrupt temperature rise can cause thermal shock, spalling, cracking, and aggregate expansion leading to high distress within the concrete.
The durability of the concrete against freeze-thaw cycles is previously investigated as a major factor indicating the ability for resistance against weathering actions.
Cold and hot weather concreting
Introduction
- Concrete and other structures are constructed in many countries around the world and in some places the climate is symbolized by the long spells of hot or cold weather. Concrete companies that are ready to integrate and build in these regions are able to produce high quality concrete despite these weather problems. In many regions with unfavorable weather conditions there are set conclusions and concrete production guidelines that provide details of the methods that can be used to combat adverse conditions.
- In the cooler parts of the world, cool, humid climates are common. In these areas, although cold or cold temperatures are not uncommon, it is often surprising when they arrive and it may be too late to apply even safety measures to minimize their undesirable effects,
- Physical effects in both hot and cold conditions should not be overlooked. Workers and managers will not be expected to produce good quality concrete if exposed to conditions for a long time without proper protection
- When the process of serving the container is done on its own it is not a matter of deciding whether to pour concrete. Air temperature, humidity, and wind speed, higher temperatures where you put concrete, water and dry concrete in the bag all play a big role and should be considered. The air, air and moisture are much better than you can handle but you can also influence it. It is important to remember that the temperature of the mixed material is as important as the temperature of the air.
- The strength and durability of concrete are at odds with the climate in which the composite process is performed. Therefore, construction workers will need to take extra care or take action when it comes to worship. In fact, some parts of the world remain hot all year long. These are situations where paying attention to a few simple but much-needed points in hot weather can definitely help to complete any display without compromising its quality. Sunlight leads to hot weather which forces us to use special methods while barking known as hot weather concreting,
Hot Weather concreting
Definitions
- The definition of a tropical climate may vary from country to country. According to the Indian climate, Indian codes determine 40 ° C as the temperature range for hot climates. That is to say, any combination made at temperatures above 40 ° C can be considered as a hot climate that allows for certain measures to be adopted.
- Obviously, this is not the case in most other parts of the world because of the climate. For example, according to ACI 305, any combination of high temperatures, high air pressure, low humidity and sunlight (sunlight) is a preconceived notion for designing a connection such as hot weather. Some theories say that any heat above a comfortable room temperature, and 25 ° C however, begins to make the concrete uncomfortable 1.e, the concrete begins to react differently which is why it requires special care due to hot weather, if strong quality to be maintained.
Hydration Process
- Therefore, it is very important to deal with how the temperature of the tropical climate differs concreting normal temperature. Concrete sets also gain strength due to the hydration of the cement inside them. The elasticity of the cement occurs quickly when it is hot. Cement installation also releases heat. Therefore, the faster the hydration of the cement the faster the heat generation. This creates the heat of the concrete, further speeds up the cementing or set-up process, Cement quickening does not allow concrete enough time to get enough strength. While the initial energy does not suffer, long-term energy (28-day energy) is negatively affected. This is a major reason why hot climates require special care. Otherwise, you will be playing with concrete designed strength.
- Water demand
- The water demand for concrete mix is high in hot weather due to rapid evaporation. Unless appropriate measures are taken, additional water will have to be added to the concrete mix to maintain the performance of the mixture. This will increase the amount of water cement which will also reduce the strength of the concrete. If more cement is added to keep the w / c ratio constant the cost will increase as cement is the most expensive ingredient concrete mix,
- Rapid drying of freshly poured concrete areas occurs when it is hot due to rapid evaporation or water loss in the mixture. If proper care is not taken, cracks known as plastic shrinkage cracks will appear, which are difficult to repair over time. The exposed area tends to shrink rapidly due to rapid moisture loss while mixing will still develop sufficient strength to withstand these shrinking pressures leading to cracking. In hot weather, concrete bed, forms, metal reinforcement, connecting or assembling equipment etc. It is also hot transferring heat to a mixture that adds to the problem.
The effects of Hot weather on concrete
- High temperatures can affect the concrete at all stages of production and laying process and many effects can have long-term or hardening effects. Some of the problems caused by high temperatures are listed in Table 1. They are the result of high temperatures that increase the rate of hydration reaction and the movement of moisture inside and outside the concrete.
- The combination of high temperature, low humidity and high air velocity adversely affects desirable concrete structures e.g. Strength, inequality, durability, weather resistance, wear and tear
- Setting time. As the temperature of the concrete increases, the laying time, and thus the laying time, the mixing and finishing of the concrete is reduced
- Workability and slump - High temperatures reduce the performance (or fall) of concrete very quickly over time. Adding more water to improve the performance of the mixture reduces energy and Increases penetration, and ultimately affects the durability of the mixture.
- Durability - Many forms of degradation depend on the transfer of fluid or respiration through a concrete structure. Acquiring a ‘non-permissible’ concrete is one of the main goals when trying to gain durability. The main ways to do this is to produce concrete with low water / cement concrete. As noted above, high temperatures affect the initial performance and the level at which they lose performance and may be tempted to add more water to the mixture or site. This will lead directly to concrete at high risk of cold, climate change, sulphate attacks and the entry of carbon dioxide and chloride solution leading to increased corrosion.
- Compressive strength - High water demand and high concrete temperatures can lead to a 28 day power reduction. If too much water is added to the concrete mix at high temperatures to maintain or restore function, the water level of the cement will increase, resulting in a loss of strength and durability. This can also increase the shrinkage of reinforced concrete. Where water is not heard, reduced set time and performance can increase insufficient mixing (actually a major impact on energy), the formation of cold joints and improper elimination.
- Concrete temperature - Warmer climates can increase the temperature of concrete caused by hydration heat. In large segments the hot gradients through the element can create thermal cracks. Laboratory tests show that very high temperatures have a significant impact on the strength of the hard concrete. Although increased concrete heat can lead to an initial increase in energy gain, in the long run, low-temperature-cooled concrete will reach higher strength.
- Poor surface appearance - With increased evaporation, the concrete surface will dry out. In the case of an infestation this can lead to premature depletion, trapping the amount of water that drips inside the mixture. The coated layer (from the finish) can cause blood clots to trickle under the surface, leading to the formation of the upper layer and subsequent eruption. Also, color variations on the face can result from different levels of hydration and cooling effects.
- Plastic shrinkage cracking - Hot weather conditions accelerate the loss of moisture on the face. If the evaporation rate is higher than the rate of bleeding (the rate at which the water rises higher) drying of the soil will occur which has led to a reduction in concrete. When the reducing pressure exceeds the capacity of the concrete, cracks will occur. The chances of cracking the plastic are reduced so it is great whenever hot weather raises steam or concrete and lowers the bleeding rate. The cracking of the shrinkage plastic can be quite deep, as the plastic concrete has little resistance to the shrinking pressure, and the cracks continue to grow and spread until the shrinkage pressures are released. (Be aware that thin plastic cracks do not usually extend to the free edges, as uncontrollable concrete cuts may occur in these areas.)
- Thermal cracking - Concrete is at risk of thermal cracking when applied for the first time, and hydration heat raises the internal temperature of the concrete. Rapid changes in the external temperature of the exterior concrete, such as where concrete slabs are laid, walls or sidewalks on a hot day followed by a cold night, lead to hot gradients between the warm / hot surface and the cold outside. The warm interior offers a cool outdoor space, which wants to make a deal. Depending on the temperature variation, there may be a concrete crash. Larger or thicker concrete objects are at greater risk because of the protective effect the concrete gives them inside the object.
Precautions in hot weather conditions
- Problems often arise when local workers are unaware of the impact of changing weather and / or climatic conditions during laying and / or finishing concrete. Improved responses to unexpected changes are not recommended because the damage that can be caused by the uncontrolled effects of tropical climates may not be completely eliminated. The first option to consider in hot weather is to postpone the placement of the concrete or not
- Make sure site staff are aware of the effects of the weather. Improved responses to unexpected changes are not recommended. The first option to consider in hot, unfavorable weather conditions is to postpone the placement of the concrete or not. It is often better to wait than to risk costly repairs (or replacements) for defective work.
- Concrete Production. The role of concrete suppliers is to help put concrete in hot climates. Shade stocks, spray aggregates before evaporation time, or cool down otherwise. Paint mixing barrels and keep them white to reduce heat loss from the sun. Use ice as part of the mixed water or cool the concrete with liquid nitrogen.
- Delivery and Delivery- Delivery delays can delay good mixing practices. The concrete supplier must plan and maintain a good non-delaying plan to deliver concrete to the required area on site
- Reduce travel time and avoid unnecessary delays.
- Avoid prolonged mixing. Mixed transport trucks should be released as soon as possible after the addition of water to that mixture.
- For large projects, consider baking and mixing using a workplace plant. •
- Water should not be installed on pre-assembled concrete in the workplace unless it is part of the amount required at the beginning of the set water limit and specified descent.
Precautions for concreting in cold weather
- Temperature control of concrete ingredients - The most effective way to maintain the temperature of concrete at the top is to control the temperature of its ingredients. The contribution of each ingredient in concrete heating is a function of heat, specific heat and the amount used for this ingredient. The water mixed with the mix has a very noticeable effect on the temperature of the concrete. Therefore, in cold weather, all available means will be used to care for these items at the highest possible temperature.
0. Many ways to reduce the effects of low temperatures include raising the level at which the concrete gains strength under these conditions in the first critical phase after laying.
2. Cement Quantity - Increasing the amount of cement (meaning using high-strength concrete) can increase the energy gain. Note that there is little or no impact during setup.
3. Admixture - The rapid addition of compounds (non-chloride) to concrete reduces the setting time and speeds up the energy gain rate by increasing the level at which cement enters
4. Hot Water - Applying hot water to the mixture will increase the temperature of the concrete, which in turn accelerates the rate at which cement enters. The temperature of the water mix should not exceed 70 ° C and the mixing should ensure the consistency of the concrete delivered to the site
5. Air entrainment - you may be able to prevent the effects of sudden cold by applying a combination of ventilation to the concrete. These compounds create minute air vents where the pore water can move as it expands during cold weather
6. On site precautions - It is advisable to take steps to prevent concrete damage by unpredictable and unexpected snow whenever the air temperature drops below 5C.
7. Cold Protection (Including cold / frozen area, winds and cold) - in some cases, the provision of a heated enclosure (simple frames covered with tarpaulin and the use of hot air) to completely seal the concrete object may be required. Note that care must be taken to prevent concrete drying when using this method.
Key takeaways
1. Concrete and other structures are constructed in many countries around the world and in some places the climate is symbolized by the long spells of hot or cold weather. Concrete companies that are ready to integrate and build in these regions are able to produce high quality concrete despite these weather problems. In many regions with unfavorable weather conditions there are set conclusions and concrete production guidelines that provide details of the methods that can be used to combat adverse conditions.
Under water concreting
There are 4 techniques of underwater concreting:
- Tremie pipe Method
- Bucket Method
- Grouting Method
- Bags stacking Methods
1)Tremie pipe Method:
- The tremie stable state of affairs method makes use of a vertical or nearly vertical pipe, thru which concrete is about with the aid of using gravity feed below water degree.
- The decrease give up of the pipe is stored soaking wet in crisp cement with the aim that stable ascending from the bottom dislodges the water, on this manner limiting washing out of the bond substance of the brand new concrete to the exposed top floor.
- The top give up of the tremie pipe is stored over the water degree amid the pour and is given a cone formed field for cluster stacking, or cement is probably siphoned into the best factor of the tremie pipe.
- Concrete should be poured at a fee which abstains from putting with inside the tremie.
2) Bucket Method:
- In this method the stable is saved submerged with the aid of using a base commencing field.
- The cans for the maximum component are outfitted with base curler or drop base doorways as regarded in Fig. The door opens uninhibitedly outward whilst stumbled.
- The pail is crammed absolutely with cement and its first-class secured with a canvas material or gunny sack and taken progressively right all the way down to avoid backwash or unsettling have an impact on to concrete because the can is added down into the water.
- The can is added down with the aid of using a crane upto the bottom floor of the stable and in a while opened both with the aid of using an affordable recreation plan from the first-class or with the aid of using a jumper.
- It is fundamental that the stable be launched straightforwardly superficially on which it's far to be saved.
Advantages:
- This method is located to have the accompanying preferences:
- Relatively lean blends is probably applied given ok versatility is held.
- No shape paintings is essential on this method.
Disadvantages:
- This method is slight and laborious as the precise situating of the packs installation should be cultivated with the aid of using the jumpers.
- Voids in adjacent sacks are difficult to fill.
- There is small preserving apart from created with the aid of using the mechanical interlock among packs.
- The method further is exorbitant as greater paintings is related to filling and tying them.
3) Grouting Method:
- These pens are laid vertically over the whole area to be cemented with the give up aim that the separation among the focuses of the pens and moreover to the essences of the stable thought now no longer surpass one meter.
- The degree of the stone over all thought to nor be beneath 50 mm in extra of 2 hundred mm.
- This overall have to be wetted earlier than storing it outdoor the metallic confines over the whole location and tallness to be cemented.
- While saving the overall, care have to be taken that no pen is uprooted from its position.
- Subsequent to storing the overall, the concrete sand grout of 1:2 quantity and water/bond share as a minimum 0.6 and now no longer greater than 0.9 is installation in a mechanical blender.
- The finest length of sand is probably five mm and the concrete sand quantity can also additionally shift from 1:1.5 to 1:4contingent at the first-rate conditions and importance of the paintings.
- In the wake of grouting the whole territory for a stature of round 60 cm s, a comparable pastime is rehashed for the subsequent layer of 60 cm and the method is rehashed until the grouting is completed up to an appropriate tallness.
- The grout to be dispatched down to be ok to fill each one of the voids.
- The extent of voids is probably typical as 55% of the extent to be cemented or observed tentatively.
- Beyond what many could recall feasible cement thought now no longer be troubled whilst it's far stored, this can restrict the association of laitence.
4) Bags stacking Methods:
- The packs are tied in order that they may be perfect right away in a profile of the floor on which they're put.
- The legitimately crammed sacks are added down into the water and set carefully in header and stretcher guides as in block workmanship improvement with the help of jumpers so the whole mass is interlocked.
Advantages:
- This method is located to have the accompanying factors of interest:
Nearly lean blends is probably applied given ok versatility is held.
- No shape paintings is vital on this method.
Disadvantages:
- This method is slight and laborious as the proper situating of the packs installation should be cultivated with the aid of using the jumpers.
Voids in contiguous packs are difficult to fill.
- There is small preserving apart from created with the aid of using the mechanical interlock among packs.
Key takeaways
1. The top give up of the tremie pipe is stored over the water degree amid the pour and is given a cone formed field for cluster stacking, or cement is probably siphoned into the best factor of the tremie pipe.
Concrete gains very little strength at low temperatures. Accordingly, freshly placed concrete must be protected against freezing until the degree of saturation of the concrete has been sufficiently reduced by cement hydration. The time at which this reduction is accomplished corresponds roughly to the time required for the concrete to attain a compressive strength of 500 psi. Concrete to be exposed to deicers should attain a strength of 4,000 psi prior to repeated cycles of freezing and thawing.
Sulphate
- Cement is composed of two minerals: tri-calcium silicate (C3S), and di-calcium silicate (C2S).
- In addition to hydration, the main reaction products are calcium silicate gel (C-SH) and calcium hydroxide Ca (OH) 2, labeled as CH in chemistry notation.
- Moisture is required in this reaction which can cause serious damage to the construction of both the walls and the walls of buildings in buildings.
- Sulphate attacks occur on the lower slabs. This problem usually affects buildings from the 1950s to the 1960s but can also affect previous buildings where the concrete floor slab is installed.
- It occurs when the filler material under the slide contains sulphates and this is considered to be a solution with soil moisture entering the concrete that forms the slab on the floor.
- Attacks can occur from MgSO4 salts, NaSO4 salts, and other salts containing SO3-ions. The interaction of Ca2 + ions with SO4 present in the solution will produce CaSO4 or gypsum.
- The effect of gypsum on C-S-H gel, which is the main component of reinforced cement, is an irreversible topic.
- Some substances present in cement, such as tri-calcium aluminate, also interact with sulphate ions. This reaction is well established in the literature.
Key takeaways
In addition to hydration, the main reaction products are calcium silicate gel (C-SH) and calcium hydroxide Ca (OH) 2, labelled as CH in chemistry notation.
Moisture is required in this reaction which can cause serious damage to the construction of both the walls and the walls of buildings in buildings.
Acid Attack
- Acid attack is the dissolution and leaching of acid-prone elements, particularly calcium hydroxide, from the cement paste of hardened concrete.
- This movement outcomes in an boom in capillary porosity, lack of cohesiveness and subsequently lack of power.
- In said instances, acid assault can be observed with the aid of using crack formation and subsequently disintegration, in particular whilst the shape is subjected at one facet to water pressure.
- Unlike sulphate assault (see beneath), the goods fashioned from acid assault aren't expansive, and leaching will handily arise in systems which are tremendously permeable.
- In excessive overall performance concrete structures containing cement pastes with a low content material of calcium hydroxide, acid assault is relative gradual and can contain handiest the finely divided calcium hydroxide crystals included withinside the interstices of the calcium silicate hydrate, C-S-H.
- The micrographs received from PFM analysis, supplemented with SEM–EDS studies, monitor that handiest the top, floor part of the concrete has been attacked with the aid of using acidic answer.
- The relaxation of the concrete suggests no shape of degradation.
- In the attacked zone, there's clean proof of leaching of the cement paste matrix, main to accelerated capillary porosity and lack of brotherly love of the matrix.
- Locally, there's lack of bonding of the cement paste to aggregate, however at the whole, those elements have now no longer adversely affected the microstructure and nice of the concrete.
- In this instance, long-time period sturdiness of the concrete isn't always probably to be compromised.
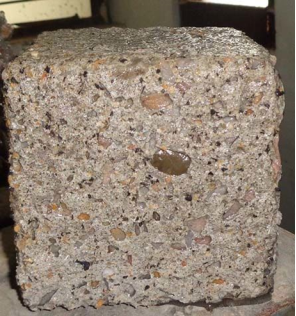
Fig no 19. Acid Attack on Concrete block
- Acid assault of concrete takes 3 forms. First, hydration merchandise reacts with the acid to shape dissolved ions, main to lack of strong material—acidolysis.
- Second, withinside the case of a few acids, insoluble salts shape, a number of which precipitates to purpose growth and cracking.
- Finally, a few acids supply complexes with calcium, aluminium, iron and silicate ions which produce an awful lot better concentrations of those ions in answer than could in any other case be the case, once more main to dissolution.
- This can probably arise at pH situations beneath which cement could usually be tremendously stable (complexolysis).
- Depending at the acid present, extra than this sort of deterioration mechanisms can be powerful.
- Where acidolysis is the main mechanism, an acid answer penetrating the pores of concrete will begin to purpose a number of the elements to dissolve.
- Calcium is generally the primary cation to be dissolved, considering that portlandite will become soluble beneath tremendously excessive pH values.
- AFm and AFt stages commonly dissolve at barely decrease pH values, even though strong aluminium and iron hydroxides are precipitated, which persist till the answer is tremendously acidic.
- Exposure to acidic answer additionally reasons lack of calcium—decalcification—of C-S-H gel, leaving tremendously vulnerable silica gel behind.
- The importance of calcium on this shape of degradation approach that adjusting the composition of the cement matrix of concrete to attain a decrease calcium content material will probably impart extra resistance.
- Thus, pozzolanic substances can be powerful in improving resistance to this form of acid assault, considering that their aggregate with PC will produce such an adjustment.
- However, decreased quotes of mass shipping and more desirable power done thru the usage of pozzolanic substances also are probably to be motives for progressed resistance.
Key takeaways
In excessive overall performance concrete structures containing cement pastes with a low content material of calcium hydroxide, acid assault is relative gradual and can contain handiest the finely divided calcium hydroxide crystals included withinside the interstices of the calcium silicate hydrates, C-S-H.
- You may also note efflorescence each interior and outside, and it may range in frequency and depth in the course of the us of a because of moisture and temperature. Three situations want to exist for efflorescence to arise: There are water-soluble salts in or at the fabric.
- Moisture is gift to make the salt turn out to be a soluble solution. As salts pass to the fabric’s surface, the moisture evaporates. This makes the salts crystallize, which leads to efflorescence.
- Water, rain and snow are the number one reassets of moisture and might effect the diploma of efflorescence.
- Condensation, groundwater wicking and indoors sports additionally may also have an effect on the diploma of moisture generation. Efflorescence can occur at exceptional times. Essentially, it may both be a hassle from the start of a constructing’s creation, or the method can arise over time.
- Primary efflorescence normally takes place inside the first seventy two hours of the constructing fabric being used, performing because of extra water being gift while the fabric became manufactured.
- Secondary efflorescence is a end result of out of doors moisture pulling the salt out of the constructing fabric. In many instances, efflorescence may also arise at some stage in domestic creation. If masonry devices get unnoticed in a single day at some stage in creation, they’ll probably soak up moisture from damp soil and rain. It is critical for masonry devices to be included and left in pallets to decrease the danger of efflorescence in the course of a creation project. Efflorescence also can arise while constructing substances are established incorrectly or troubles arise with the installation.
- Some not unusualplace examples of this include: Using through-wall flashings incorrectly. Failing to offer enough air flow for masonry. Installing masonry with out an green barrier for moisture.
- Joint substances failing after installation. Materials being saved improperly or left at the ground. Efflorescence is mostly a seasonal hassle, and humidity will effect whether or not soluble salts appear. It normally escalates in winter, due to the fact that rain, snow, sleet and different inclement climate situations may also arise. However, efflorescence can nevertheless arise in spring, fall and summer.
Fire resistance of concrete is the ability of concrete to withstand fire or to give protection against fire. This involves the ability of concrete structural element to continue perform a specific structural function or confine fire or both.
The duration of time that an element such as beam, column, wall, floor, or roof can endure the fire, which is defined in ASTM E 119, is termed fire rating.
Fire resistance is controlled by both the physical and thermal properties of the structural element. Factors governing the structural performance include stress level in the concrete and the steel, concrete cover, tendency of aggregate and free moisture to cause spalling, and lateral restraint conditions.
However, parameters that control the thermal performance involves type of aggregate, free moisture in the concrete (both absorbed and capillary), and volume of concrete per square meter of exposed area.
Inspection and testing of ready mix concrete is crucial to ensure that all specified conditions meet the acceptable criteria. Ready mix concrete, which produced in batching plant and transported to construction site by truck mounted mixers, are commonly inspected and tested in accordance with applicable standards such as ASTM international.
Batching Plant Inspection
- Firstly, examine and specify whether facilities, scales, and truck mixers meet the specified project requirements or not.
- Inspect storage areas of all materials like cement, aggregate, and admixtures to ensure their cleanness, free of contamination, and properly protect materials from effect of freezing.
- Inspect and verify that coarse and fine aggregate gradation tests are conducted in accordance applicable standards like ASTM C 136, and result reach project requirements.
Onsite Inspection of Ready Mix Concrete
- Every delivery ticket shall be inspected to ensure that a mixture with the correct designation is delivered.
- Inspect delivered concrete; it should be uniform and adequately mixed prior to discharge at the construction site.
- Inspect and monitor water, admixture, and fiber reinforcement addition onsite to make sure that the process performed properly.
- Monitor and examine concrete delivery and placement time to find out whether it completed within the time constraints of the project specifications.
Testing Ready Mix Concrete
1. Onsite Tests
There are certain types of tests that shall be conducted on ready mix concrete upon reaching construction sites. Table 1 provide lists of tests that need to be performed on ready mix concrete on project site. Table 1 Tests conducted on ready mix concrete upon reaching construction site
Type of tests | ASTM international for testing procedures | Test frequencies | Purpose of the test |
Slump | ASTM C 143/C 143M | First truck load, whenever the consistency of the concrete appears to vary. | Measure fresh concrete consistency, check its workability, and use as an indicator of poor mixed batch |
Air content | ASTM C 173, ASTM C 231 | Performed on all samples taken to measure concrete strength | To check air entrained concrete |
Temperature | ASTM C 1064 | At the time of sampling for each strength test | To make sure that concrete comply with certain specifications that define a certain allowable temperature range |
Density | ASTM C 138, ASTM C 567 | Whenever required by project specifications | To estimate concrete density |
Evaluation of crack
When inspecting a slab or conducting a crack, always measure the width of the crack and determine whether the metal reinforcement passes through it and whether the crack is active or asleep. This information, especially the details of the reinforcement and cracking function, is very important when choosing the best repair option.
Crack width
- The extent of the crack is usually measured using a crack comparison card. Measuring the width of the crack helps to separate the stiffness of the cracks and to evaluate the performance of the joint joints across the fracture of the direct direction of the fracture and the transmission of the load. Also, many repair options depend on the width of the crack.
- Unless the steel reinforcement passes through a crack, the alignment of the vertical tube and the transmission of the broken load depends on the joint bonding. If the diameter of the fracture is less than 0.035 inches, the composite particles that come from the other side of the fracture to the other side will normally provide adequate load transfer and maintain vertical alignment throughout the split.
- For larger screens, maintaining a straight slide alignment can be a challenge. The success of the remediation approach will depend on the slide loading and the quality of the base material and the ground cover.
Steel Reinforcement
- Although steel reinforcement does not prevent cracking, it limits the width of the crack so that the joint joints are maintained. Strengthening itself also provides load transfer and helps maintain vertical alignment in the cracks. When the reinforcement passes through a split, both the width split and the future width increase are controlled. The new cracks of the non-reinforced concrete will continue to grow and the diameter can double before the increase in crack-width.
- With the cracks caused by the drying shrink, the cracks will stabilize at the end. Splits due to other causes, however, such as soil erosion or height, may not be stable and may continue to increase unless a significant amount of reinforcement passes through space. Determining the amount of reinforcement that goes beyond cracking is important in predicting the performance of future cracks and choosing the best repair option.
Dormant and active crack
- Cracks that fall through steel reinforcement are generally stable and are often considered sleepy. Of course, the stability of the cracks depends on the source and the degree of reinforcement of the cracks. The lying cracks have a fixed width and can be repaired with solid or flexible materials.
- Functional cracks should only be repaired using a flexible object that can accommodate future cracked movements. Generally, the active cracks in the slabs actually belong to the active members and should be treated in the same way as the joints. After all, random or non-joining cracks in flatwork are self-assembling joints.
Key takeaways
- Evaluation of crack is
- Crack width
- Steel Reinforcement
- Dormant and active crack
1. Plastic shrinkage concrete cracks:
- When concrete remains in its plastic state (earlier than hardening), it's miles complete of water. When that water finally leaves the slab, it leaves at the back of big voids among the stable particles.
- These empty areas make the concrete weaker and greater at risk of cracking. This form of cracking takes place regularly and is stated as “plastic shrinkage cracking”.
- While plastic shrinkage cracks can manifest everywhere in a slab or wall, they nearly constantly manifest at reentrant corners (corners that factor into the slab) or with round gadgets withinside the center of a slab (pipes, plumbing fixtures, drains, and manholes).
- Since concrete cannot decrease round a corner, strain will purpose the concrete to crack from the factor of that corner. Plastic shrinkage cracks are usually very slender in width and slightly visible. While almost invisible, it's miles vital to bear in mind that plastic shrinkage cracks don’t simply exist at the surface, they increase at some point of the whole thickness of the slab.
- An excessively moist blend is a contributing element to shrinkage in concrete. While water is a critical element in each concrete blend, there's this kind of factor as an excessive amount of water.
- When the combination consists of an excessive amount of water, the slab will reduce greater than if the suitable quantity of water turned into used. Hot climate is some other massive cause for plastic shrinkage cracks. Control joints may be included into the slab to save you shrinkage cracking. The joints will open up because the concrete slab receives smaller.
2. Expansion concrete cracks:
- Enlargement cracks Just like a balloon, warmth reasons concrete to expand. When concrete expands, it pushes towards whatever in its way (a brick wall or adjoining slab for example).
- When neither has the capacity to flex, the increasing pressure may be sufficient to motive concrete to crack. Expansion joints are used as a factor of separation (or isolation), among different static surfaces.
- Typically product of a compressible fabric like asphalt, rubber, or lumber, enlargement joints should act as surprise absorbers to alleviate the strain that enlargement places on concrete and save you cracking.
3. Heaving concrete cracks heaving cracks:
- When the floor freezes, it is able to on occasion raise many inches earlier than thawing and settling lower back down.
- This floor motion delivered on through the freezing and thawing cycle is a big element contributing to concrete cracking. If the slab isn't unfastened to transport with the floor, the slab will crack.
- Large tree roots will have the identical impact on a slab. If a tree is positioned too near a slab, the developing roots can raise and crack the concrete surface. Always don't forget this while laying a slab.
- Settling concrete cracks settling cracks On the alternative hand, floor settling beneath a concrete slab also can reason cracking. Settling cracks usually arise in conditions wherein a void is created withinside the floor beneath the concrete surface.
- Think approximately whilst a huge tree is eliminated from close by and the roots start to decompose or whilst a software business enterprise digs a trench for his or her lines, pipes, etc. and don’t compact the soil once they replenish it–those are examples of times wherein settling cracks are possibly to happen.
The principal causes of cracks in a building are as follows:
- Permeability of concrete
- Thermal movement
- Creep movement
- Corrosion of reinforcement
- Moisture movement
- Poor construction practices
- Improper structural design and specifications
- Poor maintenance
- Movement due to chemical reactions
- Other factors
Remedial measures
- Use minimum possible quantity of water.
- Employ large coarse aggregate.
- Provide compression reinforcement if possible
- Avoid formwork removal at early ages.
- Cure concrete properly.
- Assign proper cross section for the concrete element.
- NDT stands for Non-Destructive Testing. It refers to an array of inspection strategies that permit inspectors to assess and acquire statistics approximately a material, system, or factor without completely changing it. NDT can also be called: NDE (non-unfavourable exam or evaluation) NDI (non-unfavourable inspection) In the subject, NDT is frequently used as an umbrella time period to consult non-unfavourable inspection strategies, inspection tools, or maybe the complete subject of non-unfavourable inspections.
- For business applications, the aim of NDT is to make certain that vital infrastructure is well maintained if you want to keep away from catastrophic accidents. While NDT techniques are generally related to business use cases, like examining vulnerable factors in a boiler used at an oil refinery, makes use of in medicinal drug are really a number of the maximum common. For example, an waiting for mom getting an ultrasound to test at the fitness of her infant could be taken into consideration an NDT use case, as could getting an X-ray or MRI to analyze extra approximately an injury.
- But it’s critical to notice that NDT does now no longer always require the usage of unique equipment, or any equipment at all. For instance, while inspectors in business settings overview the outdoor of a stress vessel with their bare eye, that could fall beneath the NDT designation, when you consider that they're accumulating facts at the popularity of the boiler without negative it.
- On the alternative hand, the use of an advanced device like an ultrasonic sensor to search for defects in a positive cloth or asset could additionally be known as NDT. Regardless of the particular use case, the underlying commonality amongst a lot of these examples is the gathering of facts in a non-intrusive manner.
- The special styles of non-damaging trying out are regularly complementary. As a result, we will take advantage of the benefits of mixed strategies. Non-damaging trying out (NDT) is a mixture of diverse inspection strategies used for my part or together to assess the integrity and residences of a material, thing or device without inflicting harm to it.
- In different words, the component that calls for the usage of one or greater of these strategies can nevertheless be used as soon as the inspection technique is over. NDT is consequently regularly used for the detection, characterization and sizing of inherent discontinuities, in addition to the ones related to harm mechanisms. NDT is regulated with the aid of using codes and requirements in keeping with the kind of industry, united states of America and different criteria. Society for Mechanical Engineers (ASME), ASTM International, COFREND, CSA, Canadian General Standards Board (CGSB), American Society for Non-destructive Testing (ASNT), etc. are well-recognize examples.
- Destructive trying out (regularly abbreviated as DT) is a take a look at technique performed to discover the precise factor of failure of substances, components, or machines.
- During the process, the examined object undergoes strain that in the end deforms or destroys the material. Naturally, examined components and substances can't be reused in normal operation after present process unfavourable trying out procedures. Destructive trying out is typically performed earlier than a aspect enters mass production. OEMs want to realize the boundaries in their merchandise for you to supply right upkeep and working guidelines for his or her machines.
Tests on cement
1. FINENESS
Objective
- The purity of the cement alone has a significant impact on the hydration rate and therefore on the energy gain rate and the degree of heat dissipation.
- Finer cement provides a large area of hydration Specific Surface versus Compressive Strength of Cement and as a result accelerates energy.
- The beauty of digestion has increased over the years. But now it is almost settled. Different cement is subject to different finishes.
- A particle size of less than 3 microns has been found to have a significant effect on energy in one day while a fraction of 3-25 micron has a significant effect on energy for 28 days.
- An increase in the thin layer is also found to increase the thickness of the concrete.
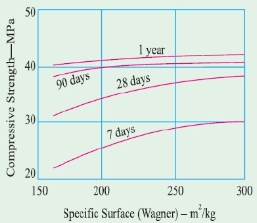
Fig no 20. Specific Surface versus Compressive Strength of Cement
Procedure
- Stir the sample of cement to be tested by stirring for 2 minutes in a preheated pot to distribute the agglomerates. Wait 2 min. Mix the resulting flour gently using a clean dry stick to spread the fine mixture all over the cement.
- Place the tray under a strainer, weigh about 10 g of cement in the nearest 0.01 g and place it in a strainer, being careful to avoid loss. Disperse any agglomerates. Place the lid on top of the filter.
- Cover the sieve with a circular motion, planetary motion and movement until it no longer exceeds the fine material in it. Remove and measure the rest. Specify its magnitude as a percentage, R1, of the pre-set filter per 0.1 percent nearby. Gently move all the fine material from the filter into the tray.
- Repeat the whole process using a new sample of 10 g to get R2. Then calculate the remnants of cement R as the value of R1, and R2, as a percentage, expressed in the percentage close to 0.1.
- When the results vary by more than 1 percent altogether, make a third reduction and calculate the meaning of the three values.
- Check the sieve after 100 filters per section 4.4.2 of IS: 4031 (Part 1)
Apparatus used
![]() | ![]() |
Fig no 21. Cement | Fig no 22. Balance |
![]() | ![]() |
Fig no 23. Seive | Fig no 24. Nylon Bristol Brush |
2. STANDARD CONSISTENCY
To determine the quantity of water required to produce a cement paste of standard consistency as per IS: 4031 (Part 4) – 1988
Apparatus
1) Vicat apparatus conforming to IS: 5513 – 1976
2) Balance, whose permissible variation at a load of 1000g should be +1.0g
3) Gauging trowel conforming to IS: 10086 – 1982
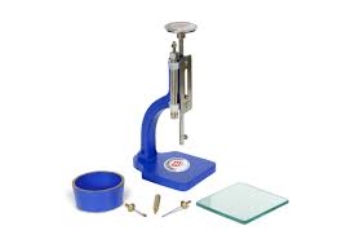
Fig no 25. Vicat apparatus
Procedure
- Measure about 400g cement and mix it with the required amount of water. Estimation time should be between 3 to 5 minutes.
- Fill the Vicat mold with glue and measure it with a trowel.
- Gently lower the plunger until it touches the cement.
- Release the plunger to allow it to sink into the paste.
- Note the reading in the scale.
- Repeat the above process and take new samples of cement with different water sizes until the gauge is 5 to 7mm.
3. SETTING TIME
Objective
- For simplicity, the initial set time is considered to have elapsed between the time when water can be added to the cement, at which point the paste begins to lose plastic.
- The last time is the last time the water is put in the cement, and the time when the glue is completely lost to the plastic and gained enough strength to withstand a certain direct pressure.
- The room temperature, dry material and water should be kept at 27 ± 2 ° C. The relative humidity associated with the laboratory will be 65 ± 5 percent.
Procedure
Preparation of test block
- Prepare a clean paste by measuring 0.85 times the water needed to give the glue a normal consistency. Portable or refined water will be used to prepare the paste. Attachments will be measured in accordance with the conditions set out in IS: 4031 (Part 4) -888.
- Start a stopwatch at a time when water can be added to the cement. Fill the Vicat mould with cement paint as limited as above, the mould stays on an empty plate. Fill the mould completely and spread the surface of the paste to make it to the top of the mould. The cement block is thus suspended from the test mould.
- Immediately after moulding, place a barrier in a damp cupboard or damp room and allow it to remain there unless a set time is set.
Determination of initial setting time
- Place the test block enclosed in the mould and rest on a waterless plate, under a needle-carrying rod (C); gently lower the needle until it meets the surface of the test block and release it immediately, allowing it to enter the test area. Initially, the needle will completely pierce the test block.
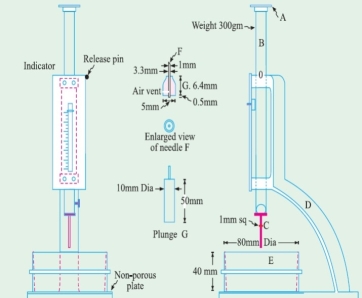
Fig no 26. Needles used in Vicat's Apparatus
- Repeat this process until the needle, when attached to the test block and removed as described above, fails to pierce the block more than 5.0 ± 0.5 mm measured from the bottom of the mould. The time elapsed between the time the water is added to the cement and the time when the needle fails to pierce the block reaches a point of 5.0 ± 0.5 mm measured from the bottom of the mould will be the first set time.
Determination of final setting time
- Insert needle (C) of Vicat resources into the needle with a secret attachment (F).
- The cement will be considered to be set at the end where, when the needle is gently inserted into the surface of the test block, the needle makes a picture of it, while the attachment fails to do so.
- The time elapsed between the time the water is added to the cement and the time when the needle makes its appearance on the surface of the block while the attachment fails to do so will be the last set time.
- In the case of a scarf that forms over the test block, use the bottom of the block to cut.
4. SOUNDNESS AND COMPRESSIVE STRENGTH
- Sensitivity refers to the ability of a glue that has been hardened to retain its volume after setting without the delay of harmful expansion.
- Thus, hearing is a very important test. The audio attachment will not make a pleasant volume change after it has hardened and as a result will not be in danger of forming cracks. Sound adhesive is the basis of sound mud or concrete mixing.
- Aircraft ash is the result of coal-fired power generation. During a fire, mineral pollutants in hot coals are released from the combustion chamber in the form of particles composed by flue gases.
- As these particles coo, they harden into round glass particles. The fly fly shows concrete structures and is used in concrete as replacement or replacement of concrete. Insufficiency can occur in the presence of very free magnesia or free lime burned in cement.
- The taste of cement can be determined in a variety of ways. In the Le Chatelier bath, a sample of cement / ash adhesive frosting is placed on the mould and boiled for a specified period of time (approximately 3hr) so that any tendency to stretch can be quickly and detected.
- After the boiling process is complete, the distance between the points of the two control indicators is measured by the nearest 0.5mm and compared to the first measured length before testing.
- This test requires Le Chatelier water bath, Le Chatelier mould, calliper, measuring cylinder, balance and length comparison. Active standards include EN 196-3, EN 459-2 and EN-450.
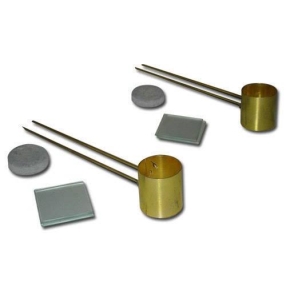
Fig no 27. Le chatelier apparatus
- Alternatively, the stability of the concrete can be determined by autoclave. These tests include an autoclave expansion of Portland cement using a test in a good cement sculpture.
- Specimens are made of oil-coated mould with reference points attached to a reference length of 250mm. Specimens extracted from the mould and measured after 24hr are placed in an autoclave at room temperature.
- After the autoclave is turned off, the specimens are exposed to a full-pressure current at a specified time. After the heating is complete, the template is rated and compared with the original length measurements.
- Equipment needed for this method includes autoclave, test bar mould, mixer equipment, balance and length gauge. Functional standards include ASTM C151 and AASHTO T107.
- The expansion of the cement can also be determined by comparing the length. The length gauge is a device used to measure changes in the length of attachment of cement, mortar and concrete according to ASTM and AASHTO data.
- The unit consists of a complex dial or digital display embedded in a solid, dual post frame structure. Moving and vertical anvils are designed to detect reference pins thrown at the edges of sample test bars.
- ELE offers a variety of devices for this method, including drying materials, shrinkage and humidity movements, as well as a ASTM-length ratio. Active standards include ASTM C151, C157, C227, C490, C531, AASHTO T-107 and T-160.
Key takeaways
- For simplicity, the initial set time is considered to have elapsed between the time when water can be added to the cement, at which point the paste begins to lose plastic.
- The last time is the last time the water is put in the cement, and the time when the glue is completely lost to the plastic and gained enough strength to withstand a certain direct pressure.
- Sensitivity refers to the ability of a glue that has been hardened to retain its volume after setting without the delay of harmful expansion.
- Thus, hearing is a very important test. The audio attachment will not make a pleasant volume change after it has hardened and as a result will not be in danger of forming cracks. Sound adhesive is the basis of sound mud or concrete mixing.
Tests on aggregate
Specific gravity
Gravity and the combined force of water are essential elements in the formation of concrete and bitumen mixtures. The thickness of a solid mass is a measure of its size to an equal volume of distilled water at a specified temperature. Because the compound can contain a void that is allowed to enter the water, two combined gravity measures are used:
- Apparent specific gravity and
- Bulk specific gravity
Apparent specific gravity, G app, is calculated on the basis of the volume of the number of compounds i.e. the volume without voids entering the water. Therefore
G app = [(MD / VN)] / W
Where,
- MD is a dry aggregate weight,
- VN integrated network volume without volume object focus,
- W the size of the water.
Bulk Specific Gravity, G bulk, is calculated on the basis of the total number of aggregates including the inlet. Therefore
G bulk = [(MD / VB)] / W
Where,
- VB total volume of aggregates including volume of water absorbed.
Grading of aggregate
- Collection placement determines the average grain size of the composite before it is used in construction.
- This is the use of a complex and clear combination. The combined sample is filtered through a set of sieves and weights stored in each filter by percentage words summarized.
- By dividing this amount by 100, The Fineness Modulus of that total is determined. This assists in the decision-making process about the number of well-known modular composites that must be combined to obtain the concrete of the desired quantity.
- The basis of a green and clear composite mix for a particular soft module is the presence of spaces or open spaces where the composite is packed together.
- For bad clean aggregates packing can leave 30-40 percent, which can only be removed by filling the fine particles.
- Similarly, in fine aggregates too, there are voids left to be filled with better particles (cement).
- This is important to get a mix of composite and blank letters.
- When other pieces of equal size are put together, voids or open spaces are always left. Percentage of voids can be as high as 45 percent of the total volume of aggregates.
- It turned out that this effect (presence of voids) was independent of the size of the aggregates used in the packaging, whether worse, medium or good.
- Only, while composite packaging should be of the same size, that is the same distance.
- Either all should be rough, or they should all be medium or good. This means that even if the sand alone is full, voids at a rate of 40-45 percent are left as well.
- This principle of spacing is the governing principle for the preparation of concrete under this method.
- When coarse aggregates are full to make concrete, the voids built into the weight should be filled with some good material. Sand is used for this purpose.
- However, there will be voids between the grains of sand as well. These are filled with cement particles.
- In this way, the weight of the resulting concrete is either empty or dense. Cement binding material is used to give this dense cone a stone-like character.
- Concrete, artificial stone, in a broad sense.
- Collection classification is intended to determine the particle size of a given group of composites.
- This is usually found by the Method of Fineness Modulus. This method can be used to determine the best modulus for coarse combinations, fine aggregates, and all composites, i.e., composite composites.
- In this way, the ideal weight of the sample is taken and filtered through a series of sieves respectively. The number of sieve is five in coarse aggregates and ten in all aggregates.
Sieve Size of Collection.
Coarse Aggregates: 80 mm, 40 mm, 20 mm, 10 mm, IS No..480
Fine Aggregates: Numbers 480, 240, 120, 60, 30 and 15.
Total included: 80 mm, 40 mm, 20 mm, 10 mm, Nos: 480, 240, 120, 60, 30 and 15.
Flakiness Index
Object
For determination of flakiness index of coarse aggregate, where the size of the coarse aggregate are larger than 6.3mm .
Apparatus
- Thickness gauge
- Sieves [63, 50, 40, 31.5, 25, 20, 16, 12.5, 10 & 6.3mm]
- Balance [0-10 kg]
- Thickness Gauge
Procedure
- The sample was removed with the IS filter defined in the Table shown below.
- Thickness size and long length
- Thickness size and long length
- A minimum of 200 pieces for each fraction is taken and measured.
- In order to separate the faulty material, each component is individually measured by the thickness of the size gauge.
- The total amount of blurring objects that transmit the size gauge is measured with an accuracy of 0.1% of the sample weight.
Elongation Index
Objective
For determination of elongation index of coarse aggregate, where the size of the coarse aggregate is larger than 6.3 mm
Apparatus
- Length gauge
- Sieves (63mm,50mm,40mm,31.5mm,25mm,20mm,16mm,12.5mm,10mm)
- Balance (0-10kg)
- Oven (3000c)
Procedure
- The sample was removed with the IS filter defined in the Table shown below.
- A minimum of 200 pieces for each fraction is taken and measured.
- To separate the extended objects, each fraction is measured individually in length in the length gauge.
- Combined pieces from each tested segment that could not exceed the specified gauge length and its long cut sides are collected separately to obtain the total composite weight stored at the gauge length from each segment.
- The total amount of extended material retained by the length gauge is measured with an accuracy of 0.1% of the sample weight.
Impact Value
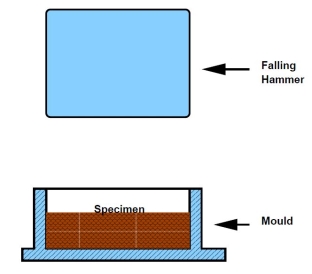
Fig no 28. Impact test apparatus
- Combined impact tests were performed to test for resistance to compound effects.
- The aggregates pass through a filter of 12.5 mm and are kept at 10 mm per filter are filled with a diameter of a diameter of 10.2 mm internal diameter and a depth of 5 cm attached to the metal base of the impact test machine.
- The content is completed in 3 layers where each layer is marked with 25 strokes.
- A steel hammer weighing 13.5 to 14 Kg is scheduled to be dropped with a free fall of 38.0 cm in v
- Ertical directions and a test sample is placed at 15 hits.
- The crushed joint is allowed to pass through a filter of 2.36 mm IS. And the impact value is measured as the percentage of aggregates that pass through the filter (W2) to the total sample weight (W1).
- Combined value = (W1 / W2) * 100
- Aggregates will be used to wear the course, the impact value should not exceed 30 percent. For bituminous macadams the maximum permissible value is 35 percent.
- In the basic studies of Water bound macadam the maximum allowable rate specified by the IRC is 40 percent.
Abrasion Value

Fig no 29. Abrasion value setup
- Abrasion testing is performed to test the hardness of the material and to determine whether it is suitable for various stone construction activities.
- The abrasion test in Los Angeles is very popular to achieve hard materials and is standardized in India (IS: 2386 part-IV).
- The goal of the Los Angeles abrasion test is to find a percentage wear due to the rubbing action associated between the balls attached to the metal used as a serious offense.
- The Los Angeles machine consists of a 700 mm diameter inner diameter and 520 mm long attached to a horizontal axis that makes it possible to rotate (see Fig-2). A circular charge with round metal balls 48 mm wide and weighing 340-445 g is inserted into the cylinder and compound.
- The number of alrasive panorama varies depending on the sample size. The amount of compounds to be used depends on the catch and usually ranges from 5-10 kg.
- The cylinder is then locked and rotated at a speed of 30-33 rpm at a rate of 500 -1000 changes depending on the assembly rate.
- After the specified changes, the material is filtered through a filter of 1.7 mm and a fraction is transferred as a percentage of the sample weight. This figure is called the Los Angeles abrasion rate.
- A maximum of 40 per cent is allowed in the WBM study in the Indian state. In bituminous concrete, a maximum of 35 percent is specified.
Crushing Value
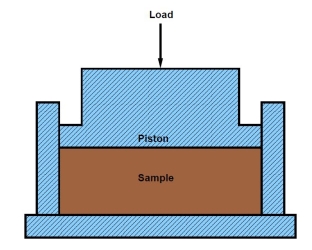
Fig no 30. Crushing test setup
- One of the models where the material is paved where it fails to press down under joint pressure.
- The test was rated with IS: 2386 part-IV and used to determine the combined crushing power.
- The combined value of the crush provides an approximate level of crushing resistance under the gradual crushing load.
- The test consists of placing a composite sample in a standard mold in a pressure test under normal load conditions.
- Dry aggregates pass through 12.5 mm sieve and 10 mm sieve are stored with a cylindrical dimension of 11.5 mm in diameter and 18 cm in height in three layers. Each layer is applied 25 times with a standard lubricant.
- The test sample is weighed and placed in a test cylinder in three layers each layer is also softened. The specimen is under a pressure load of 40 tons used slowly at an average of 4 tons per minute.
- The aggregates are then compressed and reduced by a filter of 2.36 mm and the weight of the passing object (W2) is expressed as a percentage of the total sample weight (W1) which is the total crushing value.
- Total crushing value = (W1 / W2) * 100
- A value less than 10 means a particularly strong combination while the above 35 can often be considered a weak combination.
Tests for fine aggregate:
Specific gravity
- The gravitational force of fine aggregate (sand) is defined as the mass of a given volume of aggregates in equal amounts of water. The gravitational force of fine aggregate (sand) is considered to be around 2.65 to 2.67.
- Quartz sand particles have a specific strength of between 2.65 to 2.67. While the odd clay starts from 2.70 to 2.80. Soils that contain a lot of organic matter or furry particles (such as diatomaceous earth) have a gravitational force of less than 2.60 (Some are as low as 2.00).
What is specific gravity of Aggregates?
The gravitational force of aggregate is considered to be the measure of the strength or quality of an object. The specified gravitational force is defined as the ratio of the weight of a given volume to a combination of the equivalent volume of water. Lower gravity scales are usually weaker than those with high gravity compounds. This property assists in the general identification of mergers.
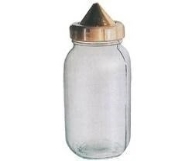
Fig no 31. Pycnometer bottle
Determination of Specific Gravity of Fine Aggregate as per IS: 2386 Part 3: (1963)
Hello friends, welcome to the world of Civil Allied Gyan. Read here the description, the list of apparatus, the IS code, the testing process, the formula and the web report about the determination of the gravitational force of a good collection.
Resources Required for Specific Integrated Voting Power Testing: -
- Pycnometer bottle of capacity 1000ml
- Touch stick
- Trench
- Balance scale
Is the Gravity Specific of Fine Aggregate test code: -
IS: 2386 (Part 3): 1963, Methods for testing concrete scales (Determining Specific Gravity of aggregates)
Procedure
- Take a clean and dry pycnometer and determine its empty weight (W₁ g).
- Take a pure sample of fine aggregate (about 1kg) to determine the gravitational force and transfer that to the pycnometer and weight (W₂ g). Aggregates better than 6.3mm taken.
- Pour the refined water into a pycnometer with a mixed sample at a temperature of 27 ºC, to water the sample only.
- Immediately after immersion, remove trapped air from the sample by moving or alternating the pycnometer, placing a finger in the hole at the top of the closed pycnometer.
- Clear the outer area of the pycnometer. Now the pycnometer is completely filled with water until the top hole, and after making sure that there is no more air trapped in the pycnometer, its weight (W₃ g).
- Transfer the value of the pycnometer to the care test being performed to ensure that all the components are transmitted. Clean the pycnometer.
- Re-fill the pycnometer with the added water to the top of the pycnometer, without any trapped air. It should be completely dry on the outside and take off weight (W₄ g).
- To fill the mineral, a special magnetic field bottle is used and the equipment is filled up to three times the volume of the bottle. The whole process of determining gravity is similar to that described above.
Seive Analysis
Objectives:
The whole process of sieve analysis determines the distribution of particle size of fine aggregates and determines whether it is suitable for use in concrete mixing.
Testing Resources
A series of IS filters
4.75 mm
2.36 mm
600 mic
300 mic
150 mic
75 mic
Procedure
- The sample was weighed exactly 1000g.
- First, we must clean all the sieve using a wire brush to make it clear that aggregates are trapped in some gaps.
- After that we have to prepare the sieve in the moving machine from top to bottom, in size from the largest (4.75mm) to the smallest (0.075mm).
- The sample was diluted using a collection of IS Sieves 10 minutes.
- After sieving is done, the merging with each filter is measured individually.
- The aggregate weight that passes through each filter is calculated as a percentage of the total sample weight.
- The same procedure is followed by two other samples.
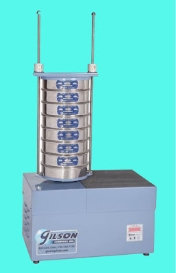
Fig no 32. Mechanical Sieve Shaker
Fineness Modules
The fineness modulus (FM) of aggregates may be a frightening term, but it is just a conceptual measure that describes the average size of particles in a composite sample. This feature provides the basis for selecting the approximate size of concrete joint design, but its actual impact is not always understood. The Fineness modulus is not a fixed value, as it provides a way to estimate the amount of integration needed to measure the mixing designs.
How to fineness modulus measure
Fineness modulus is determined using the percentage of size fractions from the sieve analysis and calculated for any selected series of sieve sizes. When designing concrete mixes, FM for good mixing is required to properly separate the mixes. Changes in the placement of the coarse aggregate section have little effect on the overall concrete structures. Combined partitions can be made using different cutting and fine-grained joints and blending techniques to control FM with concrete mix.
Origin of the Fineness Modulus Concept
Duff Abrams, an American inventor of the early 20th century, was an influential figure in the study of concrete structures and features. As well as explaining the importance of water / cement ratio and developing a fall test, he described the fineness modulus in 1918 as a way to separate concrete aggregates, simplify a gradation curve, and measure the appropriate size for use in mixing designs. Explaining the principle he said, "The integration of the same good modulus will require the same amount of water to produce the same coherence and provide the same strength concrete."
Includes Fineness Modulus
The simple FM calculation procedure requires a precise particle size analysis as described in ASTM C136, Standard Test Method for Sieve Analysis of Fine and Coarse Aggregates. In addition to the required particle size sizes, specific FM statistics must be included. Although manual upgrade of the sieve is permissible in standard, Gilson strongly recommends the use of the appropriate connector to ensure accuracy, durability and efficiency. After the filter has been analyzed and the fractions are measured in the correct proportions or proportions, the percentage of fractions is calculated.
Fineness Modulus of sand
To calculate the simple sand module, the total percentage accumulated stored in the following sieve is divided into 100: 150μm (No. 100), 300μm (No. 50), 600-μm (No. 30), 1.18mm (No. 16) , 2.36mm (No. 8), and 4.75mm (No. 4) of fine aggregates. If FM coarse aggregates are required, filters of 9.5mm (3⁄8in.), 19.0mm (3⁄4in), 37.5mm (11⁄2in) can be installed. There may be even larger sieves that can be added by continuing at a ratio of 2: 1 with the original sieve size. No additional equipment is required to make the determination. The same ASTM E11 test filters are used for integrated particle size analysis tests. In the example below, aggregate percentages from 4.75mm to 150µm are used to calculate the correct modulus for this fine mixing sample.
Alkali Aggregate Reaction
- Alkaline reaction - silica (ASR), more commonly known as "concrete cancer", is a painful inflammatory process that occurs over time in concrete between alkaline cement and active amorphous (eg, non-crystalline) silica found in many common compounds, sufficient moisture is provided.
- The pattern of cracks is associated with an alkaline-silica reaction that affects the concrete step barrier on the US highway. Note the common oily feature of the silicate debris imbibing the concrete surface on both sides of the crack.
- This undesirable chemical reaction results in the expansion of the altered composition by the formation of soluble and viscous gel of sodium silicate (Na2SiO3 • nH2O, and marked Na2H2SiO4 • nH2O, or N-S (sodium silicate hydrate), depending on the assembly received).
- This hygroscopic gel swells and increases in volume as it absorbs water: it has a high pressure inside the siliceous compound, which causes cracks and loss of concrete strength, eventually leading to its failure.
- The ASR can lead to severe cracking of the concrete, leading to serious structural problems that could force the demolition of a particular building.
- The extension of the concrete reaction between cement and composite size was first studied by Thomas E. Stanton in California in the 1930s with his publication in 1940.
Buckling of sand
- The increase in volume of a good compound due to the presence of moisture content is known as bulking. This is because the moisture causes a film of water around the sand particles leading to an increase in the volume of the sand, at a moisture content of about 5 to 8%, this increase in volume can be 20 to 40%, depending on the placement of the sand.
- The more effective it is, the more volume will be given to the moisture content provided. This practice is known as sand bulking.
- As the moisture content increases by adding more water, sand particles accumulate closer and the bulking value of the sand decreases. Therefore, dry sand and water-soaked sand are about the same size.
- Constipation of sand affects the balance of the sand to a large extent. Most with fine sand and less with coarse sand. If the right grant is not made for sand extraction, the cost of concrete, and vehicles will increase and it will result in less sandy loam and hard to operate and maintain.
Important facts regarding sand formation are as follows
- As the moisture content increases by adding more water, sand particles accumulate closer and the bulking value of the sand decreases.
- One of the reasons for adopting a weight measurement is the constipation of sand as weight loss avoids difficulty due to the abundance of sand.
- Sanding of the sand should be considered when the volumetric value of the value is accepted.
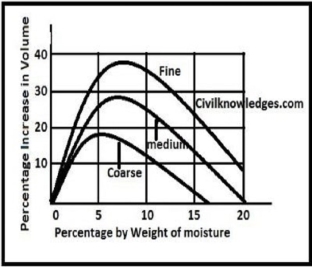
Fig no 33. Buckling of fine aggregate
Determining of buckling of fine aggregate
Opera and the process of determining the best percentage output
- Laboratory testing of bulk composites
- Field test for average quantity
Fine Aggregate Collection Laboratory Testing
Apparatus
- 250 ml measuring cylinder
- Weight balance
- Good combination
Procedure
- Take 500 grams of frozen fine aggregate at a temperature of 100 to 110 degrees Celsius for 24 hours. This is a weight measure as W1.
- Cool sand picks up airtight containers. So this weight ratio as W2.
- Sample water content is calculated as
- Wc = (W1-W2) X 100 / W1
- In a pan, 250 grams of sand take.
- In this case 2% by weight of water add. This is well integrated.
- The mixture is poured into a 250ml cylinder. This is compounded by shanking.
- The test was repeated with the remaining amount of 2% water sand at each time point. The reading takes as Y2, Y3… etc until the volume reading decreases.
- After their level, 4% of the water is added and the test continues until the sample is completely filled.
- For a standard sample in a measuring cylinder, add about 50 ml of water and stir the sample well.
ARTIFICIAL AND RECYCLED AGGREGATE
Artificial aggregates
- Many synthetic aggregates can be controlled, by industrial process products, such as various slags, or uncontrolled waste from other industrial processes, such as clinkers and ashes.
- Another important source of waste is the mining industry, including the extraction of coal and China clay.
- Some products that come out once or the waste can be made, or need to be recycled, to make things that are suitable for use as concrete mixers or that show special properties. In addition, other natural materials, such as perlite or vermiculite, can also be processed to produce compounds that reflect special properties.
- Demolition debris is reused to produce concrete scales. The RILEM (TC-121) technical committee recommended the separation of those compounds.
Recycled aggregate
- The construction industry produces a large amount of waste that needs to be recycled and used as recycled aggregates (RAs) for partial or complete environmental integration.
- Recycling reduces waste and reduces energy consumption and that is why it has an impact on the sustainable construction industry.
- In this chapter the need to redefine the current situation and situation around the world is highlighted. The structures of the RA are discussed. RAs weigh less than viral substances and higher water absorption.
- The state of the art of RA performance of concrete in a new and difficult world is summarized. The RA concrete exhibits low pressure and flexibility as well as low-strength mode and low cracking due to the porous nature of the RA and the old mud attached to the cement above the composite.
- The strength of the bond and the strength of the abrasion are less affected. Depletion, water infiltration and water infiltration by capillary increase with increased RA content.
- However, low performance can be reduced with a good mixing design using cement additives. Successful applications for RA in the manufacture of adhesive and truck concrete are also being discussed
Key takeaways
There are different tests for coarse aggregate which are
1. Specific gravity
2. Grading of aggregate
3. Flakiness index
4. Elongation index
5. Impact value
6. Abrasion value
7. Crushing value
There are different type of test for fine aggregate which are
1. Specific gravity
2. Seive analysis
3. Fineness modulus
4. Alkali aggregate
5. Buckling of sand
6. Artificial and recycle aggregate
Special Concrete - Light Weight Concrete and its Type
- Lightweight concrete may be described as a sort of concrete which incorporates an increasing agent in that it will increase the quantity of the combination whilst giving extra characteristics which includes nailability and lessened the useless weight.
- It is lighter than the traditional concrete. The use of light-weight concrete has been broadly un fold throughout international locations which includes USA, United Kingdom and Sweden.
- The essential specialties of light-weight concrete are its low density and thermal conductivity.
- Its blessings are that there may be a discount of useless load, quicker constructing quotes in creation and decrease haulage and managing costs.
- Lightweight concrete keeps its huge voids and now no longer forming laitance layers or cement movies while located at the wall.
- These studies became primarily based totally at the overall performance of aerated light-weight concrete.
- However, enough water cement ratio is essential to provide good enough concord among cement and water.
- Insufficient water can purpose loss of concord among debris, for that reason loss in energy of concrete.
- Likewise, an excessive amount of water can purpose cement to run off mixture to shape laitance layers, finally weakens in energy.
- Lightweight concrete has been used because the eighteen centuries through the Romans.
- The software at the ‘The Pantheon’ wherein it makes use of pumice mixture with inside the creation of solid in-situ concrete is the evidence of its usage.
- In USA and England with inside the overdue 19th century, clinker became used of their creation as an example the ‘British Museum’ and different low price housing.
- The light-weight concrete became extensively utilized in creation at some point of the First World War.
- The United States used particularly for shipbuilding and urban blocks.
- The foamed blast furnace-slag and pumice mixture for block making had been added in England and Sweden round 1930s.
- Nowadays with the development of technology, light-weight concrete expands its makes use of.
- For example, with inside the shape of perlite with its top notch insulating characteristics.
- It is broadly used as loose-fill insulation in masonry creation wherein it complements hearth place ratings, reduces noise transmission, does now no longer rot and termite resistant.
- It is likewise used for vessels, roof decks and different applications.
Materials utilized in Light weight concrete:
- Lightweight concrete may be produced through introducing:
- Gassing retailers which include aluminium powder or foaming retailers,
- Light-weight mineral mixture which includes per lite, vermiculite, pumice, elevated shale, slate, and clay, or plastic granules as mixture
Properties of Light weight concrete:
- Low Density
- Fire Resistance
- Sound Insulation
- Durability
- Thermal insulation
- Quality Control
Low Density
- The density of concrete varies from three hundred to 1200 kg/m³.
- The lightest grade appropriate for insulation proposed whilst the heavier grades with good enough energy appropriate for structural applications.
- The low density of cell concrete makes it appropriate for precast ground and roofing devices which can be smooth to deal with and shipping from the manufacturing unit to the sites.
Fire Resistance
- Lightweight concrete has outstanding hearth place-resisting properties.
- Its low thermal conductivity makes it appropriate for protective every other established shape the outcomes of fir
Sound Insulation
- Sound insulation in cell concrete is typically now no longer as suitable as in dense concrete.
Durability
- Aerated concrete is handiest barely alkaline. Due to its porosity and coffee alkalinity.
- It does now no longer deliver rust safety to metallic that's supplied through dense as compared concrete.
Thermal insulation
- The insulation fee of light-weight concrete is set 3 to 6, instances that of bricks and approximately ten instances of concrete.
- When a two hundred mm thick wall of aerated concrete of density 800 kg/ m3 has the identical diploma of insulation as a four hundred mm thick wall of density 1600 kg/ m3.
Quality Control
- Better first-rate manipulate exercised with inside the creation of a shape with light-weight concrete merchandise because of using manufacturing unit-made devices.
Types of Light weight Concrete:
Lightweight aggregate concrete:
- Lightweight aggregate concrete is referred to as an LWA.
- In the early 1950s, using light-weight concrete blocks familiar withinside the UK for the load-bearing internal leaf of hollow space walls.
- Soon thereafter the improvement and manufacturing of a brand new sort of synthetic LWA made it viable to introduce LWC of excessive energy, appropriate for structural work.
- These advances inspire the structural use of LWA concrete. Particularly wherein the want to lessen weight in a shape became an critical attention for layout or for the economy.
Aerated Concrete:
- Aerated concrete has the bottom density, thermal conductivity, and energy.
- Like timber, it is able to be sawn, screwed and nailed, however there are non-combustible.
- For works in-situ, the standard strategies of aeration are through blending in stabilized shape or through whipping air in with the useful resource of an air-entraining agent.
No fines concrete:
The time period no-fines concrete typically way concrete composed of cement and a coarse (9-19) aggregates handiest and the product so fashioned has many uniformly disbursed voids for the duration of its mass.
- Ordinary light-weight concrete organized from a binder, water best and coarse mixture with complete filling voids among the huge debris.
- Low Sand concrete, wherein the voids among the coarse mixture handiest partly packed with the paste.
- It additionally referred to as an opening graded concrete and dealt separately.
- In this example on best mixture use. Coarse debris of the mixture are coved through a skinny layer of cement, paste and the voids among them stay empty. It is referred to as no concrete.
- Aerated concrete crafted from a binder, water, best and coarse mixture, and a blowing agent which reduced the density of concrete.
Typical Light weight concrete mix:
- Lightweight concrete is a combination made with light-weight coarse aggregates inclusive of shale, clay, or slate, which offer it its feature low density.
- Structural light-weight concrete has an in-location density of ninety to a hundred and fifteen lb/ft³, while the density of everyday weight concrete tiers from a hundred and forty to a hundred and fifty lb/ft³.
- This makes light-weight concrete perfect for constructing current systems that require minimum pass sections with inside the foundation.
- It is being an increasing number of used to construct glossy foundations, and has emerged as a possible opportunity to everyday concrete.
- Nevertheless, a better compressive power of 7000 to 10,000 psi may be attained with light-weight concrete.
- However, this will compromise the density of the combination because it calls for the addition of greater pozzolans and water-decreasing admixtures to the concrete.
Key takeaways
1. Lightweight concrete keeps its huge voids and now no longer forming laitance layers or cement movies while located at the wall.
2. This study became primarily based totally at the overall performance of aerated light-weight concrete.
3. Aerated concrete is handiest barely alkaline. Due to its porosity and coffee alkalinity.
4. It does now no longer deliver rust safety to metallic that's supplied through dense as compared concrete.
Foam Concrete
- Foam concrete usually consists of cement mortar or fly ash and sand and water, although some suppliers recommend pure cement and water with an agent that produces lightweight mixtures.
- This slurry is also mixed with a foam made into a concrete mixing plant. The foam is made using a moisturizing agent, mixed with water and air from the generator. The foam operator used must be able to produce bubbles with a high degree of stability, resistant to physical and chemical processes of mixing, depositing and solidifying.
- Foam concrete mix can be poured or sprayed on moulds, or directly on parts of the building. Foam makes the Sulphur flow freely due to the thixotropic behaviour of foam bubbles, allowing it to be easily absorbed into the selected form or mould.
- Viscous materials require up to 24 hours to harden (or at least two hours if the smoke is treated at temperatures up to 70 ° C to speed up the process. Depending on the variability including ambient temperature. And moisture. Once solidified, the manufactured product can be removed from its mould.
- A new application in the production of foam concrete is to cut large-size concrete cakes into blocks of different sizes with a cutting machine using special metal wires. The cutting action occurs when the concrete is still soft.
Properties
Foam concrete is a versatile construction material with a simple and inexpensive method of production compared to air-cooled autoclave concrete. Foam compounds using foam-using ashes for this cheap compound are still cheap, and have little impact on the environment. Foam concrete is produced in quantities ranging from 200 kg / m3 to 1,600 kg / m3 depending on the application. Smaller products can be divided into different sizes. While the product is considered to be a type of concrete (with air bubbles replacing the whole), its thermal and sound insulation properties make it a very different application than conventional concrete.
Applications
Foam concrete can be produced in dry quantities of 400 to 1600 kg / m3 (25 lb / ft3 to 100 lb / ft3), with a capacity of about 7 to 10 days N / mm2 (145 to -1450 psi) respectively. The foam concrete is fire resistant, and its thermal and sound insulation properties make it ideal for a variety of purposes, from floor and ceiling protection, to useless filling. It also helps to restore the trench.
A few applications of foam concrete are:
- Bridge / bar road routes
- Pipe discharge / annual filling
- Back ditch
- Precast blocks
- Precast wall elements / panels
- Cast-in-situ / cast-in-place walls
- By defending the imposition of compensation
- Split down screens
- Partition roof screeds
- The filling of the deceased part
- Trench for restoration
- Sub-base on highways
- The filling of empty blocks
- Partition boards used
Key takeaways
1. Lightweight concrete may be described as a sort of concrete which incorporates an increasing agent in that it will increase the quantity of the combination whilst giving extra characteristics which includes nailbility and lessened the useless weight.
2. It is lighter than the traditional concrete. The use of light-weight concrete has been broadly un fold throughout international locations which includes USA, United Kingdom and Sweden.
No Fines Concrete
What is No-Fines Concrete?
- No-Fines Concrete is a lightweight concrete made of cement only, cement and water by leaving fine particles (sand or fine compounds) of ordinary concrete. The benefits, limitations and equity of the exemptions are discussed.
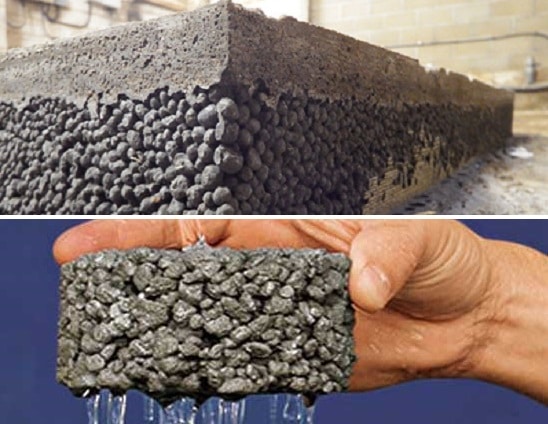
Fig no 34. No fines concrete
- Usually only one equal measurement, of more than 20 mm in size, is kept in 10mm. Concrete no-faes are popular because of the specific benefits you have over conventional concrete.
- The single-layer collection makes a beautiful, non-abrasive concrete, which in addition to getting large voids and therefore light weight, also gives a nice look to the build.
Advantages of No-Fines Concrete
- No fine concrete is a heavy concrete i.e. the density is approximately 25 to 30% less than normal concrete due to the lack of good adhesion, so the weight of the structure is small.
- Since it does not have good sand or aggregates, it has less drying shrinkage compared to conventional concrete
- It has a better heat protection feature than ordinary concrete and therefore helps in the construction of the outer wall.
- Since it does not have good aggregates, the required area for cement coverage has been greatly reduced. Therefore, the required amount of cement is reduced per cubic meter compared to conventional concrete. Therefore, it will save.
- Heavy concrete has no effect on quality due to the fragmentation of the compact cluster as it does not have good dimensions. Therefore, it can be thrown higher.
- No fine concrete can be assembled without the need for any types of concrete vibrators and can be easily made by touching the rods.
Limitations of No Fines Concrete
- Since there are no good compounds to fill the gaps in this concrete, it has a higher penetration than standard concrete. Therefore, it is not a good idea to build reinforced concrete without compensation concrete, as reinforcement can be easily eaten.
- To make this concrete inaccessible, an additional coat of construction mud is required, which adds to the cost.
- There is no concrete test that can be tested for effectiveness by using tests on standard concrete such as rolling or testing for rigidity. Performance rates and their testing methods are unknown.
Mix proportion of No-Fines Concrete
- No-fines concrete is usually made with aggregate / cement scales from 6: 1 to 10: 1. The standard aggregates used are usually sizes over 20 mm and stored at 10 mm.
- Unlike conventional concrete, where the strength is primarily controlled by the water / cement ratio, the strength of the concrete can be charged depending on the water / cement ratio, the estimated cement ratio and the weight of the concrete.
- The water / cement ratio for satisfactory consistency will vary between a minimum width of 0.38 and 0.52. The water / cement level should be chosen carefully. If a very low amount of water / cement is accepted, the adhesive will dry so much that the adhesive can be well coated with adhesive resulting in insufficient adhesion between the particles.
- On the other hand, if the water / cement ratio is too high, the glue will run down the concrete floor, especially if you move and fill in the gaps between the joints at the bottom and make that part more compact. This condition also reduces the adhesion between the adhesive and the adhesive due to the adhesion being much thinner.
- There is no standard method available, such as a descent test or an object measurement test to measure the consistency of a non-finite concrete. Perhaps a good test, visual experience and trial and error method would be the best guide to determine the water / cement ratio.
- No-faes concrete, when using standard aggregates, can show a density of about 1600 to 1900 kg / m3, but if no-faes concrete is made using lightweight aggregate, the size can reach approximately 360 kg / m3.
- Concrete of no-faes does not pose a major congestion problem. The use of a combination of equipment or vibration methods is not required. Simple rodding is sufficient for full filling.
- Concrete of no-faes does not give much to the formation side as the particles have a point of identification of the contact and the concrete does not move. Therefore, the side of the formworks can be removed in a much shorter time than ordinary concrete.
- However, the forms may need to be stored longer, when used as part of the structure, as the strength of the concrete decreases considerably. The compressive strength of the fine-grained concrete varies between 1.4 M Pa to 14 M.
- The strength of the bonded concrete bond is very low and, therefore, the reinforcement is not used in combination with the non-charged concrete. However, if the reinforcement needs to be applied to a non-abrasive concrete, it is advisable to touch the reinforcement with cement to improve the bond and protect it from cracking.
Key takeaways
1. No-Fines Concrete is a lightweight concrete made of cement only, cement and water by leaving fine particles (sand or fine compounds) of ordinary concrete. The benefits, limitations and equity of the exemptions are discussed.
2. Usually only one equal measurement, of more than 20 mm in size, is kept in 10mm. Concrete no-faces are popular because of the specific benefits you have over conventional concrete.
Self Compacting Concrete
- Self-compacting concrete (SCC) is a flowing concrete that doesn't require vibration and, indeed, have to now no longer be vibrated.
- It makes use of super plasticizers and stabilizers to seriously growth the benefit and price of glide.
- It achieves compaction into each a part of the mildew or formwork genuinely by using its personal weight with none segregation of the coarse aggregate.
- The consistence of the concrete is designated and measured as a glide price as opposed to the everyday stoop test.
SCC offers:
- Health and protection benefits (as no vibration is needed).
- Faster creation times.
- Increased workability and simplicity of glide round heavy reinforcement.
- Excellent sturdiness.
Advantages of SCC:
- No vibration is needed in the course of the position into forms.
- Placement of concrete easier.
- Reduces the concreting time.
- Increased sturdiness of structure.
- High Strength
Material used in SCC:
- The powdered substances that may be delivered are fly ash, silica fume, lime stone powder, glass filler and quartzite filler.
Tests for SCC:
Following are numerous techniques for checking out the houses of sparkling concrete:
- Slump glide test
- T50 stoop glide test
- J ring test
- V Funnel test
- V funnel at T5 minute
- L container test
- U container test
- Fill container test
- GTM display balance test
- Orimet test
Sr .no. | Method | Units | Typical mix | |
Minimum | Maximum | |||
1 | Slump cone by Abrams cone | Mm | 650 | 800 |
2 | T50slumpflow | Sec | 2 | 5 |
3 | J ring | Mm | 0 | 10 |
4 | V funnel | Sec | 8 | 12 |
5 | V funnelatT5minute | Sec | 0 | 3 |
6 | L box | (h2/h1) | 0.8 | 1.0 |
7 | U box | (h2-h1) Mm | 0 | 30 |
8 | Fill box | % | 90 | 100 |
9 | GTM screen stability test | % | 0 | 15 |
10 | Orimet | Sec | 0 | 5 |
Properties of SCC:
Strength:
Strength of concrete are of the subsequent types:
- Compressive strength
- Tensile strength
- Flexural strength
- Shear strength
1.Compressive Strength
- The dice specimens of concrete of the preferred percentage are solid in metallic or solid iron moulds, typically 6-inch dice.
- The general cylinder specimen of concrete is 6 inch in diameter and 12 inches in peak and solid in a mould commonly fabricated from solid iron;
- Standard cubes and cylinders are examined at prescribed ages, commonly, 28 days, with extra exams frequently made at 1, three, and seven days.
- The specimens are examined for crushing electricity below a checking out machine.
- The dice exams supply an awful lot more values of crushing electricity, typically 20 to 30 % extra than the ones given via way of means of cylinders.
Effect of age on concrete strength:
- Concrete attains electricity with time.
- Ordinary cement concrete profits above 70 to 75% of its very last electricity inside 28 days and approximately ninety to 95 % with inside the path of 1 year.
- It is frequently perfect to test the suitability of a concrete lengthy earlier than the effects of the 28-day check are available.
- When no particular records at the substances utilized in making concrete are available, the 28-day electricity can be assumed to be 1.5 instances of the 7 days’ electricity.
- Tests have proven that for concrete made with regular Portland cement the ratio of the 28 days to 7 days’ electricity commonly lies among 1.three to 1.7, and the bulk of the effects fall above 1.5.
2. Tensile strength
- Concrete could be very susceptible in tension.
- The tensile electricity of regular concrete levels from approximately 7 to 10 percentage of the compressive electricity.
3. Flexural strength
- The flexural electricity of undeniable concrete is nearly fully established upon the tensile electricity.
- However, experiments display that the modulus of rupture is substantially more than the electricity in tension.
4. Shear strength
- It is the actual figuring out issue with inside the compressive electricity of brief columns.
- The common electricity of concrete in direct shear varies from approximately 1/2 of of the compressive electricity for wealthy combinations to approximately 0.8 of the compressive electricity for lean combinations.
Workability:
- The electricity of concrete of a given blend percentage could be very significantly laid low with the diploma of its compaction.
- It is consequently essential that the consistency of the combinationture be such that the concrete may be transported, positioned and completed sufficiently effortlessly and without segregation.
- A concrete pleasant those situations is stated to be workable.
Elastic Properties:
- Concrete isn't always flawlessly elastic for any variety of loading, an considerable everlasting placing taking location for even low loads.
- The deformation isn't always proportional to the strain at any degree of loading.
- The elastic residences of concrete range with the richness of the aggregate and with the depth of the strain.
- They additionally range with the age of concrete.
Durability:
- Durability is the assets of concrete to face up to the circumstance for which it's been designed, without deterioration over a length of years.
- Lack of sturdiness may be resulting from outside sellers bobbing up from the surroundings or via way of means of inner sellers in the concrete.
Application of SCC:
- Construction of Bridges, buildings, tunnels.
- Precast Concrete Members
- Casting of slab and slender wall
Typical Mix:
- A easy device has been designed for self-compacting concrete (SCC) blend layout with 29% of coarse aggregate, substitute of cement with Meta kaolin and sophistication F fly ash, combos of each and managed SCC blend with 0.36 water/cement ratio(via way of means of weight) and 388 litre/m3 of cement paste volume.
Key Takeaways
1. Self-compacting concrete (SCC) is a flowing concrete that doesn't require vibration and, indeed, have to know no longer be vibrated.
2. Concrete isn't always flawlessly elastic for any variety of loading, an considerable everlasting placing taking location for even low loads.
High Density Concrete
- High density concrete is a concrete having a density with inside the variety of 6000 to 6400 kg/cu.m.
- High density concrete is likewise called Heavy weight concrete.
- High density concrete is specifically used for the cause of radiation protective, for counterweights and different makes use of in which excessive density is required.
- The excessive density concrete has a higher protective property, in order that it is able to shield dangerous radiations like X-rays, gamma rays, and neutrons.
- High density aggregates are used to attain heavy weight concrete. Some of the excessive density aggregates are, barite, ferro phosphorus, limonite, hematite, ilmenite, magnetite, goethite, metallic punching, and metallic shots.
- The factor to keep in mind is that in order to attain this sort of concrete, excessive constant water content material is required.
- The choice of the above cited aggregates specifically depends on the bodily houses like bulk density, unique gravity, Availability of substances, and its expenses.
- In order to attain workability, excessive density the aggregates have to be loose from dirt, oil or grease stains and different overseas matter.
- Or else, it's going to retard the hydration method and the powerful bonding of particles.
- Some of the boron additions like colemanite, boro calcite is used with inside the preparation of concrete to enhance the protective houses.
- These additions might also additionally have an effect on the placing time of concrete so, trial mixes have to be made and examined relying upon the suitability.
- As the call suggests, the density of this concrete varies from 3360 kg/m3 to 3840 kg/m3, while the density of regular concrete is of the order of 2400 kg/m3.
- The density of mild weight concrete is ready 1900 kg/m3 and that of regular concrete approximately 2400 kg/m3.
- Thus, the density of excessive density concrete is ready 50% greater than the density of traditional concrete.
- However, this concrete may be produced of density up to 5200 kg/m3 the use of iron as each nice and coarse mixture.
- With the arrival of the nuclear electricity, there's a big call for of the concrete technologists with inside the market.
- Due to using nuclear electricity generating reactors, big scale manufacturing of penetrating radiation and radioactive substances additionally has taken location.
- Thus, all nuclear electricity generating gadgets inclusive of nuclear reactors, particle accelerator, business radiography, x-ray and gamma ray remedy gadgets require nuclear protective cloth for the safety of the working employees in opposition to the organic risks inclusive of radiation.
- The regular in addition to excessive density concrete is powerful and low in cost for the development of everlasting guard in opposition to radiation.
Materials in High density concrete:
- All represent substances, cement, admixtures, and water utilized in excessive density concrete have to agree to the requirements as for regular density concrete, however the aggregates is unique and can require unique attention at some stage in handling, batching, blending, transporting and setting.
Aggregates:
- High density concrete (HDC), densities is executed via way of means of the use of excessive-density aggregates commonly iron oxides and relies upon on its meant use, bodily and chemical houses, availability and price.
- Concrete densities of 3700 to 3800 kg/m³, is offered utilizing aggregates with particle relative densities of as a minimum 4500 kg/m³ and for concrete densities of 4800 kg/m³ aggregates have to have a particle relative density of as a minimum 6000 kg/m³.
- Aggregate grading for HDC hardly ever agree to regular mixture requirements because the mixture are hardly ever made for concrete manufacturing, this have to be general via way of means of capacity customers because it isn't always adverse to the manufacturing of HDC.
- The maximum critical a part of HDC aggregates is that the grading have to be consistent and that a attainable grading restriction be agreed on with the dealer, to base the combination layout on.
- The chemical houses of all excessive-density aggregates have to be evaluated earlier than use, chemical reactivity and mainly in excessive alkaline environments as observed in cement pastes, long time sturdiness inclusive of alkali-mixture reactivity, sulphate and chloride assault and different impurities.
- The dealer have to be capable of offer a complete chemical evaluation of all capacity substances and opportunity substances to be used.
- With right technical assessment and planning, unique styles of aggregates may be blended on the dealer backyard to provide a concrete with predicted, detailed density.
- Cost thing are very critical as those aggregates are commonly greater highly-priced than regular aggregates, it is able to additionally be that the cloth might also additionally handiest be to be had in relative brief supply.
- The price of HDC will increase with density however now no longer essential in direct proportion.
- Aggregates have to be decided on for his or her shape (cubical or rounded and freed from flat or elongated, most density, workability, and price. Particle relative density of the nice mixture have to be just like that of the coarse mixture as decrease density nice mixture can cause segregation of the coarse mixture via the mortar.
- The grading of the coarse mixture have to be uniformly graded among 10 and 40mm, as in step with limits in Table 1. The grading of the nice mixture have to be in the restriction as proven in Table 1 as this will assist to save you segregation.
Sieve sizes mm:
Grading 1 for 37.5 mm most length aggregates % passing
Grading 2 for 19.0 mm most length aggregates % passing
Coarse aggregates:
Two styles of aggregates may be used for excessive density concrete namely:
Natural aggregates:
- Iron ores of diverse sorts had been used all over the globe for lots years (out of doors the U.K), with inside the UK imported iron ore is used.
- Using a few herbal going on aggregates concrete densities of about 4000 kg/m³ may be obtained. (J. Goodman, 2009)
- Different styles of herbal excessive-density aggregates which may be used for excessive density concrete (HDC) to be had in South Africa and the United Kingdom talk over with Table 2.
Man-made aggregates:
- To attain concrete densities above 4000 kg/m³ man-made or artificial cloth inclusive of ferrosilicon slag, metallic or lead shot may be used.
- For styles of man-made aggregates which may be used for excessive density concrete (HDC) to be had in South Africa and the United Kingdom talk over with Table 2.
Cements:
- All cements conforming to SANS 50197 as for traditional concrete may be used for HDC if it produces the desired bodily houses.
- If alkali-reactive materials are gift with inside the aggregates cements with low alkali contents or a appropriate combination of cements and cement extenders have to be used.
- Low-alkali cement now no longer having greater that zero.6 % Na2O-eq can be used with a doubtlessly alkali-reactive mixture inclusive of lead shot.
- The following extenders: Ground granulated blast furnace slag (GGBS), fly ash (FA) and Condensed silica fume (CFS) have decrease densities than Ordinary Portland Cement (OPC) and may be used in the event that they do now no longer lessen the density of the concrete under detailed limits, but states “The cement may be OPC or a mix of this with both Ground granulated blast furnace slag, Pozzolanic fly ash; the latter if you want to now no longer lessen the density of the concrete however might also additionally decorate the in any other case terrible workability”.
- Fly ash blends and decrease water contents can effectively be used to boom the density of concretes. When lad shot is used High alumina cement (HAC) should be used, because it reduces the chemical reactivity of lead in excessive alkaline conditions.
- When the use of alkali-reactive mixture (lead shot) deleterious enlargement may be avoided whilst the use of excessive-alkali cements via way of means of including extenders complying with SANS 1491 via way of means of the use of a minimal percent of the subsequent extenders via way of means of general mass of cement:
At least 40% Slag (S) via way of means of mass
At least 15% CSF via way of means of mass
At least 20%via way of means of mass
Admixtures:
- Adding admixtures can minimize segregation, bleeding, each of which may be complex with HDC. The sturdiness may be advanced with a low loose water/cement ratio (w/c) in particular so in structural grade HDC.
- Using terrific plasticizers is usually recommended which in conjunction the cement kind might also additionally marginally boom concrete density.
- Super plasticizers are useful in decreasing water to minimize bleeding and preserve a cohesive blend that has minimal segregation.
The following admixture may be utilized in HDC:
- Air-entraining admixtures because it controls bleeding and agreement enhance workability and help in acquiring greater homogenous concrete however will lessen the density of the concrete.
- Water-decreasing admixtures because it will boom concrete density via way of means of decreasing the quantity of water with inside the blend, water is the cloth utilized in HDC with the bottom density.
- Shrinkage-decreasing admixtures because it make sure dense, crack-loose concrete used for radiation-protective concrete
- When lead shot or lead containing aggregates are to be used, the subsequent have to be taken into consideration whilst choosing a chemical admixture.
- The alkali content material of chemical admixtures for concrete utilized in South Africa is among approximately zero.2 and 7%. In many times the contribution to the alkali content material of the pore answer is big and can't be ignored.
- One of the extensively used terrific plasticizers has a Na2O-eq of approximately five% and if introduced at 1% of cement to concrete with a cement content material of 350 kg/m³ it's going to advert 0.17 kg/m³ Na2O-eq to the concrete.
- Lithium primarily based totally compounds may be used with lead shot to manipulate the alkali reactivity.
- The impact of admixtures have to be installed beneath discipline conditions, ideally via way of means of testing, to decide if the admixtures attain the desired effects or completely unsuitability.
Water:
- Water will be easy and loose from adverse concentrations of acids, alkalis, salts, sugar and different natural or chemical materials that would impair the sturdiness and power of concrete or imbedded metallic.
Proportioning, blending and setting of High Density Concrete:
- The blend proportions for those excessive density concrete is identical as that of regular concrete.
- Conventional approach of blending and setting is utilized in excessive density concrete. The maximum critical aspect is to save you overloading the mixer in particular whilst heavy weight aggregates inclusive of steels are used. Batch sizes have to be decreased to forty to 50% of the allowable mixer capacity. Also keep away from extra blending as it will bring about workability and bleeding of concrete.
- Preplaced mixture strategies may be followed whilst setting heavy weight concrete. In this approach the aggregates are located in forms , an appropriate grout made from cement, sand and water is pumped over the located aggregates, a good way to fill the voids in between the aggregates. This approach prevents the segregation of coarse aggregates additionally reduces drying shrinkage and facilitates us to attain concrete of uniform density and composition.
- Puddling approach also can be followed. In this approach, the mortar is located in varieties of 2″ thick and the coarse aggregates are located over it and vibrated internally. Care have to be taken that, the coarse aggregates are allotted evenly.
- Pumping of heavy weight concrete may be followed handiest the peak is limited. The heavy weight concrete can't be pumped to large distances due to their extra densities
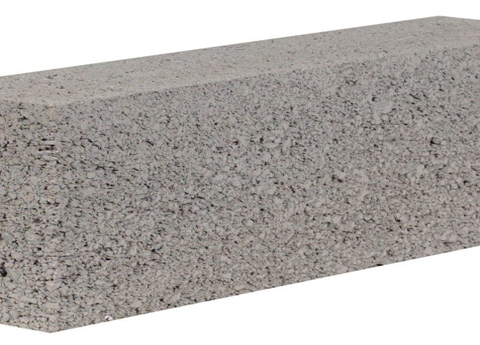
Fig no 35. High density concrete
Key takeaways
1. High density concrete is specifically used for the cause of radiation protective, for counterweights and different makes use of in which excessive density is required.
Fibre Reinforced Concrete, Geo Polymer Concrete and Ferrocement Technique
Fibre Reinforced Concrete
- Fibre Reinforced Concrete is a composite cloth which include fibrous cloth which will increase its structural integrity.
- It consists of combinations of cement, mortar or concrete and discontinuous, discrete, uniformly dispersed appropriate fibers.
- Fibers are normally utilized in concrete to govern cracking because of plastic shrinkage and to drying shrinkage.
- They additionally lessen the permeability of concrete and consequently lessen the bleeding of water.
Advantages of Fiber-strengthened concrete:
- Fibers strengthened concrete can be beneficial in which excessive tensile power and decreased cracking are proper or whilst traditional reinforcement cannot be placed.
- It improves the effect power of concrete, limits the crack boom and ends in a extra stress potential of the composite cloth.
- For commercial projects, macro-artificial fibers are used to enhance concrete’s sturdiness.
- Made from artificial substances, those fibers are lengthy and thick in length and can be used as a substitute for bar or material reinforcement.
- Adding fibers to the concrete will enhance its freeze-thaw resistance and assist maintain the concrete sturdy and appealing for prolonged periods.
- Improve blend cohesion, enhancing pumpability over lengthy distances.
- Increase resistance to plastic shrinkage in the course of curing.
- Minimizes metallic reinforcement requirements.
- Controls the crack widths tightly, consequently enhancing sturdiness.
- Reduces segregation and bleed-water.
- FRC, longevity is ready 10 to forty instances that of undeniable concrete.
- The addition of fibers will increase fatigue power.
- Fibers boom the shear potential of strengthened concrete beams.
Application of Fiber-strengthened concrete:
The programs of fiber strengthened concrete rely on the applicator and builder in taking gain of the static and dynamic traits of the cloth. Some of its vicinity of software is-
- Runway
- Aircraft Parking
- Pavements
- Tunnel Lining
- Slope Stabilization
- Thin Shell
- Walls
- Pipes
- Manholes
- Dams
- Hydraulic Structure
- Elevated decks
- Roads
- Bridges
- Warehouse floors
Fiber Types:
- Fibers for concrete are to be had in exclusive sizes and shapes.
- The essential elements affecting the function of fiber-strengthened concrete are a water-cement ratio, percent of fibers, diameter and duration of fibers.
- Given beneath are exclusive varieties of fiber-strengthened concrete utilized in production.
Steel Fiber Reinforced Concrete:
- Steel fiber is a metallic reinforcement. A sure quantity of metallic fiber in concrete can motive qualitative modifications in concrete’s bodily property.
- It can significantly boom resistance to cracking, effect, fatigue, and bending, tenacity, sturdiness, and others.
- For enhancing lengthy-time period behavior, improving power, longevity, and strain resistance, SFRC is being utilized in systems which includes flooring, housing, precast, bridges, tunneling, heavy-responsibility pavement, and mining.
- The varieties of metallic fibers are described via way of means of ASTM A820 are, Type I: cold-drawn cord, Type II; reduce sheet, Type III: melt-extracted, Type IV: mill reduce and Type V: changed cold-drawn cord
Polypropylene Fiber Reinforced (PFR) Concrete:
- Polypropylene fiber strengthened concrete is likewise referred to as poly propene or PP.
- It is a artificial fiber, converted from propylene, and utilized in loads of programs.
- These fibers are normally utilized in concrete to govern cracking because of plastic shrinkage and drying shrinkage.
- They additionally lessen the permeability of concrete and consequently lessen the bleeding of water.
- Polypropylene fiber belongs to the institution of polyolefins and is partly crystalline and non-polar.
- It has comparable homes as poly ethylene, however it's far tougher and greater warmth resistant.
- It is a white rugged cloth with excessive chemical resistance.
- Polypropylene is made from propylene fuel with inside the presence of a catalyst which includes titanium chloride.
- Polypropylene fiber shows accurate warmth-insulating homes and is especially immune to acids, alkali, and natural solvents.
Glass Fiber Reinforced Concrete:
- Glass fiber strengthened concrete is a cloth which include severa extraordinarily first-rate fibers of glass.
- Glass fiber has kind of similar mechanical homes to different fibers which includes polymers and carbon fiber.
- Although now no longer as inflexible as carbon fiber, it's far tons less expensive and notably much less brittle whilst utilized in composites.
- Glass fibers are consequently used as a reinforcing agent for lots polymer merchandise; to shape a totally sturdy and comparatively light-weight fiber-strengthened polymer (FRP) composite cloth known as glass-strengthened plastic (GRP), additionally popularly referred to as “fiberglass”.
- This cloth incorporates very little air or fuel line, is denser, and is a miles poorer thermal insulator than is glass wool.
Polyester fibers:
- Polyester fibers are utilized in fiber-strengthened concrete for commercial and warehouse floors, pavements and overlays and precast merchandise.
- Polyester micro- and macro-fibers are utilized in concrete to offer advanced resistance to the formation of plastic shrinkage cracks as opposed to welded cord material and to decorate longevity and the capacity to supply structural potential whilst well designed, respectively.
- Polyester micro- and macro-fibers are utilized in concrete to offer advanced resistance to the formation of plastic shrinkage cracks as opposed to welded cord material and to decorate longevity and the capacity to supply structural potential whilst well designed, respectively.
Carbon fibers:
- Carbon fibers are fibers approximately 5–10 micrometers in diameter and composed in general of carbon atoms.
- Carbon fibers have numerous benefits such as excessive stiffness, excessive tensile power, low weight, excessive chemical resistance, excessive-temperature tolerance and coffee thermal expansion.
- Carbon fibers are normally mixed with different substances to shape a composite.
- When impregnated with a plastic resin and baked it bureaucracy carbon-fiber-strengthened polymer (frequently known as carbon fiber) which has a totally excessive power-to-weight ratio, and is extraordinarily inflexible even though particularly brittle.
- Carbon fibers also are composited with different substances, which includes graphite, to shape strengthened carbon composites, that have a totally excessive warmth tolerance.
Macro artificial fibers:
- Macro artificial fibers are crafted from a mix of polymers and have been at the beginning advanced to offer an opportunity to metallic fibers in a few programs.
- Initially, they have been diagnosed as a ability opportunity to metallic fibers in sprayed concrete, however growing studies and improvement confirmed that that they'd a function to play withinside the layout and production of ground-supported slabs and a huge variety of different programs.
- They are specifically appropriate for presenting nominal reinforcement in competitive environments, which includes marine and coastal systems, as they do now no longer go through the troubles of staining and spalling which could end result from the corrosion of metallic.
- Besides, due to the fact they may be non-conducting, they had been utilized in tram and mild railway developments.
Micro-artificial fibers:
- Micro-artificial fibers offer advanced resistance to the formation of plastic shrinkage cracks as opposed to welded cord reinforcement, they may be not able to offer any resistance to similarly crack width openings due to drying shrinkage, structural load or different sorts of strain.
- However, those merchandise need to be frequently laid out in any form of concrete to enhance cracking resistance, spall protection, freeze-thaw sturdiness and enhance the homogeneity of concrete in the course of placement.
Natural fibers:
- The herbal fiber is without delay available from an animal, vegetable, or mineral supply and convertible into nonwoven fabric which includes felt or paper or, after spinning into yarns, into woven cloth.
- A herbal fiber can be similarly described as an agglomeration of cells wherein the diameter is negligible in evaluation with the duration.
- Although nature abounds in fibrous substances, in particular cellulosic kinds which includes cotton, wooden, grains, and straw.
- The use of herbal fibers in making concrete is usually recommended in view that numerous varieties of those fibers are to be had domestically and are plentiful.
- The concept of the use of such fibers to enhance the power and sturdiness of brittle substances isn't new; for example, straw and horsehair are used to make bricks and plaster.
- Natural fibers are appropriate for boosting concrete and are without difficulty to be had in growing countries.
Cellulose fibers:
- Cellulose fibers are made with ethers or esters of cellulose, which may be acquired from the bark, wooden or leaves of plants, or different plant-primarily based totally cloth.
- In addition to cellulose, the fibers may comprise hemi cellulose and lignin, with exclusive possibilities of those additives changing the mechanical homes of the fibers.
- The predominant programs of cellulose fibers are with inside the fabric industry, as chemical filters, and as fiber-reinforcement composites, because of their comparable homes to engineered fibers, being every other alternative for bio composites and polymer composites.
Geo Polymer Concrete
- Geo polymer is the name given to the Daidovits in 1978 for items that appear in chains or networks or unusual molecules.
- Geopolymer cement concrete is made using waste materials such as fly ash and ground granulated blast furnace slag (GGBS). An ash fly is a waste product produced from a hot power plant and the granulate blast soil in a furnace is processed as a metal waste.
- Both fly ash and GGBS are processed by appropriate technology and applied to concrete operations in the form of a geo polymer concrete. The use of this concrete helps to reduce waste stocks and reduces carbon emissions by reducing demand for Portland cement.
- A key feature of the geo polymers source of silicon and aluminum is supplied by natural thermal agents (e.g. kaolinite) or industrial products (e.g. Fly ash or slab) and an alkaline solution that makes these materials chains and networks to create strong bond. Also called alkaline cement or inorganic polymer cement.
Composition of Geo polymer Concrete
The following materials are required to produce this concrete:
- Fly ash - Fly ash generator
- GGBS - Metal Product
- Good collection and heat collection as required for standard concrete.
- GPCC alkaline activator solution as described above. The Catalytic liquid system is used as an alkaline activator solution. It is a combination of alkali silicates and hydroxide solutions, in addition to pure water. The role of the alkaline activator solution is to activate geopolymeric resource sources containing Si and Al such as fly ash and GGBS.
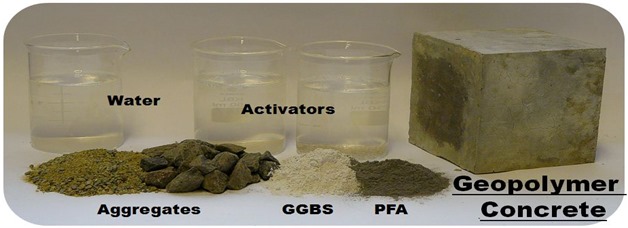
Fig no 36. Geo polymer Concrete Materials
Mechanical properties of Geo polymer Concrete
- Geo polymer concrete pressures were obtained up to 70 MP a (N / mm2). Concrete gains its compression strength much faster and faster than conventional Portland concrete.
- Concrete strength after 24 hours was found to be more than 25 M Pa. Pressure capacity after 28 days was found to be 60 to 70 M Pa. -Ref. Paper by James Aldred and John Day and test results by SERC Chennai.
Other properties of Geo polymer Concrete:
- The reduction in dryness is very small compared to cemen. This makes it ideal for members of a dense and highly restricted concrete structure.
- It has a lower hydration temperature compared to cement.
- Fire resistance is much better than OPC-based concrete. -Reference - Paper by - James Aldred and John Day.
- This concrete measure of jas chloride permeability is 'low' to 'very low' according to ASTM 1202C. It provides better protection of metal reinforcement from corrosion compared to traditional cement mortar.
- This concrete is found to have a very high acid content when tested under 2% and 10% exposure to sulfuric acid.
Application of Geo polymer Concrete
- Applications are similar to cement cement. However, the subject has not been used extensively in various programs.
- This concrete is used for the construction of paved stones, retaining walls, water tanks, precast bridge supplies.
- Recently the world's first building to be built on earth, the University of Queensland's Global Change Institute (GCI) was built using geo polymer concrete. It is a four-story high-rise building for public use.
Ferro Cement Technique
- Mining
- Crushing, stacking, and reclaiming of uncooked substances.
- Raw meal drying, grinding, and homogenization.
- Clinkerization.
- Cement grinding and garage.
- Packing
Mining:
- The cement production system begins off evolved from the mining of uncooked substances which might be utilized in cement production, specially limestone and clays.
- A limestone quarry is with inside the plant region and a clays quarry is as a ways from the plant region as 25 km.
- The limestone is excavated from open forged mines after drilling and blasting and loaded onto dumpers which shipping the substances and sell off into hoppers of limestone crushers.
- The clays are excavated from open forged mines and loaded onto dumpers which shipping the substances and sell off into open backyard garage.
- Then it's miles transported through vehicles and unloaded into the hopper of a clay crusher.
- They are 3 varieties of clay utilized in cement production, specifically silty clay, Zafarana clay, and Kaolin.
- Other uncooked substances are used to govern the kiln feed blend design, specifically sand, and iron ore.
- The sand and iron ore are shipping from outdoor the plant (from extraordinary suppliers) through vehicles and unloaded into open backyard piles, known as sand and iron ore piles.
Crushing, stacking, and reclaiming of uncooked substances:
- The limestone is beaten with inside the first crusher known as a jaw crusher after which fed into the second one crusher known as an effect crusher with blending of clays to lessen particle length beneath 50mm.
- The discharged uncooked blend (limestone 70%, clays 30%) is fed onto a belt conveyor and exceeded throughout a bulk fabric analyzer.
- The uncooked blend is fed right into a round garage unit known as a uncooked blend garage.
- Then, the combination is extracted transversely from the stockpile through reclaimers and conveyed to a uncooked mill bin known as the uncooked blend bin for grinding.
- The different uncooked substances which might be utilized in cement production, known as additives, are excessive purity limestone, sand and iron ore.
- The excessive purity limestone is beaten in a lone in jaw crusher after which beaten extra in a secondary crusher to lessen the scale to absolutely byskip via a 50mm sieve.
- Then, it's miles stacked through a limestone stacker right into a longitudinal garage unit known as the limestone garage stockpile.
- Finally, the limestone is extracted transversely from the stockpile through reclaimer and conveyed to a uncooked mill bin, known as the limestone bin, for grinding.
Raw meal drying, grinding, and homogenization:
- The uncooked blend, excessive grade limestone, sand, and iron ore are fed from their containers to uncooked turbines, known as air swept turbines, for drying and pleasant grinding.
- The uncooked mill includes chambers, separated through diaphragm, specifically a drying chamber and a grinding chamber.
- The warm gases coming from a pre heater (pre heater / kiln machine) input the mill and are utilized in uncooked turbines for drying.
- Then the drying substances input the grinding chamber of uncooked turbines for pleasant grinding.
- The grinding chamber includes a positive amount of ball price in a extraordinary sizes starting from 30mm to 90mm.
- The warm fuel line and grinding substances mill outlet feeds to a separator which separates pleasant and path product.
- The latter, known as reject, is dispatched to the mill inlet thru an air slide for regrinding.
- The warm fuel line and pleasant substances input a multistage "cyclone" to split a pleasant substances and gases.
- The pleasant fabric, known as uncooked meal, is accrued from the multi-cyclone after which fed into an air slide for lifting known as an Aeropol.
- The warm gases with very pleasant substances input an electrostatic precipitator to split the pleasant substances from gases.
- The very pleasant substances known as pre heater dirt or electrostatic separator dirt is accrued from filters and fed into screw conveyors and are then combined with the pleasant fabric in an air slide and transported to an air elevate vessel thru air slide.
- In the air elevate, the uncooked meal is lifted to the silo through compressed air to the air slide after which saved and homogenized in a concrete silo.
- Raw meal extracted from the silo, now known as kiln feed, is fed to the pinnacle of the pre heater thru an air elevate known as the Poldos for pyro-processing.
Clinkerization:
- Cement clinker is made through pyro processing of kiln feed into the pre heater-kiln machine. The pre-heater-kiln machine includes a multi-degree cyclone
- Pre heater with 5 stages, combustion chamber, riser duct, rotary kiln, and grate cooler.
- In the pre heater, the kiln feed is preheated through warm fuel line coming from the combustion chamber and rotary kiln.
- Then the preheated kiln feed is partly calcined (made powdery) in a combustion chamber and riser duct after which absolutely calcined in a rotary kiln in addition to heated to about 1400 C to shape clinker additives C3A, C4AF, C2S, and C3S.
- The foremost supply of warmth is herbal fuel line.
- Natural fuel line is fired as a major gasoline (100 %) with inside the foremost burner rotary kiln and a 95% herbal fuel line and 5.0% heavy oil aggregate with inside the combustion chamber.
- The gasoline is used to offer the warmth required to transform the kiln feed into clinker.
- Hot clinker discharge from the kiln drops onto the grate cooler for cooling from about 1350-1450 C to about one hundred twenty C.
- In the cooler, the amount of cooling air required for clinker cooling is extracted from the environment through extraordinary cooling lovers and fed into the cooler chambers and pressurized via the cooler plate and clinker bed.
- The cooled clinker discharges from the cooler into the pan conveyor and it's miles transported to the clinker garage.
- The clinker is taken from the clinker garage to cement ball mill hoppers for cement grinding.
- Part of the recent air extracted from the cooler is applied as a secondary and tertiary air for combustion in rotary kiln and combustion chamber, respectively.
Cement grinding and garage:
- Clinker and gypsum for OPC, limestone for limestone cement, and slag for slag cement are all extracted from their respective hoppers and fed to the cement turbines.
- The ball mill grinds the feed to a pleasant powder in chambers, specifically the primary and 2d chambers.
- The chambers have a positive amount of ball price of various sizes from 17mm to ninety mm.
- The mill discharge is fed to a bucket elevator which takes the fabric to a separator which separates pleasant and coarse product.
- The latter is dispatched to the mill inlet for regrinding and the very last product is saved in concrete silos.
Packing:
- Cement extracted from silos is conveyed to the automated digital packers wherein it's miles packed in 50 kg luggage and dispatched in vehicles.
Key takeaways
1. Fibers strengthened concrete can be beneficial in which excessive tensile power and decreased cracking are proper or whilst traditional reinforcement can not be placed.
2. The clays are excavated from open forged mines and loaded onto dumpers which shipping the substances and sell off into open backyard garage.
3. Geo polymer is the name given to the Daidovits in 1978 for items that appear in chains or networks or unusual molecules.
4. Geo polymer cement concrete is made using waste materials such as fly ash and ground granulated blast furnace slag (GGBS). An ash fly is a waste product produced from a hot power plant and the granulate blast soil in a furnace is processed as a metal waste.
Fiber Reinforced concrete:
- Fiber Reinforced Concrete is composite cloth which include fibrous cloth which will increase its structural integrity.
- It consists of combinations of cement, mortar or concrete and discontinuous, discrete, uniformly dispersed appropriate fibers.
- Fibers are normally utilized in concrete to govern cracking because of plastic shrinkage and to drying shrinkage.
- They additionally lessen the permeability of concrete and consequently lessen the bleeding of water.
Advantages of Fiber-strengthened concrete:
- Fibers strengthened concrete can be beneficial in which excessive tensile power and decreased cracking are proper or whilst traditional reinforcement cannot be placed.
- It improves the effect power of concrete, limits the crack boom and ends in a extra stress potential of the composite cloth.
- For commercial projects, macro-artificial fibers are used to enhance concrete’s sturdiness.
- Made from artificial substances, those fibers are lengthy and thick in length and can be used as a substitute for bar or material reinforcement.
- Adding fibers to the concrete will enhance its freeze-thaw resistance and assist maintain the concrete sturdy and appealing for prolonged periods.
- Improve blend cohesion, enhancing pump ability over lengthy distances.
- Increase resistance to plastic shrinkage in the course of curing.
- Minimizes metallic reinforcement requirements.
- Controls the crack widths tightly, consequently enhancing sturdiness.
- Reduces segregation and bleed-water.
- FRC, longevity is ready 10 to forty instances that of undeniable concrete.
- The addition of fibers will increase fatigue power.
- Fibers boom the shear potential of strengthened concrete beams.
Application of Fiber-strengthened concrete:
The programs of fiber strengthened concrete rely on the applicator and builder in taking gain of the static and dynamic traits of the cloth. Some of its vicinity of software is-
- Runway
- Aircraft Parking
- Pavements
- Tunnel Lining
- Slope Stabilization
- Thin Shell
- Walls
- Pipes
- Manholes
- Dams
- Hydraulic Structure
- Elevated decks
- Roads
- Bridges
- Warehouse floors
Fiber Types:
Fibers for concrete are to be had in exclusive sizes and shapes.
The essential elements affecting the function of fiber-strengthened concrete are a water-cement ratio, percent of fibers, diameter and duration of fibers.
Given beneath are exclusive varieties of fiber-strengthened concrete utilized in production.
Steel Fiber Reinforced Concrete:
- Steel fiber is a metallic reinforcement. A sure quantity of metallic fiber in concrete can motive qualitative modifications in concrete’s bodily property.
- It can significantly boom resistance to cracking, effect, fatigue, and bending, tenacity, sturdiness, and others.
- For enhancing lengthy-time period behavior, improving power, longevity, and strain resistance, SFRC is being utilized in systems which includes flooring, housing, precast, bridges, tunneling, heavy-responsibility pavement, and mining.
- The varieties of metallic fibers are described via way of means of ASTM A820 are, Type I: cold-drawn cord, Type II; reduce sheet, Type III: melt-extracted, Type IV: mill reduce and Type V: changed cold-drawn cord
Properties of Fiber Reinforced Concrete:
Compressive Strength:
- The presence of fibers might also additionally regulate the failure mode of cylinders; however, the fiber impact can be minor at the development of compressive power values (zero to fifteen percentage).
Modulus of Elasticity:
- Modulus of elasticity of FRC will increase slightly with a boom with inside the fibers content material.
- It became located that for every 1 percentage boom in fiber content material through quantity there may be a boom of three percentage withinside the modulus of elasticity.
Flexure:
- The flexural power became said [2j to be improved through 2. Five instances the usage of four percentage fibers.
Toughness:
- For FRC, sturdiness is set 10 to forty instances that of undeniable concrete.
Splitting Tensile Strength:
- The presence of three percentage fiber through quantity became said to boom the splitting tensile power of mortar approximately 2.5 instances that of the unreinforced one.
Fatigue Strength:
- The addition off bers will increase fatigue power of approximately ninety percentage and 70 percentage of the static power at 2 x 106 cycles for non-opposite and complete reversal of loading, respectively.
Impact Resistance:
- The effect power for fibrous concrete is typically five to ten instances that of undeniable concrete relying at the quantity of fiber
Corrosion of Steel Fibers:
- A lO-12 months’ publicity of steel fibrous mortar to out of doors weathering in an commercial surroundings confirmed no unfavourable impact at the power properties.
- Corrosion became located to be restricted best to fibers virtually uncovered at the surface.
- Steel fibrous mortar constantly immerse in seawater for 10 years exhibited a fifteen-percentage loss in comparison to forty percentage power lower of undeniable mortar.
Flexure:
- The use of fibers in bolstered concrete flexure contributors will increase ductility, tensile power, second ability, and stiffness.
- The fibers enhance crack manage and keep publish cracking structural integrity of contributors.
Torsion:
- The use of fiber do away with the unexpected failure feature of undeniable concrete beams.
- It will increase stiffness, torsion power, ductility, rotational ability, and the range of cracks with much less crack width.
Shear:
- Addition of fibers will increase shear ability of bolstered concrete beams as much as a hundred percentage.
- Addition of randomly allotted fibers will increase shear-friction power, the primary crack power, and final power.
Polymer concrete is an alternative to portland cement that is used to bond a mixture of aggregates together with epoxy binders. It is used in construction projects to provide added strength and can be modified with a range of resins. Polymer concrete provides very good resistance against corrosion and minimal chemical reactivity.
A polyester, vinyl resin or epoxy resin is often used to manufacture polymer concrete. This allows the concrete to be poured, then hardened. Polymer concrete cures through a chemical reaction with the polymer material. This type concrete is ideal for reaching areas that are not easily accessible.
Polymer concrete offers a range of benefits depending on the resin used to make it. Acrylic resins set quickly and offer resistance to harsh weather conditions, while epoxies create a strong material with little curing shrinkage. Furan resins can withstand high temperatures, and polyurea resins can replace formaldehydes or other hazardous compounds for construction purposes.
- Chemical admixtures are the components in concrete aside from port land cement, water, and combination which might be introduced to the combination at once earlier than or for the duration of blending.
- Producers use admixtures generally to lessen the value of concrete construction; to adjust the residences of hardened concrete; to make sure the best of concrete for the duration of blending, transporting, setting, and curing; and to conquer sure emergencies for the duration of concrete operations.
- Successful use of admixtures relies upon on using suitable techniques of batching and concreting.
- Most admixtures are provided in ready-to-use liquid shape and are introduced to the concrete on the plant or on the jobsite.
- Certain admixtures, along with pigments, expansive agents, and pumping aids are used most effective in extraordinarily small quantities and are commonly batched with the aid of using hand from premeasured containers.
- The effectiveness of an admixture relies upon on numerous elements including: kind and quantity of cement, water content material, blending time, stoop, and temperatures of the concrete and air.
- Sometimes, results much like the ones done thru the addition of admixtures may be done with the aid of using changing the concrete aggregate-decreasing the water-cement ratio, including extra cement, the usage of a extraordinary sort of cement, or converting the combination and combination gradation.
- Admixtures are classed consistent with characteristic. There are 5 wonderful lessons of chemical admixtures: air-entraining, water-decreasing, retarding, accelerating, and plasticizers (super plasticizers).
- All different styles of admixtures fall into the strong point class whose capabilities encompass corrosion inhibition, shrinkage reduction, alkali-silica reactivity reduction, workability enhancement, bonding, damp proofing, and coloring.
- Air-entraining admixtures, which can be used to purposely location microscopic air bubbles into the concrete, are mentioned extra completely in Air-Entrained Concrete.
- Water-decreasing admixtures commonly lessen the desired water content material for a concrete aggregate with the aid of using approximately five to ten percentage .
- Consequently, concrete containing a water-decreasing admixture wishes much less water to attain a required stoop than untreated concrete.
- The dealt with concrete could have a decrease water-cement ratio. This commonly shows that a better energy concrete may be produced without growing the quantity of cement.
- Recent improvements in admixture generation have caused the improvement of mid-variety water reducers.
- These admixtures lessen water content material with the aid of using as a minimum eight percentage and have a tendency to be extra solid over a much broader variety of temperatures.
- Mid-variety water reducers offer extra regular placing instances than popular water reducers.
- Retarding admixtures, which gradual the placing charge of concrete, are used to counteract the accelerating impact of warm climate on concrete placing.
- High temperatures frequently reason an accelerated charge of hardening which makes setting and completing difficult.
- Retarders maintain concrete manageable for the duration of placement and put off the preliminary set of concrete.
- Most retarders additionally characteristic as water reducers and can entrain a few air in concrete.
- Accelerating admixtures growth the charge of early energy improvement, lessen the time required for correct curing and protection, and accelerate the begin of completing operations.
- Accelerating admixtures are specifically beneficial for enhancing the residences of concrete in bloodless climate.
- Super plasticizers, additionally called plasticizers or excessive-variety water reducers (HRWR), lessen water content material with the aid of using 12 to 30 percentage and may be introduced to concrete with a low-to-ordinary stoop and water-cement ratio to make excessive-stoop flowing concrete.
- Flowing concrete is a extraordinarily fluid however manageable concrete that may be located with very little vibration or compaction.
- The impact of super plasticizers lasts most effective 30 to 60 minutes, relying at the emblem and dosage charge, and is observed with the aid of using a speedy loss in workability.
- As a end result of the stoop loss, super plasticizers are commonly introduced to concrete on the jobsite.
- Corrosion-inhibiting admixtures fall into the strong point admixture class and are used to gradual corrosion of reinforcing metal in concrete.
- Corrosion inhibitors may be used as a shielding method for concrete structures, along with marine facilities, motorway bridges, and parking garages, in order to be uncovered to excessive concentrations of chloride.
- Other strong point admixtures encompass shrinkage-decreasing admixtures and alkali-silica reactivity inhibitors.
- The shrinkage reducers are used to govern drying shrinkage and reduce cracking, even as ASR inhibitors manipulate sturdiness troubles related to alkali-silica reactivity.
Mechanism of Chemical Admixture:
- Concrete admixtures are used to steer concrete hardening specially with inside the early Phase of hydration.
- By including very small quantities of admixtures, homes of sparkling concrete may be inspired in a huge range.
- The hydraulic response may be elevated or retarded the use of suitable dealers and workability may be advanced the use of super plasticizers.
- Many mechanisms had been cautioned to provide an explanation for these kinds of effects .
- There continues to be no complete know-how of hydration mechanisms together with these kinds of phenomena at once.
- In this contribution emphasis will be positioned at power differences occuring at some point of physico-chemical methods of cement hydration.
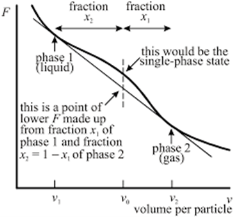
Fig no 37. Mechanisms of plasticiser
- Cement hydration evolves in a manner which in corporate segment transitions.
- In touch with water, Meta stable stable cement stages dissolve into an aqueous solution.
- This dissociation ends in an boom of Ca O attention as much as 20-forty m mol/I with inside the first hours of C3S hydration .
- Reaching a country of super saturation with inside the pore water solution, crystallization into strong and stable CSH-merchandise can follow.
- In each segment transitions a unexpected quantity extrade occurs, as a consequence of adjustments in sure forces.
- During the solvation procedure a stable-fluid section transition results in an boom in quantity (swelling).
- Crystallization entails a quantity contraction (shrinkage) that is better in absolute phrases than the preceding quantity swelling.
- A shrinkage quantity stays after fluid-stable transition and may be measured volumetrically or gravimetrically.
- Both tactics engage simultaneously, however with unique velocities.
- Hydration may be visible as a solvation-crystallization step and become first defined via way of means of Le Chatelier.
Key takeaways
- Super plasticizers, additionally called plasticizers or excessive-variety water reducers (HRWR), lessen water content material with the aid of using 12 to 30 percentage and may be introduced to concrete with a low-to-ordinary stoop and water-cement ratio to make excessive-stoop flowing concrete.
- During the solvation procedure a stable-fluid section transition results in an boom in quantity (swelling).
Deterioration - Durability
- Durability is the capacity to remaining a long term without massive deterioration.
- A long lasting cloth allows the surroundings with the aid of using keeping sources and lowering wastes and the environmental affect of restore and substitute.
- The manufacturing of substitute constructing substances depletes herbal sources and may produce air and water pollution.
- Concrete resists weathering action, chemical attack, and abrasion even as retaining its favored engineering houses.
- Different concretes require extraordinary levels of sturdiness relying at the publicity surroundings and the houses favored.
- Concrete ingredients, their proportioning, interactions among them, setting and curing practices, and the provider surroundings decide the remaining sturdiness and lifestyles of the concrete.
- The layout provider lifestyles of maximum homes regularly 30 years, despite the fact that homes regularly remaining 50 to one hundred years or longer.
- Because in their sturdiness, maximum concrete and masonry homes are demolished because of useful obsolescence in place of deterioration.
- However, a concrete shell or shape may be repurposed if a constructing use or characteristic adjustments or whilst a constructing indoors is renovated.
- Concrete, as a structural cloth and because the constructing outside skin, has the capacity to face up to nature’s ordinary deteriorating mechanisms in addition to herbal disasters.
- Durability of concrete can be described because the capacity of concrete to withstand weathering action, chemical attack, and abrasion even as retaining its favored engineering houses.
- Different concretes require extraordinary levels of sturdiness relying at the publicity surroundings and houses favored.
- For example, concrete uncovered to tidal seawater could have extraordinary necessities than an indoor concrete floor.
Key takeaways
- Durability is the capacity to remaining a long term without massive deterioration.
- A long lasting cloth allows the surroundings with the aid of using keeping sources and lowering wastes and the environmental affect of restore and substitute.
Factor affecting the durability of concrete
The following are the factors that affect the strength of concrete.
- Cement content
- Aggregate quality
- Water Quality
- Concrete compaction
- Curing period
- Permeability
- Moisture
- Temperature
- Abrasion
- Carbonation
01. Cement content
- The amount of cement used in concrete mixing is a major factor affecting the durability of concrete.
- If the cement content used is less than required, the cement water level
- Decreases and the performance of concrete also decreases.
- Adding too much water to this concrete mix causes the formation of capillary voids that will make the concrete a resilient one inviting decay.
- Adding excess cement can cause problems such as stopping the shrinkage. Alkali-silica reactions may also eventually affect the strength of the concrete.
02. Aggregate Quality
- Applying a good quality mix to the concrete mix will definitely increase the strength of the concrete.
- The shape of the composite particles should be small and circular. Flaky and compact assembly can affect the performance of the new concrete making it easier to enter where it can open and will work with less power.
- Bad angular compilation is recommended but requires a lot of cement content to get a good binding. Yes, structural composites should be used to achieve greater concrete mixing.
- Determination of the combined moisture content should be done beforehand, otherwise, it can create a more usable concrete mix and make it worse.
03. Water Quality
- The water used in the concrete mix also affects the strength of the concrete. Usually, drinking water is recommended to make concrete. The pH of the water used will be in grades 7 to 8 only.
- Water should be free and clean from fats, acids, alkalis, sugar, organic salts etc.
- Contamination in the water can lead to metal corrosion or corrosion due to different chemical attacks of concrete.
04. Concrete compaction
- Care should be taken during the installation of the concrete. It is important to glue the local concrete without splitting.
- Adequately compacted concrete contains a number of air gaps in it that reduce the strength of the concrete and its strength and will make it stronger.
05. Curing period
- Proper treatment should be done in the early stages of concrete reinforcement as it will lead to the reinforcement of the concrete.
- Adequate treatment can lead to the formation of cracks due to plastic shrinkage, dehydration, heat effects etc. due to reduced stiffness.
06. Permeability
- Due to the overcrowding of the concrete, it expands and leads to the formation of cracks and eventually, the deterioration of the concrete occurs.
- Concrete usually consists of small gel pores and capillary cavities. However, gel pores prevent water ingress because they are too small.
- Capillary holes in concrete are facing, which are formed due to the high water content of concrete
- To prevent intrusion, a very small amount of cement water should be used.
- Using a small amount of pozzolanic material also helps to reduce penetration
07. Moisture
- The moisture found in the atmosphere will also affect the strength of concrete structures.
- Concrete moisture is responsible for Efflorescence, which will convert salt into soluble solutions and when evaporated salt becomes brighter and appears on the concrete surface.
- This will definitely damage the concrete structure and the durability will decrease.
08. Temperature
- When new concrete is exposed to high temperatures, the hydration level is affected and strength and durability are reduced.
- Concrete materials have different temperature coefficients, so at higher temperatures, spelling and damage to concrete are possible.
09. Abrasion
- Concrete damage also occurs due to severe facial injuries.
- When concrete is exposed to fast-moving water, steel tires, floating ice that wears continuously on the surface occur and stiffness is affected.
- The higher the pressure of the concrete pressure the higher it will be to resist the abrasion
10. Carbonation
- When wet concrete is exposed to the atmosphere, carbon dioxide in the atmosphere reacts with concrete and reduces the pH of the concrete by reacting with CaO in concrete.
- When the pH value of concrete is reduced to 10 or 9 or more, it releases its alkali. Because it will not be able to protect the metal bars beneath it. Due to rust, rust will build up around the bar which has led to an increase in the volume of the bar. This will create cracks in the concrete. Cracking will continue to promote moisture and CO2 which will lead to the loss of alkali. So bad cycles occur, eventually causing the concrete to crack with delamination and spraying of the concrete if not done in time, the bars will start to lose their place and thus become stronger. Most of the building in modern times, suffers from this, and buildings that were supposed to be 100 years old have been extensively renovated at some point within ten years. The process of rust therefore places on the existing strength of the concrete. The rust of the reinforcement causes cracks in the solid concrete and deterioration occurs.
Key takeaways
The following are the factors that affect the strength of concrete.
- Cement content
- Aggregate quality
- Water Quality
- Concrete compaction
- Curing period
- Permeability
- Moisture
- Temperature
- Abrasion
- Carbonation
Permeability
- Definition: the capacity of a given concrete to allow drinks or gases to by skip through.- ACI Concrete Terminology
- Permeability is a degree of the quantity of water, air, and different materials which could input the concrete matrix.
- Concrete consists of pores which could permit those materials to go into or depart.
- Permeability of concrete may be a number one motive for concrete deterioration because of reinforcing metal corrosion and different deterioration mechanisms.
- On a macro scale, permeability additionally refers to “porous” slabs used to empty pavements, sidewalks, and parking regions of water, putting off the want for drainage slope, systems, and piping.
- This technology—every now and then called “no-fines concrete”—is gaining reputation once more with the preference to lessen floor run-off from pavements, sidewalks, and parking regions.
- Permeability of cement mortar or concrete is of unique importance in systems which might be meant to hold water or which come into touch with water.
- Besides useful considerations, permeability is likewise in detail associated with the sturdiness of concrete, mainly its resistance, towards revolutionary deterioration below publicity to extreme climate, and leaching because of extended seepage of water, specially whilst it consists of competitive gases or minerals in solution.
- The willpower of the permeability traits of mortar and concrete, therefore, assumes widespread importance.
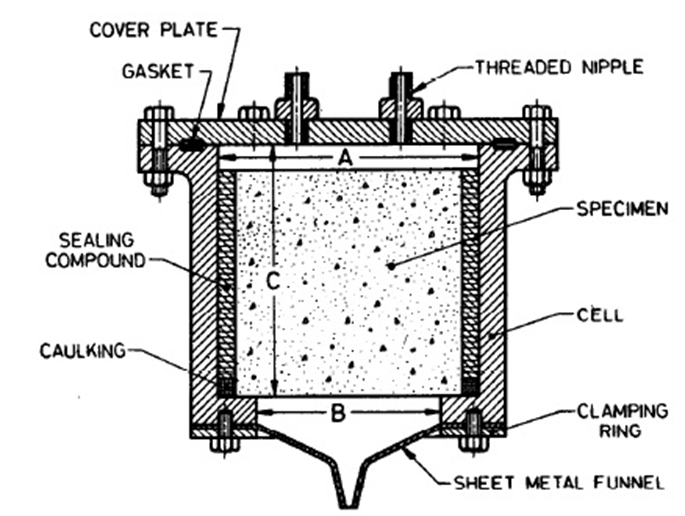
Fig no 38. Concrete permeability apparatus
- The permeability shall encompass a steel cylinder for containing the specimen.
- A rubber or neoprene O-ring or different appropriate gasket, seated in matching grooves will be used among the quilt plate to render the joint water-tight.
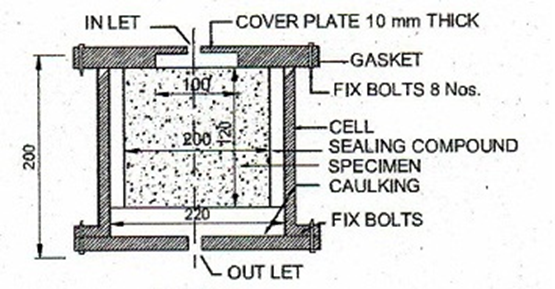
Fig no 39. Water Reservoir in Permeability Apparatus
- A appropriate reservoir may also encompass a duration of steel pipe, 50 to a hundred mm in diameter and approximately 500 mm long.
- The reservoir will be equipped with a graduated facet arm gauge-glass, and the vital fittings and valves for admitting water and compressed air and for draining, bleeding and connection to the permeability.
Procedure:
Preparation of Test Specimen
- Test specimen of 2 hundred mm diameter and a hundred and twenty mm thick will be used. After 24 hrs of casting of specimen, crucial round place of a hundred mm diameter will be roughened with a twine brush at the facet on which the water stress is to be carried out. The un roughened a part of the facet of the check specimen that's subjected to water stress is to be sealed with coats of cement water paste (W/C = 0.4).
Test Procedure
- After 28 days curing, check specimen is equipped right into a check equipment in which the water stress acts on the specified face and final faces may be observed.
- At first, a stress of one Bar is carried out for forty eight hours, then three bar for twenty-four hours and seven Bar for twenty-four hours.
- After the check, the specimen is break up with inside the center with the aid of using the compression carried out on spherical metal bars mendacity on contrary sides, above and below. The facet after the check specimen uncovered to the water stress ought to face downwards.
Observation:
- The finest water penetration depth, is taken because the common cost of the finest penetration depths on 3 check specimen.
Key takeaways
1. A rubber or neoprene O-ring or different appropriate gasket, seated in matching grooves will be used among the quilt plate to render the joint water-tight.
Chloride Attack
- Chloride Attack Chloride attack is one of the most important factors when working with concrete strength. It mainly causes corrosion. Statistics have shown that more than 40% of structural failures are due to metal corrosion.
- Concrete and the penetration layer with a strong alkaline Ca (OH) 2 (pH approximately 13) prevents metal corrosion by forming a thin film to protect the iron oxide on the surface of the metal.
- This protection is known as inaction. If concrete can penetrate in such a way that the dissolved chloride enters until it hardens and water and oxygen are also present, then corrosion of the metal will occur. This layer can also be lost due to carbonation.
- Chloride enters the concrete from cement, water, and is sometimes mixed from tips. This can come in increments from nature when the concrete is filled. The Bureau of Indian Standard specified the high chloride content in cement as 0.1%.
- The amount of chloride needed to start corrosion depends on the pH value of the pore water in the concrete. A pH value below11.5 corrosion is possible without the presence of chloride.
Key takeaways
- Chloride Attack Chloride attack is one of the most important factors when working with concrete strength. It mainly causes corrosion corrosion. Statistics have shown that more than 40% of structural failures are due to metal corrosion.
- Concrete and the penetration layer with a strong alkaline Ca (OH) 2 (pH approximately 13) prevents metal corrosion by forming a thin film to protect the iron oxide on the surface of the metal.
Corrosion of Reinforcement, Carbonation of Concrete
Corrosion of Reinforcement
- Concrete, in itself, has a low strength. To increase the strength of the concrete, the steel hardens. Steel bars are inserted inside the weight of the concrete. These steel bearings carry a high load-bearing capacity applied to concrete.
- Concrete makes metal bars obsolete due to the alkaline environment, thus preventing them from cracking. However, for a variety of reasons, metal bars can be pulled longer. And as a result of the rust of the steel bars, various weaknesses appear in the concrete structure, which could eventually collapse if not properly maintained.
- The rust of steel reinforcement bars is actually a way of responding to electricity. Small anodes and cathodes are formed and the flow of ions between these two electrodes leads to the breakdown of metal bars. There are two types of corrosion detected in steel reinforcement bars:
- Metal Rust - In small cracks in a concrete structure, solutions may remain. Anodes and cathodes can be formed within solutions due to the uneven reaction of solute ions over the volume of the solution. The flow of ions is caused by these electrodes, thus causing a gradual corrosion.
- Rust corrosion - Related to the removal of small areas in the steel bars of the reinforcement. This type of rust is extremely well-formed and small holes or holes are made in the metal.
Causes of Stainless-Steel Rust
- Corruption of steel reinforcement barriers may be due to the local failure of the metal film of chloride ions or the general failure of the concrete to malfunction due to the carbon dioxide reaction from the atmosphere. The main factors facing corrosion of reinforcement barriers are:
- Loss of alkalinity due to carbonation - When a metal surface is left unprotected in the atmosphere, corrosion begins to form on the surface of the metal and then slowly moves away.
- Loss of alkalinity due to chlorides - Chloride ions tend to remove metal energy by destroying concrete.
- Cracking of Concrete - Cracking can expose metal bars in the atmosphere and increase liquidity.
- Moisture Methods - Regular wetting of concrete can lead to water reaching the metal bars by dispersing through the pore structure of the concrete or existing cracks in the concrete. Rust of steel bars follows after that.
- Insufficient cover: Insufficient size of concrete cover.
- Metal Rust due to Improper Cover
- Damaged steel reinforcement may occur due to insufficient concrete cover
Effects of Stainless-Steel Rust
When steel bars begin to break, reinforced concrete joints begin to break down through the following stages:
- White spot formation - Atmospheric carbon dioxide reacts with calcium hydroxide present in the reduction of cement forming calcium carbonate. This calcium carbonate is treated with moisture and deposited on the surface of the white-formed concrete.
- Dirty stains by reinforcement - When the metal bars begin to deteriorate, a layer of iron oxide forms in it. This metal oxide is also transferred to the surface of the concrete with moisture.
- Formations of cracks - Rust products take on a larger volume than the original. So they put pressure on the concrete and it cracks. In the event of a lot of rust, many wide cracks are formed.
- Disintegration of concrete cover - Due to the loss of bond between concrete and steel, concrete begins to form many layers of scales and then peels off. Metal bars are also reduced in size.
- Cracking of bars - Due to the decrease in the size of the steel bars, they eventually break. Also, there is a significant reduction in the size of the main bars.
- Piercing of bars - The collapse of the concrete cover and the cracking of the bars resulted in the collapse of the main bars. This floods the concrete area and eventually the entire building collapses.
How to Avoid Rusting Metal Rust
- The rust of steel reinforcement bars can be prevented or at least delayed by good measures. Also, damaged steel bars can be repaired and the concrete structure can be properly restored. Some steps are given below:
- Providing Sufficient Concrete Cover: A good amount of concrete cover should be provided in addition to the reinforcing steel bars. This ensures proper care of the alkaline type inside the concrete and the passage of the steel bars. Metal bars should be placed precisely in place
- Use of Quality Concrete: High quality concrete should be used. It helps to maintain an alkaline environment. In concrete, a water level of 0.4 or less should be maintained. Too much water can damage metal bars
- Compact Compaction fo Concrete: Concrete must be thoroughly mixed so that no air gaps or pockets are present.
- Use of FBE Bonds: Fusion Bonded Epoxy Coating (FBEC) can be used on metal bales to prevent corrosion. Epoxy powder is still electrically distributed in metal barns. The powder melts and flows over the bars as it heats up, forming a protective coating. It is a thermoset polymer coating because the use of heat will not melt the wear. Apart from the rebar it also has extensive function in pipeline construction
- Use of Cement-Based Polymers: Cement-based polymers can be used in concrete to increase their protection against corrosion. Cement-based polymers act as a bond in concrete. They also increase the strength, durability and melting of concrete
Carbonation of Concrete
- Carbonation of concrete is associated with corrosion of steel reinforcement and shrinkage. However, it also increases both the compression strength and the strength of the concrete, so not all of its effects on concrete are bad.
- Carbonation is the result of the decomposition of CO2 in pore fluid in concrete and this reacts with calcium from calcium hydroxide and calcium silicate hydrate to form calcite (CaCO3). Aragonite can form in hot climates.
- Within a few hours, or a day or two in total, the new concrete will be processed by CO2 in the air. Gradually, the process penetrates deeper into the concrete at a rate equal to the square root of time. After a year or more it is likely to reach a depth of about 1 mm with dense low-penetration concrete made of low water / cement, or up to 5 mm or more of high-density and permitted concrete using high water / cement scale.
Carbonation determination
- The affected depth from the concrete surface can be easily indicated by the use of a phenolphthalein indicator solution. This is available from chemical suppliers. Phenolphthalein is a white or pale yellow with a crystal. Use as a solvent dissolve in a suitable solution such as isopropyl alcohol (isopropanol) by 1%.
- The indicator has not changed color near the upper and lower extremities, suggesting that these regions near the surface be carbonated at a depth of at least 4 mm from the top to the top and 6 mm from the bottom.
- When the index turns purple - in the middle of the slide - the pH of the pore fluid anchor remains high (above 8.6, about 10). Whether you are pasting the cement here is not completely illuminated, despite the strong purple color; a complete test will require very little testing.
- The index was not applied to the concrete to the right of this image so the concrete here retains its original color.
- The depth of carbonation is about the same as the square root of time. For example, if the depth of carbon is 1mm in one-year-old concrete, it will be about 3mm after 9, 5mm after 25 years and 10mm after 100 years.
Key takeaways
- Carbonation of concrete is associated with corrosion of steel reinforcement and shrinkage. However, it also increases both the compression strength and the strength of the concrete, so not all of its effects on concrete are bad.
- Concrete, in itself, has a low strength. To increase the strength of the concrete, the steel hardens. Steel bars are inserted inside the weight of the concrete. These steel bearings carry a high load-bearing capacity applied to concrete.
- Concrete makes metal bars obsolete due to the alkaline environment, thus preventing them from cracking. However, for a variety of reasons, metal bars can be pulled longer. And as a result of the rust of the steel bars, various weaknesses appear in the concrete structure, which could eventually collapse if not properly maintained.
Repair - Symptoms and Diagnosis of Distress
- The rapid industrialization of India after independence required the transportation of goods and services and led to the construction of a network of wide roads with built-in bridges and flyovers.
- Many of the existing bridges show signs of stress within their work life built in many cases in the 10-20 years of construction in India and many other countries.
- The collapse of the I-35W bridge over the Mississippi River in the United States of America in August 2007 has attracted the attention of international media. In India, the collapse of the Mandovi Bridge in Goa in 1986 (after 16 years of service) and the great tribulation at the Zuari bridge (rebuilt in 2000 by an international consultant) in Goa and many other bridges such as Khalghat and Borad Bridge on NH3 (Route) Agra to Mumbai) due to environmental constraints is attracting the attention of transport authorities and the scientific community to transform the operational bridge management system.
- The cause of the distress, the level of grief and the reduction in the capacity of the bridge can be ensured in order to further the necessary adjustments to ensure the safety of the bridge during their operation.
- An assessment of the pressure and load capacity of existing bridges and to improve the load capacity is required while upgrading highways. India has already implemented the consolidation and use of four 7000 Km of highways under the Golden Quadrilateral program where the strengthening / replacement of many existing bridges was required.
- Various causes of damage to reinforced concrete bridges are low construction standards, rust of steel on reinforced concrete bridges and pre-reinforced concrete bridges, improper shape and details of normal loads and seismic forces, improper operation of bearings etc. a number of case studies have been reported in the literature on reinforced concrete damage and compacted concrete bridges during earthquakes and the reinforcement of reinforced and compressed concrete bridges due to nature and other loads.
- A concerted effort has been made to review critical documentation of reinforced concrete damage and pre-pressure concrete bridges and repair / rehabilitation strategies based on information from bridge reconstruction projects in which the authors were involved.
Causes of distress
- Relationship problems such as conflicts, illness / death of a loved one, divorce, abuse, partner, etc.
- Financial difficulties
- Environmental remediation
- Educational difficulties
- Time management and organizational complexity
- Anxiety
- Depression
- An abusive event
- Drug abuse
Diagnosis of distress
Sometimes the cause of grief is known e.g. Suffering during an earthquake, impact and explosion is known perhaps the active load exceeds the intended load but it is often difficult to find the real cause of grief where many variables are affected e.g. Poor construction quality (faulty details, faults and performance), shrinkage, penetration, rust consolidation etc. Following a test may be necessary to determine the cause and degree of grief.
- Determination of compression strength from NDT and cores of concrete
- Strategies for detecting explosions
- Signature / Vibration Analysis
- Download tests to find deviations / issues and distribute the load
- Rust studies (pH, depth of carbon, chloride)
- Deviation / disposal slopes from Instrumented Bridge
Key takeaways
- The rapid industrialization of India after independence required the transportation of goods and services and led to the construction of a network of wide roads with built-in bridges and flyovers.
- Many of the existing bridges show signs of stress within their work life built in many cases in the 10-20 years of construction in India and many other countries.
Selection Of Repair Procedure
Structure
- Structural repairs include using epoxy frames to bind or bond concrete together. Epoxy repair not only repairs the sealing cracks but also restores the strength and durability of the concrete. Use epoxy to repair dormant cracks only. Fixing functional cracks with epoxy often leads to a new formation near the original, epoxied fragment.
- Epoxy injection is a common way to inject epoxy into cracks, especially in direct and indirect areas. But gravity filling works well and is a common way to apply epoxy to flatwork cracks or to direct surfaces.
- The filling of gravity consists of pouring low-viscosity epoxy into the cracks that have been signed or distributed and allowed the gravitational force to pull the epoxy down the cracks. Viscosity resistance to fluid flow is measured in centipoises (cps). Decreased viscosity value, less (runnier) significant. Grade I and II epoxies have viscosities of less than 20 cps and between 20 and 100 cps, respectively.
- For comparison, the viscosities of other common beverages are: water - 1 cps, milk - 3 cps, anti-freeze - 15 cps, maple syrup - 150 to 200 cps, and honey -3000 cps. Low viscosities are required for solid cracks. Otherwise, the repair material will be too large to penetrate and flow into the crack.
- Epoxies were cured or hardened due to the chemical reaction between the frame and the hardener. Chemical reactions are rapid at high temperatures. Epoxies are obtained by different injections or by temperature treatments so chemical reactions are less rapid or slow (Type A, less than 40º F; Type B, 40º F to 60º F; and type C, more than 60º F).
- With the adjustment of gravity filling culture, consider the depth and depth, epoxy viscosity, and temperature input when choosing the distance and type of epoxy. Otherwise, the epoxy can be very strong or very hard to penetrate or it can just run between the river and the pool under the slide.
Sealing and filling
- Sealing and filling of non-construction repairs. However, some repair materials include cracked surfaces and can have a strong impact that can cause cracking of the material and concrete in the event of a major crack movement.
- Typical sealants and internal fixing fillers include semi-rigid epoxies, hybrid polyurethanes and polyureas, and polymer mortar. Polyurethanes and silicones are common labels used for exterior repairs.
- Usually, sealants are flexible or elastomeric materials; and the fillers are very hard so the fixing materials support the edges of the cracks to avoid collapse or damage under load. When heavy traffic is exposed to heavy wheels, composite fillers or special cracks with about 80 Shore A Hardness should be used.
- Unfortunately, there is a trade-off to increase the complexity of explosive repair materials. As the repair material gets harder, it becomes much thinner and does not tolerate cracked movement. For example, semi-rigid epoxies usually have a hardness of about 90 and an extension value of 50%; whereas, silicone sealants have a hardness of about 5 and an extension value of 1400%. Therefore, when choosing a fix, consider the expected movement of the comparison and the need to support the edges of the cracks.
- For effective cracking with the expected cracking motion, use elastomeric sealants or sealants with sufficient elastic properties, to see that the trade-off will be a little support for the fracture edges. For cracks exposed to heavy-duty traffic, use hard materials that support the edges of the cracks. But understand that these things do not tolerate the movement of cracks.
- If you are using elastomeric sealants in active cracks, always seal the sealant with a saw or by moving the track as recommended by the repairman. Without a dam, there would not be enough to tolerate future fracture movements. Expansion structures reported by manufacturers are based on the size of the recommended lakes or, in particular, the width and depth of the dam.
- Of course, cutting or scraping increases the width of the crack and makes crack repairs more noticeable. For cosmetic repairs in colored or decorative flats where cracks lie or are well established, do not see or move the sealant or filler dam. Instead, choose a low viscosity cracker (less than 100 cps) and small injection tips for cracks to fill gravity.
- Dams are not required. But in the event of a fracture movement, the cracking of the repair material or concrete may occur due to the small diameter of the depth of the material. Also, manufacturers now offer many of these low viscosity fixes in a variety of colors or offer color production recommendations and textures similar to concrete concrete surfaces.
- Before fixing your next explosion, do a crack test and establish repair targets. Decide what kind of adjustment is needed. Options include structural repairs using epoxy, route fixes and seal applications using flexible sealant to hold future cracks, and solid or durable repairs that fill the edges of cracks, with or without. Also, set cosmetic requirements. After selecting the fix and procedure, follow the manufacturer's recommendations.
Key takeaways
- Structure
Structural repairs include using epoxy frames to bind or bond concrete together. Epoxy repair not only repairs the sealing cracks but also restores the strength and durability of the concrete. Use epoxy to repair dormant cracks only. Fixing functional cracks with epoxy often leads to a new formation near the original, epoxied fragment.
2. Sealing and filling
Sealing and filling of non-construction repairs. However, some repair materials include cracked surfaces and can have a strong impact that can cause cracking of the material and concrete in the event of a major crack movement.
Repair of defects using various type and techniques - shortcrete and grouting
Shortcrete
- Shotcrete or sprayed concrete is concrete or mortar conveyed thru a hose and pneumatically projected at excessive pace onto a floor, as a production method, first utilized in 1914.
- It is usually strengthened with the aid of using traditional metallic rods, metallic mesh, or fibers.
- Properly carried out shotcrete is a structurally sound and sturdy production cloth which well-known shows terrific bonding traits to present concrete, rock, metallic, and plenty of different materials.
- It may have excessive strength, low absorption, correct resistance to weathering, and resistance to a few varieties of chemical attack.
- Many of the bodily residences of sound shotcrete are similar or advanced to the ones of traditional concrete or mortar having the equal composition.
- Improperly carried out shotcrete can also additionally create situations a lot worse than the untreated condition.
Advantages of shotcrete:
- Shotcrete is utilized in lieu of traditional concrete, in maximum instances, for motives of fee or convenience.
- Shotcrete is fine in conditions whilst formwork is fee prohibitive or impractical and wherein paperwork may be decreased or eliminated, get entry to to the paintings place is difficult, skinny layers or variable thicknesses are required, or ordinary casting strategies cannot be employed.
- Additional financial savings are feasible due to the fact shotcrete calls for handiest a small, transportable plant for manufacture and placement.
- Shotcreting operations can regularly be executed in regions of restrained get entry to to make upkeep to structures.
Grouting
- Grout is usually a mixture of cement, sand, and water or chemicals used to fill gaps.
- They are used to repair concrete cracks, to fill gaps and gaps in tiles, to fill gaps and waterproofing, and to strengthen the soil.
- It is also used to provide additional power to load-bearing structures. It basically involves the process of injecting something that can be pumped into a building to change its body structures.
- There are different types of grinding, cement grinding, chemical grinding, and bituminous grating, depending on the material used.
- Frames are also sometimes used as grout materials. A mortar is often used to fill cracks and gaps in soil or rock.
What is Grouting
- Also, it is used to stabilize the soil and keep it out.
- Cracking is used for a variety of purposes such as water repair, standing on immersed structures such as ditches, tunnels, etc., filling in the gaps between tiles and stabilizing the soil.
- Here we have provided details on the type of grouts used to repair cracks.
Advantage of Grouting Includes:
- This can be done in almost any soil condition
- It does not vibrate and can be controlled to avoid structural damage
- Development of underground structures can be measured
- It is very useful for limited space and low head items
- It is used to install slab jacking that lifts or measures the crippled foundation
- It can be installed near existing walls
- It can be used to control the flow of water, groundwater flow, and hazardous waste materials.
Many Different Types of Grouting Materials:
- Stopping cement
- Chemical Grouting
- Bentonite grouting
- The amber is growing
- Bituminous Grouting
Key takeaways
- SHORTCRETE
Shotcrete or sprayed concrete is concrete or mortar conveyed thru a hose and pneumatically projected at excessive pace onto a floor, as a production method, first utilized in 1914. It is usually strengthened with the aid of using traditional metallic rods, metallic mesh, or fibers.
2. GROUTING
Grout is usually a mixture of cement, sand, and water or chemicals used to fill gaps. They are used to repair concrete cracks, to fill gaps and gaps in tiles, to fill gaps and waterproofing, and to strengthen the soil.
Introduction of retrofitting of Concrete Structure by Fiber Reinforced Polymer (FPP), Polymer Impregnated Concrete
Fiber Reinforced Polymer
- Fiber-reinforced polymer (FRP), also fiber-reinforced plastic, is a composite made of polymer matrix reinforced with fibers. Threads are usually glass, carbon, or aramid, although other fibers such as paper or wood or asbestos have sometimes been used. The polymer is usually epoxy, vinylester or polyester thermosetting plastic, and phenol formaldehyde frames are still active. FRPs are widely used in the aerospace, automotive, marine and construction industries.
- Composite materials are made of building materials or naturally made from two or more materials that have a structure with very different physical or chemical properties that are always different and distinct from the finished structure. Most compounds have strong, strong fibers in a weak and strong matrix. The goal is usually to make the part stronger and stronger, usually with a lower volume.
- Commercial materials usually contain glass or carbon fibers in a matrix based on thermosetting polymers, such as epoxy or polyester resins. In some cases, thermoplastic polymers may be preferred, as they form after the first production. There are additional stages of integration where the matrix is metal or ceramic. For the most part, these are still in the development phase, and the problems of high production costs have yet to be overcome [1]. Moreover, in these compounds the reasons for adding fibers (or, in some cases, particles) are often complex; for example, improvements may be required in penetration, wear, cracking, heat stabilization, etc.
- Fiber-reinforced polymer (FRP) is a compound used in almost every type of high-tech engineering facility, with its use from aircraft, helicopters and spacecraft to boats, ships and marine systems as well as automobiles, sports equipment, repair equipment chemicals and public infrastructure such as bridges and buildings.
- The use of FRP compounds continues to grow at an impressive rate as these materials are widely used in their existing markets and are being developed in brand new markets such as biomedical devices and social structures. An important factor contributing to the increased use of compounds over the years has been the development of new types of FRP materials.
- This includes the development of high-resin applications and new reinforcement styles, such as carbon nanotubes and nanoparticles. The book provides a timely account of fiction, mechanical properties, delamination resistance, impact tolerance and the use of 3D FRP compounds.
- Polymers reinforced polymer composites (FRPs) are increasingly being considered for the development and / or replacement of structural components or systems consisting of traditional engineering materials, namely concrete and steel. FRP compounds are simple, non-destructive, show a certain high strength and direct durability, are easily constructed, and can be customized to meet operational requirements.
- Because of these beneficial features, FRP compounds have been incorporated into the construction and renovation of buildings using their reinforcement in concrete, blocks, modular structures, formwork, and external reinforcement for seismic reinforcement and development.
- The effectiveness of Fiber Reinforced Polymer (FRP) reinforcement in concrete structures such as replacement of steel bars or pre-pressurized muscles has been extensively studied in many research laboratories and professional organizations around the world. FRP reinforcement offers many benefits such as corrosion resistance, non-magnetic properties, very strong, lightweight and easy to handle.
- However, they usually have a direct response to stiffness to the point of failure (defined as damaging failure) and poor resistance to friction or shear. They are also less resistant to fire and when exposed to high temperatures. They release vital energy as they bend, and they are sensitive to the effects of pressure fractures. In addition, their cost, whether considered for each weight or on the basis of strength-bearing capacity, is relatively high compared with conventional steel reinforcement bars or pressure straps.
- From a structural engineering perspective, the most serious problems with FRP reinforcement are the lack of plastic conduct and very low shear strength on the short side. Such features can lead to premature tender fragmentation, especially if mixed results are obtained, such as in shear-breaking planes on reinforced concrete pillars where there is a delow action. The downtime action reduces the remaining resistance to stiffness and shear tenderness.
- Solutions and limitations for use are provided and further improvements are expected in the future. The cost of FRP consolidation unit is expected to decrease significantly with increasing market share and demand. However, even today, there are applications where FRP consolidation is less expensive and justified. Such cases include the use of FRP sheets or bonded plates in repairing and strengthening concrete structures, as well as the use of FRP meshes or fabrics or fabrics in small cement products.
- The cost of renovating and renovating a building remains, in certain terms, much higher than the cost of the original building. Repairs usually require a small amount of repair materials but a high commitment from staff. In addition, labor costs in developed countries are so high that the cost of materials is secondary. So the performance and performance that lasts the longest, the repair is very expensive. This means that the cost of materials is not a problem to be rectified and the fact that FRP materials are expensive is not a particular problem [5].
- Given only the physical strength and resources, at the top, the controversy over FRP compounds in a sustainable built environment is questionable. However, such a conclusion needs to be evaluated in terms of the potential benefits of using FRP compounds related to assumptions such as:
- High power
- Light weight
- High performance
- It lasts a long time
- Renovating existing buildings and extending their life
- Seismic development
- Security systems
- Space programs
- Ocean areas
o. In the case of FRP compounds, environmental concerns appear to be a barrier to its functioning as a viable alternative especially in terms of fuel depletion, air pollution, fog, and acidification associated with its production. In addition, the ability to reuse FRP compounds is limited and, unlike steel and wood, structural components cannot be reused to perform the same function in another structure. However, examining the environmental impact of FRP compounds on infrastructure use, especially through life cycle analysis, may reveal more direct and indirect benefits that compete more than conventional ones.
p. The composite material has greatly improved since its inception. However, before composite materials can be used as an alternative to conventional materials as part of a sustainable environment a few needs remain.
q. Availability of durability data for FRP building materials.
r. Integration of robust data and service life prediction methods for building members using FRP combinations.
s. Development of selection methods according to the life cycle cycle of materials and systems.
t. Finally, in order for the mixtures to be considered a viable option, they must be structurally and economically viable. Many studies on the structure of the composite material are widely available in the literature.
u. However, limited studies are available on the economic and environmental availability of these items from the perspective of the life cycle, because short-term data are available or only economic costs are considered in comparison. In addition, the long-term impact of using composite materials needs to be determined.
v. The products produced, the sustainability of the materials, and the capacity to recycle the materials need to be tested to determine if the composite materials can be part of a sustainable environment. So in this chapter describe the physicochemical properties of polymers and compounds most commonly used in Civil Engineering. The theme will be presented in a simple and basic way for better understanding.
Polymer Impregnated Concrete
- In the case of pregnant polymer concrete, prepolymers or lower liquid monomers are partially or partially impregnated with a pore system of a composite cement framework. After this process, the entire treated structure is allowed to polish.
- The general process of treatment of reinforced concrete leads to the acquisition of a large amount of free water in its spaces. These water-filled voids form a significant amount of total volume. From 5% in the case of dense concrete and 15% in the case of gaped concrete.
- In the case of pregnant polymer concrete, it is these voids (holes filled with water) that should be filled with the selected polymer. So the main thing that affects the loading of the monomer is this: the moisture content in the solid concrete and the air loses energy in the concrete.
Procedure for polymer impregnated concrete manufacturing
The activities involved in the pregnancy process to improve pregnant polymer concrete are:
1. Well-constructed concrete is available. They need to get better and get stronger.
2. Moisture is removed by drying the concrete. Drying is done by heating the structure element at temperatures above the order of 120 to 150 degrees Celsius. An air oven can be used to dry small specimens.
If the element has a large surface, a thick cloth, say, 10mm thick, can be used to protect it from any hot gradient. Another complex application is the use of infrared heaters.
Complete removal of moisture from concrete, requires 6 to 8 hours of heat.
3. After complete removal, the concrete area has cooled to a safer level. This can go up to a temperature of 35 degrees Celsius. This heat will avoid overheating.
4. The concrete is now transferred to a vacuum cleaner, where all the air inside the concrete structure is removed. The amount of monomer installed will determine the time and level of use of the machine.
5. Concrete after sufficient ventilation is placed in a monomer solution. Wet for a long time until the desired depth of monomer penetration is obtained.
Filling time depends on the viscosity of the monomer, the adjustment of the template and the advanced characteristics of the concrete.
To reduce the time taken to get the desired input, it is preferable to use external pressure such as air or nitrogen gas. This helps to get in faster.
6. After the above procedure, the surface is covered with plastic paper. This helps prevent the evaporation of the monomer.
7. A high-temperature polymerization method is performed. This method involves polymerization by heating the deformed monomer to the required temperature. This will start from 60 degrees to 150 degrees Celsius. The selected temperature range depends on the type of monomer.
Heating can be done under water or with a low pressure steam injection, or with infrared heaters or an air oven. The heat decomposes the catalyst and thus initiates the polymerization reaction.
Once the monomer has penetrated the concrete, polymerization can also be initiated using ionization radiation similar to gamma rays. Polymers when they are completely polymer or when connected on the other side, act as solids that reside in the voids they are embedded in.
8. The concrete structure is then allowed to cool.
Every process from 1 to 8 can only be done in a precast factory. Monomers such as acrylate, styrene and vinyl chloride etc. are widely used for concrete installations. Another widely used material is Methyl Methacrylate (MMA).
Properties of polymer impregnated concrete
1. The polymer concrete gains the strength of the cube to strengthen more than 100N / mm2. This strength does not depend on the strength of the standard concrete.
2. The flexibility of a pregnant polymer concrete is approximately 15N / mm2. This is slightly higher than high-grade clear concrete made from common ingredients.
3. The elastic modulus lies in the range from 30 to 60N / mm2. This value is the same as the value obtained from high-strength concrete (e.g. Approximately 45N / mm2)
4. Pregnant polymer concrete has less movement problems and shrinkage due to the small number of pores.
5. Pregnant polymer concrete is more resistant to acid attacks, sulfate attacks and chloride attacks compared to PCC.
Application of polymer impregnated concrete
The use of pregnant polymer concrete in various construction sites is described below:
1. Surface Impregnation of Bridge Decks: Bridge decks are allowed to be installed to avoid the ingress of moisture, chemicals and chloride ions.
Bridge floors built in areas with high salt water and moisture exposure can be protected in this way.
2. Structural repairs: Damaged structures can be developed in the form of a polymer abstract. The life span of undeveloped buildings can be extended in this way.
This method is why it helps in the restoration and preservation of stone monuments.
3. Underwater and Marine Applications: Polymer impregnation capabilities help to improve structures, water absorption, and non-concrete structures. This makes them widely used in water and sea construction.
Buildings built on desalination plants and underwater structures use this method of building concrete. It has been shown that the small absorption of concrete masses from seawater reduces the corrosion of the steel by 24 times.
4. Use in Irrigation Systems: The use of standard methods for the repair and rehabilitation of dams and other important water structures appears to be inefficient and incomplete.
This is later found to cause significant losses in profits from irrigation, energy production, flood control etc. But the method of pregnancy works very well.
Concrete from the damaged area is removed, glued and dried. This area is later treated using polymer emissions.
5. Composite Joints: Pregnant polymer concrete is as strong as building materials. PIC also shows the amazing development of standard concrete.
Internal and empty cracks are the basic foundation for all the issues in common concrete structures. Since the suspension of the polymer determines the cause, it is best used for construction members.
Key takeaways
- FIBER REINFORCED POLYMER
Fiber-reinforced polymer (FRP), also fiber-reinforced plastic, is a composite made of polymer matrix reinforced with fibers. Threads are usually glass, carbon, or aramid, although other fibers such as paper or wood or asbestos have sometimes been used. The polymer is usually epoxy, vinylester or polyester thermosetting plastic, and phenol formaldehyde frames are still active. FRPs are widely used in the aerospace, automotive, marine and construction industries.
2. POLYMER IMPREGNATED CONCRETE
In the case of pregnant polymer concrete, prepolymers or lower liquid monomers are partially or partially impregnated with a pore system of a composite cement framework. After this process, the entire treated structure is allowed to polish.
Corrosion monitoring and preventive measures
- The rust measuring, control, and prevention field covers a wide range of technical tasks. Within the field of corrosion control and prevention, there are technical options such as cathodic and anodic protection, material selection, chemical insertion and use of indoor and outdoor clothing. The rust scale uses a variety of techniques to determine how much damage the environment consumes and how much iron loss is experienced. Rust rating is a measure of how rust management performance and prevention strategies can be implemented and provides feedback to enable rust control and preventative measures to be improved.
- Some rust measurement techniques can be used online, regularly displayed in process broadcasts, while others provide external measurement, such as those determined in laboratory analysis. Some techniques provide a precise measure of metal loss or rust ratio, while others are used to indicate the possibility of corrosion.
- Rust monitoring is the practice of measuring the deterioration of process dissemination conditions by using probes that are incorporated into process dissemination and that are continuously expressed in the process dissemination process.
- Rust monitoring probes can be mechanical, electrical or electrical devices.
- Rust monitoring alone provides accurate and online measurement of metal loss / corrosion rate in industrial process systems.
- Typically, the rust measuring system, testing and adjustment used in any industrial area will include measuring instruments provided by four combinations of on-line / offline, direct / indirect measurements.
- Corrosion Monitoring Direct, On-line
- Direct, Offline Non-Destructive Testing
- Indirect Analytical Chemistry, Off-line
- Indirect, online Operational Data
- In a well-managed and integrated system, data from each source will be used to draw reasonable conclusions about the levels of active corrosion by the process process and how they are effectively reduced.
The Need of corrosion monitoring
The level of rust determines which process plant can be used efficiently and safely for how long. The rust scale and the action of adjusting the high levels of rust allow for the efficient operation of plants that must be achieved while minimizing the life cycle costs associated with the work.
Rust monitoring techniques can help in a number of ways:
- By giving an early warning that harmful procedural conditions exist that could lead to failures caused by rust.
- By studying the integration of changes in process parameters and their effect on system corrosivity.
- By identifying a specific rust problem, identifying its cause and the parameters that control the level, such as pressure, temperature, pH, flow rate, etc.
- By evaluating the effectiveness of the corrosion / prevention control method such as chemical prevention and good use.
- By providing management information relating to conservation needs and the ongoing condition of the plant.
Corrosion monitoring techniques
A large number of rust monitoring strategies are available. The following list describes the most common strategies used in industrial applications:
- Rust Coupons (Weight Loss Rate)
- Electrical Resistance (ER)
- Linear Separation Resistance (LPR)
- Galvanic (ZRA) / Possible
- Hydrogen Ingestion
- Bacteria
- Sand / Soil erosion
Other strategies are available, but almost all require professional work, otherwise they are not enough or flexible to apply.
In the above-mentioned strategies, corrosion coupons, ER, and LPR form the core of industrial corrosion monitoring systems. The other four strategies are usually found in special programs that are discussed over time.
These rust monitoring methods have been used successfully and are being used by a growing number of applications because:
- The techniques are easy to understand and apply.
- The reliability of the equipment has been demonstrated in the field field for many years of application operation.
- The results are easy to explain.
- Measurement equipment can be made internally safe from hazardous environmental performance.
- Consumers have gained significant economic benefits by reducing planting time and extending plant life.
Preventive Measures
- Metal corrosion is a natural process that requires three conditions: moisture, metal surface, and an oxidizing agent called an electron acceptor. Rust converts the active metal into a separate form of oxide, hydroxide, or sulphide. The most common type of rust is rust.
- Metallic metal not only affects the structure of the metal, but it can also affect the people who use the material or objects close to the metal. In extreme cases, rotten metal can lead to the construction of buildings and bridges, leaking pipes, and medical implants that infect human blood.
- While all metals are in danger of corrosion, some metals, such as pure metal, deteriorate much faster than others. However, iron can be combined with other alloys to form a stainless steel that is more resistant to corrosion.
- It is estimated that approximately 25-30% of rust can be prevented using appropriate protective measures.
- In general, you can prevent rust by choosing the right type of metal, Protective Fabrics, Environmental Measures, Self-Sacrifice Items, Rust Stumbling Stuff, Metal Installation and Repairs for Your Project.
Choose the right metal type
- One of the easiest ways to prevent rust is to use rust-resistant metal such as stainless steel, duplex, super duplex, nickel alloy or 6% Moly.
- These devices are so well made that they have a high resistance to corrosion and use them to reduce the need for alternative corrosion protection.
- For Special Drawing Materials, we offer products made of the highest quality synthetic materials available - stainless steel, duplex, super duplex, 6% Moly and Nickel Alloy. A variety of materials are selected by our clients in a variety of areas, with one of the factors considered for possible corrosion.
Protective coating
- Another way to prevent rust is to cover it with a special protective paint. Paint coating can act as a barrier that works by preventing electrochemical charging that transmits to the destructive and metal solution below.
- One way to do this is to put a powder coating in a clean metal place. The metal is heated to turn the flour into a smooth, non-abrasive film that acts as a barrier to rust. Many different powder compositions can be used, such as acrylic, polyester, epoxy, nylon, and urethane.
Environmental Measures
- Rust is certainly due to the nature of the metal in it as the chemical reactions that occur are due to metal reacting with liquids and gases in the surrounding environment.
- Controlling the environment can therefore help reduce this response. This could be as simple as reducing exposure to rain or seawater or it could be steps taken to reduce the amount of sulfur, chlorine, or oxygen in the area. For example, carrying water in water boilers to adjust hardness, alkalinity, or oxygen content, before placing the metal in that water can be very helpful in preventing corrosion.
Sacrificial coating
Sacrifice cover to prevent corrosion means covering the metal with a type of metal that may have oxidise - you sacrifice this top layer to protect the lower metal.
There are two main ways to accomplish the sacrificial attire:
- Cathodic Protection: Cathodic protection works by making the metal cathode of an electrochemical cell. The most common example of cathodic protection is the coating of iron ore and zinc - this process is known as galvanizing. Zinc is more than an active metal so rust prevents metal rot. Cathodic protection is frequently used for steel or petrol pipelines, heat tanks, ports, and overseas oil platforms.
- Anodic Protection: Anodic protection is opposed to cathodic protection and works by making the metal anode of an electrochemical cell. A common way to do this is to cover a thin layer of stainless steel, such as tin. The tin will not corrode, so the metal will be protected as long as the tin coating is in place. Anodic protection is often used for carbon storage tanks used to store sulfuric acid and 50% caustic soda.
Corrosion Inhibitors
- Chemical corrosion inhibitors are selected to react to metal surfaces or surrounding gases and therefore suppress electrochemical reactions that can lead to decay. When applied to a metal surface, they form a protective film. Inhibitors can be used as a solution or as a protective cover using distribution methods.
- Corrosion inhibitors are often used in a process known as passivation. An example of passivation is the Statement of Freedom where a blue and green metal signature is actually present to protect the copper underneath.
Metal Plating
- The installation is very similar to the cover as a thin layer of metal is inserted into the metal you want to protect. As well as preventing corrosion, the metal layer provides a good finish of beauty.
There are four types of metal wraps:
- Electroplating: The application of a thin layer of metal such as chromium or nickel to the underground metal by means of an electrolyte bath.
- Mechanical Plating: this involves cold welding powder metal metal substrate.
- Electro less: Coating such as nickel or cobalt is placed on a metal substrate using non-electrical chemical reactions.
- Hot dipping: A simple covering method that involves placing the substrate in a molten metal protective tub.
Design Modification
- Changing the structure of the project can have a significant impact on rust protection as it works by eliminating the causes of rust.
Key takeaways
- The rust measuring, control, and prevention field covers a wide range of technical tasks. Within the field of corrosion control and prevention, there are technical options such as cathodic and anodic protection, material selection, chemical insertion and use of indoor and outdoor clothing. The rust scale uses a variety of techniques to determine how much damage the environment consumes and how much iron loss is experienced. Rust rating is a measure of how rust management performance and prevention strategies can be implemented and provides feedback to enable rust control and preventative measures to be improved.
Rehabilitation methods for concrete elements grouped under confining techniques included concrete jacketing, steel jacketing, ferrocement laminated jacketing and FRP confinement. Some of the methods are for cosmetic repairs required to improve appearance, restore the non-structural properties and weather protection.
These techniques and materials for repair of concrete is described. Concrete is the most widely used and versatile construction material possessing several advantages over steel and other construction materials. However very often one come across with some defects in concrete. The defects may manifest themselves in the form of cracks, spalling of concrete, exposure of reinforcement, excessive deflections or other signs of distress. On many occasions, corrosion of reinforcement may trigger off cracking and spalling of concrete, coupled with deterioration in the strength of the structure. Such situations call for repairs of affected zones and sometimes for the replacement of the entire structure.
The need of structural repairs can arise from any of the following:
- Faulty design of the structure
- Improper execution and bad workmanship
- Extreme weathering and environmental conditions
- High degree of chemical attack
- Ageing of the structure
References:
1. A.M Neville J.J. Brooks Concrete technology
2. A.M Neville Concrete technology
3. R.S. Varshney Concrete technology
4. IS 10262 - 2009, Recommend guidelines for Concrete
Unit - 1
Concrete
- Concrete is a composite fabric composed of exceptional and coarse combination bonded collectively with a fluid cement (cement paste) that hardens (cures) over time.
- In the past, lime primarily based totally cement binders, consisting of lime putty, have been regularly used however now and again with different hydraulic cements, consisting of a calcium aluminate cement or with Portland cement to shape Portland cement concrete (named for its visible resemblance to Portland stone).
- Many different non-cementitious forms of concrete exist with different techniques of binding combination collectively, together with asphalt concrete with a bitumen binder that is often used for avenue surfaces, and polymer concretes that use polymers as a binder.
- When combination is blended with dry Portland cement and water, the combination bureaucracy a fluid slurry this is without difficulty poured and molded into shape.
- The cement reacts with the water and different elements to shape a difficult matrix that binds the substances collectively right into a long lasting stone-like fabric that has many uses.
- Often, additives (consisting of pozzolans or superplasticizers) are protected with inside the combination to enhance the bodily residences of the moist blend or the completed fabric.
- Most concrete is poured with reinforcing substances (consisting of rebar) embedded to offer tensile strength, yielding bolstered concrete.
- Because concrete cures (which isn't always similar to drying), how concrete is treated after it's miles poured is simply as essential as before.
- Concrete is one of the maximum often used constructing substances.
- Ts utilization worldwide, ton for ton, is two times that of steel, wood, plastics, and aluminum combined. Globally, the ready-blend concrete industry, the biggest section of the concrete market, is projected to exceed $six hundred billion in sales with the aid of using 2025.
- Concrete is wonderful from mortar. Whereas concrete is itself a constructing fabric, mortar is a bonding agent that generally holds bricks, tiles and different masonry devices collectively.
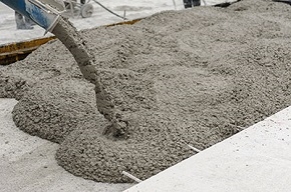
Fig 1: Concrete
Key Takeaways:
- Concrete is a composite fabric composed of exceptional and coarse combination bonded collectively with a fluid cement (cement paste) that hardens (cures) over time.
Plain concrete:
- Plain concrete, additionally referred to as undeniable cement concrete or PCC, is maximum typically used for paving and flooring.
- Made from a combination of cement, combination, and water the special varieties of combination and ratio of substances used will deliver special varieties of cement with barely special homes.
- This is one of the foremost promoting factors of geared up blend concrete as the precise values and varieties of combination may be measured and monitored exactly to offer the traits which are wished with none variance.
- The computerized production procedure limits the capacity of human blunders whilst saving time and resources.
- While there are variations with inside the composition of the concrete maximum undeniable concrete stocks the equal strengths and weaknesses.
- It is rather robust beneath Neath compression even as susceptible beneath Neath anxiety, because of this whilst on a solid, unmoving floor it's miles able to withstanding large quantities of weight.
- However, whilst located beneath Neath anxiety it's miles an awful lot weaker and might frequently crack and buckle.
- This makes it the correct cloth for floor ground layers and offering a strong or even base for strengthened concrete to be constructed onto whilst proscribing its use in large creation projects.
Key Takeaways:
- Made from a combination of cement, combination, and water the special varieties of combination and ratio of substances used will deliver special varieties of cement with barely special homes.
Reinforced concrete:
- Reinforced concrete, or strengthened cement concrete (RCC), is surely very just like PCC in phrases of substances used.
- The one massive distinction in its composition is the addition of metal rebar.
- By casting the moist cement round reinforcing metal bars the consequent composite cloth has an awful lot extra electricity beneath anxiety whilst nonetheless maintaining the homes that make PCC so effective.
- With the concrete retaining its electricity beneath compression and the metal resisting any bending or stretching way to its tensile electricity the RCC is a far extra flexible creation cloth.
- Able to rise up to weight pushing down onto it in addition to any wind stress or moving that outcomes in moderate twists and lines way to the expanded flexural capability of the concrete/metal blend, it's miles an appropriate cloth for taller and heavier homes and for roads and bridges.
- Steel is the maximum not unusual place cloth used for the introduction of rebar because it reacts to very comparable variances in temperature as concrete, that means it'll amplify and settlement with the concrete instead of cracking it from the inside.
Key Takeaways:
- By casting the moist cement round reinforcing metal bars the consequent composite cloth has an awful lot extra electricity beneath anxiety whilst nonetheless maintaining the homes that make PCC so effective.
Steel fiber/Glass fiber-strengthened concrete:
- Steel Fiber Reinforced Concrete (SFRC) is described because the concrete made with hydraulic cement containing high-quality and coarse combination and discontinuous discrete metal fiber.
- In SFRC, lots of small fibers are dispersed and disbursed randomly with inside the concrete for the duration of mixing, and hence enhance concrete homes.
- SFRC is getting used to enhance static and dynamic tensile electricity, strength soaking up capability and higher fatigue electricity.
- Steel fibers are the most powerful typically to be had fiber, and are available special lengths and shapes.
- Steel fires can simplest be used on surfaces which can tolerate or keep away from corrosion and rust stains.
- In a few cases, a metal-fiber floor is confronted with different substances.
- Glass fiber is a less expensive and corrosion-evidence fiber, however now no longer as robust as metal.
- The layout of glass fiber strengthened concrete proceeds from understanding of its fundamental homes beneath tensile, compressive, bending and shears forces, coupled with estimates of conduct beneath secondary loading results along with creep, thermal reaction and moisture movement.
Key Takeaways:
- SFRC is getting used to enhance static and dynamic tensile electricity, strength soaking up capability and higher fatigue electricity.
Light-weight concrete:
- Lightweight concrete is a combination made with light-weight coarse aggregates along with shale, clay, or slate, which provide it its feature low density.
- Structural light-weight concrete has an in-location density of ninety to a hundred and fifteen lb/ft³, while the density of everyday weight concrete stages from a hundred and forty to a hundred and fifty lb/ft³.
- This makes light-weight concrete best for constructing current systems that require minimum move sections with inside the foundation.
- It is being more and more used to construct smooth foundations, and has emerged as a possible opportunity to everyday concrete.
- Nevertheless, a better compressive electricity of 7000 to 10,000 psi may be attained with light-weight concrete.
- However, this can compromise the density of the combination because it calls for the addition of extra pozzolans and water-decreasing admixtures to the concrete.
Key Takeaways:
- Structural light-weight concrete has an in-location density of ninety to a hundred and fifteen lb/ft³, while the density of everyday weight concrete stages from a hundred and forty to a hundred and fifty lb/ft³.
High overall performance concrete:
- Concrete assembly unique combos of overall performance and uniformity necessities that cannot usually be accomplished mechanically the use of traditional parts and everyday mixing, placing, and curing practices.
- High-overall performance concrete (HPC) is concrete that has been designed to be extra-long lasting and, if necessary, more potent than traditional concrete.
- HPC combinations are composed of basically the equal substances as traditional concrete combinations, however the proportions are designed, or engineered, to offer the electricity and sturdiness wished for the structural and environmental necessities of the project.
- High-electricity concrete is described as having a targeted compressive electricity of 8000 psi (fifty-five MPa) or greater.
- The price of 8000 psi (fifty-five MPa) became decided on as it represented a electricity stage at which unique care is needed for manufacturing and checking out of the concrete and at which unique structural layout necessities can be wished.
Key Takeaways:
- HPC combinations are composed of basically the equal substances as traditional concrete combinations, however the proportions are designed, or engineered, to offer the electricity and sturdiness wished for the structural and environmental necessities of the project.
Polymer concrete:
- Polymer concrete is a combination that makes use of a few form of epoxy binder to remedy and harden into location.
- A polyester, vinyl ester, or everyday epoxy combination is frequently used, however polymer concrete may be made with many styles of polymer resins that permit the concrete to be poured or troweled after which hardened.
- It remedies via a chemical response with the polymer cloth.
- Like conventional concrete, it additionally has water, sand and gravel or overwhelmed stone as number one ingredients.
- Polymer concrete gives special blessings relying at the resin used to make it.
- Acrylic binders set right away and provide resistance to weathering, whilst epoxies create a completely robust cloth that shrinks little or no because it remedies.
- Furan resins can face up to excessive temperatures, and polyuria resins can update phenolic or formaldehydes in lots of creation projects.
- Polymer concrete is used for lots styles of specialized creation projects.
- Like different varieties of concrete, it is able to be used to sign up for special additives or to offer a shape or base.
- The cloth is utilized in electric or commercial creation in which the concrete desires to final a long term and be proof against many varieties of corrosion.
Key Takeaways:
- A polyester, vinyl ester, or everyday epoxy combination is frequently used; however, polymer concrete may be made with many styles of polymer resins that permit the concrete to be poured or troweled after which hardened.
Concrete is a commonly used construction material, which is the mixture of cement, sand, aggregate, and admixtures blended with water. Concrete gets hardened with time and gains the strength, and for the best results in a construction of your dream home, mixing of concrete is said to be the most important process. All the ingredients are to be mixed in proper proportion because the properties of concrete like workability, strength, surface finish, and durability of concrete etc. are ensured by the right and proportionate blending.
In the nominal mix concrete, all the ingredients and their proportions are prescribed in the standard specifications. These proportions are specified in the ratio of cement to aggregates for certain strength achievement.
The mix proportions like 1:1.5:3, 1:2:4, 1:3:6 etc. are adopted in nominal mix of concrete without any scientific base, only on the basis on past empirical studies. Thus, it is adopted for ordinary concrete or you can say, the nominal mix is preferred for simpler, relatively unimportant and small concrete works.
As per the ‘Indian Standard- IS 456:2000’, nominal mix concrete may be used for concrete of M20 grade or lower grade such as M5, M7.5, M10, M15.
M 20 is identified as the concrete grade in which, M denotes the Mix and 20 denotes the compressive strength of concrete cube after 28 days of curing in N/mm2. There are various grades of concrete that can be used like M10, M15, M20, M25, M30, etc.
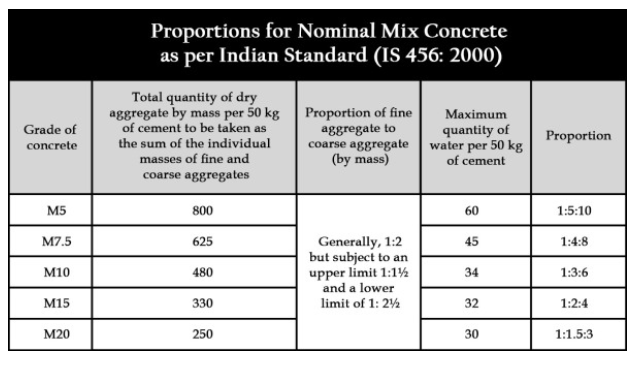
Tests on fresh concrete
Objective
- The word ―workable or concrete used has a broader and deeper meaning than the word alternative that is commonly used freely to make it work. Consistency is a general term that indicates the level of fluid or flow rate.
- Factors that help concrete to have the most effective effect of reducing internal friction that facilitates easy mixing are:
(a) Water content
(b) Mixing Dimensions
(c) Collection Size
(d) Structure Shapes
(e) Spatial Design Design
(f) Placement layout
(g) Use of Admixtures.
- Slump test is the most widely used method of measuring the consistency of concrete that can be used in a laboratory or in the workplace.
- It is not suitable for very wet or very dry concrete. It does not measure all factors that affect performance, nor does it always represent concrete placement.
- Indicates the concrete feature above the drop value. When the concrete slips evenly it is called a true slump. When one part of the lump slips, it is called a shear slump.
- In the event of a shear bend, the slump value is measured as the height difference between the height of the mold and the average amount of shrinkage.

Fig no 2 Slum cone
Procedure
- If this test is performed in the field, a mixed concrete sample will be obtained. In the case of concrete containing a diameter of more than 38 mm, the concrete will be diluted with water by one and a half inches of screen to remove compacted particles larger than 38 mm.
- The inner surface of the mold will be thoroughly cleaned and freed from unwanted moisture and pre-set concrete before testing. The mold will be placed on a smooth, horizontal, strong, and non-abrasive surface, such as a carefully weighed metal table, the mold will be kept firmly in place while filling.
- The mold will be filled in four layers, each about a quarter of the height of the mold. Each layer will be smoothed with twenty-five lashes on the round edge of the lubricating rod. The lashes will be distributed evenly over the section at the cross section of the mold and the second and subsequent layers will fit into the lower layer.
- The bottom layer will be smoothed in the depth of it all. After the upper layer has been coated, the concrete will be flattened and trimmed with a trowel, so that the mold will fill directly.
- After the top layer has been glued, remove the concrete surface by moving and moving the lubricating rod.
- Any mud that may have leaked between the mold and the base plate should be cleaned. The mold will be removed from the concrete immediately by lifting it gently and carefully in a vertical direction. This allows the concrete to drop and the fall will be measured immediately by determining the difference between the height of the mold and that of the highest of the test template.
- The above operation will be performed in a non-vibrating or panic-free environment, and within two minutes after sampling.
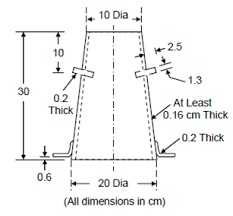
Fig no 3 Dimensions of slum cone
Key takeaways
- Slump test is the most widely used method of measuring the consistency of concrete that can be used in a laboratory or in the workplace.
- It is not suitable for very wet or very dry concrete. It does not measure all factors that affect performance, nor does it always represent concrete placement.
COMPACTION FACTOR
Objective
The compacting factor test is mainly designed for use in the laboratory but can also be used in the field. It is more accurate and sensitive than fall testing and is especially useful for very low-performance concrete mixes and is often used when the concrete will be squeezed by vibration. This method works on bare and ventilated concrete, made of lightweight, standard weight or heavy aggregates with a maximum weight of 38 mm or less but not on open concrete or non-reinforced concrete.
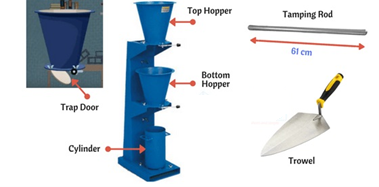
Fig no 4 Compaction factor apparatus
Procedure
- A sample of the test concrete will be gently placed on the upper hopper, using a hand scoop. The hopper will be evenly filled with its edge and the trap door will be opened so that the concrete falls to the ground.
- Some mixes tend to stick to one or both hoppers. When this happens, the concrete can be helped by pushing the rod gently into the concrete from the top. During this process, the cylinder will be covered with tiles.
- As soon as the concrete is out, the cylinder will be exposed, the door to the bottom trap will be opened, and the concrete will be allowed to fall into the cylinder. The remaining concrete over the top of the cylinder will be removed by holding a trowel in each hand, the plane of the belts horizontally, and then moving them simultaneously to each side above the cylinder, at the same time keeping them pressed against the upper edge of the cylinder.
- The outside of the cylinder when it is wiped will be clean. The above work will be done in a place that will not tremble or shake. The weight of the concrete in the container will be determined by the nearest 10 g.
- The remaining concrete over the top of the cylinder will be removed by holding a trowel in each hand, the plane of the belts horizontally, and then moving them simultaneously to each side above the cylinder, at the same time keeping them pressed against the upper edge of the cylinder. The outside of the cylinder when it is wiped will be clean. The whole process will be done in a place where there is no vibration or shock.
- This weight will be known as the weight of the partially bonded concrete. The cylinder will be filled with concrete from the same sample with layers about 5 cm deep, the layers folded tightly
- Or shaken to achieve complete integration.
- The surface of the fully covered concrete will be carefully beaten and weighed above the cylinder. The outside of the cylinder when it is wiped will be clean.
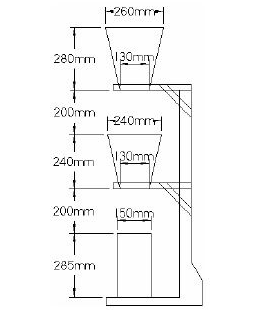
Fig no 5 Dimensions of compaction factor apparatus
Key takeaways
The compacting factor test is mainly designed for use in the laboratory but can also be used in the field. It is more accurate and sensitive than fall testing and is especially useful for very low-performance concrete mixes and is often used when the concrete will be squeezed by vibration. This method works on bare and ventilated concrete, made of lightweight, standard weight or heavy aggregates with a maximum weight of 38 mm or less but not on open concrete or non-reinforced concrete.
VEE BEE CONSISTOMETER AND FLOW TABLE APPARATUS
VEE BEE CONSISTOMETER
Objective
- The performance of the new concrete is a composite material, which incorporates various requirements for stability, mobility, durability, placement and finishing. There are various ways to measure performance.
- Each of them measures only a specific aspect of it and there is no unique test, which measures the performance of concrete completely. This test provides an indication of the flow rate of the newly mixed concrete mix.
- The test measures the concurrent effort required to change a pile of concrete from one concrete to another (e.g., from a circle to a cylindrical) using vibration.
- The amount of effort (called retrieval attempt) is taken as the time in seconds, which is required to complete the change. The results of this experiment are useful when you study the flow of concrete piles made of different amounts of water, cement and different types of composite placement.
- The time required for a full recovery in seconds is taken as a performance measure and is expressed as the Vee-Bee number of seconds.
- This method is suitable for dry concrete. With concrete drop of more than 50mm, reconstruction is so fast that time cannot be measured.
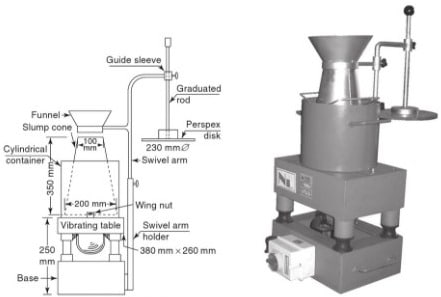
Fig no 6 Vee bee Consistometer Test
Procedure
- Slump test as described in "IS 1199: 1959 Details of Concrete Testing Equipment (Fourth Review). Confirmed- Dis 2013". Is made, inserting a collapsible lump inside a round metal pot of consist meter.
- The glass disk attached to the rotating arm will be moved to the top of the cone in the pot and before the cone is raised, the location of the concrete cone will be identified by fixing the glass disc attached to the arm wrist. The cone will then be lifted and the fall will be marked on the graduating rod by lowering the glass disc over the concrete cone. The electric heater will then light up and the concrete will be allowed to lay in the pot.
- The vibration continues until the point where the concrete shape disappears and the concrete takes on a circular shape. This can be judged by looking at the glass disc from the top disappearing visually.
- As soon as the concrete completely begins to form a circle, the stand clock is turned off. The time required for concrete formation to change from the formation of a collapsing lump into a circle in seconds is known as the Vee Bee Degree.
- This method is best suited for dry concrete with an unmeasured fall value with a Slump Test, but vibration is much stronger than concrete with a fall of more than 50 mm.
FLOW TABLE
Flow tests were performed to measure the performance of the concrete. As the name suggests, in this experiment concrete performance is measured by examining the flow of concrete material. Flow test Easy laboratory test. This test applies to the principal for the general weight loss of concrete and is measured by the flow of concrete. The flow of concrete indicates the performance of the new concrete.
Why flow test of concrete required
Flow tests are used to measure the performance of high or very active concrete, which ultimately indicates a fall. It gives an idea about the quality of concrete in terms of consistency and consistency. This performance test is easy to perform and is best suited for concrete with a high overall size of the joint less than 38 mm.
Flow Test Apparatus
Metal Cone or Mould: Mould is in the form of a frustum of a cone with a base diameter of 250 mm, upper surface diameter of 170 mm and 120 mm height. The mould comes with handles for support.
Flow Table
Trowels
Hand scoop
Scale
Tamping Rod
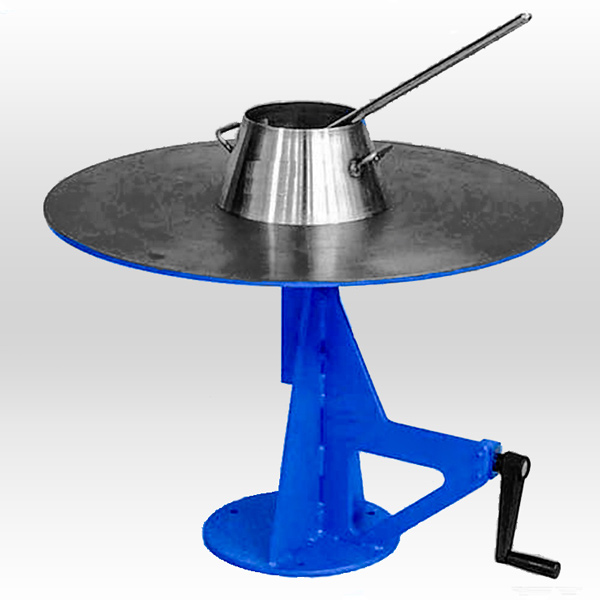
Fig no 7 Flow test apparatus
Procedure
- Clean anything toxic or dusty from the flow table and inside the mold.
- Place the lump on the marked area or in the middle of the flow table.
- Now pour the freshly mixed concrete into the mold in two layers, each layer should be moistened 25 times with a soft stick. If the concrete overflows after stamping and measure with the help of a torch, and the excess concrete should be removed from the table.
- After that, lift the mold upwards and allow the concrete to stand on its own without support.
- After that the table is raised and lowered from 12.5 mm high, 15 times in about 15 seconds.
- Next, measure the width of the concrete spread by about 6 points and write down the scale.
Key takeaways
- The performance of the new concrete is a composite material, which incorporates various requirements for stability, mobility, durability, placement and finishing. There are various ways to measure performance.
- Each of them measures only a specific aspect of it and there is no unique test, which measures the performance of concrete completely. This test provides an indication of the flow rate of the newly mixed concrete mix.
- Flow tests were performed to measure the performance of the concrete. As the name suggests, in this experiment concrete performance is measured by examining the flow of concrete material. Flow test Easy laboratory test. This test applies to the principal for the general weight loss of concrete and is measured by the flow of concrete. The flow of concrete indicates the performance of the new concrete.
Effect of admixture on workability of concrete and optimum dosage of admixture by marsh cone test
Effect of admixture on workability of concrete
- Concrete contains cement, sand, a mixture of water. Anything other than these if added to concrete before or during mixing to convert structures to our desired requirement is called admixtures. The use of admixtures provides certain beneficial effects on concrete such as improved performance, speed or delay of set time, reduction of the amount of water cement, and so on.
- There are two basic types of admixtures available: chemicals and minerals. Admixtures such as fly ash, silicate fume, slag come in the category of mineral admixtures. They are incorporated into concrete to increase performance, improve thermal resistance and alkaline reactions and enable us to reduce cement content.
- Fly ash is a good residue left over from global warming or powdered charcoal. They are all better than cement and contain mainly round glass particles as well as remnants of hematite and magnetite, char and other crystalline layers formed during cooling. The use of fly ash in concrete makes mixing more economical, and improves performance, reduces separation, bleeding and reduces hydration temperatures but also offers natural benefits.
- Silica fire, also known as micro silica. It is available as a product during the production of silicon and ferrosilicon alloys. The particles of silica fire particles are 100 times smaller than cement particles which mean their smoke like cigarettes. Its highly efficient pozzolanic material, which improves concrete structures such as improved durability, bond strength, abrasion resistance, dense concrete leading to reinforcement and rust protection.
- Chemical admixtures are applied to concrete in very small quantities especially for ventilation, reduction of water or cement content, installation of new concrete mixtures or control of concrete set time. These compounds can be widely used as super plasticizers, accelerators, retarders, water reducers and ventilation admixtures.
- Super plasticizers were added to reduce water demand by 15 to 20% without affecting performance leading to high durability and high concrete. Super plasticizers are liner polymers that contain sulfonic acid groups attached to the polymer from time to time. Commercial composition can dissolve melamine - formaldehyde condens- sates, sulfonated naphthalene formaldehyde condensates, and modified lingo sulfonates, derived from polycar- boxylate. The main purpose of super plasticizers is to produce a concrete slope with a very high drop of 175 to 200 mm that can be used effectively on reinforced concrete structures, a decrease in volume depending on the volume, type and timing of good plasticizers (preferably before adding concrete.), Water cement, environment and value of cement.
- Accelerators were added to reduce the setting time of the concrete thus facilitating pre-form removal and are also used in the combination of cold weather. Calcium chloride is the most widely used accelerator in blending. The use of calcium chloride in reinforced concrete can promote the corrosion function of the steel reinforcement. As people become aware of it there is a growing interest in using free chloride.
- Retarders were added to increase the setting time by delaying the hydration of the cement. They are popular in areas with high temperatures combined. Retarders contain organic & inorganic agents. Organic retarders include unrefined calcium, sodium and ammonia salt lignosulfonic acid, hydro carboxylic acid and carbohydrates. Inorganic retardants include lead oxides, zinc, phosphate and magnesium salts. Most retarders work as a water repellent. They are called retarders that reduce water. It is therefore caused by high pressure forces due to the low water content.
- Admixtures reduce the amount of water added to the concrete to achieve a certain effect (fall) at a lower water level. Strong concrete specified for low cement content thus saving cement. Water reducers are widely used in hot weather and assist in pumping. Water-repellent plasticizers are hygroscopic powder, which can inhale air into concrete.
- Ventilation admixtures bring in small concrete bubbles. These air bubbles act as rollers thus improving performance and also work more efficiently in thaw-chilling channels as they provide a stabilizing effect in expanding water where cold weather meets.
- Ventilation admixtures are compatible with most combinations, care should be taken to prevent them from collapsing during mixing.
- In general, the performance of both types of plasticizers depends on the ambient temperature and thus in the summer the amount of plasticizer that will be used to handle the same rate of plastic expansion may be more than the amount that will be used in winter.
- The change in the normal set time within a specific requirement also makes the product dependent on other chemicals and as plasticizers with different nomenclature available in the market.
- CICO Technologies Limited, a 75-year-old Indian company ISO 9001: 2000 supported producing a range of concrete installation admixtures.
- Many RMC companies use CICO admixtures. Further modification is required during the trial. Modification to Plasticizers can meet the needs of any particular client.
Optimum dosage of admixture by marsh cone test
- Admixtures are common and important of modern concrete. Low water content, high efficient, durable and cost-effective cement
- Many desirable properties that can be expected from concrete made of chemical and mineral composites
- Admixture-Cement mixing in concrete is complex combination of chemical and physical equipment independent.
- All combinations in large volumes offer good results when used with cement.
- Cement hydration involves a series of reaction, which is highly dependent on cement composition, water / cement ratio, surface area, particle distribution of size, temperature and integration.
- Admixtures when added in small amounts do that the hydration process is very complex. In recent times, developments in the cement product sector are related to the use of admixtures especially organic polymeric building materials.
- Many species of polymeric organisms known as super plasticizers, are used construction industries to change the way it flows again concrete machinery facilities.
- Among the various species for chemical admixtures, PCE-based admixtures are shown to develop new flow and complex areas of low-grade concrete.
Key takeaways
- Concrete contains cement, sand, a mixture of water. Anything other than these if added to concrete before or during mixing to convert structures to our desired requirement is called admixtures. The use of admixtures provides certain beneficial effects on concrete such as improved performance, speed or delay of set time, reduction of the amount of water cement, and so on.
- Admixtures are common and important of modern concrete. Low water content, high efficient, durable and cost-effective cement
- Many desirable properties that can be expected from concrete made of chemical and mineral composites.
Testing of hardened concrete
- The compression take a look at indicates the exceptional feasible electricity concrete can gain in best conditions.
- The compression take a look at measures concrete electricity withinside the hardened state.
- Field concrete samples are organized, cured and examined consistent with ASTM preferred procedures.
- Specimens are organized from concrete taken from exclusive creation sites.
- Following methods and calculations are used for measuring compressive electricity of cylindrical concrete specimens.
Test Procedure
- Placing the Specimen — The plain (decrease) bearing block is located, with its hardened face up, at the desk of the trying out device without delay beneath the spherically seated (top) bearing block. The bearing faces of the top and decrease bearing blocks are wiped clean and the take a look at specimen is located at the decrease bearing block.
- Zero Verification and Block Seating— previous to trying out the specimen, it's far demonstrated that the weight indicator is ready to zero. If the indicator isn't always well set to zero, it's far adjusted.
- Rate of Loading— the weight is implemented constantly and without shock.
- Standards specify that for trying out machines of the screw type, the shifting head shall tour at a charge of about zero.05in. (1mm)/min while the device is jogging idle .While for hydraulically operated machines, the weight will be implemented at a charge of motion (platen to crosshead measurement) similar to a loading charge at the specimen in the variety of 20 to 50 psi/sec (0.15 to 0.35 M Pa/sec).
- During the software of the primary 1/2 of of the expected loading phase, a better charge of loading is allowed.
- No adjustment is made with inside the charge of motion of the platen at any time at the same time as a specimen is yielding swiftly right away earlier than failure.
- Load is implemented till the specimen fails, and the most load carried via way of means of the specimen all through the take a look at is recorded. The form of failure and the arrival of the concrete also are noted.
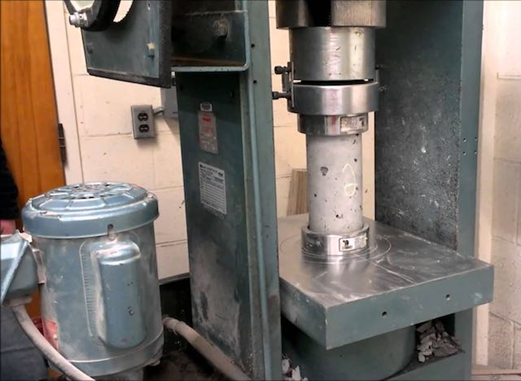
Fig no 8 Compression Testing Machine
Calculations:
Concrete Cylinder Loading Samples Compressive energy of the specimen is calculated through dividing the most load carried through the specimen all through the check with the common cross-sectional area.
Determine and specific the end result to the closest 10 psi (0.1 M Pa).
Key takeaways
The electricity of air-dried cores is on common 14 percentage large than the electricity of soaked cores.
Flexural Strength
Objective:
- To decide the Flexural Strength of Concrete, which comes into play whilst a avenue slab with insufficient sub-grade guide is subjected to wheel masses and / or there are extent modifications because of temperature / shrinking.
Equipment & Apparatus:
- Beam mildew of length 15 x 15x 70 cm (whilst length of mixture is much less than 38 mm) or of length 10 x 10 x 50 cm (whilst length of mixture is much less than 19 mm)
- Tamping bar (forty cm long, weighing 2 kg and tamping phase having length of 25 mm x 25 mm)
- Flexural take a look at gadget– The mattress of the checking out gadget will be furnished with metal rollers, 38 mm in diameter, on which the specimen is to be supported, and those rollers will be so hooked up that the space from centre to centre is 60 cm for 15.0 cm specimens or forty cm for 10.0 cm specimens.
- The load will be implemented via comparable rollers hooked up on the 1/3 factors of the assisting span that is, spaced at 20 or 13.3 cm centre to centre.
- The load will be divided similarly among the 2 loading rollers, and all rollers will be hooked up in this sort of way that the burden is implemented axially and without subjecting the specimen to any torsion stresses or restraints.
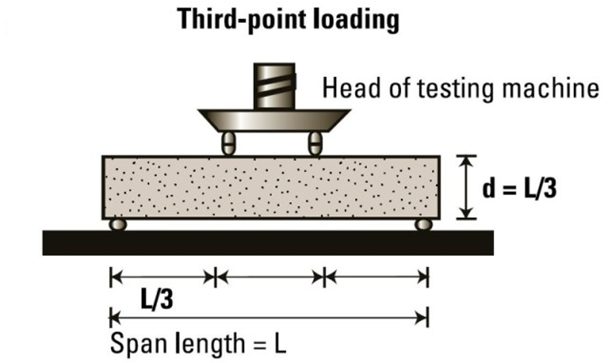
Fig no 9 Flexural testing machine
Procedure:
- Prepare the check specimen via way of means of filling the concrete into the mold in three layers of about identical thickness.
- Tamp every layer 35 instances the use of the tamping bar as distinct above.
- Tamping have to be disbursed uniformly over the whole cross section of the beam mildew and in the course of the intensity of every layer.
- Clean the bearing surfaces of the assisting and loading rollers , and get rid of any free sand or different cloth from the surfaces of the specimen in which they may be to make touch with the rollers.
- Circular rollers synthetic out of metallic having pass phase with diameter 38 mm may be used for presenting assist and loading factors to the specimens.
- The duration of the rollers will be at the least 10 mm greater than the width of the check specimen.
- A general of 4 rollers will be used, 3 out of which will be able to rotating alongside their very own axes.
- The distance among the outer rollers (i.e. span) will be 3d and the gap among the internal rollers will be d.
- The internal rollers will be similarly spaced among the outer rollers, such that the whole gadget is systematic.
- The specimen saved in water will be examined right away on elimination from water; while they may be nevertheless wet.
- The check specimen will be positioned with inside the device efficiently targeted with the longitudinal axis of the specimen at proper angles to the rollers.
- For mould specimens, the mold filling route will be ordinary to the route of loading.
- The load will be implemented at a price of loading of 400 kg/min for the 15.0 cm specimens and at a price of 180 kg/min for the 10.0 cm specimens.
Calculation:
- The Flexural Strength or modulus of rupture (fb) is given via way of means of
- F b = pl/bd2 (while a > 20.0cm for 15.0cm specimen or > 13.0cm for 10cm specimen)
O r
- F b = 3pa/bd2 (while a < 20> 17.zero for 15.0cm specimen or < 13> 11.0cm for 10.0cm specimen.
Where,
a = the gap among the road of fracture and the closer assist, measured at the middle line of the tensile aspect of the specimen
b = width of specimen (cm)
d = failure factor intensity (cm)
l = supported duration (cm)
p = max. Load (kg)
Safety & Precautions:
- Use hand gloves while, protection footwear on the time of check.
- After check transfer off the device.
- Keep all of the uncovered metallic elements greased.
- Keep the manual rods firmly constant to the bottom & pinnacle plate.
- Equipment have to be wiped clean very well earlier than trying out & after trying out.
Key takeaways
1. Beam mildew of length 15 x 15x 70 cm (whilst length of mixture is much less than 38 mm) or of length 10 x 10 x 50 cm (whilst length of mixture is much less than 19 mm)
Indirect Tensile Strength
- Indirect dynamic strength changes were tested from six samples: three dry samples and three samples exposed to water.
- During the indirect strength test, the sample is attached between two load strips and loaded freely at a speed of 50mm / min.
- The maximum load on the crack is measured. The relationship of energy values before and after water storage is determined, and is called the Indirect Tensile Strength Ratio (ITSR).
- Similar to the indirect strength test, a single-axial direct tensile test was initiated to investigate the strength structures of the study. Also, the strength was determined before and after preparing the test sample in the bath water according to EN 12697-12 B.
- The test samples used in this study included prismatic samples of the asphalt compound, as well as rods extracted from the rock and glued together with bitumen film.
- In the testing of dominant asphalt beams, every six beams are cut into slabs of composite asphalt composite (three dry, three wet). Adapters are attached with adhesives to the two parts of the sample surface.
- This is required to load samples into the machine. Strength strength is applied at a speed of 1.5mm / min at a temperature of 15 ° C. After the sample cracking, the strength of the strength is determined from high pressure, and the exact amount of strength strength (DTSR) accordingly.
- Similarly, direct strength testing was also applied to the extruded walls. On the rock covered and glued together the bitumen film.
- The power test is performed with different loading speeds and test temperatures. The broken sample.
- The materials investigated in this study include various types of bitumen (50/70, 70/100), bitumen modified polymer (PmB 40 / 100-65H, PmB 45A), of a wide range of natural materials from adhesive adhesives to adhesive markers. Fine (basalt, Taunusquarzite, limestone, granite, gabbro), and four types of asphalt mixtures (AC 11, AC 16, SMA 11, PA 8).
- Details of the composite, bitumen-aggregate composites, types of asphalt composites and related tests. Preliminary tests have shown that high image quality is very important for reproduction, because both the base installation and the descent frame depend on contrast of the image brightness.
- Therefore, image quality was guaranteed by the introduction of low levels of brightness, contrast, and sharpness of the image as measured by DSA1 software.
- About 10% of the images produced failed to meet these standards and were not included in further analysis. A small number of usable metrics are defined as 30 data points per bit bitumen.
- The data only show slightly different outputs for multiple samples, with the exception of PE6506, and the standard deviation (SD) of the method generally compared the differences between the contact angles of different locations.
- To determine whether communication angles are very different or not, statistical testing methods have been used. The first Shapiro- Wilk test was used for standardized testing. It confirms the general distribution of data. Subsequently, variance analysis (ANOVA), in particular data was subjected to the F test.
- Including all samples tested, the F test rejected the absurd notion that communication angles are very different, i. e. a group of mediators is very different from each other.
- As the mean values of PE6506 deviated significantly from the data of other bitumen, the test was repeated without PE6506. The result shows that in this experiment only PE6506 can be separated from a number of other samples, which can also be separated between them.
- Pendant suction measurements are performed using five bitumen and bitumen precursors. Excess power is measured as a heat function.
- Linear regression analysis can be used in addition to other adjacent conditions because the samples show a very similar pattern at higher temperatures, but a different tendency to deal with lower.
- For example, the two releases include a 95% confidence interval time. Places are very advanced. The results of the addition of all the bitumen studied including error bars, which are found in the external confidence interval.
- The general overlap indicates that this method cannot distinguish between the tested samples. Therefore, the development of testing in relation to rebirth is necessary. The use of small glass slides as a basic model of bitumen-mineral aggregate interface has several advantages.
- First, the surface is perfectly smooth and chemically uniform. Second, the chemical properties of glass are similar to the composition of highly acidic minerals, which usually have a very high content of SiO 2.
- To test the strength of this test, two samples of bitumen (50/70 and 70/100) and a mixture of these bitumen and adherence agent were tested (50/70 + and 70/100 +). New drops of bitumen in the glass gave the same effect to all bitumen.
- After being stored at 70 ° C for 30 minutes, in addition to the bitumen softening points (50/70 and 50/70 +: 48 ° C; 70/100 and 70/100 +: 45 ° C) the results were different. Communication angles are very different from each other. The contact angles of pure bitumen are around 6 ° below the mixtures.
- This means, however, that wettabilities are worse with bitumen containing the input. The final variation of this test was the introduction of static water storage.
Key takeaways
- Indirect dynamic strength changes were tested from six samples: three dry samples and three samples exposed to water.
- During the indirect strength test, the sample is attached between two load strips and loaded freely at a speed of 50mm / min.
Core Test
- Basic concrete testing is the most popular and well-established test method for the compressive strength of hard concrete. Critical concrete testing makes visual inspections of the internal parts of the concrete member also related to strength limitations Portable coring enables the inspection of other reinforced concrete structure structures with solid concrete testing
- In any case, the need to perform basic concrete tests often stems from the failure of concrete cubes / cylinders to get a realistic view of the strength of concrete as it exists in construction materials
Sampling of concrete core
It is very important that basic concrete samples are taken according to the guidelines given below
- Cores should be taken using pieces of diamond-filled spinal cord.
- Cores tested for power structures should have a minimum diameter three times the size design size of a rated set or 50 mm. Whoever is great
- Where possible, cores tested for energy structures should be at least twice their length width
- As far as it is concerned that the reinforcing metal should not be inserted into the spine to be tested for strength. The size, number, and location of the metal reinforcement in the proposed primary area can be determined by using magnetic resonance imaging such as a retrieval meter (cover meter) or by ground-based radar testing or by using a pull-out radar system. If the spine contains a flexible reinforcing steel, a certain effect on the strength should be expected There is a possibility of a decrease in the strength of the concrete slab depending on the position of the steel. This effect is especially important when the metal is very far from the end of the set.
- As far as possible, the foundation pit should penetrate completely into the concrete section. This prevents spinal fractures and facilitates their removal. On the other hand, if drilling is not possible due to the size and configuration of the building in the area where the coring is planned, an additional 50 mm should be bound as a share of potential damage to part of the context.
- One root should not be used to diagnose a specific problem. When cores are taken gain power, a minimum of three characters need to be removed from each location. The amount of concrete strength in the hole should be taken as the benefit of these grains
- Special care needs to be paid when choosing a place for the concrete for standing concrete members such as walls, deep beams, etc. This is due to the differences in high-rise concrete structures due to differences in laying and mixing processes, separation, and bleeding. It is known that in general, the strength of concrete decreases as its height within the placement of membership increases.
- The exact history of structural treatment is often difficult to obtain so the effect of cooling the ammunition is also uncertain. When there is no wet treatment, no power expectations should be expected
- The direction of the ball also affects the strength of the bullets. Horizontally bound cores usually have lower power than direct bound calls,
- When cutting the core, the integrity of the concrete structure in the full section (c / s) is possible is affected to some degree. This feature should be taken into account when selecting a location where the file the core should be taken
Concrete Test procedure
Concrete pieces are usually cut with rotating cutting tools with diamond pieces. The cylinder sample is obtained by concluding its unequal pieces of equal parts, square, and embedded.
Cores are inspected visually to pay attention to the distribution of the composite, the compaction of concrete (non-air visibility), and the presence of metal, etc. The concrete slab should be soaked in water, soaked in melted sulfur so that it ends up parallel to the right angle. It is also tested on a pressure-testing machine in wet conditions in accordance with BIS 1881: Part 4: 1970 or ASTM 42-77.
Use of concrete core sample
- Water or gas leakage
- Chemical analysis
- ASHTO chloride permeability testing
- Determination of strength and resilience
- Depth of concrete installation
- Petro graphic Analysis
Key takeaways
- Cores should be taken using pieces of diamond-filled spinal cord.
- Cores tested for power structures should have a minimum diameter three times the size design size of a rated set or 50 mm. Whoever is great
- Where possible, cores tested for energy structures should be at least twice their length width
Non-Destructive Test - Rebound Hammer
Objective:
- The rebound hammer technique might be used for:
- Assessing the possibly compressive electricity of concrete with the assist of appropriate correlations among rebound index and compressive electricity,
- Assessing the uniformity of concrete,
- Assessing the excellent of the concrete in relation to traditional requirements, and
- Assessing the excellent of 1 detail of concrete when it comes to another.
Principle:
- When the plunger of rebound hammer is pressed in opposition to the floor of the concrete, the spring controlled mass rebounds and the volume of such rebound relies upon up on the floor hardness of concrete.
- The floor hardness and consequently the rebound is taken to be associated with the compressive strength of the concrete.
- The rebound is examine off alongside a graduated scale and is unique as there sure variety or rebound index.
Procedure:
- For trying out, smooth, easy and dry floor is to be selected. If loosely adhering scale is present, this have to be rubbed of with a grinding wheel or stone. Rough surfaces due to incomplete compaction, lack of grout, spalled or tooled surfaces do now no longer deliver dependable outcomes and have to be avoided.
- The factor of effect is to be at the least 20 mm far from any facet or form discontinuity.
- For taking a measurement, the rebound hammer is to be held at proper angles to the floor of the concrete member. The check can as a result be performed horizontally on vertical surfaces or vertically upwards or downwards on horizontal surfaces. If the state of affairs demands, the rebound hammer may be held at intermediate angles additionally, however in every case, the rebound variety may be unique for the equal concrete.
- Rebound hammer check is performed round all of the factors of remark on all on hand faces of the structural detail. Concrete surfaces are very well wiped clean earlier than taking any measurement.
- Around every factor of remark, six readings of rebound indices are taken and common of those readings after deleting outliers as consistent with IS: 8900-1978 turns into the rebound index for the factor of remark.
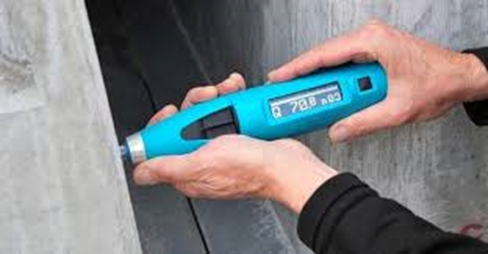
Fig no 10 Showing Rebound Hammer
Interpretation Of Result:
- The rebound hammer technique offers a handy and speedy indication of the compressive energy of concrete via organism appropriate correlation among the rebound index and the compressive energy of concrete. The process of acquiring such correlation is given in 4.2.
- It is likewise mentioned that rebound indices are indicative of compressive energy of concrete to a constrained intensity from the floor. If the concrete in a selected member has inner micro cracking, flaws or heterogeneity throughout the cross-section, rebound hammer indices will now no longer imply the equal.
- As such, the estimation of energy of concrete with the aid of using rebound hammer technique can't be held to be very correct and in all likelihood accuracy of prediction of concrete energy in a shape is ±25 percent.
- If the connection among rebound index and compressive energy may be checked with the aid of using assessments on center samples acquired from the shape or well known specimens made with the equal concrete substances and blend proportion, then the accuracy of consequences and self belief thereon are substantially increased.
Key takeaways
- The rebound is examine off alongside a graduated scale and is unique as there sure variety or rebound index.
Ultrasonic Pulse Velocity
- This take a look at is accomplished to evaluate the nice of concrete with the aid of using ultrasonic pulse pace technique as according to IS: 13311 (Part 1) – 1992. The underlying precept of this take a look at is –
- The technique includes measuring the time of journey of an ultrasonic pulse passing via the concrete being tested. Comparatively better pace is acquired whilst concrete nice is ideal in phrases of density, uniformity, homogeneity etc.
- Procedure to decide energy of hardened concrete with the aid of using Ultrasonic Pulse Velocity:
- Preparing for use: Before switching at the ‘V’ meter, the transducers ought to be linked to the sockets marked “TRAN” And ” REC”.
- The ‘V’ meter can be operated with either:
a) The inner battery,
b) An outside battery or
c) The A.C line.
- Set reference: A reference bar is supplied to test the tool zero. The pulse time for the bar is engraved on it. Apply a smear of grease to the transducer faces earlier than putting it on the other ends of the bar. Adjust the ‘SET REF’ manage till the reference bar transit time is acquired at the tool read-out.
- Range selection: For most accuracy, it's miles endorsed that the 0.1 microsecond variety be decided on for route duration up to 400mm.
- Pulse pace: Having decided the maximum appropriate take a look at factors at the fabric to be tested, make cautious dimension of the route duration ‘L’. Apply couplant to the surfaces of the transducers and press it tough onto the floor of the fabric. Do now no longer flow the transducers whilst a analyzing is being taken, as this could generate noise indicators and mistakes in measurements. Continue keeping the transducers onto the floor of the fabric till a steady analyzing seems at the show, that's the time in microsecond for the ultrasonic pulse to journey the distance ‘L’. The imply price of the show readings ought to be taken whilst the gadgets digit hunts among values.
Pulse pace= (Path duration/Travel time)
- Separation of transducer leads: It is really helpful to save you the 2 transducer leads from getting into near touch with every different whilst the transit time measurements are being taken. If this isn't always accomplished, the receiver lead would possibly pick-up undesirable indicators from the transmitter lead and this will bring about an wrong show of the transit time.
Interpretation of Results:
- The nice of concrete in phrases of uniformity, occurrence or absence of inner flaws, cracks and segregation, etc, Indicative of the extent of expertise employed, can as a consequence be assessed the use of the recommendations given below, that have been advanced for characterizing the nice of concrete in systems in phrases of the ultrasonic pulse pace.
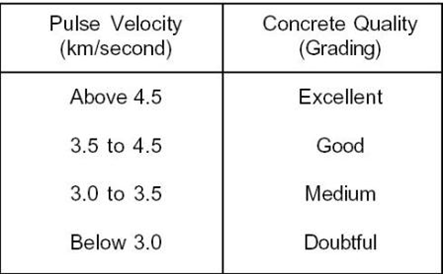
Fig no 11. Table of pulse velocity
Key takeaways
2. Set reference: A reference bar is supplied to test the tool zero. The pulse time for the bar is engraved on it. Apply a smear of grease to the transducer faces earlier than putting it on the other ends of the bar. Adjust the ‘SET REF’ manage till the reference bar transit time is acquired at the tool read-out.
Pullout Test and Impact Echo Test
Pullout Test
The principle
This test is based on the principle that the force required to extract a metal coating embedded in concrete is equal to the strength of the concrete.
Test Process
Remove the insert (shown on the fig tree) embedded in the empty concrete during pouring. When power is required to be determined, power is applied to the embedded end. The power required to issue a meeting is measured.
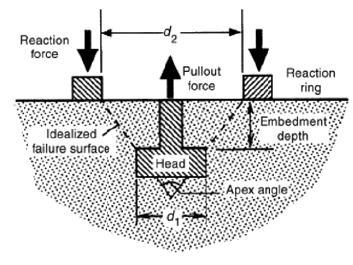
Fig no 12. Pull out the concrete test
Limitations
The steel assembly should be embedded in concrete at the time of pouring so testing may not be carried out in the years to come.
Damage to damaged concrete is required.
Evaluation
- The extraction assembly is pulled by a concrete cone, which is responsible for friction and shaving and the force required to exit is related to the cutting strength of the concrete and not the compressive force.
- The rate of dissipation in the compression force decreases slightly with increasing power level.
- Removal cannot be performed until complete. It is sufficient to insert a fixed power into the embedded pole and if not removed, the supplied power is assumed to exist.
- According to Malhotra, the output test is higher than the Schmidt hammer and the input test because a large volume and depth of concrete are involved in the test. Post-test concrete repairs are also required. The relationship between the force of gravity and gravity is shown in the figure below.
Impact Echo Test
Impact-Echo is a non-destructive exploration method for exploring concrete structures and stone structures. The test uses pressure waves (sound) that are usually made of impact-impact concrete, and to record thinking and emissions from internal errors and other parameters (Echo). Typically, a heartbeat is performed with an effect in one place. The resulting wave of depression is spreading in all directions. In this regard, the generated wave does not have a directional pulse generated by a large transducer (as in the case of ULTRASONIC PULSE VELOCITY). As the reflection reaches in all directions, the test method works well for thin objects, such as piles where the outer boundary directs the wave to the pile. In this particular application, the test is set as the low-level strength test. Learn more about the PILE INTEGRITY TEST.
Concept Behind Impact-Echo Method
The concept of Impact-Echo testing is shown in Figure. The mechanical impact of the concrete surface is used to produce a pressure wave. The production pulse creates a spread across the concrete next to circular waves such as P- and S-waves. Another is the surface wave (R) that moves over.
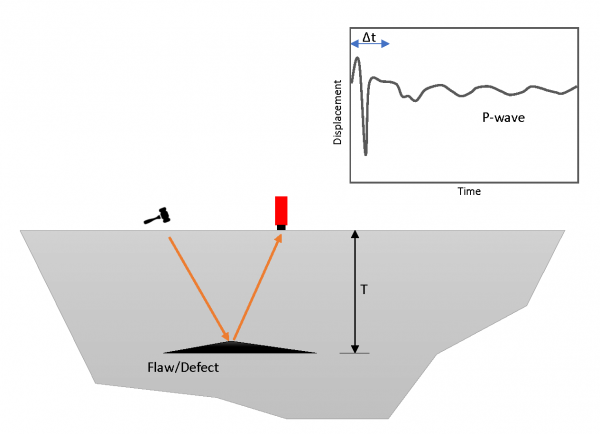
Fig no 13. Impact echo method
As the P- and S waves propagate inside the concrete object, they are indicated by internal interactions (concrete-split, air-concrete, concrete -rebar) or external boundaries. The arrival of these echo in the face causes migration. This migration can be measured by placing a sensitive transducer (which converts the transmission or acceleration of electrical energy). Data is recorded through a data acquisition and data entry system.
Analyses Impact-Echo data
Data analysis can be done in Time Domain, or Frequency Domain. While time domain analysis seems to be the best way to define sensitive data (as in the case of bulk testing), it can be a much more complex approach in the case of small slabs. In these sections, signal analysis in the domain of frequency is popular.

Fig no 14. Analysis of impact echo method
The Fast Fourier transform (FFT) process is used to analyze digital frequency frequency recordings. In this way, the wave form can be represented as a total of sine curves, each with a certain height, frequency and phase shift. According to N. J. Carino. This method is used to calculate the amplitude magnitude of a frequency form, which gives the relative height of the fractional frequencies in the wave form.
Impact-Echo Technique Applications
Impact-Echo is an effective test solution with a variety of applications in assessing the condition of concrete structures. The test can be used to:
1- Measure the thickness of the concrete labs and walls
2- Measure the thickness of the concrete walls and the tunnel line
3- Identify deformities such as delamination in concrete books.
4- Measure the storage condition of concrete, dams, tunnel lamps, sea walls.
Key takeaways
- This test is based on the principle that the force required to extract a metal coating embedded in concrete is equal to the strength of the concrete.
- Impact-Echo is a non-destructive exploration method for exploring concrete structures and stone structures. The test uses pressure waves (sound) that are usually made of impact-impact concrete, and to record thinking and emissions from internal errors and other parameters (Echo).
- Good quality concrete is actually a compact mixture of cement, composite and good mixing with water that mixes into a hard mass due to the chemical action between cement and water.
- Each of the four regions has a specific function. The coarser collection serves as a filler. A good collection fills the gaps between the attachment and the green combination. Cement by contact with water acts as a bond.
- The flow of the mixture is aided by the adhesion of cement, fines to this day, increasingly using mixtures.
- Most of the reinforced concrete materials depend on the care used in all stages of concrete production. The logical separation of concrete ingredients is the core of the mixing design.
- However, it may not guarantee the achievement of the goal of quality workmanship. The purpose of quality control is to ensure the production of concrete of the same power from batch to batch.
- This requires that certain rules be followed in the various stages of concrete production and discussed below. The stages of concrete production are:
1. Batching and measurement of material
2. Mixing
3. Transport
4. Placement
5. Compacting
6. Curing
7. Finishing
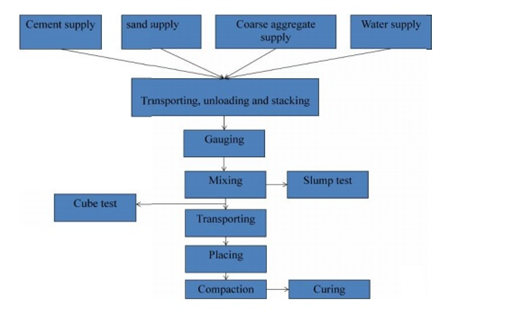
Fig no 15. Manufacturing process of concrete
Batching of material
- For good quality concrete should be used the correct and accurate amount of all ingredients. Combined, cement and water must be measured with an accuracy of 3 percent of batch quantity and admixtures at 5 percent of the total value. There are two most common forms of baking material, batching volume and heavy batching. Factors affecting the choice of baking method by the size of the work, the required production rate, the required batching performance standards. It is recommended for the most important tasks.
a) Volume batching
b) Weight batching
Mixing
1. Hand Mixing
2. Mixing Machine
a) Tilting mixers
b) Non- tilting mixer
c) Reversing Drum mixer
d) Pan type or stirring mixer
e) Transit mixer
f) Charging Mixer and mixing time
The order for the ingredients in the mixer is as follows:
- About 25 percent of the water needed for mixing is initially placed in the mixing tank to prevent any cement attachment to the rings and bottom of the drum. Then the ingredients are extracted in excess. To skip over the loading sequence should be to insert the first half of the coarse cement and then the composite half to be on top of this complete cement and the aggregate to balance. After adding the ingredients to the drum equal volume was introduced. The mixing time is calculated from the total water added to the mixture.
- The speed of the aggregates is usually 15 to 20 per minute. With proper mixing, the number of changes per minute required by the drum is 25 to 30. The mixing time also depends on the mixing capacity
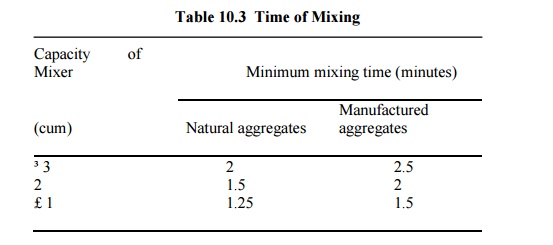
Fig no 16. Table of mixing
- Poor quality of concrete is obtained when mixing time is reduced. On the other hand if the mixing time is extended it is not economical. However, it is found that when the mixing time is extended to 2 minutes the compressive strength of the produced concrete is improved and beyond this time the improvement of the compressive strength is not significant. Prolonged mixing can cause separation. Also, due to the long mixing times water can get in or out and lead to loss of function and energy.
Transporting
The concrete should be moved to the storage area immediately without the loss of homosexuality acquired during mixing. a maximum of 2 hours from mixing time is allowed if trucks have an agitator and 1 hour using trucks without stimulants to move the concrete. And it must be ensured that separation does not occur during travel and placement. The methods used to transport concrete depend on the quality and value of the work, the distance to the placement site, and the location. Some of the concrete delivery methods are below:
a. Mortar pan
b. Wheel barrow
c. Chutes
d. Dumper
e. Bucket and ropeway
f. Belt conveyor
g. Skip and hoist
h. Pumping
Placing
- Achieving quality concrete should be placed very carefully to protect the homosexuality achieved during mixing and to avoid transport segregation. Studies have shown that delays in the installation of concrete results in gaining greater compressive strength as long as the concrete is not sufficiently compacted. In dry mixes in hot weather a delay of half an hour is allowed and in wet mixtures when it is cold it can be a few hours. The various conditions in which concrete is applied are discussed below.
Foundations
- Concrete foundations for walls and columns are provided underground. Before laying concrete on the foundation all open ground, tree roots etc., are removed. If the area is found dry it is made wet so that the soil does not absorb water from the concrete. On the other hand when the foundation bed is wet the water and mud are removed and the cement is sprinkled before laying the concrete.
Beams, columns and slabs
- Before laying the concrete, the forms must be inspected for proper alignment. They should be strong enough to withstand the weight of concrete and construction loads without undue damage. The forms should be light enough to avoid any mud loss that has resulted in concrete mixed with bees. The inside of the forms should be cleaned and oiled before use to avoid any adhesion to the concrete and forms and make it difficult to remove them.
- Concrete should not be discarded but should be placed in a place to protect against discrimination. It should be lowered as high as possible. It should be placed in one place on the formwork and allowed to flow in separate ways to take care of the bee colony.
- The formation of seas should be avoided. Can be tested by preventing concrete thickness by 150-300 mm with r c c function. Laitance, however, if constructed must be removed before laying the next layer of concrete. Several such layers form an elevator, as long as they follow each other fast enough to avoid cold joints. The top of the previous elevator is kept rugged and all the money spent is wiped out before setting the next elevator.
- Firmness should be checked for firmness and clean face. Rust or loose scales if present, are removed with a wire brush. Paint, oil or grease if found should be removed. a small tightening cover should be checked before assembly.
Mass concreting
- Where the concrete will be laid in bulk as a foundation for raft, dam, bridge, pier etc., the concrete is laid in sections of 350-450 mm in diameter. Several such layers arranged in quick succession form an elevator. Before applying the concrete to the next lift, the front elevator area is thoroughly cleaned with water jets and scrubbing with a wire brush. In the case of dams, sand explodes.
- Laitance and lax matter are removed and cement mortar is applied. Where the concrete is subjected to lateral thrust, binding bars or binding stones are provided to form the key between the various layers.
Concreting Highways and Runways
- Concrete is placed in the areas of highway, open road, or floor slabs. First the soil on which the concrete is to be placed is prepared and all loose material and grass are removed etc. The ground is wet and compacted. The subgrades into which the concrete is to be placed should be well mixed and diamond-plated to avoid any moisture loss in the concrete. The concrete is then placed elsewhere. This allows the concrete to pass through enough and the cracks do not grow after that. Concrete is not placed in a pile in one place and then pulled out, instead it is placed in the same size.
Concreting underwater
- Concrete can be placed under water with the help of dumping buckets. The concrete is soaked in water from a water-tight bucket. When you get to the floor the bucket is made open and the concrete is discarded. In this process a certain amount of cement is washed away resulting in a decrease in the strength of the concrete. Another way to make underwater concrete is to fill a bag of cement with a dry or dry mixture of cement and aggregates and lower it into the storage area. The downside to this approach is that the concrete will fill the gaps filled with the bags with the guns.
- A good way to put concrete under water is to use a termie pipe. Concrete is poured into it by a ditch. The lower edge of the pipe is covered with thick ploythene paper, below the pipe in the installation area. Concrete (150-200 mm fall) is poured into the mortar until the entire pipe is filled with cement. The pipe is slightly raised and given a jerk, the polythene metal cover falls off and the concrete is shown. It must be ensured that the end of the pipe stays inside the concrete so that water does not enter the pipe. The pipe is then filled with concrete along the border and the process is repeated to the concrete level above the water level. No reduction is required for underwater concrete as combined with hydrostatic water pressure. Concrete can also be placed under water with the help of pipes and pumps.
Compaction of concrete and curing process of concrete
1) Compaction of concrete
- Concrete should be thoroughly compacted and fully work around the reinforcement and into the corners of the formworks
- Concrete shall be compacted using mechanical vibrators
- Whenever vibration has been applied externally the design of formwork and the deposition of vibrators should receive special consideration to ensure efficient compaction and to avoid sir face blemishes
2) Curing process of concrete
- Curing of concrete is defined as the process of maintaining the moisture and temperature condition of concrete for hydration reaction to the normally so that the concrete develops hardened and properties over time
- The main components which need to be taken care of your heat and time during curing process
- Curing is the process of preventing the loss of moisture from the concrete which maintaining a satisfactory temperature effect
- If the cement has high rate of strain development and if the concrete contains granulated blast furnace and flue Ash then,
- The curing should also prevent the development of high temperature gradients within the concrete
a) Moist curing
- Surface of the concrete shall be kept continuously in Dam or wet condition by covering with the layers of materials like checking Canvas etc.
- It should be kept continuously wet for at least 7 days from the date of placing concrete.
- In case of ordinary Portland cement at least 10 days. Where mineral admixture or blended cement are used.
- The period of curing shall not be less than 10 days for concrete exposed to the dry and hot weather condition.
- In case of concrete where mineral admixture or blended cement are used it is recommended that above minimum period may be extended 14 days.
b) Membrane curing
- Approved curing compounds may be used in place of moist curing with the permission of engineer in charge.
- Search compound shall be applied to all exposed surfaces of the concrete as soon as possible after the concrete has set.
- Impermeable membrane such as polyethylene sheeting covering closely the concrete surface may also be used to provide effective barriers against evaporation.
- For the concrete containing Portland pozzolana cement, Portland slag cement or mineral admixture period of curing may be increased.
NOMINAL MIXES
- In concrete mix concrete, all ingredients and their size are determined by standard definitions. This ratio is specified in the cement ratio to the specific energy gain combination.
- Mixing ratios such as 1: 1.5: 3, 1: 2: 4, 1: 3: 6 etc. They were adopted by mixing concrete without a scientific basis, only on the basis of previous studies of solidarity. Therefore, acceptance of ordinary concrete or not to mention, the mixing of preference is preferred for simple, insignificant and minimal concrete works.
- According to the 'Indian Standard- IS 456: 2000', pre-mixed concrete can be used for M20 grade concrete or lower grade such as M5, M7.5, M10, M15.
Proportion of nominal mix as per Indian Standard
- The volume of composite materials under M20 grade concrete will comply with IS 456: 2000
- According to IS 456: 2000, in the composition of the composition can be adjusted the estimated values if the water level will be increased to overcome the difficulty of laying and density of concrete so that the water level of the cement is maintained as specified.
- Automatic mixing usually consists of volumetric batching. The measurement is usually determined by weight, and in combination it is converted to a volume value, i.e. in the case of one bag of cement, i.e. 50 kg of standard measuring boxes are made on site, at the rate of one bag of cement. These measuring boxes are called box gauges.
Advantages of nominal Mix Concrete
01. A self-proclaimed mix is a pre-determined concrete because the scale is pre-determined.
02. It is easy to do in the construction site.
03. It does not take much time to determine the value because the size is already provided with the standard code.
04. There is no need to find people who have the skills to make concrete mixing name.
Disadvantages of nominal mix concrete
01. The great recurrence of the mix of claims is that, it is based on past experience and studies of art, and has no scientifically proven method.
02. It can create or build well-designed energy unless all other factors such as density, w / c ratio, concrete treatment are strictly adhered to.
03. The amount of water cement is considered by thought and, if left unchecked, sometimes leads to bleeding and separation of the concrete which leads to poor performance and therefore impairs the strength of the concrete.
04. No consideration of composite structures such as classification and quantity of composite items etc.
05. In a word mix, cement content is sometimes used in excess, which increases the total cost of construction.
06. No laboratory tests are performed to ensure the quality of the new concrete.
07. This combination does not consider and evaluates the specific properties of each ingredient. For example, if we take cement as part, the softness of the cement, the quality of the cement and the type of cement, the size and layout of the composite etc. It is usually not counted individually when making this fake assertion mix.
Key takeaways
- In concrete mix concrete, all ingredients and their size are determined by standard definitions. This ratio is specified in the cement ratio to the specific energy gain combination.
- Mixing ratios such as 1: 1.5: 3, 1: 2: 4, 1: 3: 6 etc. They were adopted by mixing concrete without a scientific basis, only on the basis of previous studies of solidarity. Therefore, acceptance of ordinary concrete or not to mention, the mixing of preference is preferred for simple, insignificant and minimal concrete works.
- According to the 'Indian Standard- IS 456: 2000', pre-mixed concrete can be used for M20 grade concrete or lower grade such as M5, M7.5, M10, M15.
Freeze-Thaw Effect:
Concrete is very strong in compression but relatively weak in tension. It can and often does crack. Concrete is also fairly porous and subject to forces that absorb and release water. Absorbed water can freeze within the concrete and cause spalling and cracking.
Chemical Attack:
Chemical attack can occur because concrete is alkaline and chemically reactive. It can be attacked by acids; some alkalis; numerous salt solutions; and organics such as fermenting liquids, sugars, and animal oils, especially if they contain free acids.
Crazing:
This is a network of very small surface cracks usually spreading out over large areas or the entire surface. Crazing is caused by finishing the concrete with bleed water on top. The bleed water is forced down into the surface by the finisher’s trowel. This increases the ratio of water to cement, creating a weak surface layer.
Scaling:
Thin flakes of concrete come loose and flake or peel off the surface. The sizes of the flakes vary, but they usually increase over time and with traffic. Conditions that cause scaling and include freeze/thaw cycles, deicing agents with calcium or sodium chloride, fertilizers containing nitrates, working in bleed water, or improper curing.
Blisters:
These are typically about 1/4 to 1 inch diameter, but it’s not impossible to get 3 to 4 inch blisters. They are not easily seen until they are broken by traffic. Blisters are caused by working and finishing the surface while water or air is still working its way up through the mix to the surface.
Spalling:
Spalling is similar to scaling except large chunks instead of just flakes break loose. This indicates a severe weakness in some parts or the entire project. It is more likely to happen during freeze thaw conditions.
Dusting:
Also known as chalking, this is a fine loose powder caused by the deterioration of a weak surface. Causes of dusting include working in bleed water, improper curing, a bad sand-to-cement ratio, or exposure to carbon monoxide caused by using an unvented heat source to keep a project warm.
Foreign Objects:
Foreign objects can often slip into the form prior to pouring and may not become evident until after the forms are stripped. If fully embedded, the foreign object does not create a coating problem. But a piece of rope on the surface disappearing into the concrete is a problem. It must be removed, usually by chipping, and the concrete must be restored.
Efflorescence:
Efflorescence is more likely to be found on concrete that has been in place for a while. Concrete contains water-soluble salts. As water from the interior of the concrete migrates to the surface and evaporates, salts are deposited on the surface, usually as a white stain. Efflorescence can occur with concrete, brick, or concrete block construction. It can be removed with acid etching. The best way to prevent its recurrence is with adequate waterproofing.
Service / Market Area:
For industrial and commercial flooring projects we work in Michigan cities such as Muskegon, Norton Shores, Newaygo, Traverse City, Big Rapids, etc.
- Many types of admixtures or additives change the performance of a new concrete, either by construction or as a side effect.
- Surfactants such as super plasticizers reduce the attraction between cement and composite particles, allowing compounds that can flow without negative energy and the effects of excess water separation.
- The insertion of internal admixtures of durability / dissolving solids produces internal bubbles of a controlled size that can make it easier to eliminate, although overuse produces an adhesive mix with a different effect.
- The pressure of the concrete is eight times greater than its strength.
- This refers to the established relationship between the compressive strength and the strength of the concrete. In fact there is a close relationship but not a direct relationship.
- The degree of stiffness and pressure is low at high pressures.
- Experimental results also showed that concrete in stress and stress (both direct and indirect tension) is highly correlated but the relationship does not have a direct equation.
- The degree of strength and durability depends on the strength of the concrete.
- Thus, the increase in tensile strength, increases the tensile strength, but the rate of increase in tensile strength decreases steadily.
- The strength of concrete is more sensitive to improper treatment than to compressive strength.
This is possible for two reasons:
(a) The formation of a low-grade gel due to improper treatment.
(b) The formation of multiple shrinking cracks due to improper treatment. The use of pozzolanic materials showed an increase in strength.
- The Central Road Research Institute Delhi has conducted extensive research to build a relationship between the strength and durability of concrete in the construction of concrete roads.
- Based on the research experimental data, CRRI suggested the following relationship between flexural strength and concrete compression strength:
y = 11 x - 3.4
- Where is the compressive strength of MPa concrete and x and its flexibility. This relationship depends on the size of the coarse aggregate. Energy is available to vary in type and quantity of composite.
Relationships are renewed below:
(a) With a crushed stone of 20 mm y = 15.3 x - 9.0
(b) 20 mm Natural Graval y = 14.3 x - 10.4
(c) For 40 mm Crushed Stones y = 9.9 x -5.5
(d) 40 mm Natural Graval y = 9.8 x - 2.5
Key takeaways
The pressure of the concrete is eight times greater than its strength.
This refers to the established relationship between the compressive strength and the strength of the concrete. In fact there is a close relationship but not a direct relationship.
There are three main factors that affect concrete compression results: the specimen size, shape, and friction at its ends. These factors affect the observed phenomena, and they affect each other. This paper aims to review the current knowledge on concrete compression and the effect of size, shape and friction on it. Understanding their effects is essential for a safer design and more effective testing.
- Creep and thinning concrete are the two most visible features of concrete. The shrinkage of concrete, derived from calcium silicate hydrate (C-S-H) in a hardened Portland cement compound (which is responsible for mineral compounds), is quite different from the tilt of metals and polymers.
- Unlike metal cracks, it occurs at all levels of stress and, within the service level of stress, depends on what is stressed if the pore water content remains the same.
- In contrast to the eruption of polymers and metals, it exhibits several months of aging, caused by chemical hardening due to hydration that strengthens the formation of micro-organisms, and age-old aging, resulting in long-term resting of small equal pressure in nano- low CSH formation. When the concrete is completely dry, it does not move, but it is almost impossible to dry the concrete completely without severe cracking.
- Changes in water content in the pore due to dryness or watering processes cause significant changes in the volume of the concrete in non-load-bearing species. They are called shrinkage
- The age-old insect varies logarithmically over time (except for the final asymptotic value), and over normal life spans can receive values 3 to 6 times larger than the initial stretch problem. When deformation formation is abruptly induced and held inconsistently, the movement causes a break in the pressure produced in moderation. After discharge, increased recovery occurs, but in part, due to aging.
- In practice, travel during drying is inseparable from diminishing. The flow rate increases with the rate of change of pore humidity (e.g., vapor pressure associated with the pores). In the size of a small model, the penetration during drying far exceeds the total reduction of load without load and the penetration of the closed-loop template. The difference, called the drying creep or Pickett effect (or pressure-induced decrease), represents a hygro-mechanical between pore changes and pore humidity.
- The drying of the high humidity is mainly due to the pressure pressures on the solid microstructure that measure the increase in capillary tension and the surface tension in the pore walls. At low pore humidity (<75%), the shrinkage is caused by a decrease in the binding pressure across all nano-pores less than 3 nm in diameter, filled with indicated water.
- The chemical processes of Portland cement hydration lead to another type of shrinkage, called automatic shrinkage, which is detected in closed specimens, i.e., without loss of moisture. In part, this is due to changes in chemical volume, but especially energy loss due to the loss of water used by the hydration reaction.
- It achieves only about 5% of the dryness in normal cones, which self-desiccate about 97% of pore humidity. However, it can be equivalent to the reduction of drying in today's high-strength concrete containers with very low cement levels, which can cause the floor to have a humidity of less than 75%.
- The creep comes from calcium silicate hydrate (C-SH) attached to Portland cement. It is caused by slips due to breakage of bonds, by restoration of bonds in nearby areas. C-SH is highly hydrophilic, and has a colloidal microstructure separated from a few nanometers upwards. The paste has a porosity of about 0.4 to 0.55 with a large internal surface, about 500 m2 / cm3. Its main component is tri-calcium silicate hydrate gel (3 CaO · 2 SiO3 · 3 H20, abbreviated C3-S2-H3). The gel forms particles of colloidal size, which are weakly bound by van der Waals forces.
- How it works and modeling is still debated. The structural model in the following scales is not only available but at the moment has a very solid theoretical basis and fits very well with the full range of test data available.
Key takeaways
- Changes in water content in the pore due to dryness or watering processes cause significant changes in the volume of the concrete in non-load-bearing species. They are called shrinkage
- A concrete blend is a mixture of 5 primary factor numerous proportions: cement, water, coarse aggregates, quality aggregates (i.e. sand), And air.
- Additional factors including pozzolana substances and chemical admixtures also can be integrated into the combination positive ideal properties.
- While a concrete blend layout is a system of choosing substances for a concrete aggregate and choosing their proportions.
- When designing a blend, you don't forget the favored power, durability, and workability of the concrete for the venture in question.
- Needless to say, Already-blend manufacturers attempt to locate the suitable proportions of those substances to optimize the concrete mixes and provide their concrete power, durability, workability, and different ideal properties.
- It’s crucial to optimize concrete to make sure the bottom keeping the very best power of your aggregate.
- Concrete blend layout is frequently mistake analysis “cement blend layout.” However, cement is since rely one of the substances of concrete.
- It is a binding substance that let sin concrete to set, harden, and cling to different substances.
- Therefore, it can't and ought to now no longer be used interchangeably with concrete blend layout.
Objective
The following are the objectives of the concrete mix design:
a. Finding the pressure force at a certain distance.
b. Maintain concrete mixing performance throughout the work.
c. By gaining strength.
d. Achieve economy by choosing the right concrete ingredients.
e. Getting the highest yield in a cement bag.
f. Avoid bee contact and bleeding.
g. Compliance with various levels.
h. Reduce concrete damage by proper measurement.
The proportioning of concrete mixes consists of determination of quantities of different concrete-making materials necessary to produce concrete having the desired workability and 28-days compressive strength of concrete for a particular grade of concrete and durability requirements. Emphasis is laid on making the most economical use of available materials so as to produce concrete of required attributes at the minimum cost.
Concrete has to be satisfactory both in fresh and hardened states. The proportioning of concrete mixes is accomplished by the use of certain established relationships from experimental data which provides reasonably accurate guidance for selecting the best combination of ingredients so as to achieve the desired properties of the fresh and hardened concrete. Out of all the physical characteristics of concrete compressive strength is often taken as an index.
- Strength and sturdiness of the concrete blend layout are established upon the subsequent factors:
- Grade designation: Concrete’s power is measured in N/mm2 whilst issue to check after curing in any curing medium. The preference of concrete grade relies upon on its utilization.
- Choice of cement: Cement preference varies relying on utilization. The cement have to be examined for overall performance required with the aid of using their utilization earlier than being examined with inside the layout blend.
- Choice of mixture size: Aggregates wanted for every blend depends upon the bodily houses wanted for the layout. All aggregates need to be nice sized earlier than use.
- Type of water: Any water used for concrete blend layout is to be examined earlier than use to make certain it's far with inside the variety of water required for concrete. Most all consumable water is right for concrete work, however have to nevertheless be examined.
- Water to cement ratio: The ratio of water to cement have to be examined for consistency, preliminary and very last setting, soundness of the cement, workability, hunch of the concrete and compacting factor.
- Workability: This is the degree of ease of blending concrete without segregation or bleeding. It by and large relies upon at the designed hunch of the concrete.
- Durability: This is the degree of the specified power (N/mm2) of any concrete grade after 28 days of curing. Durability have to be manipulate examined on site.
Key takeaways
- Here different type of factors which affects mix proportion are durability, workability, water to cement ratio, type of water, choice of mixture size, choice of cement, grade designation.
The following points highlight five methods of concrete construction. The methods are:
1. American Method of Mix Design
2. Graphic Method of Mix Design
3. Mix Design by Indian Standard Method
4. American Concrete Institute Method of Mix Design
5. Quick Method of Mix Design.
1. The American Way of Mixing Designs:
- The American Concrete Institute (ACI) approach is based on the fact that the given size of a mixture of water content per kilogram of concrete determines the performance of a concrete mix, usually independent of the equilibrium. It is therefore possible to start the mixing formation by selecting the water content in these tables.
- In addition it is also assumed that the maximum volume of the estimated quantity of the total value of the concrete depends only on the maximum size and the combination of good composites.
2. Graphic Method of Mix Design
- This approach was developed by the Road Research Laboratory, London and its detailed procedure is described. Combined composites are supplied and their percentage above the normal working fine collection is 4.75 mm, 2.36 mm, 1.18 mm. 600 microns, 300 microns and 150 microns are used. For the maximum combined size of the allowable size, it says 38 mm, 19 mm, 9.5 mm 4.75 mm, 2.36 mm is used.
3. Assemble Design in a Traditional Indian Way:
- The Indian Bureau of Standards has recommended the concrete construction process in conjunction with the experimental work carried out in national laboratories. The mixing process is provided by IS-10262- 1982. Subsequently no updates have been made to this process , and IS 456-1968 has been updated in 2000. That is why IS 10262-1982 needs to be reviewed as the cement power available to a highly developed country.
Therefore the following changes need to be made:
1. The 28-day capacity for phase A, B, C, D, E & F renewal needs to be reviewed.
2. The relationship between the different strengths of cement and the size of w / c should be re-established.
3. The relationship between 28 days of pressure and w / c ratio should reach a pressure of 80 MPa (800 kg / cm2), if the graph is to be used for high strength concrete.
4. According to the revised IS 456-2000 the usability level is expressed in degradation instead of compacting factor. This change requires new amounts of sand and water content for the use of standard concrete up to 35 M Pa and high strength Concrete over 35 M Pa.
- However in the absence of a review on IS 10262-1982, the existing IS 10262 process is described below as a smart move.
- The IS recommendations for mixing design include the composition of the mixing of self-contained (non-ventilated) concrete of medium and high strength concrete.
The integration method consists of the following:
(a) Water content
(b) Percentage of penalty collections corresponding to the maximum aggregate size of the reference value
(c) The amount of cement water, and
(d) Preservation of penalty collection.
- Water content and percentage of fine aggregate and adjust for any differences in performance. Finally the size of the ingredients per unit of concrete volume is calculated in the form of absolute volume. This method works for both underground pozzolana centers.
- The final amount of compounds selected after the experimental mixing, may require minor adjustments. In the case of fly ash cement, the water content can be reduced by about 3 to 5% and a good portion can be reduced by 2 to 4%.
4. American Concrete Institute Method of Mix Design:
- Although the ACI committee published its mixing method in 1944 and almost all concrete dams using a lot of Indian works were designed using the ACI committee method used at the time of mixing. Since then many improvements have been introduced in a practical way. Here is a discussion of the latest method of constructing concrete mixes based on ACI 211-1 of 1991 manual part-time concrete recommendations.
The ACI committee took the following basic ideas:
1. The new collapsed concrete provided and containing a fully proportional measure of the maximum given size will have a fixed water content, regardless of the w / c ratio and the cement content associated between the maximum range of operating parameters.
2. The maximum stiffness of the coarse aggregate per unit of concrete per unit depends on its maximum size and the correct modulus of the fine compound as shown in table 20.39 taking into account the minimum particle size. The effect of angularity is reflected in the empty content. So angular green joints require more mud than circular joints.
3. Regardless of the compaction methods, even when complete compaction has been achieved, a certain percentage of air remains in the concrete and is proportional to the maximum volume.
Mix Design Process:
For compound design, the following data is required to be collected:
(a) Fineness modulus of selected fines.
(b) The unit has the weight of the selected dry fine.
(c) The gravitational force of coarse and fine aggregate in saturated, dry areas.
(d) Absorption of combined rates and penalties.
(e) The gravitational force of cement.
5. Quick methods Mixing:
- Measuring the initial amount of cement water according to purpose means the actual strength will be to combine it with 28 days of cement strength. Feature strength is found to be better related to 28 days of cement strength than in age. This method will therefore require 28 days to determine the size of the cement and the next 28 days of testing mixing the strength of the concrete. The 28-day strength of the cement can be considered as that provided by the curves
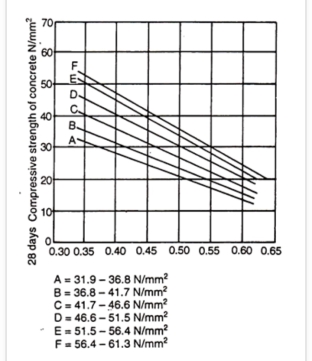
Fig no 17. Graph of compression strength of concrete
- 28 days or 56 days is too long for the contractor to wait for the results of the merger. There is a tendency to use direct mixing without trying experiment mixing. To reduce the time required for the mixing of experiments, the Cement Research Institute of India (CRI) has developed a method called rapid method, in which the compressive strength of cement and cement is obtained using a rapid therapeutic method as discussed in IS 9013-1978. This method reduces the recovery time of experimental compounds from 28 days to only 3 days.
- 28 days of concrete hardening is found to be highly correlated with statistics and rapid strength. Therefore the combination of temptation in line with the target means faster energy than the target means 28 days of energy, with the help of a combination between the two.
- This mixture is obtained independently by the type or characteristics of the cement used i.e. the mixture is not affected by the type of cement used, probably because it affects the fast and normal concrete strength of 28 days equally, so that the result is neutral in comparison. The advantage of each operation is such a combination can be established by the type of building material and assembled to the size to be used.
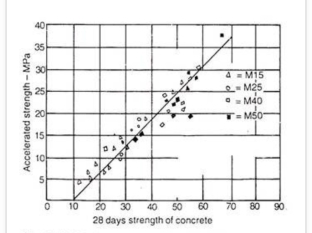
Fig no 18. Strength of concrete vs accelerated strength
- On the other hand, the results of a stable acceleration test in standard cement mortar such as IS 4932-1968 Were not found to be reliable. This problem is overcome by inspecting the cement and quickly and determining its speed.
- The concrete composite concrete or the fastened concrete mixing strength has a w / c value of about 0.35 and the performance is much lower with slump 0 to 10 or compacting factor 0.8 per available cement i.e. (cement in hand).
- The maximum size of the crushed natural compound name should be 10 mm and a good composite should correspond to area II of table 4 of IS-383-1970.
Key takeaways
The following points highlight five methods of concrete construction. The methods are:
1. American Method of Mix Design
2. Graphic Method of Mix Design
3. Mix Design by Indian Standard Method
4. American Concrete Institute Method of Mix Design
5. Quick Method of Mix Design.
The quality of concrete construction on site can be done in three different phases as follows
1. Quality control before integration
2. Quality control during integration
3. Post-construction quality control
STAGE 1 (QUALITY CONTROL BEFORE CONCRETING)
This phase of quality control has two steps.
- Assessment of specification requirements regarding mining, forms, consolidation and embedded repairs etc.
- Control test for concrete ingredients (eg cement, composite and water)
Cement
Cement quality is obtained by performing strength tests of cement cubes. However, with effective control cement:
- It should be tested first and foremost for each source and then tested every once every two months
- It should be protected from moisture
- It should be returned after the last 3 months, if long-term storage is unavoidable
- It should be rejected if a large lump is found in the cement bags.
Aggregate
Concrete composites should be validated at specified values as standard specifications.
The quality of concrete is affected by the various physical and mechanical properties of the composite, namely structure, proportions, durability, gravity and water absorption etc. These composite structures should be tested before using them to produce concrete.
The amount of horror and natural pollution should also be considered.
Sand connections are also an important asset in a number of ways. Provides incorrect results when volume encryption is performed .It increases the amount of water cement which also reduces energy.
With aggregate functional controls:
- They need to be tested once in the beginning to allow the source
- If it is to be checked once or twice daily the moisture content and grant must be made for the combined moisture content.
Water
Water quality should be assessed for needs as defined at the appropriate level. Chemical analysis will be performed to authorize the source. In the event of contamination, it is necessary to store the water for a period of time to allow it to settle. In case of doubt the concrete cubes made of this water are examined. A maximum of 28 days of pressure for at least three cubes or cylinders or a set size, prepared for the proposed water use shall not be less than 90% of the strength between three cubes of the same concrete prepared with distilled water.
STAGE 2 (QUALITY MANAGEMENT DURING CONCRETING)
Careful precaution during concrete is required for all assembly operations such as baking, mixing, transporting, placing, coating and curing. Follow-up safety measures should be taken during concreting operations.
- The concrete mix should be built into the laboratory and the materials to be used on site.
- As far as possible the concrete should be driven by weight. If weight assembly is not possible, volume collection can be allowed with proper monitoring in the presence of the lead engineer.
- During mixing the mixer should be charged in full. Building materials should be fed in the right order. The mixer speed should be from 15 to 20 fluctuations per minute. The mixing time should not be less than 2 minutes in any case. Separation should be avoided when loading concrete into the mixture.
- The performance of concrete is an important material of concrete while concrete is in its new state. Therefore testing of slump or compaction factor should be performed to check the performance of the concrete. About three tests should be performed on every 25 m3 of concrete.
- Care should be taken so that no separation occurs during the concrete transfer.
- Concrete should not be lowered from a height of not more than 1 m. If the height of the drop is more than 1 m chutes should be used.
- To avoid re-release the concrete should be placed in its final position as much as possible.
- Vibrators should be used to connect the concrete. Internal vibrator installation space should not exceed 0.6 m. It should be lightly painted so that no holes are left in the concrete. Vibrator frequency should not be less than 7000 cycles / minutes.
- The treatment should be done over a period of time so that the concrete develops the required strength. Concrete should be covered with hessian as soon as it becomes hard.
- The form function must be aligned with the final form of the form. It should be checked before the start of integration. The inside of the forms should be cleaned and oiled. Forms must be removed after the deadline.
- Concrete should be protected from hot and cold weather at an early age. Concreting should not be performed at temperatures below 4.50C and above 400 In very hot weather water and aggregates should be cooled. Approved quality retards can be used.
- In very cold weather water and aggregates should be heated. Approved quality Accelerators can also be used.
STAGE 3 (QUALITY CONTROL AFTER CONSTRUCTION)
- Once the concrete has been laid and assembled, a pressure test is performed on the tubes made of this concrete. With standard concrete, cubes are made of concrete made in the workplace.
- Reinforced concrete should be considered to be true in size, shape and size as specified in each design. The appearance of the concrete surface should also be checked. Sizes are available in various sizes. Reinforcement should have adequate concrete cover and if reinforcement is visible on the part of the structure, the part should be rejected or appropriate action taken.
Concrete strength is usually obtained by cube or cylinder samples tested within 28 days. In the event that the power received is less than the specified minimum, one or more of the following steps may be taken.
- Load testing and deviation of the deviation and / or difficulty (structural quality can also be obtained by calculating back concrete strength)
- Cutting cores from structures and testing them for strength
- Non-destructive tests such as the Schmidt rebound hammer or ultrasonic pulse velocity test. These tests give a very complex view and are used to find structural similarities.
- Chemical analysis of hard concrete.
Key takeaways
The quality of concrete construction on site can be done in three different phases as follows
1. Quality control before integration
2. Quality control during integration
3. Post-construction quality control
The behavior of the concrete under high temperature values could be affected with several factors. The temperature rate, aggregate type, and stability of the mixture are among the most important factors to be considered under high temperature condition. It is noted that the abrupt temperature rise can cause thermal shock, spalling, cracking, and aggregate expansion leading to high distress within the concrete.
The durability of the concrete against freeze-thaw cycles is previously investigated as a major factor indicating the ability for resistance against weathering actions.
Cold and hot weather concreting
Introduction
- Concrete and other structures are constructed in many countries around the world and in some places the climate is symbolized by the long spells of hot or cold weather. Concrete companies that are ready to integrate and build in these regions are able to produce high quality concrete despite these weather problems. In many regions with unfavorable weather conditions there are set conclusions and concrete production guidelines that provide details of the methods that can be used to combat adverse conditions.
- In the cooler parts of the world, cool, humid climates are common. In these areas, although cold or cold temperatures are not uncommon, it is often surprising when they arrive and it may be too late to apply even safety measures to minimize their undesirable effects,
- Physical effects in both hot and cold conditions should not be overlooked. Workers and managers will not be expected to produce good quality concrete if exposed to conditions for a long time without proper protection
- When the process of serving the container is done on its own it is not a matter of deciding whether to pour concrete. Air temperature, humidity, and wind speed, higher temperatures where you put concrete, water and dry concrete in the bag all play a big role and should be considered. The air, air and moisture are much better than you can handle but you can also influence it. It is important to remember that the temperature of the mixed material is as important as the temperature of the air.
- The strength and durability of concrete are at odds with the climate in which the composite process is performed. Therefore, construction workers will need to take extra care or take action when it comes to worship. In fact, some parts of the world remain hot all year long. These are situations where paying attention to a few simple but much-needed points in hot weather can definitely help to complete any display without compromising its quality. Sunlight leads to hot weather which forces us to use special methods while barking known as hot weather concreting,
Hot Weather concreting
Definitions
- The definition of a tropical climate may vary from country to country. According to the Indian climate, Indian codes determine 40 ° C as the temperature range for hot climates. That is to say, any combination made at temperatures above 40 ° C can be considered as a hot climate that allows for certain measures to be adopted.
- Obviously, this is not the case in most other parts of the world because of the climate. For example, according to ACI 305, any combination of high temperatures, high air pressure, low humidity and sunlight (sunlight) is a preconceived notion for designing a connection such as hot weather. Some theories say that any heat above a comfortable room temperature, and 25 ° C however, begins to make the concrete uncomfortable 1.e, the concrete begins to react differently which is why it requires special care due to hot weather, if strong quality to be maintained.
Hydration Process
- Therefore, it is very important to deal with how the temperature of the tropical climate differs concreting normal temperature. Concrete sets also gain strength due to the hydration of the cement inside them. The elasticity of the cement occurs quickly when it is hot. Cement installation also releases heat. Therefore, the faster the hydration of the cement the faster the heat generation. This creates the heat of the concrete, further speeds up the cementing or set-up process, Cement quickening does not allow concrete enough time to get enough strength. While the initial energy does not suffer, long-term energy (28-day energy) is negatively affected. This is a major reason why hot climates require special care. Otherwise, you will be playing with concrete designed strength.
- Water demand
- The water demand for concrete mix is high in hot weather due to rapid evaporation. Unless appropriate measures are taken, additional water will have to be added to the concrete mix to maintain the performance of the mixture. This will increase the amount of water cement which will also reduce the strength of the concrete. If more cement is added to keep the w / c ratio constant the cost will increase as cement is the most expensive ingredient concrete mix,
- Rapid drying of freshly poured concrete areas occurs when it is hot due to rapid evaporation or water loss in the mixture. If proper care is not taken, cracks known as plastic shrinkage cracks will appear, which are difficult to repair over time. The exposed area tends to shrink rapidly due to rapid moisture loss while mixing will still develop sufficient strength to withstand these shrinking pressures leading to cracking. In hot weather, concrete bed, forms, metal reinforcement, connecting or assembling equipment etc. It is also hot transferring heat to a mixture that adds to the problem.
The effects of Hot weather on concrete
- High temperatures can affect the concrete at all stages of production and laying process and many effects can have long-term or hardening effects. Some of the problems caused by high temperatures are listed in Table 1. They are the result of high temperatures that increase the rate of hydration reaction and the movement of moisture inside and outside the concrete.
- The combination of high temperature, low humidity and high air velocity adversely affects desirable concrete structures e.g. Strength, inequality, durability, weather resistance, wear and tear
- Setting time. As the temperature of the concrete increases, the laying time, and thus the laying time, the mixing and finishing of the concrete is reduced
- Workability and slump - High temperatures reduce the performance (or fall) of concrete very quickly over time. Adding more water to improve the performance of the mixture reduces energy and Increases penetration, and ultimately affects the durability of the mixture.
- Durability - Many forms of degradation depend on the transfer of fluid or respiration through a concrete structure. Acquiring a ‘non-permissible’ concrete is one of the main goals when trying to gain durability. The main ways to do this is to produce concrete with low water / cement concrete. As noted above, high temperatures affect the initial performance and the level at which they lose performance and may be tempted to add more water to the mixture or site. This will lead directly to concrete at high risk of cold, climate change, sulphate attacks and the entry of carbon dioxide and chloride solution leading to increased corrosion.
- Compressive strength - High water demand and high concrete temperatures can lead to a 28 day power reduction. If too much water is added to the concrete mix at high temperatures to maintain or restore function, the water level of the cement will increase, resulting in a loss of strength and durability. This can also increase the shrinkage of reinforced concrete. Where water is not heard, reduced set time and performance can increase insufficient mixing (actually a major impact on energy), the formation of cold joints and improper elimination.
- Concrete temperature - Warmer climates can increase the temperature of concrete caused by hydration heat. In large segments the hot gradients through the element can create thermal cracks. Laboratory tests show that very high temperatures have a significant impact on the strength of the hard concrete. Although increased concrete heat can lead to an initial increase in energy gain, in the long run, low-temperature-cooled concrete will reach higher strength.
- Poor surface appearance - With increased evaporation, the concrete surface will dry out. In the case of an infestation this can lead to premature depletion, trapping the amount of water that drips inside the mixture. The coated layer (from the finish) can cause blood clots to trickle under the surface, leading to the formation of the upper layer and subsequent eruption. Also, color variations on the face can result from different levels of hydration and cooling effects.
- Plastic shrinkage cracking - Hot weather conditions accelerate the loss of moisture on the face. If the evaporation rate is higher than the rate of bleeding (the rate at which the water rises higher) drying of the soil will occur which has led to a reduction in concrete. When the reducing pressure exceeds the capacity of the concrete, cracks will occur. The chances of cracking the plastic are reduced so it is great whenever hot weather raises steam or concrete and lowers the bleeding rate. The cracking of the shrinkage plastic can be quite deep, as the plastic concrete has little resistance to the shrinking pressure, and the cracks continue to grow and spread until the shrinkage pressures are released. (Be aware that thin plastic cracks do not usually extend to the free edges, as uncontrollable concrete cuts may occur in these areas.)
- Thermal cracking - Concrete is at risk of thermal cracking when applied for the first time, and hydration heat raises the internal temperature of the concrete. Rapid changes in the external temperature of the exterior concrete, such as where concrete slabs are laid, walls or sidewalks on a hot day followed by a cold night, lead to hot gradients between the warm / hot surface and the cold outside. The warm interior offers a cool outdoor space, which wants to make a deal. Depending on the temperature variation, there may be a concrete crash. Larger or thicker concrete objects are at greater risk because of the protective effect the concrete gives them inside the object.
Precautions in hot weather conditions
- Problems often arise when local workers are unaware of the impact of changing weather and / or climatic conditions during laying and / or finishing concrete. Improved responses to unexpected changes are not recommended because the damage that can be caused by the uncontrolled effects of tropical climates may not be completely eliminated. The first option to consider in hot weather is to postpone the placement of the concrete or not
- Make sure site staff are aware of the effects of the weather. Improved responses to unexpected changes are not recommended. The first option to consider in hot, unfavorable weather conditions is to postpone the placement of the concrete or not. It is often better to wait than to risk costly repairs (or replacements) for defective work.
- Concrete Production. The role of concrete suppliers is to help put concrete in hot climates. Shade stocks, spray aggregates before evaporation time, or cool down otherwise. Paint mixing barrels and keep them white to reduce heat loss from the sun. Use ice as part of the mixed water or cool the concrete with liquid nitrogen.
- Delivery and Delivery- Delivery delays can delay good mixing practices. The concrete supplier must plan and maintain a good non-delaying plan to deliver concrete to the required area on site
- Reduce travel time and avoid unnecessary delays.
- Avoid prolonged mixing. Mixed transport trucks should be released as soon as possible after the addition of water to that mixture.
- For large projects, consider baking and mixing using a workplace plant. •
- Water should not be installed on pre-assembled concrete in the workplace unless it is part of the amount required at the beginning of the set water limit and specified descent.
Precautions for concreting in cold weather
- Temperature control of concrete ingredients - The most effective way to maintain the temperature of concrete at the top is to control the temperature of its ingredients. The contribution of each ingredient in concrete heating is a function of heat, specific heat and the amount used for this ingredient. The water mixed with the mix has a very noticeable effect on the temperature of the concrete. Therefore, in cold weather, all available means will be used to care for these items at the highest possible temperature.
0. Many ways to reduce the effects of low temperatures include raising the level at which the concrete gains strength under these conditions in the first critical phase after laying.
2. Cement Quantity - Increasing the amount of cement (meaning using high-strength concrete) can increase the energy gain. Note that there is little or no impact during setup.
3. Admixture - The rapid addition of compounds (non-chloride) to concrete reduces the setting time and speeds up the energy gain rate by increasing the level at which cement enters
4. Hot Water - Applying hot water to the mixture will increase the temperature of the concrete, which in turn accelerates the rate at which cement enters. The temperature of the water mix should not exceed 70 ° C and the mixing should ensure the consistency of the concrete delivered to the site
5. Air entrainment - you may be able to prevent the effects of sudden cold by applying a combination of ventilation to the concrete. These compounds create minute air vents where the pore water can move as it expands during cold weather
6. On site precautions - It is advisable to take steps to prevent concrete damage by unpredictable and unexpected snow whenever the air temperature drops below 5C.
7. Cold Protection (Including cold / frozen area, winds and cold) - in some cases, the provision of a heated enclosure (simple frames covered with tarpaulin and the use of hot air) to completely seal the concrete object may be required. Note that care must be taken to prevent concrete drying when using this method.
Key takeaways
1. Concrete and other structures are constructed in many countries around the world and in some places the climate is symbolized by the long spells of hot or cold weather. Concrete companies that are ready to integrate and build in these regions are able to produce high quality concrete despite these weather problems. In many regions with unfavorable weather conditions there are set conclusions and concrete production guidelines that provide details of the methods that can be used to combat adverse conditions.
Under water concreting
There are 4 techniques of underwater concreting:
- Tremie pipe Method
- Bucket Method
- Grouting Method
- Bags stacking Methods
1)Tremie pipe Method:
- The tremie stable state of affairs method makes use of a vertical or nearly vertical pipe, thru which concrete is about with the aid of using gravity feed below water degree.
- The decrease give up of the pipe is stored soaking wet in crisp cement with the aim that stable ascending from the bottom dislodges the water, on this manner limiting washing out of the bond substance of the brand new concrete to the exposed top floor.
- The top give up of the tremie pipe is stored over the water degree amid the pour and is given a cone formed field for cluster stacking, or cement is probably siphoned into the best factor of the tremie pipe.
- Concrete should be poured at a fee which abstains from putting with inside the tremie.
2) Bucket Method:
- In this method the stable is saved submerged with the aid of using a base commencing field.
- The cans for the maximum component are outfitted with base curler or drop base doorways as regarded in Fig. The door opens uninhibitedly outward whilst stumbled.
- The pail is crammed absolutely with cement and its first-class secured with a canvas material or gunny sack and taken progressively right all the way down to avoid backwash or unsettling have an impact on to concrete because the can is added down into the water.
- The can is added down with the aid of using a crane upto the bottom floor of the stable and in a while opened both with the aid of using an affordable recreation plan from the first-class or with the aid of using a jumper.
- It is fundamental that the stable be launched straightforwardly superficially on which it's far to be saved.
Advantages:
- This method is located to have the accompanying preferences:
- Relatively lean blends is probably applied given ok versatility is held.
- No shape paintings is essential on this method.
Disadvantages:
- This method is slight and laborious as the precise situating of the packs installation should be cultivated with the aid of using the jumpers.
- Voids in adjacent sacks are difficult to fill.
- There is small preserving apart from created with the aid of using the mechanical interlock among packs.
- The method further is exorbitant as greater paintings is related to filling and tying them.
3) Grouting Method:
- These pens are laid vertically over the whole area to be cemented with the give up aim that the separation among the focuses of the pens and moreover to the essences of the stable thought now no longer surpass one meter.
- The degree of the stone over all thought to nor be beneath 50 mm in extra of 2 hundred mm.
- This overall have to be wetted earlier than storing it outdoor the metallic confines over the whole location and tallness to be cemented.
- While saving the overall, care have to be taken that no pen is uprooted from its position.
- Subsequent to storing the overall, the concrete sand grout of 1:2 quantity and water/bond share as a minimum 0.6 and now no longer greater than 0.9 is installation in a mechanical blender.
- The finest length of sand is probably five mm and the concrete sand quantity can also additionally shift from 1:1.5 to 1:4contingent at the first-rate conditions and importance of the paintings.
- In the wake of grouting the whole territory for a stature of round 60 cm s, a comparable pastime is rehashed for the subsequent layer of 60 cm and the method is rehashed until the grouting is completed up to an appropriate tallness.
- The grout to be dispatched down to be ok to fill each one of the voids.
- The extent of voids is probably typical as 55% of the extent to be cemented or observed tentatively.
- Beyond what many could recall feasible cement thought now no longer be troubled whilst it's far stored, this can restrict the association of laitence.
4) Bags stacking Methods:
- The packs are tied in order that they may be perfect right away in a profile of the floor on which they're put.
- The legitimately crammed sacks are added down into the water and set carefully in header and stretcher guides as in block workmanship improvement with the help of jumpers so the whole mass is interlocked.
Advantages:
- This method is located to have the accompanying factors of interest:
Nearly lean blends is probably applied given ok versatility is held.
- No shape paintings is vital on this method.
Disadvantages:
- This method is slight and laborious as the proper situating of the packs installation should be cultivated with the aid of using the jumpers.
Voids in contiguous packs are difficult to fill.
- There is small preserving apart from created with the aid of using the mechanical interlock among packs.
Key takeaways
1. The top give up of the tremie pipe is stored over the water degree amid the pour and is given a cone formed field for cluster stacking, or cement is probably siphoned into the best factor of the tremie pipe.
Concrete gains very little strength at low temperatures. Accordingly, freshly placed concrete must be protected against freezing until the degree of saturation of the concrete has been sufficiently reduced by cement hydration. The time at which this reduction is accomplished corresponds roughly to the time required for the concrete to attain a compressive strength of 500 psi. Concrete to be exposed to deicers should attain a strength of 4,000 psi prior to repeated cycles of freezing and thawing.
Sulphate
- Cement is composed of two minerals: tri-calcium silicate (C3S), and di-calcium silicate (C2S).
- In addition to hydration, the main reaction products are calcium silicate gel (C-SH) and calcium hydroxide Ca (OH) 2, labeled as CH in chemistry notation.
- Moisture is required in this reaction which can cause serious damage to the construction of both the walls and the walls of buildings in buildings.
- Sulphate attacks occur on the lower slabs. This problem usually affects buildings from the 1950s to the 1960s but can also affect previous buildings where the concrete floor slab is installed.
- It occurs when the filler material under the slide contains sulphates and this is considered to be a solution with soil moisture entering the concrete that forms the slab on the floor.
- Attacks can occur from MgSO4 salts, NaSO4 salts, and other salts containing SO3-ions. The interaction of Ca2 + ions with SO4 present in the solution will produce CaSO4 or gypsum.
- The effect of gypsum on C-S-H gel, which is the main component of reinforced cement, is an irreversible topic.
- Some substances present in cement, such as tri-calcium aluminate, also interact with sulphate ions. This reaction is well established in the literature.
Key takeaways
In addition to hydration, the main reaction products are calcium silicate gel (C-SH) and calcium hydroxide Ca (OH) 2, labelled as CH in chemistry notation.
Moisture is required in this reaction which can cause serious damage to the construction of both the walls and the walls of buildings in buildings.
Acid Attack
- Acid attack is the dissolution and leaching of acid-prone elements, particularly calcium hydroxide, from the cement paste of hardened concrete.
- This movement outcomes in an boom in capillary porosity, lack of cohesiveness and subsequently lack of power.
- In said instances, acid assault can be observed with the aid of using crack formation and subsequently disintegration, in particular whilst the shape is subjected at one facet to water pressure.
- Unlike sulphate assault (see beneath), the goods fashioned from acid assault aren't expansive, and leaching will handily arise in systems which are tremendously permeable.
- In excessive overall performance concrete structures containing cement pastes with a low content material of calcium hydroxide, acid assault is relative gradual and can contain handiest the finely divided calcium hydroxide crystals included withinside the interstices of the calcium silicate hydrate, C-S-H.
- The micrographs received from PFM analysis, supplemented with SEM–EDS studies, monitor that handiest the top, floor part of the concrete has been attacked with the aid of using acidic answer.
- The relaxation of the concrete suggests no shape of degradation.
- In the attacked zone, there's clean proof of leaching of the cement paste matrix, main to accelerated capillary porosity and lack of brotherly love of the matrix.
- Locally, there's lack of bonding of the cement paste to aggregate, however at the whole, those elements have now no longer adversely affected the microstructure and nice of the concrete.
- In this instance, long-time period sturdiness of the concrete isn't always probably to be compromised.
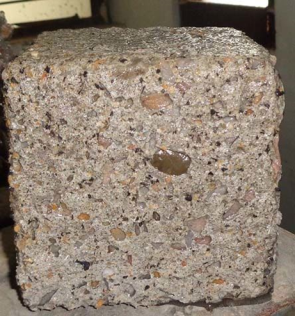
Fig no 19. Acid Attack on Concrete block
- Acid assault of concrete takes 3 forms. First, hydration merchandise reacts with the acid to shape dissolved ions, main to lack of strong material—acidolysis.
- Second, withinside the case of a few acids, insoluble salts shape, a number of which precipitates to purpose growth and cracking.
- Finally, a few acids supply complexes with calcium, aluminium, iron and silicate ions which produce an awful lot better concentrations of those ions in answer than could in any other case be the case, once more main to dissolution.
- This can probably arise at pH situations beneath which cement could usually be tremendously stable (complexolysis).
- Depending at the acid present, extra than this sort of deterioration mechanisms can be powerful.
- Where acidolysis is the main mechanism, an acid answer penetrating the pores of concrete will begin to purpose a number of the elements to dissolve.
- Calcium is generally the primary cation to be dissolved, considering that portlandite will become soluble beneath tremendously excessive pH values.
- AFm and AFt stages commonly dissolve at barely decrease pH values, even though strong aluminium and iron hydroxides are precipitated, which persist till the answer is tremendously acidic.
- Exposure to acidic answer additionally reasons lack of calcium—decalcification—of C-S-H gel, leaving tremendously vulnerable silica gel behind.
- The importance of calcium on this shape of degradation approach that adjusting the composition of the cement matrix of concrete to attain a decrease calcium content material will probably impart extra resistance.
- Thus, pozzolanic substances can be powerful in improving resistance to this form of acid assault, considering that their aggregate with PC will produce such an adjustment.
- However, decreased quotes of mass shipping and more desirable power done thru the usage of pozzolanic substances also are probably to be motives for progressed resistance.
Key takeaways
In excessive overall performance concrete structures containing cement pastes with a low content material of calcium hydroxide, acid assault is relative gradual and can contain handiest the finely divided calcium hydroxide crystals included withinside the interstices of the calcium silicate hydrates, C-S-H.
- You may also note efflorescence each interior and outside, and it may range in frequency and depth in the course of the us of a because of moisture and temperature. Three situations want to exist for efflorescence to arise: There are water-soluble salts in or at the fabric.
- Moisture is gift to make the salt turn out to be a soluble solution. As salts pass to the fabric’s surface, the moisture evaporates. This makes the salts crystallize, which leads to efflorescence.
- Water, rain and snow are the number one reassets of moisture and might effect the diploma of efflorescence.
- Condensation, groundwater wicking and indoors sports additionally may also have an effect on the diploma of moisture generation. Efflorescence can occur at exceptional times. Essentially, it may both be a hassle from the start of a constructing’s creation, or the method can arise over time.
- Primary efflorescence normally takes place inside the first seventy two hours of the constructing fabric being used, performing because of extra water being gift while the fabric became manufactured.
- Secondary efflorescence is a end result of out of doors moisture pulling the salt out of the constructing fabric. In many instances, efflorescence may also arise at some stage in domestic creation. If masonry devices get unnoticed in a single day at some stage in creation, they’ll probably soak up moisture from damp soil and rain. It is critical for masonry devices to be included and left in pallets to decrease the danger of efflorescence in the course of a creation project. Efflorescence also can arise while constructing substances are established incorrectly or troubles arise with the installation.
- Some not unusualplace examples of this include: Using through-wall flashings incorrectly. Failing to offer enough air flow for masonry. Installing masonry with out an green barrier for moisture.
- Joint substances failing after installation. Materials being saved improperly or left at the ground. Efflorescence is mostly a seasonal hassle, and humidity will effect whether or not soluble salts appear. It normally escalates in winter, due to the fact that rain, snow, sleet and different inclement climate situations may also arise. However, efflorescence can nevertheless arise in spring, fall and summer.
Fire resistance of concrete is the ability of concrete to withstand fire or to give protection against fire. This involves the ability of concrete structural element to continue perform a specific structural function or confine fire or both.
The duration of time that an element such as beam, column, wall, floor, or roof can endure the fire, which is defined in ASTM E 119, is termed fire rating.
Fire resistance is controlled by both the physical and thermal properties of the structural element. Factors governing the structural performance include stress level in the concrete and the steel, concrete cover, tendency of aggregate and free moisture to cause spalling, and lateral restraint conditions.
However, parameters that control the thermal performance involves type of aggregate, free moisture in the concrete (both absorbed and capillary), and volume of concrete per square meter of exposed area.
Inspection and testing of ready mix concrete is crucial to ensure that all specified conditions meet the acceptable criteria. Ready mix concrete, which produced in batching plant and transported to construction site by truck mounted mixers, are commonly inspected and tested in accordance with applicable standards such as ASTM international.
Batching Plant Inspection
- Firstly, examine and specify whether facilities, scales, and truck mixers meet the specified project requirements or not.
- Inspect storage areas of all materials like cement, aggregate, and admixtures to ensure their cleanness, free of contamination, and properly protect materials from effect of freezing.
- Inspect and verify that coarse and fine aggregate gradation tests are conducted in accordance applicable standards like ASTM C 136, and result reach project requirements.
Onsite Inspection of Ready Mix Concrete
- Every delivery ticket shall be inspected to ensure that a mixture with the correct designation is delivered.
- Inspect delivered concrete; it should be uniform and adequately mixed prior to discharge at the construction site.
- Inspect and monitor water, admixture, and fiber reinforcement addition onsite to make sure that the process performed properly.
- Monitor and examine concrete delivery and placement time to find out whether it completed within the time constraints of the project specifications.
Testing Ready Mix Concrete
1. Onsite Tests
There are certain types of tests that shall be conducted on ready mix concrete upon reaching construction sites. Table 1 provide lists of tests that need to be performed on ready mix concrete on project site. Table 1 Tests conducted on ready mix concrete upon reaching construction site
Type of tests | ASTM international for testing procedures | Test frequencies | Purpose of the test |
Slump | ASTM C 143/C 143M | First truck load, whenever the consistency of the concrete appears to vary. | Measure fresh concrete consistency, check its workability, and use as an indicator of poor mixed batch |
Air content | ASTM C 173, ASTM C 231 | Performed on all samples taken to measure concrete strength | To check air entrained concrete |
Temperature | ASTM C 1064 | At the time of sampling for each strength test | To make sure that concrete comply with certain specifications that define a certain allowable temperature range |
Density | ASTM C 138, ASTM C 567 | Whenever required by project specifications | To estimate concrete density |
Evaluation of crack
When inspecting a slab or conducting a crack, always measure the width of the crack and determine whether the metal reinforcement passes through it and whether the crack is active or asleep. This information, especially the details of the reinforcement and cracking function, is very important when choosing the best repair option.
Crack width
- The extent of the crack is usually measured using a crack comparison card. Measuring the width of the crack helps to separate the stiffness of the cracks and to evaluate the performance of the joint joints across the fracture of the direct direction of the fracture and the transmission of the load. Also, many repair options depend on the width of the crack.
- Unless the steel reinforcement passes through a crack, the alignment of the vertical tube and the transmission of the broken load depends on the joint bonding. If the diameter of the fracture is less than 0.035 inches, the composite particles that come from the other side of the fracture to the other side will normally provide adequate load transfer and maintain vertical alignment throughout the split.
- For larger screens, maintaining a straight slide alignment can be a challenge. The success of the remediation approach will depend on the slide loading and the quality of the base material and the ground cover.
Steel Reinforcement
- Although steel reinforcement does not prevent cracking, it limits the width of the crack so that the joint joints are maintained. Strengthening itself also provides load transfer and helps maintain vertical alignment in the cracks. When the reinforcement passes through a split, both the width split and the future width increase are controlled. The new cracks of the non-reinforced concrete will continue to grow and the diameter can double before the increase in crack-width.
- With the cracks caused by the drying shrink, the cracks will stabilize at the end. Splits due to other causes, however, such as soil erosion or height, may not be stable and may continue to increase unless a significant amount of reinforcement passes through space. Determining the amount of reinforcement that goes beyond cracking is important in predicting the performance of future cracks and choosing the best repair option.
Dormant and active crack
- Cracks that fall through steel reinforcement are generally stable and are often considered sleepy. Of course, the stability of the cracks depends on the source and the degree of reinforcement of the cracks. The lying cracks have a fixed width and can be repaired with solid or flexible materials.
- Functional cracks should only be repaired using a flexible object that can accommodate future cracked movements. Generally, the active cracks in the slabs actually belong to the active members and should be treated in the same way as the joints. After all, random or non-joining cracks in flatwork are self-assembling joints.
Key takeaways
- Evaluation of crack is
- Crack width
- Steel Reinforcement
- Dormant and active crack
1. Plastic shrinkage concrete cracks:
- When concrete remains in its plastic state (earlier than hardening), it's miles complete of water. When that water finally leaves the slab, it leaves at the back of big voids among the stable particles.
- These empty areas make the concrete weaker and greater at risk of cracking. This form of cracking takes place regularly and is stated as “plastic shrinkage cracking”.
- While plastic shrinkage cracks can manifest everywhere in a slab or wall, they nearly constantly manifest at reentrant corners (corners that factor into the slab) or with round gadgets withinside the center of a slab (pipes, plumbing fixtures, drains, and manholes).
- Since concrete cannot decrease round a corner, strain will purpose the concrete to crack from the factor of that corner. Plastic shrinkage cracks are usually very slender in width and slightly visible. While almost invisible, it's miles vital to bear in mind that plastic shrinkage cracks don’t simply exist at the surface, they increase at some point of the whole thickness of the slab.
- An excessively moist blend is a contributing element to shrinkage in concrete. While water is a critical element in each concrete blend, there's this kind of factor as an excessive amount of water.
- When the combination consists of an excessive amount of water, the slab will reduce greater than if the suitable quantity of water turned into used. Hot climate is some other massive cause for plastic shrinkage cracks. Control joints may be included into the slab to save you shrinkage cracking. The joints will open up because the concrete slab receives smaller.
2. Expansion concrete cracks:
- Enlargement cracks Just like a balloon, warmth reasons concrete to expand. When concrete expands, it pushes towards whatever in its way (a brick wall or adjoining slab for example).
- When neither has the capacity to flex, the increasing pressure may be sufficient to motive concrete to crack. Expansion joints are used as a factor of separation (or isolation), among different static surfaces.
- Typically product of a compressible fabric like asphalt, rubber, or lumber, enlargement joints should act as surprise absorbers to alleviate the strain that enlargement places on concrete and save you cracking.
3. Heaving concrete cracks heaving cracks:
- When the floor freezes, it is able to on occasion raise many inches earlier than thawing and settling lower back down.
- This floor motion delivered on through the freezing and thawing cycle is a big element contributing to concrete cracking. If the slab isn't unfastened to transport with the floor, the slab will crack.
- Large tree roots will have the identical impact on a slab. If a tree is positioned too near a slab, the developing roots can raise and crack the concrete surface. Always don't forget this while laying a slab.
- Settling concrete cracks settling cracks On the alternative hand, floor settling beneath a concrete slab also can reason cracking. Settling cracks usually arise in conditions wherein a void is created withinside the floor beneath the concrete surface.
- Think approximately whilst a huge tree is eliminated from close by and the roots start to decompose or whilst a software business enterprise digs a trench for his or her lines, pipes, etc. and don’t compact the soil once they replenish it–those are examples of times wherein settling cracks are possibly to happen.
The principal causes of cracks in a building are as follows:
- Permeability of concrete
- Thermal movement
- Creep movement
- Corrosion of reinforcement
- Moisture movement
- Poor construction practices
- Improper structural design and specifications
- Poor maintenance
- Movement due to chemical reactions
- Other factors
Remedial measures
- Use minimum possible quantity of water.
- Employ large coarse aggregate.
- Provide compression reinforcement if possible
- Avoid formwork removal at early ages.
- Cure concrete properly.
- Assign proper cross section for the concrete element.
- NDT stands for Non-Destructive Testing. It refers to an array of inspection strategies that permit inspectors to assess and acquire statistics approximately a material, system, or factor without completely changing it. NDT can also be called: NDE (non-unfavourable exam or evaluation) NDI (non-unfavourable inspection) In the subject, NDT is frequently used as an umbrella time period to consult non-unfavourable inspection strategies, inspection tools, or maybe the complete subject of non-unfavourable inspections.
- For business applications, the aim of NDT is to make certain that vital infrastructure is well maintained if you want to keep away from catastrophic accidents. While NDT techniques are generally related to business use cases, like examining vulnerable factors in a boiler used at an oil refinery, makes use of in medicinal drug are really a number of the maximum common. For example, an waiting for mom getting an ultrasound to test at the fitness of her infant could be taken into consideration an NDT use case, as could getting an X-ray or MRI to analyze extra approximately an injury.
- But it’s critical to notice that NDT does now no longer always require the usage of unique equipment, or any equipment at all. For instance, while inspectors in business settings overview the outdoor of a stress vessel with their bare eye, that could fall beneath the NDT designation, when you consider that they're accumulating facts at the popularity of the boiler without negative it.
- On the alternative hand, the use of an advanced device like an ultrasonic sensor to search for defects in a positive cloth or asset could additionally be known as NDT. Regardless of the particular use case, the underlying commonality amongst a lot of these examples is the gathering of facts in a non-intrusive manner.
- The special styles of non-damaging trying out are regularly complementary. As a result, we will take advantage of the benefits of mixed strategies. Non-damaging trying out (NDT) is a mixture of diverse inspection strategies used for my part or together to assess the integrity and residences of a material, thing or device without inflicting harm to it.
- In different words, the component that calls for the usage of one or greater of these strategies can nevertheless be used as soon as the inspection technique is over. NDT is consequently regularly used for the detection, characterization and sizing of inherent discontinuities, in addition to the ones related to harm mechanisms. NDT is regulated with the aid of using codes and requirements in keeping with the kind of industry, united states of America and different criteria. Society for Mechanical Engineers (ASME), ASTM International, COFREND, CSA, Canadian General Standards Board (CGSB), American Society for Non-destructive Testing (ASNT), etc. are well-recognize examples.
- Destructive trying out (regularly abbreviated as DT) is a take a look at technique performed to discover the precise factor of failure of substances, components, or machines.
- During the process, the examined object undergoes strain that in the end deforms or destroys the material. Naturally, examined components and substances can't be reused in normal operation after present process unfavourable trying out procedures. Destructive trying out is typically performed earlier than a aspect enters mass production. OEMs want to realize the boundaries in their merchandise for you to supply right upkeep and working guidelines for his or her machines.
Tests on cement
1. FINENESS
Objective
- The purity of the cement alone has a significant impact on the hydration rate and therefore on the energy gain rate and the degree of heat dissipation.
- Finer cement provides a large area of hydration Specific Surface versus Compressive Strength of Cement and as a result accelerates energy.
- The beauty of digestion has increased over the years. But now it is almost settled. Different cement is subject to different finishes.
- A particle size of less than 3 microns has been found to have a significant effect on energy in one day while a fraction of 3-25 micron has a significant effect on energy for 28 days.
- An increase in the thin layer is also found to increase the thickness of the concrete.
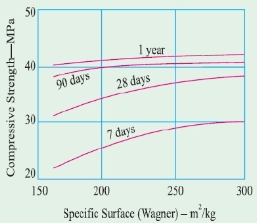
Fig no 20. Specific Surface versus Compressive Strength of Cement
Procedure
- Stir the sample of cement to be tested by stirring for 2 minutes in a preheated pot to distribute the agglomerates. Wait 2 min. Mix the resulting flour gently using a clean dry stick to spread the fine mixture all over the cement.
- Place the tray under a strainer, weigh about 10 g of cement in the nearest 0.01 g and place it in a strainer, being careful to avoid loss. Disperse any agglomerates. Place the lid on top of the filter.
- Cover the sieve with a circular motion, planetary motion and movement until it no longer exceeds the fine material in it. Remove and measure the rest. Specify its magnitude as a percentage, R1, of the pre-set filter per 0.1 percent nearby. Gently move all the fine material from the filter into the tray.
- Repeat the whole process using a new sample of 10 g to get R2. Then calculate the remnants of cement R as the value of R1, and R2, as a percentage, expressed in the percentage close to 0.1.
- When the results vary by more than 1 percent altogether, make a third reduction and calculate the meaning of the three values.
- Check the sieve after 100 filters per section 4.4.2 of IS: 4031 (Part 1)
Apparatus used
![]() | ![]() |
Fig no 21. Cement | Fig no 22. Balance |
![]() | ![]() |
Fig no 23. Seive | Fig no 24. Nylon Bristol Brush |
2. STANDARD CONSISTENCY
To determine the quantity of water required to produce a cement paste of standard consistency as per IS: 4031 (Part 4) – 1988
Apparatus
1) Vicat apparatus conforming to IS: 5513 – 1976
2) Balance, whose permissible variation at a load of 1000g should be +1.0g
3) Gauging trowel conforming to IS: 10086 – 1982
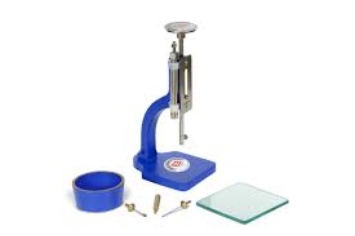
Fig no 25. Vicat apparatus
Procedure
- Measure about 400g cement and mix it with the required amount of water. Estimation time should be between 3 to 5 minutes.
- Fill the Vicat mold with glue and measure it with a trowel.
- Gently lower the plunger until it touches the cement.
- Release the plunger to allow it to sink into the paste.
- Note the reading in the scale.
- Repeat the above process and take new samples of cement with different water sizes until the gauge is 5 to 7mm.
3. SETTING TIME
Objective
- For simplicity, the initial set time is considered to have elapsed between the time when water can be added to the cement, at which point the paste begins to lose plastic.
- The last time is the last time the water is put in the cement, and the time when the glue is completely lost to the plastic and gained enough strength to withstand a certain direct pressure.
- The room temperature, dry material and water should be kept at 27 ± 2 ° C. The relative humidity associated with the laboratory will be 65 ± 5 percent.
Procedure
Preparation of test block
- Prepare a clean paste by measuring 0.85 times the water needed to give the glue a normal consistency. Portable or refined water will be used to prepare the paste. Attachments will be measured in accordance with the conditions set out in IS: 4031 (Part 4) -888.
- Start a stopwatch at a time when water can be added to the cement. Fill the Vicat mould with cement paint as limited as above, the mould stays on an empty plate. Fill the mould completely and spread the surface of the paste to make it to the top of the mould. The cement block is thus suspended from the test mould.
- Immediately after moulding, place a barrier in a damp cupboard or damp room and allow it to remain there unless a set time is set.
Determination of initial setting time
- Place the test block enclosed in the mould and rest on a waterless plate, under a needle-carrying rod (C); gently lower the needle until it meets the surface of the test block and release it immediately, allowing it to enter the test area. Initially, the needle will completely pierce the test block.
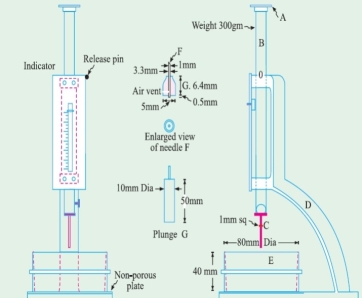
Fig no 26. Needles used in Vicat's Apparatus
- Repeat this process until the needle, when attached to the test block and removed as described above, fails to pierce the block more than 5.0 ± 0.5 mm measured from the bottom of the mould. The time elapsed between the time the water is added to the cement and the time when the needle fails to pierce the block reaches a point of 5.0 ± 0.5 mm measured from the bottom of the mould will be the first set time.
Determination of final setting time
- Insert needle (C) of Vicat resources into the needle with a secret attachment (F).
- The cement will be considered to be set at the end where, when the needle is gently inserted into the surface of the test block, the needle makes a picture of it, while the attachment fails to do so.
- The time elapsed between the time the water is added to the cement and the time when the needle makes its appearance on the surface of the block while the attachment fails to do so will be the last set time.
- In the case of a scarf that forms over the test block, use the bottom of the block to cut.
4. SOUNDNESS AND COMPRESSIVE STRENGTH
- Sensitivity refers to the ability of a glue that has been hardened to retain its volume after setting without the delay of harmful expansion.
- Thus, hearing is a very important test. The audio attachment will not make a pleasant volume change after it has hardened and as a result will not be in danger of forming cracks. Sound adhesive is the basis of sound mud or concrete mixing.
- Aircraft ash is the result of coal-fired power generation. During a fire, mineral pollutants in hot coals are released from the combustion chamber in the form of particles composed by flue gases.
- As these particles coo, they harden into round glass particles. The fly fly shows concrete structures and is used in concrete as replacement or replacement of concrete. Insufficiency can occur in the presence of very free magnesia or free lime burned in cement.
- The taste of cement can be determined in a variety of ways. In the Le Chatelier bath, a sample of cement / ash adhesive frosting is placed on the mould and boiled for a specified period of time (approximately 3hr) so that any tendency to stretch can be quickly and detected.
- After the boiling process is complete, the distance between the points of the two control indicators is measured by the nearest 0.5mm and compared to the first measured length before testing.
- This test requires Le Chatelier water bath, Le Chatelier mould, calliper, measuring cylinder, balance and length comparison. Active standards include EN 196-3, EN 459-2 and EN-450.
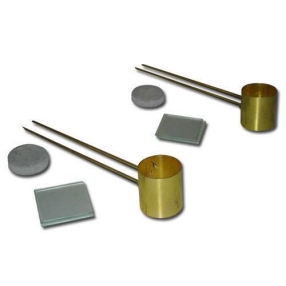
Fig no 27. Le chatelier apparatus
- Alternatively, the stability of the concrete can be determined by autoclave. These tests include an autoclave expansion of Portland cement using a test in a good cement sculpture.
- Specimens are made of oil-coated mould with reference points attached to a reference length of 250mm. Specimens extracted from the mould and measured after 24hr are placed in an autoclave at room temperature.
- After the autoclave is turned off, the specimens are exposed to a full-pressure current at a specified time. After the heating is complete, the template is rated and compared with the original length measurements.
- Equipment needed for this method includes autoclave, test bar mould, mixer equipment, balance and length gauge. Functional standards include ASTM C151 and AASHTO T107.
- The expansion of the cement can also be determined by comparing the length. The length gauge is a device used to measure changes in the length of attachment of cement, mortar and concrete according to ASTM and AASHTO data.
- The unit consists of a complex dial or digital display embedded in a solid, dual post frame structure. Moving and vertical anvils are designed to detect reference pins thrown at the edges of sample test bars.
- ELE offers a variety of devices for this method, including drying materials, shrinkage and humidity movements, as well as a ASTM-length ratio. Active standards include ASTM C151, C157, C227, C490, C531, AASHTO T-107 and T-160.
Key takeaways
- For simplicity, the initial set time is considered to have elapsed between the time when water can be added to the cement, at which point the paste begins to lose plastic.
- The last time is the last time the water is put in the cement, and the time when the glue is completely lost to the plastic and gained enough strength to withstand a certain direct pressure.
- Sensitivity refers to the ability of a glue that has been hardened to retain its volume after setting without the delay of harmful expansion.
- Thus, hearing is a very important test. The audio attachment will not make a pleasant volume change after it has hardened and as a result will not be in danger of forming cracks. Sound adhesive is the basis of sound mud or concrete mixing.
Tests on aggregate
Specific gravity
Gravity and the combined force of water are essential elements in the formation of concrete and bitumen mixtures. The thickness of a solid mass is a measure of its size to an equal volume of distilled water at a specified temperature. Because the compound can contain a void that is allowed to enter the water, two combined gravity measures are used:
- Apparent specific gravity and
- Bulk specific gravity
Apparent specific gravity, G app, is calculated on the basis of the volume of the number of compounds i.e. the volume without voids entering the water. Therefore
G app = [(MD / VN)] / W
Where,
- MD is a dry aggregate weight,
- VN integrated network volume without volume object focus,
- W the size of the water.
Bulk Specific Gravity, G bulk, is calculated on the basis of the total number of aggregates including the inlet. Therefore
G bulk = [(MD / VB)] / W
Where,
- VB total volume of aggregates including volume of water absorbed.
Grading of aggregate
- Collection placement determines the average grain size of the composite before it is used in construction.
- This is the use of a complex and clear combination. The combined sample is filtered through a set of sieves and weights stored in each filter by percentage words summarized.
- By dividing this amount by 100, The Fineness Modulus of that total is determined. This assists in the decision-making process about the number of well-known modular composites that must be combined to obtain the concrete of the desired quantity.
- The basis of a green and clear composite mix for a particular soft module is the presence of spaces or open spaces where the composite is packed together.
- For bad clean aggregates packing can leave 30-40 percent, which can only be removed by filling the fine particles.
- Similarly, in fine aggregates too, there are voids left to be filled with better particles (cement).
- This is important to get a mix of composite and blank letters.
- When other pieces of equal size are put together, voids or open spaces are always left. Percentage of voids can be as high as 45 percent of the total volume of aggregates.
- It turned out that this effect (presence of voids) was independent of the size of the aggregates used in the packaging, whether worse, medium or good.
- Only, while composite packaging should be of the same size, that is the same distance.
- Either all should be rough, or they should all be medium or good. This means that even if the sand alone is full, voids at a rate of 40-45 percent are left as well.
- This principle of spacing is the governing principle for the preparation of concrete under this method.
- When coarse aggregates are full to make concrete, the voids built into the weight should be filled with some good material. Sand is used for this purpose.
- However, there will be voids between the grains of sand as well. These are filled with cement particles.
- In this way, the weight of the resulting concrete is either empty or dense. Cement binding material is used to give this dense cone a stone-like character.
- Concrete, artificial stone, in a broad sense.
- Collection classification is intended to determine the particle size of a given group of composites.
- This is usually found by the Method of Fineness Modulus. This method can be used to determine the best modulus for coarse combinations, fine aggregates, and all composites, i.e., composite composites.
- In this way, the ideal weight of the sample is taken and filtered through a series of sieves respectively. The number of sieve is five in coarse aggregates and ten in all aggregates.
Sieve Size of Collection.
Coarse Aggregates: 80 mm, 40 mm, 20 mm, 10 mm, IS No..480
Fine Aggregates: Numbers 480, 240, 120, 60, 30 and 15.
Total included: 80 mm, 40 mm, 20 mm, 10 mm, Nos: 480, 240, 120, 60, 30 and 15.
Flakiness Index
Object
For determination of flakiness index of coarse aggregate, where the size of the coarse aggregate are larger than 6.3mm .
Apparatus
- Thickness gauge
- Sieves [63, 50, 40, 31.5, 25, 20, 16, 12.5, 10 & 6.3mm]
- Balance [0-10 kg]
- Thickness Gauge
Procedure
- The sample was removed with the IS filter defined in the Table shown below.
- Thickness size and long length
- Thickness size and long length
- A minimum of 200 pieces for each fraction is taken and measured.
- In order to separate the faulty material, each component is individually measured by the thickness of the size gauge.
- The total amount of blurring objects that transmit the size gauge is measured with an accuracy of 0.1% of the sample weight.
Elongation Index
Objective
For determination of elongation index of coarse aggregate, where the size of the coarse aggregate is larger than 6.3 mm
Apparatus
- Length gauge
- Sieves (63mm,50mm,40mm,31.5mm,25mm,20mm,16mm,12.5mm,10mm)
- Balance (0-10kg)
- Oven (3000c)
Procedure
- The sample was removed with the IS filter defined in the Table shown below.
- A minimum of 200 pieces for each fraction is taken and measured.
- To separate the extended objects, each fraction is measured individually in length in the length gauge.
- Combined pieces from each tested segment that could not exceed the specified gauge length and its long cut sides are collected separately to obtain the total composite weight stored at the gauge length from each segment.
- The total amount of extended material retained by the length gauge is measured with an accuracy of 0.1% of the sample weight.
Impact Value
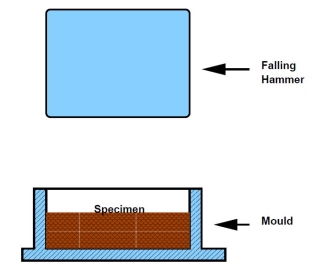
Fig no 28. Impact test apparatus
- Combined impact tests were performed to test for resistance to compound effects.
- The aggregates pass through a filter of 12.5 mm and are kept at 10 mm per filter are filled with a diameter of a diameter of 10.2 mm internal diameter and a depth of 5 cm attached to the metal base of the impact test machine.
- The content is completed in 3 layers where each layer is marked with 25 strokes.
- A steel hammer weighing 13.5 to 14 Kg is scheduled to be dropped with a free fall of 38.0 cm in v
- Ertical directions and a test sample is placed at 15 hits.
- The crushed joint is allowed to pass through a filter of 2.36 mm IS. And the impact value is measured as the percentage of aggregates that pass through the filter (W2) to the total sample weight (W1).
- Combined value = (W1 / W2) * 100
- Aggregates will be used to wear the course, the impact value should not exceed 30 percent. For bituminous macadams the maximum permissible value is 35 percent.
- In the basic studies of Water bound macadam the maximum allowable rate specified by the IRC is 40 percent.
Abrasion Value
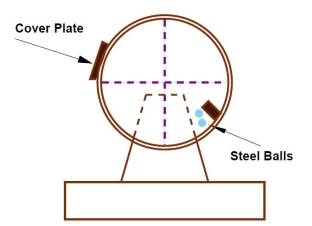
Fig no 29. Abrasion value setup
- Abrasion testing is performed to test the hardness of the material and to determine whether it is suitable for various stone construction activities.
- The abrasion test in Los Angeles is very popular to achieve hard materials and is standardized in India (IS: 2386 part-IV).
- The goal of the Los Angeles abrasion test is to find a percentage wear due to the rubbing action associated between the balls attached to the metal used as a serious offense.
- The Los Angeles machine consists of a 700 mm diameter inner diameter and 520 mm long attached to a horizontal axis that makes it possible to rotate (see Fig-2). A circular charge with round metal balls 48 mm wide and weighing 340-445 g is inserted into the cylinder and compound.
- The number of alrasive panorama varies depending on the sample size. The amount of compounds to be used depends on the catch and usually ranges from 5-10 kg.
- The cylinder is then locked and rotated at a speed of 30-33 rpm at a rate of 500 -1000 changes depending on the assembly rate.
- After the specified changes, the material is filtered through a filter of 1.7 mm and a fraction is transferred as a percentage of the sample weight. This figure is called the Los Angeles abrasion rate.
- A maximum of 40 per cent is allowed in the WBM study in the Indian state. In bituminous concrete, a maximum of 35 percent is specified.
Crushing Value
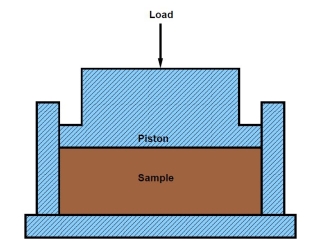
Fig no 30. Crushing test setup
- One of the models where the material is paved where it fails to press down under joint pressure.
- The test was rated with IS: 2386 part-IV and used to determine the combined crushing power.
- The combined value of the crush provides an approximate level of crushing resistance under the gradual crushing load.
- The test consists of placing a composite sample in a standard mold in a pressure test under normal load conditions.
- Dry aggregates pass through 12.5 mm sieve and 10 mm sieve are stored with a cylindrical dimension of 11.5 mm in diameter and 18 cm in height in three layers. Each layer is applied 25 times with a standard lubricant.
- The test sample is weighed and placed in a test cylinder in three layers each layer is also softened. The specimen is under a pressure load of 40 tons used slowly at an average of 4 tons per minute.
- The aggregates are then compressed and reduced by a filter of 2.36 mm and the weight of the passing object (W2) is expressed as a percentage of the total sample weight (W1) which is the total crushing value.
- Total crushing value = (W1 / W2) * 100
- A value less than 10 means a particularly strong combination while the above 35 can often be considered a weak combination.
Tests for fine aggregate:
Specific gravity
- The gravitational force of fine aggregate (sand) is defined as the mass of a given volume of aggregates in equal amounts of water. The gravitational force of fine aggregate (sand) is considered to be around 2.65 to 2.67.
- Quartz sand particles have a specific strength of between 2.65 to 2.67. While the odd clay starts from 2.70 to 2.80. Soils that contain a lot of organic matter or furry particles (such as diatomaceous earth) have a gravitational force of less than 2.60 (Some are as low as 2.00).
What is specific gravity of Aggregates?
The gravitational force of aggregate is considered to be the measure of the strength or quality of an object. The specified gravitational force is defined as the ratio of the weight of a given volume to a combination of the equivalent volume of water. Lower gravity scales are usually weaker than those with high gravity compounds. This property assists in the general identification of mergers.
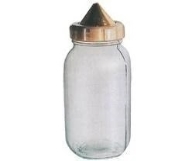
Fig no 31. Pycnometer bottle
Determination of Specific Gravity of Fine Aggregate as per IS: 2386 Part 3: (1963)
Hello friends, welcome to the world of Civil Allied Gyan. Read here the description, the list of apparatus, the IS code, the testing process, the formula and the web report about the determination of the gravitational force of a good collection.
Resources Required for Specific Integrated Voting Power Testing: -
- Pycnometer bottle of capacity 1000ml
- Touch stick
- Trench
- Balance scale
Is the Gravity Specific of Fine Aggregate test code: -
IS: 2386 (Part 3): 1963, Methods for testing concrete scales (Determining Specific Gravity of aggregates)
Procedure
- Take a clean and dry pycnometer and determine its empty weight (W₁ g).
- Take a pure sample of fine aggregate (about 1kg) to determine the gravitational force and transfer that to the pycnometer and weight (W₂ g). Aggregates better than 6.3mm taken.
- Pour the refined water into a pycnometer with a mixed sample at a temperature of 27 ºC, to water the sample only.
- Immediately after immersion, remove trapped air from the sample by moving or alternating the pycnometer, placing a finger in the hole at the top of the closed pycnometer.
- Clear the outer area of the pycnometer. Now the pycnometer is completely filled with water until the top hole, and after making sure that there is no more air trapped in the pycnometer, its weight (W₃ g).
- Transfer the value of the pycnometer to the care test being performed to ensure that all the components are transmitted. Clean the pycnometer.
- Re-fill the pycnometer with the added water to the top of the pycnometer, without any trapped air. It should be completely dry on the outside and take off weight (W₄ g).
- To fill the mineral, a special magnetic field bottle is used and the equipment is filled up to three times the volume of the bottle. The whole process of determining gravity is similar to that described above.
Seive Analysis
Objectives:
The whole process of sieve analysis determines the distribution of particle size of fine aggregates and determines whether it is suitable for use in concrete mixing.
Testing Resources
A series of IS filters
4.75 mm
2.36 mm
600 mic
300 mic
150 mic
75 mic
Procedure
- The sample was weighed exactly 1000g.
- First, we must clean all the sieve using a wire brush to make it clear that aggregates are trapped in some gaps.
- After that we have to prepare the sieve in the moving machine from top to bottom, in size from the largest (4.75mm) to the smallest (0.075mm).
- The sample was diluted using a collection of IS Sieves 10 minutes.
- After sieving is done, the merging with each filter is measured individually.
- The aggregate weight that passes through each filter is calculated as a percentage of the total sample weight.
- The same procedure is followed by two other samples.
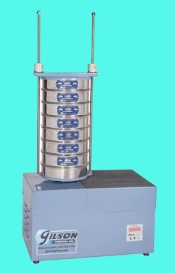
Fig no 32. Mechanical Sieve Shaker
Fineness Modules
The fineness modulus (FM) of aggregates may be a frightening term, but it is just a conceptual measure that describes the average size of particles in a composite sample. This feature provides the basis for selecting the approximate size of concrete joint design, but its actual impact is not always understood. The Fineness modulus is not a fixed value, as it provides a way to estimate the amount of integration needed to measure the mixing designs.
How to fineness modulus measure
Fineness modulus is determined using the percentage of size fractions from the sieve analysis and calculated for any selected series of sieve sizes. When designing concrete mixes, FM for good mixing is required to properly separate the mixes. Changes in the placement of the coarse aggregate section have little effect on the overall concrete structures. Combined partitions can be made using different cutting and fine-grained joints and blending techniques to control FM with concrete mix.
Origin of the Fineness Modulus Concept
Duff Abrams, an American inventor of the early 20th century, was an influential figure in the study of concrete structures and features. As well as explaining the importance of water / cement ratio and developing a fall test, he described the fineness modulus in 1918 as a way to separate concrete aggregates, simplify a gradation curve, and measure the appropriate size for use in mixing designs. Explaining the principle he said, "The integration of the same good modulus will require the same amount of water to produce the same coherence and provide the same strength concrete."
Includes Fineness Modulus
The simple FM calculation procedure requires a precise particle size analysis as described in ASTM C136, Standard Test Method for Sieve Analysis of Fine and Coarse Aggregates. In addition to the required particle size sizes, specific FM statistics must be included. Although manual upgrade of the sieve is permissible in standard, Gilson strongly recommends the use of the appropriate connector to ensure accuracy, durability and efficiency. After the filter has been analyzed and the fractions are measured in the correct proportions or proportions, the percentage of fractions is calculated.
Fineness Modulus of sand
To calculate the simple sand module, the total percentage accumulated stored in the following sieve is divided into 100: 150μm (No. 100), 300μm (No. 50), 600-μm (No. 30), 1.18mm (No. 16) , 2.36mm (No. 8), and 4.75mm (No. 4) of fine aggregates. If FM coarse aggregates are required, filters of 9.5mm (3⁄8in.), 19.0mm (3⁄4in), 37.5mm (11⁄2in) can be installed. There may be even larger sieves that can be added by continuing at a ratio of 2: 1 with the original sieve size. No additional equipment is required to make the determination. The same ASTM E11 test filters are used for integrated particle size analysis tests. In the example below, aggregate percentages from 4.75mm to 150µm are used to calculate the correct modulus for this fine mixing sample.
Alkali Aggregate Reaction
- Alkaline reaction - silica (ASR), more commonly known as "concrete cancer", is a painful inflammatory process that occurs over time in concrete between alkaline cement and active amorphous (eg, non-crystalline) silica found in many common compounds, sufficient moisture is provided.
- The pattern of cracks is associated with an alkaline-silica reaction that affects the concrete step barrier on the US highway. Note the common oily feature of the silicate debris imbibing the concrete surface on both sides of the crack.
- This undesirable chemical reaction results in the expansion of the altered composition by the formation of soluble and viscous gel of sodium silicate (Na2SiO3 • nH2O, and marked Na2H2SiO4 • nH2O, or N-S (sodium silicate hydrate), depending on the assembly received).
- This hygroscopic gel swells and increases in volume as it absorbs water: it has a high pressure inside the siliceous compound, which causes cracks and loss of concrete strength, eventually leading to its failure.
- The ASR can lead to severe cracking of the concrete, leading to serious structural problems that could force the demolition of a particular building.
- The extension of the concrete reaction between cement and composite size was first studied by Thomas E. Stanton in California in the 1930s with his publication in 1940.
Buckling of sand
- The increase in volume of a good compound due to the presence of moisture content is known as bulking. This is because the moisture causes a film of water around the sand particles leading to an increase in the volume of the sand, at a moisture content of about 5 to 8%, this increase in volume can be 20 to 40%, depending on the placement of the sand.
- The more effective it is, the more volume will be given to the moisture content provided. This practice is known as sand bulking.
- As the moisture content increases by adding more water, sand particles accumulate closer and the bulking value of the sand decreases. Therefore, dry sand and water-soaked sand are about the same size.
- Constipation of sand affects the balance of the sand to a large extent. Most with fine sand and less with coarse sand. If the right grant is not made for sand extraction, the cost of concrete, and vehicles will increase and it will result in less sandy loam and hard to operate and maintain.
Important facts regarding sand formation are as follows
- As the moisture content increases by adding more water, sand particles accumulate closer and the bulking value of the sand decreases.
- One of the reasons for adopting a weight measurement is the constipation of sand as weight loss avoids difficulty due to the abundance of sand.
- Sanding of the sand should be considered when the volumetric value of the value is accepted.
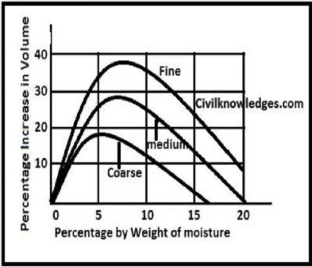
Fig no 33. Buckling of fine aggregate
Determining of buckling of fine aggregate
Opera and the process of determining the best percentage output
- Laboratory testing of bulk composites
- Field test for average quantity
Fine Aggregate Collection Laboratory Testing
Apparatus
- 250 ml measuring cylinder
- Weight balance
- Good combination
Procedure
- Take 500 grams of frozen fine aggregate at a temperature of 100 to 110 degrees Celsius for 24 hours. This is a weight measure as W1.
- Cool sand picks up airtight containers. So this weight ratio as W2.
- Sample water content is calculated as
- Wc = (W1-W2) X 100 / W1
- In a pan, 250 grams of sand take.
- In this case 2% by weight of water add. This is well integrated.
- The mixture is poured into a 250ml cylinder. This is compounded by shanking.
- The test was repeated with the remaining amount of 2% water sand at each time point. The reading takes as Y2, Y3… etc until the volume reading decreases.
- After their level, 4% of the water is added and the test continues until the sample is completely filled.
- For a standard sample in a measuring cylinder, add about 50 ml of water and stir the sample well.
ARTIFICIAL AND RECYCLED AGGREGATE
Artificial aggregates
- Many synthetic aggregates can be controlled, by industrial process products, such as various slags, or uncontrolled waste from other industrial processes, such as clinkers and ashes.
- Another important source of waste is the mining industry, including the extraction of coal and China clay.
- Some products that come out once or the waste can be made, or need to be recycled, to make things that are suitable for use as concrete mixers or that show special properties. In addition, other natural materials, such as perlite or vermiculite, can also be processed to produce compounds that reflect special properties.
- Demolition debris is reused to produce concrete scales. The RILEM (TC-121) technical committee recommended the separation of those compounds.
Recycled aggregate
- The construction industry produces a large amount of waste that needs to be recycled and used as recycled aggregates (RAs) for partial or complete environmental integration.
- Recycling reduces waste and reduces energy consumption and that is why it has an impact on the sustainable construction industry.
- In this chapter the need to redefine the current situation and situation around the world is highlighted. The structures of the RA are discussed. RAs weigh less than viral substances and higher water absorption.
- The state of the art of RA performance of concrete in a new and difficult world is summarized. The RA concrete exhibits low pressure and flexibility as well as low-strength mode and low cracking due to the porous nature of the RA and the old mud attached to the cement above the composite.
- The strength of the bond and the strength of the abrasion are less affected. Depletion, water infiltration and water infiltration by capillary increase with increased RA content.
- However, low performance can be reduced with a good mixing design using cement additives. Successful applications for RA in the manufacture of adhesive and truck concrete are also being discussed
Key takeaways
There are different tests for coarse aggregate which are
1. Specific gravity
2. Grading of aggregate
3. Flakiness index
4. Elongation index
5. Impact value
6. Abrasion value
7. Crushing value
There are different type of test for fine aggregate which are
1. Specific gravity
2. Seive analysis
3. Fineness modulus
4. Alkali aggregate
5. Buckling of sand
6. Artificial and recycle aggregate
Special Concrete - Light Weight Concrete and its Type
- Lightweight concrete may be described as a sort of concrete which incorporates an increasing agent in that it will increase the quantity of the combination whilst giving extra characteristics which includes nailability and lessened the useless weight.
- It is lighter than the traditional concrete. The use of light-weight concrete has been broadly un fold throughout international locations which includes USA, United Kingdom and Sweden.
- The essential specialties of light-weight concrete are its low density and thermal conductivity.
- Its blessings are that there may be a discount of useless load, quicker constructing quotes in creation and decrease haulage and managing costs.
- Lightweight concrete keeps its huge voids and now no longer forming laitance layers or cement movies while located at the wall.
- These studies became primarily based totally at the overall performance of aerated light-weight concrete.
- However, enough water cement ratio is essential to provide good enough concord among cement and water.
- Insufficient water can purpose loss of concord among debris, for that reason loss in energy of concrete.
- Likewise, an excessive amount of water can purpose cement to run off mixture to shape laitance layers, finally weakens in energy.
- Lightweight concrete has been used because the eighteen centuries through the Romans.
- The software at the ‘The Pantheon’ wherein it makes use of pumice mixture with inside the creation of solid in-situ concrete is the evidence of its usage.
- In USA and England with inside the overdue 19th century, clinker became used of their creation as an example the ‘British Museum’ and different low price housing.
- The light-weight concrete became extensively utilized in creation at some point of the First World War.
- The United States used particularly for shipbuilding and urban blocks.
- The foamed blast furnace-slag and pumice mixture for block making had been added in England and Sweden round 1930s.
- Nowadays with the development of technology, light-weight concrete expands its makes use of.
- For example, with inside the shape of perlite with its top notch insulating characteristics.
- It is broadly used as loose-fill insulation in masonry creation wherein it complements hearth place ratings, reduces noise transmission, does now no longer rot and termite resistant.
- It is likewise used for vessels, roof decks and different applications.
Materials utilized in Light weight concrete:
- Lightweight concrete may be produced through introducing:
- Gassing retailers which include aluminium powder or foaming retailers,
- Light-weight mineral mixture which includes per lite, vermiculite, pumice, elevated shale, slate, and clay, or plastic granules as mixture
Properties of Light weight concrete:
- Low Density
- Fire Resistance
- Sound Insulation
- Durability
- Thermal insulation
- Quality Control
Low Density
- The density of concrete varies from three hundred to 1200 kg/m³.
- The lightest grade appropriate for insulation proposed whilst the heavier grades with good enough energy appropriate for structural applications.
- The low density of cell concrete makes it appropriate for precast ground and roofing devices which can be smooth to deal with and shipping from the manufacturing unit to the sites.
Fire Resistance
- Lightweight concrete has outstanding hearth place-resisting properties.
- Its low thermal conductivity makes it appropriate for protective every other established shape the outcomes of fir
Sound Insulation
- Sound insulation in cell concrete is typically now no longer as suitable as in dense concrete.
Durability
- Aerated concrete is handiest barely alkaline. Due to its porosity and coffee alkalinity.
- It does now no longer deliver rust safety to metallic that's supplied through dense as compared concrete.
Thermal insulation
- The insulation fee of light-weight concrete is set 3 to 6, instances that of bricks and approximately ten instances of concrete.
- When a two hundred mm thick wall of aerated concrete of density 800 kg/ m3 has the identical diploma of insulation as a four hundred mm thick wall of density 1600 kg/ m3.
Quality Control
- Better first-rate manipulate exercised with inside the creation of a shape with light-weight concrete merchandise because of using manufacturing unit-made devices.
Types of Light weight Concrete:
Lightweight aggregate concrete:
- Lightweight aggregate concrete is referred to as an LWA.
- In the early 1950s, using light-weight concrete blocks familiar withinside the UK for the load-bearing internal leaf of hollow space walls.
- Soon thereafter the improvement and manufacturing of a brand new sort of synthetic LWA made it viable to introduce LWC of excessive energy, appropriate for structural work.
- These advances inspire the structural use of LWA concrete. Particularly wherein the want to lessen weight in a shape became an critical attention for layout or for the economy.
Aerated Concrete:
- Aerated concrete has the bottom density, thermal conductivity, and energy.
- Like timber, it is able to be sawn, screwed and nailed, however there are non-combustible.
- For works in-situ, the standard strategies of aeration are through blending in stabilized shape or through whipping air in with the useful resource of an air-entraining agent.
No fines concrete:
The time period no-fines concrete typically way concrete composed of cement and a coarse (9-19) aggregates handiest and the product so fashioned has many uniformly disbursed voids for the duration of its mass.
- Ordinary light-weight concrete organized from a binder, water best and coarse mixture with complete filling voids among the huge debris.
- Low Sand concrete, wherein the voids among the coarse mixture handiest partly packed with the paste.
- It additionally referred to as an opening graded concrete and dealt separately.
- In this example on best mixture use. Coarse debris of the mixture are coved through a skinny layer of cement, paste and the voids among them stay empty. It is referred to as no concrete.
- Aerated concrete crafted from a binder, water, best and coarse mixture, and a blowing agent which reduced the density of concrete.
Typical Light weight concrete mix:
- Lightweight concrete is a combination made with light-weight coarse aggregates inclusive of shale, clay, or slate, which offer it its feature low density.
- Structural light-weight concrete has an in-location density of ninety to a hundred and fifteen lb/ft³, while the density of everyday weight concrete tiers from a hundred and forty to a hundred and fifty lb/ft³.
- This makes light-weight concrete perfect for constructing current systems that require minimum pass sections with inside the foundation.
- It is being an increasing number of used to construct glossy foundations, and has emerged as a possible opportunity to everyday concrete.
- Nevertheless, a better compressive power of 7000 to 10,000 psi may be attained with light-weight concrete.
- However, this will compromise the density of the combination because it calls for the addition of greater pozzolans and water-decreasing admixtures to the concrete.
Key takeaways
1. Lightweight concrete keeps its huge voids and now no longer forming laitance layers or cement movies while located at the wall.
2. This study became primarily based totally at the overall performance of aerated light-weight concrete.
3. Aerated concrete is handiest barely alkaline. Due to its porosity and coffee alkalinity.
4. It does now no longer deliver rust safety to metallic that's supplied through dense as compared concrete.
Foam Concrete
- Foam concrete usually consists of cement mortar or fly ash and sand and water, although some suppliers recommend pure cement and water with an agent that produces lightweight mixtures.
- This slurry is also mixed with a foam made into a concrete mixing plant. The foam is made using a moisturizing agent, mixed with water and air from the generator. The foam operator used must be able to produce bubbles with a high degree of stability, resistant to physical and chemical processes of mixing, depositing and solidifying.
- Foam concrete mix can be poured or sprayed on moulds, or directly on parts of the building. Foam makes the Sulphur flow freely due to the thixotropic behaviour of foam bubbles, allowing it to be easily absorbed into the selected form or mould.
- Viscous materials require up to 24 hours to harden (or at least two hours if the smoke is treated at temperatures up to 70 ° C to speed up the process. Depending on the variability including ambient temperature. And moisture. Once solidified, the manufactured product can be removed from its mould.
- A new application in the production of foam concrete is to cut large-size concrete cakes into blocks of different sizes with a cutting machine using special metal wires. The cutting action occurs when the concrete is still soft.
Properties
Foam concrete is a versatile construction material with a simple and inexpensive method of production compared to air-cooled autoclave concrete. Foam compounds using foam-using ashes for this cheap compound are still cheap, and have little impact on the environment. Foam concrete is produced in quantities ranging from 200 kg / m3 to 1,600 kg / m3 depending on the application. Smaller products can be divided into different sizes. While the product is considered to be a type of concrete (with air bubbles replacing the whole), its thermal and sound insulation properties make it a very different application than conventional concrete.
Applications
Foam concrete can be produced in dry quantities of 400 to 1600 kg / m3 (25 lb / ft3 to 100 lb / ft3), with a capacity of about 7 to 10 days N / mm2 (145 to -1450 psi) respectively. The foam concrete is fire resistant, and its thermal and sound insulation properties make it ideal for a variety of purposes, from floor and ceiling protection, to useless filling. It also helps to restore the trench.
A few applications of foam concrete are:
- Bridge / bar road routes
- Pipe discharge / annual filling
- Back ditch
- Precast blocks
- Precast wall elements / panels
- Cast-in-situ / cast-in-place walls
- By defending the imposition of compensation
- Split down screens
- Partition roof screeds
- The filling of the deceased part
- Trench for restoration
- Sub-base on highways
- The filling of empty blocks
- Partition boards used
Key takeaways
1. Lightweight concrete may be described as a sort of concrete which incorporates an increasing agent in that it will increase the quantity of the combination whilst giving extra characteristics which includes nailbility and lessened the useless weight.
2. It is lighter than the traditional concrete. The use of light-weight concrete has been broadly un fold throughout international locations which includes USA, United Kingdom and Sweden.
No Fines Concrete
What is No-Fines Concrete?
- No-Fines Concrete is a lightweight concrete made of cement only, cement and water by leaving fine particles (sand or fine compounds) of ordinary concrete. The benefits, limitations and equity of the exemptions are discussed.
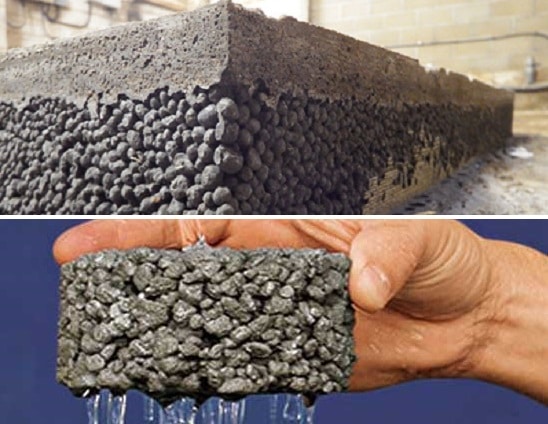
Fig no 34. No fines concrete
- Usually only one equal measurement, of more than 20 mm in size, is kept in 10mm. Concrete no-faes are popular because of the specific benefits you have over conventional concrete.
- The single-layer collection makes a beautiful, non-abrasive concrete, which in addition to getting large voids and therefore light weight, also gives a nice look to the build.
Advantages of No-Fines Concrete
- No fine concrete is a heavy concrete i.e. the density is approximately 25 to 30% less than normal concrete due to the lack of good adhesion, so the weight of the structure is small.
- Since it does not have good sand or aggregates, it has less drying shrinkage compared to conventional concrete
- It has a better heat protection feature than ordinary concrete and therefore helps in the construction of the outer wall.
- Since it does not have good aggregates, the required area for cement coverage has been greatly reduced. Therefore, the required amount of cement is reduced per cubic meter compared to conventional concrete. Therefore, it will save.
- Heavy concrete has no effect on quality due to the fragmentation of the compact cluster as it does not have good dimensions. Therefore, it can be thrown higher.
- No fine concrete can be assembled without the need for any types of concrete vibrators and can be easily made by touching the rods.
Limitations of No Fines Concrete
- Since there are no good compounds to fill the gaps in this concrete, it has a higher penetration than standard concrete. Therefore, it is not a good idea to build reinforced concrete without compensation concrete, as reinforcement can be easily eaten.
- To make this concrete inaccessible, an additional coat of construction mud is required, which adds to the cost.
- There is no concrete test that can be tested for effectiveness by using tests on standard concrete such as rolling or testing for rigidity. Performance rates and their testing methods are unknown.
Mix proportion of No-Fines Concrete
- No-fines concrete is usually made with aggregate / cement scales from 6: 1 to 10: 1. The standard aggregates used are usually sizes over 20 mm and stored at 10 mm.
- Unlike conventional concrete, where the strength is primarily controlled by the water / cement ratio, the strength of the concrete can be charged depending on the water / cement ratio, the estimated cement ratio and the weight of the concrete.
- The water / cement ratio for satisfactory consistency will vary between a minimum width of 0.38 and 0.52. The water / cement level should be chosen carefully. If a very low amount of water / cement is accepted, the adhesive will dry so much that the adhesive can be well coated with adhesive resulting in insufficient adhesion between the particles.
- On the other hand, if the water / cement ratio is too high, the glue will run down the concrete floor, especially if you move and fill in the gaps between the joints at the bottom and make that part more compact. This condition also reduces the adhesion between the adhesive and the adhesive due to the adhesion being much thinner.
- There is no standard method available, such as a descent test or an object measurement test to measure the consistency of a non-finite concrete. Perhaps a good test, visual experience and trial and error method would be the best guide to determine the water / cement ratio.
- No-faes concrete, when using standard aggregates, can show a density of about 1600 to 1900 kg / m3, but if no-faes concrete is made using lightweight aggregate, the size can reach approximately 360 kg / m3.
- Concrete of no-faes does not pose a major congestion problem. The use of a combination of equipment or vibration methods is not required. Simple rodding is sufficient for full filling.
- Concrete of no-faes does not give much to the formation side as the particles have a point of identification of the contact and the concrete does not move. Therefore, the side of the formworks can be removed in a much shorter time than ordinary concrete.
- However, the forms may need to be stored longer, when used as part of the structure, as the strength of the concrete decreases considerably. The compressive strength of the fine-grained concrete varies between 1.4 M Pa to 14 M.
- The strength of the bonded concrete bond is very low and, therefore, the reinforcement is not used in combination with the non-charged concrete. However, if the reinforcement needs to be applied to a non-abrasive concrete, it is advisable to touch the reinforcement with cement to improve the bond and protect it from cracking.
Key takeaways
1. No-Fines Concrete is a lightweight concrete made of cement only, cement and water by leaving fine particles (sand or fine compounds) of ordinary concrete. The benefits, limitations and equity of the exemptions are discussed.
2. Usually only one equal measurement, of more than 20 mm in size, is kept in 10mm. Concrete no-faces are popular because of the specific benefits you have over conventional concrete.
Self Compacting Concrete
- Self-compacting concrete (SCC) is a flowing concrete that doesn't require vibration and, indeed, have to now no longer be vibrated.
- It makes use of super plasticizers and stabilizers to seriously growth the benefit and price of glide.
- It achieves compaction into each a part of the mildew or formwork genuinely by using its personal weight with none segregation of the coarse aggregate.
- The consistence of the concrete is designated and measured as a glide price as opposed to the everyday stoop test.
SCC offers:
- Health and protection benefits (as no vibration is needed).
- Faster creation times.
- Increased workability and simplicity of glide round heavy reinforcement.
- Excellent sturdiness.
Advantages of SCC:
- No vibration is needed in the course of the position into forms.
- Placement of concrete easier.
- Reduces the concreting time.
- Increased sturdiness of structure.
- High Strength
Material used in SCC:
- The powdered substances that may be delivered are fly ash, silica fume, lime stone powder, glass filler and quartzite filler.
Tests for SCC:
Following are numerous techniques for checking out the houses of sparkling concrete:
- Slump glide test
- T50 stoop glide test
- J ring test
- V Funnel test
- V funnel at T5 minute
- L container test
- U container test
- Fill container test
- GTM display balance test
- Orimet test
Sr .no. | Method | Units | Typical mix | |
Minimum | Maximum | |||
1 | Slump cone by Abrams cone | Mm | 650 | 800 |
2 | T50slumpflow | Sec | 2 | 5 |
3 | J ring | Mm | 0 | 10 |
4 | V funnel | Sec | 8 | 12 |
5 | V funnelatT5minute | Sec | 0 | 3 |
6 | L box | (h2/h1) | 0.8 | 1.0 |
7 | U box | (h2-h1) Mm | 0 | 30 |
8 | Fill box | % | 90 | 100 |
9 | GTM screen stability test | % | 0 | 15 |
10 | Orimet | Sec | 0 | 5 |
Properties of SCC:
Strength:
Strength of concrete are of the subsequent types:
- Compressive strength
- Tensile strength
- Flexural strength
- Shear strength
1.Compressive Strength
- The dice specimens of concrete of the preferred percentage are solid in metallic or solid iron moulds, typically 6-inch dice.
- The general cylinder specimen of concrete is 6 inch in diameter and 12 inches in peak and solid in a mould commonly fabricated from solid iron;
- Standard cubes and cylinders are examined at prescribed ages, commonly, 28 days, with extra exams frequently made at 1, three, and seven days.
- The specimens are examined for crushing electricity below a checking out machine.
- The dice exams supply an awful lot more values of crushing electricity, typically 20 to 30 % extra than the ones given via way of means of cylinders.
Effect of age on concrete strength:
- Concrete attains electricity with time.
- Ordinary cement concrete profits above 70 to 75% of its very last electricity inside 28 days and approximately ninety to 95 % with inside the path of 1 year.
- It is frequently perfect to test the suitability of a concrete lengthy earlier than the effects of the 28-day check are available.
- When no particular records at the substances utilized in making concrete are available, the 28-day electricity can be assumed to be 1.5 instances of the 7 days’ electricity.
- Tests have proven that for concrete made with regular Portland cement the ratio of the 28 days to 7 days’ electricity commonly lies among 1.three to 1.7, and the bulk of the effects fall above 1.5.
2. Tensile strength
- Concrete could be very susceptible in tension.
- The tensile electricity of regular concrete levels from approximately 7 to 10 percentage of the compressive electricity.
3. Flexural strength
- The flexural electricity of undeniable concrete is nearly fully established upon the tensile electricity.
- However, experiments display that the modulus of rupture is substantially more than the electricity in tension.
4. Shear strength
- It is the actual figuring out issue with inside the compressive electricity of brief columns.
- The common electricity of concrete in direct shear varies from approximately 1/2 of of the compressive electricity for wealthy combinations to approximately 0.8 of the compressive electricity for lean combinations.
Workability:
- The electricity of concrete of a given blend percentage could be very significantly laid low with the diploma of its compaction.
- It is consequently essential that the consistency of the combinationture be such that the concrete may be transported, positioned and completed sufficiently effortlessly and without segregation.
- A concrete pleasant those situations is stated to be workable.
Elastic Properties:
- Concrete isn't always flawlessly elastic for any variety of loading, an considerable everlasting placing taking location for even low loads.
- The deformation isn't always proportional to the strain at any degree of loading.
- The elastic residences of concrete range with the richness of the aggregate and with the depth of the strain.
- They additionally range with the age of concrete.
Durability:
- Durability is the assets of concrete to face up to the circumstance for which it's been designed, without deterioration over a length of years.
- Lack of sturdiness may be resulting from outside sellers bobbing up from the surroundings or via way of means of inner sellers in the concrete.
Application of SCC:
- Construction of Bridges, buildings, tunnels.
- Precast Concrete Members
- Casting of slab and slender wall
Typical Mix:
- A easy device has been designed for self-compacting concrete (SCC) blend layout with 29% of coarse aggregate, substitute of cement with Meta kaolin and sophistication F fly ash, combos of each and managed SCC blend with 0.36 water/cement ratio(via way of means of weight) and 388 litre/m3 of cement paste volume.
Key Takeaways
1. Self-compacting concrete (SCC) is a flowing concrete that doesn't require vibration and, indeed, have to know no longer be vibrated.
2. Concrete isn't always flawlessly elastic for any variety of loading, an considerable everlasting placing taking location for even low loads.
High Density Concrete
- High density concrete is a concrete having a density with inside the variety of 6000 to 6400 kg/cu.m.
- High density concrete is likewise called Heavy weight concrete.
- High density concrete is specifically used for the cause of radiation protective, for counterweights and different makes use of in which excessive density is required.
- The excessive density concrete has a higher protective property, in order that it is able to shield dangerous radiations like X-rays, gamma rays, and neutrons.
- High density aggregates are used to attain heavy weight concrete. Some of the excessive density aggregates are, barite, ferro phosphorus, limonite, hematite, ilmenite, magnetite, goethite, metallic punching, and metallic shots.
- The factor to keep in mind is that in order to attain this sort of concrete, excessive constant water content material is required.
- The choice of the above cited aggregates specifically depends on the bodily houses like bulk density, unique gravity, Availability of substances, and its expenses.
- In order to attain workability, excessive density the aggregates have to be loose from dirt, oil or grease stains and different overseas matter.
- Or else, it's going to retard the hydration method and the powerful bonding of particles.
- Some of the boron additions like colemanite, boro calcite is used with inside the preparation of concrete to enhance the protective houses.
- These additions might also additionally have an effect on the placing time of concrete so, trial mixes have to be made and examined relying upon the suitability.
- As the call suggests, the density of this concrete varies from 3360 kg/m3 to 3840 kg/m3, while the density of regular concrete is of the order of 2400 kg/m3.
- The density of mild weight concrete is ready 1900 kg/m3 and that of regular concrete approximately 2400 kg/m3.
- Thus, the density of excessive density concrete is ready 50% greater than the density of traditional concrete.
- However, this concrete may be produced of density up to 5200 kg/m3 the use of iron as each nice and coarse mixture.
- With the arrival of the nuclear electricity, there's a big call for of the concrete technologists with inside the market.
- Due to using nuclear electricity generating reactors, big scale manufacturing of penetrating radiation and radioactive substances additionally has taken location.
- Thus, all nuclear electricity generating gadgets inclusive of nuclear reactors, particle accelerator, business radiography, x-ray and gamma ray remedy gadgets require nuclear protective cloth for the safety of the working employees in opposition to the organic risks inclusive of radiation.
- The regular in addition to excessive density concrete is powerful and low in cost for the development of everlasting guard in opposition to radiation.
Materials in High density concrete:
- All represent substances, cement, admixtures, and water utilized in excessive density concrete have to agree to the requirements as for regular density concrete, however the aggregates is unique and can require unique attention at some stage in handling, batching, blending, transporting and setting.
Aggregates:
- High density concrete (HDC), densities is executed via way of means of the use of excessive-density aggregates commonly iron oxides and relies upon on its meant use, bodily and chemical houses, availability and price.
- Concrete densities of 3700 to 3800 kg/m³, is offered utilizing aggregates with particle relative densities of as a minimum 4500 kg/m³ and for concrete densities of 4800 kg/m³ aggregates have to have a particle relative density of as a minimum 6000 kg/m³.
- Aggregate grading for HDC hardly ever agree to regular mixture requirements because the mixture are hardly ever made for concrete manufacturing, this have to be general via way of means of capacity customers because it isn't always adverse to the manufacturing of HDC.
- The maximum critical a part of HDC aggregates is that the grading have to be consistent and that a attainable grading restriction be agreed on with the dealer, to base the combination layout on.
- The chemical houses of all excessive-density aggregates have to be evaluated earlier than use, chemical reactivity and mainly in excessive alkaline environments as observed in cement pastes, long time sturdiness inclusive of alkali-mixture reactivity, sulphate and chloride assault and different impurities.
- The dealer have to be capable of offer a complete chemical evaluation of all capacity substances and opportunity substances to be used.
- With right technical assessment and planning, unique styles of aggregates may be blended on the dealer backyard to provide a concrete with predicted, detailed density.
- Cost thing are very critical as those aggregates are commonly greater highly-priced than regular aggregates, it is able to additionally be that the cloth might also additionally handiest be to be had in relative brief supply.
- The price of HDC will increase with density however now no longer essential in direct proportion.
- Aggregates have to be decided on for his or her shape (cubical or rounded and freed from flat or elongated, most density, workability, and price. Particle relative density of the nice mixture have to be just like that of the coarse mixture as decrease density nice mixture can cause segregation of the coarse mixture via the mortar.
- The grading of the coarse mixture have to be uniformly graded among 10 and 40mm, as in step with limits in Table 1. The grading of the nice mixture have to be in the restriction as proven in Table 1 as this will assist to save you segregation.
Sieve sizes mm:
Grading 1 for 37.5 mm most length aggregates % passing
Grading 2 for 19.0 mm most length aggregates % passing
Coarse aggregates:
Two styles of aggregates may be used for excessive density concrete namely:
Natural aggregates:
- Iron ores of diverse sorts had been used all over the globe for lots years (out of doors the U.K), with inside the UK imported iron ore is used.
- Using a few herbal going on aggregates concrete densities of about 4000 kg/m³ may be obtained. (J. Goodman, 2009)
- Different styles of herbal excessive-density aggregates which may be used for excessive density concrete (HDC) to be had in South Africa and the United Kingdom talk over with Table 2.
Man-made aggregates:
- To attain concrete densities above 4000 kg/m³ man-made or artificial cloth inclusive of ferrosilicon slag, metallic or lead shot may be used.
- For styles of man-made aggregates which may be used for excessive density concrete (HDC) to be had in South Africa and the United Kingdom talk over with Table 2.
Cements:
- All cements conforming to SANS 50197 as for traditional concrete may be used for HDC if it produces the desired bodily houses.
- If alkali-reactive materials are gift with inside the aggregates cements with low alkali contents or a appropriate combination of cements and cement extenders have to be used.
- Low-alkali cement now no longer having greater that zero.6 % Na2O-eq can be used with a doubtlessly alkali-reactive mixture inclusive of lead shot.
- The following extenders: Ground granulated blast furnace slag (GGBS), fly ash (FA) and Condensed silica fume (CFS) have decrease densities than Ordinary Portland Cement (OPC) and may be used in the event that they do now no longer lessen the density of the concrete under detailed limits, but states “The cement may be OPC or a mix of this with both Ground granulated blast furnace slag, Pozzolanic fly ash; the latter if you want to now no longer lessen the density of the concrete however might also additionally decorate the in any other case terrible workability”.
- Fly ash blends and decrease water contents can effectively be used to boom the density of concretes. When lad shot is used High alumina cement (HAC) should be used, because it reduces the chemical reactivity of lead in excessive alkaline conditions.
- When the use of alkali-reactive mixture (lead shot) deleterious enlargement may be avoided whilst the use of excessive-alkali cements via way of means of including extenders complying with SANS 1491 via way of means of the use of a minimal percent of the subsequent extenders via way of means of general mass of cement:
At least 40% Slag (S) via way of means of mass
At least 15% CSF via way of means of mass
At least 20%via way of means of mass
Admixtures:
- Adding admixtures can minimize segregation, bleeding, each of which may be complex with HDC. The sturdiness may be advanced with a low loose water/cement ratio (w/c) in particular so in structural grade HDC.
- Using terrific plasticizers is usually recommended which in conjunction the cement kind might also additionally marginally boom concrete density.
- Super plasticizers are useful in decreasing water to minimize bleeding and preserve a cohesive blend that has minimal segregation.
The following admixture may be utilized in HDC:
- Air-entraining admixtures because it controls bleeding and agreement enhance workability and help in acquiring greater homogenous concrete however will lessen the density of the concrete.
- Water-decreasing admixtures because it will boom concrete density via way of means of decreasing the quantity of water with inside the blend, water is the cloth utilized in HDC with the bottom density.
- Shrinkage-decreasing admixtures because it make sure dense, crack-loose concrete used for radiation-protective concrete
- When lead shot or lead containing aggregates are to be used, the subsequent have to be taken into consideration whilst choosing a chemical admixture.
- The alkali content material of chemical admixtures for concrete utilized in South Africa is among approximately zero.2 and 7%. In many times the contribution to the alkali content material of the pore answer is big and can't be ignored.
- One of the extensively used terrific plasticizers has a Na2O-eq of approximately five% and if introduced at 1% of cement to concrete with a cement content material of 350 kg/m³ it's going to advert 0.17 kg/m³ Na2O-eq to the concrete.
- Lithium primarily based totally compounds may be used with lead shot to manipulate the alkali reactivity.
- The impact of admixtures have to be installed beneath discipline conditions, ideally via way of means of testing, to decide if the admixtures attain the desired effects or completely unsuitability.
Water:
- Water will be easy and loose from adverse concentrations of acids, alkalis, salts, sugar and different natural or chemical materials that would impair the sturdiness and power of concrete or imbedded metallic.
Proportioning, blending and setting of High Density Concrete:
- The blend proportions for those excessive density concrete is identical as that of regular concrete.
- Conventional approach of blending and setting is utilized in excessive density concrete. The maximum critical aspect is to save you overloading the mixer in particular whilst heavy weight aggregates inclusive of steels are used. Batch sizes have to be decreased to forty to 50% of the allowable mixer capacity. Also keep away from extra blending as it will bring about workability and bleeding of concrete.
- Preplaced mixture strategies may be followed whilst setting heavy weight concrete. In this approach the aggregates are located in forms , an appropriate grout made from cement, sand and water is pumped over the located aggregates, a good way to fill the voids in between the aggregates. This approach prevents the segregation of coarse aggregates additionally reduces drying shrinkage and facilitates us to attain concrete of uniform density and composition.
- Puddling approach also can be followed. In this approach, the mortar is located in varieties of 2″ thick and the coarse aggregates are located over it and vibrated internally. Care have to be taken that, the coarse aggregates are allotted evenly.
- Pumping of heavy weight concrete may be followed handiest the peak is limited. The heavy weight concrete can't be pumped to large distances due to their extra densities
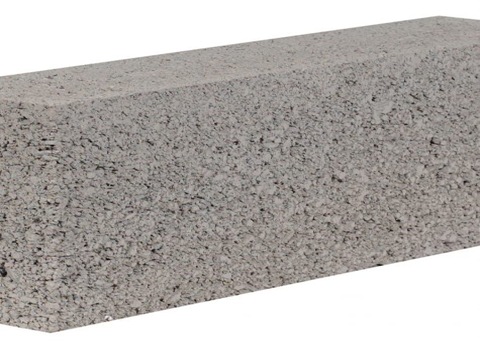
Fig no 35. High density concrete
Key takeaways
1. High density concrete is specifically used for the cause of radiation protective, for counterweights and different makes use of in which excessive density is required.
Fibre Reinforced Concrete, Geo Polymer Concrete and Ferrocement Technique
Fibre Reinforced Concrete
- Fibre Reinforced Concrete is a composite cloth which include fibrous cloth which will increase its structural integrity.
- It consists of combinations of cement, mortar or concrete and discontinuous, discrete, uniformly dispersed appropriate fibers.
- Fibers are normally utilized in concrete to govern cracking because of plastic shrinkage and to drying shrinkage.
- They additionally lessen the permeability of concrete and consequently lessen the bleeding of water.
Advantages of Fiber-strengthened concrete:
- Fibers strengthened concrete can be beneficial in which excessive tensile power and decreased cracking are proper or whilst traditional reinforcement cannot be placed.
- It improves the effect power of concrete, limits the crack boom and ends in a extra stress potential of the composite cloth.
- For commercial projects, macro-artificial fibers are used to enhance concrete’s sturdiness.
- Made from artificial substances, those fibers are lengthy and thick in length and can be used as a substitute for bar or material reinforcement.
- Adding fibers to the concrete will enhance its freeze-thaw resistance and assist maintain the concrete sturdy and appealing for prolonged periods.
- Improve blend cohesion, enhancing pumpability over lengthy distances.
- Increase resistance to plastic shrinkage in the course of curing.
- Minimizes metallic reinforcement requirements.
- Controls the crack widths tightly, consequently enhancing sturdiness.
- Reduces segregation and bleed-water.
- FRC, longevity is ready 10 to forty instances that of undeniable concrete.
- The addition of fibers will increase fatigue power.
- Fibers boom the shear potential of strengthened concrete beams.
Application of Fiber-strengthened concrete:
The programs of fiber strengthened concrete rely on the applicator and builder in taking gain of the static and dynamic traits of the cloth. Some of its vicinity of software is-
- Runway
- Aircraft Parking
- Pavements
- Tunnel Lining
- Slope Stabilization
- Thin Shell
- Walls
- Pipes
- Manholes
- Dams
- Hydraulic Structure
- Elevated decks
- Roads
- Bridges
- Warehouse floors
Fiber Types:
- Fibers for concrete are to be had in exclusive sizes and shapes.
- The essential elements affecting the function of fiber-strengthened concrete are a water-cement ratio, percent of fibers, diameter and duration of fibers.
- Given beneath are exclusive varieties of fiber-strengthened concrete utilized in production.
Steel Fiber Reinforced Concrete:
- Steel fiber is a metallic reinforcement. A sure quantity of metallic fiber in concrete can motive qualitative modifications in concrete’s bodily property.
- It can significantly boom resistance to cracking, effect, fatigue, and bending, tenacity, sturdiness, and others.
- For enhancing lengthy-time period behavior, improving power, longevity, and strain resistance, SFRC is being utilized in systems which includes flooring, housing, precast, bridges, tunneling, heavy-responsibility pavement, and mining.
- The varieties of metallic fibers are described via way of means of ASTM A820 are, Type I: cold-drawn cord, Type II; reduce sheet, Type III: melt-extracted, Type IV: mill reduce and Type V: changed cold-drawn cord
Polypropylene Fiber Reinforced (PFR) Concrete:
- Polypropylene fiber strengthened concrete is likewise referred to as poly propene or PP.
- It is a artificial fiber, converted from propylene, and utilized in loads of programs.
- These fibers are normally utilized in concrete to govern cracking because of plastic shrinkage and drying shrinkage.
- They additionally lessen the permeability of concrete and consequently lessen the bleeding of water.
- Polypropylene fiber belongs to the institution of polyolefins and is partly crystalline and non-polar.
- It has comparable homes as poly ethylene, however it's far tougher and greater warmth resistant.
- It is a white rugged cloth with excessive chemical resistance.
- Polypropylene is made from propylene fuel with inside the presence of a catalyst which includes titanium chloride.
- Polypropylene fiber shows accurate warmth-insulating homes and is especially immune to acids, alkali, and natural solvents.
Glass Fiber Reinforced Concrete:
- Glass fiber strengthened concrete is a cloth which include severa extraordinarily first-rate fibers of glass.
- Glass fiber has kind of similar mechanical homes to different fibers which includes polymers and carbon fiber.
- Although now no longer as inflexible as carbon fiber, it's far tons less expensive and notably much less brittle whilst utilized in composites.
- Glass fibers are consequently used as a reinforcing agent for lots polymer merchandise; to shape a totally sturdy and comparatively light-weight fiber-strengthened polymer (FRP) composite cloth known as glass-strengthened plastic (GRP), additionally popularly referred to as “fiberglass”.
- This cloth incorporates very little air or fuel line, is denser, and is a miles poorer thermal insulator than is glass wool.
Polyester fibers:
- Polyester fibers are utilized in fiber-strengthened concrete for commercial and warehouse floors, pavements and overlays and precast merchandise.
- Polyester micro- and macro-fibers are utilized in concrete to offer advanced resistance to the formation of plastic shrinkage cracks as opposed to welded cord material and to decorate longevity and the capacity to supply structural potential whilst well designed, respectively.
- Polyester micro- and macro-fibers are utilized in concrete to offer advanced resistance to the formation of plastic shrinkage cracks as opposed to welded cord material and to decorate longevity and the capacity to supply structural potential whilst well designed, respectively.
Carbon fibers:
- Carbon fibers are fibers approximately 5–10 micrometers in diameter and composed in general of carbon atoms.
- Carbon fibers have numerous benefits such as excessive stiffness, excessive tensile power, low weight, excessive chemical resistance, excessive-temperature tolerance and coffee thermal expansion.
- Carbon fibers are normally mixed with different substances to shape a composite.
- When impregnated with a plastic resin and baked it bureaucracy carbon-fiber-strengthened polymer (frequently known as carbon fiber) which has a totally excessive power-to-weight ratio, and is extraordinarily inflexible even though particularly brittle.
- Carbon fibers also are composited with different substances, which includes graphite, to shape strengthened carbon composites, that have a totally excessive warmth tolerance.
Macro artificial fibers:
- Macro artificial fibers are crafted from a mix of polymers and have been at the beginning advanced to offer an opportunity to metallic fibers in a few programs.
- Initially, they have been diagnosed as a ability opportunity to metallic fibers in sprayed concrete, however growing studies and improvement confirmed that that they'd a function to play withinside the layout and production of ground-supported slabs and a huge variety of different programs.
- They are specifically appropriate for presenting nominal reinforcement in competitive environments, which includes marine and coastal systems, as they do now no longer go through the troubles of staining and spalling which could end result from the corrosion of metallic.
- Besides, due to the fact they may be non-conducting, they had been utilized in tram and mild railway developments.
Micro-artificial fibers:
- Micro-artificial fibers offer advanced resistance to the formation of plastic shrinkage cracks as opposed to welded cord reinforcement, they may be not able to offer any resistance to similarly crack width openings due to drying shrinkage, structural load or different sorts of strain.
- However, those merchandise need to be frequently laid out in any form of concrete to enhance cracking resistance, spall protection, freeze-thaw sturdiness and enhance the homogeneity of concrete in the course of placement.
Natural fibers:
- The herbal fiber is without delay available from an animal, vegetable, or mineral supply and convertible into nonwoven fabric which includes felt or paper or, after spinning into yarns, into woven cloth.
- A herbal fiber can be similarly described as an agglomeration of cells wherein the diameter is negligible in evaluation with the duration.
- Although nature abounds in fibrous substances, in particular cellulosic kinds which includes cotton, wooden, grains, and straw.
- The use of herbal fibers in making concrete is usually recommended in view that numerous varieties of those fibers are to be had domestically and are plentiful.
- The concept of the use of such fibers to enhance the power and sturdiness of brittle substances isn't new; for example, straw and horsehair are used to make bricks and plaster.
- Natural fibers are appropriate for boosting concrete and are without difficulty to be had in growing countries.
Cellulose fibers:
- Cellulose fibers are made with ethers or esters of cellulose, which may be acquired from the bark, wooden or leaves of plants, or different plant-primarily based totally cloth.
- In addition to cellulose, the fibers may comprise hemi cellulose and lignin, with exclusive possibilities of those additives changing the mechanical homes of the fibers.
- The predominant programs of cellulose fibers are with inside the fabric industry, as chemical filters, and as fiber-reinforcement composites, because of their comparable homes to engineered fibers, being every other alternative for bio composites and polymer composites.
Geo Polymer Concrete
- Geo polymer is the name given to the Daidovits in 1978 for items that appear in chains or networks or unusual molecules.
- Geopolymer cement concrete is made using waste materials such as fly ash and ground granulated blast furnace slag (GGBS). An ash fly is a waste product produced from a hot power plant and the granulate blast soil in a furnace is processed as a metal waste.
- Both fly ash and GGBS are processed by appropriate technology and applied to concrete operations in the form of a geo polymer concrete. The use of this concrete helps to reduce waste stocks and reduces carbon emissions by reducing demand for Portland cement.
- A key feature of the geo polymers source of silicon and aluminum is supplied by natural thermal agents (e.g. kaolinite) or industrial products (e.g. Fly ash or slab) and an alkaline solution that makes these materials chains and networks to create strong bond. Also called alkaline cement or inorganic polymer cement.
Composition of Geo polymer Concrete
The following materials are required to produce this concrete:
- Fly ash - Fly ash generator
- GGBS - Metal Product
- Good collection and heat collection as required for standard concrete.
- GPCC alkaline activator solution as described above. The Catalytic liquid system is used as an alkaline activator solution. It is a combination of alkali silicates and hydroxide solutions, in addition to pure water. The role of the alkaline activator solution is to activate geopolymeric resource sources containing Si and Al such as fly ash and GGBS.
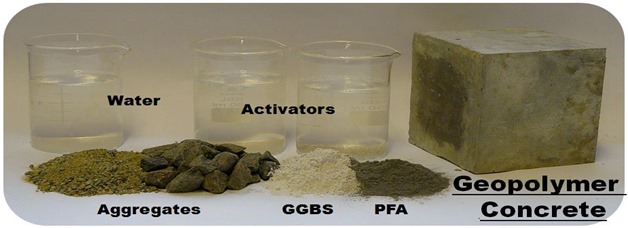
Fig no 36. Geo polymer Concrete Materials
Mechanical properties of Geo polymer Concrete
- Geo polymer concrete pressures were obtained up to 70 MP a (N / mm2). Concrete gains its compression strength much faster and faster than conventional Portland concrete.
- Concrete strength after 24 hours was found to be more than 25 M Pa. Pressure capacity after 28 days was found to be 60 to 70 M Pa. -Ref. Paper by James Aldred and John Day and test results by SERC Chennai.
Other properties of Geo polymer Concrete:
- The reduction in dryness is very small compared to cemen. This makes it ideal for members of a dense and highly restricted concrete structure.
- It has a lower hydration temperature compared to cement.
- Fire resistance is much better than OPC-based concrete. -Reference - Paper by - James Aldred and John Day.
- This concrete measure of jas chloride permeability is 'low' to 'very low' according to ASTM 1202C. It provides better protection of metal reinforcement from corrosion compared to traditional cement mortar.
- This concrete is found to have a very high acid content when tested under 2% and 10% exposure to sulfuric acid.
Application of Geo polymer Concrete
- Applications are similar to cement cement. However, the subject has not been used extensively in various programs.
- This concrete is used for the construction of paved stones, retaining walls, water tanks, precast bridge supplies.
- Recently the world's first building to be built on earth, the University of Queensland's Global Change Institute (GCI) was built using geo polymer concrete. It is a four-story high-rise building for public use.
Ferro Cement Technique
- Mining
- Crushing, stacking, and reclaiming of uncooked substances.
- Raw meal drying, grinding, and homogenization.
- Clinkerization.
- Cement grinding and garage.
- Packing
Mining:
- The cement production system begins off evolved from the mining of uncooked substances which might be utilized in cement production, specially limestone and clays.
- A limestone quarry is with inside the plant region and a clays quarry is as a ways from the plant region as 25 km.
- The limestone is excavated from open forged mines after drilling and blasting and loaded onto dumpers which shipping the substances and sell off into hoppers of limestone crushers.
- The clays are excavated from open forged mines and loaded onto dumpers which shipping the substances and sell off into open backyard garage.
- Then it's miles transported through vehicles and unloaded into the hopper of a clay crusher.
- They are 3 varieties of clay utilized in cement production, specifically silty clay, Zafarana clay, and Kaolin.
- Other uncooked substances are used to govern the kiln feed blend design, specifically sand, and iron ore.
- The sand and iron ore are shipping from outdoor the plant (from extraordinary suppliers) through vehicles and unloaded into open backyard piles, known as sand and iron ore piles.
Crushing, stacking, and reclaiming of uncooked substances:
- The limestone is beaten with inside the first crusher known as a jaw crusher after which fed into the second one crusher known as an effect crusher with blending of clays to lessen particle length beneath 50mm.
- The discharged uncooked blend (limestone 70%, clays 30%) is fed onto a belt conveyor and exceeded throughout a bulk fabric analyzer.
- The uncooked blend is fed right into a round garage unit known as a uncooked blend garage.
- Then, the combination is extracted transversely from the stockpile through reclaimers and conveyed to a uncooked mill bin known as the uncooked blend bin for grinding.
- The different uncooked substances which might be utilized in cement production, known as additives, are excessive purity limestone, sand and iron ore.
- The excessive purity limestone is beaten in a lone in jaw crusher after which beaten extra in a secondary crusher to lessen the scale to absolutely byskip via a 50mm sieve.
- Then, it's miles stacked through a limestone stacker right into a longitudinal garage unit known as the limestone garage stockpile.
- Finally, the limestone is extracted transversely from the stockpile through reclaimer and conveyed to a uncooked mill bin, known as the limestone bin, for grinding.
Raw meal drying, grinding, and homogenization:
- The uncooked blend, excessive grade limestone, sand, and iron ore are fed from their containers to uncooked turbines, known as air swept turbines, for drying and pleasant grinding.
- The uncooked mill includes chambers, separated through diaphragm, specifically a drying chamber and a grinding chamber.
- The warm gases coming from a pre heater (pre heater / kiln machine) input the mill and are utilized in uncooked turbines for drying.
- Then the drying substances input the grinding chamber of uncooked turbines for pleasant grinding.
- The grinding chamber includes a positive amount of ball price in a extraordinary sizes starting from 30mm to 90mm.
- The warm fuel line and grinding substances mill outlet feeds to a separator which separates pleasant and path product.
- The latter, known as reject, is dispatched to the mill inlet thru an air slide for regrinding.
- The warm fuel line and pleasant substances input a multistage "cyclone" to split a pleasant substances and gases.
- The pleasant fabric, known as uncooked meal, is accrued from the multi-cyclone after which fed into an air slide for lifting known as an Aeropol.
- The warm gases with very pleasant substances input an electrostatic precipitator to split the pleasant substances from gases.
- The very pleasant substances known as pre heater dirt or electrostatic separator dirt is accrued from filters and fed into screw conveyors and are then combined with the pleasant fabric in an air slide and transported to an air elevate vessel thru air slide.
- In the air elevate, the uncooked meal is lifted to the silo through compressed air to the air slide after which saved and homogenized in a concrete silo.
- Raw meal extracted from the silo, now known as kiln feed, is fed to the pinnacle of the pre heater thru an air elevate known as the Poldos for pyro-processing.
Clinkerization:
- Cement clinker is made through pyro processing of kiln feed into the pre heater-kiln machine. The pre-heater-kiln machine includes a multi-degree cyclone
- Pre heater with 5 stages, combustion chamber, riser duct, rotary kiln, and grate cooler.
- In the pre heater, the kiln feed is preheated through warm fuel line coming from the combustion chamber and rotary kiln.
- Then the preheated kiln feed is partly calcined (made powdery) in a combustion chamber and riser duct after which absolutely calcined in a rotary kiln in addition to heated to about 1400 C to shape clinker additives C3A, C4AF, C2S, and C3S.
- The foremost supply of warmth is herbal fuel line.
- Natural fuel line is fired as a major gasoline (100 %) with inside the foremost burner rotary kiln and a 95% herbal fuel line and 5.0% heavy oil aggregate with inside the combustion chamber.
- The gasoline is used to offer the warmth required to transform the kiln feed into clinker.
- Hot clinker discharge from the kiln drops onto the grate cooler for cooling from about 1350-1450 C to about one hundred twenty C.
- In the cooler, the amount of cooling air required for clinker cooling is extracted from the environment through extraordinary cooling lovers and fed into the cooler chambers and pressurized via the cooler plate and clinker bed.
- The cooled clinker discharges from the cooler into the pan conveyor and it's miles transported to the clinker garage.
- The clinker is taken from the clinker garage to cement ball mill hoppers for cement grinding.
- Part of the recent air extracted from the cooler is applied as a secondary and tertiary air for combustion in rotary kiln and combustion chamber, respectively.
Cement grinding and garage:
- Clinker and gypsum for OPC, limestone for limestone cement, and slag for slag cement are all extracted from their respective hoppers and fed to the cement turbines.
- The ball mill grinds the feed to a pleasant powder in chambers, specifically the primary and 2d chambers.
- The chambers have a positive amount of ball price of various sizes from 17mm to ninety mm.
- The mill discharge is fed to a bucket elevator which takes the fabric to a separator which separates pleasant and coarse product.
- The latter is dispatched to the mill inlet for regrinding and the very last product is saved in concrete silos.
Packing:
- Cement extracted from silos is conveyed to the automated digital packers wherein it's miles packed in 50 kg luggage and dispatched in vehicles.
Key takeaways
1. Fibers strengthened concrete can be beneficial in which excessive tensile power and decreased cracking are proper or whilst traditional reinforcement can not be placed.
2. The clays are excavated from open forged mines and loaded onto dumpers which shipping the substances and sell off into open backyard garage.
3. Geo polymer is the name given to the Daidovits in 1978 for items that appear in chains or networks or unusual molecules.
4. Geo polymer cement concrete is made using waste materials such as fly ash and ground granulated blast furnace slag (GGBS). An ash fly is a waste product produced from a hot power plant and the granulate blast soil in a furnace is processed as a metal waste.
Fiber Reinforced concrete:
- Fiber Reinforced Concrete is composite cloth which include fibrous cloth which will increase its structural integrity.
- It consists of combinations of cement, mortar or concrete and discontinuous, discrete, uniformly dispersed appropriate fibers.
- Fibers are normally utilized in concrete to govern cracking because of plastic shrinkage and to drying shrinkage.
- They additionally lessen the permeability of concrete and consequently lessen the bleeding of water.
Advantages of Fiber-strengthened concrete:
- Fibers strengthened concrete can be beneficial in which excessive tensile power and decreased cracking are proper or whilst traditional reinforcement cannot be placed.
- It improves the effect power of concrete, limits the crack boom and ends in a extra stress potential of the composite cloth.
- For commercial projects, macro-artificial fibers are used to enhance concrete’s sturdiness.
- Made from artificial substances, those fibers are lengthy and thick in length and can be used as a substitute for bar or material reinforcement.
- Adding fibers to the concrete will enhance its freeze-thaw resistance and assist maintain the concrete sturdy and appealing for prolonged periods.
- Improve blend cohesion, enhancing pump ability over lengthy distances.
- Increase resistance to plastic shrinkage in the course of curing.
- Minimizes metallic reinforcement requirements.
- Controls the crack widths tightly, consequently enhancing sturdiness.
- Reduces segregation and bleed-water.
- FRC, longevity is ready 10 to forty instances that of undeniable concrete.
- The addition of fibers will increase fatigue power.
- Fibers boom the shear potential of strengthened concrete beams.
Application of Fiber-strengthened concrete:
The programs of fiber strengthened concrete rely on the applicator and builder in taking gain of the static and dynamic traits of the cloth. Some of its vicinity of software is-
- Runway
- Aircraft Parking
- Pavements
- Tunnel Lining
- Slope Stabilization
- Thin Shell
- Walls
- Pipes
- Manholes
- Dams
- Hydraulic Structure
- Elevated decks
- Roads
- Bridges
- Warehouse floors
Fiber Types:
Fibers for concrete are to be had in exclusive sizes and shapes.
The essential elements affecting the function of fiber-strengthened concrete are a water-cement ratio, percent of fibers, diameter and duration of fibers.
Given beneath are exclusive varieties of fiber-strengthened concrete utilized in production.
Steel Fiber Reinforced Concrete:
- Steel fiber is a metallic reinforcement. A sure quantity of metallic fiber in concrete can motive qualitative modifications in concrete’s bodily property.
- It can significantly boom resistance to cracking, effect, fatigue, and bending, tenacity, sturdiness, and others.
- For enhancing lengthy-time period behavior, improving power, longevity, and strain resistance, SFRC is being utilized in systems which includes flooring, housing, precast, bridges, tunneling, heavy-responsibility pavement, and mining.
- The varieties of metallic fibers are described via way of means of ASTM A820 are, Type I: cold-drawn cord, Type II; reduce sheet, Type III: melt-extracted, Type IV: mill reduce and Type V: changed cold-drawn cord
Properties of Fiber Reinforced Concrete:
Compressive Strength:
- The presence of fibers might also additionally regulate the failure mode of cylinders; however, the fiber impact can be minor at the development of compressive power values (zero to fifteen percentage).
Modulus of Elasticity:
- Modulus of elasticity of FRC will increase slightly with a boom with inside the fibers content material.
- It became located that for every 1 percentage boom in fiber content material through quantity there may be a boom of three percentage withinside the modulus of elasticity.
Flexure:
- The flexural power became said [2j to be improved through 2. Five instances the usage of four percentage fibers.
Toughness:
- For FRC, sturdiness is set 10 to forty instances that of undeniable concrete.
Splitting Tensile Strength:
- The presence of three percentage fiber through quantity became said to boom the splitting tensile power of mortar approximately 2.5 instances that of the unreinforced one.
Fatigue Strength:
- The addition off bers will increase fatigue power of approximately ninety percentage and 70 percentage of the static power at 2 x 106 cycles for non-opposite and complete reversal of loading, respectively.
Impact Resistance:
- The effect power for fibrous concrete is typically five to ten instances that of undeniable concrete relying at the quantity of fiber
Corrosion of Steel Fibers:
- A lO-12 months’ publicity of steel fibrous mortar to out of doors weathering in an commercial surroundings confirmed no unfavourable impact at the power properties.
- Corrosion became located to be restricted best to fibers virtually uncovered at the surface.
- Steel fibrous mortar constantly immerse in seawater for 10 years exhibited a fifteen-percentage loss in comparison to forty percentage power lower of undeniable mortar.
Flexure:
- The use of fibers in bolstered concrete flexure contributors will increase ductility, tensile power, second ability, and stiffness.
- The fibers enhance crack manage and keep publish cracking structural integrity of contributors.
Torsion:
- The use of fiber do away with the unexpected failure feature of undeniable concrete beams.
- It will increase stiffness, torsion power, ductility, rotational ability, and the range of cracks with much less crack width.
Shear:
- Addition of fibers will increase shear ability of bolstered concrete beams as much as a hundred percentage.
- Addition of randomly allotted fibers will increase shear-friction power, the primary crack power, and final power.
Polymer concrete is an alternative to portland cement that is used to bond a mixture of aggregates together with epoxy binders. It is used in construction projects to provide added strength and can be modified with a range of resins. Polymer concrete provides very good resistance against corrosion and minimal chemical reactivity.
A polyester, vinyl resin or epoxy resin is often used to manufacture polymer concrete. This allows the concrete to be poured, then hardened. Polymer concrete cures through a chemical reaction with the polymer material. This type concrete is ideal for reaching areas that are not easily accessible.
Polymer concrete offers a range of benefits depending on the resin used to make it. Acrylic resins set quickly and offer resistance to harsh weather conditions, while epoxies create a strong material with little curing shrinkage. Furan resins can withstand high temperatures, and polyurea resins can replace formaldehydes or other hazardous compounds for construction purposes.
- Chemical admixtures are the components in concrete aside from port land cement, water, and combination which might be introduced to the combination at once earlier than or for the duration of blending.
- Producers use admixtures generally to lessen the value of concrete construction; to adjust the residences of hardened concrete; to make sure the best of concrete for the duration of blending, transporting, setting, and curing; and to conquer sure emergencies for the duration of concrete operations.
- Successful use of admixtures relies upon on using suitable techniques of batching and concreting.
- Most admixtures are provided in ready-to-use liquid shape and are introduced to the concrete on the plant or on the jobsite.
- Certain admixtures, along with pigments, expansive agents, and pumping aids are used most effective in extraordinarily small quantities and are commonly batched with the aid of using hand from premeasured containers.
- The effectiveness of an admixture relies upon on numerous elements including: kind and quantity of cement, water content material, blending time, stoop, and temperatures of the concrete and air.
- Sometimes, results much like the ones done thru the addition of admixtures may be done with the aid of using changing the concrete aggregate-decreasing the water-cement ratio, including extra cement, the usage of a extraordinary sort of cement, or converting the combination and combination gradation.
- Admixtures are classed consistent with characteristic. There are 5 wonderful lessons of chemical admixtures: air-entraining, water-decreasing, retarding, accelerating, and plasticizers (super plasticizers).
- All different styles of admixtures fall into the strong point class whose capabilities encompass corrosion inhibition, shrinkage reduction, alkali-silica reactivity reduction, workability enhancement, bonding, damp proofing, and coloring.
- Air-entraining admixtures, which can be used to purposely location microscopic air bubbles into the concrete, are mentioned extra completely in Air-Entrained Concrete.
- Water-decreasing admixtures commonly lessen the desired water content material for a concrete aggregate with the aid of using approximately five to ten percentage .
- Consequently, concrete containing a water-decreasing admixture wishes much less water to attain a required stoop than untreated concrete.
- The dealt with concrete could have a decrease water-cement ratio. This commonly shows that a better energy concrete may be produced without growing the quantity of cement.
- Recent improvements in admixture generation have caused the improvement of mid-variety water reducers.
- These admixtures lessen water content material with the aid of using as a minimum eight percentage and have a tendency to be extra solid over a much broader variety of temperatures.
- Mid-variety water reducers offer extra regular placing instances than popular water reducers.
- Retarding admixtures, which gradual the placing charge of concrete, are used to counteract the accelerating impact of warm climate on concrete placing.
- High temperatures frequently reason an accelerated charge of hardening which makes setting and completing difficult.
- Retarders maintain concrete manageable for the duration of placement and put off the preliminary set of concrete.
- Most retarders additionally characteristic as water reducers and can entrain a few air in concrete.
- Accelerating admixtures growth the charge of early energy improvement, lessen the time required for correct curing and protection, and accelerate the begin of completing operations.
- Accelerating admixtures are specifically beneficial for enhancing the residences of concrete in bloodless climate.
- Super plasticizers, additionally called plasticizers or excessive-variety water reducers (HRWR), lessen water content material with the aid of using 12 to 30 percentage and may be introduced to concrete with a low-to-ordinary stoop and water-cement ratio to make excessive-stoop flowing concrete.
- Flowing concrete is a extraordinarily fluid however manageable concrete that may be located with very little vibration or compaction.
- The impact of super plasticizers lasts most effective 30 to 60 minutes, relying at the emblem and dosage charge, and is observed with the aid of using a speedy loss in workability.
- As a end result of the stoop loss, super plasticizers are commonly introduced to concrete on the jobsite.
- Corrosion-inhibiting admixtures fall into the strong point admixture class and are used to gradual corrosion of reinforcing metal in concrete.
- Corrosion inhibitors may be used as a shielding method for concrete structures, along with marine facilities, motorway bridges, and parking garages, in order to be uncovered to excessive concentrations of chloride.
- Other strong point admixtures encompass shrinkage-decreasing admixtures and alkali-silica reactivity inhibitors.
- The shrinkage reducers are used to govern drying shrinkage and reduce cracking, even as ASR inhibitors manipulate sturdiness troubles related to alkali-silica reactivity.
Mechanism of Chemical Admixture:
- Concrete admixtures are used to steer concrete hardening specially with inside the early Phase of hydration.
- By including very small quantities of admixtures, homes of sparkling concrete may be inspired in a huge range.
- The hydraulic response may be elevated or retarded the use of suitable dealers and workability may be advanced the use of super plasticizers.
- Many mechanisms had been cautioned to provide an explanation for these kinds of effects .
- There continues to be no complete know-how of hydration mechanisms together with these kinds of phenomena at once.
- In this contribution emphasis will be positioned at power differences occuring at some point of physico-chemical methods of cement hydration.
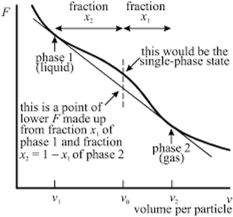
Fig no 37. Mechanisms of plasticiser
- Cement hydration evolves in a manner which in corporate segment transitions.
- In touch with water, Meta stable stable cement stages dissolve into an aqueous solution.
- This dissociation ends in an boom of Ca O attention as much as 20-forty m mol/I with inside the first hours of C3S hydration .
- Reaching a country of super saturation with inside the pore water solution, crystallization into strong and stable CSH-merchandise can follow.
- In each segment transitions a unexpected quantity extrade occurs, as a consequence of adjustments in sure forces.
- During the solvation procedure a stable-fluid section transition results in an boom in quantity (swelling).
- Crystallization entails a quantity contraction (shrinkage) that is better in absolute phrases than the preceding quantity swelling.
- A shrinkage quantity stays after fluid-stable transition and may be measured volumetrically or gravimetrically.
- Both tactics engage simultaneously, however with unique velocities.
- Hydration may be visible as a solvation-crystallization step and become first defined via way of means of Le Chatelier.
Key takeaways
- Super plasticizers, additionally called plasticizers or excessive-variety water reducers (HRWR), lessen water content material with the aid of using 12 to 30 percentage and may be introduced to concrete with a low-to-ordinary stoop and water-cement ratio to make excessive-stoop flowing concrete.
- During the solvation procedure a stable-fluid section transition results in an boom in quantity (swelling).
Deterioration - Durability
- Durability is the capacity to remaining a long term without massive deterioration.
- A long lasting cloth allows the surroundings with the aid of using keeping sources and lowering wastes and the environmental affect of restore and substitute.
- The manufacturing of substitute constructing substances depletes herbal sources and may produce air and water pollution.
- Concrete resists weathering action, chemical attack, and abrasion even as retaining its favored engineering houses.
- Different concretes require extraordinary levels of sturdiness relying at the publicity surroundings and the houses favored.
- Concrete ingredients, their proportioning, interactions among them, setting and curing practices, and the provider surroundings decide the remaining sturdiness and lifestyles of the concrete.
- The layout provider lifestyles of maximum homes regularly 30 years, despite the fact that homes regularly remaining 50 to one hundred years or longer.
- Because in their sturdiness, maximum concrete and masonry homes are demolished because of useful obsolescence in place of deterioration.
- However, a concrete shell or shape may be repurposed if a constructing use or characteristic adjustments or whilst a constructing indoors is renovated.
- Concrete, as a structural cloth and because the constructing outside skin, has the capacity to face up to nature’s ordinary deteriorating mechanisms in addition to herbal disasters.
- Durability of concrete can be described because the capacity of concrete to withstand weathering action, chemical attack, and abrasion even as retaining its favored engineering houses.
- Different concretes require extraordinary levels of sturdiness relying at the publicity surroundings and houses favored.
- For example, concrete uncovered to tidal seawater could have extraordinary necessities than an indoor concrete floor.
Key takeaways
- Durability is the capacity to remaining a long term without massive deterioration.
- A long lasting cloth allows the surroundings with the aid of using keeping sources and lowering wastes and the environmental affect of restore and substitute.
Factor affecting the durability of concrete
The following are the factors that affect the strength of concrete.
- Cement content
- Aggregate quality
- Water Quality
- Concrete compaction
- Curing period
- Permeability
- Moisture
- Temperature
- Abrasion
- Carbonation
01. Cement content
- The amount of cement used in concrete mixing is a major factor affecting the durability of concrete.
- If the cement content used is less than required, the cement water level
- Decreases and the performance of concrete also decreases.
- Adding too much water to this concrete mix causes the formation of capillary voids that will make the concrete a resilient one inviting decay.
- Adding excess cement can cause problems such as stopping the shrinkage. Alkali-silica reactions may also eventually affect the strength of the concrete.
02. Aggregate Quality
- Applying a good quality mix to the concrete mix will definitely increase the strength of the concrete.
- The shape of the composite particles should be small and circular. Flaky and compact assembly can affect the performance of the new concrete making it easier to enter where it can open and will work with less power.
- Bad angular compilation is recommended but requires a lot of cement content to get a good binding. Yes, structural composites should be used to achieve greater concrete mixing.
- Determination of the combined moisture content should be done beforehand, otherwise, it can create a more usable concrete mix and make it worse.
03. Water Quality
- The water used in the concrete mix also affects the strength of the concrete. Usually, drinking water is recommended to make concrete. The pH of the water used will be in grades 7 to 8 only.
- Water should be free and clean from fats, acids, alkalis, sugar, organic salts etc.
- Contamination in the water can lead to metal corrosion or corrosion due to different chemical attacks of concrete.
04. Concrete compaction
- Care should be taken during the installation of the concrete. It is important to glue the local concrete without splitting.
- Adequately compacted concrete contains a number of air gaps in it that reduce the strength of the concrete and its strength and will make it stronger.
05. Curing period
- Proper treatment should be done in the early stages of concrete reinforcement as it will lead to the reinforcement of the concrete.
- Adequate treatment can lead to the formation of cracks due to plastic shrinkage, dehydration, heat effects etc. due to reduced stiffness.
06. Permeability
- Due to the overcrowding of the concrete, it expands and leads to the formation of cracks and eventually, the deterioration of the concrete occurs.
- Concrete usually consists of small gel pores and capillary cavities. However, gel pores prevent water ingress because they are too small.
- Capillary holes in concrete are facing, which are formed due to the high water content of concrete
- To prevent intrusion, a very small amount of cement water should be used.
- Using a small amount of pozzolanic material also helps to reduce penetration
07. Moisture
- The moisture found in the atmosphere will also affect the strength of concrete structures.
- Concrete moisture is responsible for Efflorescence, which will convert salt into soluble solutions and when evaporated salt becomes brighter and appears on the concrete surface.
- This will definitely damage the concrete structure and the durability will decrease.
08. Temperature
- When new concrete is exposed to high temperatures, the hydration level is affected and strength and durability are reduced.
- Concrete materials have different temperature coefficients, so at higher temperatures, spelling and damage to concrete are possible.
09. Abrasion
- Concrete damage also occurs due to severe facial injuries.
- When concrete is exposed to fast-moving water, steel tires, floating ice that wears continuously on the surface occur and stiffness is affected.
- The higher the pressure of the concrete pressure the higher it will be to resist the abrasion
10. Carbonation
- When wet concrete is exposed to the atmosphere, carbon dioxide in the atmosphere reacts with concrete and reduces the pH of the concrete by reacting with CaO in concrete.
- When the pH value of concrete is reduced to 10 or 9 or more, it releases its alkali. Because it will not be able to protect the metal bars beneath it. Due to rust, rust will build up around the bar which has led to an increase in the volume of the bar. This will create cracks in the concrete. Cracking will continue to promote moisture and CO2 which will lead to the loss of alkali. So bad cycles occur, eventually causing the concrete to crack with delamination and spraying of the concrete if not done in time, the bars will start to lose their place and thus become stronger. Most of the building in modern times, suffers from this, and buildings that were supposed to be 100 years old have been extensively renovated at some point within ten years. The process of rust therefore places on the existing strength of the concrete. The rust of the reinforcement causes cracks in the solid concrete and deterioration occurs.
Key takeaways
The following are the factors that affect the strength of concrete.
- Cement content
- Aggregate quality
- Water Quality
- Concrete compaction
- Curing period
- Permeability
- Moisture
- Temperature
- Abrasion
- Carbonation
Permeability
- Definition: the capacity of a given concrete to allow drinks or gases to by skip through.- ACI Concrete Terminology
- Permeability is a degree of the quantity of water, air, and different materials which could input the concrete matrix.
- Concrete consists of pores which could permit those materials to go into or depart.
- Permeability of concrete may be a number one motive for concrete deterioration because of reinforcing metal corrosion and different deterioration mechanisms.
- On a macro scale, permeability additionally refers to “porous” slabs used to empty pavements, sidewalks, and parking regions of water, putting off the want for drainage slope, systems, and piping.
- This technology—every now and then called “no-fines concrete”—is gaining reputation once more with the preference to lessen floor run-off from pavements, sidewalks, and parking regions.
- Permeability of cement mortar or concrete is of unique importance in systems which might be meant to hold water or which come into touch with water.
- Besides useful considerations, permeability is likewise in detail associated with the sturdiness of concrete, mainly its resistance, towards revolutionary deterioration below publicity to extreme climate, and leaching because of extended seepage of water, specially whilst it consists of competitive gases or minerals in solution.
- The willpower of the permeability traits of mortar and concrete, therefore, assumes widespread importance.
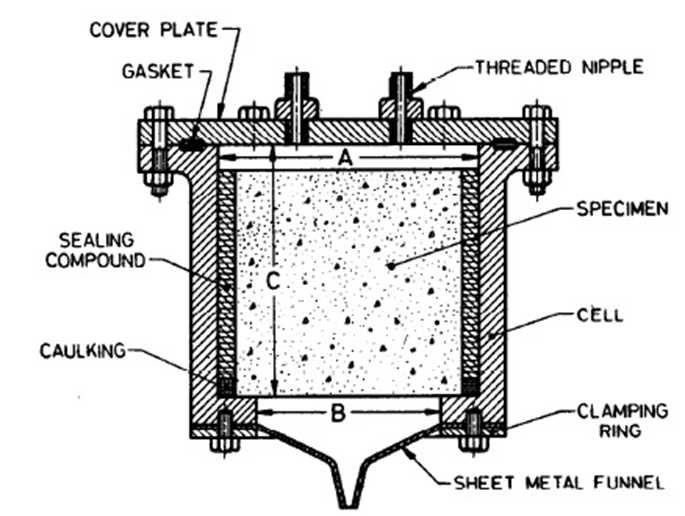
Fig no 38. Concrete permeability apparatus
- The permeability shall encompass a steel cylinder for containing the specimen.
- A rubber or neoprene O-ring or different appropriate gasket, seated in matching grooves will be used among the quilt plate to render the joint water-tight.
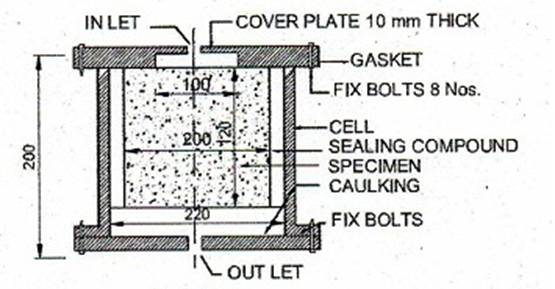
Fig no 39. Water Reservoir in Permeability Apparatus
- A appropriate reservoir may also encompass a duration of steel pipe, 50 to a hundred mm in diameter and approximately 500 mm long.
- The reservoir will be equipped with a graduated facet arm gauge-glass, and the vital fittings and valves for admitting water and compressed air and for draining, bleeding and connection to the permeability.
Procedure:
Preparation of Test Specimen
- Test specimen of 2 hundred mm diameter and a hundred and twenty mm thick will be used. After 24 hrs of casting of specimen, crucial round place of a hundred mm diameter will be roughened with a twine brush at the facet on which the water stress is to be carried out. The un roughened a part of the facet of the check specimen that's subjected to water stress is to be sealed with coats of cement water paste (W/C = 0.4).
Test Procedure
- After 28 days curing, check specimen is equipped right into a check equipment in which the water stress acts on the specified face and final faces may be observed.
- At first, a stress of one Bar is carried out for forty eight hours, then three bar for twenty-four hours and seven Bar for twenty-four hours.
- After the check, the specimen is break up with inside the center with the aid of using the compression carried out on spherical metal bars mendacity on contrary sides, above and below. The facet after the check specimen uncovered to the water stress ought to face downwards.
Observation:
- The finest water penetration depth, is taken because the common cost of the finest penetration depths on 3 check specimen.
Key takeaways
1. A rubber or neoprene O-ring or different appropriate gasket, seated in matching grooves will be used among the quilt plate to render the joint water-tight.
Chloride Attack
- Chloride Attack Chloride attack is one of the most important factors when working with concrete strength. It mainly causes corrosion. Statistics have shown that more than 40% of structural failures are due to metal corrosion.
- Concrete and the penetration layer with a strong alkaline Ca (OH) 2 (pH approximately 13) prevents metal corrosion by forming a thin film to protect the iron oxide on the surface of the metal.
- This protection is known as inaction. If concrete can penetrate in such a way that the dissolved chloride enters until it hardens and water and oxygen are also present, then corrosion of the metal will occur. This layer can also be lost due to carbonation.
- Chloride enters the concrete from cement, water, and is sometimes mixed from tips. This can come in increments from nature when the concrete is filled. The Bureau of Indian Standard specified the high chloride content in cement as 0.1%.
- The amount of chloride needed to start corrosion depends on the pH value of the pore water in the concrete. A pH value below11.5 corrosion is possible without the presence of chloride.
Key takeaways
- Chloride Attack Chloride attack is one of the most important factors when working with concrete strength. It mainly causes corrosion corrosion. Statistics have shown that more than 40% of structural failures are due to metal corrosion.
- Concrete and the penetration layer with a strong alkaline Ca (OH) 2 (pH approximately 13) prevents metal corrosion by forming a thin film to protect the iron oxide on the surface of the metal.
Corrosion of Reinforcement, Carbonation of Concrete
Corrosion of Reinforcement
- Concrete, in itself, has a low strength. To increase the strength of the concrete, the steel hardens. Steel bars are inserted inside the weight of the concrete. These steel bearings carry a high load-bearing capacity applied to concrete.
- Concrete makes metal bars obsolete due to the alkaline environment, thus preventing them from cracking. However, for a variety of reasons, metal bars can be pulled longer. And as a result of the rust of the steel bars, various weaknesses appear in the concrete structure, which could eventually collapse if not properly maintained.
- The rust of steel reinforcement bars is actually a way of responding to electricity. Small anodes and cathodes are formed and the flow of ions between these two electrodes leads to the breakdown of metal bars. There are two types of corrosion detected in steel reinforcement bars:
- Metal Rust - In small cracks in a concrete structure, solutions may remain. Anodes and cathodes can be formed within solutions due to the uneven reaction of solute ions over the volume of the solution. The flow of ions is caused by these electrodes, thus causing a gradual corrosion.
- Rust corrosion - Related to the removal of small areas in the steel bars of the reinforcement. This type of rust is extremely well-formed and small holes or holes are made in the metal.
Causes of Stainless-Steel Rust
- Corruption of steel reinforcement barriers may be due to the local failure of the metal film of chloride ions or the general failure of the concrete to malfunction due to the carbon dioxide reaction from the atmosphere. The main factors facing corrosion of reinforcement barriers are:
- Loss of alkalinity due to carbonation - When a metal surface is left unprotected in the atmosphere, corrosion begins to form on the surface of the metal and then slowly moves away.
- Loss of alkalinity due to chlorides - Chloride ions tend to remove metal energy by destroying concrete.
- Cracking of Concrete - Cracking can expose metal bars in the atmosphere and increase liquidity.
- Moisture Methods - Regular wetting of concrete can lead to water reaching the metal bars by dispersing through the pore structure of the concrete or existing cracks in the concrete. Rust of steel bars follows after that.
- Insufficient cover: Insufficient size of concrete cover.
- Metal Rust due to Improper Cover
- Damaged steel reinforcement may occur due to insufficient concrete cover
Effects of Stainless-Steel Rust
When steel bars begin to break, reinforced concrete joints begin to break down through the following stages:
- White spot formation - Atmospheric carbon dioxide reacts with calcium hydroxide present in the reduction of cement forming calcium carbonate. This calcium carbonate is treated with moisture and deposited on the surface of the white-formed concrete.
- Dirty stains by reinforcement - When the metal bars begin to deteriorate, a layer of iron oxide forms in it. This metal oxide is also transferred to the surface of the concrete with moisture.
- Formations of cracks - Rust products take on a larger volume than the original. So they put pressure on the concrete and it cracks. In the event of a lot of rust, many wide cracks are formed.
- Disintegration of concrete cover - Due to the loss of bond between concrete and steel, concrete begins to form many layers of scales and then peels off. Metal bars are also reduced in size.
- Cracking of bars - Due to the decrease in the size of the steel bars, they eventually break. Also, there is a significant reduction in the size of the main bars.
- Piercing of bars - The collapse of the concrete cover and the cracking of the bars resulted in the collapse of the main bars. This floods the concrete area and eventually the entire building collapses.
How to Avoid Rusting Metal Rust
- The rust of steel reinforcement bars can be prevented or at least delayed by good measures. Also, damaged steel bars can be repaired and the concrete structure can be properly restored. Some steps are given below:
- Providing Sufficient Concrete Cover: A good amount of concrete cover should be provided in addition to the reinforcing steel bars. This ensures proper care of the alkaline type inside the concrete and the passage of the steel bars. Metal bars should be placed precisely in place
- Use of Quality Concrete: High quality concrete should be used. It helps to maintain an alkaline environment. In concrete, a water level of 0.4 or less should be maintained. Too much water can damage metal bars
- Compact Compaction fo Concrete: Concrete must be thoroughly mixed so that no air gaps or pockets are present.
- Use of FBE Bonds: Fusion Bonded Epoxy Coating (FBEC) can be used on metal bales to prevent corrosion. Epoxy powder is still electrically distributed in metal barns. The powder melts and flows over the bars as it heats up, forming a protective coating. It is a thermoset polymer coating because the use of heat will not melt the wear. Apart from the rebar it also has extensive function in pipeline construction
- Use of Cement-Based Polymers: Cement-based polymers can be used in concrete to increase their protection against corrosion. Cement-based polymers act as a bond in concrete. They also increase the strength, durability and melting of concrete
Carbonation of Concrete
- Carbonation of concrete is associated with corrosion of steel reinforcement and shrinkage. However, it also increases both the compression strength and the strength of the concrete, so not all of its effects on concrete are bad.
- Carbonation is the result of the decomposition of CO2 in pore fluid in concrete and this reacts with calcium from calcium hydroxide and calcium silicate hydrate to form calcite (CaCO3). Aragonite can form in hot climates.
- Within a few hours, or a day or two in total, the new concrete will be processed by CO2 in the air. Gradually, the process penetrates deeper into the concrete at a rate equal to the square root of time. After a year or more it is likely to reach a depth of about 1 mm with dense low-penetration concrete made of low water / cement, or up to 5 mm or more of high-density and permitted concrete using high water / cement scale.
Carbonation determination
- The affected depth from the concrete surface can be easily indicated by the use of a phenolphthalein indicator solution. This is available from chemical suppliers. Phenolphthalein is a white or pale yellow with a crystal. Use as a solvent dissolve in a suitable solution such as isopropyl alcohol (isopropanol) by 1%.
- The indicator has not changed color near the upper and lower extremities, suggesting that these regions near the surface be carbonated at a depth of at least 4 mm from the top to the top and 6 mm from the bottom.
- When the index turns purple - in the middle of the slide - the pH of the pore fluid anchor remains high (above 8.6, about 10). Whether you are pasting the cement here is not completely illuminated, despite the strong purple color; a complete test will require very little testing.
- The index was not applied to the concrete to the right of this image so the concrete here retains its original color.
- The depth of carbonation is about the same as the square root of time. For example, if the depth of carbon is 1mm in one-year-old concrete, it will be about 3mm after 9, 5mm after 25 years and 10mm after 100 years.
Key takeaways
- Carbonation of concrete is associated with corrosion of steel reinforcement and shrinkage. However, it also increases both the compression strength and the strength of the concrete, so not all of its effects on concrete are bad.
- Concrete, in itself, has a low strength. To increase the strength of the concrete, the steel hardens. Steel bars are inserted inside the weight of the concrete. These steel bearings carry a high load-bearing capacity applied to concrete.
- Concrete makes metal bars obsolete due to the alkaline environment, thus preventing them from cracking. However, for a variety of reasons, metal bars can be pulled longer. And as a result of the rust of the steel bars, various weaknesses appear in the concrete structure, which could eventually collapse if not properly maintained.
Repair - Symptoms and Diagnosis of Distress
- The rapid industrialization of India after independence required the transportation of goods and services and led to the construction of a network of wide roads with built-in bridges and flyovers.
- Many of the existing bridges show signs of stress within their work life built in many cases in the 10-20 years of construction in India and many other countries.
- The collapse of the I-35W bridge over the Mississippi River in the United States of America in August 2007 has attracted the attention of international media. In India, the collapse of the Mandovi Bridge in Goa in 1986 (after 16 years of service) and the great tribulation at the Zuari bridge (rebuilt in 2000 by an international consultant) in Goa and many other bridges such as Khalghat and Borad Bridge on NH3 (Route) Agra to Mumbai) due to environmental constraints is attracting the attention of transport authorities and the scientific community to transform the operational bridge management system.
- The cause of the distress, the level of grief and the reduction in the capacity of the bridge can be ensured in order to further the necessary adjustments to ensure the safety of the bridge during their operation.
- An assessment of the pressure and load capacity of existing bridges and to improve the load capacity is required while upgrading highways. India has already implemented the consolidation and use of four 7000 Km of highways under the Golden Quadrilateral program where the strengthening / replacement of many existing bridges was required.
- Various causes of damage to reinforced concrete bridges are low construction standards, rust of steel on reinforced concrete bridges and pre-reinforced concrete bridges, improper shape and details of normal loads and seismic forces, improper operation of bearings etc. a number of case studies have been reported in the literature on reinforced concrete damage and compacted concrete bridges during earthquakes and the reinforcement of reinforced and compressed concrete bridges due to nature and other loads.
- A concerted effort has been made to review critical documentation of reinforced concrete damage and pre-pressure concrete bridges and repair / rehabilitation strategies based on information from bridge reconstruction projects in which the authors were involved.
Causes of distress
- Relationship problems such as conflicts, illness / death of a loved one, divorce, abuse, partner, etc.
- Financial difficulties
- Environmental remediation
- Educational difficulties
- Time management and organizational complexity
- Anxiety
- Depression
- An abusive event
- Drug abuse
Diagnosis of distress
Sometimes the cause of grief is known e.g. Suffering during an earthquake, impact and explosion is known perhaps the active load exceeds the intended load but it is often difficult to find the real cause of grief where many variables are affected e.g. Poor construction quality (faulty details, faults and performance), shrinkage, penetration, rust consolidation etc. Following a test may be necessary to determine the cause and degree of grief.
- Determination of compression strength from NDT and cores of concrete
- Strategies for detecting explosions
- Signature / Vibration Analysis
- Download tests to find deviations / issues and distribute the load
- Rust studies (pH, depth of carbon, chloride)
- Deviation / disposal slopes from Instrumented Bridge
Key takeaways
- The rapid industrialization of India after independence required the transportation of goods and services and led to the construction of a network of wide roads with built-in bridges and flyovers.
- Many of the existing bridges show signs of stress within their work life built in many cases in the 10-20 years of construction in India and many other countries.
Selection Of Repair Procedure
Structure
- Structural repairs include using epoxy frames to bind or bond concrete together. Epoxy repair not only repairs the sealing cracks but also restores the strength and durability of the concrete. Use epoxy to repair dormant cracks only. Fixing functional cracks with epoxy often leads to a new formation near the original, epoxied fragment.
- Epoxy injection is a common way to inject epoxy into cracks, especially in direct and indirect areas. But gravity filling works well and is a common way to apply epoxy to flatwork cracks or to direct surfaces.
- The filling of gravity consists of pouring low-viscosity epoxy into the cracks that have been signed or distributed and allowed the gravitational force to pull the epoxy down the cracks. Viscosity resistance to fluid flow is measured in centipoises (cps). Decreased viscosity value, less (runnier) significant. Grade I and II epoxies have viscosities of less than 20 cps and between 20 and 100 cps, respectively.
- For comparison, the viscosities of other common beverages are: water - 1 cps, milk - 3 cps, anti-freeze - 15 cps, maple syrup - 150 to 200 cps, and honey -3000 cps. Low viscosities are required for solid cracks. Otherwise, the repair material will be too large to penetrate and flow into the crack.
- Epoxies were cured or hardened due to the chemical reaction between the frame and the hardener. Chemical reactions are rapid at high temperatures. Epoxies are obtained by different injections or by temperature treatments so chemical reactions are less rapid or slow (Type A, less than 40º F; Type B, 40º F to 60º F; and type C, more than 60º F).
- With the adjustment of gravity filling culture, consider the depth and depth, epoxy viscosity, and temperature input when choosing the distance and type of epoxy. Otherwise, the epoxy can be very strong or very hard to penetrate or it can just run between the river and the pool under the slide.
Sealing and filling
- Sealing and filling of non-construction repairs. However, some repair materials include cracked surfaces and can have a strong impact that can cause cracking of the material and concrete in the event of a major crack movement.
- Typical sealants and internal fixing fillers include semi-rigid epoxies, hybrid polyurethanes and polyureas, and polymer mortar. Polyurethanes and silicones are common labels used for exterior repairs.
- Usually, sealants are flexible or elastomeric materials; and the fillers are very hard so the fixing materials support the edges of the cracks to avoid collapse or damage under load. When heavy traffic is exposed to heavy wheels, composite fillers or special cracks with about 80 Shore A Hardness should be used.
- Unfortunately, there is a trade-off to increase the complexity of explosive repair materials. As the repair material gets harder, it becomes much thinner and does not tolerate cracked movement. For example, semi-rigid epoxies usually have a hardness of about 90 and an extension value of 50%; whereas, silicone sealants have a hardness of about 5 and an extension value of 1400%. Therefore, when choosing a fix, consider the expected movement of the comparison and the need to support the edges of the cracks.
- For effective cracking with the expected cracking motion, use elastomeric sealants or sealants with sufficient elastic properties, to see that the trade-off will be a little support for the fracture edges. For cracks exposed to heavy-duty traffic, use hard materials that support the edges of the cracks. But understand that these things do not tolerate the movement of cracks.
- If you are using elastomeric sealants in active cracks, always seal the sealant with a saw or by moving the track as recommended by the repairman. Without a dam, there would not be enough to tolerate future fracture movements. Expansion structures reported by manufacturers are based on the size of the recommended lakes or, in particular, the width and depth of the dam.
- Of course, cutting or scraping increases the width of the crack and makes crack repairs more noticeable. For cosmetic repairs in colored or decorative flats where cracks lie or are well established, do not see or move the sealant or filler dam. Instead, choose a low viscosity cracker (less than 100 cps) and small injection tips for cracks to fill gravity.
- Dams are not required. But in the event of a fracture movement, the cracking of the repair material or concrete may occur due to the small diameter of the depth of the material. Also, manufacturers now offer many of these low viscosity fixes in a variety of colors or offer color production recommendations and textures similar to concrete concrete surfaces.
- Before fixing your next explosion, do a crack test and establish repair targets. Decide what kind of adjustment is needed. Options include structural repairs using epoxy, route fixes and seal applications using flexible sealant to hold future cracks, and solid or durable repairs that fill the edges of cracks, with or without. Also, set cosmetic requirements. After selecting the fix and procedure, follow the manufacturer's recommendations.
Key takeaways
- Structure
Structural repairs include using epoxy frames to bind or bond concrete together. Epoxy repair not only repairs the sealing cracks but also restores the strength and durability of the concrete. Use epoxy to repair dormant cracks only. Fixing functional cracks with epoxy often leads to a new formation near the original, epoxied fragment.
2. Sealing and filling
Sealing and filling of non-construction repairs. However, some repair materials include cracked surfaces and can have a strong impact that can cause cracking of the material and concrete in the event of a major crack movement.
Repair of defects using various type and techniques - shortcrete and grouting
Shortcrete
- Shotcrete or sprayed concrete is concrete or mortar conveyed thru a hose and pneumatically projected at excessive pace onto a floor, as a production method, first utilized in 1914.
- It is usually strengthened with the aid of using traditional metallic rods, metallic mesh, or fibers.
- Properly carried out shotcrete is a structurally sound and sturdy production cloth which well-known shows terrific bonding traits to present concrete, rock, metallic, and plenty of different materials.
- It may have excessive strength, low absorption, correct resistance to weathering, and resistance to a few varieties of chemical attack.
- Many of the bodily residences of sound shotcrete are similar or advanced to the ones of traditional concrete or mortar having the equal composition.
- Improperly carried out shotcrete can also additionally create situations a lot worse than the untreated condition.
Advantages of shotcrete:
- Shotcrete is utilized in lieu of traditional concrete, in maximum instances, for motives of fee or convenience.
- Shotcrete is fine in conditions whilst formwork is fee prohibitive or impractical and wherein paperwork may be decreased or eliminated, get entry to to the paintings place is difficult, skinny layers or variable thicknesses are required, or ordinary casting strategies cannot be employed.
- Additional financial savings are feasible due to the fact shotcrete calls for handiest a small, transportable plant for manufacture and placement.
- Shotcreting operations can regularly be executed in regions of restrained get entry to to make upkeep to structures.
Grouting
- Grout is usually a mixture of cement, sand, and water or chemicals used to fill gaps.
- They are used to repair concrete cracks, to fill gaps and gaps in tiles, to fill gaps and waterproofing, and to strengthen the soil.
- It is also used to provide additional power to load-bearing structures. It basically involves the process of injecting something that can be pumped into a building to change its body structures.
- There are different types of grinding, cement grinding, chemical grinding, and bituminous grating, depending on the material used.
- Frames are also sometimes used as grout materials. A mortar is often used to fill cracks and gaps in soil or rock.
What is Grouting
- Also, it is used to stabilize the soil and keep it out.
- Cracking is used for a variety of purposes such as water repair, standing on immersed structures such as ditches, tunnels, etc., filling in the gaps between tiles and stabilizing the soil.
- Here we have provided details on the type of grouts used to repair cracks.
Advantage of Grouting Includes:
- This can be done in almost any soil condition
- It does not vibrate and can be controlled to avoid structural damage
- Development of underground structures can be measured
- It is very useful for limited space and low head items
- It is used to install slab jacking that lifts or measures the crippled foundation
- It can be installed near existing walls
- It can be used to control the flow of water, groundwater flow, and hazardous waste materials.
Many Different Types of Grouting Materials:
- Stopping cement
- Chemical Grouting
- Bentonite grouting
- The amber is growing
- Bituminous Grouting
Key takeaways
- SHORTCRETE
Shotcrete or sprayed concrete is concrete or mortar conveyed thru a hose and pneumatically projected at excessive pace onto a floor, as a production method, first utilized in 1914. It is usually strengthened with the aid of using traditional metallic rods, metallic mesh, or fibers.
2. GROUTING
Grout is usually a mixture of cement, sand, and water or chemicals used to fill gaps. They are used to repair concrete cracks, to fill gaps and gaps in tiles, to fill gaps and waterproofing, and to strengthen the soil.
Introduction of retrofitting of Concrete Structure by Fiber Reinforced Polymer (FPP), Polymer Impregnated Concrete
Fiber Reinforced Polymer
- Fiber-reinforced polymer (FRP), also fiber-reinforced plastic, is a composite made of polymer matrix reinforced with fibers. Threads are usually glass, carbon, or aramid, although other fibers such as paper or wood or asbestos have sometimes been used. The polymer is usually epoxy, vinylester or polyester thermosetting plastic, and phenol formaldehyde frames are still active. FRPs are widely used in the aerospace, automotive, marine and construction industries.
- Composite materials are made of building materials or naturally made from two or more materials that have a structure with very different physical or chemical properties that are always different and distinct from the finished structure. Most compounds have strong, strong fibers in a weak and strong matrix. The goal is usually to make the part stronger and stronger, usually with a lower volume.
- Commercial materials usually contain glass or carbon fibers in a matrix based on thermosetting polymers, such as epoxy or polyester resins. In some cases, thermoplastic polymers may be preferred, as they form after the first production. There are additional stages of integration where the matrix is metal or ceramic. For the most part, these are still in the development phase, and the problems of high production costs have yet to be overcome [1]. Moreover, in these compounds the reasons for adding fibers (or, in some cases, particles) are often complex; for example, improvements may be required in penetration, wear, cracking, heat stabilization, etc.
- Fiber-reinforced polymer (FRP) is a compound used in almost every type of high-tech engineering facility, with its use from aircraft, helicopters and spacecraft to boats, ships and marine systems as well as automobiles, sports equipment, repair equipment chemicals and public infrastructure such as bridges and buildings.
- The use of FRP compounds continues to grow at an impressive rate as these materials are widely used in their existing markets and are being developed in brand new markets such as biomedical devices and social structures. An important factor contributing to the increased use of compounds over the years has been the development of new types of FRP materials.
- This includes the development of high-resin applications and new reinforcement styles, such as carbon nanotubes and nanoparticles. The book provides a timely account of fiction, mechanical properties, delamination resistance, impact tolerance and the use of 3D FRP compounds.
- Polymers reinforced polymer composites (FRPs) are increasingly being considered for the development and / or replacement of structural components or systems consisting of traditional engineering materials, namely concrete and steel. FRP compounds are simple, non-destructive, show a certain high strength and direct durability, are easily constructed, and can be customized to meet operational requirements.
- Because of these beneficial features, FRP compounds have been incorporated into the construction and renovation of buildings using their reinforcement in concrete, blocks, modular structures, formwork, and external reinforcement for seismic reinforcement and development.
- The effectiveness of Fiber Reinforced Polymer (FRP) reinforcement in concrete structures such as replacement of steel bars or pre-pressurized muscles has been extensively studied in many research laboratories and professional organizations around the world. FRP reinforcement offers many benefits such as corrosion resistance, non-magnetic properties, very strong, lightweight and easy to handle.
- However, they usually have a direct response to stiffness to the point of failure (defined as damaging failure) and poor resistance to friction or shear. They are also less resistant to fire and when exposed to high temperatures. They release vital energy as they bend, and they are sensitive to the effects of pressure fractures. In addition, their cost, whether considered for each weight or on the basis of strength-bearing capacity, is relatively high compared with conventional steel reinforcement bars or pressure straps.
- From a structural engineering perspective, the most serious problems with FRP reinforcement are the lack of plastic conduct and very low shear strength on the short side. Such features can lead to premature tender fragmentation, especially if mixed results are obtained, such as in shear-breaking planes on reinforced concrete pillars where there is a delow action. The downtime action reduces the remaining resistance to stiffness and shear tenderness.
- Solutions and limitations for use are provided and further improvements are expected in the future. The cost of FRP consolidation unit is expected to decrease significantly with increasing market share and demand. However, even today, there are applications where FRP consolidation is less expensive and justified. Such cases include the use of FRP sheets or bonded plates in repairing and strengthening concrete structures, as well as the use of FRP meshes or fabrics or fabrics in small cement products.
- The cost of renovating and renovating a building remains, in certain terms, much higher than the cost of the original building. Repairs usually require a small amount of repair materials but a high commitment from staff. In addition, labor costs in developed countries are so high that the cost of materials is secondary. So the performance and performance that lasts the longest, the repair is very expensive. This means that the cost of materials is not a problem to be rectified and the fact that FRP materials are expensive is not a particular problem [5].
- Given only the physical strength and resources, at the top, the controversy over FRP compounds in a sustainable built environment is questionable. However, such a conclusion needs to be evaluated in terms of the potential benefits of using FRP compounds related to assumptions such as:
- High power
- Light weight
- High performance
- It lasts a long time
- Renovating existing buildings and extending their life
- Seismic development
- Security systems
- Space programs
- Ocean areas
o. In the case of FRP compounds, environmental concerns appear to be a barrier to its functioning as a viable alternative especially in terms of fuel depletion, air pollution, fog, and acidification associated with its production. In addition, the ability to reuse FRP compounds is limited and, unlike steel and wood, structural components cannot be reused to perform the same function in another structure. However, examining the environmental impact of FRP compounds on infrastructure use, especially through life cycle analysis, may reveal more direct and indirect benefits that compete more than conventional ones.
p. The composite material has greatly improved since its inception. However, before composite materials can be used as an alternative to conventional materials as part of a sustainable environment a few needs remain.
q. Availability of durability data for FRP building materials.
r. Integration of robust data and service life prediction methods for building members using FRP combinations.
s. Development of selection methods according to the life cycle cycle of materials and systems.
t. Finally, in order for the mixtures to be considered a viable option, they must be structurally and economically viable. Many studies on the structure of the composite material are widely available in the literature.
u. However, limited studies are available on the economic and environmental availability of these items from the perspective of the life cycle, because short-term data are available or only economic costs are considered in comparison. In addition, the long-term impact of using composite materials needs to be determined.
v. The products produced, the sustainability of the materials, and the capacity to recycle the materials need to be tested to determine if the composite materials can be part of a sustainable environment. So in this chapter describe the physicochemical properties of polymers and compounds most commonly used in Civil Engineering. The theme will be presented in a simple and basic way for better understanding.
Polymer Impregnated Concrete
- In the case of pregnant polymer concrete, prepolymers or lower liquid monomers are partially or partially impregnated with a pore system of a composite cement framework. After this process, the entire treated structure is allowed to polish.
- The general process of treatment of reinforced concrete leads to the acquisition of a large amount of free water in its spaces. These water-filled voids form a significant amount of total volume. From 5% in the case of dense concrete and 15% in the case of gaped concrete.
- In the case of pregnant polymer concrete, it is these voids (holes filled with water) that should be filled with the selected polymer. So the main thing that affects the loading of the monomer is this: the moisture content in the solid concrete and the air loses energy in the concrete.
Procedure for polymer impregnated concrete manufacturing
The activities involved in the pregnancy process to improve pregnant polymer concrete are:
1. Well-constructed concrete is available. They need to get better and get stronger.
2. Moisture is removed by drying the concrete. Drying is done by heating the structure element at temperatures above the order of 120 to 150 degrees Celsius. An air oven can be used to dry small specimens.
If the element has a large surface, a thick cloth, say, 10mm thick, can be used to protect it from any hot gradient. Another complex application is the use of infrared heaters.
Complete removal of moisture from concrete, requires 6 to 8 hours of heat.
3. After complete removal, the concrete area has cooled to a safer level. This can go up to a temperature of 35 degrees Celsius. This heat will avoid overheating.
4. The concrete is now transferred to a vacuum cleaner, where all the air inside the concrete structure is removed. The amount of monomer installed will determine the time and level of use of the machine.
5. Concrete after sufficient ventilation is placed in a monomer solution. Wet for a long time until the desired depth of monomer penetration is obtained.
Filling time depends on the viscosity of the monomer, the adjustment of the template and the advanced characteristics of the concrete.
To reduce the time taken to get the desired input, it is preferable to use external pressure such as air or nitrogen gas. This helps to get in faster.
6. After the above procedure, the surface is covered with plastic paper. This helps prevent the evaporation of the monomer.
7. A high-temperature polymerization method is performed. This method involves polymerization by heating the deformed monomer to the required temperature. This will start from 60 degrees to 150 degrees Celsius. The selected temperature range depends on the type of monomer.
Heating can be done under water or with a low pressure steam injection, or with infrared heaters or an air oven. The heat decomposes the catalyst and thus initiates the polymerization reaction.
Once the monomer has penetrated the concrete, polymerization can also be initiated using ionization radiation similar to gamma rays. Polymers when they are completely polymer or when connected on the other side, act as solids that reside in the voids they are embedded in.
8. The concrete structure is then allowed to cool.
Every process from 1 to 8 can only be done in a precast factory. Monomers such as acrylate, styrene and vinyl chloride etc. are widely used for concrete installations. Another widely used material is Methyl Methacrylate (MMA).
Properties of polymer impregnated concrete
1. The polymer concrete gains the strength of the cube to strengthen more than 100N / mm2. This strength does not depend on the strength of the standard concrete.
2. The flexibility of a pregnant polymer concrete is approximately 15N / mm2. This is slightly higher than high-grade clear concrete made from common ingredients.
3. The elastic modulus lies in the range from 30 to 60N / mm2. This value is the same as the value obtained from high-strength concrete (e.g. Approximately 45N / mm2)
4. Pregnant polymer concrete has less movement problems and shrinkage due to the small number of pores.
5. Pregnant polymer concrete is more resistant to acid attacks, sulfate attacks and chloride attacks compared to PCC.
Application of polymer impregnated concrete
The use of pregnant polymer concrete in various construction sites is described below:
1. Surface Impregnation of Bridge Decks: Bridge decks are allowed to be installed to avoid the ingress of moisture, chemicals and chloride ions.
Bridge floors built in areas with high salt water and moisture exposure can be protected in this way.
2. Structural repairs: Damaged structures can be developed in the form of a polymer abstract. The life span of undeveloped buildings can be extended in this way.
This method is why it helps in the restoration and preservation of stone monuments.
3. Underwater and Marine Applications: Polymer impregnation capabilities help to improve structures, water absorption, and non-concrete structures. This makes them widely used in water and sea construction.
Buildings built on desalination plants and underwater structures use this method of building concrete. It has been shown that the small absorption of concrete masses from seawater reduces the corrosion of the steel by 24 times.
4. Use in Irrigation Systems: The use of standard methods for the repair and rehabilitation of dams and other important water structures appears to be inefficient and incomplete.
This is later found to cause significant losses in profits from irrigation, energy production, flood control etc. But the method of pregnancy works very well.
Concrete from the damaged area is removed, glued and dried. This area is later treated using polymer emissions.
5. Composite Joints: Pregnant polymer concrete is as strong as building materials. PIC also shows the amazing development of standard concrete.
Internal and empty cracks are the basic foundation for all the issues in common concrete structures. Since the suspension of the polymer determines the cause, it is best used for construction members.
Key takeaways
- FIBER REINFORCED POLYMER
Fiber-reinforced polymer (FRP), also fiber-reinforced plastic, is a composite made of polymer matrix reinforced with fibers. Threads are usually glass, carbon, or aramid, although other fibers such as paper or wood or asbestos have sometimes been used. The polymer is usually epoxy, vinylester or polyester thermosetting plastic, and phenol formaldehyde frames are still active. FRPs are widely used in the aerospace, automotive, marine and construction industries.
2. POLYMER IMPREGNATED CONCRETE
In the case of pregnant polymer concrete, prepolymers or lower liquid monomers are partially or partially impregnated with a pore system of a composite cement framework. After this process, the entire treated structure is allowed to polish.
Corrosion monitoring and preventive measures
- The rust measuring, control, and prevention field covers a wide range of technical tasks. Within the field of corrosion control and prevention, there are technical options such as cathodic and anodic protection, material selection, chemical insertion and use of indoor and outdoor clothing. The rust scale uses a variety of techniques to determine how much damage the environment consumes and how much iron loss is experienced. Rust rating is a measure of how rust management performance and prevention strategies can be implemented and provides feedback to enable rust control and preventative measures to be improved.
- Some rust measurement techniques can be used online, regularly displayed in process broadcasts, while others provide external measurement, such as those determined in laboratory analysis. Some techniques provide a precise measure of metal loss or rust ratio, while others are used to indicate the possibility of corrosion.
- Rust monitoring is the practice of measuring the deterioration of process dissemination conditions by using probes that are incorporated into process dissemination and that are continuously expressed in the process dissemination process.
- Rust monitoring probes can be mechanical, electrical or electrical devices.
- Rust monitoring alone provides accurate and online measurement of metal loss / corrosion rate in industrial process systems.
- Typically, the rust measuring system, testing and adjustment used in any industrial area will include measuring instruments provided by four combinations of on-line / offline, direct / indirect measurements.
- Corrosion Monitoring Direct, On-line
- Direct, Offline Non-Destructive Testing
- Indirect Analytical Chemistry, Off-line
- Indirect, online Operational Data
- In a well-managed and integrated system, data from each source will be used to draw reasonable conclusions about the levels of active corrosion by the process process and how they are effectively reduced.
The Need of corrosion monitoring
The level of rust determines which process plant can be used efficiently and safely for how long. The rust scale and the action of adjusting the high levels of rust allow for the efficient operation of plants that must be achieved while minimizing the life cycle costs associated with the work.
Rust monitoring techniques can help in a number of ways:
- By giving an early warning that harmful procedural conditions exist that could lead to failures caused by rust.
- By studying the integration of changes in process parameters and their effect on system corrosivity.
- By identifying a specific rust problem, identifying its cause and the parameters that control the level, such as pressure, temperature, pH, flow rate, etc.
- By evaluating the effectiveness of the corrosion / prevention control method such as chemical prevention and good use.
- By providing management information relating to conservation needs and the ongoing condition of the plant.
Corrosion monitoring techniques
A large number of rust monitoring strategies are available. The following list describes the most common strategies used in industrial applications:
- Rust Coupons (Weight Loss Rate)
- Electrical Resistance (ER)
- Linear Separation Resistance (LPR)
- Galvanic (ZRA) / Possible
- Hydrogen Ingestion
- Bacteria
- Sand / Soil erosion
Other strategies are available, but almost all require professional work, otherwise they are not enough or flexible to apply.
In the above-mentioned strategies, corrosion coupons, ER, and LPR form the core of industrial corrosion monitoring systems. The other four strategies are usually found in special programs that are discussed over time.
These rust monitoring methods have been used successfully and are being used by a growing number of applications because:
- The techniques are easy to understand and apply.
- The reliability of the equipment has been demonstrated in the field field for many years of application operation.
- The results are easy to explain.
- Measurement equipment can be made internally safe from hazardous environmental performance.
- Consumers have gained significant economic benefits by reducing planting time and extending plant life.
Preventive Measures
- Metal corrosion is a natural process that requires three conditions: moisture, metal surface, and an oxidizing agent called an electron acceptor. Rust converts the active metal into a separate form of oxide, hydroxide, or sulphide. The most common type of rust is rust.
- Metallic metal not only affects the structure of the metal, but it can also affect the people who use the material or objects close to the metal. In extreme cases, rotten metal can lead to the construction of buildings and bridges, leaking pipes, and medical implants that infect human blood.
- While all metals are in danger of corrosion, some metals, such as pure metal, deteriorate much faster than others. However, iron can be combined with other alloys to form a stainless steel that is more resistant to corrosion.
- It is estimated that approximately 25-30% of rust can be prevented using appropriate protective measures.
- In general, you can prevent rust by choosing the right type of metal, Protective Fabrics, Environmental Measures, Self-Sacrifice Items, Rust Stumbling Stuff, Metal Installation and Repairs for Your Project.
Choose the right metal type
- One of the easiest ways to prevent rust is to use rust-resistant metal such as stainless steel, duplex, super duplex, nickel alloy or 6% Moly.
- These devices are so well made that they have a high resistance to corrosion and use them to reduce the need for alternative corrosion protection.
- For Special Drawing Materials, we offer products made of the highest quality synthetic materials available - stainless steel, duplex, super duplex, 6% Moly and Nickel Alloy. A variety of materials are selected by our clients in a variety of areas, with one of the factors considered for possible corrosion.
Protective coating
- Another way to prevent rust is to cover it with a special protective paint. Paint coating can act as a barrier that works by preventing electrochemical charging that transmits to the destructive and metal solution below.
- One way to do this is to put a powder coating in a clean metal place. The metal is heated to turn the flour into a smooth, non-abrasive film that acts as a barrier to rust. Many different powder compositions can be used, such as acrylic, polyester, epoxy, nylon, and urethane.
Environmental Measures
- Rust is certainly due to the nature of the metal in it as the chemical reactions that occur are due to metal reacting with liquids and gases in the surrounding environment.
- Controlling the environment can therefore help reduce this response. This could be as simple as reducing exposure to rain or seawater or it could be steps taken to reduce the amount of sulfur, chlorine, or oxygen in the area. For example, carrying water in water boilers to adjust hardness, alkalinity, or oxygen content, before placing the metal in that water can be very helpful in preventing corrosion.
Sacrificial coating
Sacrifice cover to prevent corrosion means covering the metal with a type of metal that may have oxidise - you sacrifice this top layer to protect the lower metal.
There are two main ways to accomplish the sacrificial attire:
- Cathodic Protection: Cathodic protection works by making the metal cathode of an electrochemical cell. The most common example of cathodic protection is the coating of iron ore and zinc - this process is known as galvanizing. Zinc is more than an active metal so rust prevents metal rot. Cathodic protection is frequently used for steel or petrol pipelines, heat tanks, ports, and overseas oil platforms.
- Anodic Protection: Anodic protection is opposed to cathodic protection and works by making the metal anode of an electrochemical cell. A common way to do this is to cover a thin layer of stainless steel, such as tin. The tin will not corrode, so the metal will be protected as long as the tin coating is in place. Anodic protection is often used for carbon storage tanks used to store sulfuric acid and 50% caustic soda.
Corrosion Inhibitors
- Chemical corrosion inhibitors are selected to react to metal surfaces or surrounding gases and therefore suppress electrochemical reactions that can lead to decay. When applied to a metal surface, they form a protective film. Inhibitors can be used as a solution or as a protective cover using distribution methods.
- Corrosion inhibitors are often used in a process known as passivation. An example of passivation is the Statement of Freedom where a blue and green metal signature is actually present to protect the copper underneath.
Metal Plating
- The installation is very similar to the cover as a thin layer of metal is inserted into the metal you want to protect. As well as preventing corrosion, the metal layer provides a good finish of beauty.
There are four types of metal wraps:
- Electroplating: The application of a thin layer of metal such as chromium or nickel to the underground metal by means of an electrolyte bath.
- Mechanical Plating: this involves cold welding powder metal metal substrate.
- Electro less: Coating such as nickel or cobalt is placed on a metal substrate using non-electrical chemical reactions.
- Hot dipping: A simple covering method that involves placing the substrate in a molten metal protective tub.
Design Modification
- Changing the structure of the project can have a significant impact on rust protection as it works by eliminating the causes of rust.
Key takeaways
- The rust measuring, control, and prevention field covers a wide range of technical tasks. Within the field of corrosion control and prevention, there are technical options such as cathodic and anodic protection, material selection, chemical insertion and use of indoor and outdoor clothing. The rust scale uses a variety of techniques to determine how much damage the environment consumes and how much iron loss is experienced. Rust rating is a measure of how rust management performance and prevention strategies can be implemented and provides feedback to enable rust control and preventative measures to be improved.
Rehabilitation methods for concrete elements grouped under confining techniques included concrete jacketing, steel jacketing, ferrocement laminated jacketing and FRP confinement. Some of the methods are for cosmetic repairs required to improve appearance, restore the non-structural properties and weather protection.
These techniques and materials for repair of concrete is described. Concrete is the most widely used and versatile construction material possessing several advantages over steel and other construction materials. However very often one come across with some defects in concrete. The defects may manifest themselves in the form of cracks, spalling of concrete, exposure of reinforcement, excessive deflections or other signs of distress. On many occasions, corrosion of reinforcement may trigger off cracking and spalling of concrete, coupled with deterioration in the strength of the structure. Such situations call for repairs of affected zones and sometimes for the replacement of the entire structure.
The need of structural repairs can arise from any of the following:
- Faulty design of the structure
- Improper execution and bad workmanship
- Extreme weathering and environmental conditions
- High degree of chemical attack
- Ageing of the structure
References:
1. A.M Neville J.J. Brooks Concrete technology
2. A.M Neville Concrete technology
3. R.S. Varshney Concrete technology
4. IS 10262 - 2009, Recommend guidelines for Concrete
Unit - 1
Concrete
Unit - 1
Concrete
- Concrete is a composite fabric composed of exceptional and coarse combination bonded collectively with a fluid cement (cement paste) that hardens (cures) over time.
- In the past, lime primarily based totally cement binders, consisting of lime putty, have been regularly used however now and again with different hydraulic cements, consisting of a calcium aluminate cement or with Portland cement to shape Portland cement concrete (named for its visible resemblance to Portland stone).
- Many different non-cementitious forms of concrete exist with different techniques of binding combination collectively, together with asphalt concrete with a bitumen binder that is often used for avenue surfaces, and polymer concretes that use polymers as a binder.
- When combination is blended with dry Portland cement and water, the combination bureaucracy a fluid slurry this is without difficulty poured and molded into shape.
- The cement reacts with the water and different elements to shape a difficult matrix that binds the substances collectively right into a long lasting stone-like fabric that has many uses.
- Often, additives (consisting of pozzolans or superplasticizers) are protected with inside the combination to enhance the bodily residences of the moist blend or the completed fabric.
- Most concrete is poured with reinforcing substances (consisting of rebar) embedded to offer tensile strength, yielding bolstered concrete.
- Because concrete cures (which isn't always similar to drying), how concrete is treated after it's miles poured is simply as essential as before.
- Concrete is one of the maximum often used constructing substances.
- Ts utilization worldwide, ton for ton, is two times that of steel, wood, plastics, and aluminum combined. Globally, the ready-blend concrete industry, the biggest section of the concrete market, is projected to exceed $six hundred billion in sales with the aid of using 2025.
- Concrete is wonderful from mortar. Whereas concrete is itself a constructing fabric, mortar is a bonding agent that generally holds bricks, tiles and different masonry devices collectively.
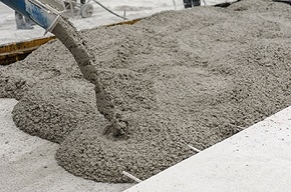
Fig 1: Concrete
Key Takeaways:
- Concrete is a composite fabric composed of exceptional and coarse combination bonded collectively with a fluid cement (cement paste) that hardens (cures) over time.
Plain concrete:
- Plain concrete, additionally referred to as undeniable cement concrete or PCC, is maximum typically used for paving and flooring.
- Made from a combination of cement, combination, and water the special varieties of combination and ratio of substances used will deliver special varieties of cement with barely special homes.
- This is one of the foremost promoting factors of geared up blend concrete as the precise values and varieties of combination may be measured and monitored exactly to offer the traits which are wished with none variance.
- The computerized production procedure limits the capacity of human blunders whilst saving time and resources.
- While there are variations with inside the composition of the concrete maximum undeniable concrete stocks the equal strengths and weaknesses.
- It is rather robust beneath Neath compression even as susceptible beneath Neath anxiety, because of this whilst on a solid, unmoving floor it's miles able to withstanding large quantities of weight.
- However, whilst located beneath Neath anxiety it's miles an awful lot weaker and might frequently crack and buckle.
- This makes it the correct cloth for floor ground layers and offering a strong or even base for strengthened concrete to be constructed onto whilst proscribing its use in large creation projects.
Key Takeaways:
- Made from a combination of cement, combination, and water the special varieties of combination and ratio of substances used will deliver special varieties of cement with barely special homes.
Reinforced concrete:
- Reinforced concrete, or strengthened cement concrete (RCC), is surely very just like PCC in phrases of substances used.
- The one massive distinction in its composition is the addition of metal rebar.
- By casting the moist cement round reinforcing metal bars the consequent composite cloth has an awful lot extra electricity beneath anxiety whilst nonetheless maintaining the homes that make PCC so effective.
- With the concrete retaining its electricity beneath compression and the metal resisting any bending or stretching way to its tensile electricity the RCC is a far extra flexible creation cloth.
- Able to rise up to weight pushing down onto it in addition to any wind stress or moving that outcomes in moderate twists and lines way to the expanded flexural capability of the concrete/metal blend, it's miles an appropriate cloth for taller and heavier homes and for roads and bridges.
- Steel is the maximum not unusual place cloth used for the introduction of rebar because it reacts to very comparable variances in temperature as concrete, that means it'll amplify and settlement with the concrete instead of cracking it from the inside.
Key Takeaways:
- By casting the moist cement round reinforcing metal bars the consequent composite cloth has an awful lot extra electricity beneath anxiety whilst nonetheless maintaining the homes that make PCC so effective.
Steel fiber/Glass fiber-strengthened concrete:
- Steel Fiber Reinforced Concrete (SFRC) is described because the concrete made with hydraulic cement containing high-quality and coarse combination and discontinuous discrete metal fiber.
- In SFRC, lots of small fibers are dispersed and disbursed randomly with inside the concrete for the duration of mixing, and hence enhance concrete homes.
- SFRC is getting used to enhance static and dynamic tensile electricity, strength soaking up capability and higher fatigue electricity.
- Steel fibers are the most powerful typically to be had fiber, and are available special lengths and shapes.
- Steel fires can simplest be used on surfaces which can tolerate or keep away from corrosion and rust stains.
- In a few cases, a metal-fiber floor is confronted with different substances.
- Glass fiber is a less expensive and corrosion-evidence fiber, however now no longer as robust as metal.
- The layout of glass fiber strengthened concrete proceeds from understanding of its fundamental homes beneath tensile, compressive, bending and shears forces, coupled with estimates of conduct beneath secondary loading results along with creep, thermal reaction and moisture movement.
Key Takeaways:
- SFRC is getting used to enhance static and dynamic tensile electricity, strength soaking up capability and higher fatigue electricity.
Light-weight concrete:
- Lightweight concrete is a combination made with light-weight coarse aggregates along with shale, clay, or slate, which provide it its feature low density.
- Structural light-weight concrete has an in-location density of ninety to a hundred and fifteen lb/ft³, while the density of everyday weight concrete stages from a hundred and forty to a hundred and fifty lb/ft³.
- This makes light-weight concrete best for constructing current systems that require minimum move sections with inside the foundation.
- It is being more and more used to construct smooth foundations, and has emerged as a possible opportunity to everyday concrete.
- Nevertheless, a better compressive electricity of 7000 to 10,000 psi may be attained with light-weight concrete.
- However, this can compromise the density of the combination because it calls for the addition of extra pozzolans and water-decreasing admixtures to the concrete.
Key Takeaways:
- Structural light-weight concrete has an in-location density of ninety to a hundred and fifteen lb/ft³, while the density of everyday weight concrete stages from a hundred and forty to a hundred and fifty lb/ft³.
High overall performance concrete:
- Concrete assembly unique combos of overall performance and uniformity necessities that cannot usually be accomplished mechanically the use of traditional parts and everyday mixing, placing, and curing practices.
- High-overall performance concrete (HPC) is concrete that has been designed to be extra-long lasting and, if necessary, more potent than traditional concrete.
- HPC combinations are composed of basically the equal substances as traditional concrete combinations, however the proportions are designed, or engineered, to offer the electricity and sturdiness wished for the structural and environmental necessities of the project.
- High-electricity concrete is described as having a targeted compressive electricity of 8000 psi (fifty-five MPa) or greater.
- The price of 8000 psi (fifty-five MPa) became decided on as it represented a electricity stage at which unique care is needed for manufacturing and checking out of the concrete and at which unique structural layout necessities can be wished.
Key Takeaways:
- HPC combinations are composed of basically the equal substances as traditional concrete combinations, however the proportions are designed, or engineered, to offer the electricity and sturdiness wished for the structural and environmental necessities of the project.
Polymer concrete:
- Polymer concrete is a combination that makes use of a few form of epoxy binder to remedy and harden into location.
- A polyester, vinyl ester, or everyday epoxy combination is frequently used, however polymer concrete may be made with many styles of polymer resins that permit the concrete to be poured or troweled after which hardened.
- It remedies via a chemical response with the polymer cloth.
- Like conventional concrete, it additionally has water, sand and gravel or overwhelmed stone as number one ingredients.
- Polymer concrete gives special blessings relying at the resin used to make it.
- Acrylic binders set right away and provide resistance to weathering, whilst epoxies create a completely robust cloth that shrinks little or no because it remedies.
- Furan resins can face up to excessive temperatures, and polyuria resins can update phenolic or formaldehydes in lots of creation projects.
- Polymer concrete is used for lots styles of specialized creation projects.
- Like different varieties of concrete, it is able to be used to sign up for special additives or to offer a shape or base.
- The cloth is utilized in electric or commercial creation in which the concrete desires to final a long term and be proof against many varieties of corrosion.
Key Takeaways:
- A polyester, vinyl ester, or everyday epoxy combination is frequently used; however, polymer concrete may be made with many styles of polymer resins that permit the concrete to be poured or troweled after which hardened.
Concrete is a commonly used construction material, which is the mixture of cement, sand, aggregate, and admixtures blended with water. Concrete gets hardened with time and gains the strength, and for the best results in a construction of your dream home, mixing of concrete is said to be the most important process. All the ingredients are to be mixed in proper proportion because the properties of concrete like workability, strength, surface finish, and durability of concrete etc. are ensured by the right and proportionate blending.
In the nominal mix concrete, all the ingredients and their proportions are prescribed in the standard specifications. These proportions are specified in the ratio of cement to aggregates for certain strength achievement.
The mix proportions like 1:1.5:3, 1:2:4, 1:3:6 etc. are adopted in nominal mix of concrete without any scientific base, only on the basis on past empirical studies. Thus, it is adopted for ordinary concrete or you can say, the nominal mix is preferred for simpler, relatively unimportant and small concrete works.
As per the ‘Indian Standard- IS 456:2000’, nominal mix concrete may be used for concrete of M20 grade or lower grade such as M5, M7.5, M10, M15.
M 20 is identified as the concrete grade in which, M denotes the Mix and 20 denotes the compressive strength of concrete cube after 28 days of curing in N/mm2. There are various grades of concrete that can be used like M10, M15, M20, M25, M30, etc.
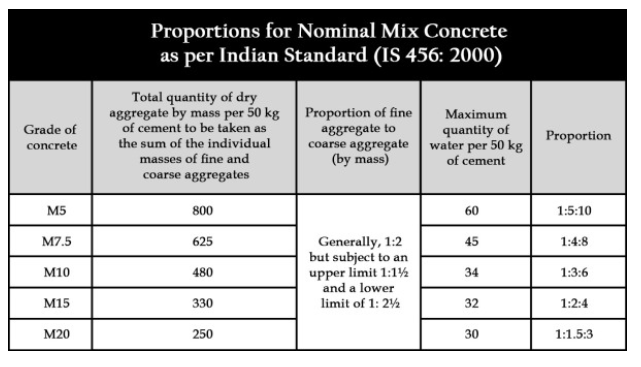
Tests on fresh concrete
Objective
- The word ―workable or concrete used has a broader and deeper meaning than the word alternative that is commonly used freely to make it work. Consistency is a general term that indicates the level of fluid or flow rate.
- Factors that help concrete to have the most effective effect of reducing internal friction that facilitates easy mixing are:
(a) Water content
(b) Mixing Dimensions
(c) Collection Size
(d) Structure Shapes
(e) Spatial Design Design
(f) Placement layout
(g) Use of Admixtures.
- Slump test is the most widely used method of measuring the consistency of concrete that can be used in a laboratory or in the workplace.
- It is not suitable for very wet or very dry concrete. It does not measure all factors that affect performance, nor does it always represent concrete placement.
- Indicates the concrete feature above the drop value. When the concrete slips evenly it is called a true slump. When one part of the lump slips, it is called a shear slump.
- In the event of a shear bend, the slump value is measured as the height difference between the height of the mold and the average amount of shrinkage.
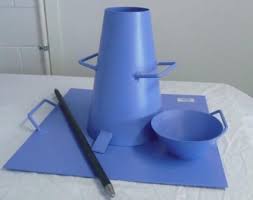
Fig no 2 Slum cone
Procedure
- If this test is performed in the field, a mixed concrete sample will be obtained. In the case of concrete containing a diameter of more than 38 mm, the concrete will be diluted with water by one and a half inches of screen to remove compacted particles larger than 38 mm.
- The inner surface of the mold will be thoroughly cleaned and freed from unwanted moisture and pre-set concrete before testing. The mold will be placed on a smooth, horizontal, strong, and non-abrasive surface, such as a carefully weighed metal table, the mold will be kept firmly in place while filling.
- The mold will be filled in four layers, each about a quarter of the height of the mold. Each layer will be smoothed with twenty-five lashes on the round edge of the lubricating rod. The lashes will be distributed evenly over the section at the cross section of the mold and the second and subsequent layers will fit into the lower layer.
- The bottom layer will be smoothed in the depth of it all. After the upper layer has been coated, the concrete will be flattened and trimmed with a trowel, so that the mold will fill directly.
- After the top layer has been glued, remove the concrete surface by moving and moving the lubricating rod.
- Any mud that may have leaked between the mold and the base plate should be cleaned. The mold will be removed from the concrete immediately by lifting it gently and carefully in a vertical direction. This allows the concrete to drop and the fall will be measured immediately by determining the difference between the height of the mold and that of the highest of the test template.
- The above operation will be performed in a non-vibrating or panic-free environment, and within two minutes after sampling.
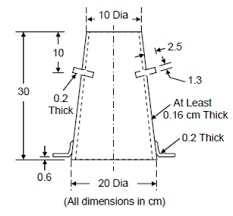
Fig no 3 Dimensions of slum cone
Key takeaways
- Slump test is the most widely used method of measuring the consistency of concrete that can be used in a laboratory or in the workplace.
- It is not suitable for very wet or very dry concrete. It does not measure all factors that affect performance, nor does it always represent concrete placement.
COMPACTION FACTOR
Objective
The compacting factor test is mainly designed for use in the laboratory but can also be used in the field. It is more accurate and sensitive than fall testing and is especially useful for very low-performance concrete mixes and is often used when the concrete will be squeezed by vibration. This method works on bare and ventilated concrete, made of lightweight, standard weight or heavy aggregates with a maximum weight of 38 mm or less but not on open concrete or non-reinforced concrete.
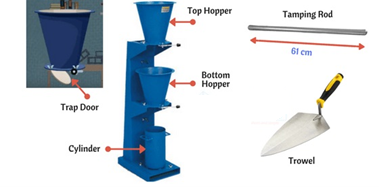
Fig no 4 Compaction factor apparatus
Procedure
- A sample of the test concrete will be gently placed on the upper hopper, using a hand scoop. The hopper will be evenly filled with its edge and the trap door will be opened so that the concrete falls to the ground.
- Some mixes tend to stick to one or both hoppers. When this happens, the concrete can be helped by pushing the rod gently into the concrete from the top. During this process, the cylinder will be covered with tiles.
- As soon as the concrete is out, the cylinder will be exposed, the door to the bottom trap will be opened, and the concrete will be allowed to fall into the cylinder. The remaining concrete over the top of the cylinder will be removed by holding a trowel in each hand, the plane of the belts horizontally, and then moving them simultaneously to each side above the cylinder, at the same time keeping them pressed against the upper edge of the cylinder.
- The outside of the cylinder when it is wiped will be clean. The above work will be done in a place that will not tremble or shake. The weight of the concrete in the container will be determined by the nearest 10 g.
- The remaining concrete over the top of the cylinder will be removed by holding a trowel in each hand, the plane of the belts horizontally, and then moving them simultaneously to each side above the cylinder, at the same time keeping them pressed against the upper edge of the cylinder. The outside of the cylinder when it is wiped will be clean. The whole process will be done in a place where there is no vibration or shock.
- This weight will be known as the weight of the partially bonded concrete. The cylinder will be filled with concrete from the same sample with layers about 5 cm deep, the layers folded tightly
- Or shaken to achieve complete integration.
- The surface of the fully covered concrete will be carefully beaten and weighed above the cylinder. The outside of the cylinder when it is wiped will be clean.
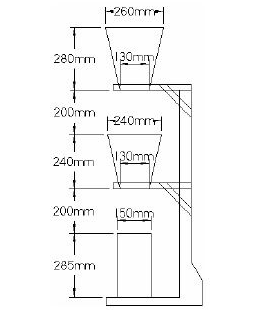
Fig no 5 Dimensions of compaction factor apparatus
Key takeaways
The compacting factor test is mainly designed for use in the laboratory but can also be used in the field. It is more accurate and sensitive than fall testing and is especially useful for very low-performance concrete mixes and is often used when the concrete will be squeezed by vibration. This method works on bare and ventilated concrete, made of lightweight, standard weight or heavy aggregates with a maximum weight of 38 mm or less but not on open concrete or non-reinforced concrete.
VEE BEE CONSISTOMETER AND FLOW TABLE APPARATUS
VEE BEE CONSISTOMETER
Objective
- The performance of the new concrete is a composite material, which incorporates various requirements for stability, mobility, durability, placement and finishing. There are various ways to measure performance.
- Each of them measures only a specific aspect of it and there is no unique test, which measures the performance of concrete completely. This test provides an indication of the flow rate of the newly mixed concrete mix.
- The test measures the concurrent effort required to change a pile of concrete from one concrete to another (e.g., from a circle to a cylindrical) using vibration.
- The amount of effort (called retrieval attempt) is taken as the time in seconds, which is required to complete the change. The results of this experiment are useful when you study the flow of concrete piles made of different amounts of water, cement and different types of composite placement.
- The time required for a full recovery in seconds is taken as a performance measure and is expressed as the Vee-Bee number of seconds.
- This method is suitable for dry concrete. With concrete drop of more than 50mm, reconstruction is so fast that time cannot be measured.
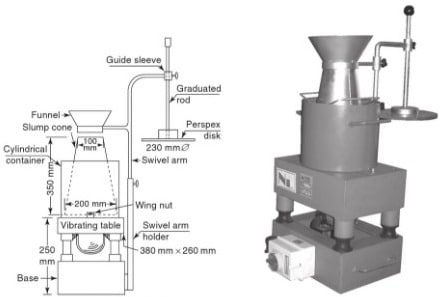
Fig no 6 Vee bee Consistometer Test
Procedure
- Slump test as described in "IS 1199: 1959 Details of Concrete Testing Equipment (Fourth Review). Confirmed- Dis 2013". Is made, inserting a collapsible lump inside a round metal pot of consist meter.
- The glass disk attached to the rotating arm will be moved to the top of the cone in the pot and before the cone is raised, the location of the concrete cone will be identified by fixing the glass disc attached to the arm wrist. The cone will then be lifted and the fall will be marked on the graduating rod by lowering the glass disc over the concrete cone. The electric heater will then light up and the concrete will be allowed to lay in the pot.
- The vibration continues until the point where the concrete shape disappears and the concrete takes on a circular shape. This can be judged by looking at the glass disc from the top disappearing visually.
- As soon as the concrete completely begins to form a circle, the stand clock is turned off. The time required for concrete formation to change from the formation of a collapsing lump into a circle in seconds is known as the Vee Bee Degree.
- This method is best suited for dry concrete with an unmeasured fall value with a Slump Test, but vibration is much stronger than concrete with a fall of more than 50 mm.
FLOW TABLE
Flow tests were performed to measure the performance of the concrete. As the name suggests, in this experiment concrete performance is measured by examining the flow of concrete material. Flow test Easy laboratory test. This test applies to the principal for the general weight loss of concrete and is measured by the flow of concrete. The flow of concrete indicates the performance of the new concrete.
Why flow test of concrete required
Flow tests are used to measure the performance of high or very active concrete, which ultimately indicates a fall. It gives an idea about the quality of concrete in terms of consistency and consistency. This performance test is easy to perform and is best suited for concrete with a high overall size of the joint less than 38 mm.
Flow Test Apparatus
Metal Cone or Mould: Mould is in the form of a frustum of a cone with a base diameter of 250 mm, upper surface diameter of 170 mm and 120 mm height. The mould comes with handles for support.
Flow Table
Trowels
Hand scoop
Scale
Tamping Rod
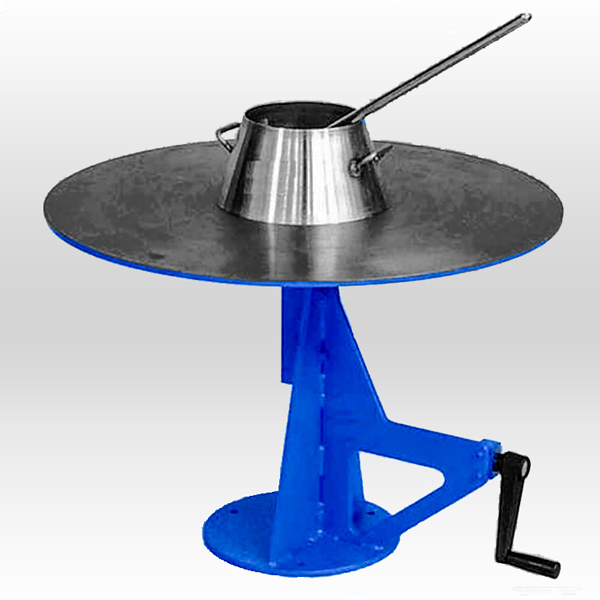
Fig no 7 Flow test apparatus
Procedure
- Clean anything toxic or dusty from the flow table and inside the mold.
- Place the lump on the marked area or in the middle of the flow table.
- Now pour the freshly mixed concrete into the mold in two layers, each layer should be moistened 25 times with a soft stick. If the concrete overflows after stamping and measure with the help of a torch, and the excess concrete should be removed from the table.
- After that, lift the mold upwards and allow the concrete to stand on its own without support.
- After that the table is raised and lowered from 12.5 mm high, 15 times in about 15 seconds.
- Next, measure the width of the concrete spread by about 6 points and write down the scale.
Key takeaways
- The performance of the new concrete is a composite material, which incorporates various requirements for stability, mobility, durability, placement and finishing. There are various ways to measure performance.
- Each of them measures only a specific aspect of it and there is no unique test, which measures the performance of concrete completely. This test provides an indication of the flow rate of the newly mixed concrete mix.
- Flow tests were performed to measure the performance of the concrete. As the name suggests, in this experiment concrete performance is measured by examining the flow of concrete material. Flow test Easy laboratory test. This test applies to the principal for the general weight loss of concrete and is measured by the flow of concrete. The flow of concrete indicates the performance of the new concrete.
Effect of admixture on workability of concrete and optimum dosage of admixture by marsh cone test
Effect of admixture on workability of concrete
- Concrete contains cement, sand, a mixture of water. Anything other than these if added to concrete before or during mixing to convert structures to our desired requirement is called admixtures. The use of admixtures provides certain beneficial effects on concrete such as improved performance, speed or delay of set time, reduction of the amount of water cement, and so on.
- There are two basic types of admixtures available: chemicals and minerals. Admixtures such as fly ash, silicate fume, slag come in the category of mineral admixtures. They are incorporated into concrete to increase performance, improve thermal resistance and alkaline reactions and enable us to reduce cement content.
- Fly ash is a good residue left over from global warming or powdered charcoal. They are all better than cement and contain mainly round glass particles as well as remnants of hematite and magnetite, char and other crystalline layers formed during cooling. The use of fly ash in concrete makes mixing more economical, and improves performance, reduces separation, bleeding and reduces hydration temperatures but also offers natural benefits.
- Silica fire, also known as micro silica. It is available as a product during the production of silicon and ferrosilicon alloys. The particles of silica fire particles are 100 times smaller than cement particles which mean their smoke like cigarettes. Its highly efficient pozzolanic material, which improves concrete structures such as improved durability, bond strength, abrasion resistance, dense concrete leading to reinforcement and rust protection.
- Chemical admixtures are applied to concrete in very small quantities especially for ventilation, reduction of water or cement content, installation of new concrete mixtures or control of concrete set time. These compounds can be widely used as super plasticizers, accelerators, retarders, water reducers and ventilation admixtures.
- Super plasticizers were added to reduce water demand by 15 to 20% without affecting performance leading to high durability and high concrete. Super plasticizers are liner polymers that contain sulfonic acid groups attached to the polymer from time to time. Commercial composition can dissolve melamine - formaldehyde condens- sates, sulfonated naphthalene formaldehyde condensates, and modified lingo sulfonates, derived from polycar- boxylate. The main purpose of super plasticizers is to produce a concrete slope with a very high drop of 175 to 200 mm that can be used effectively on reinforced concrete structures, a decrease in volume depending on the volume, type and timing of good plasticizers (preferably before adding concrete.), Water cement, environment and value of cement.
- Accelerators were added to reduce the setting time of the concrete thus facilitating pre-form removal and are also used in the combination of cold weather. Calcium chloride is the most widely used accelerator in blending. The use of calcium chloride in reinforced concrete can promote the corrosion function of the steel reinforcement. As people become aware of it there is a growing interest in using free chloride.
- Retarders were added to increase the setting time by delaying the hydration of the cement. They are popular in areas with high temperatures combined. Retarders contain organic & inorganic agents. Organic retarders include unrefined calcium, sodium and ammonia salt lignosulfonic acid, hydro carboxylic acid and carbohydrates. Inorganic retardants include lead oxides, zinc, phosphate and magnesium salts. Most retarders work as a water repellent. They are called retarders that reduce water. It is therefore caused by high pressure forces due to the low water content.
- Admixtures reduce the amount of water added to the concrete to achieve a certain effect (fall) at a lower water level. Strong concrete specified for low cement content thus saving cement. Water reducers are widely used in hot weather and assist in pumping. Water-repellent plasticizers are hygroscopic powder, which can inhale air into concrete.
- Ventilation admixtures bring in small concrete bubbles. These air bubbles act as rollers thus improving performance and also work more efficiently in thaw-chilling channels as they provide a stabilizing effect in expanding water where cold weather meets.
- Ventilation admixtures are compatible with most combinations, care should be taken to prevent them from collapsing during mixing.
- In general, the performance of both types of plasticizers depends on the ambient temperature and thus in the summer the amount of plasticizer that will be used to handle the same rate of plastic expansion may be more than the amount that will be used in winter.
- The change in the normal set time within a specific requirement also makes the product dependent on other chemicals and as plasticizers with different nomenclature available in the market.
- CICO Technologies Limited, a 75-year-old Indian company ISO 9001: 2000 supported producing a range of concrete installation admixtures.
- Many RMC companies use CICO admixtures. Further modification is required during the trial. Modification to Plasticizers can meet the needs of any particular client.
Optimum dosage of admixture by marsh cone test
- Admixtures are common and important of modern concrete. Low water content, high efficient, durable and cost-effective cement
- Many desirable properties that can be expected from concrete made of chemical and mineral composites
- Admixture-Cement mixing in concrete is complex combination of chemical and physical equipment independent.
- All combinations in large volumes offer good results when used with cement.
- Cement hydration involves a series of reaction, which is highly dependent on cement composition, water / cement ratio, surface area, particle distribution of size, temperature and integration.
- Admixtures when added in small amounts do that the hydration process is very complex. In recent times, developments in the cement product sector are related to the use of admixtures especially organic polymeric building materials.
- Many species of polymeric organisms known as super plasticizers, are used construction industries to change the way it flows again concrete machinery facilities.
- Among the various species for chemical admixtures, PCE-based admixtures are shown to develop new flow and complex areas of low-grade concrete.
Key takeaways
- Concrete contains cement, sand, a mixture of water. Anything other than these if added to concrete before or during mixing to convert structures to our desired requirement is called admixtures. The use of admixtures provides certain beneficial effects on concrete such as improved performance, speed or delay of set time, reduction of the amount of water cement, and so on.
- Admixtures are common and important of modern concrete. Low water content, high efficient, durable and cost-effective cement
- Many desirable properties that can be expected from concrete made of chemical and mineral composites.
Testing of hardened concrete
- The compression take a look at indicates the exceptional feasible electricity concrete can gain in best conditions.
- The compression take a look at measures concrete electricity withinside the hardened state.
- Field concrete samples are organized, cured and examined consistent with ASTM preferred procedures.
- Specimens are organized from concrete taken from exclusive creation sites.
- Following methods and calculations are used for measuring compressive electricity of cylindrical concrete specimens.
Test Procedure
- Placing the Specimen — The plain (decrease) bearing block is located, with its hardened face up, at the desk of the trying out device without delay beneath the spherically seated (top) bearing block. The bearing faces of the top and decrease bearing blocks are wiped clean and the take a look at specimen is located at the decrease bearing block.
- Zero Verification and Block Seating— previous to trying out the specimen, it's far demonstrated that the weight indicator is ready to zero. If the indicator isn't always well set to zero, it's far adjusted.
- Rate of Loading— the weight is implemented constantly and without shock.
- Standards specify that for trying out machines of the screw type, the shifting head shall tour at a charge of about zero.05in. (1mm)/min while the device is jogging idle .While for hydraulically operated machines, the weight will be implemented at a charge of motion (platen to crosshead measurement) similar to a loading charge at the specimen in the variety of 20 to 50 psi/sec (0.15 to 0.35 M Pa/sec).
- During the software of the primary 1/2 of of the expected loading phase, a better charge of loading is allowed.
- No adjustment is made with inside the charge of motion of the platen at any time at the same time as a specimen is yielding swiftly right away earlier than failure.
- Load is implemented till the specimen fails, and the most load carried via way of means of the specimen all through the take a look at is recorded. The form of failure and the arrival of the concrete also are noted.

Fig no 8 Compression Testing Machine
Calculations:
Concrete Cylinder Loading Samples Compressive energy of the specimen is calculated through dividing the most load carried through the specimen all through the check with the common cross-sectional area.
Determine and specific the end result to the closest 10 psi (0.1 M Pa).
Key takeaways
The electricity of air-dried cores is on common 14 percentage large than the electricity of soaked cores.
Flexural Strength
Objective:
- To decide the Flexural Strength of Concrete, which comes into play whilst a avenue slab with insufficient sub-grade guide is subjected to wheel masses and / or there are extent modifications because of temperature / shrinking.
Equipment & Apparatus:
- Beam mildew of length 15 x 15x 70 cm (whilst length of mixture is much less than 38 mm) or of length 10 x 10 x 50 cm (whilst length of mixture is much less than 19 mm)
- Tamping bar (forty cm long, weighing 2 kg and tamping phase having length of 25 mm x 25 mm)
- Flexural take a look at gadget– The mattress of the checking out gadget will be furnished with metal rollers, 38 mm in diameter, on which the specimen is to be supported, and those rollers will be so hooked up that the space from centre to centre is 60 cm for 15.0 cm specimens or forty cm for 10.0 cm specimens.
- The load will be implemented via comparable rollers hooked up on the 1/3 factors of the assisting span that is, spaced at 20 or 13.3 cm centre to centre.
- The load will be divided similarly among the 2 loading rollers, and all rollers will be hooked up in this sort of way that the burden is implemented axially and without subjecting the specimen to any torsion stresses or restraints.
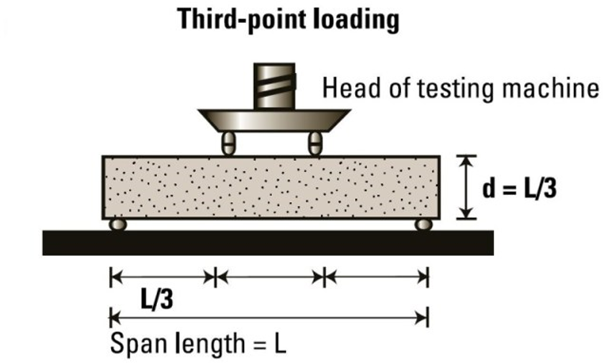
Fig no 9 Flexural testing machine
Procedure:
- Prepare the check specimen via way of means of filling the concrete into the mold in three layers of about identical thickness.
- Tamp every layer 35 instances the use of the tamping bar as distinct above.
- Tamping have to be disbursed uniformly over the whole cross section of the beam mildew and in the course of the intensity of every layer.
- Clean the bearing surfaces of the assisting and loading rollers , and get rid of any free sand or different cloth from the surfaces of the specimen in which they may be to make touch with the rollers.
- Circular rollers synthetic out of metallic having pass phase with diameter 38 mm may be used for presenting assist and loading factors to the specimens.
- The duration of the rollers will be at the least 10 mm greater than the width of the check specimen.
- A general of 4 rollers will be used, 3 out of which will be able to rotating alongside their very own axes.
- The distance among the outer rollers (i.e. span) will be 3d and the gap among the internal rollers will be d.
- The internal rollers will be similarly spaced among the outer rollers, such that the whole gadget is systematic.
- The specimen saved in water will be examined right away on elimination from water; while they may be nevertheless wet.
- The check specimen will be positioned with inside the device efficiently targeted with the longitudinal axis of the specimen at proper angles to the rollers.
- For mould specimens, the mold filling route will be ordinary to the route of loading.
- The load will be implemented at a price of loading of 400 kg/min for the 15.0 cm specimens and at a price of 180 kg/min for the 10.0 cm specimens.
Calculation:
- The Flexural Strength or modulus of rupture (fb) is given via way of means of
- F b = pl/bd2 (while a > 20.0cm for 15.0cm specimen or > 13.0cm for 10cm specimen)
O r
- F b = 3pa/bd2 (while a < 20> 17.zero for 15.0cm specimen or < 13> 11.0cm for 10.0cm specimen.
Where,
a = the gap among the road of fracture and the closer assist, measured at the middle line of the tensile aspect of the specimen
b = width of specimen (cm)
d = failure factor intensity (cm)
l = supported duration (cm)
p = max. Load (kg)
Safety & Precautions:
- Use hand gloves while, protection footwear on the time of check.
- After check transfer off the device.
- Keep all of the uncovered metallic elements greased.
- Keep the manual rods firmly constant to the bottom & pinnacle plate.
- Equipment have to be wiped clean very well earlier than trying out & after trying out.
Key takeaways
1. Beam mildew of length 15 x 15x 70 cm (whilst length of mixture is much less than 38 mm) or of length 10 x 10 x 50 cm (whilst length of mixture is much less than 19 mm)
Indirect Tensile Strength
- Indirect dynamic strength changes were tested from six samples: three dry samples and three samples exposed to water.
- During the indirect strength test, the sample is attached between two load strips and loaded freely at a speed of 50mm / min.
- The maximum load on the crack is measured. The relationship of energy values before and after water storage is determined, and is called the Indirect Tensile Strength Ratio (ITSR).
- Similar to the indirect strength test, a single-axial direct tensile test was initiated to investigate the strength structures of the study. Also, the strength was determined before and after preparing the test sample in the bath water according to EN 12697-12 B.
- The test samples used in this study included prismatic samples of the asphalt compound, as well as rods extracted from the rock and glued together with bitumen film.
- In the testing of dominant asphalt beams, every six beams are cut into slabs of composite asphalt composite (three dry, three wet). Adapters are attached with adhesives to the two parts of the sample surface.
- This is required to load samples into the machine. Strength strength is applied at a speed of 1.5mm / min at a temperature of 15 ° C. After the sample cracking, the strength of the strength is determined from high pressure, and the exact amount of strength strength (DTSR) accordingly.
- Similarly, direct strength testing was also applied to the extruded walls. On the rock covered and glued together the bitumen film.
- The power test is performed with different loading speeds and test temperatures. The broken sample.
- The materials investigated in this study include various types of bitumen (50/70, 70/100), bitumen modified polymer (PmB 40 / 100-65H, PmB 45A), of a wide range of natural materials from adhesive adhesives to adhesive markers. Fine (basalt, Taunusquarzite, limestone, granite, gabbro), and four types of asphalt mixtures (AC 11, AC 16, SMA 11, PA 8).
- Details of the composite, bitumen-aggregate composites, types of asphalt composites and related tests. Preliminary tests have shown that high image quality is very important for reproduction, because both the base installation and the descent frame depend on contrast of the image brightness.
- Therefore, image quality was guaranteed by the introduction of low levels of brightness, contrast, and sharpness of the image as measured by DSA1 software.
- About 10% of the images produced failed to meet these standards and were not included in further analysis. A small number of usable metrics are defined as 30 data points per bit bitumen.
- The data only show slightly different outputs for multiple samples, with the exception of PE6506, and the standard deviation (SD) of the method generally compared the differences between the contact angles of different locations.
- To determine whether communication angles are very different or not, statistical testing methods have been used. The first Shapiro- Wilk test was used for standardized testing. It confirms the general distribution of data. Subsequently, variance analysis (ANOVA), in particular data was subjected to the F test.
- Including all samples tested, the F test rejected the absurd notion that communication angles are very different, i. e. a group of mediators is very different from each other.
- As the mean values of PE6506 deviated significantly from the data of other bitumen, the test was repeated without PE6506. The result shows that in this experiment only PE6506 can be separated from a number of other samples, which can also be separated between them.
- Pendant suction measurements are performed using five bitumen and bitumen precursors. Excess power is measured as a heat function.
- Linear regression analysis can be used in addition to other adjacent conditions because the samples show a very similar pattern at higher temperatures, but a different tendency to deal with lower.
- For example, the two releases include a 95% confidence interval time. Places are very advanced. The results of the addition of all the bitumen studied including error bars, which are found in the external confidence interval.
- The general overlap indicates that this method cannot distinguish between the tested samples. Therefore, the development of testing in relation to rebirth is necessary. The use of small glass slides as a basic model of bitumen-mineral aggregate interface has several advantages.
- First, the surface is perfectly smooth and chemically uniform. Second, the chemical properties of glass are similar to the composition of highly acidic minerals, which usually have a very high content of SiO 2.
- To test the strength of this test, two samples of bitumen (50/70 and 70/100) and a mixture of these bitumen and adherence agent were tested (50/70 + and 70/100 +). New drops of bitumen in the glass gave the same effect to all bitumen.
- After being stored at 70 ° C for 30 minutes, in addition to the bitumen softening points (50/70 and 50/70 +: 48 ° C; 70/100 and 70/100 +: 45 ° C) the results were different. Communication angles are very different from each other. The contact angles of pure bitumen are around 6 ° below the mixtures.
- This means, however, that wettabilities are worse with bitumen containing the input. The final variation of this test was the introduction of static water storage.
Key takeaways
- Indirect dynamic strength changes were tested from six samples: three dry samples and three samples exposed to water.
- During the indirect strength test, the sample is attached between two load strips and loaded freely at a speed of 50mm / min.
Core Test
- Basic concrete testing is the most popular and well-established test method for the compressive strength of hard concrete. Critical concrete testing makes visual inspections of the internal parts of the concrete member also related to strength limitations Portable coring enables the inspection of other reinforced concrete structure structures with solid concrete testing
- In any case, the need to perform basic concrete tests often stems from the failure of concrete cubes / cylinders to get a realistic view of the strength of concrete as it exists in construction materials
Sampling of concrete core
It is very important that basic concrete samples are taken according to the guidelines given below
- Cores should be taken using pieces of diamond-filled spinal cord.
- Cores tested for power structures should have a minimum diameter three times the size design size of a rated set or 50 mm. Whoever is great
- Where possible, cores tested for energy structures should be at least twice their length width
- As far as it is concerned that the reinforcing metal should not be inserted into the spine to be tested for strength. The size, number, and location of the metal reinforcement in the proposed primary area can be determined by using magnetic resonance imaging such as a retrieval meter (cover meter) or by ground-based radar testing or by using a pull-out radar system. If the spine contains a flexible reinforcing steel, a certain effect on the strength should be expected There is a possibility of a decrease in the strength of the concrete slab depending on the position of the steel. This effect is especially important when the metal is very far from the end of the set.
- As far as possible, the foundation pit should penetrate completely into the concrete section. This prevents spinal fractures and facilitates their removal. On the other hand, if drilling is not possible due to the size and configuration of the building in the area where the coring is planned, an additional 50 mm should be bound as a share of potential damage to part of the context.
- One root should not be used to diagnose a specific problem. When cores are taken gain power, a minimum of three characters need to be removed from each location. The amount of concrete strength in the hole should be taken as the benefit of these grains
- Special care needs to be paid when choosing a place for the concrete for standing concrete members such as walls, deep beams, etc. This is due to the differences in high-rise concrete structures due to differences in laying and mixing processes, separation, and bleeding. It is known that in general, the strength of concrete decreases as its height within the placement of membership increases.
- The exact history of structural treatment is often difficult to obtain so the effect of cooling the ammunition is also uncertain. When there is no wet treatment, no power expectations should be expected
- The direction of the ball also affects the strength of the bullets. Horizontally bound cores usually have lower power than direct bound calls,
- When cutting the core, the integrity of the concrete structure in the full section (c / s) is possible is affected to some degree. This feature should be taken into account when selecting a location where the file the core should be taken
Concrete Test procedure
Concrete pieces are usually cut with rotating cutting tools with diamond pieces. The cylinder sample is obtained by concluding its unequal pieces of equal parts, square, and embedded.
Cores are inspected visually to pay attention to the distribution of the composite, the compaction of concrete (non-air visibility), and the presence of metal, etc. The concrete slab should be soaked in water, soaked in melted sulfur so that it ends up parallel to the right angle. It is also tested on a pressure-testing machine in wet conditions in accordance with BIS 1881: Part 4: 1970 or ASTM 42-77.
Use of concrete core sample
- Water or gas leakage
- Chemical analysis
- ASHTO chloride permeability testing
- Determination of strength and resilience
- Depth of concrete installation
- Petro graphic Analysis
Key takeaways
- Cores should be taken using pieces of diamond-filled spinal cord.
- Cores tested for power structures should have a minimum diameter three times the size design size of a rated set or 50 mm. Whoever is great
- Where possible, cores tested for energy structures should be at least twice their length width
Non-Destructive Test - Rebound Hammer
Objective:
- The rebound hammer technique might be used for:
- Assessing the possibly compressive electricity of concrete with the assist of appropriate correlations among rebound index and compressive electricity,
- Assessing the uniformity of concrete,
- Assessing the excellent of the concrete in relation to traditional requirements, and
- Assessing the excellent of 1 detail of concrete when it comes to another.
Principle:
- When the plunger of rebound hammer is pressed in opposition to the floor of the concrete, the spring controlled mass rebounds and the volume of such rebound relies upon up on the floor hardness of concrete.
- The floor hardness and consequently the rebound is taken to be associated with the compressive strength of the concrete.
- The rebound is examine off alongside a graduated scale and is unique as there sure variety or rebound index.
Procedure:
- For trying out, smooth, easy and dry floor is to be selected. If loosely adhering scale is present, this have to be rubbed of with a grinding wheel or stone. Rough surfaces due to incomplete compaction, lack of grout, spalled or tooled surfaces do now no longer deliver dependable outcomes and have to be avoided.
- The factor of effect is to be at the least 20 mm far from any facet or form discontinuity.
- For taking a measurement, the rebound hammer is to be held at proper angles to the floor of the concrete member. The check can as a result be performed horizontally on vertical surfaces or vertically upwards or downwards on horizontal surfaces. If the state of affairs demands, the rebound hammer may be held at intermediate angles additionally, however in every case, the rebound variety may be unique for the equal concrete.
- Rebound hammer check is performed round all of the factors of remark on all on hand faces of the structural detail. Concrete surfaces are very well wiped clean earlier than taking any measurement.
- Around every factor of remark, six readings of rebound indices are taken and common of those readings after deleting outliers as consistent with IS: 8900-1978 turns into the rebound index for the factor of remark.
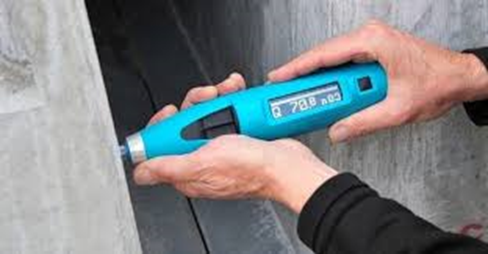
Fig no 10 Showing Rebound Hammer
Interpretation Of Result:
- The rebound hammer technique offers a handy and speedy indication of the compressive energy of concrete via organism appropriate correlation among the rebound index and the compressive energy of concrete. The process of acquiring such correlation is given in 4.2.
- It is likewise mentioned that rebound indices are indicative of compressive energy of concrete to a constrained intensity from the floor. If the concrete in a selected member has inner micro cracking, flaws or heterogeneity throughout the cross-section, rebound hammer indices will now no longer imply the equal.
- As such, the estimation of energy of concrete with the aid of using rebound hammer technique can't be held to be very correct and in all likelihood accuracy of prediction of concrete energy in a shape is ±25 percent.
- If the connection among rebound index and compressive energy may be checked with the aid of using assessments on center samples acquired from the shape or well known specimens made with the equal concrete substances and blend proportion, then the accuracy of consequences and self belief thereon are substantially increased.
Key takeaways
- The rebound is examine off alongside a graduated scale and is unique as there sure variety or rebound index.
Ultrasonic Pulse Velocity
- This take a look at is accomplished to evaluate the nice of concrete with the aid of using ultrasonic pulse pace technique as according to IS: 13311 (Part 1) – 1992. The underlying precept of this take a look at is –
- The technique includes measuring the time of journey of an ultrasonic pulse passing via the concrete being tested. Comparatively better pace is acquired whilst concrete nice is ideal in phrases of density, uniformity, homogeneity etc.
- Procedure to decide energy of hardened concrete with the aid of using Ultrasonic Pulse Velocity:
- Preparing for use: Before switching at the ‘V’ meter, the transducers ought to be linked to the sockets marked “TRAN” And ” REC”.
- The ‘V’ meter can be operated with either:
a) The inner battery,
b) An outside battery or
c) The A.C line.
- Set reference: A reference bar is supplied to test the tool zero. The pulse time for the bar is engraved on it. Apply a smear of grease to the transducer faces earlier than putting it on the other ends of the bar. Adjust the ‘SET REF’ manage till the reference bar transit time is acquired at the tool read-out.
- Range selection: For most accuracy, it's miles endorsed that the 0.1 microsecond variety be decided on for route duration up to 400mm.
- Pulse pace: Having decided the maximum appropriate take a look at factors at the fabric to be tested, make cautious dimension of the route duration ‘L’. Apply couplant to the surfaces of the transducers and press it tough onto the floor of the fabric. Do now no longer flow the transducers whilst a analyzing is being taken, as this could generate noise indicators and mistakes in measurements. Continue keeping the transducers onto the floor of the fabric till a steady analyzing seems at the show, that's the time in microsecond for the ultrasonic pulse to journey the distance ‘L’. The imply price of the show readings ought to be taken whilst the gadgets digit hunts among values.
Pulse pace= (Path duration/Travel time)
- Separation of transducer leads: It is really helpful to save you the 2 transducer leads from getting into near touch with every different whilst the transit time measurements are being taken. If this isn't always accomplished, the receiver lead would possibly pick-up undesirable indicators from the transmitter lead and this will bring about an wrong show of the transit time.
Interpretation of Results:
- The nice of concrete in phrases of uniformity, occurrence or absence of inner flaws, cracks and segregation, etc, Indicative of the extent of expertise employed, can as a consequence be assessed the use of the recommendations given below, that have been advanced for characterizing the nice of concrete in systems in phrases of the ultrasonic pulse pace.
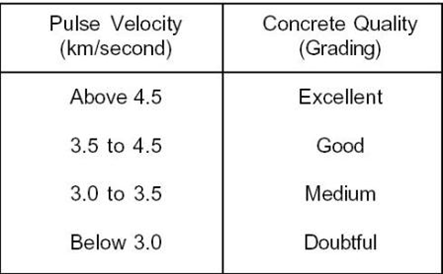
Fig no 11. Table of pulse velocity
Key takeaways
2. Set reference: A reference bar is supplied to test the tool zero. The pulse time for the bar is engraved on it. Apply a smear of grease to the transducer faces earlier than putting it on the other ends of the bar. Adjust the ‘SET REF’ manage till the reference bar transit time is acquired at the tool read-out.
Pullout Test and Impact Echo Test
Pullout Test
The principle
This test is based on the principle that the force required to extract a metal coating embedded in concrete is equal to the strength of the concrete.
Test Process
Remove the insert (shown on the fig tree) embedded in the empty concrete during pouring. When power is required to be determined, power is applied to the embedded end. The power required to issue a meeting is measured.
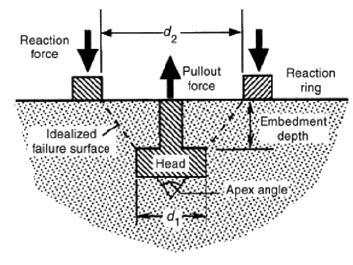
Fig no 12. Pull out the concrete test
Limitations
The steel assembly should be embedded in concrete at the time of pouring so testing may not be carried out in the years to come.
Damage to damaged concrete is required.
Evaluation
- The extraction assembly is pulled by a concrete cone, which is responsible for friction and shaving and the force required to exit is related to the cutting strength of the concrete and not the compressive force.
- The rate of dissipation in the compression force decreases slightly with increasing power level.
- Removal cannot be performed until complete. It is sufficient to insert a fixed power into the embedded pole and if not removed, the supplied power is assumed to exist.
- According to Malhotra, the output test is higher than the Schmidt hammer and the input test because a large volume and depth of concrete are involved in the test. Post-test concrete repairs are also required. The relationship between the force of gravity and gravity is shown in the figure below.
Impact Echo Test
Impact-Echo is a non-destructive exploration method for exploring concrete structures and stone structures. The test uses pressure waves (sound) that are usually made of impact-impact concrete, and to record thinking and emissions from internal errors and other parameters (Echo). Typically, a heartbeat is performed with an effect in one place. The resulting wave of depression is spreading in all directions. In this regard, the generated wave does not have a directional pulse generated by a large transducer (as in the case of ULTRASONIC PULSE VELOCITY). As the reflection reaches in all directions, the test method works well for thin objects, such as piles where the outer boundary directs the wave to the pile. In this particular application, the test is set as the low-level strength test. Learn more about the PILE INTEGRITY TEST.
Concept Behind Impact-Echo Method
The concept of Impact-Echo testing is shown in Figure. The mechanical impact of the concrete surface is used to produce a pressure wave. The production pulse creates a spread across the concrete next to circular waves such as P- and S-waves. Another is the surface wave (R) that moves over.
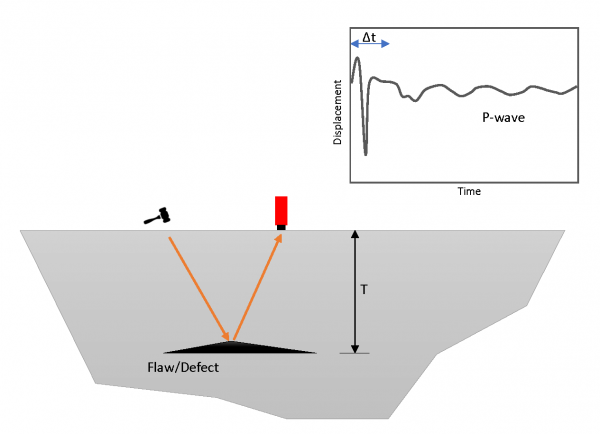
Fig no 13. Impact echo method
As the P- and S waves propagate inside the concrete object, they are indicated by internal interactions (concrete-split, air-concrete, concrete -rebar) or external boundaries. The arrival of these echo in the face causes migration. This migration can be measured by placing a sensitive transducer (which converts the transmission or acceleration of electrical energy). Data is recorded through a data acquisition and data entry system.
Analyses Impact-Echo data
Data analysis can be done in Time Domain, or Frequency Domain. While time domain analysis seems to be the best way to define sensitive data (as in the case of bulk testing), it can be a much more complex approach in the case of small slabs. In these sections, signal analysis in the domain of frequency is popular.
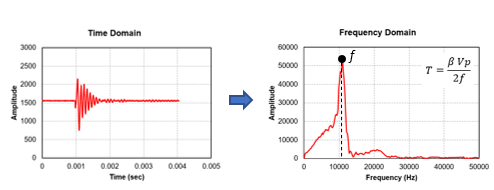
Fig no 14. Analysis of impact echo method
The Fast Fourier transform (FFT) process is used to analyze digital frequency frequency recordings. In this way, the wave form can be represented as a total of sine curves, each with a certain height, frequency and phase shift. According to N. J. Carino. This method is used to calculate the amplitude magnitude of a frequency form, which gives the relative height of the fractional frequencies in the wave form.
Impact-Echo Technique Applications
Impact-Echo is an effective test solution with a variety of applications in assessing the condition of concrete structures. The test can be used to:
1- Measure the thickness of the concrete labs and walls
2- Measure the thickness of the concrete walls and the tunnel line
3- Identify deformities such as delamination in concrete books.
4- Measure the storage condition of concrete, dams, tunnel lamps, sea walls.
Key takeaways
- This test is based on the principle that the force required to extract a metal coating embedded in concrete is equal to the strength of the concrete.
- Impact-Echo is a non-destructive exploration method for exploring concrete structures and stone structures. The test uses pressure waves (sound) that are usually made of impact-impact concrete, and to record thinking and emissions from internal errors and other parameters (Echo).
- Good quality concrete is actually a compact mixture of cement, composite and good mixing with water that mixes into a hard mass due to the chemical action between cement and water.
- Each of the four regions has a specific function. The coarser collection serves as a filler. A good collection fills the gaps between the attachment and the green combination. Cement by contact with water acts as a bond.
- The flow of the mixture is aided by the adhesion of cement, fines to this day, increasingly using mixtures.
- Most of the reinforced concrete materials depend on the care used in all stages of concrete production. The logical separation of concrete ingredients is the core of the mixing design.
- However, it may not guarantee the achievement of the goal of quality workmanship. The purpose of quality control is to ensure the production of concrete of the same power from batch to batch.
- This requires that certain rules be followed in the various stages of concrete production and discussed below. The stages of concrete production are:
1. Batching and measurement of material
2. Mixing
3. Transport
4. Placement
5. Compacting
6. Curing
7. Finishing
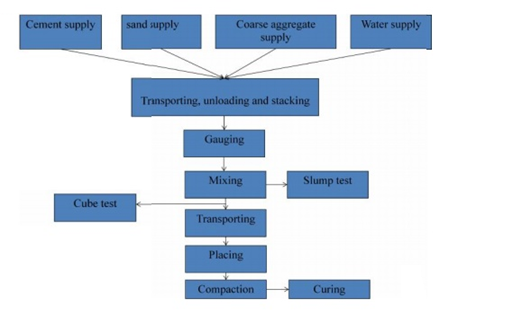
Fig no 15. Manufacturing process of concrete
Batching of material
- For good quality concrete should be used the correct and accurate amount of all ingredients. Combined, cement and water must be measured with an accuracy of 3 percent of batch quantity and admixtures at 5 percent of the total value. There are two most common forms of baking material, batching volume and heavy batching. Factors affecting the choice of baking method by the size of the work, the required production rate, the required batching performance standards. It is recommended for the most important tasks.
a) Volume batching
b) Weight batching
Mixing
1. Hand Mixing
2. Mixing Machine
a) Tilting mixers
b) Non- tilting mixer
c) Reversing Drum mixer
d) Pan type or stirring mixer
e) Transit mixer
f) Charging Mixer and mixing time
The order for the ingredients in the mixer is as follows:
- About 25 percent of the water needed for mixing is initially placed in the mixing tank to prevent any cement attachment to the rings and bottom of the drum. Then the ingredients are extracted in excess. To skip over the loading sequence should be to insert the first half of the coarse cement and then the composite half to be on top of this complete cement and the aggregate to balance. After adding the ingredients to the drum equal volume was introduced. The mixing time is calculated from the total water added to the mixture.
- The speed of the aggregates is usually 15 to 20 per minute. With proper mixing, the number of changes per minute required by the drum is 25 to 30. The mixing time also depends on the mixing capacity
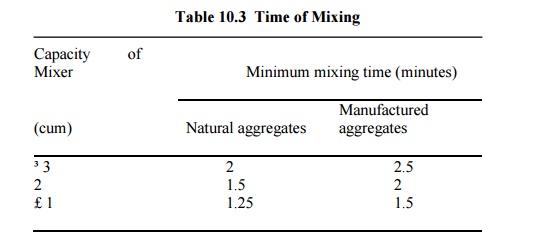
Fig no 16. Table of mixing
- Poor quality of concrete is obtained when mixing time is reduced. On the other hand if the mixing time is extended it is not economical. However, it is found that when the mixing time is extended to 2 minutes the compressive strength of the produced concrete is improved and beyond this time the improvement of the compressive strength is not significant. Prolonged mixing can cause separation. Also, due to the long mixing times water can get in or out and lead to loss of function and energy.
Transporting
The concrete should be moved to the storage area immediately without the loss of homosexuality acquired during mixing. a maximum of 2 hours from mixing time is allowed if trucks have an agitator and 1 hour using trucks without stimulants to move the concrete. And it must be ensured that separation does not occur during travel and placement. The methods used to transport concrete depend on the quality and value of the work, the distance to the placement site, and the location. Some of the concrete delivery methods are below:
a. Mortar pan
b. Wheel barrow
c. Chutes
d. Dumper
e. Bucket and ropeway
f. Belt conveyor
g. Skip and hoist
h. Pumping
Placing
- Achieving quality concrete should be placed very carefully to protect the homosexuality achieved during mixing and to avoid transport segregation. Studies have shown that delays in the installation of concrete results in gaining greater compressive strength as long as the concrete is not sufficiently compacted. In dry mixes in hot weather a delay of half an hour is allowed and in wet mixtures when it is cold it can be a few hours. The various conditions in which concrete is applied are discussed below.
Foundations
- Concrete foundations for walls and columns are provided underground. Before laying concrete on the foundation all open ground, tree roots etc., are removed. If the area is found dry it is made wet so that the soil does not absorb water from the concrete. On the other hand when the foundation bed is wet the water and mud are removed and the cement is sprinkled before laying the concrete.
Beams, columns and slabs
- Before laying the concrete, the forms must be inspected for proper alignment. They should be strong enough to withstand the weight of concrete and construction loads without undue damage. The forms should be light enough to avoid any mud loss that has resulted in concrete mixed with bees. The inside of the forms should be cleaned and oiled before use to avoid any adhesion to the concrete and forms and make it difficult to remove them.
- Concrete should not be discarded but should be placed in a place to protect against discrimination. It should be lowered as high as possible. It should be placed in one place on the formwork and allowed to flow in separate ways to take care of the bee colony.
- The formation of seas should be avoided. Can be tested by preventing concrete thickness by 150-300 mm with r c c function. Laitance, however, if constructed must be removed before laying the next layer of concrete. Several such layers form an elevator, as long as they follow each other fast enough to avoid cold joints. The top of the previous elevator is kept rugged and all the money spent is wiped out before setting the next elevator.
- Firmness should be checked for firmness and clean face. Rust or loose scales if present, are removed with a wire brush. Paint, oil or grease if found should be removed. a small tightening cover should be checked before assembly.
Mass concreting
- Where the concrete will be laid in bulk as a foundation for raft, dam, bridge, pier etc., the concrete is laid in sections of 350-450 mm in diameter. Several such layers arranged in quick succession form an elevator. Before applying the concrete to the next lift, the front elevator area is thoroughly cleaned with water jets and scrubbing with a wire brush. In the case of dams, sand explodes.
- Laitance and lax matter are removed and cement mortar is applied. Where the concrete is subjected to lateral thrust, binding bars or binding stones are provided to form the key between the various layers.
Concreting Highways and Runways
- Concrete is placed in the areas of highway, open road, or floor slabs. First the soil on which the concrete is to be placed is prepared and all loose material and grass are removed etc. The ground is wet and compacted. The subgrades into which the concrete is to be placed should be well mixed and diamond-plated to avoid any moisture loss in the concrete. The concrete is then placed elsewhere. This allows the concrete to pass through enough and the cracks do not grow after that. Concrete is not placed in a pile in one place and then pulled out, instead it is placed in the same size.
Concreting underwater
- Concrete can be placed under water with the help of dumping buckets. The concrete is soaked in water from a water-tight bucket. When you get to the floor the bucket is made open and the concrete is discarded. In this process a certain amount of cement is washed away resulting in a decrease in the strength of the concrete. Another way to make underwater concrete is to fill a bag of cement with a dry or dry mixture of cement and aggregates and lower it into the storage area. The downside to this approach is that the concrete will fill the gaps filled with the bags with the guns.
- A good way to put concrete under water is to use a termie pipe. Concrete is poured into it by a ditch. The lower edge of the pipe is covered with thick ploythene paper, below the pipe in the installation area. Concrete (150-200 mm fall) is poured into the mortar until the entire pipe is filled with cement. The pipe is slightly raised and given a jerk, the polythene metal cover falls off and the concrete is shown. It must be ensured that the end of the pipe stays inside the concrete so that water does not enter the pipe. The pipe is then filled with concrete along the border and the process is repeated to the concrete level above the water level. No reduction is required for underwater concrete as combined with hydrostatic water pressure. Concrete can also be placed under water with the help of pipes and pumps.
Compaction of concrete and curing process of concrete
1) Compaction of concrete
- Concrete should be thoroughly compacted and fully work around the reinforcement and into the corners of the formworks
- Concrete shall be compacted using mechanical vibrators
- Whenever vibration has been applied externally the design of formwork and the deposition of vibrators should receive special consideration to ensure efficient compaction and to avoid sir face blemishes
2) Curing process of concrete
- Curing of concrete is defined as the process of maintaining the moisture and temperature condition of concrete for hydration reaction to the normally so that the concrete develops hardened and properties over time
- The main components which need to be taken care of your heat and time during curing process
- Curing is the process of preventing the loss of moisture from the concrete which maintaining a satisfactory temperature effect
- If the cement has high rate of strain development and if the concrete contains granulated blast furnace and flue Ash then,
- The curing should also prevent the development of high temperature gradients within the concrete
a) Moist curing
- Surface of the concrete shall be kept continuously in Dam or wet condition by covering with the layers of materials like checking Canvas etc.
- It should be kept continuously wet for at least 7 days from the date of placing concrete.
- In case of ordinary Portland cement at least 10 days. Where mineral admixture or blended cement are used.
- The period of curing shall not be less than 10 days for concrete exposed to the dry and hot weather condition.
- In case of concrete where mineral admixture or blended cement are used it is recommended that above minimum period may be extended 14 days.
b) Membrane curing
- Approved curing compounds may be used in place of moist curing with the permission of engineer in charge.
- Search compound shall be applied to all exposed surfaces of the concrete as soon as possible after the concrete has set.
- Impermeable membrane such as polyethylene sheeting covering closely the concrete surface may also be used to provide effective barriers against evaporation.
- For the concrete containing Portland pozzolana cement, Portland slag cement or mineral admixture period of curing may be increased.
NOMINAL MIXES
- In concrete mix concrete, all ingredients and their size are determined by standard definitions. This ratio is specified in the cement ratio to the specific energy gain combination.
- Mixing ratios such as 1: 1.5: 3, 1: 2: 4, 1: 3: 6 etc. They were adopted by mixing concrete without a scientific basis, only on the basis of previous studies of solidarity. Therefore, acceptance of ordinary concrete or not to mention, the mixing of preference is preferred for simple, insignificant and minimal concrete works.
- According to the 'Indian Standard- IS 456: 2000', pre-mixed concrete can be used for M20 grade concrete or lower grade such as M5, M7.5, M10, M15.
Proportion of nominal mix as per Indian Standard
- The volume of composite materials under M20 grade concrete will comply with IS 456: 2000
- According to IS 456: 2000, in the composition of the composition can be adjusted the estimated values if the water level will be increased to overcome the difficulty of laying and density of concrete so that the water level of the cement is maintained as specified.
- Automatic mixing usually consists of volumetric batching. The measurement is usually determined by weight, and in combination it is converted to a volume value, i.e. in the case of one bag of cement, i.e. 50 kg of standard measuring boxes are made on site, at the rate of one bag of cement. These measuring boxes are called box gauges.
Advantages of nominal Mix Concrete
01. A self-proclaimed mix is a pre-determined concrete because the scale is pre-determined.
02. It is easy to do in the construction site.
03. It does not take much time to determine the value because the size is already provided with the standard code.
04. There is no need to find people who have the skills to make concrete mixing name.
Disadvantages of nominal mix concrete
01. The great recurrence of the mix of claims is that, it is based on past experience and studies of art, and has no scientifically proven method.
02. It can create or build well-designed energy unless all other factors such as density, w / c ratio, concrete treatment are strictly adhered to.
03. The amount of water cement is considered by thought and, if left unchecked, sometimes leads to bleeding and separation of the concrete which leads to poor performance and therefore impairs the strength of the concrete.
04. No consideration of composite structures such as classification and quantity of composite items etc.
05. In a word mix, cement content is sometimes used in excess, which increases the total cost of construction.
06. No laboratory tests are performed to ensure the quality of the new concrete.
07. This combination does not consider and evaluates the specific properties of each ingredient. For example, if we take cement as part, the softness of the cement, the quality of the cement and the type of cement, the size and layout of the composite etc. It is usually not counted individually when making this fake assertion mix.
Key takeaways
- In concrete mix concrete, all ingredients and their size are determined by standard definitions. This ratio is specified in the cement ratio to the specific energy gain combination.
- Mixing ratios such as 1: 1.5: 3, 1: 2: 4, 1: 3: 6 etc. They were adopted by mixing concrete without a scientific basis, only on the basis of previous studies of solidarity. Therefore, acceptance of ordinary concrete or not to mention, the mixing of preference is preferred for simple, insignificant and minimal concrete works.
- According to the 'Indian Standard- IS 456: 2000', pre-mixed concrete can be used for M20 grade concrete or lower grade such as M5, M7.5, M10, M15.
Freeze-Thaw Effect:
Concrete is very strong in compression but relatively weak in tension. It can and often does crack. Concrete is also fairly porous and subject to forces that absorb and release water. Absorbed water can freeze within the concrete and cause spalling and cracking.
Chemical Attack:
Chemical attack can occur because concrete is alkaline and chemically reactive. It can be attacked by acids; some alkalis; numerous salt solutions; and organics such as fermenting liquids, sugars, and animal oils, especially if they contain free acids.
Crazing:
This is a network of very small surface cracks usually spreading out over large areas or the entire surface. Crazing is caused by finishing the concrete with bleed water on top. The bleed water is forced down into the surface by the finisher’s trowel. This increases the ratio of water to cement, creating a weak surface layer.
Scaling:
Thin flakes of concrete come loose and flake or peel off the surface. The sizes of the flakes vary, but they usually increase over time and with traffic. Conditions that cause scaling and include freeze/thaw cycles, deicing agents with calcium or sodium chloride, fertilizers containing nitrates, working in bleed water, or improper curing.
Blisters:
These are typically about 1/4 to 1 inch diameter, but it’s not impossible to get 3 to 4 inch blisters. They are not easily seen until they are broken by traffic. Blisters are caused by working and finishing the surface while water or air is still working its way up through the mix to the surface.
Spalling:
Spalling is similar to scaling except large chunks instead of just flakes break loose. This indicates a severe weakness in some parts or the entire project. It is more likely to happen during freeze thaw conditions.
Dusting:
Also known as chalking, this is a fine loose powder caused by the deterioration of a weak surface. Causes of dusting include working in bleed water, improper curing, a bad sand-to-cement ratio, or exposure to carbon monoxide caused by using an unvented heat source to keep a project warm.
Foreign Objects:
Foreign objects can often slip into the form prior to pouring and may not become evident until after the forms are stripped. If fully embedded, the foreign object does not create a coating problem. But a piece of rope on the surface disappearing into the concrete is a problem. It must be removed, usually by chipping, and the concrete must be restored.
Efflorescence:
Efflorescence is more likely to be found on concrete that has been in place for a while. Concrete contains water-soluble salts. As water from the interior of the concrete migrates to the surface and evaporates, salts are deposited on the surface, usually as a white stain. Efflorescence can occur with concrete, brick, or concrete block construction. It can be removed with acid etching. The best way to prevent its recurrence is with adequate waterproofing.
Service / Market Area:
For industrial and commercial flooring projects we work in Michigan cities such as Muskegon, Norton Shores, Newaygo, Traverse City, Big Rapids, etc.
- Many types of admixtures or additives change the performance of a new concrete, either by construction or as a side effect.
- Surfactants such as super plasticizers reduce the attraction between cement and composite particles, allowing compounds that can flow without negative energy and the effects of excess water separation.
- The insertion of internal admixtures of durability / dissolving solids produces internal bubbles of a controlled size that can make it easier to eliminate, although overuse produces an adhesive mix with a different effect.
- The pressure of the concrete is eight times greater than its strength.
- This refers to the established relationship between the compressive strength and the strength of the concrete. In fact there is a close relationship but not a direct relationship.
- The degree of stiffness and pressure is low at high pressures.
- Experimental results also showed that concrete in stress and stress (both direct and indirect tension) is highly correlated but the relationship does not have a direct equation.
- The degree of strength and durability depends on the strength of the concrete.
- Thus, the increase in tensile strength, increases the tensile strength, but the rate of increase in tensile strength decreases steadily.
- The strength of concrete is more sensitive to improper treatment than to compressive strength.
This is possible for two reasons:
(a) The formation of a low-grade gel due to improper treatment.
(b) The formation of multiple shrinking cracks due to improper treatment. The use of pozzolanic materials showed an increase in strength.
- The Central Road Research Institute Delhi has conducted extensive research to build a relationship between the strength and durability of concrete in the construction of concrete roads.
- Based on the research experimental data, CRRI suggested the following relationship between flexural strength and concrete compression strength:
y = 11 x - 3.4
- Where is the compressive strength of MPa concrete and x and its flexibility. This relationship depends on the size of the coarse aggregate. Energy is available to vary in type and quantity of composite.
Relationships are renewed below:
(a) With a crushed stone of 20 mm y = 15.3 x - 9.0
(b) 20 mm Natural Graval y = 14.3 x - 10.4
(c) For 40 mm Crushed Stones y = 9.9 x -5.5
(d) 40 mm Natural Graval y = 9.8 x - 2.5
Key takeaways
The pressure of the concrete is eight times greater than its strength.
This refers to the established relationship between the compressive strength and the strength of the concrete. In fact there is a close relationship but not a direct relationship.
There are three main factors that affect concrete compression results: the specimen size, shape, and friction at its ends. These factors affect the observed phenomena, and they affect each other. This paper aims to review the current knowledge on concrete compression and the effect of size, shape and friction on it. Understanding their effects is essential for a safer design and more effective testing.
- Creep and thinning concrete are the two most visible features of concrete. The shrinkage of concrete, derived from calcium silicate hydrate (C-S-H) in a hardened Portland cement compound (which is responsible for mineral compounds), is quite different from the tilt of metals and polymers.
- Unlike metal cracks, it occurs at all levels of stress and, within the service level of stress, depends on what is stressed if the pore water content remains the same.
- In contrast to the eruption of polymers and metals, it exhibits several months of aging, caused by chemical hardening due to hydration that strengthens the formation of micro-organisms, and age-old aging, resulting in long-term resting of small equal pressure in nano- low CSH formation. When the concrete is completely dry, it does not move, but it is almost impossible to dry the concrete completely without severe cracking.
- Changes in water content in the pore due to dryness or watering processes cause significant changes in the volume of the concrete in non-load-bearing species. They are called shrinkage
- The age-old insect varies logarithmically over time (except for the final asymptotic value), and over normal life spans can receive values 3 to 6 times larger than the initial stretch problem. When deformation formation is abruptly induced and held inconsistently, the movement causes a break in the pressure produced in moderation. After discharge, increased recovery occurs, but in part, due to aging.
- In practice, travel during drying is inseparable from diminishing. The flow rate increases with the rate of change of pore humidity (e.g., vapor pressure associated with the pores). In the size of a small model, the penetration during drying far exceeds the total reduction of load without load and the penetration of the closed-loop template. The difference, called the drying creep or Pickett effect (or pressure-induced decrease), represents a hygro-mechanical between pore changes and pore humidity.
- The drying of the high humidity is mainly due to the pressure pressures on the solid microstructure that measure the increase in capillary tension and the surface tension in the pore walls. At low pore humidity (<75%), the shrinkage is caused by a decrease in the binding pressure across all nano-pores less than 3 nm in diameter, filled with indicated water.
- The chemical processes of Portland cement hydration lead to another type of shrinkage, called automatic shrinkage, which is detected in closed specimens, i.e., without loss of moisture. In part, this is due to changes in chemical volume, but especially energy loss due to the loss of water used by the hydration reaction.
- It achieves only about 5% of the dryness in normal cones, which self-desiccate about 97% of pore humidity. However, it can be equivalent to the reduction of drying in today's high-strength concrete containers with very low cement levels, which can cause the floor to have a humidity of less than 75%.
- The creep comes from calcium silicate hydrate (C-SH) attached to Portland cement. It is caused by slips due to breakage of bonds, by restoration of bonds in nearby areas. C-SH is highly hydrophilic, and has a colloidal microstructure separated from a few nanometers upwards. The paste has a porosity of about 0.4 to 0.55 with a large internal surface, about 500 m2 / cm3. Its main component is tri-calcium silicate hydrate gel (3 CaO · 2 SiO3 · 3 H20, abbreviated C3-S2-H3). The gel forms particles of colloidal size, which are weakly bound by van der Waals forces.
- How it works and modeling is still debated. The structural model in the following scales is not only available but at the moment has a very solid theoretical basis and fits very well with the full range of test data available.
Key takeaways
- Changes in water content in the pore due to dryness or watering processes cause significant changes in the volume of the concrete in non-load-bearing species. They are called shrinkage
- A concrete blend is a mixture of 5 primary factor numerous proportions: cement, water, coarse aggregates, quality aggregates (i.e. sand), And air.
- Additional factors including pozzolana substances and chemical admixtures also can be integrated into the combination positive ideal properties.
- While a concrete blend layout is a system of choosing substances for a concrete aggregate and choosing their proportions.
- When designing a blend, you don't forget the favored power, durability, and workability of the concrete for the venture in question.
- Needless to say, Already-blend manufacturers attempt to locate the suitable proportions of those substances to optimize the concrete mixes and provide their concrete power, durability, workability, and different ideal properties.
- It’s crucial to optimize concrete to make sure the bottom keeping the very best power of your aggregate.
- Concrete blend layout is frequently mistake analysis “cement blend layout.” However, cement is since rely one of the substances of concrete.
- It is a binding substance that let sin concrete to set, harden, and cling to different substances.
- Therefore, it can't and ought to now no longer be used interchangeably with concrete blend layout.
Objective
The following are the objectives of the concrete mix design:
a. Finding the pressure force at a certain distance.
b. Maintain concrete mixing performance throughout the work.
c. By gaining strength.
d. Achieve economy by choosing the right concrete ingredients.
e. Getting the highest yield in a cement bag.
f. Avoid bee contact and bleeding.
g. Compliance with various levels.
h. Reduce concrete damage by proper measurement.
The proportioning of concrete mixes consists of determination of quantities of different concrete-making materials necessary to produce concrete having the desired workability and 28-days compressive strength of concrete for a particular grade of concrete and durability requirements. Emphasis is laid on making the most economical use of available materials so as to produce concrete of required attributes at the minimum cost.
Concrete has to be satisfactory both in fresh and hardened states. The proportioning of concrete mixes is accomplished by the use of certain established relationships from experimental data which provides reasonably accurate guidance for selecting the best combination of ingredients so as to achieve the desired properties of the fresh and hardened concrete. Out of all the physical characteristics of concrete compressive strength is often taken as an index.
- Strength and sturdiness of the concrete blend layout are established upon the subsequent factors:
- Grade designation: Concrete’s power is measured in N/mm2 whilst issue to check after curing in any curing medium. The preference of concrete grade relies upon on its utilization.
- Choice of cement: Cement preference varies relying on utilization. The cement have to be examined for overall performance required with the aid of using their utilization earlier than being examined with inside the layout blend.
- Choice of mixture size: Aggregates wanted for every blend depends upon the bodily houses wanted for the layout. All aggregates need to be nice sized earlier than use.
- Type of water: Any water used for concrete blend layout is to be examined earlier than use to make certain it's far with inside the variety of water required for concrete. Most all consumable water is right for concrete work, however have to nevertheless be examined.
- Water to cement ratio: The ratio of water to cement have to be examined for consistency, preliminary and very last setting, soundness of the cement, workability, hunch of the concrete and compacting factor.
- Workability: This is the degree of ease of blending concrete without segregation or bleeding. It by and large relies upon at the designed hunch of the concrete.
- Durability: This is the degree of the specified power (N/mm2) of any concrete grade after 28 days of curing. Durability have to be manipulate examined on site.
Key takeaways
- Here different type of factors which affects mix proportion are durability, workability, water to cement ratio, type of water, choice of mixture size, choice of cement, grade designation.
The following points highlight five methods of concrete construction. The methods are:
1. American Method of Mix Design
2. Graphic Method of Mix Design
3. Mix Design by Indian Standard Method
4. American Concrete Institute Method of Mix Design
5. Quick Method of Mix Design.
1. The American Way of Mixing Designs:
- The American Concrete Institute (ACI) approach is based on the fact that the given size of a mixture of water content per kilogram of concrete determines the performance of a concrete mix, usually independent of the equilibrium. It is therefore possible to start the mixing formation by selecting the water content in these tables.
- In addition it is also assumed that the maximum volume of the estimated quantity of the total value of the concrete depends only on the maximum size and the combination of good composites.
2. Graphic Method of Mix Design
- This approach was developed by the Road Research Laboratory, London and its detailed procedure is described. Combined composites are supplied and their percentage above the normal working fine collection is 4.75 mm, 2.36 mm, 1.18 mm. 600 microns, 300 microns and 150 microns are used. For the maximum combined size of the allowable size, it says 38 mm, 19 mm, 9.5 mm 4.75 mm, 2.36 mm is used.
3. Assemble Design in a Traditional Indian Way:
- The Indian Bureau of Standards has recommended the concrete construction process in conjunction with the experimental work carried out in national laboratories. The mixing process is provided by IS-10262- 1982. Subsequently no updates have been made to this process , and IS 456-1968 has been updated in 2000. That is why IS 10262-1982 needs to be reviewed as the cement power available to a highly developed country.
Therefore the following changes need to be made:
1. The 28-day capacity for phase A, B, C, D, E & F renewal needs to be reviewed.
2. The relationship between the different strengths of cement and the size of w / c should be re-established.
3. The relationship between 28 days of pressure and w / c ratio should reach a pressure of 80 MPa (800 kg / cm2), if the graph is to be used for high strength concrete.
4. According to the revised IS 456-2000 the usability level is expressed in degradation instead of compacting factor. This change requires new amounts of sand and water content for the use of standard concrete up to 35 M Pa and high strength Concrete over 35 M Pa.
- However in the absence of a review on IS 10262-1982, the existing IS 10262 process is described below as a smart move.
- The IS recommendations for mixing design include the composition of the mixing of self-contained (non-ventilated) concrete of medium and high strength concrete.
The integration method consists of the following:
(a) Water content
(b) Percentage of penalty collections corresponding to the maximum aggregate size of the reference value
(c) The amount of cement water, and
(d) Preservation of penalty collection.
- Water content and percentage of fine aggregate and adjust for any differences in performance. Finally the size of the ingredients per unit of concrete volume is calculated in the form of absolute volume. This method works for both underground pozzolana centers.
- The final amount of compounds selected after the experimental mixing, may require minor adjustments. In the case of fly ash cement, the water content can be reduced by about 3 to 5% and a good portion can be reduced by 2 to 4%.
4. American Concrete Institute Method of Mix Design:
- Although the ACI committee published its mixing method in 1944 and almost all concrete dams using a lot of Indian works were designed using the ACI committee method used at the time of mixing. Since then many improvements have been introduced in a practical way. Here is a discussion of the latest method of constructing concrete mixes based on ACI 211-1 of 1991 manual part-time concrete recommendations.
The ACI committee took the following basic ideas:
1. The new collapsed concrete provided and containing a fully proportional measure of the maximum given size will have a fixed water content, regardless of the w / c ratio and the cement content associated between the maximum range of operating parameters.
2. The maximum stiffness of the coarse aggregate per unit of concrete per unit depends on its maximum size and the correct modulus of the fine compound as shown in table 20.39 taking into account the minimum particle size. The effect of angularity is reflected in the empty content. So angular green joints require more mud than circular joints.
3. Regardless of the compaction methods, even when complete compaction has been achieved, a certain percentage of air remains in the concrete and is proportional to the maximum volume.
Mix Design Process:
For compound design, the following data is required to be collected:
(a) Fineness modulus of selected fines.
(b) The unit has the weight of the selected dry fine.
(c) The gravitational force of coarse and fine aggregate in saturated, dry areas.
(d) Absorption of combined rates and penalties.
(e) The gravitational force of cement.
5. Quick methods Mixing:
- Measuring the initial amount of cement water according to purpose means the actual strength will be to combine it with 28 days of cement strength. Feature strength is found to be better related to 28 days of cement strength than in age. This method will therefore require 28 days to determine the size of the cement and the next 28 days of testing mixing the strength of the concrete. The 28-day strength of the cement can be considered as that provided by the curves
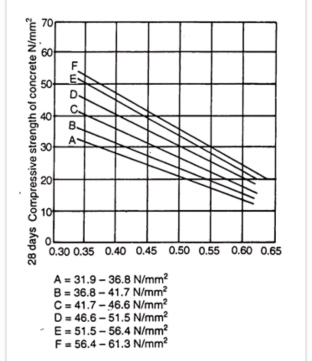
Fig no 17. Graph of compression strength of concrete
- 28 days or 56 days is too long for the contractor to wait for the results of the merger. There is a tendency to use direct mixing without trying experiment mixing. To reduce the time required for the mixing of experiments, the Cement Research Institute of India (CRI) has developed a method called rapid method, in which the compressive strength of cement and cement is obtained using a rapid therapeutic method as discussed in IS 9013-1978. This method reduces the recovery time of experimental compounds from 28 days to only 3 days.
- 28 days of concrete hardening is found to be highly correlated with statistics and rapid strength. Therefore the combination of temptation in line with the target means faster energy than the target means 28 days of energy, with the help of a combination between the two.
- This mixture is obtained independently by the type or characteristics of the cement used i.e. the mixture is not affected by the type of cement used, probably because it affects the fast and normal concrete strength of 28 days equally, so that the result is neutral in comparison. The advantage of each operation is such a combination can be established by the type of building material and assembled to the size to be used.
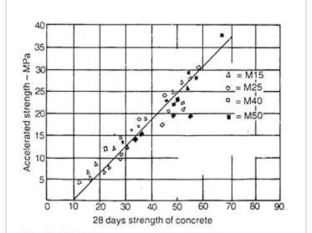
Fig no 18. Strength of concrete vs accelerated strength
- On the other hand, the results of a stable acceleration test in standard cement mortar such as IS 4932-1968 Were not found to be reliable. This problem is overcome by inspecting the cement and quickly and determining its speed.
- The concrete composite concrete or the fastened concrete mixing strength has a w / c value of about 0.35 and the performance is much lower with slump 0 to 10 or compacting factor 0.8 per available cement i.e. (cement in hand).
- The maximum size of the crushed natural compound name should be 10 mm and a good composite should correspond to area II of table 4 of IS-383-1970.
Key takeaways
The following points highlight five methods of concrete construction. The methods are:
1. American Method of Mix Design
2. Graphic Method of Mix Design
3. Mix Design by Indian Standard Method
4. American Concrete Institute Method of Mix Design
5. Quick Method of Mix Design.
The quality of concrete construction on site can be done in three different phases as follows
1. Quality control before integration
2. Quality control during integration
3. Post-construction quality control
STAGE 1 (QUALITY CONTROL BEFORE CONCRETING)
This phase of quality control has two steps.
- Assessment of specification requirements regarding mining, forms, consolidation and embedded repairs etc.
- Control test for concrete ingredients (eg cement, composite and water)
Cement
Cement quality is obtained by performing strength tests of cement cubes. However, with effective control cement:
- It should be tested first and foremost for each source and then tested every once every two months
- It should be protected from moisture
- It should be returned after the last 3 months, if long-term storage is unavoidable
- It should be rejected if a large lump is found in the cement bags.
Aggregate
Concrete composites should be validated at specified values as standard specifications.
The quality of concrete is affected by the various physical and mechanical properties of the composite, namely structure, proportions, durability, gravity and water absorption etc. These composite structures should be tested before using them to produce concrete.
The amount of horror and natural pollution should also be considered.
Sand connections are also an important asset in a number of ways. Provides incorrect results when volume encryption is performed .It increases the amount of water cement which also reduces energy.
With aggregate functional controls:
- They need to be tested once in the beginning to allow the source
- If it is to be checked once or twice daily the moisture content and grant must be made for the combined moisture content.
Water
Water quality should be assessed for needs as defined at the appropriate level. Chemical analysis will be performed to authorize the source. In the event of contamination, it is necessary to store the water for a period of time to allow it to settle. In case of doubt the concrete cubes made of this water are examined. A maximum of 28 days of pressure for at least three cubes or cylinders or a set size, prepared for the proposed water use shall not be less than 90% of the strength between three cubes of the same concrete prepared with distilled water.
STAGE 2 (QUALITY MANAGEMENT DURING CONCRETING)
Careful precaution during concrete is required for all assembly operations such as baking, mixing, transporting, placing, coating and curing. Follow-up safety measures should be taken during concreting operations.
- The concrete mix should be built into the laboratory and the materials to be used on site.
- As far as possible the concrete should be driven by weight. If weight assembly is not possible, volume collection can be allowed with proper monitoring in the presence of the lead engineer.
- During mixing the mixer should be charged in full. Building materials should be fed in the right order. The mixer speed should be from 15 to 20 fluctuations per minute. The mixing time should not be less than 2 minutes in any case. Separation should be avoided when loading concrete into the mixture.
- The performance of concrete is an important material of concrete while concrete is in its new state. Therefore testing of slump or compaction factor should be performed to check the performance of the concrete. About three tests should be performed on every 25 m3 of concrete.
- Care should be taken so that no separation occurs during the concrete transfer.
- Concrete should not be lowered from a height of not more than 1 m. If the height of the drop is more than 1 m chutes should be used.
- To avoid re-release the concrete should be placed in its final position as much as possible.
- Vibrators should be used to connect the concrete. Internal vibrator installation space should not exceed 0.6 m. It should be lightly painted so that no holes are left in the concrete. Vibrator frequency should not be less than 7000 cycles / minutes.
- The treatment should be done over a period of time so that the concrete develops the required strength. Concrete should be covered with hessian as soon as it becomes hard.
- The form function must be aligned with the final form of the form. It should be checked before the start of integration. The inside of the forms should be cleaned and oiled. Forms must be removed after the deadline.
- Concrete should be protected from hot and cold weather at an early age. Concreting should not be performed at temperatures below 4.50C and above 400 In very hot weather water and aggregates should be cooled. Approved quality retards can be used.
- In very cold weather water and aggregates should be heated. Approved quality Accelerators can also be used.
STAGE 3 (QUALITY CONTROL AFTER CONSTRUCTION)
- Once the concrete has been laid and assembled, a pressure test is performed on the tubes made of this concrete. With standard concrete, cubes are made of concrete made in the workplace.
- Reinforced concrete should be considered to be true in size, shape and size as specified in each design. The appearance of the concrete surface should also be checked. Sizes are available in various sizes. Reinforcement should have adequate concrete cover and if reinforcement is visible on the part of the structure, the part should be rejected or appropriate action taken.
Concrete strength is usually obtained by cube or cylinder samples tested within 28 days. In the event that the power received is less than the specified minimum, one or more of the following steps may be taken.
- Load testing and deviation of the deviation and / or difficulty (structural quality can also be obtained by calculating back concrete strength)
- Cutting cores from structures and testing them for strength
- Non-destructive tests such as the Schmidt rebound hammer or ultrasonic pulse velocity test. These tests give a very complex view and are used to find structural similarities.
- Chemical analysis of hard concrete.
Key takeaways
The quality of concrete construction on site can be done in three different phases as follows
1. Quality control before integration
2. Quality control during integration
3. Post-construction quality control
The behavior of the concrete under high temperature values could be affected with several factors. The temperature rate, aggregate type, and stability of the mixture are among the most important factors to be considered under high temperature condition. It is noted that the abrupt temperature rise can cause thermal shock, spalling, cracking, and aggregate expansion leading to high distress within the concrete.
The durability of the concrete against freeze-thaw cycles is previously investigated as a major factor indicating the ability for resistance against weathering actions.
Cold and hot weather concreting
Introduction
- Concrete and other structures are constructed in many countries around the world and in some places the climate is symbolized by the long spells of hot or cold weather. Concrete companies that are ready to integrate and build in these regions are able to produce high quality concrete despite these weather problems. In many regions with unfavorable weather conditions there are set conclusions and concrete production guidelines that provide details of the methods that can be used to combat adverse conditions.
- In the cooler parts of the world, cool, humid climates are common. In these areas, although cold or cold temperatures are not uncommon, it is often surprising when they arrive and it may be too late to apply even safety measures to minimize their undesirable effects,
- Physical effects in both hot and cold conditions should not be overlooked. Workers and managers will not be expected to produce good quality concrete if exposed to conditions for a long time without proper protection
- When the process of serving the container is done on its own it is not a matter of deciding whether to pour concrete. Air temperature, humidity, and wind speed, higher temperatures where you put concrete, water and dry concrete in the bag all play a big role and should be considered. The air, air and moisture are much better than you can handle but you can also influence it. It is important to remember that the temperature of the mixed material is as important as the temperature of the air.
- The strength and durability of concrete are at odds with the climate in which the composite process is performed. Therefore, construction workers will need to take extra care or take action when it comes to worship. In fact, some parts of the world remain hot all year long. These are situations where paying attention to a few simple but much-needed points in hot weather can definitely help to complete any display without compromising its quality. Sunlight leads to hot weather which forces us to use special methods while barking known as hot weather concreting,
Hot Weather concreting
Definitions
- The definition of a tropical climate may vary from country to country. According to the Indian climate, Indian codes determine 40 ° C as the temperature range for hot climates. That is to say, any combination made at temperatures above 40 ° C can be considered as a hot climate that allows for certain measures to be adopted.
- Obviously, this is not the case in most other parts of the world because of the climate. For example, according to ACI 305, any combination of high temperatures, high air pressure, low humidity and sunlight (sunlight) is a preconceived notion for designing a connection such as hot weather. Some theories say that any heat above a comfortable room temperature, and 25 ° C however, begins to make the concrete uncomfortable 1.e, the concrete begins to react differently which is why it requires special care due to hot weather, if strong quality to be maintained.
Hydration Process
- Therefore, it is very important to deal with how the temperature of the tropical climate differs concreting normal temperature. Concrete sets also gain strength due to the hydration of the cement inside them. The elasticity of the cement occurs quickly when it is hot. Cement installation also releases heat. Therefore, the faster the hydration of the cement the faster the heat generation. This creates the heat of the concrete, further speeds up the cementing or set-up process, Cement quickening does not allow concrete enough time to get enough strength. While the initial energy does not suffer, long-term energy (28-day energy) is negatively affected. This is a major reason why hot climates require special care. Otherwise, you will be playing with concrete designed strength.
- Water demand
- The water demand for concrete mix is high in hot weather due to rapid evaporation. Unless appropriate measures are taken, additional water will have to be added to the concrete mix to maintain the performance of the mixture. This will increase the amount of water cement which will also reduce the strength of the concrete. If more cement is added to keep the w / c ratio constant the cost will increase as cement is the most expensive ingredient concrete mix,
- Rapid drying of freshly poured concrete areas occurs when it is hot due to rapid evaporation or water loss in the mixture. If proper care is not taken, cracks known as plastic shrinkage cracks will appear, which are difficult to repair over time. The exposed area tends to shrink rapidly due to rapid moisture loss while mixing will still develop sufficient strength to withstand these shrinking pressures leading to cracking. In hot weather, concrete bed, forms, metal reinforcement, connecting or assembling equipment etc. It is also hot transferring heat to a mixture that adds to the problem.
The effects of Hot weather on concrete
- High temperatures can affect the concrete at all stages of production and laying process and many effects can have long-term or hardening effects. Some of the problems caused by high temperatures are listed in Table 1. They are the result of high temperatures that increase the rate of hydration reaction and the movement of moisture inside and outside the concrete.
- The combination of high temperature, low humidity and high air velocity adversely affects desirable concrete structures e.g. Strength, inequality, durability, weather resistance, wear and tear
- Setting time. As the temperature of the concrete increases, the laying time, and thus the laying time, the mixing and finishing of the concrete is reduced
- Workability and slump - High temperatures reduce the performance (or fall) of concrete very quickly over time. Adding more water to improve the performance of the mixture reduces energy and Increases penetration, and ultimately affects the durability of the mixture.
- Durability - Many forms of degradation depend on the transfer of fluid or respiration through a concrete structure. Acquiring a ‘non-permissible’ concrete is one of the main goals when trying to gain durability. The main ways to do this is to produce concrete with low water / cement concrete. As noted above, high temperatures affect the initial performance and the level at which they lose performance and may be tempted to add more water to the mixture or site. This will lead directly to concrete at high risk of cold, climate change, sulphate attacks and the entry of carbon dioxide and chloride solution leading to increased corrosion.
- Compressive strength - High water demand and high concrete temperatures can lead to a 28 day power reduction. If too much water is added to the concrete mix at high temperatures to maintain or restore function, the water level of the cement will increase, resulting in a loss of strength and durability. This can also increase the shrinkage of reinforced concrete. Where water is not heard, reduced set time and performance can increase insufficient mixing (actually a major impact on energy), the formation of cold joints and improper elimination.
- Concrete temperature - Warmer climates can increase the temperature of concrete caused by hydration heat. In large segments the hot gradients through the element can create thermal cracks. Laboratory tests show that very high temperatures have a significant impact on the strength of the hard concrete. Although increased concrete heat can lead to an initial increase in energy gain, in the long run, low-temperature-cooled concrete will reach higher strength.
- Poor surface appearance - With increased evaporation, the concrete surface will dry out. In the case of an infestation this can lead to premature depletion, trapping the amount of water that drips inside the mixture. The coated layer (from the finish) can cause blood clots to trickle under the surface, leading to the formation of the upper layer and subsequent eruption. Also, color variations on the face can result from different levels of hydration and cooling effects.
- Plastic shrinkage cracking - Hot weather conditions accelerate the loss of moisture on the face. If the evaporation rate is higher than the rate of bleeding (the rate at which the water rises higher) drying of the soil will occur which has led to a reduction in concrete. When the reducing pressure exceeds the capacity of the concrete, cracks will occur. The chances of cracking the plastic are reduced so it is great whenever hot weather raises steam or concrete and lowers the bleeding rate. The cracking of the shrinkage plastic can be quite deep, as the plastic concrete has little resistance to the shrinking pressure, and the cracks continue to grow and spread until the shrinkage pressures are released. (Be aware that thin plastic cracks do not usually extend to the free edges, as uncontrollable concrete cuts may occur in these areas.)
- Thermal cracking - Concrete is at risk of thermal cracking when applied for the first time, and hydration heat raises the internal temperature of the concrete. Rapid changes in the external temperature of the exterior concrete, such as where concrete slabs are laid, walls or sidewalks on a hot day followed by a cold night, lead to hot gradients between the warm / hot surface and the cold outside. The warm interior offers a cool outdoor space, which wants to make a deal. Depending on the temperature variation, there may be a concrete crash. Larger or thicker concrete objects are at greater risk because of the protective effect the concrete gives them inside the object.
Precautions in hot weather conditions
- Problems often arise when local workers are unaware of the impact of changing weather and / or climatic conditions during laying and / or finishing concrete. Improved responses to unexpected changes are not recommended because the damage that can be caused by the uncontrolled effects of tropical climates may not be completely eliminated. The first option to consider in hot weather is to postpone the placement of the concrete or not
- Make sure site staff are aware of the effects of the weather. Improved responses to unexpected changes are not recommended. The first option to consider in hot, unfavorable weather conditions is to postpone the placement of the concrete or not. It is often better to wait than to risk costly repairs (or replacements) for defective work.
- Concrete Production. The role of concrete suppliers is to help put concrete in hot climates. Shade stocks, spray aggregates before evaporation time, or cool down otherwise. Paint mixing barrels and keep them white to reduce heat loss from the sun. Use ice as part of the mixed water or cool the concrete with liquid nitrogen.
- Delivery and Delivery- Delivery delays can delay good mixing practices. The concrete supplier must plan and maintain a good non-delaying plan to deliver concrete to the required area on site
- Reduce travel time and avoid unnecessary delays.
- Avoid prolonged mixing. Mixed transport trucks should be released as soon as possible after the addition of water to that mixture.
- For large projects, consider baking and mixing using a workplace plant. •
- Water should not be installed on pre-assembled concrete in the workplace unless it is part of the amount required at the beginning of the set water limit and specified descent.
Precautions for concreting in cold weather
- Temperature control of concrete ingredients - The most effective way to maintain the temperature of concrete at the top is to control the temperature of its ingredients. The contribution of each ingredient in concrete heating is a function of heat, specific heat and the amount used for this ingredient. The water mixed with the mix has a very noticeable effect on the temperature of the concrete. Therefore, in cold weather, all available means will be used to care for these items at the highest possible temperature.
0. Many ways to reduce the effects of low temperatures include raising the level at which the concrete gains strength under these conditions in the first critical phase after laying.
2. Cement Quantity - Increasing the amount of cement (meaning using high-strength concrete) can increase the energy gain. Note that there is little or no impact during setup.
3. Admixture - The rapid addition of compounds (non-chloride) to concrete reduces the setting time and speeds up the energy gain rate by increasing the level at which cement enters
4. Hot Water - Applying hot water to the mixture will increase the temperature of the concrete, which in turn accelerates the rate at which cement enters. The temperature of the water mix should not exceed 70 ° C and the mixing should ensure the consistency of the concrete delivered to the site
5. Air entrainment - you may be able to prevent the effects of sudden cold by applying a combination of ventilation to the concrete. These compounds create minute air vents where the pore water can move as it expands during cold weather
6. On site precautions - It is advisable to take steps to prevent concrete damage by unpredictable and unexpected snow whenever the air temperature drops below 5C.
7. Cold Protection (Including cold / frozen area, winds and cold) - in some cases, the provision of a heated enclosure (simple frames covered with tarpaulin and the use of hot air) to completely seal the concrete object may be required. Note that care must be taken to prevent concrete drying when using this method.
Key takeaways
1. Concrete and other structures are constructed in many countries around the world and in some places the climate is symbolized by the long spells of hot or cold weather. Concrete companies that are ready to integrate and build in these regions are able to produce high quality concrete despite these weather problems. In many regions with unfavorable weather conditions there are set conclusions and concrete production guidelines that provide details of the methods that can be used to combat adverse conditions.
Under water concreting
There are 4 techniques of underwater concreting:
- Tremie pipe Method
- Bucket Method
- Grouting Method
- Bags stacking Methods
1)Tremie pipe Method:
- The tremie stable state of affairs method makes use of a vertical or nearly vertical pipe, thru which concrete is about with the aid of using gravity feed below water degree.
- The decrease give up of the pipe is stored soaking wet in crisp cement with the aim that stable ascending from the bottom dislodges the water, on this manner limiting washing out of the bond substance of the brand new concrete to the exposed top floor.
- The top give up of the tremie pipe is stored over the water degree amid the pour and is given a cone formed field for cluster stacking, or cement is probably siphoned into the best factor of the tremie pipe.
- Concrete should be poured at a fee which abstains from putting with inside the tremie.
2) Bucket Method:
- In this method the stable is saved submerged with the aid of using a base commencing field.
- The cans for the maximum component are outfitted with base curler or drop base doorways as regarded in Fig. The door opens uninhibitedly outward whilst stumbled.
- The pail is crammed absolutely with cement and its first-class secured with a canvas material or gunny sack and taken progressively right all the way down to avoid backwash or unsettling have an impact on to concrete because the can is added down into the water.
- The can is added down with the aid of using a crane upto the bottom floor of the stable and in a while opened both with the aid of using an affordable recreation plan from the first-class or with the aid of using a jumper.
- It is fundamental that the stable be launched straightforwardly superficially on which it's far to be saved.
Advantages:
- This method is located to have the accompanying preferences:
- Relatively lean blends is probably applied given ok versatility is held.
- No shape paintings is essential on this method.
Disadvantages:
- This method is slight and laborious as the precise situating of the packs installation should be cultivated with the aid of using the jumpers.
- Voids in adjacent sacks are difficult to fill.
- There is small preserving apart from created with the aid of using the mechanical interlock among packs.
- The method further is exorbitant as greater paintings is related to filling and tying them.
3) Grouting Method:
- These pens are laid vertically over the whole area to be cemented with the give up aim that the separation among the focuses of the pens and moreover to the essences of the stable thought now no longer surpass one meter.
- The degree of the stone over all thought to nor be beneath 50 mm in extra of 2 hundred mm.
- This overall have to be wetted earlier than storing it outdoor the metallic confines over the whole location and tallness to be cemented.
- While saving the overall, care have to be taken that no pen is uprooted from its position.
- Subsequent to storing the overall, the concrete sand grout of 1:2 quantity and water/bond share as a minimum 0.6 and now no longer greater than 0.9 is installation in a mechanical blender.
- The finest length of sand is probably five mm and the concrete sand quantity can also additionally shift from 1:1.5 to 1:4contingent at the first-rate conditions and importance of the paintings.
- In the wake of grouting the whole territory for a stature of round 60 cm s, a comparable pastime is rehashed for the subsequent layer of 60 cm and the method is rehashed until the grouting is completed up to an appropriate tallness.
- The grout to be dispatched down to be ok to fill each one of the voids.
- The extent of voids is probably typical as 55% of the extent to be cemented or observed tentatively.
- Beyond what many could recall feasible cement thought now no longer be troubled whilst it's far stored, this can restrict the association of laitence.
4) Bags stacking Methods:
- The packs are tied in order that they may be perfect right away in a profile of the floor on which they're put.
- The legitimately crammed sacks are added down into the water and set carefully in header and stretcher guides as in block workmanship improvement with the help of jumpers so the whole mass is interlocked.
Advantages:
- This method is located to have the accompanying factors of interest:
Nearly lean blends is probably applied given ok versatility is held.
- No shape paintings is vital on this method.
Disadvantages:
- This method is slight and laborious as the proper situating of the packs installation should be cultivated with the aid of using the jumpers.
Voids in contiguous packs are difficult to fill.
- There is small preserving apart from created with the aid of using the mechanical interlock among packs.
Key takeaways
1. The top give up of the tremie pipe is stored over the water degree amid the pour and is given a cone formed field for cluster stacking, or cement is probably siphoned into the best factor of the tremie pipe.
Concrete gains very little strength at low temperatures. Accordingly, freshly placed concrete must be protected against freezing until the degree of saturation of the concrete has been sufficiently reduced by cement hydration. The time at which this reduction is accomplished corresponds roughly to the time required for the concrete to attain a compressive strength of 500 psi. Concrete to be exposed to deicers should attain a strength of 4,000 psi prior to repeated cycles of freezing and thawing.
Sulphate
- Cement is composed of two minerals: tri-calcium silicate (C3S), and di-calcium silicate (C2S).
- In addition to hydration, the main reaction products are calcium silicate gel (C-SH) and calcium hydroxide Ca (OH) 2, labeled as CH in chemistry notation.
- Moisture is required in this reaction which can cause serious damage to the construction of both the walls and the walls of buildings in buildings.
- Sulphate attacks occur on the lower slabs. This problem usually affects buildings from the 1950s to the 1960s but can also affect previous buildings where the concrete floor slab is installed.
- It occurs when the filler material under the slide contains sulphates and this is considered to be a solution with soil moisture entering the concrete that forms the slab on the floor.
- Attacks can occur from MgSO4 salts, NaSO4 salts, and other salts containing SO3-ions. The interaction of Ca2 + ions with SO4 present in the solution will produce CaSO4 or gypsum.
- The effect of gypsum on C-S-H gel, which is the main component of reinforced cement, is an irreversible topic.
- Some substances present in cement, such as tri-calcium aluminate, also interact with sulphate ions. This reaction is well established in the literature.
Key takeaways
In addition to hydration, the main reaction products are calcium silicate gel (C-SH) and calcium hydroxide Ca (OH) 2, labelled as CH in chemistry notation.
Moisture is required in this reaction which can cause serious damage to the construction of both the walls and the walls of buildings in buildings.
Acid Attack
- Acid attack is the dissolution and leaching of acid-prone elements, particularly calcium hydroxide, from the cement paste of hardened concrete.
- This movement outcomes in an boom in capillary porosity, lack of cohesiveness and subsequently lack of power.
- In said instances, acid assault can be observed with the aid of using crack formation and subsequently disintegration, in particular whilst the shape is subjected at one facet to water pressure.
- Unlike sulphate assault (see beneath), the goods fashioned from acid assault aren't expansive, and leaching will handily arise in systems which are tremendously permeable.
- In excessive overall performance concrete structures containing cement pastes with a low content material of calcium hydroxide, acid assault is relative gradual and can contain handiest the finely divided calcium hydroxide crystals included withinside the interstices of the calcium silicate hydrate, C-S-H.
- The micrographs received from PFM analysis, supplemented with SEM–EDS studies, monitor that handiest the top, floor part of the concrete has been attacked with the aid of using acidic answer.
- The relaxation of the concrete suggests no shape of degradation.
- In the attacked zone, there's clean proof of leaching of the cement paste matrix, main to accelerated capillary porosity and lack of brotherly love of the matrix.
- Locally, there's lack of bonding of the cement paste to aggregate, however at the whole, those elements have now no longer adversely affected the microstructure and nice of the concrete.
- In this instance, long-time period sturdiness of the concrete isn't always probably to be compromised.
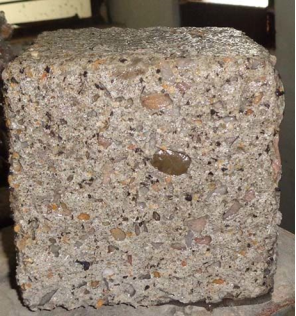
Fig no 19. Acid Attack on Concrete block
- Acid assault of concrete takes 3 forms. First, hydration merchandise reacts with the acid to shape dissolved ions, main to lack of strong material—acidolysis.
- Second, withinside the case of a few acids, insoluble salts shape, a number of which precipitates to purpose growth and cracking.
- Finally, a few acids supply complexes with calcium, aluminium, iron and silicate ions which produce an awful lot better concentrations of those ions in answer than could in any other case be the case, once more main to dissolution.
- This can probably arise at pH situations beneath which cement could usually be tremendously stable (complexolysis).
- Depending at the acid present, extra than this sort of deterioration mechanisms can be powerful.
- Where acidolysis is the main mechanism, an acid answer penetrating the pores of concrete will begin to purpose a number of the elements to dissolve.
- Calcium is generally the primary cation to be dissolved, considering that portlandite will become soluble beneath tremendously excessive pH values.
- AFm and AFt stages commonly dissolve at barely decrease pH values, even though strong aluminium and iron hydroxides are precipitated, which persist till the answer is tremendously acidic.
- Exposure to acidic answer additionally reasons lack of calcium—decalcification—of C-S-H gel, leaving tremendously vulnerable silica gel behind.
- The importance of calcium on this shape of degradation approach that adjusting the composition of the cement matrix of concrete to attain a decrease calcium content material will probably impart extra resistance.
- Thus, pozzolanic substances can be powerful in improving resistance to this form of acid assault, considering that their aggregate with PC will produce such an adjustment.
- However, decreased quotes of mass shipping and more desirable power done thru the usage of pozzolanic substances also are probably to be motives for progressed resistance.
Key takeaways
In excessive overall performance concrete structures containing cement pastes with a low content material of calcium hydroxide, acid assault is relative gradual and can contain handiest the finely divided calcium hydroxide crystals included withinside the interstices of the calcium silicate hydrates, C-S-H.
- You may also note efflorescence each interior and outside, and it may range in frequency and depth in the course of the us of a because of moisture and temperature. Three situations want to exist for efflorescence to arise: There are water-soluble salts in or at the fabric.
- Moisture is gift to make the salt turn out to be a soluble solution. As salts pass to the fabric’s surface, the moisture evaporates. This makes the salts crystallize, which leads to efflorescence.
- Water, rain and snow are the number one reassets of moisture and might effect the diploma of efflorescence.
- Condensation, groundwater wicking and indoors sports additionally may also have an effect on the diploma of moisture generation. Efflorescence can occur at exceptional times. Essentially, it may both be a hassle from the start of a constructing’s creation, or the method can arise over time.
- Primary efflorescence normally takes place inside the first seventy two hours of the constructing fabric being used, performing because of extra water being gift while the fabric became manufactured.
- Secondary efflorescence is a end result of out of doors moisture pulling the salt out of the constructing fabric. In many instances, efflorescence may also arise at some stage in domestic creation. If masonry devices get unnoticed in a single day at some stage in creation, they’ll probably soak up moisture from damp soil and rain. It is critical for masonry devices to be included and left in pallets to decrease the danger of efflorescence in the course of a creation project. Efflorescence also can arise while constructing substances are established incorrectly or troubles arise with the installation.
- Some not unusualplace examples of this include: Using through-wall flashings incorrectly. Failing to offer enough air flow for masonry. Installing masonry with out an green barrier for moisture.
- Joint substances failing after installation. Materials being saved improperly or left at the ground. Efflorescence is mostly a seasonal hassle, and humidity will effect whether or not soluble salts appear. It normally escalates in winter, due to the fact that rain, snow, sleet and different inclement climate situations may also arise. However, efflorescence can nevertheless arise in spring, fall and summer.
Fire resistance of concrete is the ability of concrete to withstand fire or to give protection against fire. This involves the ability of concrete structural element to continue perform a specific structural function or confine fire or both.
The duration of time that an element such as beam, column, wall, floor, or roof can endure the fire, which is defined in ASTM E 119, is termed fire rating.
Fire resistance is controlled by both the physical and thermal properties of the structural element. Factors governing the structural performance include stress level in the concrete and the steel, concrete cover, tendency of aggregate and free moisture to cause spalling, and lateral restraint conditions.
However, parameters that control the thermal performance involves type of aggregate, free moisture in the concrete (both absorbed and capillary), and volume of concrete per square meter of exposed area.
Inspection and testing of ready mix concrete is crucial to ensure that all specified conditions meet the acceptable criteria. Ready mix concrete, which produced in batching plant and transported to construction site by truck mounted mixers, are commonly inspected and tested in accordance with applicable standards such as ASTM international.
Batching Plant Inspection
- Firstly, examine and specify whether facilities, scales, and truck mixers meet the specified project requirements or not.
- Inspect storage areas of all materials like cement, aggregate, and admixtures to ensure their cleanness, free of contamination, and properly protect materials from effect of freezing.
- Inspect and verify that coarse and fine aggregate gradation tests are conducted in accordance applicable standards like ASTM C 136, and result reach project requirements.
Onsite Inspection of Ready Mix Concrete
- Every delivery ticket shall be inspected to ensure that a mixture with the correct designation is delivered.
- Inspect delivered concrete; it should be uniform and adequately mixed prior to discharge at the construction site.
- Inspect and monitor water, admixture, and fiber reinforcement addition onsite to make sure that the process performed properly.
- Monitor and examine concrete delivery and placement time to find out whether it completed within the time constraints of the project specifications.
Testing Ready Mix Concrete
1. Onsite Tests
There are certain types of tests that shall be conducted on ready mix concrete upon reaching construction sites. Table 1 provide lists of tests that need to be performed on ready mix concrete on project site. Table 1 Tests conducted on ready mix concrete upon reaching construction site
Type of tests | ASTM international for testing procedures | Test frequencies | Purpose of the test |
Slump | ASTM C 143/C 143M | First truck load, whenever the consistency of the concrete appears to vary. | Measure fresh concrete consistency, check its workability, and use as an indicator of poor mixed batch |
Air content | ASTM C 173, ASTM C 231 | Performed on all samples taken to measure concrete strength | To check air entrained concrete |
Temperature | ASTM C 1064 | At the time of sampling for each strength test | To make sure that concrete comply with certain specifications that define a certain allowable temperature range |
Density | ASTM C 138, ASTM C 567 | Whenever required by project specifications | To estimate concrete density |
Evaluation of crack
When inspecting a slab or conducting a crack, always measure the width of the crack and determine whether the metal reinforcement passes through it and whether the crack is active or asleep. This information, especially the details of the reinforcement and cracking function, is very important when choosing the best repair option.
Crack width
- The extent of the crack is usually measured using a crack comparison card. Measuring the width of the crack helps to separate the stiffness of the cracks and to evaluate the performance of the joint joints across the fracture of the direct direction of the fracture and the transmission of the load. Also, many repair options depend on the width of the crack.
- Unless the steel reinforcement passes through a crack, the alignment of the vertical tube and the transmission of the broken load depends on the joint bonding. If the diameter of the fracture is less than 0.035 inches, the composite particles that come from the other side of the fracture to the other side will normally provide adequate load transfer and maintain vertical alignment throughout the split.
- For larger screens, maintaining a straight slide alignment can be a challenge. The success of the remediation approach will depend on the slide loading and the quality of the base material and the ground cover.
Steel Reinforcement
- Although steel reinforcement does not prevent cracking, it limits the width of the crack so that the joint joints are maintained. Strengthening itself also provides load transfer and helps maintain vertical alignment in the cracks. When the reinforcement passes through a split, both the width split and the future width increase are controlled. The new cracks of the non-reinforced concrete will continue to grow and the diameter can double before the increase in crack-width.
- With the cracks caused by the drying shrink, the cracks will stabilize at the end. Splits due to other causes, however, such as soil erosion or height, may not be stable and may continue to increase unless a significant amount of reinforcement passes through space. Determining the amount of reinforcement that goes beyond cracking is important in predicting the performance of future cracks and choosing the best repair option.
Dormant and active crack
- Cracks that fall through steel reinforcement are generally stable and are often considered sleepy. Of course, the stability of the cracks depends on the source and the degree of reinforcement of the cracks. The lying cracks have a fixed width and can be repaired with solid or flexible materials.
- Functional cracks should only be repaired using a flexible object that can accommodate future cracked movements. Generally, the active cracks in the slabs actually belong to the active members and should be treated in the same way as the joints. After all, random or non-joining cracks in flatwork are self-assembling joints.
Key takeaways
- Evaluation of crack is
- Crack width
- Steel Reinforcement
- Dormant and active crack
1. Plastic shrinkage concrete cracks:
- When concrete remains in its plastic state (earlier than hardening), it's miles complete of water. When that water finally leaves the slab, it leaves at the back of big voids among the stable particles.
- These empty areas make the concrete weaker and greater at risk of cracking. This form of cracking takes place regularly and is stated as “plastic shrinkage cracking”.
- While plastic shrinkage cracks can manifest everywhere in a slab or wall, they nearly constantly manifest at reentrant corners (corners that factor into the slab) or with round gadgets withinside the center of a slab (pipes, plumbing fixtures, drains, and manholes).
- Since concrete cannot decrease round a corner, strain will purpose the concrete to crack from the factor of that corner. Plastic shrinkage cracks are usually very slender in width and slightly visible. While almost invisible, it's miles vital to bear in mind that plastic shrinkage cracks don’t simply exist at the surface, they increase at some point of the whole thickness of the slab.
- An excessively moist blend is a contributing element to shrinkage in concrete. While water is a critical element in each concrete blend, there's this kind of factor as an excessive amount of water.
- When the combination consists of an excessive amount of water, the slab will reduce greater than if the suitable quantity of water turned into used. Hot climate is some other massive cause for plastic shrinkage cracks. Control joints may be included into the slab to save you shrinkage cracking. The joints will open up because the concrete slab receives smaller.
2. Expansion concrete cracks:
- Enlargement cracks Just like a balloon, warmth reasons concrete to expand. When concrete expands, it pushes towards whatever in its way (a brick wall or adjoining slab for example).
- When neither has the capacity to flex, the increasing pressure may be sufficient to motive concrete to crack. Expansion joints are used as a factor of separation (or isolation), among different static surfaces.
- Typically product of a compressible fabric like asphalt, rubber, or lumber, enlargement joints should act as surprise absorbers to alleviate the strain that enlargement places on concrete and save you cracking.
3. Heaving concrete cracks heaving cracks:
- When the floor freezes, it is able to on occasion raise many inches earlier than thawing and settling lower back down.
- This floor motion delivered on through the freezing and thawing cycle is a big element contributing to concrete cracking. If the slab isn't unfastened to transport with the floor, the slab will crack.
- Large tree roots will have the identical impact on a slab. If a tree is positioned too near a slab, the developing roots can raise and crack the concrete surface. Always don't forget this while laying a slab.
- Settling concrete cracks settling cracks On the alternative hand, floor settling beneath a concrete slab also can reason cracking. Settling cracks usually arise in conditions wherein a void is created withinside the floor beneath the concrete surface.
- Think approximately whilst a huge tree is eliminated from close by and the roots start to decompose or whilst a software business enterprise digs a trench for his or her lines, pipes, etc. and don’t compact the soil once they replenish it–those are examples of times wherein settling cracks are possibly to happen.
The principal causes of cracks in a building are as follows:
- Permeability of concrete
- Thermal movement
- Creep movement
- Corrosion of reinforcement
- Moisture movement
- Poor construction practices
- Improper structural design and specifications
- Poor maintenance
- Movement due to chemical reactions
- Other factors
Remedial measures
- Use minimum possible quantity of water.
- Employ large coarse aggregate.
- Provide compression reinforcement if possible
- Avoid formwork removal at early ages.
- Cure concrete properly.
- Assign proper cross section for the concrete element.
- NDT stands for Non-Destructive Testing. It refers to an array of inspection strategies that permit inspectors to assess and acquire statistics approximately a material, system, or factor without completely changing it. NDT can also be called: NDE (non-unfavourable exam or evaluation) NDI (non-unfavourable inspection) In the subject, NDT is frequently used as an umbrella time period to consult non-unfavourable inspection strategies, inspection tools, or maybe the complete subject of non-unfavourable inspections.
- For business applications, the aim of NDT is to make certain that vital infrastructure is well maintained if you want to keep away from catastrophic accidents. While NDT techniques are generally related to business use cases, like examining vulnerable factors in a boiler used at an oil refinery, makes use of in medicinal drug are really a number of the maximum common. For example, an waiting for mom getting an ultrasound to test at the fitness of her infant could be taken into consideration an NDT use case, as could getting an X-ray or MRI to analyze extra approximately an injury.
- But it’s critical to notice that NDT does now no longer always require the usage of unique equipment, or any equipment at all. For instance, while inspectors in business settings overview the outdoor of a stress vessel with their bare eye, that could fall beneath the NDT designation, when you consider that they're accumulating facts at the popularity of the boiler without negative it.
- On the alternative hand, the use of an advanced device like an ultrasonic sensor to search for defects in a positive cloth or asset could additionally be known as NDT. Regardless of the particular use case, the underlying commonality amongst a lot of these examples is the gathering of facts in a non-intrusive manner.
- The special styles of non-damaging trying out are regularly complementary. As a result, we will take advantage of the benefits of mixed strategies. Non-damaging trying out (NDT) is a mixture of diverse inspection strategies used for my part or together to assess the integrity and residences of a material, thing or device without inflicting harm to it.
- In different words, the component that calls for the usage of one or greater of these strategies can nevertheless be used as soon as the inspection technique is over. NDT is consequently regularly used for the detection, characterization and sizing of inherent discontinuities, in addition to the ones related to harm mechanisms. NDT is regulated with the aid of using codes and requirements in keeping with the kind of industry, united states of America and different criteria. Society for Mechanical Engineers (ASME), ASTM International, COFREND, CSA, Canadian General Standards Board (CGSB), American Society for Non-destructive Testing (ASNT), etc. are well-recognize examples.
- Destructive trying out (regularly abbreviated as DT) is a take a look at technique performed to discover the precise factor of failure of substances, components, or machines.
- During the process, the examined object undergoes strain that in the end deforms or destroys the material. Naturally, examined components and substances can't be reused in normal operation after present process unfavourable trying out procedures. Destructive trying out is typically performed earlier than a aspect enters mass production. OEMs want to realize the boundaries in their merchandise for you to supply right upkeep and working guidelines for his or her machines.
Tests on cement
1. FINENESS
Objective
- The purity of the cement alone has a significant impact on the hydration rate and therefore on the energy gain rate and the degree of heat dissipation.
- Finer cement provides a large area of hydration Specific Surface versus Compressive Strength of Cement and as a result accelerates energy.
- The beauty of digestion has increased over the years. But now it is almost settled. Different cement is subject to different finishes.
- A particle size of less than 3 microns has been found to have a significant effect on energy in one day while a fraction of 3-25 micron has a significant effect on energy for 28 days.
- An increase in the thin layer is also found to increase the thickness of the concrete.
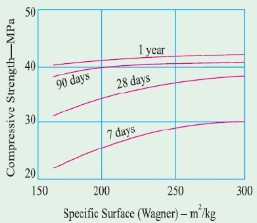
Fig no 20. Specific Surface versus Compressive Strength of Cement
Procedure
- Stir the sample of cement to be tested by stirring for 2 minutes in a preheated pot to distribute the agglomerates. Wait 2 min. Mix the resulting flour gently using a clean dry stick to spread the fine mixture all over the cement.
- Place the tray under a strainer, weigh about 10 g of cement in the nearest 0.01 g and place it in a strainer, being careful to avoid loss. Disperse any agglomerates. Place the lid on top of the filter.
- Cover the sieve with a circular motion, planetary motion and movement until it no longer exceeds the fine material in it. Remove and measure the rest. Specify its magnitude as a percentage, R1, of the pre-set filter per 0.1 percent nearby. Gently move all the fine material from the filter into the tray.
- Repeat the whole process using a new sample of 10 g to get R2. Then calculate the remnants of cement R as the value of R1, and R2, as a percentage, expressed in the percentage close to 0.1.
- When the results vary by more than 1 percent altogether, make a third reduction and calculate the meaning of the three values.
- Check the sieve after 100 filters per section 4.4.2 of IS: 4031 (Part 1)
Apparatus used
![]() | ![]() |
Fig no 21. Cement | Fig no 22. Balance |
![]() | ![]() |
Fig no 23. Seive | Fig no 24. Nylon Bristol Brush |
2. STANDARD CONSISTENCY
To determine the quantity of water required to produce a cement paste of standard consistency as per IS: 4031 (Part 4) – 1988
Apparatus
1) Vicat apparatus conforming to IS: 5513 – 1976
2) Balance, whose permissible variation at a load of 1000g should be +1.0g
3) Gauging trowel conforming to IS: 10086 – 1982
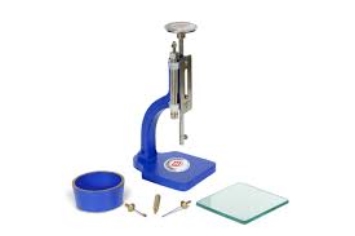
Fig no 25. Vicat apparatus
Procedure
- Measure about 400g cement and mix it with the required amount of water. Estimation time should be between 3 to 5 minutes.
- Fill the Vicat mold with glue and measure it with a trowel.
- Gently lower the plunger until it touches the cement.
- Release the plunger to allow it to sink into the paste.
- Note the reading in the scale.
- Repeat the above process and take new samples of cement with different water sizes until the gauge is 5 to 7mm.
3. SETTING TIME
Objective
- For simplicity, the initial set time is considered to have elapsed between the time when water can be added to the cement, at which point the paste begins to lose plastic.
- The last time is the last time the water is put in the cement, and the time when the glue is completely lost to the plastic and gained enough strength to withstand a certain direct pressure.
- The room temperature, dry material and water should be kept at 27 ± 2 ° C. The relative humidity associated with the laboratory will be 65 ± 5 percent.
Procedure
Preparation of test block
- Prepare a clean paste by measuring 0.85 times the water needed to give the glue a normal consistency. Portable or refined water will be used to prepare the paste. Attachments will be measured in accordance with the conditions set out in IS: 4031 (Part 4) -888.
- Start a stopwatch at a time when water can be added to the cement. Fill the Vicat mould with cement paint as limited as above, the mould stays on an empty plate. Fill the mould completely and spread the surface of the paste to make it to the top of the mould. The cement block is thus suspended from the test mould.
- Immediately after moulding, place a barrier in a damp cupboard or damp room and allow it to remain there unless a set time is set.
Determination of initial setting time
- Place the test block enclosed in the mould and rest on a waterless plate, under a needle-carrying rod (C); gently lower the needle until it meets the surface of the test block and release it immediately, allowing it to enter the test area. Initially, the needle will completely pierce the test block.
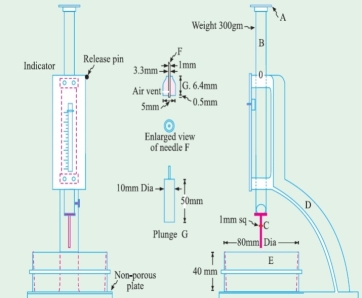
Fig no 26. Needles used in Vicat's Apparatus
- Repeat this process until the needle, when attached to the test block and removed as described above, fails to pierce the block more than 5.0 ± 0.5 mm measured from the bottom of the mould. The time elapsed between the time the water is added to the cement and the time when the needle fails to pierce the block reaches a point of 5.0 ± 0.5 mm measured from the bottom of the mould will be the first set time.
Determination of final setting time
- Insert needle (C) of Vicat resources into the needle with a secret attachment (F).
- The cement will be considered to be set at the end where, when the needle is gently inserted into the surface of the test block, the needle makes a picture of it, while the attachment fails to do so.
- The time elapsed between the time the water is added to the cement and the time when the needle makes its appearance on the surface of the block while the attachment fails to do so will be the last set time.
- In the case of a scarf that forms over the test block, use the bottom of the block to cut.
4. SOUNDNESS AND COMPRESSIVE STRENGTH
- Sensitivity refers to the ability of a glue that has been hardened to retain its volume after setting without the delay of harmful expansion.
- Thus, hearing is a very important test. The audio attachment will not make a pleasant volume change after it has hardened and as a result will not be in danger of forming cracks. Sound adhesive is the basis of sound mud or concrete mixing.
- Aircraft ash is the result of coal-fired power generation. During a fire, mineral pollutants in hot coals are released from the combustion chamber in the form of particles composed by flue gases.
- As these particles coo, they harden into round glass particles. The fly fly shows concrete structures and is used in concrete as replacement or replacement of concrete. Insufficiency can occur in the presence of very free magnesia or free lime burned in cement.
- The taste of cement can be determined in a variety of ways. In the Le Chatelier bath, a sample of cement / ash adhesive frosting is placed on the mould and boiled for a specified period of time (approximately 3hr) so that any tendency to stretch can be quickly and detected.
- After the boiling process is complete, the distance between the points of the two control indicators is measured by the nearest 0.5mm and compared to the first measured length before testing.
- This test requires Le Chatelier water bath, Le Chatelier mould, calliper, measuring cylinder, balance and length comparison. Active standards include EN 196-3, EN 459-2 and EN-450.
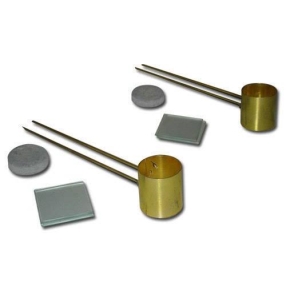
Fig no 27. Le chatelier apparatus
- Alternatively, the stability of the concrete can be determined by autoclave. These tests include an autoclave expansion of Portland cement using a test in a good cement sculpture.
- Specimens are made of oil-coated mould with reference points attached to a reference length of 250mm. Specimens extracted from the mould and measured after 24hr are placed in an autoclave at room temperature.
- After the autoclave is turned off, the specimens are exposed to a full-pressure current at a specified time. After the heating is complete, the template is rated and compared with the original length measurements.
- Equipment needed for this method includes autoclave, test bar mould, mixer equipment, balance and length gauge. Functional standards include ASTM C151 and AASHTO T107.
- The expansion of the cement can also be determined by comparing the length. The length gauge is a device used to measure changes in the length of attachment of cement, mortar and concrete according to ASTM and AASHTO data.
- The unit consists of a complex dial or digital display embedded in a solid, dual post frame structure. Moving and vertical anvils are designed to detect reference pins thrown at the edges of sample test bars.
- ELE offers a variety of devices for this method, including drying materials, shrinkage and humidity movements, as well as a ASTM-length ratio. Active standards include ASTM C151, C157, C227, C490, C531, AASHTO T-107 and T-160.
Key takeaways
- For simplicity, the initial set time is considered to have elapsed between the time when water can be added to the cement, at which point the paste begins to lose plastic.
- The last time is the last time the water is put in the cement, and the time when the glue is completely lost to the plastic and gained enough strength to withstand a certain direct pressure.
- Sensitivity refers to the ability of a glue that has been hardened to retain its volume after setting without the delay of harmful expansion.
- Thus, hearing is a very important test. The audio attachment will not make a pleasant volume change after it has hardened and as a result will not be in danger of forming cracks. Sound adhesive is the basis of sound mud or concrete mixing.
Tests on aggregate
Specific gravity
Gravity and the combined force of water are essential elements in the formation of concrete and bitumen mixtures. The thickness of a solid mass is a measure of its size to an equal volume of distilled water at a specified temperature. Because the compound can contain a void that is allowed to enter the water, two combined gravity measures are used:
- Apparent specific gravity and
- Bulk specific gravity
Apparent specific gravity, G app, is calculated on the basis of the volume of the number of compounds i.e. the volume without voids entering the water. Therefore
G app = [(MD / VN)] / W
Where,
- MD is a dry aggregate weight,
- VN integrated network volume without volume object focus,
- W the size of the water.
Bulk Specific Gravity, G bulk, is calculated on the basis of the total number of aggregates including the inlet. Therefore
G bulk = [(MD / VB)] / W
Where,
- VB total volume of aggregates including volume of water absorbed.
Grading of aggregate
- Collection placement determines the average grain size of the composite before it is used in construction.
- This is the use of a complex and clear combination. The combined sample is filtered through a set of sieves and weights stored in each filter by percentage words summarized.
- By dividing this amount by 100, The Fineness Modulus of that total is determined. This assists in the decision-making process about the number of well-known modular composites that must be combined to obtain the concrete of the desired quantity.
- The basis of a green and clear composite mix for a particular soft module is the presence of spaces or open spaces where the composite is packed together.
- For bad clean aggregates packing can leave 30-40 percent, which can only be removed by filling the fine particles.
- Similarly, in fine aggregates too, there are voids left to be filled with better particles (cement).
- This is important to get a mix of composite and blank letters.
- When other pieces of equal size are put together, voids or open spaces are always left. Percentage of voids can be as high as 45 percent of the total volume of aggregates.
- It turned out that this effect (presence of voids) was independent of the size of the aggregates used in the packaging, whether worse, medium or good.
- Only, while composite packaging should be of the same size, that is the same distance.
- Either all should be rough, or they should all be medium or good. This means that even if the sand alone is full, voids at a rate of 40-45 percent are left as well.
- This principle of spacing is the governing principle for the preparation of concrete under this method.
- When coarse aggregates are full to make concrete, the voids built into the weight should be filled with some good material. Sand is used for this purpose.
- However, there will be voids between the grains of sand as well. These are filled with cement particles.
- In this way, the weight of the resulting concrete is either empty or dense. Cement binding material is used to give this dense cone a stone-like character.
- Concrete, artificial stone, in a broad sense.
- Collection classification is intended to determine the particle size of a given group of composites.
- This is usually found by the Method of Fineness Modulus. This method can be used to determine the best modulus for coarse combinations, fine aggregates, and all composites, i.e., composite composites.
- In this way, the ideal weight of the sample is taken and filtered through a series of sieves respectively. The number of sieve is five in coarse aggregates and ten in all aggregates.
Sieve Size of Collection.
Coarse Aggregates: 80 mm, 40 mm, 20 mm, 10 mm, IS No..480
Fine Aggregates: Numbers 480, 240, 120, 60, 30 and 15.
Total included: 80 mm, 40 mm, 20 mm, 10 mm, Nos: 480, 240, 120, 60, 30 and 15.
Flakiness Index
Object
For determination of flakiness index of coarse aggregate, where the size of the coarse aggregate are larger than 6.3mm .
Apparatus
- Thickness gauge
- Sieves [63, 50, 40, 31.5, 25, 20, 16, 12.5, 10 & 6.3mm]
- Balance [0-10 kg]
- Thickness Gauge
Procedure
- The sample was removed with the IS filter defined in the Table shown below.
- Thickness size and long length
- Thickness size and long length
- A minimum of 200 pieces for each fraction is taken and measured.
- In order to separate the faulty material, each component is individually measured by the thickness of the size gauge.
- The total amount of blurring objects that transmit the size gauge is measured with an accuracy of 0.1% of the sample weight.
Elongation Index
Objective
For determination of elongation index of coarse aggregate, where the size of the coarse aggregate is larger than 6.3 mm
Apparatus
- Length gauge
- Sieves (63mm,50mm,40mm,31.5mm,25mm,20mm,16mm,12.5mm,10mm)
- Balance (0-10kg)
- Oven (3000c)
Procedure
- The sample was removed with the IS filter defined in the Table shown below.
- A minimum of 200 pieces for each fraction is taken and measured.
- To separate the extended objects, each fraction is measured individually in length in the length gauge.
- Combined pieces from each tested segment that could not exceed the specified gauge length and its long cut sides are collected separately to obtain the total composite weight stored at the gauge length from each segment.
- The total amount of extended material retained by the length gauge is measured with an accuracy of 0.1% of the sample weight.
Impact Value
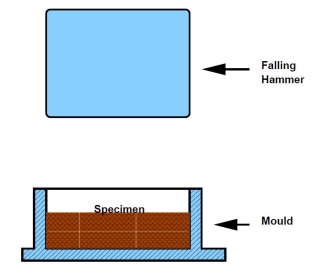
Fig no 28. Impact test apparatus
- Combined impact tests were performed to test for resistance to compound effects.
- The aggregates pass through a filter of 12.5 mm and are kept at 10 mm per filter are filled with a diameter of a diameter of 10.2 mm internal diameter and a depth of 5 cm attached to the metal base of the impact test machine.
- The content is completed in 3 layers where each layer is marked with 25 strokes.
- A steel hammer weighing 13.5 to 14 Kg is scheduled to be dropped with a free fall of 38.0 cm in v
- Ertical directions and a test sample is placed at 15 hits.
- The crushed joint is allowed to pass through a filter of 2.36 mm IS. And the impact value is measured as the percentage of aggregates that pass through the filter (W2) to the total sample weight (W1).
- Combined value = (W1 / W2) * 100
- Aggregates will be used to wear the course, the impact value should not exceed 30 percent. For bituminous macadams the maximum permissible value is 35 percent.
- In the basic studies of Water bound macadam the maximum allowable rate specified by the IRC is 40 percent.
Abrasion Value
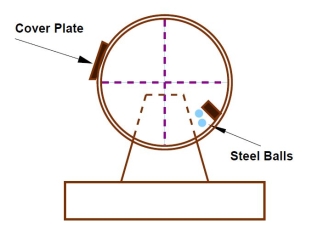
Fig no 29. Abrasion value setup
- Abrasion testing is performed to test the hardness of the material and to determine whether it is suitable for various stone construction activities.
- The abrasion test in Los Angeles is very popular to achieve hard materials and is standardized in India (IS: 2386 part-IV).
- The goal of the Los Angeles abrasion test is to find a percentage wear due to the rubbing action associated between the balls attached to the metal used as a serious offense.
- The Los Angeles machine consists of a 700 mm diameter inner diameter and 520 mm long attached to a horizontal axis that makes it possible to rotate (see Fig-2). A circular charge with round metal balls 48 mm wide and weighing 340-445 g is inserted into the cylinder and compound.
- The number of alrasive panorama varies depending on the sample size. The amount of compounds to be used depends on the catch and usually ranges from 5-10 kg.
- The cylinder is then locked and rotated at a speed of 30-33 rpm at a rate of 500 -1000 changes depending on the assembly rate.
- After the specified changes, the material is filtered through a filter of 1.7 mm and a fraction is transferred as a percentage of the sample weight. This figure is called the Los Angeles abrasion rate.
- A maximum of 40 per cent is allowed in the WBM study in the Indian state. In bituminous concrete, a maximum of 35 percent is specified.
Crushing Value
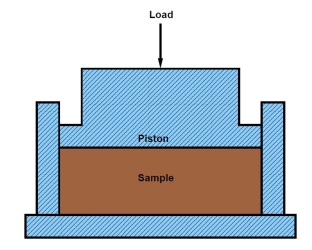
Fig no 30. Crushing test setup
- One of the models where the material is paved where it fails to press down under joint pressure.
- The test was rated with IS: 2386 part-IV and used to determine the combined crushing power.
- The combined value of the crush provides an approximate level of crushing resistance under the gradual crushing load.
- The test consists of placing a composite sample in a standard mold in a pressure test under normal load conditions.
- Dry aggregates pass through 12.5 mm sieve and 10 mm sieve are stored with a cylindrical dimension of 11.5 mm in diameter and 18 cm in height in three layers. Each layer is applied 25 times with a standard lubricant.
- The test sample is weighed and placed in a test cylinder in three layers each layer is also softened. The specimen is under a pressure load of 40 tons used slowly at an average of 4 tons per minute.
- The aggregates are then compressed and reduced by a filter of 2.36 mm and the weight of the passing object (W2) is expressed as a percentage of the total sample weight (W1) which is the total crushing value.
- Total crushing value = (W1 / W2) * 100
- A value less than 10 means a particularly strong combination while the above 35 can often be considered a weak combination.
Tests for fine aggregate:
Specific gravity
- The gravitational force of fine aggregate (sand) is defined as the mass of a given volume of aggregates in equal amounts of water. The gravitational force of fine aggregate (sand) is considered to be around 2.65 to 2.67.
- Quartz sand particles have a specific strength of between 2.65 to 2.67. While the odd clay starts from 2.70 to 2.80. Soils that contain a lot of organic matter or furry particles (such as diatomaceous earth) have a gravitational force of less than 2.60 (Some are as low as 2.00).
What is specific gravity of Aggregates?
The gravitational force of aggregate is considered to be the measure of the strength or quality of an object. The specified gravitational force is defined as the ratio of the weight of a given volume to a combination of the equivalent volume of water. Lower gravity scales are usually weaker than those with high gravity compounds. This property assists in the general identification of mergers.
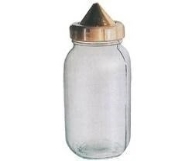
Fig no 31. Pycnometer bottle
Determination of Specific Gravity of Fine Aggregate as per IS: 2386 Part 3: (1963)
Hello friends, welcome to the world of Civil Allied Gyan. Read here the description, the list of apparatus, the IS code, the testing process, the formula and the web report about the determination of the gravitational force of a good collection.
Resources Required for Specific Integrated Voting Power Testing: -
- Pycnometer bottle of capacity 1000ml
- Touch stick
- Trench
- Balance scale
Is the Gravity Specific of Fine Aggregate test code: -
IS: 2386 (Part 3): 1963, Methods for testing concrete scales (Determining Specific Gravity of aggregates)
Procedure
- Take a clean and dry pycnometer and determine its empty weight (W₁ g).
- Take a pure sample of fine aggregate (about 1kg) to determine the gravitational force and transfer that to the pycnometer and weight (W₂ g). Aggregates better than 6.3mm taken.
- Pour the refined water into a pycnometer with a mixed sample at a temperature of 27 ºC, to water the sample only.
- Immediately after immersion, remove trapped air from the sample by moving or alternating the pycnometer, placing a finger in the hole at the top of the closed pycnometer.
- Clear the outer area of the pycnometer. Now the pycnometer is completely filled with water until the top hole, and after making sure that there is no more air trapped in the pycnometer, its weight (W₃ g).
- Transfer the value of the pycnometer to the care test being performed to ensure that all the components are transmitted. Clean the pycnometer.
- Re-fill the pycnometer with the added water to the top of the pycnometer, without any trapped air. It should be completely dry on the outside and take off weight (W₄ g).
- To fill the mineral, a special magnetic field bottle is used and the equipment is filled up to three times the volume of the bottle. The whole process of determining gravity is similar to that described above.
Seive Analysis
Objectives:
The whole process of sieve analysis determines the distribution of particle size of fine aggregates and determines whether it is suitable for use in concrete mixing.
Testing Resources
A series of IS filters
4.75 mm
2.36 mm
600 mic
300 mic
150 mic
75 mic
Procedure
- The sample was weighed exactly 1000g.
- First, we must clean all the sieve using a wire brush to make it clear that aggregates are trapped in some gaps.
- After that we have to prepare the sieve in the moving machine from top to bottom, in size from the largest (4.75mm) to the smallest (0.075mm).
- The sample was diluted using a collection of IS Sieves 10 minutes.
- After sieving is done, the merging with each filter is measured individually.
- The aggregate weight that passes through each filter is calculated as a percentage of the total sample weight.
- The same procedure is followed by two other samples.
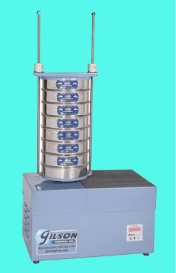
Fig no 32. Mechanical Sieve Shaker
Fineness Modules
The fineness modulus (FM) of aggregates may be a frightening term, but it is just a conceptual measure that describes the average size of particles in a composite sample. This feature provides the basis for selecting the approximate size of concrete joint design, but its actual impact is not always understood. The Fineness modulus is not a fixed value, as it provides a way to estimate the amount of integration needed to measure the mixing designs.
How to fineness modulus measure
Fineness modulus is determined using the percentage of size fractions from the sieve analysis and calculated for any selected series of sieve sizes. When designing concrete mixes, FM for good mixing is required to properly separate the mixes. Changes in the placement of the coarse aggregate section have little effect on the overall concrete structures. Combined partitions can be made using different cutting and fine-grained joints and blending techniques to control FM with concrete mix.
Origin of the Fineness Modulus Concept
Duff Abrams, an American inventor of the early 20th century, was an influential figure in the study of concrete structures and features. As well as explaining the importance of water / cement ratio and developing a fall test, he described the fineness modulus in 1918 as a way to separate concrete aggregates, simplify a gradation curve, and measure the appropriate size for use in mixing designs. Explaining the principle he said, "The integration of the same good modulus will require the same amount of water to produce the same coherence and provide the same strength concrete."
Includes Fineness Modulus
The simple FM calculation procedure requires a precise particle size analysis as described in ASTM C136, Standard Test Method for Sieve Analysis of Fine and Coarse Aggregates. In addition to the required particle size sizes, specific FM statistics must be included. Although manual upgrade of the sieve is permissible in standard, Gilson strongly recommends the use of the appropriate connector to ensure accuracy, durability and efficiency. After the filter has been analyzed and the fractions are measured in the correct proportions or proportions, the percentage of fractions is calculated.
Fineness Modulus of sand
To calculate the simple sand module, the total percentage accumulated stored in the following sieve is divided into 100: 150μm (No. 100), 300μm (No. 50), 600-μm (No. 30), 1.18mm (No. 16) , 2.36mm (No. 8), and 4.75mm (No. 4) of fine aggregates. If FM coarse aggregates are required, filters of 9.5mm (3⁄8in.), 19.0mm (3⁄4in), 37.5mm (11⁄2in) can be installed. There may be even larger sieves that can be added by continuing at a ratio of 2: 1 with the original sieve size. No additional equipment is required to make the determination. The same ASTM E11 test filters are used for integrated particle size analysis tests. In the example below, aggregate percentages from 4.75mm to 150µm are used to calculate the correct modulus for this fine mixing sample.
Alkali Aggregate Reaction
- Alkaline reaction - silica (ASR), more commonly known as "concrete cancer", is a painful inflammatory process that occurs over time in concrete between alkaline cement and active amorphous (eg, non-crystalline) silica found in many common compounds, sufficient moisture is provided.
- The pattern of cracks is associated with an alkaline-silica reaction that affects the concrete step barrier on the US highway. Note the common oily feature of the silicate debris imbibing the concrete surface on both sides of the crack.
- This undesirable chemical reaction results in the expansion of the altered composition by the formation of soluble and viscous gel of sodium silicate (Na2SiO3 • nH2O, and marked Na2H2SiO4 • nH2O, or N-S (sodium silicate hydrate), depending on the assembly received).
- This hygroscopic gel swells and increases in volume as it absorbs water: it has a high pressure inside the siliceous compound, which causes cracks and loss of concrete strength, eventually leading to its failure.
- The ASR can lead to severe cracking of the concrete, leading to serious structural problems that could force the demolition of a particular building.
- The extension of the concrete reaction between cement and composite size was first studied by Thomas E. Stanton in California in the 1930s with his publication in 1940.
Buckling of sand
- The increase in volume of a good compound due to the presence of moisture content is known as bulking. This is because the moisture causes a film of water around the sand particles leading to an increase in the volume of the sand, at a moisture content of about 5 to 8%, this increase in volume can be 20 to 40%, depending on the placement of the sand.
- The more effective it is, the more volume will be given to the moisture content provided. This practice is known as sand bulking.
- As the moisture content increases by adding more water, sand particles accumulate closer and the bulking value of the sand decreases. Therefore, dry sand and water-soaked sand are about the same size.
- Constipation of sand affects the balance of the sand to a large extent. Most with fine sand and less with coarse sand. If the right grant is not made for sand extraction, the cost of concrete, and vehicles will increase and it will result in less sandy loam and hard to operate and maintain.
Important facts regarding sand formation are as follows
- As the moisture content increases by adding more water, sand particles accumulate closer and the bulking value of the sand decreases.
- One of the reasons for adopting a weight measurement is the constipation of sand as weight loss avoids difficulty due to the abundance of sand.
- Sanding of the sand should be considered when the volumetric value of the value is accepted.
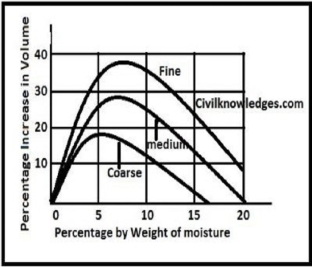
Fig no 33. Buckling of fine aggregate
Determining of buckling of fine aggregate
Opera and the process of determining the best percentage output
- Laboratory testing of bulk composites
- Field test for average quantity
Fine Aggregate Collection Laboratory Testing
Apparatus
- 250 ml measuring cylinder
- Weight balance
- Good combination
Procedure
- Take 500 grams of frozen fine aggregate at a temperature of 100 to 110 degrees Celsius for 24 hours. This is a weight measure as W1.
- Cool sand picks up airtight containers. So this weight ratio as W2.
- Sample water content is calculated as
- Wc = (W1-W2) X 100 / W1
- In a pan, 250 grams of sand take.
- In this case 2% by weight of water add. This is well integrated.
- The mixture is poured into a 250ml cylinder. This is compounded by shanking.
- The test was repeated with the remaining amount of 2% water sand at each time point. The reading takes as Y2, Y3… etc until the volume reading decreases.
- After their level, 4% of the water is added and the test continues until the sample is completely filled.
- For a standard sample in a measuring cylinder, add about 50 ml of water and stir the sample well.
ARTIFICIAL AND RECYCLED AGGREGATE
Artificial aggregates
- Many synthetic aggregates can be controlled, by industrial process products, such as various slags, or uncontrolled waste from other industrial processes, such as clinkers and ashes.
- Another important source of waste is the mining industry, including the extraction of coal and China clay.
- Some products that come out once or the waste can be made, or need to be recycled, to make things that are suitable for use as concrete mixers or that show special properties. In addition, other natural materials, such as perlite or vermiculite, can also be processed to produce compounds that reflect special properties.
- Demolition debris is reused to produce concrete scales. The RILEM (TC-121) technical committee recommended the separation of those compounds.
Recycled aggregate
- The construction industry produces a large amount of waste that needs to be recycled and used as recycled aggregates (RAs) for partial or complete environmental integration.
- Recycling reduces waste and reduces energy consumption and that is why it has an impact on the sustainable construction industry.
- In this chapter the need to redefine the current situation and situation around the world is highlighted. The structures of the RA are discussed. RAs weigh less than viral substances and higher water absorption.
- The state of the art of RA performance of concrete in a new and difficult world is summarized. The RA concrete exhibits low pressure and flexibility as well as low-strength mode and low cracking due to the porous nature of the RA and the old mud attached to the cement above the composite.
- The strength of the bond and the strength of the abrasion are less affected. Depletion, water infiltration and water infiltration by capillary increase with increased RA content.
- However, low performance can be reduced with a good mixing design using cement additives. Successful applications for RA in the manufacture of adhesive and truck concrete are also being discussed
Key takeaways
There are different tests for coarse aggregate which are
1. Specific gravity
2. Grading of aggregate
3. Flakiness index
4. Elongation index
5. Impact value
6. Abrasion value
7. Crushing value
There are different type of test for fine aggregate which are
1. Specific gravity
2. Seive analysis
3. Fineness modulus
4. Alkali aggregate
5. Buckling of sand
6. Artificial and recycle aggregate
Special Concrete - Light Weight Concrete and its Type
- Lightweight concrete may be described as a sort of concrete which incorporates an increasing agent in that it will increase the quantity of the combination whilst giving extra characteristics which includes nailability and lessened the useless weight.
- It is lighter than the traditional concrete. The use of light-weight concrete has been broadly un fold throughout international locations which includes USA, United Kingdom and Sweden.
- The essential specialties of light-weight concrete are its low density and thermal conductivity.
- Its blessings are that there may be a discount of useless load, quicker constructing quotes in creation and decrease haulage and managing costs.
- Lightweight concrete keeps its huge voids and now no longer forming laitance layers or cement movies while located at the wall.
- These studies became primarily based totally at the overall performance of aerated light-weight concrete.
- However, enough water cement ratio is essential to provide good enough concord among cement and water.
- Insufficient water can purpose loss of concord among debris, for that reason loss in energy of concrete.
- Likewise, an excessive amount of water can purpose cement to run off mixture to shape laitance layers, finally weakens in energy.
- Lightweight concrete has been used because the eighteen centuries through the Romans.
- The software at the ‘The Pantheon’ wherein it makes use of pumice mixture with inside the creation of solid in-situ concrete is the evidence of its usage.
- In USA and England with inside the overdue 19th century, clinker became used of their creation as an example the ‘British Museum’ and different low price housing.
- The light-weight concrete became extensively utilized in creation at some point of the First World War.
- The United States used particularly for shipbuilding and urban blocks.
- The foamed blast furnace-slag and pumice mixture for block making had been added in England and Sweden round 1930s.
- Nowadays with the development of technology, light-weight concrete expands its makes use of.
- For example, with inside the shape of perlite with its top notch insulating characteristics.
- It is broadly used as loose-fill insulation in masonry creation wherein it complements hearth place ratings, reduces noise transmission, does now no longer rot and termite resistant.
- It is likewise used for vessels, roof decks and different applications.
Materials utilized in Light weight concrete:
- Lightweight concrete may be produced through introducing:
- Gassing retailers which include aluminium powder or foaming retailers,
- Light-weight mineral mixture which includes per lite, vermiculite, pumice, elevated shale, slate, and clay, or plastic granules as mixture
Properties of Light weight concrete:
- Low Density
- Fire Resistance
- Sound Insulation
- Durability
- Thermal insulation
- Quality Control
Low Density
- The density of concrete varies from three hundred to 1200 kg/m³.
- The lightest grade appropriate for insulation proposed whilst the heavier grades with good enough energy appropriate for structural applications.
- The low density of cell concrete makes it appropriate for precast ground and roofing devices which can be smooth to deal with and shipping from the manufacturing unit to the sites.
Fire Resistance
- Lightweight concrete has outstanding hearth place-resisting properties.
- Its low thermal conductivity makes it appropriate for protective every other established shape the outcomes of fir
Sound Insulation
- Sound insulation in cell concrete is typically now no longer as suitable as in dense concrete.
Durability
- Aerated concrete is handiest barely alkaline. Due to its porosity and coffee alkalinity.
- It does now no longer deliver rust safety to metallic that's supplied through dense as compared concrete.
Thermal insulation
- The insulation fee of light-weight concrete is set 3 to 6, instances that of bricks and approximately ten instances of concrete.
- When a two hundred mm thick wall of aerated concrete of density 800 kg/ m3 has the identical diploma of insulation as a four hundred mm thick wall of density 1600 kg/ m3.
Quality Control
- Better first-rate manipulate exercised with inside the creation of a shape with light-weight concrete merchandise because of using manufacturing unit-made devices.
Types of Light weight Concrete:
Lightweight aggregate concrete:
- Lightweight aggregate concrete is referred to as an LWA.
- In the early 1950s, using light-weight concrete blocks familiar withinside the UK for the load-bearing internal leaf of hollow space walls.
- Soon thereafter the improvement and manufacturing of a brand new sort of synthetic LWA made it viable to introduce LWC of excessive energy, appropriate for structural work.
- These advances inspire the structural use of LWA concrete. Particularly wherein the want to lessen weight in a shape became an critical attention for layout or for the economy.
Aerated Concrete:
- Aerated concrete has the bottom density, thermal conductivity, and energy.
- Like timber, it is able to be sawn, screwed and nailed, however there are non-combustible.
- For works in-situ, the standard strategies of aeration are through blending in stabilized shape or through whipping air in with the useful resource of an air-entraining agent.
No fines concrete:
The time period no-fines concrete typically way concrete composed of cement and a coarse (9-19) aggregates handiest and the product so fashioned has many uniformly disbursed voids for the duration of its mass.
- Ordinary light-weight concrete organized from a binder, water best and coarse mixture with complete filling voids among the huge debris.
- Low Sand concrete, wherein the voids among the coarse mixture handiest partly packed with the paste.
- It additionally referred to as an opening graded concrete and dealt separately.
- In this example on best mixture use. Coarse debris of the mixture are coved through a skinny layer of cement, paste and the voids among them stay empty. It is referred to as no concrete.
- Aerated concrete crafted from a binder, water, best and coarse mixture, and a blowing agent which reduced the density of concrete.
Typical Light weight concrete mix:
- Lightweight concrete is a combination made with light-weight coarse aggregates inclusive of shale, clay, or slate, which offer it its feature low density.
- Structural light-weight concrete has an in-location density of ninety to a hundred and fifteen lb/ft³, while the density of everyday weight concrete tiers from a hundred and forty to a hundred and fifty lb/ft³.
- This makes light-weight concrete perfect for constructing current systems that require minimum pass sections with inside the foundation.
- It is being an increasing number of used to construct glossy foundations, and has emerged as a possible opportunity to everyday concrete.
- Nevertheless, a better compressive power of 7000 to 10,000 psi may be attained with light-weight concrete.
- However, this will compromise the density of the combination because it calls for the addition of greater pozzolans and water-decreasing admixtures to the concrete.
Key takeaways
1. Lightweight concrete keeps its huge voids and now no longer forming laitance layers or cement movies while located at the wall.
2. This study became primarily based totally at the overall performance of aerated light-weight concrete.
3. Aerated concrete is handiest barely alkaline. Due to its porosity and coffee alkalinity.
4. It does now no longer deliver rust safety to metallic that's supplied through dense as compared concrete.
Foam Concrete
- Foam concrete usually consists of cement mortar or fly ash and sand and water, although some suppliers recommend pure cement and water with an agent that produces lightweight mixtures.
- This slurry is also mixed with a foam made into a concrete mixing plant. The foam is made using a moisturizing agent, mixed with water and air from the generator. The foam operator used must be able to produce bubbles with a high degree of stability, resistant to physical and chemical processes of mixing, depositing and solidifying.
- Foam concrete mix can be poured or sprayed on moulds, or directly on parts of the building. Foam makes the Sulphur flow freely due to the thixotropic behaviour of foam bubbles, allowing it to be easily absorbed into the selected form or mould.
- Viscous materials require up to 24 hours to harden (or at least two hours if the smoke is treated at temperatures up to 70 ° C to speed up the process. Depending on the variability including ambient temperature. And moisture. Once solidified, the manufactured product can be removed from its mould.
- A new application in the production of foam concrete is to cut large-size concrete cakes into blocks of different sizes with a cutting machine using special metal wires. The cutting action occurs when the concrete is still soft.
Properties
Foam concrete is a versatile construction material with a simple and inexpensive method of production compared to air-cooled autoclave concrete. Foam compounds using foam-using ashes for this cheap compound are still cheap, and have little impact on the environment. Foam concrete is produced in quantities ranging from 200 kg / m3 to 1,600 kg / m3 depending on the application. Smaller products can be divided into different sizes. While the product is considered to be a type of concrete (with air bubbles replacing the whole), its thermal and sound insulation properties make it a very different application than conventional concrete.
Applications
Foam concrete can be produced in dry quantities of 400 to 1600 kg / m3 (25 lb / ft3 to 100 lb / ft3), with a capacity of about 7 to 10 days N / mm2 (145 to -1450 psi) respectively. The foam concrete is fire resistant, and its thermal and sound insulation properties make it ideal for a variety of purposes, from floor and ceiling protection, to useless filling. It also helps to restore the trench.
A few applications of foam concrete are:
- Bridge / bar road routes
- Pipe discharge / annual filling
- Back ditch
- Precast blocks
- Precast wall elements / panels
- Cast-in-situ / cast-in-place walls
- By defending the imposition of compensation
- Split down screens
- Partition roof screeds
- The filling of the deceased part
- Trench for restoration
- Sub-base on highways
- The filling of empty blocks
- Partition boards used
Key takeaways
1. Lightweight concrete may be described as a sort of concrete which incorporates an increasing agent in that it will increase the quantity of the combination whilst giving extra characteristics which includes nailbility and lessened the useless weight.
2. It is lighter than the traditional concrete. The use of light-weight concrete has been broadly un fold throughout international locations which includes USA, United Kingdom and Sweden.
No Fines Concrete
What is No-Fines Concrete?
- No-Fines Concrete is a lightweight concrete made of cement only, cement and water by leaving fine particles (sand or fine compounds) of ordinary concrete. The benefits, limitations and equity of the exemptions are discussed.
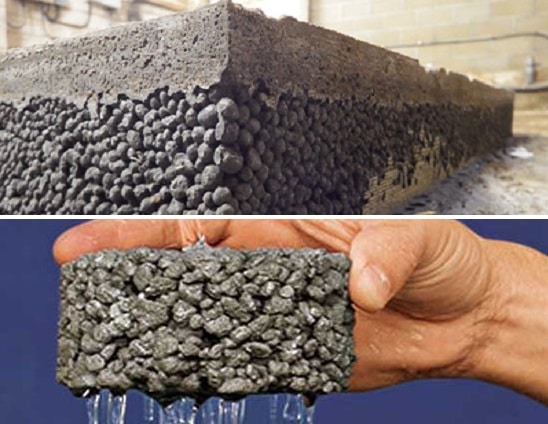
Fig no 34. No fines concrete
- Usually only one equal measurement, of more than 20 mm in size, is kept in 10mm. Concrete no-faes are popular because of the specific benefits you have over conventional concrete.
- The single-layer collection makes a beautiful, non-abrasive concrete, which in addition to getting large voids and therefore light weight, also gives a nice look to the build.
Advantages of No-Fines Concrete
- No fine concrete is a heavy concrete i.e. the density is approximately 25 to 30% less than normal concrete due to the lack of good adhesion, so the weight of the structure is small.
- Since it does not have good sand or aggregates, it has less drying shrinkage compared to conventional concrete
- It has a better heat protection feature than ordinary concrete and therefore helps in the construction of the outer wall.
- Since it does not have good aggregates, the required area for cement coverage has been greatly reduced. Therefore, the required amount of cement is reduced per cubic meter compared to conventional concrete. Therefore, it will save.
- Heavy concrete has no effect on quality due to the fragmentation of the compact cluster as it does not have good dimensions. Therefore, it can be thrown higher.
- No fine concrete can be assembled without the need for any types of concrete vibrators and can be easily made by touching the rods.
Limitations of No Fines Concrete
- Since there are no good compounds to fill the gaps in this concrete, it has a higher penetration than standard concrete. Therefore, it is not a good idea to build reinforced concrete without compensation concrete, as reinforcement can be easily eaten.
- To make this concrete inaccessible, an additional coat of construction mud is required, which adds to the cost.
- There is no concrete test that can be tested for effectiveness by using tests on standard concrete such as rolling or testing for rigidity. Performance rates and their testing methods are unknown.
Mix proportion of No-Fines Concrete
- No-fines concrete is usually made with aggregate / cement scales from 6: 1 to 10: 1. The standard aggregates used are usually sizes over 20 mm and stored at 10 mm.
- Unlike conventional concrete, where the strength is primarily controlled by the water / cement ratio, the strength of the concrete can be charged depending on the water / cement ratio, the estimated cement ratio and the weight of the concrete.
- The water / cement ratio for satisfactory consistency will vary between a minimum width of 0.38 and 0.52. The water / cement level should be chosen carefully. If a very low amount of water / cement is accepted, the adhesive will dry so much that the adhesive can be well coated with adhesive resulting in insufficient adhesion between the particles.
- On the other hand, if the water / cement ratio is too high, the glue will run down the concrete floor, especially if you move and fill in the gaps between the joints at the bottom and make that part more compact. This condition also reduces the adhesion between the adhesive and the adhesive due to the adhesion being much thinner.
- There is no standard method available, such as a descent test or an object measurement test to measure the consistency of a non-finite concrete. Perhaps a good test, visual experience and trial and error method would be the best guide to determine the water / cement ratio.
- No-faes concrete, when using standard aggregates, can show a density of about 1600 to 1900 kg / m3, but if no-faes concrete is made using lightweight aggregate, the size can reach approximately 360 kg / m3.
- Concrete of no-faes does not pose a major congestion problem. The use of a combination of equipment or vibration methods is not required. Simple rodding is sufficient for full filling.
- Concrete of no-faes does not give much to the formation side as the particles have a point of identification of the contact and the concrete does not move. Therefore, the side of the formworks can be removed in a much shorter time than ordinary concrete.
- However, the forms may need to be stored longer, when used as part of the structure, as the strength of the concrete decreases considerably. The compressive strength of the fine-grained concrete varies between 1.4 M Pa to 14 M.
- The strength of the bonded concrete bond is very low and, therefore, the reinforcement is not used in combination with the non-charged concrete. However, if the reinforcement needs to be applied to a non-abrasive concrete, it is advisable to touch the reinforcement with cement to improve the bond and protect it from cracking.
Key takeaways
1. No-Fines Concrete is a lightweight concrete made of cement only, cement and water by leaving fine particles (sand or fine compounds) of ordinary concrete. The benefits, limitations and equity of the exemptions are discussed.
2. Usually only one equal measurement, of more than 20 mm in size, is kept in 10mm. Concrete no-faces are popular because of the specific benefits you have over conventional concrete.
Self Compacting Concrete
- Self-compacting concrete (SCC) is a flowing concrete that doesn't require vibration and, indeed, have to now no longer be vibrated.
- It makes use of super plasticizers and stabilizers to seriously growth the benefit and price of glide.
- It achieves compaction into each a part of the mildew or formwork genuinely by using its personal weight with none segregation of the coarse aggregate.
- The consistence of the concrete is designated and measured as a glide price as opposed to the everyday stoop test.
SCC offers:
- Health and protection benefits (as no vibration is needed).
- Faster creation times.
- Increased workability and simplicity of glide round heavy reinforcement.
- Excellent sturdiness.
Advantages of SCC:
- No vibration is needed in the course of the position into forms.
- Placement of concrete easier.
- Reduces the concreting time.
- Increased sturdiness of structure.
- High Strength
Material used in SCC:
- The powdered substances that may be delivered are fly ash, silica fume, lime stone powder, glass filler and quartzite filler.
Tests for SCC:
Following are numerous techniques for checking out the houses of sparkling concrete:
- Slump glide test
- T50 stoop glide test
- J ring test
- V Funnel test
- V funnel at T5 minute
- L container test
- U container test
- Fill container test
- GTM display balance test
- Orimet test
Sr .no. | Method | Units | Typical mix | |
Minimum | Maximum | |||
1 | Slump cone by Abrams cone | Mm | 650 | 800 |
2 | T50slumpflow | Sec | 2 | 5 |
3 | J ring | Mm | 0 | 10 |
4 | V funnel | Sec | 8 | 12 |
5 | V funnelatT5minute | Sec | 0 | 3 |
6 | L box | (h2/h1) | 0.8 | 1.0 |
7 | U box | (h2-h1) Mm | 0 | 30 |
8 | Fill box | % | 90 | 100 |
9 | GTM screen stability test | % | 0 | 15 |
10 | Orimet | Sec | 0 | 5 |
Properties of SCC:
Strength:
Strength of concrete are of the subsequent types:
- Compressive strength
- Tensile strength
- Flexural strength
- Shear strength
1.Compressive Strength
- The dice specimens of concrete of the preferred percentage are solid in metallic or solid iron moulds, typically 6-inch dice.
- The general cylinder specimen of concrete is 6 inch in diameter and 12 inches in peak and solid in a mould commonly fabricated from solid iron;
- Standard cubes and cylinders are examined at prescribed ages, commonly, 28 days, with extra exams frequently made at 1, three, and seven days.
- The specimens are examined for crushing electricity below a checking out machine.
- The dice exams supply an awful lot more values of crushing electricity, typically 20 to 30 % extra than the ones given via way of means of cylinders.
Effect of age on concrete strength:
- Concrete attains electricity with time.
- Ordinary cement concrete profits above 70 to 75% of its very last electricity inside 28 days and approximately ninety to 95 % with inside the path of 1 year.
- It is frequently perfect to test the suitability of a concrete lengthy earlier than the effects of the 28-day check are available.
- When no particular records at the substances utilized in making concrete are available, the 28-day electricity can be assumed to be 1.5 instances of the 7 days’ electricity.
- Tests have proven that for concrete made with regular Portland cement the ratio of the 28 days to 7 days’ electricity commonly lies among 1.three to 1.7, and the bulk of the effects fall above 1.5.
2. Tensile strength
- Concrete could be very susceptible in tension.
- The tensile electricity of regular concrete levels from approximately 7 to 10 percentage of the compressive electricity.
3. Flexural strength
- The flexural electricity of undeniable concrete is nearly fully established upon the tensile electricity.
- However, experiments display that the modulus of rupture is substantially more than the electricity in tension.
4. Shear strength
- It is the actual figuring out issue with inside the compressive electricity of brief columns.
- The common electricity of concrete in direct shear varies from approximately 1/2 of of the compressive electricity for wealthy combinations to approximately 0.8 of the compressive electricity for lean combinations.
Workability:
- The electricity of concrete of a given blend percentage could be very significantly laid low with the diploma of its compaction.
- It is consequently essential that the consistency of the combinationture be such that the concrete may be transported, positioned and completed sufficiently effortlessly and without segregation.
- A concrete pleasant those situations is stated to be workable.
Elastic Properties:
- Concrete isn't always flawlessly elastic for any variety of loading, an considerable everlasting placing taking location for even low loads.
- The deformation isn't always proportional to the strain at any degree of loading.
- The elastic residences of concrete range with the richness of the aggregate and with the depth of the strain.
- They additionally range with the age of concrete.
Durability:
- Durability is the assets of concrete to face up to the circumstance for which it's been designed, without deterioration over a length of years.
- Lack of sturdiness may be resulting from outside sellers bobbing up from the surroundings or via way of means of inner sellers in the concrete.
Application of SCC:
- Construction of Bridges, buildings, tunnels.
- Precast Concrete Members
- Casting of slab and slender wall
Typical Mix:
- A easy device has been designed for self-compacting concrete (SCC) blend layout with 29% of coarse aggregate, substitute of cement with Meta kaolin and sophistication F fly ash, combos of each and managed SCC blend with 0.36 water/cement ratio(via way of means of weight) and 388 litre/m3 of cement paste volume.
Key Takeaways
1. Self-compacting concrete (SCC) is a flowing concrete that doesn't require vibration and, indeed, have to know no longer be vibrated.
2. Concrete isn't always flawlessly elastic for any variety of loading, an considerable everlasting placing taking location for even low loads.
High Density Concrete
- High density concrete is a concrete having a density with inside the variety of 6000 to 6400 kg/cu.m.
- High density concrete is likewise called Heavy weight concrete.
- High density concrete is specifically used for the cause of radiation protective, for counterweights and different makes use of in which excessive density is required.
- The excessive density concrete has a higher protective property, in order that it is able to shield dangerous radiations like X-rays, gamma rays, and neutrons.
- High density aggregates are used to attain heavy weight concrete. Some of the excessive density aggregates are, barite, ferro phosphorus, limonite, hematite, ilmenite, magnetite, goethite, metallic punching, and metallic shots.
- The factor to keep in mind is that in order to attain this sort of concrete, excessive constant water content material is required.
- The choice of the above cited aggregates specifically depends on the bodily houses like bulk density, unique gravity, Availability of substances, and its expenses.
- In order to attain workability, excessive density the aggregates have to be loose from dirt, oil or grease stains and different overseas matter.
- Or else, it's going to retard the hydration method and the powerful bonding of particles.
- Some of the boron additions like colemanite, boro calcite is used with inside the preparation of concrete to enhance the protective houses.
- These additions might also additionally have an effect on the placing time of concrete so, trial mixes have to be made and examined relying upon the suitability.
- As the call suggests, the density of this concrete varies from 3360 kg/m3 to 3840 kg/m3, while the density of regular concrete is of the order of 2400 kg/m3.
- The density of mild weight concrete is ready 1900 kg/m3 and that of regular concrete approximately 2400 kg/m3.
- Thus, the density of excessive density concrete is ready 50% greater than the density of traditional concrete.
- However, this concrete may be produced of density up to 5200 kg/m3 the use of iron as each nice and coarse mixture.
- With the arrival of the nuclear electricity, there's a big call for of the concrete technologists with inside the market.
- Due to using nuclear electricity generating reactors, big scale manufacturing of penetrating radiation and radioactive substances additionally has taken location.
- Thus, all nuclear electricity generating gadgets inclusive of nuclear reactors, particle accelerator, business radiography, x-ray and gamma ray remedy gadgets require nuclear protective cloth for the safety of the working employees in opposition to the organic risks inclusive of radiation.
- The regular in addition to excessive density concrete is powerful and low in cost for the development of everlasting guard in opposition to radiation.
Materials in High density concrete:
- All represent substances, cement, admixtures, and water utilized in excessive density concrete have to agree to the requirements as for regular density concrete, however the aggregates is unique and can require unique attention at some stage in handling, batching, blending, transporting and setting.
Aggregates:
- High density concrete (HDC), densities is executed via way of means of the use of excessive-density aggregates commonly iron oxides and relies upon on its meant use, bodily and chemical houses, availability and price.
- Concrete densities of 3700 to 3800 kg/m³, is offered utilizing aggregates with particle relative densities of as a minimum 4500 kg/m³ and for concrete densities of 4800 kg/m³ aggregates have to have a particle relative density of as a minimum 6000 kg/m³.
- Aggregate grading for HDC hardly ever agree to regular mixture requirements because the mixture are hardly ever made for concrete manufacturing, this have to be general via way of means of capacity customers because it isn't always adverse to the manufacturing of HDC.
- The maximum critical a part of HDC aggregates is that the grading have to be consistent and that a attainable grading restriction be agreed on with the dealer, to base the combination layout on.
- The chemical houses of all excessive-density aggregates have to be evaluated earlier than use, chemical reactivity and mainly in excessive alkaline environments as observed in cement pastes, long time sturdiness inclusive of alkali-mixture reactivity, sulphate and chloride assault and different impurities.
- The dealer have to be capable of offer a complete chemical evaluation of all capacity substances and opportunity substances to be used.
- With right technical assessment and planning, unique styles of aggregates may be blended on the dealer backyard to provide a concrete with predicted, detailed density.
- Cost thing are very critical as those aggregates are commonly greater highly-priced than regular aggregates, it is able to additionally be that the cloth might also additionally handiest be to be had in relative brief supply.
- The price of HDC will increase with density however now no longer essential in direct proportion.
- Aggregates have to be decided on for his or her shape (cubical or rounded and freed from flat or elongated, most density, workability, and price. Particle relative density of the nice mixture have to be just like that of the coarse mixture as decrease density nice mixture can cause segregation of the coarse mixture via the mortar.
- The grading of the coarse mixture have to be uniformly graded among 10 and 40mm, as in step with limits in Table 1. The grading of the nice mixture have to be in the restriction as proven in Table 1 as this will assist to save you segregation.
Sieve sizes mm:
Grading 1 for 37.5 mm most length aggregates % passing
Grading 2 for 19.0 mm most length aggregates % passing
Coarse aggregates:
Two styles of aggregates may be used for excessive density concrete namely:
Natural aggregates:
- Iron ores of diverse sorts had been used all over the globe for lots years (out of doors the U.K), with inside the UK imported iron ore is used.
- Using a few herbal going on aggregates concrete densities of about 4000 kg/m³ may be obtained. (J. Goodman, 2009)
- Different styles of herbal excessive-density aggregates which may be used for excessive density concrete (HDC) to be had in South Africa and the United Kingdom talk over with Table 2.
Man-made aggregates:
- To attain concrete densities above 4000 kg/m³ man-made or artificial cloth inclusive of ferrosilicon slag, metallic or lead shot may be used.
- For styles of man-made aggregates which may be used for excessive density concrete (HDC) to be had in South Africa and the United Kingdom talk over with Table 2.
Cements:
- All cements conforming to SANS 50197 as for traditional concrete may be used for HDC if it produces the desired bodily houses.
- If alkali-reactive materials are gift with inside the aggregates cements with low alkali contents or a appropriate combination of cements and cement extenders have to be used.
- Low-alkali cement now no longer having greater that zero.6 % Na2O-eq can be used with a doubtlessly alkali-reactive mixture inclusive of lead shot.
- The following extenders: Ground granulated blast furnace slag (GGBS), fly ash (FA) and Condensed silica fume (CFS) have decrease densities than Ordinary Portland Cement (OPC) and may be used in the event that they do now no longer lessen the density of the concrete under detailed limits, but states “The cement may be OPC or a mix of this with both Ground granulated blast furnace slag, Pozzolanic fly ash; the latter if you want to now no longer lessen the density of the concrete however might also additionally decorate the in any other case terrible workability”.
- Fly ash blends and decrease water contents can effectively be used to boom the density of concretes. When lad shot is used High alumina cement (HAC) should be used, because it reduces the chemical reactivity of lead in excessive alkaline conditions.
- When the use of alkali-reactive mixture (lead shot) deleterious enlargement may be avoided whilst the use of excessive-alkali cements via way of means of including extenders complying with SANS 1491 via way of means of the use of a minimal percent of the subsequent extenders via way of means of general mass of cement:
At least 40% Slag (S) via way of means of mass
At least 15% CSF via way of means of mass
At least 20%via way of means of mass
Admixtures:
- Adding admixtures can minimize segregation, bleeding, each of which may be complex with HDC. The sturdiness may be advanced with a low loose water/cement ratio (w/c) in particular so in structural grade HDC.
- Using terrific plasticizers is usually recommended which in conjunction the cement kind might also additionally marginally boom concrete density.
- Super plasticizers are useful in decreasing water to minimize bleeding and preserve a cohesive blend that has minimal segregation.
The following admixture may be utilized in HDC:
- Air-entraining admixtures because it controls bleeding and agreement enhance workability and help in acquiring greater homogenous concrete however will lessen the density of the concrete.
- Water-decreasing admixtures because it will boom concrete density via way of means of decreasing the quantity of water with inside the blend, water is the cloth utilized in HDC with the bottom density.
- Shrinkage-decreasing admixtures because it make sure dense, crack-loose concrete used for radiation-protective concrete
- When lead shot or lead containing aggregates are to be used, the subsequent have to be taken into consideration whilst choosing a chemical admixture.
- The alkali content material of chemical admixtures for concrete utilized in South Africa is among approximately zero.2 and 7%. In many times the contribution to the alkali content material of the pore answer is big and can't be ignored.
- One of the extensively used terrific plasticizers has a Na2O-eq of approximately five% and if introduced at 1% of cement to concrete with a cement content material of 350 kg/m³ it's going to advert 0.17 kg/m³ Na2O-eq to the concrete.
- Lithium primarily based totally compounds may be used with lead shot to manipulate the alkali reactivity.
- The impact of admixtures have to be installed beneath discipline conditions, ideally via way of means of testing, to decide if the admixtures attain the desired effects or completely unsuitability.
Water:
- Water will be easy and loose from adverse concentrations of acids, alkalis, salts, sugar and different natural or chemical materials that would impair the sturdiness and power of concrete or imbedded metallic.
Proportioning, blending and setting of High Density Concrete:
- The blend proportions for those excessive density concrete is identical as that of regular concrete.
- Conventional approach of blending and setting is utilized in excessive density concrete. The maximum critical aspect is to save you overloading the mixer in particular whilst heavy weight aggregates inclusive of steels are used. Batch sizes have to be decreased to forty to 50% of the allowable mixer capacity. Also keep away from extra blending as it will bring about workability and bleeding of concrete.
- Preplaced mixture strategies may be followed whilst setting heavy weight concrete. In this approach the aggregates are located in forms , an appropriate grout made from cement, sand and water is pumped over the located aggregates, a good way to fill the voids in between the aggregates. This approach prevents the segregation of coarse aggregates additionally reduces drying shrinkage and facilitates us to attain concrete of uniform density and composition.
- Puddling approach also can be followed. In this approach, the mortar is located in varieties of 2″ thick and the coarse aggregates are located over it and vibrated internally. Care have to be taken that, the coarse aggregates are allotted evenly.
- Pumping of heavy weight concrete may be followed handiest the peak is limited. The heavy weight concrete can't be pumped to large distances due to their extra densities
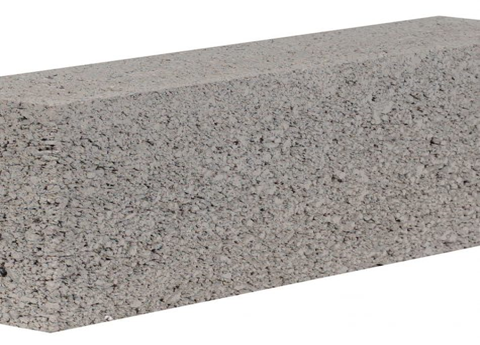
Fig no 35. High density concrete
Key takeaways
1. High density concrete is specifically used for the cause of radiation protective, for counterweights and different makes use of in which excessive density is required.
Fibre Reinforced Concrete, Geo Polymer Concrete and Ferrocement Technique
Fibre Reinforced Concrete
- Fibre Reinforced Concrete is a composite cloth which include fibrous cloth which will increase its structural integrity.
- It consists of combinations of cement, mortar or concrete and discontinuous, discrete, uniformly dispersed appropriate fibers.
- Fibers are normally utilized in concrete to govern cracking because of plastic shrinkage and to drying shrinkage.
- They additionally lessen the permeability of concrete and consequently lessen the bleeding of water.
Advantages of Fiber-strengthened concrete:
- Fibers strengthened concrete can be beneficial in which excessive tensile power and decreased cracking are proper or whilst traditional reinforcement cannot be placed.
- It improves the effect power of concrete, limits the crack boom and ends in a extra stress potential of the composite cloth.
- For commercial projects, macro-artificial fibers are used to enhance concrete’s sturdiness.
- Made from artificial substances, those fibers are lengthy and thick in length and can be used as a substitute for bar or material reinforcement.
- Adding fibers to the concrete will enhance its freeze-thaw resistance and assist maintain the concrete sturdy and appealing for prolonged periods.
- Improve blend cohesion, enhancing pumpability over lengthy distances.
- Increase resistance to plastic shrinkage in the course of curing.
- Minimizes metallic reinforcement requirements.
- Controls the crack widths tightly, consequently enhancing sturdiness.
- Reduces segregation and bleed-water.
- FRC, longevity is ready 10 to forty instances that of undeniable concrete.
- The addition of fibers will increase fatigue power.
- Fibers boom the shear potential of strengthened concrete beams.
Application of Fiber-strengthened concrete:
The programs of fiber strengthened concrete rely on the applicator and builder in taking gain of the static and dynamic traits of the cloth. Some of its vicinity of software is-
- Runway
- Aircraft Parking
- Pavements
- Tunnel Lining
- Slope Stabilization
- Thin Shell
- Walls
- Pipes
- Manholes
- Dams
- Hydraulic Structure
- Elevated decks
- Roads
- Bridges
- Warehouse floors
Fiber Types:
- Fibers for concrete are to be had in exclusive sizes and shapes.
- The essential elements affecting the function of fiber-strengthened concrete are a water-cement ratio, percent of fibers, diameter and duration of fibers.
- Given beneath are exclusive varieties of fiber-strengthened concrete utilized in production.
Steel Fiber Reinforced Concrete:
- Steel fiber is a metallic reinforcement. A sure quantity of metallic fiber in concrete can motive qualitative modifications in concrete’s bodily property.
- It can significantly boom resistance to cracking, effect, fatigue, and bending, tenacity, sturdiness, and others.
- For enhancing lengthy-time period behavior, improving power, longevity, and strain resistance, SFRC is being utilized in systems which includes flooring, housing, precast, bridges, tunneling, heavy-responsibility pavement, and mining.
- The varieties of metallic fibers are described via way of means of ASTM A820 are, Type I: cold-drawn cord, Type II; reduce sheet, Type III: melt-extracted, Type IV: mill reduce and Type V: changed cold-drawn cord
Polypropylene Fiber Reinforced (PFR) Concrete:
- Polypropylene fiber strengthened concrete is likewise referred to as poly propene or PP.
- It is a artificial fiber, converted from propylene, and utilized in loads of programs.
- These fibers are normally utilized in concrete to govern cracking because of plastic shrinkage and drying shrinkage.
- They additionally lessen the permeability of concrete and consequently lessen the bleeding of water.
- Polypropylene fiber belongs to the institution of polyolefins and is partly crystalline and non-polar.
- It has comparable homes as poly ethylene, however it's far tougher and greater warmth resistant.
- It is a white rugged cloth with excessive chemical resistance.
- Polypropylene is made from propylene fuel with inside the presence of a catalyst which includes titanium chloride.
- Polypropylene fiber shows accurate warmth-insulating homes and is especially immune to acids, alkali, and natural solvents.
Glass Fiber Reinforced Concrete:
- Glass fiber strengthened concrete is a cloth which include severa extraordinarily first-rate fibers of glass.
- Glass fiber has kind of similar mechanical homes to different fibers which includes polymers and carbon fiber.
- Although now no longer as inflexible as carbon fiber, it's far tons less expensive and notably much less brittle whilst utilized in composites.
- Glass fibers are consequently used as a reinforcing agent for lots polymer merchandise; to shape a totally sturdy and comparatively light-weight fiber-strengthened polymer (FRP) composite cloth known as glass-strengthened plastic (GRP), additionally popularly referred to as “fiberglass”.
- This cloth incorporates very little air or fuel line, is denser, and is a miles poorer thermal insulator than is glass wool.
Polyester fibers:
- Polyester fibers are utilized in fiber-strengthened concrete for commercial and warehouse floors, pavements and overlays and precast merchandise.
- Polyester micro- and macro-fibers are utilized in concrete to offer advanced resistance to the formation of plastic shrinkage cracks as opposed to welded cord material and to decorate longevity and the capacity to supply structural potential whilst well designed, respectively.
- Polyester micro- and macro-fibers are utilized in concrete to offer advanced resistance to the formation of plastic shrinkage cracks as opposed to welded cord material and to decorate longevity and the capacity to supply structural potential whilst well designed, respectively.
Carbon fibers:
- Carbon fibers are fibers approximately 5–10 micrometers in diameter and composed in general of carbon atoms.
- Carbon fibers have numerous benefits such as excessive stiffness, excessive tensile power, low weight, excessive chemical resistance, excessive-temperature tolerance and coffee thermal expansion.
- Carbon fibers are normally mixed with different substances to shape a composite.
- When impregnated with a plastic resin and baked it bureaucracy carbon-fiber-strengthened polymer (frequently known as carbon fiber) which has a totally excessive power-to-weight ratio, and is extraordinarily inflexible even though particularly brittle.
- Carbon fibers also are composited with different substances, which includes graphite, to shape strengthened carbon composites, that have a totally excessive warmth tolerance.
Macro artificial fibers:
- Macro artificial fibers are crafted from a mix of polymers and have been at the beginning advanced to offer an opportunity to metallic fibers in a few programs.
- Initially, they have been diagnosed as a ability opportunity to metallic fibers in sprayed concrete, however growing studies and improvement confirmed that that they'd a function to play withinside the layout and production of ground-supported slabs and a huge variety of different programs.
- They are specifically appropriate for presenting nominal reinforcement in competitive environments, which includes marine and coastal systems, as they do now no longer go through the troubles of staining and spalling which could end result from the corrosion of metallic.
- Besides, due to the fact they may be non-conducting, they had been utilized in tram and mild railway developments.
Micro-artificial fibers:
- Micro-artificial fibers offer advanced resistance to the formation of plastic shrinkage cracks as opposed to welded cord reinforcement, they may be not able to offer any resistance to similarly crack width openings due to drying shrinkage, structural load or different sorts of strain.
- However, those merchandise need to be frequently laid out in any form of concrete to enhance cracking resistance, spall protection, freeze-thaw sturdiness and enhance the homogeneity of concrete in the course of placement.
Natural fibers:
- The herbal fiber is without delay available from an animal, vegetable, or mineral supply and convertible into nonwoven fabric which includes felt or paper or, after spinning into yarns, into woven cloth.
- A herbal fiber can be similarly described as an agglomeration of cells wherein the diameter is negligible in evaluation with the duration.
- Although nature abounds in fibrous substances, in particular cellulosic kinds which includes cotton, wooden, grains, and straw.
- The use of herbal fibers in making concrete is usually recommended in view that numerous varieties of those fibers are to be had domestically and are plentiful.
- The concept of the use of such fibers to enhance the power and sturdiness of brittle substances isn't new; for example, straw and horsehair are used to make bricks and plaster.
- Natural fibers are appropriate for boosting concrete and are without difficulty to be had in growing countries.
Cellulose fibers:
- Cellulose fibers are made with ethers or esters of cellulose, which may be acquired from the bark, wooden or leaves of plants, or different plant-primarily based totally cloth.
- In addition to cellulose, the fibers may comprise hemi cellulose and lignin, with exclusive possibilities of those additives changing the mechanical homes of the fibers.
- The predominant programs of cellulose fibers are with inside the fabric industry, as chemical filters, and as fiber-reinforcement composites, because of their comparable homes to engineered fibers, being every other alternative for bio composites and polymer composites.
Geo Polymer Concrete
- Geo polymer is the name given to the Daidovits in 1978 for items that appear in chains or networks or unusual molecules.
- Geopolymer cement concrete is made using waste materials such as fly ash and ground granulated blast furnace slag (GGBS). An ash fly is a waste product produced from a hot power plant and the granulate blast soil in a furnace is processed as a metal waste.
- Both fly ash and GGBS are processed by appropriate technology and applied to concrete operations in the form of a geo polymer concrete. The use of this concrete helps to reduce waste stocks and reduces carbon emissions by reducing demand for Portland cement.
- A key feature of the geo polymers source of silicon and aluminum is supplied by natural thermal agents (e.g. kaolinite) or industrial products (e.g. Fly ash or slab) and an alkaline solution that makes these materials chains and networks to create strong bond. Also called alkaline cement or inorganic polymer cement.
Composition of Geo polymer Concrete
The following materials are required to produce this concrete:
- Fly ash - Fly ash generator
- GGBS - Metal Product
- Good collection and heat collection as required for standard concrete.
- GPCC alkaline activator solution as described above. The Catalytic liquid system is used as an alkaline activator solution. It is a combination of alkali silicates and hydroxide solutions, in addition to pure water. The role of the alkaline activator solution is to activate geopolymeric resource sources containing Si and Al such as fly ash and GGBS.
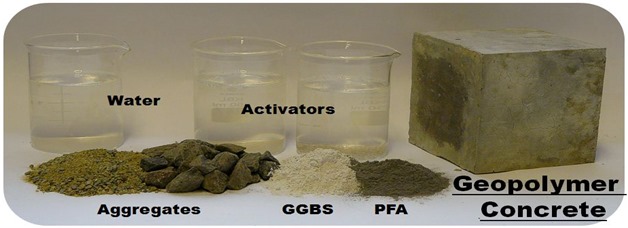
Fig no 36. Geo polymer Concrete Materials
Mechanical properties of Geo polymer Concrete
- Geo polymer concrete pressures were obtained up to 70 MP a (N / mm2). Concrete gains its compression strength much faster and faster than conventional Portland concrete.
- Concrete strength after 24 hours was found to be more than 25 M Pa. Pressure capacity after 28 days was found to be 60 to 70 M Pa. -Ref. Paper by James Aldred and John Day and test results by SERC Chennai.
Other properties of Geo polymer Concrete:
- The reduction in dryness is very small compared to cemen. This makes it ideal for members of a dense and highly restricted concrete structure.
- It has a lower hydration temperature compared to cement.
- Fire resistance is much better than OPC-based concrete. -Reference - Paper by - James Aldred and John Day.
- This concrete measure of jas chloride permeability is 'low' to 'very low' according to ASTM 1202C. It provides better protection of metal reinforcement from corrosion compared to traditional cement mortar.
- This concrete is found to have a very high acid content when tested under 2% and 10% exposure to sulfuric acid.
Application of Geo polymer Concrete
- Applications are similar to cement cement. However, the subject has not been used extensively in various programs.
- This concrete is used for the construction of paved stones, retaining walls, water tanks, precast bridge supplies.
- Recently the world's first building to be built on earth, the University of Queensland's Global Change Institute (GCI) was built using geo polymer concrete. It is a four-story high-rise building for public use.
Ferro Cement Technique
- Mining
- Crushing, stacking, and reclaiming of uncooked substances.
- Raw meal drying, grinding, and homogenization.
- Clinkerization.
- Cement grinding and garage.
- Packing
Mining:
- The cement production system begins off evolved from the mining of uncooked substances which might be utilized in cement production, specially limestone and clays.
- A limestone quarry is with inside the plant region and a clays quarry is as a ways from the plant region as 25 km.
- The limestone is excavated from open forged mines after drilling and blasting and loaded onto dumpers which shipping the substances and sell off into hoppers of limestone crushers.
- The clays are excavated from open forged mines and loaded onto dumpers which shipping the substances and sell off into open backyard garage.
- Then it's miles transported through vehicles and unloaded into the hopper of a clay crusher.
- They are 3 varieties of clay utilized in cement production, specifically silty clay, Zafarana clay, and Kaolin.
- Other uncooked substances are used to govern the kiln feed blend design, specifically sand, and iron ore.
- The sand and iron ore are shipping from outdoor the plant (from extraordinary suppliers) through vehicles and unloaded into open backyard piles, known as sand and iron ore piles.
Crushing, stacking, and reclaiming of uncooked substances:
- The limestone is beaten with inside the first crusher known as a jaw crusher after which fed into the second one crusher known as an effect crusher with blending of clays to lessen particle length beneath 50mm.
- The discharged uncooked blend (limestone 70%, clays 30%) is fed onto a belt conveyor and exceeded throughout a bulk fabric analyzer.
- The uncooked blend is fed right into a round garage unit known as a uncooked blend garage.
- Then, the combination is extracted transversely from the stockpile through reclaimers and conveyed to a uncooked mill bin known as the uncooked blend bin for grinding.
- The different uncooked substances which might be utilized in cement production, known as additives, are excessive purity limestone, sand and iron ore.
- The excessive purity limestone is beaten in a lone in jaw crusher after which beaten extra in a secondary crusher to lessen the scale to absolutely byskip via a 50mm sieve.
- Then, it's miles stacked through a limestone stacker right into a longitudinal garage unit known as the limestone garage stockpile.
- Finally, the limestone is extracted transversely from the stockpile through reclaimer and conveyed to a uncooked mill bin, known as the limestone bin, for grinding.
Raw meal drying, grinding, and homogenization:
- The uncooked blend, excessive grade limestone, sand, and iron ore are fed from their containers to uncooked turbines, known as air swept turbines, for drying and pleasant grinding.
- The uncooked mill includes chambers, separated through diaphragm, specifically a drying chamber and a grinding chamber.
- The warm gases coming from a pre heater (pre heater / kiln machine) input the mill and are utilized in uncooked turbines for drying.
- Then the drying substances input the grinding chamber of uncooked turbines for pleasant grinding.
- The grinding chamber includes a positive amount of ball price in a extraordinary sizes starting from 30mm to 90mm.
- The warm fuel line and grinding substances mill outlet feeds to a separator which separates pleasant and path product.
- The latter, known as reject, is dispatched to the mill inlet thru an air slide for regrinding.
- The warm fuel line and pleasant substances input a multistage "cyclone" to split a pleasant substances and gases.
- The pleasant fabric, known as uncooked meal, is accrued from the multi-cyclone after which fed into an air slide for lifting known as an Aeropol.
- The warm gases with very pleasant substances input an electrostatic precipitator to split the pleasant substances from gases.
- The very pleasant substances known as pre heater dirt or electrostatic separator dirt is accrued from filters and fed into screw conveyors and are then combined with the pleasant fabric in an air slide and transported to an air elevate vessel thru air slide.
- In the air elevate, the uncooked meal is lifted to the silo through compressed air to the air slide after which saved and homogenized in a concrete silo.
- Raw meal extracted from the silo, now known as kiln feed, is fed to the pinnacle of the pre heater thru an air elevate known as the Poldos for pyro-processing.
Clinkerization:
- Cement clinker is made through pyro processing of kiln feed into the pre heater-kiln machine. The pre-heater-kiln machine includes a multi-degree cyclone
- Pre heater with 5 stages, combustion chamber, riser duct, rotary kiln, and grate cooler.
- In the pre heater, the kiln feed is preheated through warm fuel line coming from the combustion chamber and rotary kiln.
- Then the preheated kiln feed is partly calcined (made powdery) in a combustion chamber and riser duct after which absolutely calcined in a rotary kiln in addition to heated to about 1400 C to shape clinker additives C3A, C4AF, C2S, and C3S.
- The foremost supply of warmth is herbal fuel line.
- Natural fuel line is fired as a major gasoline (100 %) with inside the foremost burner rotary kiln and a 95% herbal fuel line and 5.0% heavy oil aggregate with inside the combustion chamber.
- The gasoline is used to offer the warmth required to transform the kiln feed into clinker.
- Hot clinker discharge from the kiln drops onto the grate cooler for cooling from about 1350-1450 C to about one hundred twenty C.
- In the cooler, the amount of cooling air required for clinker cooling is extracted from the environment through extraordinary cooling lovers and fed into the cooler chambers and pressurized via the cooler plate and clinker bed.
- The cooled clinker discharges from the cooler into the pan conveyor and it's miles transported to the clinker garage.
- The clinker is taken from the clinker garage to cement ball mill hoppers for cement grinding.
- Part of the recent air extracted from the cooler is applied as a secondary and tertiary air for combustion in rotary kiln and combustion chamber, respectively.
Cement grinding and garage:
- Clinker and gypsum for OPC, limestone for limestone cement, and slag for slag cement are all extracted from their respective hoppers and fed to the cement turbines.
- The ball mill grinds the feed to a pleasant powder in chambers, specifically the primary and 2d chambers.
- The chambers have a positive amount of ball price of various sizes from 17mm to ninety mm.
- The mill discharge is fed to a bucket elevator which takes the fabric to a separator which separates pleasant and coarse product.
- The latter is dispatched to the mill inlet for regrinding and the very last product is saved in concrete silos.
Packing:
- Cement extracted from silos is conveyed to the automated digital packers wherein it's miles packed in 50 kg luggage and dispatched in vehicles.
Key takeaways
1. Fibers strengthened concrete can be beneficial in which excessive tensile power and decreased cracking are proper or whilst traditional reinforcement can not be placed.
2. The clays are excavated from open forged mines and loaded onto dumpers which shipping the substances and sell off into open backyard garage.
3. Geo polymer is the name given to the Daidovits in 1978 for items that appear in chains or networks or unusual molecules.
4. Geo polymer cement concrete is made using waste materials such as fly ash and ground granulated blast furnace slag (GGBS). An ash fly is a waste product produced from a hot power plant and the granulate blast soil in a furnace is processed as a metal waste.
Fiber Reinforced concrete:
- Fiber Reinforced Concrete is composite cloth which include fibrous cloth which will increase its structural integrity.
- It consists of combinations of cement, mortar or concrete and discontinuous, discrete, uniformly dispersed appropriate fibers.
- Fibers are normally utilized in concrete to govern cracking because of plastic shrinkage and to drying shrinkage.
- They additionally lessen the permeability of concrete and consequently lessen the bleeding of water.
Advantages of Fiber-strengthened concrete:
- Fibers strengthened concrete can be beneficial in which excessive tensile power and decreased cracking are proper or whilst traditional reinforcement cannot be placed.
- It improves the effect power of concrete, limits the crack boom and ends in a extra stress potential of the composite cloth.
- For commercial projects, macro-artificial fibers are used to enhance concrete’s sturdiness.
- Made from artificial substances, those fibers are lengthy and thick in length and can be used as a substitute for bar or material reinforcement.
- Adding fibers to the concrete will enhance its freeze-thaw resistance and assist maintain the concrete sturdy and appealing for prolonged periods.
- Improve blend cohesion, enhancing pump ability over lengthy distances.
- Increase resistance to plastic shrinkage in the course of curing.
- Minimizes metallic reinforcement requirements.
- Controls the crack widths tightly, consequently enhancing sturdiness.
- Reduces segregation and bleed-water.
- FRC, longevity is ready 10 to forty instances that of undeniable concrete.
- The addition of fibers will increase fatigue power.
- Fibers boom the shear potential of strengthened concrete beams.
Application of Fiber-strengthened concrete:
The programs of fiber strengthened concrete rely on the applicator and builder in taking gain of the static and dynamic traits of the cloth. Some of its vicinity of software is-
- Runway
- Aircraft Parking
- Pavements
- Tunnel Lining
- Slope Stabilization
- Thin Shell
- Walls
- Pipes
- Manholes
- Dams
- Hydraulic Structure
- Elevated decks
- Roads
- Bridges
- Warehouse floors
Fiber Types:
Fibers for concrete are to be had in exclusive sizes and shapes.
The essential elements affecting the function of fiber-strengthened concrete are a water-cement ratio, percent of fibers, diameter and duration of fibers.
Given beneath are exclusive varieties of fiber-strengthened concrete utilized in production.
Steel Fiber Reinforced Concrete:
- Steel fiber is a metallic reinforcement. A sure quantity of metallic fiber in concrete can motive qualitative modifications in concrete’s bodily property.
- It can significantly boom resistance to cracking, effect, fatigue, and bending, tenacity, sturdiness, and others.
- For enhancing lengthy-time period behavior, improving power, longevity, and strain resistance, SFRC is being utilized in systems which includes flooring, housing, precast, bridges, tunneling, heavy-responsibility pavement, and mining.
- The varieties of metallic fibers are described via way of means of ASTM A820 are, Type I: cold-drawn cord, Type II; reduce sheet, Type III: melt-extracted, Type IV: mill reduce and Type V: changed cold-drawn cord
Properties of Fiber Reinforced Concrete:
Compressive Strength:
- The presence of fibers might also additionally regulate the failure mode of cylinders; however, the fiber impact can be minor at the development of compressive power values (zero to fifteen percentage).
Modulus of Elasticity:
- Modulus of elasticity of FRC will increase slightly with a boom with inside the fibers content material.
- It became located that for every 1 percentage boom in fiber content material through quantity there may be a boom of three percentage withinside the modulus of elasticity.
Flexure:
- The flexural power became said [2j to be improved through 2. Five instances the usage of four percentage fibers.
Toughness:
- For FRC, sturdiness is set 10 to forty instances that of undeniable concrete.
Splitting Tensile Strength:
- The presence of three percentage fiber through quantity became said to boom the splitting tensile power of mortar approximately 2.5 instances that of the unreinforced one.
Fatigue Strength:
- The addition off bers will increase fatigue power of approximately ninety percentage and 70 percentage of the static power at 2 x 106 cycles for non-opposite and complete reversal of loading, respectively.
Impact Resistance:
- The effect power for fibrous concrete is typically five to ten instances that of undeniable concrete relying at the quantity of fiber
Corrosion of Steel Fibers:
- A lO-12 months’ publicity of steel fibrous mortar to out of doors weathering in an commercial surroundings confirmed no unfavourable impact at the power properties.
- Corrosion became located to be restricted best to fibers virtually uncovered at the surface.
- Steel fibrous mortar constantly immerse in seawater for 10 years exhibited a fifteen-percentage loss in comparison to forty percentage power lower of undeniable mortar.
Flexure:
- The use of fibers in bolstered concrete flexure contributors will increase ductility, tensile power, second ability, and stiffness.
- The fibers enhance crack manage and keep publish cracking structural integrity of contributors.
Torsion:
- The use of fiber do away with the unexpected failure feature of undeniable concrete beams.
- It will increase stiffness, torsion power, ductility, rotational ability, and the range of cracks with much less crack width.
Shear:
- Addition of fibers will increase shear ability of bolstered concrete beams as much as a hundred percentage.
- Addition of randomly allotted fibers will increase shear-friction power, the primary crack power, and final power.
Polymer concrete is an alternative to portland cement that is used to bond a mixture of aggregates together with epoxy binders. It is used in construction projects to provide added strength and can be modified with a range of resins. Polymer concrete provides very good resistance against corrosion and minimal chemical reactivity.
A polyester, vinyl resin or epoxy resin is often used to manufacture polymer concrete. This allows the concrete to be poured, then hardened. Polymer concrete cures through a chemical reaction with the polymer material. This type concrete is ideal for reaching areas that are not easily accessible.
Polymer concrete offers a range of benefits depending on the resin used to make it. Acrylic resins set quickly and offer resistance to harsh weather conditions, while epoxies create a strong material with little curing shrinkage. Furan resins can withstand high temperatures, and polyurea resins can replace formaldehydes or other hazardous compounds for construction purposes.
- Chemical admixtures are the components in concrete aside from port land cement, water, and combination which might be introduced to the combination at once earlier than or for the duration of blending.
- Producers use admixtures generally to lessen the value of concrete construction; to adjust the residences of hardened concrete; to make sure the best of concrete for the duration of blending, transporting, setting, and curing; and to conquer sure emergencies for the duration of concrete operations.
- Successful use of admixtures relies upon on using suitable techniques of batching and concreting.
- Most admixtures are provided in ready-to-use liquid shape and are introduced to the concrete on the plant or on the jobsite.
- Certain admixtures, along with pigments, expansive agents, and pumping aids are used most effective in extraordinarily small quantities and are commonly batched with the aid of using hand from premeasured containers.
- The effectiveness of an admixture relies upon on numerous elements including: kind and quantity of cement, water content material, blending time, stoop, and temperatures of the concrete and air.
- Sometimes, results much like the ones done thru the addition of admixtures may be done with the aid of using changing the concrete aggregate-decreasing the water-cement ratio, including extra cement, the usage of a extraordinary sort of cement, or converting the combination and combination gradation.
- Admixtures are classed consistent with characteristic. There are 5 wonderful lessons of chemical admixtures: air-entraining, water-decreasing, retarding, accelerating, and plasticizers (super plasticizers).
- All different styles of admixtures fall into the strong point class whose capabilities encompass corrosion inhibition, shrinkage reduction, alkali-silica reactivity reduction, workability enhancement, bonding, damp proofing, and coloring.
- Air-entraining admixtures, which can be used to purposely location microscopic air bubbles into the concrete, are mentioned extra completely in Air-Entrained Concrete.
- Water-decreasing admixtures commonly lessen the desired water content material for a concrete aggregate with the aid of using approximately five to ten percentage .
- Consequently, concrete containing a water-decreasing admixture wishes much less water to attain a required stoop than untreated concrete.
- The dealt with concrete could have a decrease water-cement ratio. This commonly shows that a better energy concrete may be produced without growing the quantity of cement.
- Recent improvements in admixture generation have caused the improvement of mid-variety water reducers.
- These admixtures lessen water content material with the aid of using as a minimum eight percentage and have a tendency to be extra solid over a much broader variety of temperatures.
- Mid-variety water reducers offer extra regular placing instances than popular water reducers.
- Retarding admixtures, which gradual the placing charge of concrete, are used to counteract the accelerating impact of warm climate on concrete placing.
- High temperatures frequently reason an accelerated charge of hardening which makes setting and completing difficult.
- Retarders maintain concrete manageable for the duration of placement and put off the preliminary set of concrete.
- Most retarders additionally characteristic as water reducers and can entrain a few air in concrete.
- Accelerating admixtures growth the charge of early energy improvement, lessen the time required for correct curing and protection, and accelerate the begin of completing operations.
- Accelerating admixtures are specifically beneficial for enhancing the residences of concrete in bloodless climate.
- Super plasticizers, additionally called plasticizers or excessive-variety water reducers (HRWR), lessen water content material with the aid of using 12 to 30 percentage and may be introduced to concrete with a low-to-ordinary stoop and water-cement ratio to make excessive-stoop flowing concrete.
- Flowing concrete is a extraordinarily fluid however manageable concrete that may be located with very little vibration or compaction.
- The impact of super plasticizers lasts most effective 30 to 60 minutes, relying at the emblem and dosage charge, and is observed with the aid of using a speedy loss in workability.
- As a end result of the stoop loss, super plasticizers are commonly introduced to concrete on the jobsite.
- Corrosion-inhibiting admixtures fall into the strong point admixture class and are used to gradual corrosion of reinforcing metal in concrete.
- Corrosion inhibitors may be used as a shielding method for concrete structures, along with marine facilities, motorway bridges, and parking garages, in order to be uncovered to excessive concentrations of chloride.
- Other strong point admixtures encompass shrinkage-decreasing admixtures and alkali-silica reactivity inhibitors.
- The shrinkage reducers are used to govern drying shrinkage and reduce cracking, even as ASR inhibitors manipulate sturdiness troubles related to alkali-silica reactivity.
Mechanism of Chemical Admixture:
- Concrete admixtures are used to steer concrete hardening specially with inside the early Phase of hydration.
- By including very small quantities of admixtures, homes of sparkling concrete may be inspired in a huge range.
- The hydraulic response may be elevated or retarded the use of suitable dealers and workability may be advanced the use of super plasticizers.
- Many mechanisms had been cautioned to provide an explanation for these kinds of effects .
- There continues to be no complete know-how of hydration mechanisms together with these kinds of phenomena at once.
- In this contribution emphasis will be positioned at power differences occuring at some point of physico-chemical methods of cement hydration.
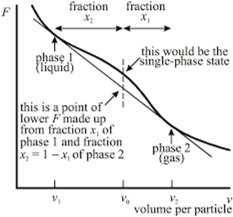
Fig no 37. Mechanisms of plasticiser
- Cement hydration evolves in a manner which in corporate segment transitions.
- In touch with water, Meta stable stable cement stages dissolve into an aqueous solution.
- This dissociation ends in an boom of Ca O attention as much as 20-forty m mol/I with inside the first hours of C3S hydration .
- Reaching a country of super saturation with inside the pore water solution, crystallization into strong and stable CSH-merchandise can follow.
- In each segment transitions a unexpected quantity extrade occurs, as a consequence of adjustments in sure forces.
- During the solvation procedure a stable-fluid section transition results in an boom in quantity (swelling).
- Crystallization entails a quantity contraction (shrinkage) that is better in absolute phrases than the preceding quantity swelling.
- A shrinkage quantity stays after fluid-stable transition and may be measured volumetrically or gravimetrically.
- Both tactics engage simultaneously, however with unique velocities.
- Hydration may be visible as a solvation-crystallization step and become first defined via way of means of Le Chatelier.
Key takeaways
- Super plasticizers, additionally called plasticizers or excessive-variety water reducers (HRWR), lessen water content material with the aid of using 12 to 30 percentage and may be introduced to concrete with a low-to-ordinary stoop and water-cement ratio to make excessive-stoop flowing concrete.
- During the solvation procedure a stable-fluid section transition results in an boom in quantity (swelling).
Deterioration - Durability
- Durability is the capacity to remaining a long term without massive deterioration.
- A long lasting cloth allows the surroundings with the aid of using keeping sources and lowering wastes and the environmental affect of restore and substitute.
- The manufacturing of substitute constructing substances depletes herbal sources and may produce air and water pollution.
- Concrete resists weathering action, chemical attack, and abrasion even as retaining its favored engineering houses.
- Different concretes require extraordinary levels of sturdiness relying at the publicity surroundings and the houses favored.
- Concrete ingredients, their proportioning, interactions among them, setting and curing practices, and the provider surroundings decide the remaining sturdiness and lifestyles of the concrete.
- The layout provider lifestyles of maximum homes regularly 30 years, despite the fact that homes regularly remaining 50 to one hundred years or longer.
- Because in their sturdiness, maximum concrete and masonry homes are demolished because of useful obsolescence in place of deterioration.
- However, a concrete shell or shape may be repurposed if a constructing use or characteristic adjustments or whilst a constructing indoors is renovated.
- Concrete, as a structural cloth and because the constructing outside skin, has the capacity to face up to nature’s ordinary deteriorating mechanisms in addition to herbal disasters.
- Durability of concrete can be described because the capacity of concrete to withstand weathering action, chemical attack, and abrasion even as retaining its favored engineering houses.
- Different concretes require extraordinary levels of sturdiness relying at the publicity surroundings and houses favored.
- For example, concrete uncovered to tidal seawater could have extraordinary necessities than an indoor concrete floor.
Key takeaways
- Durability is the capacity to remaining a long term without massive deterioration.
- A long lasting cloth allows the surroundings with the aid of using keeping sources and lowering wastes and the environmental affect of restore and substitute.
Factor affecting the durability of concrete
The following are the factors that affect the strength of concrete.
- Cement content
- Aggregate quality
- Water Quality
- Concrete compaction
- Curing period
- Permeability
- Moisture
- Temperature
- Abrasion
- Carbonation
01. Cement content
- The amount of cement used in concrete mixing is a major factor affecting the durability of concrete.
- If the cement content used is less than required, the cement water level
- Decreases and the performance of concrete also decreases.
- Adding too much water to this concrete mix causes the formation of capillary voids that will make the concrete a resilient one inviting decay.
- Adding excess cement can cause problems such as stopping the shrinkage. Alkali-silica reactions may also eventually affect the strength of the concrete.
02. Aggregate Quality
- Applying a good quality mix to the concrete mix will definitely increase the strength of the concrete.
- The shape of the composite particles should be small and circular. Flaky and compact assembly can affect the performance of the new concrete making it easier to enter where it can open and will work with less power.
- Bad angular compilation is recommended but requires a lot of cement content to get a good binding. Yes, structural composites should be used to achieve greater concrete mixing.
- Determination of the combined moisture content should be done beforehand, otherwise, it can create a more usable concrete mix and make it worse.
03. Water Quality
- The water used in the concrete mix also affects the strength of the concrete. Usually, drinking water is recommended to make concrete. The pH of the water used will be in grades 7 to 8 only.
- Water should be free and clean from fats, acids, alkalis, sugar, organic salts etc.
- Contamination in the water can lead to metal corrosion or corrosion due to different chemical attacks of concrete.
04. Concrete compaction
- Care should be taken during the installation of the concrete. It is important to glue the local concrete without splitting.
- Adequately compacted concrete contains a number of air gaps in it that reduce the strength of the concrete and its strength and will make it stronger.
05. Curing period
- Proper treatment should be done in the early stages of concrete reinforcement as it will lead to the reinforcement of the concrete.
- Adequate treatment can lead to the formation of cracks due to plastic shrinkage, dehydration, heat effects etc. due to reduced stiffness.
06. Permeability
- Due to the overcrowding of the concrete, it expands and leads to the formation of cracks and eventually, the deterioration of the concrete occurs.
- Concrete usually consists of small gel pores and capillary cavities. However, gel pores prevent water ingress because they are too small.
- Capillary holes in concrete are facing, which are formed due to the high water content of concrete
- To prevent intrusion, a very small amount of cement water should be used.
- Using a small amount of pozzolanic material also helps to reduce penetration
07. Moisture
- The moisture found in the atmosphere will also affect the strength of concrete structures.
- Concrete moisture is responsible for Efflorescence, which will convert salt into soluble solutions and when evaporated salt becomes brighter and appears on the concrete surface.
- This will definitely damage the concrete structure and the durability will decrease.
08. Temperature
- When new concrete is exposed to high temperatures, the hydration level is affected and strength and durability are reduced.
- Concrete materials have different temperature coefficients, so at higher temperatures, spelling and damage to concrete are possible.
09. Abrasion
- Concrete damage also occurs due to severe facial injuries.
- When concrete is exposed to fast-moving water, steel tires, floating ice that wears continuously on the surface occur and stiffness is affected.
- The higher the pressure of the concrete pressure the higher it will be to resist the abrasion
10. Carbonation
- When wet concrete is exposed to the atmosphere, carbon dioxide in the atmosphere reacts with concrete and reduces the pH of the concrete by reacting with CaO in concrete.
- When the pH value of concrete is reduced to 10 or 9 or more, it releases its alkali. Because it will not be able to protect the metal bars beneath it. Due to rust, rust will build up around the bar which has led to an increase in the volume of the bar. This will create cracks in the concrete. Cracking will continue to promote moisture and CO2 which will lead to the loss of alkali. So bad cycles occur, eventually causing the concrete to crack with delamination and spraying of the concrete if not done in time, the bars will start to lose their place and thus become stronger. Most of the building in modern times, suffers from this, and buildings that were supposed to be 100 years old have been extensively renovated at some point within ten years. The process of rust therefore places on the existing strength of the concrete. The rust of the reinforcement causes cracks in the solid concrete and deterioration occurs.
Key takeaways
The following are the factors that affect the strength of concrete.
- Cement content
- Aggregate quality
- Water Quality
- Concrete compaction
- Curing period
- Permeability
- Moisture
- Temperature
- Abrasion
- Carbonation
Permeability
- Definition: the capacity of a given concrete to allow drinks or gases to by skip through.- ACI Concrete Terminology
- Permeability is a degree of the quantity of water, air, and different materials which could input the concrete matrix.
- Concrete consists of pores which could permit those materials to go into or depart.
- Permeability of concrete may be a number one motive for concrete deterioration because of reinforcing metal corrosion and different deterioration mechanisms.
- On a macro scale, permeability additionally refers to “porous” slabs used to empty pavements, sidewalks, and parking regions of water, putting off the want for drainage slope, systems, and piping.
- This technology—every now and then called “no-fines concrete”—is gaining reputation once more with the preference to lessen floor run-off from pavements, sidewalks, and parking regions.
- Permeability of cement mortar or concrete is of unique importance in systems which might be meant to hold water or which come into touch with water.
- Besides useful considerations, permeability is likewise in detail associated with the sturdiness of concrete, mainly its resistance, towards revolutionary deterioration below publicity to extreme climate, and leaching because of extended seepage of water, specially whilst it consists of competitive gases or minerals in solution.
- The willpower of the permeability traits of mortar and concrete, therefore, assumes widespread importance.
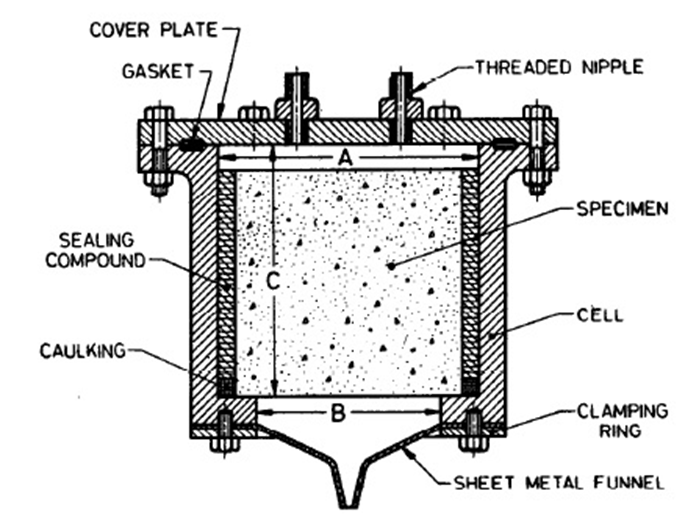
Fig no 38. Concrete permeability apparatus
- The permeability shall encompass a steel cylinder for containing the specimen.
- A rubber or neoprene O-ring or different appropriate gasket, seated in matching grooves will be used among the quilt plate to render the joint water-tight.
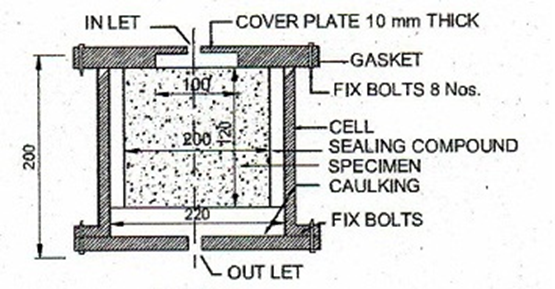
Fig no 39. Water Reservoir in Permeability Apparatus
- A appropriate reservoir may also encompass a duration of steel pipe, 50 to a hundred mm in diameter and approximately 500 mm long.
- The reservoir will be equipped with a graduated facet arm gauge-glass, and the vital fittings and valves for admitting water and compressed air and for draining, bleeding and connection to the permeability.
Procedure:
Preparation of Test Specimen
- Test specimen of 2 hundred mm diameter and a hundred and twenty mm thick will be used. After 24 hrs of casting of specimen, crucial round place of a hundred mm diameter will be roughened with a twine brush at the facet on which the water stress is to be carried out. The un roughened a part of the facet of the check specimen that's subjected to water stress is to be sealed with coats of cement water paste (W/C = 0.4).
Test Procedure
- After 28 days curing, check specimen is equipped right into a check equipment in which the water stress acts on the specified face and final faces may be observed.
- At first, a stress of one Bar is carried out for forty eight hours, then three bar for twenty-four hours and seven Bar for twenty-four hours.
- After the check, the specimen is break up with inside the center with the aid of using the compression carried out on spherical metal bars mendacity on contrary sides, above and below. The facet after the check specimen uncovered to the water stress ought to face downwards.
Observation:
- The finest water penetration depth, is taken because the common cost of the finest penetration depths on 3 check specimen.
Key takeaways
1. A rubber or neoprene O-ring or different appropriate gasket, seated in matching grooves will be used among the quilt plate to render the joint water-tight.
Chloride Attack
- Chloride Attack Chloride attack is one of the most important factors when working with concrete strength. It mainly causes corrosion. Statistics have shown that more than 40% of structural failures are due to metal corrosion.
- Concrete and the penetration layer with a strong alkaline Ca (OH) 2 (pH approximately 13) prevents metal corrosion by forming a thin film to protect the iron oxide on the surface of the metal.
- This protection is known as inaction. If concrete can penetrate in such a way that the dissolved chloride enters until it hardens and water and oxygen are also present, then corrosion of the metal will occur. This layer can also be lost due to carbonation.
- Chloride enters the concrete from cement, water, and is sometimes mixed from tips. This can come in increments from nature when the concrete is filled. The Bureau of Indian Standard specified the high chloride content in cement as 0.1%.
- The amount of chloride needed to start corrosion depends on the pH value of the pore water in the concrete. A pH value below11.5 corrosion is possible without the presence of chloride.
Key takeaways
- Chloride Attack Chloride attack is one of the most important factors when working with concrete strength. It mainly causes corrosion corrosion. Statistics have shown that more than 40% of structural failures are due to metal corrosion.
- Concrete and the penetration layer with a strong alkaline Ca (OH) 2 (pH approximately 13) prevents metal corrosion by forming a thin film to protect the iron oxide on the surface of the metal.
Corrosion of Reinforcement, Carbonation of Concrete
Corrosion of Reinforcement
- Concrete, in itself, has a low strength. To increase the strength of the concrete, the steel hardens. Steel bars are inserted inside the weight of the concrete. These steel bearings carry a high load-bearing capacity applied to concrete.
- Concrete makes metal bars obsolete due to the alkaline environment, thus preventing them from cracking. However, for a variety of reasons, metal bars can be pulled longer. And as a result of the rust of the steel bars, various weaknesses appear in the concrete structure, which could eventually collapse if not properly maintained.
- The rust of steel reinforcement bars is actually a way of responding to electricity. Small anodes and cathodes are formed and the flow of ions between these two electrodes leads to the breakdown of metal bars. There are two types of corrosion detected in steel reinforcement bars:
- Metal Rust - In small cracks in a concrete structure, solutions may remain. Anodes and cathodes can be formed within solutions due to the uneven reaction of solute ions over the volume of the solution. The flow of ions is caused by these electrodes, thus causing a gradual corrosion.
- Rust corrosion - Related to the removal of small areas in the steel bars of the reinforcement. This type of rust is extremely well-formed and small holes or holes are made in the metal.
Causes of Stainless-Steel Rust
- Corruption of steel reinforcement barriers may be due to the local failure of the metal film of chloride ions or the general failure of the concrete to malfunction due to the carbon dioxide reaction from the atmosphere. The main factors facing corrosion of reinforcement barriers are:
- Loss of alkalinity due to carbonation - When a metal surface is left unprotected in the atmosphere, corrosion begins to form on the surface of the metal and then slowly moves away.
- Loss of alkalinity due to chlorides - Chloride ions tend to remove metal energy by destroying concrete.
- Cracking of Concrete - Cracking can expose metal bars in the atmosphere and increase liquidity.
- Moisture Methods - Regular wetting of concrete can lead to water reaching the metal bars by dispersing through the pore structure of the concrete or existing cracks in the concrete. Rust of steel bars follows after that.
- Insufficient cover: Insufficient size of concrete cover.
- Metal Rust due to Improper Cover
- Damaged steel reinforcement may occur due to insufficient concrete cover
Effects of Stainless-Steel Rust
When steel bars begin to break, reinforced concrete joints begin to break down through the following stages:
- White spot formation - Atmospheric carbon dioxide reacts with calcium hydroxide present in the reduction of cement forming calcium carbonate. This calcium carbonate is treated with moisture and deposited on the surface of the white-formed concrete.
- Dirty stains by reinforcement - When the metal bars begin to deteriorate, a layer of iron oxide forms in it. This metal oxide is also transferred to the surface of the concrete with moisture.
- Formations of cracks - Rust products take on a larger volume than the original. So they put pressure on the concrete and it cracks. In the event of a lot of rust, many wide cracks are formed.
- Disintegration of concrete cover - Due to the loss of bond between concrete and steel, concrete begins to form many layers of scales and then peels off. Metal bars are also reduced in size.
- Cracking of bars - Due to the decrease in the size of the steel bars, they eventually break. Also, there is a significant reduction in the size of the main bars.
- Piercing of bars - The collapse of the concrete cover and the cracking of the bars resulted in the collapse of the main bars. This floods the concrete area and eventually the entire building collapses.
How to Avoid Rusting Metal Rust
- The rust of steel reinforcement bars can be prevented or at least delayed by good measures. Also, damaged steel bars can be repaired and the concrete structure can be properly restored. Some steps are given below:
- Providing Sufficient Concrete Cover: A good amount of concrete cover should be provided in addition to the reinforcing steel bars. This ensures proper care of the alkaline type inside the concrete and the passage of the steel bars. Metal bars should be placed precisely in place
- Use of Quality Concrete: High quality concrete should be used. It helps to maintain an alkaline environment. In concrete, a water level of 0.4 or less should be maintained. Too much water can damage metal bars
- Compact Compaction fo Concrete: Concrete must be thoroughly mixed so that no air gaps or pockets are present.
- Use of FBE Bonds: Fusion Bonded Epoxy Coating (FBEC) can be used on metal bales to prevent corrosion. Epoxy powder is still electrically distributed in metal barns. The powder melts and flows over the bars as it heats up, forming a protective coating. It is a thermoset polymer coating because the use of heat will not melt the wear. Apart from the rebar it also has extensive function in pipeline construction
- Use of Cement-Based Polymers: Cement-based polymers can be used in concrete to increase their protection against corrosion. Cement-based polymers act as a bond in concrete. They also increase the strength, durability and melting of concrete
Carbonation of Concrete
- Carbonation of concrete is associated with corrosion of steel reinforcement and shrinkage. However, it also increases both the compression strength and the strength of the concrete, so not all of its effects on concrete are bad.
- Carbonation is the result of the decomposition of CO2 in pore fluid in concrete and this reacts with calcium from calcium hydroxide and calcium silicate hydrate to form calcite (CaCO3). Aragonite can form in hot climates.
- Within a few hours, or a day or two in total, the new concrete will be processed by CO2 in the air. Gradually, the process penetrates deeper into the concrete at a rate equal to the square root of time. After a year or more it is likely to reach a depth of about 1 mm with dense low-penetration concrete made of low water / cement, or up to 5 mm or more of high-density and permitted concrete using high water / cement scale.
Carbonation determination
- The affected depth from the concrete surface can be easily indicated by the use of a phenolphthalein indicator solution. This is available from chemical suppliers. Phenolphthalein is a white or pale yellow with a crystal. Use as a solvent dissolve in a suitable solution such as isopropyl alcohol (isopropanol) by 1%.
- The indicator has not changed color near the upper and lower extremities, suggesting that these regions near the surface be carbonated at a depth of at least 4 mm from the top to the top and 6 mm from the bottom.
- When the index turns purple - in the middle of the slide - the pH of the pore fluid anchor remains high (above 8.6, about 10). Whether you are pasting the cement here is not completely illuminated, despite the strong purple color; a complete test will require very little testing.
- The index was not applied to the concrete to the right of this image so the concrete here retains its original color.
- The depth of carbonation is about the same as the square root of time. For example, if the depth of carbon is 1mm in one-year-old concrete, it will be about 3mm after 9, 5mm after 25 years and 10mm after 100 years.
Key takeaways
- Carbonation of concrete is associated with corrosion of steel reinforcement and shrinkage. However, it also increases both the compression strength and the strength of the concrete, so not all of its effects on concrete are bad.
- Concrete, in itself, has a low strength. To increase the strength of the concrete, the steel hardens. Steel bars are inserted inside the weight of the concrete. These steel bearings carry a high load-bearing capacity applied to concrete.
- Concrete makes metal bars obsolete due to the alkaline environment, thus preventing them from cracking. However, for a variety of reasons, metal bars can be pulled longer. And as a result of the rust of the steel bars, various weaknesses appear in the concrete structure, which could eventually collapse if not properly maintained.
Repair - Symptoms and Diagnosis of Distress
- The rapid industrialization of India after independence required the transportation of goods and services and led to the construction of a network of wide roads with built-in bridges and flyovers.
- Many of the existing bridges show signs of stress within their work life built in many cases in the 10-20 years of construction in India and many other countries.
- The collapse of the I-35W bridge over the Mississippi River in the United States of America in August 2007 has attracted the attention of international media. In India, the collapse of the Mandovi Bridge in Goa in 1986 (after 16 years of service) and the great tribulation at the Zuari bridge (rebuilt in 2000 by an international consultant) in Goa and many other bridges such as Khalghat and Borad Bridge on NH3 (Route) Agra to Mumbai) due to environmental constraints is attracting the attention of transport authorities and the scientific community to transform the operational bridge management system.
- The cause of the distress, the level of grief and the reduction in the capacity of the bridge can be ensured in order to further the necessary adjustments to ensure the safety of the bridge during their operation.
- An assessment of the pressure and load capacity of existing bridges and to improve the load capacity is required while upgrading highways. India has already implemented the consolidation and use of four 7000 Km of highways under the Golden Quadrilateral program where the strengthening / replacement of many existing bridges was required.
- Various causes of damage to reinforced concrete bridges are low construction standards, rust of steel on reinforced concrete bridges and pre-reinforced concrete bridges, improper shape and details of normal loads and seismic forces, improper operation of bearings etc. a number of case studies have been reported in the literature on reinforced concrete damage and compacted concrete bridges during earthquakes and the reinforcement of reinforced and compressed concrete bridges due to nature and other loads.
- A concerted effort has been made to review critical documentation of reinforced concrete damage and pre-pressure concrete bridges and repair / rehabilitation strategies based on information from bridge reconstruction projects in which the authors were involved.
Causes of distress
- Relationship problems such as conflicts, illness / death of a loved one, divorce, abuse, partner, etc.
- Financial difficulties
- Environmental remediation
- Educational difficulties
- Time management and organizational complexity
- Anxiety
- Depression
- An abusive event
- Drug abuse
Diagnosis of distress
Sometimes the cause of grief is known e.g. Suffering during an earthquake, impact and explosion is known perhaps the active load exceeds the intended load but it is often difficult to find the real cause of grief where many variables are affected e.g. Poor construction quality (faulty details, faults and performance), shrinkage, penetration, rust consolidation etc. Following a test may be necessary to determine the cause and degree of grief.
- Determination of compression strength from NDT and cores of concrete
- Strategies for detecting explosions
- Signature / Vibration Analysis
- Download tests to find deviations / issues and distribute the load
- Rust studies (pH, depth of carbon, chloride)
- Deviation / disposal slopes from Instrumented Bridge
Key takeaways
- The rapid industrialization of India after independence required the transportation of goods and services and led to the construction of a network of wide roads with built-in bridges and flyovers.
- Many of the existing bridges show signs of stress within their work life built in many cases in the 10-20 years of construction in India and many other countries.
Selection Of Repair Procedure
Structure
- Structural repairs include using epoxy frames to bind or bond concrete together. Epoxy repair not only repairs the sealing cracks but also restores the strength and durability of the concrete. Use epoxy to repair dormant cracks only. Fixing functional cracks with epoxy often leads to a new formation near the original, epoxied fragment.
- Epoxy injection is a common way to inject epoxy into cracks, especially in direct and indirect areas. But gravity filling works well and is a common way to apply epoxy to flatwork cracks or to direct surfaces.
- The filling of gravity consists of pouring low-viscosity epoxy into the cracks that have been signed or distributed and allowed the gravitational force to pull the epoxy down the cracks. Viscosity resistance to fluid flow is measured in centipoises (cps). Decreased viscosity value, less (runnier) significant. Grade I and II epoxies have viscosities of less than 20 cps and between 20 and 100 cps, respectively.
- For comparison, the viscosities of other common beverages are: water - 1 cps, milk - 3 cps, anti-freeze - 15 cps, maple syrup - 150 to 200 cps, and honey -3000 cps. Low viscosities are required for solid cracks. Otherwise, the repair material will be too large to penetrate and flow into the crack.
- Epoxies were cured or hardened due to the chemical reaction between the frame and the hardener. Chemical reactions are rapid at high temperatures. Epoxies are obtained by different injections or by temperature treatments so chemical reactions are less rapid or slow (Type A, less than 40º F; Type B, 40º F to 60º F; and type C, more than 60º F).
- With the adjustment of gravity filling culture, consider the depth and depth, epoxy viscosity, and temperature input when choosing the distance and type of epoxy. Otherwise, the epoxy can be very strong or very hard to penetrate or it can just run between the river and the pool under the slide.
Sealing and filling
- Sealing and filling of non-construction repairs. However, some repair materials include cracked surfaces and can have a strong impact that can cause cracking of the material and concrete in the event of a major crack movement.
- Typical sealants and internal fixing fillers include semi-rigid epoxies, hybrid polyurethanes and polyureas, and polymer mortar. Polyurethanes and silicones are common labels used for exterior repairs.
- Usually, sealants are flexible or elastomeric materials; and the fillers are very hard so the fixing materials support the edges of the cracks to avoid collapse or damage under load. When heavy traffic is exposed to heavy wheels, composite fillers or special cracks with about 80 Shore A Hardness should be used.
- Unfortunately, there is a trade-off to increase the complexity of explosive repair materials. As the repair material gets harder, it becomes much thinner and does not tolerate cracked movement. For example, semi-rigid epoxies usually have a hardness of about 90 and an extension value of 50%; whereas, silicone sealants have a hardness of about 5 and an extension value of 1400%. Therefore, when choosing a fix, consider the expected movement of the comparison and the need to support the edges of the cracks.
- For effective cracking with the expected cracking motion, use elastomeric sealants or sealants with sufficient elastic properties, to see that the trade-off will be a little support for the fracture edges. For cracks exposed to heavy-duty traffic, use hard materials that support the edges of the cracks. But understand that these things do not tolerate the movement of cracks.
- If you are using elastomeric sealants in active cracks, always seal the sealant with a saw or by moving the track as recommended by the repairman. Without a dam, there would not be enough to tolerate future fracture movements. Expansion structures reported by manufacturers are based on the size of the recommended lakes or, in particular, the width and depth of the dam.
- Of course, cutting or scraping increases the width of the crack and makes crack repairs more noticeable. For cosmetic repairs in colored or decorative flats where cracks lie or are well established, do not see or move the sealant or filler dam. Instead, choose a low viscosity cracker (less than 100 cps) and small injection tips for cracks to fill gravity.
- Dams are not required. But in the event of a fracture movement, the cracking of the repair material or concrete may occur due to the small diameter of the depth of the material. Also, manufacturers now offer many of these low viscosity fixes in a variety of colors or offer color production recommendations and textures similar to concrete concrete surfaces.
- Before fixing your next explosion, do a crack test and establish repair targets. Decide what kind of adjustment is needed. Options include structural repairs using epoxy, route fixes and seal applications using flexible sealant to hold future cracks, and solid or durable repairs that fill the edges of cracks, with or without. Also, set cosmetic requirements. After selecting the fix and procedure, follow the manufacturer's recommendations.
Key takeaways
- Structure
Structural repairs include using epoxy frames to bind or bond concrete together. Epoxy repair not only repairs the sealing cracks but also restores the strength and durability of the concrete. Use epoxy to repair dormant cracks only. Fixing functional cracks with epoxy often leads to a new formation near the original, epoxied fragment.
2. Sealing and filling
Sealing and filling of non-construction repairs. However, some repair materials include cracked surfaces and can have a strong impact that can cause cracking of the material and concrete in the event of a major crack movement.
Repair of defects using various type and techniques - shortcrete and grouting
Shortcrete
- Shotcrete or sprayed concrete is concrete or mortar conveyed thru a hose and pneumatically projected at excessive pace onto a floor, as a production method, first utilized in 1914.
- It is usually strengthened with the aid of using traditional metallic rods, metallic mesh, or fibers.
- Properly carried out shotcrete is a structurally sound and sturdy production cloth which well-known shows terrific bonding traits to present concrete, rock, metallic, and plenty of different materials.
- It may have excessive strength, low absorption, correct resistance to weathering, and resistance to a few varieties of chemical attack.
- Many of the bodily residences of sound shotcrete are similar or advanced to the ones of traditional concrete or mortar having the equal composition.
- Improperly carried out shotcrete can also additionally create situations a lot worse than the untreated condition.
Advantages of shotcrete:
- Shotcrete is utilized in lieu of traditional concrete, in maximum instances, for motives of fee or convenience.
- Shotcrete is fine in conditions whilst formwork is fee prohibitive or impractical and wherein paperwork may be decreased or eliminated, get entry to to the paintings place is difficult, skinny layers or variable thicknesses are required, or ordinary casting strategies cannot be employed.
- Additional financial savings are feasible due to the fact shotcrete calls for handiest a small, transportable plant for manufacture and placement.
- Shotcreting operations can regularly be executed in regions of restrained get entry to to make upkeep to structures.
Grouting
- Grout is usually a mixture of cement, sand, and water or chemicals used to fill gaps.
- They are used to repair concrete cracks, to fill gaps and gaps in tiles, to fill gaps and waterproofing, and to strengthen the soil.
- It is also used to provide additional power to load-bearing structures. It basically involves the process of injecting something that can be pumped into a building to change its body structures.
- There are different types of grinding, cement grinding, chemical grinding, and bituminous grating, depending on the material used.
- Frames are also sometimes used as grout materials. A mortar is often used to fill cracks and gaps in soil or rock.
What is Grouting
- Also, it is used to stabilize the soil and keep it out.
- Cracking is used for a variety of purposes such as water repair, standing on immersed structures such as ditches, tunnels, etc., filling in the gaps between tiles and stabilizing the soil.
- Here we have provided details on the type of grouts used to repair cracks.
Advantage of Grouting Includes:
- This can be done in almost any soil condition
- It does not vibrate and can be controlled to avoid structural damage
- Development of underground structures can be measured
- It is very useful for limited space and low head items
- It is used to install slab jacking that lifts or measures the crippled foundation
- It can be installed near existing walls
- It can be used to control the flow of water, groundwater flow, and hazardous waste materials.
Many Different Types of Grouting Materials:
- Stopping cement
- Chemical Grouting
- Bentonite grouting
- The amber is growing
- Bituminous Grouting
Key takeaways
- SHORTCRETE
Shotcrete or sprayed concrete is concrete or mortar conveyed thru a hose and pneumatically projected at excessive pace onto a floor, as a production method, first utilized in 1914. It is usually strengthened with the aid of using traditional metallic rods, metallic mesh, or fibers.
2. GROUTING
Grout is usually a mixture of cement, sand, and water or chemicals used to fill gaps. They are used to repair concrete cracks, to fill gaps and gaps in tiles, to fill gaps and waterproofing, and to strengthen the soil.
Introduction of retrofitting of Concrete Structure by Fiber Reinforced Polymer (FPP), Polymer Impregnated Concrete
Fiber Reinforced Polymer
- Fiber-reinforced polymer (FRP), also fiber-reinforced plastic, is a composite made of polymer matrix reinforced with fibers. Threads are usually glass, carbon, or aramid, although other fibers such as paper or wood or asbestos have sometimes been used. The polymer is usually epoxy, vinylester or polyester thermosetting plastic, and phenol formaldehyde frames are still active. FRPs are widely used in the aerospace, automotive, marine and construction industries.
- Composite materials are made of building materials or naturally made from two or more materials that have a structure with very different physical or chemical properties that are always different and distinct from the finished structure. Most compounds have strong, strong fibers in a weak and strong matrix. The goal is usually to make the part stronger and stronger, usually with a lower volume.
- Commercial materials usually contain glass or carbon fibers in a matrix based on thermosetting polymers, such as epoxy or polyester resins. In some cases, thermoplastic polymers may be preferred, as they form after the first production. There are additional stages of integration where the matrix is metal or ceramic. For the most part, these are still in the development phase, and the problems of high production costs have yet to be overcome [1]. Moreover, in these compounds the reasons for adding fibers (or, in some cases, particles) are often complex; for example, improvements may be required in penetration, wear, cracking, heat stabilization, etc.
- Fiber-reinforced polymer (FRP) is a compound used in almost every type of high-tech engineering facility, with its use from aircraft, helicopters and spacecraft to boats, ships and marine systems as well as automobiles, sports equipment, repair equipment chemicals and public infrastructure such as bridges and buildings.
- The use of FRP compounds continues to grow at an impressive rate as these materials are widely used in their existing markets and are being developed in brand new markets such as biomedical devices and social structures. An important factor contributing to the increased use of compounds over the years has been the development of new types of FRP materials.
- This includes the development of high-resin applications and new reinforcement styles, such as carbon nanotubes and nanoparticles. The book provides a timely account of fiction, mechanical properties, delamination resistance, impact tolerance and the use of 3D FRP compounds.
- Polymers reinforced polymer composites (FRPs) are increasingly being considered for the development and / or replacement of structural components or systems consisting of traditional engineering materials, namely concrete and steel. FRP compounds are simple, non-destructive, show a certain high strength and direct durability, are easily constructed, and can be customized to meet operational requirements.
- Because of these beneficial features, FRP compounds have been incorporated into the construction and renovation of buildings using their reinforcement in concrete, blocks, modular structures, formwork, and external reinforcement for seismic reinforcement and development.
- The effectiveness of Fiber Reinforced Polymer (FRP) reinforcement in concrete structures such as replacement of steel bars or pre-pressurized muscles has been extensively studied in many research laboratories and professional organizations around the world. FRP reinforcement offers many benefits such as corrosion resistance, non-magnetic properties, very strong, lightweight and easy to handle.
- However, they usually have a direct response to stiffness to the point of failure (defined as damaging failure) and poor resistance to friction or shear. They are also less resistant to fire and when exposed to high temperatures. They release vital energy as they bend, and they are sensitive to the effects of pressure fractures. In addition, their cost, whether considered for each weight or on the basis of strength-bearing capacity, is relatively high compared with conventional steel reinforcement bars or pressure straps.
- From a structural engineering perspective, the most serious problems with FRP reinforcement are the lack of plastic conduct and very low shear strength on the short side. Such features can lead to premature tender fragmentation, especially if mixed results are obtained, such as in shear-breaking planes on reinforced concrete pillars where there is a delow action. The downtime action reduces the remaining resistance to stiffness and shear tenderness.
- Solutions and limitations for use are provided and further improvements are expected in the future. The cost of FRP consolidation unit is expected to decrease significantly with increasing market share and demand. However, even today, there are applications where FRP consolidation is less expensive and justified. Such cases include the use of FRP sheets or bonded plates in repairing and strengthening concrete structures, as well as the use of FRP meshes or fabrics or fabrics in small cement products.
- The cost of renovating and renovating a building remains, in certain terms, much higher than the cost of the original building. Repairs usually require a small amount of repair materials but a high commitment from staff. In addition, labor costs in developed countries are so high that the cost of materials is secondary. So the performance and performance that lasts the longest, the repair is very expensive. This means that the cost of materials is not a problem to be rectified and the fact that FRP materials are expensive is not a particular problem [5].
- Given only the physical strength and resources, at the top, the controversy over FRP compounds in a sustainable built environment is questionable. However, such a conclusion needs to be evaluated in terms of the potential benefits of using FRP compounds related to assumptions such as:
- High power
- Light weight
- High performance
- It lasts a long time
- Renovating existing buildings and extending their life
- Seismic development
- Security systems
- Space programs
- Ocean areas
o. In the case of FRP compounds, environmental concerns appear to be a barrier to its functioning as a viable alternative especially in terms of fuel depletion, air pollution, fog, and acidification associated with its production. In addition, the ability to reuse FRP compounds is limited and, unlike steel and wood, structural components cannot be reused to perform the same function in another structure. However, examining the environmental impact of FRP compounds on infrastructure use, especially through life cycle analysis, may reveal more direct and indirect benefits that compete more than conventional ones.
p. The composite material has greatly improved since its inception. However, before composite materials can be used as an alternative to conventional materials as part of a sustainable environment a few needs remain.
q. Availability of durability data for FRP building materials.
r. Integration of robust data and service life prediction methods for building members using FRP combinations.
s. Development of selection methods according to the life cycle cycle of materials and systems.
t. Finally, in order for the mixtures to be considered a viable option, they must be structurally and economically viable. Many studies on the structure of the composite material are widely available in the literature.
u. However, limited studies are available on the economic and environmental availability of these items from the perspective of the life cycle, because short-term data are available or only economic costs are considered in comparison. In addition, the long-term impact of using composite materials needs to be determined.
v. The products produced, the sustainability of the materials, and the capacity to recycle the materials need to be tested to determine if the composite materials can be part of a sustainable environment. So in this chapter describe the physicochemical properties of polymers and compounds most commonly used in Civil Engineering. The theme will be presented in a simple and basic way for better understanding.
Polymer Impregnated Concrete
- In the case of pregnant polymer concrete, prepolymers or lower liquid monomers are partially or partially impregnated with a pore system of a composite cement framework. After this process, the entire treated structure is allowed to polish.
- The general process of treatment of reinforced concrete leads to the acquisition of a large amount of free water in its spaces. These water-filled voids form a significant amount of total volume. From 5% in the case of dense concrete and 15% in the case of gaped concrete.
- In the case of pregnant polymer concrete, it is these voids (holes filled with water) that should be filled with the selected polymer. So the main thing that affects the loading of the monomer is this: the moisture content in the solid concrete and the air loses energy in the concrete.
Procedure for polymer impregnated concrete manufacturing
The activities involved in the pregnancy process to improve pregnant polymer concrete are:
1. Well-constructed concrete is available. They need to get better and get stronger.
2. Moisture is removed by drying the concrete. Drying is done by heating the structure element at temperatures above the order of 120 to 150 degrees Celsius. An air oven can be used to dry small specimens.
If the element has a large surface, a thick cloth, say, 10mm thick, can be used to protect it from any hot gradient. Another complex application is the use of infrared heaters.
Complete removal of moisture from concrete, requires 6 to 8 hours of heat.
3. After complete removal, the concrete area has cooled to a safer level. This can go up to a temperature of 35 degrees Celsius. This heat will avoid overheating.
4. The concrete is now transferred to a vacuum cleaner, where all the air inside the concrete structure is removed. The amount of monomer installed will determine the time and level of use of the machine.
5. Concrete after sufficient ventilation is placed in a monomer solution. Wet for a long time until the desired depth of monomer penetration is obtained.
Filling time depends on the viscosity of the monomer, the adjustment of the template and the advanced characteristics of the concrete.
To reduce the time taken to get the desired input, it is preferable to use external pressure such as air or nitrogen gas. This helps to get in faster.
6. After the above procedure, the surface is covered with plastic paper. This helps prevent the evaporation of the monomer.
7. A high-temperature polymerization method is performed. This method involves polymerization by heating the deformed monomer to the required temperature. This will start from 60 degrees to 150 degrees Celsius. The selected temperature range depends on the type of monomer.
Heating can be done under water or with a low pressure steam injection, or with infrared heaters or an air oven. The heat decomposes the catalyst and thus initiates the polymerization reaction.
Once the monomer has penetrated the concrete, polymerization can also be initiated using ionization radiation similar to gamma rays. Polymers when they are completely polymer or when connected on the other side, act as solids that reside in the voids they are embedded in.
8. The concrete structure is then allowed to cool.
Every process from 1 to 8 can only be done in a precast factory. Monomers such as acrylate, styrene and vinyl chloride etc. are widely used for concrete installations. Another widely used material is Methyl Methacrylate (MMA).
Properties of polymer impregnated concrete
1. The polymer concrete gains the strength of the cube to strengthen more than 100N / mm2. This strength does not depend on the strength of the standard concrete.
2. The flexibility of a pregnant polymer concrete is approximately 15N / mm2. This is slightly higher than high-grade clear concrete made from common ingredients.
3. The elastic modulus lies in the range from 30 to 60N / mm2. This value is the same as the value obtained from high-strength concrete (e.g. Approximately 45N / mm2)
4. Pregnant polymer concrete has less movement problems and shrinkage due to the small number of pores.
5. Pregnant polymer concrete is more resistant to acid attacks, sulfate attacks and chloride attacks compared to PCC.
Application of polymer impregnated concrete
The use of pregnant polymer concrete in various construction sites is described below:
1. Surface Impregnation of Bridge Decks: Bridge decks are allowed to be installed to avoid the ingress of moisture, chemicals and chloride ions.
Bridge floors built in areas with high salt water and moisture exposure can be protected in this way.
2. Structural repairs: Damaged structures can be developed in the form of a polymer abstract. The life span of undeveloped buildings can be extended in this way.
This method is why it helps in the restoration and preservation of stone monuments.
3. Underwater and Marine Applications: Polymer impregnation capabilities help to improve structures, water absorption, and non-concrete structures. This makes them widely used in water and sea construction.
Buildings built on desalination plants and underwater structures use this method of building concrete. It has been shown that the small absorption of concrete masses from seawater reduces the corrosion of the steel by 24 times.
4. Use in Irrigation Systems: The use of standard methods for the repair and rehabilitation of dams and other important water structures appears to be inefficient and incomplete.
This is later found to cause significant losses in profits from irrigation, energy production, flood control etc. But the method of pregnancy works very well.
Concrete from the damaged area is removed, glued and dried. This area is later treated using polymer emissions.
5. Composite Joints: Pregnant polymer concrete is as strong as building materials. PIC also shows the amazing development of standard concrete.
Internal and empty cracks are the basic foundation for all the issues in common concrete structures. Since the suspension of the polymer determines the cause, it is best used for construction members.
Key takeaways
- FIBER REINFORCED POLYMER
Fiber-reinforced polymer (FRP), also fiber-reinforced plastic, is a composite made of polymer matrix reinforced with fibers. Threads are usually glass, carbon, or aramid, although other fibers such as paper or wood or asbestos have sometimes been used. The polymer is usually epoxy, vinylester or polyester thermosetting plastic, and phenol formaldehyde frames are still active. FRPs are widely used in the aerospace, automotive, marine and construction industries.
2. POLYMER IMPREGNATED CONCRETE
In the case of pregnant polymer concrete, prepolymers or lower liquid monomers are partially or partially impregnated with a pore system of a composite cement framework. After this process, the entire treated structure is allowed to polish.
Corrosion monitoring and preventive measures
- The rust measuring, control, and prevention field covers a wide range of technical tasks. Within the field of corrosion control and prevention, there are technical options such as cathodic and anodic protection, material selection, chemical insertion and use of indoor and outdoor clothing. The rust scale uses a variety of techniques to determine how much damage the environment consumes and how much iron loss is experienced. Rust rating is a measure of how rust management performance and prevention strategies can be implemented and provides feedback to enable rust control and preventative measures to be improved.
- Some rust measurement techniques can be used online, regularly displayed in process broadcasts, while others provide external measurement, such as those determined in laboratory analysis. Some techniques provide a precise measure of metal loss or rust ratio, while others are used to indicate the possibility of corrosion.
- Rust monitoring is the practice of measuring the deterioration of process dissemination conditions by using probes that are incorporated into process dissemination and that are continuously expressed in the process dissemination process.
- Rust monitoring probes can be mechanical, electrical or electrical devices.
- Rust monitoring alone provides accurate and online measurement of metal loss / corrosion rate in industrial process systems.
- Typically, the rust measuring system, testing and adjustment used in any industrial area will include measuring instruments provided by four combinations of on-line / offline, direct / indirect measurements.
- Corrosion Monitoring Direct, On-line
- Direct, Offline Non-Destructive Testing
- Indirect Analytical Chemistry, Off-line
- Indirect, online Operational Data
- In a well-managed and integrated system, data from each source will be used to draw reasonable conclusions about the levels of active corrosion by the process process and how they are effectively reduced.
The Need of corrosion monitoring
The level of rust determines which process plant can be used efficiently and safely for how long. The rust scale and the action of adjusting the high levels of rust allow for the efficient operation of plants that must be achieved while minimizing the life cycle costs associated with the work.
Rust monitoring techniques can help in a number of ways:
- By giving an early warning that harmful procedural conditions exist that could lead to failures caused by rust.
- By studying the integration of changes in process parameters and their effect on system corrosivity.
- By identifying a specific rust problem, identifying its cause and the parameters that control the level, such as pressure, temperature, pH, flow rate, etc.
- By evaluating the effectiveness of the corrosion / prevention control method such as chemical prevention and good use.
- By providing management information relating to conservation needs and the ongoing condition of the plant.
Corrosion monitoring techniques
A large number of rust monitoring strategies are available. The following list describes the most common strategies used in industrial applications:
- Rust Coupons (Weight Loss Rate)
- Electrical Resistance (ER)
- Linear Separation Resistance (LPR)
- Galvanic (ZRA) / Possible
- Hydrogen Ingestion
- Bacteria
- Sand / Soil erosion
Other strategies are available, but almost all require professional work, otherwise they are not enough or flexible to apply.
In the above-mentioned strategies, corrosion coupons, ER, and LPR form the core of industrial corrosion monitoring systems. The other four strategies are usually found in special programs that are discussed over time.
These rust monitoring methods have been used successfully and are being used by a growing number of applications because:
- The techniques are easy to understand and apply.
- The reliability of the equipment has been demonstrated in the field field for many years of application operation.
- The results are easy to explain.
- Measurement equipment can be made internally safe from hazardous environmental performance.
- Consumers have gained significant economic benefits by reducing planting time and extending plant life.
Preventive Measures
- Metal corrosion is a natural process that requires three conditions: moisture, metal surface, and an oxidizing agent called an electron acceptor. Rust converts the active metal into a separate form of oxide, hydroxide, or sulphide. The most common type of rust is rust.
- Metallic metal not only affects the structure of the metal, but it can also affect the people who use the material or objects close to the metal. In extreme cases, rotten metal can lead to the construction of buildings and bridges, leaking pipes, and medical implants that infect human blood.
- While all metals are in danger of corrosion, some metals, such as pure metal, deteriorate much faster than others. However, iron can be combined with other alloys to form a stainless steel that is more resistant to corrosion.
- It is estimated that approximately 25-30% of rust can be prevented using appropriate protective measures.
- In general, you can prevent rust by choosing the right type of metal, Protective Fabrics, Environmental Measures, Self-Sacrifice Items, Rust Stumbling Stuff, Metal Installation and Repairs for Your Project.
Choose the right metal type
- One of the easiest ways to prevent rust is to use rust-resistant metal such as stainless steel, duplex, super duplex, nickel alloy or 6% Moly.
- These devices are so well made that they have a high resistance to corrosion and use them to reduce the need for alternative corrosion protection.
- For Special Drawing Materials, we offer products made of the highest quality synthetic materials available - stainless steel, duplex, super duplex, 6% Moly and Nickel Alloy. A variety of materials are selected by our clients in a variety of areas, with one of the factors considered for possible corrosion.
Protective coating
- Another way to prevent rust is to cover it with a special protective paint. Paint coating can act as a barrier that works by preventing electrochemical charging that transmits to the destructive and metal solution below.
- One way to do this is to put a powder coating in a clean metal place. The metal is heated to turn the flour into a smooth, non-abrasive film that acts as a barrier to rust. Many different powder compositions can be used, such as acrylic, polyester, epoxy, nylon, and urethane.
Environmental Measures
- Rust is certainly due to the nature of the metal in it as the chemical reactions that occur are due to metal reacting with liquids and gases in the surrounding environment.
- Controlling the environment can therefore help reduce this response. This could be as simple as reducing exposure to rain or seawater or it could be steps taken to reduce the amount of sulfur, chlorine, or oxygen in the area. For example, carrying water in water boilers to adjust hardness, alkalinity, or oxygen content, before placing the metal in that water can be very helpful in preventing corrosion.
Sacrificial coating
Sacrifice cover to prevent corrosion means covering the metal with a type of metal that may have oxidise - you sacrifice this top layer to protect the lower metal.
There are two main ways to accomplish the sacrificial attire:
- Cathodic Protection: Cathodic protection works by making the metal cathode of an electrochemical cell. The most common example of cathodic protection is the coating of iron ore and zinc - this process is known as galvanizing. Zinc is more than an active metal so rust prevents metal rot. Cathodic protection is frequently used for steel or petrol pipelines, heat tanks, ports, and overseas oil platforms.
- Anodic Protection: Anodic protection is opposed to cathodic protection and works by making the metal anode of an electrochemical cell. A common way to do this is to cover a thin layer of stainless steel, such as tin. The tin will not corrode, so the metal will be protected as long as the tin coating is in place. Anodic protection is often used for carbon storage tanks used to store sulfuric acid and 50% caustic soda.
Corrosion Inhibitors
- Chemical corrosion inhibitors are selected to react to metal surfaces or surrounding gases and therefore suppress electrochemical reactions that can lead to decay. When applied to a metal surface, they form a protective film. Inhibitors can be used as a solution or as a protective cover using distribution methods.
- Corrosion inhibitors are often used in a process known as passivation. An example of passivation is the Statement of Freedom where a blue and green metal signature is actually present to protect the copper underneath.
Metal Plating
- The installation is very similar to the cover as a thin layer of metal is inserted into the metal you want to protect. As well as preventing corrosion, the metal layer provides a good finish of beauty.
There are four types of metal wraps:
- Electroplating: The application of a thin layer of metal such as chromium or nickel to the underground metal by means of an electrolyte bath.
- Mechanical Plating: this involves cold welding powder metal metal substrate.
- Electro less: Coating such as nickel or cobalt is placed on a metal substrate using non-electrical chemical reactions.
- Hot dipping: A simple covering method that involves placing the substrate in a molten metal protective tub.
Design Modification
- Changing the structure of the project can have a significant impact on rust protection as it works by eliminating the causes of rust.
Key takeaways
- The rust measuring, control, and prevention field covers a wide range of technical tasks. Within the field of corrosion control and prevention, there are technical options such as cathodic and anodic protection, material selection, chemical insertion and use of indoor and outdoor clothing. The rust scale uses a variety of techniques to determine how much damage the environment consumes and how much iron loss is experienced. Rust rating is a measure of how rust management performance and prevention strategies can be implemented and provides feedback to enable rust control and preventative measures to be improved.
Rehabilitation methods for concrete elements grouped under confining techniques included concrete jacketing, steel jacketing, ferrocement laminated jacketing and FRP confinement. Some of the methods are for cosmetic repairs required to improve appearance, restore the non-structural properties and weather protection.
These techniques and materials for repair of concrete is described. Concrete is the most widely used and versatile construction material possessing several advantages over steel and other construction materials. However very often one come across with some defects in concrete. The defects may manifest themselves in the form of cracks, spalling of concrete, exposure of reinforcement, excessive deflections or other signs of distress. On many occasions, corrosion of reinforcement may trigger off cracking and spalling of concrete, coupled with deterioration in the strength of the structure. Such situations call for repairs of affected zones and sometimes for the replacement of the entire structure.
The need of structural repairs can arise from any of the following:
- Faulty design of the structure
- Improper execution and bad workmanship
- Extreme weathering and environmental conditions
- High degree of chemical attack
- Ageing of the structure
References:
1. A.M Neville J.J. Brooks Concrete technology
2. A.M Neville Concrete technology
3. R.S. Varshney Concrete technology
4. IS 10262 - 2009, Recommend guidelines for Concrete
Unit - 1
Concrete
Unit - 1
Concrete
Unit - 1
Concrete
- Concrete is a composite fabric composed of exceptional and coarse combination bonded collectively with a fluid cement (cement paste) that hardens (cures) over time.
- In the past, lime primarily based totally cement binders, consisting of lime putty, have been regularly used however now and again with different hydraulic cements, consisting of a calcium aluminate cement or with Portland cement to shape Portland cement concrete (named for its visible resemblance to Portland stone).
- Many different non-cementitious forms of concrete exist with different techniques of binding combination collectively, together with asphalt concrete with a bitumen binder that is often used for avenue surfaces, and polymer concretes that use polymers as a binder.
- When combination is blended with dry Portland cement and water, the combination bureaucracy a fluid slurry this is without difficulty poured and molded into shape.
- The cement reacts with the water and different elements to shape a difficult matrix that binds the substances collectively right into a long lasting stone-like fabric that has many uses.
- Often, additives (consisting of pozzolans or superplasticizers) are protected with inside the combination to enhance the bodily residences of the moist blend or the completed fabric.
- Most concrete is poured with reinforcing substances (consisting of rebar) embedded to offer tensile strength, yielding bolstered concrete.
- Because concrete cures (which isn't always similar to drying), how concrete is treated after it's miles poured is simply as essential as before.
- Concrete is one of the maximum often used constructing substances.
- Ts utilization worldwide, ton for ton, is two times that of steel, wood, plastics, and aluminum combined. Globally, the ready-blend concrete industry, the biggest section of the concrete market, is projected to exceed $six hundred billion in sales with the aid of using 2025.
- Concrete is wonderful from mortar. Whereas concrete is itself a constructing fabric, mortar is a bonding agent that generally holds bricks, tiles and different masonry devices collectively.
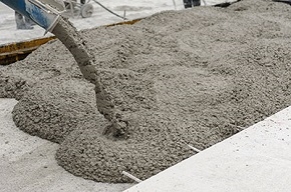
Fig 1: Concrete
Key Takeaways:
- Concrete is a composite fabric composed of exceptional and coarse combination bonded collectively with a fluid cement (cement paste) that hardens (cures) over time.
Plain concrete:
- Plain concrete, additionally referred to as undeniable cement concrete or PCC, is maximum typically used for paving and flooring.
- Made from a combination of cement, combination, and water the special varieties of combination and ratio of substances used will deliver special varieties of cement with barely special homes.
- This is one of the foremost promoting factors of geared up blend concrete as the precise values and varieties of combination may be measured and monitored exactly to offer the traits which are wished with none variance.
- The computerized production procedure limits the capacity of human blunders whilst saving time and resources.
- While there are variations with inside the composition of the concrete maximum undeniable concrete stocks the equal strengths and weaknesses.
- It is rather robust beneath Neath compression even as susceptible beneath Neath anxiety, because of this whilst on a solid, unmoving floor it's miles able to withstanding large quantities of weight.
- However, whilst located beneath Neath anxiety it's miles an awful lot weaker and might frequently crack and buckle.
- This makes it the correct cloth for floor ground layers and offering a strong or even base for strengthened concrete to be constructed onto whilst proscribing its use in large creation projects.
Key Takeaways:
- Made from a combination of cement, combination, and water the special varieties of combination and ratio of substances used will deliver special varieties of cement with barely special homes.
Reinforced concrete:
- Reinforced concrete, or strengthened cement concrete (RCC), is surely very just like PCC in phrases of substances used.
- The one massive distinction in its composition is the addition of metal rebar.
- By casting the moist cement round reinforcing metal bars the consequent composite cloth has an awful lot extra electricity beneath anxiety whilst nonetheless maintaining the homes that make PCC so effective.
- With the concrete retaining its electricity beneath compression and the metal resisting any bending or stretching way to its tensile electricity the RCC is a far extra flexible creation cloth.
- Able to rise up to weight pushing down onto it in addition to any wind stress or moving that outcomes in moderate twists and lines way to the expanded flexural capability of the concrete/metal blend, it's miles an appropriate cloth for taller and heavier homes and for roads and bridges.
- Steel is the maximum not unusual place cloth used for the introduction of rebar because it reacts to very comparable variances in temperature as concrete, that means it'll amplify and settlement with the concrete instead of cracking it from the inside.
Key Takeaways:
- By casting the moist cement round reinforcing metal bars the consequent composite cloth has an awful lot extra electricity beneath anxiety whilst nonetheless maintaining the homes that make PCC so effective.
Steel fiber/Glass fiber-strengthened concrete:
- Steel Fiber Reinforced Concrete (SFRC) is described because the concrete made with hydraulic cement containing high-quality and coarse combination and discontinuous discrete metal fiber.
- In SFRC, lots of small fibers are dispersed and disbursed randomly with inside the concrete for the duration of mixing, and hence enhance concrete homes.
- SFRC is getting used to enhance static and dynamic tensile electricity, strength soaking up capability and higher fatigue electricity.
- Steel fibers are the most powerful typically to be had fiber, and are available special lengths and shapes.
- Steel fires can simplest be used on surfaces which can tolerate or keep away from corrosion and rust stains.
- In a few cases, a metal-fiber floor is confronted with different substances.
- Glass fiber is a less expensive and corrosion-evidence fiber, however now no longer as robust as metal.
- The layout of glass fiber strengthened concrete proceeds from understanding of its fundamental homes beneath tensile, compressive, bending and shears forces, coupled with estimates of conduct beneath secondary loading results along with creep, thermal reaction and moisture movement.
Key Takeaways:
- SFRC is getting used to enhance static and dynamic tensile electricity, strength soaking up capability and higher fatigue electricity.
Light-weight concrete:
- Lightweight concrete is a combination made with light-weight coarse aggregates along with shale, clay, or slate, which provide it its feature low density.
- Structural light-weight concrete has an in-location density of ninety to a hundred and fifteen lb/ft³, while the density of everyday weight concrete stages from a hundred and forty to a hundred and fifty lb/ft³.
- This makes light-weight concrete best for constructing current systems that require minimum move sections with inside the foundation.
- It is being more and more used to construct smooth foundations, and has emerged as a possible opportunity to everyday concrete.
- Nevertheless, a better compressive electricity of 7000 to 10,000 psi may be attained with light-weight concrete.
- However, this can compromise the density of the combination because it calls for the addition of extra pozzolans and water-decreasing admixtures to the concrete.
Key Takeaways:
- Structural light-weight concrete has an in-location density of ninety to a hundred and fifteen lb/ft³, while the density of everyday weight concrete stages from a hundred and forty to a hundred and fifty lb/ft³.
High overall performance concrete:
- Concrete assembly unique combos of overall performance and uniformity necessities that cannot usually be accomplished mechanically the use of traditional parts and everyday mixing, placing, and curing practices.
- High-overall performance concrete (HPC) is concrete that has been designed to be extra-long lasting and, if necessary, more potent than traditional concrete.
- HPC combinations are composed of basically the equal substances as traditional concrete combinations, however the proportions are designed, or engineered, to offer the electricity and sturdiness wished for the structural and environmental necessities of the project.
- High-electricity concrete is described as having a targeted compressive electricity of 8000 psi (fifty-five MPa) or greater.
- The price of 8000 psi (fifty-five MPa) became decided on as it represented a electricity stage at which unique care is needed for manufacturing and checking out of the concrete and at which unique structural layout necessities can be wished.
Key Takeaways:
- HPC combinations are composed of basically the equal substances as traditional concrete combinations, however the proportions are designed, or engineered, to offer the electricity and sturdiness wished for the structural and environmental necessities of the project.
Polymer concrete:
- Polymer concrete is a combination that makes use of a few form of epoxy binder to remedy and harden into location.
- A polyester, vinyl ester, or everyday epoxy combination is frequently used, however polymer concrete may be made with many styles of polymer resins that permit the concrete to be poured or troweled after which hardened.
- It remedies via a chemical response with the polymer cloth.
- Like conventional concrete, it additionally has water, sand and gravel or overwhelmed stone as number one ingredients.
- Polymer concrete gives special blessings relying at the resin used to make it.
- Acrylic binders set right away and provide resistance to weathering, whilst epoxies create a completely robust cloth that shrinks little or no because it remedies.
- Furan resins can face up to excessive temperatures, and polyuria resins can update phenolic or formaldehydes in lots of creation projects.
- Polymer concrete is used for lots styles of specialized creation projects.
- Like different varieties of concrete, it is able to be used to sign up for special additives or to offer a shape or base.
- The cloth is utilized in electric or commercial creation in which the concrete desires to final a long term and be proof against many varieties of corrosion.
Key Takeaways:
- A polyester, vinyl ester, or everyday epoxy combination is frequently used; however, polymer concrete may be made with many styles of polymer resins that permit the concrete to be poured or troweled after which hardened.
Concrete is a commonly used construction material, which is the mixture of cement, sand, aggregate, and admixtures blended with water. Concrete gets hardened with time and gains the strength, and for the best results in a construction of your dream home, mixing of concrete is said to be the most important process. All the ingredients are to be mixed in proper proportion because the properties of concrete like workability, strength, surface finish, and durability of concrete etc. are ensured by the right and proportionate blending.
In the nominal mix concrete, all the ingredients and their proportions are prescribed in the standard specifications. These proportions are specified in the ratio of cement to aggregates for certain strength achievement.
The mix proportions like 1:1.5:3, 1:2:4, 1:3:6 etc. are adopted in nominal mix of concrete without any scientific base, only on the basis on past empirical studies. Thus, it is adopted for ordinary concrete or you can say, the nominal mix is preferred for simpler, relatively unimportant and small concrete works.
As per the ‘Indian Standard- IS 456:2000’, nominal mix concrete may be used for concrete of M20 grade or lower grade such as M5, M7.5, M10, M15.
M 20 is identified as the concrete grade in which, M denotes the Mix and 20 denotes the compressive strength of concrete cube after 28 days of curing in N/mm2. There are various grades of concrete that can be used like M10, M15, M20, M25, M30, etc.
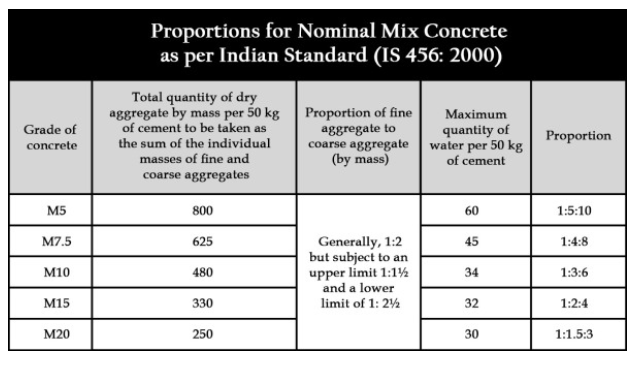
Tests on fresh concrete
Objective
- The word ―workable or concrete used has a broader and deeper meaning than the word alternative that is commonly used freely to make it work. Consistency is a general term that indicates the level of fluid or flow rate.
- Factors that help concrete to have the most effective effect of reducing internal friction that facilitates easy mixing are:
(a) Water content
(b) Mixing Dimensions
(c) Collection Size
(d) Structure Shapes
(e) Spatial Design Design
(f) Placement layout
(g) Use of Admixtures.
- Slump test is the most widely used method of measuring the consistency of concrete that can be used in a laboratory or in the workplace.
- It is not suitable for very wet or very dry concrete. It does not measure all factors that affect performance, nor does it always represent concrete placement.
- Indicates the concrete feature above the drop value. When the concrete slips evenly it is called a true slump. When one part of the lump slips, it is called a shear slump.
- In the event of a shear bend, the slump value is measured as the height difference between the height of the mold and the average amount of shrinkage.
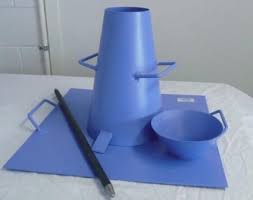
Fig no 2 Slum cone
Procedure
- If this test is performed in the field, a mixed concrete sample will be obtained. In the case of concrete containing a diameter of more than 38 mm, the concrete will be diluted with water by one and a half inches of screen to remove compacted particles larger than 38 mm.
- The inner surface of the mold will be thoroughly cleaned and freed from unwanted moisture and pre-set concrete before testing. The mold will be placed on a smooth, horizontal, strong, and non-abrasive surface, such as a carefully weighed metal table, the mold will be kept firmly in place while filling.
- The mold will be filled in four layers, each about a quarter of the height of the mold. Each layer will be smoothed with twenty-five lashes on the round edge of the lubricating rod. The lashes will be distributed evenly over the section at the cross section of the mold and the second and subsequent layers will fit into the lower layer.
- The bottom layer will be smoothed in the depth of it all. After the upper layer has been coated, the concrete will be flattened and trimmed with a trowel, so that the mold will fill directly.
- After the top layer has been glued, remove the concrete surface by moving and moving the lubricating rod.
- Any mud that may have leaked between the mold and the base plate should be cleaned. The mold will be removed from the concrete immediately by lifting it gently and carefully in a vertical direction. This allows the concrete to drop and the fall will be measured immediately by determining the difference between the height of the mold and that of the highest of the test template.
- The above operation will be performed in a non-vibrating or panic-free environment, and within two minutes after sampling.
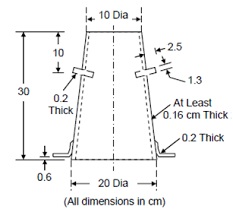
Fig no 3 Dimensions of slum cone
Key takeaways
- Slump test is the most widely used method of measuring the consistency of concrete that can be used in a laboratory or in the workplace.
- It is not suitable for very wet or very dry concrete. It does not measure all factors that affect performance, nor does it always represent concrete placement.
COMPACTION FACTOR
Objective
The compacting factor test is mainly designed for use in the laboratory but can also be used in the field. It is more accurate and sensitive than fall testing and is especially useful for very low-performance concrete mixes and is often used when the concrete will be squeezed by vibration. This method works on bare and ventilated concrete, made of lightweight, standard weight or heavy aggregates with a maximum weight of 38 mm or less but not on open concrete or non-reinforced concrete.
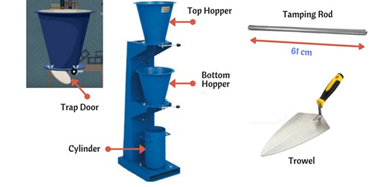
Fig no 4 Compaction factor apparatus
Procedure
- A sample of the test concrete will be gently placed on the upper hopper, using a hand scoop. The hopper will be evenly filled with its edge and the trap door will be opened so that the concrete falls to the ground.
- Some mixes tend to stick to one or both hoppers. When this happens, the concrete can be helped by pushing the rod gently into the concrete from the top. During this process, the cylinder will be covered with tiles.
- As soon as the concrete is out, the cylinder will be exposed, the door to the bottom trap will be opened, and the concrete will be allowed to fall into the cylinder. The remaining concrete over the top of the cylinder will be removed by holding a trowel in each hand, the plane of the belts horizontally, and then moving them simultaneously to each side above the cylinder, at the same time keeping them pressed against the upper edge of the cylinder.
- The outside of the cylinder when it is wiped will be clean. The above work will be done in a place that will not tremble or shake. The weight of the concrete in the container will be determined by the nearest 10 g.
- The remaining concrete over the top of the cylinder will be removed by holding a trowel in each hand, the plane of the belts horizontally, and then moving them simultaneously to each side above the cylinder, at the same time keeping them pressed against the upper edge of the cylinder. The outside of the cylinder when it is wiped will be clean. The whole process will be done in a place where there is no vibration or shock.
- This weight will be known as the weight of the partially bonded concrete. The cylinder will be filled with concrete from the same sample with layers about 5 cm deep, the layers folded tightly
- Or shaken to achieve complete integration.
- The surface of the fully covered concrete will be carefully beaten and weighed above the cylinder. The outside of the cylinder when it is wiped will be clean.
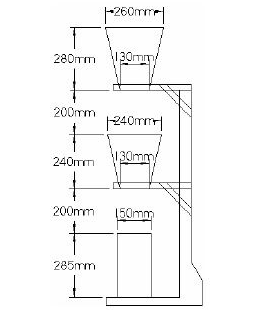
Fig no 5 Dimensions of compaction factor apparatus
Key takeaways
The compacting factor test is mainly designed for use in the laboratory but can also be used in the field. It is more accurate and sensitive than fall testing and is especially useful for very low-performance concrete mixes and is often used when the concrete will be squeezed by vibration. This method works on bare and ventilated concrete, made of lightweight, standard weight or heavy aggregates with a maximum weight of 38 mm or less but not on open concrete or non-reinforced concrete.
VEE BEE CONSISTOMETER AND FLOW TABLE APPARATUS
VEE BEE CONSISTOMETER
Objective
- The performance of the new concrete is a composite material, which incorporates various requirements for stability, mobility, durability, placement and finishing. There are various ways to measure performance.
- Each of them measures only a specific aspect of it and there is no unique test, which measures the performance of concrete completely. This test provides an indication of the flow rate of the newly mixed concrete mix.
- The test measures the concurrent effort required to change a pile of concrete from one concrete to another (e.g., from a circle to a cylindrical) using vibration.
- The amount of effort (called retrieval attempt) is taken as the time in seconds, which is required to complete the change. The results of this experiment are useful when you study the flow of concrete piles made of different amounts of water, cement and different types of composite placement.
- The time required for a full recovery in seconds is taken as a performance measure and is expressed as the Vee-Bee number of seconds.
- This method is suitable for dry concrete. With concrete drop of more than 50mm, reconstruction is so fast that time cannot be measured.
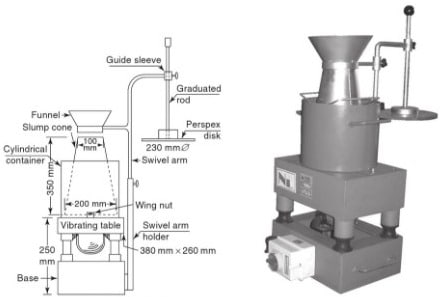
Fig no 6 Vee bee Consistometer Test
Procedure
- Slump test as described in "IS 1199: 1959 Details of Concrete Testing Equipment (Fourth Review). Confirmed- Dis 2013". Is made, inserting a collapsible lump inside a round metal pot of consist meter.
- The glass disk attached to the rotating arm will be moved to the top of the cone in the pot and before the cone is raised, the location of the concrete cone will be identified by fixing the glass disc attached to the arm wrist. The cone will then be lifted and the fall will be marked on the graduating rod by lowering the glass disc over the concrete cone. The electric heater will then light up and the concrete will be allowed to lay in the pot.
- The vibration continues until the point where the concrete shape disappears and the concrete takes on a circular shape. This can be judged by looking at the glass disc from the top disappearing visually.
- As soon as the concrete completely begins to form a circle, the stand clock is turned off. The time required for concrete formation to change from the formation of a collapsing lump into a circle in seconds is known as the Vee Bee Degree.
- This method is best suited for dry concrete with an unmeasured fall value with a Slump Test, but vibration is much stronger than concrete with a fall of more than 50 mm.
FLOW TABLE
Flow tests were performed to measure the performance of the concrete. As the name suggests, in this experiment concrete performance is measured by examining the flow of concrete material. Flow test Easy laboratory test. This test applies to the principal for the general weight loss of concrete and is measured by the flow of concrete. The flow of concrete indicates the performance of the new concrete.
Why flow test of concrete required
Flow tests are used to measure the performance of high or very active concrete, which ultimately indicates a fall. It gives an idea about the quality of concrete in terms of consistency and consistency. This performance test is easy to perform and is best suited for concrete with a high overall size of the joint less than 38 mm.
Flow Test Apparatus
Metal Cone or Mould: Mould is in the form of a frustum of a cone with a base diameter of 250 mm, upper surface diameter of 170 mm and 120 mm height. The mould comes with handles for support.
Flow Table
Trowels
Hand scoop
Scale
Tamping Rod
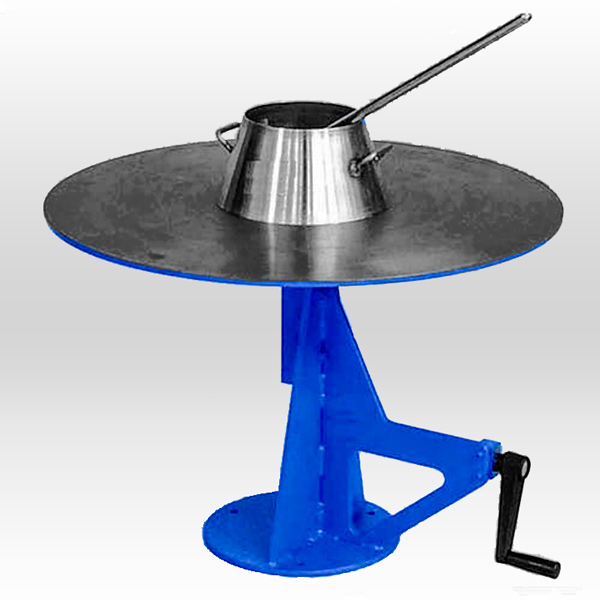
Fig no 7 Flow test apparatus
Procedure
- Clean anything toxic or dusty from the flow table and inside the mold.
- Place the lump on the marked area or in the middle of the flow table.
- Now pour the freshly mixed concrete into the mold in two layers, each layer should be moistened 25 times with a soft stick. If the concrete overflows after stamping and measure with the help of a torch, and the excess concrete should be removed from the table.
- After that, lift the mold upwards and allow the concrete to stand on its own without support.
- After that the table is raised and lowered from 12.5 mm high, 15 times in about 15 seconds.
- Next, measure the width of the concrete spread by about 6 points and write down the scale.
Key takeaways
- The performance of the new concrete is a composite material, which incorporates various requirements for stability, mobility, durability, placement and finishing. There are various ways to measure performance.
- Each of them measures only a specific aspect of it and there is no unique test, which measures the performance of concrete completely. This test provides an indication of the flow rate of the newly mixed concrete mix.
- Flow tests were performed to measure the performance of the concrete. As the name suggests, in this experiment concrete performance is measured by examining the flow of concrete material. Flow test Easy laboratory test. This test applies to the principal for the general weight loss of concrete and is measured by the flow of concrete. The flow of concrete indicates the performance of the new concrete.
Effect of admixture on workability of concrete and optimum dosage of admixture by marsh cone test
Effect of admixture on workability of concrete
- Concrete contains cement, sand, a mixture of water. Anything other than these if added to concrete before or during mixing to convert structures to our desired requirement is called admixtures. The use of admixtures provides certain beneficial effects on concrete such as improved performance, speed or delay of set time, reduction of the amount of water cement, and so on.
- There are two basic types of admixtures available: chemicals and minerals. Admixtures such as fly ash, silicate fume, slag come in the category of mineral admixtures. They are incorporated into concrete to increase performance, improve thermal resistance and alkaline reactions and enable us to reduce cement content.
- Fly ash is a good residue left over from global warming or powdered charcoal. They are all better than cement and contain mainly round glass particles as well as remnants of hematite and magnetite, char and other crystalline layers formed during cooling. The use of fly ash in concrete makes mixing more economical, and improves performance, reduces separation, bleeding and reduces hydration temperatures but also offers natural benefits.
- Silica fire, also known as micro silica. It is available as a product during the production of silicon and ferrosilicon alloys. The particles of silica fire particles are 100 times smaller than cement particles which mean their smoke like cigarettes. Its highly efficient pozzolanic material, which improves concrete structures such as improved durability, bond strength, abrasion resistance, dense concrete leading to reinforcement and rust protection.
- Chemical admixtures are applied to concrete in very small quantities especially for ventilation, reduction of water or cement content, installation of new concrete mixtures or control of concrete set time. These compounds can be widely used as super plasticizers, accelerators, retarders, water reducers and ventilation admixtures.
- Super plasticizers were added to reduce water demand by 15 to 20% without affecting performance leading to high durability and high concrete. Super plasticizers are liner polymers that contain sulfonic acid groups attached to the polymer from time to time. Commercial composition can dissolve melamine - formaldehyde condens- sates, sulfonated naphthalene formaldehyde condensates, and modified lingo sulfonates, derived from polycar- boxylate. The main purpose of super plasticizers is to produce a concrete slope with a very high drop of 175 to 200 mm that can be used effectively on reinforced concrete structures, a decrease in volume depending on the volume, type and timing of good plasticizers (preferably before adding concrete.), Water cement, environment and value of cement.
- Accelerators were added to reduce the setting time of the concrete thus facilitating pre-form removal and are also used in the combination of cold weather. Calcium chloride is the most widely used accelerator in blending. The use of calcium chloride in reinforced concrete can promote the corrosion function of the steel reinforcement. As people become aware of it there is a growing interest in using free chloride.
- Retarders were added to increase the setting time by delaying the hydration of the cement. They are popular in areas with high temperatures combined. Retarders contain organic & inorganic agents. Organic retarders include unrefined calcium, sodium and ammonia salt lignosulfonic acid, hydro carboxylic acid and carbohydrates. Inorganic retardants include lead oxides, zinc, phosphate and magnesium salts. Most retarders work as a water repellent. They are called retarders that reduce water. It is therefore caused by high pressure forces due to the low water content.
- Admixtures reduce the amount of water added to the concrete to achieve a certain effect (fall) at a lower water level. Strong concrete specified for low cement content thus saving cement. Water reducers are widely used in hot weather and assist in pumping. Water-repellent plasticizers are hygroscopic powder, which can inhale air into concrete.
- Ventilation admixtures bring in small concrete bubbles. These air bubbles act as rollers thus improving performance and also work more efficiently in thaw-chilling channels as they provide a stabilizing effect in expanding water where cold weather meets.
- Ventilation admixtures are compatible with most combinations, care should be taken to prevent them from collapsing during mixing.
- In general, the performance of both types of plasticizers depends on the ambient temperature and thus in the summer the amount of plasticizer that will be used to handle the same rate of plastic expansion may be more than the amount that will be used in winter.
- The change in the normal set time within a specific requirement also makes the product dependent on other chemicals and as plasticizers with different nomenclature available in the market.
- CICO Technologies Limited, a 75-year-old Indian company ISO 9001: 2000 supported producing a range of concrete installation admixtures.
- Many RMC companies use CICO admixtures. Further modification is required during the trial. Modification to Plasticizers can meet the needs of any particular client.
Optimum dosage of admixture by marsh cone test
- Admixtures are common and important of modern concrete. Low water content, high efficient, durable and cost-effective cement
- Many desirable properties that can be expected from concrete made of chemical and mineral composites
- Admixture-Cement mixing in concrete is complex combination of chemical and physical equipment independent.
- All combinations in large volumes offer good results when used with cement.
- Cement hydration involves a series of reaction, which is highly dependent on cement composition, water / cement ratio, surface area, particle distribution of size, temperature and integration.
- Admixtures when added in small amounts do that the hydration process is very complex. In recent times, developments in the cement product sector are related to the use of admixtures especially organic polymeric building materials.
- Many species of polymeric organisms known as super plasticizers, are used construction industries to change the way it flows again concrete machinery facilities.
- Among the various species for chemical admixtures, PCE-based admixtures are shown to develop new flow and complex areas of low-grade concrete.
Key takeaways
- Concrete contains cement, sand, a mixture of water. Anything other than these if added to concrete before or during mixing to convert structures to our desired requirement is called admixtures. The use of admixtures provides certain beneficial effects on concrete such as improved performance, speed or delay of set time, reduction of the amount of water cement, and so on.
- Admixtures are common and important of modern concrete. Low water content, high efficient, durable and cost-effective cement
- Many desirable properties that can be expected from concrete made of chemical and mineral composites.
Testing of hardened concrete
- The compression take a look at indicates the exceptional feasible electricity concrete can gain in best conditions.
- The compression take a look at measures concrete electricity withinside the hardened state.
- Field concrete samples are organized, cured and examined consistent with ASTM preferred procedures.
- Specimens are organized from concrete taken from exclusive creation sites.
- Following methods and calculations are used for measuring compressive electricity of cylindrical concrete specimens.
Test Procedure
- Placing the Specimen — The plain (decrease) bearing block is located, with its hardened face up, at the desk of the trying out device without delay beneath the spherically seated (top) bearing block. The bearing faces of the top and decrease bearing blocks are wiped clean and the take a look at specimen is located at the decrease bearing block.
- Zero Verification and Block Seating— previous to trying out the specimen, it's far demonstrated that the weight indicator is ready to zero. If the indicator isn't always well set to zero, it's far adjusted.
- Rate of Loading— the weight is implemented constantly and without shock.
- Standards specify that for trying out machines of the screw type, the shifting head shall tour at a charge of about zero.05in. (1mm)/min while the device is jogging idle .While for hydraulically operated machines, the weight will be implemented at a charge of motion (platen to crosshead measurement) similar to a loading charge at the specimen in the variety of 20 to 50 psi/sec (0.15 to 0.35 M Pa/sec).
- During the software of the primary 1/2 of of the expected loading phase, a better charge of loading is allowed.
- No adjustment is made with inside the charge of motion of the platen at any time at the same time as a specimen is yielding swiftly right away earlier than failure.
- Load is implemented till the specimen fails, and the most load carried via way of means of the specimen all through the take a look at is recorded. The form of failure and the arrival of the concrete also are noted.
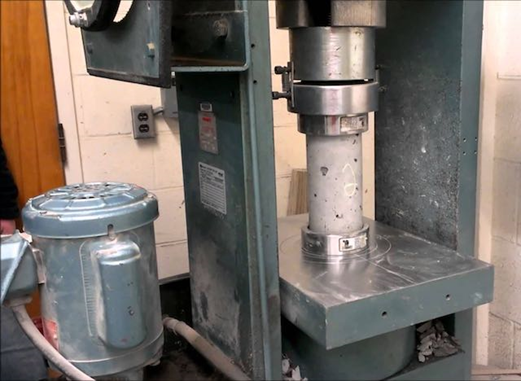
Fig no 8 Compression Testing Machine
Calculations:
Concrete Cylinder Loading Samples Compressive energy of the specimen is calculated through dividing the most load carried through the specimen all through the check with the common cross-sectional area.
Determine and specific the end result to the closest 10 psi (0.1 M Pa).
Key takeaways
The electricity of air-dried cores is on common 14 percentage large than the electricity of soaked cores.
Flexural Strength
Objective:
- To decide the Flexural Strength of Concrete, which comes into play whilst a avenue slab with insufficient sub-grade guide is subjected to wheel masses and / or there are extent modifications because of temperature / shrinking.
Equipment & Apparatus:
- Beam mildew of length 15 x 15x 70 cm (whilst length of mixture is much less than 38 mm) or of length 10 x 10 x 50 cm (whilst length of mixture is much less than 19 mm)
- Tamping bar (forty cm long, weighing 2 kg and tamping phase having length of 25 mm x 25 mm)
- Flexural take a look at gadget– The mattress of the checking out gadget will be furnished with metal rollers, 38 mm in diameter, on which the specimen is to be supported, and those rollers will be so hooked up that the space from centre to centre is 60 cm for 15.0 cm specimens or forty cm for 10.0 cm specimens.
- The load will be implemented via comparable rollers hooked up on the 1/3 factors of the assisting span that is, spaced at 20 or 13.3 cm centre to centre.
- The load will be divided similarly among the 2 loading rollers, and all rollers will be hooked up in this sort of way that the burden is implemented axially and without subjecting the specimen to any torsion stresses or restraints.
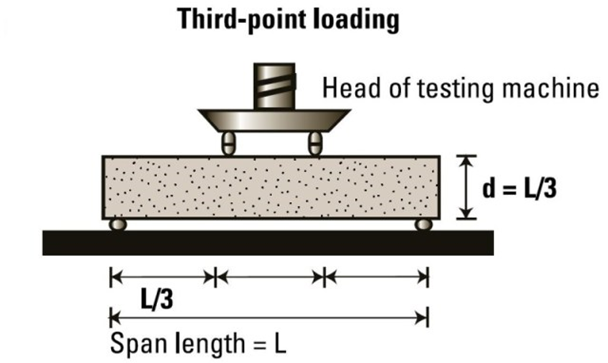
Fig no 9 Flexural testing machine
Procedure:
- Prepare the check specimen via way of means of filling the concrete into the mold in three layers of about identical thickness.
- Tamp every layer 35 instances the use of the tamping bar as distinct above.
- Tamping have to be disbursed uniformly over the whole cross section of the beam mildew and in the course of the intensity of every layer.
- Clean the bearing surfaces of the assisting and loading rollers , and get rid of any free sand or different cloth from the surfaces of the specimen in which they may be to make touch with the rollers.
- Circular rollers synthetic out of metallic having pass phase with diameter 38 mm may be used for presenting assist and loading factors to the specimens.
- The duration of the rollers will be at the least 10 mm greater than the width of the check specimen.
- A general of 4 rollers will be used, 3 out of which will be able to rotating alongside their very own axes.
- The distance among the outer rollers (i.e. span) will be 3d and the gap among the internal rollers will be d.
- The internal rollers will be similarly spaced among the outer rollers, such that the whole gadget is systematic.
- The specimen saved in water will be examined right away on elimination from water; while they may be nevertheless wet.
- The check specimen will be positioned with inside the device efficiently targeted with the longitudinal axis of the specimen at proper angles to the rollers.
- For mould specimens, the mold filling route will be ordinary to the route of loading.
- The load will be implemented at a price of loading of 400 kg/min for the 15.0 cm specimens and at a price of 180 kg/min for the 10.0 cm specimens.
Calculation:
- The Flexural Strength or modulus of rupture (fb) is given via way of means of
- F b = pl/bd2 (while a > 20.0cm for 15.0cm specimen or > 13.0cm for 10cm specimen)
O r
- F b = 3pa/bd2 (while a < 20> 17.zero for 15.0cm specimen or < 13> 11.0cm for 10.0cm specimen.
Where,
a = the gap among the road of fracture and the closer assist, measured at the middle line of the tensile aspect of the specimen
b = width of specimen (cm)
d = failure factor intensity (cm)
l = supported duration (cm)
p = max. Load (kg)
Safety & Precautions:
- Use hand gloves while, protection footwear on the time of check.
- After check transfer off the device.
- Keep all of the uncovered metallic elements greased.
- Keep the manual rods firmly constant to the bottom & pinnacle plate.
- Equipment have to be wiped clean very well earlier than trying out & after trying out.
Key takeaways
1. Beam mildew of length 15 x 15x 70 cm (whilst length of mixture is much less than 38 mm) or of length 10 x 10 x 50 cm (whilst length of mixture is much less than 19 mm)
Indirect Tensile Strength
- Indirect dynamic strength changes were tested from six samples: three dry samples and three samples exposed to water.
- During the indirect strength test, the sample is attached between two load strips and loaded freely at a speed of 50mm / min.
- The maximum load on the crack is measured. The relationship of energy values before and after water storage is determined, and is called the Indirect Tensile Strength Ratio (ITSR).
- Similar to the indirect strength test, a single-axial direct tensile test was initiated to investigate the strength structures of the study. Also, the strength was determined before and after preparing the test sample in the bath water according to EN 12697-12 B.
- The test samples used in this study included prismatic samples of the asphalt compound, as well as rods extracted from the rock and glued together with bitumen film.
- In the testing of dominant asphalt beams, every six beams are cut into slabs of composite asphalt composite (three dry, three wet). Adapters are attached with adhesives to the two parts of the sample surface.
- This is required to load samples into the machine. Strength strength is applied at a speed of 1.5mm / min at a temperature of 15 ° C. After the sample cracking, the strength of the strength is determined from high pressure, and the exact amount of strength strength (DTSR) accordingly.
- Similarly, direct strength testing was also applied to the extruded walls. On the rock covered and glued together the bitumen film.
- The power test is performed with different loading speeds and test temperatures. The broken sample.
- The materials investigated in this study include various types of bitumen (50/70, 70/100), bitumen modified polymer (PmB 40 / 100-65H, PmB 45A), of a wide range of natural materials from adhesive adhesives to adhesive markers. Fine (basalt, Taunusquarzite, limestone, granite, gabbro), and four types of asphalt mixtures (AC 11, AC 16, SMA 11, PA 8).
- Details of the composite, bitumen-aggregate composites, types of asphalt composites and related tests. Preliminary tests have shown that high image quality is very important for reproduction, because both the base installation and the descent frame depend on contrast of the image brightness.
- Therefore, image quality was guaranteed by the introduction of low levels of brightness, contrast, and sharpness of the image as measured by DSA1 software.
- About 10% of the images produced failed to meet these standards and were not included in further analysis. A small number of usable metrics are defined as 30 data points per bit bitumen.
- The data only show slightly different outputs for multiple samples, with the exception of PE6506, and the standard deviation (SD) of the method generally compared the differences between the contact angles of different locations.
- To determine whether communication angles are very different or not, statistical testing methods have been used. The first Shapiro- Wilk test was used for standardized testing. It confirms the general distribution of data. Subsequently, variance analysis (ANOVA), in particular data was subjected to the F test.
- Including all samples tested, the F test rejected the absurd notion that communication angles are very different, i. e. a group of mediators is very different from each other.
- As the mean values of PE6506 deviated significantly from the data of other bitumen, the test was repeated without PE6506. The result shows that in this experiment only PE6506 can be separated from a number of other samples, which can also be separated between them.
- Pendant suction measurements are performed using five bitumen and bitumen precursors. Excess power is measured as a heat function.
- Linear regression analysis can be used in addition to other adjacent conditions because the samples show a very similar pattern at higher temperatures, but a different tendency to deal with lower.
- For example, the two releases include a 95% confidence interval time. Places are very advanced. The results of the addition of all the bitumen studied including error bars, which are found in the external confidence interval.
- The general overlap indicates that this method cannot distinguish between the tested samples. Therefore, the development of testing in relation to rebirth is necessary. The use of small glass slides as a basic model of bitumen-mineral aggregate interface has several advantages.
- First, the surface is perfectly smooth and chemically uniform. Second, the chemical properties of glass are similar to the composition of highly acidic minerals, which usually have a very high content of SiO 2.
- To test the strength of this test, two samples of bitumen (50/70 and 70/100) and a mixture of these bitumen and adherence agent were tested (50/70 + and 70/100 +). New drops of bitumen in the glass gave the same effect to all bitumen.
- After being stored at 70 ° C for 30 minutes, in addition to the bitumen softening points (50/70 and 50/70 +: 48 ° C; 70/100 and 70/100 +: 45 ° C) the results were different. Communication angles are very different from each other. The contact angles of pure bitumen are around 6 ° below the mixtures.
- This means, however, that wettabilities are worse with bitumen containing the input. The final variation of this test was the introduction of static water storage.
Key takeaways
- Indirect dynamic strength changes were tested from six samples: three dry samples and three samples exposed to water.
- During the indirect strength test, the sample is attached between two load strips and loaded freely at a speed of 50mm / min.
Core Test
- Basic concrete testing is the most popular and well-established test method for the compressive strength of hard concrete. Critical concrete testing makes visual inspections of the internal parts of the concrete member also related to strength limitations Portable coring enables the inspection of other reinforced concrete structure structures with solid concrete testing
- In any case, the need to perform basic concrete tests often stems from the failure of concrete cubes / cylinders to get a realistic view of the strength of concrete as it exists in construction materials
Sampling of concrete core
It is very important that basic concrete samples are taken according to the guidelines given below
- Cores should be taken using pieces of diamond-filled spinal cord.
- Cores tested for power structures should have a minimum diameter three times the size design size of a rated set or 50 mm. Whoever is great
- Where possible, cores tested for energy structures should be at least twice their length width
- As far as it is concerned that the reinforcing metal should not be inserted into the spine to be tested for strength. The size, number, and location of the metal reinforcement in the proposed primary area can be determined by using magnetic resonance imaging such as a retrieval meter (cover meter) or by ground-based radar testing or by using a pull-out radar system. If the spine contains a flexible reinforcing steel, a certain effect on the strength should be expected There is a possibility of a decrease in the strength of the concrete slab depending on the position of the steel. This effect is especially important when the metal is very far from the end of the set.
- As far as possible, the foundation pit should penetrate completely into the concrete section. This prevents spinal fractures and facilitates their removal. On the other hand, if drilling is not possible due to the size and configuration of the building in the area where the coring is planned, an additional 50 mm should be bound as a share of potential damage to part of the context.
- One root should not be used to diagnose a specific problem. When cores are taken gain power, a minimum of three characters need to be removed from each location. The amount of concrete strength in the hole should be taken as the benefit of these grains
- Special care needs to be paid when choosing a place for the concrete for standing concrete members such as walls, deep beams, etc. This is due to the differences in high-rise concrete structures due to differences in laying and mixing processes, separation, and bleeding. It is known that in general, the strength of concrete decreases as its height within the placement of membership increases.
- The exact history of structural treatment is often difficult to obtain so the effect of cooling the ammunition is also uncertain. When there is no wet treatment, no power expectations should be expected
- The direction of the ball also affects the strength of the bullets. Horizontally bound cores usually have lower power than direct bound calls,
- When cutting the core, the integrity of the concrete structure in the full section (c / s) is possible is affected to some degree. This feature should be taken into account when selecting a location where the file the core should be taken
Concrete Test procedure
Concrete pieces are usually cut with rotating cutting tools with diamond pieces. The cylinder sample is obtained by concluding its unequal pieces of equal parts, square, and embedded.
Cores are inspected visually to pay attention to the distribution of the composite, the compaction of concrete (non-air visibility), and the presence of metal, etc. The concrete slab should be soaked in water, soaked in melted sulfur so that it ends up parallel to the right angle. It is also tested on a pressure-testing machine in wet conditions in accordance with BIS 1881: Part 4: 1970 or ASTM 42-77.
Use of concrete core sample
- Water or gas leakage
- Chemical analysis
- ASHTO chloride permeability testing
- Determination of strength and resilience
- Depth of concrete installation
- Petro graphic Analysis
Key takeaways
- Cores should be taken using pieces of diamond-filled spinal cord.
- Cores tested for power structures should have a minimum diameter three times the size design size of a rated set or 50 mm. Whoever is great
- Where possible, cores tested for energy structures should be at least twice their length width
Non-Destructive Test - Rebound Hammer
Objective:
- The rebound hammer technique might be used for:
- Assessing the possibly compressive electricity of concrete with the assist of appropriate correlations among rebound index and compressive electricity,
- Assessing the uniformity of concrete,
- Assessing the excellent of the concrete in relation to traditional requirements, and
- Assessing the excellent of 1 detail of concrete when it comes to another.
Principle:
- When the plunger of rebound hammer is pressed in opposition to the floor of the concrete, the spring controlled mass rebounds and the volume of such rebound relies upon up on the floor hardness of concrete.
- The floor hardness and consequently the rebound is taken to be associated with the compressive strength of the concrete.
- The rebound is examine off alongside a graduated scale and is unique as there sure variety or rebound index.
Procedure:
- For trying out, smooth, easy and dry floor is to be selected. If loosely adhering scale is present, this have to be rubbed of with a grinding wheel or stone. Rough surfaces due to incomplete compaction, lack of grout, spalled or tooled surfaces do now no longer deliver dependable outcomes and have to be avoided.
- The factor of effect is to be at the least 20 mm far from any facet or form discontinuity.
- For taking a measurement, the rebound hammer is to be held at proper angles to the floor of the concrete member. The check can as a result be performed horizontally on vertical surfaces or vertically upwards or downwards on horizontal surfaces. If the state of affairs demands, the rebound hammer may be held at intermediate angles additionally, however in every case, the rebound variety may be unique for the equal concrete.
- Rebound hammer check is performed round all of the factors of remark on all on hand faces of the structural detail. Concrete surfaces are very well wiped clean earlier than taking any measurement.
- Around every factor of remark, six readings of rebound indices are taken and common of those readings after deleting outliers as consistent with IS: 8900-1978 turns into the rebound index for the factor of remark.
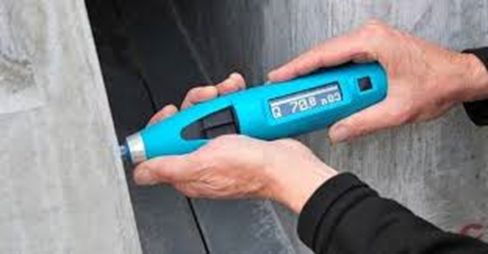
Fig no 10 Showing Rebound Hammer
Interpretation Of Result:
- The rebound hammer technique offers a handy and speedy indication of the compressive energy of concrete via organism appropriate correlation among the rebound index and the compressive energy of concrete. The process of acquiring such correlation is given in 4.2.
- It is likewise mentioned that rebound indices are indicative of compressive energy of concrete to a constrained intensity from the floor. If the concrete in a selected member has inner micro cracking, flaws or heterogeneity throughout the cross-section, rebound hammer indices will now no longer imply the equal.
- As such, the estimation of energy of concrete with the aid of using rebound hammer technique can't be held to be very correct and in all likelihood accuracy of prediction of concrete energy in a shape is ±25 percent.
- If the connection among rebound index and compressive energy may be checked with the aid of using assessments on center samples acquired from the shape or well known specimens made with the equal concrete substances and blend proportion, then the accuracy of consequences and self belief thereon are substantially increased.
Key takeaways
- The rebound is examine off alongside a graduated scale and is unique as there sure variety or rebound index.
Ultrasonic Pulse Velocity
- This take a look at is accomplished to evaluate the nice of concrete with the aid of using ultrasonic pulse pace technique as according to IS: 13311 (Part 1) – 1992. The underlying precept of this take a look at is –
- The technique includes measuring the time of journey of an ultrasonic pulse passing via the concrete being tested. Comparatively better pace is acquired whilst concrete nice is ideal in phrases of density, uniformity, homogeneity etc.
- Procedure to decide energy of hardened concrete with the aid of using Ultrasonic Pulse Velocity:
- Preparing for use: Before switching at the ‘V’ meter, the transducers ought to be linked to the sockets marked “TRAN” And ” REC”.
- The ‘V’ meter can be operated with either:
a) The inner battery,
b) An outside battery or
c) The A.C line.
- Set reference: A reference bar is supplied to test the tool zero. The pulse time for the bar is engraved on it. Apply a smear of grease to the transducer faces earlier than putting it on the other ends of the bar. Adjust the ‘SET REF’ manage till the reference bar transit time is acquired at the tool read-out.
- Range selection: For most accuracy, it's miles endorsed that the 0.1 microsecond variety be decided on for route duration up to 400mm.
- Pulse pace: Having decided the maximum appropriate take a look at factors at the fabric to be tested, make cautious dimension of the route duration ‘L’. Apply couplant to the surfaces of the transducers and press it tough onto the floor of the fabric. Do now no longer flow the transducers whilst a analyzing is being taken, as this could generate noise indicators and mistakes in measurements. Continue keeping the transducers onto the floor of the fabric till a steady analyzing seems at the show, that's the time in microsecond for the ultrasonic pulse to journey the distance ‘L’. The imply price of the show readings ought to be taken whilst the gadgets digit hunts among values.
Pulse pace= (Path duration/Travel time)
- Separation of transducer leads: It is really helpful to save you the 2 transducer leads from getting into near touch with every different whilst the transit time measurements are being taken. If this isn't always accomplished, the receiver lead would possibly pick-up undesirable indicators from the transmitter lead and this will bring about an wrong show of the transit time.
Interpretation of Results:
- The nice of concrete in phrases of uniformity, occurrence or absence of inner flaws, cracks and segregation, etc, Indicative of the extent of expertise employed, can as a consequence be assessed the use of the recommendations given below, that have been advanced for characterizing the nice of concrete in systems in phrases of the ultrasonic pulse pace.
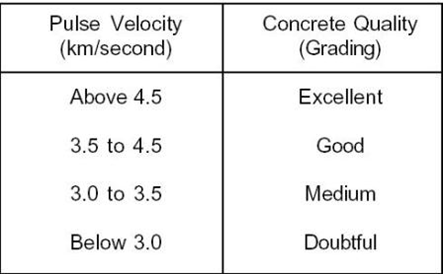
Fig no 11. Table of pulse velocity
Key takeaways
2. Set reference: A reference bar is supplied to test the tool zero. The pulse time for the bar is engraved on it. Apply a smear of grease to the transducer faces earlier than putting it on the other ends of the bar. Adjust the ‘SET REF’ manage till the reference bar transit time is acquired at the tool read-out.
Pullout Test and Impact Echo Test
Pullout Test
The principle
This test is based on the principle that the force required to extract a metal coating embedded in concrete is equal to the strength of the concrete.
Test Process
Remove the insert (shown on the fig tree) embedded in the empty concrete during pouring. When power is required to be determined, power is applied to the embedded end. The power required to issue a meeting is measured.
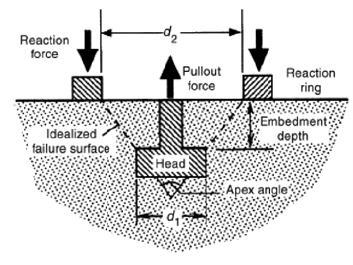
Fig no 12. Pull out the concrete test
Limitations
The steel assembly should be embedded in concrete at the time of pouring so testing may not be carried out in the years to come.
Damage to damaged concrete is required.
Evaluation
- The extraction assembly is pulled by a concrete cone, which is responsible for friction and shaving and the force required to exit is related to the cutting strength of the concrete and not the compressive force.
- The rate of dissipation in the compression force decreases slightly with increasing power level.
- Removal cannot be performed until complete. It is sufficient to insert a fixed power into the embedded pole and if not removed, the supplied power is assumed to exist.
- According to Malhotra, the output test is higher than the Schmidt hammer and the input test because a large volume and depth of concrete are involved in the test. Post-test concrete repairs are also required. The relationship between the force of gravity and gravity is shown in the figure below.
Impact Echo Test
Impact-Echo is a non-destructive exploration method for exploring concrete structures and stone structures. The test uses pressure waves (sound) that are usually made of impact-impact concrete, and to record thinking and emissions from internal errors and other parameters (Echo). Typically, a heartbeat is performed with an effect in one place. The resulting wave of depression is spreading in all directions. In this regard, the generated wave does not have a directional pulse generated by a large transducer (as in the case of ULTRASONIC PULSE VELOCITY). As the reflection reaches in all directions, the test method works well for thin objects, such as piles where the outer boundary directs the wave to the pile. In this particular application, the test is set as the low-level strength test. Learn more about the PILE INTEGRITY TEST.
Concept Behind Impact-Echo Method
The concept of Impact-Echo testing is shown in Figure. The mechanical impact of the concrete surface is used to produce a pressure wave. The production pulse creates a spread across the concrete next to circular waves such as P- and S-waves. Another is the surface wave (R) that moves over.
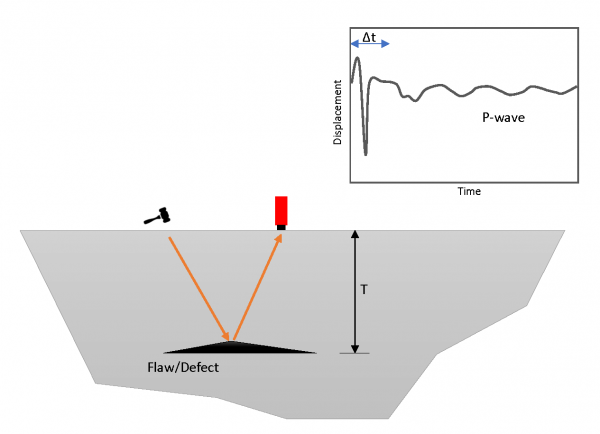
Fig no 13. Impact echo method
As the P- and S waves propagate inside the concrete object, they are indicated by internal interactions (concrete-split, air-concrete, concrete -rebar) or external boundaries. The arrival of these echo in the face causes migration. This migration can be measured by placing a sensitive transducer (which converts the transmission or acceleration of electrical energy). Data is recorded through a data acquisition and data entry system.
Analyses Impact-Echo data
Data analysis can be done in Time Domain, or Frequency Domain. While time domain analysis seems to be the best way to define sensitive data (as in the case of bulk testing), it can be a much more complex approach in the case of small slabs. In these sections, signal analysis in the domain of frequency is popular.
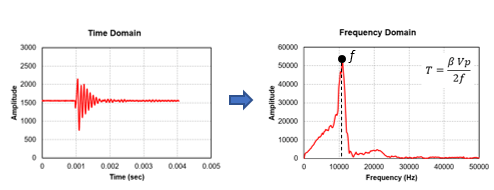
Fig no 14. Analysis of impact echo method
The Fast Fourier transform (FFT) process is used to analyze digital frequency frequency recordings. In this way, the wave form can be represented as a total of sine curves, each with a certain height, frequency and phase shift. According to N. J. Carino. This method is used to calculate the amplitude magnitude of a frequency form, which gives the relative height of the fractional frequencies in the wave form.
Impact-Echo Technique Applications
Impact-Echo is an effective test solution with a variety of applications in assessing the condition of concrete structures. The test can be used to:
1- Measure the thickness of the concrete labs and walls
2- Measure the thickness of the concrete walls and the tunnel line
3- Identify deformities such as delamination in concrete books.
4- Measure the storage condition of concrete, dams, tunnel lamps, sea walls.
Key takeaways
- This test is based on the principle that the force required to extract a metal coating embedded in concrete is equal to the strength of the concrete.
- Impact-Echo is a non-destructive exploration method for exploring concrete structures and stone structures. The test uses pressure waves (sound) that are usually made of impact-impact concrete, and to record thinking and emissions from internal errors and other parameters (Echo).
- Good quality concrete is actually a compact mixture of cement, composite and good mixing with water that mixes into a hard mass due to the chemical action between cement and water.
- Each of the four regions has a specific function. The coarser collection serves as a filler. A good collection fills the gaps between the attachment and the green combination. Cement by contact with water acts as a bond.
- The flow of the mixture is aided by the adhesion of cement, fines to this day, increasingly using mixtures.
- Most of the reinforced concrete materials depend on the care used in all stages of concrete production. The logical separation of concrete ingredients is the core of the mixing design.
- However, it may not guarantee the achievement of the goal of quality workmanship. The purpose of quality control is to ensure the production of concrete of the same power from batch to batch.
- This requires that certain rules be followed in the various stages of concrete production and discussed below. The stages of concrete production are:
1. Batching and measurement of material
2. Mixing
3. Transport
4. Placement
5. Compacting
6. Curing
7. Finishing
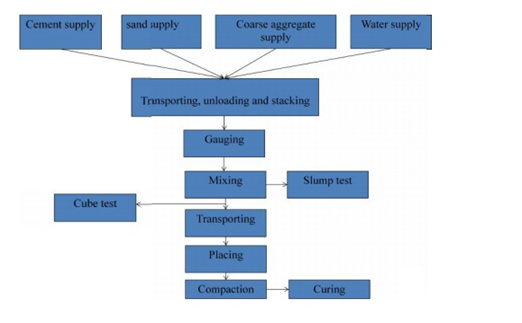
Fig no 15. Manufacturing process of concrete
Batching of material
- For good quality concrete should be used the correct and accurate amount of all ingredients. Combined, cement and water must be measured with an accuracy of 3 percent of batch quantity and admixtures at 5 percent of the total value. There are two most common forms of baking material, batching volume and heavy batching. Factors affecting the choice of baking method by the size of the work, the required production rate, the required batching performance standards. It is recommended for the most important tasks.
a) Volume batching
b) Weight batching
Mixing
1. Hand Mixing
2. Mixing Machine
a) Tilting mixers
b) Non- tilting mixer
c) Reversing Drum mixer
d) Pan type or stirring mixer
e) Transit mixer
f) Charging Mixer and mixing time
The order for the ingredients in the mixer is as follows:
- About 25 percent of the water needed for mixing is initially placed in the mixing tank to prevent any cement attachment to the rings and bottom of the drum. Then the ingredients are extracted in excess. To skip over the loading sequence should be to insert the first half of the coarse cement and then the composite half to be on top of this complete cement and the aggregate to balance. After adding the ingredients to the drum equal volume was introduced. The mixing time is calculated from the total water added to the mixture.
- The speed of the aggregates is usually 15 to 20 per minute. With proper mixing, the number of changes per minute required by the drum is 25 to 30. The mixing time also depends on the mixing capacity
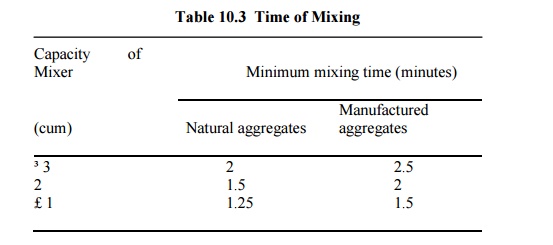
Fig no 16. Table of mixing
- Poor quality of concrete is obtained when mixing time is reduced. On the other hand if the mixing time is extended it is not economical. However, it is found that when the mixing time is extended to 2 minutes the compressive strength of the produced concrete is improved and beyond this time the improvement of the compressive strength is not significant. Prolonged mixing can cause separation. Also, due to the long mixing times water can get in or out and lead to loss of function and energy.
Transporting
The concrete should be moved to the storage area immediately without the loss of homosexuality acquired during mixing. a maximum of 2 hours from mixing time is allowed if trucks have an agitator and 1 hour using trucks without stimulants to move the concrete. And it must be ensured that separation does not occur during travel and placement. The methods used to transport concrete depend on the quality and value of the work, the distance to the placement site, and the location. Some of the concrete delivery methods are below:
a. Mortar pan
b. Wheel barrow
c. Chutes
d. Dumper
e. Bucket and ropeway
f. Belt conveyor
g. Skip and hoist
h. Pumping
Placing
- Achieving quality concrete should be placed very carefully to protect the homosexuality achieved during mixing and to avoid transport segregation. Studies have shown that delays in the installation of concrete results in gaining greater compressive strength as long as the concrete is not sufficiently compacted. In dry mixes in hot weather a delay of half an hour is allowed and in wet mixtures when it is cold it can be a few hours. The various conditions in which concrete is applied are discussed below.
Foundations
- Concrete foundations for walls and columns are provided underground. Before laying concrete on the foundation all open ground, tree roots etc., are removed. If the area is found dry it is made wet so that the soil does not absorb water from the concrete. On the other hand when the foundation bed is wet the water and mud are removed and the cement is sprinkled before laying the concrete.
Beams, columns and slabs
- Before laying the concrete, the forms must be inspected for proper alignment. They should be strong enough to withstand the weight of concrete and construction loads without undue damage. The forms should be light enough to avoid any mud loss that has resulted in concrete mixed with bees. The inside of the forms should be cleaned and oiled before use to avoid any adhesion to the concrete and forms and make it difficult to remove them.
- Concrete should not be discarded but should be placed in a place to protect against discrimination. It should be lowered as high as possible. It should be placed in one place on the formwork and allowed to flow in separate ways to take care of the bee colony.
- The formation of seas should be avoided. Can be tested by preventing concrete thickness by 150-300 mm with r c c function. Laitance, however, if constructed must be removed before laying the next layer of concrete. Several such layers form an elevator, as long as they follow each other fast enough to avoid cold joints. The top of the previous elevator is kept rugged and all the money spent is wiped out before setting the next elevator.
- Firmness should be checked for firmness and clean face. Rust or loose scales if present, are removed with a wire brush. Paint, oil or grease if found should be removed. a small tightening cover should be checked before assembly.
Mass concreting
- Where the concrete will be laid in bulk as a foundation for raft, dam, bridge, pier etc., the concrete is laid in sections of 350-450 mm in diameter. Several such layers arranged in quick succession form an elevator. Before applying the concrete to the next lift, the front elevator area is thoroughly cleaned with water jets and scrubbing with a wire brush. In the case of dams, sand explodes.
- Laitance and lax matter are removed and cement mortar is applied. Where the concrete is subjected to lateral thrust, binding bars or binding stones are provided to form the key between the various layers.
Concreting Highways and Runways
- Concrete is placed in the areas of highway, open road, or floor slabs. First the soil on which the concrete is to be placed is prepared and all loose material and grass are removed etc. The ground is wet and compacted. The subgrades into which the concrete is to be placed should be well mixed and diamond-plated to avoid any moisture loss in the concrete. The concrete is then placed elsewhere. This allows the concrete to pass through enough and the cracks do not grow after that. Concrete is not placed in a pile in one place and then pulled out, instead it is placed in the same size.
Concreting underwater
- Concrete can be placed under water with the help of dumping buckets. The concrete is soaked in water from a water-tight bucket. When you get to the floor the bucket is made open and the concrete is discarded. In this process a certain amount of cement is washed away resulting in a decrease in the strength of the concrete. Another way to make underwater concrete is to fill a bag of cement with a dry or dry mixture of cement and aggregates and lower it into the storage area. The downside to this approach is that the concrete will fill the gaps filled with the bags with the guns.
- A good way to put concrete under water is to use a termie pipe. Concrete is poured into it by a ditch. The lower edge of the pipe is covered with thick ploythene paper, below the pipe in the installation area. Concrete (150-200 mm fall) is poured into the mortar until the entire pipe is filled with cement. The pipe is slightly raised and given a jerk, the polythene metal cover falls off and the concrete is shown. It must be ensured that the end of the pipe stays inside the concrete so that water does not enter the pipe. The pipe is then filled with concrete along the border and the process is repeated to the concrete level above the water level. No reduction is required for underwater concrete as combined with hydrostatic water pressure. Concrete can also be placed under water with the help of pipes and pumps.
Compaction of concrete and curing process of concrete
1) Compaction of concrete
- Concrete should be thoroughly compacted and fully work around the reinforcement and into the corners of the formworks
- Concrete shall be compacted using mechanical vibrators
- Whenever vibration has been applied externally the design of formwork and the deposition of vibrators should receive special consideration to ensure efficient compaction and to avoid sir face blemishes
2) Curing process of concrete
- Curing of concrete is defined as the process of maintaining the moisture and temperature condition of concrete for hydration reaction to the normally so that the concrete develops hardened and properties over time
- The main components which need to be taken care of your heat and time during curing process
- Curing is the process of preventing the loss of moisture from the concrete which maintaining a satisfactory temperature effect
- If the cement has high rate of strain development and if the concrete contains granulated blast furnace and flue Ash then,
- The curing should also prevent the development of high temperature gradients within the concrete
a) Moist curing
- Surface of the concrete shall be kept continuously in Dam or wet condition by covering with the layers of materials like checking Canvas etc.
- It should be kept continuously wet for at least 7 days from the date of placing concrete.
- In case of ordinary Portland cement at least 10 days. Where mineral admixture or blended cement are used.
- The period of curing shall not be less than 10 days for concrete exposed to the dry and hot weather condition.
- In case of concrete where mineral admixture or blended cement are used it is recommended that above minimum period may be extended 14 days.
b) Membrane curing
- Approved curing compounds may be used in place of moist curing with the permission of engineer in charge.
- Search compound shall be applied to all exposed surfaces of the concrete as soon as possible after the concrete has set.
- Impermeable membrane such as polyethylene sheeting covering closely the concrete surface may also be used to provide effective barriers against evaporation.
- For the concrete containing Portland pozzolana cement, Portland slag cement or mineral admixture period of curing may be increased.
NOMINAL MIXES
- In concrete mix concrete, all ingredients and their size are determined by standard definitions. This ratio is specified in the cement ratio to the specific energy gain combination.
- Mixing ratios such as 1: 1.5: 3, 1: 2: 4, 1: 3: 6 etc. They were adopted by mixing concrete without a scientific basis, only on the basis of previous studies of solidarity. Therefore, acceptance of ordinary concrete or not to mention, the mixing of preference is preferred for simple, insignificant and minimal concrete works.
- According to the 'Indian Standard- IS 456: 2000', pre-mixed concrete can be used for M20 grade concrete or lower grade such as M5, M7.5, M10, M15.
Proportion of nominal mix as per Indian Standard
- The volume of composite materials under M20 grade concrete will comply with IS 456: 2000
- According to IS 456: 2000, in the composition of the composition can be adjusted the estimated values if the water level will be increased to overcome the difficulty of laying and density of concrete so that the water level of the cement is maintained as specified.
- Automatic mixing usually consists of volumetric batching. The measurement is usually determined by weight, and in combination it is converted to a volume value, i.e. in the case of one bag of cement, i.e. 50 kg of standard measuring boxes are made on site, at the rate of one bag of cement. These measuring boxes are called box gauges.
Advantages of nominal Mix Concrete
01. A self-proclaimed mix is a pre-determined concrete because the scale is pre-determined.
02. It is easy to do in the construction site.
03. It does not take much time to determine the value because the size is already provided with the standard code.
04. There is no need to find people who have the skills to make concrete mixing name.
Disadvantages of nominal mix concrete
01. The great recurrence of the mix of claims is that, it is based on past experience and studies of art, and has no scientifically proven method.
02. It can create or build well-designed energy unless all other factors such as density, w / c ratio, concrete treatment are strictly adhered to.
03. The amount of water cement is considered by thought and, if left unchecked, sometimes leads to bleeding and separation of the concrete which leads to poor performance and therefore impairs the strength of the concrete.
04. No consideration of composite structures such as classification and quantity of composite items etc.
05. In a word mix, cement content is sometimes used in excess, which increases the total cost of construction.
06. No laboratory tests are performed to ensure the quality of the new concrete.
07. This combination does not consider and evaluates the specific properties of each ingredient. For example, if we take cement as part, the softness of the cement, the quality of the cement and the type of cement, the size and layout of the composite etc. It is usually not counted individually when making this fake assertion mix.
Key takeaways
- In concrete mix concrete, all ingredients and their size are determined by standard definitions. This ratio is specified in the cement ratio to the specific energy gain combination.
- Mixing ratios such as 1: 1.5: 3, 1: 2: 4, 1: 3: 6 etc. They were adopted by mixing concrete without a scientific basis, only on the basis of previous studies of solidarity. Therefore, acceptance of ordinary concrete or not to mention, the mixing of preference is preferred for simple, insignificant and minimal concrete works.
- According to the 'Indian Standard- IS 456: 2000', pre-mixed concrete can be used for M20 grade concrete or lower grade such as M5, M7.5, M10, M15.
Freeze-Thaw Effect:
Concrete is very strong in compression but relatively weak in tension. It can and often does crack. Concrete is also fairly porous and subject to forces that absorb and release water. Absorbed water can freeze within the concrete and cause spalling and cracking.
Chemical Attack:
Chemical attack can occur because concrete is alkaline and chemically reactive. It can be attacked by acids; some alkalis; numerous salt solutions; and organics such as fermenting liquids, sugars, and animal oils, especially if they contain free acids.
Crazing:
This is a network of very small surface cracks usually spreading out over large areas or the entire surface. Crazing is caused by finishing the concrete with bleed water on top. The bleed water is forced down into the surface by the finisher’s trowel. This increases the ratio of water to cement, creating a weak surface layer.
Scaling:
Thin flakes of concrete come loose and flake or peel off the surface. The sizes of the flakes vary, but they usually increase over time and with traffic. Conditions that cause scaling and include freeze/thaw cycles, deicing agents with calcium or sodium chloride, fertilizers containing nitrates, working in bleed water, or improper curing.
Blisters:
These are typically about 1/4 to 1 inch diameter, but it’s not impossible to get 3 to 4 inch blisters. They are not easily seen until they are broken by traffic. Blisters are caused by working and finishing the surface while water or air is still working its way up through the mix to the surface.
Spalling:
Spalling is similar to scaling except large chunks instead of just flakes break loose. This indicates a severe weakness in some parts or the entire project. It is more likely to happen during freeze thaw conditions.
Dusting:
Also known as chalking, this is a fine loose powder caused by the deterioration of a weak surface. Causes of dusting include working in bleed water, improper curing, a bad sand-to-cement ratio, or exposure to carbon monoxide caused by using an unvented heat source to keep a project warm.
Foreign Objects:
Foreign objects can often slip into the form prior to pouring and may not become evident until after the forms are stripped. If fully embedded, the foreign object does not create a coating problem. But a piece of rope on the surface disappearing into the concrete is a problem. It must be removed, usually by chipping, and the concrete must be restored.
Efflorescence:
Efflorescence is more likely to be found on concrete that has been in place for a while. Concrete contains water-soluble salts. As water from the interior of the concrete migrates to the surface and evaporates, salts are deposited on the surface, usually as a white stain. Efflorescence can occur with concrete, brick, or concrete block construction. It can be removed with acid etching. The best way to prevent its recurrence is with adequate waterproofing.
Service / Market Area:
For industrial and commercial flooring projects we work in Michigan cities such as Muskegon, Norton Shores, Newaygo, Traverse City, Big Rapids, etc.
- Many types of admixtures or additives change the performance of a new concrete, either by construction or as a side effect.
- Surfactants such as super plasticizers reduce the attraction between cement and composite particles, allowing compounds that can flow without negative energy and the effects of excess water separation.
- The insertion of internal admixtures of durability / dissolving solids produces internal bubbles of a controlled size that can make it easier to eliminate, although overuse produces an adhesive mix with a different effect.
- The pressure of the concrete is eight times greater than its strength.
- This refers to the established relationship between the compressive strength and the strength of the concrete. In fact there is a close relationship but not a direct relationship.
- The degree of stiffness and pressure is low at high pressures.
- Experimental results also showed that concrete in stress and stress (both direct and indirect tension) is highly correlated but the relationship does not have a direct equation.
- The degree of strength and durability depends on the strength of the concrete.
- Thus, the increase in tensile strength, increases the tensile strength, but the rate of increase in tensile strength decreases steadily.
- The strength of concrete is more sensitive to improper treatment than to compressive strength.
This is possible for two reasons:
(a) The formation of a low-grade gel due to improper treatment.
(b) The formation of multiple shrinking cracks due to improper treatment. The use of pozzolanic materials showed an increase in strength.
- The Central Road Research Institute Delhi has conducted extensive research to build a relationship between the strength and durability of concrete in the construction of concrete roads.
- Based on the research experimental data, CRRI suggested the following relationship between flexural strength and concrete compression strength:
y = 11 x - 3.4
- Where is the compressive strength of MPa concrete and x and its flexibility. This relationship depends on the size of the coarse aggregate. Energy is available to vary in type and quantity of composite.
Relationships are renewed below:
(a) With a crushed stone of 20 mm y = 15.3 x - 9.0
(b) 20 mm Natural Graval y = 14.3 x - 10.4
(c) For 40 mm Crushed Stones y = 9.9 x -5.5
(d) 40 mm Natural Graval y = 9.8 x - 2.5
Key takeaways
The pressure of the concrete is eight times greater than its strength.
This refers to the established relationship between the compressive strength and the strength of the concrete. In fact there is a close relationship but not a direct relationship.
There are three main factors that affect concrete compression results: the specimen size, shape, and friction at its ends. These factors affect the observed phenomena, and they affect each other. This paper aims to review the current knowledge on concrete compression and the effect of size, shape and friction on it. Understanding their effects is essential for a safer design and more effective testing.
- Creep and thinning concrete are the two most visible features of concrete. The shrinkage of concrete, derived from calcium silicate hydrate (C-S-H) in a hardened Portland cement compound (which is responsible for mineral compounds), is quite different from the tilt of metals and polymers.
- Unlike metal cracks, it occurs at all levels of stress and, within the service level of stress, depends on what is stressed if the pore water content remains the same.
- In contrast to the eruption of polymers and metals, it exhibits several months of aging, caused by chemical hardening due to hydration that strengthens the formation of micro-organisms, and age-old aging, resulting in long-term resting of small equal pressure in nano- low CSH formation. When the concrete is completely dry, it does not move, but it is almost impossible to dry the concrete completely without severe cracking.
- Changes in water content in the pore due to dryness or watering processes cause significant changes in the volume of the concrete in non-load-bearing species. They are called shrinkage
- The age-old insect varies logarithmically over time (except for the final asymptotic value), and over normal life spans can receive values 3 to 6 times larger than the initial stretch problem. When deformation formation is abruptly induced and held inconsistently, the movement causes a break in the pressure produced in moderation. After discharge, increased recovery occurs, but in part, due to aging.
- In practice, travel during drying is inseparable from diminishing. The flow rate increases with the rate of change of pore humidity (e.g., vapor pressure associated with the pores). In the size of a small model, the penetration during drying far exceeds the total reduction of load without load and the penetration of the closed-loop template. The difference, called the drying creep or Pickett effect (or pressure-induced decrease), represents a hygro-mechanical between pore changes and pore humidity.
- The drying of the high humidity is mainly due to the pressure pressures on the solid microstructure that measure the increase in capillary tension and the surface tension in the pore walls. At low pore humidity (<75%), the shrinkage is caused by a decrease in the binding pressure across all nano-pores less than 3 nm in diameter, filled with indicated water.
- The chemical processes of Portland cement hydration lead to another type of shrinkage, called automatic shrinkage, which is detected in closed specimens, i.e., without loss of moisture. In part, this is due to changes in chemical volume, but especially energy loss due to the loss of water used by the hydration reaction.
- It achieves only about 5% of the dryness in normal cones, which self-desiccate about 97% of pore humidity. However, it can be equivalent to the reduction of drying in today's high-strength concrete containers with very low cement levels, which can cause the floor to have a humidity of less than 75%.
- The creep comes from calcium silicate hydrate (C-SH) attached to Portland cement. It is caused by slips due to breakage of bonds, by restoration of bonds in nearby areas. C-SH is highly hydrophilic, and has a colloidal microstructure separated from a few nanometers upwards. The paste has a porosity of about 0.4 to 0.55 with a large internal surface, about 500 m2 / cm3. Its main component is tri-calcium silicate hydrate gel (3 CaO · 2 SiO3 · 3 H20, abbreviated C3-S2-H3). The gel forms particles of colloidal size, which are weakly bound by van der Waals forces.
- How it works and modeling is still debated. The structural model in the following scales is not only available but at the moment has a very solid theoretical basis and fits very well with the full range of test data available.
Key takeaways
- Changes in water content in the pore due to dryness or watering processes cause significant changes in the volume of the concrete in non-load-bearing species. They are called shrinkage
- A concrete blend is a mixture of 5 primary factor numerous proportions: cement, water, coarse aggregates, quality aggregates (i.e. sand), And air.
- Additional factors including pozzolana substances and chemical admixtures also can be integrated into the combination positive ideal properties.
- While a concrete blend layout is a system of choosing substances for a concrete aggregate and choosing their proportions.
- When designing a blend, you don't forget the favored power, durability, and workability of the concrete for the venture in question.
- Needless to say, Already-blend manufacturers attempt to locate the suitable proportions of those substances to optimize the concrete mixes and provide their concrete power, durability, workability, and different ideal properties.
- It’s crucial to optimize concrete to make sure the bottom keeping the very best power of your aggregate.
- Concrete blend layout is frequently mistake analysis “cement blend layout.” However, cement is since rely one of the substances of concrete.
- It is a binding substance that let sin concrete to set, harden, and cling to different substances.
- Therefore, it can't and ought to now no longer be used interchangeably with concrete blend layout.
Objective
The following are the objectives of the concrete mix design:
a. Finding the pressure force at a certain distance.
b. Maintain concrete mixing performance throughout the work.
c. By gaining strength.
d. Achieve economy by choosing the right concrete ingredients.
e. Getting the highest yield in a cement bag.
f. Avoid bee contact and bleeding.
g. Compliance with various levels.
h. Reduce concrete damage by proper measurement.
The proportioning of concrete mixes consists of determination of quantities of different concrete-making materials necessary to produce concrete having the desired workability and 28-days compressive strength of concrete for a particular grade of concrete and durability requirements. Emphasis is laid on making the most economical use of available materials so as to produce concrete of required attributes at the minimum cost.
Concrete has to be satisfactory both in fresh and hardened states. The proportioning of concrete mixes is accomplished by the use of certain established relationships from experimental data which provides reasonably accurate guidance for selecting the best combination of ingredients so as to achieve the desired properties of the fresh and hardened concrete. Out of all the physical characteristics of concrete compressive strength is often taken as an index.
- Strength and sturdiness of the concrete blend layout are established upon the subsequent factors:
- Grade designation: Concrete’s power is measured in N/mm2 whilst issue to check after curing in any curing medium. The preference of concrete grade relies upon on its utilization.
- Choice of cement: Cement preference varies relying on utilization. The cement have to be examined for overall performance required with the aid of using their utilization earlier than being examined with inside the layout blend.
- Choice of mixture size: Aggregates wanted for every blend depends upon the bodily houses wanted for the layout. All aggregates need to be nice sized earlier than use.
- Type of water: Any water used for concrete blend layout is to be examined earlier than use to make certain it's far with inside the variety of water required for concrete. Most all consumable water is right for concrete work, however have to nevertheless be examined.
- Water to cement ratio: The ratio of water to cement have to be examined for consistency, preliminary and very last setting, soundness of the cement, workability, hunch of the concrete and compacting factor.
- Workability: This is the degree of ease of blending concrete without segregation or bleeding. It by and large relies upon at the designed hunch of the concrete.
- Durability: This is the degree of the specified power (N/mm2) of any concrete grade after 28 days of curing. Durability have to be manipulate examined on site.
Key takeaways
- Here different type of factors which affects mix proportion are durability, workability, water to cement ratio, type of water, choice of mixture size, choice of cement, grade designation.
The following points highlight five methods of concrete construction. The methods are:
1. American Method of Mix Design
2. Graphic Method of Mix Design
3. Mix Design by Indian Standard Method
4. American Concrete Institute Method of Mix Design
5. Quick Method of Mix Design.
1. The American Way of Mixing Designs:
- The American Concrete Institute (ACI) approach is based on the fact that the given size of a mixture of water content per kilogram of concrete determines the performance of a concrete mix, usually independent of the equilibrium. It is therefore possible to start the mixing formation by selecting the water content in these tables.
- In addition it is also assumed that the maximum volume of the estimated quantity of the total value of the concrete depends only on the maximum size and the combination of good composites.
2. Graphic Method of Mix Design
- This approach was developed by the Road Research Laboratory, London and its detailed procedure is described. Combined composites are supplied and their percentage above the normal working fine collection is 4.75 mm, 2.36 mm, 1.18 mm. 600 microns, 300 microns and 150 microns are used. For the maximum combined size of the allowable size, it says 38 mm, 19 mm, 9.5 mm 4.75 mm, 2.36 mm is used.
3. Assemble Design in a Traditional Indian Way:
- The Indian Bureau of Standards has recommended the concrete construction process in conjunction with the experimental work carried out in national laboratories. The mixing process is provided by IS-10262- 1982. Subsequently no updates have been made to this process , and IS 456-1968 has been updated in 2000. That is why IS 10262-1982 needs to be reviewed as the cement power available to a highly developed country.
Therefore the following changes need to be made:
1. The 28-day capacity for phase A, B, C, D, E & F renewal needs to be reviewed.
2. The relationship between the different strengths of cement and the size of w / c should be re-established.
3. The relationship between 28 days of pressure and w / c ratio should reach a pressure of 80 MPa (800 kg / cm2), if the graph is to be used for high strength concrete.
4. According to the revised IS 456-2000 the usability level is expressed in degradation instead of compacting factor. This change requires new amounts of sand and water content for the use of standard concrete up to 35 M Pa and high strength Concrete over 35 M Pa.
- However in the absence of a review on IS 10262-1982, the existing IS 10262 process is described below as a smart move.
- The IS recommendations for mixing design include the composition of the mixing of self-contained (non-ventilated) concrete of medium and high strength concrete.
The integration method consists of the following:
(a) Water content
(b) Percentage of penalty collections corresponding to the maximum aggregate size of the reference value
(c) The amount of cement water, and
(d) Preservation of penalty collection.
- Water content and percentage of fine aggregate and adjust for any differences in performance. Finally the size of the ingredients per unit of concrete volume is calculated in the form of absolute volume. This method works for both underground pozzolana centers.
- The final amount of compounds selected after the experimental mixing, may require minor adjustments. In the case of fly ash cement, the water content can be reduced by about 3 to 5% and a good portion can be reduced by 2 to 4%.
4. American Concrete Institute Method of Mix Design:
- Although the ACI committee published its mixing method in 1944 and almost all concrete dams using a lot of Indian works were designed using the ACI committee method used at the time of mixing. Since then many improvements have been introduced in a practical way. Here is a discussion of the latest method of constructing concrete mixes based on ACI 211-1 of 1991 manual part-time concrete recommendations.
The ACI committee took the following basic ideas:
1. The new collapsed concrete provided and containing a fully proportional measure of the maximum given size will have a fixed water content, regardless of the w / c ratio and the cement content associated between the maximum range of operating parameters.
2. The maximum stiffness of the coarse aggregate per unit of concrete per unit depends on its maximum size and the correct modulus of the fine compound as shown in table 20.39 taking into account the minimum particle size. The effect of angularity is reflected in the empty content. So angular green joints require more mud than circular joints.
3. Regardless of the compaction methods, even when complete compaction has been achieved, a certain percentage of air remains in the concrete and is proportional to the maximum volume.
Mix Design Process:
For compound design, the following data is required to be collected:
(a) Fineness modulus of selected fines.
(b) The unit has the weight of the selected dry fine.
(c) The gravitational force of coarse and fine aggregate in saturated, dry areas.
(d) Absorption of combined rates and penalties.
(e) The gravitational force of cement.
5. Quick methods Mixing:
- Measuring the initial amount of cement water according to purpose means the actual strength will be to combine it with 28 days of cement strength. Feature strength is found to be better related to 28 days of cement strength than in age. This method will therefore require 28 days to determine the size of the cement and the next 28 days of testing mixing the strength of the concrete. The 28-day strength of the cement can be considered as that provided by the curves
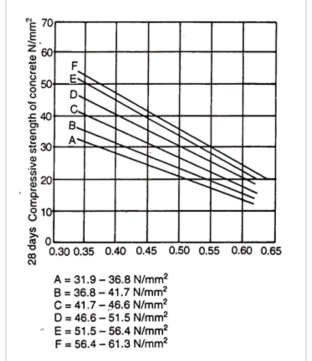
Fig no 17. Graph of compression strength of concrete
- 28 days or 56 days is too long for the contractor to wait for the results of the merger. There is a tendency to use direct mixing without trying experiment mixing. To reduce the time required for the mixing of experiments, the Cement Research Institute of India (CRI) has developed a method called rapid method, in which the compressive strength of cement and cement is obtained using a rapid therapeutic method as discussed in IS 9013-1978. This method reduces the recovery time of experimental compounds from 28 days to only 3 days.
- 28 days of concrete hardening is found to be highly correlated with statistics and rapid strength. Therefore the combination of temptation in line with the target means faster energy than the target means 28 days of energy, with the help of a combination between the two.
- This mixture is obtained independently by the type or characteristics of the cement used i.e. the mixture is not affected by the type of cement used, probably because it affects the fast and normal concrete strength of 28 days equally, so that the result is neutral in comparison. The advantage of each operation is such a combination can be established by the type of building material and assembled to the size to be used.
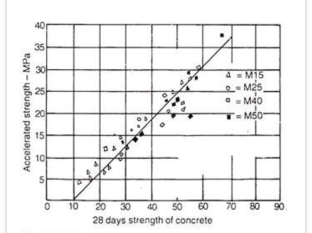
Fig no 18. Strength of concrete vs accelerated strength
- On the other hand, the results of a stable acceleration test in standard cement mortar such as IS 4932-1968 Were not found to be reliable. This problem is overcome by inspecting the cement and quickly and determining its speed.
- The concrete composite concrete or the fastened concrete mixing strength has a w / c value of about 0.35 and the performance is much lower with slump 0 to 10 or compacting factor 0.8 per available cement i.e. (cement in hand).
- The maximum size of the crushed natural compound name should be 10 mm and a good composite should correspond to area II of table 4 of IS-383-1970.
Key takeaways
The following points highlight five methods of concrete construction. The methods are:
1. American Method of Mix Design
2. Graphic Method of Mix Design
3. Mix Design by Indian Standard Method
4. American Concrete Institute Method of Mix Design
5. Quick Method of Mix Design.
The quality of concrete construction on site can be done in three different phases as follows
1. Quality control before integration
2. Quality control during integration
3. Post-construction quality control
STAGE 1 (QUALITY CONTROL BEFORE CONCRETING)
This phase of quality control has two steps.
- Assessment of specification requirements regarding mining, forms, consolidation and embedded repairs etc.
- Control test for concrete ingredients (eg cement, composite and water)
Cement
Cement quality is obtained by performing strength tests of cement cubes. However, with effective control cement:
- It should be tested first and foremost for each source and then tested every once every two months
- It should be protected from moisture
- It should be returned after the last 3 months, if long-term storage is unavoidable
- It should be rejected if a large lump is found in the cement bags.
Aggregate
Concrete composites should be validated at specified values as standard specifications.
The quality of concrete is affected by the various physical and mechanical properties of the composite, namely structure, proportions, durability, gravity and water absorption etc. These composite structures should be tested before using them to produce concrete.
The amount of horror and natural pollution should also be considered.
Sand connections are also an important asset in a number of ways. Provides incorrect results when volume encryption is performed .It increases the amount of water cement which also reduces energy.
With aggregate functional controls:
- They need to be tested once in the beginning to allow the source
- If it is to be checked once or twice daily the moisture content and grant must be made for the combined moisture content.
Water
Water quality should be assessed for needs as defined at the appropriate level. Chemical analysis will be performed to authorize the source. In the event of contamination, it is necessary to store the water for a period of time to allow it to settle. In case of doubt the concrete cubes made of this water are examined. A maximum of 28 days of pressure for at least three cubes or cylinders or a set size, prepared for the proposed water use shall not be less than 90% of the strength between three cubes of the same concrete prepared with distilled water.
STAGE 2 (QUALITY MANAGEMENT DURING CONCRETING)
Careful precaution during concrete is required for all assembly operations such as baking, mixing, transporting, placing, coating and curing. Follow-up safety measures should be taken during concreting operations.
- The concrete mix should be built into the laboratory and the materials to be used on site.
- As far as possible the concrete should be driven by weight. If weight assembly is not possible, volume collection can be allowed with proper monitoring in the presence of the lead engineer.
- During mixing the mixer should be charged in full. Building materials should be fed in the right order. The mixer speed should be from 15 to 20 fluctuations per minute. The mixing time should not be less than 2 minutes in any case. Separation should be avoided when loading concrete into the mixture.
- The performance of concrete is an important material of concrete while concrete is in its new state. Therefore testing of slump or compaction factor should be performed to check the performance of the concrete. About three tests should be performed on every 25 m3 of concrete.
- Care should be taken so that no separation occurs during the concrete transfer.
- Concrete should not be lowered from a height of not more than 1 m. If the height of the drop is more than 1 m chutes should be used.
- To avoid re-release the concrete should be placed in its final position as much as possible.
- Vibrators should be used to connect the concrete. Internal vibrator installation space should not exceed 0.6 m. It should be lightly painted so that no holes are left in the concrete. Vibrator frequency should not be less than 7000 cycles / minutes.
- The treatment should be done over a period of time so that the concrete develops the required strength. Concrete should be covered with hessian as soon as it becomes hard.
- The form function must be aligned with the final form of the form. It should be checked before the start of integration. The inside of the forms should be cleaned and oiled. Forms must be removed after the deadline.
- Concrete should be protected from hot and cold weather at an early age. Concreting should not be performed at temperatures below 4.50C and above 400 In very hot weather water and aggregates should be cooled. Approved quality retards can be used.
- In very cold weather water and aggregates should be heated. Approved quality Accelerators can also be used.
STAGE 3 (QUALITY CONTROL AFTER CONSTRUCTION)
- Once the concrete has been laid and assembled, a pressure test is performed on the tubes made of this concrete. With standard concrete, cubes are made of concrete made in the workplace.
- Reinforced concrete should be considered to be true in size, shape and size as specified in each design. The appearance of the concrete surface should also be checked. Sizes are available in various sizes. Reinforcement should have adequate concrete cover and if reinforcement is visible on the part of the structure, the part should be rejected or appropriate action taken.
Concrete strength is usually obtained by cube or cylinder samples tested within 28 days. In the event that the power received is less than the specified minimum, one or more of the following steps may be taken.
- Load testing and deviation of the deviation and / or difficulty (structural quality can also be obtained by calculating back concrete strength)
- Cutting cores from structures and testing them for strength
- Non-destructive tests such as the Schmidt rebound hammer or ultrasonic pulse velocity test. These tests give a very complex view and are used to find structural similarities.
- Chemical analysis of hard concrete.
Key takeaways
The quality of concrete construction on site can be done in three different phases as follows
1. Quality control before integration
2. Quality control during integration
3. Post-construction quality control
The behavior of the concrete under high temperature values could be affected with several factors. The temperature rate, aggregate type, and stability of the mixture are among the most important factors to be considered under high temperature condition. It is noted that the abrupt temperature rise can cause thermal shock, spalling, cracking, and aggregate expansion leading to high distress within the concrete.
The durability of the concrete against freeze-thaw cycles is previously investigated as a major factor indicating the ability for resistance against weathering actions.
Cold and hot weather concreting
Introduction
- Concrete and other structures are constructed in many countries around the world and in some places the climate is symbolized by the long spells of hot or cold weather. Concrete companies that are ready to integrate and build in these regions are able to produce high quality concrete despite these weather problems. In many regions with unfavorable weather conditions there are set conclusions and concrete production guidelines that provide details of the methods that can be used to combat adverse conditions.
- In the cooler parts of the world, cool, humid climates are common. In these areas, although cold or cold temperatures are not uncommon, it is often surprising when they arrive and it may be too late to apply even safety measures to minimize their undesirable effects,
- Physical effects in both hot and cold conditions should not be overlooked. Workers and managers will not be expected to produce good quality concrete if exposed to conditions for a long time without proper protection
- When the process of serving the container is done on its own it is not a matter of deciding whether to pour concrete. Air temperature, humidity, and wind speed, higher temperatures where you put concrete, water and dry concrete in the bag all play a big role and should be considered. The air, air and moisture are much better than you can handle but you can also influence it. It is important to remember that the temperature of the mixed material is as important as the temperature of the air.
- The strength and durability of concrete are at odds with the climate in which the composite process is performed. Therefore, construction workers will need to take extra care or take action when it comes to worship. In fact, some parts of the world remain hot all year long. These are situations where paying attention to a few simple but much-needed points in hot weather can definitely help to complete any display without compromising its quality. Sunlight leads to hot weather which forces us to use special methods while barking known as hot weather concreting,
Hot Weather concreting
Definitions
- The definition of a tropical climate may vary from country to country. According to the Indian climate, Indian codes determine 40 ° C as the temperature range for hot climates. That is to say, any combination made at temperatures above 40 ° C can be considered as a hot climate that allows for certain measures to be adopted.
- Obviously, this is not the case in most other parts of the world because of the climate. For example, according to ACI 305, any combination of high temperatures, high air pressure, low humidity and sunlight (sunlight) is a preconceived notion for designing a connection such as hot weather. Some theories say that any heat above a comfortable room temperature, and 25 ° C however, begins to make the concrete uncomfortable 1.e, the concrete begins to react differently which is why it requires special care due to hot weather, if strong quality to be maintained.
Hydration Process
- Therefore, it is very important to deal with how the temperature of the tropical climate differs concreting normal temperature. Concrete sets also gain strength due to the hydration of the cement inside them. The elasticity of the cement occurs quickly when it is hot. Cement installation also releases heat. Therefore, the faster the hydration of the cement the faster the heat generation. This creates the heat of the concrete, further speeds up the cementing or set-up process, Cement quickening does not allow concrete enough time to get enough strength. While the initial energy does not suffer, long-term energy (28-day energy) is negatively affected. This is a major reason why hot climates require special care. Otherwise, you will be playing with concrete designed strength.
- Water demand
- The water demand for concrete mix is high in hot weather due to rapid evaporation. Unless appropriate measures are taken, additional water will have to be added to the concrete mix to maintain the performance of the mixture. This will increase the amount of water cement which will also reduce the strength of the concrete. If more cement is added to keep the w / c ratio constant the cost will increase as cement is the most expensive ingredient concrete mix,
- Rapid drying of freshly poured concrete areas occurs when it is hot due to rapid evaporation or water loss in the mixture. If proper care is not taken, cracks known as plastic shrinkage cracks will appear, which are difficult to repair over time. The exposed area tends to shrink rapidly due to rapid moisture loss while mixing will still develop sufficient strength to withstand these shrinking pressures leading to cracking. In hot weather, concrete bed, forms, metal reinforcement, connecting or assembling equipment etc. It is also hot transferring heat to a mixture that adds to the problem.
The effects of Hot weather on concrete
- High temperatures can affect the concrete at all stages of production and laying process and many effects can have long-term or hardening effects. Some of the problems caused by high temperatures are listed in Table 1. They are the result of high temperatures that increase the rate of hydration reaction and the movement of moisture inside and outside the concrete.
- The combination of high temperature, low humidity and high air velocity adversely affects desirable concrete structures e.g. Strength, inequality, durability, weather resistance, wear and tear
- Setting time. As the temperature of the concrete increases, the laying time, and thus the laying time, the mixing and finishing of the concrete is reduced
- Workability and slump - High temperatures reduce the performance (or fall) of concrete very quickly over time. Adding more water to improve the performance of the mixture reduces energy and Increases penetration, and ultimately affects the durability of the mixture.
- Durability - Many forms of degradation depend on the transfer of fluid or respiration through a concrete structure. Acquiring a ‘non-permissible’ concrete is one of the main goals when trying to gain durability. The main ways to do this is to produce concrete with low water / cement concrete. As noted above, high temperatures affect the initial performance and the level at which they lose performance and may be tempted to add more water to the mixture or site. This will lead directly to concrete at high risk of cold, climate change, sulphate attacks and the entry of carbon dioxide and chloride solution leading to increased corrosion.
- Compressive strength - High water demand and high concrete temperatures can lead to a 28 day power reduction. If too much water is added to the concrete mix at high temperatures to maintain or restore function, the water level of the cement will increase, resulting in a loss of strength and durability. This can also increase the shrinkage of reinforced concrete. Where water is not heard, reduced set time and performance can increase insufficient mixing (actually a major impact on energy), the formation of cold joints and improper elimination.
- Concrete temperature - Warmer climates can increase the temperature of concrete caused by hydration heat. In large segments the hot gradients through the element can create thermal cracks. Laboratory tests show that very high temperatures have a significant impact on the strength of the hard concrete. Although increased concrete heat can lead to an initial increase in energy gain, in the long run, low-temperature-cooled concrete will reach higher strength.
- Poor surface appearance - With increased evaporation, the concrete surface will dry out. In the case of an infestation this can lead to premature depletion, trapping the amount of water that drips inside the mixture. The coated layer (from the finish) can cause blood clots to trickle under the surface, leading to the formation of the upper layer and subsequent eruption. Also, color variations on the face can result from different levels of hydration and cooling effects.
- Plastic shrinkage cracking - Hot weather conditions accelerate the loss of moisture on the face. If the evaporation rate is higher than the rate of bleeding (the rate at which the water rises higher) drying of the soil will occur which has led to a reduction in concrete. When the reducing pressure exceeds the capacity of the concrete, cracks will occur. The chances of cracking the plastic are reduced so it is great whenever hot weather raises steam or concrete and lowers the bleeding rate. The cracking of the shrinkage plastic can be quite deep, as the plastic concrete has little resistance to the shrinking pressure, and the cracks continue to grow and spread until the shrinkage pressures are released. (Be aware that thin plastic cracks do not usually extend to the free edges, as uncontrollable concrete cuts may occur in these areas.)
- Thermal cracking - Concrete is at risk of thermal cracking when applied for the first time, and hydration heat raises the internal temperature of the concrete. Rapid changes in the external temperature of the exterior concrete, such as where concrete slabs are laid, walls or sidewalks on a hot day followed by a cold night, lead to hot gradients between the warm / hot surface and the cold outside. The warm interior offers a cool outdoor space, which wants to make a deal. Depending on the temperature variation, there may be a concrete crash. Larger or thicker concrete objects are at greater risk because of the protective effect the concrete gives them inside the object.
Precautions in hot weather conditions
- Problems often arise when local workers are unaware of the impact of changing weather and / or climatic conditions during laying and / or finishing concrete. Improved responses to unexpected changes are not recommended because the damage that can be caused by the uncontrolled effects of tropical climates may not be completely eliminated. The first option to consider in hot weather is to postpone the placement of the concrete or not
- Make sure site staff are aware of the effects of the weather. Improved responses to unexpected changes are not recommended. The first option to consider in hot, unfavorable weather conditions is to postpone the placement of the concrete or not. It is often better to wait than to risk costly repairs (or replacements) for defective work.
- Concrete Production. The role of concrete suppliers is to help put concrete in hot climates. Shade stocks, spray aggregates before evaporation time, or cool down otherwise. Paint mixing barrels and keep them white to reduce heat loss from the sun. Use ice as part of the mixed water or cool the concrete with liquid nitrogen.
- Delivery and Delivery- Delivery delays can delay good mixing practices. The concrete supplier must plan and maintain a good non-delaying plan to deliver concrete to the required area on site
- Reduce travel time and avoid unnecessary delays.
- Avoid prolonged mixing. Mixed transport trucks should be released as soon as possible after the addition of water to that mixture.
- For large projects, consider baking and mixing using a workplace plant. •
- Water should not be installed on pre-assembled concrete in the workplace unless it is part of the amount required at the beginning of the set water limit and specified descent.
Precautions for concreting in cold weather
- Temperature control of concrete ingredients - The most effective way to maintain the temperature of concrete at the top is to control the temperature of its ingredients. The contribution of each ingredient in concrete heating is a function of heat, specific heat and the amount used for this ingredient. The water mixed with the mix has a very noticeable effect on the temperature of the concrete. Therefore, in cold weather, all available means will be used to care for these items at the highest possible temperature.
0. Many ways to reduce the effects of low temperatures include raising the level at which the concrete gains strength under these conditions in the first critical phase after laying.
2. Cement Quantity - Increasing the amount of cement (meaning using high-strength concrete) can increase the energy gain. Note that there is little or no impact during setup.
3. Admixture - The rapid addition of compounds (non-chloride) to concrete reduces the setting time and speeds up the energy gain rate by increasing the level at which cement enters
4. Hot Water - Applying hot water to the mixture will increase the temperature of the concrete, which in turn accelerates the rate at which cement enters. The temperature of the water mix should not exceed 70 ° C and the mixing should ensure the consistency of the concrete delivered to the site
5. Air entrainment - you may be able to prevent the effects of sudden cold by applying a combination of ventilation to the concrete. These compounds create minute air vents where the pore water can move as it expands during cold weather
6. On site precautions - It is advisable to take steps to prevent concrete damage by unpredictable and unexpected snow whenever the air temperature drops below 5C.
7. Cold Protection (Including cold / frozen area, winds and cold) - in some cases, the provision of a heated enclosure (simple frames covered with tarpaulin and the use of hot air) to completely seal the concrete object may be required. Note that care must be taken to prevent concrete drying when using this method.
Key takeaways
1. Concrete and other structures are constructed in many countries around the world and in some places the climate is symbolized by the long spells of hot or cold weather. Concrete companies that are ready to integrate and build in these regions are able to produce high quality concrete despite these weather problems. In many regions with unfavorable weather conditions there are set conclusions and concrete production guidelines that provide details of the methods that can be used to combat adverse conditions.
Under water concreting
There are 4 techniques of underwater concreting:
- Tremie pipe Method
- Bucket Method
- Grouting Method
- Bags stacking Methods
1)Tremie pipe Method:
- The tremie stable state of affairs method makes use of a vertical or nearly vertical pipe, thru which concrete is about with the aid of using gravity feed below water degree.
- The decrease give up of the pipe is stored soaking wet in crisp cement with the aim that stable ascending from the bottom dislodges the water, on this manner limiting washing out of the bond substance of the brand new concrete to the exposed top floor.
- The top give up of the tremie pipe is stored over the water degree amid the pour and is given a cone formed field for cluster stacking, or cement is probably siphoned into the best factor of the tremie pipe.
- Concrete should be poured at a fee which abstains from putting with inside the tremie.
2) Bucket Method:
- In this method the stable is saved submerged with the aid of using a base commencing field.
- The cans for the maximum component are outfitted with base curler or drop base doorways as regarded in Fig. The door opens uninhibitedly outward whilst stumbled.
- The pail is crammed absolutely with cement and its first-class secured with a canvas material or gunny sack and taken progressively right all the way down to avoid backwash or unsettling have an impact on to concrete because the can is added down into the water.
- The can is added down with the aid of using a crane upto the bottom floor of the stable and in a while opened both with the aid of using an affordable recreation plan from the first-class or with the aid of using a jumper.
- It is fundamental that the stable be launched straightforwardly superficially on which it's far to be saved.
Advantages:
- This method is located to have the accompanying preferences:
- Relatively lean blends is probably applied given ok versatility is held.
- No shape paintings is essential on this method.
Disadvantages:
- This method is slight and laborious as the precise situating of the packs installation should be cultivated with the aid of using the jumpers.
- Voids in adjacent sacks are difficult to fill.
- There is small preserving apart from created with the aid of using the mechanical interlock among packs.
- The method further is exorbitant as greater paintings is related to filling and tying them.
3) Grouting Method:
- These pens are laid vertically over the whole area to be cemented with the give up aim that the separation among the focuses of the pens and moreover to the essences of the stable thought now no longer surpass one meter.
- The degree of the stone over all thought to nor be beneath 50 mm in extra of 2 hundred mm.
- This overall have to be wetted earlier than storing it outdoor the metallic confines over the whole location and tallness to be cemented.
- While saving the overall, care have to be taken that no pen is uprooted from its position.
- Subsequent to storing the overall, the concrete sand grout of 1:2 quantity and water/bond share as a minimum 0.6 and now no longer greater than 0.9 is installation in a mechanical blender.
- The finest length of sand is probably five mm and the concrete sand quantity can also additionally shift from 1:1.5 to 1:4contingent at the first-rate conditions and importance of the paintings.
- In the wake of grouting the whole territory for a stature of round 60 cm s, a comparable pastime is rehashed for the subsequent layer of 60 cm and the method is rehashed until the grouting is completed up to an appropriate tallness.
- The grout to be dispatched down to be ok to fill each one of the voids.
- The extent of voids is probably typical as 55% of the extent to be cemented or observed tentatively.
- Beyond what many could recall feasible cement thought now no longer be troubled whilst it's far stored, this can restrict the association of laitence.
4) Bags stacking Methods:
- The packs are tied in order that they may be perfect right away in a profile of the floor on which they're put.
- The legitimately crammed sacks are added down into the water and set carefully in header and stretcher guides as in block workmanship improvement with the help of jumpers so the whole mass is interlocked.
Advantages:
- This method is located to have the accompanying factors of interest:
Nearly lean blends is probably applied given ok versatility is held.
- No shape paintings is vital on this method.
Disadvantages:
- This method is slight and laborious as the proper situating of the packs installation should be cultivated with the aid of using the jumpers.
Voids in contiguous packs are difficult to fill.
- There is small preserving apart from created with the aid of using the mechanical interlock among packs.
Key takeaways
1. The top give up of the tremie pipe is stored over the water degree amid the pour and is given a cone formed field for cluster stacking, or cement is probably siphoned into the best factor of the tremie pipe.
Concrete gains very little strength at low temperatures. Accordingly, freshly placed concrete must be protected against freezing until the degree of saturation of the concrete has been sufficiently reduced by cement hydration. The time at which this reduction is accomplished corresponds roughly to the time required for the concrete to attain a compressive strength of 500 psi. Concrete to be exposed to deicers should attain a strength of 4,000 psi prior to repeated cycles of freezing and thawing.
Sulphate
- Cement is composed of two minerals: tri-calcium silicate (C3S), and di-calcium silicate (C2S).
- In addition to hydration, the main reaction products are calcium silicate gel (C-SH) and calcium hydroxide Ca (OH) 2, labeled as CH in chemistry notation.
- Moisture is required in this reaction which can cause serious damage to the construction of both the walls and the walls of buildings in buildings.
- Sulphate attacks occur on the lower slabs. This problem usually affects buildings from the 1950s to the 1960s but can also affect previous buildings where the concrete floor slab is installed.
- It occurs when the filler material under the slide contains sulphates and this is considered to be a solution with soil moisture entering the concrete that forms the slab on the floor.
- Attacks can occur from MgSO4 salts, NaSO4 salts, and other salts containing SO3-ions. The interaction of Ca2 + ions with SO4 present in the solution will produce CaSO4 or gypsum.
- The effect of gypsum on C-S-H gel, which is the main component of reinforced cement, is an irreversible topic.
- Some substances present in cement, such as tri-calcium aluminate, also interact with sulphate ions. This reaction is well established in the literature.
Key takeaways
In addition to hydration, the main reaction products are calcium silicate gel (C-SH) and calcium hydroxide Ca (OH) 2, labelled as CH in chemistry notation.
Moisture is required in this reaction which can cause serious damage to the construction of both the walls and the walls of buildings in buildings.
Acid Attack
- Acid attack is the dissolution and leaching of acid-prone elements, particularly calcium hydroxide, from the cement paste of hardened concrete.
- This movement outcomes in an boom in capillary porosity, lack of cohesiveness and subsequently lack of power.
- In said instances, acid assault can be observed with the aid of using crack formation and subsequently disintegration, in particular whilst the shape is subjected at one facet to water pressure.
- Unlike sulphate assault (see beneath), the goods fashioned from acid assault aren't expansive, and leaching will handily arise in systems which are tremendously permeable.
- In excessive overall performance concrete structures containing cement pastes with a low content material of calcium hydroxide, acid assault is relative gradual and can contain handiest the finely divided calcium hydroxide crystals included withinside the interstices of the calcium silicate hydrate, C-S-H.
- The micrographs received from PFM analysis, supplemented with SEM–EDS studies, monitor that handiest the top, floor part of the concrete has been attacked with the aid of using acidic answer.
- The relaxation of the concrete suggests no shape of degradation.
- In the attacked zone, there's clean proof of leaching of the cement paste matrix, main to accelerated capillary porosity and lack of brotherly love of the matrix.
- Locally, there's lack of bonding of the cement paste to aggregate, however at the whole, those elements have now no longer adversely affected the microstructure and nice of the concrete.
- In this instance, long-time period sturdiness of the concrete isn't always probably to be compromised.
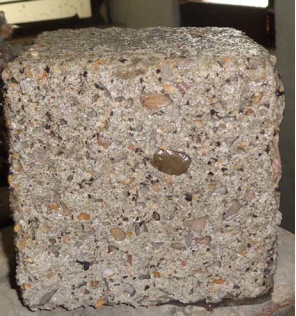
Fig no 19. Acid Attack on Concrete block
- Acid assault of concrete takes 3 forms. First, hydration merchandise reacts with the acid to shape dissolved ions, main to lack of strong material—acidolysis.
- Second, withinside the case of a few acids, insoluble salts shape, a number of which precipitates to purpose growth and cracking.
- Finally, a few acids supply complexes with calcium, aluminium, iron and silicate ions which produce an awful lot better concentrations of those ions in answer than could in any other case be the case, once more main to dissolution.
- This can probably arise at pH situations beneath which cement could usually be tremendously stable (complexolysis).
- Depending at the acid present, extra than this sort of deterioration mechanisms can be powerful.
- Where acidolysis is the main mechanism, an acid answer penetrating the pores of concrete will begin to purpose a number of the elements to dissolve.
- Calcium is generally the primary cation to be dissolved, considering that portlandite will become soluble beneath tremendously excessive pH values.
- AFm and AFt stages commonly dissolve at barely decrease pH values, even though strong aluminium and iron hydroxides are precipitated, which persist till the answer is tremendously acidic.
- Exposure to acidic answer additionally reasons lack of calcium—decalcification—of C-S-H gel, leaving tremendously vulnerable silica gel behind.
- The importance of calcium on this shape of degradation approach that adjusting the composition of the cement matrix of concrete to attain a decrease calcium content material will probably impart extra resistance.
- Thus, pozzolanic substances can be powerful in improving resistance to this form of acid assault, considering that their aggregate with PC will produce such an adjustment.
- However, decreased quotes of mass shipping and more desirable power done thru the usage of pozzolanic substances also are probably to be motives for progressed resistance.
Key takeaways
In excessive overall performance concrete structures containing cement pastes with a low content material of calcium hydroxide, acid assault is relative gradual and can contain handiest the finely divided calcium hydroxide crystals included withinside the interstices of the calcium silicate hydrates, C-S-H.
- You may also note efflorescence each interior and outside, and it may range in frequency and depth in the course of the us of a because of moisture and temperature. Three situations want to exist for efflorescence to arise: There are water-soluble salts in or at the fabric.
- Moisture is gift to make the salt turn out to be a soluble solution. As salts pass to the fabric’s surface, the moisture evaporates. This makes the salts crystallize, which leads to efflorescence.
- Water, rain and snow are the number one reassets of moisture and might effect the diploma of efflorescence.
- Condensation, groundwater wicking and indoors sports additionally may also have an effect on the diploma of moisture generation. Efflorescence can occur at exceptional times. Essentially, it may both be a hassle from the start of a constructing’s creation, or the method can arise over time.
- Primary efflorescence normally takes place inside the first seventy two hours of the constructing fabric being used, performing because of extra water being gift while the fabric became manufactured.
- Secondary efflorescence is a end result of out of doors moisture pulling the salt out of the constructing fabric. In many instances, efflorescence may also arise at some stage in domestic creation. If masonry devices get unnoticed in a single day at some stage in creation, they’ll probably soak up moisture from damp soil and rain. It is critical for masonry devices to be included and left in pallets to decrease the danger of efflorescence in the course of a creation project. Efflorescence also can arise while constructing substances are established incorrectly or troubles arise with the installation.
- Some not unusualplace examples of this include: Using through-wall flashings incorrectly. Failing to offer enough air flow for masonry. Installing masonry with out an green barrier for moisture.
- Joint substances failing after installation. Materials being saved improperly or left at the ground. Efflorescence is mostly a seasonal hassle, and humidity will effect whether or not soluble salts appear. It normally escalates in winter, due to the fact that rain, snow, sleet and different inclement climate situations may also arise. However, efflorescence can nevertheless arise in spring, fall and summer.
Fire resistance of concrete is the ability of concrete to withstand fire or to give protection against fire. This involves the ability of concrete structural element to continue perform a specific structural function or confine fire or both.
The duration of time that an element such as beam, column, wall, floor, or roof can endure the fire, which is defined in ASTM E 119, is termed fire rating.
Fire resistance is controlled by both the physical and thermal properties of the structural element. Factors governing the structural performance include stress level in the concrete and the steel, concrete cover, tendency of aggregate and free moisture to cause spalling, and lateral restraint conditions.
However, parameters that control the thermal performance involves type of aggregate, free moisture in the concrete (both absorbed and capillary), and volume of concrete per square meter of exposed area.
Inspection and testing of ready mix concrete is crucial to ensure that all specified conditions meet the acceptable criteria. Ready mix concrete, which produced in batching plant and transported to construction site by truck mounted mixers, are commonly inspected and tested in accordance with applicable standards such as ASTM international.
Batching Plant Inspection
- Firstly, examine and specify whether facilities, scales, and truck mixers meet the specified project requirements or not.
- Inspect storage areas of all materials like cement, aggregate, and admixtures to ensure their cleanness, free of contamination, and properly protect materials from effect of freezing.
- Inspect and verify that coarse and fine aggregate gradation tests are conducted in accordance applicable standards like ASTM C 136, and result reach project requirements.
Onsite Inspection of Ready Mix Concrete
- Every delivery ticket shall be inspected to ensure that a mixture with the correct designation is delivered.
- Inspect delivered concrete; it should be uniform and adequately mixed prior to discharge at the construction site.
- Inspect and monitor water, admixture, and fiber reinforcement addition onsite to make sure that the process performed properly.
- Monitor and examine concrete delivery and placement time to find out whether it completed within the time constraints of the project specifications.
Testing Ready Mix Concrete
1. Onsite Tests
There are certain types of tests that shall be conducted on ready mix concrete upon reaching construction sites. Table 1 provide lists of tests that need to be performed on ready mix concrete on project site. Table 1 Tests conducted on ready mix concrete upon reaching construction site
Type of tests | ASTM international for testing procedures | Test frequencies | Purpose of the test |
Slump | ASTM C 143/C 143M | First truck load, whenever the consistency of the concrete appears to vary. | Measure fresh concrete consistency, check its workability, and use as an indicator of poor mixed batch |
Air content | ASTM C 173, ASTM C 231 | Performed on all samples taken to measure concrete strength | To check air entrained concrete |
Temperature | ASTM C 1064 | At the time of sampling for each strength test | To make sure that concrete comply with certain specifications that define a certain allowable temperature range |
Density | ASTM C 138, ASTM C 567 | Whenever required by project specifications | To estimate concrete density |
Evaluation of crack
When inspecting a slab or conducting a crack, always measure the width of the crack and determine whether the metal reinforcement passes through it and whether the crack is active or asleep. This information, especially the details of the reinforcement and cracking function, is very important when choosing the best repair option.
Crack width
- The extent of the crack is usually measured using a crack comparison card. Measuring the width of the crack helps to separate the stiffness of the cracks and to evaluate the performance of the joint joints across the fracture of the direct direction of the fracture and the transmission of the load. Also, many repair options depend on the width of the crack.
- Unless the steel reinforcement passes through a crack, the alignment of the vertical tube and the transmission of the broken load depends on the joint bonding. If the diameter of the fracture is less than 0.035 inches, the composite particles that come from the other side of the fracture to the other side will normally provide adequate load transfer and maintain vertical alignment throughout the split.
- For larger screens, maintaining a straight slide alignment can be a challenge. The success of the remediation approach will depend on the slide loading and the quality of the base material and the ground cover.
Steel Reinforcement
- Although steel reinforcement does not prevent cracking, it limits the width of the crack so that the joint joints are maintained. Strengthening itself also provides load transfer and helps maintain vertical alignment in the cracks. When the reinforcement passes through a split, both the width split and the future width increase are controlled. The new cracks of the non-reinforced concrete will continue to grow and the diameter can double before the increase in crack-width.
- With the cracks caused by the drying shrink, the cracks will stabilize at the end. Splits due to other causes, however, such as soil erosion or height, may not be stable and may continue to increase unless a significant amount of reinforcement passes through space. Determining the amount of reinforcement that goes beyond cracking is important in predicting the performance of future cracks and choosing the best repair option.
Dormant and active crack
- Cracks that fall through steel reinforcement are generally stable and are often considered sleepy. Of course, the stability of the cracks depends on the source and the degree of reinforcement of the cracks. The lying cracks have a fixed width and can be repaired with solid or flexible materials.
- Functional cracks should only be repaired using a flexible object that can accommodate future cracked movements. Generally, the active cracks in the slabs actually belong to the active members and should be treated in the same way as the joints. After all, random or non-joining cracks in flatwork are self-assembling joints.
Key takeaways
- Evaluation of crack is
- Crack width
- Steel Reinforcement
- Dormant and active crack
1. Plastic shrinkage concrete cracks:
- When concrete remains in its plastic state (earlier than hardening), it's miles complete of water. When that water finally leaves the slab, it leaves at the back of big voids among the stable particles.
- These empty areas make the concrete weaker and greater at risk of cracking. This form of cracking takes place regularly and is stated as “plastic shrinkage cracking”.
- While plastic shrinkage cracks can manifest everywhere in a slab or wall, they nearly constantly manifest at reentrant corners (corners that factor into the slab) or with round gadgets withinside the center of a slab (pipes, plumbing fixtures, drains, and manholes).
- Since concrete cannot decrease round a corner, strain will purpose the concrete to crack from the factor of that corner. Plastic shrinkage cracks are usually very slender in width and slightly visible. While almost invisible, it's miles vital to bear in mind that plastic shrinkage cracks don’t simply exist at the surface, they increase at some point of the whole thickness of the slab.
- An excessively moist blend is a contributing element to shrinkage in concrete. While water is a critical element in each concrete blend, there's this kind of factor as an excessive amount of water.
- When the combination consists of an excessive amount of water, the slab will reduce greater than if the suitable quantity of water turned into used. Hot climate is some other massive cause for plastic shrinkage cracks. Control joints may be included into the slab to save you shrinkage cracking. The joints will open up because the concrete slab receives smaller.
2. Expansion concrete cracks:
- Enlargement cracks Just like a balloon, warmth reasons concrete to expand. When concrete expands, it pushes towards whatever in its way (a brick wall or adjoining slab for example).
- When neither has the capacity to flex, the increasing pressure may be sufficient to motive concrete to crack. Expansion joints are used as a factor of separation (or isolation), among different static surfaces.
- Typically product of a compressible fabric like asphalt, rubber, or lumber, enlargement joints should act as surprise absorbers to alleviate the strain that enlargement places on concrete and save you cracking.
3. Heaving concrete cracks heaving cracks:
- When the floor freezes, it is able to on occasion raise many inches earlier than thawing and settling lower back down.
- This floor motion delivered on through the freezing and thawing cycle is a big element contributing to concrete cracking. If the slab isn't unfastened to transport with the floor, the slab will crack.
- Large tree roots will have the identical impact on a slab. If a tree is positioned too near a slab, the developing roots can raise and crack the concrete surface. Always don't forget this while laying a slab.
- Settling concrete cracks settling cracks On the alternative hand, floor settling beneath a concrete slab also can reason cracking. Settling cracks usually arise in conditions wherein a void is created withinside the floor beneath the concrete surface.
- Think approximately whilst a huge tree is eliminated from close by and the roots start to decompose or whilst a software business enterprise digs a trench for his or her lines, pipes, etc. and don’t compact the soil once they replenish it–those are examples of times wherein settling cracks are possibly to happen.
The principal causes of cracks in a building are as follows:
- Permeability of concrete
- Thermal movement
- Creep movement
- Corrosion of reinforcement
- Moisture movement
- Poor construction practices
- Improper structural design and specifications
- Poor maintenance
- Movement due to chemical reactions
- Other factors
Remedial measures
- Use minimum possible quantity of water.
- Employ large coarse aggregate.
- Provide compression reinforcement if possible
- Avoid formwork removal at early ages.
- Cure concrete properly.
- Assign proper cross section for the concrete element.
- NDT stands for Non-Destructive Testing. It refers to an array of inspection strategies that permit inspectors to assess and acquire statistics approximately a material, system, or factor without completely changing it. NDT can also be called: NDE (non-unfavourable exam or evaluation) NDI (non-unfavourable inspection) In the subject, NDT is frequently used as an umbrella time period to consult non-unfavourable inspection strategies, inspection tools, or maybe the complete subject of non-unfavourable inspections.
- For business applications, the aim of NDT is to make certain that vital infrastructure is well maintained if you want to keep away from catastrophic accidents. While NDT techniques are generally related to business use cases, like examining vulnerable factors in a boiler used at an oil refinery, makes use of in medicinal drug are really a number of the maximum common. For example, an waiting for mom getting an ultrasound to test at the fitness of her infant could be taken into consideration an NDT use case, as could getting an X-ray or MRI to analyze extra approximately an injury.
- But it’s critical to notice that NDT does now no longer always require the usage of unique equipment, or any equipment at all. For instance, while inspectors in business settings overview the outdoor of a stress vessel with their bare eye, that could fall beneath the NDT designation, when you consider that they're accumulating facts at the popularity of the boiler without negative it.
- On the alternative hand, the use of an advanced device like an ultrasonic sensor to search for defects in a positive cloth or asset could additionally be known as NDT. Regardless of the particular use case, the underlying commonality amongst a lot of these examples is the gathering of facts in a non-intrusive manner.
- The special styles of non-damaging trying out are regularly complementary. As a result, we will take advantage of the benefits of mixed strategies. Non-damaging trying out (NDT) is a mixture of diverse inspection strategies used for my part or together to assess the integrity and residences of a material, thing or device without inflicting harm to it.
- In different words, the component that calls for the usage of one or greater of these strategies can nevertheless be used as soon as the inspection technique is over. NDT is consequently regularly used for the detection, characterization and sizing of inherent discontinuities, in addition to the ones related to harm mechanisms. NDT is regulated with the aid of using codes and requirements in keeping with the kind of industry, united states of America and different criteria. Society for Mechanical Engineers (ASME), ASTM International, COFREND, CSA, Canadian General Standards Board (CGSB), American Society for Non-destructive Testing (ASNT), etc. are well-recognize examples.
- Destructive trying out (regularly abbreviated as DT) is a take a look at technique performed to discover the precise factor of failure of substances, components, or machines.
- During the process, the examined object undergoes strain that in the end deforms or destroys the material. Naturally, examined components and substances can't be reused in normal operation after present process unfavourable trying out procedures. Destructive trying out is typically performed earlier than a aspect enters mass production. OEMs want to realize the boundaries in their merchandise for you to supply right upkeep and working guidelines for his or her machines.
Tests on cement
1. FINENESS
Objective
- The purity of the cement alone has a significant impact on the hydration rate and therefore on the energy gain rate and the degree of heat dissipation.
- Finer cement provides a large area of hydration Specific Surface versus Compressive Strength of Cement and as a result accelerates energy.
- The beauty of digestion has increased over the years. But now it is almost settled. Different cement is subject to different finishes.
- A particle size of less than 3 microns has been found to have a significant effect on energy in one day while a fraction of 3-25 micron has a significant effect on energy for 28 days.
- An increase in the thin layer is also found to increase the thickness of the concrete.
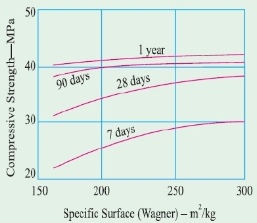
Fig no 20. Specific Surface versus Compressive Strength of Cement
Procedure
- Stir the sample of cement to be tested by stirring for 2 minutes in a preheated pot to distribute the agglomerates. Wait 2 min. Mix the resulting flour gently using a clean dry stick to spread the fine mixture all over the cement.
- Place the tray under a strainer, weigh about 10 g of cement in the nearest 0.01 g and place it in a strainer, being careful to avoid loss. Disperse any agglomerates. Place the lid on top of the filter.
- Cover the sieve with a circular motion, planetary motion and movement until it no longer exceeds the fine material in it. Remove and measure the rest. Specify its magnitude as a percentage, R1, of the pre-set filter per 0.1 percent nearby. Gently move all the fine material from the filter into the tray.
- Repeat the whole process using a new sample of 10 g to get R2. Then calculate the remnants of cement R as the value of R1, and R2, as a percentage, expressed in the percentage close to 0.1.
- When the results vary by more than 1 percent altogether, make a third reduction and calculate the meaning of the three values.
- Check the sieve after 100 filters per section 4.4.2 of IS: 4031 (Part 1)
Apparatus used
![]() | ![]() |
Fig no 21. Cement | Fig no 22. Balance |
![]() | ![]() |
Fig no 23. Seive | Fig no 24. Nylon Bristol Brush |
2. STANDARD CONSISTENCY
To determine the quantity of water required to produce a cement paste of standard consistency as per IS: 4031 (Part 4) – 1988
Apparatus
1) Vicat apparatus conforming to IS: 5513 – 1976
2) Balance, whose permissible variation at a load of 1000g should be +1.0g
3) Gauging trowel conforming to IS: 10086 – 1982
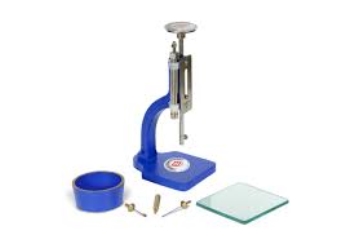
Fig no 25. Vicat apparatus
Procedure
- Measure about 400g cement and mix it with the required amount of water. Estimation time should be between 3 to 5 minutes.
- Fill the Vicat mold with glue and measure it with a trowel.
- Gently lower the plunger until it touches the cement.
- Release the plunger to allow it to sink into the paste.
- Note the reading in the scale.
- Repeat the above process and take new samples of cement with different water sizes until the gauge is 5 to 7mm.
3. SETTING TIME
Objective
- For simplicity, the initial set time is considered to have elapsed between the time when water can be added to the cement, at which point the paste begins to lose plastic.
- The last time is the last time the water is put in the cement, and the time when the glue is completely lost to the plastic and gained enough strength to withstand a certain direct pressure.
- The room temperature, dry material and water should be kept at 27 ± 2 ° C. The relative humidity associated with the laboratory will be 65 ± 5 percent.
Procedure
Preparation of test block
- Prepare a clean paste by measuring 0.85 times the water needed to give the glue a normal consistency. Portable or refined water will be used to prepare the paste. Attachments will be measured in accordance with the conditions set out in IS: 4031 (Part 4) -888.
- Start a stopwatch at a time when water can be added to the cement. Fill the Vicat mould with cement paint as limited as above, the mould stays on an empty plate. Fill the mould completely and spread the surface of the paste to make it to the top of the mould. The cement block is thus suspended from the test mould.
- Immediately after moulding, place a barrier in a damp cupboard or damp room and allow it to remain there unless a set time is set.
Determination of initial setting time
- Place the test block enclosed in the mould and rest on a waterless plate, under a needle-carrying rod (C); gently lower the needle until it meets the surface of the test block and release it immediately, allowing it to enter the test area. Initially, the needle will completely pierce the test block.
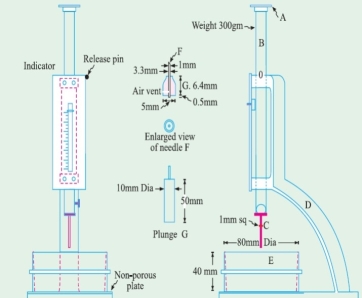
Fig no 26. Needles used in Vicat's Apparatus
- Repeat this process until the needle, when attached to the test block and removed as described above, fails to pierce the block more than 5.0 ± 0.5 mm measured from the bottom of the mould. The time elapsed between the time the water is added to the cement and the time when the needle fails to pierce the block reaches a point of 5.0 ± 0.5 mm measured from the bottom of the mould will be the first set time.
Determination of final setting time
- Insert needle (C) of Vicat resources into the needle with a secret attachment (F).
- The cement will be considered to be set at the end where, when the needle is gently inserted into the surface of the test block, the needle makes a picture of it, while the attachment fails to do so.
- The time elapsed between the time the water is added to the cement and the time when the needle makes its appearance on the surface of the block while the attachment fails to do so will be the last set time.
- In the case of a scarf that forms over the test block, use the bottom of the block to cut.
4. SOUNDNESS AND COMPRESSIVE STRENGTH
- Sensitivity refers to the ability of a glue that has been hardened to retain its volume after setting without the delay of harmful expansion.
- Thus, hearing is a very important test. The audio attachment will not make a pleasant volume change after it has hardened and as a result will not be in danger of forming cracks. Sound adhesive is the basis of sound mud or concrete mixing.
- Aircraft ash is the result of coal-fired power generation. During a fire, mineral pollutants in hot coals are released from the combustion chamber in the form of particles composed by flue gases.
- As these particles coo, they harden into round glass particles. The fly fly shows concrete structures and is used in concrete as replacement or replacement of concrete. Insufficiency can occur in the presence of very free magnesia or free lime burned in cement.
- The taste of cement can be determined in a variety of ways. In the Le Chatelier bath, a sample of cement / ash adhesive frosting is placed on the mould and boiled for a specified period of time (approximately 3hr) so that any tendency to stretch can be quickly and detected.
- After the boiling process is complete, the distance between the points of the two control indicators is measured by the nearest 0.5mm and compared to the first measured length before testing.
- This test requires Le Chatelier water bath, Le Chatelier mould, calliper, measuring cylinder, balance and length comparison. Active standards include EN 196-3, EN 459-2 and EN-450.
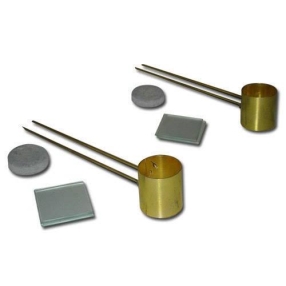
Fig no 27. Le chatelier apparatus
- Alternatively, the stability of the concrete can be determined by autoclave. These tests include an autoclave expansion of Portland cement using a test in a good cement sculpture.
- Specimens are made of oil-coated mould with reference points attached to a reference length of 250mm. Specimens extracted from the mould and measured after 24hr are placed in an autoclave at room temperature.
- After the autoclave is turned off, the specimens are exposed to a full-pressure current at a specified time. After the heating is complete, the template is rated and compared with the original length measurements.
- Equipment needed for this method includes autoclave, test bar mould, mixer equipment, balance and length gauge. Functional standards include ASTM C151 and AASHTO T107.
- The expansion of the cement can also be determined by comparing the length. The length gauge is a device used to measure changes in the length of attachment of cement, mortar and concrete according to ASTM and AASHTO data.
- The unit consists of a complex dial or digital display embedded in a solid, dual post frame structure. Moving and vertical anvils are designed to detect reference pins thrown at the edges of sample test bars.
- ELE offers a variety of devices for this method, including drying materials, shrinkage and humidity movements, as well as a ASTM-length ratio. Active standards include ASTM C151, C157, C227, C490, C531, AASHTO T-107 and T-160.
Key takeaways
- For simplicity, the initial set time is considered to have elapsed between the time when water can be added to the cement, at which point the paste begins to lose plastic.
- The last time is the last time the water is put in the cement, and the time when the glue is completely lost to the plastic and gained enough strength to withstand a certain direct pressure.
- Sensitivity refers to the ability of a glue that has been hardened to retain its volume after setting without the delay of harmful expansion.
- Thus, hearing is a very important test. The audio attachment will not make a pleasant volume change after it has hardened and as a result will not be in danger of forming cracks. Sound adhesive is the basis of sound mud or concrete mixing.
Tests on aggregate
Specific gravity
Gravity and the combined force of water are essential elements in the formation of concrete and bitumen mixtures. The thickness of a solid mass is a measure of its size to an equal volume of distilled water at a specified temperature. Because the compound can contain a void that is allowed to enter the water, two combined gravity measures are used:
- Apparent specific gravity and
- Bulk specific gravity
Apparent specific gravity, G app, is calculated on the basis of the volume of the number of compounds i.e. the volume without voids entering the water. Therefore
G app = [(MD / VN)] / W
Where,
- MD is a dry aggregate weight,
- VN integrated network volume without volume object focus,
- W the size of the water.
Bulk Specific Gravity, G bulk, is calculated on the basis of the total number of aggregates including the inlet. Therefore
G bulk = [(MD / VB)] / W
Where,
- VB total volume of aggregates including volume of water absorbed.
Grading of aggregate
- Collection placement determines the average grain size of the composite before it is used in construction.
- This is the use of a complex and clear combination. The combined sample is filtered through a set of sieves and weights stored in each filter by percentage words summarized.
- By dividing this amount by 100, The Fineness Modulus of that total is determined. This assists in the decision-making process about the number of well-known modular composites that must be combined to obtain the concrete of the desired quantity.
- The basis of a green and clear composite mix for a particular soft module is the presence of spaces or open spaces where the composite is packed together.
- For bad clean aggregates packing can leave 30-40 percent, which can only be removed by filling the fine particles.
- Similarly, in fine aggregates too, there are voids left to be filled with better particles (cement).
- This is important to get a mix of composite and blank letters.
- When other pieces of equal size are put together, voids or open spaces are always left. Percentage of voids can be as high as 45 percent of the total volume of aggregates.
- It turned out that this effect (presence of voids) was independent of the size of the aggregates used in the packaging, whether worse, medium or good.
- Only, while composite packaging should be of the same size, that is the same distance.
- Either all should be rough, or they should all be medium or good. This means that even if the sand alone is full, voids at a rate of 40-45 percent are left as well.
- This principle of spacing is the governing principle for the preparation of concrete under this method.
- When coarse aggregates are full to make concrete, the voids built into the weight should be filled with some good material. Sand is used for this purpose.
- However, there will be voids between the grains of sand as well. These are filled with cement particles.
- In this way, the weight of the resulting concrete is either empty or dense. Cement binding material is used to give this dense cone a stone-like character.
- Concrete, artificial stone, in a broad sense.
- Collection classification is intended to determine the particle size of a given group of composites.
- This is usually found by the Method of Fineness Modulus. This method can be used to determine the best modulus for coarse combinations, fine aggregates, and all composites, i.e., composite composites.
- In this way, the ideal weight of the sample is taken and filtered through a series of sieves respectively. The number of sieve is five in coarse aggregates and ten in all aggregates.
Sieve Size of Collection.
Coarse Aggregates: 80 mm, 40 mm, 20 mm, 10 mm, IS No..480
Fine Aggregates: Numbers 480, 240, 120, 60, 30 and 15.
Total included: 80 mm, 40 mm, 20 mm, 10 mm, Nos: 480, 240, 120, 60, 30 and 15.
Flakiness Index
Object
For determination of flakiness index of coarse aggregate, where the size of the coarse aggregate are larger than 6.3mm .
Apparatus
- Thickness gauge
- Sieves [63, 50, 40, 31.5, 25, 20, 16, 12.5, 10 & 6.3mm]
- Balance [0-10 kg]
- Thickness Gauge
Procedure
- The sample was removed with the IS filter defined in the Table shown below.
- Thickness size and long length
- Thickness size and long length
- A minimum of 200 pieces for each fraction is taken and measured.
- In order to separate the faulty material, each component is individually measured by the thickness of the size gauge.
- The total amount of blurring objects that transmit the size gauge is measured with an accuracy of 0.1% of the sample weight.
Elongation Index
Objective
For determination of elongation index of coarse aggregate, where the size of the coarse aggregate is larger than 6.3 mm
Apparatus
- Length gauge
- Sieves (63mm,50mm,40mm,31.5mm,25mm,20mm,16mm,12.5mm,10mm)
- Balance (0-10kg)
- Oven (3000c)
Procedure
- The sample was removed with the IS filter defined in the Table shown below.
- A minimum of 200 pieces for each fraction is taken and measured.
- To separate the extended objects, each fraction is measured individually in length in the length gauge.
- Combined pieces from each tested segment that could not exceed the specified gauge length and its long cut sides are collected separately to obtain the total composite weight stored at the gauge length from each segment.
- The total amount of extended material retained by the length gauge is measured with an accuracy of 0.1% of the sample weight.
Impact Value
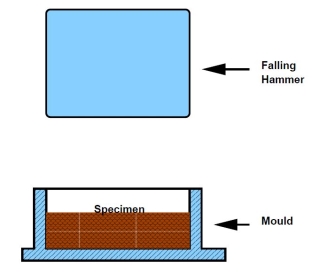
Fig no 28. Impact test apparatus
- Combined impact tests were performed to test for resistance to compound effects.
- The aggregates pass through a filter of 12.5 mm and are kept at 10 mm per filter are filled with a diameter of a diameter of 10.2 mm internal diameter and a depth of 5 cm attached to the metal base of the impact test machine.
- The content is completed in 3 layers where each layer is marked with 25 strokes.
- A steel hammer weighing 13.5 to 14 Kg is scheduled to be dropped with a free fall of 38.0 cm in v
- Ertical directions and a test sample is placed at 15 hits.
- The crushed joint is allowed to pass through a filter of 2.36 mm IS. And the impact value is measured as the percentage of aggregates that pass through the filter (W2) to the total sample weight (W1).
- Combined value = (W1 / W2) * 100
- Aggregates will be used to wear the course, the impact value should not exceed 30 percent. For bituminous macadams the maximum permissible value is 35 percent.
- In the basic studies of Water bound macadam the maximum allowable rate specified by the IRC is 40 percent.
Abrasion Value
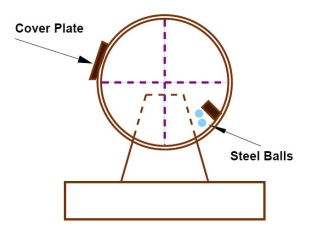
Fig no 29. Abrasion value setup
- Abrasion testing is performed to test the hardness of the material and to determine whether it is suitable for various stone construction activities.
- The abrasion test in Los Angeles is very popular to achieve hard materials and is standardized in India (IS: 2386 part-IV).
- The goal of the Los Angeles abrasion test is to find a percentage wear due to the rubbing action associated between the balls attached to the metal used as a serious offense.
- The Los Angeles machine consists of a 700 mm diameter inner diameter and 520 mm long attached to a horizontal axis that makes it possible to rotate (see Fig-2). A circular charge with round metal balls 48 mm wide and weighing 340-445 g is inserted into the cylinder and compound.
- The number of alrasive panorama varies depending on the sample size. The amount of compounds to be used depends on the catch and usually ranges from 5-10 kg.
- The cylinder is then locked and rotated at a speed of 30-33 rpm at a rate of 500 -1000 changes depending on the assembly rate.
- After the specified changes, the material is filtered through a filter of 1.7 mm and a fraction is transferred as a percentage of the sample weight. This figure is called the Los Angeles abrasion rate.
- A maximum of 40 per cent is allowed in the WBM study in the Indian state. In bituminous concrete, a maximum of 35 percent is specified.
Crushing Value
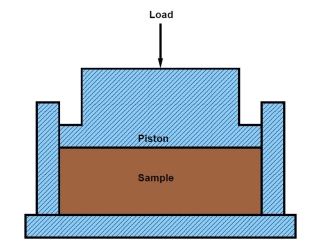
Fig no 30. Crushing test setup
- One of the models where the material is paved where it fails to press down under joint pressure.
- The test was rated with IS: 2386 part-IV and used to determine the combined crushing power.
- The combined value of the crush provides an approximate level of crushing resistance under the gradual crushing load.
- The test consists of placing a composite sample in a standard mold in a pressure test under normal load conditions.
- Dry aggregates pass through 12.5 mm sieve and 10 mm sieve are stored with a cylindrical dimension of 11.5 mm in diameter and 18 cm in height in three layers. Each layer is applied 25 times with a standard lubricant.
- The test sample is weighed and placed in a test cylinder in three layers each layer is also softened. The specimen is under a pressure load of 40 tons used slowly at an average of 4 tons per minute.
- The aggregates are then compressed and reduced by a filter of 2.36 mm and the weight of the passing object (W2) is expressed as a percentage of the total sample weight (W1) which is the total crushing value.
- Total crushing value = (W1 / W2) * 100
- A value less than 10 means a particularly strong combination while the above 35 can often be considered a weak combination.
Tests for fine aggregate:
Specific gravity
- The gravitational force of fine aggregate (sand) is defined as the mass of a given volume of aggregates in equal amounts of water. The gravitational force of fine aggregate (sand) is considered to be around 2.65 to 2.67.
- Quartz sand particles have a specific strength of between 2.65 to 2.67. While the odd clay starts from 2.70 to 2.80. Soils that contain a lot of organic matter or furry particles (such as diatomaceous earth) have a gravitational force of less than 2.60 (Some are as low as 2.00).
What is specific gravity of Aggregates?
The gravitational force of aggregate is considered to be the measure of the strength or quality of an object. The specified gravitational force is defined as the ratio of the weight of a given volume to a combination of the equivalent volume of water. Lower gravity scales are usually weaker than those with high gravity compounds. This property assists in the general identification of mergers.
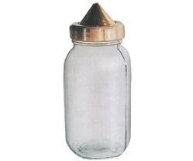
Fig no 31. Pycnometer bottle
Determination of Specific Gravity of Fine Aggregate as per IS: 2386 Part 3: (1963)
Hello friends, welcome to the world of Civil Allied Gyan. Read here the description, the list of apparatus, the IS code, the testing process, the formula and the web report about the determination of the gravitational force of a good collection.
Resources Required for Specific Integrated Voting Power Testing: -
- Pycnometer bottle of capacity 1000ml
- Touch stick
- Trench
- Balance scale
Is the Gravity Specific of Fine Aggregate test code: -
IS: 2386 (Part 3): 1963, Methods for testing concrete scales (Determining Specific Gravity of aggregates)
Procedure
- Take a clean and dry pycnometer and determine its empty weight (W₁ g).
- Take a pure sample of fine aggregate (about 1kg) to determine the gravitational force and transfer that to the pycnometer and weight (W₂ g). Aggregates better than 6.3mm taken.
- Pour the refined water into a pycnometer with a mixed sample at a temperature of 27 ºC, to water the sample only.
- Immediately after immersion, remove trapped air from the sample by moving or alternating the pycnometer, placing a finger in the hole at the top of the closed pycnometer.
- Clear the outer area of the pycnometer. Now the pycnometer is completely filled with water until the top hole, and after making sure that there is no more air trapped in the pycnometer, its weight (W₃ g).
- Transfer the value of the pycnometer to the care test being performed to ensure that all the components are transmitted. Clean the pycnometer.
- Re-fill the pycnometer with the added water to the top of the pycnometer, without any trapped air. It should be completely dry on the outside and take off weight (W₄ g).
- To fill the mineral, a special magnetic field bottle is used and the equipment is filled up to three times the volume of the bottle. The whole process of determining gravity is similar to that described above.
Seive Analysis
Objectives:
The whole process of sieve analysis determines the distribution of particle size of fine aggregates and determines whether it is suitable for use in concrete mixing.
Testing Resources
A series of IS filters
4.75 mm
2.36 mm
600 mic
300 mic
150 mic
75 mic
Procedure
- The sample was weighed exactly 1000g.
- First, we must clean all the sieve using a wire brush to make it clear that aggregates are trapped in some gaps.
- After that we have to prepare the sieve in the moving machine from top to bottom, in size from the largest (4.75mm) to the smallest (0.075mm).
- The sample was diluted using a collection of IS Sieves 10 minutes.
- After sieving is done, the merging with each filter is measured individually.
- The aggregate weight that passes through each filter is calculated as a percentage of the total sample weight.
- The same procedure is followed by two other samples.
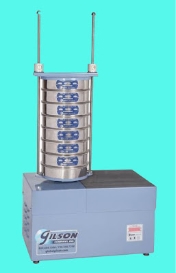
Fig no 32. Mechanical Sieve Shaker
Fineness Modules
The fineness modulus (FM) of aggregates may be a frightening term, but it is just a conceptual measure that describes the average size of particles in a composite sample. This feature provides the basis for selecting the approximate size of concrete joint design, but its actual impact is not always understood. The Fineness modulus is not a fixed value, as it provides a way to estimate the amount of integration needed to measure the mixing designs.
How to fineness modulus measure
Fineness modulus is determined using the percentage of size fractions from the sieve analysis and calculated for any selected series of sieve sizes. When designing concrete mixes, FM for good mixing is required to properly separate the mixes. Changes in the placement of the coarse aggregate section have little effect on the overall concrete structures. Combined partitions can be made using different cutting and fine-grained joints and blending techniques to control FM with concrete mix.
Origin of the Fineness Modulus Concept
Duff Abrams, an American inventor of the early 20th century, was an influential figure in the study of concrete structures and features. As well as explaining the importance of water / cement ratio and developing a fall test, he described the fineness modulus in 1918 as a way to separate concrete aggregates, simplify a gradation curve, and measure the appropriate size for use in mixing designs. Explaining the principle he said, "The integration of the same good modulus will require the same amount of water to produce the same coherence and provide the same strength concrete."
Includes Fineness Modulus
The simple FM calculation procedure requires a precise particle size analysis as described in ASTM C136, Standard Test Method for Sieve Analysis of Fine and Coarse Aggregates. In addition to the required particle size sizes, specific FM statistics must be included. Although manual upgrade of the sieve is permissible in standard, Gilson strongly recommends the use of the appropriate connector to ensure accuracy, durability and efficiency. After the filter has been analyzed and the fractions are measured in the correct proportions or proportions, the percentage of fractions is calculated.
Fineness Modulus of sand
To calculate the simple sand module, the total percentage accumulated stored in the following sieve is divided into 100: 150μm (No. 100), 300μm (No. 50), 600-μm (No. 30), 1.18mm (No. 16) , 2.36mm (No. 8), and 4.75mm (No. 4) of fine aggregates. If FM coarse aggregates are required, filters of 9.5mm (3⁄8in.), 19.0mm (3⁄4in), 37.5mm (11⁄2in) can be installed. There may be even larger sieves that can be added by continuing at a ratio of 2: 1 with the original sieve size. No additional equipment is required to make the determination. The same ASTM E11 test filters are used for integrated particle size analysis tests. In the example below, aggregate percentages from 4.75mm to 150µm are used to calculate the correct modulus for this fine mixing sample.
Alkali Aggregate Reaction
- Alkaline reaction - silica (ASR), more commonly known as "concrete cancer", is a painful inflammatory process that occurs over time in concrete between alkaline cement and active amorphous (eg, non-crystalline) silica found in many common compounds, sufficient moisture is provided.
- The pattern of cracks is associated with an alkaline-silica reaction that affects the concrete step barrier on the US highway. Note the common oily feature of the silicate debris imbibing the concrete surface on both sides of the crack.
- This undesirable chemical reaction results in the expansion of the altered composition by the formation of soluble and viscous gel of sodium silicate (Na2SiO3 • nH2O, and marked Na2H2SiO4 • nH2O, or N-S (sodium silicate hydrate), depending on the assembly received).
- This hygroscopic gel swells and increases in volume as it absorbs water: it has a high pressure inside the siliceous compound, which causes cracks and loss of concrete strength, eventually leading to its failure.
- The ASR can lead to severe cracking of the concrete, leading to serious structural problems that could force the demolition of a particular building.
- The extension of the concrete reaction between cement and composite size was first studied by Thomas E. Stanton in California in the 1930s with his publication in 1940.
Buckling of sand
- The increase in volume of a good compound due to the presence of moisture content is known as bulking. This is because the moisture causes a film of water around the sand particles leading to an increase in the volume of the sand, at a moisture content of about 5 to 8%, this increase in volume can be 20 to 40%, depending on the placement of the sand.
- The more effective it is, the more volume will be given to the moisture content provided. This practice is known as sand bulking.
- As the moisture content increases by adding more water, sand particles accumulate closer and the bulking value of the sand decreases. Therefore, dry sand and water-soaked sand are about the same size.
- Constipation of sand affects the balance of the sand to a large extent. Most with fine sand and less with coarse sand. If the right grant is not made for sand extraction, the cost of concrete, and vehicles will increase and it will result in less sandy loam and hard to operate and maintain.
Important facts regarding sand formation are as follows
- As the moisture content increases by adding more water, sand particles accumulate closer and the bulking value of the sand decreases.
- One of the reasons for adopting a weight measurement is the constipation of sand as weight loss avoids difficulty due to the abundance of sand.
- Sanding of the sand should be considered when the volumetric value of the value is accepted.
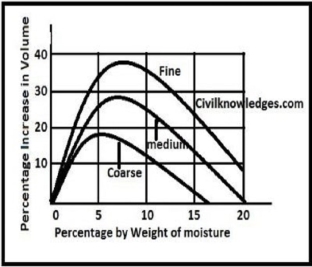
Fig no 33. Buckling of fine aggregate
Determining of buckling of fine aggregate
Opera and the process of determining the best percentage output
- Laboratory testing of bulk composites
- Field test for average quantity
Fine Aggregate Collection Laboratory Testing
Apparatus
- 250 ml measuring cylinder
- Weight balance
- Good combination
Procedure
- Take 500 grams of frozen fine aggregate at a temperature of 100 to 110 degrees Celsius for 24 hours. This is a weight measure as W1.
- Cool sand picks up airtight containers. So this weight ratio as W2.
- Sample water content is calculated as
- Wc = (W1-W2) X 100 / W1
- In a pan, 250 grams of sand take.
- In this case 2% by weight of water add. This is well integrated.
- The mixture is poured into a 250ml cylinder. This is compounded by shanking.
- The test was repeated with the remaining amount of 2% water sand at each time point. The reading takes as Y2, Y3… etc until the volume reading decreases.
- After their level, 4% of the water is added and the test continues until the sample is completely filled.
- For a standard sample in a measuring cylinder, add about 50 ml of water and stir the sample well.
ARTIFICIAL AND RECYCLED AGGREGATE
Artificial aggregates
- Many synthetic aggregates can be controlled, by industrial process products, such as various slags, or uncontrolled waste from other industrial processes, such as clinkers and ashes.
- Another important source of waste is the mining industry, including the extraction of coal and China clay.
- Some products that come out once or the waste can be made, or need to be recycled, to make things that are suitable for use as concrete mixers or that show special properties. In addition, other natural materials, such as perlite or vermiculite, can also be processed to produce compounds that reflect special properties.
- Demolition debris is reused to produce concrete scales. The RILEM (TC-121) technical committee recommended the separation of those compounds.
Recycled aggregate
- The construction industry produces a large amount of waste that needs to be recycled and used as recycled aggregates (RAs) for partial or complete environmental integration.
- Recycling reduces waste and reduces energy consumption and that is why it has an impact on the sustainable construction industry.
- In this chapter the need to redefine the current situation and situation around the world is highlighted. The structures of the RA are discussed. RAs weigh less than viral substances and higher water absorption.
- The state of the art of RA performance of concrete in a new and difficult world is summarized. The RA concrete exhibits low pressure and flexibility as well as low-strength mode and low cracking due to the porous nature of the RA and the old mud attached to the cement above the composite.
- The strength of the bond and the strength of the abrasion are less affected. Depletion, water infiltration and water infiltration by capillary increase with increased RA content.
- However, low performance can be reduced with a good mixing design using cement additives. Successful applications for RA in the manufacture of adhesive and truck concrete are also being discussed
Key takeaways
There are different tests for coarse aggregate which are
1. Specific gravity
2. Grading of aggregate
3. Flakiness index
4. Elongation index
5. Impact value
6. Abrasion value
7. Crushing value
There are different type of test for fine aggregate which are
1. Specific gravity
2. Seive analysis
3. Fineness modulus
4. Alkali aggregate
5. Buckling of sand
6. Artificial and recycle aggregate
Special Concrete - Light Weight Concrete and its Type
- Lightweight concrete may be described as a sort of concrete which incorporates an increasing agent in that it will increase the quantity of the combination whilst giving extra characteristics which includes nailability and lessened the useless weight.
- It is lighter than the traditional concrete. The use of light-weight concrete has been broadly un fold throughout international locations which includes USA, United Kingdom and Sweden.
- The essential specialties of light-weight concrete are its low density and thermal conductivity.
- Its blessings are that there may be a discount of useless load, quicker constructing quotes in creation and decrease haulage and managing costs.
- Lightweight concrete keeps its huge voids and now no longer forming laitance layers or cement movies while located at the wall.
- These studies became primarily based totally at the overall performance of aerated light-weight concrete.
- However, enough water cement ratio is essential to provide good enough concord among cement and water.
- Insufficient water can purpose loss of concord among debris, for that reason loss in energy of concrete.
- Likewise, an excessive amount of water can purpose cement to run off mixture to shape laitance layers, finally weakens in energy.
- Lightweight concrete has been used because the eighteen centuries through the Romans.
- The software at the ‘The Pantheon’ wherein it makes use of pumice mixture with inside the creation of solid in-situ concrete is the evidence of its usage.
- In USA and England with inside the overdue 19th century, clinker became used of their creation as an example the ‘British Museum’ and different low price housing.
- The light-weight concrete became extensively utilized in creation at some point of the First World War.
- The United States used particularly for shipbuilding and urban blocks.
- The foamed blast furnace-slag and pumice mixture for block making had been added in England and Sweden round 1930s.
- Nowadays with the development of technology, light-weight concrete expands its makes use of.
- For example, with inside the shape of perlite with its top notch insulating characteristics.
- It is broadly used as loose-fill insulation in masonry creation wherein it complements hearth place ratings, reduces noise transmission, does now no longer rot and termite resistant.
- It is likewise used for vessels, roof decks and different applications.
Materials utilized in Light weight concrete:
- Lightweight concrete may be produced through introducing:
- Gassing retailers which include aluminium powder or foaming retailers,
- Light-weight mineral mixture which includes per lite, vermiculite, pumice, elevated shale, slate, and clay, or plastic granules as mixture
Properties of Light weight concrete:
- Low Density
- Fire Resistance
- Sound Insulation
- Durability
- Thermal insulation
- Quality Control
Low Density
- The density of concrete varies from three hundred to 1200 kg/m³.
- The lightest grade appropriate for insulation proposed whilst the heavier grades with good enough energy appropriate for structural applications.
- The low density of cell concrete makes it appropriate for precast ground and roofing devices which can be smooth to deal with and shipping from the manufacturing unit to the sites.
Fire Resistance
- Lightweight concrete has outstanding hearth place-resisting properties.
- Its low thermal conductivity makes it appropriate for protective every other established shape the outcomes of fir
Sound Insulation
- Sound insulation in cell concrete is typically now no longer as suitable as in dense concrete.
Durability
- Aerated concrete is handiest barely alkaline. Due to its porosity and coffee alkalinity.
- It does now no longer deliver rust safety to metallic that's supplied through dense as compared concrete.
Thermal insulation
- The insulation fee of light-weight concrete is set 3 to 6, instances that of bricks and approximately ten instances of concrete.
- When a two hundred mm thick wall of aerated concrete of density 800 kg/ m3 has the identical diploma of insulation as a four hundred mm thick wall of density 1600 kg/ m3.
Quality Control
- Better first-rate manipulate exercised with inside the creation of a shape with light-weight concrete merchandise because of using manufacturing unit-made devices.
Types of Light weight Concrete:
Lightweight aggregate concrete:
- Lightweight aggregate concrete is referred to as an LWA.
- In the early 1950s, using light-weight concrete blocks familiar withinside the UK for the load-bearing internal leaf of hollow space walls.
- Soon thereafter the improvement and manufacturing of a brand new sort of synthetic LWA made it viable to introduce LWC of excessive energy, appropriate for structural work.
- These advances inspire the structural use of LWA concrete. Particularly wherein the want to lessen weight in a shape became an critical attention for layout or for the economy.
Aerated Concrete:
- Aerated concrete has the bottom density, thermal conductivity, and energy.
- Like timber, it is able to be sawn, screwed and nailed, however there are non-combustible.
- For works in-situ, the standard strategies of aeration are through blending in stabilized shape or through whipping air in with the useful resource of an air-entraining agent.
No fines concrete:
The time period no-fines concrete typically way concrete composed of cement and a coarse (9-19) aggregates handiest and the product so fashioned has many uniformly disbursed voids for the duration of its mass.
- Ordinary light-weight concrete organized from a binder, water best and coarse mixture with complete filling voids among the huge debris.
- Low Sand concrete, wherein the voids among the coarse mixture handiest partly packed with the paste.
- It additionally referred to as an opening graded concrete and dealt separately.
- In this example on best mixture use. Coarse debris of the mixture are coved through a skinny layer of cement, paste and the voids among them stay empty. It is referred to as no concrete.
- Aerated concrete crafted from a binder, water, best and coarse mixture, and a blowing agent which reduced the density of concrete.
Typical Light weight concrete mix:
- Lightweight concrete is a combination made with light-weight coarse aggregates inclusive of shale, clay, or slate, which offer it its feature low density.
- Structural light-weight concrete has an in-location density of ninety to a hundred and fifteen lb/ft³, while the density of everyday weight concrete tiers from a hundred and forty to a hundred and fifty lb/ft³.
- This makes light-weight concrete perfect for constructing current systems that require minimum pass sections with inside the foundation.
- It is being an increasing number of used to construct glossy foundations, and has emerged as a possible opportunity to everyday concrete.
- Nevertheless, a better compressive power of 7000 to 10,000 psi may be attained with light-weight concrete.
- However, this will compromise the density of the combination because it calls for the addition of greater pozzolans and water-decreasing admixtures to the concrete.
Key takeaways
1. Lightweight concrete keeps its huge voids and now no longer forming laitance layers or cement movies while located at the wall.
2. This study became primarily based totally at the overall performance of aerated light-weight concrete.
3. Aerated concrete is handiest barely alkaline. Due to its porosity and coffee alkalinity.
4. It does now no longer deliver rust safety to metallic that's supplied through dense as compared concrete.
Foam Concrete
- Foam concrete usually consists of cement mortar or fly ash and sand and water, although some suppliers recommend pure cement and water with an agent that produces lightweight mixtures.
- This slurry is also mixed with a foam made into a concrete mixing plant. The foam is made using a moisturizing agent, mixed with water and air from the generator. The foam operator used must be able to produce bubbles with a high degree of stability, resistant to physical and chemical processes of mixing, depositing and solidifying.
- Foam concrete mix can be poured or sprayed on moulds, or directly on parts of the building. Foam makes the Sulphur flow freely due to the thixotropic behaviour of foam bubbles, allowing it to be easily absorbed into the selected form or mould.
- Viscous materials require up to 24 hours to harden (or at least two hours if the smoke is treated at temperatures up to 70 ° C to speed up the process. Depending on the variability including ambient temperature. And moisture. Once solidified, the manufactured product can be removed from its mould.
- A new application in the production of foam concrete is to cut large-size concrete cakes into blocks of different sizes with a cutting machine using special metal wires. The cutting action occurs when the concrete is still soft.
Properties
Foam concrete is a versatile construction material with a simple and inexpensive method of production compared to air-cooled autoclave concrete. Foam compounds using foam-using ashes for this cheap compound are still cheap, and have little impact on the environment. Foam concrete is produced in quantities ranging from 200 kg / m3 to 1,600 kg / m3 depending on the application. Smaller products can be divided into different sizes. While the product is considered to be a type of concrete (with air bubbles replacing the whole), its thermal and sound insulation properties make it a very different application than conventional concrete.
Applications
Foam concrete can be produced in dry quantities of 400 to 1600 kg / m3 (25 lb / ft3 to 100 lb / ft3), with a capacity of about 7 to 10 days N / mm2 (145 to -1450 psi) respectively. The foam concrete is fire resistant, and its thermal and sound insulation properties make it ideal for a variety of purposes, from floor and ceiling protection, to useless filling. It also helps to restore the trench.
A few applications of foam concrete are:
- Bridge / bar road routes
- Pipe discharge / annual filling
- Back ditch
- Precast blocks
- Precast wall elements / panels
- Cast-in-situ / cast-in-place walls
- By defending the imposition of compensation
- Split down screens
- Partition roof screeds
- The filling of the deceased part
- Trench for restoration
- Sub-base on highways
- The filling of empty blocks
- Partition boards used
Key takeaways
1. Lightweight concrete may be described as a sort of concrete which incorporates an increasing agent in that it will increase the quantity of the combination whilst giving extra characteristics which includes nailbility and lessened the useless weight.
2. It is lighter than the traditional concrete. The use of light-weight concrete has been broadly un fold throughout international locations which includes USA, United Kingdom and Sweden.
No Fines Concrete
What is No-Fines Concrete?
- No-Fines Concrete is a lightweight concrete made of cement only, cement and water by leaving fine particles (sand or fine compounds) of ordinary concrete. The benefits, limitations and equity of the exemptions are discussed.
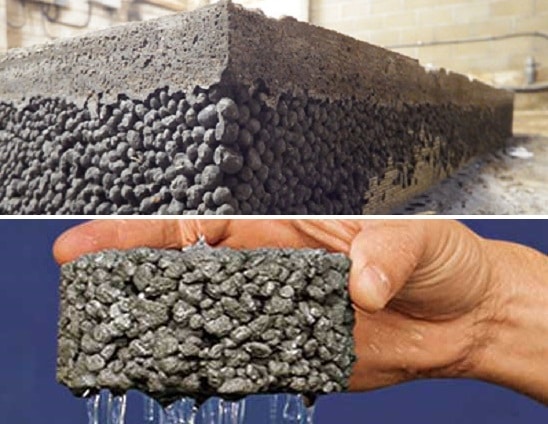
Fig no 34. No fines concrete
- Usually only one equal measurement, of more than 20 mm in size, is kept in 10mm. Concrete no-faes are popular because of the specific benefits you have over conventional concrete.
- The single-layer collection makes a beautiful, non-abrasive concrete, which in addition to getting large voids and therefore light weight, also gives a nice look to the build.
Advantages of No-Fines Concrete
- No fine concrete is a heavy concrete i.e. the density is approximately 25 to 30% less than normal concrete due to the lack of good adhesion, so the weight of the structure is small.
- Since it does not have good sand or aggregates, it has less drying shrinkage compared to conventional concrete
- It has a better heat protection feature than ordinary concrete and therefore helps in the construction of the outer wall.
- Since it does not have good aggregates, the required area for cement coverage has been greatly reduced. Therefore, the required amount of cement is reduced per cubic meter compared to conventional concrete. Therefore, it will save.
- Heavy concrete has no effect on quality due to the fragmentation of the compact cluster as it does not have good dimensions. Therefore, it can be thrown higher.
- No fine concrete can be assembled without the need for any types of concrete vibrators and can be easily made by touching the rods.
Limitations of No Fines Concrete
- Since there are no good compounds to fill the gaps in this concrete, it has a higher penetration than standard concrete. Therefore, it is not a good idea to build reinforced concrete without compensation concrete, as reinforcement can be easily eaten.
- To make this concrete inaccessible, an additional coat of construction mud is required, which adds to the cost.
- There is no concrete test that can be tested for effectiveness by using tests on standard concrete such as rolling or testing for rigidity. Performance rates and their testing methods are unknown.
Mix proportion of No-Fines Concrete
- No-fines concrete is usually made with aggregate / cement scales from 6: 1 to 10: 1. The standard aggregates used are usually sizes over 20 mm and stored at 10 mm.
- Unlike conventional concrete, where the strength is primarily controlled by the water / cement ratio, the strength of the concrete can be charged depending on the water / cement ratio, the estimated cement ratio and the weight of the concrete.
- The water / cement ratio for satisfactory consistency will vary between a minimum width of 0.38 and 0.52. The water / cement level should be chosen carefully. If a very low amount of water / cement is accepted, the adhesive will dry so much that the adhesive can be well coated with adhesive resulting in insufficient adhesion between the particles.
- On the other hand, if the water / cement ratio is too high, the glue will run down the concrete floor, especially if you move and fill in the gaps between the joints at the bottom and make that part more compact. This condition also reduces the adhesion between the adhesive and the adhesive due to the adhesion being much thinner.
- There is no standard method available, such as a descent test or an object measurement test to measure the consistency of a non-finite concrete. Perhaps a good test, visual experience and trial and error method would be the best guide to determine the water / cement ratio.
- No-faes concrete, when using standard aggregates, can show a density of about 1600 to 1900 kg / m3, but if no-faes concrete is made using lightweight aggregate, the size can reach approximately 360 kg / m3.
- Concrete of no-faes does not pose a major congestion problem. The use of a combination of equipment or vibration methods is not required. Simple rodding is sufficient for full filling.
- Concrete of no-faes does not give much to the formation side as the particles have a point of identification of the contact and the concrete does not move. Therefore, the side of the formworks can be removed in a much shorter time than ordinary concrete.
- However, the forms may need to be stored longer, when used as part of the structure, as the strength of the concrete decreases considerably. The compressive strength of the fine-grained concrete varies between 1.4 M Pa to 14 M.
- The strength of the bonded concrete bond is very low and, therefore, the reinforcement is not used in combination with the non-charged concrete. However, if the reinforcement needs to be applied to a non-abrasive concrete, it is advisable to touch the reinforcement with cement to improve the bond and protect it from cracking.
Key takeaways
1. No-Fines Concrete is a lightweight concrete made of cement only, cement and water by leaving fine particles (sand or fine compounds) of ordinary concrete. The benefits, limitations and equity of the exemptions are discussed.
2. Usually only one equal measurement, of more than 20 mm in size, is kept in 10mm. Concrete no-faces are popular because of the specific benefits you have over conventional concrete.
Self Compacting Concrete
- Self-compacting concrete (SCC) is a flowing concrete that doesn't require vibration and, indeed, have to now no longer be vibrated.
- It makes use of super plasticizers and stabilizers to seriously growth the benefit and price of glide.
- It achieves compaction into each a part of the mildew or formwork genuinely by using its personal weight with none segregation of the coarse aggregate.
- The consistence of the concrete is designated and measured as a glide price as opposed to the everyday stoop test.
SCC offers:
- Health and protection benefits (as no vibration is needed).
- Faster creation times.
- Increased workability and simplicity of glide round heavy reinforcement.
- Excellent sturdiness.
Advantages of SCC:
- No vibration is needed in the course of the position into forms.
- Placement of concrete easier.
- Reduces the concreting time.
- Increased sturdiness of structure.
- High Strength
Material used in SCC:
- The powdered substances that may be delivered are fly ash, silica fume, lime stone powder, glass filler and quartzite filler.
Tests for SCC:
Following are numerous techniques for checking out the houses of sparkling concrete:
- Slump glide test
- T50 stoop glide test
- J ring test
- V Funnel test
- V funnel at T5 minute
- L container test
- U container test
- Fill container test
- GTM display balance test
- Orimet test
Sr .no. | Method | Units | Typical mix | |
Minimum | Maximum | |||
1 | Slump cone by Abrams cone | Mm | 650 | 800 |
2 | T50slumpflow | Sec | 2 | 5 |
3 | J ring | Mm | 0 | 10 |
4 | V funnel | Sec | 8 | 12 |
5 | V funnelatT5minute | Sec | 0 | 3 |
6 | L box | (h2/h1) | 0.8 | 1.0 |
7 | U box | (h2-h1) Mm | 0 | 30 |
8 | Fill box | % | 90 | 100 |
9 | GTM screen stability test | % | 0 | 15 |
10 | Orimet | Sec | 0 | 5 |
Properties of SCC:
Strength:
Strength of concrete are of the subsequent types:
- Compressive strength
- Tensile strength
- Flexural strength
- Shear strength
1.Compressive Strength
- The dice specimens of concrete of the preferred percentage are solid in metallic or solid iron moulds, typically 6-inch dice.
- The general cylinder specimen of concrete is 6 inch in diameter and 12 inches in peak and solid in a mould commonly fabricated from solid iron;
- Standard cubes and cylinders are examined at prescribed ages, commonly, 28 days, with extra exams frequently made at 1, three, and seven days.
- The specimens are examined for crushing electricity below a checking out machine.
- The dice exams supply an awful lot more values of crushing electricity, typically 20 to 30 % extra than the ones given via way of means of cylinders.
Effect of age on concrete strength:
- Concrete attains electricity with time.
- Ordinary cement concrete profits above 70 to 75% of its very last electricity inside 28 days and approximately ninety to 95 % with inside the path of 1 year.
- It is frequently perfect to test the suitability of a concrete lengthy earlier than the effects of the 28-day check are available.
- When no particular records at the substances utilized in making concrete are available, the 28-day electricity can be assumed to be 1.5 instances of the 7 days’ electricity.
- Tests have proven that for concrete made with regular Portland cement the ratio of the 28 days to 7 days’ electricity commonly lies among 1.three to 1.7, and the bulk of the effects fall above 1.5.
2. Tensile strength
- Concrete could be very susceptible in tension.
- The tensile electricity of regular concrete levels from approximately 7 to 10 percentage of the compressive electricity.
3. Flexural strength
- The flexural electricity of undeniable concrete is nearly fully established upon the tensile electricity.
- However, experiments display that the modulus of rupture is substantially more than the electricity in tension.
4. Shear strength
- It is the actual figuring out issue with inside the compressive electricity of brief columns.
- The common electricity of concrete in direct shear varies from approximately 1/2 of of the compressive electricity for wealthy combinations to approximately 0.8 of the compressive electricity for lean combinations.
Workability:
- The electricity of concrete of a given blend percentage could be very significantly laid low with the diploma of its compaction.
- It is consequently essential that the consistency of the combinationture be such that the concrete may be transported, positioned and completed sufficiently effortlessly and without segregation.
- A concrete pleasant those situations is stated to be workable.
Elastic Properties:
- Concrete isn't always flawlessly elastic for any variety of loading, an considerable everlasting placing taking location for even low loads.
- The deformation isn't always proportional to the strain at any degree of loading.
- The elastic residences of concrete range with the richness of the aggregate and with the depth of the strain.
- They additionally range with the age of concrete.
Durability:
- Durability is the assets of concrete to face up to the circumstance for which it's been designed, without deterioration over a length of years.
- Lack of sturdiness may be resulting from outside sellers bobbing up from the surroundings or via way of means of inner sellers in the concrete.
Application of SCC:
- Construction of Bridges, buildings, tunnels.
- Precast Concrete Members
- Casting of slab and slender wall
Typical Mix:
- A easy device has been designed for self-compacting concrete (SCC) blend layout with 29% of coarse aggregate, substitute of cement with Meta kaolin and sophistication F fly ash, combos of each and managed SCC blend with 0.36 water/cement ratio(via way of means of weight) and 388 litre/m3 of cement paste volume.
Key Takeaways
1. Self-compacting concrete (SCC) is a flowing concrete that doesn't require vibration and, indeed, have to know no longer be vibrated.
2. Concrete isn't always flawlessly elastic for any variety of loading, an considerable everlasting placing taking location for even low loads.
High Density Concrete
- High density concrete is a concrete having a density with inside the variety of 6000 to 6400 kg/cu.m.
- High density concrete is likewise called Heavy weight concrete.
- High density concrete is specifically used for the cause of radiation protective, for counterweights and different makes use of in which excessive density is required.
- The excessive density concrete has a higher protective property, in order that it is able to shield dangerous radiations like X-rays, gamma rays, and neutrons.
- High density aggregates are used to attain heavy weight concrete. Some of the excessive density aggregates are, barite, ferro phosphorus, limonite, hematite, ilmenite, magnetite, goethite, metallic punching, and metallic shots.
- The factor to keep in mind is that in order to attain this sort of concrete, excessive constant water content material is required.
- The choice of the above cited aggregates specifically depends on the bodily houses like bulk density, unique gravity, Availability of substances, and its expenses.
- In order to attain workability, excessive density the aggregates have to be loose from dirt, oil or grease stains and different overseas matter.
- Or else, it's going to retard the hydration method and the powerful bonding of particles.
- Some of the boron additions like colemanite, boro calcite is used with inside the preparation of concrete to enhance the protective houses.
- These additions might also additionally have an effect on the placing time of concrete so, trial mixes have to be made and examined relying upon the suitability.
- As the call suggests, the density of this concrete varies from 3360 kg/m3 to 3840 kg/m3, while the density of regular concrete is of the order of 2400 kg/m3.
- The density of mild weight concrete is ready 1900 kg/m3 and that of regular concrete approximately 2400 kg/m3.
- Thus, the density of excessive density concrete is ready 50% greater than the density of traditional concrete.
- However, this concrete may be produced of density up to 5200 kg/m3 the use of iron as each nice and coarse mixture.
- With the arrival of the nuclear electricity, there's a big call for of the concrete technologists with inside the market.
- Due to using nuclear electricity generating reactors, big scale manufacturing of penetrating radiation and radioactive substances additionally has taken location.
- Thus, all nuclear electricity generating gadgets inclusive of nuclear reactors, particle accelerator, business radiography, x-ray and gamma ray remedy gadgets require nuclear protective cloth for the safety of the working employees in opposition to the organic risks inclusive of radiation.
- The regular in addition to excessive density concrete is powerful and low in cost for the development of everlasting guard in opposition to radiation.
Materials in High density concrete:
- All represent substances, cement, admixtures, and water utilized in excessive density concrete have to agree to the requirements as for regular density concrete, however the aggregates is unique and can require unique attention at some stage in handling, batching, blending, transporting and setting.
Aggregates:
- High density concrete (HDC), densities is executed via way of means of the use of excessive-density aggregates commonly iron oxides and relies upon on its meant use, bodily and chemical houses, availability and price.
- Concrete densities of 3700 to 3800 kg/m³, is offered utilizing aggregates with particle relative densities of as a minimum 4500 kg/m³ and for concrete densities of 4800 kg/m³ aggregates have to have a particle relative density of as a minimum 6000 kg/m³.
- Aggregate grading for HDC hardly ever agree to regular mixture requirements because the mixture are hardly ever made for concrete manufacturing, this have to be general via way of means of capacity customers because it isn't always adverse to the manufacturing of HDC.
- The maximum critical a part of HDC aggregates is that the grading have to be consistent and that a attainable grading restriction be agreed on with the dealer, to base the combination layout on.
- The chemical houses of all excessive-density aggregates have to be evaluated earlier than use, chemical reactivity and mainly in excessive alkaline environments as observed in cement pastes, long time sturdiness inclusive of alkali-mixture reactivity, sulphate and chloride assault and different impurities.
- The dealer have to be capable of offer a complete chemical evaluation of all capacity substances and opportunity substances to be used.
- With right technical assessment and planning, unique styles of aggregates may be blended on the dealer backyard to provide a concrete with predicted, detailed density.
- Cost thing are very critical as those aggregates are commonly greater highly-priced than regular aggregates, it is able to additionally be that the cloth might also additionally handiest be to be had in relative brief supply.
- The price of HDC will increase with density however now no longer essential in direct proportion.
- Aggregates have to be decided on for his or her shape (cubical or rounded and freed from flat or elongated, most density, workability, and price. Particle relative density of the nice mixture have to be just like that of the coarse mixture as decrease density nice mixture can cause segregation of the coarse mixture via the mortar.
- The grading of the coarse mixture have to be uniformly graded among 10 and 40mm, as in step with limits in Table 1. The grading of the nice mixture have to be in the restriction as proven in Table 1 as this will assist to save you segregation.
Sieve sizes mm:
Grading 1 for 37.5 mm most length aggregates % passing
Grading 2 for 19.0 mm most length aggregates % passing
Coarse aggregates:
Two styles of aggregates may be used for excessive density concrete namely:
Natural aggregates:
- Iron ores of diverse sorts had been used all over the globe for lots years (out of doors the U.K), with inside the UK imported iron ore is used.
- Using a few herbal going on aggregates concrete densities of about 4000 kg/m³ may be obtained. (J. Goodman, 2009)
- Different styles of herbal excessive-density aggregates which may be used for excessive density concrete (HDC) to be had in South Africa and the United Kingdom talk over with Table 2.
Man-made aggregates:
- To attain concrete densities above 4000 kg/m³ man-made or artificial cloth inclusive of ferrosilicon slag, metallic or lead shot may be used.
- For styles of man-made aggregates which may be used for excessive density concrete (HDC) to be had in South Africa and the United Kingdom talk over with Table 2.
Cements:
- All cements conforming to SANS 50197 as for traditional concrete may be used for HDC if it produces the desired bodily houses.
- If alkali-reactive materials are gift with inside the aggregates cements with low alkali contents or a appropriate combination of cements and cement extenders have to be used.
- Low-alkali cement now no longer having greater that zero.6 % Na2O-eq can be used with a doubtlessly alkali-reactive mixture inclusive of lead shot.
- The following extenders: Ground granulated blast furnace slag (GGBS), fly ash (FA) and Condensed silica fume (CFS) have decrease densities than Ordinary Portland Cement (OPC) and may be used in the event that they do now no longer lessen the density of the concrete under detailed limits, but states “The cement may be OPC or a mix of this with both Ground granulated blast furnace slag, Pozzolanic fly ash; the latter if you want to now no longer lessen the density of the concrete however might also additionally decorate the in any other case terrible workability”.
- Fly ash blends and decrease water contents can effectively be used to boom the density of concretes. When lad shot is used High alumina cement (HAC) should be used, because it reduces the chemical reactivity of lead in excessive alkaline conditions.
- When the use of alkali-reactive mixture (lead shot) deleterious enlargement may be avoided whilst the use of excessive-alkali cements via way of means of including extenders complying with SANS 1491 via way of means of the use of a minimal percent of the subsequent extenders via way of means of general mass of cement:
At least 40% Slag (S) via way of means of mass
At least 15% CSF via way of means of mass
At least 20%via way of means of mass
Admixtures:
- Adding admixtures can minimize segregation, bleeding, each of which may be complex with HDC. The sturdiness may be advanced with a low loose water/cement ratio (w/c) in particular so in structural grade HDC.
- Using terrific plasticizers is usually recommended which in conjunction the cement kind might also additionally marginally boom concrete density.
- Super plasticizers are useful in decreasing water to minimize bleeding and preserve a cohesive blend that has minimal segregation.
The following admixture may be utilized in HDC:
- Air-entraining admixtures because it controls bleeding and agreement enhance workability and help in acquiring greater homogenous concrete however will lessen the density of the concrete.
- Water-decreasing admixtures because it will boom concrete density via way of means of decreasing the quantity of water with inside the blend, water is the cloth utilized in HDC with the bottom density.
- Shrinkage-decreasing admixtures because it make sure dense, crack-loose concrete used for radiation-protective concrete
- When lead shot or lead containing aggregates are to be used, the subsequent have to be taken into consideration whilst choosing a chemical admixture.
- The alkali content material of chemical admixtures for concrete utilized in South Africa is among approximately zero.2 and 7%. In many times the contribution to the alkali content material of the pore answer is big and can't be ignored.
- One of the extensively used terrific plasticizers has a Na2O-eq of approximately five% and if introduced at 1% of cement to concrete with a cement content material of 350 kg/m³ it's going to advert 0.17 kg/m³ Na2O-eq to the concrete.
- Lithium primarily based totally compounds may be used with lead shot to manipulate the alkali reactivity.
- The impact of admixtures have to be installed beneath discipline conditions, ideally via way of means of testing, to decide if the admixtures attain the desired effects or completely unsuitability.
Water:
- Water will be easy and loose from adverse concentrations of acids, alkalis, salts, sugar and different natural or chemical materials that would impair the sturdiness and power of concrete or imbedded metallic.
Proportioning, blending and setting of High Density Concrete:
- The blend proportions for those excessive density concrete is identical as that of regular concrete.
- Conventional approach of blending and setting is utilized in excessive density concrete. The maximum critical aspect is to save you overloading the mixer in particular whilst heavy weight aggregates inclusive of steels are used. Batch sizes have to be decreased to forty to 50% of the allowable mixer capacity. Also keep away from extra blending as it will bring about workability and bleeding of concrete.
- Preplaced mixture strategies may be followed whilst setting heavy weight concrete. In this approach the aggregates are located in forms , an appropriate grout made from cement, sand and water is pumped over the located aggregates, a good way to fill the voids in between the aggregates. This approach prevents the segregation of coarse aggregates additionally reduces drying shrinkage and facilitates us to attain concrete of uniform density and composition.
- Puddling approach also can be followed. In this approach, the mortar is located in varieties of 2″ thick and the coarse aggregates are located over it and vibrated internally. Care have to be taken that, the coarse aggregates are allotted evenly.
- Pumping of heavy weight concrete may be followed handiest the peak is limited. The heavy weight concrete can't be pumped to large distances due to their extra densities
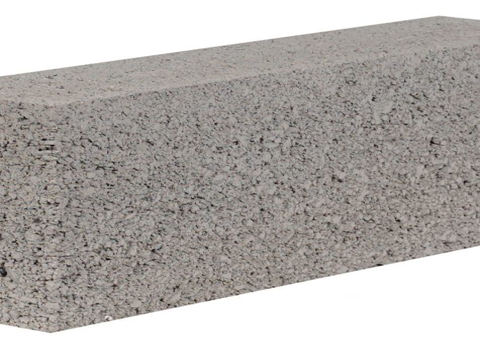
Fig no 35. High density concrete
Key takeaways
1. High density concrete is specifically used for the cause of radiation protective, for counterweights and different makes use of in which excessive density is required.
Fibre Reinforced Concrete, Geo Polymer Concrete and Ferrocement Technique
Fibre Reinforced Concrete
- Fibre Reinforced Concrete is a composite cloth which include fibrous cloth which will increase its structural integrity.
- It consists of combinations of cement, mortar or concrete and discontinuous, discrete, uniformly dispersed appropriate fibers.
- Fibers are normally utilized in concrete to govern cracking because of plastic shrinkage and to drying shrinkage.
- They additionally lessen the permeability of concrete and consequently lessen the bleeding of water.
Advantages of Fiber-strengthened concrete:
- Fibers strengthened concrete can be beneficial in which excessive tensile power and decreased cracking are proper or whilst traditional reinforcement cannot be placed.
- It improves the effect power of concrete, limits the crack boom and ends in a extra stress potential of the composite cloth.
- For commercial projects, macro-artificial fibers are used to enhance concrete’s sturdiness.
- Made from artificial substances, those fibers are lengthy and thick in length and can be used as a substitute for bar or material reinforcement.
- Adding fibers to the concrete will enhance its freeze-thaw resistance and assist maintain the concrete sturdy and appealing for prolonged periods.
- Improve blend cohesion, enhancing pumpability over lengthy distances.
- Increase resistance to plastic shrinkage in the course of curing.
- Minimizes metallic reinforcement requirements.
- Controls the crack widths tightly, consequently enhancing sturdiness.
- Reduces segregation and bleed-water.
- FRC, longevity is ready 10 to forty instances that of undeniable concrete.
- The addition of fibers will increase fatigue power.
- Fibers boom the shear potential of strengthened concrete beams.
Application of Fiber-strengthened concrete:
The programs of fiber strengthened concrete rely on the applicator and builder in taking gain of the static and dynamic traits of the cloth. Some of its vicinity of software is-
- Runway
- Aircraft Parking
- Pavements
- Tunnel Lining
- Slope Stabilization
- Thin Shell
- Walls
- Pipes
- Manholes
- Dams
- Hydraulic Structure
- Elevated decks
- Roads
- Bridges
- Warehouse floors
Fiber Types:
- Fibers for concrete are to be had in exclusive sizes and shapes.
- The essential elements affecting the function of fiber-strengthened concrete are a water-cement ratio, percent of fibers, diameter and duration of fibers.
- Given beneath are exclusive varieties of fiber-strengthened concrete utilized in production.
Steel Fiber Reinforced Concrete:
- Steel fiber is a metallic reinforcement. A sure quantity of metallic fiber in concrete can motive qualitative modifications in concrete’s bodily property.
- It can significantly boom resistance to cracking, effect, fatigue, and bending, tenacity, sturdiness, and others.
- For enhancing lengthy-time period behavior, improving power, longevity, and strain resistance, SFRC is being utilized in systems which includes flooring, housing, precast, bridges, tunneling, heavy-responsibility pavement, and mining.
- The varieties of metallic fibers are described via way of means of ASTM A820 are, Type I: cold-drawn cord, Type II; reduce sheet, Type III: melt-extracted, Type IV: mill reduce and Type V: changed cold-drawn cord
Polypropylene Fiber Reinforced (PFR) Concrete:
- Polypropylene fiber strengthened concrete is likewise referred to as poly propene or PP.
- It is a artificial fiber, converted from propylene, and utilized in loads of programs.
- These fibers are normally utilized in concrete to govern cracking because of plastic shrinkage and drying shrinkage.
- They additionally lessen the permeability of concrete and consequently lessen the bleeding of water.
- Polypropylene fiber belongs to the institution of polyolefins and is partly crystalline and non-polar.
- It has comparable homes as poly ethylene, however it's far tougher and greater warmth resistant.
- It is a white rugged cloth with excessive chemical resistance.
- Polypropylene is made from propylene fuel with inside the presence of a catalyst which includes titanium chloride.
- Polypropylene fiber shows accurate warmth-insulating homes and is especially immune to acids, alkali, and natural solvents.
Glass Fiber Reinforced Concrete:
- Glass fiber strengthened concrete is a cloth which include severa extraordinarily first-rate fibers of glass.
- Glass fiber has kind of similar mechanical homes to different fibers which includes polymers and carbon fiber.
- Although now no longer as inflexible as carbon fiber, it's far tons less expensive and notably much less brittle whilst utilized in composites.
- Glass fibers are consequently used as a reinforcing agent for lots polymer merchandise; to shape a totally sturdy and comparatively light-weight fiber-strengthened polymer (FRP) composite cloth known as glass-strengthened plastic (GRP), additionally popularly referred to as “fiberglass”.
- This cloth incorporates very little air or fuel line, is denser, and is a miles poorer thermal insulator than is glass wool.
Polyester fibers:
- Polyester fibers are utilized in fiber-strengthened concrete for commercial and warehouse floors, pavements and overlays and precast merchandise.
- Polyester micro- and macro-fibers are utilized in concrete to offer advanced resistance to the formation of plastic shrinkage cracks as opposed to welded cord material and to decorate longevity and the capacity to supply structural potential whilst well designed, respectively.
- Polyester micro- and macro-fibers are utilized in concrete to offer advanced resistance to the formation of plastic shrinkage cracks as opposed to welded cord material and to decorate longevity and the capacity to supply structural potential whilst well designed, respectively.
Carbon fibers:
- Carbon fibers are fibers approximately 5–10 micrometers in diameter and composed in general of carbon atoms.
- Carbon fibers have numerous benefits such as excessive stiffness, excessive tensile power, low weight, excessive chemical resistance, excessive-temperature tolerance and coffee thermal expansion.
- Carbon fibers are normally mixed with different substances to shape a composite.
- When impregnated with a plastic resin and baked it bureaucracy carbon-fiber-strengthened polymer (frequently known as carbon fiber) which has a totally excessive power-to-weight ratio, and is extraordinarily inflexible even though particularly brittle.
- Carbon fibers also are composited with different substances, which includes graphite, to shape strengthened carbon composites, that have a totally excessive warmth tolerance.
Macro artificial fibers:
- Macro artificial fibers are crafted from a mix of polymers and have been at the beginning advanced to offer an opportunity to metallic fibers in a few programs.
- Initially, they have been diagnosed as a ability opportunity to metallic fibers in sprayed concrete, however growing studies and improvement confirmed that that they'd a function to play withinside the layout and production of ground-supported slabs and a huge variety of different programs.
- They are specifically appropriate for presenting nominal reinforcement in competitive environments, which includes marine and coastal systems, as they do now no longer go through the troubles of staining and spalling which could end result from the corrosion of metallic.
- Besides, due to the fact they may be non-conducting, they had been utilized in tram and mild railway developments.
Micro-artificial fibers:
- Micro-artificial fibers offer advanced resistance to the formation of plastic shrinkage cracks as opposed to welded cord reinforcement, they may be not able to offer any resistance to similarly crack width openings due to drying shrinkage, structural load or different sorts of strain.
- However, those merchandise need to be frequently laid out in any form of concrete to enhance cracking resistance, spall protection, freeze-thaw sturdiness and enhance the homogeneity of concrete in the course of placement.
Natural fibers:
- The herbal fiber is without delay available from an animal, vegetable, or mineral supply and convertible into nonwoven fabric which includes felt or paper or, after spinning into yarns, into woven cloth.
- A herbal fiber can be similarly described as an agglomeration of cells wherein the diameter is negligible in evaluation with the duration.
- Although nature abounds in fibrous substances, in particular cellulosic kinds which includes cotton, wooden, grains, and straw.
- The use of herbal fibers in making concrete is usually recommended in view that numerous varieties of those fibers are to be had domestically and are plentiful.
- The concept of the use of such fibers to enhance the power and sturdiness of brittle substances isn't new; for example, straw and horsehair are used to make bricks and plaster.
- Natural fibers are appropriate for boosting concrete and are without difficulty to be had in growing countries.
Cellulose fibers:
- Cellulose fibers are made with ethers or esters of cellulose, which may be acquired from the bark, wooden or leaves of plants, or different plant-primarily based totally cloth.
- In addition to cellulose, the fibers may comprise hemi cellulose and lignin, with exclusive possibilities of those additives changing the mechanical homes of the fibers.
- The predominant programs of cellulose fibers are with inside the fabric industry, as chemical filters, and as fiber-reinforcement composites, because of their comparable homes to engineered fibers, being every other alternative for bio composites and polymer composites.
Geo Polymer Concrete
- Geo polymer is the name given to the Daidovits in 1978 for items that appear in chains or networks or unusual molecules.
- Geopolymer cement concrete is made using waste materials such as fly ash and ground granulated blast furnace slag (GGBS). An ash fly is a waste product produced from a hot power plant and the granulate blast soil in a furnace is processed as a metal waste.
- Both fly ash and GGBS are processed by appropriate technology and applied to concrete operations in the form of a geo polymer concrete. The use of this concrete helps to reduce waste stocks and reduces carbon emissions by reducing demand for Portland cement.
- A key feature of the geo polymers source of silicon and aluminum is supplied by natural thermal agents (e.g. kaolinite) or industrial products (e.g. Fly ash or slab) and an alkaline solution that makes these materials chains and networks to create strong bond. Also called alkaline cement or inorganic polymer cement.
Composition of Geo polymer Concrete
The following materials are required to produce this concrete:
- Fly ash - Fly ash generator
- GGBS - Metal Product
- Good collection and heat collection as required for standard concrete.
- GPCC alkaline activator solution as described above. The Catalytic liquid system is used as an alkaline activator solution. It is a combination of alkali silicates and hydroxide solutions, in addition to pure water. The role of the alkaline activator solution is to activate geopolymeric resource sources containing Si and Al such as fly ash and GGBS.
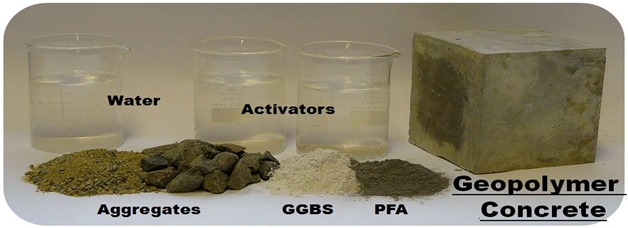
Fig no 36. Geo polymer Concrete Materials
Mechanical properties of Geo polymer Concrete
- Geo polymer concrete pressures were obtained up to 70 MP a (N / mm2). Concrete gains its compression strength much faster and faster than conventional Portland concrete.
- Concrete strength after 24 hours was found to be more than 25 M Pa. Pressure capacity after 28 days was found to be 60 to 70 M Pa. -Ref. Paper by James Aldred and John Day and test results by SERC Chennai.
Other properties of Geo polymer Concrete:
- The reduction in dryness is very small compared to cemen. This makes it ideal for members of a dense and highly restricted concrete structure.
- It has a lower hydration temperature compared to cement.
- Fire resistance is much better than OPC-based concrete. -Reference - Paper by - James Aldred and John Day.
- This concrete measure of jas chloride permeability is 'low' to 'very low' according to ASTM 1202C. It provides better protection of metal reinforcement from corrosion compared to traditional cement mortar.
- This concrete is found to have a very high acid content when tested under 2% and 10% exposure to sulfuric acid.
Application of Geo polymer Concrete
- Applications are similar to cement cement. However, the subject has not been used extensively in various programs.
- This concrete is used for the construction of paved stones, retaining walls, water tanks, precast bridge supplies.
- Recently the world's first building to be built on earth, the University of Queensland's Global Change Institute (GCI) was built using geo polymer concrete. It is a four-story high-rise building for public use.
Ferro Cement Technique
- Mining
- Crushing, stacking, and reclaiming of uncooked substances.
- Raw meal drying, grinding, and homogenization.
- Clinkerization.
- Cement grinding and garage.
- Packing
Mining:
- The cement production system begins off evolved from the mining of uncooked substances which might be utilized in cement production, specially limestone and clays.
- A limestone quarry is with inside the plant region and a clays quarry is as a ways from the plant region as 25 km.
- The limestone is excavated from open forged mines after drilling and blasting and loaded onto dumpers which shipping the substances and sell off into hoppers of limestone crushers.
- The clays are excavated from open forged mines and loaded onto dumpers which shipping the substances and sell off into open backyard garage.
- Then it's miles transported through vehicles and unloaded into the hopper of a clay crusher.
- They are 3 varieties of clay utilized in cement production, specifically silty clay, Zafarana clay, and Kaolin.
- Other uncooked substances are used to govern the kiln feed blend design, specifically sand, and iron ore.
- The sand and iron ore are shipping from outdoor the plant (from extraordinary suppliers) through vehicles and unloaded into open backyard piles, known as sand and iron ore piles.
Crushing, stacking, and reclaiming of uncooked substances:
- The limestone is beaten with inside the first crusher known as a jaw crusher after which fed into the second one crusher known as an effect crusher with blending of clays to lessen particle length beneath 50mm.
- The discharged uncooked blend (limestone 70%, clays 30%) is fed onto a belt conveyor and exceeded throughout a bulk fabric analyzer.
- The uncooked blend is fed right into a round garage unit known as a uncooked blend garage.
- Then, the combination is extracted transversely from the stockpile through reclaimers and conveyed to a uncooked mill bin known as the uncooked blend bin for grinding.
- The different uncooked substances which might be utilized in cement production, known as additives, are excessive purity limestone, sand and iron ore.
- The excessive purity limestone is beaten in a lone in jaw crusher after which beaten extra in a secondary crusher to lessen the scale to absolutely byskip via a 50mm sieve.
- Then, it's miles stacked through a limestone stacker right into a longitudinal garage unit known as the limestone garage stockpile.
- Finally, the limestone is extracted transversely from the stockpile through reclaimer and conveyed to a uncooked mill bin, known as the limestone bin, for grinding.
Raw meal drying, grinding, and homogenization:
- The uncooked blend, excessive grade limestone, sand, and iron ore are fed from their containers to uncooked turbines, known as air swept turbines, for drying and pleasant grinding.
- The uncooked mill includes chambers, separated through diaphragm, specifically a drying chamber and a grinding chamber.
- The warm gases coming from a pre heater (pre heater / kiln machine) input the mill and are utilized in uncooked turbines for drying.
- Then the drying substances input the grinding chamber of uncooked turbines for pleasant grinding.
- The grinding chamber includes a positive amount of ball price in a extraordinary sizes starting from 30mm to 90mm.
- The warm fuel line and grinding substances mill outlet feeds to a separator which separates pleasant and path product.
- The latter, known as reject, is dispatched to the mill inlet thru an air slide for regrinding.
- The warm fuel line and pleasant substances input a multistage "cyclone" to split a pleasant substances and gases.
- The pleasant fabric, known as uncooked meal, is accrued from the multi-cyclone after which fed into an air slide for lifting known as an Aeropol.
- The warm gases with very pleasant substances input an electrostatic precipitator to split the pleasant substances from gases.
- The very pleasant substances known as pre heater dirt or electrostatic separator dirt is accrued from filters and fed into screw conveyors and are then combined with the pleasant fabric in an air slide and transported to an air elevate vessel thru air slide.
- In the air elevate, the uncooked meal is lifted to the silo through compressed air to the air slide after which saved and homogenized in a concrete silo.
- Raw meal extracted from the silo, now known as kiln feed, is fed to the pinnacle of the pre heater thru an air elevate known as the Poldos for pyro-processing.
Clinkerization:
- Cement clinker is made through pyro processing of kiln feed into the pre heater-kiln machine. The pre-heater-kiln machine includes a multi-degree cyclone
- Pre heater with 5 stages, combustion chamber, riser duct, rotary kiln, and grate cooler.
- In the pre heater, the kiln feed is preheated through warm fuel line coming from the combustion chamber and rotary kiln.
- Then the preheated kiln feed is partly calcined (made powdery) in a combustion chamber and riser duct after which absolutely calcined in a rotary kiln in addition to heated to about 1400 C to shape clinker additives C3A, C4AF, C2S, and C3S.
- The foremost supply of warmth is herbal fuel line.
- Natural fuel line is fired as a major gasoline (100 %) with inside the foremost burner rotary kiln and a 95% herbal fuel line and 5.0% heavy oil aggregate with inside the combustion chamber.
- The gasoline is used to offer the warmth required to transform the kiln feed into clinker.
- Hot clinker discharge from the kiln drops onto the grate cooler for cooling from about 1350-1450 C to about one hundred twenty C.
- In the cooler, the amount of cooling air required for clinker cooling is extracted from the environment through extraordinary cooling lovers and fed into the cooler chambers and pressurized via the cooler plate and clinker bed.
- The cooled clinker discharges from the cooler into the pan conveyor and it's miles transported to the clinker garage.
- The clinker is taken from the clinker garage to cement ball mill hoppers for cement grinding.
- Part of the recent air extracted from the cooler is applied as a secondary and tertiary air for combustion in rotary kiln and combustion chamber, respectively.
Cement grinding and garage:
- Clinker and gypsum for OPC, limestone for limestone cement, and slag for slag cement are all extracted from their respective hoppers and fed to the cement turbines.
- The ball mill grinds the feed to a pleasant powder in chambers, specifically the primary and 2d chambers.
- The chambers have a positive amount of ball price of various sizes from 17mm to ninety mm.
- The mill discharge is fed to a bucket elevator which takes the fabric to a separator which separates pleasant and coarse product.
- The latter is dispatched to the mill inlet for regrinding and the very last product is saved in concrete silos.
Packing:
- Cement extracted from silos is conveyed to the automated digital packers wherein it's miles packed in 50 kg luggage and dispatched in vehicles.
Key takeaways
1. Fibers strengthened concrete can be beneficial in which excessive tensile power and decreased cracking are proper or whilst traditional reinforcement can not be placed.
2. The clays are excavated from open forged mines and loaded onto dumpers which shipping the substances and sell off into open backyard garage.
3. Geo polymer is the name given to the Daidovits in 1978 for items that appear in chains or networks or unusual molecules.
4. Geo polymer cement concrete is made using waste materials such as fly ash and ground granulated blast furnace slag (GGBS). An ash fly is a waste product produced from a hot power plant and the granulate blast soil in a furnace is processed as a metal waste.
Fiber Reinforced concrete:
- Fiber Reinforced Concrete is composite cloth which include fibrous cloth which will increase its structural integrity.
- It consists of combinations of cement, mortar or concrete and discontinuous, discrete, uniformly dispersed appropriate fibers.
- Fibers are normally utilized in concrete to govern cracking because of plastic shrinkage and to drying shrinkage.
- They additionally lessen the permeability of concrete and consequently lessen the bleeding of water.
Advantages of Fiber-strengthened concrete:
- Fibers strengthened concrete can be beneficial in which excessive tensile power and decreased cracking are proper or whilst traditional reinforcement cannot be placed.
- It improves the effect power of concrete, limits the crack boom and ends in a extra stress potential of the composite cloth.
- For commercial projects, macro-artificial fibers are used to enhance concrete’s sturdiness.
- Made from artificial substances, those fibers are lengthy and thick in length and can be used as a substitute for bar or material reinforcement.
- Adding fibers to the concrete will enhance its freeze-thaw resistance and assist maintain the concrete sturdy and appealing for prolonged periods.
- Improve blend cohesion, enhancing pump ability over lengthy distances.
- Increase resistance to plastic shrinkage in the course of curing.
- Minimizes metallic reinforcement requirements.
- Controls the crack widths tightly, consequently enhancing sturdiness.
- Reduces segregation and bleed-water.
- FRC, longevity is ready 10 to forty instances that of undeniable concrete.
- The addition of fibers will increase fatigue power.
- Fibers boom the shear potential of strengthened concrete beams.
Application of Fiber-strengthened concrete:
The programs of fiber strengthened concrete rely on the applicator and builder in taking gain of the static and dynamic traits of the cloth. Some of its vicinity of software is-
- Runway
- Aircraft Parking
- Pavements
- Tunnel Lining
- Slope Stabilization
- Thin Shell
- Walls
- Pipes
- Manholes
- Dams
- Hydraulic Structure
- Elevated decks
- Roads
- Bridges
- Warehouse floors
Fiber Types:
Fibers for concrete are to be had in exclusive sizes and shapes.
The essential elements affecting the function of fiber-strengthened concrete are a water-cement ratio, percent of fibers, diameter and duration of fibers.
Given beneath are exclusive varieties of fiber-strengthened concrete utilized in production.
Steel Fiber Reinforced Concrete:
- Steel fiber is a metallic reinforcement. A sure quantity of metallic fiber in concrete can motive qualitative modifications in concrete’s bodily property.
- It can significantly boom resistance to cracking, effect, fatigue, and bending, tenacity, sturdiness, and others.
- For enhancing lengthy-time period behavior, improving power, longevity, and strain resistance, SFRC is being utilized in systems which includes flooring, housing, precast, bridges, tunneling, heavy-responsibility pavement, and mining.
- The varieties of metallic fibers are described via way of means of ASTM A820 are, Type I: cold-drawn cord, Type II; reduce sheet, Type III: melt-extracted, Type IV: mill reduce and Type V: changed cold-drawn cord
Properties of Fiber Reinforced Concrete:
Compressive Strength:
- The presence of fibers might also additionally regulate the failure mode of cylinders; however, the fiber impact can be minor at the development of compressive power values (zero to fifteen percentage).
Modulus of Elasticity:
- Modulus of elasticity of FRC will increase slightly with a boom with inside the fibers content material.
- It became located that for every 1 percentage boom in fiber content material through quantity there may be a boom of three percentage withinside the modulus of elasticity.
Flexure:
- The flexural power became said [2j to be improved through 2. Five instances the usage of four percentage fibers.
Toughness:
- For FRC, sturdiness is set 10 to forty instances that of undeniable concrete.
Splitting Tensile Strength:
- The presence of three percentage fiber through quantity became said to boom the splitting tensile power of mortar approximately 2.5 instances that of the unreinforced one.
Fatigue Strength:
- The addition off bers will increase fatigue power of approximately ninety percentage and 70 percentage of the static power at 2 x 106 cycles for non-opposite and complete reversal of loading, respectively.
Impact Resistance:
- The effect power for fibrous concrete is typically five to ten instances that of undeniable concrete relying at the quantity of fiber
Corrosion of Steel Fibers:
- A lO-12 months’ publicity of steel fibrous mortar to out of doors weathering in an commercial surroundings confirmed no unfavourable impact at the power properties.
- Corrosion became located to be restricted best to fibers virtually uncovered at the surface.
- Steel fibrous mortar constantly immerse in seawater for 10 years exhibited a fifteen-percentage loss in comparison to forty percentage power lower of undeniable mortar.
Flexure:
- The use of fibers in bolstered concrete flexure contributors will increase ductility, tensile power, second ability, and stiffness.
- The fibers enhance crack manage and keep publish cracking structural integrity of contributors.
Torsion:
- The use of fiber do away with the unexpected failure feature of undeniable concrete beams.
- It will increase stiffness, torsion power, ductility, rotational ability, and the range of cracks with much less crack width.
Shear:
- Addition of fibers will increase shear ability of bolstered concrete beams as much as a hundred percentage.
- Addition of randomly allotted fibers will increase shear-friction power, the primary crack power, and final power.
Polymer concrete is an alternative to portland cement that is used to bond a mixture of aggregates together with epoxy binders. It is used in construction projects to provide added strength and can be modified with a range of resins. Polymer concrete provides very good resistance against corrosion and minimal chemical reactivity.
A polyester, vinyl resin or epoxy resin is often used to manufacture polymer concrete. This allows the concrete to be poured, then hardened. Polymer concrete cures through a chemical reaction with the polymer material. This type concrete is ideal for reaching areas that are not easily accessible.
Polymer concrete offers a range of benefits depending on the resin used to make it. Acrylic resins set quickly and offer resistance to harsh weather conditions, while epoxies create a strong material with little curing shrinkage. Furan resins can withstand high temperatures, and polyurea resins can replace formaldehydes or other hazardous compounds for construction purposes.
- Chemical admixtures are the components in concrete aside from port land cement, water, and combination which might be introduced to the combination at once earlier than or for the duration of blending.
- Producers use admixtures generally to lessen the value of concrete construction; to adjust the residences of hardened concrete; to make sure the best of concrete for the duration of blending, transporting, setting, and curing; and to conquer sure emergencies for the duration of concrete operations.
- Successful use of admixtures relies upon on using suitable techniques of batching and concreting.
- Most admixtures are provided in ready-to-use liquid shape and are introduced to the concrete on the plant or on the jobsite.
- Certain admixtures, along with pigments, expansive agents, and pumping aids are used most effective in extraordinarily small quantities and are commonly batched with the aid of using hand from premeasured containers.
- The effectiveness of an admixture relies upon on numerous elements including: kind and quantity of cement, water content material, blending time, stoop, and temperatures of the concrete and air.
- Sometimes, results much like the ones done thru the addition of admixtures may be done with the aid of using changing the concrete aggregate-decreasing the water-cement ratio, including extra cement, the usage of a extraordinary sort of cement, or converting the combination and combination gradation.
- Admixtures are classed consistent with characteristic. There are 5 wonderful lessons of chemical admixtures: air-entraining, water-decreasing, retarding, accelerating, and plasticizers (super plasticizers).
- All different styles of admixtures fall into the strong point class whose capabilities encompass corrosion inhibition, shrinkage reduction, alkali-silica reactivity reduction, workability enhancement, bonding, damp proofing, and coloring.
- Air-entraining admixtures, which can be used to purposely location microscopic air bubbles into the concrete, are mentioned extra completely in Air-Entrained Concrete.
- Water-decreasing admixtures commonly lessen the desired water content material for a concrete aggregate with the aid of using approximately five to ten percentage .
- Consequently, concrete containing a water-decreasing admixture wishes much less water to attain a required stoop than untreated concrete.
- The dealt with concrete could have a decrease water-cement ratio. This commonly shows that a better energy concrete may be produced without growing the quantity of cement.
- Recent improvements in admixture generation have caused the improvement of mid-variety water reducers.
- These admixtures lessen water content material with the aid of using as a minimum eight percentage and have a tendency to be extra solid over a much broader variety of temperatures.
- Mid-variety water reducers offer extra regular placing instances than popular water reducers.
- Retarding admixtures, which gradual the placing charge of concrete, are used to counteract the accelerating impact of warm climate on concrete placing.
- High temperatures frequently reason an accelerated charge of hardening which makes setting and completing difficult.
- Retarders maintain concrete manageable for the duration of placement and put off the preliminary set of concrete.
- Most retarders additionally characteristic as water reducers and can entrain a few air in concrete.
- Accelerating admixtures growth the charge of early energy improvement, lessen the time required for correct curing and protection, and accelerate the begin of completing operations.
- Accelerating admixtures are specifically beneficial for enhancing the residences of concrete in bloodless climate.
- Super plasticizers, additionally called plasticizers or excessive-variety water reducers (HRWR), lessen water content material with the aid of using 12 to 30 percentage and may be introduced to concrete with a low-to-ordinary stoop and water-cement ratio to make excessive-stoop flowing concrete.
- Flowing concrete is a extraordinarily fluid however manageable concrete that may be located with very little vibration or compaction.
- The impact of super plasticizers lasts most effective 30 to 60 minutes, relying at the emblem and dosage charge, and is observed with the aid of using a speedy loss in workability.
- As a end result of the stoop loss, super plasticizers are commonly introduced to concrete on the jobsite.
- Corrosion-inhibiting admixtures fall into the strong point admixture class and are used to gradual corrosion of reinforcing metal in concrete.
- Corrosion inhibitors may be used as a shielding method for concrete structures, along with marine facilities, motorway bridges, and parking garages, in order to be uncovered to excessive concentrations of chloride.
- Other strong point admixtures encompass shrinkage-decreasing admixtures and alkali-silica reactivity inhibitors.
- The shrinkage reducers are used to govern drying shrinkage and reduce cracking, even as ASR inhibitors manipulate sturdiness troubles related to alkali-silica reactivity.
Mechanism of Chemical Admixture:
- Concrete admixtures are used to steer concrete hardening specially with inside the early Phase of hydration.
- By including very small quantities of admixtures, homes of sparkling concrete may be inspired in a huge range.
- The hydraulic response may be elevated or retarded the use of suitable dealers and workability may be advanced the use of super plasticizers.
- Many mechanisms had been cautioned to provide an explanation for these kinds of effects .
- There continues to be no complete know-how of hydration mechanisms together with these kinds of phenomena at once.
- In this contribution emphasis will be positioned at power differences occuring at some point of physico-chemical methods of cement hydration.

Fig no 37. Mechanisms of plasticiser
- Cement hydration evolves in a manner which in corporate segment transitions.
- In touch with water, Meta stable stable cement stages dissolve into an aqueous solution.
- This dissociation ends in an boom of Ca O attention as much as 20-forty m mol/I with inside the first hours of C3S hydration .
- Reaching a country of super saturation with inside the pore water solution, crystallization into strong and stable CSH-merchandise can follow.
- In each segment transitions a unexpected quantity extrade occurs, as a consequence of adjustments in sure forces.
- During the solvation procedure a stable-fluid section transition results in an boom in quantity (swelling).
- Crystallization entails a quantity contraction (shrinkage) that is better in absolute phrases than the preceding quantity swelling.
- A shrinkage quantity stays after fluid-stable transition and may be measured volumetrically or gravimetrically.
- Both tactics engage simultaneously, however with unique velocities.
- Hydration may be visible as a solvation-crystallization step and become first defined via way of means of Le Chatelier.
Key takeaways
- Super plasticizers, additionally called plasticizers or excessive-variety water reducers (HRWR), lessen water content material with the aid of using 12 to 30 percentage and may be introduced to concrete with a low-to-ordinary stoop and water-cement ratio to make excessive-stoop flowing concrete.
- During the solvation procedure a stable-fluid section transition results in an boom in quantity (swelling).
Deterioration - Durability
- Durability is the capacity to remaining a long term without massive deterioration.
- A long lasting cloth allows the surroundings with the aid of using keeping sources and lowering wastes and the environmental affect of restore and substitute.
- The manufacturing of substitute constructing substances depletes herbal sources and may produce air and water pollution.
- Concrete resists weathering action, chemical attack, and abrasion even as retaining its favored engineering houses.
- Different concretes require extraordinary levels of sturdiness relying at the publicity surroundings and the houses favored.
- Concrete ingredients, their proportioning, interactions among them, setting and curing practices, and the provider surroundings decide the remaining sturdiness and lifestyles of the concrete.
- The layout provider lifestyles of maximum homes regularly 30 years, despite the fact that homes regularly remaining 50 to one hundred years or longer.
- Because in their sturdiness, maximum concrete and masonry homes are demolished because of useful obsolescence in place of deterioration.
- However, a concrete shell or shape may be repurposed if a constructing use or characteristic adjustments or whilst a constructing indoors is renovated.
- Concrete, as a structural cloth and because the constructing outside skin, has the capacity to face up to nature’s ordinary deteriorating mechanisms in addition to herbal disasters.
- Durability of concrete can be described because the capacity of concrete to withstand weathering action, chemical attack, and abrasion even as retaining its favored engineering houses.
- Different concretes require extraordinary levels of sturdiness relying at the publicity surroundings and houses favored.
- For example, concrete uncovered to tidal seawater could have extraordinary necessities than an indoor concrete floor.
Key takeaways
- Durability is the capacity to remaining a long term without massive deterioration.
- A long lasting cloth allows the surroundings with the aid of using keeping sources and lowering wastes and the environmental affect of restore and substitute.
Factor affecting the durability of concrete
The following are the factors that affect the strength of concrete.
- Cement content
- Aggregate quality
- Water Quality
- Concrete compaction
- Curing period
- Permeability
- Moisture
- Temperature
- Abrasion
- Carbonation
01. Cement content
- The amount of cement used in concrete mixing is a major factor affecting the durability of concrete.
- If the cement content used is less than required, the cement water level
- Decreases and the performance of concrete also decreases.
- Adding too much water to this concrete mix causes the formation of capillary voids that will make the concrete a resilient one inviting decay.
- Adding excess cement can cause problems such as stopping the shrinkage. Alkali-silica reactions may also eventually affect the strength of the concrete.
02. Aggregate Quality
- Applying a good quality mix to the concrete mix will definitely increase the strength of the concrete.
- The shape of the composite particles should be small and circular. Flaky and compact assembly can affect the performance of the new concrete making it easier to enter where it can open and will work with less power.
- Bad angular compilation is recommended but requires a lot of cement content to get a good binding. Yes, structural composites should be used to achieve greater concrete mixing.
- Determination of the combined moisture content should be done beforehand, otherwise, it can create a more usable concrete mix and make it worse.
03. Water Quality
- The water used in the concrete mix also affects the strength of the concrete. Usually, drinking water is recommended to make concrete. The pH of the water used will be in grades 7 to 8 only.
- Water should be free and clean from fats, acids, alkalis, sugar, organic salts etc.
- Contamination in the water can lead to metal corrosion or corrosion due to different chemical attacks of concrete.
04. Concrete compaction
- Care should be taken during the installation of the concrete. It is important to glue the local concrete without splitting.
- Adequately compacted concrete contains a number of air gaps in it that reduce the strength of the concrete and its strength and will make it stronger.
05. Curing period
- Proper treatment should be done in the early stages of concrete reinforcement as it will lead to the reinforcement of the concrete.
- Adequate treatment can lead to the formation of cracks due to plastic shrinkage, dehydration, heat effects etc. due to reduced stiffness.
06. Permeability
- Due to the overcrowding of the concrete, it expands and leads to the formation of cracks and eventually, the deterioration of the concrete occurs.
- Concrete usually consists of small gel pores and capillary cavities. However, gel pores prevent water ingress because they are too small.
- Capillary holes in concrete are facing, which are formed due to the high water content of concrete
- To prevent intrusion, a very small amount of cement water should be used.
- Using a small amount of pozzolanic material also helps to reduce penetration
07. Moisture
- The moisture found in the atmosphere will also affect the strength of concrete structures.
- Concrete moisture is responsible for Efflorescence, which will convert salt into soluble solutions and when evaporated salt becomes brighter and appears on the concrete surface.
- This will definitely damage the concrete structure and the durability will decrease.
08. Temperature
- When new concrete is exposed to high temperatures, the hydration level is affected and strength and durability are reduced.
- Concrete materials have different temperature coefficients, so at higher temperatures, spelling and damage to concrete are possible.
09. Abrasion
- Concrete damage also occurs due to severe facial injuries.
- When concrete is exposed to fast-moving water, steel tires, floating ice that wears continuously on the surface occur and stiffness is affected.
- The higher the pressure of the concrete pressure the higher it will be to resist the abrasion
10. Carbonation
- When wet concrete is exposed to the atmosphere, carbon dioxide in the atmosphere reacts with concrete and reduces the pH of the concrete by reacting with CaO in concrete.
- When the pH value of concrete is reduced to 10 or 9 or more, it releases its alkali. Because it will not be able to protect the metal bars beneath it. Due to rust, rust will build up around the bar which has led to an increase in the volume of the bar. This will create cracks in the concrete. Cracking will continue to promote moisture and CO2 which will lead to the loss of alkali. So bad cycles occur, eventually causing the concrete to crack with delamination and spraying of the concrete if not done in time, the bars will start to lose their place and thus become stronger. Most of the building in modern times, suffers from this, and buildings that were supposed to be 100 years old have been extensively renovated at some point within ten years. The process of rust therefore places on the existing strength of the concrete. The rust of the reinforcement causes cracks in the solid concrete and deterioration occurs.
Key takeaways
The following are the factors that affect the strength of concrete.
- Cement content
- Aggregate quality
- Water Quality
- Concrete compaction
- Curing period
- Permeability
- Moisture
- Temperature
- Abrasion
- Carbonation
Permeability
- Definition: the capacity of a given concrete to allow drinks or gases to by skip through.- ACI Concrete Terminology
- Permeability is a degree of the quantity of water, air, and different materials which could input the concrete matrix.
- Concrete consists of pores which could permit those materials to go into or depart.
- Permeability of concrete may be a number one motive for concrete deterioration because of reinforcing metal corrosion and different deterioration mechanisms.
- On a macro scale, permeability additionally refers to “porous” slabs used to empty pavements, sidewalks, and parking regions of water, putting off the want for drainage slope, systems, and piping.
- This technology—every now and then called “no-fines concrete”—is gaining reputation once more with the preference to lessen floor run-off from pavements, sidewalks, and parking regions.
- Permeability of cement mortar or concrete is of unique importance in systems which might be meant to hold water or which come into touch with water.
- Besides useful considerations, permeability is likewise in detail associated with the sturdiness of concrete, mainly its resistance, towards revolutionary deterioration below publicity to extreme climate, and leaching because of extended seepage of water, specially whilst it consists of competitive gases or minerals in solution.
- The willpower of the permeability traits of mortar and concrete, therefore, assumes widespread importance.
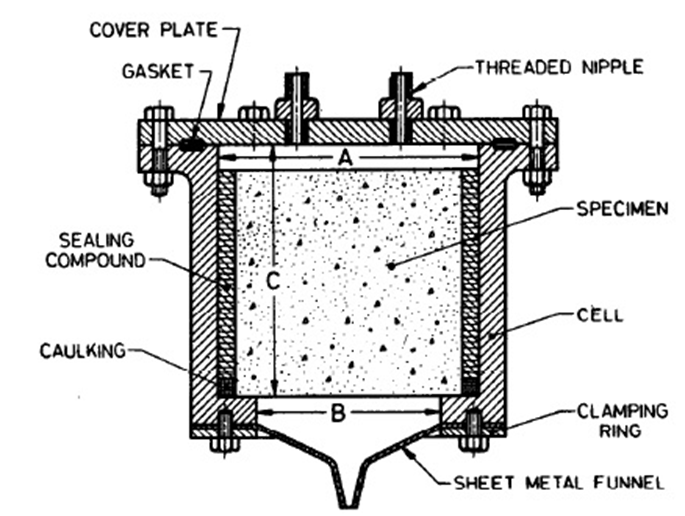
Fig no 38. Concrete permeability apparatus
- The permeability shall encompass a steel cylinder for containing the specimen.
- A rubber or neoprene O-ring or different appropriate gasket, seated in matching grooves will be used among the quilt plate to render the joint water-tight.
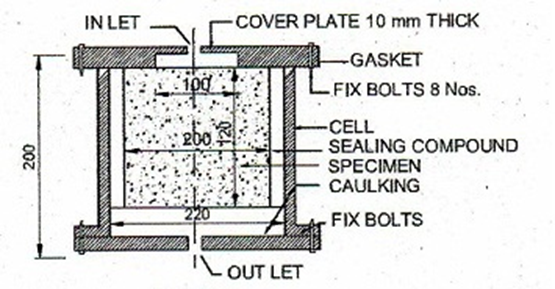
Fig no 39. Water Reservoir in Permeability Apparatus
- A appropriate reservoir may also encompass a duration of steel pipe, 50 to a hundred mm in diameter and approximately 500 mm long.
- The reservoir will be equipped with a graduated facet arm gauge-glass, and the vital fittings and valves for admitting water and compressed air and for draining, bleeding and connection to the permeability.
Procedure:
Preparation of Test Specimen
- Test specimen of 2 hundred mm diameter and a hundred and twenty mm thick will be used. After 24 hrs of casting of specimen, crucial round place of a hundred mm diameter will be roughened with a twine brush at the facet on which the water stress is to be carried out. The un roughened a part of the facet of the check specimen that's subjected to water stress is to be sealed with coats of cement water paste (W/C = 0.4).
Test Procedure
- After 28 days curing, check specimen is equipped right into a check equipment in which the water stress acts on the specified face and final faces may be observed.
- At first, a stress of one Bar is carried out for forty eight hours, then three bar for twenty-four hours and seven Bar for twenty-four hours.
- After the check, the specimen is break up with inside the center with the aid of using the compression carried out on spherical metal bars mendacity on contrary sides, above and below. The facet after the check specimen uncovered to the water stress ought to face downwards.
Observation:
- The finest water penetration depth, is taken because the common cost of the finest penetration depths on 3 check specimen.
Key takeaways
1. A rubber or neoprene O-ring or different appropriate gasket, seated in matching grooves will be used among the quilt plate to render the joint water-tight.
Chloride Attack
- Chloride Attack Chloride attack is one of the most important factors when working with concrete strength. It mainly causes corrosion. Statistics have shown that more than 40% of structural failures are due to metal corrosion.
- Concrete and the penetration layer with a strong alkaline Ca (OH) 2 (pH approximately 13) prevents metal corrosion by forming a thin film to protect the iron oxide on the surface of the metal.
- This protection is known as inaction. If concrete can penetrate in such a way that the dissolved chloride enters until it hardens and water and oxygen are also present, then corrosion of the metal will occur. This layer can also be lost due to carbonation.
- Chloride enters the concrete from cement, water, and is sometimes mixed from tips. This can come in increments from nature when the concrete is filled. The Bureau of Indian Standard specified the high chloride content in cement as 0.1%.
- The amount of chloride needed to start corrosion depends on the pH value of the pore water in the concrete. A pH value below11.5 corrosion is possible without the presence of chloride.
Key takeaways
- Chloride Attack Chloride attack is one of the most important factors when working with concrete strength. It mainly causes corrosion corrosion. Statistics have shown that more than 40% of structural failures are due to metal corrosion.
- Concrete and the penetration layer with a strong alkaline Ca (OH) 2 (pH approximately 13) prevents metal corrosion by forming a thin film to protect the iron oxide on the surface of the metal.
Corrosion of Reinforcement, Carbonation of Concrete
Corrosion of Reinforcement
- Concrete, in itself, has a low strength. To increase the strength of the concrete, the steel hardens. Steel bars are inserted inside the weight of the concrete. These steel bearings carry a high load-bearing capacity applied to concrete.
- Concrete makes metal bars obsolete due to the alkaline environment, thus preventing them from cracking. However, for a variety of reasons, metal bars can be pulled longer. And as a result of the rust of the steel bars, various weaknesses appear in the concrete structure, which could eventually collapse if not properly maintained.
- The rust of steel reinforcement bars is actually a way of responding to electricity. Small anodes and cathodes are formed and the flow of ions between these two electrodes leads to the breakdown of metal bars. There are two types of corrosion detected in steel reinforcement bars:
- Metal Rust - In small cracks in a concrete structure, solutions may remain. Anodes and cathodes can be formed within solutions due to the uneven reaction of solute ions over the volume of the solution. The flow of ions is caused by these electrodes, thus causing a gradual corrosion.
- Rust corrosion - Related to the removal of small areas in the steel bars of the reinforcement. This type of rust is extremely well-formed and small holes or holes are made in the metal.
Causes of Stainless-Steel Rust
- Corruption of steel reinforcement barriers may be due to the local failure of the metal film of chloride ions or the general failure of the concrete to malfunction due to the carbon dioxide reaction from the atmosphere. The main factors facing corrosion of reinforcement barriers are:
- Loss of alkalinity due to carbonation - When a metal surface is left unprotected in the atmosphere, corrosion begins to form on the surface of the metal and then slowly moves away.
- Loss of alkalinity due to chlorides - Chloride ions tend to remove metal energy by destroying concrete.
- Cracking of Concrete - Cracking can expose metal bars in the atmosphere and increase liquidity.
- Moisture Methods - Regular wetting of concrete can lead to water reaching the metal bars by dispersing through the pore structure of the concrete or existing cracks in the concrete. Rust of steel bars follows after that.
- Insufficient cover: Insufficient size of concrete cover.
- Metal Rust due to Improper Cover
- Damaged steel reinforcement may occur due to insufficient concrete cover
Effects of Stainless-Steel Rust
When steel bars begin to break, reinforced concrete joints begin to break down through the following stages:
- White spot formation - Atmospheric carbon dioxide reacts with calcium hydroxide present in the reduction of cement forming calcium carbonate. This calcium carbonate is treated with moisture and deposited on the surface of the white-formed concrete.
- Dirty stains by reinforcement - When the metal bars begin to deteriorate, a layer of iron oxide forms in it. This metal oxide is also transferred to the surface of the concrete with moisture.
- Formations of cracks - Rust products take on a larger volume than the original. So they put pressure on the concrete and it cracks. In the event of a lot of rust, many wide cracks are formed.
- Disintegration of concrete cover - Due to the loss of bond between concrete and steel, concrete begins to form many layers of scales and then peels off. Metal bars are also reduced in size.
- Cracking of bars - Due to the decrease in the size of the steel bars, they eventually break. Also, there is a significant reduction in the size of the main bars.
- Piercing of bars - The collapse of the concrete cover and the cracking of the bars resulted in the collapse of the main bars. This floods the concrete area and eventually the entire building collapses.
How to Avoid Rusting Metal Rust
- The rust of steel reinforcement bars can be prevented or at least delayed by good measures. Also, damaged steel bars can be repaired and the concrete structure can be properly restored. Some steps are given below:
- Providing Sufficient Concrete Cover: A good amount of concrete cover should be provided in addition to the reinforcing steel bars. This ensures proper care of the alkaline type inside the concrete and the passage of the steel bars. Metal bars should be placed precisely in place
- Use of Quality Concrete: High quality concrete should be used. It helps to maintain an alkaline environment. In concrete, a water level of 0.4 or less should be maintained. Too much water can damage metal bars
- Compact Compaction fo Concrete: Concrete must be thoroughly mixed so that no air gaps or pockets are present.
- Use of FBE Bonds: Fusion Bonded Epoxy Coating (FBEC) can be used on metal bales to prevent corrosion. Epoxy powder is still electrically distributed in metal barns. The powder melts and flows over the bars as it heats up, forming a protective coating. It is a thermoset polymer coating because the use of heat will not melt the wear. Apart from the rebar it also has extensive function in pipeline construction
- Use of Cement-Based Polymers: Cement-based polymers can be used in concrete to increase their protection against corrosion. Cement-based polymers act as a bond in concrete. They also increase the strength, durability and melting of concrete
Carbonation of Concrete
- Carbonation of concrete is associated with corrosion of steel reinforcement and shrinkage. However, it also increases both the compression strength and the strength of the concrete, so not all of its effects on concrete are bad.
- Carbonation is the result of the decomposition of CO2 in pore fluid in concrete and this reacts with calcium from calcium hydroxide and calcium silicate hydrate to form calcite (CaCO3). Aragonite can form in hot climates.
- Within a few hours, or a day or two in total, the new concrete will be processed by CO2 in the air. Gradually, the process penetrates deeper into the concrete at a rate equal to the square root of time. After a year or more it is likely to reach a depth of about 1 mm with dense low-penetration concrete made of low water / cement, or up to 5 mm or more of high-density and permitted concrete using high water / cement scale.
Carbonation determination
- The affected depth from the concrete surface can be easily indicated by the use of a phenolphthalein indicator solution. This is available from chemical suppliers. Phenolphthalein is a white or pale yellow with a crystal. Use as a solvent dissolve in a suitable solution such as isopropyl alcohol (isopropanol) by 1%.
- The indicator has not changed color near the upper and lower extremities, suggesting that these regions near the surface be carbonated at a depth of at least 4 mm from the top to the top and 6 mm from the bottom.
- When the index turns purple - in the middle of the slide - the pH of the pore fluid anchor remains high (above 8.6, about 10). Whether you are pasting the cement here is not completely illuminated, despite the strong purple color; a complete test will require very little testing.
- The index was not applied to the concrete to the right of this image so the concrete here retains its original color.
- The depth of carbonation is about the same as the square root of time. For example, if the depth of carbon is 1mm in one-year-old concrete, it will be about 3mm after 9, 5mm after 25 years and 10mm after 100 years.
Key takeaways
- Carbonation of concrete is associated with corrosion of steel reinforcement and shrinkage. However, it also increases both the compression strength and the strength of the concrete, so not all of its effects on concrete are bad.
- Concrete, in itself, has a low strength. To increase the strength of the concrete, the steel hardens. Steel bars are inserted inside the weight of the concrete. These steel bearings carry a high load-bearing capacity applied to concrete.
- Concrete makes metal bars obsolete due to the alkaline environment, thus preventing them from cracking. However, for a variety of reasons, metal bars can be pulled longer. And as a result of the rust of the steel bars, various weaknesses appear in the concrete structure, which could eventually collapse if not properly maintained.
Repair - Symptoms and Diagnosis of Distress
- The rapid industrialization of India after independence required the transportation of goods and services and led to the construction of a network of wide roads with built-in bridges and flyovers.
- Many of the existing bridges show signs of stress within their work life built in many cases in the 10-20 years of construction in India and many other countries.
- The collapse of the I-35W bridge over the Mississippi River in the United States of America in August 2007 has attracted the attention of international media. In India, the collapse of the Mandovi Bridge in Goa in 1986 (after 16 years of service) and the great tribulation at the Zuari bridge (rebuilt in 2000 by an international consultant) in Goa and many other bridges such as Khalghat and Borad Bridge on NH3 (Route) Agra to Mumbai) due to environmental constraints is attracting the attention of transport authorities and the scientific community to transform the operational bridge management system.
- The cause of the distress, the level of grief and the reduction in the capacity of the bridge can be ensured in order to further the necessary adjustments to ensure the safety of the bridge during their operation.
- An assessment of the pressure and load capacity of existing bridges and to improve the load capacity is required while upgrading highways. India has already implemented the consolidation and use of four 7000 Km of highways under the Golden Quadrilateral program where the strengthening / replacement of many existing bridges was required.
- Various causes of damage to reinforced concrete bridges are low construction standards, rust of steel on reinforced concrete bridges and pre-reinforced concrete bridges, improper shape and details of normal loads and seismic forces, improper operation of bearings etc. a number of case studies have been reported in the literature on reinforced concrete damage and compacted concrete bridges during earthquakes and the reinforcement of reinforced and compressed concrete bridges due to nature and other loads.
- A concerted effort has been made to review critical documentation of reinforced concrete damage and pre-pressure concrete bridges and repair / rehabilitation strategies based on information from bridge reconstruction projects in which the authors were involved.
Causes of distress
- Relationship problems such as conflicts, illness / death of a loved one, divorce, abuse, partner, etc.
- Financial difficulties
- Environmental remediation
- Educational difficulties
- Time management and organizational complexity
- Anxiety
- Depression
- An abusive event
- Drug abuse
Diagnosis of distress
Sometimes the cause of grief is known e.g. Suffering during an earthquake, impact and explosion is known perhaps the active load exceeds the intended load but it is often difficult to find the real cause of grief where many variables are affected e.g. Poor construction quality (faulty details, faults and performance), shrinkage, penetration, rust consolidation etc. Following a test may be necessary to determine the cause and degree of grief.
- Determination of compression strength from NDT and cores of concrete
- Strategies for detecting explosions
- Signature / Vibration Analysis
- Download tests to find deviations / issues and distribute the load
- Rust studies (pH, depth of carbon, chloride)
- Deviation / disposal slopes from Instrumented Bridge
Key takeaways
- The rapid industrialization of India after independence required the transportation of goods and services and led to the construction of a network of wide roads with built-in bridges and flyovers.
- Many of the existing bridges show signs of stress within their work life built in many cases in the 10-20 years of construction in India and many other countries.
Selection Of Repair Procedure
Structure
- Structural repairs include using epoxy frames to bind or bond concrete together. Epoxy repair not only repairs the sealing cracks but also restores the strength and durability of the concrete. Use epoxy to repair dormant cracks only. Fixing functional cracks with epoxy often leads to a new formation near the original, epoxied fragment.
- Epoxy injection is a common way to inject epoxy into cracks, especially in direct and indirect areas. But gravity filling works well and is a common way to apply epoxy to flatwork cracks or to direct surfaces.
- The filling of gravity consists of pouring low-viscosity epoxy into the cracks that have been signed or distributed and allowed the gravitational force to pull the epoxy down the cracks. Viscosity resistance to fluid flow is measured in centipoises (cps). Decreased viscosity value, less (runnier) significant. Grade I and II epoxies have viscosities of less than 20 cps and between 20 and 100 cps, respectively.
- For comparison, the viscosities of other common beverages are: water - 1 cps, milk - 3 cps, anti-freeze - 15 cps, maple syrup - 150 to 200 cps, and honey -3000 cps. Low viscosities are required for solid cracks. Otherwise, the repair material will be too large to penetrate and flow into the crack.
- Epoxies were cured or hardened due to the chemical reaction between the frame and the hardener. Chemical reactions are rapid at high temperatures. Epoxies are obtained by different injections or by temperature treatments so chemical reactions are less rapid or slow (Type A, less than 40º F; Type B, 40º F to 60º F; and type C, more than 60º F).
- With the adjustment of gravity filling culture, consider the depth and depth, epoxy viscosity, and temperature input when choosing the distance and type of epoxy. Otherwise, the epoxy can be very strong or very hard to penetrate or it can just run between the river and the pool under the slide.
Sealing and filling
- Sealing and filling of non-construction repairs. However, some repair materials include cracked surfaces and can have a strong impact that can cause cracking of the material and concrete in the event of a major crack movement.
- Typical sealants and internal fixing fillers include semi-rigid epoxies, hybrid polyurethanes and polyureas, and polymer mortar. Polyurethanes and silicones are common labels used for exterior repairs.
- Usually, sealants are flexible or elastomeric materials; and the fillers are very hard so the fixing materials support the edges of the cracks to avoid collapse or damage under load. When heavy traffic is exposed to heavy wheels, composite fillers or special cracks with about 80 Shore A Hardness should be used.
- Unfortunately, there is a trade-off to increase the complexity of explosive repair materials. As the repair material gets harder, it becomes much thinner and does not tolerate cracked movement. For example, semi-rigid epoxies usually have a hardness of about 90 and an extension value of 50%; whereas, silicone sealants have a hardness of about 5 and an extension value of 1400%. Therefore, when choosing a fix, consider the expected movement of the comparison and the need to support the edges of the cracks.
- For effective cracking with the expected cracking motion, use elastomeric sealants or sealants with sufficient elastic properties, to see that the trade-off will be a little support for the fracture edges. For cracks exposed to heavy-duty traffic, use hard materials that support the edges of the cracks. But understand that these things do not tolerate the movement of cracks.
- If you are using elastomeric sealants in active cracks, always seal the sealant with a saw or by moving the track as recommended by the repairman. Without a dam, there would not be enough to tolerate future fracture movements. Expansion structures reported by manufacturers are based on the size of the recommended lakes or, in particular, the width and depth of the dam.
- Of course, cutting or scraping increases the width of the crack and makes crack repairs more noticeable. For cosmetic repairs in colored or decorative flats where cracks lie or are well established, do not see or move the sealant or filler dam. Instead, choose a low viscosity cracker (less than 100 cps) and small injection tips for cracks to fill gravity.
- Dams are not required. But in the event of a fracture movement, the cracking of the repair material or concrete may occur due to the small diameter of the depth of the material. Also, manufacturers now offer many of these low viscosity fixes in a variety of colors or offer color production recommendations and textures similar to concrete concrete surfaces.
- Before fixing your next explosion, do a crack test and establish repair targets. Decide what kind of adjustment is needed. Options include structural repairs using epoxy, route fixes and seal applications using flexible sealant to hold future cracks, and solid or durable repairs that fill the edges of cracks, with or without. Also, set cosmetic requirements. After selecting the fix and procedure, follow the manufacturer's recommendations.
Key takeaways
- Structure
Structural repairs include using epoxy frames to bind or bond concrete together. Epoxy repair not only repairs the sealing cracks but also restores the strength and durability of the concrete. Use epoxy to repair dormant cracks only. Fixing functional cracks with epoxy often leads to a new formation near the original, epoxied fragment.
2. Sealing and filling
Sealing and filling of non-construction repairs. However, some repair materials include cracked surfaces and can have a strong impact that can cause cracking of the material and concrete in the event of a major crack movement.
Repair of defects using various type and techniques - shortcrete and grouting
Shortcrete
- Shotcrete or sprayed concrete is concrete or mortar conveyed thru a hose and pneumatically projected at excessive pace onto a floor, as a production method, first utilized in 1914.
- It is usually strengthened with the aid of using traditional metallic rods, metallic mesh, or fibers.
- Properly carried out shotcrete is a structurally sound and sturdy production cloth which well-known shows terrific bonding traits to present concrete, rock, metallic, and plenty of different materials.
- It may have excessive strength, low absorption, correct resistance to weathering, and resistance to a few varieties of chemical attack.
- Many of the bodily residences of sound shotcrete are similar or advanced to the ones of traditional concrete or mortar having the equal composition.
- Improperly carried out shotcrete can also additionally create situations a lot worse than the untreated condition.
Advantages of shotcrete:
- Shotcrete is utilized in lieu of traditional concrete, in maximum instances, for motives of fee or convenience.
- Shotcrete is fine in conditions whilst formwork is fee prohibitive or impractical and wherein paperwork may be decreased or eliminated, get entry to to the paintings place is difficult, skinny layers or variable thicknesses are required, or ordinary casting strategies cannot be employed.
- Additional financial savings are feasible due to the fact shotcrete calls for handiest a small, transportable plant for manufacture and placement.
- Shotcreting operations can regularly be executed in regions of restrained get entry to to make upkeep to structures.
Grouting
- Grout is usually a mixture of cement, sand, and water or chemicals used to fill gaps.
- They are used to repair concrete cracks, to fill gaps and gaps in tiles, to fill gaps and waterproofing, and to strengthen the soil.
- It is also used to provide additional power to load-bearing structures. It basically involves the process of injecting something that can be pumped into a building to change its body structures.
- There are different types of grinding, cement grinding, chemical grinding, and bituminous grating, depending on the material used.
- Frames are also sometimes used as grout materials. A mortar is often used to fill cracks and gaps in soil or rock.
What is Grouting
- Also, it is used to stabilize the soil and keep it out.
- Cracking is used for a variety of purposes such as water repair, standing on immersed structures such as ditches, tunnels, etc., filling in the gaps between tiles and stabilizing the soil.
- Here we have provided details on the type of grouts used to repair cracks.
Advantage of Grouting Includes:
- This can be done in almost any soil condition
- It does not vibrate and can be controlled to avoid structural damage
- Development of underground structures can be measured
- It is very useful for limited space and low head items
- It is used to install slab jacking that lifts or measures the crippled foundation
- It can be installed near existing walls
- It can be used to control the flow of water, groundwater flow, and hazardous waste materials.
Many Different Types of Grouting Materials:
- Stopping cement
- Chemical Grouting
- Bentonite grouting
- The amber is growing
- Bituminous Grouting
Key takeaways
- SHORTCRETE
Shotcrete or sprayed concrete is concrete or mortar conveyed thru a hose and pneumatically projected at excessive pace onto a floor, as a production method, first utilized in 1914. It is usually strengthened with the aid of using traditional metallic rods, metallic mesh, or fibers.
2. GROUTING
Grout is usually a mixture of cement, sand, and water or chemicals used to fill gaps. They are used to repair concrete cracks, to fill gaps and gaps in tiles, to fill gaps and waterproofing, and to strengthen the soil.
Introduction of retrofitting of Concrete Structure by Fiber Reinforced Polymer (FPP), Polymer Impregnated Concrete
Fiber Reinforced Polymer
- Fiber-reinforced polymer (FRP), also fiber-reinforced plastic, is a composite made of polymer matrix reinforced with fibers. Threads are usually glass, carbon, or aramid, although other fibers such as paper or wood or asbestos have sometimes been used. The polymer is usually epoxy, vinylester or polyester thermosetting plastic, and phenol formaldehyde frames are still active. FRPs are widely used in the aerospace, automotive, marine and construction industries.
- Composite materials are made of building materials or naturally made from two or more materials that have a structure with very different physical or chemical properties that are always different and distinct from the finished structure. Most compounds have strong, strong fibers in a weak and strong matrix. The goal is usually to make the part stronger and stronger, usually with a lower volume.
- Commercial materials usually contain glass or carbon fibers in a matrix based on thermosetting polymers, such as epoxy or polyester resins. In some cases, thermoplastic polymers may be preferred, as they form after the first production. There are additional stages of integration where the matrix is metal or ceramic. For the most part, these are still in the development phase, and the problems of high production costs have yet to be overcome [1]. Moreover, in these compounds the reasons for adding fibers (or, in some cases, particles) are often complex; for example, improvements may be required in penetration, wear, cracking, heat stabilization, etc.
- Fiber-reinforced polymer (FRP) is a compound used in almost every type of high-tech engineering facility, with its use from aircraft, helicopters and spacecraft to boats, ships and marine systems as well as automobiles, sports equipment, repair equipment chemicals and public infrastructure such as bridges and buildings.
- The use of FRP compounds continues to grow at an impressive rate as these materials are widely used in their existing markets and are being developed in brand new markets such as biomedical devices and social structures. An important factor contributing to the increased use of compounds over the years has been the development of new types of FRP materials.
- This includes the development of high-resin applications and new reinforcement styles, such as carbon nanotubes and nanoparticles. The book provides a timely account of fiction, mechanical properties, delamination resistance, impact tolerance and the use of 3D FRP compounds.
- Polymers reinforced polymer composites (FRPs) are increasingly being considered for the development and / or replacement of structural components or systems consisting of traditional engineering materials, namely concrete and steel. FRP compounds are simple, non-destructive, show a certain high strength and direct durability, are easily constructed, and can be customized to meet operational requirements.
- Because of these beneficial features, FRP compounds have been incorporated into the construction and renovation of buildings using their reinforcement in concrete, blocks, modular structures, formwork, and external reinforcement for seismic reinforcement and development.
- The effectiveness of Fiber Reinforced Polymer (FRP) reinforcement in concrete structures such as replacement of steel bars or pre-pressurized muscles has been extensively studied in many research laboratories and professional organizations around the world. FRP reinforcement offers many benefits such as corrosion resistance, non-magnetic properties, very strong, lightweight and easy to handle.
- However, they usually have a direct response to stiffness to the point of failure (defined as damaging failure) and poor resistance to friction or shear. They are also less resistant to fire and when exposed to high temperatures. They release vital energy as they bend, and they are sensitive to the effects of pressure fractures. In addition, their cost, whether considered for each weight or on the basis of strength-bearing capacity, is relatively high compared with conventional steel reinforcement bars or pressure straps.
- From a structural engineering perspective, the most serious problems with FRP reinforcement are the lack of plastic conduct and very low shear strength on the short side. Such features can lead to premature tender fragmentation, especially if mixed results are obtained, such as in shear-breaking planes on reinforced concrete pillars where there is a delow action. The downtime action reduces the remaining resistance to stiffness and shear tenderness.
- Solutions and limitations for use are provided and further improvements are expected in the future. The cost of FRP consolidation unit is expected to decrease significantly with increasing market share and demand. However, even today, there are applications where FRP consolidation is less expensive and justified. Such cases include the use of FRP sheets or bonded plates in repairing and strengthening concrete structures, as well as the use of FRP meshes or fabrics or fabrics in small cement products.
- The cost of renovating and renovating a building remains, in certain terms, much higher than the cost of the original building. Repairs usually require a small amount of repair materials but a high commitment from staff. In addition, labor costs in developed countries are so high that the cost of materials is secondary. So the performance and performance that lasts the longest, the repair is very expensive. This means that the cost of materials is not a problem to be rectified and the fact that FRP materials are expensive is not a particular problem [5].
- Given only the physical strength and resources, at the top, the controversy over FRP compounds in a sustainable built environment is questionable. However, such a conclusion needs to be evaluated in terms of the potential benefits of using FRP compounds related to assumptions such as:
- High power
- Light weight
- High performance
- It lasts a long time
- Renovating existing buildings and extending their life
- Seismic development
- Security systems
- Space programs
- Ocean areas
o. In the case of FRP compounds, environmental concerns appear to be a barrier to its functioning as a viable alternative especially in terms of fuel depletion, air pollution, fog, and acidification associated with its production. In addition, the ability to reuse FRP compounds is limited and, unlike steel and wood, structural components cannot be reused to perform the same function in another structure. However, examining the environmental impact of FRP compounds on infrastructure use, especially through life cycle analysis, may reveal more direct and indirect benefits that compete more than conventional ones.
p. The composite material has greatly improved since its inception. However, before composite materials can be used as an alternative to conventional materials as part of a sustainable environment a few needs remain.
q. Availability of durability data for FRP building materials.
r. Integration of robust data and service life prediction methods for building members using FRP combinations.
s. Development of selection methods according to the life cycle cycle of materials and systems.
t. Finally, in order for the mixtures to be considered a viable option, they must be structurally and economically viable. Many studies on the structure of the composite material are widely available in the literature.
u. However, limited studies are available on the economic and environmental availability of these items from the perspective of the life cycle, because short-term data are available or only economic costs are considered in comparison. In addition, the long-term impact of using composite materials needs to be determined.
v. The products produced, the sustainability of the materials, and the capacity to recycle the materials need to be tested to determine if the composite materials can be part of a sustainable environment. So in this chapter describe the physicochemical properties of polymers and compounds most commonly used in Civil Engineering. The theme will be presented in a simple and basic way for better understanding.
Polymer Impregnated Concrete
- In the case of pregnant polymer concrete, prepolymers or lower liquid monomers are partially or partially impregnated with a pore system of a composite cement framework. After this process, the entire treated structure is allowed to polish.
- The general process of treatment of reinforced concrete leads to the acquisition of a large amount of free water in its spaces. These water-filled voids form a significant amount of total volume. From 5% in the case of dense concrete and 15% in the case of gaped concrete.
- In the case of pregnant polymer concrete, it is these voids (holes filled with water) that should be filled with the selected polymer. So the main thing that affects the loading of the monomer is this: the moisture content in the solid concrete and the air loses energy in the concrete.
Procedure for polymer impregnated concrete manufacturing
The activities involved in the pregnancy process to improve pregnant polymer concrete are:
1. Well-constructed concrete is available. They need to get better and get stronger.
2. Moisture is removed by drying the concrete. Drying is done by heating the structure element at temperatures above the order of 120 to 150 degrees Celsius. An air oven can be used to dry small specimens.
If the element has a large surface, a thick cloth, say, 10mm thick, can be used to protect it from any hot gradient. Another complex application is the use of infrared heaters.
Complete removal of moisture from concrete, requires 6 to 8 hours of heat.
3. After complete removal, the concrete area has cooled to a safer level. This can go up to a temperature of 35 degrees Celsius. This heat will avoid overheating.
4. The concrete is now transferred to a vacuum cleaner, where all the air inside the concrete structure is removed. The amount of monomer installed will determine the time and level of use of the machine.
5. Concrete after sufficient ventilation is placed in a monomer solution. Wet for a long time until the desired depth of monomer penetration is obtained.
Filling time depends on the viscosity of the monomer, the adjustment of the template and the advanced characteristics of the concrete.
To reduce the time taken to get the desired input, it is preferable to use external pressure such as air or nitrogen gas. This helps to get in faster.
6. After the above procedure, the surface is covered with plastic paper. This helps prevent the evaporation of the monomer.
7. A high-temperature polymerization method is performed. This method involves polymerization by heating the deformed monomer to the required temperature. This will start from 60 degrees to 150 degrees Celsius. The selected temperature range depends on the type of monomer.
Heating can be done under water or with a low pressure steam injection, or with infrared heaters or an air oven. The heat decomposes the catalyst and thus initiates the polymerization reaction.
Once the monomer has penetrated the concrete, polymerization can also be initiated using ionization radiation similar to gamma rays. Polymers when they are completely polymer or when connected on the other side, act as solids that reside in the voids they are embedded in.
8. The concrete structure is then allowed to cool.
Every process from 1 to 8 can only be done in a precast factory. Monomers such as acrylate, styrene and vinyl chloride etc. are widely used for concrete installations. Another widely used material is Methyl Methacrylate (MMA).
Properties of polymer impregnated concrete
1. The polymer concrete gains the strength of the cube to strengthen more than 100N / mm2. This strength does not depend on the strength of the standard concrete.
2. The flexibility of a pregnant polymer concrete is approximately 15N / mm2. This is slightly higher than high-grade clear concrete made from common ingredients.
3. The elastic modulus lies in the range from 30 to 60N / mm2. This value is the same as the value obtained from high-strength concrete (e.g. Approximately 45N / mm2)
4. Pregnant polymer concrete has less movement problems and shrinkage due to the small number of pores.
5. Pregnant polymer concrete is more resistant to acid attacks, sulfate attacks and chloride attacks compared to PCC.
Application of polymer impregnated concrete
The use of pregnant polymer concrete in various construction sites is described below:
1. Surface Impregnation of Bridge Decks: Bridge decks are allowed to be installed to avoid the ingress of moisture, chemicals and chloride ions.
Bridge floors built in areas with high salt water and moisture exposure can be protected in this way.
2. Structural repairs: Damaged structures can be developed in the form of a polymer abstract. The life span of undeveloped buildings can be extended in this way.
This method is why it helps in the restoration and preservation of stone monuments.
3. Underwater and Marine Applications: Polymer impregnation capabilities help to improve structures, water absorption, and non-concrete structures. This makes them widely used in water and sea construction.
Buildings built on desalination plants and underwater structures use this method of building concrete. It has been shown that the small absorption of concrete masses from seawater reduces the corrosion of the steel by 24 times.
4. Use in Irrigation Systems: The use of standard methods for the repair and rehabilitation of dams and other important water structures appears to be inefficient and incomplete.
This is later found to cause significant losses in profits from irrigation, energy production, flood control etc. But the method of pregnancy works very well.
Concrete from the damaged area is removed, glued and dried. This area is later treated using polymer emissions.
5. Composite Joints: Pregnant polymer concrete is as strong as building materials. PIC also shows the amazing development of standard concrete.
Internal and empty cracks are the basic foundation for all the issues in common concrete structures. Since the suspension of the polymer determines the cause, it is best used for construction members.
Key takeaways
- FIBER REINFORCED POLYMER
Fiber-reinforced polymer (FRP), also fiber-reinforced plastic, is a composite made of polymer matrix reinforced with fibers. Threads are usually glass, carbon, or aramid, although other fibers such as paper or wood or asbestos have sometimes been used. The polymer is usually epoxy, vinylester or polyester thermosetting plastic, and phenol formaldehyde frames are still active. FRPs are widely used in the aerospace, automotive, marine and construction industries.
2. POLYMER IMPREGNATED CONCRETE
In the case of pregnant polymer concrete, prepolymers or lower liquid monomers are partially or partially impregnated with a pore system of a composite cement framework. After this process, the entire treated structure is allowed to polish.
Corrosion monitoring and preventive measures
- The rust measuring, control, and prevention field covers a wide range of technical tasks. Within the field of corrosion control and prevention, there are technical options such as cathodic and anodic protection, material selection, chemical insertion and use of indoor and outdoor clothing. The rust scale uses a variety of techniques to determine how much damage the environment consumes and how much iron loss is experienced. Rust rating is a measure of how rust management performance and prevention strategies can be implemented and provides feedback to enable rust control and preventative measures to be improved.
- Some rust measurement techniques can be used online, regularly displayed in process broadcasts, while others provide external measurement, such as those determined in laboratory analysis. Some techniques provide a precise measure of metal loss or rust ratio, while others are used to indicate the possibility of corrosion.
- Rust monitoring is the practice of measuring the deterioration of process dissemination conditions by using probes that are incorporated into process dissemination and that are continuously expressed in the process dissemination process.
- Rust monitoring probes can be mechanical, electrical or electrical devices.
- Rust monitoring alone provides accurate and online measurement of metal loss / corrosion rate in industrial process systems.
- Typically, the rust measuring system, testing and adjustment used in any industrial area will include measuring instruments provided by four combinations of on-line / offline, direct / indirect measurements.
- Corrosion Monitoring Direct, On-line
- Direct, Offline Non-Destructive Testing
- Indirect Analytical Chemistry, Off-line
- Indirect, online Operational Data
- In a well-managed and integrated system, data from each source will be used to draw reasonable conclusions about the levels of active corrosion by the process process and how they are effectively reduced.
The Need of corrosion monitoring
The level of rust determines which process plant can be used efficiently and safely for how long. The rust scale and the action of adjusting the high levels of rust allow for the efficient operation of plants that must be achieved while minimizing the life cycle costs associated with the work.
Rust monitoring techniques can help in a number of ways:
- By giving an early warning that harmful procedural conditions exist that could lead to failures caused by rust.
- By studying the integration of changes in process parameters and their effect on system corrosivity.
- By identifying a specific rust problem, identifying its cause and the parameters that control the level, such as pressure, temperature, pH, flow rate, etc.
- By evaluating the effectiveness of the corrosion / prevention control method such as chemical prevention and good use.
- By providing management information relating to conservation needs and the ongoing condition of the plant.
Corrosion monitoring techniques
A large number of rust monitoring strategies are available. The following list describes the most common strategies used in industrial applications:
- Rust Coupons (Weight Loss Rate)
- Electrical Resistance (ER)
- Linear Separation Resistance (LPR)
- Galvanic (ZRA) / Possible
- Hydrogen Ingestion
- Bacteria
- Sand / Soil erosion
Other strategies are available, but almost all require professional work, otherwise they are not enough or flexible to apply.
In the above-mentioned strategies, corrosion coupons, ER, and LPR form the core of industrial corrosion monitoring systems. The other four strategies are usually found in special programs that are discussed over time.
These rust monitoring methods have been used successfully and are being used by a growing number of applications because:
- The techniques are easy to understand and apply.
- The reliability of the equipment has been demonstrated in the field field for many years of application operation.
- The results are easy to explain.
- Measurement equipment can be made internally safe from hazardous environmental performance.
- Consumers have gained significant economic benefits by reducing planting time and extending plant life.
Preventive Measures
- Metal corrosion is a natural process that requires three conditions: moisture, metal surface, and an oxidizing agent called an electron acceptor. Rust converts the active metal into a separate form of oxide, hydroxide, or sulphide. The most common type of rust is rust.
- Metallic metal not only affects the structure of the metal, but it can also affect the people who use the material or objects close to the metal. In extreme cases, rotten metal can lead to the construction of buildings and bridges, leaking pipes, and medical implants that infect human blood.
- While all metals are in danger of corrosion, some metals, such as pure metal, deteriorate much faster than others. However, iron can be combined with other alloys to form a stainless steel that is more resistant to corrosion.
- It is estimated that approximately 25-30% of rust can be prevented using appropriate protective measures.
- In general, you can prevent rust by choosing the right type of metal, Protective Fabrics, Environmental Measures, Self-Sacrifice Items, Rust Stumbling Stuff, Metal Installation and Repairs for Your Project.
Choose the right metal type
- One of the easiest ways to prevent rust is to use rust-resistant metal such as stainless steel, duplex, super duplex, nickel alloy or 6% Moly.
- These devices are so well made that they have a high resistance to corrosion and use them to reduce the need for alternative corrosion protection.
- For Special Drawing Materials, we offer products made of the highest quality synthetic materials available - stainless steel, duplex, super duplex, 6% Moly and Nickel Alloy. A variety of materials are selected by our clients in a variety of areas, with one of the factors considered for possible corrosion.
Protective coating
- Another way to prevent rust is to cover it with a special protective paint. Paint coating can act as a barrier that works by preventing electrochemical charging that transmits to the destructive and metal solution below.
- One way to do this is to put a powder coating in a clean metal place. The metal is heated to turn the flour into a smooth, non-abrasive film that acts as a barrier to rust. Many different powder compositions can be used, such as acrylic, polyester, epoxy, nylon, and urethane.
Environmental Measures
- Rust is certainly due to the nature of the metal in it as the chemical reactions that occur are due to metal reacting with liquids and gases in the surrounding environment.
- Controlling the environment can therefore help reduce this response. This could be as simple as reducing exposure to rain or seawater or it could be steps taken to reduce the amount of sulfur, chlorine, or oxygen in the area. For example, carrying water in water boilers to adjust hardness, alkalinity, or oxygen content, before placing the metal in that water can be very helpful in preventing corrosion.
Sacrificial coating
Sacrifice cover to prevent corrosion means covering the metal with a type of metal that may have oxidise - you sacrifice this top layer to protect the lower metal.
There are two main ways to accomplish the sacrificial attire:
- Cathodic Protection: Cathodic protection works by making the metal cathode of an electrochemical cell. The most common example of cathodic protection is the coating of iron ore and zinc - this process is known as galvanizing. Zinc is more than an active metal so rust prevents metal rot. Cathodic protection is frequently used for steel or petrol pipelines, heat tanks, ports, and overseas oil platforms.
- Anodic Protection: Anodic protection is opposed to cathodic protection and works by making the metal anode of an electrochemical cell. A common way to do this is to cover a thin layer of stainless steel, such as tin. The tin will not corrode, so the metal will be protected as long as the tin coating is in place. Anodic protection is often used for carbon storage tanks used to store sulfuric acid and 50% caustic soda.
Corrosion Inhibitors
- Chemical corrosion inhibitors are selected to react to metal surfaces or surrounding gases and therefore suppress electrochemical reactions that can lead to decay. When applied to a metal surface, they form a protective film. Inhibitors can be used as a solution or as a protective cover using distribution methods.
- Corrosion inhibitors are often used in a process known as passivation. An example of passivation is the Statement of Freedom where a blue and green metal signature is actually present to protect the copper underneath.
Metal Plating
- The installation is very similar to the cover as a thin layer of metal is inserted into the metal you want to protect. As well as preventing corrosion, the metal layer provides a good finish of beauty.
There are four types of metal wraps:
- Electroplating: The application of a thin layer of metal such as chromium or nickel to the underground metal by means of an electrolyte bath.
- Mechanical Plating: this involves cold welding powder metal metal substrate.
- Electro less: Coating such as nickel or cobalt is placed on a metal substrate using non-electrical chemical reactions.
- Hot dipping: A simple covering method that involves placing the substrate in a molten metal protective tub.
Design Modification
- Changing the structure of the project can have a significant impact on rust protection as it works by eliminating the causes of rust.
Key takeaways
- The rust measuring, control, and prevention field covers a wide range of technical tasks. Within the field of corrosion control and prevention, there are technical options such as cathodic and anodic protection, material selection, chemical insertion and use of indoor and outdoor clothing. The rust scale uses a variety of techniques to determine how much damage the environment consumes and how much iron loss is experienced. Rust rating is a measure of how rust management performance and prevention strategies can be implemented and provides feedback to enable rust control and preventative measures to be improved.
Rehabilitation methods for concrete elements grouped under confining techniques included concrete jacketing, steel jacketing, ferrocement laminated jacketing and FRP confinement. Some of the methods are for cosmetic repairs required to improve appearance, restore the non-structural properties and weather protection.
These techniques and materials for repair of concrete is described. Concrete is the most widely used and versatile construction material possessing several advantages over steel and other construction materials. However very often one come across with some defects in concrete. The defects may manifest themselves in the form of cracks, spalling of concrete, exposure of reinforcement, excessive deflections or other signs of distress. On many occasions, corrosion of reinforcement may trigger off cracking and spalling of concrete, coupled with deterioration in the strength of the structure. Such situations call for repairs of affected zones and sometimes for the replacement of the entire structure.
The need of structural repairs can arise from any of the following:
- Faulty design of the structure
- Improper execution and bad workmanship
- Extreme weathering and environmental conditions
- High degree of chemical attack
- Ageing of the structure
References:
1. A.M Neville J.J. Brooks Concrete technology
2. A.M Neville Concrete technology
3. R.S. Varshney Concrete technology
4. IS 10262 - 2009, Recommend guidelines for Concrete