Module 4
Pavement Materials – Materials used in Highway Construction
Desirable Properties
- Stability
- Incompressibility
- Permanent strength
- Minimum change in volume
- Good drainage
- Easy to compact
Factors on which Strength of Soil depends
- Soil type
- Moisture content
- Dry density
- Internal structure of soil
- Type and mode of stress application
Evaluation of Soil Strength
- Shear tests: carried out for small samples in laboratories
- Bearing tests: loading tests carried out in the field
- Penetration tests: small-scale bearing tests that can be carried out in the field or in the laboratory
- Plate Bearing Test
- Used to find the supporting power of sub-grade using relatively large diameter plates
- Was first used by Westergaard to determine modulus of sub-grade reaction (k)
- Modulus of sub-grade reaction (k) is defined as the pressure sustained per unit deformation of sub-grade at specified deformation using specified plate size
- The standard plate size used for finding ‘k’ is of 75 cm diameter but in some cases, a smaller plate of 30 cm diameter can also be used
- Pressure ‘p’ corresponding to a settlement of 0.125 cm is read and the ‘k’ value is calculated as:
k = =
(kg/cm3)
- For consolidated and soaked specimen, pressure ‘ps’ required for same deformation Δ is noted then the modulus of sub-grade reaction ka for soaked condition is ka = k
- When the load is not adequate to cause 0.125 cm deflection of 75 cm plate, then smaller plate may be used. In this case, corrected ‘k’ value will be k =
where,
Δ =
Therefore, k =
Also, k1a1 = k2a2
Where, a = radius of the plate
k = modulus of sub-grade reaction
E = modulus of elasticity
2. CBR Test
- This is a penetration test carried out to evaluate the stability of soil sub-grade and other flexible pavement materials
- The test consists of a cylindrical plunger of 50mm diameter to penetrate material at 1.25 mm/minute
- The standard load values obtained from test on crushed stones are 1370 (70 kg/cm2) and 2055 (105 kg/cm2) at 2.5 and 5.0 mm penetration respectively at 50mm diameter plunger.
% CBR = 100
- Normally, CBR value at 2.5 mm penetration is higher than at 5.0 mm penetration and the higher value is reported. However, if CBR at 5.0 mm penetration is higher, the test is repeated for check but finally higher value is reported
- Presence of coarse grained material gives poor results. Hence, material passing 20mm sieve only is used.
Desirable Properties
- Strength: they should be strong to withstand stresses due to wheel loads
- Hardness: they should be hard enough to resist wear & tear due to abrasive action.
Mutual rubbing of stones is known as attrition.
- Toughness: resistance to impact due to moving wheel loads
- Durability: the property to withstand the adverse action of weather
- Shape of aggregates:
Flaky and elongated particles have lesser strength than cubical and angular or rounded particles.
Rounded aggregates may be preferred in cement concrete mix due to low specific area and better workability. However, rounded particles are not preferred in granular base-course.
WBM and bituminous construction provides better stability with angular particles than rounded particles.
Tests for Road Aggregates
- Crushing Test
- Aggregates possessing resistance to crushing under gradually applied crushing load or having low aggregate crushing value are preferred
- Dry aggregates passing 1.25 mm I.S. Sieve and retained on 10 mm sieve is filled in a cylindrical vessel in 3 equal layers
- A crushing load of 40 tonnes is applied @ 4 tonnes/minute and the crushed aggregate is sieved on 2.36 mm I.S. Sieve
- Aggregate crushing value =
100
Where, W2 = crushed material passed 2.36 mm sieve
W1 = sample material
- The crushing value for surface course should be less than 30% and should not exceed 45% for base course
2. Los Angeles Abrasion Test
- Carried out to test the hardness of stones
- Based on rubbing action between the aggregates and steel balls
- Machine is rotated at 30-33 rpm for 500-1000 revolutions
- Abrasion value for good quality aggregates to be used in high quality pavement should be less than 30%. However, for base course in WBM, it may be 50%
- The abrasion value is expressed as the percentage loss in weight due to abrasion
- Coefficient of hardness = 20 –
3. Impact Test
- Used to evaluate the toughness of stone or resistance to fracture under repeated impacts
- A metal hammer of weight 13.5 to 14 kg having a free fall from a height of 38 cm is dropped through vertical guides
- After 15 blows, the crushed aggregate is sieved on a 2.36 mm sieve
- Aggregates should have size between 10-12.5 mm and are filled in 3 layers
- Total impact energy = 15 14 38 = 7980 kg-cm
- Impact value should not normally exceed 30% for wearing surface
- Maximum permissible value for bituminous macadam is 35% and WBM base course is 40%
4. Soundness Test
- Used to study resistance to weathering action
- Resistance to disintegration of aggregate is determined by using saturated solution of sodium sulphate and magnesium sulphate. Dry aggregate is immersed in the solution for 16-18 hours. Then the specimen is oven-dried at 105-110ᵒC to constant weight, known as one cycle of immersion and drying
- The average loss in weight of aggregates to be used in pavement construction after 10 cycles should not exceed 12% when tested with sodium sulphate and 18% when tested with magnesium sulphate
5. Shape Test
a) Flakiness Index
- The flakiness index of aggregate is the percentage by weight of aggregate particles whose least dimension is less than 0.6 times of their mean dimension
- The test is applicable to size larger than 6.3 mm only
- Desirable flakiness index of aggregates used in road construction is less than 15% and should not exceed 25%
b) Elongation Index
- The elongation index of an aggregate is the percentage by weight of particles whose greatest dimension or length is greater than 1.8 times their mean dimension
- The test is not applicable to size smaller than 6.3 mm
- Flakiness index and elongation index values in excess of 15% are undesirable
c) Angularity Number
- Represents the degree of packing and measures the voids in excess of 33%
- Higher the angularity number, more angular is the aggregate
- Range of Angularity Number for aggregates used in construction is 0-11
Angularity Number A.N. = 67 –
W=Weight of aggregate in kg
G= Specific Gravity
C= Weight of water filled in the cylinder in kg
6. Water Absorption Test
- Rock specimen having more than 0.6% water absorption are considered unsatisfactory
7. Bitumen Adhesion Test
- Aggregates which are electro-negative such as silica are water-liking and are called hydrophilic
- Aggregates which have positive surface charge such as limestone are basic in nature and have dislike for water. These are known as hydrophobic aggregates
- Stripping of binders from coated aggregates is the main problem
- IRC has specified that stripping value of aggregates should not exceed 25% for use in bituminous surface, when aggregate coated with bitumen is immersed in water bath at 40ᵒC for 24 hours
- Bituminous materials or asphalts are widely used in construction of roads
- Bituminous materials have excellent binding characteristics, water-proofing abilities and relatively low cost
- They comprise of bitumen which is a black-coloured solid or viscous material obtained from distillation of petroleum or natural asphalt
Production of Bitumen
- Bitumen is a by-product derived during refining of crude petroleum
- Different refinery processes, such as the straight distillation process, solvent extraction process etc. may produce bitumen of different consistencies and properties.
Vacuum Steam Distillation of Petroleum Oils
- In this process, crude oil is heated and is introduced into a large cylindrical container.
- Steam is introduced into the container to help in vapourisation of the volatile constituents of petroleum and to reduce decomposition of residues.
- The volatile constituents are then collected, condensed, and refined by being fed into a vacuum distillation unit, to further separate out heavier gas oils.
- The bottom fraction obtained from this unit is the vacuum-steam-refined asphalt cement.
- As the asphalt cools down to room temperature, it becomes a semi-solid viscous material, known as bitumen.
Different Forms of Bitumen
Cutback Bitumen
- It is a normal practice to heat bitumen in order to reduce its viscosity.
- However, sometimes, preference is given to use liquid binders such as cutback bitumen to lower the viscosity of the bitumen by adding suitable solvents like naphtha, kerosene, diesel oil, and furnace oil to bitumen.
- The solvent from bituminous material will evaporate and bitumen will bind the aggregate.
- Cutback bitumen is used for road construction in cold weather.
- There are different types of cutback bitumen: rapid curing (RC), medium curing (MC), and slow curing (SC).
Types of Bitumen | Solvent | Use |
RC | Naphtha or gasoline | Surface dressing and patchwork |
MC | Kerosene and light diesel oil | Premix with less quantity of fine aggregates |
SC | Furnace oil | Premix with appreciable quantity of fine aggregates |
Bitumen Emulsion
- It is a liquid product in which bitumen is suspended in a finely divided condition in an aqueous medium.
- Ideal binders for hill road construction.
- Bitumen content in the emulsion is around 60% while the remaining is water. When the emulsion is applied on the surface of the road, it breaks down and releases water causing the bitumen-mix to set. This setting time depends upon the grade of bitumen.
- The viscosity of bituminous emulsions is measured as per IS: 8887-1995.
Types of Bituminous Emulsions | Use |
Rapid Setting (RS) | Surface dressing work |
Medium Setting (MS) | Premix jobs and patch repairs work |
Slow Setting (SS) | Preferred in rainy season |
Bituminous primers
- Prepared on road sites by mixing penetration bitumen with petroleum distillate
- Used on stabilized surfaces and water bound macadam base course
Modified Bitumen
- Certain additives known as bitumen modifiers can improve the properties of bitumen and bituminous mixes, forming modified bitumen such as Polymer modified bitumen (PMB), crumb rubber modified bitumen (CRMB) etc.
- IRC: SP: 53-1999 can be referred to for detailed specifications on modified bitumen.
- The performance of PMB and CRMB is strictly temperature-dependent.
- Advantages of Modified Bitumen:
Lower susceptibility to temperature variations
Higher resistance to deformation at high temperature
Better age-resistance properties
Higher fatigue-life
Better adhesion between aggregates and binder
Prevention of cracking
Requirements of Bitumen
- Low temperature susceptibility: the mix should not become too soft or unstable during hot weather, or become too brittle during cold weather.
- Adequate viscosity at the time of mixing and compaction: to be achieved by using cutbacks or emulsions of suitable grades or by heating the bitumen and aggregates prior to mixing.
- No stripping: adequate adhesion between the bitumen and aggregates used in the mix such that it does not strip off from the aggregate.
Tests on bitumen
- Penetration test
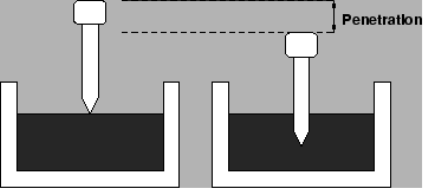
Determines the hardness or softness (consistency) of bitumen by measuring the depth in tenths of a millimetre to which a standard loaded needle will penetrate vertically in 5 seconds.
The sample is maintained at 25ᵒC.
The penetrometer is a needle assembly of weight 100g and comprises of an arrangement for releasing and locking in any position.
The bitumen is softened to a pouring consistency, stirred thoroughly and poured into containers.
A grade of 80/100 bitumen means the penetration value is in the range 80 to 100 at standard test conditions.
2. Ductility test
Ductility is expressed as the distance in centimetres, to which a standard briquette of bitumen can be spread before the thread breaks.
Cross-section of this specimen is 10mm 10mm.
The test is conducted at 27ᵒC and pull @ 50mm/min is applied.
IS Code has recommended a minimum ductility value of 75 cm for grades of 45 & above.
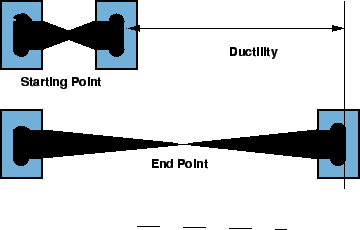
3. Softening point test
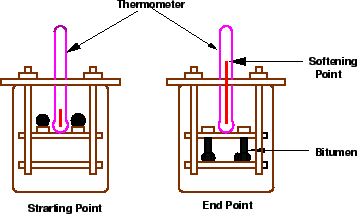
Softening point denotes the temperature at which the bitumen attains a particular degree of softening. This is called the Ring & Ball Test.
A brass ring containing test sample of bitumen is suspended in water and a steel ball is placed upon the sample. The liquid medium is heated.
As soon as the softened bitumen touches the metal plate which is at a specified distance below, the temperature is noted down.
Higher softening point indicates lower temperature susceptibility making the sample preferable in hot weather conditions.
4. Specific gravity test
The specific gravity of bitumen is expressed as the ratio of mass of given volume of bitumen to the mass of equal volume of water at 27ᵒC.
It is measured with either a pycnometre or by preparing a cube specimen of bitumen in semi solid or solid state.
Specific gravity is greatly influenced by chemical composition of the sample.
The specific gravity of bitumen varies between 0.97-1.02.
5. Viscosity test
Viscosity is a measure of resistance to flow.
Orifice type viscometers are commonly used.
Viscosity is expressed in seconds and is defined as the time taken by the 50 ml bitumen material to pass through the orifice of a cup, under standard conditions and temperature.

6. Flash and fire point test
Flash point is the lowest temperature at which the vapour of a substance momentarily takes fire in the form of a flash under specified test conditions.
Fire point is the lowest temperature at which the material gets ignited and burns under specified test conditions.
Pensky-marten’s closed cup apparatus can be used for conducting these tests.
7. Float test
This test is used to measure the consistency of the materials for which neither penetration test nor viscosity test is suitable.
The test specimen is first cooled to a temperature of 5ᵒC. The total test assembly is then floated in a water bath at 50ᵒC.
The time required by water to force its way through the specimen plug is noted as the float value and is expressed in seconds.
Higher the float value, stiffer is the material.
8. Water content test
Bitumen must contain minimum water content to prevent foaming at surface when it is heated above the boiling point of water.
The maximum allowable water content in bitumen should not exceed 0.2% by weight.
9. Loss on heating test
50gm of the sample is heated at a temperature of 163ᵒC for 5 hours and loss of weight is expressed as % by weight.
Loss in weight of bitumen sample to be used for pavement mixes should not be more than 1%, but for bitumen with penetration values 150-200, loss in weight up to 2% is allowed.
10. Spot test
Test is conducted for detecting over-heating or cracks in bitumen.
2 gm of bitumen is dissolved in 100 gm of naphtha. A drop of this solution is taken out and placed on filter paper.
If the stain on the paper is uniform in colour, the bitumen is accepted as un-cracked. Dark or brown stain in centre with an annular ring of lighter colour outside will indicate over-heated or cracked bitumen.
11. Solubility test
Pure bitumen is completely soluble in carbon disulphide and carbon tetra chloride. Hence, insoluble material should be less than 1%.
The material is said to be cracked if solubility is less than 0.5%.
A bituminous mix is defined as a mixture of coarse aggregates, fine aggregates, filler and binder in order to produce a mix with desirable properties like workability, strength, durability and economic considerations.
The objective of the mix design is to produce a bituminous mix with the following properties:
- Higher durability of the pavement surface
- Sufficient strength to resist shear deformation under varying traffic load
- Sufficient number of air voids in the compacted bitumen so as to allow additional compaction by traffic loads
- High workability to allow easy placement without segregation
- Sufficient flexibility so as to avoid premature cracking due to varying temperature and traffic loads
Three design methods for mix are available:
Marshall Method
Modified Hubbard-field Method
Hveem Method
Today, the Marshall method is considered to be the standard method of bituminous mix design. It is therefore discussed in detail below.
Constituents of a mix
- Coarse aggregates: provide compressive strength, shear strength and good interlocking properties to the mix (Example: Granite)
- Fine aggregates: fill the voids between the coarse aggregate and stiffen the binder (Example: Sand, Rock dust)
- Filler: fills voids, stiffens binder and increases the permeability of the mix (Example: Rock dust, cement, lime)
- Binder: Fills voids and imparts adhesiveness & impermeability to the mix (Example: Bitumen, Asphalt, Tar)
Types of mix
- Well-graded mix: It has a good proportion of all constituents and offers good compressive strength and some tensile strength to the mix. It is a dense mix and is also known as bituminous concrete.
- Gap-graded mix: Few large coarse aggregates are missing from the mix but it has good fatigue and tensile strength.
- Open-graded mix: Fine aggregate and filler are missing from the mix. It is porous and offers good friction It also has low strength.
- Unbounded: Binder is absent in the mix. Under loads, it behaves as if its components are not linked together even though good interlocking exists. It has very low tensile strength and requires kerb protection.
Design of bituminous mixes
- Selection of Aggregate
Crushed aggregates and sharp sands produce higher stability of the mix when compared with gravel and rounded sands.
In base course, aggregates of size 2.5 to 5 cm are used whereas in surface course, 1.25 to 1.87 cm size aggregates are used.
Binder content is 5 to 7.5% by weight of mix.
2. Determination of Specific Gravity
The average specific gravity Gm of the blended aggregate mix is calculated from the equation:
Gm =
Here, W1, W2, W3, W4 are % by weight of aggregates and G1, G2, G3, G4 are their respective specific gravity.
Marshall Method of Bituminous Mix Design
Marshall Mix Design method involves selecting the bitumen binder content of a suitable density that satisfies minimum stability and range of flow values.
Marshall Stability of a test specimen is defined as the maximum load that produces failure when the specimen is pre-heated to a prescribed temperature and load is applied at a constant strain rate of 5 cm per minute. Simultaneously, a dial gauge is used to measure the vertical deformation of the specimen. Deformation value of 0.25 mm is called the Marshall Flow Value of the specimen.
Steps in Marshall Mix Design
Step 1: Determine the physical properties, size and gradation of aggregates.
Step 2: Select the type of asphalt/ bitumen binder.
Step 3: Prepare initial samples, each with different bitumen binder content.
Step 4: Average value of various properties are determined for each mix and the following graphical plots are prepared:
Bitumen binder content vs. Density
Bitumen binder content vs. Marshall stability
Bitumen binder content vs. Flow
Bitumen binder content vs. Air voids
Bitumen binder content vs. Voids in mineral aggregates (VMA)
Bitumen binder content vs. Voids filled with asphalt (VFA)
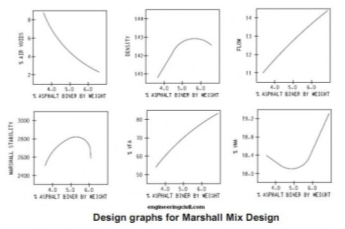
Step 5: Determine the optimum bitumen content for the mix design by taking average value of the following three bitumen contents found form the graphs obtained in the previous step:
Binder content corresponding to maximum stability
Binder content corresponding to maximum bulk specific gravity
Binder content corresponding to the to the air void content of 4 percent
Step 6: Compare each of these values against design requirements and if all comply with design requirements, then the selected bitumen content is acceptable. Otherwise, redesign the mixture.
Portland cement concrete (PCC) pavements, also known as rigid pavements consist of a PCC slab that is usually supported by a stabilized base, and a sub-base. In some cases, the slab may be overlaid with a layer of bitumen concrete.
PCC is produced at a central plant and transported to the job site in transit mixers or batched into truck mixers directly and then mixed on-site. In either case, the PCC is then dumped, spread, leveled, and consolidated.
Tests on Cement
The following are some of the important tests conducted on concrete:
- Slump test
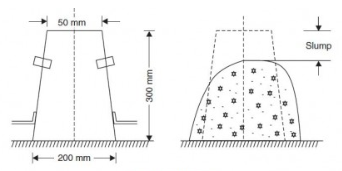
- It is conducted to determine the workability of concrete.
- It needs a slump cone which is a vessel in the shape of a frustum of a cone with top diameter = 50-100 mm, bottom diameter = 100-200 mm and height = 200-300 mm.
- This cone is kept over a flat platform and is filled with concrete in 4 layers.
- Each layer is rammed with a 16 mm pointed rod 25 times.
- After filling the cone completely, it is gently pulled up.
- The sudden decrease in the height of the concrete is called slump.
- Higher the slump, more workable is the concrete.
2. Compaction factor test
- This is another test conducted in the laboratory to identify the workability of concrete.
- The equipment comprises of 2 hoppers and 1 cylinder fixed to a stand, having standard dimensions.
- Hoppers have hinged bottoms whereas the cylinder has fixed bottom.
- The top vessel is filled with the concrete sample. The hinged door is opened as soon as it is filled. Concrete is then collected in the second vessel. Then the hinged door of the second vessel is opened to collect concrete in the bottom cylinder. The concrete in cylinder is then weighted. Let it be W1.
- Now the cylinder is again filled with a sample of concrete, which is compacted by ramming & vibrating. The concrete in cylinder is then weighted. Let it be W2.
- Ratio W1/W2 is termed as compaction factor.
3. Crushing strength test
- Metallic moulds of size 15 cm × 15 cm × 15 cm are used for casting concrete cubes.
- Before filling the mould, it is properly oiled on its inner surfaces, so that cubes can be easily separated.
- The cube is filled with concrete to be tested in 3 layers and kept in a room.
- After 24 hours, the cube is removed from the mould and kept under water for curing for 28 days before being tested in the compression testing machine.
- In CTM, the crushing load is noted and crushing strength is found as load divided by surface area (15 × 15 cm2).
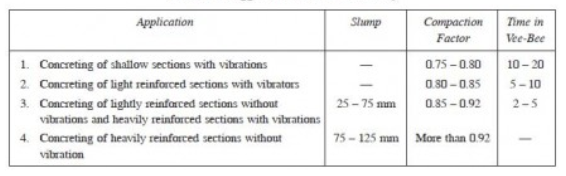
Components of Pavement
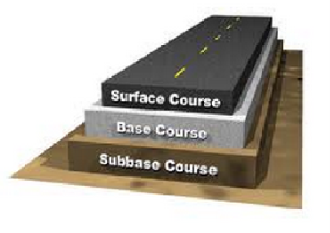
- Soil subgrade
The pavement load is ultimately taken by soil subgrade. Hence, it should not be over-stressed. Common strength tests used for evaluation of soil subgrade are:
CBR Test
California Resistance Value Test
Triaxial Compression Test
Plate Bearing Test
2. Sub-base & base course
These are broken stone aggregates. It is desirable to use smaller size graded aggregates for sub-base course instead of boulder stones.
Base & sub-base courses are used below flexible pavements to improve load supporting capacity by distribution of the load through a finite section.
Base course is used in case of rigid pavements to protect the sub-grade against frost action.
3. Wearing course
Purpose of this course is to give smooth riding surface. It resists pressure exerted by tyres and takes up wear & tear due to traffic. It also offers water tightness.
The stability of wearing course is estimated by Marshall stability test.
Classification of Pavement based on Structural Behaviour
- Flexible pavements
- Flexible pavements are those which have low or negligible flexural strength.
- The flexible pavement layers reflect the deformation of the lower layers on the surface of the layer.
- Flexible pavements consist of 4 pavements:
- Soil subgrade
- Sub-base course
- Base course
- Surface course
- Flexible pavement layers transmit the vertical stresses to the lower layers grain by grain through points of contact.
- Example: bituminous concrete, WBM, soil aggregate mixes , granular materials with or without bituminous binders
- Flexible pavements are designed using empirical charts, semi-empirical and theoretical methods.
2. Rigid pavements
- Rigid pavements possess note-worthy flexible strength or flexural rigidity.
- These transfer the load through slab action but not grain to grain.
- These consist of 3 layers: cement concrete slab, base course and soil subgrade.
- These rigid pavements are made of Portland cement concrete: plain, reinforced or prestressed.
- Plain cement concrete is expected to take-up about 40 kg/cm2 flexural stress.
- These are designed using elastic theory.
3. Semi-rigid pavements
- When bonded materials like pozzolanic concrete, lean cement concrete or soil cement are used then pavement layer has considerably higher flexural strength than the other layers, such pavements are called semi-rigid pavements.
- These materials have low resistance to impact and abrasion.
Reference Books:
- S.K. Khanna and C.E.G. Justo - Highway Engineering - 10th Edition, Nem Chand and Bros. Roorkee
- L.R. Kadiyali - Traffic Engineering and Transport Planning - Khanna Publishers