Unit - 2
Components of EB billing
Electricity is a powerful form of energy that is essential to the operation of virtually every facility in the world. It is also an expensive form of energy that can represent a significant portion of a manufacturing facility’s cost of production.
5 Key Elements of Your Electricity Bill
This energy management primer is intended to introduce some electricity billing fundamentals, especially focusing on the two major aspects of the electricity bill, demand and energy.
1. Electricity metering-
Electric utilities meter both the real and reactive power consumption of a facility. The real power consumption, and its integral – energy, usually comprise the largest portion of the electric bill.
2. Demand-
Real power consumption, typically expressed in kilowatts or megawatts, varies instantaneously over the course of a day as facility loads change. While instantaneous power fluctuations can be significant, electric utilities have found that average power consumption over a time interval of 15, 30, or 60 minutes is a better indicator of the “demand” on electrical distribution equipment.
The demand rate, in $ Kw may also be referred to as a capacity charge, since it has historically been related to the necessary construction of new generating stations, transmission lines, and other utility capital projects. Demand charges often represent 40% or more of an industrial customer’s monthly bill.
3. Energy consumption-
The other major component of an electric bill is energy. The same metering equipment that measures power demand also records customer energy consumption. Energy consumption is reported in kilowatt-hours or megawatt-hours. Unlike power demand with its capacity relationship, customer energy consumption is sometimes related to fuel requirements in electric utility generating stations.
4. Load factor- Demand/ Energy relationship-
One useful parameter to calculate each month is the ratio of the average demand to the peak demand. This unit-less number is a useful parameter that tracks the effectiveness of demand management techniques. A load factor of 100% means that the facility operated at the same demand the entire month, a so-called “flat” profile. This type of usage results in the lowest unit cost of electricity.
Few facilities operate at a load factor of 100%, and that is not likely to represent an economical goal for most facilities. But a facility can calculate its historical load factor, and seek to improve it by reducing usage at peak times, moving batch processes to times of lower demand, and so forth.
5. Power factor-
The relationship of real, reactive, and total power has been introduced previously, and described as the “power triangle”. For effective electricity cost reduction, it is important to understand how the customer’s electric utility recoups its costs associated with reactive power requirements of its system.
Even if a utility does not charge directly for poor power factor, there are at least three other reasons that a customer may find it economical to install equipment to improve power factor within its facility, thereby reducing the reactive power requirements of the utility.
The transformer in the simplest way can be described as a thing that steps up or steps down voltage. In a step-up transformer, the output voltage is increased and in a step-down transformer, the output voltage is decreased. The step-up transformer will decrease the output current and the step-down transformer will increase the output current for keeping the input and the output power of the system equal.
The transformer is basically a voltage control device that is used widely in the distribution and transmission of alternating current power. The idea of a transformer was first discussed by Michael Faraday in the year 1831 and was carried forward by many other prominent scientific scholars. However, the general purpose of using transformers was to maintain a balance between the electricity that was generated at very high voltages and consumption which was done at very low voltages.
Transformer Types
Transformers are used in various fields like power generation grid, distribution sector, transmission and electric energy consumption. There are various types of transformers which are classified based on the following factors;
- Working voltage range.
- The medium used in the core.
- Winding arrangement.
- Installation location.
Based on Voltage Levels
Commonly used transformer type, depending upon voltage they are classified as:
- Step-up Transformer: They are used between the power generator and the power grid. The secondary output voltage is higher than the input voltage.
- Step down Transformer: These transformers are used to convert high voltage primary supply to low voltage secondary output.
Based on the Medium of Core Used
In a transformer, we will find different types of cores that are used.
- Air core Transformer: The flux linkage between primary and secondary winding is through the air. The coil or windings wound on the non-magnetic strip.
- Iron core Transformer: Windings are wound on multiple iron plates stacked together, which provides a perfect linkage path to generate flux.
Based on the Winding Arrangement
- Autotransformer: It will have only one winding wound over a laminated core. The primary and secondary share the same coil. Auto also means “self” in language Greek.
Based on Install Location
- Power Transformer: It is used at power generation stations as they are suitable for high voltage application
- Distribution Transformer: Mostly used at distribution lanes for domestic purposes. They are designed for carrying low voltages. It is very easy to install and characterized by low magnetic losses.
- Measurement Transformers: These are further classified. They are mainly used for measuring voltage, current, power.
- Protection Transformers: They are used for component protection purposes. In circuits, some components must be protected from voltage fluctuation etc. Protection transformers ensure component protection.
Working Principle of a Transformer-
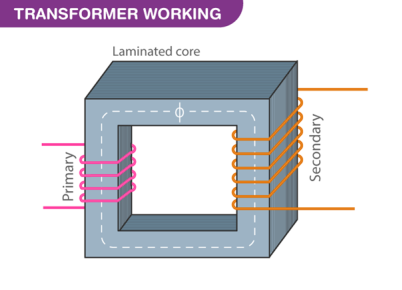
The transformer works on the principle of Faraday’s law of electromagnetic induction and mutual induction.
There are usually two coils primary coil and secondary coil on the transformer core. The core laminations are joined in the form of strips. The two coils have high mutual inductance. When an alternating current pass through the primary coil it creates a varying magnetic flux. As per faraday’s law of electromagnetic induction, this change in magnetic flux induces an emf (electromotive force) in the secondary coil which is linked to the core having a primary coil. This is mutual induction.
Overall, a transformer carries the below operations:
- Transfer of electrical energy from circuit to another
- Transfer of electrical power through electromagnetic induction
- Electric power transfer without any change in frequency
- Two circuits are linked with mutual induction
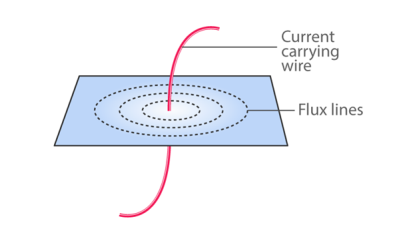
The figure shows the formation of magnetic flux lines around a current-carrying wire. The normal of the plane containing the flux lines are parallel to normal of a cross-section of a wire.
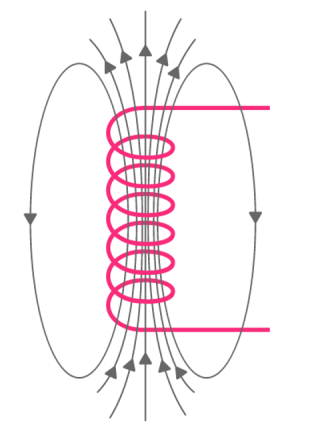
The figure shows the formation of varying magnetic flux lines around a wire-wound. The interesting part is that reverse is also true, when a magnetic flux line fluctuates around a piece of wire, a current will be induced in it. This was what Michael faraday found in 1831 which is the fundamental working principle of electric generators as well as transformers.
Thepropersizingofanelectrical(loadbearing)cableisimportanttoensurethatthecable can:
- Operatecontinuouslyunderfullloadwithoutbeingdamaged
- Withstandtheworstshortcircuitscurrentsflowingthroughthecable
- Providetheloadwithasuitablevoltage(andavoidexcessivevoltagedrops)
- Ensureoperationofprotectivedevicesduringanearthfault
Allcablesizingmethodsmoreorlessfollow thesamebasicsixstepprocess:
- Gatheringdataaboutthecable,itsinstallationconditions,theloadthatit will carry,etc.
- Determinetheminimumcablesizebasedoncontinuouscurrentcarryingcapacity
- Determinetheminimumcablesizebasedonvoltagedropconsiderations
- Determinetheminimumcablesizebasedonshortcircuittemperaturerise
- Determinetheminimumcablesizebasedonearthfaultloopimpedance
- Selectthecablebasedonthelowestofthesizescalculatedinstep2,3,4and5
Step 1: Data Gathering
Thefirststepistocollecttherelevantinformationthatisrequiredtoperformthesizing calculation. Following data has to be obtained:
LoadDetails: Thecharacteristicsoftheloadthatthecablewillsupply,whichincludes: Loadtype- motororfeeder, threephase/singlephaseorDC, system/sourcevoltage, fullloadcurrent, fullloadpowerfactor.
Cable Construction: Thebasiccharacteristicsofthecable'sphysicalconstruction,whichincludes:
- Conductormaterial-normallycopperoraluminium
- Conductorshape-e.g.,circularorshaped
- Conductortype-e.g.,strandedorsolid
- Conductorsurfacecoating-e.g.,plain(nocoating),tinned,silverornickel
- Insulationtype-e.g.,PVC,XLPE,EPR
InstallationConditions: Howthecablewillbeinstalled,whichincludes:
- Abovegroundorunderground
- Installation / arrangement - e.g., for underground cables, is it directly buried orburiedinconduit?forabovegroundcables,isitinstalledoncabletray/ladder,againstawall,inair,etc.
- Ambientorsoiltemperatureoftheinstallationsite
- Cablebunching,i.e.,thenumberofcablesthatarebunchedtogether
- Cablespacing,i.e.,whethercablesareinstalledtouchingorspaced
- Soilthermalresistivity(forundergroundcables)
- Depthoflaying(forundergroundcables)
- Forsinglecorethree-phasecables,arethecablesinstalledintrefoilorlaidflat?
Step2:CableSelectionBasedonCurrentRating
Current flowing through a cable generates heat through the resistive losses in theconductors,dielectriclossesthroughtheinsulationandresistivelossesfromcurrentflowingthroughanycablescreens/shields andarmouring. The cable components (particularly the insulation) must be capable of withstanding thetemperature rise and heat emanating from the cable. The current carrying capacity of a cableisthemaximumcurrentthatcanflowcontinuouslythroughacable.Itissometimes also referredtoasthecontinuouscurrentratingorampacityofacable.
Cableswithlargerconductorcross-sectionalareas(i.e.,morecopperoraluminium)havelowerresistivelossesandareabletodissipatetheheatbetterthansmallercables. Therefore a 16 mm2 cable will haveahighercurrentcarryingcapacitythana 4mm2 cable.
Step 3: Voltage Drop
Acable'sconductorcanbeseenasanimpedance and as a result, whenever current flows in a cable, there will be a voltage drop across it as per Ohm’s Law (V=IZ). The voltage drop will depend on two things:
Current through the cable – The higher the current, higher the voltage drops
Impedance of the conductor – The larger the impedance, the higher the voltage drop
Step 4: Short Circuit Temperature rise
During a short circuit, a high amount of current can flow through a cable for a short time. This surge in current flow causes a temperature rise within the cable. High temperatures can trigger unwanted reactions in the cable insulation, sheath materials and other components, which can prematurely degrade the condition of the cable. As the cross-sectional area of the cable increases, it can dissipate higher fault currents for a given temperature rise. Therefore, cables should be sized to withstand the largest short circuit that it is expected to see.
Step 5: Earth Fault Loop Impedance
Sometimes it is desirable (or necessary) to consider the earth fault loop impedance of circuit in the sizing of a cable. Suppose a bolted earth fault occurs between an active conductor and earth. During such an earth fault, it is desirable that the upstream protective device acts to interrupt the fault within a maximum disconnection time so as to protect against any inadvertent contact to exposed live parts.
Ideally the circuit will have earth fault protection, in which case the protection will be fast acting and well within the maximum disconnection time. The maximum disconnection time is chosen so that a dangerous touch voltage does not persist for long enough to cause injury or death. For most circuits, a maximum disconnection time of 5s is sufficient, though for portable equipment and socket outlets, a faster disconnection time is desirable (i.e., <1s and will definitely require earth fault protection).
A capacitor (originally known as a condenser) is a passive two-terminal electrical component used to store energy electrostatically in an electric field. The forms of practical capacitors vary widely, but all contain at least two electrical conductors (plates) separated by a dielectric (i.e., insulator). The conductors can be thin films of metal, aluminium foil or disks, etc. The 'nonconducting' dielectric acts to increase the capacitor's charge capacity. A dielectric can be glass, ceramic, plastic film, air, paper, mica, etc. Capacitors are widely used as parts of electrical circuits in many common electrical devices. Unlike a resistor, a capacitor does not dissipate energy. Instead, a capacitor stores energy in the form of an electrostatic field between its plates.
When there is a potential difference across the conductors (e.g., when a capacitor is attached across a battery), an electric field develops across the dielectric, causing positive charge (+Q) to collect on one plate and negative charge (-Q) to collect on the other plate. If a battery has been attached to a capacitor for a sufficient amount of time, no current can flow through the capacitor. However, if an accelerating or alternating voltage is applied across the leads of the capacitor, a displacement current can flow.
An ideal capacitor is characterized by a single constant value for its capacitance. Capacitance is expressed as the ratio of the electric charge (Q) on each conductor to the potential difference (V) between them. The SI unit of capacitance is the farad (F), which is equal to one coulomb per volt (1 C/V). Typical capacitance values range from about 1 pF (10−12 F) to about 1 mF (10−3 F).
The term power factor comes into the picture in AC circuits only. Mathematically it is the cosine of the phase difference between the source voltage and current. It refers to the fraction of total power (apparent power) which is utilized to do the useful work called active power.
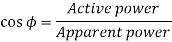
Need for Power Factor Improvement
- Real power is given by P = VIcosφ. The electrical current is inversely proportional to cosφ for transferring a given amount of power at a certain voltage. Hence higher the pf lower will be the current flowing. A small current flow requires a less cross-sectional area of conductors, and thus it saves conductors and money.
- From the above relation, we see having a poor power factor increases the current flowing in a conductor, and thus copper loss increases. A large voltage drop occurs in the alternator, electrical transformer, and transmission, and distribution lines – which gives very poor voltage regulation.
- The KVA rating of machines is also reduced by having a higher power factor, as per the formula:
KVA= KW/COS
Hence, the size and cost of the machine are also reduced. This is why the electrical power factor should be maintained close to unity – it is significantly cheaper.
Power factor improvement methods and correction is one of the crucial aspects to ensure that the appliances are not drawing more current for executing the same amount of work, which is possible with less current consumption. It is one of the most common terms that is used for defining energy efficiency.
Power factor is used to define the efficiency of the electrical systems and is mostly done in the case of AC systems. It needs to be close to unity at all times to ensure that the system is high efficiency. In case the power factor drops to 95%, the current power demand will increase, which will hamper the efficiency quotient of the system.
Therefore, seeking the use of active and passive power factor correction filters is highly essential. Apart from that here are some of the methods or ways to correct the power factor.
Use Of Static Capacitors
The first amongst the several power factor improvement methods is to use static capacitors; these capacitors have the potential to control the current lagging effects. That occurs due to the presence of excessive inductive loads. Static capacitors, when installed parallelly with the equipment that is probably running on a low power factor, will enhance the power factor quotient.
The use of static capacitors will use the leading current to neutralize the lagging current in the system and will correct the reactive component of the load current. It is easy to install, and the losses are low, which ensures less maintenance hassle.
However, you might have to change the static capacitors after every 8-10 years as it is the maximum age for them to handle the fluctuations. Along with that, with the increase in rated voltage, the capacitors might experience damage. Therefore, you need to keep a watch on that!
What are the power factor improvement methods?
Power factor improvement methods and correction is one of the crucial aspects to ensure that the appliances are not drawing more current for executing the same amount of work, which is possible with less current consumption. It is one of the most common terms that is used for defining energy efficiency.
Power factor is used to define the efficiency of the electrical systems and is mostly done in the case of AC systems. It needs to be close to unity at all times to ensure that the system is high efficiency. In case the power factor drops to 95%, the current power demand will increase, which will hamper the efficiency quotient of the system.
Therefore, seeking the use of active and passive power factor correction filters is highly essential. Apart from that here are some of the methods or ways to correct the power factor.
Use Of Static Capacitors
The first amongst the several power factor improvement methods is to use static capacitors; these capacitors have the potential to control the current lagging effects. That occurs due to the presence of excessive inductive loads. Static capacitors, when installed parallelly with the equipment that is probably running on a low power factor, will enhance the power factor quotient.
The use of static capacitors will use the leading current to neutralize the lagging current in the system and will correct the reactive component of the load current. It is easy to install, and the losses are low, which ensures less maintenance hassle.
However, you might have to change the static capacitors after every 8-10 years as it is the maximum age for them to handle the fluctuations. Along with that, with the increase in rated voltage, the capacitors might experience damage. Therefore, you need to keep a watch on that!
Use Of Synchronous Condenser
Make use of a three-phase synchronous motor that has the potential to run on no-load. This complete setup is known as synchronous condenser which can operate on unity, lagging and leading power factor rating.
Due to the presence of the inductive load, the synchronous condenser will be installed onto the side of the load. Hence, it will behave as a capacitor for correcting the power factor of the system. The best part of using the setup of the synchronous condenser is that it lasts for up to 25 years without much need for maintenance. Along with that, it also stays unaffected by the harmonics of the system.
Use Of Phase Advancer
Phase advancer is the last and the most effective method for correcting the power factor as it uses an AC exciter for the correction aspects. It is connected to the motor’s rotor circuit to enhance the ampere-turns. It can help obtain a leading power factor as well with higher ampere-turns. The only drawback for this method is that the motors are below 200 H.P. Cannot integrate it.
Harmonics are currents or voltages with frequencies that are integer multiples of the fundamental power frequency. If the fundamental frequency is 60 Hz, then the 2nd harmonic is 120 Hz, the third is 180 Hz, etc. Harmonics are created by non-linear loads that draw current in abrupt pulses rather than in smooth sinusoidal manner. These pulses cause distorted current wave shapes, which in turn cause harmonic currents to flow back into other parts of the power system.
While any electronic load can generate harmonics, inefficiency is prevalent wherever there are large numbers of personal computers and other types of equipment that draw current in short pulses. Variable frequency drives (VFD) on the other hand are more efficient, as they are designed to draw current only during a controlled portion of the incoming voltage waveform.
While VFDs dramatically improve efficiency, they can cause harmonics in the load current, which can lead to overheated transformers as well as tripped circuit breakers. Power-quality analysers and power loggers can help you identify harmonics in these systems
These unwanted frequencies cause other problems as well, including heat and efficiency losses in motors. The most severe symptoms created by harmonics are typically the result of the harmonics distorting the fundamental 60 Hz sine wave found in facilities. This sine wave distortion results in improper operation of electronic equipment, spurious alarms, data losses and what are often reported as “mysterious” problems.
Total harmonic distortion (THD)
When symptoms of harmonics occur, troubleshoot by observing total harmonic distortion (THD). THD is the relationship of all present harmonics to the fundamental frequency—expressed as the ratio of the sum of the powers of all harmonics to the power of fundamental frequency. A significant increase in THD under varying load conditions warrants a percentage comparison of each individual harmonic current level as compared to the total fundamental current flow in the system.
Knowing the effects created by each harmonic current and comparing them to identified symptoms will aid in troubleshooting. The source of the harmonic must then be isolated and corrected. Summary Voltage problems and the creation of harmonic currents are the two broad areas under which power quality problems occur. Dips and swells, voltage transients, power interruptions, and voltage unbalance all can be monitored, analysed and compared to equipment operation histories to determine the cause and severity of the power quality problem. The same can be done with the various harmonic currents in a system.
Electrical motor efficiency is the ratio between shaft output power - and electrical input power.
Electrical Motor Efficiency when Shaft Output is measured in Watt
If power output is measured in Watt (W) then efficiency can be expressed as
ηm = Pout / Pin (1)
Where
ηm = motor efficiency
Pout = shaft power out (Watt, W)
Pin = electric power in to the motor (Watt, W)
Electrical Motor Efficiency when Shaft Output is measured in Horsepower
If power output is measured in horsepower (hp), efficiency can be expressed as
ηm = Pout 746 / Pin (2)
Where
Pout = shaft power out (horsepower, hp)
Pin = electric power in to the motor (Watt, W)
Primary and Secondary Resistance Losses
The electrical power lost in the primary rotor and secondary stator winding resistance are also called copper losses. The copper loss varies with the load in proportion to the current squared - and can be expressed as
Pcl = R I2 (3)
Where
Pcl = stator winding - copper loss (W, watts)
R = resistance (Ω)
I = current (A, amps)
Iron Losses
These losses are the result of magnetic energy dissipated when the motors magnetic field is applied to the stator core.
Stray Losses
Stray losses are the losses that remains after primary copper and secondary losses, iron losses and mechanical losses. The largest contribution to the stray losses is harmonic energies generated when the motor operates under load. These energies are dissipated as currents in the copper winding, harmonic flux components in the iron parts, leakage in the laminate core.
Mechanical Losses
Mechanical losses include friction in the motor bearings and the fan for air cooling.
NEMA Design B Electrical Motors
Electrical motors constructed according NEMA Design B must meet the efficiencies below:
Power | Minimum Nominal Efficiency1) |
1 - 4 | 78.8 |
5 - 9 | 84.0 |
10 - 19 | 85.5 |
20 - 49 | 88.5 |
50 - 99 | 90.2 |
100 - 124 | 91.7 |
> 125 | 92.4 |
NEMA Design B, Single Speed 1200, 1800, 3600 RPM. Open Drip Proof (ODP) or Totally Enclosed Fan Cooled (TEFC) motors 1 hp and larger that operate more than 500 hours per year.
Electric motors are of utmost importance in industrial as well as agriculture sector. These motors found their application as constant speed drives with very low rating as well as variable speed drives with very high rating. Energy efficiency and energy conservation are very closely related to each other. With increase in demand of energy and due to uncertainties in oil supply and fluctuating price of conventional fuels, efficiency and conservation of energy has become an important aspect of industrial as well as rural development. A large amount of electrical energy is consumed by induction motor used for irrigation in rural sector and industrial purpose in urban sector. In country like India agriculture and industrial sector is developing rapidly, in same way electrical energy consumption is increasing. A study indicated that a 5 per cent improvement in overall efficiency of induction motor would save enough energy that would be comparable to energy produced by a new power plant of few hundred megawatts.
Energy-efficient motors are the ones in which, design improvements are incorporated specifically to increase operating efficiency over motors of standard design. Design improvements focus on reducing intrinsic motor losses. Improvements include the use of lower-loss silicon steel, a longer core (to increase active material), thicker wires (to reduce resistance), thinner laminations, smaller air gap between stator and rotor, copper instead of aluminium bars in the rotor, superior bearings and a smaller fan, etc. Energy-efficient motors now available in India operate with efficiencies that are typically 3 to 4 percentage higher than standard motors.
The suitable selection of copper conductor size will reduce the resistance. Reducing the motor current is the most readily accomplished by decreasing the magnetising component of current. This involves lowering the operating flux density and possible shortening of air gap. Rotor I2 R losses are a function of the rotor conductors (usually aluminium) and the rotor slip. Utilisation of copper conductors will reduce the winding resistance. Motor operation closer to synchronous speed will also reduce rotor I2 R losses. Core losses are those found in the stator-rotor magnetic steel and are due to hysteresis effect and eddy current effect during 50 Hz magnetisation of the core material. These losses are independent of load and account for 20 – 25 per cent of the total losses. The hysteresis losses which are a function of flux density, are to be reduced by utilising low loss grade of silicon steel laminations. The reduction of flux density is achieved by suitable increase in the core length of stator and rotor. Eddy current losses are generated by circulating current within the core steel laminations. These are reduced by using thinner laminations.
Friction and windage losses result from bearing friction, windage and circulating air through the motor and account for 8 – 12 per cent of total losses. These losses are independent of load. The windage losses also reduce with the diameter of fan leading to reduction in windage losses. Stray load losses vary according to square of the load current and are caused by leakage flux induced by load currents in the laminations and account for 4 to 5 per cent of total losses. These losses are reduced by careful selection of slot numbers, tooth/slot geometry and air gap.
Energy efficient motors cover a wide range of ratings and the full load efficiencies are higher by 3 to 7 per cent. The mounting dimensions are also maintained to enable easy replacement. As a result of the modifications to improve performance, the costs of energy-efficient motors are higher than those of standard motors. The higher cost will often be paid back rapidly in saved operating costs, particularly, in new applications or end-of-life motor replacements.
Illumination or illuminance is the total quantity of light per unit area on a surface. The unit of illuminance is lux and abbreviated as lux.
Abbreviation is used after numerical expression, just like in lumens and Candela terms. For example; 100 lx, 1.000 lx, 10.000 lx.
1 lux is equal to 1 lumen per square meter. 1 candela light intensity provides 1 lux light level in 1-meter distance.
Illumination of an environment is expressed with lux value. Higher lux value means higher illuminance. However, it should not be forgotten that excess lighting does not mean good lighting. Excessive lighting has also negative effect like insufficient lighting.
If we mention about the proper common illuminance; in a sunny day 10.000 lux, in a cloudy day 1.000 lux, sunset 10 lux, in a moonlight 0,1 lux illuminance can be seen.
Lux value is related to lumen which expressed the total light output of a light source. As you move away from the light source, lux value decreased.
If the light concentrated on a small area, this area perceived as brighter and reached to high lux value. However, the same amount of light concentrated on a wider area, more soft light occurred and has less lux value measured. Although both light sources emitted same amount of light, in the concentrated light source, it is perceived as brighter because the light is more intense.
In general, lux is the measure of the intensity of light that reaches an area.
If lighting equipment with high light output in other words high lumen value is used in an area, high level of illumination is obtained. This means high lux level is obtained.
The level of illumination or lux value in an environment is measured by devices called lux meter. These devices only measure illuminance and they are designed as portable. Also, these devices are not so expensive.
For example, in the office, 500 lux lighting is required and 100 lux lighting is sufficient in the living room. In areas like drawing offices, textile mills and laboratories require high light levels such as 1.000 lux. At this point, updated lighting requirements should be reviewed according to the type of application.
In LED lighting, lumens measure the brightness of a light. This is different than Watts, which measure the amount of energy in a light. The term lumen means “light,” which makes sense when you understand what these measures. In other words, lumens measure the amount of light your LED light puts out. The higher the lumens, the brighter the light will be.
Why Are LED Lights Measured in Lumens?
Measuring the brightness of a light is more important than measuring its power. Traditional incandescent bulbs were measured in watts, which showed how much power they used. More wattage meant brighter light. Now that the industry has so many energy efficient lighting options, more wattage does not actually mean more light, unless you are staying within the same type of light bulb. That is why LED lighting is measured in lumens.
Lumens are a particularly helpful unit when trying to calculate how many lights to buy for your facility. Most facilities have a minimum requirement for proper visibility, and you can only calculate how many lights you need if you calculate in lumens. If you need a particular number of lumens per square foot, and know how many lumens the light produces, you can install or purchase the right number of lights.
How Do Lumens Compare to Watts?
Lumens and watts measure different things, so they can’t really be compared. This would be like comparing a pound of apples to a gallon of milk – the measurements are completely different. However, you can estimate the number of lumens a particular watt bulb would produce. An incandescent bulb that uses 100 watts, for example, produces about 1600 lumens. In the world of LED, a 26-watt bulb creates the same number of lumens.
The three most common energy-efficient lighting types are Halogen Incandescent Lights, Compact Fluorescent Lamps (CFL), and Light Emitting Diodes (LED). Each of them comes in a variety of wattage power, light spectrum colour, and size. Which one you choose will depend on several factors.
Halogen Incandescent Lights
While mostly associated with offices, halogen incandescent lights are starting to appear more and more in homes. Halogen incandescent lights have a capsule inside that holds gas around a filament to increase its efficiency. The cost of halogen lighting has come down significantly over the past decade, and there is a larger range of styles of bulbs and colours too. Halogen creates a more focused “clean” spectrum of light that can help to relieve vision strain.
Compact Fluorescent Lamps (CFL)
CFL bulbs are what you will generally find on the store shelves today. They are shaped in the same size and style as the traditional incandescent, but the bulb itself almost looks like a soft ice cream twist. This was an ingenious way to take the power and capacity of the traditional long tube fluorescent light and adapt it to be able to fit house lighting designed to support the traditional incandescent. There is a broad spectrum of light available in these lamps.
One thing that they are becoming known for is that while their cost has come down significantly, they are still more expensive than the traditional incandescent – but they also last 14 times longer. Replacing the old-style bulb with the new CFL is as simple as just using the CFL in place of the traditional lamp.
Compared to incandescent lamp, an Energy Star CFL’s use 1/5 or 1/3 of electric power and last eight to fifteen times longer. CFL’s cost more than an incandescent lamp but can save you five times over its purchase price in electricity costs over the lamp’s lifetime. A CFL uses about one-third the energy of a halogen incandescent.
Light Emitting Diodes (LED)
LEDs in white light hold the greatest potential for the future of all the common lighting types as they are one of today’s most energy efficient and rapidly growing technologies. LED’s get illuminated by the movement of electrons in the semiconductor. They are tiny little bulbs that easily fit into an electrical circuit. They perform variety of jobs and can be found in many different devices. For instance, they transmit information from remote controls, illuminate traffic lights, form numbers on digital clocks, lights up watches and many others. It is one of the most energy efficient types, with a lifespan that can last more than 50 times the CFL.
LEDs with Energy Star rating use 20-25% of the energy and last 20-25 times longer than traditional incandescent bulbs. LED bulbs and lights cost more initially but that cost can be recovered at a later stage as they consume less energy and last a long time. LED bulbs are becoming less expensive as various technology innovations are being discovered that all more of the individual LED’s to be grouped cheaply to provide efficient light.
Switching to one of the common energy efficient lighting types is easier, and more affordable than ever. The latest generations of lamp design allow CFL bulbs to be used interchangeably with traditional lamps in most cases, and you can even retrofit the old-style fluorescent tube light box with sockets for bulb CFLs easily. Halogens and LEDs still use different lamps, but their cost has dropped significantly too. What you really should be looking for is the quality of light you need to know what lamp to choose. There are charts that will show you which spectrum of light and wattage you need to do certain activities to help you save energy, and keep your eyes from straining.
While just switching your bulbs over to one of the most common energy efficient lighting types will significantly reduce the amount of energy you consume, it isn’t the only thing you should be doing to conserve energy. Practicing good energy habits is essential to saving money, and saving energy.
- Turn off lights when they are not in use.
- Only use the lights you need.
- Keep the bulbs free of dust and grime.
- Use energy efficient lamps.
The more you can do to change how you consume electricity, the better we all will be in the long run.
The light-emitting diode (LED) is today's most energy-efficient and rapidly-developing lighting technology. Quality LED light bulbs last longer, are more durable, and offer comparable or better light quality than other types of lighting.
LED is a highly energy-efficient lighting technology, and has the potential to fundamentally change the future of lighting in the United States. Residential LEDs -- especially ENERGY STAR rated products -- use at least 75% less energy, and last up to 25 times longer, than incandescent lighting.
Widespread use of LED lighting has a large potential impact on energy savings in the United States. By 2035, the majority of lighting installations are anticipated to use LED technology, and energy savings from LED lighting could top 569 TWh annually by 2035, equal to the annual energy output of more than 92 1,000 MW power plants.
How LEDs are Different
LED lighting is very different from other lighting types such as incandescent and CFL. Key differences include:
- Light Source: LEDs are the size of a fleck of pepper, and can emit light in a range of colours. A mix of red, green, and blue LEDs is sometimes used to make white light.
- Direction: LEDs emit light in a specific direction, reducing the need for reflectors and diffusers that can trap light. This feature makes LEDs more efficient for many uses such as recessed downlights and task lighting. With other types of lighting, the light must be reflected to the desired direction and more than half of the light may never leave the fixture.
- Heat: LEDs emit very little heat. In comparison, incandescent bulbs release 90% of their energy as heat and CFLs release about 80% of their energy as heat.
- Lifetime: LED lighting products typically last much longer than other lighting types. A good quality LED bulb can last 3 to 5 times longer than a CFL and 30 times longer than an incandescent bulb.
LED Products
LED lighting is available in a wide variety of home and industrial products, and the list is growing every year. The rapid development of LED technology has resulted in increased product availability, improved manufacturing efficiency, and lower prices. Below are some of the most common types of LED products.
Industrial and Commercial Lighting
The high efficiency and directional nature of LEDs makes them ideal for many industrial uses. LEDs are increasingly common in street lights, parking garage lighting, walkway and other outdoor area lighting, refrigerated case lighting, modular lighting, and task lighting.
Under-Cabinet Lighting
Because LEDs are small and directional, they are ideal for lighting tight spaces such as countertops for cooking and reading recipes. Since there can be variation in light colour and directionality, it is important to compare products to find the best fixture for your space.
Recessed Downlights
Recessed downlights are commonly used in residential kitchens, hallways, and bathrooms, and in a number of office and commercial settings. DOE estimates there are more than 600 million recessed downlights installed in U.S. Homes and businesses.
LED Replacement Bulbs
With performance improvements and dropping prices, LED lamps can affordably and effectively replace 40, 60, 75, and even 100-Watt incandescent bulbs. It's important to read the Lighting Facts Label to make sure the product is the right brightness and colour for its intended use and location.
LED Holiday Lights
LEDs consume far less electricity than incandescent bulbs, and decorative LED light strings such as Christmas tree lights are no different. Not only do LED holiday lights consume less electricity, they also have the following advantages:
- Safer: LEDs are much cooler than incandescent lights, reducing the risk of combustion or burnt fingers.
- Sturdier: LEDs are made with epoxy lenses, not glass, and are much more resistant to breakage.
- Longer lasting: The same LED string could still be in use 40 holiday seasons from now.
- Easier to install: Up to 25 strings of LEDs can be connected end-to-end without overloading a wall socket.
It is well known that the scope for energy conservation in India is enormous. There are huge gains to be made by upgrading technology, equipment and appliances in a wide range of applications – furnaces, motors, insulation systems, automobile engines, cooking burners, power generating systems, and so on. However, what is less well known is that the energy intensity of GDP in India has been declining ever since the introduction of economic reforms in 1991. A key question is whether India will realise some of its potential for energy conservation and thereby continue to reduce the energy intensity of its economy.
Energy consumption at the national level
In recent work (Sengupta 2012), I have looked at how different energy-consuming sectors1 of the economy respond to changes in the price of energy and changes in their own income (known as partial elasticities). Taking these responses, I have projected how companies will respond to forecasted changes in India’s economy, allowing me to project the energy-intensity of India’s economy up until 2032.
Table 1 gives these results with 2009-2010 as base for the four scenarios of GDP growth rates of 8% and 6% combined with no rise in the real price of energy beyond 2009-2010 and a 3% annual increase in real energy prices. As these have been based on the post-reform data of the period 1989-1990 to 2009-2010, these results strongly indicate that India has been already moving along an energy-conserving growth path and the trend looks set to continue.
Table 1. Energy intensity of GDP (gm/Rs) for 8% GDP growth and 6% GDP growth Scenarios
Year | Real Price of Energy Index change of 0% | Real Price of Energy Index change of 3 % | ||
| 8% GDP | 6% GDP | 8% GDP | 6% GDP |
2009 | 0.065 | 0.065 | 0.065 | 0.065 |
2021 | 0.047 | 0.053 | 0.039 | 0.045 |
2031 | 0.038 | 0.045 | 0.026 | 0.033 |
Energy consumption at the industrial level
While at the individual industry level there has been a general decline in the energy intensity of production, future sustainable development requires further energy conservation at the level of the individual firm. This is important since many firms across various industries are inefficient by either national or international standards. In a recent study with Manish Gupta (Manish and Sengupta 2012), I find that the seven most energy-intensive industries in India each have high energy-saving potential. I find the potential for energy saving as percentage of the actual consumption to be in the ranges2 of 46%-88% for textiles, 43%-94% for paper and pulp, 51%-92% for iron and steel, 26%-94% for fertiliser, 37%-95% for chlor-alkali, 3%-84% for cement and 9%-58% for aluminium.
The study further assesses the behavioural response of firms in these seven energy-intensive industries to changes in the price of energy and other factors. Our estimates suggest that a 10% increase in the price of energy would result in a reduction in the demand for energy in the range of 2.99% (Iron and Steel) to 12.29% (Chlor Alkali) depending on the elasticity value in the selected industries3 and 9.9% for the entire registered manufacturing sector. Thus, any energy price rise would result in energy conservation in these industries, although its impact on the demand for capital is ambiguous. These results caution us against the common perception that energy conservation would necessarily be capital-intensive in the Indian situation. More capital-intensive technology uses more energy in several manufacturing industries like cement, iron and steel, textiles and all manufacturing.
Energy consumption in other sectors
Although industry receives most of the attention in energy conservation discussions because of its large share in total energy consumption, there is also huge scope for saving energy in other sectors such as agriculture, transport and lighting, though modernisation of machinery, equipment and infrastructure. In machinery, such as various types of motors, drives, capacitors, and buildings there is an energy saving potential of 10% to 20%. Meanwhile, in lighting of all kinds of commercial and institutional establishments there is the potential to reduce energy consumption by 50% to 60% and the use of efficient pump sets in agriculture has the potential to reduce energy consumption by 30% (Lenora 2010).
In the residential sector, switching to the use of more efficient refrigerators and air-conditioners is also going to be important for energy conservation as there will likely be fast growth in use of these energy-intensive appliances by India’s growing middle class. Solar hot water systems and solar cook stoves also deserve to be promoted in the interest of saving fossil fuels and energy.
Finally, inter-city transport offers substantive scope for energy conservation by switching from road to rail and from private to public transport, especially if public transport runs on electricity. For this to happen there must be a change in transport and urban development policies as a complement to energy policy.
Energy consumption in electricity supply
While electricity is a high quality, clean and efficient fuel used widely across every segment of the economy and society, the power sector causes substantial material and energy losses and pollution in the process of its generation, transmission and distribution. The total energy loss as a share of throughput energy in the electricity industry in 2009 was of the order of 78.5%. The reduction of such losses is of critical importance for supply side efficiency improvement in the power sector. This can be achieved through higher boiler efficiency of coal-fired subcritical units and oil-based thermal units in the range of 35 to 38% efficiency and also by the upgrading of the Combined Cycle Gas Turbine (CCGT) to the range of 45% to 60% conversion efficiency. Apart from raising the conversion efficiency, the efficiency on the supply side can also be improved by reducing auxiliary losses from 6.8% on average for all types of plant technologies to 5% and the transmission and distribution losses from 25.8% in 2005 to 15% in 2031. India’s power sector reforms are supposed to provide an enabling legal and institutional framework so that the unbundled generating and distributing companies can work efficiently. However, the persistence of political interference in tariff setting and cross-subsidisation of power for agriculture and household sectors are standing in the way of diffusion of power-conserving technologies both in the end-use non-energy sector and in the energy conversion in the supply side of the power sector.
References:
1. Witte L.C., Schmidt P.S. And Brown D.R., Industrial Energy Management and Utilization, Hemisphere Publ., Washington,1988.
2. Callaghan P.W., Design and Management for Energy Conservation, Pergamon Press, Oxford, 1981.
3. Murphy W.R. And McKay G., Energy Management, Butterworths, London,1987.