Unit - 3
Thermal systems
Thermal energy storage systems are very cost-effective compared to other storage technologies. In terms of environmental impact, it is a clean energy storage technology. Thermal energy storage systems are a suitable storage method for large buildings. Thermal energy storage systems are generally used in small-scale applications for hot water and heating. It is also used in the field of electrical energy generation in large-scale applications. Thus, electricity generation is realized with the stored heat energy during periods of intense power demand. Thanks to thermal energy storage systems, short-term high load demands can be responded quickly. Storage is made at high temperatures in thermal energy storage systems. While electricity is produced with high temperature, residential heating can be performed with the heat at the turbine outlet. Thus, every process of thermal transformation is utilized. Thermal energy storage systems have low initial investment and maintenance costs. Thermal energy storage systems should be specially designed according to the application area. Compressor, pump, storage tank, and distribution lines are installed according to the application area requirement. Optimum thermal energy storage feasibility for the application site is achieved with a rational design.
The peak loads in a region can be met with thermal energy storage systems. The thermal energy storage unit operator determines the peak load times and activates the system, thus reducing the load on the grid. In addition, the cost of electricity at high tariff rates is reduced by using a thermal energy storage system. On the contrary to this process, heat is added to the thermal energy storage system in the period when electricity prices are low. There is no fuel cost in thermal energy storage systems with solar collector since the energy source is solar.
Thermal energy storage systems are most commonly used to heat or cool a particular area. It is preferred for the water heating in residential or industrial application areas. Thermal energy storage is widely used in agricultural application, especially in greenhouses. It is also used in water pumping systems in the agriculture. Other areas of use are small power plants.
Classification of steam generators
The creation of the steam generator, or boiler, converted normal existence lengthy earlier than digital improvements did, and arguably had an extra usual effect than greater current improvements inclusive of as on-line commerce, social media and wi-fi technology. It is difficult to realize now simply how a lot of a game-changer it became which will get from region to region without both private or animal (e.g., horse-drawn carriage) energy.
On its face, the manufacturing of steam on reason looks as if an odd choice.
Looking at the sector the manner a younger baby might, steam seems to be little greater than a compulsory watery waste fabricated from numerous tactics regarding warmness era, from cooking a container of pasta to warming the corridors of a building.
The first-class manner to narrate your thoughts to the price of nicely harnessed steam is to photo what takes place while something that has steam billowing from its miles abruptly capped or in any other case bodily averted from emitting that steam – for example, clamping a lid tightly down on a pot of boiling water for even a 2nd earlier than freeing it.
The Basics and Origins of Steam Power Steam is water vapor, or greater generally, the gaseous shape of the molecule.
Water includes hydrogen and oxygen atoms and has a molecular system of H2O. Like different depend with a selected boiling point, water is capable of input the gaseous segment while it reaches that temperature (for water, a hundred C, or stages Celsius (212 F, or stages Fahrenheit) and receives a tiny electricity push so it could conquer its warmness of vaporization, a type of toll that depend normally has to pay to extrude among states (solid, liquid or today, steam's maximum critical full-size function is with inside the era of electrical energy.
But lower back with inside the overdue 1600s, it became observed that it became less difficult to take away waste water from mines while it became condensed.
In the system, it became observed that the system of water condensing creates a vacuum (bad stress on the subject of anything lies out of doors the vicinity of condensation activity). This locating became ultimately included into cutting-edge steam engines and generators.
Types of Steam Generators
Fire tube
These are most customarily utilized in tactics that want everywhere from 15 to 2,2 hundred horsepower (1 hp = 746 watts, or W). This sort of boiler is cylindrical, with the flame with inside the furnace hollow space itself and the combustion gases themselves stored inner a sequence of tubes. These are available in fundamental designs: dry lower back and moist lower back.
Water tube
In this arrangement, tubes include steam, water or both, even as the goods of combustion by skip across the out of doors of tubes. These frequently have more than one unit of drums, and due to the fact, they use incredibly little water, those boilers provide strangely speedy steaming capabilities. Commercial. These normally characteristic combos of water tube, fire tube and electric powered-resistance designs.
They are famous in huge homes requiring a typically steady temperature, inclusive of colleges and libraries, workplace and authorities’ homes, airports, condo complexes, university and different studies laboratories hospitals, and so on.
Condensing
Condensing boilers can attain thermal performance tiers of two ninety-eight percentage, in comparison to 70 to eighty percentage plausible the usage of well-known boiler designs.
Typical performance tiers attain approximately ninety percentage while the go back water temperature is at a hundred and ten F or lower, and upward push with lowering water-go back temperature thereafter.
Flexible water tube (flex tube)
This production is in particular resistant to "warmness shock," making it an herbal choice for heating uses. Flexible water tube boilers are available in a huge variety of gasoline inputs and are well-ideal for low-stress packages the usage of both steam and warm water. (Not all "boilers" without a doubt boil water!) These also are pretty clean to maintain, with clean get right of entry to their operating components from the out of doors.
Electric
These boilers are famously low-effect: clean, quiet, clean to install, and small on the subject of their utility. Because not anything is without a doubt burned (that is, there may be no flame to fear approximately), electric powered boilers are marvellously simple. There aren't any fuels or gasoline dealing with device with inside the mix, and subsequently no exhaust and no want for related pipes and ports. In addition, those have heating factors which can be clean to replace.
Heat restoration steam generator (HRSG)
This is a progressive electricity-restoration "warmness exchanger" that recovers warmness from a circulate of warm fuelling passing through. These create steam that may be used to power a selected a system or used to power a steam turbine to energy strength era the usage of an electromagnet. HRSGs are constructed on a basis of 3 number one components – an evaporator, a super heater and an economizer.
Steam as Nuclear Reactor Fuel
Nuclear energy plant life use electricity now no longer from the combustion of gasoline however through the mechanical separation of its tiniest components. That is a totally slight manner of describing nuclear fission, wherein atoms (on this case, the ones belonging to the detail uranium) are damaged into smaller atoms, freeing full-size quantities of electricity. The electricity launched through fission is captured and used to warmness and boil water, and the ensuing steam is used to energy a turbine for the reason of strength era.
Fire tube boiler
A hearth place-tube boiler is a kind of boiler wherein warm gases by skip from a hearth place via one or greater tubes strolling via a sealed field of water.
The warmth of the gases is transferred via the partitions of the tubes with the aid of using thermal conduction, heating the water and in the long run growing steam.
The hearth place-tube boiler advanced because the 0.33 of the 4 principal ancient forms of boilers: low-strain tank or "haystack" boilers, fluid boilers with one or massive flues, hearth place-tube boilers with many small tubes, and high-strain water-tube boilers.
Their benefit over fluid boilers with an unmarried massive flue is that the various small tubes provide some distance more heating floor place for the identical average boiler volume.
The well-known creation is as a tank of water penetrated with the aid of using tubes that bring the recent flue gases from the hearth place.
The tank is typically cylindrical for the maximum part
Being the most powerful sensible form for a pressurized field
And this cylindrical tank can be both horizontal and vertical.
This kind of boiler changed into used on without a doubt all steam locomotives with inside the horizontal "locomotive" shape. This has a cylindrical barrel containing the hearth place tubes, however additionally has an extension at one stop to residence the "firebox".
This firebox has an open base to offer a massive grate place and regularly extends past the cylindrical barrel to shape a square or tapered enclosure.
The horizontal hearth place-tube boiler is likewise regular of marine applications, the usage of the Scotch boiler; thus, those boilers are generally stated as "scotch-marine" or "marine" kind boilers.
Vertical boilers have additionally been constructed of the couple of hearth place-tube kind, even though those are relatively rare; maximum vertical boilers have been both fluids, or with pass water-tubes.
Fire Tube boiler is the best shape of the inner furnace, vertical hearth place tube boiler. Fire tube boilers are a transportable boiler and it calls for a small ground area. The steam score in hearth place tube boilers doesn’t exceed 2500 kg in line with hour and strain is restricted to ten bars.
A hearth place-tube boiler is a kind of boiler wherein warm gases by skip from a hearth place via one or (many) greater tubes strolling via a sealed field of water.
The hearth place-tube boiler advanced because the 0.33 of the 4 principal ancient forms of boilers: low-strain tank or “haystack” boilers, fluid boilers small tubes provide a miles more heating floor place for the identical average boiler volume.
The well-known creation is as a tank of water penetrated with the aid of using tubes that bring the recent flue gases from the hearth place.
This kind of boiler changed into used on without a doubt all steam locomotives with inside the horizontal “locomotive” shape.
This has a cylindrical barrel containing the hearth place tubes, however additionally has an extension at one stop to residence the “firebox”.
This firebox has an open base to offer a massive grate place and regularly extends past the cylindrical barrel to shape a square or tapered enclosure.
The horizontal hearth place-tube boiler is likewise regular of marine applications, the usage of the Scotch boiler; thus, those boilers are generally stated as “scotch-marine” or “marine” kind boilers.
Vertical boilers have additionally been constructed of the couple of hearth place-tube types, even though those are relatively rare; maximum vertical boilers have been both fluted or with pass water-tubes.
Fire Tube Boiler Construction
Fire tube boiler includes a vertical, cylindrical shell, prepared with a firebox with inside the bottom, water area with inside the centre element and steam area with inside the higher element.
The hearth place grate is located at the lowest of the firebox and coal is fired on the firebox. An ash pit is positioned at the lowest of the grate to acquire the ash of burnt coal, that's periodically removed.
One or greater pass tubes are both flanged or riveted to the water area are positioned with inside the firebox to growth the heating floor place to enhance the water stream.
A brief chimney is attached on the pinnacle of the firebox to discharge the waste flue exhaust gases at a few more height.
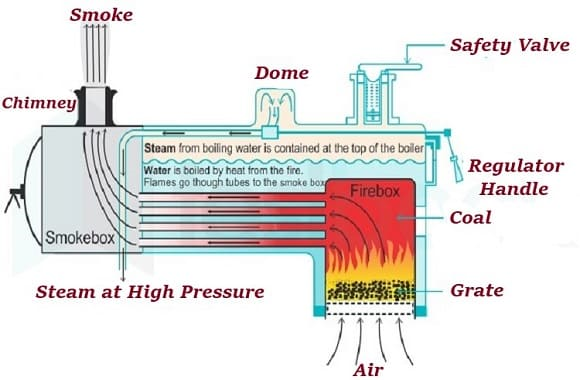
Manhole and hand holes are supplied for cleansing the indoors of the boiler shell and pass tubes.
The boiler includes a strain gauge, water degree indicator, protection valve, steam forestall valve, and a manhole as mountings to offer protection and simplicity of working.
Fire Tube Boiler Working
Fuel burns at the grate with inside the firebox. The ensuing warm flue gases are allowed to by skip across the pass tubes.
The water surrounding the cylindrical firebox additionally gets warmth with the aid of using convection and radiation.
Thus, steam is produced.
The water stream with inside the boiler relies upon at the density distinction in water, created with the aid of using the temperature distinction in water.
Water tube boilers:
Steam is one of the top notches reasserts of electricity for our contemporary-day age. We have used steam from the very starting of our first business revolution in human history.
It gives warmness for system heating, sterilization, and lots of different packages which can be more and more vital to business facilities, amongst others.
A boiler or steam generator is a tool used to create steam with the aid of using making use of warmness electricity to water.
Different kinds of boilers are to be had in numerous sizes and bureaucracy and discover their use in numerous packages.
The water tube boiler is one in all them this is implemented broadly in industries. In this article, we’re going to have an outline of water tube boilers along with operation, components, types, blessings, and drawbacks. Read this new weblog on Liquid to discover extra.
Water Tube Boilers Features
The water tube boiler represents one of the numerous pressurized gadget alternatives used to transform water into steam below managed conditions.
A manner to swiftly produce steam is to feed the water below stress right into a tube or tubes surrounded with the aid of using the combustion gases.
The earliest instance of this become evolved with the aid of using Goldsworthy Gurney with inside the overdue 1820s to be used in steam avenue carriages.
Modern excessive capability boilers are of water tube kind.
Basically, on this boiler, water may be flown with inside the tubes surrounded with the aid of using flue gases.
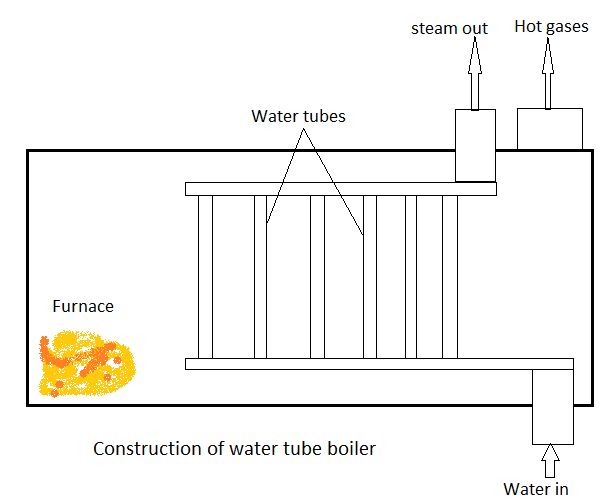
More steam is generated with the aid of using the usage of this boiler, so the general performance of the boiler is excessive.
The capacity of water tube boilers to be designed without using excessively massive and thick-walled stress vessels makes those boilers in particular appealing in packages that require:
An excessive steam output (as much as 500 kg/s) High-stress steam (as much as a hundred and sixty bar)
Superheated steam (as much as 550°C)
The water tube boiler is not unusual place in papermaking, sugar, and different Industries that call for electric electricity and steam.
Owing to their brilliant operating properties, using water tube boilers is surprisingly desired with inside the following main areas: Variety of system packages in industries Chemical processing divisions Pulp and Paper production plant life
The massive generators of application companies
Refining units Water Tube Boiler Components Here is evaluate of the water tube boiler components and functions.
Boiler Shell: This shell is the outside cylindrical a part of a stress container.
Steam drum: It is a set vessel for steam and water.
Mud drum: This is a cylindrical fashioned area at the bottom of the water area. It will collect impurities like dust, sediment, and others.
Water walls: It is a tubing association across the furnace to extract warmness from gasoline to generate steam.
Furnace: An enclosed area supplied for the combustion of gasoline.
Safety valve: It reveals a use for preventing the needless pressure from the development of a boiler.
Strainer: This is a form of tool as a clear out to keep strong factors permit a fluid deliver.
Sight glass: A glass tube is applied on steam kind boilers for giving observable symptoms and symptoms of the water degree in boilers.
Steam prevent valve: It controls the steam float deliver outside.
Feed takes a look at valve: The excessive-pressure water flows thru this valve, which releases to the boiler actually and materials the water to the water kind boiler.
Burner: This is one form of tool for the start of air and gasoline right into a boiler on the desired velocity. It is the maximum important equipment for the firing of fuelling or oil.
Economizer: Accessory used to get better the warmth of flue fuelling that leaving the boiler with the aid of using heating feed water.
Superheater: It reveals use to growth the temperature of the steam. Working
Principle of Water Tube Boilers
Let’s realize approximately the operating precept of a water tube boiler, and it'll assist you to recognize its blessings and drawbacks clearly. The Feed Water is authorized with inside the steam drum with the aid of using a feed take a look at valve.
- The water travels to the dust drum wherein any undesirable debris will settle at the lowest of the dust drum.
- The water flow is maintained with the aid of using circulating tubes and steam stress is maintained with the aid of using equalizing tubes.
- The gasoline this is burnt with inside the firebox over the grate produces warm flue gases that journey over the water tubes giving its temperature.
- For the right passage of warm flue gases over the water tubes baffle plates are arranged.
- The heated water generates excessive-stress steam used for the manufacturing of electricity.
- To growth the economic system of the boiler, exhaust gases additionally discover use to preheat combustion air blown into the burners and to heat the feed water deliver in an economizer.
Types of Water Tube Boilers
Here is a listing of water tube boiler types: Babcock and Wilcox boiler: Designed with the aid of using the American company of Babcock & Wilcox, this boiler reveals use in desk bound and marine engines. It completely reveals use whilst the stress above 10 bar and steam producing capability extra than 7000 kg/hr is required.
Sterling boiler:
This boiler is an early shape of water tube boilers, used to generate steam in massive land-primarily based totally desk bound plant life. They have become full-size in industries that produced flammable waste and required system steam. Sterling boilers are one in all the bigger preparations for a water tube boiler.
Simple vertical boiler:
These boilers discover use in steam electricity-pushed automobiles in addition to cell machines like railway steam engines, steam tractors, Steam shovels, and steam cranes.
Keep that during mind, opposite to famous perception that a locomotive boiler is a water tube boiler, you higher realize that it’s a hearth place tube boiler, and it isn't a water tube boiler instance.
Water Tube Boilers Pros
- Significant blessings of a water tube boiler gadget include:
- Safe and clean operation
- Fast response to steam call for
- Provides surprisingly green performance, as much as 90% with an economizer
- Rapid warmness transmission
- Requires much less ground place for a given output
- Can be effortlessly transported
- Easy get admission to all components for cleaning, inspecting, and repairing
- Can tolerate excessive steam pressures
- Large evaporative capacity
Water Tube Boilers Cons
Few obstacles related to using water tube boiler plant life include:
- High preservation cost
- Complicated and time-eating set up procedure
- Cannot be synthetic in packaged shape
- Uneconomical for small industries
High pressure boilers
An excessive stress boiler is a shell and tube warmness exchanger that use boiled water to create steam or excessive stress warm water. Using water crammed tubes in a metallic tank or enclosure, they devise electricity with the aid of using changing water into steam thru thermal power, that's used to electricity equipment.
The stress and steam of an excessive stress boiler is produced with the aid of using burning a gasoline, inclusive of coal, herbal fuelling, or petroleum.
The heated gases, from the burning gasoline, are circulated with the aid of using herbal convection or pressured with the aid of using a pump.
Forced circulate is produced with the aid of using a centrifugal pump to growth the evaporation charge to 210 ok of pressure in step with rectangular centimetre. Natural circulate is tons greater restricted and has a decrease pressure in step with rectangular centimetre. Two kinds of the boiler techniques are water tube and hearth place tube.
The majority of boilers paintings the usage of the equal precept of heated water generating steam.
The versions among the differing types are their geometric orientation, outside or inner hearth place, stress, water circulate, variety of tubes, and the circulate of gases. The geometric orientation of a boiler may be horizontal, vertical, or willing with hearth place outdoor or inside, relying at the boiler ‘s design.
The department of mega Pascal stress (MPa) determines whether or not a boiler is low and excessive stress. Boilers that produce stress above eighty MPa are taken into consideration to be excessive stress. Low stress boilers have an MPa beneath eighty MPa.
Water circulate may be pressured or herbal. If the water is pumped, its miles pressured. If it's miles herbal, it's miles with the aid of using convection. Gas circulate is decided with the aid of using the form of tubing, which may be hearth place or tube. With hearth place tube, warmness movements thru tubes with inside the water.
In water tubing, water movements thru the tubes. Tubing for a boiler may be both unmarried and a couple of. The conventional Cornish boiler is an instance of an unmarried tube boiler because it has simplest one hearth place tube.
There is an extended listing of boilers which have a couple of tubes, that's current boiler design.
Types of High-Pressure Boilers
La Mont Boiler:
The Lamont boiler is a pressured convection water tube boiler that makes use of a pump to flow into water. It has an economizer to shop on power and growth efficiency, a boiler drum, super heater, evaporator, and air preheater. The combustion chamber for a La Mont Boiler is vertical.
Water is pumped thru the economizer and preheater into the boiler drum. The boiler drum serves as a steam separator. The pump pushes the water to a distributor header that has nozzles to ship the feed water into the evaporator tubes positioned with inside the partitions of the boiler to growth floor heating.
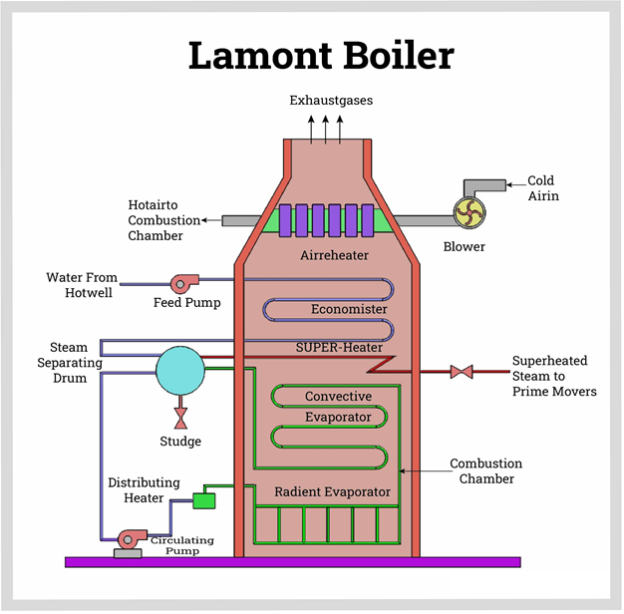
The water and steam pass into the boiler drum, wherein the steam is separated and exceeded to the super heater and directly to the turbine.
The super heater will increase the temperature of the saturated steam to save you water droplets from getting into the turbine.
Benson Boiler:
The Benson boiler has a number of the equal functions because the La Mont boiler without a steam separator and works below essential stress.
It is a water tube, pressured circulate boiler, wherein the feed water is compressed to supercritical stress to save you the formation of bubbles with inside the water tube. The compressed water feed will increase the density of the water such that its density and that of the steam emerge as the equal, which reduces the latent warmness with inside the water to 0 making it less complicated to transform to steam.
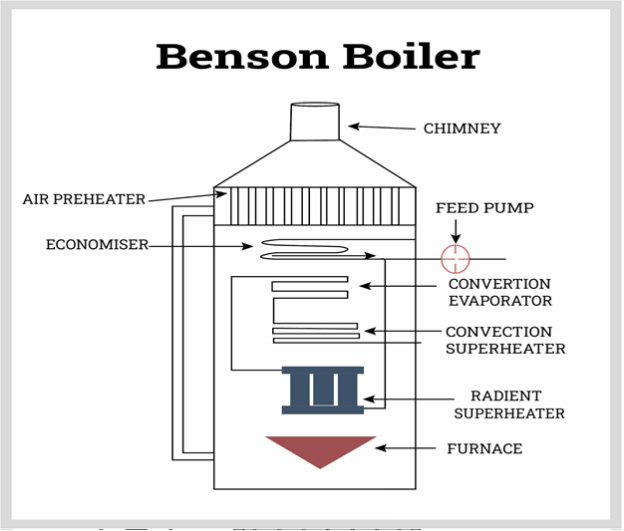
The characteristic of the air preheater, economizer, super heater, evaporator, and combustion chamber are the equal. Unlike the La Mont boiler, the combustion chamber may be installed vertically or horizontally.
Loffler Boiler:
The Loffler boiler became advanced to solve a hassle with the La Mont boiler, which became salt and sediment build-up at the floor of the water tube and decreased warmness switch. Like the Benson boiler, water is circulated below excessive stress with inside the water tube. The Loffler boiler has radiant and convective super heaters that paintings collectively to distribute the steam to the turbine.
The radiant super heater heats the saturated steam the usage of radiant power produced with the aid of using the burning gasoline and is wherein warmness switch takes place.
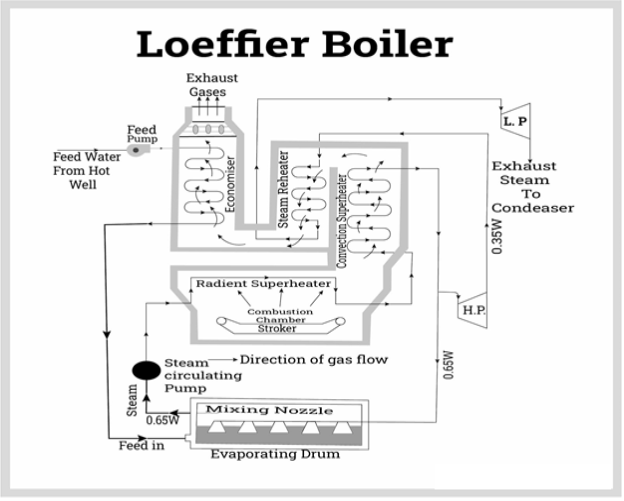
The steam then passes thru the convective super heater this is heated with the aid of using the flue gases, which similarly heats the steam earlier than it passes directly to the turbine.
Velox Boiler:
The Velox boiler is a pressured circulate water tube boiler that makes use of excessive pace to unexpectedly produce steam.
The precept of the Velox boiler is constructed on the speed of the fuelling, which movements quicker than the velocity of sound and will increase the charge of warmth switch.
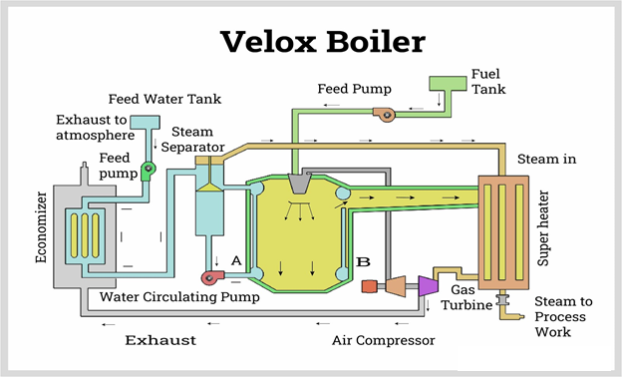
The Velox boiler has a fuelling turbine compressor that sends compressed air into the combustion chamber, wherein greater warmness is released. The extended charge of warmth launch complements the flue gases pace to the velocity of sound.
The flue gases by skip from the hearth place tubes at the lowest of the combustion chamber and surround water crammed tubes. Water is pressured from the economizer to the circulating pump at excessive pace inflicting the warmth to switch from the gases to the water very unexpectedly.
The water and steam pass to the water separator and directly to the super heater. As with the Loffler boiler, the flue gases are used to warmness the super heater.
Cornish Boiler:
The Cornish boiler is the most effective shape of boiler. It is a hearth place tube boiler that has an extended horizontal tube with an unmarried flue that carries the hearth place.
The cylindrical shell of a Cornish boiler is one to 2 meters in diameter and may be 4 to seven meters long.
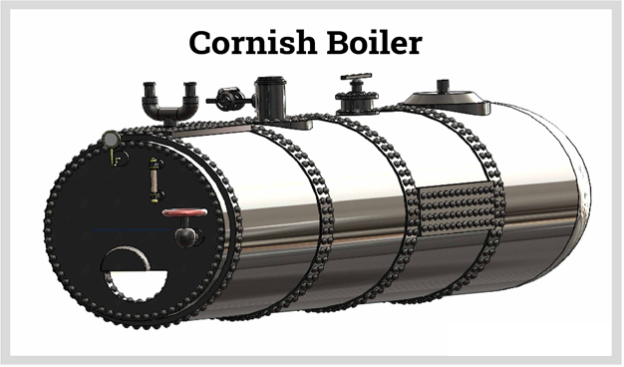
The gasoline for a Cornish boil is loaded right into a grate thru a door, wherein it burns to supply warm gases that pass into the hearth place tube this is surrounded with the aid of using water, wherein the water is heated to supply steam.
Cornish Boiler Babcock and Wilcox Boiler:
The Babcock and Wilcox boiler is a water tube horizontal boiler with herbal draft circulate and a couple of tubing. Water enters the tubes with the aid of using a down take header, is heated with the aid of using warm flue gases and movements in a zigzag style pressured with the aid of using baffle plates.
The steam with inside the tubes movements to an uptake header, wherein its miles accumulated in a boiler drum.
An anti-priming pump filters the steam to get rid of any water droplets in order that simplest steam is dispatched to the super heater, which will increase the temperature of the steam. The steam from the super heater is accumulated or dispatched directly to the turbine.
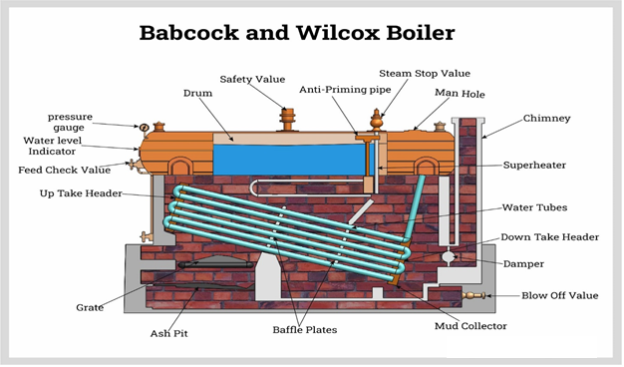
Boiler mountings and accessories.
The boiler mountings are fittings which might be installed at the boiler for its right functioning.
Mountings are water stage indicator, protection valve, stress gauge, etc.
It can be mentioned that a boiler cannot characteristic thoroughly without the mountings.
The boiler add-ons are the gadgets, which shape an essential a part of a boiler however isn’t installed on it.
They consist of super heater, economizer, feed pump etc.
It can be mentioned the add-ons assist in controlling and going for walks the boiler efficiently.
Boiler Mountings
Following are the essential boiler mountings:
- Water stage indicator
- Pressure gauge
- Safety valve
- Stop valve
- Blow off
- Feed takes a look at valve
- Fusible plug
Water Level Indicator
It is a protection tool upon which secure running of the boiler depends. Water stage indicator diagram
Working Principle
Water-tube indicator the water includes a vertical tough glass tube G that is geared up with gunmetal tubes A and B.
The tubes A connects the steam area of the boiler with the glass tube and the tube B connects the water area of the boiler with the glass tube. The tube A is supplied with a valve ‘S’, referred to as a steam valve, and tube B is geared up with any other valve ‘W’, referred to as a water valve.
In addition to those valves, a 3rd valve, referred to as drain valve, is suited for the water stage indicator via which water collectively with condensed steam from the gunmetal tube A is tired from time to time.
Pressure Gauge
Pressure gauges are used to degree the stress of steam interior a steam boiler. The stress gauge is constant in the front of a steam boiler. Pressure Gauge diagram
Working Principle
The stress gauge proven in fig is bourdon stress gauge. It includes a round spring tube A.
One gives up of the bourdon tube is closed and related to a hyperlink L and the opposite give up is squared to a Hollow block B.
The hyperlink L connects the closed give up of the tube to the toothed region C that is hinged at O.
The toothed region gears with pinion D which includes a pointer P. The pointer actions on a dial graduated in stress units.
Safety valves
These are the gadgets connected with inside the steam boiler for stopping explosions because of immoderate inner stress of steam.
Safety Valve diagram
The protection valve is a device which prevents the boiler stress from growing above its ordinary running stress with the aid of using routinely beginning whilst the boiler stress exceeds the ordinary running stress,
Thus, permitting extra steam to break out into the environment till the stress comes right all the way down to its ordinary valve.
Thus, a protection valve guarantees protection to a boiler from being broken because of immoderate steam stress.
- The protection valves usually used are:
- Deadweight protection valve,
- Lever protection valve,
- Spring-loaded protection valve,
- Steam prevent valve
The characteristic of a prevent valve is to govern the float of the steam from with inside the boiler and to prevent it absolutely whilst required.
A prevent valve or junction valve is used to adjust the float of steam from the boiler.
Steam Stop Valve diagram
The valves installed at the boilers, which alternate the route of float of steam with the aid of using 90° are referred to as junction valves, even as valves geared up in pipelines which permitting the steam with inside the identical route are referred to as prevent valve.
Blow-off Valve
The characteristic of a blow-off valve is to take away periodically the sediments deposited at the lowest of the boiler even as the boiler is in operation and to drain the boiler even as its miles being wiped clean or inspected.
Blow off Valve or Cock –
Boiler Mountings and Accessories When the blow-off valve is opened the water that is beneath Neath the stress of steam, rushes out with high-quality speed accordingly wearing out the sediments together with it.
Feed Check Valve
When the extent of water with inside the boiler falls, its miles added returned to the desired stage with the aid of using providing the extra water referred to as feed water.
The stress in the boiler could be excessive consequently the stress of the feed water must be raised with the aid of using a pump earlier than its miles fed into the boiler.
The feed water beneath Neath excessive stress is fed into the boiler via the feed take a look at valve.
The characteristic of a feed takes a look at valve is to govern the float of water from the feed pump to the boiler and to save you the backflow of water from the boiler to the pump whilst the pump stress is much less than the stress or whilst the feed pump ceases to work.
Evidently feed take a look at valve is located on the boiler give up of the transport pipe of the feed pump. Fusible Plug
Fusible Plug –
The plug is made from tin or leads alloy, which has a low melting point.
The characteristic of the fusible plug is to put-off the hearth place with inside the furnace of the boiler whilst the water stage falls beneath Neath and risky stage and accordingly avoids the explosion, which might also additionally take region because of overheating of the tubes and the shell. It is geared up over the crown of the furnace or the combustion chamber.
Boiler Accessories
The boiler add-ons are required to enhance the performance of the steam energy plant and to allow for the right running of the boiler.
The boiler add-ons aren’t installed at once at the boiler. The vital boiler add-ons are:
- Economizer
- Air pre-heater
- Superheater
- Feed pump
- Steam Separator
- Steam trap
Economizer
The combustion gases popping out of the boiler include a massive amount of warmth. Therefore, the most quantity of warmth from the gases have to be recovered earlier than it escapes to the chimney. Economizer - Boiler Mountings and Accessories In the economizer, heating the feed water does the recuperation of warmth with inside the flue gases.
The economizer is located with inside the direction of the gases. They enhance the general performance of the boiler with the aid of using decreasing gasoline consumption.
Air Pre-heater
The air preheater is an accent that recovers the warmth with inside the exhaust fuelling with the aid of using heating the air provided to the furnace of the boiler. Supplying preheated air into the furnace produces an excessive furnace temperature and hurries up the combustion of the gasoline.
Thus, the thermal performance of the plant could be increased.
The benefits of air pre-heater are, Increase with inside the steam technology rate. Better combustion with much less soot, smoke and ash, and Low-grade fuels may be used.
Superheater
The superheater is utilized in boilers to boom the temperature of the steam above the saturation temperature.
The dry saturated steam generated with inside the boiler is handed via a hard and fast of tubes located with inside the direction of the flue gases, wherein it'll be heated in addition with the aid of using the recent fuelling to boom its temperature approximately the saturation temperature.
Feed Pump
A feed pump is a boiler accent required to pressure the feed water at excessive stress into the boiler. Commonly used pumps are, Reciprocating pumps Rotary pumps
The reciprocating pumps are pushed at once with the aid of using coupling them to the steam engine.
The rotary pumps are pushed with the aid of using the steam mills or with the aid of using electric powered motors.
The steam distribution system is the essential link between the steam generator and the steam user. There are various methods to carry steam from a central source to the point of use. The central source might be a boiler house or the discharge from a co-generation plant. The boilers may burn primary fuel, or be waste heat boilers using exhaust gases from high temperature processes, engines or even incinerators. Whatever the source, an efficient steam distribution system is essential if steam of the right quality and pressure is to be supplied, in the right quantity, to the steam using equipment. Installation and maintenance of the steam system are important issues, and must be considered at the design stage. An understanding of the basic steam circuit or ‘steam and condensate loop’ is required (see Figure 3). As steam condenses in a process, flow is induced in the supply pipe. Condensate has a very small volume compared to the steam, and this causes a pressure drop, which causes the steam to flow through the pipes. The steam generated in the boiler must be conveyed through pipework to the point where its heat energy is required. Initially there will be one or more main pipes, or 'steam mains', which carry steam from the boiler in the general direction of the steam using plant. Smaller branch pipes can then carry the steam to the individual pieces of equipment. When the boiler main isolating valve (sometimes referred to as the ‘crown’ valve) is opened, steam immediately passes from the boiler into and along the steam mains to the points at lower pressure. The pipework is initially cooler than the steam, so heat is transferred from the steam to the pipe. The air surrounding the pipes is also cooler than the steam, so the pipework will begin to transfer heat to the air.
Steam on contact with the cooler pipes will begin to condense immediately. On start-up of the system, the condensing rate will be at its maximum, as this is the time where there is maximum temperature difference between the steam and the pipework. This condensing rate is commonly called the ‘starting load’. Once the pipework has warmed up, the temperature difference between the steam and pipework is minimal, but some condensation will occur as the pipework still continues to transfer heat to the surrounding air. This condensing rate is commonly called the ‘running load’. The resulting condensation (condensate) falls to the bottom of the pipe and is carried along by the steam flow and assisted by gravity, due to the gradient in the steam main that should be arranged to fall in the direction of steam flow. The condensate will then have to be drained from various strategic points in the steam main. When the valve on the steam pipe serving an item of steam using plant is opened, steam flowing from the distribution system enters the plant and again comes in contact with cooler surfaces. The steam then transfers its energy in warming up an equipment and product (starting load), and, when up to temperature, continues to transfer heat to the process (running load). There is now a continuous supply of steam from the boiler to satisfy the connected load and to maintain this supply more steam must be generated. In order to do this, more water (and fuel to heat this water) is supplied to the boiler to make up for the water which has previously been evaporated into steam. The condensate formed in both the steam distribution pipework and in the process, equipment is a convenient supply of useable hot boiler feedwater. Although it is important to remove this condensate from the steam space, it is a valuable commodity and should not be allowed to run to waste. Returning all condensate to the boiler feed tank closes the steam energy loop, and should be practiced wherever practical.
The distribution pressure of steam is influenced by a number of factors, but is limited by: ß the maximum safe working pressure of the boiler ß the minimum pressure required at the plant as steam passes through the distribution pipework, it will inevitably lose pressure due to: ß Frictional resistance within the pipework ß Condensation within the pipework as heat is transferred to the environment. Therefore, allowance should be made for this pressure loss when deciding upon the initial distribution pressure. A kilogram of steam at a higher pressure occupies less volume than at a lower pressure. It follows that, if steam is generated in the boiler at high pressure and also distributed at a high pressure, then the size of the distribution mains will be smaller than that for the same heat load. Generating and distributing steam at higher pressure offers three important advantages: ß the thermal storage capacity of the boiler is increased, helping it to cope more efficiently with fluctuating loads, minimizing the risk of producing wet and dirty steam. ß Smaller bore steam mains are required, resulting in lower capital cost, for materials such as pipes, flanges, supports, insulation and labour. ß Smaller bore steam mains cost less to insulate. Having distributed at a high pressure, it will be necessary to reduce the steam pressure to each zone or point of use in the system in order to correspond with the maximum pressure required by the application. Local pressure reduction to suit individual plant will also result in drier steam at the point of use.
A Steam trap an automatic drain valve which distinguishes between steam and condensate. A steam trap holds back steam & discharges condensate under varying pressures or loads. The steam traps should have good capacity to vent out air and other non-condensable gases quickly while holding back the live steam.
Why steam traps are used?
Steam generated by a boiler contains heat energy which is used to heat the product. When steam loses it energy by heating the product, condensate is formed. Also, a part of energy contained by steam is lost through radiation losses from pipes and fittings. After losing this heat, steam gets converted into condensate. If this condensate is not drained immediately as soon as it forms, it can reduce the operating efficiency of the system by slowing the heat transfer to the process. Presence of condensate in a steam system can also cause physical damage due to water hammer or corrosion.
As shown in the accompanying sketch, the condensate accumulates in the bottom of a horizontal pipe with steam passing over it. As the condensate builds up, it can form a solid slug of incompressible water traveling at high velocities. When the slug of water is suddenly stopped by a pipe bend, fitting or a valve, it can result in mechanical damage to the pipe or fitting.
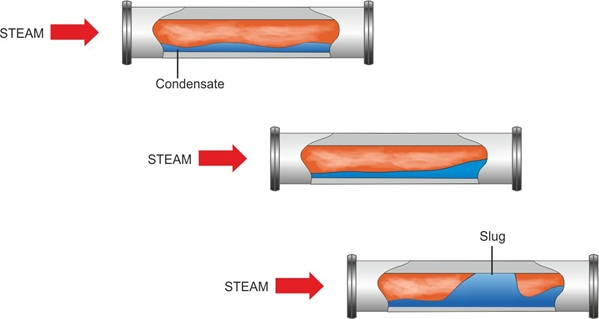
It is equally important to remove air and other non-condensable gases from the steam system for four important reasons.
(1) On start-up, steam enters the system only as fast as the air is vented.
(2) An air steam mixture has a temperature well below steam temperature lowering the heat transferred.
(3) Air is an insulator and clings to the surface of the pipe or vessel causing slow and uneven heat transfer.
(4) Dissolved in condensate, the non-condensable gases from acid which corrode the system.
Types of steam traps: Based on working principle
Over the period, different types of steam traps have been developed to suit different applications. The essential property of a steam trap is to be able to distinguish between steam and condensate. Different types of steam traps employ different working principles and mechanisms to distinguish between steam, condensate and air. When classified according to these operating principles, each design has advantages and limitations which must be considered while selecting a steam trap for a specific application.
Generally, based on the principle used to distinguish between steam and condensate, steam traps are categorized as follows-
Density Operated-Mechanical Traps
Density operated or mechanical types of steam traps distinguish between steam and condensate based on difference in their densities. Steam is always lighter and hence, has a density much lower than condensate. A mechanical type of steam trap will allow only the heavy condensate to get discharged and hold back the steam.
As we have seen, quick removal of air and other non-condensable gases is essential for proper running of steam system. Float traps come with an optional air vent which quickly removes air and other gases during start-ups.
There are two main types of mechanical steam traps which are commonly used.
a. Ball Float
Float traps or ball float traps are ideal for process heating applications. Float traps are designed in such a way that the valve seat is always submerged under water preventing any steam loss. The discharge is continuous and modulates with the condensing rate. It is unaffected by changes in inlet pressure. A separate thermostatic air vent independently purges air giving a fast start-up.
Advantages of Float Traps
- Discharge condensate continuously as rapidly as it forms
- High air venting capacity through auxiliary balanced- pressure air vent, which is self-adjusting for varying steam pressures.
- High thermal efficiency at both light and heavy loads. Continuous modulating discharge does not create pressure disturbances, which may affect control in air heating coils, shell and tube exchanges, etc.
- Steam lock release (S.L.R) Facility available
- Inline inlet and outlet facility, easy installation at low cost. Also available with vertical inlet & outlet connections
- Robust, fair resistance to water hammer.
- Wide range of orifices to suit inlet pressure.
Limitations
- Cannot be used on high degree of superheat.
- Applications subjected to freezing must be protected with insulation & SLR
- Water hammer can damage float
b. Inverted Bucket Traps
As the name explains, inverted bucket traps have an inverted bucket inside them. These are mechanical type of steam traps working on the principle of buoyancy.
1. Initially, the bucket is resting at the bottom of the steam trap and the valve seat is wide open. At star-up, air will enter the steam trap and will be discharged out through the bleed hole.
2. As condensate enters the trap, it forms a water seal inside the body. The weight of the bucket keeps the valve off its seat and so condensate can flow around the bottom of the bucket and out of the trap. Under low load or super heat conditions, the trap may need to be ‘primed’ with water before system start-up.
3. When steam enters the underside of the bucket, the bucket becomes buoyant and rises. This positions the valve lever such that the valve gets closed.
4. The bucket will lose its buoyancy as a part of the steam under the bucket condenses due to radiation losses and the remaining steam escapes through the vent hole. The weight of the bucket will pull the valve off its seat and the cycle is then repeated.
5. Inverted bucket traps discharge condensate intermittently and at steam temperature
Advantages:
Resistant to water hammer
Disadvantages:
Low loads or high super heat conditions can lead to loss of water seal. In such situations, the trap will vent live steam.
- Poor air venting capability.
- Intermittent discharge of condensate.
Temperature Operated-Thermostatic Traps
Thermostatic Steam Traps work on the temperature difference between steam and condensate. Condensate is at a temperature lower than the steam being used. Thermostatic type of steam trap has a port which is opened or closed based on the temperature of the inlet fluid. If the temperature is above the specified range, the port is closed. The port open when the temperature of the fluid falls down below the previously specified value.
Since air and other gases have a temperature much lower than that of steam, these steam traps can also be used as air vents.
Based on the actual working mechanism, they are classified as-
a. Balanced Pressure Thermostatic
b. Thermostatic
c. Liquid Expansion
d. Bimetal Expansion
Kinetic Energy Operated Steam Traps- Thermodynamic Steam Traps
Thermodynamic steam traps are operated by the principle of thermodynamics. The main principle behind the operation of thermodynamic steam traps is Bernoulli's principle.
Thermodynamic Traps are the most widely used steam traps for removing condensate from main lines largely due to their small size, wide pressure range, one moving part, and resistance to water hammer and corrosion. Because operation of each model depends on the manufacturer’s seat and disc design, results obtained by the user may vary widely.
Condensate recovery is a process to reuse the water and sensible heat contained in the discharged condensate. Recovering condensate instead of throwing it away can lead to significant savings of energy, chemical treatment and make-up water.
Condensate can be reused in many different ways, for example:
- As heated feedwater, by sending hot condensate back to the boiler’s deaerator
- As pre-heat, for any applicable heating system
- As steam, by reusing flash steam
- As hot water, for cleaning equipment or other cleaning applications
The Benefits of Condensate Recovery
Reusing hot condensate can lead to considerable savings in terms of energy and water resources, as well as improve working conditions and reduce your plant's carbon footprint.
Reduced Fuel Costs
Condensate contains a significant amount of sensible heat that can account for about 10% to 30% of the initial heat energy contained in the steam.
Feeding the boiler with high-temperature condensate can maximize boiler output because less heat energy is required to turn water into steam. When efficiently recovered and reused, it can even be possible to reduce boiler fuel needs by up to 10 to 20%.
Lower Water-related Expenses
As long as any impurities picked up during condensate transport are removed, condensate can be reused as boiler feedwater, reducing water supply and treatment costs, as well as costs associated with cold water used to lower condensate temperatures before sewering, where applicable.
Positive Impact on Safety and the Environment
Reducing boiler fuel needs through condensate recovery leads to less air pollution by lowering CO2, NOx and SOx emissions.
Additionally, condensate recovery lines can also limit vapor clouds to reduce noise generated from atmospheric condensate discharge and help prevent build-up of water on the ground, considerably improving a plant’s work environment.
Depending on the amount of condensate being recovered and reused, other benefits may include a reduced need for boiler blowdown through better feedwater quality, and less corrosion in the system as water quality becomes more consistent throughout the grid.
Flash steam is a name given to the steam formed from hot condensate when the pressure is reduced. It occurs when high pressure / high temperature condensate is exposed to a large pressure drop such as when exiting a steam trap. When hot condensate is discharged into a lower pressure environment, its enthalpy (total energy) remains the same, but its saturation points drops (the temperature at which condensate can exist in both the liquid and gaseous state). To compensate for the excess amount of energy, part of the water molecules absorbs the excess energy as latent heat and evaporate to form steam. (TLV, 2015) [3] The flashing of condensate under reduced pressure as it moves from the conditions of on effect to that of the next is used to recover part of the energy of the condensate. The vapour recovered is equivalent to the change in liquid enthalpy or sensible heat. (RASITC 1999). Calculating the % Flash Steam Generated 7 The % of flash steam generated (flash steam ratio) can be calculated from: 𝐹𝑙𝑎𝑠ℎ % = ℎ𝑓1 − ℎ𝑓2 ℎ𝑓𝑔2 where: • hf1 = Specific Enthalpy of Saturated Water at Inlet* • hf2 = Specific Enthalpy of Saturated Water at Outlet • hfg2 = Latent Heat of Saturated Steam at Outlet.
Requirements for successful flash steam applications
If full use is to be made of flash steam, some basic requirements must be satisfied:
It is essential to have a continual supply of sufficient condensate from applications operating at higher pressures, to ensure that enough flash steam can be released for economic recovery.
The steam traps and the equipment they are draining must be able to function satisfactorily against the backpressure applied by the flash system.
Care must be taken when attempting flash steam recovery with condensate from temperature-controlled equipment. At less than full-load, the steam space pressure will be lowered by the closing action of the steam control valve. If the steam pressure in the equipment approaches or falls below the specified flash steam pressure, the overall amount of flash steam formed will be marginal, and one must question whether recovery is worthwhile in this instance.
It is important that there is a demand for low pressure flash steam that either equals or exceeds the flash steam being produced. Any deficit of flash steam can be made up by live steam from a pressure reducing valve. If the supply of flash steam exceeds its demand, surplus pressure will be created in the flash steam distribution system, which will then have to be vented to waste through a surplus sing valve.
It is possible to utilise the flash steam from condensate on a space heating installation - but savings will only be achieved during the heating season. When heating is not required, the recovery system becomes ineffective. Wherever possible, the best arrangement is to use flash steam from process condensate to supply process loads - and flash steam from heating condensate to supply heating loads. Supply and demand are then more likely to remain in-step.
It is preferable to actually use the flash steam close to the high-pressure condensate source. Relatively large diameter pipes are used for low pressure steam, to reduce pressure loss and velocity, which can mean costly installation if the flash steam has to be piped any distance.
A thermal insulator is a poor conductor of heat and has a low thermal conductivity. Insulation is used in buildings and in manufacturing processes to prevent heat loss or heat gain. Although its primary purpose is an economic one, it also provides more accurate control of process temperatures and protection of personnel. It prevents condensation on cold surfaces and the resulting corrosion. Such materials are porous, containing large number of dormant air cells. Thermal insulation delivers the following benefits:
• Reduces over-all energy consumption
• Offers better process control by maintaining process temperature.
• Prevents corrosion by keeping the exposed surface of a refrigerated system above dew point
• Provides fire protection to equipment
• Absorbs vibration
Types and Application the Insulation can be classified into three groups according to the temperature ranges for which they are used. Low Temperature Insulations (up to 90 °C) This ranges covers insulating materials for refrigerators, cold and hot water systems, storage tanks, etc. The commonly used materials are Cork, Wood, 85% magnesia, Mineral Fibers, Polyurethane and expanded Polystyrene, etc. Medium Temperature Insulations (90 – 325 °C) Insulators in this range are used in low temperature, heating and steam raising equipment, steam lines, flue ducts etc. The types of materials used in this temperatures range include 85% Magnesia, Asbestos, Calcium Silicate and Mineral Fibres etc. High Temperature Insulations (325 °C – above) Typical uses of such materials are super-heated steam system, oven dryer and furnaces etc. The most extensively used materials in this range are Asbestos, Calcium Silicate, Mineral Fibre, Mica and Vermiculite based insulation, Fireclay or Silica based insulation and Ceramic Fibre.
Insulation material-
Insulation materials can also be classified into organic and inorganic types. Organic insulations are based on hydrocarbon polymers, which can be expanded to obtain high void structures Example: Thermocol (Expanded Polystyrene) and Poly Urethane Form (PUF). Inorganic insulation is based on Siliceous/Aluminous/Calcium materials in fibrous, granular or powder forms. Example: Mineral wool, Calcium silicate etc. Properties of common insulating materials are as under: Calcium Silicate: Used in industrial process plant piping where high service temperature and compressive strength are needed. Temperature ranges varies from 40 °C to 950 °C. Glass mineral wool: These are available in flexible forms, rigid slabs and preformed pipe work sections. Good for thermal and acoustic insulation for heating and chilling system pipelines. Temperature range of application is –10 to 500 °C. Thermocol: These are mainly used as cold insulation for piping and cold storage construction.
Expanded nitrile rubber: This is a flexible material that forms a closed cell integral vapour barrier. Originally developed for condensation control in refrigeration pipe work and chilled water lines; now-a-days also used for ducting insulation for air conditioning. Rock mineral wool: This is available in a range of forms from light weight rolled products to heavy rigid slabs including preformed pipe sections. In addition to good thermal insulation properties, it can also provide acoustic insulation and is fire retardant.
Refractories-
Any material can be described as ‘refractory’, if it can with stand the action of abrasive or corrosive solids, liquids or gases at high temperatures. The various combinations of operating conditions in which refractories are used, make it necessary to manufacture a range of refractory materials with different properties. Refractory materials are made in varying combinations and shapes and for different applications. The general requirements of a refractory material can be summed up as: • Ability to withstand high temperatures. • Ability to withstand sudden changes of temperatures. • Ability to withstand action of molten metal slag, glass, hot gases, etc. • Ability to withstand load at service conditions. • Ability to withstand load and abrasive forces. • Low coefficient of thermal expansion. • Should be able to conserve heat. • Should not contaminate the material with which it comes into contact.
Properties of Refractories
Some of the important properties of refractories are:
Melting point: Pure substances melt sharply at a definite temperature. Most refractory materials consist of high melting particles bonded together. At high temperature, glass fuses and as the temperature rises, the resulting slag increases in quantity by partial solution of the refractory particles. The temperature at which this action results in failure of a test pyramid (cone) to support its own weight is called, for convenience, the melting point of the refractory. Size: The size and shape of the refractories is a part of the design feature. It is an important feature in design since it affects the stability of any structure. Accuracy and size are extremely important to enable proper fitting of the refractory shape and to minimize the thickness and joints in construction. Bulk density: A useful property of refractories is bulk density, which defines the material present in a given volume. An increase in bulk density of a given refractory increases its volume stability, its heat capacity, as well as resistance to slag penetration. Porosity: The apparent porosity is a measure of the volume of the open pores, into which a liquid can penetrate, as a percentage of the total volume. This is an important property in cases where the refractory is in contact with molten charge and slags. A low apparent porosity is desirable since it would prevent easy penetration of the refractory size and continuity of pores will have important influences on refractory behaviour. A large number of small pores is generally preferable to an equivalent number of large pores. Cold crushing strength: The cold crushing strength, which is considered by some to be of doubtful relevance as a useful property, other than that it reveals little more than the ability to withstand the rigors of transport, can be used as a useful indicator to the adequacy of firing and abrasion resistance in consonance with other properties such as bulk density and porosity. Pyrometric cone equivalent (PCE): Temperature at which a refractory will deform under its own weight is known as its softening temperature which is indicated by PCE. Refractories, due to their chemical complexity, melt progressively over a range of temperature. Hence refractoriness or fusion point is ideally assessed by the cone fusion method. The equivalent standard cone which melts to the same extent as the test cone is known as the pyrometric cone equivalent. Thus, in the Figure 5.5 refractoriness of Sample A is much higher than B and C. The pyrometric cone equivalent indicates only the softening temperature. But, in service the refractory is subjected to loads which would deform the refractory at a much lower temperature than that indicated by PCE. With change in the environmental conditions, such as reducing atmosphere, the P.C.E. Value changes drastically. Refractoriness under load (RUL): The refractoriness under load test (RUL test) gives an indication of the temperature at which the bricks will collapse, in service conditions with similar load. Creep at high temperature: Creep is a time dependent property which determines the deformation in a given time and at a given temperature by a material under stress. Volume stability, expansion, and shrinkage at high temperatures: The contraction or expansion of the refractories can take place during service. Such permanent changes in dimensions may be due to: i) The changes in the allotropic forms which cause a change in specific gravity. Ii) A chemical reaction which produces a new material of altered specific gravity. Iii) The formation of liquid phase. Iv) Sintering reactions. v) It may also happen on account of fluxing with dust and stag or by the action of alkalies on fireclay refractories, to form alkali-alumina silicates, causing expansion and disruption. This is an example which is generally observed in blast furnaces. Reversible Thermal Expansion: Any material when heated, expands, and contracts on cooling. The reversible thermal expansion is a reflection on the phase transformations that occur during heating and cooling. Thermal Conductivity: Thermal conductivity depends upon the chemical and mineralogical compositions as well as the glassy phase contained in the refractory and the application temperature. The conductivity usually changes with rise in temperature. In cases where heat transfer is required though the brick work, for example in recuperators, regenerators, muffles, etc. the refractory should have high conductivity. Low thermal conductivity is desirable for conservation of heat by providing adequate insulation. The provisions for back-up insulation, conserves heat but at the same time it increases the hot face temperature and hence the demand on the refractory quality increases. Accordingly, insulation on the roof in open hearth furnaces is normally not provided, otherwise it would cause failure due to severe dripping. Depending on the characteristic of the refractory used in the hot face, such as the high temperature load bearing capacity, it may be required that the quality of the brick be increased to match the rise temperature caused by over insulation.
Typical Refractories in Industrial Use
Depending on the area of application such as boilers, furnaces, kilns, ovens etc, temperatures and atmospheres encountered different types of refractories are used.
Fireclay Refractories Fireclay refractories, such as firebricks, siliceous fireclays and aluminous clay refractories consist of aluminium silicates with various amounts of silica ranging from SiO2 content of less than 78% and containing less than 44% of Al2O3.
High Alumina Refractories Alumina silicate refractories containing more than 45% alumina are generally termed as high alumina materials. The alumina concentration ranges from 45 to 100%. The refractoriness of high alumina refractories increases with increase in alumina percentage. The applications of high alumina refractories include the hearth and shaft of blast furnaces, ceramic kilns, cement kilns, glass tanks and crucibles for melting a wide range of metals. Silica Brick Silica brick (or Dinas) is a refractory material containing at least 93% SiO2. The raw material is quality rocks. Various grades of silica brick have found extensive use in the iron and steel melting furnaces. In addition to high fusion point multi-type refractories, the other important properties are their high resistance to thermal shock (spalling) and their high refractoriness. It finds typical use in glass making and steel industry. The outstanding property of silica brick is that it does not begin to soften under high loads until its fusion point is approached. This behaviour contrasts with that of many other refractories, for example alumina silicate materials, which begin to fuse and creep at temperatures considerably lower than their fusion points. Other advantages are flux and stag resistance, volume stability and high spalling resistance. Magnesite refractories are chemically basic materials, containing at least 85% magnesium oxide. They are made from naturally occurring magnesite (MgCO3). The properties of magnesite refractories depend on the concentration of silicate bond at the operating temperatures. Good quality magnesite usually results from a CaO-SiO2 ratio of less than 2 with a minimum ferrite concentration, particularly if the furnaces lined with the refractory operate in oxidizing and reducing conditions. The slag resistance is very high particularly to lime and iron rich slags.
Chromite Refractories
Here, a distinction must be made between chrome-magnesite refractories and magnesite chromite-refractories. Chrome magnesite material usually contain 15-35% Cr2O3 and 42-50% MgO whereas magnesite-chromite refractories contain at least 60% MgO and 8-18% Cr2O3. Chrome-magnesite refractories are made in a wide range of qualities and are used for building the critical parts of high temperature furnaces. These materials can withstand corrosive slags and gases and have high refractoriness. The magnesite-chromite products are suitable for service at the highest temperatures and in contact with the most basic slags used in steel melting. Magnesite-chromite usually has a better spalling resistance than chrome-magnesite.
Zirconia Refractories
Zirconium dioxide (ZrO2) is a polymorphic, material. There are certain difficulties in its usage and fabrication as a refractory material. It is essential to stabilize it before application as a refractory. This is achieved by incorporating small quantities of calcium, magnesium and cerium oxide, etc. Its properties depend mainly on the degree of stabilization and quantity of stabilizer as well as the quality of the original raw material. Zirconia refractories have a very high strength at room temperature which is maintained up to temperatures as high as 1500 °C. They are, therefore, useful as high temperature constructional materials for furnaces and kilns. The thermal conductivity, of zirconium dioxide is found to be much lower than that of most other refractories and the material is therefore used as a high temperature insulating refractory. Since Zirconia exhibits very low thermal losses and does not react readily with liquid metals, it is particularly useful for making refractory crucibles and other vessels for metallurgical purposes. Zirconia is a useful refractory material for glass furnaces primarily since it is not easily wetted by molten glasses and because of its low reaction with them.
Oxide Refractories (Alumina)
Alumina refractory materials which consist of aluminium oxide with little traces of impurities are often known as pure alumina. Alumina is one of the most chemically stable oxides known. It is mechanically very strong, insoluble in water and super-heated steam, and in most inorganic acids and alkalies. Its properties make it suitable for the shaping of crucibles for fusing sodium carbonate, sodium hydroxide and sodium peroxide. It has a high resistance in oxidizing and reducing atmosphere. Alumina is extensively used in heat processing industries. Highly porous alumina is used for lining furnaces operating up to 1850 °C.
Monolithic refractories
Monolithic refractories are replacing the conventional type fired refractories at a much faster rate in many applications including those of industrial furnaces. The main advantages being: • It eliminates joints which is an inherent weakness • Method of application is faster and skilled measures in large number are not required • Transportation and handling are simple • Offers better scope to reduce downtime for repairs
Offers considerable scope to reduce inventory and eliminate special shapes • It is a heat saver • Has better spalling resistance • Has greater volume stability Various means are employed in the placement of monolithic like ramming, casting, gunniting, spraying, sand slinging, etc. Ramming masses are used mostly in cold applications where proper consolidation of the material is important. The same practice can be adopted with both air setting and heat setting materials. Proper ramming tools need to be selected. Castable by name implies a material of hydraulic setting in nature. Calcium aluminate cement being the binder, it will have to be stored properly to prevent moisture absorption. Further its strength starts deteriorating after a period of 6 to 12 months.
Key Takeaways:
- Water is pressured from the economizer to the circulating pump at excessive pace inflicting the warmth to switch from the gases to the water very unexpectedly.
- The boiler add-ons are the gadgets, which shape an essential a part of a boiler however isn’t installed on it.
- The characteristic of a prevent valve is to govern the float of the steam from with inside the boiler and to prevent it absolutely whilst required.
References:
1. Witte L.C., Schmidt P.S. And Brown D.R., Industrial Energy Management and Utilization, Hemisphere Publ., Washington,1988.
2. Callaghan P.W., Design and Management for Energy Conservation, Pergamon Press, Oxford, 1981.
3. Murphy W.R. And McKay G., Energy Management, Butterworths, London,1987.