UNIT 3
Single phase Transformers
The response of a material when subjected to an external magnetic field is the root of magnetism. The spinning electrons in the material behave like tiny magnets. These tiny magnets are aligned in the direction of applied magnetic field and thereby the material is magnetized.
An applied magnetic field H incites a response from a 2 material called magnetic induction B. The relationship between B and H can be defined by
B = μo H + μo I ------------------------(1)
Where I is the magnetic moment per unit volume. μo is a constant called the permeability of free space. So, the ratio of I to H is called the susceptibility and is indicative of the ease with which a material can be magnetized by an applied magnetic field.
----------------------------------------(2)
Equation(2) is called the suspectability.
The ratio of B to H is called the permeability and it is the property of the material which allows magnetic lines of force (field) to penetrate the material.
μ=B/H ----------------------------- (3) defines magnetic permeability.
BH Characteristics
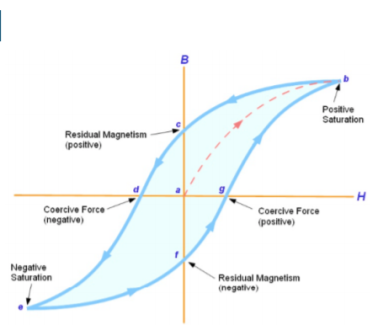
- When tested experimentally, a ferromagnetic material such as iron will produce a curve similar to that shown above.
- First there is an upper/lower limit to the magnetic flux density which may be achieved, which occurs at positive or negative saturation, respectively. This is related to the crystalline structure of the iron, where each crystal has its own – initially random – magnetic orientation.
- Increasing the magnetic field strength in either direction causes more and more magnetic 'domains' to align with the external magnetic field, but once almost all of the domains have aligned themselves, then little further increase in magnetic flux density is possible. The ferromagnetic material is said to be saturated.
- The curve demonstrates magnetic hysteresis or 'lag' as the sample is alternatively magnetized in the positive and negative directions. When initially magnetized, the curve follows points a–b on the graph, but on reducing H to zero, some residual magnetism remains (point c - also known as the remanent flux density).
- In order to fully demagnetize the specimen, it is necessary to apply a negative magnetic field strength (point d - called the coercive force). Making H increasingly negative leads to negative saturation (point e). If H is reduced back to zero, point f is reached (negative residual magnetism). As H becomes positive, the flux density reduces to zero (point g) and then becomes positive.
- Finally returning back to point b (positive saturation), after which the cycle b–g repeats. The area enclosed by the B-H curve (shaded light blue above) is proportional to the energy loss as the ferromagnetic material is magnetized with varying polarity by connection to an alternating (AC) power supply.
- This energy loss is undesirable and causes unwanted heating of the material. In general, harder ferromagnetic materials have higher hysteresis losses, since more energy is required to realign the magnetic domains. Steel, to which a small proportion of silicon has been added, is commonly used for applications such as transformer cores and motor rotors, due to its lower hysteresis loss.
- For smaller applications, such as inductor cores, passive filters, miniature transformers and antennas, then ferrite (a ceramic-like combination of metallic oxides including ferric oxide) is a popular choice.
- Types of transformers
Acc to input supply: I phase and phase
Acc to construction: core and shell type
Acc to 0/P: step up and step down
Construction of transformers (study only for MCQs)
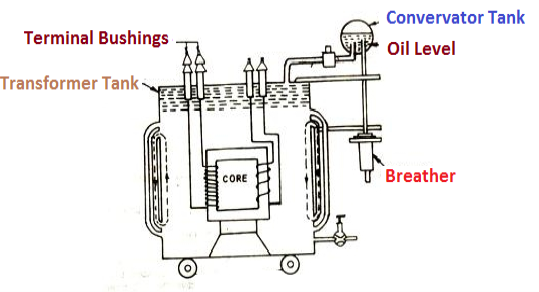
- Laminated steel core
Material used for core is (silicon steel) it is used for its (high permeability) and (low magnetic reluctance) magnetic field produced is very strong
The core is formed of (stacks of laminated thin steel sheets) which are electrically isolated from each other. They are typically (0.35 to 0.5 mm thick)
We can used 2 ‘L’ shaped sheets or 2 shaped sheets for laminations
- There a 2 types of winding
- Concentric or cylindrical
- Sandwiched type
- Cylindrical
L.V. = low voltage H.V. = high voltage are mounted on same limb to minimum leakage.
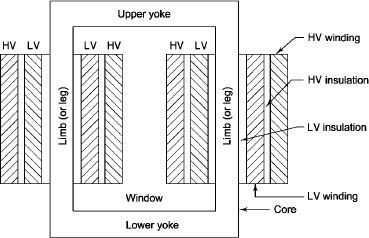
L.V. Winding placed inside and H.V. Winding placed outside with (proper insulation between the winding as it is easy to insulated L.V. Winding) than H.V. Winding.
2. Sandwiched
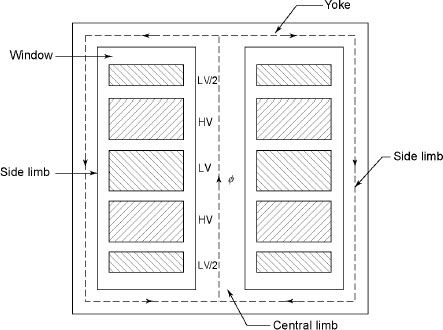
The H.V. And L.V. Winding are divided into no. Of small coils and there small windings are interleaved.
(the top and bottom winding are L.V. Coils because they are close to core)
- Transformer tank : wholes assembly of winding and core placed inside the Transformer tank (sheet metal tank) which is filled with Transformer oil or insulating oil which acts as an (insulator or coolant ) MCQ
- Transformer oil : (The function of oil is to remove efficiently the heat generated in core and in winding)
- Moisture should not be allowed which creeps the insulation which achieved by closed Transformer tank.
(To increase cooling surface are tubes or fins are provided)
- Conservator tank: above tank T/F tank there is one small tank in which same empty space is always provided above the oil level. (this space is required for oil to expand or contract due to temperature change) MCQ
However during contraction outside air can have moisture which will deteriorate the insulating properly of oil?
- Breather : the air goes in or out through the breather (To reduce the moisture content of their air . Same drying agents such as (silica gel or) calcium chloride) is used in the breather (The dust particles present in air are also removed by breather)
- BuccholzRelay : (for incipient (slowly increasing) faults
There is pipe connecting rain tank and conservator. On the pipe a protective device called Buccholz Relay is mounted.
When the Transformer is about to be faulty and draw range current the oil becomes very hot and decompose.
During this process different types of gases are liberated. (The Buccholz Relay get operated by these gases) and gives an alarm to the operator. ɡȴ the fault continues to persist then there lay will trip off main circuit breaker to protect the Transformer.
- Explosion Vent :
An explosion Vent or relief value is the bent up pipe filled on the main tank.
(The explosion vent consist of aluminium of oil) when the T/F becomes faulty the cooling oil get decomposed and various types of gases are liberated
(ɡȴ the gas pressure exodus certain level then the aluminium of oil (diagram) in explosion vent will burst) to release pressure. The will save main tank from getting damaged.
- Single phase transformer - for MCQs
(Symbol and principal of operation)
It is a static device which can transfer electrical energy from one ac circuit to another ac circuit without change in frequency
It can increase or decrease the voltage but with corresponding decrease or increase in current
It works on Principle
“Mutual Induction”
A major application of transformer is to increase voltage before transmitting electrical energy over a long distance through conductors and to again reduce voltage at place where it is to be used.
Symbol
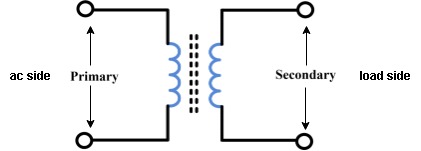
- Primary winding : (ac supply side) For MCQs
The winding which is connected to supply is called primary side
2. Secondary winding : (load side) for MCQs
The winding which is connected to load is called as secondary winding
- Working : For MCQs
It works on principle of mutual Induction i.e “when 2 coils are inductively coupled and if current in one coil is changed uniformly then an emf get induced in another coil”
- When alternating voltage V1 is applied to primary winding am alternating current I1 flows in it producing alternating flux in the core.
- As per Faradays Law of Electromagnetic Induction 1 an emf E1 is induced in the primary winding E = N1
- The emf induced in the primary winding is nearly equal and opposite to applied voltage V1
- Assuming leakage flux to be negligible almost whole flux produced in primary winding links with secondary winding thence emf induced in the secondary winding E2 = N2
- Core and shall type transformers
Core Diagram
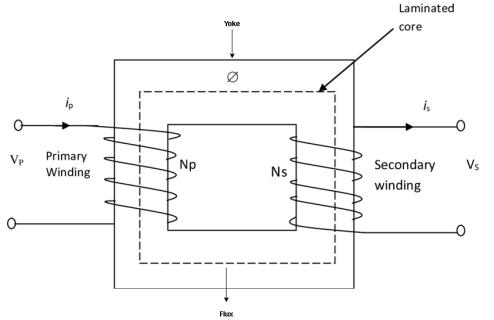
Shell Diagram:
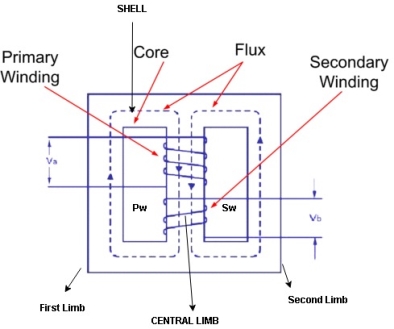
- It consists of magnetic frame with 1. 3 Limbs
2 limbs
2. single magnetic circuit 2. Double magnetic ckt.
3. Winding encircles the core 3. Core encircles the winding
4. One window 4. Two window
5. Cylindrical type winding is used 5. Sandwich type is used
6. Easy to repair 6. Not easy repair
7. Preferred for Low voltage application 7. Preferred for high voltage application
8. Provides better cooling since winding 8. Does not provide effective cooling as
Are uniformly distributed on 2 limbs the winding are surrounding core.
The B-H curve of transformer core is never linear rather it becomes flat as the value of magnetizing current increases.
This means, transformer exciting current will not be in phase with the core flux. In fact, exciting current leads the core flux by some angle “α”. This angle is known as Hysteretic Angle.
This angle is dependent on the hysteresis loop of the core material.
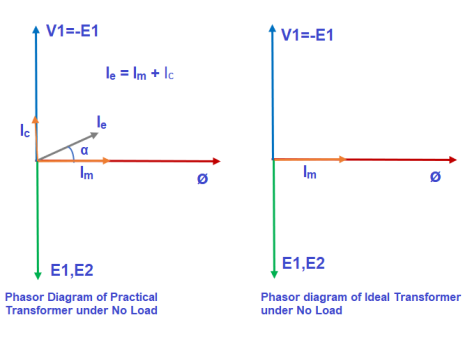
In an ideal transformer, magnetization curve is assumed to be linear. This means, magnetizing current and core flux are in phase.
In practical/real transformer, the exciting current (current in primary winding under no load condition) drawn from the source is composed of magnetizing current (Im) and core loss component (Ic). This is because, core loss is supplied by the primary source only. However, in an Ideal Transformer, as there is no core loss, the exciting current is equal to magnetizing current.
An ideal transformer is one that has
- No winding resistance
- No leakage flux i.e., the same flux links both the windings
- No iron losses (i.e., eddy current and hysteresis losses) in the core
Although an ideal transformer cannot be physically realized, yet its study provides a very powerful tool in the analysis of a practical transformer. In fact, practical transformers have properties that approach very close to an ideal transformer.
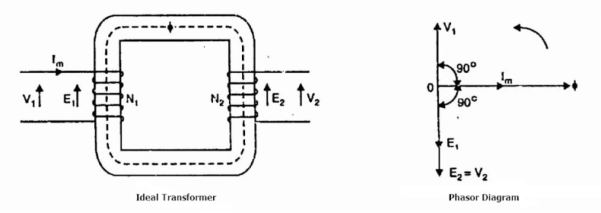
Consider an ideal transformer on no load i.e., the secondary is open-circuited as shown in the figure. Under such conditions, the primary is simply a coil of pure inductance.
When an alternating voltage V₁ is applied to the primary, it draws a small magnetizing current Iₘ which lags behind the applied voltage by 90°. This alternating current Iₘ produces an alternating flux ϕ which is proportional to and in phase with it.
The alternating flux ϕ links both the windings and induces e.m.f. E₁ in the primary and e.m.f. E₂ in the secondary. The primary e.m.f. E₁ is, at every instant, equal to and in opposition to V₁ (Lenz’s law). Both e.m.f.sE₁ and E₂ lag behind flux ϕ by 90°. However, their magnitudes depend upon the number of primary and secondary turns.
Phasor Diagram of Ideal Transformer
The phasor diagram of an ideal transformer on no load is also shown above. Since flux ϕ is common to both the windings, it has been taken as the reference phasor.
The primary e.m.f. E₁ and secondary e.m.f. E₂ lag behind the flux ϕ by 90°.
Note that E₁ and E₂ are in phase. But E₁ is equal to V₁ and 180° out of phase with it.
Practical Transformer
A practical transformer differs from the ideal transformer in many respects. The practical transformer has,
- Iron losses,
- Winding resistances and,
- Magnetic leakage, giving rise to leakage reactance.
1. Iron Losses
Since the iron core is subjected to alternating flux, there occurs eddy current and hysteresis loss in it. These two losses together are known as iron losses or core losses.
The iron losses depend upon the supply frequency, the maximum flux density in the core, volume of the core, etc.
It may be noted that the magnitude of iron losses is quite small in a practical transformer.
2. Winding resistances
Since the windings consist of copper conductors, it immediately follows that both primary and secondary will have winding resistance. The primary resistance R₁ and secondary resistance R₂ act in series with the respective windings as shown in the figure.
When current flows through the windings, there will be power loss as well as a loss in voltage due to IR drop. This will affect the power factor and E₁ will be less than V₁ while V₂ will be less than E₂.
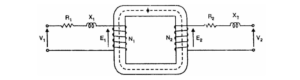
3. Leakage reactances
Both primary and secondary currents produce flux. The flux ϕ which links both the windings is the useful flux and is called mutual flux.
However, the primary current would produce some flux ϕ which would not link the secondary winding. Similarly, the secondary current would produce some flux ϕ that would not link the primary winding.
The flux such as ϕ₁ or ϕ₂ which links only one winding is called leakage flux. The leakage flux paths are mainly through the air. The effect of these leakage fluxes would be the same as though inductive reactance were connected in series with each winding of the transformer that had no leakage flux as shown in the figure.
In other words, the effect of primary leakage flux ϕ₁ is to introduce an inductive reactance X₁ in series with the primary winding as shown. Similarly, the secondary leakage flux ϕ₂ introduces an inductive reactance X₂ in series with the secondary winding.
There will be no power loss due to leakage reactance. However, the presence of leakage reactance in the windings changes the power factor as well as there is voltage loss due to IX drop.
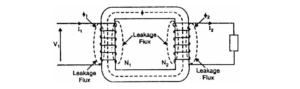
Note.
Although leakage flux in a transformer is quite small (about 5% of ϕ) compared to the mutual flux ϕ, yet it cannot be ignored.
It is because leakage flux paths are through the air of high reluctance and hence require considerable e.m.f. It may be noted that energy is conveyed from the primary winding to the secondary winding by mutual flux f which links both the windings.
When the transformer is operating at no load, the secondary winding is open-circuited, which means there is no load on the secondary side of the transformer and, therefore, current in the secondary will be zero. While primary winding carries a small current I0 called no-load current which is 2 to 10% of the rated current.
This current is responsible for supplying the iron losses (hysteresis and eddy current losses) in the core and a very small amount of copper losses in the primary winding. The angle of lag depends upon the losses in the transformer. The power factor is very low and varies from 0.1 to 0.15.
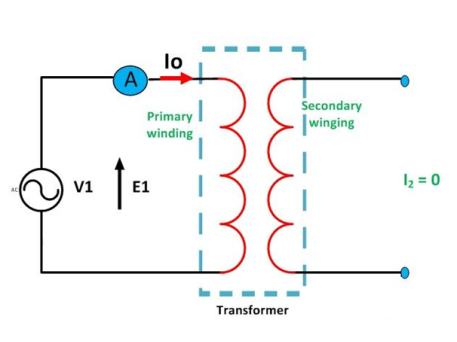
The no-load current consists of two components:
- Reactive or magnetizing component I: m
It is in quadrature with the applied voltage V1. It produces flux in the core and does not consume any power.
- Active or power component Iw:
- It is also known as a working component.
It is in phase with the applied voltage V1. It supplies the iron losses and a small amount of primary copper loss.
The following steps are given below to draw the phasor diagram:
- The function of the magnetizing component is to produce the magnetizing flux, and thus, it will be in phase with the flux.
- Induced emf in the primary and the secondary winding lags the flux ϕ by 90 degrees.
- The primary copper loss is neglected, and secondary current losses are zero as
I2 = 0.
Therefore, the current I0 lags behind the voltage vector V1 by an angle ϕ0 called the no-load power factor angle and are shown in the phasor diagram above. - The applied voltage V1 is drawn equal and opposite of the induced emf E1 because the difference between the two, at no load, is negligible.
- Active component Iw is drawn in phase with the applied voltage V1.
- The phasor sum of magnetizing current Im and the working current Iw gives the no-load current I0.
From the phasor diagram drawn above, the following conclusions are made
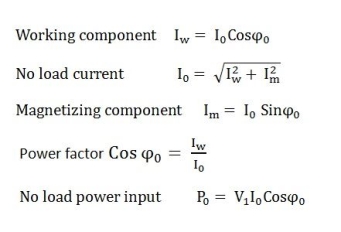
This is all about transformer in no-load condition.
- Losses in a Transformer [6m]
There are 2 types of losses occurring in a transformer
A) 1. Core loss or Iron loss
B) 2. Copper loss
- Core losses:
- This loss is due to the reversal of flux
- The flux set up in the core is dependent on the i/p supply
as the i/p supply is constant in magnitude
the flux set up will be constant and
core losses are also constant.
- Core losses are voltage dependent loss they can be subdivided in 2
1 Hysteresis loss
2 reedy current loss
- Hysteresis loss: The iron loss occurring in the core of T/F due to the Hysteresis curve of the magnetic material used for core is called as Hysteresis loss.
Hysteresis curve is the curve as loop which shows the properly of magnetic material to lag the flux density B behind the field Intensely H
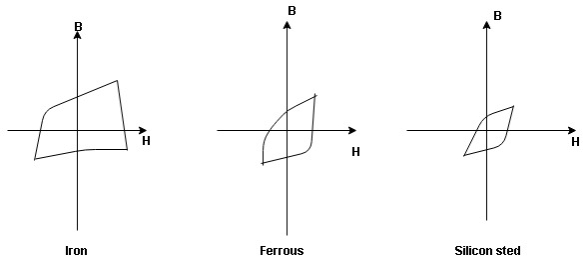
Above are the 3 different loops (Hysteresis of 3 diff. Materials)
the selection of magnetic material for the construction of core depends upon Hysteresis loop of that material having tall and narrow Hysteresis loop is selected for the T/F core
silicon Steel
Hysteresis loss depends on fold factor
PH = KH. Bm1.67 F V – watts
Where KH = constant (Hyst)
Bm = max Flux density
F = Frequency
= Volume of core.
2. Reedy current loss :
This loss is due to the flow of reedy (circular) current in the core caused by induced emf in core
PE = Ke Bm2 f2 t2 v – watts
Where
Ke = reedy current const.
t = thickness of core
It can be reduced by using stacks of laminations instead of solid core
B] Copper loss: PCU
The Copper loss is due to resistance of the primary and secondary winding
It is load dependent / current dependent loss
As load on a transformer is variable (changing) current changes
copper loss is a variable loss
Primary secondary
Total C is loss = I12R12 + I22 R22
Copper loss depends upon load on T/F and is proportional to square of load current or KVA rating of transformer
PCU
2
(KVA)2
F.L = full load
PCU (at half load) =
2 PCu F.L
= (0.5)2 PCU F.L.
Or PCu (load) = (
) 2 PCu F.L