Unit – 2
Building Construction
The four materials go to make cement concrete:
(i) Cement ;
(ii) Sand (i.e. fine aggregate);
(iii) Stone/Brick ballast (i.e., coarse aggregate) and
(iv) Water.
(i) Cement
Normally ordinary Portland cement satisfying the requirements of the Indian Standards Institution is used. However, for special conditions the type of cement suiting the requirements is used.
Cement, being hygroscopic, attracts moisture quickly and sets, So storage of cement should be carefully attended to and no set or even partially set cement should be used.
(ii) Fine aggregates
Sand and crushed stone are the commonly used fine aggregates in cement concrete.
(iii) Coarse aggregate
Stone ballast, gravel, shingle and brick ballast are the usual coarse aggregates used in making cement concrete. Size of aggregate shall depend upon the type of work and the reinforcement. The size of aggregate should be less than the distance between two consecutive steel bars in RCC.
Strength of concrete shall depend to a great extent on the voids in it. As such to have lesser voids so as to get stronger concrete the aggregates should be well graded i.e., they should have particles of various sizes so that the voids of bigger particles are filled up by the particles of smaller sizes.Graded aggregates give solid and dense concrete (free from holes or voids) which is stronger, more durable and water tight.
(v) Water
Only good clean water should be used for making concrete. It should be free from silt, salts or any organic matter. Generally speaking, water that is good for drinking is good enough for concrete work.
Nominal Proportion Of Concrete Preparation Of Concrete, Compaction and Curing
Nominal Proportion Of Concrete Preparation Of Concrete
Concrete is a commonly used construction material, which is the mixture of cement, sand, aggregate, and admixtures blended with water. Concrete gets hardened with time and gains the strength, and for the best results in a construction of your dream home, mixing of concrete is said to be the most important process. All the ingredients are to be mixed in proper proportion because the properties of concrete like workability, strength, surface finish, and durability of concrete etc. are ensured by the right and proportionate blending.
In the nominal mix concrete, all the ingredients and their proportions are prescribed in the standard specifications. These proportions are specified in the ratio of cement to aggregates for certain strength achievement.
The mix proportions like 1:1.5:3, 1:2:4, 1:3:6 etc. are adopted in nominal mix of concrete without any scientific base, only on the basis on past empirical studies. Thus, it is adopted for ordinary concrete or you can say, the nominal mix is preferred for simpler, relatively unimportant and small concrete works.
As per the ‘Indian Standard- IS 456:2000’, nominal mix concrete may be used for concrete of M20 grade or lower grade such as M5, M7.5, M10, M15.
M 20 is identified as the concrete grade in which, M denotes the Mix and 20 denotes the compressive strength of concrete cube after 28 days of curing in N/mm2. There are various grades of concrete that can be used like M10, M15, M20, M25, M30, etc.
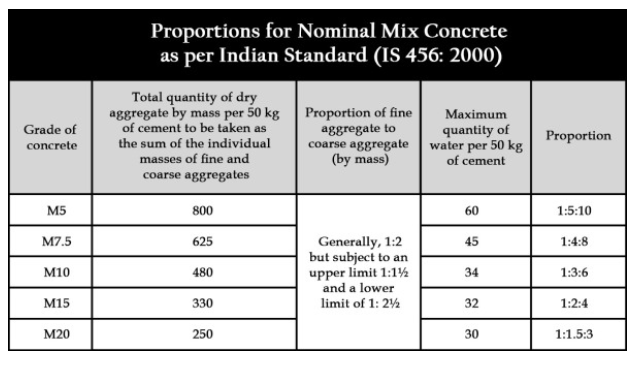
Workability, Strength properties of Concrete
- Concrete is an artificial conglomerate stone made essentially of Portland cement, water, and aggregates.
- Portland cement is produced by mixing ground limestone, clay or shale, sand and iron ore.
- This mixture is heated in a rotary kiln to temperatures as high as 1 600 degrees Celsius high as 1,600 degrees Celsius. The heating process causes the materials to break down and recombine into new compounds that can react with water in a crystallization process called hydration.
- The raw ingredients of Portland cement are iron ore, lime, alumina and silica. These are ground up and fired in a kiln to produce a clinker. After cooling, the clinker is very finery ground.
- When first mixed the water and cement constitute a paste which surrounds all the individual pieces of aggregate to make a plastic mixture.
- A chemical reaction called hydration takes place between the water and cement, and concrete normally changes from a plastic to a solid state in about 2 hours.
- Concrete continues to gain strength as it cures. Heat of hydration - is the heat given off during the chemical reaction as the cement hydrates.
Workability that property of freshly mixed concrete that determines its working characteristics, i.e. the ease with which it can be mixed, placed, compacted and finished.
Factors effecting workability:
- Method and duration of transportation
- Quantity and characteristics of cementing materials
- Concrete consistency (slump)
- Aggregate grading, shape & surface texture
- % entrained air
- Water content
- Concrete & ambient air temperature Admixtures
Curing process of concrete
•Curing of concrete is defined as the process of maintaining the moisture and temperature condition of concrete for hydration reaction to the normally so that the concrete develops hardened and properties over time
•The main components which need to be taken care of your heat and time during curing process
•Curing is the process of preventing the loss of moisture from the concrete which maintaining a satisfactory temperature effect
•If the cement has high rate of strain development and if the concrete contains granulated blast furnace and flue Ash then,
•The curing should also prevent the development of high temperature gradients within the concrete
a) Moist curing
•Surface of the concrete shall be kept continuously in Dam or wet condition by covering with the layers of materials like checking Canvas etc.
•it should be kept continuously wet for at least 7 days from the date of placing concrete.
•In case of ordinary Portland cement at least 10 days where mineral admixture or blended cement are used.
•The period of curing shall not be less than 10 days for concrete exposed to the dry and hot weather condition.
•In case of concrete where mineral admixture or blended cement are used it is recommended that above minimum period may be extended 14 days.
b) Membrane curing
•Approved curing compounds may be used in place of moist curing with the permission of engineer in charge.
•Search compound shall be applied to all exposed surfaces of the concrete as soon as possible after the concrete has set.
•Impermeable membrane such as polyethylene sheeting covering closely the concrete surface may also be used to provide effective barriers against evaporation.
•For the concrete containing Portland pozzolana cement, Portland slag cement or mineral admixture period of curing may be increased.
Purpose of Foundation:
All engineering structures are provided with foundations at the base to fulfil the following objectives and purposes;
- To distribute the load of the structure over a large bearing area so as to bring intensity of loading within the safe bearing capacity of the soil lying underneath.
- To load the bearing surface at a uniform rate so as to prevent unequal settlement.
- To prevent the lateral movement of the supporting material.
- To secure a level and firm bed for building operations.
- To increase the stability of the structure as a whole.
Safe bearing capacity: It is the bearing capacity after applying the factor of safety (FS). These are of two types, Safe net bearing capacity (qns ) : It is the net soil pressure which can be safety applied to the soil considering only shear failure. It is given by,

Ultimate bearing capacity or Gross bearing capacity ( qu): It is the least gross pressure which will cause shear failure of the supporting soil immediately below the footing.
Net ultimate bearing capacity (qun ): It is the net pressure that can be applied to the footing by external loads that will just initiate failure in the underlying soil. It is equal to ultimate bearing capacity minus the stress due to the weight of the footing and any soil or surcharge directly above it. Assuming the density of the footing (concrete) and soil (Ƴ ) are close enough to be considered equal, then where, is the depth of the footing,
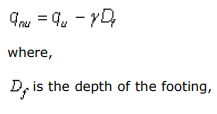
Factor of safety (FoS)
It is the ability of a system's structural capacity to be viable beyond its expected or actual loads. A FoS may be expressed as a ratio that compares absolute strength to actual applied load, or it may be expressed as a constant value that a structure must meet or exceed according to law, specification, contract or standard.
Load Bearing Construction
- Almost all the walls are load bearing walls.
- Almost all the should be provided with foundation
- Load bearing walls are taken deep into the subsoil foundation.
- Any load bearing wall should have minimum thickness of 200 mm.
- Wall are usually constructed of bricks or stone
- In a multi-storeyed building for every wall in the floor above there must be a corresponding wall in continuation in the floor below to support it.
- In a multi – stored building the thickness of the wall increase as we descend from a floor above to one below it.
- A load bearing wall once constructed shall remain in position and should never be dismantled in full or part.
- This type of construction does not favour too many openings for windows, doors, ventilation etc., in the ground floor as required for show room etc., as the load bearing length of wall is considerably reduced.
- In case of multi – stored buildings, the room area is reduced as we go down due to thicker walls.
- Plans of the different floors must be the same. Very little changes are only possible between one floor and the one above.
- May not withstand seismic forces and other forces and other type of vibration because composed of different blocks as bricks and stones being bonded together.
Framed Construction
- None of the wall are load bearing. They serve the same purpose as partition or screen.
- None of the walls are provided with any type of foundation. Walls do not go below the plinth beam.
- Only column are taken deep into subsoil and provided with foundation footing.
- Exterior wall subjected to weathering elements are generally 200 mm thick. All other wall can be 100 mm thick or even thinner.
- Column supporting beam supporting slab are all of R.C. C.
- There is no such necessity. As none of the walls are load bearing. Every floor may have wall independent of the one below it.
- These walls do not take the load and need not be thicker. They may not even continue in the floor below.
- The wall of framed structure can be displaced at will as they are lighter and non load bearing.
- The space between column can remains as open space as the case with multi – stored residential flats where the ground floor is left with no walls for easy parking of vehicle.
- Thickness of wall remains uniform, therefore the carpet area in any floor remains the same.
- Plans of different floor are independent of each floor. The ground floor may have a commercial complex, first floor an office or a bank and second floor onward of residential complexes of different types of plans and function within the same building.
- More rigid and withstand seismic forces because of the entire frame of column, beam and slabs act as one unit of R.C.C.
Reference Books
- A Text Book of Building Materials, by C.J. Kulkarrni
- Building Materials, by P. C. Varghese
- Building Construction, by P. C. Varghese