Unit - 1
Overview of Industrial Engineering
A production system is a group of people, equipment, and procedures that are structured to carry out a company's manufacturing operations. It is made up of two major parts.
- Infrastructure: The equipment, the way the equipment is laid out, and the factory in which the equipment is located are all examples of physical facilities in the production system.
- Support systems for manufacturing: These are the company's methods for managing production and resolving technical and logistical issues that arise during the ordering of materials, moving work through the facility, and ensuring that goods satisfy quality requirements. Manufacturing support systems include product design and certain business tasks.
Parts of the production system in modern manufacturing activities are automated and/or computerised. People are also a part of manufacturing systems. These systems are made to work by people. Direct labourers (blue-collar workers) oversee operating the facilities, while professional staffers (white-collar workers) oversee the production support systems.
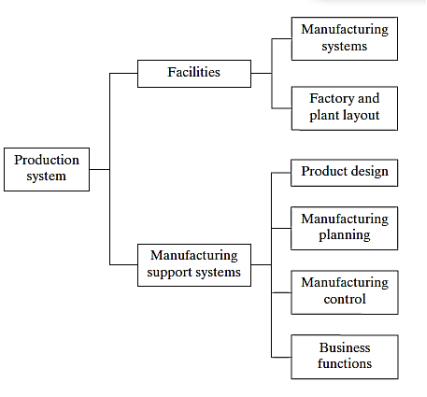
Facilities:
The factory, production machinery and tools, material handling equipment, inspection equipment, and computer systems that govern manufacturing activities are all part of the production system. The plant layout, or how the equipment is physically situated in the factory, is also included in the facilities. Manufacturing systems, which are logical groupings of equipment and employees that complete the processing and assembly activities on the factory's parts and products, are frequently used to organise the equipment.
Individual work cells, consisting of a single production machine and a worker allocated to that equipment, can make up manufacturing systems. A production line, for example, is a more complex manufacturing system that consists of a collection of machinery and employees. The parts and/or assemblies being manufactured come into direct physical touch with the manufacturing systems. The product is "touched" by them. There are three fundamental forms of human engagement in the processes performed by manufacturing systems: (a) manual work systems, (b) worker-machine systems, and (c) automated systems.
Manual Work System:
One or more workers execute one or more activities without the use of powered tools in a manual work system. In manual work systems, manual material handling duties are common. Typical production operations necessitate Hand tools, such as screwdrivers and hammers, are used. When working with hand tools, a work holder is essential. Is frequently used to grip the job portion and secure it for processing. The following are some examples of production-related manual jobs that require the use of hand tools:
- A machinist using a file to round the edges of a newly milled rectangular part.
- A quality control inspector measuring the diameter of a shaft with a micrometre
- A material handling worker moving cartons in a warehouse with a dolly.
- A team of assembly workers putting together a piece of machinery with hand tools
Worker Machine System:
A human worker runs powered equipment, such as a machine tool or other manufacturing machine, in a worker-machine system. One of the most extensively used production systems is this one. Combinations of one or more workers and one or more pieces of equipment make up worker-machine systems. Workers and machines are joined to maximise their respective skills and abilities.
- A fitter and an industrial robot working together in an arc–welding work cell
- A crew of workers operating a rolling mill that converts hot steel slabs into flat plates
- A production line in which products are moved by mechanised conveyor and workers at some of the stations use power tools to complete their processing or assembly tasks
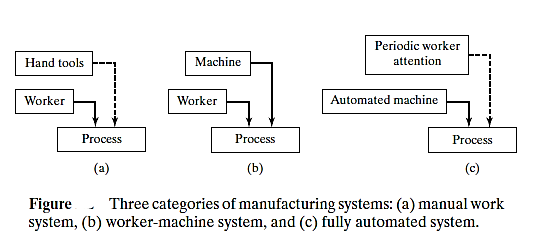
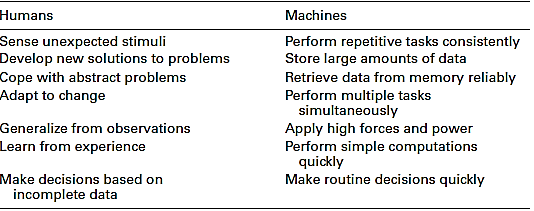
Automated System:
An automated system is one in which a machine completes a task without the involvement of a human worker. Automation is accomplished using a set of instructions and a control system to carry them out. Power is necessary to operate the programme and control system as well as to drive the process.
Because many worker-machine systems function with some level of automation, there isn't always a clear distinction between them. There are two types of automation: semiautomated and completely automated.
A semiautomated machine completes a portion of the work cycle under programme control, while a human worker attends to the machine for the remainder of the cycle, loading and unloading it or completing other activities.
The ability to operate for an extended period without human intervention distinguishes a fully automated machine from its semiautomated counterpart. The term "extended period" refers to a period that is longer than one work cycle; a worker is not required to be present for each cycle. Rather, the worker may be required to attend to the machine every tenth or hundredth cycle.
Many injection moulding facilities are examples of this style of operation, where the moulding machines run on automatic cycles, but the moulded parts must be retrieved by a worker on a regular basis.
One or more workers are required to be present in certain completely automated processes to continuously supervise the operation and ensure that it works according to the desired specifications. Complex chemical processes, oil refineries, and nuclear power plants are all examples of automated processes.
Workers do not actively participate in the process other than to make minor tweaks to the equipment settings, perform routine maintenance, and respond quickly if something goes wrong.
Manufacturing Support System:
A corporation must organise itself to develop procedures and equipment, plan, and control production orders, and meet product quality criteria in order to operate production facilities efficiently. Manufacturing support systems—the personnel and procedures that a corporation uses to manage its production operations—carry out these functions.
Most of these support systems do not interact with the product directly, but they do plan and control its journey through the plant.
Manufacturing support entails a series of actions that contain a lot of data flow and processing. These activities include (1) business functions, (2) product design, (3) manufacturing planning, and (4) manufacturing control.
Business Function:
The Business Processes the primary mechanism by which the company communicates with its customers is through its business operations. As a result, they are the start and end of the information-processing chain. Sales & marketing, sales forecasting, order entry, and customer billing are all included in this category.
The order to manufacture a product usually comes from the customer and is routed through the company's sales department. One of the following forms will be used to place the production order: (1) a client order to have an item manufactured according to their requirements, (2) a customer order to purchase one or more of the manufacturer's proprietary items, or (3) an internal business order based on a projection of future demand for a proprietary product.
Product Design:
The design has been provided by the customer, and the manufacturer's product design department is not involved if the product is made to customer design. If the product is to be manufactured to client requirements, the manufacturer's product design department may be hired to both design and create the product.
The manufacturing company oversees product development and design if the product is proprietary. The series of events that leads to the creation of a new product design frequently begins in the sales department, the flow of information.
Research and development, design engineering, and even a prototype shop is some of the divisions that are organised to execute product design.
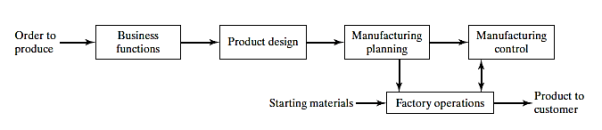
Manufacturing Planning:
The manufacturing planning function receives the information and documentation that make up the product design. Process planning, master scheduling, material needs planning, and capacity planning are examples of information-processing tasks in production planning.
The sequence of individual processing and assembly procedures required to make the part is determined by process planning. The manufacturing engineering department oversees process planning as well as technical elements like tooling.
Logistics difficulties are included in manufacturing planning, which is also known as production planning. The product's authorisation to be manufactured must be converted into a master production schedule, which is a list of the items to be manufactured, the dates on which they must be delivered, and the quantities of each. The individual components and subassemblies that make up each product must be scheduled based on this master schedule.
Parts must be bought from vendors, and raw materials must be purchased or requisitioned from storage, and all these items must be scheduled so that they are available when needed.
Material requirements planning performs the calculations for this planning. Furthermore, the master schedule must not include greater product quantities than the facility can produce each month with its current equipment and workforce.
Capacity planning include identifying the firm's personnel and equipment resources as well as ensuring that the production plan is realistic.
Manufacturing Control:
Manufacturing control is involved with managing and controlling the factory's physical operations so that the manufacturing plans can be carried out. Information goes back and forth between production control and factory operations, as well as from planning to control. Shop floor control, inventory control, and quality control are all part of this job. The challenge of monitoring the progress of the product while it is processed, assembled, transferred, and inspected in the factory is addressed by shop floor control. In the sense that the commodities being processed in the plant constitute work-in-process inventory, shop floor control is concerned with inventory.
As a result, inventory control and shop floor control overlap to some extent. Inventory control aims to establish a good balance between the risk of having too little inventory (which could lead to material shortages) and the cost of carrying too much inventory. It addresses challenges such as determining the appropriate quantity of materials to order and when to reorder a certain item when stock levels are low. The purpose of quality control is to guarantee that the product and its components meet the product designer's specifications for quality.
Quality control relies on inspection operations undertaken in the factory at various stages during the product's manufacture to carry out its function. Additionally, raw materials and component parts from outside sources are occasionally inspected upon receipt, and the finished product is inspected and tested to guarantee functional quality and aesthetics. Data collection and problem-solving methodologies to address quality-related process challenges, such as statistical process control (SPC) and Six Sigma, are also included in quality control.
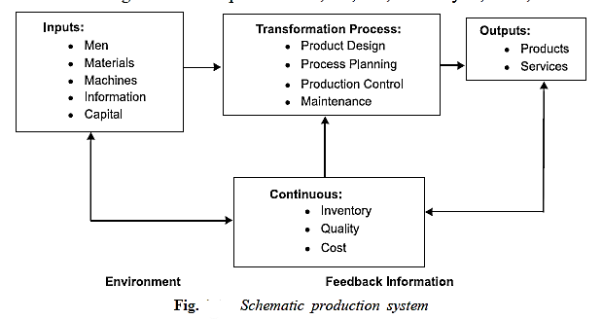
The following are the characteristics of the production system:
- Because production is a planned activity, each production system must have a goal.
- The system converts different inputs into useful outputs.
- It does not function in a vacuum from the rest of the organization's systems.
- There is activity feedback, which is necessary for controlling and improving system performance.
Classification:
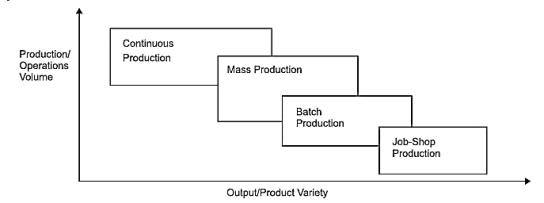
JOB SHOP PRODUCTION
Job shop production is defined as the production of one or few quantities of products developed and manufactured to clients' specifications within a predetermined time and cost. This is distinguished by its modest volume and wide range of products. A job shop is a collection of general-purpose machines organised into departments. Each work has its own set of technological requirements, requiring processing on machines in a specific order.
Characteristics
When there is a high diversity of products and low volume, the job-shop production system is used.
- General-purpose machines and facilities are used.
- Highly skilled operators who can approach each work as a challenge due of its individuality.
- A large supply of materials, tools, and parts.
- For sequencing the requirements of each product, capacity for each work centre, and order priorities, detailed planning is required.
Advantages
The following are some of the benefits of workshop production:
- A wide range of items can be produced using general-purpose machines and facilities.
- Operators will improve their skills and competence since each work provides them with new opportunity to learn.
- Operators' full potential can be realised.
- There is room for creative thinking and novel ideas.
Limitations
The following are some of the drawbacks of workshop production:
- Excessive set-up modifications result in higher costs.
- Higher inventory levels at all levels, resulting in higher inventory costs.
- Production planning is time-consuming.
- A larger amount of room is required.
BATCH PRODUCTION
"A method of manufacturing in which the job moves through the functional departments in lots or batches, and each lot may have a different routing," according to the American Production and Inventory Control Society (APICS). It is defined by the production of a small quantity of products at regular intervals, which are then stocked and sold.
Characteristics
In the following situations, a batch manufacturing system is used:
- When there are shorter production runs.
- When equipment and plant are adaptable.
- When a plant and machinery set up is utilised to create an item in a batch and a change in set up is necessary for the following batch to be processed.
- When compared to work order production, manufacturing lead time and cost are reduced.
Advantages
- Batch production has the following advantages:
- More efficient use of plant and machinery.
- Assists in the development of functional specialisation.
- When compared to work order production, the cost per unit is lower.
- Lower capital expenditures on plant and machinery.
- Ability to accommodate and process a large quantity of items with ease.
- Operators are satisfied with their jobs.
Limitations
Batch production has the following limitations:
- Because of the uneven and lengthier flows, material handling is complicated.
- Production planning and control are difficult to manage.
- When compared to continuous production, work-in-process inventory is higher.
- Increased set-up costs as a result of frequent changes in set-up.
MASS PRODUCTION
Mass production refers to the continuous manufacture of discrete pieces or assemblies. The high volume of production justifies this production strategy. A line or product arrangement is used to organise the machines. Standardization of products and processes exists, and all outputs follow the same path.
Characteristics:
When the following conditions apply, mass production is used:
- Product and process sequence standardisation.
- Dedicated special-purpose machines with increased output rates and production capacity.
- Many products
- Production cycle time is reduced.
- Inventory in the process is reduced.
- Lines of production that are well balanced.
- The flow of materials, components, and parts is continuous and error-free.
- It's simple to plan and control production.
- Material handling can be automated totally.
Advantages
Following are the advantages of mass production:
- Faster production rate with shorter cycle times.
- Due to line balancing, capacity utilisation is higher.
- Operators with fewer skills are required.
- Process inventory is low.
- The cost of production per unit is minimal.
Limitations
Following are the limitations of mass production:
- If one machine fails, the entire manufacturing line will come to a halt.
- Modifications in product design necessitate considerable changes in line layout.
- Significant investment in manufacturing facilities.
- The slowest process determines the cycle time.
CONTINUOUS PRODUCTION
From the beginning operations to the finished product, production facilities are organised according to the sequence of operations. Material handling devices such as conveyors, transfer devices, and other devices are used to make the objects move through the sequence of processes.
Characteristics
Continuous manufacturing is employed in the following situations
- Fixed plant and equipment with no flexibility
- The material handling process is completely automated.
- The process is carried out in a predetermined order.
- Component materials are difficult to distinguish from final product materials.
- Making plans and booking appointments is a common occurrence.
Advantages
Following are the advantages of continuous production:
- Product and process sequence standardisation.
- Faster production rate with shorter cycle times.
- Due to line balancing, capacity utilisation is higher.
- Material handling does not require any human intervention because it is totally automated.
- A person with little abilities can work on the assembly line.
- Because of the great volume of production, the unit cost is reduced.
Limitations
Following are the limitations of continuous production:
- There is no flexibility to accommodate and process a large quantity of items.
- Setting up flow lines requires a significant investment, and product differentiation is limited.
Productivity is a notion that may be applied to any economy, including small, medium, and big businesses, government, and individuals. Productivity is defined as the most efficient use of resources to produce as many goods and services as feasible at the lowest possible cost. Productivity is defined as the ratio of output to input during a given time.
The following formula can be used to calculate productivity:
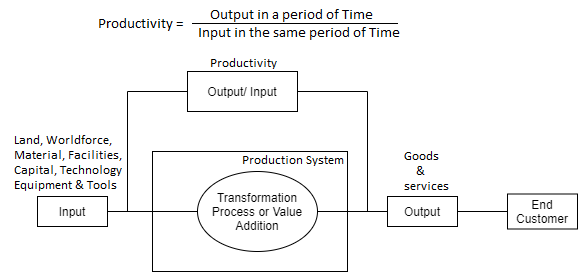
Simply expressed, productivity refers to the ratio of output to some or all of the resources utilised to create the output.
As a result, productivity can be quantified as follows:

Mathematically
"Productivity is the quantitative relationship between what a company creates and what it utilises as a resource to produce output, i.e., the arithmetic ratio of output (output) to input (input)."
Key Takeaway:

Mathematically
Measurement of Productivity
Productivity is a metric that measures how efficient a company's production is. Productivity is defined as total output divided by one unit of total input. After all, the bottom line is the ultimate indicator of a company's success, therefore productivity evaluations must show a link to profitability. Capital, labour, material, and energy are all inputs in every manufacturing process.
Each resource's productivity can be measured separately. A single factor productivity can be calculated using this method. The multi-factor productivity approach to assessing productivity is a method of calculating productivity using several resources. The productivity of all resources combined is referred to as total productivity (total productivity index). As a result, total productivity is determined by the productivity of all resources combined.
There are broadly three types of productivity measurements, and these are explained below:
- Single-Factor Productivity Measurement.
- Multi-Factor Productivity Measurement.
- Total (Composite) Factor Productivity Measures.
- Total Productivity Model
Single-Factor Productivity Measurement:
Single-Factor Productivity is a metric that compares output to a single input. The efficiency of one type of input is the focus of partial productivity. Its importance stems from the fact that it focuses on the efficient use of a single resource. Labor productivity is a single factor measure of productivity. It is the output to labour input ratio (units of output per Labor hour). The ratio of output to materials input is known as material productivity.
The ratio of machine units of output per machine hour, or output per unit machine, is known as machine productivity. The ratio of output to capital input is known as capital productivity, and it is measured in Rupees. The units of output per kilowatt-hour are known as energy productivity (Rupee value of output per kilowatt-hour).

Advantages of Single-Factor Productivity:
- Access to essential data is simple and straightforward.
- By analysing inputs independently throughout the outcome, it serves as a good diagnostic metric for identifying areas for improvement.
- Comparisons with other businesses in the industry are simple.
Disadvantages of Single-Factor Productivity:
Is misinterpreted as technological change or labour efficiency/effectiveness and does not reflect the entire success of the firm. If the focal areas of a business are not analysed appropriately, management may identify the wrong areas for improvement.
Multi-Factor Productivity Measurement:
Scott D. Sink established the notion of multi-factor productivity. The multi-factor productivity measurement model took labour, material, and energy as significant inputs. Capital was purposefully left out since estimating how much capital is expended per unit/time is extremely difficult.
Accounting's idea of depreciation makes estimating actual capital use even more complicated. The ratio of output to a group of inputs, such as labour, energy, and material, is known as multi-factor productivity. Multi-factor productivity is a measure of output derived from more than one of the production resources (inputs). It's the proportion of net output to the sum of associated labour and other costs.

Advantages of Multi-Factor Productivity:
- Considers a company's intermediate inputs.
- An industry's technical change is measured. Multi-Factor Productivity's Drawbacks
- Obtaining all the inputs is difficult.
- Communication of inter-industry links and aggregation is difficult.
Total (Composite) Factor Productivity Measures:
Only labour and capital are considered input elements in John W. Kendrick's Total Factor Productivity model, which he established in 1951. To increase labour productivity, a corporation may invest in more machinery, which will increase labour productivity while decreasing capital productivity.
As a result, the most significant contributions in the manufacturing process are believed to be labour and capital.
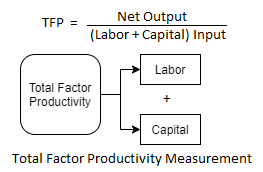
Advantages of Total Factor Productivity:
- Data collection and comprehension are simple.
- Ease of comprehension.
- Aggregation across industries is simple.
Disadvantages of Total Factor Productivity:
- Other inputs are disregarded, making this a poor indicator of technical change.
- Net output does not accurately reflect the efficiency of the industrial system.
Total Productivity Model:
David J. Sumanth established the Total Productivity Model in 1979, which included five inputs. These expenses include people, material, capital, energy, and other costs. Any manufacturing or service business can use this model.

Total Tangible Output = Value of finished units produced + Partial units produced + Dividends from securities + Interests from bonds + other incomes.
Total Tangible Inputs = Value of human inputs + Capital inputs + Materials purchased + Energy inputs + other expenses (taxes, transport & office expenses etc.).
Advantages of Total Productivity:
- All quantifiable inputs are considered.
- Sensitivity analysis can be done.
- Provides both firm level and operational unit level productivity.
Disadvantages of Total Productivity:
- Data is difficult to compute.
- Does not consider intangible factors of input and output.
Key takeaway:


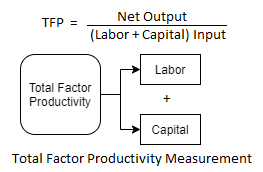
Productivity increase is a must-have in any company's operations plan. To be competitive, a company must constantly look for new methods to cut expenses and improve processes. Productivity improvement must become a managerial religion for companies functioning in global markets. Improvement in productivity must become a managerial religion. Production and operations strategies are used to boost productivity.
Operation strategy is concerned with establishing broad policies and procedures for utilising the firm's resources to effectively support the company's long-term competitive strategy.
Operations strategy, according to Schroeder, Anderson, and Cleveland (1986), consists of four components: mission, distinctive competency, objectives, and policies.
These four elements aid in determining what objectives operations should pursue and how they should be achieved. The resulting plan should be used to guide decision-making throughout the manufacturing process. As a result, an operations strategy is a vision for the operations functions that establishes a broad direction or push for decision-making.
What constitutes an operations strategy?
According to Laseter, the four most important aspects of your operations
Structure to consider in your operations strategy are:
- The level of vertical integration you want to achieve - Which value-adding activities do you want to do yourself versus which ones do you want someone else (e.g., an outsourcer, a supplier, etc.) to do?
- Capacity you want your operations to have - how much do you want to be able to create, and when do you want to be able to put that capacity online?
- Operating locations - Where do you want your operations to take place (both geographically and in terms of your customer's point of service)?
- Process Technology - Which technologies will you use to carry out your operations?
Types of operational strategy
Basically, there are two diametrically opposite business strategies that can be selected.
The first is a product imitator business strategy, which is defined by a mature, price-sensitive market and a standardised product. The operations mission would prioritise cost as a primary goal. Superior process technology, low human expenses, low inventory costs, a high degree of vertical integration, and cost-cutting quality assurance would all be used to minimise costs. The product imitator strategy would be practised and supported by marketing and finance.
Product innovation and new product introduction strategy is the second strategy. This strategy would typically be used in a developing or emerging market where the advantage is gained by releasing superior products in a short period of time. For competition, price is not the most important factor. In this case, operations will indeed flexibility· to introduce new products as a dominant objective in its mission. Operations policies include the product teams, flexible automation to be adapted to new products work force with flexible skills, outsourcing some key services and parts to retain flexibility. Japanese strategy believed and is successful in using imitator strategy.
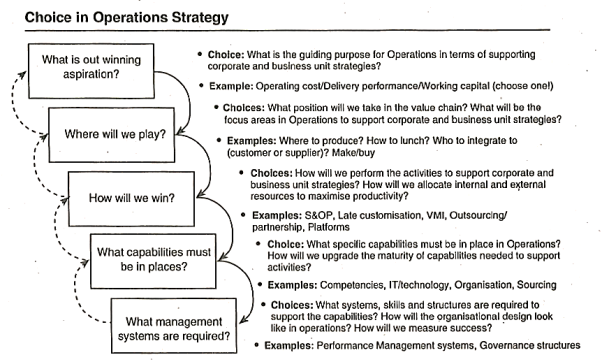
Core operational strategies
The ways corporations utilise to achieve their goals are referred to as operational strategies. A corporation can study and execute effective and efficient procedures for employing resources, staff, and the work process by designing operational strategies. Basic operational strategies are also used by service-oriented businesses to link long- and short-term company decisions and build an effective management team.
- Corporate Strategy
A company's strategy should be viewed as a system of interconnected parts. Each department in a corporation relies on the others to stay healthy and produce intended objectives, just as the muscles of the heart rely on brain activities in the human body. Additional fundamental strategies used by a corporation should complement the corporate strategy and involve cross-functional collaboration.
- Customer-driven Strategies
Customer-driven initiatives should be used in operational strategies to fulfil the demands and wants of a target market. To do so, a corporation must create plans that review and adapt to changing circumstances, consistently improve core capabilities, and continuously generate new strengths. When assessing environments, a corporation should keep an eye on market changes to seize new possibilities and avoid potential risks.
- Developing Core Competencies
A company's core competencies are its strengths and resources. Core competences vary by industry and business, but they can include having well-trained employees, having the best location for your organisation, and having marketing and financial expertise. A corporation can establish processes such as customer satisfaction, product creation, and building professional connections with stakeholders by defining core competencies.
- Competitive Priorities
The establishment of a company strategy, market analysis, identifying key processes, and completing a needs analysis all contribute to the formation of competitive priorities. A company examines operating expenses, product or service quality, the time it takes to produce and deliver a good or service, and the flexibility of a good or service in terms of variety, volume, and customisation to set competitive priorities. Being able to provide a high-quality product or service at a reasonable price that consistently meets the expectations of a customer should be a competitive priority.
- Product and Service Development
Design, innovation, and added value should all be considered in product and service development strategies. When it comes to developing new client products, a firm might choose to be first to market with a new product or service, wait for market innovations to improve upon them, or wait to see if a company's innovation is successful before moving forward.
Companies should consider bundling a service with instantly observable and psychological benefits, as well as support services, while designing it. When creating a product or service, a corporation should think about what its customers want, how it compares to the competitors, and how its technical metrics connect to their demands.
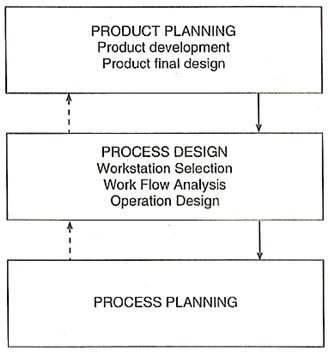
The key decisions affecting production and operations at the strategic level are those involving the design of physical processes for creating goods and services.
These considerations include process selection, technology selection, process flow analysis, and facility layout. The process type, degree of automation, physical layout, and task design are all substantially defined once these decisions are taken.
Apart from technical considerations, the process also includes social, economic, and environmental considerations. As a result, process design is a macroscope decision making of an overall process path for converting raw materials to finished products.
Functions of Process Design:
The important decisions in process design are:
- To analyse the workflow for converting raw material in to finished product (flow analysis)
- To select the workstation for each included in the workflow.
These two aspects of process design are interrelated and thus needs the simultaneous decisions regarding the two.
Choice of Technology:
Technology is defined as "the use of knowledge to address human problems; in a narrower sense, technology is defined as a set of techniques, tools, methods, procedures, and equipment used to produce commodities and services." Managers should be conscious of their understanding of the performance characteristics of the technology they supervise.
Possible effects of technology on inputs, outputs, process flow, and costs are among the performance criteria that managers might assess.
Process Selection:
Process selection is a high-level strategic choice on which types of industrial processes to include in the plant. Process selection is frequently considered as a layout challenge involving a lower-level decision. Process selection, on the other hand, is a higher-level (strategic) decision that influences operational costs, quality, and flexibility. Once a process is chosen, it binds the business to certain equipment, facilities, and types of labour, limiting future strategic decisions.
Types of Processes:
- Conversion Processes - conversion of raw materials into the finished products, i.e., conversion of iron ore into steel products.
- Fabrication Processes - changing raw materials into some specific form, i.e., making of a sheet metal into a storage box.
- Assembly Processes — mainly join parts already processed into subassemblies or final assemblies.
- Analytic, Synthetic and Modifying Processes.
The refining of crude oil into gasoline, diesel, and other products, for example, is an analytic process that breaks down the raw materials into their constituent constituents. Parts are combined into larger items via a synthetic method. For example, a car or a refrigerator.
In the metal working industry, modifying methods are employed. A casting or forging, for example, is machined to achieve precise dimensions and shapes.
Process flow characteristics:
Characteristics | Line flow | Intermittent flow | Project or job flow |
Product | Large batch or continuous | Batch type | Single or very few |
Variety | Low | Medium | Very large |
Market | Mass | Customized | Unique |
Volume | High | Medium | Single or very low |
Labour skill | Low | High | Very high |
Job nature | Repetitive | May repeat after some time | Non repetitive |
Investment | High | Medium | Low |
Plant & machinery | SPM | General purpose | General purpose |
Flexibility | Low | Medium | High |
Cost of product | Low | Medium | High |
Type of layout | Product | Process/ Group layout | Functional |
Planning & control | Easy | Difficult | Difficult |
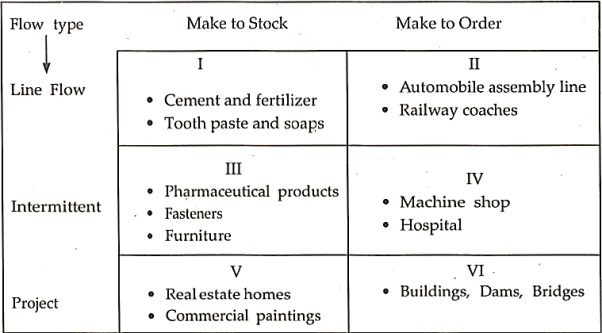
Process flow design:
The specific processes that raw materials, parts, and subassemblies follow as they travel through the plant are the focus of process flow design. The micro level process design decisions are process flow design and facility design. These micro-level decisions have an impact on other aspects of operations, such as scheduling and inventing. Pry levels, the types of jobs created, and the quality control system utilised
Assembly drawings, assembly charts, route sheets, and flow process charts are the most typical production management tools used to organise the process flow. Each of these graphs is a useful diagnostic tool that can be utilised to improve operations while the production system is in a steady state.
A series of flows connecting inputs and outputs can be considered as the process flow. The system approach aids in a more thorough examination of process flows that are part of the system.
Customer, outputs, inputs, supplier, boundaries, and transformation are all things that need to be considered.
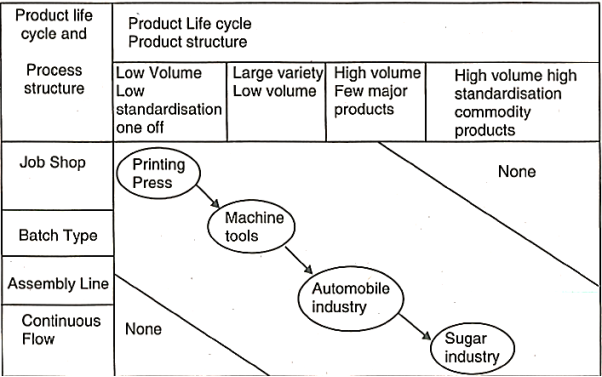
Material flow analysis:
The goal of material flow analysis is to reduce production throughput time (cycle time), as well as the time it takes to order, create, and distribute a product from beginning to end. This is accomplished by lowering waste. The material flow is described in greater detail for analysis using four types of principal types of documents:'. Assembly drawing, assembly charts, route sheets and flow process chart.
Information Flow Analysis:
The goal of information flow analysis is to make the process more efficient and effective. There are two types of information flows: one is the product of operations, and the other is used for management or decision-making for the aim of control.
Not only in the design of the new system, but also in getting approval for the new modifications, process flow analysis should take human factors into account. The easiest approach to do this is to include those who are affected at every stage of the diagnosis and design process. This has the effect of increasing individual ownership of new systems and lowering the fear of change. As a result, a socio-technical approach is required to consider physical flow design with job design. This strategy should provide processes that are both economically and humanely gratifying.
Process Planning Defined:
It is described as the methodical determination of ways for producing a product in a cost-effective and competitive manner. It entails selecting the appropriate equipment, determining the order of processes, specifying the inspection stages, as well as tools, jigs, and fixtures, to ensure that the product meets the specified specifications. At each component level, a thorough process map is created.
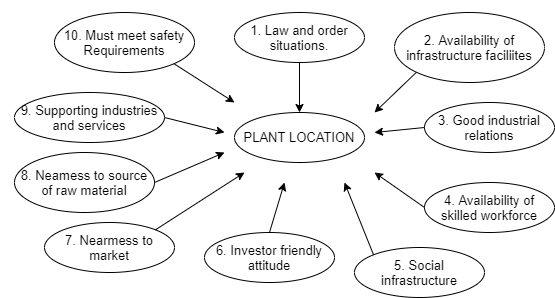
Availability of Raw Materials:
The availability of required raw materials is one of the most significant factors to consider when choosing an industrial location. The primary benefit of having raw materials close to where the industry is located is that it saves money on transportation. If the raw resources are perishable and must be utilised immediately, industries would always seek to locate closer to the source of the raw materials. Examples are the steel and cement sectors. Food and fruit processing, meat and fish canning, jams, juices, and ketchups are examples of small-scale industries.
Proximity to Market:
The evidence of pudding is in the eating, and the proof of production is in the eating. Without consumption, production has no value. Consumption entails a market, or the act of selling goods and services to customers. As a result, an industry cannot exist without a market.
As a result, when evaluating the market, an entrepreneur must examine not just the present sector and territory, but also the potential for expansion, newer regions, and competition locations.
Infrastructure Facilities:
Of course, the degree of reliance on infrastructural facilities varies by industry, but there is no doubting that the availability of infrastructural facilities is a deciding factor in an industry's location selection. Power, transportation and communication, water, banking, and other infrastructure facilities are included.
Government Policy:
To encourage entrepreneurs to establish enterprises in less developed and backward areas, the government offers a variety of incentives, discounts, tax vacations for several years, cheaper electricity supplies, industrial sheds, and other benefits. Then, when other considerations are compared, these factors become the most important in selecting where an industry should be located.
Availability of Manpower:
Another deciding factor for the location of skill-intensive companies could be the availability of essential workforce specialised in specific professions. The presence of technical training colleges in the area helps with the availability of competent labour. In addition, an entrepreneur should research labour relations by looking at turnover rates, absenteeism, and the level of trade unionism in the area.
Local Laws, Regulations and Taxes:
Polluting industries are not permitted to be established in high-risk locations, particularly those that are environmentally sensitive. The Air (Prevention and Control of Pollution) Act of 1981 is a famous example of such legislation barring polluting companies from being built in environmentally sensitive areas.
As a result, policies are enforced to decongest some locations while concurrently encouraging other places to limit industrial growth.
Ecological and Environmental Factors:
In some businesses, ecological and environmental problems such as water and air pollution may prove to be a negative consideration when determining where to locate a business. Manufacturing plants, for example, can damage water and air in addition to producing solid waste. Furthermore, in the case of such sectors, strict waste disposal restrictions drive up manufacturing costs to astronomical levels.
As a result, industries that are likely to harm an area's ecology and environment will not be built in such locations. Entrepreneurs will not be permitted to create such industries in such ecologically and environmentally sensitive locations by the government.
Competition:
In some businesses, such as retail establishments, where a site's earnings are contingent on its location, The proximity of other rivals' location plays a critical effect in the degree of competitiveness. When it comes to deciding where a business should be located. Areas where there is a lot of competition The new units will not be built in these industries. The, on the other hand, new businesses will thrive in locations where there is little or no competition. Such regions are well-established
Incentives, Land Costs, Subsidies for Backward Areas:
The government decentralises industries to less developed and backward areas of the country to promote balanced economic development. This is because progress accomplished on islands may only last so long. It's not difficult to figure out why.
Climatic Conditions:
In any country, including India, climatic conditions differ from place to location. Climate change has an impact on both people and manufacturing. It has a significant impact on human productivity and behaviour. Higher productivity thrives in a wild and frigid climate.
Similarly, several sectors require specialised climatic conditions in order to manufacture their products. The manufacturing of jute and textiles, for example, necessitates a high level of humidity.
Political Conditions:
Industrial development necessitates political stability. Political stability promotes economic development, while political turmoil stymies it, as seen by political situations in different countries and regions within the same country. It's not difficult to figure out why.
The important factors include:
- Trade barriers
- International customers
- International competition
- Regulations
- Additional resources
- Low cost
- Incentives
- Market access and proximity
- Customer responsiveness
- New, expanded markets
- Excess resources
- Exploitation of firm specific advantages
- Taxes
- Economies of scale
- Synergy
- Power and prestige
- Protect home market through offence in competitor's home.
Hundreds of hybrid design layouts exist, but they are all based on three core layout concepts that are designed to fit the needs of specific production processes. Process Layout Design, Fixed-Position Layout Design, and Product Layout Design are among the layout designs available. Each plan has its own set of pros and limitations, as well as its own material management setup. Material management is important in all three layouts, but it is practically required in the Product Layout Design approach.
Process (Functional) Layout:
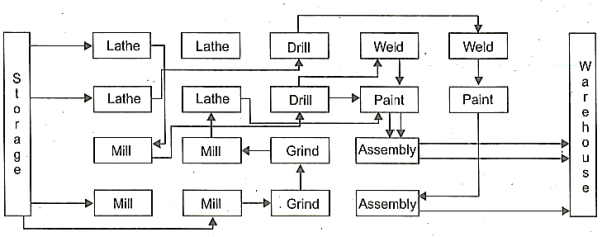
Machines are organised according to function to machine centres in the job shop layout. Individual product orders are sent through several machine centres to receive the necessary processing. Designed to make the process of processing products or providing services easier that have a wide range of processing needs Departments or sections are included in the design other functional groups in which similar types of tasks are carried out This kind of When the manufacturing process is arranged in batches, a plant layout is useful.
Personnel and equipment for the same task are assigned to the same location. The various items must be moved from one place to another in accordance with the previously specified sequence of procedures. The facility's multiplicity of products will result in a variety of flow patterns. Variations in production volumes from one period to the next (during a short period of time) may result in changes in manufactured quantities as well as the types of items to be manufactured.
Advantages
- Equipment and personnel flexibility.
- Cheaper initial investment due to a fewer number of machines and lower general-purpose machine costs.
- More efficient use of production facilities.
- More flexibility in how work is distributed among machines and workers.
- Supervisors will become extremely educated about the functions within their department, making the job hard and exciting.
Disadvantages
- In the handling of materials, backtracking and extended moves may occur, lowering material handling efficiency.
- Material handling cannot be automated, which increases costs.
- Process time is extended, resulting in lower inventory turnover and higher inventory investment.
- It's tough to plan and control production.
- There is a need for more space.
- Productivity has suffered as a result of the increased number of set-ups.
Product (Line) Layout:
In this case, the product (or products) follows a predetermined course through the manufacturing resources. The resources are structured in such a way that material transportation is minimised. When the production process is structured in a continuous or repeating manner, this form of plant layout is advantageous.
One of the most common facility layouts in the manufacturing industry is product layout design. Product layouts (also known as assembly lines) organise activities in a production line in accordance with a sequence of operations that must be completed in order to construct a specific product.
Product Layouts are best suited to mass manufacturing or repetitive processes with a high volume of demand. As a result, Product Layouts are more self-contained than the other designs outlined earlier. Materials must be moved in one direction and in the same pattern along the assembly line according to a Product Layout Design. The main challenge for Product Layout Design is balancing the assembly line such that no single workstation creates a bottleneck and slows down the flow of work. The Product Layout Design has the advantage of being efficient and simple to utilise. The downside is that it is rigid.
- Continuous flow
The layout design, as well as the equipment and machinery specifications, are used to achieve the correct operations flow. Flow that repeats itself (assembly line)
To avoid problems caused by bottlenecks, the correct operations flow will be based on a line balancing exercise.
The plant layout will be based on placing a machine as near as feasible to the next in line in order to create the product in the proper sequence. A work is broken down into a sequence of defined tasks, allowing for labour and equipment specialisation. Due to the enormous volume of production, the equipment on the line can be built to have a high level of fixed automation and require very little manual labour. The operations are organised in the order in which they must be completed to complete the product.
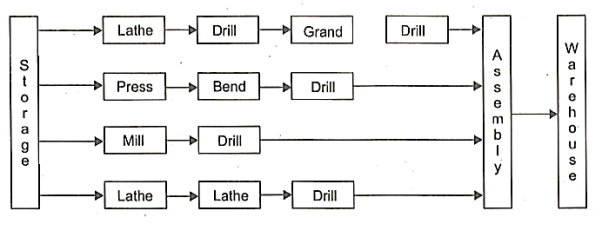
Advantages
- Mechanized handling systems and straight flow reduce material handling costs.
- Line balance is perfect, eliminating bottlenecks and idle capacity.
- Due to the continuous flow of materials, the manufacturing cycle is quick.
- Production, planning, and control have all been simplified.
- Inventory of work in progress is minimal.
- Unskilled personnel have the ability to learn and control production.
Disadvantages
- Inflexibility – A change in product may need a facility change.
- Significant financial outlay.
- Machines that are dedicated to a specific task.
- Each portion is dependent on the rest of the action. If any one of the machines in the sequence fails, the entire process may come to a halt. In terms of production.
Fixed position Layout:
For activities involving huge things, such as the fabrication of an electrical generator, the construction of a building, or the repair of a large aircraft, the machines that carry out the operation must come to the product rather than the product travelling to the machine. The item being worked on remains in fixed position layouts.
Workers, supplies, and equipment are moved around as needed. Big construction projects (buildings, power plants, and dams), shipbuilding, and the production of large aircraft and space mission rockets all utilise fixed positions layouts. The use of a fixed position is common. Utilised for farming, firefighting, road construction, house construction, remodelling and maintenance, and oil drilling
Advantages
- Material mobility is decreased, which reduces damage and transportation costs.
- Encourages employment expansion by allowing individuals or groups to do the entire task.
- The team ensures operational continuity and accountability. This eliminates the need to re-plan and train employees every time a new sort of activity begins.
- Extremely adaptable; can handle changes in product design, product mix, and volume.
- Production centres' independence allows scheduling to reach a minimum total production time.
Disadvantages
- Increased staff and equipment movement could be costly.
- Finding the right combination of abilities might be challenging, and high pay may be required.
- Equipment duplication is possible.
- Personnel have higher skill requirements as they are involved in more operations.
- General supervision is necessary.
- Time-consuming and costly material and machinery positioning.
- Low equipment usage because equipment may be left in a location where it will be needed again in a few days rather than being transferred to a productive area.
Key Takeaway:
- In Process layout keep similar machines and similar operations in one place. In other words, machines are arranged according to their function.
- Plant layout means the arrangement of equipment, material, etc facilities and services of the plant within the selected work area to achieve the productivity as high as possible.
- An ideal location is one where the cost of the product is kept to minimum, with large market share, the least risk and the maximum social gain. It is the place of maximum net advantage, or which gives lowest unit cost of production and distribution. For achieving this objective, small-scale entrepreneur can make use of locational analysis for this purpose.
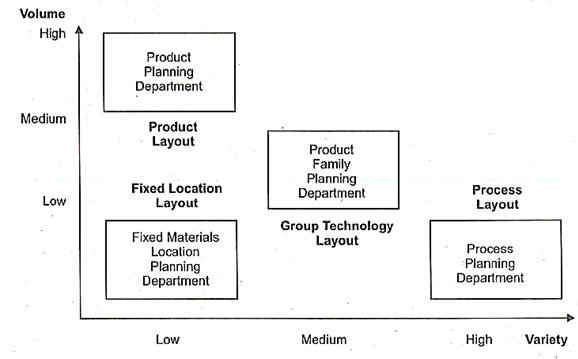
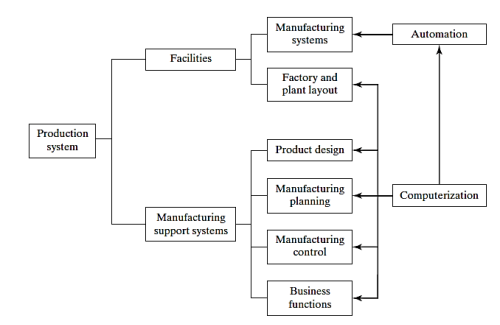
Computer Aided Layout or CAL is the design and/or improvement of facility layouts with the help from computer programs.
Advantages:
- The computer's processing capability and precision enable the development and evaluation of numerous alternative layouts.
- The computer solves each problem independently, using objective and methodical techniques, and may yield novel or unexpected arrangements.
- A clear problem and objective definition are required by the computer.
- The computer necessitates careful data preparation.
Disadvantages:
- Due to the limits of current CAL programmes, the layout problem must be severely simplified in order to be solved.
- The computer is unable to take into account subjective goals and/or limits.
The CAL programmes are quite helpful in the development of many alternative and preliminary plans, but they are currently incapable of producing a feasible final layout without human assistance and fine tuning. Human interpretation and revision are required for the layouts created by CAL programmes.
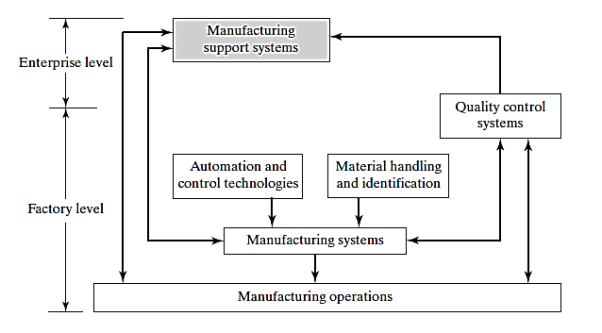
Product design is an important part of the manufacturing process. The quality of a product's design is almost certainly the most critical aspect in determining its commercial success and societal worth. No matter how well a product is created, if the design is inadequate, the product is bound to contribute nothing to the prosperity and well-being of the company that developed it. Even if the product design is good, the question of whether it can be produced at a low enough cost to contribute to the company's profitability and success remains.
One of the realities of product design is that the design determines a major amount of the cost of the product. In the production system, design and manufacturing cannot be separated. They are functionally, technologically, and economically intertwined.
The Design Process:
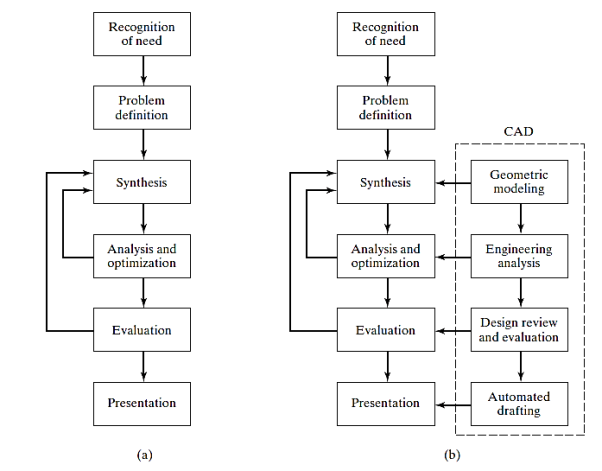
Computer aided Design:
Any design activity that involves the effective use of computer systems to generate, alter, analyse, optimise, and document an engineering design is referred to as computer-aided design (CAD). CAD is most usually connected with the use of a CAD system, which is an interactive computer graphics system. If the system contains both manufacturing and design applications, it is referred to as CAD/CAM.
With reference to the six phases of design, a CAD system can facilitate four of the design phases,
- Geometric Modelling
2 D & 3D Models ( Wireframe & Solid Modelling)

- Engineering Analysis
Stress–strain calculations, heat transfer analysis, and dynamic simulation may all be used in the analysis. The calculations are frequently complex and time-consuming, and prior to the invention of the digital computer, these studies were frequently considerably reduced or even deleted from the design process.
Mass property analysis
Interference checking
Tolerance Analysis
Finite element analysis
Kinematic & dynamic analysis
Discrete event simulation
- Design Evaluation & Review
Automatic dimensioning
Error checking
Animation of discrete event simulation solution
Plat layout design scores
- Rapid Prototyping
(RP) is a group of fabrication methods that allow engineers to make solid component engineering prototypes in a short amount of time. These technologies all manufacture the part directly from the CAD geometric model. This is normally accomplished by separating the solid object into a series of thin layers and then determining the geometry of each layer's region.
- Virtual Prototyping
Based on virtual reality technology, it entails using a CAD geometric model to create a digital mock-up of the product, allowing the designer and others to experience the genuine product without having to build a physical prototype. In the automotive industry, virtual prototyping has been used to assess new car type concepts. Even though there is no real model on display, the observer of the virtual prototype can analyse the appearance of the new design. Virtual prototyping can also be used to test the viability of assembly procedures such as part mating, part access and clearance during assembly, and assembly sequencing.
- Automated Drafting
- CAD Workstations
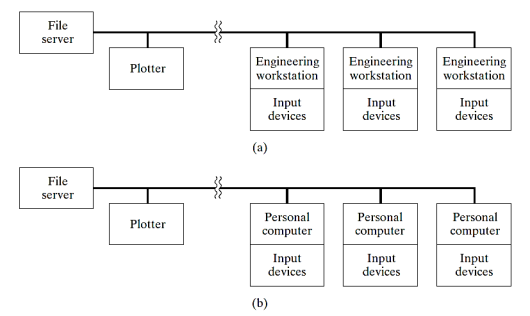
- Managing the product design
Huge amounts of data must be kept and managed as a result of the creative design process. Product data management is frequently used in modern CAD systems to fulfil these purposes. A product data management (PDM) system is made up of computer software that connects users to a central database that maintains design data such as geometric models, product structures (such as bills of materials), and related documents. The database is also managed by the software, which tracks user identities, facilitates and documents engineering modifications, keeps track of engineering changes on each part and product, and performs similar documentation activities.
Advantage of CAD Management system:
Increased design productivity
Increased available geometric forms in the design.
Improved quality of the design.
Improved design documentation.
Creation of a manufacturing database.
Design standardization.
Computer Aided Manufacturing:
Manufacturing Planning
Computer-aided process planning (CAPP)
CAD/CAM NC part programming
Computerized machinability data systems
Computerized work standards
Cost estimating
Production and inventory planning
Computer-aided line balancing
Manufacturing Control
Process monitoring and control
Quality control
Shop floor control
Inventory control
Just-in-time production systems
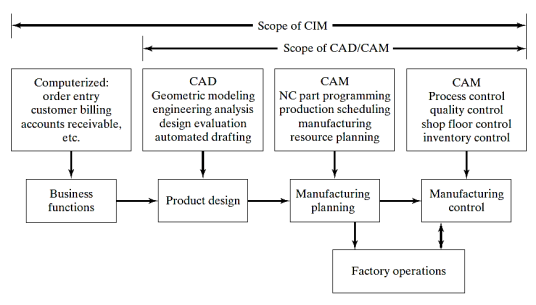
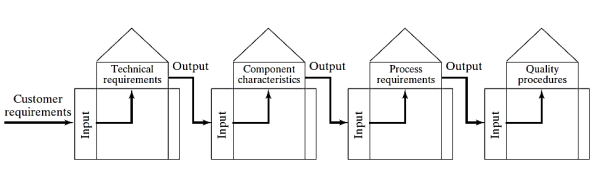
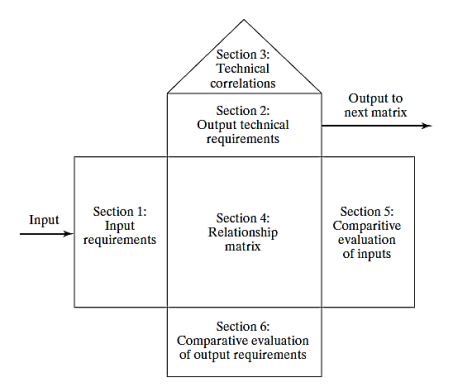
The term "assembly line balancing" refers to a product architecture in which products are processed as they move through a series of work centres. An assembly line is a "PRODUCTION SEQUENCE" in which pieces are put together to generate a finished product. At several workstations along the line, the procedures are carried out.
Advantages of Assembly Line (or flow line)
- Uniform rate of production.
- Less material handling.
- Less work-in-process.
- Easy production control.
- Effective use of facilities/labour.
- Less congestion.
Disadvantages
- More capital intensive (i.e., demands larger investments).
- Low flexibility.
- Monotony of work for operators.
Example:
For example, the production capacities of two machines, lathe and milling is as under for a particular job.
Lathe 50 pieces/hour
Milling 25 pieces/hour
If just one machine of each type is available, machine B will create 25 units per hour whereas machine A will generate 50. However, due to the sequence, only 25 units are created per hour, implying that machine A will only operate half of its capacity and will be idle for the remaining 30 minutes of the hour. By adding one more machine of type B to the production line, this idle time can be reduced.
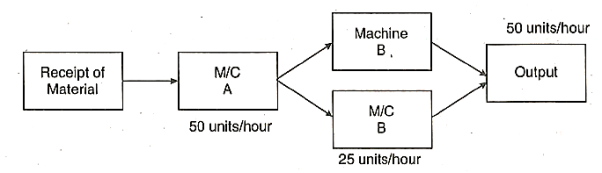
The Problem of Line Balancing arises due to the following factors
- The finished product is the result of many sequential operations.
- There is a difference in production capacities of different machines (The output from different machines is not identical).
Line balancing is the division of consecutive work operations into workstations to maximise labour and equipment utilisation and reduce idle time.
Definitions:
- Workstation: A workstation is a location on assembly line where given amount of work is performed.
- Cycle time: It is the amount of time for which a unit that is assembled is available to any operator on the line or it is the time the product spends at each workstation.

- Task: The smallest grouping of work that can be assigned to a workstation.
- Predecessor task: A task that must be performed before performing another (successor) task.
- Task time
: Standard time to perform element task.
- Station time
: Total standard work content of specific workstation.
- Balance Delay (BD): Percentage of total idle time on the line to total time spent by the product from beginning to end of line.
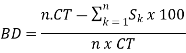
Were,
B. D. = Balance delay
n = number of workstations
CT = Cycle time
= Station time
Steps in solving line balancing problems:
- Define task.
- Identify precedence requirements.
- Calculate minimum number of workstations required to produce desired output.
- Apply heuristics to assign task to each station.
- Evaluate effectiveness and efficiency.
- Seek further improvement.
Three important parameters in line balancing,
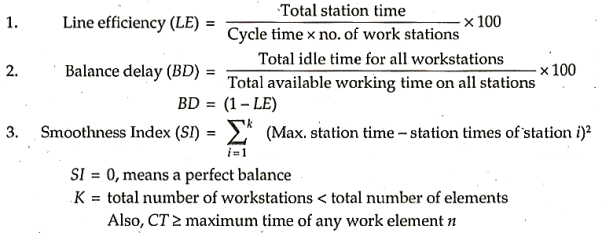
Heuristic Method,
In this method, numbers are assigned to each operation to denote how many predecessors it has. Those operations showing the lowest predecessor number are taken first on the workstations.
- Draw the precedence diagram of work elements first and then succeeding elements within the columns are assigned to workstation after all the elements of previous columns have been assigned.
- Select Cycle time (CT) which is feasible.
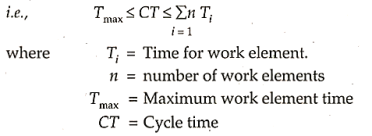
3. Assign work elements to workstations sum of elemental times should not exceed
4. cycle time (CT) while doing so proceed from column Ito column II and so on. Break intra column tie by using minimum amount of precedence.
5. Deduct assigned work elements from total elements. Repeat step (3).
6. If workstations (ws) time is more than CT, identify work element due to which this happens and carry it forward to next workstation.
7. Repeat steps (3) to (5) till all elements are fully assigned.
Example:
- Consider Sans, a specialty cake producer that just won a contract to supply a major grocery chain with a space rocket-shaped specialty cake. The supermarket's volume requirements have led to the decision that the finishing, decorating, and packing of the cake should be done on a separate manufacturing line. This line would be responsible for carrying out the items depicted in the following slide, which also includes a precedence diagram for the entire operation. The supermarket has placed an initial order for 5000 cakes per week, with the factory working 40 hours per week. As a result of this:





2. The precedence diagram is shown below for six workstations. Assign the work elements to workstations. Calculate line efficiency and balance delay
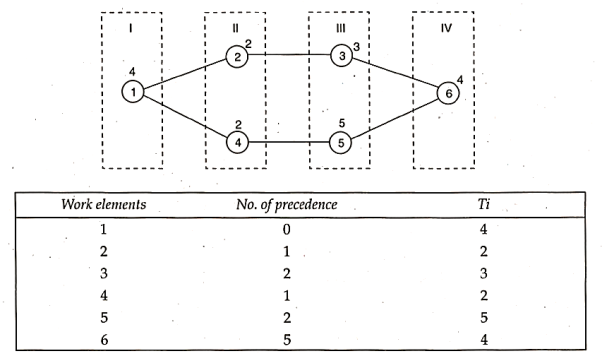
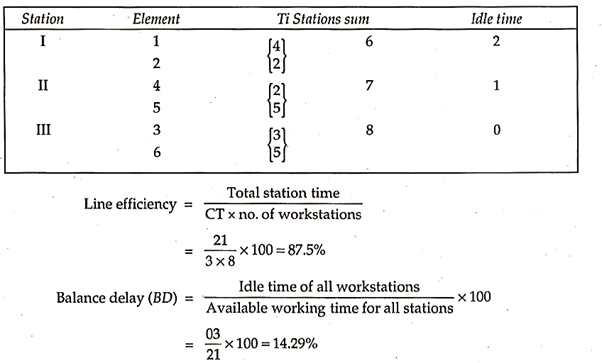
Key Takeaway:
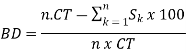
- Line efficiency (LE) =
- Balance delay (BD) =
BD = (1-LE)
3. Smoothness index (SI)=
SI = 0, means a perfect balance
K = total number of workstations < total number of elements
Also, CT maximum time of any work element n.
- Planning Principle: It is necessary to plan all handling activities.
- Plan a system that integrates as many handling actions as possible while also coordinating the entire scope of operations (receiving, storage, production, inspection, packing, warehousing, supply, and transportation).
- The Principle of Space Utilization: Make the most of cubic space.
- Increase the quantity, size, and weight of the load handled using the unit load principle.
- Gravity Principle: Whenever possible, use gravity to move a substance.
- Material Flow Principle: To optimise material flow, plan an operating sequence and equipment configuration.
- Eliminate or reduce unnecessary movement and/or equipment using the simplification principle.
- Safety Principle: Ensure that handling methods and equipment are safe.
- Mechanical or automated material handling equipment is used as a mechanisation principle.
- Standardization Principle: Standardize material handling equipment methods, types, and sizes.
- Principle of Flexibility: Use methods and equipment that can handle a wide range of tasks and applications.
- Equipment Selection Principle: Think about every facet of the material, move, and approach you're going to use.
- Dead Weight Principle: In mobile equipment, reduce the ratio of dead weight to pay load.
- Motion Principle: Material-transporting equipment should be continually moving.
- Idle Time Principle: Both MH equipment and people should have less idle time/unproductive time.
- Maintenance Principle: All handling equipment should be scheduled for preventive maintenance or scheduled repairs.
- Obsolescence Principle: When a more efficient method/equipment can improve operation, replace obsolete handling methods/equipment.
- Principle of Capacity: Use handling equipment to assist the facility reach its full capacity.
- Control Principle: Improve production control, inventory control, and other handling by using material handling equipment.
- Principle of Performance: Determine handling efficiency in terms of cost per unit handled, which is the key criterion.
The material handling equipment are classified based on:
- Types of services required: (1) Lifting, (2) Moving, (3) Stacking, and (4) Positioning
- Types of equipment
- Relative mobility of equipment: (a) Travel between fixed points, and (b) Travel over wide areas
- Movement of equipment.
On the floor.
Above the floor
Overhead.
Underground
- Categories of equipment
Conveyers:
Cranes and hoists.
Industrial trucks.
There are 4 main categories of material handling equipment:
- Bulk material handling
- Engineered systems
- Industrial trucks
- Storage and handling equipment
Bulk Handling Material Equipment
Bulk handling equipment is used for storing, controlling, and transporting items in bulk and loose form. The handling of food, beverages, liquids, metal goods (such as screws and nails), and minerals are only a few examples of its application.
These pieces of equipment, in general, are used to handle these objects when they are loose. A conveyor belt, for example, is used to carry products from one stage of the manufacturing process to another. Drums and hoppers can also be used to 'funnel' loose goods into a stage where they can be controlled or packaged more simply.
Horizontal transportation is done via conveyor belts. Elevators are the most common mode of vertical transportation.
Types of bulk handling material equipment
- Bucket and grain elevators
- Conveyor belts
- Hoppers and silos
- Reclaimers
- Stackers
Engineered Systems
The term "engineered system" refers to a system that is often automated. These systems are frequently made up of a multitude of components. When used together, they allow for both storage and transit.
One example of a system that is engineered is a 'Automated Storage and Retrieval System' (or AS/RS for short). This is a big, fully automated machine featuring racks, shelves, and aisles. A ‘shuttle,' a motorised vehicle akin to a cherry picker, is used to reach these storage options. The system operator can utilise this device to choose objects manually as needed, or the entire system can be digitised and automated.
To maintain track of stock control and other logistical systems, an AS/RS can be integrated with a production facility's current computer network. It can also be linked to other stages of the manufacturing process to provide as much automation as possible.
Types of engineered systems
- Automated guided vehicles (AGVs)
- Conveyor systems
- Robotic delivery systems
Industrial Trucks
This is another broad phrase that can be used to describe a wide range of devices. However, all these pieces of equipment have one thing in common: they all provide transportation.
This phrase can refer to small, hand-operated devices as well as large-scale powered vehicles. Some equipment, such as pallet trucks, can be driven, while others, such as forklifts, simply lend mobility to the materials being handled.
Many of these vehicles include beneficial features like forks or a flat surface that may be inserted underneath pallets or other storage platforms. Other vehicles require a separate piece of lifting equipment.
Trucks can elevate via powered or manual means and can be ridden in the driver's cab or simply pushed with power assistance. These tucks can be guided by humans or entirely automated, following a pre-determined path on the manufacturing floor, recessed, or raised rails, or coloured strips set out and sensed by optical sensors. Anti-collision equipment on these unmanned industrial trucks detects when an employee or other barrier is approaching.
Stacking trucks are used to stack objects, whereas non-stacking trucks are just used for transportation and not for loading products.
Types of industrial trucks:
- Automated guided vehicles (AGVs)
- Hand, platform, and pallet trucks
- Order pickers
- Pallet jacks
- Side-loaders
- Walking stackers
Storage and Handling Equipment
Storage equipment usually exclusively consists of non-automated objects. Automated storage and handling equipment is referred to as "engineered systems."
Storage equipment is used to keep products and materials safe while they are not in use or while they are waiting to enter or exit the manufacturing process. These intervals could be extensive or short, but they must allow for a sufficient build-up of stock or finished goods.
Pallets, racking, and shelves are the most common items classified as storage and handling equipment. Materials are stored in a neat and easy manner in preparation for transit or, if necessary, admission into the manufacturing process.
Having enough storage equipment will improve a company's productivity. The ease with which each stage of a manufacturing system functions maximises the efficiency of the total system. Any inefficient component of the system produces a bottleneck that affects all other areas further down the production line.
If you run a production setup, space is also limited. You'll be able to store more stuff if you make better use of your allocated space. As a result, you can keep your workflow running for much longer without having to worry about restocking. This will help you improve your efficiency even more.
Types of storage and handling equipment
- Drive-through or drive-in racks
- Pallet racks
- Push-back racks
- Shelving
- Sliding racks
- Stacking frames
Key Takeaway:
- The term ‘material handling equipment’ is a pretty broad one. There’s plenty of situations where it’s critical to move large and often heavy materials in a production environment. Any piece of equipment that helps with this process could be labelled ‘material handling equipment’.
- Plenty of items fall under this definition, from tools and storage units to vehicles and major appliances. Anything that deals with the transportation, storage and control at any stage of the processing of materials can be classified as material handling equipment. The term ‘bulk handling equipment’ refers to the storage, control and transportation of materials by bulk, and in loose form. There are plenty of examples of this application – the handling of food, beverages, liquids, metal items (such as screws and nails) and minerals are just a few.
- An engineered system is one that is typically automated. Such systems are also usually created from a variety of units. When combined, they work to enable both storage and transportation. This term is another broad definition that can be applied to many different types of equipment. Such pieces of equipment do have one thing in common, though – they all provide transportation.
- The scope of this term can include both small, hand-operated devices, and large-scale motorized vehicles. Some items can be driven, while others – such as pallet trucks – simply add mobility to the materials that are being handled.
- Equipment that is used for storage usually only encompasses items that are not automated. Storage and handling equipment that is automated falls under the term ‘engineered systems’
It is described as the methodical determination of ways for producing a product in a cost-effective and competitive manner. It entails selecting the appropriate machines, setting the sequence of processes, 1specifying the inspection stages, as well as tools, jigs, and fixtures to ensure that the product meets the specified specifications. Each component has its own specific process planning level
Process and Equipment Selection
- Economic considerations: Due analysis should be made with respect to the initial cost, maintenance and running cost. An alternative which results in lower total cost should be selected.
- Production rate and unit cost of production
- Durability and dependability Quality and reliability aspects.
- Lower process rejection
- 5Minimum set-up and put away times.
- Longer productive life of machines or equipment.
- Functional versatility-should be able to perform more than one functions.
The activities that are associated with process planning are
- List of operations to.be performed and their sequence.
- Specifications of the machines and equipment required.
- Necessary tooling's jigs and fixtures:
- Gives the manufacturing details with respect to feed, speed, and depth of, cut for each operation to be performed.
- It gives the estimated or processing times of operations
All the above information is represented in the form of a document called process sheet or route sheet. The information given in the process sheet can be used for variety of activities
- It becomes the important document for costing and provides the information on the various details like set-up and operation times for each job.
- The machine and manpower requirements can be computed from the set-up and operational times.
- Helps to carryout scheduling.
- The material movement can be traced.
- It helps in cost reduction and cost control.
- It helps in cost reduction and cost control.
- It helps to determine the efficiency of a work centre.
The information required for process planning
- Assembly and component drawings and bill of materials (part list)
- Machine or equipment details with respect to.
- The standard times for operation and details of set-up time for each job.
- Availability of tooling's (both standard and special purpose tooling’s).
Factors Affecting Process Planning
- Volume (quantity) of production.
- Delivery dates for components or products.
- Accuracy and process capability of machines.
- The skill and expertise of manpower.
- Material specifications.
- Accuracy requirements of components or parts.
- In-depth examination of component designs to discover key characteristics that influence process selection, machine selection, inspection stages, and tooling requirements.
- Make a list of the surfaces that will be machined.
- Basic processes are used to unite the surfaces to be machined. This stage assists in the selection of machines for use.
- Identify the workstation/tools, cutting tools, jigs and fixtures, as well as inspection stages and equipment.
- For each operation, determine the speed, feed, and cut depth.
- Calculate the duration of the operation.
- Calculate the entire time it will take to perform the job, including loading and unloading periods, handling times, and other allowances.
- On the process sheet, represent the specifics.
All manufacturing characteristics, as well as production equipment and tools, will be completely detailed in the process planning paperwork. However, the tooling engineer, who oversees designing and manufacturing the jigs/fixtures specified in the process plan, may identify tooling alternatives in some circumstances. As a result, to have a meaningful conversation with the tooling engineer, the process planner should be well-versed in the fundamentals of jig and fixture design. A discussion like this might include topics like:
- Type/size of machine tool
The type and size of the machine tool(s) to be utilised have a significant impact on the jig/fixture design. This is because the numerous component pieces, such as clamps and locators, must be included into the jig/fixture without interfering with the machine tool and tooling operation.
- Type/size of tooling
Although the process planner selects all production equipment and tooling, the tooling engineer may identify viable alternatives in some cases, as previously indicated. In terms of jig/fixture design, the two key challenges relating to type/size of tooling are ensuring that the workpiece is appropriately referred to the cutting tool and that adequate clearance is integrated to allow the tool to complete its activity, such as burr grooves.
- Sequence of operations
The tooling engineer will use the sequence of processes for two purposes. The first step is to figure out if more than one jig/fixture is needed and, if so, which one should be built first. The other is that the order in which procedures are performed has an impact on the selection of an appropriate clamping surface and placement.
- Orientation of the workpiece relative to the tooling
The orientation of the workpiece in relation to the tooling has two effects on the jig/fixture design. As previously stated, clearance for machining processes must be included into the jig/fixture, and the orientation of the workpiece is a crucial component in this. The position of locators and clamps will also be affected by the orientation.
- Cutting forces.
The cutting forces had previously been determined in order to verify that the production equipment and tooling could withstand them during processing. The cutting forces are applied in the same way in connection to the jig/fixture design, and they will have an impact on the rigidity and stability of the design. This will have an impact on the materials used for the jig/fixture, the type of jig/fixture to be utilised, as well as the size and weight of the jig/fixture.
Finally, the tooling engineer will conduct the analysis using external reference material, such as machine tool data and costing data, in addition to the process planning documents.
GT (Group Technology) is a manufacturing concept in which related pieces (geometry, manufacturing process, and/or function) are grouped together to produce a better level of integration between a company's design and manufacturing activities.
- A part family is a collection of comparable parts, and a machine cell is a collection of machineries used to process a single part family.
- Because group technology focuses on part families based on design and manufacturing commonalities, GT aids in the integration of CAD (Computer Aided Design) and CAM (Computer Aided Manufacturing).
Cellular layout:
The practise of identifying and bringing together related or comparable pieces in a manufacturing process to take advantage of the inherent economy of flow production methods is known as group technology. The term "cellular layout" refers to a layout in which machines are arranged into cells. The activities required to complete work for a group of related items or part families that require similar processing identify groupings.
Each cell is programmed to generate a member of the component family. A component family is a group of parts that share the same machinery, tooling, machine processes, and jig or fixture requirements. Normally, the parts in a family go from raw material to final parts in a single cell. Reorganization of machine layout is something to think about during implementation. Supervisors must also be knowledgeable in a variety of fields. Cell notions result in an unequal workload on machines and should be examined on a regular basis.
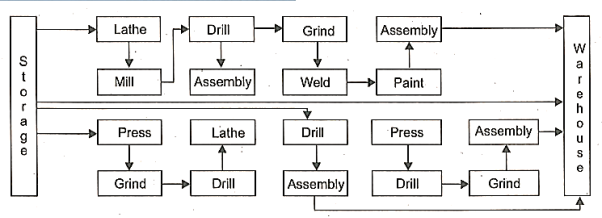
A flexible manufacturing system (FMS) is a highly automated Group Technology (GT) machine cell made up of a group of processing workstations (typically CNC machine tools) linked by an automated material management and storage system and managed by a distributed computer system.
"A system that comprises of several programmable machine tools connected by an automated material handling system," according to the definition of an FMS.
The FMS is named flexible because it can process several different component styles at the various workstations at the same time, and the mix of part styles and production volumes may be modified in response to changing demand patterns.
• The FMS is best suited to medium-variety, medium-volume production.
The ability to identify and distinguish among the different part or product styles produced by the system, (II) Quick changeover of operating instructions, and (III) Quick changeover of physical setup are three capabilities that a production system must have to be flexible.
FMS is intended for a specific application, i.e., a group of parts and procedures. As a result, each FMS is custom-engineered and one-of-a-kind.
FMS can be distinguished according to the kind of
Manufacturing operations they perform
1. Processing operations
2. Assembly operations
FMS can also be classified by
1. Number of machines.
2. Level of Flexibility
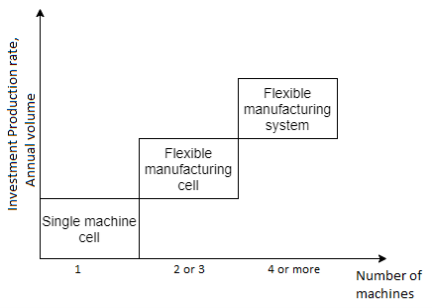
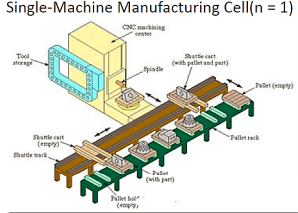
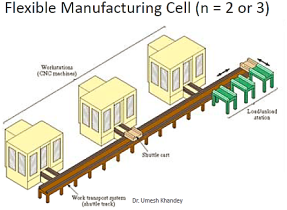
Types:
- In‐line
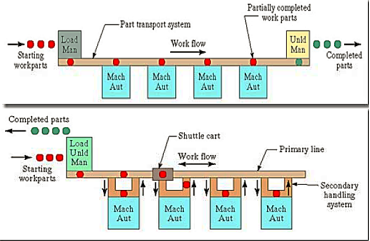
- Loop
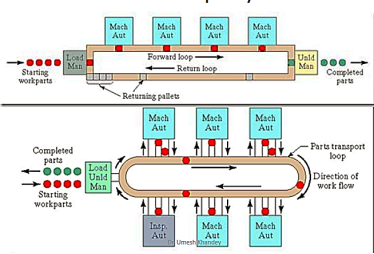
- Ladder
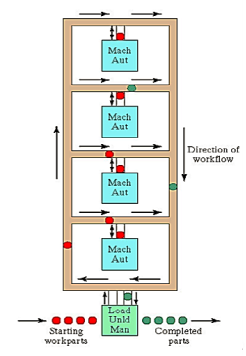
- Open field
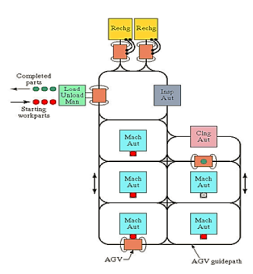
- Robot‐centred cell
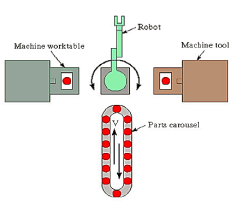
References:
- Industrial Engineering and Production Management by Martand T Telsang S. Chand Publishing
- Operations Research Theory & Applications by J K Sharma, Macmillan India Ltd,
- Automation, Production Systems & Computer Integrated Manufacturing by Groover, M.P. PHI
- Operations Research by P. K. Gupta and D. S. Hira, S. Chand & Co.
- FMS by Dr. Umesh Khandey ,Department of Manufacturing Eng, Hatia, Ranchi
- ASKIN R. G., and STANDRIDGE C. R., 1993 “Modeling and Analysis of Manufacturing Systems”. John Wiley and Sons, Inc
- SHANKAR, K., and SRINIVASULU, A., 1989, Some solution methodologies for loading problems in flexible manufacturing system, International Journal of Production Research, 27 (6), 1019-1034.