Unit - 4
Work System Design
Frederick Taylor (1859-1915)
Frederick Taylor is widely regarded as the founder of industrial management and engineering. Taylor, a mechanical engineer, was the first to construct an integrated theory of management concepts and methodology. He felt that a scientific approach to management could enhance labour efficiency. He suggested the following steps:
- Gather data on each aspect of the job and design standard operating procedures for employees.
- Instead of allowing workers to train themselves, scientifically select, train, and develop them.
- Strive for a spirit of collaboration between management and workers to create high productivity at a fair wage.
- Divide the workload between management and labour so that each group can focus on its strengths.
The above principles over the periods, developed into method study and work measurement, training, selection, placement, and Industrial relations. So, Taylor's contribution is
- Constitution of day's work
- Wage payment system
- Elimination of waste
- Training of workers
- Understanding between managers and workers
Frank and Lillian Gilbreth (1917)
Gilbreth made a significant contribution to the growth of motion studies. He developed method research as a technique for work analysis with the help of his wife. Gilbreth emphasised the connection between output and the worker's effort. Micro motion studies, a reduction of work into essential elements known as Therbligs, was established by him.
Work-study is the foundation for creating a work system. The goal of work design is to figure out how to get the job done in the most efficient way possible. Historically, the goal of this work study has been to improve the existing and planned ways of conducting work and to set regular work times.
“Work-study is a generic term for those techniques, method study and work measurement which are used in the examination of human work in all its contexts, and which lead systematically to the investigation of all the factors which affect the efficiency and economy of the situation being reviewed, in order to effect improvement."
Method study and time measurement are two strategies that are used in work-study.
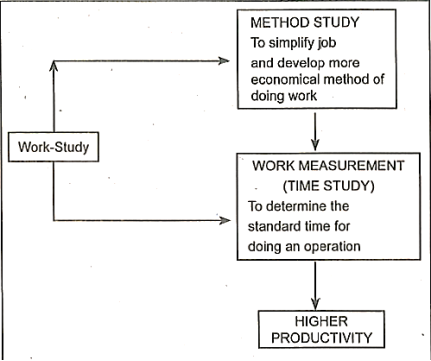
"Method study is the systematic recording and critical
Examination of existing and proposed ways of doing work, as a means of developing and applying easier and more effective methods and reducing costs."
"Work measurement is the application of techniques designed to establish the time for a qualified worker to carry out a specified job at a defined level of performance."
The method study and the work measurement are inextricably linked. Work measurement is concerned with investigating and reducing any ineffective time associated with the job, as well as establishing time standards for an operation carried out according to the standard method. Method study is concerned with reducing the work content and establishing the one best way of doing the job, whereas work measurement is concerned with investigating and reducing any ineffective time associated with the job and establishing time standards for an operation carried out according to the standard method.
Importance:
- Work-study is a method of increasing a company's production efficiency (productivity) by eliminating waste and redundant procedures.
- It is a method for identifying non-value-adding procedures by examining all of the elements that affect the job.
- It is the only method for establishing time standards that is both precise and systematic.
- It will add to profit because the savings will begin immediately and continue throughout the product's life.
- It has a wide range of applications.
Advantages:
- It aids in maintaining a steady production flow with minimal disruptions.
- It aids in the reduction of product costs by removing waste and superfluous activities.
- Improved management-worker interactions.
- Meets or exceeds the deadline.
- Reduced rejects and scrap, as well as better utilisation of the organization's resources.
- Assists in the improvement of working conditions.
- A more functional workplace layout.
- Contributes to the standardisation and simplification of existing processes or methods.
- Assists in determining the typical time for an operation or job, which is useful in workforce and production planning.
Work-study procedure:
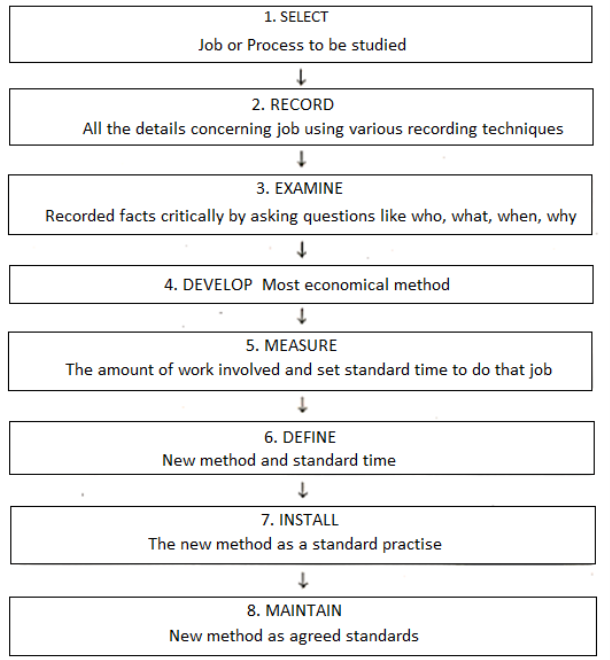
Work simplification and work-study:
Process management is critical to the product's and company's success. The goal of a method research is to identify the most important processes and process parameters. A thorough investigation is conducted to obtain all "essential details" in order to analyse the present process and break it down into sections (operations), making it easier to plan and control. To improve the process and achieve the intended level of output in terms of both quality and quantity, a complete study of the process inputs (personnel, material, and money) as well as the process parameters is carried out.
Work simplification begins with a thorough examination of the product and a thorough assessment of whether it can be changed to make it easier to create by decreasing waste, removing non-value-adding procedures, changing the design, and so on.
As a result, work-study is an effective instrument for work simplification.
Human considerations in work-study:
Only if a good relationship is developed between managers, supervisors, and employees can work-study become a powerful management tool for increasing productivity (workers).
Everyone involved as an individual should be given due care, and no one should perceive a threat to his security or self-respect.
As work-study is a participatory instrument for investigating the work being performed, it is critical to explore the link between work-study and workers, supervisors, and management.
Work-study and the management:
Management must maintain a favourable attitude toward all parties involved, including supervisors and employees. Traditionally, management has been preoccupied with changing the preoccupied belief that workers always do not want to work and putting too much emphasis on increasing labour productivity (making workers work hard) without taking into account other factors such as the working environment, technology, and worker motivation. Workers are the most important contributors to the organization's productivity and performance, and management should recognise this.
Workers should be adequately compensated for their contributions and given the opportunity to participate in decision-making about their jobs and work-related issues. As a result, management should foster an atmosphere of mutual trust and confidence in which everyone feels empowered to participate positively to the transformation.
As a result, work-study Because this strategy is worker-centred, adequate thought should be paid to their requirements, motivation, and issues in order to get the most out of it. Thus, management may gain a lot from work-study if it can persuade workers and unions of the program's goals, and there should be free and open communication between management and employees to get the most out of work-study.
Work-study and supervisor:
The work-study programme Because of the supervisor's or foreman's attitude, a guy will confront significant challenges. The success of work-study in all of its phases is dependent on the foreman, as he is the one who will cooperate with the work-study man on the shop floor.
Before the work-study begins, the entire aim of the work-study as well as the methods involved in the work-study must be thoroughly described to the foreman so that he fully comprehends what is being done. This makes the work of the work-study man easier since he will be able to communicate and persuade the workers about the goal and benefits of work study.
As a result, the work-shy individual must create trust and camaraderie, as well as sell his proposal, to gain the foreman's approval.
Work-study and the workers:
Improvements are achieved by changes in methods, procedures, and even some habits as a result of work-study. This change is always perceived as a threat to the workers' job security and familiarity. Humans are always resistant to change since it involves a great deal of uncertainty (probability). As a result, management and the work-study guy should be able to acquire the workers' acceptance and confidence by explaining why the change is necessary and how it would benefit both the workers and the organisation.
Workers' attitudes regarding work are rapidly changing, and they no longer accept boredom and repetition at work. Because they have had more years of schooling and exposure, they want to be masters of their own domain and make decisions about their work on their own. As a result, management now bears a bigger duty for constructively channelling their efforts into constructive outlets by providing an environment and climate in which people will feel connected and work to their maximum capacity. Work study from the perspective of the workers is garnering a lot of interest in this setting.
Work-study man:
Work-study men are expected to have certain skills and qualifications. He needs to be educated to the point where he understands the issues. If he is anticipated to take on extra responsibilities in the area of production management, a university degree in engineering is desirable.
Basic requirements are:
- Exposure and experience to the various production systems.
- A good knowledge of methods and systems of work-study.
- Objective approach to shop floor problems.
- A strong believer of improvement of work methods through work-study.
- Mentally suited to the work.
Personal Qualities:
- Sincerity and honesty.
- Enthusiasm.
- Interest in and sympathy with people.
- Good appearance and self-confidence.
- Tact in dealing with people.
Influence of method and time study on production activities:
The primary goal of production management is to produce the proper number and quality of items at the right time and at the right cost. Work-study is a technique for achieving this goal. The methods of manufacture are fixed during product and process design, and process planning is done using standard schedules and standard procedures. Methods analysis informs how the task should be completed, while time standards tell how long the job will take to complete. The impact of method and time on manufacturing activities is demonstrated.
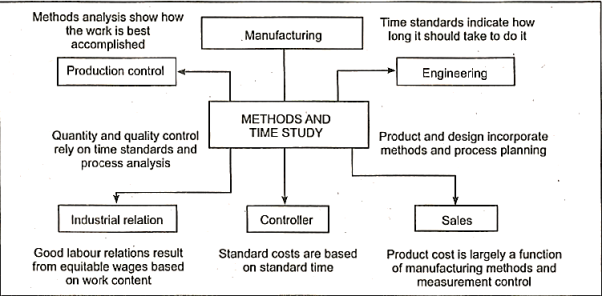
Process analysis and standard times aid in maintaining quality and quantity control. Standard costs are calculated based on standard timings, which aids in the examination of deviation between actual and standard costs. To stay competitive, product cost, which is a function of method and standard time, and cost control are critical. Compensation is calculated using standard time. This aids in the connection between pay and the nature of the task. As a result, work-study done in the proper spirit aids in the achievement of production goals.
Concept of work content:
The amount of work contained in each job is referred to as work content.
Basic work content:
Which is the theoretically required time to complete an operation or job. This is unavoidable. The following conditions will arise as a result of the basic work content:
• The layout and specifications are flawless.
• The manufacturing process is followed to the letter.
• There will be no loss of working time because of any of the factors.
As a result, the basic work content portrays an ideal situation that cannot be realised.
Excess work content:
In most cases, the actual time required to accomplish an operation or project exceeds the basic time. Excess work content refers to this additional portion of the work content.
Reasons for excess work content:
- Work content added due to defects in design or specification of a product
Bad design of the product.
Lack of standardisation of components.
Incorrect specifications and quality standards.
Faulty design of components.
- Work content added due to inefficient methods of manufacture
Improper selection of a manufacturing process/machine.
Wrong selection of tools.
Lack of process standardisation.
Improper layout of the shop/factory.
Inefficient methods of material handling.
- Ineffective time added due to shortcomings of the management
Bad working conditions.
Frequent production interruptions due to breakdowns.
Poor production planning and control.
Lack of safety measures.
Lack of quality mindedness.
Improper communication (lack of instructions).
Frequent changes in set-ups (smaller lot size).
Lack of performance standards.
Shortage of materials/tools.
- In effective time added due to reasons attributed to work man
Unauthorised absence from work.
Substandard performance.
Carelessness in working.
Unnecessary wastage of time (Idleness)
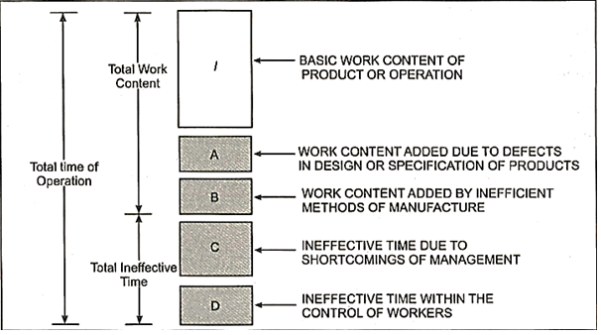
Techniques to reduce work content:
- Management techniques to reduce work content due to product
(a) Product development.
(b) Standardisation (variety reduction).
(c) Value analysis.
(d) Market research/consumer research.
- Management techniques to reduce work content due to process or methods
(a) Process planning.
(b) Methods study.
- Management techniques to reduce ineffective time due to management
(a) Product standardisation and simplification.
(b) Product specialisation.
(c) Standardisation of component.
(d) Production planning and control.
(e) Materials control.
(f) Plant maintenance.
(g) Safety measures and improved working condition.
- Management techniques to reduce ineffective time within control of the workers
(a) Sound personnel policies.
(b) Operators training.
(c) Safety training.
(d) Financial incentives.
Work-study as a tool to improve productivity:
Setting up the most effective technique of completing the operation (standard method) and control or effective resource utilisation are two fundamental responsibilities of production management.
These two needs will be met by a work-study that includes technique study and work measurement. The goal of a method study is to determine the most efficient method of performing the job, the most logical layout for manufacturing facilities, and an uninterrupted flow of materials throughout the organisation, all of which will aid in completing the job in the shortest possible time and at the lowest possible cost. Work measurement, on the other hand, determines how long it takes an operator to execute a standard method operation or job at a set level of performance.
Work-study is the most effective strategy for raising productivity because:
1. It is a straightforward way of increasing the organization's productive efficiency.
2. Considers all of the elements that influence production.
Key Takeaway
- "Work-study is a generic term for those techniques, method study and work measurement which are used in the examination of human work in all its contexts, and which lead systematically to the investigation of all the factors which affect the efficiency and economy of the situation being reviewed, in order to effect improvement."
- "Method study is the systematic recording and critical examination of existing and proposed ways of doing work, as a means of developing and applying easier and more effective methods and reducing costs."
- "Work measurement is the application of techniques designed to establish the time for a qualified worker to carry out a specified job at a defined level of performance."
The industrial engine.er can use method study to conduct a systematic analysis of each activity. The fundamental goal of method research is to minimise needless operations and find the optimal way to complete the task.
Method study is also known as job design or methods engineering. The term "method engineering" refers to a group of analysis approaches aimed at increasing the efficiency of humans and robots.
According to British Standards Institution (BS 3138):
"Method study is the systematic recording and critical examination of existing and proposed ways of doing work as a means of developing and applying easier and more effective methods and reducing cost."
The separation of an operation or procedure into its component pieces and their systematic investigation is what method study is all about. It is critical to have the correct mental attitude when conducting the method study. The method study man should have
- The desire and determination to produce results
- Ability to achieve results.
- An understanding of the human factors involved.
The goal of a method study is to improve work procedures by analysing processes and operations such as:
- Manufacturing operations and their sequence.
- Workmen.
- Materials, tools and gauges.
- Layout of physical facilities and workstation design.
- Movement of men and material handling.
- Work environment.
Objectives of method study:
Finding better methods to accomplish things is at the heart of method research. By eliminating superfluous activities, avoidable delays, and other forms of waste, it creates value and improves efficiency.
The improvement in efficiency is achieved through:
- Workplace layout and design have been improved.
- More efficient and improved work practises.
- Efficient use of people, machinery, and materials.
- The final product's design or specification has been improved.
The objectives of method study techniques are:
- To present and analyse the situation's genuine facts.
- To critically analyse such facts.
- To come up with the best feasible solution under the circumstances based on a careful evaluation of the facts.
Scope of method study:
The scope of method research isn't limited to the manufacturing sector. Method research techniques can also be used effectively in the service industry. ' It's suitable for use in offices, hospitals, banks, and other service businesses.
The areas to which method study can be applied successfully in manufacturing are:
- To improve work procedures and methodologies.
- To figure out the optimal order in which to do tasks.
- To improve layout and smooth out material flow with the least amount of backtracking possible.
- To improve working conditions and, as a result, labour productivity.
- To break up the monotony of the job.
- To increase the efficiency of plant and material utilisation.
- Waste and inefficient operations are eliminated.
- To lower production costs by shortening operating cycle times.
Steps involved in method study:
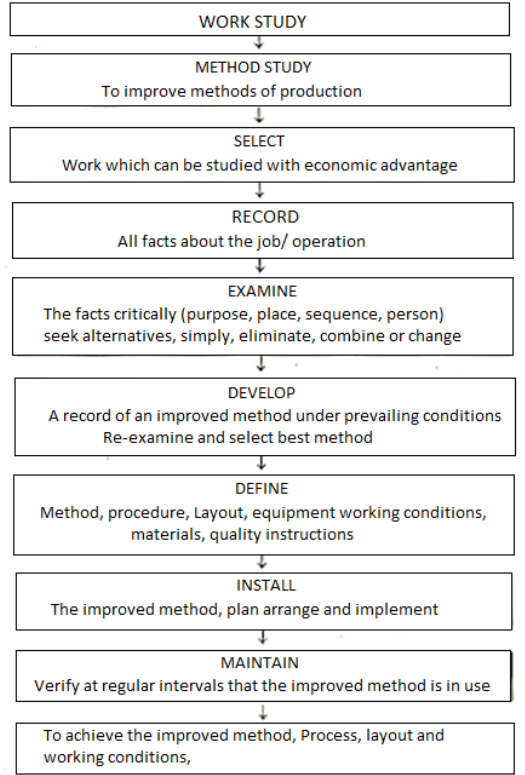
Selection of job for method study:
For methodologies analysis, cost is the most important criterion for selecting a job, process, or department. A job is chosen for the method research so that the suggested technique achieves one or more of the following outcomes:
- Increased quality due to fewer scrap.
- Increased output due to better resource utilisation.
- Unnecessary operations and movements are eliminated.
- A better layout leads to a smoother material flow and a more balanced manufacturing line.
- A better working environment.
For the method study, the job should be chosen based on the following factors:
- Aspect of the economy
If adequate results are not obtained, the entire operation will be a waste of time. As a result, the money spent should be justified by the money saved.
The guidelines below can be utilised to help you choose a job.
Bottleneck operations that stymie other production processes.
Operations that require a lot of labour.
Operations that generate a large amount of scrap or defectives.
Operations with inefficient resource utilisation..
Material backtracking and excessive material movement.
- Human aspect
Method research is a change because it will influence the way the job is currently done and is not totally supported by the workers and the union. The importance of human consideration in method research cannot be overstated. These are some of the scenarios in which the human element should be prioritised.
Workers complaining about unnecessary and tiring work.
More frequency of accidents.
Inconsistent earnings.
- Technical aspect
The technique study individual should choose a career for which he has the necessary technical skills and expertise. A guy who chooses a job in his field of expertise will do it justice.
Other variables that favour technical choices include:
Consistently high-quality work.
Operations that produce a lot of scrap.
A lot of complaints from co-workers about the job.
Recording Techniques:
Following the selection of the task to be analysed, the next step in the fundamental technique is to capture all details pertaining to the existing method. It is crucial to have some way of recording all of the necessary details about the existing approach in order to visualise the actions chosen for inquiry in their totality and to improve them through subsequent critical analysis. Records are extremely useful for comparing the effectiveness of the proposed better procedure before and after.
The recording techniques are intended to make the process of recording easier and more consistent.
Gilbreth invented the graphical way of recording. It is useful to utilise symbols instead of written descriptions to explain information simply, without ambiguity, and to enable people to comprehend them quickly and clearly.
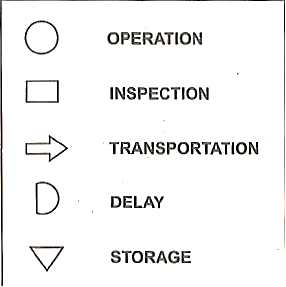
Recording techniques:
- Charts
- Diagrams.
- Templates and models.
Charts:
Charts is the most common way to keep track of information. Method study symbols are used to record the activities that make up the jobs. The charts must be prepared with considerable care so that the information they display is easily understood and recognised. The graphic should include the following information:
- A detailed description of the activities is provided.
- Is the charting for the current or proposed method?
- A specific reference to the start and end times of the activities.
- Wherever possible, time and distance scales are employed.
- The date of the charting and the name of the charting person
Operational process chart
It's also known as an outline process diagram. By capturing only the major operations and inspections involved in the process, an operation process chart provides a bird's-eye view of the entire process. Only two symbols are used in the operation process chart: operation and inspection.
- Visualize the entire sequence of operations and inspections in the process using an operation, process chart.
- Understand how the activity under investigation fits into the overall process.
- The graphic representation of the points at which materials are brought into the process and what operations and inspections are performed on them is shown in the operation process chart.
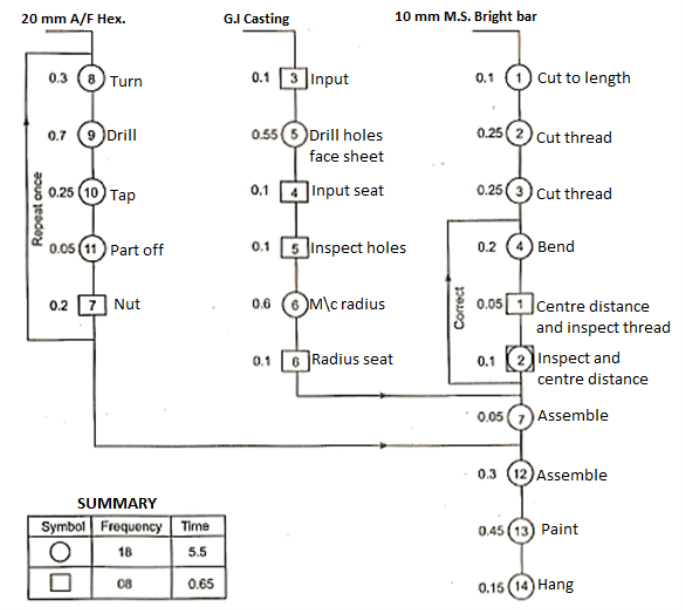
Process flow chart
The sequence of workflow of a product, or any component of it, through the work centre or department is represented by a flow process chart, which records the events using appropriate symbols. It is a simplified version of the operation process diagram, which depicts operations, inspection, storage, delay, and transportation. There are three types of flow process diagrams:
- Material type—This identifies the types of events that occur in materials.
- Guy type—Activities that a man engages in.
- Type of equipment—How the equipment is used.
The flow process diagram is beneficial.
- Men's travel distances should be reduced (or materials).
- To avoid unnecessary delays and waiting times.
- By merging or removing procedures, the cycle time can be reduced.
- To correct the operation order.
- The inspection stages will be relocated.
Flow process charts, like operation process charts, are created by inserting symbols one after the other. According to the occurrence of the. Activities, they are arranged below one another and connected by a vertical line. On the right-hand side of the activity icon is a brief explanation of the activity. On the left, the time or distance is indicated.
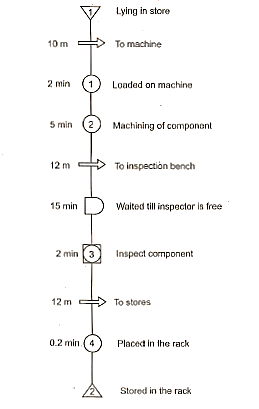
Two handed Process chart:
The most complex sort of flow chart is a two-handed (operator process chart), in which the activities of the employees' hands are recorded in connection to one another. The two-handed process chart is often limited to tasks done at a single location. This also provides a graphical picture of the worker's manual tasks in a synchronised manner. This chart can be used to:
- Visualise the entire sequence of activities in a repetitive task.
- Examine the layout of the workstation.
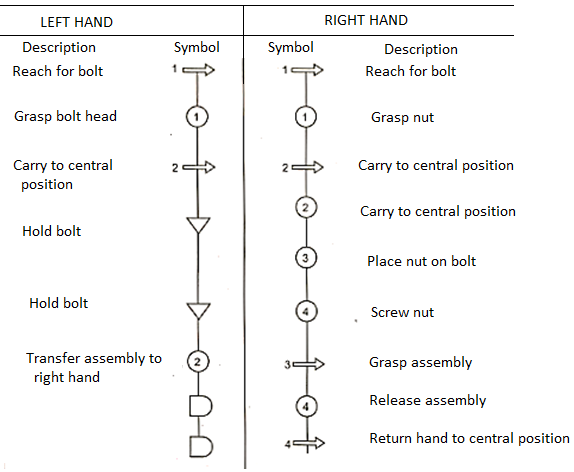
Multiple Activity Chart:
It's a graph in which the activities of multiple subjects (worker or equipment) are recorded on a similar time scale to demonstrate their interdependence. A multiple activity chart is created to
- Investigate man and machine idle time.
- Determine the number of machines that can be operated by a single operator
- Determine the number of operators needed in a team to complete the project.
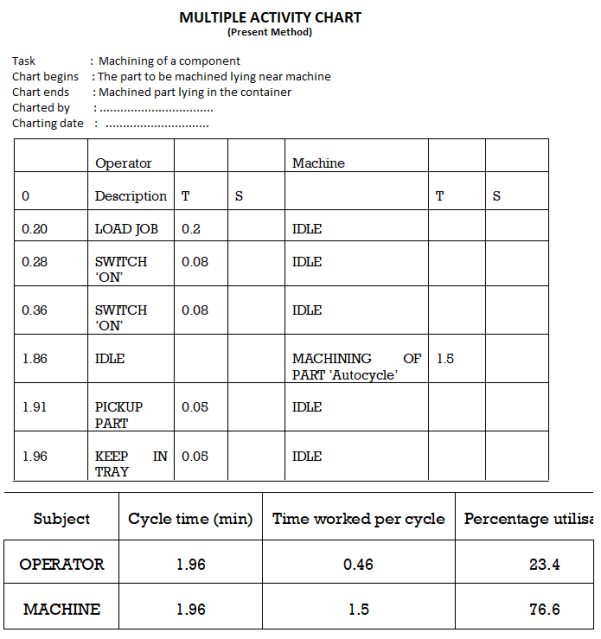
Diagram:
The flow process diagram displays the sequence and character of movement, but not their path. Congestion, retracing, and unnecessary long moves are all common characteristics of movement pathways. To record these unnecessary aspects, a representation of the working area in the form of flow diagrams or string diagrams can be created:
- Examining a variety of layout options and deciding on the best one.
- To look at the amount of traffic and how frequently it occurs along the plant's various routes.
- When moving, backtracking and obstructions are detected.
Flow diagram:
A flow diagram is a depiction of the working area that is drawn to scale and shows the position of the various activities that are indicated by numbered symbols and are related with a specific flow process chart that is either man type or material type.
The routes taken in transportation are depicted by connecting the symbols in a sequence with a line that symbolises the subject's journey or movement as closely as possible.
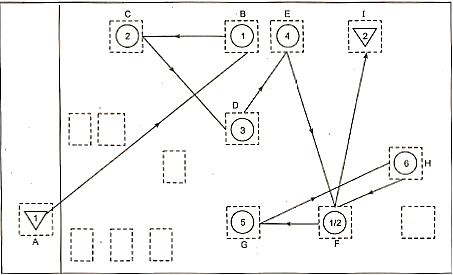
String Diagram:
A string diagram is a scale layout drawing in which the length of a string is used to record the extent and pattern of movement of a worker operating inside a constrained space over a period of time. It's especially useful when the journeys are so erratic in terms of distance and frequency to be able to observe exactly what's going on.
A string diagram's main purpose is to provide a record of an existing set of conditions so that determining what is actually happening is as simple as feasible.
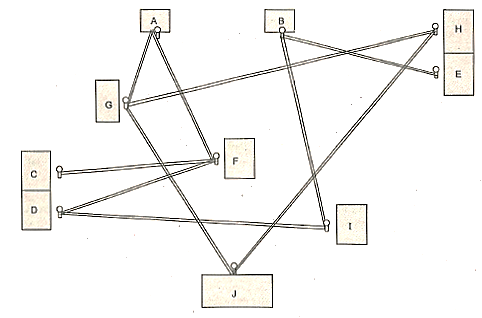
An approach for recording and timing an action is micro-motion studies. Micromotion study is a set of techniques designed to divide human activities into groups of movements or Micro-motions (also known as Therbligs), and the study of such movement’s aids in the discovery of the best pattern of movement for an operator that takes less time and effort to complete the task. Frank B. Gilbreth, the originator of motion study, suggested therbligs. Micro-motions analysis was originally used for work analysis, but it has since found other applications. The following are some of the uses of micro-motion analysis:
- Is it possible to study the activities of two or more people in a group?
- As a tool for analysing the relationship between the operator's and the machine's activities in order to time operations.
- To assist in the acquisition of motion time data for time standards.
- Serves as a permanent record of the operator's and machine's methods and times of operation.
The idea behind the micro-motion method group is to divide human activity into divisions of movements or groups of movements (Therbligs) based on the reason for which they are made. Gilbreth distinguished 17 fundamental hand or hand and eye motions, with an additional eighteen added afterwards. For recordkeeping purposes, each Therblig has its own colour, symbol, and letter.
Therbligs refers to the motions of the human body at work and the mental activities that go along with them. They provide for far more precise and extensive descriptions of the work than any other recording method.
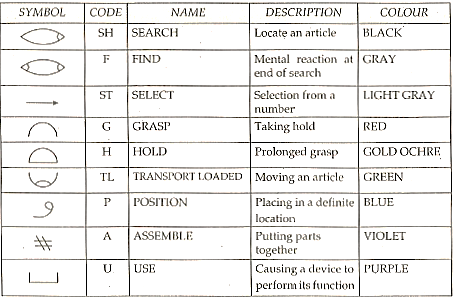
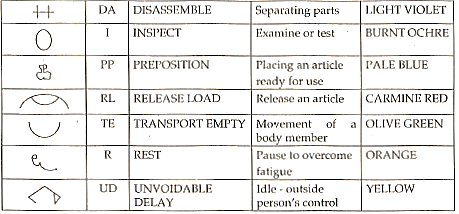
The following are the steps in a micro-motion study:
- Creating a video of the operation to be studied.
Filming the Operation: In a micro-motion research, motion photographs of an activity are taken while it is being conducted by an operator. A 16 mm movie camera, 16 mm film, a wink counter (micro-chronometer), and other standard photographic tools are required to make a film or video tape of the operation.
A micro-chronometer (also known as a wink counter) is a timing device that is positioned in the filming field of view. Winks are used to keep track of time. 1 blink equals 1/1000 of a minute
- Data from the films are analysed.
Analysis of Data from Films: After the procedure has been filmed and the film has been processed, the film is examined using a projector for micro-motion analysis.
The following is a breakdown of the film:
The film is played at a typical pace to familiarise the audience with the movement pattern.
From the filmed work cycles, a typical work cycle is chosen.
To detect the motions, the film is run at a very slow pace and constantly stopped or reversed (therbligs).
Therbligs are recorded in the analysis sheet after they have been identified.
- Keeping a record of the information
Recording of Data is Done Using SIMO Chart.
The Simultaneous Motion ‘Cycle Chart (SIMO chart) is a micro-motion capturing tool. A SIMO chart is a chart based on film analysis that is used to record therbligs or a set of therbligs done by distinct areas of the body of one or more operators on a common time scale.
It is the man type flow process chart in micro-motion. A complicated technique and the use of expensive equipment are necessary to construct a SIMO chart, and this study is warranted when the savings coming from the study will be quite high.
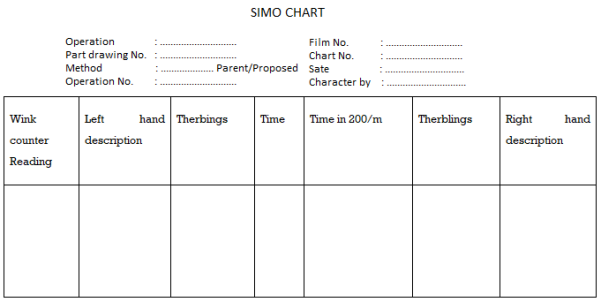
The principles of motion economy are a set of guidelines and recommendations for improving manual labour in manufacturing and reducing worker fatigue and superfluous motions, which can contribute to a reduction in work-related trauma. At the workstation or sub-micro level, motion economy aids productivity and reduces cumulative trauma. The Motion Economy Principles remove wasteful motion, make Operator jobs easier, reduce fatigue, and lessen cumulative injuries like Carpal Tunnel and Tendonitis.
The principles of motion economy are a set of guidelines and recommendations for improving manual labour in manufacturing and reducing worker fatigue and superfluous motions, which can contribute to a reduction in work-related trauma.
At the workstation or sub-micro level, motion economy aids productivity and reduces cumulative trauma. A better method of executing a job is one that uses the least amount of time and energy to conduct limb (hand, foot, leg, etc.) motions in order to complete the task, which is made feasible by economising motion use. They were first employed by Frank Gilbert, the father of motion analysis, and have since been expanded upon by others, most notably Professor Barnes.
They are recommendations that can be used to help determine Work method, Workplace layout, Tools, and equipment. They were developed over many years of practical experience in work design. The goal is to maximise efficiency while reducing worker tiredness.
The three categories of motion economics principles are as follows:
- Principles that apply to the human body's use.
- Principles that apply to the arrangement of the workplace
- Principles that apply to tooling and equipment design
Use of Human Body:
- The two hands should begin and complete their movements at the same time
- The two hands should not be idle at the same time expect during periods of rest
- Motions of the arms should be made simultaneously
- Hand and body motions should be made at the lowest classification at which it is possible to do the work satisfactorily
- Momentum should be employed to help the worker but should be reduced to a minimum whenever it has to be overcome by muscular effort.
- Use momentum to facilitate task
- Take advantage of gravity- ·don’t oppose it
- Method should achieve a natural cadence of the motions. Involved
- Use lowest classification of hand and arm motion (five classifications)
- Minimize eye focus and travel
- The method should be designed to utilize the worker's feet and legs when appropriate.
Workplace arrangement:
- Locate tools and materials in fixed positions within the work area
- Locate tools and materials close to where they are used
- Locate tools and materials to be consistent with sequence of work elements
- Gravity feed bins and containers should be used to deliver material close to the point of use.
- Drop deliveries should be used wherever possible.
- Materials and tools should be located to permit the best sequence of motions.
- Provisions should be made for adequate conditions for seeing. Good illumination is the first requirement for satisfactory visual perception.
Related to the Design of Tools and Equipment
- The hands should be relieved of all work that can be done more advantageously by a jig, a fixture, or a foot-operated device
- Two or more tools should be combined wherever possible
- Tools and materials should be prepositioned whenever possible
- Where each finger performs some specific movement, such as in typewriting, the load should be distributed in accordance with the inherent capacities of the fingers
- Levers, hand wheels and other controls should be in such positions that the operator can manipulate them with the least change in body position and with the greatest speed and ease.
Time study has been defined by British Standard Institution as "The application of techniques designed to establish the time for a qualified worker to carry out a specified job at a defined level of performance."
Objective:
1. Comparing alternative methods.
2. Assessing the correct initial manning (manpower requirement planning).
3. Planning and control.
4. Realistic costing.
5. Financial incentive schemes.
6. Delivery date of goods.
· 7. Cost reduction and cost control.
1 8. Identifying substandard. Workers.
9. Training new employees.
Techniques of work measurement:
It is critical for practitioners to know what they wish to study while doing a time study. Work is a process, not just a series of disconnected activities. These processes have names like maintenance or transfers, and they start with inputs and progress to activities in the future which inputs are changed, and finally, outputs due to the high cost of time studying,
Care is important in terms of both wasted work time and tapping employee trust and engagement. They must be planned carefully. To think through a moment, follow these eight basic actions.
- Know Why the Study is Being Conducted
- Understand and Articulate the Different Types of Work to Measure
- Measure Work Elements Down to a Level of Desired Complexity
- Ensure the Study Takes Place during a Representative Time Period
- Allow the Process to 'Settle Down' Before Recording Results
- Use Good Sampling Procedures for Reliable Results
- Understand the Basic Measures of Central Tendency
- Learn some common terms
Inputs such as consumer needs and transaction volumes are referred to as demand.
It is difficult or impossible to quantify demand without a time standard.
The quantity of work a team can complete in a given length of time is referred to as capacity.
The efficiency with which capacity is applied based on demand is known as utilisation. It is one type of productivity metric.
The ability to employ capacity metrics to adjust the workforce to changing demand is known as demand management. This is only possible with a clear awareness of the team's capabilities.
When work is assigned based on transaction categories rather than time criteria, capacity imbalances might occur. An organization's capacity can be balanced by using time criteria. When capacity is balanced, utilisation rises, allowing for the pursuit of other value-added activities when everyone is working to capacity and contributing their fair part.
The ability of a manager to find the right balance between capacity and demand is measured by utilisation. Demand, capacity, seasonal considerations, and other constraints such as turnover, training time, vacation time, and so on will all influence utilisation. As a result, it's critical to rebalance on a frequent basis.
Techniques of work measurement:
1. Repetitive Work: Work in which the principal procedure or combination of processes is repeated repeatedly throughout the duration of the job. These rules apply to work cycles that are only a few minutes long.
2. Non-repetitive Work: This category comprises various types of maintenance and construction work in which the work cycle is rarely repeated in the same way.
Various techniques of work measurement are:
1. Time study (stopwatch technique)
2. Synthesis
3. Work sampling
4. Analytical estimating
5. Predetermined motion and time study
Time study and work sampling involve direct observation and the remaining are data based and analytical in nature.
- Time study: A work measuring approach for documenting the times and rates of work for the elements of a certain project performed under specific conditions and analysing the data to determine the amount of time required to complete the job at the defined level of performance.
- Synthetic data is a work measurement technique that totals element times received previously through time studies on other tasks including the elements in question or from synthetic data to build up the time for a job or parts of a job at a predetermined level of performance.
- Work sampling is a technique in which a large number of observations of one or more machines, processes, or personnel are made over a period of time. Each observation documents what is happening at that precise moment, as well as the percentage of observations recorded for that specific. The proportion of time that an activity is delayed is measured by the activity's m delay.
- PMTS (Predetermined Motion Time Study): A work measuring technique in which times for basic human motions (classified according to the nature of the motion and the conditions under which it is made) are used to build up the time for a job at a given level of performance. The most widely used PMTS is called Methods Time Measurement (MTM)
- Estimating Analytically: A work measurement technique that is a development of estimating in which the time required to complete pieces of a job at a set level of performance is estimated using a combination of knowledge and practical experience with the elements in question, as well as synthetic data.
S.No. | Techniques | Applications | Unit of Measurement |
![]() | Time study | Short cycle repetitive jobs. Widely used for direct work | Centi minute ![]() |
![]() | Working sampling | Long cycle jobs/heterogeneous operations. | Minutes |
![]() | Synthetic Data | Short cycle repetitive jobs | Centi minutes |
![]() | MTM | Manual operations confined to one work centre | TMU (1 TMU=0.006 min) |
![]() | Analytical estimating | Short cycle non-repetitive job | Minutes |
Steps in Making Time Study:
- Choose the work that will be examined.
- Gather and document all available information regarding the job, the operator, and the working environment that are likely to affect time study work.
- Break the procedure down into its constituent parts. A discrete aspect of a specific activity is an element, which is made up of one or more fundamental motions chosen for ease of observation and timing.
- Measure the time taken by the operator to complete each aspect of the process using a stopwatch. Timing could be done in two ways: continuously or with a snap back.
- Evaluate the operator's effective work pace in comparison to the observer's definition of "Normal" speed. This is referred to as performance evaluation.
- To obtain normal time for each element, adjust the observed time by the rating factor.

- Allow for fatigue, personal needs, contingencies, and other factors to arrive at a standard time for each element.
- Calculate the total time permitted for the job by summing elemental standard times and considering the frequency of each element's occurrence.
- Write a detailed work description that explains how the standard time is determined.
- If necessary, test and revise standards.
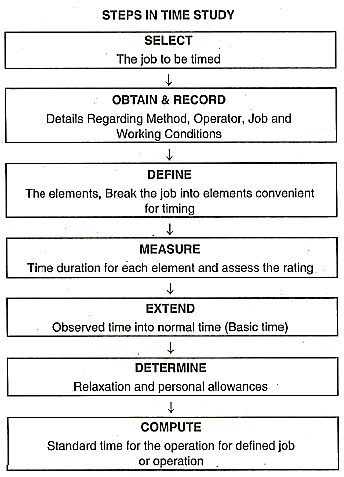
- Selecting Job for Time Study:
The following are some of the reasons why time study may be done:
- The job in issue is new or has never been done before.,
- Modification of the present time standard's technique.
- A complaint about the time standard has been received from workers or unions.
- A certain operation creates a bottleneck, causing a number of subsequent tasks to be delayed.
- A shift in management policy involving the application of time standards, such as general purpose or wage incentive plans.
The general guidelines for selecting the job for time study:
- Bottle-neck operations.
- Repetitive jobs.
- Jobs using a greater deal of manual labour.
- Jobs with longer cycle time.
- Sections/department frequently working overtime.
2. Obtaining and Recording Information
During this step, all the relevant and necessary information regarding the method, operator and details of working conditions are recorded:
3. Breaking the Jobs into Elements
After the essential information about the work and the operator has been recorded, the next step is to split the job down into pieces.
A unique section of a certain job chosen for ease of observation, measurement, and analysis is referred to as an element.
A work cycle is the whole set of elements required to complete a specific activity or job in order to produce one unit of output. It could also comprise aspects that don't appear in every cycle.
Breaking the Jobs into Elements for a Variety of Reasons
- Ensure that productive time is segregated from non-productive activities (effective time and ineffective time are separated).
- To allow for a more accurate assessment of the pace of performance than would be achievable if the assessment were done over the course of a full cycle.
- To allow different sorts of items to be detected and distinguished so that each element receives the attention it deserves.
- To ensure that elements involving a high level of tiredness are identified and that fatigue allowances are distributed more precisely.
- To enable the creation of a thorough task specification...
- To separate mechanical elements from 'human' elements.
- To allow time standards to be examined or amended at a later period, as well as to correct omissions and errors.
- For rating accuracy.
- To allow time values for regularly occurring elements, such as task loading and unloading, machine adjustment, to be extracted and used in standard data compilation.
Types of elements
- A repetitive element is one that occurs during each work cycle of the project, such as picking up a part for assembly or locating a work piece in a holding device.
- An occasional element is one that occurs only occasionally. Does not happen during every work cycle of the task or at regular intervals. For example, tool replacement after a period, tension or machine setting adjustments, and supervisory instructions. A helpful work to be included in standard time is the occasional element.
- A constant element is one whose basic time remains constant regardless of how it is done. For example, turn on the machine, measure the diameter, then insert the cutting tools.
- A variable element is one whose basic time fluctuates depending on certain fundamental aspects of the product, equipment, or process. Dimensions, weight, quality, and so forth are some examples.
- A manual element is one that is completed by a worker.
- A machine element is a task that a power-driven machine performs automatically. Working parts for presses and annealing tubes are two examples.
- A governing element is an element that takes up more time than any other element that is being executed at the same moment, for example. Dimensions of gauges while turning diameter (turning diameter will be a governing element).
- A foreign element is one that is observed during research but is not a part of the cycle's specific activity. For instance, an operator may dump work on the floor while conversing with a co-worker.
Breaking Jobs Down into Elements: Guidelines
- The elements should be easily distinguishable.
- Each element should have a distinct start and finish point.
- Manual and variable elements should be kept separate.
- Separate timers should be used for sporadic elements.
- Elements should be as short as a qualified observer can comfortably time them.
- Elements should be chosen to represent naturally cohesive and easily identifiable district divisions of the activity.
How Many Cycles to be Timed?
- The number of cycles through which each given task should be watched is proportional to the amount of variation in the times of the job's elements.
- The number of cycles to watch is determined by the level of precision sought. This, in turn, will be determined by the job's duration and the number of individuals working on it.
- The research should be carried out over a sufficient number of cycles to guarantee that minor details such as handling boxes of finished components, routine machine cleaning, and so on may be seen multiple times.
- When more than one operator is working on the same job, it's better to do a quick study on each of them rather than spending too much time on a single one.
The number of observations at 95% confidence level and accuracy of ± 5 per cent is given by the statistical formula
Where

(Measure) Duration of Each Element:
After the elements have been chosen, the following step is to begin timing the operations. When using a stopwatch, there are two main techniques of timing: cumulative timing and fly back timing.
The watch runs continuously throughout the study in cumulative mode. It begins at the commencement of the first element of the first cycle to be timed and continues until the entire research is completed. After the study is finished, the watch reading is recorded at the end of each element, and individual element times are derived by sequential subtractions.
The hands of the stopwatch are returned to zero at the end of each element and permitted to begin immediately in fly back timing, and the time for each element is acquired directly.
Operator speed of work is examined and documented on the observation sheet while recording the time of the elements. The time study engineer's judgement of the operator's working pace in respect to the concept of standard or normal is called a rating. The term "rating" refers to the process of converting observed time into normal time.
Extend observed time into normal time:
The representative time calculated from observation data is the amount of time an operator spent operating at a set speed. By multiplying the observed time by the rating factor, the observed time is transformed to basic or normal time.

Calculate standard time for the job:
The various allowances are added to the normal time as applicable to get the standard
Time. Thus, basic constituents of standard time are:
1. Elemental (observed time).
2. Performance rating to compensate for difference in pace of working.
3. Relaxation allowance.
4. Interference and contingency allowance.
5. Policy allowance.
Time study equipment’s:
- Time study board
A time study board is just a flat piece of plywood or any other suitable plastic sheet with fittings to hold a stopwatch and time study forms. The usage of a board gives stability and a testing face while writing observations on the work floor, as well as freeing up hands to write and run a stopwatch.
- Stopwatch
- Time study forms
Time study forms are normally standard-size printed forms. Standard forms are preferable because the consistent information, such as part number and part name, operation description, observers name, and other descriptions, are pre-printed on the top of the form, ensuring that no details are overlooked. Because the forms are uniform in size, they may be readily filed for future reference.
Performance Rating:
The technique of altering an operator's real pace of work by comparing it to a mental image of an operator working at regular speed is known as performance rating.

To put it another way, rating acts as a levelling factor when converting observed timings to normal timings.
Factors Affecting Performance Rating:
There are differences between elements and even between elements in the same operation. This is due to the operator's irregularity in the speed with which he works.
Each employee has a unique temperament and approach toward their profession. Some workers are naturally fast (above the average worker's pace), whereas others are naturally slow. Both of these employees will not be typical employees.
The change in real timeframes for a given element could be attributable to both internal and external causes. The following are external circumstances that are beyond the control of the work study man:
- Variation in the material's quality or other qualities, despite the fact that it is within the tolerance limit.
- Changes in the efficiency of tools and equipment over the course of their useful lives.
- Unavoidable changes in operation methods or situations.
- Changes in working environment, such as temperature, light, and dust.
Internal factors that are under your control include:
- Acceptable variance in product quality.
- Variation due to the ability of the operator.
- Variation due to his mental state.
The various methods of performance rating are: (1) Speed rating, (2) Westing house system of rating, (3) Synthetic rating, and (4) Objective rating.
Speed Rating:
The only criteria examined for performance assessment in this technique is the speed of the operator's movements. The observer determines the speed rating by comparing the speed of the operators operating with his own definition of normal speed.
The technique of speed rating is limited to comparing the speed of motions to a concept of normal speed. The rating procedure is simplified based on this assumption, and the observer can become quite good in his judgement with instruction in creating the concept of normal pace.
Westing House Method of Rating:
Westing house system utilises a set of criteria to measure the performance of the operators. The factors are:
- Skill
- Effort
- Consistency
- Conditions
Synthetic Rating:
Under this method, the performance rating is derived by comparing the observed time of some manual elements to the known time values of the elements from predetermined motion and time studies (PMTS).
The process entails performing a standard time study and then comparing the actual time for each element to specified time values for the same elements.
Between the element's predetermined time value and its actual time value, a ratio is calculated.
This ratio is the operator's performance index or rating factor for the specific element. The performance rating factor (R) is calculated as follows:

P = Predetermined time for elements (minutes)
A = Average actual time value (selected time) for the same element 'P' (minutes)
Objective Rating:
The operator's speed is measured against a single standard pace that is unaffected by job difficulty. The spectator is just concerned with the rate of movement or activity, not with the task itself. To account for job difficulty, an allowance or a secondary adjustment is added to the pace rating after it is completed.
The job complexity is divided into six categories, with a percentage assigned to each.
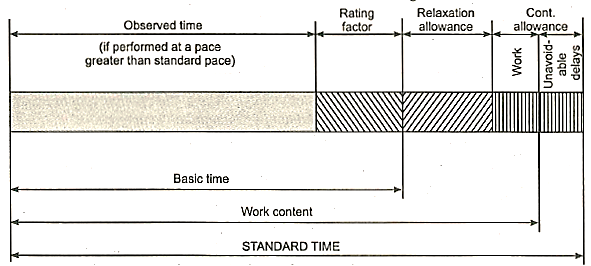
L.H.C. Tippett created work sampling in 1934 for the British Cotton Industry Research Board in the United Kingdom. Work sampling is a technique for gathering information.
Work sampling is defined as:
"A technique in which a statistically competent number of instantaneous observations are taken, over a period of time, of a group of machines, processes or workers. Each observation recorded for a particular activity or delay is a measure of the percentage of time observed by the occurrence."
There are three main applications for work sampling:
- Activity and Delay Sampling: This is used to track the activities and delays of employees or machines. For example, how much of a person's day is spent working and how much time is spent not working.
- Performance Sampling: To determine a person's working and non-working time while performing manual labour, as well as to produce a performance index or level for that individual during his working hours.
- Work Measurement: To measure a manual work, that is, to define a time standard for an operation, in particular conditions.
Procedure for Conducting a Work Sampling Study
The following steps are involved in making sampling study:
- Determine the Study's Objective: It is critical to initially determine the study's objectives, as the duration of the study, number of observations, design study sheet, and elemental breakdown are all dependent on the objective.
- Get permission from the supervisor of the department where the work study will be done. Ensure that the operators being researched, as well as the rest of the department, are aware of the study's goal. Collaborate with them.
- Choose Work and Delay Elements: Work and delay elements are the headings for the observations to be recorded under. The kind of the task and the length of time it takes to complete it varies from firm to company, based on the study's and work's goals.
- Determine the Study's Duration: The duration of the study is determined by the objective, the number of observers, the level of precision desired, and the frequency with which the activity occurs.
- Determine the intended accuracy of the results: This might be expressed as a percentage standard error or desired accuracy. It is also necessary to specify the level of confidence.
- Calculate a rough estimate of the proportion of time the activity or delay will occur.
- Design the Study:
- Determine number of observations to be made.
- Determine number of observers needed.
- Determine the number of days or shifts needed for the study.
- Make the detailed plans for taking observations.
- Design the observation form.
- Make the observations as planned, then analyse and summarise the information.
- At the conclusion of the study, double-check the data for accuracy and precision.
- Write the report and present the findings.
Design of Work Sampling Study:
Determination of Required Number of Observations
The number of observations depends upon:
• Activity percentage (P)
• Limits of accuracy (A)
• Confidence level (C)
Number of observations at a confidence level of 95% is given by

Setting Performance Standards with Work Sampling:
Procedure to develop performance standards are detailed below
- Taking the Study:
For the operation whose standard time needs to be calculated, a work sampling study is carried out. At random intervals of time, observations are made and recorded. It is noticed whether the subject of investigation is working or not. The causes of delays and interruptions are documented. Machine working and manual working are the two types of observations of production activity (working). When manual work is monitored, the speed with which the operators perform is noted.
2. Rating Index:
An overall rating index is calculated by averaging individual performance ratings.
3. Production Quantity:
Production reports are used to determine the number of pieces produced throughout the research period.
4. Effective Time Per Unit :
Even time spent on non-productive activity is included in the overall time per piece. The effective time per piece is calculated by multiplying total time by the percentage of productive activities.
Let
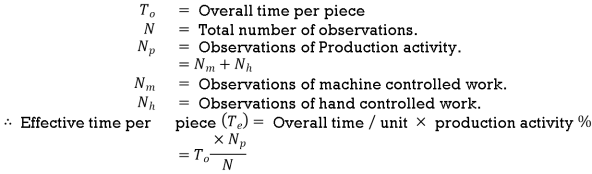
The effective time per piece (Te) can be compared to observed time of stopwatch study. To get the normal time, effective time is broken down into manual and machine-controlled time.
Machine controlled effective time
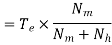
And Manual (hand) controlled time or

Normal Time Per Piece
Let be the performance rating index

Rating is applied to only manual (hand controlled) elements
Standard time per piece
Standard time is calculated by adding relevant allowances to the normal time.
Advantages of Work Sampling Compared to Time Study:
- Work sampling can be used to measure many operations or activities that are impractical or expensive to quantify using time studies.
- A single observer can conduct a simultaneous work sample investigation of numerous operators or machines.
- Compared to a continuous time study, a work sample study usually involves fewer man-hours and costs less.
- Observations can be made over a period of days or weeks, limiting the risk of results being influenced by day-to-day fluctuations.
- Any interruptions to the study will have no effect on the outcome.
- Work sample measures can be done with a predetermined level of accuracy.
- The operators being investigated prefer work sample studies over continuous time investigations.
- Work sampling studies do not require the use of a stopwatch.
- Work sampling studies are less tiring and time-consuming.
Disadvantages of Work Sampling:
- Work sampling is inefficient for occupations with short cycle times.
- Researching a single worker or even a small group of workers or robots is likewise uneconomical.
- A finer segmentation of activities and delays is feasible with time study than with work sampling study.
- Workers may alter their typical work patterns in response to seeing the observer, rendering the sampling study useless.
- Results that are based on insufficient observations are likely to be erroneous.
- It does not generally take into account the operator's speed.
Synthetic data is a work measurement technique for accumulating time for a job at a particular level of performance by adding elemental times already gathered from time studies on other works including the elements in question.
Synthetic data involves the following steps:
- Gather all job-related information (dimensions, tools, methods, conditions).
- Break jobs down into their component parts (activity grouping to allow for the use of synthetic elements if necessary).
- From synthetic data encompassing contingent elements, choose acceptable basic times.
- Choose and use synthetic data to account for situational circumstances.
- Check the elemental analysis details for the task technique and condition.
- Add up the fundamental times, ratings, and allowances to get the job's standard time.
Advantages:
Although synthesis was created to identify the work content for short batch production and jobbing labour, it can be used instead of time study to determine times for a variety of other tasks, including repetitive work, if the relevant data is available.
The key benefit of synthesis is the lower application cost. Synthesis allows for the establishment of timeframes that are equally suitable for planning and production control purposes.
Time research, work sampling, or the use of fixed times can all be used to establish a standard time for a job or an operation.
A predefined time system consists of a set of time data and a systematic technique for analysing and subdividing any manual human work into motions, bodily motions, or any parts of human performance, and assigning a time value to each. This time data system was created as a result of intensive research into all areas of human performance using measurement, evaluation, and validation techniques.
The tabulated values of normal times required to complete various movements, such as moving an arm from one position to another, are known as predetermined timings. The sum of the times required for basic motions equals the overall time required to complete the operation.
An existing task or a projected action can be timed without actually doing it by arranging the essential motions and aggregating corresponding timings.
Factors to be Considered While Using PMTS:
- To use PMTS, an operation must be broken into basic motions according to the system chosen. Each system has its own set of rules and processes that must be strictly adhered to.
- Because most PMTS do not include allowances, these must be inserted manually as in a stopwatch study.
- If necessary, adjustments should be made at the time of the first application of PMTS in a company to match the company's performance level, which is a one-time activity. PMTS can be classified according to the level of accuracy, the time required for application, and the extent of method description.
Types of PMTS:
- Methods Time Analysis (MTA):
One of the first to establish the relationship between the time factor and the motion itself was A. B. Segui of Oak Park, Illinois. Before attempting to time-analyse the motions involved, Segur noted that the procedure must be adequately specified. Many of his essential motions, such as hold, grip, preposition, position, unnecessary delay, and balance delay, were incorporated into a table of improvement principles. The elimination of the left hand as a holding device is the improvement principle at work here. Motion values are supplied up to the fifth decimal place in MTA.
2. Work Factor System (WF):
This is the first PMTS method to be widely used. Using the work factor system, it is feasible to calculate the work factor time for manual jobs using specified data. The identification of important work factors and the use of work factor as a unit of measure are used to conduct a detailed analysis of each task. Then, for each motion, the standard time from the table of motion values is applied.
Four major variables of work factor system are:
1. Body member
2. Distance
3. Manual control
4. Weight or resistance
This system is applicable to highly repetitive system.
3. Methods Time Measurement (MTM)
Methods Time Measurement procedure is defined as:
"A procedure which analysis any manual operation or method into the basic motions required to perform it and assigns to each motion a predetermined time standard which is determined by the nature of the motion and the conditions under which it was made."
MTM's main goal is to improve operational procedures, and it does so by defining the correct times and activities before production begins.
The goal of MTM is to create measurable, understandable, and accepted data for scientifically measuring human effort.
"A procedure which analyses any manual operation or method into the basic motions required to perform it and assigns to each motion a predetermined time standard which is determined by the nature of the motion and the conditions under which it is made."
Uses of MTM
1. Developing effective methods and plans in advance of beginning production.
2. Improving existing methods.
3. Establishing time standards.
4. Cost estimating.
5. Training supervisors to become method conscious.
6 Research in the areas like operating methods, performance rating.
MTM procedure recognises:
• Eight manual movements.
• Nine pedal and frunk movements.
• Two ocular movements.
As a result, there are nineteen primary motions to consider while creating a motion pattern. The duration of each of these motions is governed not only by the physical conditions in which they are performed, but also by the nature of the circumstances in which they are performed. As a result, a mix of physical and mental factors influence the duration of a given motion.
Conventions for Recording MTM Data:
Reach: Reach is the basic element when the predominant purpose is to move the hand or finger to a destination. The time for making a reach varies with
(1) condition (nature of destination), (2) length of the destination, (3) type of reach. Classes of reach: There are five classes of reach. The time to perform a reach is affected by the nature of the object towards the reach is made.
Case A Reach: to object in fixed location or to object in other hand or on which other hand rests.
Case B Reach: to object whose general location known. Location may vary slightly from cycle to cycle.
Case C Reach: to object jumbled with other objects in group.
Case D Reach: to very small object or where accurate grasp required.
Case E Reach: to indefinite location to get hand into position for body balance or next move or out of the way.
MTM Versions
MTM-1 is the most accurate. Provides the most detailed method detailed description but requires the longest time for analysis.
MTM-2 was developed. By constructing motion combinations from basic motion of
MTM-1.
The analysis can be done more quickly than MTM-1.
MTM-3 is the simplest of the MTM systems and is intended for use with long cycle short run operations. Speed of analysis is seven times faster than MTM-1.
MTM-3 should not be used for analysing manual motions with a frequency higher than 10 or sequence of eye motions.
The MTM should be used with caution. A sufficient training is essential to take up the MTM measurement.
4. Basic Motion Time study (BMT)
Basic motion time study was developed and is thought by J.P. Woods and Gordon Limited, Toronto, Canada. Like other predetermined motion time system, all manual activity has been divided into basic motions.
A basic motion, according to Woods and Gordon, is defined as "Any motion which starts from rest, moves through space, and ends at rest
(Type 1) Reach
(Type 2) Move
(Type 3) Turn
The body motion and symbols are very similar to the body motions employed by MTM. The only difference lies in the step, where the distance measured is the distance the foot travels.
Advantages of PMTS
- Short cycle jobs can be timed accurately.
- Rating, the most difficult part of time study is not necessary.
- The results obtained are consistent.
- A reasonable estimate of work content can be obtained before the task is carried out.
Key Takeaway
Time Study - A work measurement techniques for recording the times and rates of working for the elements of a specified job carried out under specified conditions and for analysing the data so as to determine the time necessary for carrying out the job at the defined level of performance.
Synthetic Data - A work measurement technique for building up the time for a job or parts of the job at a defined level of performance by totalling element times obtained previously from time studies on other jobs containing the elements concerned or from synthetic data
Work Sampling - A technique in which a large number of observations are made over a period of time of one or group of machines, processes or workers. Each observation records what is happening at that instant and the percentage of observations recorded for a particular activity, or delay is a measure of the percentage of time during which that activities delay occurs.
Predetermined Motion Time Study (PMTS) - A work measurement technique whereby times established for basic human motions (classified according to the nature of the motion and conditions under which it is made) are used to build up the time for a job at the defined level of performance. The most commonly used PMTS is known as Methods Time Measurement (MTM).
"The design of human tasks, man machine system, and effective accomplishment of the job, including displays for presenting information
To human sensors, controls for human operations and complex man-machine systems."
Objective of Human Engineering:
- To improve the efficiency and effectiveness with which actions (work) are carried out in order to improve user convenience, eliminate errors, and boost productivity.
- To promote some desirable human values such as safety, stress and fatigue reduction, and overall quality of life.
Thus, in general the scope and objective of ergonomics is "designing for human use and optimising working and living conditions."
Human factors (ergonomics) is the study of human behaviour, skills, limitations, and other qualities in order to develop tools, machines, systems, processes, jobs, and environments that are productive, safe, comfortable, and successful for humans.
Productivity is a great weapon for raising people's living standards and improving the quality of their work lives (QWL). Ergonomics is the study of man and his working environment. Ergonomics strives to provide comfort and better working circumstances so that workers' energy and abilities can be channelled into productive work. This results in enhanced production, increased safety, and decreased weariness. This contributes to increased plant use.
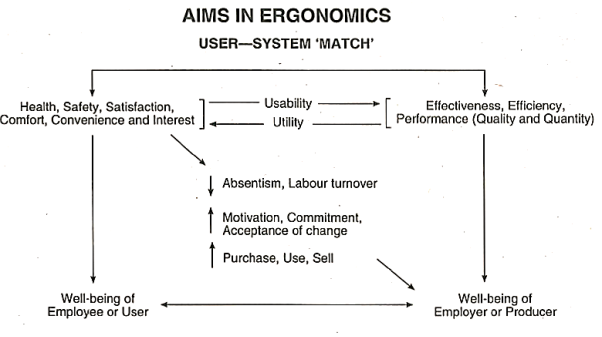
Study of human engineering areas:
- Anthropometry and biomechanics
- Control of physical work environment
- Design of man-machine system
- Design of controls and displays
- Accident’s fatigue and safety
- Workplace design
Man -Machine System:
The system is the most essential notion in human engineering. A system is made up of humans, machines, and other objects that collaborate (or interact) to achieve a goal that these components could not achieve on their own.
A man-machine system is made up of one or more humans and one or more physical components that work together to produce a desired output from given inputs. Any type of physical object, device, equipment, facility, or activity performed by man is included in the man-machine system.
- Manual system
- Mechanical system
- Automated system
- Man machine system
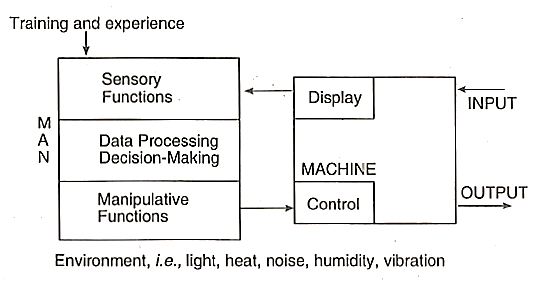
Aspects:
- Design of information displays
Quantitative Information
Status information
Warning and Signal Indicators
Representational Information
Identification Information
Time phased Information
Types of display - Visual Displays & Auditory displays:
- Design of controls
Man in control loop system
Hand controls
Hand Levers
Hand Wheels
Cranks
Knobs
Push buttons
Toggle switches
Joysticks
Foot pedals
Decision Communication Channel
Control Communication Channel
- Environmental factors
Environmental Factors: Ergonomics has a three-fold role in the human-machine interface in the environment.
- Identifying the influence of the environment on man's physiological and psychological processes is the first step.
- Second, making sure that work patterns, equipment, and machine interfaces are all structured to reduce individual performance variation.
- Third, all required protective measures must be built to accommodate for physiological and psychological variances in humans.
Anthropometry:
Anthropometry is the science of measuring body dimensions and other physical qualities such as volumes, centre of gravity, inertial properties, and mass of body segments. Body measurements are divided into two categories: static and dynamic (functional). When the body is in a fixed (static) position, static dimensions are taken. These include: • Skeletal dimensions (the distance between joint dimensions); and • Contour dimensions (skin surface dimensions).
Ergonomics deals with:
- Manual material handling (MMH)
Biomechanical Approach
The body is viewed as a system of links and linking joints that correspond to body segments in this method. For instance, consider the upper arm (link) and the elbow (joint). The mechanical stresses on the body and the muscular forces required to counteract these stresses are calculated using physics principles. The goal of this method is to keep task demands within the body's strength capacity and compressive force tolerance. This mostly includes MMH tasks that occur seldom.
Physiological Approach.
This method works best for MMH tasks that are repeated frequently and over a long period of time. The physiological approach focuses on energy use and the pressures that the cardiovascular system faces.
Psychophysical Approach
This technique is based on the fact that people's subjective assessments of perceived stress include both biomechanical and physiological stresses. Subjects change the weight of a load to the highest amount they can sustain without strain or discomfort, and without getting unusually weary or weaker, using psychophysics to analyse a lifting activity. The "Maximum allowable weight of load (MAWL)" is the maximum specified weight.
- Physiological aspects of muscular work
- Workplace design
Dimensions of Working Surface
Dimensions of the Working Envelope
Workplace Height
Sit-Stand and Standing Workplace
Selection of Chairs
- Workstation Design
Branches of Workplace Ergonomics:
- Physical Ergonomics
By fostering neutral body postures and healthy mobility and motion, experts have proved that utilising an ergonomically sound approach to work helps minimise and prevent pain and discomfort. It may even improve our health.
- Cognitive ergonomics
Cognitive ergonomics teaches us how to think about and approach our work and tools. The environment influences how well we work and how happy we are at work, and happiness influences productivity.
- Social ergonomics in the workspace
The study of how the environment influences people's behaviour and relationships with one another is known as social ergonomics.
- Support groups of different sizes
- Allow people to choose how much personal space they want
- Encourage spontaneous interaction through shared pathways and resources
- Allow people to regulate their privacy
- Allow people to personalize their private spaces
Position evaluation is the process of determining the value of each job in an organisation in a systematic and analytical manner, based on a set of carefully selected characteristics such as skill effort and responsibility expected by the job, and translating this value into monetary terms, i.e. salary and wages.
It is an attempt to determine and compare the demands that normal job performance places on ordinary workers without taking into account the workers' specific abilities or performance. It is a method of job evaluation rather than a method of job evaluation.
The goal of job evaluation is to design a remuneration structure that is acceptable to both workers and management.
Objectives:
- To build a sound wage and salary system by calculating the value of each position in the factory in proportion to numerous aspects such as the level of skill required, the amount of work required, and the level of responsibility involved.
- To eradicate salary disparities
- To determine a general salary level for a particular factory.
- Establish a clear line of authority and duty.
- To create a fair and consistent wage structure.
- Establish a solid foundation for employee recruiting, selection, promotion, and transfer
- Determine employee training needs in order to prepare them for future jobs
- A solid foundation for evaluating individual achievement
- To foster positive employee-employer relationships.
Procedure:
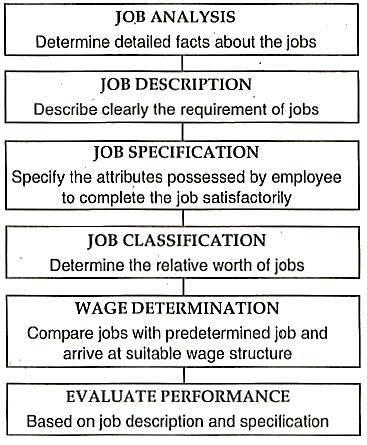
Job evaluation system:
Ranking System:
Jobs are graded in order of importance (in terms of number of obligations and responsibilities) from lowest to highest in this system. The job is ranked as a whole, rather than divided down into distinct sections or tasks. The committee determines the rank. This is the simplest and most straightforward way.
The major steps involved in ranking system are:
- Selection of the jobs.
- Job analysis.
- Choosing the committee for ranking jobs.
- Ranking of the jobs.
- Grouping the job into groups by the committee.
The benefit of this strategy is that it is simple, takes less time, and requires less documentation (forms). The biggest drawback is that there are no set standards for grading jobs, making it less accurate. When only a few jobs need to be examined, this method is appropriate.
Job Classification System:
The practise of assigning jobs to specified grades is known as the job classification system.
The yardstick is given to the rater. Grade disparities are defined by variances in the degrees of obligations, responsibilities, and particular skill requirements.
The job evaluation by this method involves the following steps:
- Decide and describe number of grades.
- Write grade level descriptions
- Listing of jobs to be evaluated
- Assigning the jobs to grades based upon grade and job level description.
Major Advantages:
- Method is easily understood by all and easy to use.
- The results are fairly accurate.
The limitation being the system gets complicated as the number of jobs are increased and grade descriptions are relatively difficult to write.
Factor Comparison Method:
It is a method of work appraisal that is qualitative. This process entails a thorough examination of the jobs, which are then graded against present criteria. When evaluating occupations, five elements are taken into account.
- Mental effort.
- Skill requirement.
- Physical requirement.
- Responsibility.
- Working conditions.
The steps that make up the factor comparison approach.
- The most important jobs must be selected and accurately described. The key positions are chosen to represent each main level of obligations, responsibilities, skill, and so on, and to cover the complete range of jobs.
- For each of the five stated variables, key jobs are examined.
- The pay for each key task is distributed among the factors.
- For each key task, the compensation is divided among the factors in accordance to their importance in the work. As a result, each of the criteria has a monetary rating scale.
- On its money rating scale of vital jobs, each of the jobs is appraised for each of the variables. The job's monitory value is calculated by adding up the individual monetary values for each of the criteria, which varies based on the job's relevance.
Advantages
- Job-to-job comparison ensures that positions are compared on a level playing field.
- The job's monetary value is determined directly
- It considers all of the aspects that go into creating a job.
- This strategy can be used by even huge organisations.
Limitations
- Choosing an incorrectly paid employment is likely to result in a significant amount of error.
- There is a great deal of subjectivity in the construction of money value rating scales.
- Employees find it difficult to understand the rating scale.
- It requires additional time.
Point rating method:
Merill. R. Lott devised this method, which is the most popular and quantifiable. This system assesses jobs based on a set of carefully chosen criteria such as education, experience, physical exertion, and responsibility for machinery and materials, all of which are common to most jobs. The following are the primary steps involved in the point rating system:
- Decide the type of jobs to be evaluated:
The tasks to be evaluated are specified in this stage, and only jobs with varied work contents are to be documented.
- Select the factors:
- Education.
- Experience.
- Judgement and initiative.
- Physical effort.
- Mental effort.
- Responsibility for equipment, materials.
- Responsibility for process.
- Responsibility for the work of others.
- Working conditions.
- Hazards.
- Adaptability.
- Creative ability.
- Aptitude for learning.
- Initiative.
- Definition of factors:
There should be no ambiguity about the meaning of the factor. Each factor should be defined in such a way that everyone understands it. Simple terminology should be utilised, and difficult words, such as Education, should be avoided.
This element is utilised in the context of acquiring competence through academic or technical training. Must be aware of the job being done and the obligations that come with it It excludes on-the-job training and practical vocational knowledge.
- Define the degrees for each factor:
Degree | Description |
1. | Requires the ability to understand simple verbal instructions. |
2. | Requires the ability to read and write. Requires trade knowledge equivalent to use hand tools or/and operation of simple machines. |
3. | Requires the knowledge to be able to operate the machines or repetitive jobs with few set-ups. Knowledge of the part and tools. Be able to do arithmetic calculations. |
4. | Specialised knowledge regarding the engineering drawing mathematics and English. |
![]() | The factors (5,6...etc.) are defined with respect to further educational requirements. |
- Assigning weightages to the factors:
The weightages are assigned to each factor on a percentage basis, based on how much each aspect contributes to the job. At the joint committee of management and union, weightages are determined by consensus.
- Assigning points to the degrees:
- The next step is to allocate points to the degrees once the weightages have been determined. The most popular way is to use the factor's percentage weightage to represent the point value of the first degree in each factor, and the other degrees' values to follow an arithmetic progression, with the factor's weightage as the difference between two degrees
- Creating the job evaluation handbook: The job factors and their degrees are defined in this manual. As a result, it may be used to determine the relative worth of existing and projected occupations.
- Preparing job descriptions and specifications is number eight on the list.
- Job evaluations (determining the points)
- Assigning grades to jobs: After the jobs have been graded in terms of points, they are assigned grades.
Advantages
- More accurate and reliable compared to other methods
- More objectivity due to quantification of factors
- It is logical and practicable
- Good acceptability
Limitations
- Requires a large experience and expertise to define degrees and points
- Points allocated to degree are arbitrary
Job evaluation assesses the worth of a person executing the job, while merit rating assesses the worth of a person performing the job. Performance appraisal is another name for merit rating. It assesses, monitors, and assesses performance. Both job evaluation and performance appraisal are aimed at calculating the salary rates provided to employees in a methodical manner.
Benefits:
- It helps to identify the person's potential to perform the assigned jobs and to decide the future positions he can take up
- It helps to identify the training needs of the employees
- It helps in counselling employees regarding their strengths and weaknesses
- It motivates employees to perform better.
- Serves as a system for constructive performance evaluation.
Methods:
- Ranking Method: This is the most common and straightforward technique of ranking. Employees are usually ranked in order of best to worst performance. This is applicable to sectors with a small workforce. The method's drawback is that it can't pinpoint individual strengths and weaknesses. As the number of employees grows, ranking gets more challenging.
- Paired comparison technique: The rater compares each employee in a group to the remaining employees in this method. The only criterion for comparison is performance. When the group is vast, it becomes even more difficult to compare.
- Forced choice method: In this method, a number of statements are provided for each trait or behaviour, and the rater is required to choose only one statement that describes the specific behaviour of the employee being assessed. Because the rater is only allowed to check one statement and is not allowed to explain behaviour in his own words, this method is known as forced choice. This is the most common way for grading lower-level employees.
- Method of the check list: These are lists made up of a series of questions or statements that are concerned with the important parts of an employee's work performance. The rating process is as simple as checking the items that pertain to the ratee and responding with a "YES" or "NO." This strategy makes it simple to compare employees.
- Scale plan: This is a widely used strategy in the business world. The scale is designed to define the different levels of the qualities.
Scale plans are divided into two categories:
(a) Continuous scale: This scale is ill-designed to reflect the highest to lowest degree of the needed trait: (a) Numerical scales; (b) Scales of description.
(b) Discontinuous scales: This is a scale that provides a detailed description of the facts that must be rated.
Incentive plans are designed to boost employee motivation by allowing them to earn proportionately higher rewards for putting in more effort.
American Society of Mechanical Engineers (ASME) defines a wage incentive plan as
"a method of payment which directly relates ·earning to production. A system which enables workmen to increase their earning by maintaining or exceeding an established standard of performance."
These are management's techniques for stimulating output by encouraging employees to produce more than average in terms of their productivity.
There are two types of incentive plans:
- Financial incentives: These are monetary prizes given to employees for their performance.
- Non-monetary incentives: These are incentives that are not monetary in nature (other than cash). Gift items, discount coupons, special holidays, and so on are examples of this.
Non-monetary incentives include
- Management may create a competitive environment among employees to encourage them to contribute constructively to the organisation.
- This incentive encourages creativity and idea generation
- This incentive includes providing good housing with all modern amenities, recreation facilities, medical facilities, and so on.
- Employee promotions and opportunities for personal development
- International business or educational travels
Individual and group incentive schemes:
Individual incentive schemes pay an incentive to each employee based on their individual performance or output. This incentive is given regardless of the department's or organization's output or performance. Employers are obligated to provide bonuses to employees who produce more than the standard output.
Under group incentive scheme, each employee is paid incentive on the basis of collective performance of his group to which he belongs. This group incentive scheme is preferred by the management as in turn they are getting an output from the group. Within the group, each employee is going to get equal share of the incentive. Highly competent or
Productive employees are not in favour of this scheme.
Characteristics of a good incentive system:
- The strategy should be simple to comprehend and implement. The employee should be able to figure out how much money he makes.
- The incentive programme should be uniform. The incentive structure should not be changed too frequently once it has been set up.
- The incentive programme should be designed to encourage employees to create more.
- The labour and the reward should be in direct proportion.
- Employees should not be dissatisfied with the incentive system.
Key takeaway
"A method of payment which directly relates ·earning to production. A system which enables workmen to increase their earning by maintaining or exceeding an established standard of performance."
Wage payments are the result of the research of work measurement. In theory, the wages a worker receives are proportional to the quantity of work he performs. Wages are meant to motivate people to work harder and more effectively. Wages are the workers' primary source of income for the services they provide. To pay workers for their labour, a reasonable wage policy is required.
Employee remuneration entails the following considerations:
- Establishing salary structures/levels for various jobs within the organisation
- Establishing a pay for each employee that works in the position deciding on a wage payment mechanism
l. Wages: These are the payments paid by the employer in exchange for the workers' efforts in the production process. Wages affect the standard of living and should reflect a fair return for the worker's efforts. Wages should also be able to meet the workers' primary and secondary requirements. They should be sufficient to maintain a respectable quality of living for him.
2. Nominal Wages: This is the amount of money paid to a worker in cash for his or her labour in the production process, with no further advantages. This is referred to as a monetary wage. Wage rates differ from one location to the next, depending on labour demand and availability, as well as the requirements of living.
3. Real Wages: This refers to the quantity of necessities, comforts, pleasures, and money a worker receives in exchange for his or her labour. In addition to income, some organisations provide their employees with certain needed goods, such as accommodation with free electricity and water, uniforms, and other such benefits. When all of these figures are factored in for pay, the real figure emerges. Wage.
4. Living Salary: When wage rates are such that they would cover some of a family's fundamental needs such as food, clothing, education, and insurance against disaster, among other things, they are referred to as living wages.
5. Fair Wage: This is a wage that should be deemed a fair level of compensation for the employees' efforts and should be able to meet other essentials of life in addition to basic needs such as food, clothing, and shelter for his family. The fair wage rate is somewhere between the real wage and the minimum wage.
6. Minimum Wage: A minimum pay is a wage that provides not just for basic sustenance but also for something more. It should be able to keep employees motivated and provide some form of education, medical care, and other necessities. It should also consider the cost of living.
Characteristics of a good wage system:
Employees and management should both be happy with a solid wage system. It should ensure that the employee receives a minimal pay.
It is necessary to be able to keep employees motivated. It should give employees the opportunity to be rewarded for their additional or extra effort (incentives)
It should be constant and should not be changed on a regular basis.
Should be a firm believer in equal compensation for equal labour. All parties involved should be able to understand and use the system.
Employees should be encouraged to reach their maximum potential, and the work should be difficult and engaging.
Types of wage payments:
- Wage payment on time basis: Wages are paid to employees based on the amount of time they labour under this technique. The wage rates are set in advance for each month, day, or hour of work. Workers in this system are paid on time and work regardless of the amount of output produced. This technique can be used in situations where the output isn't quantifiable and isn't used as a payment criterion, such as when the labour isn't repeated.
Advantages:
- The system is simple to understand and operate
- It reduces labour relations issues
- The quality of the work is maintained because employees are not in a rush to increase quantity
- The worker can demonstrate his efficiency and craftsmanship without risking his job
- Work methods can be improved.
Disadvantages:
- Does not provide any incentive to ambitious and efficient personnel
- In the absence of strong monitoring, output will be reduced
- Wages are based on time rather than output or efficiency. As a result, less efficient workers get paid the same as efficient workers.
- An increase or drop in output will benefit or harm the employer.
2. Wage payment based on output (piece rate system): Employees are paid wages based on the amount of output produced in this system. This method is particularly convenient because each worker is capable of performing his or her work without relying on the work of others, and the output produced is quantifiable. When the output is standardised, this method can be used. The labour is monotonous in nature.
Advantages:
- Higher speed raises the production rate and so reduces the cost per unit
- Increases the utilisation of production facilities
- Workers invent new ways and techniques of completing the work in order to minimise the time per unit
- Motivates workers to produce more
Disadvantages:
- Workers may overlook quality in order to raise their income by working faster.
- Due to speed, a worker may be more likely to be involved in an accident because he may overlook precautions and safety procedures.
- Worker security is poor, which may severely penalise the elderly and ineffective workers.
Conception:
At this stage, the product's draught specifications are set out, taking into account the user's requirements. All following design tasks are built on the foundation of this stage. The marketing department must prepare the suggested product specs in as much detail as feasible.
The following information on design specifications should be included as a bare minimum:
• The requirements for performance
• Requirements for appearance or styling.
• The projected number of units to be sold.
• The maximum price that the product should be available for.
• When the product will most likely be available on the market.
Acceptance:
After the feasibility study, model making, and calculations of the product have been accepted, the design activity of the product begins.
Execution:
A model is created based on general design considerations and acceptance of standards. Specifications should be followed by the models. The model will disclose the specific viability and special considerations of proposed designs. At this point, the product's cost is calculated, and the production engineers make every effort to stick to it. For prototype, modelling, and testing, modern approaches such as rapid prototyping technique (RPT) and experimental stress analysis techniques are now accessible.
Translation:
The production engineering section is now engaged in design development. At this point, the manufacturing feasibility is assessed. The final manufacturing designs are currently being produced.
Pre-production:
It is advised that a pilot run under production circumstances be carried out in large-scale production. This will entail totally assembling a quantity of production from parts or components manufactured using standard manufacturing methods, with the same level of competence in the operatives as in the end product. The pre-production run will guarantee that the product meets the criteria in terms of quality and dependability before commercial production begins.
Thus, the pre-production stage will check:
1. Drawings
2. Final tools.
3. Production techniques and estimates.
4. Specifications.
Product analysis:
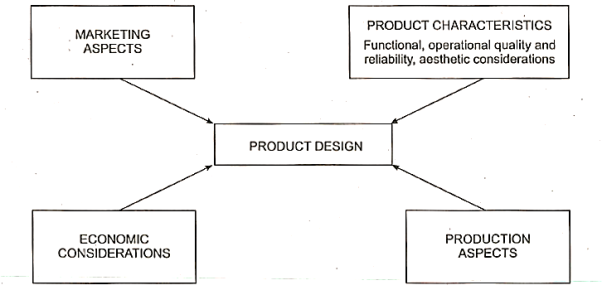
- Marketing aspects
Whether the functions that are offered by the product are desirable and acceptable
to the customers?
What will be the status of the product in the market Product is already existing? Entirely new product about which the customer is totally unaware.
What will be the expected demand for the product both short-term and long-term?
The factors that influence the demand for this proposed product.
What is the level of competition and basis of competition for product?
What are the distinguishing features offered by competitors?
The price prevailing in the market.
Distribution system, etc.
- Functional aspects
What are the functions the product is expected to perform?
Whether we should give a single function or multiple functions are to be incorporated.
Cost considerations due to offering multiple functions.
- Operational aspects
The operational features of the products must be decided after the functions expected to be served by the product have been identified. The product should not only work properly, but it should also be simple to handle and operate on the customer's end.
The product is employed in a variety of operational situations, and customers vary in terms of ability and knowledge, therefore the designer's challenge grows more complicated as more features are added.
The designer must consider the customer's preparation time (set-up time), operating time, and put-away time. As a result, the operational component becomes even more critical, as it is the customer who will be operating at his location, and care must be made to ensure that. That the product should be simple to use
- Durability & dependability
These two variables determine the product's quality and dependability. The term "durability" refers to a product's active life under specified working conditions. The term "reliability" refers to how well a thing performs its intended function. As a result, the product's quality is directly related to the quality of the inputs (materials, labour, etc.) and the manufacturing process. As a result, it is a cost function.
Depending on the product philosophy of the management, a balance between quality and cost must be found. To be competitive, businesses must provide higher-quality items at an affordable price. Various areas of quality control, safety, and maintenance should be given careful consideration.
- Aesthetic aspects
Use of Special Materials:
Use of Colour:
Texture as a Supplement to ·Colour:
Use of Lines.
Scaling the Product
Packaging
- Economic analysis
The key to making a management decision in product design policy is to do an economic analysis. Once adequate information about the product's marketability has been acquired, several areas of the product, such as functional, operational, quality, and aesthetic, have been investigated for the proposed product.
Then the next steps is the economic analysis which seeks to answer the following
Questions:
What will be the amount of investment needed to manufacture the new product?
What are the estimated production costs per piece?
What will be the expected profit+ margin?
Whether the prices (cost + profit) proposed to be offered by the company are
competitive?
What is the expected volume of sales?
- Reliability
It is a measurement of a product's, a component's, a service, or an entire system's ability to execute its intended function under a set of conditions. The importance of reliability is highlighted by the fact that prospective buyers use it to compare alternatives and sellers use it as a price factor. Reliability can affect repeat purchases, reflect on a product's reputation, and, if it's too low, have legal ramifications.
The tolerances for product design characteristics are defined in this step, considering the loss that would be incurred to society if performance deviates from the target.
The designer must set the tolerance of the parameters after the system has been designed and the values for the parameters have been determined. Environmental elements, as well as system parameters, must be considered.
Production tolerances that reduce the effect of noise effects and manufacturing costs are determined in tolerance design. In this case, the Tauguchi loss function is applied.
The goal of tolerance design is to strike a balance between the quality loss caused by performance variation and any increase in production costs.
The loss function recognises the customer's demand for more consistent products from part to part, as well as the producer's aim to provide a low-cost product. Costs incurred in the production process
- Costs incurred in the production process
- Costs incurred in the production process
- Costs incurred in the production process
- Costs incurred by the client during use, such as repair and lost business.
Quality, according to Dr. Tauguchi, is defined as the entire damage inflicted on society from the time the product is distributed. Due to performance variation, any user of the product is liable to suffer at any time over the product's lifetime. Other societal losses may emerge as a result of negative effects such as pollution, the presence of hydrocarbons, and so on.
Tauguchi defined the loss function as a quantity proportional to the divergence of quality characteristics from the target value. The loss function is used to assess the impact of improving quality. The relationship between quality loss and performance variation from the target is seen in the graph below.
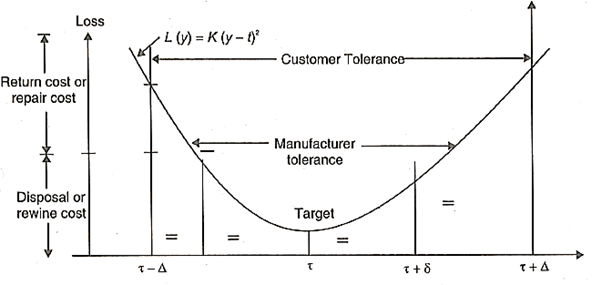
If y is the performance characteristic measured on a continuous scale when the ideal or target performance level is
Then according to Tauguchi the loss caused L (y) can be effectively modelled by a quadratic function

And K here is the proportionality constant and can be determined by

The loss function is a mathematical formula that connects quality to a monetary loss. The quadratic loss function offers the essential information (via the signal-to-noise ratio) for quality enhancement to be effective.
The loss function also explains why it is sufficient for products to fall within specified limitations. Parts and components that must work together are better constructed at their usual (midpoint specification) dimensions rather than within their tolerance limitations.
When the performance varies the average loss can be determined by statistically averaging the quadratic loss. The average loss is proportional to the mean square of error of y about its target value .
Suppose the ' ' units are produced giving the performances
respectively, then the average loss caused by these units because of their of being on target
is
where
Thus, the average loss caused by variability has two components
(i) The average performance ( ) being different from the target
, contributes to the loss
(ii) Loss results from performance
of the individual items being different from their own average
.
The fundamental measure of variability is the mean squared error of y about the target (\tau) and not the variance alone. The ideal performance requires perfection in both accuracy (i.e.,
to be equal
) as well as the precision (i.e.,
should be zero).
S/N Ratio:
The Tauguchi method's overall goal is to minimise the average loss function. Tauguchi, on the other hand, advocated for a metric known as the signal to noise (S/N) ratio. The S/N ratio is a robustness metric. The lower the S/N ratio, the less impact variances have on the product. As a result, at the design stage, the resilient conditions are investigated by increasing the effect of the S/N ratio.
The output is ideally expressed as

Where is the signal and
is a constant. Noise occurs due to the controllable variables
,
and error factors
Hence,

The ideal state (helpful part) is represented by the first term of the RHS (βM), and the departure from the ideal state (damaging part) represents the robustness of y. By raising the former and decreasing the latter, an improved state can be defined. The S/N ratio, which is the ratio between the useful and detrimental parts given as a percentage, is one statistic that indicates this enhanced state.
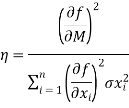
Where is the observed standard deviation for
.
If the harmful part is expressed by a single error and its standard deviation is

As a result, the goal of resilient design is to find the best settings for desired performance in order to attain a specific target performance value under noisy situations. Assume that the average quality characteristic in a collection of statistical experiments is , and the standard deviation induced by noise effects is
. Because the goal is to offer on-target performance, a modification to the design is required to achieve this, and the loss after the process has been modified is attributable to the residual variability.
Loss after adjustment:

The factor reflects the ratio of average performance
(signal) and
variance in performance (noise). Maximizing
(S/N ratio) therefore becomes equivalent to minimizing loss after adjustment. Thus, S/N ratio is a predictor of quality loss that is isolates the sensitivity of the products function to noise factors. In robust design, one minimizes this sensitivity to noise be seeking combinations of the DP setting that maximize the S/N ratio.
To appeal to a wider range of clients, some businesses offer products that are the best combination of quality and price. In relation to the pricing, the products are of reasonable quality. These businesses strive to provide clients with good value for their money.
It's critical to examine the cost elements that go into each phase of manufacturing while creating a new product. One can calculate target sales pricing and profitability by analysing each phase and cost component, but more importantly, how much product re-design and various features cost by studying each phase and cost factor. Manufacturers can gain a better understanding of the various processes and characteristics of their goods by using Design-To-Cost (DTC) analysis.
It's critical to evaluate the cost of various production processes early in the design process as part of Design-for-Manufacturing (DFM) best practises. Overly complex features, strict tolerances, and in-depth manufacturing requirements can lead to exceedingly specialised and costly production procedures, tooling, and fixtures.
According to studies, the choices an engineer takes during the design process account for more than 70% of a new product's life cycle expenses. Long after prototype and initial item approval, the influence of a thorough DTC and DFM study pays off. Product Development Consulting services are available to assist with manufacturing design and cost, as well as to ensure that your production plans are set up for long-term profitability and success.
A few crucial elements to consider when creating your product are listed below.
Recurring production cost:
A recurring production cost is exactly what it sounds like: a cost that is incurred repeatedly over the course of a product's manufacturing life cycle. Production labour, materials, process costs, overhead, and outside processing are all included in these costs. The majority of your overall programme cost will be driven by recurring costs, thus pragmatism is critical when choosing materials, suppliers, and other production requirements. Despite the fact that these charges are usually not disguised, citing overly elaborate requirements can result in considerable cost increases.
Non-recurring costs
One-time costs that arise during the development stages of a product are known as non-recurring costs. Research & development, prototyping, tooling, and even expedited transportation or production lead times are all included in these costs. Although non-recurring expenditures are easy to overlook because they should be rare, the complexity of your product design will determine the amount of non-recurring investment required. Cost analysis of non-recurring elements can result in significant cost savings over the product's lifecycle, avoiding the need for re-design.
External product costs:
Logistics, packaging, currency exchange, VAT tax, and customs are all examples of external product costs. Working with logistics consulting services can help you have a better understanding of long-term expenses and how to increase efficiency. Taking into account specific product coatings or packaging requirements, as well as their impact on logistics costs, can also play a big role in deciding your final product cost.
Sales costs:
Inventory, customisation, warranties, and any other administrative or sales charges are all factored into sales costs. Large changes in manufacturing costs or inventory requirements can occur depending on how flexible your product is to client demand. Some end-product expenses might be offset by incorporating risk mitigation strategies into your product design.
Production aspects of product design:
The design will be brought to life in the production shop, where it will be turned into an actual product that can be sold to customers. As a result, transforming a design into a marketable product is a difficult task for the company. This necessitates close cooperation between the production and design departments at all phases of the product's manufacturing. As a result, a designer cannot develop a product in isolation, and increasing collaboration between production and other departments is required to produce designs that work and can be made without issues.
Selection of Suitable Process:
- Production quantity (volume of production).
- Information regarding utilisation of equipment, capacity of equipment, accuracy,
- Selection of tooling such as jigs and fixtures.
- Sequence of operations and methods of assembly.
- Possibility of applications of new techniques, processes.
Utilisation of Materials and Components with a View of
- Selection of method to reduce waste and scrap.
- Usage of standard components and parts.
- Interchangeability of components and assemblies within the product.
Selecting the proper tolerances and work method
Using available methods and equipment, meet the stated quality standard. The selection of a process will be influenced by the quality specification.
A designer engineer and a project manager should collaborate closely to ensure a successful design transformation. Engineer a designer to specify engineer the best should available work process of transformation keeping in mind the constraints of the production to accomplish coordination a successful with production transformation ‘and of the methods design.
Steps in quality control:
- Formulate quality policy.
- Set the standards or specifications on the basis of customer’s preference, cost and profit.
- Select inspection plan and set up procedure for checking.
- Detect deviations from set standards of specifications.
- Take corrective actions or necessary changes to achieve standards.
- Decide on salvage method i.e., to decide how the defective parts are disposed of entire scrap or rework.
- Coordination of quality problems.
- Developing quality consciousness both within and outside the organization.
- Developing procedures for good vendor-vendee relations.
Objectives of Quality Control:
- To increase the company's revenue by improving customer acceptance of the product, such as by offering longer life, more usability, and maintainability, among other things.
- To save company costs by reducing defects-related losses.
- To accomplish manufacturing interchangeability in large-scale production.
- To make high-quality goods at a low cost.
- To assure customer satisfaction with products or services of a high-quality level, as well as to build consumer goodwill, confidence, and the manufacturer's reputation.
- To ensure quality control, do inspections as soon as possible.
- To monitor variance during the manufacturing process.
Benefits of Quality Control:
- Improving the product and service quality.
- Manufacturing operations, commercial businesses, and organisations can all benefit from increased productivity.
- Manufacturing and corporate costs are being cut.
- Identifying and increasing a product's or service's marketability.
- Reducing the cost of goods and services for consumers.
- Improving and/or ensuring delivery and availability on time.
- Assisting with the management of a business.
The product once introduced into the market will undergo definite phases
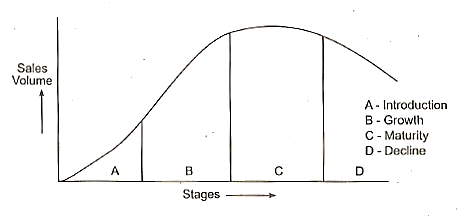
Characteristics of Phases in Product Lifecycle (PLC):
The demand for a product follows a predictable pattern known as the product life cycle (PLC). Products move through a succession of stages, starting with product launch or introduction, then rapid growth, maturity or saturation, and finally demand reduction. The length of time that these items spend in various phases varies greatly between businesses.
These time periods range from a few weeks or months (for novelty and fashion items) to years (for other things).
- The introduction stage is when the product is first introduced to the market. It could be a completely new product on the market, or an established product being introduced to a new market. Customers have little knowledge of the goods; hence demand is modest. As a result, businesses must spend a significant amount of money on advertising to familiarise customers with their products. The number of sales will be minimal, and if necessary, precautions are not taken, there will be a considerable risk of product failure.
- Growth: Once the product has passed the introduction stage, sales begin to increase due to the customer's acceptance of the product. Because there is little or no competition, the sales growth rate is tremendous.
- Maturity (Saturation): When sales growth reaches a point where it can no longer expand any further. This is due to the competitor's products stealing market share. As a result, sales will continue for a while.
- Competitors will enter the market with superior product features, advanced technology, and lower prices, causing the market to decline. This puts the product's very existence in jeopardy, and sales begin to decline. If sufficient 'care' is not taken, such as the incorporation of specific features or design revisions, the products will be recalled from the market.
Particulars | Introduction | Growth | Maturity | Decline |
1.Product variety | High Variety | Increasing Standardisation | Dominant Design feature of product | High standard commodity |
2.Volume | Low volume | Increasing volume consolidation | High Volume | Decreasing volume |
3. Industry Structure | Small competition | Beginning of Competition | Few Large companies | Survivors |
4. Form of Competition | Product characteristics | Product Quality and availability | Price and dependability | Price |
Standardisation is a tool for variety reduction-"Standardisation is a process of defining and applying the conditions necessary to ensure that given range of requirements can normally i.e., met with a minimum of variety and in a reproducible and economic manner based on the best current techniques
The other two words associated with standardisation are:
Simplification-"a process of reducing types of products within a definite range".
Specialisation-" a process were in particular. Firms concentrate on the manufacture of the limited number of product types".
The three S are usually linked together and develop a logical sequence.
Objectives of Standardisation:
- Parts, components, and other items should be interchangeable.
- Variety should be kept to a minimum.
- As a result of the reduced diversity, it is easier to maintain control.
Advantages:
- Waste and obsolescence reduction.
- Inventory reduction.
- Less time and effort required for bookkeeping and accounting.
- Standardization lowers the cost due to economies of scale.
- Procurement is simplified due to availability.
- Costs of maintenance and repair are reduced.
Standardization applies to a wide range of activities. The following main categories can be used to characterise standardisation.
- Components with a defined range of physical dimensions and tolerances.
- Machine and equipment evaluations (energy, speed, voltage, temperature, etc.).
- Characteristics testing methods
- Performance expectations.
- Material qualities are specified (Physical and chemical).
- Safety considerations methods.
- Installation methods that comply with safety precautions and ease of usage.
Key Takeaway
"Standardisation is a process of defining and applying the conditions necessary to ensure that given range of requirements can normally i.e., met with a minimum of variety and in a reproducible and economic manner based on the best current techniques
Between the production and marketing divisions, simplification is a topic of contention. The production department prefers minimal variation since it decreases the amount of set ups and, as a result, production utilisation. The facilities have been expanded, and the component may now be produced at a lower cost than before due to the increased diversity.
Higher diversity, according to marketing experts, helps them sell more since it allows them to address the wants of a wider range of customers.
As a result, a balance is struck between the two in order to get the best range of product types to be made.
Advantages:
1. Reduce material and component part inventories.
2. Lower capital expenditures on equipment and machinery.
3. Storage space requirements are reduced.
4. Planning and control are simple.
5. A decrease in the selling price.
6. Inspection and control are simplified.
Disadvantages:
1. Unable to cater to a diverse range of customer demands.
2. There's a chance you'll lose orders to competitors.
3. It causes a perpetual struggle between marketing and manufacturing.
The practise of enlarging a product's original market is known as product diversification. This method is utilised to boost sales of an existing product line, and it's especially effective for a company that's been facing stagnant or declining sales.
Product Diversification Techniques:
Repackaging. To make a product available to a different audience, the way it is presented can be changed. A residential cleaning product, for example, could be repackaged and offered as a car cleaning agent.
Renaming. A current product could be renamed and offered in a different nation, possibly with somewhat modified packaging. The goal is to stay true to the product's original purpose while adapting it to fit the local culture.
Resizing. Repackaging a product into a different size or standard selling quantity is an option. For instance, a product that is generally sold in single units could be packaged in tents and offered through a warehouse shop.
Repricing. A product's pricing, as well as other enhancements, might be changed to reposition it for sale through a new distribution channel. For example, instead of being sold as a sport watch, a watch movement could be put into a platinum shell and sold through jewellery stores.
Extensions of a brand. It may be conceivable to extend an existing brand at the low or high end, or to fill a gap in the product line anywhere in the middle. For instance, suppose a car business intends to construct a sports car at the top of its product line.
Extensions to a product. It may be conceivable to sell multiple versions of the same product, perhaps with various features or colours. A smart phone, for example, might come in a variety of hues.
According to the Society of American Value Engineers (SAVE) "Value analysis is the systematic application of recognised techniques which identify the function of a product or service, establish a monetary value for the function and provide the necessary function reliably at that lowest overall cost."
Value analysis is a functionally oriented strategy for improving product value by linking various elements of product worth to their associated cost elements.
Value Engineering is a systematic, innovative method to ensuring that a product's or service's core functions are given at the lowest possible cost without losing quality or reliability.
The goal of value analysis is not to degrade or make items cheaper, but to increase their worth by lowering costs. The removal of needless costs has no negative impact on the product's quality or reliability. As a result, Value Engineering is a cost-cutting strategy that eliminates unneeded costs that have been integrated into the product.
Value analysis and value engineering
Despite the fact that the two terms are often used interchangeably, and the basic principle is the same, namely the removal of superfluous costs, there is a distinction between the two. The difference is in the amount of time and the stage of the product life cycle where the technology is used.
The existing product is subjected to a value analysis in order to improve its worth. It is a post-mortem investigation and a corrective procedure.
Value Engineering is used throughout the design phase of a product to ensure prevention rather than elimination.
Uses of value engineering
- It is a cost-cutting and cost-reduction approach that lowers the product's cost.
- Assists employees in better understanding their jobs and encourages them to think creatively.
- Strike a balance between price and performance.
- Prevents component overdesign
- Encourages staff to come up with novel ideas.
- Increases profitability while lowering costs
- Assists in ensuring that customers are satisfied with the company's products
When to apply value analysis:
When value analysis is used at the right moment and at the right phase of the product, excellent outcomes can be expected. The cycle of life. In the case of the following indications, V.E. Should be used:
- The company's products are losing market share and revenues are declining.
- The company's products are more expensive than those of its competitors.
- New product design is being pursued
- Signs of a disproportionately high cost of production
- Profitability and return on investment are declining (ROI)
- Failure of the company to achieve its delivery deadlines
Key Takeaway:
According to the Society of American Value Engineers (SAVE) "Value analysis is the systematic application of recognised techniques which identify the function of a product or service, establish a monetary value for the function and provide the necessary function reliably at that lowest overall cost."
Many firms use concurrent engineering, or simultaneous development, to ensure a smoother transition from product design to production and to save product development time. Concurrent engineering, in its most basic form, entails bringing design and manufacturing engineers together early in the design phase to develop a product and its manufacturing processes at the same time.
This notion has lately been broadened to include production personnel (for example, materials specialists) as well as marketing and purchasing personnel in loosely connected, cross-functional teams.
In addition, suppliers and customers' opinions are routinely requested. Of course, the goal is to create product designs that represent both client desires and manufacturing capabilities. Traditionally, designers created a new product without consulting production, then turned the design over to manufacturing, which had to build a procedure for producing the new product.
This "out-of-the-box" approach posed significant production issues, resulting in multiple conflicts and significantly increasing the time required to properly develop a new product. It also led to the ethos of "we versus them." The simultaneous development technique has a lot of appeal for these and other reasons.
The following are some of the major benefits of this strategy:
- Manufacturing employees can recognise production capabilities and capacity. They frequently have some design freedom in terms of selecting appropriate materials and methods. The ability to understand manufacturing capacities can aid in the selecting process. Furthermore, design can have a significant impact on cost and quality issues, as well as reducing production conflicts.
- Early chances for crucial tools design or purchase, some of which may have considerable lead periods. This could result in a significant reduction in the time it takes to develop a product, which could be a significant competitive advantage.
- Early consideration of a designs or a portion of a design's technical feasibility. Again, this can help to avoid major issues during production.
Instead of focusing on conflict resolution, the focus could be on problem solving. This co-development strategy, however, has several potential drawbacks. The following are two important ones:
- It can be difficult to break down long-standing barriers between design and manufacturing. Bringing a group of people together and expecting them to be able to work effectively together is probably foolish.
- If the process is to succeed, more communication and flexibility are required, both of which might be difficult to obtain.
Key Takeaway:
Concurrent engineering, in its most basic form, entails bringing design and manufacturing engineers together early in the design phase to develop a product and its manufacturing processes at the same time.
References:
- Industrial Engineering and Production Management by Martand T Telsang S. Chand Publishing
- Operations Research Theory & Applications by J K Sharma, Macmillan India Ltd,
- Automation, Production Systems & Computer Integrated Manufacturing by Groover, M.P. PHI
- Operations Research by P. K. Gupta and D. S. Hira, S. Chand & Co.
- Production & Operations Management by S.Anil Kumar 2nd edition ,New age publications