Unit - 1
Introduction
The sort of masses that change constantly at the shape or a frame are known as fluctuating masses. For instance visitors passing on a bridge applies specific masses of various nature. When load is fluctuating, the most pressure degree circumstance seems frequently.
So fluctuating masses lessen the persistence limit. Fluctuating stresses (repeated over lengthy length of time) will motive a element to fail (fracture) at a pressure degree a lot smaller than the remaining energy (or maybe the yield energy in a few cases).
Fatigue failure is one way or the other much like brittle fracture wherein the fracture surfaces are perpendicular to the weight axis. Fluctuating stresses are the ones whose significance is various with time. It isn't always vital that the curve displaying fluctuating pressure passes thru 0 or imply pressure via way of means of 0. Commonly the fluctuating stresses are categorized as alternating stresses, reversed and repeated stresses. These stresses range among their most (sigma max) (σ max) and minimum (sigma min) (σ m in) values as proven with inside the Figure 1.
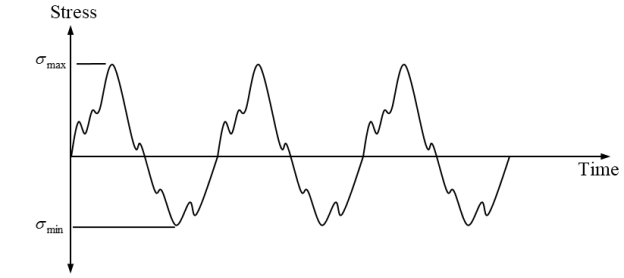
The broad objective of designing a machine element is to ensure that it preserves its operating capacity during the stipulated service life with minimum manufacturing and operating cost
In order to achieve this objective the machine element should satisfy the following basic requirements
1) Strength
2) Rigidity
3) Wear resistance
4) Minimum dimensions and weights
5) Manufacturability
6) Safety
7) Conformance to standards
8) Reliability
9) Maintainability
Strength
A system element have to now no longer fail below the impact of the forces that act up on it. In have to have enough electricity to keep away from failure both because of fracture (and) because of trendy yielding.
Rigidity
A system additives have to be inflexible this is it have to now no longer deflect (or) bend an excessive amount of because of the forces or moments that act up on it.
Wear resistance
Wear is the principle purpose that places the system elements out of order. It reduces the beneficial lifestyles of the component.
There are special forms of put on inclusive of
a. Abrasive put on
b. Corrosive put on
c. Pitting
Surface hardening can growth the damage resistance of the system additives inclusive of gears and cams.
Minimum dimensions and weights
A system element have to be sufficiently robust inflexible put on resistance and on the equal time with minimal viable dimensions and weights
Manufacturability
The form and cloth of the system element have to be decided on in any such manner that it is able to be produced with minimal exertions fee.
Safety
The form and dimensions of system elements have to make certain protection to the operator of system.
Conformance to requirements
A system element have to verify to the country wide requirements protecting its profile dimensions grade and cloth.
Reliability
It is the chance that a system element will carry out its supposed feature. Over a particular time period this is it have to carry out its feature over its lifestyles time.
Maintainability
It is the benefit with which a system element may be serviced or repaired. Minimum lifestyles cycle fee. It is the full fee to be paid through the patron for buying the element and working it over its lifestyles time.
Key Takeaways:
- When load is fluctuating, the most pressure degree circumstance seems frequently.
- Commonly the fluctuating stresses are categorized as alternating stresses, reversed and repeated stresses
- In have to have enough electricity to keep away from failure both because of fracture (and) because of trendy yielding
- The form and cloth of the system element have to be decided on in any such manner that it is able to be produced with minimal exertions fee.
There isn't any any inflexible rule for the technique of device layout, however, there's a few standard technique for device layout. Various steps blanketed with inside the technique of device layout is defined below.
Understand the Requirements:
Recognition of the requirement is step one of all type of engineering layout. It consists of the special announcement of the trouble, aim, and cause of the device is to be designed. The announcement must be clean and special as feasible.
Recognising the answer for a trouble through giving a whole assertion of the trouble through figuring out the intention and cause of why the device is wanted to be designed.
Synthesis of mechanism:
It is the identity of favoured movement and mechanism. Shortlist all feasible mechanism then pick the best-desirable mechanism as in keeping with trouble requirement. Analysis of pressure: Find out the forces appearing on every element of mechanism and electricity transmitted through every element.
Synthesise the distinctive mechanism and pick out the first-rate mechanism for the specified motions a few of the distinctive mechanisms
Material choice:
Select the cloth desirable for the device. The choice relies upon at the importance of the weight at the device element, the opportunity of carrying of a mating element, environmental factors (inclusive of humidity, temperature etc.), and the cost.
Designing of element:
Find the dimension/length of every member of the device through thinking about the pressure evaluation and permissible strain restriction of the chosen cloth.
We need to lay out a device that need to be given the operation situations as properly because it need to face up to for an extended life. For that, we want to examine the dimensions and stresses appearing in distinctive factors with inside the device through thinking about the forces appearing at the device factors. We need to test those stresses with the permissible strain of every cloth we've got used with inside the making of device factors.
Modification
To lessen the general value of the productions and because of the supply of the resources, we need to make a few concerns to house the changes. We need to alter the dimensions or some other change desires to happen. That is the case we want to be prepared to do change with inside the layout.
Consider beyond enjoy and layout modification:
Here the designed device is changed in step with the preceding record. This non-public judgment makes essential adjustments in layout both to enhance the great and to lessen the cost.
Analysis of Forces
Analyse the distinctive gadget of forces with inside the movement of the device individuals and energy transmissions a few of the distinctive device factors. Selection of Materials
Detailed drawing:
Make the drawing of every element and the complete meeting of device. Specify the cloth, dimension, accuracy, floor end and different parameters with inside the drawing. Now the CAD software’s are giving extraordinary help in drawing.
We can say that is the very last degree for figuring out what type of device we're going to build. Once we've got executed with the detailing of every and each additives and meeting and subassemblies drawings, we need to continue with the production.
Production:
The additives are synthetic with inside the workshop as in keeping with engineering drawing.
As consistent with the drawing, the additives may be synthetic with inside the production units. And assembled as consistent with the distinct drawings. Her the entirety may be produced and despatched them to the subsequent step nice checking (QC). If any distinction is there then it need to come lower back for the reproduction.
Quality Checking
This is the very last step to decide whether or not the manufacturing of every device detail is as consistent with the distinct drawings we've got provided. This is the device layout technique
Key Takeaways:
- Analysis of pressure: Find out the forces appearing on every element of mechanism and electricity transmitted through every element.
- We need to test those stresses with the permissible strain of every cloth we've got used with inside the making of device factors.
- That is the case we want to be prepared to do change with inside the layout.
- If any distinction is there then it need to come lower back for the reproduction.
Standards are files that describe the vital capabilities of a product, provider or system. For example, CSA Standard Z262.34-00 Ice Hockey Pucks specifies a hockey puck's material, size, and mass, hardness at room temperature and check methods. There are thousands of requirements in use across the world.
They cowl the entirety from the best screw thread to the maximum complicated records generation network. By making use of requirements, businesses can assist to make sure that their services and products are consistent, compatible, secure and powerful.
Today, merchandise are assembled from additives made in one of a kind international locations, and are then offered across the world, so requirements are greater vital than ever. Standards have an effect on almost each services or products we stumble upon in our everyday lives.
Just believe how tough and threatening it can be to alternate a mild bulb if there have been now no longer requirements regarding electric powered safety, voltage, and mild bulb sizes.
The Standards Council of Canada is a federal Crown employer with the mandate to sell green and powerful standardization in Canada.
It has approved 4 requirements improvement businesses: the Canadian General Standards Board (CGSB), the Canadian Standards Association (CSA), Underwriters' Laboratories of Canada (ULC) and the Bureau de normalisation du Quebec (BNQ).
Two of the maximum vital global corporations for standardization are the International Organization for Standardization (ISO) and the International Electro technical Commission (IEC).
ISO and IEC requirements are regularly followed with the aid of using international locations as voluntary requirements, or blanketed in country wide guidelines and regulations. Standards organized with the aid of using a few American institutions are used as global requirements.
Here are a few examples: American Society for Testing and Materials (ASTM), American Society of Mechanical Engineers (ASME), and the Society of Automotive Engineers (SAE).
Importance of Standards:
Enhance health, protection and first-class of life
Improve performance
Reduce risk
Become greater sustainable
Facilitate worldwide alternate and marketplace access
Help produce green and powerful products
Reduce costs, enhance provider relations
Guide enterprise communications and marketing
Advance innovation and new technologies
Support regulatory desires and compliance
Transfer era to the marketplace
Make contemporary-day conveniences possible
Inability to promote finished product
Damage dating with suppliers
Interoperability issues
Product now no longer permitted through regulators
Possible governmental sanctions, fine, and/or reprimands
Possible civil lawsuits
Possible crook lawsuits
Loss of revenue
Accidents Illness
Property damage
Loss of expert license
Loss of or incapacity to achieve insurance
Key Takeaways:
- There are thousands of requirements in use across the world.
- The Standards Council of Canada is a federal Crown employer with the mandate to sell green and powerful standardization in Canada.
- Standards organized with the aid of using a few American institutions are used as global requirements.
- Advance innovation and new technologies
A designation is the unique identity of every grade, kind, or elegance of metallic with the aid of using a variety, letter, symbol, name, or appropriate combination. Unique to a specific metallic grade, kind and sophistication are phrases used to categorise metallic merchandise.
Within the metallic industry, they've very unique makes use of: grade is used to indicate chemical composition; kind is used to signify DE oxidation exercise; and sophistication is used to explain a few different attribute, including energy stage or floor smoothness. This article describes fundamentals of SAE, AISI, UNS, AMS, European and Japanese designation systems.
A designation is the unique identity of every grade, kind, or elegance of metallic with the aid of using a variety, letter, symbol, name, or appropriate combination. In ASTM specs, however, those phrases are used fairly interchangeably.
In ASTM A 533, for example, kind denotes chemical composition, at the same time as elegance shows energy stage. In ASTM A 515, grade identifies energy stage; the most carbon content material authorised with the aid of using this specification relies upon on each plate thickness and energy stage.
SAE-AISI Designations
Carbon steels incorporate much less than 1.65% Mn, 0.60% Si, and 0.60% Cu; they include the lxxx corporation’s with inside the SAE-AISI machine and are subdivided into 4 wonderful collection because of the distinction in sure essential houses amongst them.
Designations for service provider first-rate steels encompass the prefix M. A carbon metallic designation with the letter B inserted among the second one and 0.33 digits shows the metallic includes 0.0005 to 0.003% B. Likewise, the letter L inserted among the second one and 0.33 digits shows that the metallic includes 0.15 to 0.35% Pb for more desirable machinability.
Desulfurized carbon steels of the 11xx organization and desulfurized and rephosphorized carbon steels of the 12xx organization are produced for packages requiring true machinability.
Steels that having nominal manganese contents of among 0.nine and 1.5% however no different alloying additions now have 15xx designations in location of the 10xx designations previously used.
Alloy steels incorporate manganese, silicon, or copper in portions more than the ones indexed for the carbon steels, or they've special tiers or minimums for one or greater of the opposite alloying factors.
In the AISI-SAE machine of designations, the fundamental alloying factors are indicated with the aid of using the primary digits of the designation. The quantity of carbon, in hundredths of a percent, is indicated with the aid of using the final (or three) digits.
For alloy steels which have unique hardenability necessities, the suffix H is used to differentiate those steels from corresponding grades that haven't any hardenability requirement.
As with carbon steels, the letter B inserted among the second one and 0.33 digits shows that the metallic includes boron.
The prefix E means that the metallic become produced with the aid of using the electrical furnace process. HSLA Steels.
Several grades of HSLA metallic are defined in SAE Recommended Practice J410. These steels were advanced as a compromise among the handy fabrication traits and occasional price of undeniable carbon steels and the excessive energy of heat-handled alloy steels. These steels have extraordinary energy and ductility as-rolled.
UNS Designations
The Unified Numbering System (UNS) has been advanced with the aid of using ASTM and SAE and numerous different technical societies, exchange associations, and United States authorities’ agencies.
A UNS variety, that is a designation of chemical composition and now no longer a specification, is assigned to every chemical composition of a steel alloy. The UNS designation of an alloy includes a letter and 5 numerals.
The letters imply the huge elegance of alloys; the numerals outline unique alloys inside that elegance. Existing designation machine, including the AISI-SAE machine for steels, were included into UNS designations. UNS is defined in more element in SAE J1086 and ASTM E 527.
AMS Designation
Aerospace Materials Specifications (AMS), posted with the aid of using SAE, are whole specs which might be normally good enough for procurement purposes. Most of the AMS designations pertain to substances supposed for aerospace packages
Processing necessities, including for consumable electrode remelting, are not unusual place in AMS steels. ASTM (ASME)
Specifications
The maximum extensively used widespread specs for metallic merchandise with inside the
United States are the ones posted with the aid of using ASTM.
These are whole specs, normally good enough for procurement purposes.
Many ASTM specs follow to unique merchandise, including A 574 for alloy metallic socket head cap screws.
These specs are normally orientated closer to overall performance of the fabricated cease product, with massive range in chemical composition of the metallic used to make the cease product.
ASTM specs constitute a consensus amongst producers, specifies, fabricators, and customers of metallic mill merchandise. In many cases, the dimensions, tolerances, limits, and regulations with inside the ASTM specs are just like or similar to the corresponding gadgets of the same old practices with inside the AISI Steel Products Manuals.
Many of the ASTM specs were followed with the aid of using the American Society of Mechanical Engineers (ASME) with very little modification; ASME makes use of the prefix S and the ASTM designation for those specs. For example, ASME-SA213 and ASTM A 213 are equal.
Key Takeaways:
- Unique to a specific metallic grade, kind and sophistication are phrases used to categorise metallic merchandise.
- This article describes fundamentals of SAE, AISI, UNS, AMS, European and Japanese designation systems.
- The quantity of carbon, in hundredths of a percent, is indicated with the aid of using the final (or three) digits.
- Processing necessities, including for consumable electrode remelting, are not unusual place in AMS steels. ASTM (ASME)
- In commercial design, desired numbers (additionally known as desired values or desired series) are widespread tips for selecting actual product dimensions inside a given set of constraints.
- Product builders need to pick out several lengths, distances, diameters, volumes, and different feature quantities.
- While all of those picks are restricted through issues of functionality, usability, compatibility, protection or cost, there typically stays good sized leeway with inside the actual desire for plenty dimensions.
- Preferred numbers serve purposes: Using them will increase the opportunity of compatibility among items designed at exceptional instances through exceptional people.
- In different words, it's miles one tactic amongst many in standardization, whether or not inside an organisation or inside an industry, and additionally it is acceptable in commercial contexts (except the purpose is supplier lock-in or deliberate obsolescence)
- They are selected such that once a product is synthetic in lots of exceptional sizes, those will emerge as more or less similarly spaced on a logarithmic scale.
- They consequently assist to reduce the variety of various sizes that want to be synthetic or saved in stock.
The Preferred Series Number is a designed system element that desires standardization to keep away from variations. It means that the product’s vital parameters ought to be not unusual place in nature.
For example, the sizes of the ingots (Raw Material) to be had with inside the marketplace have well-known sizes.
A producer does now no longer produce ingots of sizes of his wish, he should comply with a particular sample to supply the ingots in that size. The fashion dressmaker can pick out the size from the ones well-known to be had sizes.
Motor pace, the engine strength of a tractor, system device pace and feed, all comply with a particular sample or series. This additionally enables with inside the interchangeability of products.
Key Takeaways:
- They consequently assist to reduce the variety of various sizes that want to be synthetic or saved in stock.
- The fashion dressmaker can pick out the size from the ones well-known to be had sizes.
One of the maximum hard project of substances engineer is the right choice of the cloth for a selected job, e.g., a selected element of a device or structure. An engineer must be in a role to select the most beneficial aggregate of residences in a cloth on the lowest feasible value without compromising the quality.
Factors affecting the choice of substances:
(i) Component form:
The form and length of an element has top notch impact on the selection of the processing unit which in the end consequences the selection of the cloth. To make it extra clear, we don't forget an example, permit the quality feasible manufacturing approach is selected, beneath Neath given conditions, it is die casting, obviously, now the selection of the cloth will become limited, i.e. you'll be able to only select substances with decrease melting points, e.g. Aluminium, zinc, magnesium and thermoplastics.
(ii) Dimensional tolerance:
There are a few substances which may be completed to shut tolerance even as others cannot. Obviously, the desired dimensional tolerance for completed additives will, have an impact on the desire of substances.
(iii) Mechanical residences:
To pick an appropriate cloth for particular conditions, all mechanical residences, e.g., toughness, hardness, strength, etc. manual us.
(iv) Fabrication (Manufacturing) necessities:
Method of processing of the cloth additionally influences the residences of an element, e.g., cast additives may be more potent than the casted additives. Different kinds of operating approaches may supply distinctive kinds of fibre structure. However, investment casting can offer particular dimensions at low value in contrast to device operations.
Service necessities:
- Service necessities are:
- Dimensional stability,
- Strength,
- Toughness,
- Warmness resistance,
- Corrosion resistance,
- Fatigue and creep resistance,
- Electric and thermal conductivity etc
Mechanical Properties of Metals
The mechanical homes of the metals are the ones which can be related to the cap potential of the fabric to face up to mechanical forces and load. These mechanical homes of the steel consist of strength, stiffness, elasticity, plasticity, ductility, brittleness, malleability, durability, resilience, creep and hardness. We shall now speak those homes as follows:
Static strength
It is the cap potential of a cloth to face up to the externally implemented forces without breaking or yielding. The inner resistance presented with the aid of using a cloth to an externally implemented pressure is known as pressure.
Stiffness
The modulus of elasticity is the degree of stiffness.
Elasticity
It is the assets of a cloth to regain its unique length and form after deformation while the outside forces are removed. This assets is suited for substances utilized in equipment and machines.
Plasticity
It is assets of a cloth which keeps the deformation produced beneath Neath load permanently. This assets of the fabric is essential for forgings, in stamping photos on cash and in decorative work
Ductility
It is the assets of a cloth allowing it to be drawn into cord with the software of a tensile pressure. A ductile fabric need to be each robust and plastic. The ductility is commonly measured with the aid of using the terms-percent elongation and percent discount in area. The ductile fabric normally utilized in engineering exercise are moderate steel, copper, aluminium, nickel, zinc, tin and lead.
Brittleness
It is the assets of a cloth contrary to ductility. It is the assets of breaking of a cloth with little everlasting distortion. Brittle substances while subjected to tensile hundreds snap off without giving any practical elongation. Cast iron is a brittle fabric.
Malleability
It is a unique case of ductility which lets in substances to be rolled or hammered into skinny sheets. A malleable fabric need to be plastic however it isn't important to be so robust. The malleable substances normally utilized in engineering exercise (so as of diminishing malleability) are lead, gentle steel, wrought iron, copper and aluminium
Toughness
It is the assets of a cloth to face up to fracture because of excessive effect hundreds like hammer blows. The durability of the fabric decreases while it's far heated. It is measured with the aid of using the quantity of power that a unit extent of the fabric has absorbed after being burdened as much as the factor of fracture. This assets is suited in elements subjected to surprise and effect hundreds.
Machinability
It is the assets of a cloth which refers to a relative case with which a cloth may be reduce. The machinability of a cloth may be measured in some of methods including evaluating the device lifestyles for slicing unique substances or thrust required to dispose of the fabric at a few given price or the power required to dispose of a unit extent of the fabric. It can be mentioned that brass may be without problems machined than steel.
Resilience
It is the assets of a cloth to take in power and to face up to surprise and effect hundreds. It is measured with the aid of using the quantity of power absorbed in keeping with unit extent with inelastic limit. This assets is important for spring substances.
Creep
When a element is subjected to a steady pressure at excessive temperature for a protracted duration of time, it's going to go through a gradual a everlasting deformation known as creep. This assets is taken into consideration in designing inner combustion engines, boilers and turbines.
Fatigue
When a cloth is subjected to repeated stresses, it fails at stresses under the yield factor stresses. Such form of failure of a cloth is called fatigue. The failure is resulting from way of a modern crack formation which can be commonly high-quality and of microscopic length. This assets is taken into consideration in designing shafts, connecting rods, springs, gears, etc.
Hardness
It is a completely essential assets of the metals and has a huge type of meanings .It embraces many unique homes including resistance to wear, scratching, deformation and machinability etc. It additionally way the cap potential of a steel to reduce every other steel. The hardness is commonly expressed in numbers which can be depending on the approach of creating the test. The hardness of a steel can be decided with the aid of using the subsequent tests:
- Brunel hardness test
- Rockwell hardness test
- Vickers hardness
- Shore sclera scope.
Key Takeaways:
- Obviously, the desired dimensional tolerance for completed additives will, have an impact on the desire of substances.
- However, investment casting can offer particular dimensions at low value in contrast to device operations.
- . It can be mentioned that brass may be without problems machined than steel.
- This assets is taken into consideration in designing shafts, connecting rods, springs, gears, etc.
The static load safety factor is calculated by dividing the basic static load rating (C0) by the static equivalent load of the most heavily loaded bearing.
When the shaft is subjected to a twisting moment (or torque) only, then the diameter of the shaft only may be obtained by using the torsion equation. We know that T/J=Ϡ/r……………………………..(i)
Where, T= twisting moment acting on the shaft
J=Polar moment of inertia
Ϡ= Torsional shear stress
R= distance from neutral axis to the outermost fibre
=d/2, where d is the diameter of shaft
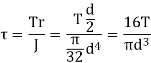
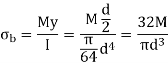
Cyclic strain is the repetitive incidence and redistribution of forces appearing on a fabric. Periodic or ordinary cyclic strain situations result in elevated put on and tear of the fabric, therefore growing the charge of fabric degradation and failure.
An instance of an item susceptible to cyclic strain is a device containing wheels this is used to guide a lift-pulley device, which include determined in a ski lift. Such a configuration guarantees that implemented forces are vertical to the ground, which will increase the direct effect of gravitational forces at the fabric and the degradation charge.
The repeated effect of stresses beneath anxiety and compression supported with the aid of using a rotating movement generates fatigue and put on. Cyclic strain is a first-rate supply of crack propagation, strain corrosion and crevice corrosion.
Cyclic strain is the distribution of forces (aka stresses) that alternate through the years in a repetitive fashion. As an instance, bear in mind one of the big wheels used to force an aerial raise inclusive of a ski raise.
- The cord cable wrapped across the wheel exerts a downward pressure at the wheel and the force shaft assisting the wheel. Although the shaft, wheel, and cable move, the pressure stays almost vertical relative to the floor.
- Thus a factor at the floor of the force shaft will go through anxiety whilst it's miles pointing in the direction of the floor and compression whilst it's miles pointing to the sky. Cyclic strain is often encountered in rotating equipment wherein a bending second is carried out to a rotating part.
- This is referred to as a cyclic bending strain and the aerial raise above is a great instance. However, cyclic axial stresses and cyclic torsional stresses additionally exist. An instance of cyclic axial strain might be a bungee wire (see bungee jumping), which have to aid the mass of human beings as they bounce off systems inclusive of bridges. When someone reaches the cease of a wire, the wire deflects elastically and prevents the character's descent.
- This creates a big axial strain with inside the wire.
- A fraction of the elastic capacity power saved with inside the wire is commonly transferred returned to the character, throwing the character upwards a few fraction of the space she or he fell.
- The character then falls at the wire again, inducing strain with inside the wire. This takes place a couple of instances in keeping with bounce.
- The identical wire is used for numerous jumps, growing cyclical stresses with inside the wire that would subsequently reason failure if now no longer replaced.
Key Takeaways:
- Cyclic strain is the repetitive incidence and redistribution of forces appearing on a fabric. Periodic or ordinary cyclic strain situations result in elevated put
- As an instance, bear in mind one of the big wheels used to force an aerial raise inclusive of a ski raise.
- Cyclic strain is often encountered in rotating equipment wherein a bending second is carried out to a rotating part.
- It has been experimentally found that when a material is subjected to repeated stress, it fails at stresses below the yield point stresses.
- Such type of failure of a material is known as fatigue.
- The failure is caused using a progressive crack formation which is usually fine and of microscopic size.
- The failure may occur even without any prior indication.
- The fatigue of material is affected by the size of the component, relative magnitude of static and fluctuating loads, and the number of load reversals.
- To study the effect of fatigue of a material, a rotating mirror beam method is used.
- In this method, a standard mirror-polished specimen, as shown in Fig (a), is rotated in a fatigue testing machine while the specimen is loaded in bending.
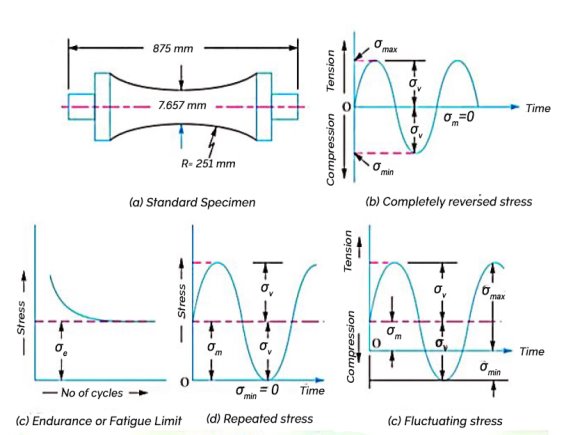
- As the specimen rotates, the bending stress at the upper fibers varies from maximum compressive to maximum tensile while the bending stress at the lower fibers varies from maximum tensile to maximum compressive.
- The specimen is subjected to a completely reversed stress cycle.
- This is represented by a time stress diagram as shown in figure (b).
- A record is kept of the number of cycles required to produce failure at given stress, and the results are plotted in the stress cycle curve as shown in figure (c).
- A little consideration will show that if the stress is kept below a certain value as shown in by the dotted line in figure (c), the material will not fail whatever may be the number of cycles.
- This maximum stress, represented by a dotted line is known as endurance or fatigue limit
.
- It is defined as a maximum value of the completely reversed bending stress which is polished standard specimen can withstand without failure, for the infinite number of cycles (usually
cycles).
- It may be noted that the term endurance limit is used for reverse bending only while for other types of loading, the term endurance strength may be used when referring to the fatigue strength of the material.
- It may be defined as the safe maximum stress which can be applied to the machine part working under actual conditions.
- We have seen that when a machine member is subjected to a completely reversed stress, the maximum stress in tension is equal to the maximum stress in compression as shown in figure (b). In actual practice, many machine members undergo a different range of stress than completely reversed stress.
- The stress versus time diagram for fluctuating stress having values
is shown in figure (c).
- The variables test, in general, may be considered as a combination of study (or mean or average) stress and a completely reversed stress component
.
- The following relations are derived from figure 6.2 (c).
- Mean or average stress
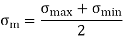
2. Reversed stress component or alternating or variable stress
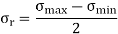
3. For repeated loading, the stress varies from maximum to zero each cycle as shown in figure (d).
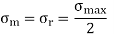
4. Stress ratio, For completely reversed stresses, R = -1 and for repeated stresses, R = 0. It may be noted that R cannot be greater than unity.
5. The following relation between endurance limit and stress ratio may be used.
Key Takeaways:
- The fatigue of material is affected by the size of the component, relative magnitude of static and fluctuating loads, and the number of load reversals.
- This is represented by a time stress diagram as shown in figure (b).
- It may be defined as the safe maximum stress which can be applied to the machine part working under actual conditions.
- Whenever a machine component changes the shape of its cross-section, the simple stress distribution no longer holds good and the neighborhood of the discontinuity is different.
- This is regularity is the stress distribution caused by abrupt changes of form is called stress concentration.
- It occurs for all kinds of stresses in the presence of fillets, notches, holes, keyways, splines, surface roughness or scratches, etc.
- Consider a member with a different cross-section under a tensile load as shown in the figure.
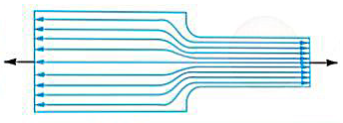
- A little consideration will show that the nominal stress in the right and left-hand sides will be uniform but in the region where the cross-section is changing, a redistribution of the forces within the member must take place.
- The material near the edges is stressed considerably e higher than the average value.
- The maximum stress occurs at some point on the fillet and is directed parallel to the boundary at that point.
The causes of stress concentration are as follows
(i) Variation in properties of materials.
- In the design of machine components, it is assumed that the material is homogeneous throughout the component.
- In practice, there is a variation in material properties from one end to another due to the following factors:
(a) Internal cracks and flaws like blowholes
(b) Cavities in welds
(c) Air holes in steel components, and
(d) Non-metallic or foreign inclusions
- These variations act as discontinuities in the component and cause stress concentration.
(ii) Load application
- Machine components are subjected to forces.
- These forces act either at a point or over a small area on the component.
- Since the area is small, the pressure at these points is excessive.
- This results in stress concentration.
- The examples of these load applications are as follows:
(a) Contact between the meshing teeth of the driving and the driver gear
(b) Contact between the cam and follower
(c) Contact between the balls and the races of ball bearing
(d) Contact between the rail and wheel
(e) Contact between the crane hook and the chain.
- In all these cases, the concentrated load is applied over a very small area resulting in stress concentration.
(iii) Abrupt changes in section.
- To Mount gears, sprockets, pulleys, and ball bearings on a transmission shaft, steps are cut on the shaft, and shoulders are provided from assembly considerations.
- Although these features are essential, they create a change of the cross-section of the shaft.
- This results in stress concentration at these cross-sections.
(iv) Discontinuities in the component.
- Certain features of machine components such as oil holes or oil grooves keyways and splines and screw threads result in discontinuities in the cross-section of the component.
- There is stress concentration in the vicinity of these discontinuities.
(v) Machining scratches
- Machining scratches stamp mark or inspection marks are surface irregularities, which cause stress concentration.
Methods of reducing stress concentration
- The presence of stress concentration cannot be eliminated but it may be reduced to some extent.
- In fig. 1 (a) we see that stress lines tend to bunch up and cut very close to the sharp reentrant corner.
- To improve the situation, fillets may be provided, as shown in figure (b) and (c) to give more equally spaced flow lines.
- Following Figures show several ways of reducing the stress concentration in the shaft and other cylindrical members with shoulders, holes, and threads respectively.
- It may be noted that it is not practicable to use large radius fillets as in case of ball and roller bearing mountings. In such cases, notches may be cut as shown in figure 1 (d) and figure 2 (b) and (c).
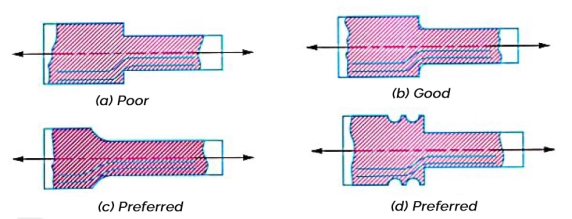
Fig. 1
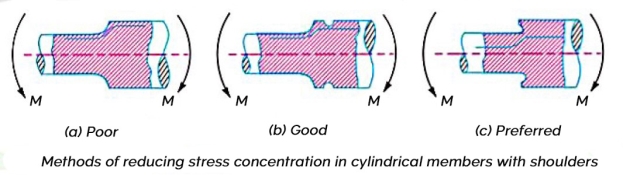
Fig 2
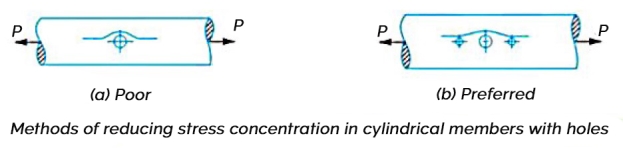
Fig 3
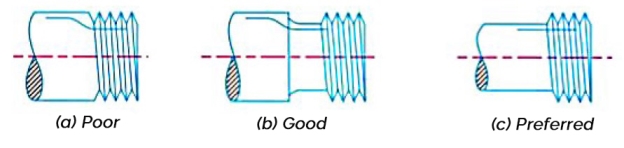
Fig 4
- The stress concentration effects of a press-fit may be reduced by making for a gradual transition from the rigid to the more flexible shaft.
- The various ways of reducing stress concentration for such cases are shown in figure 4 (a), (b), and (c).
Key Takeaways:
- It occurs for all kinds of stresses in the presence of fillets, notches, holes, keyways, splines, surface roughness or scratches, etc.
- The material near the edges is stressed considerably e higher than the average value.
- In all these cases, the concentrated load is applied over a very small area resulting in stress concentration.
A pressure attention component (Kt) is a dimensionless component this is used to quantify how focused the pressure is in a mechanical component. It is described because the ratio of the best pressure with inside the component as compared to a reference pressure.
A pressure attention, additionally called a pressure riser/raiser, is a factor in a component wherein the pressure is notably extra than its surrounding area. Stress concentrations arise due to irregularities with inside the geometry or in the cloth of a thing shape that motive an interruption of the pressure flow.
These interruptions usually stand up from discontinuities which includes holes, grooves, notches and fillets. Stress concentrations can also be due to unintentional harm which includes nicks and scratches.
A discontinuity’s diploma of attention below traditional tensile masses is normally expressed through the non-dimensional pressure attention component (Kt), that's the ratio of the best pressure to the reference (some distance field) pressure:

Note that the reference stress is the total stress within an element under the same loading conditions, but without any stress concentrators (i.e., the total stress on the part when it is free from discontinuities).
An understanding of the stress concentration factor is important during the material selection process as well as for anticipating stress corrosion cracking, fretting corrosion and material failures.
Basic strain evaluation calculations anticipate that elements are smooth, have a uniform cross-phase, and haven't any irregularities. In practice, without a doubt all engineering additives have at the least minimum adjustments in phase and/or shape. Shoulders on shafts, oil holes, key methods and screw threads all can extrude the strain distribution such that the simple strain evaluation equations now not apply.
Such discontinuities motive a nearby growth in strain, called a strain attention thing. If the cloth is ideal without a discontinuities, then the strain attention thing is 1. If there may be a discontinuity, then the strain attention thing is extra than
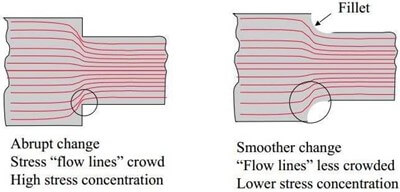
How Stress Concentration Factor (Kt) Values are Determined
- The strain attention thing related to a part’s particular geometry and loading situation may be derived thru experimentation, evaluation or computational strategies.
- Experimental strategies: Optical strategies consisting of photo elasticity are very reliable and broadly used for experimentally figuring out the strain attention at a factor on a part.
- However, numerous opportunity strategies which have been traditionally used consist of the grid technique, brittle coating, brittle version and stress gauge.
- Analytical strategies: The concept of elasticity may be used to investigate positive geometrical shapes to calculate strain attention factors.
- Computational strategies: Finite detail strategies offer a effective and cheaper computational technique to evaluate strain attention factors.
Key Takeaways:
- Stress concentrations can also be due to unintentional harm which includes nicks and scratches.
- Shoulders on shafts, oil holes, key methods and screw threads all can extrude the strain distribution such that the simple strain evaluation equations now not apply.
- The concept of elasticity may be used to investigate positive geometrical shapes to calculate strain attention factors.
Let us begin to have a glance to the fatigue restriction (additionally called fatigue power). For steady amplitude loading that is the pressure amplitude that suggests the transition from countless existence to finite existence. If the pressure amplitude is smaller than the fatigue restriction, the fatigue existence can be countless.
At least, for steady amplitude loading it can be. So in case you need to layout for countless existence, simply preserve all pressure amplitudes under the fatigue restriction. That appears quite straightforward, however there are a few issues:
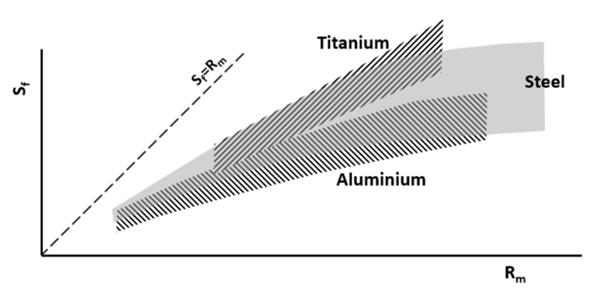
Some materials, like titanium and maximum steels, have a clean fatigue restriction. So under that restriction, the fatigue existence is certainly countless.
Unfortunately, lots of different materials (aluminium, magnesium, copper, austenitic metallic) do now no longer display a completely clean fatigue restriction.
There continues to be a knick with inside the S-N curve at a big range of cycles (106 or more), however past that range of cycles, the S-N isn't completely flat.
The curve nevertheless has a completely shallow gradient. In widespread it isn't recognized how a ways this shallow gradient continues. For aluminium, the fatigue restriction is frequently given for 5⋅108 cycles.
Although metallic display a completely wonderful fatigue restriction, there are nevertheless reviews of fatigue screw ups at very excessive range of cycles (108-1010). This phenomenon (VHCF: very excessive cycle fatigue) but appears best to arise below very particular conditions.
Despite of the truth that the knick with inside the S-N curve of lies round 106 cycles, fatigue failure may also arise at large range of cycles. Some viable reasons are referred to above.
Apart from that, the scale of the factor may also play a function as well. S-N curves are frequently decided the usage of small specimens, while systems are frequently lots large. Small specimens will fail quickly after initiation, however the length of big systems permit cracks to develop to a far large duration earlier than you get very last failure.
Obtaining the Fatigue Limit
To get an affordable correct fee of the fatigue restriction, assessments need to be done.
A very not unusual place form of trying out to decide the fatigue restriction is staircase trying out. But frequently, required statistics may be observed in literature. That statistics is both received with the aid of using trying out or with the aid of using estimating.
Testing is OK, however estimating Look on the graph under. It shows that there's a relation among the fatigue power and closing power of a cloth. But that relation isn't linear. And the relation indicates a lousy lot of scatter.
Moreover, static power is decided with the aid of using bulk cloth residences while fatigue is basically decided with the aid of using floor conditions.
Estimating the fatigue restriction with the aid of using making use of a few issue at the tensile power is simply an excessive amount of a simplification. Nevertheless, it's miles frequently done, e.g. With inside the FKM Guidelines.
If you want to do so, e.g. In case of loss of statistics, be very careful! As referred to earlier, in case you need to layout for countless existence, simply preserve all pressure amplitudes under the fatigue restriction.
As lengthy as even the most important pressure amplitude is under the fatigue restriction, existence can be countless. But changed into occurs if a few amplitudes are above and a few are under the fatigue restriction.
It is plain that the amplitudes above the fatigue restriction will cause a finite existence. The amplitudes under the fatigue restriction will now no longer make contributions to the earliest section of initiation.
But as soon as the crack is initiated (eleven though nevertheless very small), the ones small amplitudes begin contributing to harm accumulation. So in case of variable amplitude loading, additionally cycles with amplitudes under the fatigue restriction must be taken into account.
Key Takeaways:
- That appears quite straightforward, however there are a few issues:
- Some viable reasons are referred to above.
- To get an affordable correct fee of the fatigue restriction, assessments need to be done.
- When a component is subjected to fluctuating stresses as shown in figure (a), there is mean stress
as well as stress amplitude
.
- It has been observed that the mean stress component affects fatigue failure when it is present in combination with the alternating component.
- The fatigue diagram for the general case is shown in the figure.
- In this diagram, the mean stress is plotted on the abscissa.
- The stress amplitude is plotted on the ordinate.
- The magnitude of
depends upon the magnitude of maximum and minimum force acting on the component.
- When stress amplitude
is zero, the load is purely static and the criterion of failure is
.
- These limits are plotted on the abscissa. When the mean stress
is zero, the stress is completely reversing in the criterion of failure is endurance limit
that is plotted on the ordinate.
- When the component is subjected to both components of stress
the actual failure occurs at different scattered points shown in the figure.
- There exists a border, which divides a safe region from the unsafe reason for various combinations of
.
- Different criteria are proposed to construct the borderline dividing safe zone and failure zone.
- They include Gerber line, Soderberg line, and Goodman line.
- Gerber Line: A parabolic of joining
on the ordinate to
on the abscissa is called the Gerber line.
- Soderberg Line: A straight line joining
on the ordinate to
on the abscissa is called the Soderberg line.
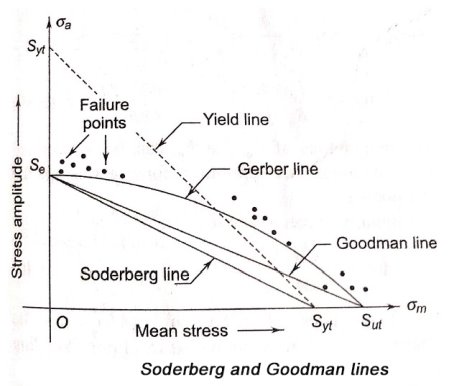
Key Takeaways:
- The fatigue diagram for the general case is shown in the figure.
- When the component is subjected to both components of stress
the actual failure occurs at different scattered points shown in the figure.
Goodman line: A straight line joining on the ordinate to
on the abscissa is called the Goodman line.
- The Gerber parabola fits the failure points of test data in the best possible way.
- Goodman line fits beneath the scatter of this data.
- Both Gerber parabola and Goodman line intersect at
on the ordinate to
on the abscissa.
- However, the Goodman line is safer from design considerations because it is completely inside the Gerber parabola and inside the failure points.
- The Soderberg line is a more conservative failure criterion and there is no need to consider even yielding in this case.
- A Yield line is constructed connecting
on both axes.
- It is said as a limit on the first cycle of stress.
- This is because if a part yields, it has failed, regardless of its safety in fatigue.
- We will apply the following form for the equation of the straight line,

Where a and b are the intercepts of the line on X and Y axes respectively.
Applying the above formula, the equation of the Soderberg line is given by

Similarly, the equation of the Goodman line is given by

Goodman line is widely used as the criterion of failure when the component is subjected to mean stress as well as stress amplitude. It is because of the following reasons:
(i) Goodman line is safe from design considerations because it is completely inside the failure points of test data.
(ii) Equation of straight line is simple compared with the equation of the parabolic curve.
(iii) It is not necessary to construct a scale diagram and the rough sketch is enough to construct a fatigue diagram.
Key Takeaways:
- Goodman line fits beneath the scatter of this data.
- The Soderberg line is a more conservative failure criterion and there is no need to consider even yielding in this case.
- The Soderberg line and Goodman line illustrated in Fig are straight lines.
- The theories using such straight lines for predicting fatigue failure are called linear theories.
- Some theories use parabolic or elliptical curves instead of straight lines.
- These theories are called nonlinear theories.
- One of the most popular non-linear theories is Gerber's theory that is based on the parabolic curve.
- The Gerber curve is shown in Fig.
- The equation for Gerber curve is as follows:
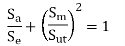
- The above equation is called the Gerber equation. It can be also written in the following form,
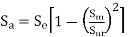
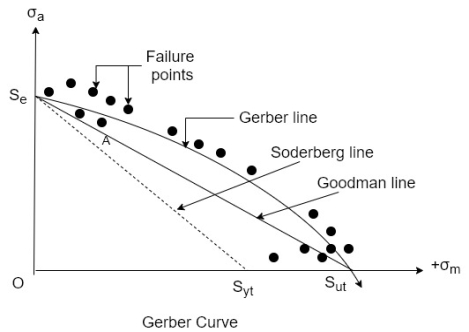
- Theories based on the Soderberg line or Goodman line, as failure criteria are consecutive theories. This results in increased dimensions of the component.
- The Gerber curve takes the mean path through failure points. It is, therefore, more accurate in predicting fatigue failure.
Key Takeaways:
- The theories using such straight lines for predicting fatigue failure are called linear theories.
- The Gerber curve takes the mean path through failure points. It is, therefore, more accurate in predicting fatigue failure.
References:
1. Mechanical Engineering Design, 9e – Joseph E. Shigely, McGraw Hill Education.
2. Machine Design‐Maleev and Hartman, CBS Publishers.
3. Design of Machine Design‐M.F. Spott, Pearson Education.
4. Elements of Machine Component Design, Juvinal & Marshek, John Wiley & Sons.
5. Machine design, Robert L. Norton, Pearson Education