Unit – 1
Conventional Power Generation
Steam Power station
The schematic diagram of steam power station is shown in the figure below. The whole arrangement can be divided into the following stages for the sake of simplicity :
1. Coal and ash handling arrangement
2. Steam generating plant
3. Steam turbine
4. Alternator
5. Feed water
6. Cooling arrangement

1.Coal and ash handling plant: The coal is transported to the steam power station by road or rail and is stored in the coal storage plant. Storage of coal is primarily a matter of protection against coal strikes, failure of the transportation system and general coal shortages. From the coal storage plant, coal is delivered to the coal handling plant where it is pulverised (i.e., crushed into small pieces) in order to increase its surface exposure, thus promoting rapid combustion without using large quantity of excess air.
The pulverised coal is fed to the boiler by belt conveyors. The coal is burnt in the boiler and the ash produced after the complete combustion of coal is removed to the ash handling plant and then delivered to the ash storage plant for disposal. The removal of the ash from the boiler furnace is necessary for proper burning of coal.
2. Steam generating plant: The steam generating plant consists of a boiler for the production of steam and other auxiliary equipment for the utilisation of flue gases.
(i) Boiler: The heat of combustion of coal in the boiler is utilised to convert water into steam at high temperature and pressure. The flue gases from the boiler make their journey through super heater economiser, air pre-heater and are finally exhausted to atmosphere through the chimney.
(ii) Super heater: The steam produced in the boiler is wet and is passed through a super heater where it is dried and superheated (i.e.., the steam temperature increased above that of the boiling point of water) by the flue gases on their way to the chimney. Super heating provides two principal benefits. Firstly, the overall efficiency is increased. Secondly, too much condensation in the last stages of the turbine is avoided. The superheated steam from the super heater is fed to the steam turbine through the main valve.
(iii) Economiser: An economiser is essentially a feed water heater and derives heat from the flue gases for this purpose. The feed water is fed to the economiser before supplying to the boiler. The economiser extracts a part of the heat of flue gases to increase the feed water temperature.
(iv) Air pre-heater: An air pre-heater increases the temperature of the air supplied for coal burning by deriving heat from flue gases. Air is drawn from the atmosphere by a forced draught fan and is passed through air pre-heater before supplying to the boiler furnace. The air pre-heater extracts heat from flue gases and increases the temperature of air used for coal combustion. The principal benefits of preheating the air are increased thermal efficiency and increased steam capacity per square metre of boiler surface.
3. Steam turbine: The dry and superheated steam from the super heater is fed to the steam turbine through the main valve. The heat energy of steam when passing over the blades of the turbine is converted into mechanical energy. After giving heat energy to the turbine, the steam is exhausted to the condenser which condenses the exhausted steam by means of cold water circulation.
4.Alternator: The steam turbine is coupled to an alternator. The alternator converts mechanical energy of turbine into electrical energy. The electrical output from the alternator is delivered to the bus bars through transformer, circuit breakers and isolators.
5. Feed water: The condensate from the condenser is used as feed water to the boiler. Some water may be lost in the cycle which is suitably made up from external source. The feed water on its way to the boiler is heated by water heaters and economiser. This helps in raising the overall efficiency of the plant.
6. Cooling arrangement: In order to improve the efficiency of the steam power plant, the steam exhausted from the turbine is condensed by means of a condenser. Water is drawn from a natural source of supply such as a river, canal or lake and is circulated through the condenser. The circulating water takes up the heat of the exhausted steam and itself becomes hot.
This hot water coming out from the condenser is discharged at a suitable location down the river. In case the availability of water from the source of supply is not assured throughout the year, cooling towers are used. During the scarcity of water in the river, hot water from the condenser is passed on to the cooling towers where it is cooled. The cold water from the cooling tower is reused in the condenser.
Advantages
- The fuel (i.e., coal) used is quite cheap.
- Less initial cost as compared to other generating stations.
- It can be installed at any place irrespective of the existence of coal.
- The coal can be transported to the site of the plant by rail or road.
- It requires less space as compared to the hydro electric power station.
- The cost of generation is lesser than that of the diesel power station.
Disadvantages
- It pollutes the atmosphere due to the production of a large amount of smoke and fumes.
- It is costlier in running cost as compared to hydro electric plant.
Nuclear power plant
In the power plant, the fission takes place in the reactor and the middle of the reactor is known as the core that includes uranium fuel, and this can be formed into pellets of ceramic. Every pellet generates 150 gallons of oil energy. The total energy generated from the pellets is stacked in metal fuel rods. A bunch of these rods is known as a fuel assembly and a reactor core includes several fuel assemblies.
During nuclear fission, the heat can be generated within the core of the reactor. This heat can be used to warm the water into steam so that turbine blades can be activated. Once the turbine blades activated then they drive the generators to make electricity. In a power plant, a cooling tower is available to cool the steam into the water otherwise they use the water from different resources. Finally, the cooled water can be reused to generate steam.
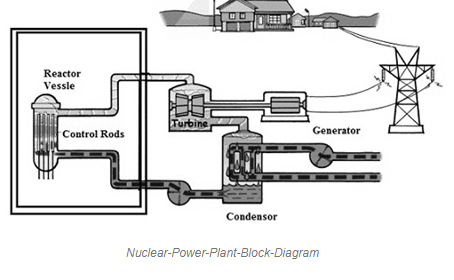
Components of Nuclear Power Plant
There are different components which include the following.
Nuclear Reactor
In a power plant, a nuclear reactor is an essential component like a heat source that includes the fuel & its reaction of nuclear chain including the waste products of nuclear. The nuclear fuel used in the nuclear reactor is Uranium & its reactions are heat generated in a reactor. Then, this heat can be transferred to the coolant of the reactor to generate heat to all the parts in the power plant.
Steam Generation
In all the power plants, the production of steam is general; however, the way of generating will change. Most of the plants use water reactors by using two loops of rotating water to generate steam. The primary loop carries very hot water for heating an exchange once water at a low-pressure is circulated, then it warms the water to generate the steam to transmit to the turbine section.
Steam Generation
In all the power plants, the production of steam is general; however, the way of generating will change. Most of the plants use water reactors by using two loops of rotating water to generate steam. The primary loop carries very hot water for heating an exchange once water at a low-pressure is circulated, then it warms the water to generate the steam to transmit to the turbine section.
- Steam Generation
In all the power plants, the production of steam is general; however, the way of generating will change. Most of the plants use water reactors by using two loops of rotating water to generate steam. The primary loop carries very hot water for heating an exchange once water at a low-pressure is circulated, then it warms the water to generate the steam to transmit to the turbine section.
Generator & Turbine
Once the steam is generated, then it travels with high pressures to speed up the turbine. The rotating of the turbines can be used to rotate an electric generator for generating electricity that is transmitted to the electrical grid.
Cooling Towers
In a nuclear power plant, the most essential part is a cooling tower which is used to reduce the heat of the water. Please refer to this link to know more about what is a cooling tower – components, construction & applications
Working of Nuclear Power Plant
The elements like Uranium or Thorium are sued nuclear fission reaction of a nuclear reactor. Because of this fission, a huge amount of heat energy can be generated and it is transmitted to the coolant reactor. Here, the coolant is nothing but water, liquid metal otherwise gas. The water is heated to flow in a heat exchanger so that it changes into high-temperature steam. Then the steam which is produced is permitted to make a steam turbine run. Again the steam can be changed back into the coolant & recycled to use for the heat exchanger. So, the turbine and alternator are connected to produce electricity. By using a transformer, the electricity which is produced can be increased to use in long-distance communication.
Advantages
- It uses less space compared with other power plants
- It is extremely economical and generates huge electric power.
- These plants are located near the load center because there is no requirement of huge fuel.
- It generates a huge amount of power in the process of each nuclear fission
- It uses less fuel to generate huge energy
- Its operation is reliable
- When compared with steam power plants, it is very clean and neat
- The operating cost is small
- It doesn’t produce polluting gases
Disadvantages
- The cost of primary installation is extremely high when compared with other power stations.
- The nuclear fuel is expensive so recovering is difficult
- High capital cost compare with other power plants
- Technical knowledge is required to operate this plat. So maintenance, as well as salary, will be high.
- There is a chance of radioactive pollution
- The response is not efficient
- The requirement of cooling water is double compare with a steam power plant.
Gas turbine power plant
The main components are
- Compressor,
- Regenerator,
- Combustion chamber,
- Gas turbine,
- Alternator, and
- Starting motor
Compressor
Air compressor used in a gas turbine power plant is mainly of the rotary type. The air filter is attached at the inlet of the compressor where air gets filtered from dust. The rotary blades attached to the shaft push the air between stationary blocks, and consequently, the pressure of the air is increased. High pressure air is available at the outlet of the compressor.
Regenerator
There is always some heat presents in the exhaust gases in gas turbine power plant . A portion of this heat is utilized in the regenerator. In regenerator, there is a net of fine tubes. The compressed air is passed through these fine tubes. The whole arrangement is enclosed in a vessel through which hot exhaust gases from turbine pass. During passing through the fine tubes, compressed air gets a portion of heat carried by exhaust gases. In this way, a significant portion of the heat of exhaust gases raises the temperature of the compressed air before it enters into the combustion chamber.
Combustion Chamber
After passing through the regenerator, the hot compressed air enters into the combustion chamber. In the combustion chamber, there are burners through which fuel oil is injected in the form of oil spray. Due to combustion of this hot oil spray inside the combustion chamber, the air attends a very high temperature. The temperature is about 3000oF. The compressed air mixed with combustion gases then cooled down to 1500oF to 1300oF before it is being delivered to the turbine for doing mechanical work there.
Alternator
The rotor of an alternator is attached to the same shaft of the turbine hence the alternator rotates along with the turbine and produces electrical energy.
Starting Motor
In gas turbine power plant the compressor, alternator, and turbine are attached to the same shaft. For starting the system, the compressor has to deliver pre-compressed air at starting. The shaft has to rotate to produce required compressed air for starting purpose. Hence, an alternative arrangement is required to run the compressor before the system is being started. This is done by a starting motor connected to the same shaft. A motor coupled with the main shaft supplies the required mechanical power for compressing air before starting.
Turbine
The compressed air mixed with combustion gases then enters in the turbine through nozzles. Here, the mixture of gases is suddenly expanded and it gains required kinetic energy to do mechanical work to rotate the turbine shaft (main shaft). In the turbine the temperature of the gases comes down to 900oF.
Advantages
(i) It is simple in design as compared to steam power station since no boilers and their auxiliaries are required.
(ii) It is much smaller in size as compared to the steam power station of the same capacity. This is expected since the gas turbine power plant does not require a boiler, feed water arrangement etc.
(iii) The initial and operating costs are much lower than that of the equivalent steam power station.
(iv) It requires comparatively less water as no condenser is used.
(v) The maintenance charges are quite small.
(vi) Gas turbines are much simpler in construction and operation than steam turbines.
(vii) It can be started quickly form cold conditions.
(viii) There are no standby losses. However, in a steam power station, these losses occur because the boiler is kept in operation even when the steam turbine is supplying no load.
Disadvantages
(i) There is a problem with starting the unit. It is because before starting the turbine, the compressor has to be operated for which power is required from some external source. However, once the unit starts, the external power is not needed as the turbine itself supplies the necessary power to the compressor.
(ii) Since a greater part of power developed by the turbine is used in driving the compressor, the net output is low.
(iii) The overall efficiency of such plants is low (about 20%) because the exhaust gases from the turbine contain sufficient heat.
(iv) The temperature of the combustion chamber is quite high (3000F) so that its life is comparatively reduced.
Hydro power station
.
A hydro electric power station simply involves the conversion of hydraulic energy into electrical energy, yet it embraces many arrangements for proper working and efficiency. The schematic diagram of hydro electric plant is shown in the figure below. The dam is constructed across a river or lake and water from the catchment area collects at the back of the dam to form a reservoir. A pressure tunnel is taken off from the reservoir and water brought to the valve house at the start of the penstock.
The valve house contains main sluice valves and automatic isolating valves. The former controls the water flow to the power house and the latter cuts off the supply of water when the penstock bursts. From the valve house, water is taken to water turbine through a huge steel pipe known as penstock. The water turbine converts hydraulic energy into mechanical energy. The turbine drives the alternator which converts mechanical energy into electrical energy.
A surge tank (open from top) is built just before the valve house and protects the penstock from bursting in case the turbine gates suddenly closed due to electrical load being thrown off. When the gates close, there is a sudden stopping of water at the lower end of the penstock and consequently, he penstock can burst like a paper log. The surge tank absorbs this pressure swing by increase in its level of water.
The constituents of a hydro electric plant are
(1) Hydraulic structures
(2) Water turbines and
(3) Electrical equipment
1. Hydraulic structures : Hydraulic structures in a hydro electric power station include dam, spillways, head works, surge tank, penstock and accessory works.
(i) Dam : A dam is a barrier which stores water and creates water head. Dams are built of concrete or stone masonary, earth or rock fill. The type and arrangement depends upon the topography of the site. A masonary dam may be built in a narrow canyon. An earth dam may be best suited for a wide valley. The type of dam also depends upon the foundation conditions, local materials and transportation available, occurrence of earthquakes and other hazards. At most of sites, more than one type of dam may be suitable and the one which is most economical is chosen.
(ii) Spillways : There are times when the river flow exceeds the storage capacity of the reservoir. Such a situation arises during heavy rainfall in the catchment area. In order to discharge the surplus water from the storage reservoir into the river on the down-stream side of the dam, spillways are used. Spillways are constructed of concrete piers on the top of the dam. Gates are provided between these piers and surplus water is discharged over the crest of the dam by opening these gates.
(iii) Head works : The head works consists of the diversion structures at the head of an intake. They generally include booms and racks for diverting floating debris, sluices for by-passing debris and sediments and valves for controlling the flow of water to the turbine. The flow of water into and through head works should be as smooth as possible to avoid head loss and cavitation. For this purpose, it is necessary to avoid sharp corners and abrupt contractions or enlargements.
(iv) Surge tank : Open conduits leading water to the turbine require no protection. However, when closed conduits are used, protection becomes necessary to limit the abnormal pressure in the conduit. For this reason, closed conduits are always provided with a surge tank. A surge tank is a small reservoir or tank (open at the top) in which water level rises or falls to reduce the pressure swings in the conduit.
A surge tank is located near the beginning of the conduit. When the turbine is running at a steady load, there are no surges in the flow of water through the conduit i.e., the quantity of water flowing in the conduit is just sufficient to meet the turbine requirements. However, when the load on the turbine decreases, the governor closes the gates of turbine, reducing water supply to the turbine. The excess water at the lower end of the conduit rushes back to the surge tank and increases its water level.
Thus the conduit is prevented from bursting. On the other hand, when load on the turbine increases, additional water is drawn from the surge tank to meet the increased load requirement. Hence, a surge tank overcomes the abnormal pressure in the conduit when load on the turbine falls and acts as a reservoir during increase of load on the turbine.
(v) Penstocks : Penstocks are open or closed conduits which carry water to the turbines. They are generally made of reinforced concrete or steel. Concrete penstocks are suitable for low heads (< 30 m) as greater pressure causes rapid deterioration of concrete. The steel penstocks can be designed for any head; the thickness of the penstock increases with the head or working pressure.
2. Water turbines : Water turbines are used to convert the energy of falling water into mechanical energy. The principal types of water turbines are :
(i) Impulse turbines
(ii) Reaction turbines
- Impulse turbines : Such turbines are used for high heads. In an impulse turbine, the entire pressure of water is converted into kinetic energy in a nozzle and the velocity of the jet drives the wheel. The example of this type of turbine is the Pelton wheel. It consists of a wheel fitted with elliptical buckets along its periphery. The force of water jet striking the buckets on the wheel drives the turbine.
The quantity of water jet falling on the turbine is controlled by means of a needle or spear (not shown in the figure) placed in the tip of the nozzle. The movement of the needle is controlled by the governor. If the load on the turbine decreases, the governor pushes the needle into the nozzle, thereby reducing the quantity of water striking the buckets. Reverse action takes place if the load on the turbine increases.
- Reaction turbines: Reaction turbines are used for low and medium heads. In a reaction turbine, water enters the runner partly with pressure energy and partly with velocity head. The important types of reaction turbines are
- Francis turbines
- Kaplan turbines
3.Electrical equipment: The electrical equipment of a hydro electric power station includes alternators, transformers, circuit breakers and other switching and protective devices.
Advantages
(i) It requires no fuel as water is used for the generation of electrical energy.
(ii) It is quite neat and clean as no smoke or ash is produced.
(iii) It requires very small running charges because water is the source of energy which is available free of cost.
(iv) It is comparatively simple in construction and requires less maintenance.
(v) It does not require a long starting time like a steam power station. In fact, such plants can be put into service instantly.
(vi) It is robust and has a longer life.
(vii) Such plants serve many purposes. In addition to the generation of electrical energy, they also help in irrigation and controlling floods.
(viii) Although such plants require the attention of highly skilled persons at the time of construction, yet for operation, a few experienced persons may do the job well.
Disadvantages
(i) It involves high capital cost due to construction of dam.
(ii) There is uncertainty about the availability of huge amount of water due to dependence on weather conditions.
(iii) Skilled and experienced hands are required to build the plant.
(iv) It requires high cost of transmission lines as the plant is located in hilly areas which are quite away from the consumers.
Thermo electric generators
- Thermoelectricity refers to a class of phenomena in which a temperature difference creates an electric potential or an electric potential creates a temperature difference.
- Thermoelectric power generator is a device that converts the heat energy into electrical energy based on the principles of Seebeck effect
Thermoelectric materials
The good thermoelectric materials should possess
- Large Seebeck coefficients
- High electrical conductivity
- Low thermal conductivity
Working
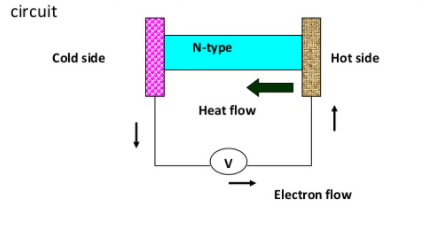
When the two sides of semiconductor are maintained with different temperature, the emf is flows across the output circuit Cold side N-type Hot side Heat flow V Electron flow
As the heat moves from hot side to cold side, the carrier moves in the semiconductor materials and the potential deference is created. Charge hence
The electrons are the charge carriers in the case of Ntype semiconductor and Hole are in P-type semiconductors. • In a stack, number of semiconductors is connected. P-type and
A single PN connection can produce a Seebeck of 40 mV. N-type voltage
The heat source such as natural gas or propane are used for remote power generation
Thermionic generators
- Thermionic Power Convertor is a static device that converts heat into electricity by boiling electrons from a hot emitter surface(approx 1800 K) across a small inter electrode gap(< 0.5 mm) to a cooler collector surface(approx 1000 K)
- A Thermionic Generator consists of one or more of these convertors coupled to give desired power output
- Thermionic generators can be operated from any primary heat source.
- For low power level(3 kW or less) solar energy can be used
- For high power level (50 kW or more) nuclear heat source can be used
Comparison
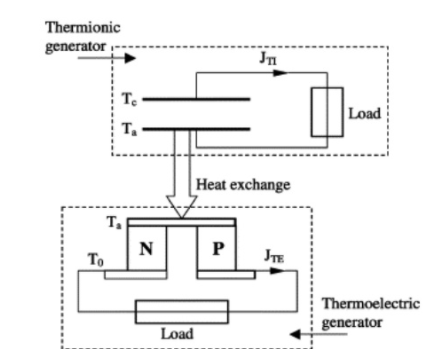
Both thermionic and thermoelectric generators employ the electron gas as the working fluid
A thermionic generator based on the ballistic current flow which is highly efficient, and its theoretical efficiency is close to the Carnot efficiency
A thermoelectric generator, however, has poor efficiency due to the diffusive current flow
A thermionic generator usually requires a high temperature heat source (e.g. 1500 K) to generate a practically useful current
A thermoelectric generator, however, can produce electrical power from low-quality heat energy sources
1. Cost of Transmission of Energy
A power plant should be located as near to the load centre as possible. This reduces the transmission costs and losses in transmission.
2. Cost of Fuel
The cost of fuel is an important consideration in deciding the type of power plant for a particular location. With hydroelectric power plants there is no cost of fuel as the source of power is water but water should be available in huge quantity and at sufficient head.
For steam plants, the cost of coal for the boilers and the availability of coal are important considerations. If cheap oil is available, the boilers may be oil fired and steam plants may complete other types of power plants. Steam power plants are most economical near coal mines and by the side of river or canal.
Fuel used in nuclear power plant is expensive and is difficult to recover. Diesel engines need oil as fuel and cost of this depends on the location of the power plant. For instance, if the plant is to be located near oil fields where oil is available in plenty and at cheaper rates and the transportation cost is extremely small, it may be economical to install a diesel power plant from the point of view of fuel cost.
3. Cost of Land and Taxes
The costs of land as well as taxes on the land are dependent on the situation of the proposed power plant. The cost of land near a load centre (in a big city) may be very high as compared to that at remote place. The taxes also would be higher for land in the centre of a commercial city. This is therefore, an important point to be considered in the economic selection of site.
4. Requirement of Space
The space and building requirements of the power plant is another point to be considered. If the building and space required are both large, the cost of land as well as building will be large. Thus, large power plants in the hearts of big cities and near the centre of gravity of load are not economical.
A hydroelectric power plant requires a lot of space for civil engineering construction works like dams etc., the building has to be much larger than required by other types of power plants, and a number of arrangements have to be provided in the building as special features which are quite different from those in other types of power plants. The location, however, is suitable at site where water is available at enough head and the cost of land is not excessive.
Steam power plants do not need so much space, but they require space more than that required by other power plants (diesel, gas turbine, nuclear). Diesel power plant needs minimum space. The space required for gas turbine power plant is more than that for diesel power plant but less than that for hydro, steam and nuclear power plants.
5. Availability of Site for Water Power
In deciding the type of power plant for a given location, it is desirable to investigate whether any suitable source of water and sites are available for the development of hydroelectric power plant. Some of the considerations are topography of land, rainfall during the year, catchment area, suitable site for storing water behind the dam, huge quantity of water at sufficient head and cost of civil engineering works.
6. Storage Space for Fuel
A steam (coal-based) power plant needs space for storage of coal in amounts depending on the size of plant. A supply of coal for the next 2/3 weeks at least should always be available on site. The amount of reserve stock required depends on the location of power plant. If the plant is near a coal mine it may not be necessary to store a large quantity, while if the coal has to be transported from a long distance over lake or rail etc., a large stock may be required.
For oil fuel the space required is comparatively small. The quantity required as space depends to a great extent on the degree of security of oil supplies.
7. Transportation Facilities
The location of a power plant is dependent to some extent on the availability of transportation facilities. It is necessary to have a railway, line available and extended to the yard for bringing in heavy machinery for installation in the beginning and for bringing in fuel-coal or oil as well as material required for maintenance. Alternatively, the plant may be located on the bank of a river where facilities are available for transport by barges or ships.
The machinery to be transported for a steam plant is rather heavy, as the plant will in general be much larger than a diesel plant. For a diesel power plant the problem of transport is not so acute, the plant is generally small, the machines and equipment to be brought in are not very heavy, and large quantities of fuels are not required.
Road transport should, however, be available. For hydroelectric power plants, remote from the normal available rail and other transport facilities, roads are to be built leading to the site and arrangements made so that the equipment can be taken to site. Heavy equipment may have to be transported in parts and assembled on site. As nuclear power plant needs very little fuel, hence it does not require direct rail facilities for fuel transport. However, transportation facilities are required during the construction stage.
8. Availability of Cooling Water
A steam power plant needs larger quantities of cooling water than diesel and gas turbine power plants. Water is circulated through condenser tubes to condense the steam and to maintain a high vacuum in the turbine condenser for high efficiency. Thus, site adjacent to larger bodies of water are preferable. Alternatively, tube-wells and cooling towers have to be installed and their cost must be taken into account.
9. Disposal of Ash
A steam power plant produces huge quantity of ash. A site where ash can be disposed off easily will naturally be beneficial. In case of nuclear power plants, the disposal of products (radioactive in nature) is a big problem. They have either to be disposed off in a deep trench or in a sea away from the seashore.
10. Pollution and Noise
A site for a power plant near a load centre may be objectionable from the point of view of noise and pollution. Diesel engines are noisy and people in the vicinity are likely to raise complaints. Similarly gas turbine power plants also produce noise. A steam power plant in the centre of city may also cause noise, though not so much as a diesel power plant. Smoke from the chimney of a steam power plant is undesirable in cities.
There is a danger of presence of radioactivity in the atmosphere near a nuclear power plant. However, as a precautionary measure, a dome is used in the plant which does not allow the radioactivity to spread by wind or underground water ways. Noise of exhaust from diesel engines is objectionable, but may be reduced to some extent by means of silencers.
11. Nature of Load
The nature of load to be supplied affects the choice of the power plant to a certain extent. If the load varies suddenly to a great extent; so that the load factor is poor, and if the load is not very large, a diesel or a gas turbine plant will be chosen as they are more adaptable than a steam/nuclear power plants as they can be started quickly and can be put to share full load within few minutes.
With a steam plant the boilers have to keep banked and ready to pick up load any time. The steam power plant also requires a longer time for starting and for taking load, as the necessary vacuum has to be created and maintained before the load can be shared. Nuclear power plants are not well suited for varying load since the reactor does not respond to the fluctuations of load efficiently.
Nuclear power plants also needs a longer time (2-3 hours) for starting and taking load. If hydroelectric power plant of small or suitable capacity is available, it can be started quickly and take up load, and thus can be employed for the varying loads.
12. Reliability of Supply
In case all the big power plants are located on one side of a state, the reliability of supply in remote areas would be poor. As such power plants should be located in different areas of the state so that reliability of supply is good everywhere.
13. Equitable Growth of Different Areas
It has been seen that availability of power from a nearby source in an area encourages setting up of heavy industries in that area and consequently, the ancillary industries are also to come up. This can improve the economy of a backward area significantly. In a welfare state committed to growth of all regions, some power plants should, therefore, be installed in backward areas. In such areas land and labour will also be available at cheaper rates.
Reference Books
- Environmental pollution and Control by Ruth Weiner et al
- Environmental Pollution Control Engineering by C S Rao
- Environmental Engineering-1 by H.S Vishwanath et al