Unit – 3
Energy conservation
It is well known that the scope for energy conservation in India is enormous. There are huge gains to be made by upgrading technology, equipment and appliances in a wide range of applications – furnaces, motors, insulation systems, automobile engines, cooking burners, power generating systems, and so on.
It is well known that the scope for energy conservation in India is enormous. There are huge gains to be made by upgrading technology, equipment and appliances in a wide range of applications – furnaces, motors, insulation systems, automobile engines, cooking burners, power generating systems, and so on.
Conservation of electrical energy means the reduction in energy consumption but without making any sacrifice of quantity & quality of production1 .In other words, for the same energy consumption, higher production, it does not prevent you use of energy by fixing some limit quantitatively within the agreement but insists for use efficiently thus decreasing the cost of production to some extent by the way of reduction in the energy bill. 2. It can also be defined as the substitution of energy with capital, labour, material & time. This definition also covers the substitution of scarce type of energy (e.g. Oil) with abundant type of energy (e.g. Coal) or the substitution of energy with convenience.
PRINCIPLES OF ENERGY CONSERVATION
Two principles governing energy conservation policies are maximum thermodynamics efficiency and maximum cost effectiveness in energy use. The first and second law of thermodynamics measure the efficiency of energy use, allocation of available production factors determine the cost effectiveness of conservation. Maximum thermodynamics efficiency in energy use is defined as maximum work production by using a given amount of primary energy input. Maximum Work= (Energy input)–(energy loss in transfer)–(energy discharge).
Energy is a scarce commodity. Energy in any form is a scarce commodity & an inexpensive resource. However, if look at the predicted future human population fugues & consider the probability that the individual life expectations will increase, we see that energy could be in future is in short supply.
ENERGY CONSERVATION OBJECTIVEs
Broadly energy conservation program initiated at micro or macro level will have the following objectives:-
- To reduce imports of energy & reduce the drain on foreign exchange.
- To improve exports & manufactured goods or of energy or both.
- To reduce the environmental pollution per unit of industrial output as carbon dioxide, smoke, sulphur dioxide, dust or coal mine discard etc.
- Thus reducing the costs that pollution incurs either directly as damage or as needing special measures to combat it once the pollutants are produced.
- Generally to relieve shortage & improve development.
HVAC systems
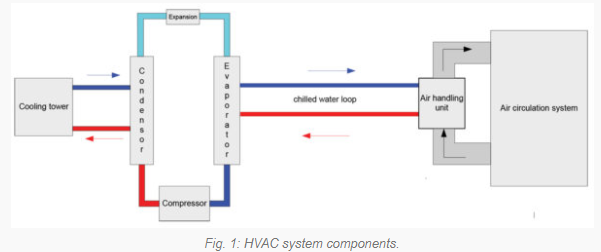
HVAC systems account for more than 50% of a facility’s energy usage [1]. After the cooling load has been reduced and the HVAC system has been optimized in terms of airflow, environmental controls and sensors, there still remain major areas of possible energy savings in the major components that form the basis of the system.
Most HVAC systems are designed to handle the maximum cooling or heating load required by the building. This maximum only occurs for a short period in the year and, for most of the time, the system is faced with a load below the maximum, and operates below full capacity. Operating below capacity generally means inefficient operation, and energy savings can be achieved by the use of systems that optimise operation under conditions below full capacity.
The HVAC system consists of the following components:
- Central chilled water plant.
- Chiller water cooling system.
- Chilled water circulation system.
- Air cooling (handling) and circulation system.
In addition to these units, there are numerous pumps and fans, each of which contributes to the energy demand, and each of which can be configured to run energy-efficiently.
Heating, Ventilation and Air-Conditioning (HVAC) Equipment Considering HVAC processes, improved equipment components available on the market may be purchased and installed, replacing existing inefficient components. The typical layout of a large-scale HVAC system is illustrated in Figure . Typical energy usage of HVAC components may be divided into five categories, these are; fans, cooling, heating, pumps and cooling towers. The energy usage of fans, cooling and heating account for 34%, 27% and 17%, respectively. Pumps and cooling towers are responsible for 16% and 6%, respectively. In hindsight, replacing existing equipment, responsible for these energy-intensive processes with higher efficiency equipment, may offer substantial savings. Furthermore, existing systems are usually outdated and subjected to poor performance, due to degradation over time. The main contributor to the degradation of these systems may be a result of continuous operation, poor maintenance and prolonged exposure to environmental conditions.
Moreover, recently developed equipment may offer substantial improvements in terms of energy efficiency. For instance, the use of variable speed drives to control compressor systems in chillers, as opposed to standalone fixed speed compressors, may offer substantial savings. A demand response component is introduced, as opposed to the constant supply of compressed refrigerant being delivered by the conventional system. In addition, variable speed drives have similarly been introduced to water pumps and fans, to obtain further efficiency gains. Pumps are located in both the evaporator and condenser sections, while fans, responsible for heat extraction and airflow regulation, are located at the condenser section and the air-handling units, respectively.
Other improvements in HVAC design may incorporate permanent magnet synchronous motors, rather than induction motors, offering average energy-efficiency gains of up to 10.4% across the total speed range. To put this into perspective, the overall energy savings in HVAC systems may be as high as 8.58% as a result of replacing induction motors. Permanent magnet synchronous motors may replace all existing induction motors in the HVAC system, so that overall energy efficiency may be increased. Additionally, permanent magnet synchronous motors usually operate at a near constant efficiency of approximately 96%, at any given speed percentile.
Moreover, when considering the evaporator, significant advancements have been made in recent years to improve evaporator performance. The most commonly used evaporator design in the past was the flooded type, where refrigerant completely covered water conduits within the evaporator. Two other arrangements were introduced to decrease the amount of refrigerant required to deliver the same results as the most commonly utilized system i.e., the flooded type. A reduction in refrigerant may result in less energy spent in terms of work required to compress and pump refrigerant around the cooling loop. These improved evaporator systems comprise of the mixed falling (MF) film evaporator and the full falling (FF) film evaporator. The MF type evaporator was observed to use approximately 15% less refrigerant than the conventional flooded type, while the FF type may reduce the required refrigerant by up to 40%, as compared to the flooded type. Therefore, in choosing the FF type, the energy required through compression and pumping of the refrigerant may be reduced by approximately 40%. This roughly translates into energy savings of approximately 10.8%, considering the total energy consumption of HVAC equipment. Additionally, the use of state-of-the-art variable refrigerant flow (VRF) systems may offer savings of 30%–40% on overall HVAC energy consumption
Pumps and pump controllers
There are numerous pumps in the system and all play a part in energy savings. When operating at below full capacity, the amount of refrigerant and cooling liquids required to be moved through the system is reduced. This is accomplished by controlling the pump system. Traditional means of controlling the pump output involve dissipating or diverting the output of the pump running at full speed by means of bypass and throttle valves, which meant that the pump was still running at full load or close to full load. VSD drives allow flow control by varying the speed or other parameters of the pump to achieve the required flow rate.
The latest improvements in smart VSDs factor in the effects of speed on the pump’s hydraulic performance to better control processes. This is accomplished through embedded pump-specific algorithms that use information such as torque, speed and power received from the VSD to escalate KPIs specifically related to pumps and pump systems. An example is smart VSDs controlling processes using torque rather than speed.
Fans and fan controllers
Energy saving on fans is much greater than on other equipment. On fan loads, the power requirement varies as the cube of the speed, so the slower the fan speed, the less energy required. A fan running at 80% speed will consume 50% of the energy at 100% speed. Modern fan controls consist of much more than just speed controls and variable speed drives.
Key to identifying the energy savings opportunities of VSDs in HVAC systems is an understanding of the operating cycle of the system versus the heating and cooling needs actually required. Most HVAC systems are designed to keep the building cool on the hottest days and warm on the coldest days. Therefore, the HVAC system only needs to work at full capacity on those days.
For the rest of the year, the HVAC system can operate at reduced capacity. This is where a variable air volume system with variable speed drives (also-called variable frequency drives, or VFDs) can be used to match air flow to actual heating and cooling demands. The VSD can reduce the motor speed when full flow is not required, thereby reducing the power and the electrical energy used.
This can result in significantly improved process control compared to traditional speed control when controlling pumps with relatively flat performance curves. Because of the significant advancements in drive technology and the information’s accuracy and reliability, industry professionals can better estimate pump performance parameters such as flow and head solely by using drive output torque and speed data. VSD controllers available today offer features unique to HVAC systems that can schedule the operation of multiple pump installations with rotation of the duty pump, ensuring maximum service life and system efficiency.
ELECTRIC FURNACE
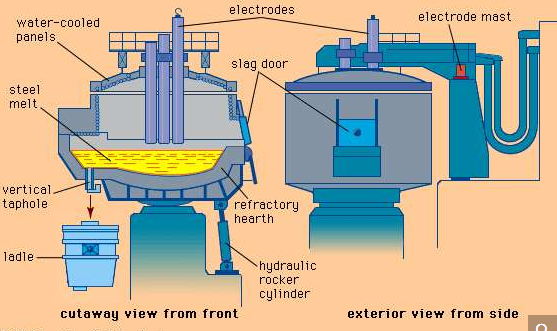
Electric furnace, heating chamber with electricity as the heat source for achieving very high temperatures to melt and alloy metals and refectories. The electricity has no electrochemical effect on the metal but simply heats it.
Modern electric furnaces generally are either arc furnaces or induction furnaces. A third type, the resistance furnace, is still used in the production of silicon carbide and electrolytic aluminum; in this type, the furnace charge (i.e., the material to be heated) serves as the resistance element. In one type of resistance furnace, the heat-producing current is introduced by electrodes buried in the metal. Heat also may be produced by resistance elements lining the interior of the furnace.
Electric furnaces produce roughly two-fifths of the steel made in the United States. They are used by specialty steelmakers to produce almost all the stainless steels, electrical steels, tool steels, and special alloys required by the chemical, automotive, aircraft, machine-tool, transportation, and food-processing industries. Electric furnaces also are employed, exclusively, by mini-mills, small plants using scrap charges to produce reinforcing bars, merchant bars (e.g., angles and channels), and structural sections.
OVENS/MICROWAVE OVEN
- To conserve energy while using ovens we should keep in mind the following
- We should use microwaves as they consume 50% less energy than conventional ovens.
- The oven door should not have any cracks or tears in it.
- We should use “lids-on” cooking to permit temperature over heating.
- Keep reflector pans beneath stove top heating elements bright and clear.
- Carefully measure water used for cooking to avoid having to heat needed.
- Begin cooking on highest heat until liquid begins to boil. Then lower the settings and allow food to simmer until fully cooked.
- One should cook as much of the meal in the oven at one time as possible.
- Rearrange oven shelves before turning your oven on and do not peep in oven. Every time the oven is opened temperature is lowered by 4° - 5°C.
- When preheating an oven for baking, time the pre-heat period carefully, minutes should be sufficient.
BOILER
A boiler is an enclosed vessel that provides a means for combustion heat to be transferred into water until it becomes heated water or steam. The hot water or steam under pressure is then usable for transferring the heat to a process. Heat is transferred from one body to another by means of:
- Radiation
- Convection
- Conduction
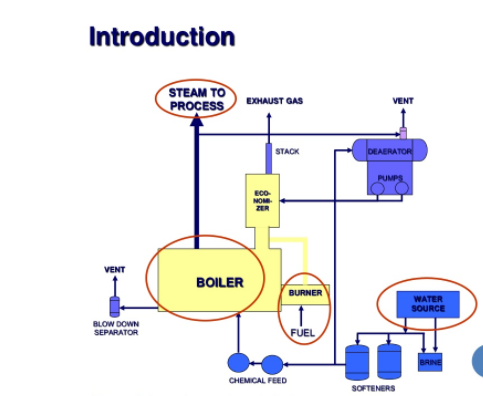
The boiler system comprises of feed water system steam system and fuel system. The feed water system provides water to the boiler and regulates it automatically to meet the steam demand. Various valves provide access for maintenance and repair. The steam system collects and controls the steam produced in the boiler. Steam is directed through a piping system to the point of use.
Energy Efficient Lighting
- High Energy Bills
- Significant growth in Energy Demand
- Environmental Problems
- Lighting is a most visible form of Electricity Consumption
- Exhaustion of Electricity Generation Sources
- Lighting energy consumption
- 20-45% in commercial buildings
- 3-10% in industrial plants
- More Light from Less Power
Compact Fluorescent Lamp (CFL)
- CFL is a compact variant of the fluorescent lamp.
- The overall length is shortened & luminous efficacy is about four times higher than that of incandescent lamps
- It is possible to save energy and costs in lighting by replacing incandescent lamps with CFLs.
Induction Lighting
- Benefits & Features
- Longer Life Span
- High Energy Conservation
- High Power Factor
- Low Maintenance Problems
- Minimum Lumen Depreciation
- Instant On and Off
- Environmental Friendly
LED Lighting
- Benefits & Features
- Cycling
- Dimming
- Energy Savings
- Size and Focus
- Green Product – No Harm Emissions
- Long Life
- Lower Temperatures
- Shock Resistance
Reference Books
- Environmental pollution and Control by Ruth Weiner et al
- Environmental Pollution Control Engineering by C S Rao
3. Environmental Engineering-1 by H.S Vishwanath et al