Unit II
Water Technology
Content
Hardness can be defined as a soap consuming capacity of water sample. Soaps are sodium salts of fatty acids like oleic acid, palmetic acid and stearic acid. They dissolve readily .in water to form lather due to which it has cleansing property.
- But compounds of fatty acids with other metals done dissolve in water.
- If water contains other metal ions like calcium and magnesium ions they react with sodium salts of long chain fatty acids to form in soluble soap which we observe as curd.
2
(calciumstearate)
- If water contains other metal ions like calcium and magnesium ions they react with sodium salts of long chain fatty acids to form in soluble soap which we observe as curd
- These other metal ions are responsible for the hardness of water most important metal of ions which cause hardness to water are calcium and magnesium ions.
- The hardness of water along can be calculated from the amount of calcium and magnesium ions present in water along with bicarbonates, sulphates chlorides and nitrates.
TYPES OF WATER | HARDNESS |
Soft | 0 – 75 |
Moderately hard | 75 – 150 |
Hard | 150 – 300 |
Very hard | Above 300 |
Underground Water: Underground water consists of that water level that is present under the earth which has been absorbed by the surface level of the earth.
Surface Water: Rain water is one of the purest forms of natural water present on the surface of the earth while sea water is the most impure form of the water. Rivers join sea and throw in the impurities carried by them.
The impurities of water are filtered from the drinking water to make the water pure for drink. The types of impurities in water can include dust, dirt, harmful chemicals, biological contaminants, radiological contaminants, and total suspended solids (TSS). Total suspended solids are visible particles that can make water appear cloudy or hazy.
| Concentration found in Ground Water | Concentration found in surface water |
Total Hardness | 300 – 400 ppm | 75 – 200 ppm |
Alkalinity | 250 – 350 ppm | 45 – 250 ppm |
Dissolved Oxygen | Near 0 | 2 – 14 ppm |
CO2 | 1 – 10 ppm | Low |
Calcium Hardness | High | Usually low |
Magnesium Hardness | Tends to be high | Usually low |
Hard water: is water that contains an required quantity of dissolved minerals (like calcium and magnesium) As rainwater falls, it is naturally soft. However, as water flows through the ground and into waterways, it picks up minerals like chalk, lime and mostly calcium and magnesium and becomes hard water. Since hard water contains essential minerals, it is essentially used as drinking water. Not only because of the health benefits, but also the flavour. Water that does not produce lather with soap readily is called hard water. Water hardness is usually measured as calcium hardness in milligrams per litre (mg/l) OR parts per million (ppm) OR in grains per gallon (GPG).
For eg: sea water, river water, spring water, lake water and well water.
Types of hardness: -
- Temporary hardness ( carbonate) :-
- When water containing calcium and magnesium bicarbonates is heated , bicarbonate decompose and from insoluble carbonate and form hydroxide.
- On filtering such water , soft water is obtained.
- The hardness which can be removed by more boiling is referred as ‘temporary hardness ’ or bicarbonate hardness.

Ca
Mg Mg
+ 2 CO
(Bicarbonates)
II. Permanent hardness :-
- The term permanent hardness ornon carbonate is the term applied to the hardness caused by dissolved chlorides , nitrates and sulphate of calcium and magnesium.
- This cannot be removed by boiling the water sample.
- Sum of temporary and permanent hardness is referred to as total hardness.
III. Alkaline or carbonate and non – alkaline or non – carbonate hardness :-
- Like all carbonate and bicarbonate , calcium and magnesium carbonate and bicarbonate are alkaline.
- Then hardness due to the carbonate and bicarbonate is called alkaline hardness or carbonate hardness.
- The alkalinity can be measures by titration with standard mineral acid using methyl orange and or phenol phthalein as an indicator.
4. As the sulphate and chloride are neutral salts , the hardness caused by presence of calcium and magnesium sulphate , chlorides and nitrates is termed as non alkaline hardness or non carbonate hardness.
IV. Total hardness :-
The hardness due to all hardness causing salts , known as total hardness.
Total hardness = temporary + permanent
Estimation of hardness :-
Hardness of weather can be determined by two methods.
1) Soap solution method :-
- Total hardness of water can be determined by titrating a fixed volume of water sample (100ml) against standard alcoholic soap solution.
- Appearance of stable lather which persists for two minutes is the end point of titration.
- In the beginning sodium soap will precipitate all the hardness causing metal ions in the form of their soap (card) and then it will form free lather.
- If same water sample is boiled for 30minutes and then titrated against same soap solution the titration reading corresponds to permanent hardness.
The difference between two measurements corresponds to the temporary hardness of water.
Estimation of hardness of water by complexometric method:
Complexometric titration is a form of volumetric analysis in which the formation of a colored complex is used to indicate the end point of a titration. Complexometric titrations are particularly useful for the determination of a mixture of different metal ions in solution. An indicator capable of producing an unambiguous color change is used to detect the end-point of the titration. Complexometric titration are those reactions where a simple ion is transformed into a complex ion and the equivalence point is determined by using metal indicators or electrometrically.
- The reaction reaches equilibrium rapidly after each portion of titration is added.
- Interfering situations do not arise.
- A complexometric indicator capable of locating equivalence point with fair accuracy is available.
Titration with EDTA
EDTA(Ethylene Diamine Tetra Acetic Acid) , has four carboxyl groups and two amine groups that can act as electron pair donors. The ability of EDTA to potentially donate its six lone pairs of electrons for the formation of coordinate covalent bonds to metal cations makes EDTA a hexadentate ligand. However, in practice EDTA is usually only partially ionized, and thus forms fewer than six coordinate covalent bonds with metal cations.
Disodium EDTA is commonly used to standardize aqueous solutions of transition metal cations. Disodium EDTA (often written as Na2H2Y) only forms four coordinate covalent bonds to metal cations at pH values ≤ 12. In this pH range, the amine groups remain protonated and thus unable to donate electrons to the formation of coordinate covalent bonds. Note that the shorthand form Na4−xHxY can be used to represent any species of EDTA, with x designating the number of acidic protons bonded to the EDTA molecule.
EDTA forms an octahedral complex with most 2+ metal cations, M2+, in aqueous solution. The main reason that EDTA is used so extensively in the standardization of metal cation solutions is that the formation constant for most metal cation-EDTA complexes is very high, meaning that the equilibrium for the reaction:
M2+ + H4Y → MH2Y + 2H+
Lies far to the right. Carrying out the reaction in a basic buffer solution removes H+ as it is formed, which also favors the formation of the EDTA-metal cation complex reaction product. For most purposes it can be considered that the formation of the metal cation-EDTA complex goes to completion, and this is chiefly why EDTA is used in titrations and standardizations of this type.
Determination of hardness of water by EDTA method:
Principle: This is a complex metric method. It is in the form of its sodium salt which yields the anion and this forms complex with Ca+2 and Mg+2 ions.
(Molecular Wt. - 372.24, Equivalent Wt. - 186.14 i.e., M=2N)
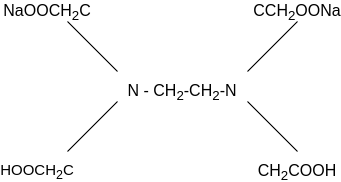
In order to determine the equivalence point (i.e., just completion of metal-EDTA complex formation) indicator Eriochrome Black-T (EBT) an alcoholic solution of blue dye is employed which forms an unstable wine red complex with Ca+2 and Mg+2 ions. The indicator is effective at about pH 10. When EBT is added to hard water, buffered to a pH of about 10 (employing NH4OH-NH4Cl buffer), a wine red unstable complex is formed. Thus,

During the course of titration against EDTA solution, EDTA combines with M+2 (or Ca+2 or Mg+2) ions from stable complex M-EDTA and releasing free EBT, which instantaneously combines with M+2 ions still present in the solution, thereby wine red color is retained. Thus, titration

When nearly all M+2 (Ca+2 or Mg+2) ions have formed [M-EDTA] complex, then next drop of EDTA added drop wise displace the EBT indicator from [M-EBT] complex and wine red color changes to blue color (due to EBT). Thus at equivalence point

Steps involved:
1. Preparation of Standard Hard Water: Dissolve 1gm of pure dry CaCO3 in minimum quantity of dil. HCl and then evaporate the solution to dryness on water bath. Dissolve the residue n distilled water to make 1L solution. Each 1ml of this solution contains 1mg of CaCO3 hardness. 6
2. Standardization of EDTA solution: Rinse and fill the burette with EDTA solution. Pipette out 50ml of standard hard water in a conical flask. Add 10-15ml of buffer solution and 4 drops of indicator. Titrate with EDTA solution till wine red color changes to clear blue. Let the volume used be V1ml.
3. Titration of Unknown Hard Water: Titrate 50ml of water sample just in step5. Let the volume used be V2ml.
4. Titration of Permanent Hardness: Take 250ml of water sample in a large beaker. Boil till the volume is reduced to about 50ml (all the bicarbonates are decomposed into insoluble CaCO3+Mg(OH)2). Filter, wash the precipitate with distilled water collecting filtrate and washings in a 250 ml measuring flask. Finally make up the volume to 250ml with distilled water.
The water that is fed into the boiler for the production of steam is called boiler feed water. The fed water into the boiler must be free from turbidity, free from oil, alkalis and most important things the hardness causing substances. The used water are contaminated in maximum time. If the hard water is used then it leads to 4 major problems that are-
- Scale & Sludge Formation
- Primming and Foaming
- Caustic Embrittlement
- Boiler Corrosion
Scale & Sludge Formation: The water evaporates continuously and the dissolved salts concentration increases progressively. When their concentrations reach at saturation point, they are thrown out of water in precipitate form which get stick in inner walls of boiler. If the precipitation takes place in the form of loose or slimy precipitate it is called sludge. While if the precipitated matter forms a hard adhering coating on inner walls of boiler, then it is called as scale. Eg- MgCO3, MgCl2, MgSO4 etc.
Priming & Foaming: The duration at which boiler is producing steam rapidly, some particles of the condensed liquid are carried along with the steam. The process of wet steam formation is called priming. Priming is mainly caused by the presence of large amounts of dissolved solids, high steam velocities,sudden boiling etc. Whereas the continuous production of foam or bubbles in boilers which do not break easily are called as the foaming. This is caused due to the presence of substance like oils in water that reduce the surface tension in water.
Caustic Embrittelment: The use of high alkaline water in the boiler cause rust in the boiler which is called as Caustic Embrittelment. The presence of sodium carbonate plays a major role during the softening process.
Na2CO3 + H2O → NaOH + CO2
the caustic embrittelment is caused by using sodium phosphate as a softening agent instead of sodium carbonate.
Boiler Corrosion: The decay of the boiler material by attack of chemicals or electro-chemicals at its environment is called as boiler corrosion.
Reasons of boiler corrosion:
(i) Dissolved Oxygen
(ii) Dissolved Carbon di oxide
(iii) Acid from dissolved salts
Sludge, scale, priming and foaming, caustic embrittlement, boiler corrosion are collectively known as boiler troubles.
Boiler feed water treatment
Makeup water intake
The water replacing evaporated or leaked water from the boiler, is first drawn from its source, whether raw water, city water, city-treated effluent, in-plant wastewater recycle, well water, or any other surface water source.
Coagulation and chemical precipitation
After all the large objects are removed from the original water source, various chemicals are added to a reaction tank to remove the bulk suspended solids and other various contaminants. This process starts off with an assortment of mixing reactors, typically one or two reactors that add specific chemicals to take out all the finer particles in the water by combining them into heavier particles that settle out. The most widely used coagulates are aluminum-based such as polyaluminum chloride.
Filtration and ultrafiltration
The next step is generally running through some type of filtration to remove any suspended particles such as sediment, turbidity, and certain types of organic matter. It is often useful to do this early on in the process, as the removal of suspended solids upstream can help protect membranes and ion exchange resins from fouling later on in the pretreatment process. Depending on the type of filtration used, suspended particles can be removed down to under one micron.
Ion exchange softening
When pre-treating boiler feed water, if there’s high hardness complex with bicarbonates, sulphate, chlorides, or nitrates, a softening resin can be used. This procedure uses a strong acid cation exchange process, whereby resin is charged with a sodium ion, and as the hardness comes through, it has a higher affinity for calcium, magnesium, and iron so it will grab that molecule and release the sodium molecule into the water.
Dealkalization
After the softening process, some boiler feed water treatment systems will utilize dealkalization to reduce pH, an impurity in boiler feed water that can cause foaming, corrosion, and embrittlement. Sodium chloride dealkalization uses a strong anion exchange resin to replace bicarbonate, sulfate, and nitrate for chloride anions. Although it doesn’t remove alkalinity 100%, it does remove the majority of it with what can be an easy-to-implement and economical process. Weak acid dealkalization only removes cations bound to bicarbonate, converting it to carbon dioxide (and therefore requiring degasification). It is a partial softening process that is also economical for adjusting the boiler feed water pH.
Reverse osmosis (RO) and nanofiltration (NF)
Reverse osmosis (RO) and nanofiltration (NF) are often used down the line in the boiler feed water treatment system process so most of the harmful impurities that can foul and clog the RO/NF membranes have been removed. Similar processes of separation, they both force pressurized water through semipermeable membranes, trapping contaminants such as bacteria, salts, organics, silica, and hardness, while allowing concentrated, purified water through. Not always required in boiler feed water treatment, these filtration units are used mostly with high-pressure boilers where concentration of suspended and dissolved solids needs to be extremely low.
Deaeration or degasification
At this point in the boiler feed water treatment process, any condensate being returned to the system will mix with the treated makeup water and enter the deaeration or degasification process. Any amount of gasses such as oxygen and carbon dioxide can be extremely corrosive to boiler equipment and piping when they attach to them, forming oxides and causing rust. Therefore, removing these gases to acceptable levels (nearly 100%) can be imperative to the service life and safety of the boiler system. There are several types of deaeration devices that come in a range of configurations depending on the manufacturer, but generally, you might use a tray- or spray-type deaerator for degasification or oxygen scavengers.
Distribution
After the boiler feed water has been sufficiently purified according to the boiler manufacturer’s recommendation and other industry-wide regulations, the water is fed to the boiler where it is heated and used to generate steam. Pure steam is used in the facility, steam and condensate are lost, and condensate return is pumped back into the process to meet up with the pretreated makeup water to cycle through pretreatment again.
Ion exchange or de ionization or de mineralization ion exchange resins are insoluble cross linked long chain organic polymers with a microporous structure and the functional group attached to the chains are responsible for the ion exchange properties resins contaning acidic function groups are capable of exchaning their anions with other anions which comes in their contact the ion exchange resins may be classified as :-
Cation exchange resins ( RH+) :-
They are mainly styrene divinly benzene co-polymers which on sulphonation or carbonoxylation become capable to exchange their hydrogen ions with the cations in the water.

- Anion exchange resins :-
They are styrene – divinly benzene or amine fermaldehyde which contain amino or quaternary ammonium or4 quaternary phosphonium or tertiary sulphonium group as an integral part of the resin matrix.these after treatment with dilute NaOH solution become capable to exchange their OH- anions with anions in water .
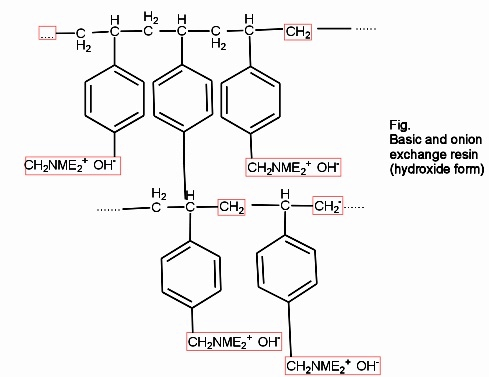
Processes :-
The hard water is passed first through cation exchange column which removes all the cations like Ca²+ , Mg² + e.t.c . From it and equivalent amount of H+ ions are released from this column Water
2RH+ + Ca².+ ---------------------- R2Ca2+ + 2H
2RH+ Mg2+ --------------------------- R2Mg2+ 2H+
After cation exchange column the hard water passed through anion like cl- . Present in the water and equivalent amount of OH- ions are released from this column to water,
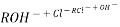


H+ And OH – ions ( released from cation exchange and anion exchange columns respectively ) get combined to produce water molecule.
H+ + OH - H2O
Thus,
The water coming out form the exchanger is free from cations as well as an ions . Ion free water is known as de mineralizes water.
Regeneration :-
When capacities of cation and anion exchangers to exchange H+ and OH- ions respectively . Are lost they are then said to be exhausted.
The exhausted cation exchange column is regenerated by passing a solution of dil.HclH2SO4. The regeneration can be represented as
( washing )
The column is washed with deionized water and washing ( which contains Ca2+ and Cl2- ions ) is passed to sink or drain.
The exhausted anion exchange column is regenerated by passing a solution of dil. NaOH.
The column is washed with de-ionized water and washing (which contains NA+ and ions ) is pass to sink or drain.
The regenerated ion exchange ion exchange resins are then used again.
Advantages :-
- The processes can be used to soften highly acidic or alkaline waters.
- It produces water of very low hardness ( say 2 ppm ) so it is very good for treating water for use in high pressure boilers.
Disadvantages :-
- The equipment is costly and more expensive chemicals are needed.
- If water contains turbidity, then the out- put of the processes is reduced .the turbidity must be below 10 ppm if it is more it has to be removed first by filtration.
Makeup water intake
The water replacing evaporated or leaked water from the boiler, is first drawn from its source, whether raw water, city water, city-treated effluent, in-plant wastewater recycle, well water, or any other surface water source.
Coagulation and chemical precipitation
After all the large objects are removed from the original water source, various chemicals are added to a reaction tank to remove the bulk suspended solids and other various contaminants. This process starts off with an assortment of mixing reactors, typically one or two reactors that add specific chemicals to take out all the finer particles in the water by combining them into heavier particles that settle out. The most widely used coagulates are aluminum-based such as polyaluminum chloride.
Filtration and ultrafiltration
The next step is generally running through some type of filtration to remove any suspended particles such as sediment, turbidity, and certain types of organic matter. It is often useful to do this early on in the process, as the removal of suspended solids upstream can help protect membranes and ion exchange resins from fouling later on in the pretreatment process. Depending on the type of filtration used, suspended particles can be removed down to under one micron.
Ion exchange softening
When pre-treating boiler feed water, if there’s high hardness complex with bicarbonates, sulphate, chlorides, or nitrates, a softening resin can be used. This procedure uses a strong acid cation exchange process, whereby resin is charged with a sodium ion, and as the hardness comes through, it has a higher affinity for calcium, magnesium, and iron so it will grab that molecule and release the sodium molecule into the water.
Dealkalization
After the softening process, some boiler feed water treatment systems will utilize dealkalization to reduce pH, an impurity in boiler feed water that can cause foaming, corrosion, and embrittlement. Sodium chloride dealkalization uses a strong anion exchange resin to replace bicarbonate, sulfate, and nitrate for chloride anions. Although it doesn’t remove alkalinity 100%, it does remove the majority of it with what can be an easy-to-implement and economical process. Weak acid dealkalization only removes cations bound to bicarbonate, converting it to carbon dioxide (and therefore requiring degasification). It is a partial softening process that is also economical for adjusting the boiler feed water pH.
Reverse osmosis (RO) and nanofiltration (NF)
Reverse osmosis (RO) and nanofiltration (NF) are often used down the line in the boiler feed water treatment system process so most of the harmful impurities that can foul and clog the RO/NF membranes have been removed. Similar processes of separation, they both force pressurized water through semipermeable membranes, trapping contaminants such as bacteria, salts, organics, silica, and hardness, while allowing concentrated, purified water through. Not always required in boiler feed water treatment, these filtration units are used mostly with high-pressure boilers where concentration of suspended and dissolved solids needs to be extremely low.
Deaeration or degasification
At this point in the boiler feed water treatment process, any condensate being returned to the system will mix with the treated makeup water and enter the deaeration or degasification process. Any amount of gasses such as oxygen and carbon dioxide can be extremely corrosive to boiler equipment and piping when they attach to them, forming oxides and causing rust. Therefore, removing these gases to acceptable levels (nearly 100%) can be imperative to the service life and safety of the boiler system. There are several types of deaeration devices that come in a range of configurations depending on the manufacturer, but generally, you might use a tray- or spray-type deaerator for degasification or oxygen scavengers.
Distribution
After the boiler feed water has been sufficiently purified according to the boiler manufacturer’s recommendation and other industry-wide regulations, the water is fed to the boiler where it is heated and used to generate steam. Pure steam is used in the facility, steam and condensate are lost, and condensate return is pumped back into the process to meet up with the pretreated makeup water to cycle through pretreatment again.
Desalination: The process of converting up of saline water into fresh water by removing of salts and minerals from the target source is called as the Desalination. Saltwater is desalinated to produce water suitable for human consumption or irrigation. The by-product of the desalination process is brine. Desalination is used on many seagoing ships and submarines. Most of the modern interest in desalination is focused on cost-effective provision of fresh water for human use. Along with recycled wastewater, it is one of the few rainfall-independent water sources.
Desalination using electro dialysis:
The passing up of direct current through the water in order to drive the ions through membranes to electrodes of opposite charge. The common techniques which applied the electro dialysis principle is electro dialysis reversal (EDR). This system uses ion transfer anion and cation membranes to separate the ions in source water. This membrane allows the unidirectional transfer of ions of given charge through them. E.g.- the cation transfer membranes allow only positive charge ions to pass.
Desalination using reverse osmosis:
Reverse osmosis is a process where the water is separated from the salts in the source water by pressure-driven transport through a membrane. This process uses semi-permeable membrane and applied pressure to preferentially induce water permeation through the membrane while rejecting salts. The RO plant uses less energy than thermal desalination process. This process uses thin-film composite membrane that too comprises of ultra thin aromatic polyamide thin film. The used polyamide film gives the transparent properties while the remaining part provides the mechanical supports. The polyamide films are very dense void free polymer with high surface area allowing for its high permeability. RO desalination plant include source water intake system, pretreatment facilities and high pressure feed pumps, RO membrane trains, energy recovery and desalinated water conditioning system. The intake system may be the open surface water intake or series of seawater beach wells. The pretreatment system may be the screening, chemical conditioning, sedimentation or filtration that totally depends on the used quality water further the filtered water is conveyed by transfer pump from filtrate water storage tank through cartridge filter and into the suction pipe of high pressure RO feed pumps. The cartridge filters are designed in such a manner that can retain 1 to 20 microns particles which remained in the source water after pretreatment. The high pressure feed pumps are designed to deliver the source water to the RO membranes at pressure required for membrane separation of the fresh water from the salts. The actual required feed pressure is site-specific and is mainly determined by the source water salinity and the configuration of the RO system.
Reference Books:
1. Engineering Chemistry by Jain and Jain, Dhanpat Rai Publishing Co.
2. Engineering Chemistry Willey India Publisher
3. Engineering Chemistry by Marry Jane & Shultz, Cencage Learning Publisher
4. Engineering Chemistry by N. Krishnamurthy, P. Vallinaygam and D. Madhavan,
Prentice Hall of India Pvt. Ltd.
5. Engineering Chemistry by K. Sesha Maheswaramma and Mridula Chugh, Pearson India Education Pvt Ltd.
6. Engineering Chemistry by B K. Sharma, Krishna Prakashan Media (P) Ltd.
7. A textbook of Engineering Chemistry by Shashi Chawla, Dhanpatrai Publishing Co. Ltd.
8. Fundamentals of Biotechnology by B D Singh, Kalyani Publisher. New Delhi.
9. Essential of Physical Chemistry by Bahl and Tuli., S Chand & Co. Ltd, New Delhi.
10. Introduction to Nano Science by N N. Lindsay, Oxford University Press.
11. NANO: The Essentials by T Pradeep Tata McGraw-Hill Publishing Company, New Delhi.