UNIT 5
Stresses and Strains
When a body is subjected to a system of external forces, it undergoes a deformation. At the same time, by virtue of its strength, it offers a resistance against this deformation. This internal resistance offered by the body to counteract the applied load is called stress.
The resistance per unit cross sectional are is called stress. The deformation in unit original dimension is termed as stain.
Types of stresses and strains
Tensile stress
When an external force produces elongation of the body in its direction, it is termed as tensile force.
P= External tensile load
R= Resistance induced in the material of the body
A=Cross sectional area
Tensile stress =Tensile load / Cross sectional are of the body
Tensile strain
Tensile strain =Increase in length/ Original length
Compressive stress
When an external force causes shortening of the body in the direction of force, it is termed as a compressive force. The stress developed in the body due to a compressive force is called as compressive stress.
P= External compressive load
R=Resistance induced in the material of the body
A=Cross sectional area of the body
Compressive Stress = compressive load/ cross sectional area of the body
Compressive strain
Compressive strain = decrease in length/ Original length
Shear stress
When a body is subjected to two equal and opposite forces acting tangentially across the resisting section, as a result of which the body tends to shear off across the section, then this tangential force is termed as shear force and the stress induced is called shear stress.
Shear stress = Shear force/ Shear area
Shear strain
Shear strain =Transverse displacement/ Distance from the fixed base
Volumetric strain
The change in volume of an elastic body due to external force in unit original volume is called as the volumetric strain
Volumetric strain = dv/V
Lateral strain
When a material is subjected to uniaxial stress within the elastic limit, it deforms not only longitudinally but also laterally. Under tension the lateral dimensions diminish and under compression they increase. The lateral deformation per unit original lateral dimension is called lateral strain.
Poisson’s ratio is “the ratio of transverse contraction strain to longitudinal extension strain in the direction of the stretching force.” Here,
- Compressive deformation is considered negative
- Tensile deformation is considered positive.
Symbol | Greek letter ‘nu’,ν |
Formula | Poisson’s ratio = – Lateral strain / Longitudinal strain |
Range | -1.0 to +0.5 |
Units | Unit less quantity |
Scalar / Vector | Scalar quantity |
Poisson’s Ratio Formula
Imagine a piece of rubber, in the usual shape of a cuboid. Then imagine pulling it along the sides. What happens now?
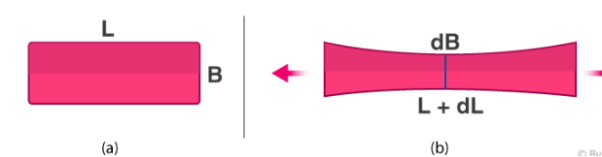
It will compress in the middle. If the original length and breadth of the rubber are taken as L and B respectively, then when pulled longitudinally, it tends to get compressed laterally. In simple words, length has increased by an amount dL and the breadth has increased by an amount dB.
In this case,
εt=−dB/B εl=−dL/L
The formula for Poisson’s ratio is,
Poisson′s ratio=Transverse strain/ Longitudinal strain
⇒ν=−εt / εl
Where,
εt is the Lateral or Transverse Strain
εl is the Longitudinal or Axial Strain
ν is the Poisson’s Ratio
The strain on its own is defined as the change in dimension (length, breadth, area…) divided by the original dimension.
Poisson Effect
When a material is stretched in one direction, it tends to compress in the direction perpendicular to that of force application and vice versa. The measure of this phenomenon is given in terms of Poisson’s ratio. For example, a rubber band tends to become thinner when stretched.
Poisson’s ratio values for different material
It is the ratio of transverse contraction strain to longitudinal extension strain, in the direction of the stretching force. There can be a stress and strain relation that is generated with the application of force on a body.
- For tensile deformation, Poisson’s ratio is positive.
- For compressive deformation, it is negative.
Here, the negative Poisson ratio suggests that the material will exhibit a positive strain in the transverse direction, even though the longitudinal strain is positive as well.
For most materials, the value of Poisson’s ratio lies in the range, 0 to 0.5.
A few examples of Poisson ratio is given below for different materials.
Material | Values |
Concrete | 0.1 – 0.2 |
Cast iron | 0.21 – 0.26 |
Steel | 0.27 – 0.30 |
Rubber | 0.4999 |
Gold | 0.42 – 0.44 |
Glass | 0.18 – 0.3 |
Cork | 0.0 |
Copper | 0.33 |
Clay | 0.30 – 0.45 |
Stainless steel | 0.30 – 0.31 |
Foam | 0.10 – 0.50 |
Stress-Strain Curve
The stress-strain relationship for materials is given by the material’s stress-strain curve. Under different loads, the stress and corresponding strain values are plotted. An example of a stress-strain curve is given below.
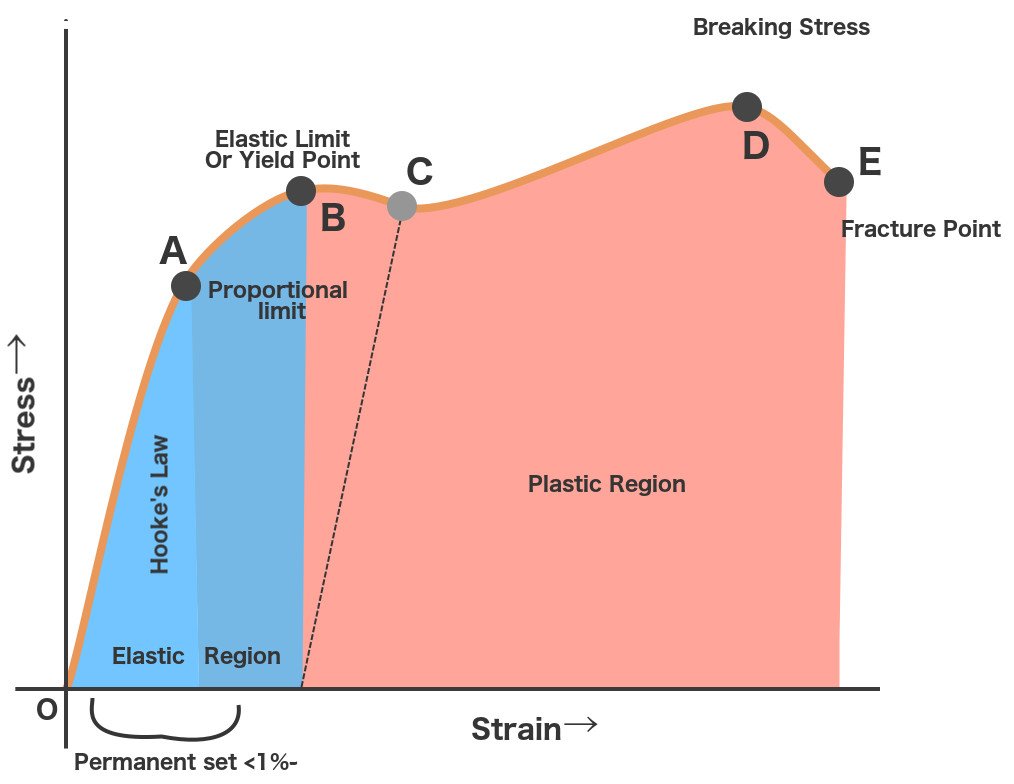
Stress-Strain Curve
Explaining Stress-Strain Graph
The stress-strain graph has different points or regions as follows:
- Proportional limit
- Elastic limit
- Yield point
- Ultimate stress point
- Fracture or breaking point
(i) Proportional Limit
It is the region in the stress-strain curve that obeys Hooke’s Law. In this limit, the ratio of stress with strain gives us proportionality constant known as young’s modulus. The point OA in the graph is called the proportional limit.
(ii) Elastic Limit
It is the point in the graph up to which the material returns to its original position when the load acting on it is completely removed. Beyond this limit, the material doesn’t return to its original position and a plastic deformation starts to appear in it.
(iii) Yield Point
The yield point is defined as the point at which the material starts to deform plastically. After the yield point is passed, permanent plastic deformation occurs. There are two yield points (i) upper yield point (ii) lower yield point.
(iv) Ultimate Stress Point
It is a point that represents the maximum stress that a material can endure before failure. Beyond this point, failure occurs.
(v) Fracture or Breaking Point
It is the point in the stress-strain curve at which the failure of the material takes place.
Hooke’s Law
In the 19th-century, while studying springs and elasticity, English scientist Robert Hooke noticed that many materials exhibited a similar property when the stress-strain relationship was studied. There was a linear region where the force required to stretch the material was proportional to the extension of the material. This is known as Hooke’s Law.
Hooke’s Law states that the strain of the material is proportional to the applied stress within the elastic limit of that material.
Mathematically, Hooke’s law is commonly expressed as:
F = –k.x
Where,
- F is the force
- x is the extension length
k is the constant of proportionality known as spring constant in N/m
Material is nothing but a matter of substance used to create a certain thing. Engineering materials are the materials used to for the application of engineering works. Based on the mechanical, physical, chemical and manufacturing properties materials are selected according to the application.
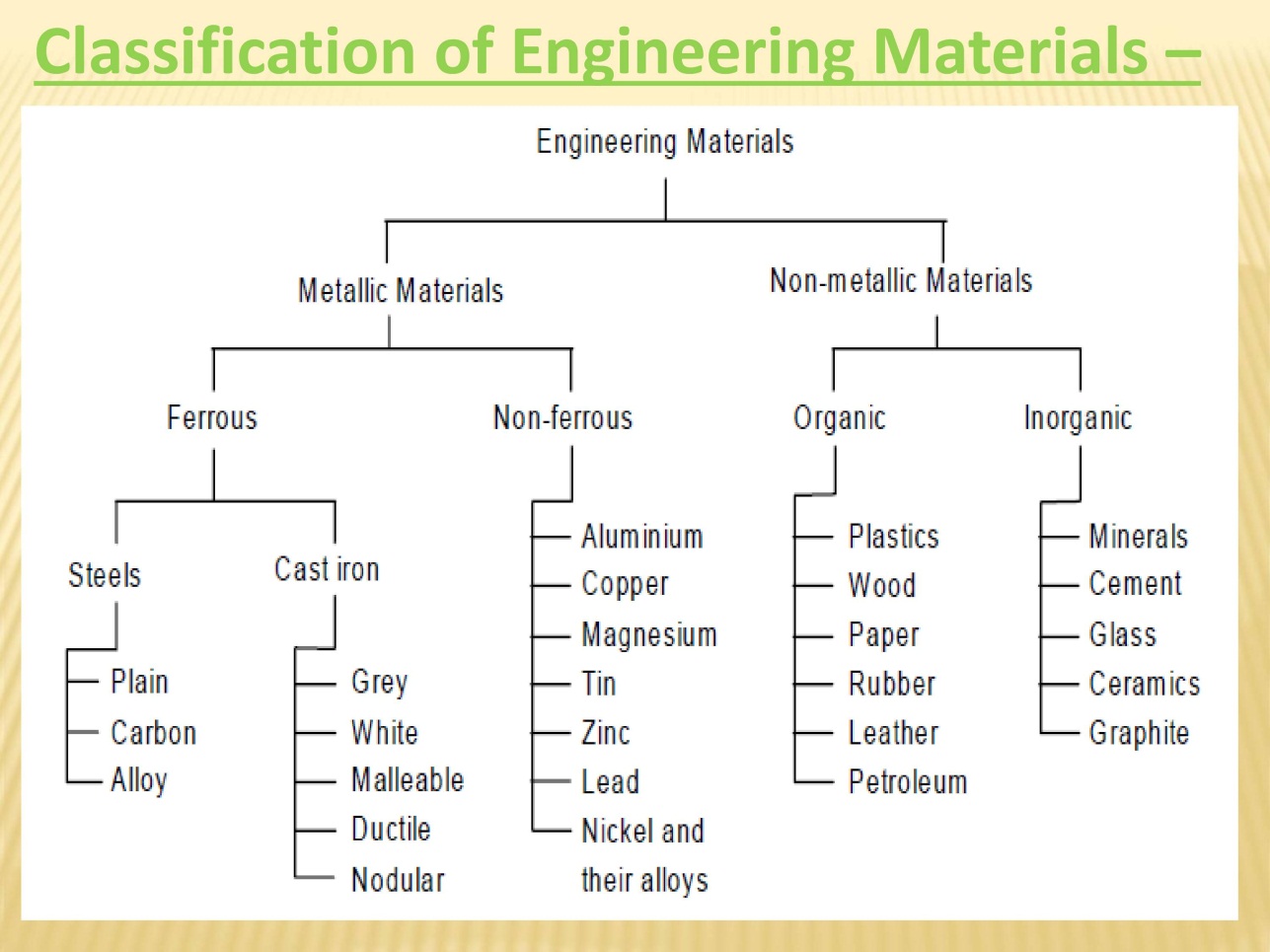
Mechanical properties of the materials are strength (compressive or tensile), toughness, stiffness, elasticity, plasticity, ductility, brittleness and hardness.
Physical properties of materials are density, conductivity (thermal or electrical), acoustical (sound transmission or absorption), optical, combustibility.
Chemical properties of materials are composition (oxide or compound), acidity or alkalinity, weathering corrosion.
Manufacturing properties of materials are castability, machinability rating, machining speeds and feeds and for dimensioning purpose shape and size.
The selection of material for the required functioning application is based on some of the following factors:
- Stresses to which the work piece or component will be subjected.
- Corrosion resistance.
- Temperature, wear and tear resistance.
- Flexibility and rigidity.
- Easiness of the manufacturing process.
- Cost effectiveness for the product development.
- Availability of the material.
Classification of Engineering Material:
Depending upon the nature of substance materials are classified as
- Metals and alloys
- Ferrous metals
- Non ferrous metals
- Non metals
- Ceramics
- Polymers
- Composites
- Semi conductors
- Bio materials
1. METALS AND ALLOYS:
Metallic materials are combination of metallic elements.
The most prominent property of metals is electrons are non localized i.e. in atomic arrangement outer valence electrons do not belong to individual atom rather it belong to whole bulk of material. Non localized electron is free to carry charge to conduct electricity. Hence they are good conductors for electrical and thermal charge.
Metals have lustrous appearance. At normal temperature majority of the materials are in solid state, but some metals like mercury lies in liquid state.
Based upon the presence of iron content metals are named as
- Ferrous metals
- Non ferrous metals
Ferrous metals:
The primary content of ferrous metals is iron and carbon. Ferrous metals are magnetic and are vulnerable to rust when exposed to moisture. Wrought iron won’t rust due to purity and stainless steel due to presence of chromium.
Eg: iron, steel, etc.
Due to their magnetic property ferrous metals are used in motor and electrical applications.
Non Ferrous Metals:
Iron is not primary content. Due to the non-presence of iron these metals have high resistance to rust and corrosion and they are nonmagnetic.
Eg: copper, brass, aluminum, tungsten, lead, zinc, gold, etc.
Alloy:
Alloy is a combination of two or more metals. It is named based on metallic bonding character. It is of two types’ ferrous metal alloy and non ferrous metal alloy. Cast iron is an alloy made from iron, carbon and silicon. Brass is an alloy of copper and zinc.
Applications:
- Due to their toughness and ability to sterilize at high temperatures metals are used as needles, surgical blades.
- Due to their strength and ability to withstand heavy weights metals like iron and steel are used in construction.
- Metals like gold, silver, platinum, etc. are used in jewellery.
- Metals are used in machines and automobiles as they can withstand high temperature, pressure and workloads.
- Aluminum and titanium play important role in light weight category for aircraft alloys.
- Tungsten is used in high temperature applications.
2. CERAMICS:
A particle or fibrous which are used in terms of making ceramic products. Ceramics have regular atomic structure and crystal structure. Ceramics are mainly oxides, nitrides and carbides. They are non conducting materials, due to its insulating property they are used as insulators. They are very hard and brittle in nature.
E.g.: alumina, silica, silicon carbide, diamond, bricks, etc.
Applications:
- Due to the compressive strength bricks are used in construction
- Because of their good thermal insulation ceramic tiles are used in ovens.
- Some ceramics are transparent to radar and other electromagnetic waves are used in radomes and transmitters.
- Glass ceramics have high temperature capabilities so they are used in optical equipment and fiber insulation.
- Alumina, silica, silicon carbide are used in making tools.
- Diamond is used in ornaments and cutting tool applications.
3. POLYMERS:
Polymers have chain molecule structure of carbon as back bone atoms. They are mainly made up of tough organic materials. They are low density materials and also flexible. In some cases polymers are not flexible.
Polymers are not only used as structural materials, they can be used as fiber and resins in the matrix of composite materials.
e.g.: polyester as fibers, phenolic and epoxides as resins.
Elastomers are also polymers but they are considered separately due to their specific design for certain purposes like shock and vibration absorption.
Natural polymers:
Eg : wool, silk, DNA, cellulose, proteins, etc.
Synthetic polymers:
- Thermo plastics
- Thermosetting plastics
Eg: nylon, polyethylene, polyester, Teflon, epoxy, Bakelite, etc.
Applications:
- Polyethylene is used for making carry bags.
- Polypropylene is used for making high temperature resistance products like feeding bottle.
- Polyether ether ketone and polyethylene ketone are used in mineral water bottle concept.
- Poly carbonate is used to make high performance polymers like transparent polymers
- Polyaniline is a conducting polymer.
- Bakelite used for making insulating materials.
4. COMPOSITE:
Composite material is the composition of two or more constituent materials with different physical and chemical properties to produce a different characteristic material.
Composite material may be both metals or metal and ceramic or metal and polymer, depending upon the application requirement the combination is made.
Eg : wood, concrete, fiber glass, CFRP (carbon fiber reinforced plastic), GFRP (glass fiber reinforced plastic), etc.
Applications:
- CFRP and GFRP are used for automotive body parts.
- CRPF and honeycomb composites are used for chassis.
- Some fuel tanks are made up of Kevlar reinforced fiber.
- Reinforced thermosets are used in springs and bumper system.
- Fiberglas reinforced plastic has been used for boat hulls, fishing rods, tennis rackets, helmets, bows and arrows.
5. SEMICONDUCTORS:
Semiconductor is an intermediate conducting material. Their conductivity is not high as like metals and low as like insulating ceramic materials. In these materials resistance decreases as their temperature increases.
The unique atomic structure allows controlling the conductivity.
Eg : silicon, germanium, gallium arsenide, selenium, etc.
Applications:
- Gallium arsenide is widely used in low noise, high gain and weak signal amplifying devices.
- A semiconductor device can perform the function of a vacuum tube having hundreds of times its volume.
6. BIO MATERIALS:
Bio materials are non-viable materials .Eg : alumina, zirconia, titanium, tantalum, niobium, carbon, etc.
Applications:
- Metals are used in medicine to cure any micronutrient metal deficiency diseases in humans and animals, like iron is a part of hemoglobin a bio molecule which can be used as ferrous sulphate to cure some forms of anemia.
- Implants in the body to repair or replace the damaged tissue.
In composite materials the name itself indicates as composite (composition), it is the composition of two or more materials. In semiconductors the name itself indicates as semi (half) and conductor (conducting) The difference between an alloy and composite is that the composite is a reinforcement of other material. Whereas alloy is a combination (mixture) of both or required number of materials in the required quantity as per the necessary product.
Both semiconductors and bio materials are substitutes in metals, ceramics and polymers in the required places
Composition of cast iron and carbon steel
CAST IRON
Cast iron is an iron alloy containing 2 wt.% – 4 wt.% carbon, 1 wt.% – 3 wt.% silicon and smaller amounts of minor elements . In comparison, steel has a lower carbon content of up to 2 wt. % and lower silicon content.
Cast iron can also be further optimized by alloying with small quantities of manganese, molybdenum, cerium, nickel, copper, vanadium and titanium before being cast. Depending on the silicon content of the cast iron, it is classified as either white cast iron or grey cast iron and may be treated further under particular temperatures to produce malleable or ductile cast iron.
General properties of cast iron
Cast iron is highly favored for its ability to be easily cast into complex shapes when molten and for its low cost. In addition, its properties can be easily altered by adjusting the composition and cooling rate without significant changes to production methods. Its other main advantages over cast steel include ease of machining, vibration dampening, compressive strength, wear resistance and corrosion resistance. Corrosion resistance of cast iron is improved via the addition of minor elements such as silicon, nickel, chromium, molybdenum and copper.
Types of cast iron and their applications
Cast iron can be classified into grey cast iron, white cast iron, malleable cast iron and ductile cast iron, depending on its composition.
i) Grey cast iron
Grey cast iron, or gray iron, has a dark grey fracture colour due to a graphitic microstructure. The presence of graphite flakes is due to the addition of silicon, which acts to stabilize carbon in the form of graphite as opposed to iron carbide. Grey cast iron typically has a composition of 2.5 wt.% – 4.0 wt.% carbon and 1.0 wt.% – 3.0 wt.% silicon.
Grey cast iron applications
Grey cast iron is the most common form of cast iron. It is used in applications where its high stiffness, machinability, vibration dampening, high heat capacity and high thermal conductivity are of advantage, such as internal combustion engine cylinder blocks, flywheels, gearbox cases, manifolds, disk brake rotors and cookware.
A commonly used classification for grey cast iron is ASTM International standard A48. Under this system, grey cast irons are graded according to their tensile strength with class 20 grey cast iron for example, having a minimum tensile strength of 20,000 psi (140 MPa).
Ii) White cast iron
White cast iron has a white fracture colour due to the presence of iron carbide, or cementite Fe3C. The presence of carbon in this form, as opposed to graphite, is the result of a lower silicon content compared to grey cast iron. White cast iron typically contains 1.8 wt.% – 3.6 wt.% carbon, 0.5 wt.% – 1.9 wt.% silicon and 1.0 wt.% – 2.0 wt.% manganese. White cast irons are extremely wear-resistant yet brittle. They exhibit high hardness as a result of their microstructure containing large iron carbide particles and are not easily machined.
White cast iron applications
White cast irons are used in abrasion-resistant parts where its brittleness is of minimum concern such as shell liners, slurry pumps, ball mills, lifter bars, extrusion nozzles, cement mixers, pipe fittings, flanges, crushers and pump impellers. A popular grade of white iron is high chrome white irons, ASTM A532. This contains nickel and chromium for good low-impact abrasion applications .
Iii) Malleable cast iron
Malleable cast irons are formed via a slow annealing heat treatment of white cast iron. This results in the conversion of carbon, in the form of iron carbide in white iron, to graphite, with the remaining matrix being composed of ferrite or pearlite. The graphite is present in the form of spherical or nodular shapes.
Malleable cast iron exhibits good malleability and good ductility. Due to the lower silicon content compared to other cast irons, it exhibits good fracture toughness at low temperature.
Malleable cast iron applications
As a result of its good tensile strength and ductility, malleable cast iron is used for electrical fittings and equipment, hand tools, pipe fittings, washers, brackets, farm equipment, mining hardware, and machine parts.
Iv) Ductile cast iron
Ductile cast iron, also known as nodular cast iron and spheroidal graphite cast iron, is defined by the presence of graphite in the form of spherical nodules, as with malleable cast iron. Differently to malleable cast iron, ductile cast iron is formed not by heat treatment of white iron, but through a specific chemical composition.
Ductile cast iron contains 3.2 wt.% – 3.6 wt.% carbon, 2.2 wt.% – 2.8 wt.% silicon and 0.1 wt.% – 0.2 wt.% manganese, as well as smaller amounts of magnesium, phosphorus, sulfur and copper. The presence of manganese is responsible for the spherical form of the graphite inclusions.
Ductile cast iron applications
Due to its microstructure, this material is more ductile than grey or white cast irons. For this reason, it is used as ductile iron pipe for water and sewage infrastructure. It can also withstand thermal cycling and is therefore used in vehicle gears and suspension components, brakes and valves, pumps and hydraulic parts, and housings for wind turbines.
Production and processing
To produce cast iron, the iron must be extracted from iron ore. The ore is smelted in a blast furnace where it separates into pig iron and slag. The furnace is heated to around 1800 degrees Celsius in an oxygen atmosphere and the slag formed rises to the top and can be removed. The molten pig iron below contains around 3 wt.% – 5 wt.% carbon. This is then combined with iron, steel, coke and limestone.
Once impurities are removed selectively from this iron, the carbon content is reduced. At this point, silicon may be added to convert the carbon content to graphite or cementite. The iron is then cast into various forms.
CARBON STEEL
Carbon steel is an iron-carbon alloy, which contains up to 2.1 wt.% carbon. For carbon steels, there is no minimum specified content of other alloying elements; however, they often contain manganese. The maximum manganese, silicon and copper content should be less than 1.65 wt. %, 0.6 wt. % and 0.6 wt. %, respectively.
Types of carbon steel and their properties
Carbon steel can be classified into three categories according to its carbon content: low-carbon steel (or mild-carbon steel), medium-carbon steel and high-carbon steel their carbon content, microstructure and properties compare as follows:
Low-carbon steel
Low-carbon steel is the most widely used form of carbon steel. These steels usually have a carbon content of less than 0.25 wt.%. They cannot be hardened by heat treatment (to form martensite) so this is usually achieved by cold work.
Carbon steels are usually relatively soft and have low strength. They do, however, have high ductility, making them excellent for machining, welding and low cost. High-strength, low-alloy steels (HSLA) are also often classified as low-carbon steels, however, also contains other elements such as copper, nickel, vanadium and molybdenum. Combined, these comprise up to 10 wt.% of the steel content. High-strength, low-alloy steels, as the name suggests, have higher strengths, which is achieved by heat treatment. They also retain ductility, making them easily formable and machinable. HSLA are more resistant to corrosion than plain low-carbon steels.
Medium-carbon steel
Medium-carbon steel has a carbon content of 0.25 – 0.60 wt. % and a manganese content of 0.60 – 1.65 wt. %. The mechanical properties of this steel are improved via heat treatment involving autenitising followed by quenching and tempering, giving them a martensitic microstructure. Heat treatment can only be performed on very thin sections, however, additional alloying elements, such as chromium, molybdenum and nickel, can be added to improve the steels ability to be heat treated and, thus, hardened. Hardened medium-carbon steels have greater strength than low-carbon steels, however, this comes at the expense of ductility and toughness.
High-carbon steel
High-carbon steel has a carbon content of 0.60– 1.25 wt.% and a manganese content of 0.30 – 0.90 wt.%. It has the highest hardness and toughness of the carbon steels and the lowest ductility. High-carbon steels are very wear-resistant as a result of the fact that they are almost always hardened and tempered.
Tool steels and die steels are types of high-carbon steels, which contain additional alloying elements including chromium, vanadium, molybdenum and tungsten. The addition of these elements results in the very hard wear-resistant steel, which is a result of the formation of carbide compounds such as tungsten carbide (WC).
Production and processing
Carbon steel can be produced from recycled steel, virgin steel or a combination of both. Virgin steel is made by combining iron ore, coke (produced by heating coal in the absence of air) and lime in a blast furnace at around 1650 °C. The molten iron extracted from the iron ore is enriched with carbon from the burning coke. The remaining impurities combine with the lime to form slag, which floats on top of the molten metal where it can be extracted.
The resulting molten steel contains roughly 4 wt.% carbon. This carbon content is then reduced to the desired amount in a process called decarburization. This is achieved by passing oxygen through the melt, which oxidizes the carbon in the steel, producing carbon monoxide and carbon dioxide.
Carbon content (wt.%) | Microstructure | Properties | Examples | |
Low-carbon steel | < 0.25 | Ferrite, pearlite | Low hardness and cost. High ductility, toughness, machinability and weldability | AISI 304, ASTM A815, AISI 316L |
Medium-carbon steel | 0.25 – 0.60 | Martensite | Low hardenability, medium strength, ductility and toughness | AISI 409, ASTM A29, SCM435 |
High-carbon steel | 0.60 – 1.25 | Pearlite | High hardness, strength, low ductility | AISI 440C, EN 10088-3 |
Examples & Applications
Low-carbon steel
Low carbon steels are often used in automobile body components, structural shapes (I-beams, channel and angle iron), pipes, construction and bridge components, and food cans.
Medium-carbon steel
As a result of their high strength, resistance to wear and toughness, medium-carbon steels are often used for railway tracks, train wheels, crankshafts, and gears and machinery parts requiring this combination of properties.
High-carbon steel
Due to their high wear-resistance and hardness, high-carbon steels are used in cutting tools, springs high strength wire and dies.