UNIT 2
Water and its treatment
Hardness can be defined as a soap consuming capacity of water sample. Soaps are sodium salts of fatty acids like oleic acid, palmitic acid and stearic acid. They dissolve readily .in water to form lather due to which it has cleansing property.
- But compounds of fatty acids with other metals done dissolve in water.
- If water contains other metal ions like calcium and magnesium ions they react with sodium salts of long chain fatty acids to form in soluble soap which we observe as curd.
2
(calcium stearate)
- If water contains other metal ions like calcium and magnesium ions they react with sodium salts of long chain fatty acids to form in soluble soap which we observe as curd
- These other metal ions are responsible for the hardness of water most important metal of ions which cause hardness to water are calcium and magnesium ions.
- The hardness of water along can be calculated from the amount of calcium and magnesium ions present in water along with bicarbonates, sulphates chlorides and nitrates.
TYPES OF WATER | HARDNESS |
Soft | 0 – 75 |
Moderately hard | 75 – 150 |
Hard | 150 – 300 |
Very hard | Above 300 |
Types of hardness: -
- Temporary hardness ( carbonate) :-
- When water containing calcium and magnesium bicarbonates is heated, bicarbonate decompose and from insoluble carbonate and form hydroxide.
- On filtering such water, soft water is obtained.
- The hardness which can be removed by more boiling is referred as ‘temporary hardness’ or bicarbonate hardness.

Ca

Mg Mg
+ 2 CO
(Bicarbonates)
II. Permanent hardness :-
- The term permanent hardness or non-carbonate is the term applied to the hardness caused by dissolved chlorides, nitrates and sulphate of calcium and magnesium.
- This cannot be removed by boiling the water sample.
- Sum of temporary and permanent hardness is referred to as total hardness.
III. Alkaline or carbonate and non – alkaline or non – carbonate hardness :-
- Like all carbonate and bicarbonate, calcium and magnesium carbonate and bicarbonate are alkaline.
- Then hardness due to the carbonate and bicarbonate is called alkaline hardness or carbonate hardness.
- The alkalinity can be measures by titration with standard mineral acid using methyl orange and or phenol phthalein as an indicator.
4. As the sulphate and chloride are neutral salts, the hardness caused by presence of calcium and magnesium sulphate, chlorides and nitrates are termed as non-alkaline hardness or non-carbonate hardness.
IV. Total hardness: -
The hardness due to all hardness causing salts, known as total hardness.
Total hardness = temporary + permanent
Estimation of hardness: -
Hardness of weather can be determined by two methods.
1) Soap solution method :-
- Total hardness of water can be determined by titrating a fixed volume of water sample (100ml) against standard alcoholic soap solution.
- Appearance of stable lather which persists for two minutes is the end point of titration.
- In the beginning sodium soap will precipitate all the hardness causing metal ions in the form of their soap (card) and then it will form free lather.
- If same water sample is boiled for 30minutes and then titrated against same soap solution the titration reading corresponds to permanent hardness.
The difference between two measurements corresponds to the temporary hardness of water.
Estimation of hardness of water by complexometric method:
Complexometric titration is a form of volumetric analysis in which the formation of a colored complex is used to indicate the end point of a titration. Complexometric titrations are particularly useful for the determination of a mixture of different metal ions in solution. An indicator capable of producing an unambiguous color change is used to detect the end-point of the titration. Complexometric titration are those reactions where a simple ion is transformed into a complex ion and the equivalence point is determined by using metal indicators or electrometrically.
- The reaction reaches equilibrium rapidly after each portion of titration is added.
- Interfering situations do not arise.
- A complexometric indicator capable of locating equivalence point with fair accuracy is available.
Titration with EDTA
EDTA (Ethylene Diamine Tetra Acetic Acid), has four carboxyl groups and two amine groups that can act as electron pair donors. The ability of EDTA to potentially donate its six lone pairs of electrons for the formation of coordinate covalent bonds to metal cations makes EDTA a hexadentate ligand. However, in practice EDTA is usually only partially ionized, and thus forms fewer than six coordinate covalent bonds with metal cations.
Disodium EDTA is commonly used to standardize aqueous solutions of transition metal cations. Disodium EDTA (often written as Na2H2Y) only forms four coordinate covalent bonds to metal cations at pH values ≤ 12. In this pH range, the amine groups remain protonated and thus unable to donate electrons to the formation of coordinate covalent bonds. Note that the shorthand form Na4−xHxY can be used to represent any species of EDTA, with x designating the number of acidic protons bonded to the EDTA molecule.
EDTA forms an octahedral complex with most 2+ metal cations, M2+, in aqueous solution. The main reason that EDTA is used so extensively in the standardization of metal cation solutions is that the formation constant for most metal cation-EDTA complexes is very high, meaning that the equilibrium for the reaction:
M2+ + H4Y → MH2Y + 2H+
Lies far to the right. Carrying out the reaction in a basic buffer solution removes H+ as it is formed, which also favors the formation of the EDTA-metal cation complex reaction product. For most purposes it can be considered that the formation of the metal cation-EDTA complex goes to completion, and this is chiefly why EDTA is used in titrations and standardizations of this type.
“Potable water” simply means water that is safe to drink, and it is becoming scarcer in the world. Increasing use is stressing freshwater resources worldwide, and a seemingly endless list of contaminants can turn once potable water into a health hazard or simply make it unacceptable aesthetically.
Of the more than 2 billion people who lack potable water at home, 844 million don’t have even basic drinking water service, including 263 million who must travel 30 minutes per trip to collect water. Unsafe drinking water is a major cause of diarrheal disease, which kills about 800,000 children under the age of 5 a year, usually in developing countries, but 90 countries are expected to fail to reach the goal of universal coverage by 2030. Physical requirement of potable water are-
S.No. | Characteristics | Treated Potable Water | Natural Potable Water | Method of Test |
1 | Color | 15 | 50 | ISO7887 |
2 | Turbidity | 5 | 25 | ISO7027 |
3 | PH | 6.5-8.5 | 5.5-9.5 | ISO10523 |
4 | Taste | - | - | - |
5 | Odor | Odorless | Odorless | - |
6 | Conductivity | 1500 | 2500 | ISO7888 |
7 | Suspended Matter | Non-deductable | Non-deductable | ISO11923 |
Drinking water are contaminated and hence it requires the appropriate treatment to remove the disease-causing agents. There are several measures taken in consideration for the treatment of water. The most common treatment methods used by community water system include:
Coagulation & Flocculation
Water is contaminated with several type of impurities, dirt with other dissolved impurities. Chemicals with the positive charged ions are added to the water to neutralize the negative charges of the dirt, impurities etc. When this occurs, the particles bind with the chemical and form larger particles known as floc.
Sedimentation
In this process floc settles to the bottom of the water supply due to its weight. This settling process is called as the sedimentation.
Filtration
When the floc settles at the bottom of the water supply, the clear water will pass on top through filters of varying composition and pore sizes, in order to remove dissolved particles such as dust, parasites, bacteria, viruses and chemicals.
Disinfection
After the filtration the disinfectant is added in order to kill any remaining parasites, bacteria, viruses and to protect the water from germs when it is piped to houses.
Disinfection of water by chlorination and ozonization
Ozonization
Ozone consist of three oxygen atoms that is unstable gas, this ozone gas converted into oxygen by loss of its 1 oxygen atom the free radical formed is highly reactive and very short lived. Ozone is colorless. Ozone has greater disinfection effectiveness against bacteria and viruses with comparison to the chlorination.
Ozone Process
The formation of oxygen into ozone occurs with the use of energy. This process is carried out by an electric discharge field as in the CD-type ozone generators, by ultraviolet radiation as in UV-type ozone generators. In addition to these commercial methods, ozone may also be made through electrolytic and chemical reactions. In general, an ozonation system includes passing dry, clean air through a high voltage electric discharge, i.e., corona discharge, which creates and ozone concentration of approximately 1%. In treating small quantities of waste, the UV ozonation is the most common while large-scale systems use either corona discharge or other bulk ozone-producing methods. Ozoner test strips a must.
The raw water is then passed through a venturi throat which creates a vacuum and pulls the ozone gas into the water or the air is then bubbled up through the water being treated. Since the ozone will react with metals to create insoluble metal oxides, post filtration is required.
Chlorination:
Chlorination is the process of adding chlorine to drinking water to disinfect it and kill germs. Different processes can be used to achieve safe levels of chlorine in drinking water. Chlorine is available as compressed elemental gas, sodium hypochlorite solution (NaOCl) or solid calcium hypochlorite (Ca(OCl)2). While the chemicals could be harmful in high doses, when they are added to water, they all mix in and spread out, resulting in low levels that kills germs but are still safe to drink. Chlorine combines with dissolved chemicals of water, micro-organisms. It is important to add sufficient amount of chlorine to the water to meet the chlorine demand and provide residual disinfection. The chlorine that does not combine with other components in the water is free chlorine, and the breakpoint is the point at which free chlorine is available for continuous disinfection. An ideal system supplies free chlorine at a concentration of 0.3-0.5 mg/l. Simple test kits, most commonly the DPD colorimetric test kit (so called because diethyl phenylene diamine produces the color reaction), are available for testing breakpoint and chlorine residual in private systems. The kit must test free chlorine, not total chlorine.
The water that is fed into the boiler for the production of steam is called boiler feed water. The fed water into the boiler must be free from turbidity, free from oil, alkalis and most important things the hardness causing substances. The used water is contaminated in maximum time. If the hard water is used then it leads to 4 major problems that are-
- Scale & Sludge Formation
- Primming and Foaming
- Caustic Embrittlement
- Boiler Corrosion
Scale & Sludge Formation: The water evaporates continuously and the dissolved salts concentration increases progressively. When their concentrations reach at saturation point, they are thrown out of water in precipitate form which get stick in inner walls of boiler. If the precipitation takes place in the form of loose or slimy precipitate it is called sludge. While if the precipitated matter forms a hard adhering coating on inner walls of boiler, then it is called as scale. E.g.- MgCO3, MgCl2, MgSO4 etc.
Priming & Foaming: The duration at which boiler is producing steam rapidly, some particles of the condensed liquid are carried along with the steam. The process of wet steam formation is called priming. Priming is mainly caused by the presence of large amounts of dissolved solids, high steam velocities, sudden boiling etc. Whereas the continuous production of foam or bubbles in boilers which do not break easily are called as the foaming. This is caused due to the presence of substance like oils in water that reduce the surface tension in water.
Caustic Embrittlement: The use of high alkaline water in the boiler cause rust in the boiler which is called as Caustic Embrittlement. The presence of sodium carbonate plays a major role during the softening process.
Na2CO3 + H2O → NaOH + CO2
the caustic embrittlement is caused by using sodium phosphate as a softening agent instead of sodium carbonate.
Boiler Corrosion: The decay of the boiler material by attack of chemicals or electro-chemicals at its environment is called as boiler corrosion.
Reasons of boiler corrosion:
(i) Dissolved Oxygen
(ii) Dissolved Carbon di oxide
(iii) Acid from dissolved salts
Sludge, scale, priming and foaming, caustic embrittlement, boiler corrosion are collectively known as boiler troubles.
Boiler feed water treatment
Makeup water intake
The water replacing evaporated or leaked water from the boiler, is first drawn from its source, whether raw water, city water, city-treated effluent, in-plant wastewater recycle, well water, or any other surface water source.
Coagulation and chemical precipitation
After all the large objects are removed from the original water source, various chemicals are added to a reaction tank to remove the bulk suspended solids and other various contaminants. This process starts off with an assortment of mixing reactors, typically one or two reactors that add specific chemicals to take out all the finer particles in the water by combining them into heavier particles that settle out. The most widely used coagulates are aluminum-based such as polyaluminum chloride.
Filtration and ultrafiltration
The next step is generally running through some type of filtration to remove any suspended particles such as sediment, turbidity, and certain types of organic matter. It is often useful to do this early on in the process, as the removal of suspended solids upstream can help protect membranes and ion exchange resins from fouling later on in the pretreatment process. Depending on the type of filtration used, suspended particles can be removed down to under one micron.
Ion exchange softening
When pre-treating boiler feed water, if there’s high hardness complex with bicarbonates, sulphate, chlorides, or nitrates, a softening resin can be used. This procedure uses a strong acid cation exchange process, whereby resin is charged with a sodium ion, and as the hardness comes through, it has a higher affinity for calcium, magnesium, and iron so it will grab that molecule and release the sodium molecule into the water.
Dealkalization
After the softening process, some boiler feed water treatment systems will utilize dealkalization to reduce pH, an impurity in boiler feed water that can cause foaming, corrosion, and embrittlement. Sodium chloride dealkalization uses a strong anion exchange resin to replace bicarbonate, sulfate, and nitrate for chloride anions. Although it doesn’t remove alkalinity 100%, it does remove the majority of it with what can be an easy-to-implement and economical process. Weak acid dealkalization only removes cations bound to bicarbonate, converting it to carbon dioxide (and therefore requiring degasification). It is a partial softening process that is also economical for adjusting the boiler feed water pH.
Reverse osmosis (RO) and nanofiltration (NF)
Reverse osmosis (RO) and nanofiltration (NF) are often used down the line in the boiler feed water treatment system process so most of the harmful impurities that can foul and clog the RO/NF membranes have been removed. Similar processes of separation, they both force pressurized water through semipermeable membranes, trapping contaminants such as bacteria, salts, organics, silica, and hardness, while allowing concentrated, purified water through. Not always required in boiler feed water treatment, these filtration units are used mostly with high-pressure boilers where concentration of suspended and dissolved solids needs to be extremely low.
Deaeration or degasification
At this point in the boiler feed water treatment process, any condensate being returned to the system will mix with the treated makeup water and enter the deaeration or degasification process. Any amount of gasses such as oxygen and carbon dioxide can be extremely corrosive to boiler equipment and piping when they attach to them, forming oxides and causing rust. Therefore, removing these gases to acceptable levels (nearly 100%) can be imperative to the service life and safety of the boiler system. There are several types of deaeration devices that come in a range of configurations depending on the manufacturer, but generally, you might use a tray- or spray-type deaerator for degasification or oxygen scavengers.
Distribution
After the boiler feed water has been sufficiently purified according to the boiler manufacturer’s recommendation and other industry-wide regulations, the water is fed to the boiler where it is heated and used to generate steam. Pure steam is used in the facility, steam and condensate are lost, and condensate return is pumped back into the process to meet up with the pretreated makeup water to cycle through pretreatment again.
Calgon conditioning
This is the internal water softening method. When Sodium meta Phosphate reacts with boiler water then it prevents the formation of scales & sludges. Calgon converts the scale forming impurities like CaSO4 into soluble complex which are less dangerous to boilers.
Na2[Na4(PO3)6] 2Na+ + [Na4(PO3)6]2-
(Calgon)
2CaSO4 + [Na4(PO3)6]2- [Ca2(PO3)6]2- + 2Na2SO4
(Soluble Complex
Ion)
On addition of (0.5 to 5 ppm) prevents the sludge and scale formation.
At low temperature and pressure it forms quite stable & soluble complex with calcium salts.
At high temperature & pressure calogen is converted into sodium orthophosphate which react with calcium salts to form calcium orthophosphates.
2Na2[Na4(PO3)6] + 6H2O 6Na2P2O7 + 6H2
I + CaSO4 CaP2O7 + Na2SO4
Phosphate conditioning and Colloidal conditioning
Phosphate conditioning is applicable only for high pressure boilers. Scale formation is prevented by adding sodium phosphate which reacts with Mg & Ca salt forming a non-adherent and easily removable, soft sludges of Ca & Mg phosphate and later removed by blow down process.
3MCl2 + 2Na3PO4 M3(PO4)2 + 6NaCl
3MSO4 + 2Na3PO4 M3(PO4)2 + 6NaSO4
Where, M= Ca2+, Mg2+
The choice of phosphate selection depends upon the pH of boiler feed water. If the water used in boiler then there is a use of acidic phosphate i.e.; NaH2PO4 while the condition at which boiler water is normal means that is neither more acidic nor basic then there is a use of weak alkaline phosphate i.e.; Na2HPO4 while if the boiler alkanity is very low then there is a use of Na3PO4.
Ion exchange technology is a proven method of producing high purity softened and demineralized water. It is used in most industries that require high purity water and to reclaim water from processes. The Ion exchange process involves the exchanging of contaminant ions for Na+ ions in a softening application and H+ and OH- ions in pure water application. Cations and anions can be removed by the cation and anion exchange resins. Resins containing –COOH, SO3H are capable for exchanging their H+ ions to cationic portion of minerals then it is called as cation exchanger while the resins containing –NH2, NHCH3 are capable for exchanging the anionic portion of the minerals then it is termed as anionic exchanger.
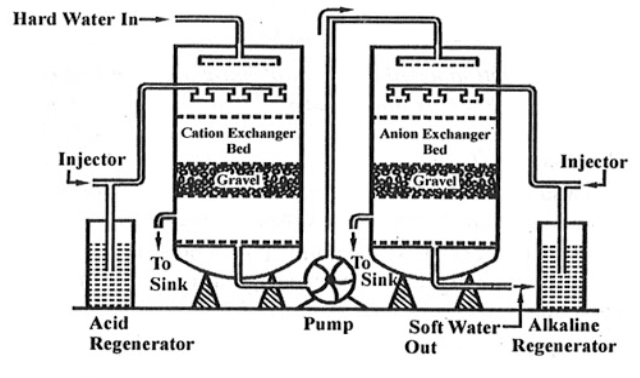
On supplying the hard water in first chamber which consists of Ca2+ or Mg2+ then the cation exchanger exchange it with H+ hence the cation exchanger absorbs the Ca2+ ions the left water are free from cations are passed to another chamber by the help of pump this water consists of anions such as Cl or SO4 on sprinkle up of these water at anion exchanger bed then it exchanged the anions and hence release the demeneralise water. The absorbed cation and anion are sinked out through the outlet present in chamber.
Desalination: The process of converting up of saline water into fresh water by removing of salts and minerals from the target source is called as the Desalination. Saltwater is desalinated to produce water suitable for human consumption or irrigation. The by-product of the desalination process is brine. Desalination is used on many seagoing ships and submarines. Most of the modern interest in desalination is focused on cost-effective provision of fresh water for human use. Along with recycled wastewater, it is one of the few rainfall-independent water sources.
Desalination using electro dialysis:
The passing up of direct current through the water in order to drive the ions through membranes to electrodes of opposite charge. The common techniques which applied the electro dialysis principle is electro dialysis reversal (EDR). This system uses ion transfer anion and cation membranes to separate the ions in source water. This membrane allows the unidirectional transfer of ions of given charge through them. E.g.- the cation transfer membranes allow only positive charge ions to pass.
Desalination using reverse osmosis:
Reverse osmosis is a process where the water is separated from the salts in the source water by pressure-driven transport through a membrane. This process uses semi-permeable membrane and applied pressure to preferentially induce water permeation through the membrane while rejecting salts. The RO plant uses less energy than thermal desalination process. This process uses thin-film composite membrane that too comprises of ultra thin aromatic polyamide thin film. The used polyamide film gives the transparent properties while the remaining part provides the mechanical supports. The polyamide films are very dense void free polymer with high surface area allowing for its high permeability. RO desalination plant include source water intake system, pretreatment facilities and high pressure feed pumps, RO membrane trains, energy recovery and desalinated water conditioning system. The intake system may be the open surface water intake or series of seawater beach wells. The pretreatment system may be the screening, chemical conditioning, sedimentation or filtration that totally depends on the used quality water further the filtered water is conveyed by transfer pump from filtrate water storage tank through cartridge filter and into the suction pipe of high pressure RO feed pumps. The cartridge filters are designed in such a manner that can retain 1 to 20 microns particles which remained in the source water after pretreatment. The high pressure feed pumps are designed to deliver the source water to the RO membranes at pressure required for membrane separation of the fresh water from the salts. The actual required feed pressure is site-specific and is mainly determined by the source water salinity and the configuration of the RO system.