Unit – 6
Beam column
The number one goal of this bankruptcy is to increase techniques for predicting the deformation reaction of character narrow individuals or easy frames composed of such individuals subjected concurrently to axial pressure and bending second. Such structural individuals are termed beam-columns. In this bankruptcy we're especially concerned with lateral deformations i.e. deformations perpendicular to the longitudinal axis of the member. The evaluation approaches are primarily based totally upon the answer of appropriate differential equations. It is acknowledged that the have an impact on of axial pressure on bending deformations is one of the maximum critical elements of the structural evaluation and design. The lateral masses and/or cease moments purpose deflections that are similarly amplified via way of means of axial compression inflicting second, Py alongside the member. These extra deflections upload drastically to the moments, which may also end result nonetheless similarly deflections. Finally, a strong scenario is reached in which deflections correspond to the bending moments because of each lateral load and Py. Because of this interplay among the axial pressure and the moments, the overall superposition approaches are inappropriate. However, because the bending second techniques zero, the member has a tendency to grow to be axially loaded strut, a hassle that has been dealt with in information. On the opposite hand, if the axial pressure vanishes, the hassle reduces to that of a beam.
Laterally Supported Beams
Beams subjected to BM develop compressive and tensile forces and the flange subjected to compressive forces has the tendency to deflect laterally. This out of plane bending is called lateral bending or buckling of beams. The lateral bending of beams depends on the effective span between the restraints, minimum moment of inertia (Iyy) and its presence reduces the plastic moment capacity of the section.
Beams where lateral buckling of the compression flange are prevented are called laterally restrained beams. Such continuous lateral supports are provided in two ways:
i) The compression flange is connected to an RC slab throughout by shear connectors.
Ii) External lateral supports are provided at closer intervals to the compression flange so that it is as good continuous lateral support. Cl 8.2.1 (pg - 52 and 53) gives the specifications in this regard.
Design of such laterally supported beams are carried out using Clauses 8.2.1.2, 8.2.1.3, 8.2.1.5, 8.4, 8.4.1, 8.4.1.1, 8.4.2.1 and 5.6.1 (Deflection) In addition, the beams shall be checked for vertical buckling of web and web crippling. The design is simple, but lengthy and does not involve trial and error procedure.
1. Laterally supported beams:
- Calculate the factored load and the maximum bending moment and shear force
- Obtain the plastic section modulus required
Zp = (M*Vmo /Fy)
a suitable section for the beam-ISLB, ISMB, ISWB or suitable built-up
Sections (doubly symmetric only). (Doubly symmetric, singly symmetric
And asymmetric- procedures are different)
3. Check for section classification such as plastic, compact, semi-compact or slender. Most of the sections are either plastic or compact. Flange and web criteria.
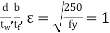
4. Calculate the design shear for the web and is given by

5. Calculate the design bending moment or moment resisted by the section (for plastic and compact)

6. Check for buckling
7. Check for crippling or bearing
8. Check for deflection
Laterally Unsupported Beams
Beams subjected to BM develop compressive and tensile forces and the flange subjected to compressive forces has the tendency to deflect laterally. This out of plane bending is called lateral bending or buckling of beams. Lateral buckling of beams involves three kinds of deformations namely lateral bending, twisting and warping. The lateral bending of beams depends on the effective span between the restraints, minimum moment of inertia (Iyy) and can reduce the plastic moment capacity of the section.
The value of Mer can be calculated using the equations given in cl. 8.2.2.1 pg-54 for doubly symmetric c/s and annex E (pg 128-129) for c/s symmetrical about the minor axis. The design bending compressive strength can be calculated using a set of equations as specified in cl.8.2.2 (Table 13a and 13 pg-54 to 57.
- Calculate the factored load and the maximum bending moment and shear force
- Design of LSB is by trial-and-error method. The design bending stress is significantly less which is to be assumed to start with. Assume slenderness ratio and h/tf and get the corresponding critical bending stress and hence the corresponding design bending stress.
- Determine the required plastic section modulus and select the section.
- Determine the actual design bending stress of this selected section knowing its slenderness ratio which should be greater than that assumed previously. Otherwise revise the section.
- Check for shear, buckling, crippling and deflection should be done Design bending strength can be calculated as per IS: 800
Design bending strength can be calculated as per IS: 800


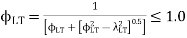
rolled or welded sections
can b Elastic lateral buckling,
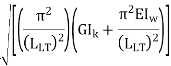
Torsional constant,
Warping constant,
Key takeaways:
- Beams subjected to BM develop compressive and tensile forces and the flange subjected to compressive forces has the tendency to deflect laterally.
- This out of plane bending is called lateral bending or buckling of beams. Lateral buckling of beams involves three kinds of deformations namely lateral bending, twisting and warping.
- The lateral bending of beams depends on the effective span between the restraints, minimum moment of inertia (Iyy) and can reduce the plastic moment capacity of the section.
The behaviour of a beam-column is commonly dealt with because the reaction of a remote structural member to a acknowledged gadget of stop forces and moments. For exercise purposes, each the layout and take a look at of beam-columns are commonly performed primarily based totally at the idea of interplay formulae.
Structural participants subjected to axial compression and bending are referred to as beam columns.
• The interplay of regular pressure and bending can be dealt with elastically or plastically the usage of equilibrium for the class of cross-section.
• The behaviour and layout of beam-columns are offered withinside the context of participants subjected to uniaxial bending, i.e. deformation takes area best withinside the aircraft of the carried out moments.
• In the case of beam-columns that are vulnerable to lateral-torsional buckling, the out-of-aircraft flexural buckling of the column needs to be blended with the lateral-torsional buckling of the beam the usage of the applicable interplay formulae.
• For beam-columns with biaxial bending, the interplay method is extended through an extra term.
OBJECTIVES:
• Evaluate the in-aircraft bending and axial compression pressure for beam-columns.
• Calculate the lateral-torsional buckling of beam-columns.
• Calculate the biaxial bending and axial compression pressure for beam-columns.
Beam-columns are described as individuals situation to blended bending and compression. In principle, all individuals in body systems are without a doubt beam-columns, with the precise instances of beams (N = 0) and columns (M = 0) truely being the 2 extremes. Depending upon the precise manner wherein the implemented loading is transferred into the member, the shape of help supplied and the member's cross-sectional shape, one of a kind kinds of reaction can be possible. The only of those includes bending implemented approximately one important axis only, with the member responding through bending totally within side the aircraft of the implemented moment
Key takeaways:
The behaviour of a beam-column is commonly dealt with because the reaction of a remote structural member to a acknowledged gadget of stop forces and moments
The columns are supported at the column bases. The column bases transmit the column load to the concrete or masonry basis blocks.
The column load is unfold over massive location on concrete or masonry blocks. The depth of bearing stress on concrete or masonry is stored inside the most permissible bearing stress.
The protection of the shape relies upon up on balance of basis. The column bases need to be designed with utmost care and skill. In the column bases, depth of stress on concrete block is thought to be uniform.
The column bases will be of ok strength, stiffness and location to unfold the burden upon the concrete, masonry, different basis or different helps without exceeding the allowable strain on such basis below any mixture of the burden and bending moments.
The column bases are of types;
- Slab base
- Gusseted bases
Slab base
The column give up is confronted for bearing over the complete area. The gussets (gusset plates and gusset angles) aren't supplied with the column with slab bases. The enough fastenings are used to hold the elements securely in plate and to withstand all moments and forces, apart from the direct compression. The forces and moments springing up all through transit, unloading and erection also are considered. When the slab by myself distributes the weight uniformly the minimal thickness of a square slab is derived as below;
Procedure
Step 1) Assume a suitable grade of concrete. Depending upon the grade of concrete used bearing strength of concrete is determine by 0.45fck
Step 2) The area of a slab base may be computed by
A= P/ bearing strength of concrete
Where,
A= area of base plate
P= Factored load
Step 3) A square base plate is generally provided. The side of the base plate may be worked out
L= B=
Some designer feel that the projections of the base plate beyond column edges a and b are kept equal and these sides can be work out.
Using
( D+2b) x (bf+2a)= A
Where,
L= length of base plate in mm
B= width of base plate in mm
D= depth of column section in mm
Step 4) The intensity of pressure w from the concrete pedestal is determine by
W= P/A1
Where, w= intensity of pressure from concrete under the slab base
A1= Area of base plate provided in mm2
Step 5) The minimum thickness ts of the base plate is calculated by using

Step 6) Holding down bolts 2 or 4 in number and of 20 mm diameter are usually provided. When the base subjected to only axial compressive load two bolt will be enough.
Step 7) welded joint between the column and base plate is designed.
Step 8) Detailing
Q.1 Design a slab base for the column consisting of ISMB 400@ 61.6 kg/m carrying an axial factored load of 450kN. Use M20 grade of concrete.
Solution:
- Area of base plate


2. Size of base plate
Provide 430 x 170 mm size of base plate
Area provide = 73100> A required
3. Intensity of pressure w from concrete pedestal
w = P/A provides
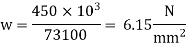

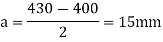

4. Thickness of base plate (ts)

Provides base plate of size 430 x 170 x 16 mm
Key takeaways:
The columns are supported at the column bases. The column bases transmit the column load to the concrete or masonry basis blocks.
Gusseted base
Gusseted bases are supplied for columns sporting heavier hundreds requiring huge base plates. A gusseted base includes a base of decreased thickness and gusseted plates are connected one to every flange of the column.
The gusseted plates, cleat angles and fastenings (bolts, rivets) in aggregate with bearing place of shaft will be enough to take all loads.
Procedure
Step 1) Bearing strength of concrete is determined = 0.45 f
Step 2) Area of the base plate may be computed by,
A = P/0.45 fck
Step 3) The size of gusset base assumed
(i) Thickness: For bolted gusset base t <16 mm.
(ii) The gusset angle is chosen so as to accommodate two rows of bolts in the vertical leg and one row of bolt in the horizontal leg. Therefore an unequal angle section is provided.
(iii) The thickness of gusset angle should be same as thickness of gusset plate.
(iv) Width of base plate.
L = depth of section + 2 (thickness of gusset plate +
Leg length of angle + over hang) (for bolted connections)
L = depth of section + 2x (thickness of gusset plate + overhang)
(for welded connections)
(v) Width of base plate
B = A/L
Step 4) The intensity of bearing pressure
W = P/A1
Where
A₁ = Area of base plate provided
Step 5) The thickness of the base plate is computed by equating the moment at the critical section to the moment of resistance of the gusset at that section.
B.M. At critical section
M = wc12/2(considering unit width)
Where
c.- Minimum over hang
Design bending moment at critical section M, 12

Now equating, M = Md
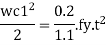
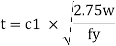
Where,
t= Total thickness including thickness of base plate and gusset angle (for bolted gusset base)
= Thickness of base plates (for welded gusset base)
W= Intensity of pressure from concrete under the slab faze.
C₁=Cantilever portion of base plate
Step 6) Holding down bolts 2 or 4 in numbers and of 20 diameter are usually provided.
Step 7) Design connection
Step 8) Detailing
Key takeaways:
Step 1) Assume a suitable grade of concrete. Depending upon the grade of concrete used bearing strength of concrete is determine by 0.45fck
Step 2) The area of a slab base may be computed by
A= P/ bearing strength of concrete
Step 3) A square base plate is generally provided. The side of the base plate may be worked out
L= B=
Step 4) The intensity of pressure w from the concrete pedestal is determine by
W= P/A1
Step 5) The minimum thickness ts of the base plate is calculated by using
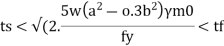
Step 6) Holding down bolts 2 or 4 in number and of 20 mm diameter are usually provided. When the base subjected to only axial compressive load two bolt will be enough.
Step 7) welded joint between the column and base plate is designed.
Step 8) Detailing
Grillage footing
High upward push homes are constructed with metal columns encased in concrete. Such columns bring very heavy load and therefore they want unique foundations to unfold the weight to a bigger region of soil. Grillage basis is one such unique basis. It includes one tier or extra ranges of I-sections metal beams. Suggests a standard tier grillage basis. Top tier includes much less wide variety however massive length metal segment even as decrease tier includes large wide variety however smaller length metal sections. Column load is transferred to the pinnacle tier via a base plate. The grillage beams are unpainted and are encased in concrete with minimal cowl of a hundred mm past the rims of metal sections. A minimal clean area of seventy five mm have to be maintained among the flanges of adjoining grillage beams in order that concreting may be made properly. To preserve spacing, pipe separators are used.
Grillage basis is a kind of basis that includes multiple greater layer of beams that are normally metal positioned on a layer of concrete to distribute and transfers the structural load on a huge region of soil under the basis.
These styles of foundations are used for closely loaded columns. Grillage basis has numerous layers of the beam which can be cowl into concrete and every organized ninety ranges to the different. This basis kind is usually used for scaffolds, closely loaded structures, and column construction. Though different styles of foundations and grillage footing appearance comparable they’re absolutely different. Wherever the muse takes the structural load and transfers it to the bottom, the footing grid unfold it over a big location of soil underneath the muse.
Types of Grillage Foundation Following are the Grillage Footings types:
- Steel Grillage Foundation
- Timber grill foundation.
- Steel Grillage Foundation
Steel Grillage basis is made of beams and metal joints or they may be assembled in a single or greater layers. Its call suggests its characteristic due to the fact it's miles made of beams which might be mare made of metal. It is likewise known as as-rolled metal beams.
A minimal cover of 10cm is intact at the outdoor face of outside beams moreover is better than the better flanges of the tallest tier. The concrete intensity have to be not less than 15cm. When we have a tendency to degree the lowest and urban pouring, we should constantly make certain if concrete compaction is completed nicely and minimal cowl need to be left between. The metallic furnished on this sort of grillage basis presents a guard in opposition to the groundwater which may also reason corrosion of metallic used for the basis. Thereafter, primary layers of beams are unfold over concrete retaining a minimal distance of one hundred fifty mm to 350 mm via way of means of the usage of a pipe as a transient separator. Concrete pouring is finished round the principle beam layers with right compaction and supervision such that no metallic is unnoticed of concrete. After the concrete is advantage enough strength, the 2d layer of metallic beams is located within side the role used pipe separators. The concrete pouring is once more finished to cowl the beam from all sides.
Then the second layer of the beam is hooked up to the top metal column footing with the assist of perspective cheats and base plate assembly. The connection of base plate and top metal column footing is poured with concrete to cover the joint among them. Steel Grillage Foundation is constructed of metal beams, structurally called rolled metal joists(RSJ.), furnished in 2 or extra tiers. Within the case of double tier grillage(that is generally furnished), the best tier of grillage beams is organized at proper angles to a totally reasonably-priced tier. The joists or beams of each tier are instructions in function with the aid of using twenty-milli meter diameter spacer bars with twenty-five-milli meter diameter pipe separators indicates the association and phase of one of these basis. The grillage beams are embedded in concrete.
2. Timber Grillage Foundation
In an area in which the soil is located to be waterlogged or completely smooth in nature, load structural partitions may be economically supported with the aid of using the right layout of Timber Grillage Foundation. Timber Grillage basis may be used to assemble a low-loading constructing with the aid of using minimizing the burden on soil as much as 5.5 tonnes/sq.mt. In the development of the basis, a concrete block this is located beneath the burden-bearing wall is changed with the aid of using Timber Platforms.
The Timber Platforms used on this basis is commonly having a thickness of eighty mm to one hundred mm. These structures had been positioned in 2 layers, one longitudinally throughout the inspiration and different the positioned extending past the footing base in more than a few 45cm to 60 cm on each sides. The bottommost layers of planks are stored 50 mm to one hundred mm thick through thinking about web page situations and loading on walls. Timber planks layers are divided with assist of a square wood phase that's spaced now no longer greater than 380 mm. The intensity of every phase is stored round 0.75 instances the width of the phase.
Key takeaways:
The Timber Platforms used on this basis is commonly having a thickness of eighty mm to one hundred mm. These structures had been positioned in 2 layers, one longitudinally throughout the inspiration and different the positioned extending past the footing base in more than a few 45cm to 60 cm on each sides.
References:
1. Subramanian N, Design of Steel Structures, Oxford University Press, New Delhi2008.
2. Dayaratnam P, Design of Steel Structures, S. Chand & Co., New Delhi, 2003.
3. Arya, A.S and Ajmani, A.L., Design of Steel Structures, Nemchand and brothers, Roorkee, 1992.
4. Punmia, B.C., Ashok Kumar Jain and Arun Kumar Jain. Comprehensive Design of Steel Structures, Laxmi Publications Pvt. Ltd., New Delhi2000.
5. IS 800-2007, Code of practice for general construction in steel, Bureau of Indian Standards, New Delhi.