Unit - 3
Metallic Materials
Ferrous alloys:
Those in which iron is the primary component are produced in greater quantities than any other metal. They're particularly useful as engineering building materials. Three variables account for their extensive use: (1) iron-containing compounds are abundant in the earth's crust; (2) metallic iron and steel alloys can be made with relatively low-cost extraction, refining, alloying, and fabrication techniques; and (3) ferrous alloys are extremely versatile, as they can be tailored to have a wide range of mechanical and physical properties.
The main disadvantage of many ferrous alloys is their corrosion resistance. This section covers the compositions, microstructures, and properties of a variety of steels and cast irons.
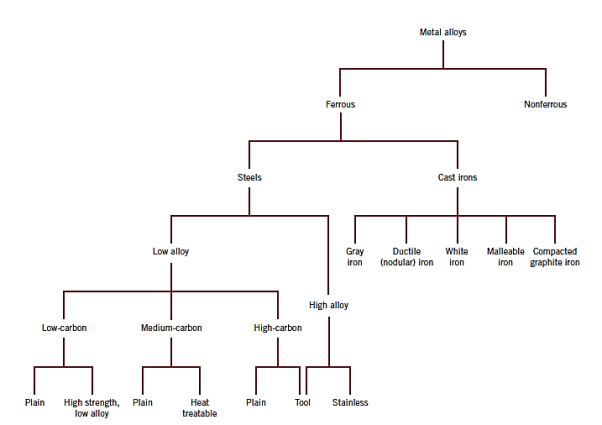
Steels:
Steels are iron–carbon alloys that may contain significant amounts of additional alloying elements; there are thousands of distinct alloys with various compositions and heat treatments. The mechanical properties are affected by the carbon content, which is typically less than 1.0 wt%. Some of the more prevalent steels are divided into low-, medium-, and high-carbon categories based on carbon content. Within each group, subclasses exist based on the concentration of various alloying elements. Other than carbon and a small amount of manganese, plain carbon steels contain only residual impurities. More alloying elements are purposely introduced in specified concentrations to alloy steels.
1) Low carbon steel:
Low-carbon steels account for the majority of the numerous types of steel manufactured. These typically contain less than 0.25 wt% C and are insensitive to heat treatments designed to create martensite; cold work is used to reinforce them. The elements of microstructures are ferrite and pearlite. As a result, these alloys are relatively soft and weak but have exceptional ductility and toughness; they are also machinable, weldable, and the least expensive to create of all steels.
Automobile body components, structural shapes (I-beams, channel and angle iron), and sheets used in pipelines, buildings, bridges, and tin cans are only a few examples. They have a yield strength of 275 MPa (40,000 psi), tensile strengths of 415 to 550 MPa (60,000 to 80,000 psi), and 25 percent EL ductility. The high-strength, low-alloy (HSLA) steels are another type of low-carbon alloy. They have higher strengths than ordinary low-carbon steels because they incorporate various alloying elements such as copper, vanadium, nickel, and molybdenum in combined concentrations as high as 10% by weight.
Heat treatment can increase tensile strength to above 480 MPa (70,000 psi); they are also ductile, formable, and machinable. In normal environments, HSLA steels are more corrosion resistant than ordinary carbon steels, which they have largely supplanted in many applications where structural strength is required (for example, bridges, towers, high-rise building support columns, and pressure vessels).
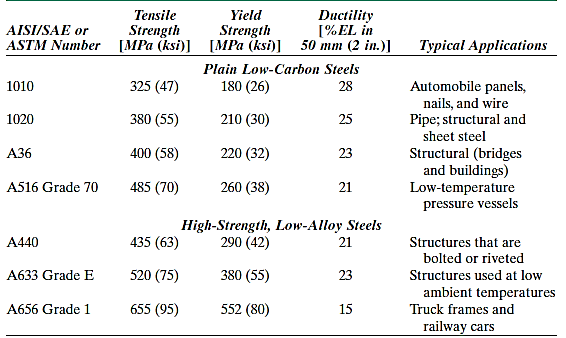
2) Medium-Carbon Steels
Carbon contents in medium-carbon steels range from 0.25 to 0.60 wt percent. To improve their mechanical properties, these alloys can be heat-treated by austenitizing, quenching, and tempering. They are most used in tempered form, with tempered martensite microstructures. Plain medium-carbon steels have low hardenability and can only be heat-treated satisfactorily in very thin sections and at extremely high quenching rates.
Additions of chromium, nickel, and molybdenum improve the alloys' heat-treatability, resulting in a wide range of strength–ductility combinations. These heat-treated alloys are stronger than low-carbon steels, but ductility and toughness are sacrificed. Railway wheels and tracks, gears, crankshafts, and other machine elements, as well as high-strength structural components, all require a blend of strength, wear resistance, and toughness.
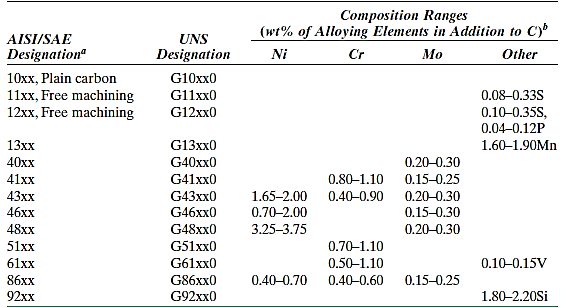
3) High-Carbon Steels
High-carbon steels, with carbon levels typically ranging from 0.60 to 1.4 wt%, are the hardest, strongest, and least ductile of the carbon steels. They are virtually always hardened and tempered, which makes them particularly wear resistant and capable of keeping a sharp cutting edge. High-carbon alloys with chromium, vanadium, tungsten, and molybdenum are used in tool and die steels. These alloying elements mix with carbon to generate carbide compounds that are extremely hard and wear resistant.
These steels are used in knives, razors, hacksaw blades, springs, and high-strength wire, as well as cutting tools and dies for moulding and shaping materials.
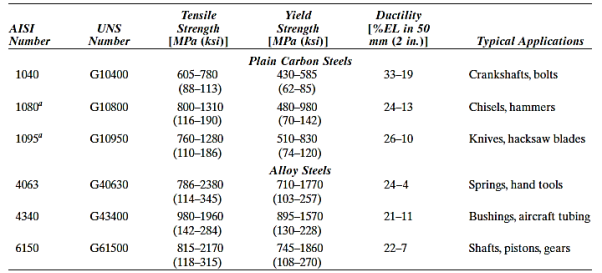
4) Stainless Steels
In a range of conditions, including the ambient atmosphere, stainless steels are highly resistant to corrosion (rusting). The most common alloying element is chromium, which must have a concentration of at least 11 weight percent Cr. Nickel and molybdenum additives can also improve corrosion resistance. On the basis of the major phase composition of the microstructure, stainless steels are classified as martensitic, ferritic, or austenitic. Stainless steels are extremely adaptable in their use due to their wide range of mechanical qualities and good corrosion resistance. Heat-treating martensitic stainless steels to make martensite the predominant microconstituent is possible. The iron–iron carbide phase diagram changes dramatically when alloying metals are added in considerable amounts.
The austenite (or ) phase field in austenitic stainless steels is extended to ambient temperature. The α-ferrite (BCC) phase is found in ferritic stainless steels. Because austenitic and ferritic stainless steels cannot be heat-treated, cold work is used to harden and strengthen them. Because of the high chromium content and nickel additions, austenitic stainless steels are the most corrosion resistant, and they are manufactured in the greatest amounts. Stainless steels that are martensitic or ferritic are magnetic; stainless steels that are austenitic are not.
Because they resist oxidation and maintain mechanical integrity at high temperatures and in harsh environments, several stainless steels are extensively utilised; the top temperature limit in oxidising atmospheres is around 1000C (1800F). Gas turbines, high-temperature steam boilers, heat-treating furnaces, aircraft, missiles, and nuclear power-generating equipment all use these steels.
Cast Iron
Cast irons are a type of ferrous alloy with a carbon concentration greater than 2.14 weight percent; however, most cast irons possess between 3.0 and 4.5 weight percent C, as well as other alloying elements. A closer look at the iron–iron carbide phase diagram reveals that alloys in this composition range become entirely liquid at temperatures between 1150 and 1300C (2100 and 2350F), which is significantly lower than steel temperatures. As a result, they are easily melted and castable. Furthermore, some cast irons are extremely fragile, and casting is the most practical method of manufacturing.
Cementite (Fe3C) is a metastable chemical that can be caused to dissociate or breakdown into α-ferrite and graphite under certain conditions, according to the reaction.

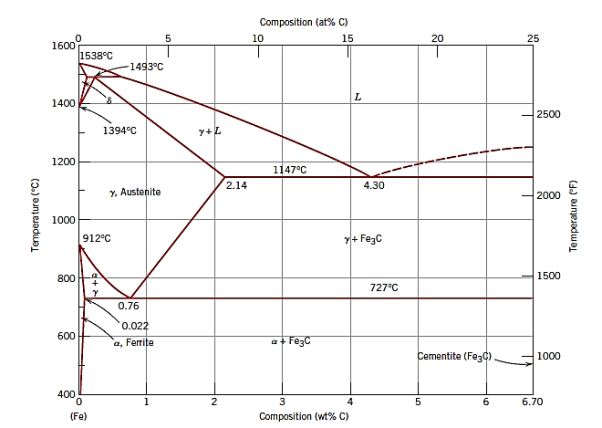
Fig (a): The iron–iron carbide phase diagram
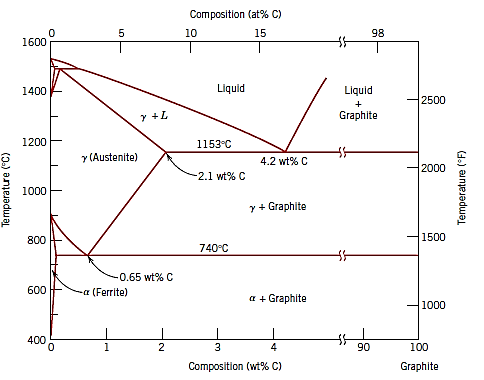
Fig (b): The true equilibrium iron–carbon phase diagram with graphite instead of cementite as a stable phase.
As a result, the actual equilibrium diagram for iron and carbon is displayed in Figure b rather than Figure a. On the iron-rich side, the two diagrams are nearly identical (eutectic and eutectoid temperatures for the Fe–Fe3C system are 1147 and 727C, respectively, compared to 1153 and 740C for Fe–C); however, Figure b extends to 100 wt% C, making graphite the carbon-rich phase rather than cementite at 6.7 wt% C.
The composition and pace of cooling control the tendency to generate graphite. The inclusion of silicon in amounts larger than around 1 wt% promotes graphite production. In addition, graphitization is favoured by slower cooling rates during solidification (the formation of graphite). Carbon exists as graphite in most cast irons, and both microstructure and mechanical behaviour are affected by composition and heat treatment. Gray, nodular, white, malleable, and compacted graphite are the most frequent cast iron varieties.
Gray iron
Gray cast irons have carbon and silicon concentrations of 2.5 to 4.0 wt percent and 1.0 to 3.0 wt percent, respectively. The graphite in most of these cast irons is in the form of flakes (like corn flakes), which are usually surrounded by an x-ferrite or pearlite matrix; this is the microstructure of a typical grey iron. A shattered surface takes on a grey look as a result of the graphite flakes, hence the name.
Because of its microstructure, grey iron is comparatively weak and brittle in tension; the tips of the graphite flakes are sharp and pointed and may act as stress concentration locations when an external tensile load is applied. Under compressive loads, strength and ductility are substantially higher.
Gray irons have several useful properties and are widely used. When comparing the respective damping capacities of steel and grey iron, they are quite effective in damping vibrational energy. This material is widely used to build the base constructions of machinery and heavy equipment that are subjected to vibrations. In addition, grey irons have a good wear resistance. Furthermore, they have a high fluidity at casting temperature in the molten state, allowing for the casting of intricately shaped objects, as well as reduced casting shrinkage. Finally, and perhaps most importantly, grey cast iron is one of the most affordable metals available.
Ductile (or Nodular) Iron
Before casting, a small quantity of magnesium and/or cerium is added to the grey iron, resulting in a specific microstructure and set of mechanical properties. Graphite still exists, albeit in the shape of nodules or spherelike particles rather than flakes. The resulting alloy has a characteristic microstructure and is known as ductile or nodular iron. Depending on the heat treatment, the matrix phase enclosing these particles is either pearlite or ferrite; for an as cast piece, the matrix phase is usually pearlite. However, a heat treatment at around 700C (1300F) for several hours will result in a ferrite matrix, as seen in this photomicrograph. Castings are substantially more ductile and stronger than grey iron.
White Iron and Malleable Iron
Most of the carbon in low silicon cast irons (less than 1.0 wt percent Si) and quick cooling rates resides as cementite rather than graphite. Because the fracture surface of this alloy is white, it is known as white cast iron. Thick portions may only have a thin layer of white iron on the top that was "chilled" during the casting process; grey iron forms in the inside, which cools more slowly. White iron is highly hard but also extremely brittle, to the point of being essentially unmachinable, due to large concentrations of the cementite phase. Its applications are limited to those that require a highly hard and wear-resistant surface without a significant degree of ductility, such as rollers in rolling mills. White iron is typically utilised as a step between the manufacture of malleable iron and another type of cast iron.
Heating white iron for a long time at temperatures between 800 and 900 degrees Celsius (1470- and 1650-degrees Fahrenheit) in a neutral atmosphere (to prevent oxidation) causes the cementite to decompose, forming graphite in the form of clusters or rosettes surrounded by a ferrite or pearlite matrix, depending on the cooling rate.
Key Takeaway:
Ferrous alloys (steels and cast irons) include iron as the primary component. Most steels have less than 1.0 weight percent C, as well as other alloying elements that make them more heat treatable (and so improve mechanical qualities) and/or corrosion resistant.
Ferrous alloys are widely employed as engineering materials due to the abundance of iron-bearing compounds. Techniques for extraction, refining, and manufacture that are cost-effective are available. They can be customised to have a wide range of mechanical and physical characteristics.
The following are some of the drawbacks of ferrous alloys: Densities that are rather high
Electrical conductivities that are relatively low Corrosion susceptibility in common environments
The most common types of steels are plain low-carbon, high-strength low-alloy, medium-carbon, tool, and stainless steels. • Plain carbon steels include a little amount of manganese and only minor amounts of other impurities in addition to carbon. The major microstructural constituent is used to classify stainless steels. Ferritic, austenitic, and martensitic are the three classifications.
Cast irons have a higher carbon concentration than steels, ranging between 3.0 and 4.5 weight percent carbon, as well as other alloying elements, particularly silicon. The majority of the carbon in these minerals is in the form of graphite, rather than being mixed with iron as cementite.
The four most commonly used cast irons are grey, ductile (or nodular), malleable, and compacted graphite irons; the latter three are relatively ductile.
In the Fe–Fe3C phase diagram, the components are Fe and Fe3C (iron carbide). It is also feasible to have a phase diagram with the components Fe and C (graphite). Graphite has a higher stability than Fe3C. As a result, the Fe–Fe3C phase diagram might be called metastable. The majority of steels do not include graphite and instead contain just iron carbide.
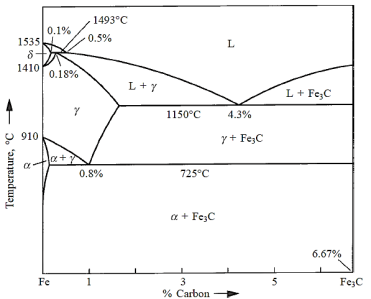
Pure iron melts at 1535°C. A peritectic invariant reaction occurs at 1493°C with the peritectic composition at 0.18% carbon.
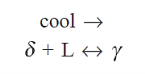
Austenite is the name for the product phase . At 1150°C, a eutectic reaction occurs, with the following eutectic composition.
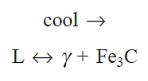
At 725°C, a eutectoid reaction occurs, with the following eutectoid composition.
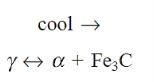
Austenite () breaks down into two phases: ferrite (x) and cementite (α) (Fe3C).
Steels are Fe–C alloys having 0–1.4 percent carbon. Mild steels have a carbon percentage of 0–0.3 percent, medium carbon steels have a carbon content of 0.3–0.6 percent, and high carbon steels have a carbon content of 0.8–1.4 percent. We'll look at the microstructures of slowly cooled steels with various carbon contents. Steel's structure is fundamentally polycrystalline (ferrite), which is the interstitial solid solution of carbon in BCC iron, when the carbon percentage is minimal.
The microstructure of steel with a eutectoid carbon content of 0.8 percent consists of alternate layers of thin, parallel plates of α (ferrite) and Fe3C. (cementite). Pearlite is the name for this eutectoidal combination. Pearlite is not a single phase, but rather a microconstituent. It gets its name from its iridescent appearance under the microscope, which resembles mother of pearl.
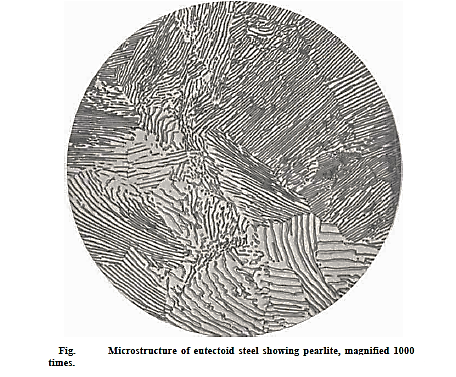
About 75% of proeutectoid ferrite, which occurs above the eutectoid temperature, and 25% of pearlite make up mild steel with 0.2 percent carbon. The amount of pearlite grows as the carbon percentage of the steel increases, until we reach the totally pearlitic structure at 0.8 percent carbon. In addition to pearlite, high carbon steels contain proeutectoid cementite above 0.8 percent.
The relative proportions of the soft, ductile ferrite and the hard, brittle cementite govern the overall hardness and ductility of slowly cooled carbon steels. As we progress from low carbon to high carbon steels, the cementite content increases, resulting in an increase in hardness and a decrease in ductility.
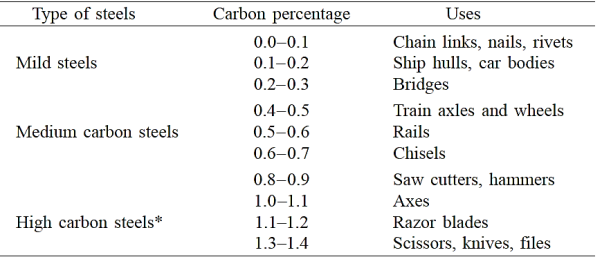
Cast irons are Fe–C alloys containing more than 2% carbon. Consider the cooling of a 3 percent carbon cast iron, for example. Proeutectic (austenite) crystallises first upon crossing the liquidus into the (L +
) zone.
When a liquid with eutectic composition passes through the eutectic temperature, it decomposes into a mixture of austenite and cementite.
The austenite decomposes to pearlite when it cools to the eutectoid temperature, providing white cast iron. White cast iron is highly hard and brittle due to the presence of a large amount of cementite.
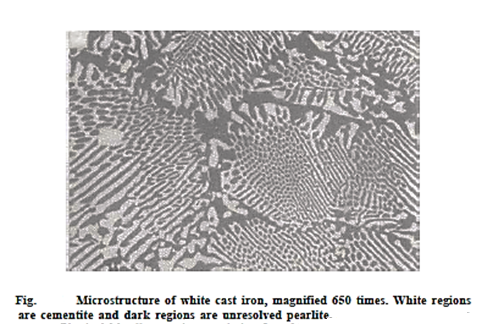
The carbon in cast iron may be present as graphite or cementite, depending on the cooling rate and any alloying components present. Graphite flakes can be found in grey cast iron. The creation of graphite is aided by slow cooling rates and the presence of silicon. Gray cast iron has a microstructure of graphite flakes in a ferrite matrix. The sharp tips of the graphite flakes work as stress relievers. Gray cast iron is fragile under tensile pressures as a result of this, despite the fact that graphite is softer than the exceedingly strong cementite found in white cast iron.
Brittleness can be prevented by manufacturing graphite in the shape of spherical nodules (without stress-inducing sharp ends), as in malleable cast iron and SG (spheroidal graphite) iron.
Malleable cast iron is made by heating white cast iron to around 900°C for a long time and then cooling it gently. To ensure that cementite rather than flaky graphite forms during solidification, the alloy's silicon concentration must be less than 1%. During the subsequent heat treatment, the cementite decomposes into the more stable graphite.
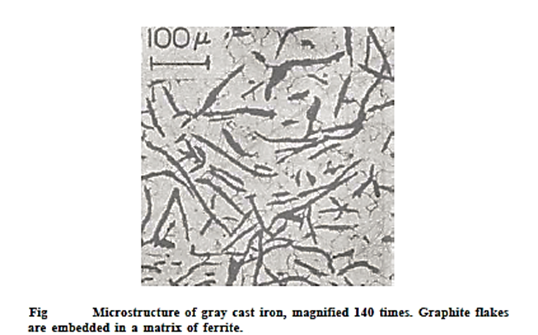
In the heat-treated microstructure, graphite appears as roughly spherical temper carbon particles. SG iron (also known as nodular iron) is made by adding specific alloys to molten iron, such as Mg or Ce. To encourage graphitization, the silicon content must be around 2.5 percent. The alloy additives change the development rate of graphite from the melt to be more or less equal in all directions, resulting in nodules (rather than flakes) of graphite. SG iron does not require any additional heat treatment.
Key Takeaway:
- α–ferrite (BCC),
–austenite (FCC), and the intermetallic complex iron carbide [or cementite (Fe3C)] are important phases on the iron–iron carbide phase diagram
- Ferrous alloys are classified into three groups based on their composition: a set of irons ( 0.008 wt percent C), Steels are a type of metal that can be (0.008 wt percent C to 2.14 wt percent C), Cast irons (2.14 percent carbon)
- Many iron–carbon alloys and steels generate microstructure as a result of a eutectoid reaction in which the austenite phase with a composition of 0.76 wt% C converts isothermally (at 727C) to α-ferrite (0.022 wt percent C) as well as cementite
- Pearlite, a microconstituent made up of alternating layers of ferrite and cementite, is the microstructural result of a eutectoid iron–carbon alloy.
- In addition to pearlite, the microstructures of alloys with carbon concentrations smaller than the eutectoid (i.e., hypoeutectoid alloys) contain a proeutectoid ferrite phase.
- The microconstituents for pearlite and proeutectoid cementite are pearlite and proeutectoid cementite.
- Hypereutectoid alloys—those with carbon concentrations in excess of the eutectoid composition.
Annealing processes:
The term annealing refers to a thermal treatment in which a material is heated to a high temperature for a long time and then cooled gently. Annealing is typically used to (1) relieve stresses, (2) enhance softness, ductility, and toughness, and/or (3) create a specified microstructure. There are many different types of annealing heat treatments; they are distinguished by the changes that are generated, which are often microstructural and are responsible for the change in mechanical properties.
Any annealing process has three stages: heating to the required temperature, holding or "soaking" at that temperature, and cooling to room temperature. In these operations, time is a crucial factor. Temperature gradients exist between the outer and interior components of the piece during heating and cooling; their magnitudes are dependent on the item's size and form.
Temperature gradients and internal tensions may be created if the rate of temperature change is too fast, resulting in warping or breaking. In addition, the actual annealing period must be sufficient to allow for any required transformation reactions. The annealing temperature is also crucial to consider; because diffusional processes are generally involved, annealing can be hastened by increasing the temperature.
- Process Annealing:
Process annealing is a heat treatment that softens and increases the ductility of a previously strain-hardened metal, thereby negating the effects of cold work. It's widely used in fabrication techniques that demand a lot of plastic deformation to keep the deformation going without fracturing or wasting a lot of energy. Processes of recovery and recrystallization are permitted to take place. Typically, a fine-grained microstructure is desired, so the heat treatment is stopped before significant grain growth occurs. By annealing at a low temperature (but above the recrystallization point) or in a nonoxidizing environment, surface oxidation or scaling can be avoided or minimised.
- Stress Relief
Internal residual tensions in metal parts may emerge as a result of the following: (1) plastic deformation processes such as machining and grinding; (2) nonuniform cooling of a piece that has been processed or fabricated at a high temperature, such as a weld or a casting; and (3) a phase transformation induced by cooling in which the parent and product phases have different densities. If these residual pressures are not eliminated, distortion and warpage may occur. A stress relief annealing heat treatment, in which the piece is heated to the recommended temperature, kept there long enough to achieve a consistent temperature, and then cooled to room temperature in air, may be used to eradicate them. The annealing temperature is usually kept low enough to preserve the effects of cold working and other heat treatments.
- Annealing of Ferrous Alloys:
To improve the characteristics of steel alloys, a variety of annealing processes are used. In the neighbourhood of the eutectoid on the phase diagram of iron–iron carbide. The lower critical temperature is the horizontal line at the eutectoid temperature, traditionally denoted A1, below which, under equilibrium conditions, all austenite will have changed into ferrite and cementite phases. The top critical temperature lines for hypoeutectoid and hypereutectoid steels are represented by the letters A3 and A cm, respectively. Only the austenite phase will survive at temperatures and compositions exceeding these limits.
Tempering:
The tempering process provides a method for transforming martensite into ferrite and cementite. How much of the martensite is transformed depends on the temperature and time of the tempering process.
Tempering occurs in four stages:
Stage 1:
Heating hardened steel up to a temperature of 200^0 C causes the martensite to reject some of the interstitial carbon.
In doing this, the tetragonal martensite structure comes closer to the equilibrium B.C.C. Structure of ferrite.
This rejected carbon combines with some martensite to form a carbide whose composition ranges from 〖Fe〗_(2 ) C to 〖Fe〗_3 C. This precipitation is called epsilon carbide or hexagonal closed packed carbide.
Its presence distorts the martensite matrix and results in a slight hardening of the steel.
Stage 2:
Further heating to about 300^0 C, causes any austenite that was retained by the steel after quenching to decompose into ferrite and cementite. Some softening accompanies this transformation.
Stage 3:
Further heating to about 400^0 C, causes the epsilon carbide to transform to cementite and ferrite.
Most of it forms to cementite because the composition of epsilon carbide is close to that of cementite. This portion of the tempering cause significant softening. If the transformation is allowed to progress long enough, the final structure will consist of cementite and ferrite.
Often the tempering process is stopped at a point where steel contains cementite, ferrite and martensite.
Stage 4:
If tempering is done at a temperature just below the lower critical point or the eutectic point, the cementite forms spheres or spheroidized steel.
In steel containing one alloying addition, cementite forms first and the alloy diffuse to it.
Austempering:
It is very similar to martempering. Steel is austenitized and then quenched in a salt bath maintained at a constant temperature in the range of 〖260-400〗^0 C.
The article is held at this temperature for long enough to allow isothermal transformation to be completed.
After the complete transformation of austenite to bainite, steel is cooled to room temperature in air. It is also called isothermal quenching.
The temperature of quenching lies below the nose of the TTT curve and above the M_s temperature.
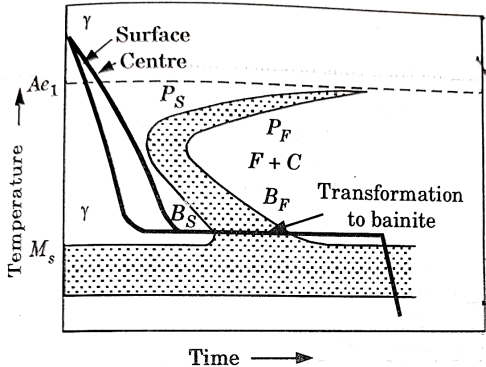
Key Takeaways:
The principal purpose of austempering is to obtain high impact strength and increased notch toughness at a given high hardness level.
Martempering:
This is a hardening method that produces martensite. This method is also known as hardening by interrupted quenching
First the steel is heated to the hardening temperature then quenched in a medium (salt bath) having a temperature slightly above the point where martensite starts to form (usually from 〖150-300〗^0 C.
It is held until it reaches the temperature of the medium and then cooled further to room temperature in air or oil. The holding time in quenching medium or bath should be sufficient to enable a uniform temperature to be reduced throughout the cross section but not long enough to cause austenite decomposition.
Austenite is transformed into martensite during the subsequent period of cooling to room temperature.
Key Takeaways:
This treatment provides a structure of martensite and retained austenite in the hardening steel.
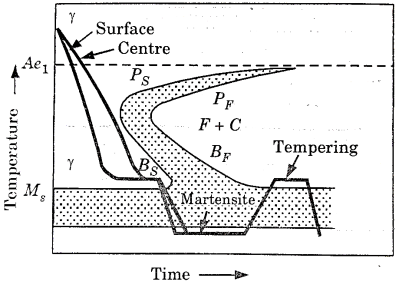
Normalizing:
Steels that have been plastically deformed, such as by rolling, include irregularly shaped pearlite grains (and most likely a proeutectoid phase) that are quite large yet vary significantly in size. Normalizing is an annealing heat treatment that refines the grains (i.e., reduces the average grain size) and produces a more uniform and acceptable size distribution; fine-grained pearlitic steels are tougher than coarse-grained pearlitic steels. Heating to at least 55°C (100°F) over the upper critical temperature—that is, above A3 for compositions less than the eutectoid (0.76 wt percent C), and above Acm for compositions more than the eutectoid (0.76 wt percent C)—is required to normalise. After allowing enough time for the alloy to fully change to austenite (a process known as austenitizing), the treatment is completed by cooling in air.
Full Anneal:
In low- and medium-carbon steels that will be machined or will encounter considerable plastic deformation during a forming operation, complete annealing is commonly used. In general, the alloy is heated to roughly 50C over the A3 line (to form austenite) for compositions less than the eutectoid, or 50C above the A1 line for compositions greater than the eutectoid (to form austenite and Fe3C phases),
The alloy is next furnace cooled, which involves turning off the heat-treating furnace and allowing both the furnace and the steel to cool to room temperature at the same time, which can take several hours. In addition to any proeutectoid phase, the microstructural result of this anneal is coarse pearlite, which is relatively soft and ductile. The full-anneal cooling technique takes a long time, but the end result is a microstructure with small grains and a homogenous grain structure.
Spheroidising:
This is a form of annealing in which cementite is in the granular (globular) form is produced in the structure of steel.
This process causes the agglomeration of all carbides in the steel in the form of small globules or spheroids.
This process is usually applied to high-carbon steels which are difficult to machine.
The process consists of heating the steel slightly above the lower critical point (〖730-770〗^0 C) holding at this temperature, and then cooling slowly to a temperature of 600^0 C.
The rate of cooling in the furnace is from 〖25-30〗^0 C per hour
Heat treatment of steels:
- Hardenability
Hardenability is a measure that relates the effect of alloy composition on a steel alloy's ability to transition to martensite for a specific quenching procedure. There is a unique relationship between mechanical qualities and cooling rate for each distinct steel alloy. The ability of an alloy to be hardened by the development of martensite as a result of a specific heat treatment is referred to as hardenability.
Hardenability is a qualitative measure of the rate at which hardness drops down with distance into the interior of a specimen as a result of decreasing martensite content, rather than "hardness," which is the resistance to indentation. A steel alloy with a high hardenability hardens, or develops martensite, not only on the surface but also throughout the inside to a great extent.
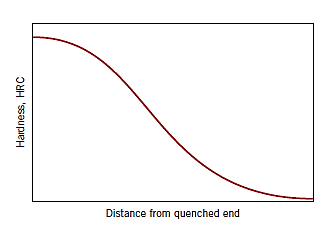
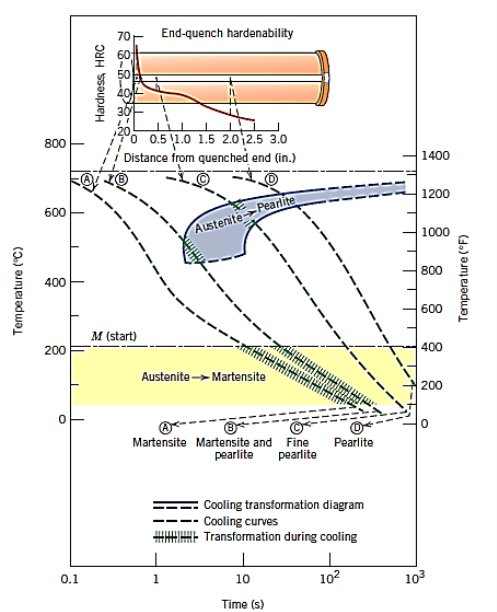
Precipitation hardening:
The development of extremely small uniformly dispersed particles of a second phase within the original phase matrix can improve the strength and hardness of particular metal alloys; this must be accomplished by phase transformations induced by proper heat treatments. Precipitation hardening is the name given to the process since the new phase's microscopic particles are called precipitates. The term "age hardening" is also used to describe this operation because the alloy's strength increases over time.
Aluminum–copper, copper–beryllium, copper–tin, and magnesium–aluminum alloys are examples of precipitation hardenable alloys; some ferrous alloys are also precipitation hardenable.
Even though the heat treatment procedures are similar, precipitation hardening and the treatment of steel to generate tempered martensite are two distinct phenomena that should not be conflated. The main distinction is in the processes used to accomplish hardening and strengthening. As precipitation hardening is explained, they should become clear.
- Solution Heat treatment:
Solution treatment is the process of heating an alloy to an appropriate temperature, maintaining it there long enough for one or more constituents to enter a solid solution, and then rapidly cooling it to keep these elements in solution.
Solution annealing (also known as solution treating) is a popular heat-treatment method for a wide range of metals. Solution annealing may be required for stainless steels, aluminium alloys, nickel-based superalloys, titanium alloys, and some copper-based alloys.
The goal of solution annealing is to dissolve any precipitates in the material and change it into a single phase structure at the solution annealing temperature. To avoid precipitation during cooling through lower temperature ranges, the material is promptly quenched down to room temperature at the end of the solution annealing process. After treatment, the single-phase solution annealed material will be soft.
Prior to age hardening / precipitation hardening, a solution annealing treatment is required. Prior to age hardening, the single-phase microstructure generated by solution annealing is essential, so that only the precipitates developed during age hardening are present in the final product. The hardness, strength, and mechanical qualities of the final product will be determined by the composition, size, and quantity of those precipitates generated during ageing. In order to achieve all of these requirements, the structure must be appropriately solution treated prior to age.
- Precipitation Heat Treating
Precipitation heat treatment entails heating alloys to a certain temperature and holding it for an extended period of time in order to introduce one or more constituents into the solid solution, followed by quick cooling to enclose them inside the solution.
It's best described as an artificial ageing process in which elements precipitate from the solid component, resulting in a significant increase in hardness.
Materials commonly treated are:
Titanium alloys
Aluminum alloys
Nickel-based alloys
Alloys of beryllium copper
Maraging steels
Heat-resistant alloys
In order to produce small and impure particles that can inhibit dislocations or crystal lattice defects, this procedure relies on solid solubility variations with temperature. Plasticity, which is a crucial component in hardening the material, might have a lot of dislocations. Impurities have an important role, especially in particle-reinforced composite materials. Solid precipitation or precipitation heat treatment can produce particles of diverse sizes with different properties, like how cold, moist air can form clouds, hail, or snow depending on meteorological conditions.
This type of treatment is particularly effective in manufacturing procedures such as welding, flame cutting, and brazing. It can also be utilised to create materials that meet specific design and functionality requirements.
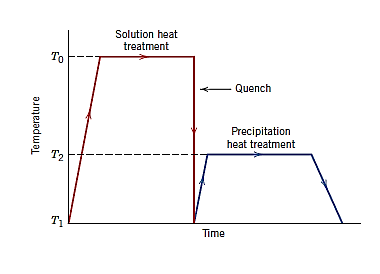
Key Takeaway:
Annealing is the process of heating a material to a high temperature for an extended period of time and then slowly cooling it to room temperature.
- Recrystallization causes a cold-worked object to become softer and more ductile during process annealing.
- During a stressrelief anneal, any internal residual strains that have been introduced are removed.
- Normalizing is used to refine and improve the grain structure of ferrous alloys.
- For high-strength steels, the optimal combination of mechanical properties can be achieved by developing a mainly martensitic microstructure throughout the cross section, which is then transformed to tempered martensite during tempering.
- Hardenability is a criterion for determining the impact of composition on the likelihood of a primarily martensitic structure forming during a given heat treatment. Hardness measurements are used to determine martensite content.
- The amount of martensite that develops is also influenced by the quenching media. Water is the most efficient quenching medium, followed by aqueous polymers, oil, and air, in that order. The effectiveness of quenching can also be improved by increasing the degree of medium agitation.
• Precipitation hardening—that is, strengthening by the development of extremely minute particles of a second, or precipitate, phase—is possible for some alloys.
• Two heat treatments are used to control particle size and, as a result, strength: All solute atoms are dissolved to form a single-phase solid solution in the first, or solution heat treatment; cooling to a relatively low temperature preserves this condition.
• Precipitate particles form and grow during the second or precipitation treatment (at constant temperature); heat treating time affects strength, hardness, and ductility (and particle size).
• Strength and hardness peak at a certain age and then decline as we become older.
• As the temperature rises, this process accelerates. The strengthening phenomenon is explained by lattice stresses that form in the vicinity of these microscopically small precipitate particles, which improve resistance to dislocation motion.
Case Hardening (or Carburizing):
It is a process through which a hard, wear resistant and shock resistant surface is produced on steel, having a tough core inside.
In this process the steel is heated to red hot and then carbon contents are forced into its surface structure. It is then hardened as usual. For this reason this process is also frequently known as carburizing.
Case Hardening has following objectives:
- For getting a hard and wear resistant surface.
- For increasing the machinability of surface.
Types of Carburizing (Case Hardening) Processes:
Pack Carburizing:
As name suggests it is a method in which components or specimen is packed in a steel box with carbon-rich powder of charcoal or coke in granules form. Then box is heated slowly above the lower critical temperature and soaking is done.
The depth of soaking depends on the time of exposure between steel and solid fumes. After soaking, box is then cooled slowly.
This method has disadvantages of scale formation at the surface of metal.
Liquid Carburizing:
In liquid carburizing, liquid carbon is used to impinge upon the heated steel by jets from nozzles. Due to this, carbon gets deposited on the steel.
This method has a disadvantage of scale formation at the surface of metal.
Gas Carburizing:
In this method, heating of steel is done in a carbon rich gaseous (as methane, propane, etc.) environment.
At high temperature, hydrocarbon gets decompose into carbon and hydrogen. This decomposed carbon gets deposited on the metal surface.
The thickness of hardened case can be controlled by rate of gas flow.
Nitriding:
This process is used to form a hard surface of nitride on the surface of metal (or steel). This is also, surface hardening process like carburizing.
This process consists of:
Heating of specimen below the lower critical temperature approximately up to
Soaking is done in the atmosphere of ammonia (. The nitrogen from
penetrates into the surface of steel to form very hard nitride surface.
Nitriding improves corrosion resistance and provides hard surface after this process, there is no need of any heat treatment process. Disadvantage is only its cost and time consumption to complete the process.
Cyaniding:
In cyaniding we dipped the components in a bath of sodium cyanide (NaCN) at a temperature . Soaking process is completed in the sodium cyanide (NaCN) bath.
After completion of soaking, metal or steel is quenched in oil (or water) to harden the surface.
The case contains about 4 to 4.5% Carbon and 0.5 to 3% nitrogen.
Cyaniding process is used to increase the fatigue strength of steel. It is less time-consuming process but a costly process.
Carbo-Nitriding:
In carbon-nitriding process both carbon and nitrogen are introduced on the surface of steel at the same time during heating process.
Heating is done in a temperature range in an environment containing anhydrous ammonia and carbon thus carbide layer provides a prevention to the nitride layer.
After heating, quenching is done in a suitable medium. The surface hardness is much higher than the carburizing steel.
Flame and Induction Hardening:
Flame Hardening-
This process is based on rapid heating and quenching in order to produce a hard surface and soft core in the work.
An oxy-acetylene flame is used to heat the work above its critical temperature and quenching is done by means of a spray of water directed on the surface.
The torch for heating the work may be stationary or may move progressively over the work which may or may not spin as shown in figure 7.
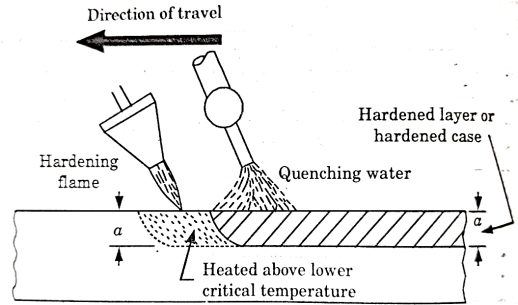
Figure: Flame Hardening
This method is applied for hardening cast gears, mill rolls or worms.
Induction Hardening-
It is a process of surface hardening in which the surface to be hardened is surrounded by copper inductor through which a high frequency current of about 2000 cycles per second is passed.
The inductor acts a primary coil of a transformer.
The work to be hardened is placed in the inductor in such a way that it does not touch the inductor as shown in fig.
The inductor block has a number of holes to spray water for quenching. The heating effect in the work is produced by the induced eddy currents and hysteresis loss in the surface of the work.
Key Takeaways:
Steels containing 0.35-0.55% carbon are most frequently induction hardened. The hardening temperature is above (Curie point) in order to increase the depth of current penetration.
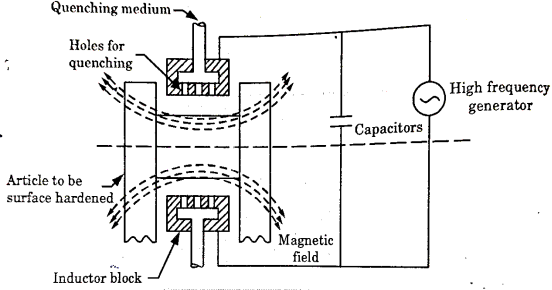
Figure: Arrangement for high- frequency induction heating
The heated areas are quenched immediately by water sprays directed from the inductor.
Induction hardening is, extensively used in many industrial plants.
Since antiquity, copper and copper-based alloys have been used in a wide range of applications due to their ideal mix of physical qualities. Unalloyed copper is difficult to mill because it is so soft and malleable; nonetheless, it has an almost limitless capacity for cold working. It also has a strong corrosion resistance in a variety of conditions, including the ambient atmosphere, seawater, and several industrial chemicals.
Copper can be alloyed to improve its mechanical and corrosion resistant qualities. Because heat-treating techniques cannot harden or strengthen most copper alloys, mechanical characteristics must be improved through cold working and/or solid solution alloying. Brasses are the most frequent copper alloys, with zinc being the most common alloying element as a substitutional impurity.
Yellow, naval, and cartridge brass; muntz metal; and gilding metal are some of the most prevalent brasses.
Bronzes are copper alloys with a variety of additional elements such as tin, aluminium, silicon, and nickel. These alloys are a little stronger than brasses, yet they still have excellent corrosion resistance. The beryllium coppers are the most prevalent heat-treatable copper alloys. They have tensile strengths of up to 1400 MPa (200,000 psi), excellent electrical and corrosion properties, and wear resistance when properly lubricated; they can be cast, hot worked, or cold worked. Precipitation-hardening heat treatments are used to achieve high strengths.
Because of the beryllium additions, which range between 1.0 and 2.5 weight percent, these alloys are expensive. Landing gear bearings and bushings for jet aircraft, springs, and surgical and dental tools are all examples of applications.
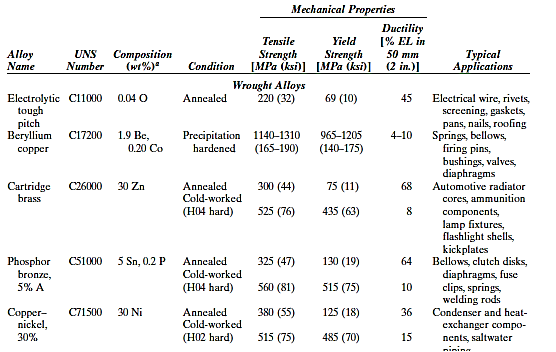
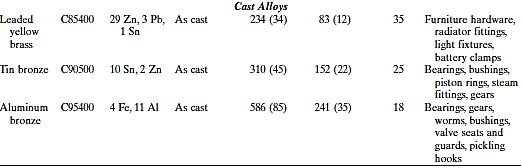
Aluminum and its alloys have a low density (2.7 g/cm3 compared to 7.9 g/cm3 for steel), good electrical and thermal conductivities, and corrosion resistance in a variety of conditions, including the ambient atmosphere. Because of their ductility, many of these alloys are simple to make, as illustrated by the thin aluminium foil sheet into which the relatively pure material can be rolled.
Aluminum's ductility is maintained even at very low temperatures due to its FCC crystal structure. Aluminum's main drawback is its low melting point of 660°C (1220°F), which limits the maximum temperature at which it may be employed.
Aluminum's mechanical strength can be increased through cold work and alloying, but both techniques reduce corrosion resistance. Copper, magnesium, silicon, manganese, and zinc are common alloying elements. Nonheat-treatable alloys are made up of a single phase, and solid-solution strengthening is used to boost their strength. As a result of alloying, some materials become heat treatable (i.e., they can be precipitation hardened). Precipitation hardening occurs in several of these alloys when two elements other than aluminium precipitate to produce an intermetallic complex such as MgZn2.
Aluminum alloys are generally classed as either cast or wrought. Both forms of composition are identified by a four-digit number that specifies the major contaminants and, in some situations, the purity level. A decimal point is placed between the last two numbers of cast alloys. After these numbers, there's a hyphen and the basic temper designation, which is a letter and perhaps a one- to three-digit number that specifies the alloy's mechanical and/or heat treatment. F, H, and O, for example, denote the as-fabricated, strain-hardened, and annealed states, respectively; T3 indicates that the alloy was solution heat-treated, cold worked, and naturally aged.
Aluminum alloys are used in a variety of applications, including aeroplane structural elements, beverage cans, bus bodywork, and automobile parts (engine blocks, pistons, and manifolds). Aluminum alloys and other low-density metals (e.g., Mg and Ti) have recently received attention as engineering materials for transportation, with the goal of reducing fuel consumption. Specific strength, as measured by the tensile strength–specific gravity ratio, is an important feature of these materials. Even if an alloy of one of these metals has a lower tensile strength than a denser substance (such as steel), it may support a greater load on a weight basis.
The aircraft and aerospace industries have lately produced a new generation of aluminum–lithium alloys. Low densities (between 2.5 and 2.6 g/cm3), high specific moduli (elastic modulus–specific gravity ratios), and outstanding fatigue and low-temperature toughness qualities characterise these materials. Furthermore, some of them may have hardened due to precipitation. However, due of lithium's chemical reactivity, unique processing processes are necessary, making these materials more expensive to produce than normal aluminium alloys.
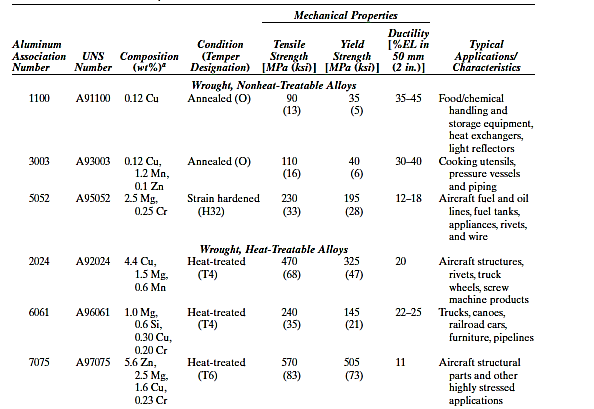

Magnesium & its alloys:
Magnesium's density, 1.7 g/cm3, is the lowest of all structural metals; as a result, its alloys are used when light weight is a key issue (e.g., in aircraft components). Magnesium is a soft metal with an HCP crystal structure and a low elastic modulus of 45 GPa (6.5 *10^6 psi).
Magnesium and related alloys are difficult to deform at room temperature; in fact, only minor cold work may be applied without annealing.
As a result, the majority of fabrication is done by casting or hot working at temperatures ranging from 200 to 350 degrees Celsius (400 to 650 degrees Fahrenheit). Magnesium, like aluminium, has a somewhat low melting temperature of 651 degrees Celsius (1204 degrees Fahrenheit). Magnesium alloys are chemically unstable and are particularly prone to corrosion in marine conditions.
In the usual atmosphere, however, corrosion or oxidation resistance is fairly good; this behaviour is thought to be attributable to impurities rather than being an intrinsic quality of Mg alloys. When fine magnesium powder is heated in air, it easily ignites; as a result, caution should be given when handling it in this state.
Some of these alloys can be cast or wrought, and some of them can be heat-treated. The main alloying elements include aluminium, zinc, manganese, and several rare earths. A composition–temper designation scheme is also employed, similar to that of aluminium alloys.
These alloys are utilised in aircraft, missiles, and baggage, among other things. Furthermore, demand for magnesium alloys has risen rapidly in a variety of industries during the last few years. Magnesium alloys have replaced engineered plastics with equal density in many applications because they are stiffer, more recyclable, and less expensive to make.
Magnesium, for example, is now used in a wide range of handheld devices (e.g., chainsaws, power tools, hedge clippers), automobiles (e.g., steering wheels and columns, seat frames, transmission cases), and audio-video-computer-communications equipment (e.g., laptop computers, camcorders, TV sets, cellular telephones).
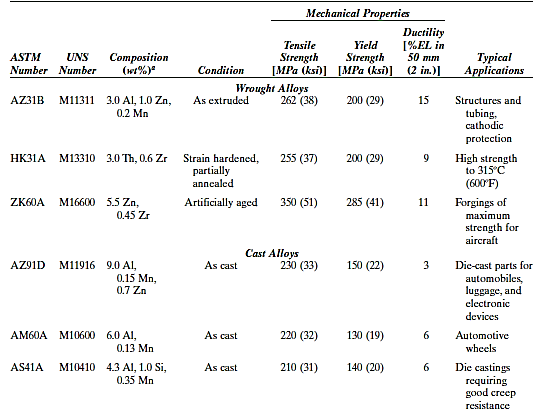
Titanium and Its Alloys
Titanium and its alloys are relatively new technical materials with an unusually diverse set of features. The pure metal has a low density (4.5 g/cm3), a high melting point [1668C (3035F), and a 107 GPa (15.5 *10^6 psi) elastic modulus. Titanium alloys are incredibly strong, with tensile strengths as high as 1400 MPa (200,000 psi) at room temperature, resulting in extraordinary specific strengths. The alloys are also very ductile and easy to forge and manufacture.
At room temperature, unalloyed (i.e., economically pure) titanium has a hexagonal close-packed crystal structure, sometimes referred to as the α phase. The HCP material transitions to a body-centered cubic (or β) phase at 883°C (1621°F). The presence of alloying elements has a significant impact on the transformation temperature. Vanadium, niobium, and molybdenum, for example, lower the temperature of the (α to β) transformation and enhance the creation of the β phase.
This is possible to find at room temperature Furthermore, both the α and β phases will coexist in some compositions.
Titanium alloys are classified into four categories based on which phase(s) are present after processing: alpha, beta, alpha+beta, and near alpha.
Because of their excellent creep characteristics, alpha titanium alloys, which are frequently alloyed with aluminium and tin, are favoured for high-temperature applications. Furthermore, because α is the stable phase, heat treatment cannot be used to strengthen the material; as a result, these materials are typically used in annealed or recrystallized states. The strength and toughness of this Ti alloy are satisfactory, but the forgeability is lower to that of other Ti alloy kinds.
The beta-stabilizing elements (V and Mo) in β titanium alloys are present in sufficient proportions that the β (metastable) phase is retained at room temperature after rapid cooling. These materials are easy to work with and have a high fracture toughness.
Both constituent phases of alpha + beta materials are alloyed with stabilising elements. Heat treatment can improve and control the strength of these alloys. An alpha phase, as well as a preserved or modified beta phase, can be found in a number of microstructures. These materials are, on the whole, quite formable.
Near-alpha alloys have both alpha and beta phases, but only a small amount of beta—that is, they have low beta stabiliser concentrations. Their qualities and fabrication features are comparable to those of alpha materials, with the exception that near-alpha alloys can have a wider range of microstructures and properties.
Titanium's chemical reactivity with other materials at high temperatures is a serious drawback. This feature forced the development of non-traditional refining, melting, and casting procedures, resulting in the high cost of titanium alloys. Despite their high temperature reactivity, titanium alloys have an extraordinarily strong corrosion resistance at normal temperatures; they are almost impervious to air, sea, and a range of industrial conditions.
They're widely used in aircraft structures, spacecraft, surgical implants, and the petroleum and chemical industries.
Super alloys
Superalloys feature extraordinary combinations of characteristics. The majority are utilised in aircraft turbine components, which must endure prolonged exposure to highly oxidising conditions and high temperatures. Under these conditions, mechanical integrity is vital; density is a key issue in this regard because centrifugal stresses in rotating members are reduced when density is lowered.
These materials are divided into three groups based on the major metal(s) in the alloy: iron–nickel, nickel, and cobalt. Refractory metals (Nb, Mo, W, Ta), chromium, and titanium are some of the other alloying components. Additionally, these alloys are classified as wrought or cast.
Superalloys are used in nuclear reactors and petrochemical equipment, in addition to turbines.
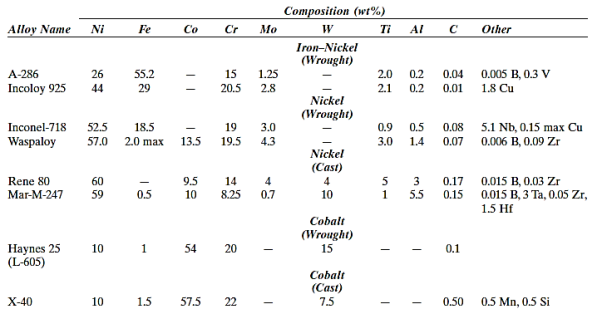
The Noble Metals
The noble metals, often known as valuable metals, are a collection of eight elements that share some physical properties. They are valuable (precious) and have outstanding or notable (noble) qualities, such as being soft, ductile, and resistant to oxidation. Silver, gold, platinum, palladium, rhodium, ruthenium, iridium, and osmium are the noble metals; the first three are the most abundant and are often used in jewellery.
Solid-solution alloying with copper can strengthen silver and gold; sterling silver is a silver–copper alloy with around 7.5 wt% Cu. Dental restoration materials are made of silver and gold alloys, while certain integrated circuit electrical connections are made of gold. Platinum is employed in chemical laboratory equipment, as a catalyst (particularly in the production of gasoline), and in thermocouples to measure high temperatures.
Miscellaneous Nonferrous Alloys
Nickel and its alloys are highly corrosion resistant in a variety of conditions, particularly those that are basic (alkaline). As a corrosion preventative treatment, nickel is frequently coated or plated on several metals that are prone to corrosion. Monel, a nickel-based alloy with around 65 percent Ni and 28 percent Cu (the rest is iron), is used in pumps, valves, and other components that come into contact with acid or petroleum solutions.
Nickel is one of the main alloying elements in stainless steels and a prominent constituent in superalloys, as previously stated.
Lead, tin, and their alloys are used in several engineering applications. Both are mechanically soft and weak, with low melting temperatures, good corrosion resistance, and recrystallization temperatures below room temperature.
Lead–tin alloys, which have low melting temperatures, are among frequent solders. X-ray shielding and storage batteries are two applications for lead and its alloys. Tin is most commonly employed as a very thin coating on the inside of simple carbon steel cans (tin cans) for food storage; this coating prevents chemical interactions between the steel and the food.
Unalloyed zinc is also a soft metal with a low melting point and a recrystallization temperature below ambient. It is chemically reactive in a variety of common settings, making it prone to corrosion. Galvanized steel is just carbon steel that has been coated with a thin zinc layer that corrodes and protects the steel preferentially.
Galvanized steel is commonly used in a variety of applications (sheet metal, fences, screen, screws, etc.). Padlocks, plumbing fixtures, vehicle parts (door handles and grilles), and office equipment are all examples of zinc alloys in use.
Despite the fact that zirconium is very common in the earth's crust, commercial refining procedures have only recently been established. Zirconium and its alloys are ductile, and their mechanical properties are similar to those of titanium alloys and austenitic stainless steels. The fundamental advantage of these alloys is their corrosion resistance in a variety of corrosive conditions, including superheated water.
Key Takeaways:
All other alloys are classified as nonferrous, which is further separated into subcategories based on the base metal or a distinguishing feature shared by a group of alloys. Wrought and cast nonferrous alloys are the two types of nonferrous alloys. Wrought alloys are deformable alloys that can be formed through deformation. Because cast alloys are brittle, casting is the most efficient method of manufacture. Copper, aluminium, magnesium, titanium, the refractory metals, the superalloys, and the noble metals, as well as miscellaneous nonferrous alloys, were all examined (nickel, lead, tin, zinc, and zirconium).
References:
- Material Science and Engineering by V. Raghavan
- Material Science and Engineering by William D. Callister
- Material Science by Prof. Satish V. Kailas (Associate Professor, Dept. Of Mechanical Engineering, Indian Institute of Science, Bangalore – 560012) NPTEL