Unit - 4
Polymers
Wood, rubber, cotton, wool, leather, and silk are examples of naturally occurring polymers (those produced from plants and animals) that have been used for ages. Proteins, enzymes, starches, and cellulose are examples of natural polymers that are crucial in biological and physiological processes in plants and animals. The determination of the molecular structures of this group of materials, as well as the production of countless polymers made from tiny organic molecules, has been made possible by modern scientific research instruments. Synthetic polymers make up a large portion of the plastics, rubbers, and fibre materials we use.
To begin with, many organic materials are hydrocarbons, which are made up of hydrogen and carbon. Furthermore, covalent intramolecular bonds exist. Each carbon atom has four electrons available for covalent bonding, but each hydrogen atom only has one bonding electron. When each of the two bonding atoms donates one electron, a single covalent bond is formed. Ex. Methane
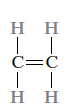
Two or three pairs of electrons are shared between two carbon atoms in double and triple bonds, respectively.
Ex: Ethylene

Ex: Acetylene
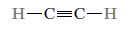
Unsaturated molecules are those with double and triple covalent bonds. That is, each carbon atom is not connected to the maximum number of (four) other atoms, allowing another atom or group of atoms to attach to the original molecule. Furthermore, all bonds in a saturated hydrocarbon are single, and no new atoms can be added without removing those that are already connected.
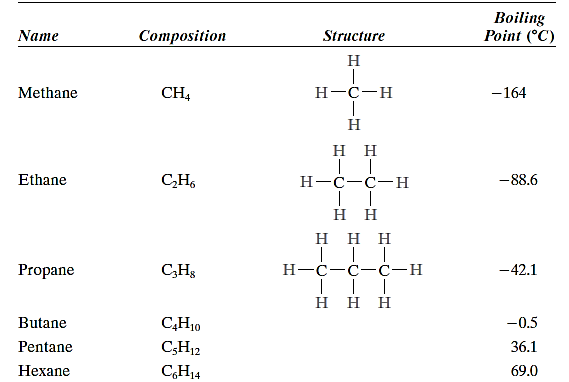
Because each molecule's covalent bonds are strong, but only weak hydrogen and van der Waals bonds exist between them, these hydrocarbons have low melting and boiling temperatures. Boiling temperatures, on the other hand, climb as molecular weight rises.
Isomerism refers to the fact that hydrocarbon molecules with the same composition can have distinct atomic configurations. Butane, for example, contains two isomers: regular butane.
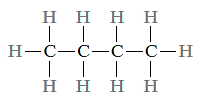
Whereas a molecule of isobutane is represented as
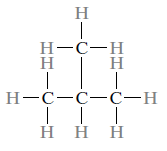
Polymer molecules are enormous in comparison to hydrocarbon molecules, and they are commonly referred to as macromolecules because of their size. The atoms in each molecule are held together by covalent interatomic connections.
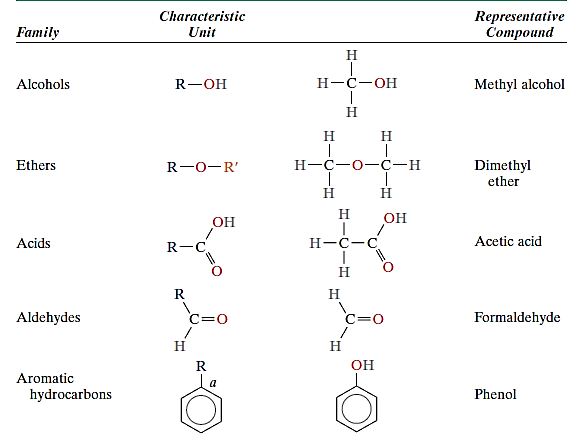
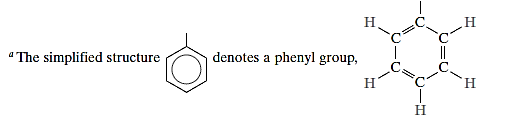
Each carbon chain polymer has a string of carbon atoms as its backbone. Many times, each carbon atom links to two nearby carbon atoms on either side, as seen in the diagram below in two dimensions:
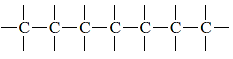
Each of the two remaining valence electrons in a carbon atom may be involved in side bonding with atoms or radicals in the chain's vicinity. Both chain and side double bonds are, of course, possible.
These lengthy molecules are made up of repeat units, which are structural entities that are repeated in a chain. The tiny molecule from which a polymer is made is referred to as a monomer. As a result, the terms monomer and repeat unit have different meanings, however the phrase monomer or monomer unit is occasionally used instead of the more precise term repeat unit.
Example:
Consider the hydrocarbon ethylene (C2H4), which is a gas with the following molecular structure at room temperature and pressure:

When ethylene gas is treated under the right conditions, it turns into polyethylene (PE), a solid polymeric substance. The reaction between an initiator or catalyst species (R.) and the ethylene monomer produces an active centre, which starts the process.
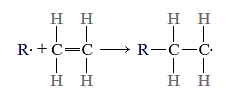
The polymer chain is then formed by adding monomer units to this active developing chain molecule in a sequential manner. As each end monomer is joined to the chain, the active site, or unpaired electron (denoted by.), is transferred. This can be depicted in diagram form as follows:
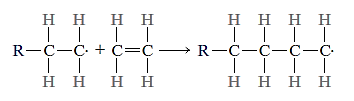
The final result, after the addition of many ethylene monomer units, is the polyethylene molecule,
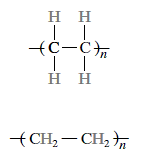
The repeat units are wrapped in parenthesis, and the number of times it repeats is indicated by the subscript n.
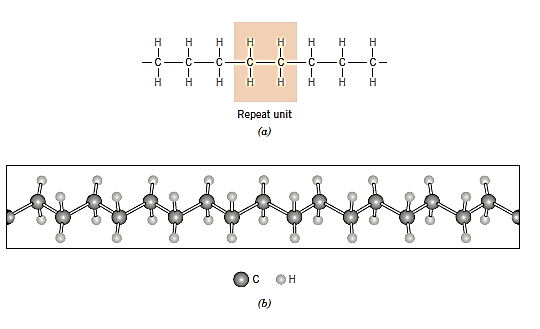
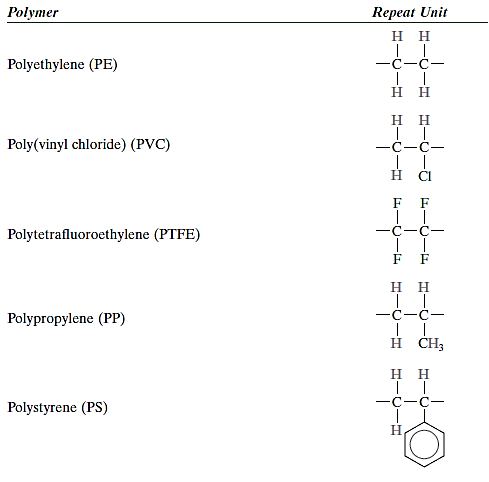
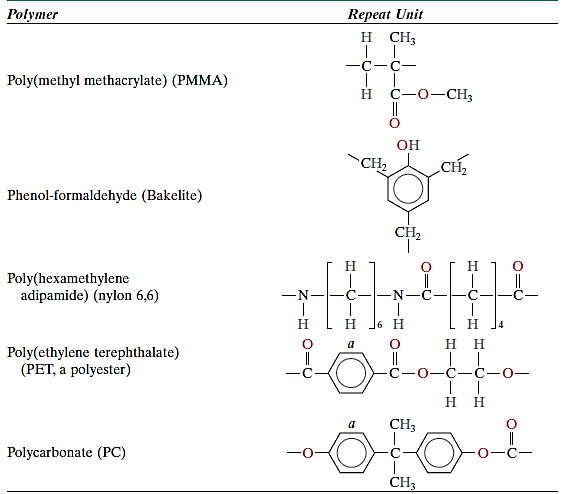
The resulting polymer is called a homopolymer when all of the repeating units along a chain are of the same kind. In what are known as copolymers, chains can be made up of two or more distinct repeat units.
As with ethylene, the monomers examined thus far have an active bond that can react with other monomers to generate two covalent bonds, generating a two-dimensional chainlike molecular structure. Bifunctional monomers are those that have two functions. The functionality of a monomer is defined as the number of bonds that it can create. Monomers like phenol–formaldehyde, for example, are trifunctional; they have three active bonds, resulting in a three-dimensional molecular network structure.
Key Takeaway:
- Polymer molecules are enormous in comparison to hydrocarbon molecules, and they are commonly referred to as macromolecules because of their size. The atoms in each molecule are held together by covalent interatomic connections.
- Each carbon chain polymer has a string of carbon atoms as its backbone.
- The polymer chain is then formed by adding monomer units to this active developing chain molecule in a sequential manner.
- The repeat units are wrapped in parenthesis, and the number of times it repeats is indicated by the subscript n.
- Polymer is called a homopolymer when all of the repeating units along a chain are of the same kind.
- In copolymers, chains can be made up of two or more distinct repeat units
Polymer molecules were formerly depicted as linear chains, ignoring the zigzag arrangement of the backbone atoms. In three dimensions, single chain bonds are capable of rotating and bending.
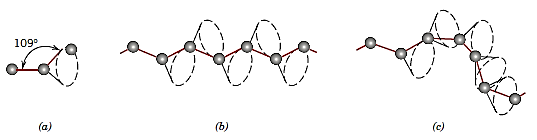
Polymers are made up of a vast number of molecular chains that can bend, coil, and kink in various ways. These random coils and molecular entanglements are responsible for a number of essential polymer features, including the huge elastic extensions demonstrated by rubber materials.
A polymer's physical properties are determined not only by its molecular weight and form, but also by changes in molecular chain structure. Modern polymer synthesis techniques provide for a great deal of flexibility in terms of structural possibilities.
Linear Polymers:
Linear polymers are ones in which the repeat units are connected in single chains from end to end. These long strands are malleable and can be compared to a spaghetti mass, with each circle representing a repetition unit. There may be considerable van der Waals and hydrogen bonding between the chains of linear polymers. Polyethylene, poly(vinyl chloride), polystyrene, poly(methyl methacrylate), nylon, and fluorocarbons are some of the most popular linear polymers.
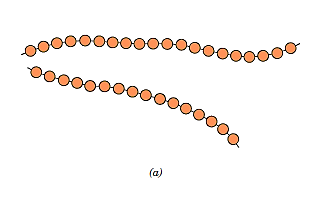
Branched Polymer:
Side-branch chains can be joined to the main chains to create branched polymers, which are appropriately named. The branches, which are regarded to be part of the main-chain molecule, could be the product of side reactions that occur during polymer synthesis. With the production of side branches, the chain packing efficiency is diminished, resulting in a decrease in polymer density. Branched polymers can also form linear structures. High-density polyethylene (HDPE), for example, is mostly a linear polymer, whereas low-density polyethylene (LDPE) has short chain branching.
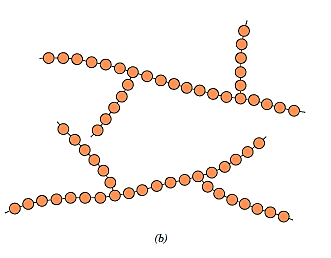
Crosslinked Polymers:
Covalent bonds are used to unite adjacent linear chains at various points in crosslinked polymers. Crosslinking can happen during synthesis or because of a non-reversible chemical reaction. Additive atoms or molecules covalently linked to the chains are frequently used to crosslink the chains. Many rubber elastic materials are crosslinked; process is known as vulcanization in rubbers.
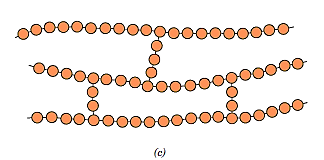
Network Polymers:
Network polymers are made up of multifunctional monomers that create three or more active covalent linkages to form three-dimensional networks.
In fact, a heavily crosslinked polymer can also be characterised as a network polymer. Epoxies, polyurethanes, and phenol-formaldehyde are examples of materials with unique mechanical and thermal properties. Polymers typically do not have a single structural type. A primarily linear polymer, for example, may have low branching and crosslinking.
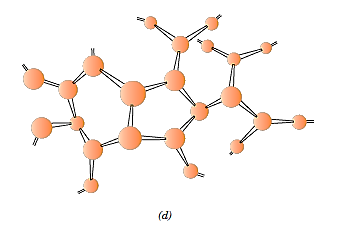
Polymer Types:
- Plastics:
The plastic categorization encompasses the highest number of distinct polymeric materials. Plastics are materials with some structural rigidity under load and are utilised for a variety of purposes. Plastics include polyethylene, polypropylene, poly(vinyl chloride), polystyrene, and fluorocarbons, epoxies, phenolics, and polyesters. They come in a wide range of property combinations. Some plastics are brittle and hard. Others are more malleable, exhibiting both elastic and plastic deformations when pressured, and occasionally undergoing significant deformation prior to fracture.
Polymers that belong within this category can have any degree of crystallinity and can have any molecular structure or configuration (linear, branching, isotactic, etc.). Plastic materials can be classed as either thermoplastic or thermosetting; in fact, this is how they are commonly classified. To be classified as plastics, linear or branching polymers must be utilised at temperatures below their glass transition temperatures (if amorphous) or melting temperatures (if semicrystalline), or be sufficiently crosslinked to maintain their shape.
Several polymers have very impressive qualities. Polystyrene and poly(methyl methacrylate) are particularly well suited to applications requiring optical transparency; nonetheless, the material must be very amorphous or, if semicrystalline, have very small crystallites. The fluorocarbons have a low coefficient of friction and are very resistant to a variety of chemicals, even at high temperatures. They're employed as non-stick cookware coatings, bearings and bushings, and high-temperature electronic components, among other things.
- Elastomers:
The rubberlike flexibility of elastomeric materials is one of their most interesting features. That is, they can be deformed to extremely massive deformations and then elastically return to their original shape. This is due to crosslinks in the polymer providing a force to return the chains to their original state.
- Fibres:
The fibre polymers can be pulled into long filaments with a length-to-diameter ratio of at least 100:1. The textile industry uses most commercial fibre polymers, which are woven or knit into cloth or fabric. Furthermore, aramid fibres are used in composite materials. A fibre polymer must possess several physical and chemical qualities in order to be usable as a textile material. Fibres are subjected to a range of mechanical deformations when in use, including stretching, twisting, shearing, and abrasion. As a result, they must have a high tensile strength (across a wide temperature range) as well as a high modulus of elasticity and abrasion resistance.
Fibre materials must have a reasonably high molecular weight, or the molten material will be too weak and break during the drawing process. The structure and orientation of the chains should also allow for the development of a highly crystalline polymer, as tensile strength improves with crystallinity. This necessitates the use of symmetrical, unbranched linear and unbranched chains with regular repeat units. The fibre-forming characteristics of the polymer are additionally improved by polar groups in the polymer, which increase both crystallinity and intermolecular forces between the chains.
The melting and glass transition temperatures of the fibre polymer, as well as its thermal properties, determine how easy it is to wash and maintain garments. In addition, fibre polymers must be chemically stable in a wide range of conditions, including acids, bases, bleaches, dry-cleaning solvents, and sunshine. Additionally, they must be somewhat non-flammable and dryable.
Key Takeaway:
- Linear polymers are ones in which the repeat units are connected in single chains from end to end.
- Side-branch chains can be joined to the main chains to create branched polymers, which are appropriately named.
- Covalent bonds are used to unite adjacent linear chains at various points in crosslinked polymers.
- Network polymers are made up of multifunctional monomers that create three or more active covalent linkages to form three-dimensional networks.
- One method to categorise polymeric materials is by their intended application. Plastics, fibres, coatings, adhesives, films, foams, and advanced are among the various categories listed in this scheme.
- Plastic materials, which include polyethylene, polypropylene, poly(vinyl chloride), polystyrene, and the fluorocarbons, epoxies, phenolics, and polyesters, are possibly the most frequently utilised group of polymers.
- A wide variety of polymeric materials can be spun into fibres, which are typically utilised in textiles. These materials' mechanical, thermal, and chemical properties are extremely important.
- Ultra-high-molecular-weight polyethylene, liquid crystal polymers, and thermoplastic elastomers were the three advanced polymeric materials mentioned. These materials are unique in their characteristics and are employed in a variety of high-tech applications.
Polymeric materials may have a crystalline state. Polymers, on the other hand, will have more complex atomic arrangements than metals and ceramics because they incorporate molecules rather than just atoms or ions. Polymer crystallinity is defined as the packing of molecular chains into an ordered atomic array. Unit cells, which are typically highly complicated, can be used to specify crystal structures.
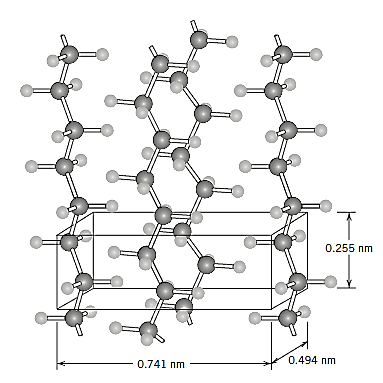
Small-molecule molecular compounds (such as water and methane) are usually either fully crystalline (as solids) or totally amorphous (as liquids). Polymer molecules are frequently only partially crystalline (or semicrystalline) due to their size and often complexity, with crystalline areas distributed within the remaining amorphous material. Because twisting, kinking, and coiling of the chains prevent the strict ordering of every segment of every chain, any chain disorder or misalignment will result in an amorphous region, a condition that is fairly common.
The degree of crystallinity can range from fully amorphous to nearly wholly crystalline (up to roughly 95 percent); in contrast, metal specimens are almost always entirely crystalline, whereas many ceramics are either completely crystalline or completely non crystalline. Semicrystalline polymers are similar to two-phase metal alloys in some ways.
The pace of cooling during solidification, as well as the chain structure, influence the degree of crystallinity of a polymer. The chains, which are very random and intertwined in the viscous liquid, must assume an ordered configuration during crystallisation after cooling to the melting point. For this to happen, the chains must be given enough time to move and align themselves.
The ability of a polymer to crystallise is also influenced by its molecular chemistry and chain arrangement. In polymers made up of chemically complicated repeat units, crystallisation is not preferred (e.g., polyisoprene). Crystallization, on the other hand, is difficult to avoid in chemically simple polymers like polyethylene and polytetrafluoroethylene, even at very high cooling rates.
Because there are minimal constraints to hinder chain alignment in linear polymers, crystallisation is simple. Side branches obstruct crystallisation, resulting in branched polymers that are never highly crystalline; in fact, severe branching may prohibit any crystallisation at all. Because the crosslinks prevent the polymer chains from reorganising and aligning into a crystalline structure, most network and crosslinked polymers are virtually entirely amorphous.
A few partly crystalline crosslinked polymers exist. In terms of stereoisomers, atactic polymers are difficult to crystallise; however, isotactic and syndiotactic polymers crystallise much more easily due to the regularity of the side group geometry, which makes fitting adjacent chains easier. In addition, the larger or bulkier the side-bonded groups of atoms, the less likely they are to crystallise.
In general, the more irregular and random the repeat unit configurations are in copolymers, the higher the likelihood for non-crystallinity to emerge. There is a chance of crystallisation in alternating and block copolymers. Random and graft copolymers, on the other hand, are typically amorphous.
The degree of crystallinity influences the physical properties of polymeric materials to some extent. Crystalline polymers are typically more resistant to dissolution and heat softening.
A semicrystalline polymer is thought to be made up of small crystalline patches (crystallites) with exact alignments interspersed with amorphous regions made up of randomly aligned molecules. Examining polymer single crystals, which may be generated from dilute solutions, can reveal the structure of the crystalline regions. These crystals are thin platelets (or lamellae) with a regular form and a thickness of 10 to 20 um and a length of 10 u m. These platelets frequently create a multi-layered structure.
Each platelet's molecular chains fold back and forth on themselves, with folds at the faces; this structure is known as the chain-folded model. Each platelet will be made up of a number of molecules, but the average chain length will be much longer than the platelet thickness.
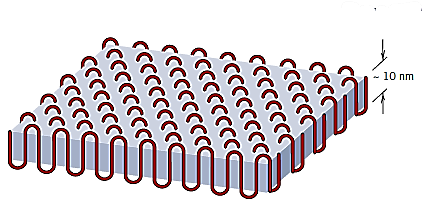
Many semicrystalline bulk polymers that crystallise from a melt have a spherulite structure. Each spherulite can develop to be roughly spherical in shape, as implied by the name; one of them, as found in natural rubber. The spherulite is made up of a tangle of ribbon-like chain-folded crystallites (lamellae) that radiate outward from a single nucleation site in the centre.
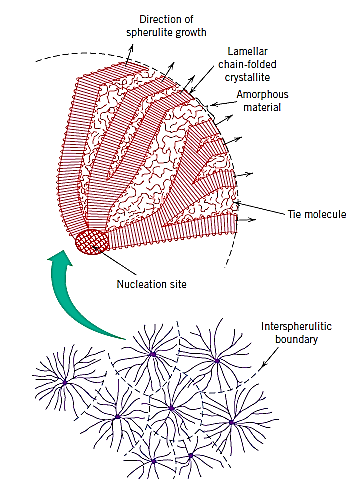
The extremities of adjacent spherulites begin to impinge on one another as the crystallisation of a spherulitic structure nears completion, establishing more or less planar boundaries; previous to this time, they maintain their spherical shape. Within each spherulite, a distinctive Maltese cross pattern appears. The twisting of the lamellar crystals as they expand like ribbons from the centre causes the bands or rings in the spherulite appearance.
In polycrystalline metals and ceramics, spherulites are thought to be the polymer equivalent of grains.
Each spherulite is made up of a variety of distinct lamellar crystals as well as some amorphous material. When polyethylene, polypropylene, poly(vinyl chloride), polytetrafluoroethylene, and nylon crystallise from a melt, they form a spherulitic structure.
Defects in polymers:
Because of the chainlike macromolecules and the nature of the crystalline state for polymers, the point defect notion differs from that of metals and ceramics. In crystalline portions of polymeric materials, point defects similar to those seen in metals, such as vacancies and interstitial atoms and ions, have been identified. Because chain ends differ chemically from typical chain units, they are termed defects.
The chain ends are also associated with vacancies. Additional flaws, on the other hand, can be caused by branching in the polymer chain or chain segments that protrude from the crystal. A chain portion can exit a polymer crystal and renter it at a different place, forming a loop, or it can enter a second crystal to act as a tie molecule. Polymer crystals can also have screw dislocations.
Impurity atoms/ions or groups of atoms/ions can be included as interstitials in the molecular structure, as well as coupled with major chains or as short side branches. Interfacial faults include the surfaces of chain-folded layers, as well as the boundaries between two neighbouring crystalline areas.
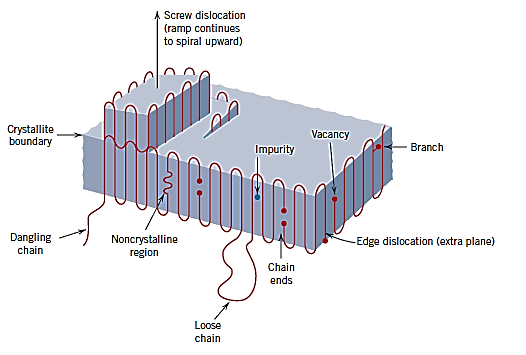
Key Takeaway:
- The condition of crystallinity exists when the molecular chains are aligned and packed in an ordered atomic configuration.
- Amorphous polymers with misaligned and disordered chains are also feasible.
- Polymers can be completely amorphous or have different degrees of crystallinity, which means that crystalline regions are interspersed among amorphous sections.
- Crystallinity is aided by polymers with regular and symmetrical chain architectures that are chemically simple.
- The density of a semicrystalline polymer, as well as the densities of entirely crystalline and totally amorphous materials, determines its percent crystallinity.
- Crystalline areas (or crystallites) are plate-shaped and have a chain-folded structure, with folds at the faces.
- Spherulites are made up of a group of ribbonlike chain-folded lamellar crystallites that radiate outward from the core of a semicrystalline polymer.
- Vacancies, interstitial atoms, impurity atoms/ions, and groups of atoms/ions as interstitials have been discovered in crystalline regions, despite the fact that the point defect concept in polymers differs from that in metals and ceramics.
- Chain ends, dangling and loose chains, and dislocations are examples of other faults.
Polymer chemists and scientists are constantly looking for new materials that can be synthesised and produced quickly and cheaply, and that have better qualities or better property combinations than the homopolymers previously addressed. Copolymers are one type of these materials.
Take a look at a copolymer made up of two repetition units. Different sequencing configurations along polymer chains are available depending on the polymerization process and the relative proportions of various repeat unit types.
- In a random copolymer, the two distinct units are randomly spread along the chain.
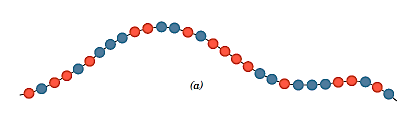
- The two repeat units in an alternating copolymer alternate chain place, as the name implies.
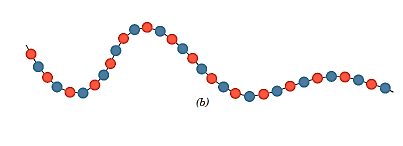
- Identical repeat units are packed in blocks along the chain in a block copolymer.
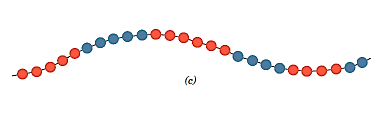
- For homopolymer side branches of one type can be grafted onto homopolymer main chains made up of a different repeat unit, resulting in graft copolymers.

Copolymers are frequently used in synthetic rubbers. Automobile tyres are constructed from styrene–butadiene rubber (SBR), a popular random copolymer. Another random copolymer made up of acrylonitrile and butadiene is nitrile rubber (NBR). NBR is also highly elastic and resistant to swelling in organic solvents; it is used to make gasoline hoses. The block copolymer impact-modified polystyrene is made up of alternating blocks of styrene and butadiene. The springy isoprene blocks prevent the spread of cracks in the material.
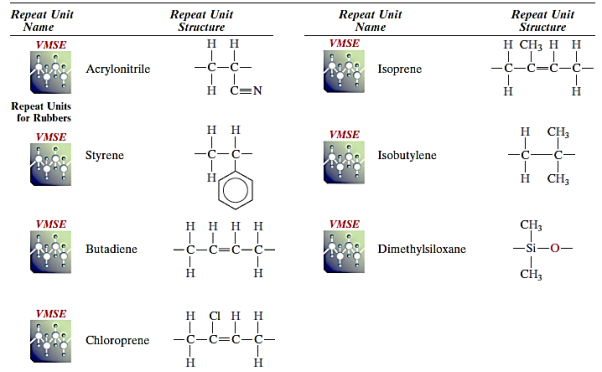
Key Takeaway:
- Random alternating, block, and graft copolymers are among the copolymers available.
- Units used in copolymer rubber products that are repeated.
The dominant molecular structure of a polymer is connected to its responsiveness to mechanical forces at high temperatures. Indeed, one classification approach for these materials is based on their behaviour as temperature rises. The two subcategories are thermoplastics (or thermoplastic polymers) and thermosets (or thermosetting polymers). Thermoplastics soften (and eventually liquefy) when heated and harden when cooled—completely reversible and repeatable processes.
On a molecular level, when the temperature rises, secondary bonding forces decrease (due to increased molecular motion), allowing neighbouring chains to move closer together when a stress is applied. When a molten thermoplastic polymer is heated to too high a temperature, irreversible deterioration occurs. Furthermore, thermoplastics are a somewhat soft material. The majority of linear polymers, as well as those with branching structures and flexible chains, are thermoplastic. Normally, these materials are created by applying heat and pressure at the same time.
Polyethylene, polystyrene, poly(ethylene terephthalate), and polypropylene are examples of typical thermoplastic polymers (vinyl chloride). Network polymers are thermosetting polymers.
During the formation process, they become permanently rigid and do not soften when heated. Covalent crosslinks exist between adjacent molecular chains in network polymers. These connections hold the chains together during heat treatments, preventing vibrational and rotational chain motions at high temperatures.
As a result, when heated, the materials do not soften. In most cases, crosslinking is significant, with 10 to 50 percent of the chain repeat units being crosslinked.
The severance of these crosslink connections and polymer breakdown can only be caused by heating to extremely high temperatures. Thermoset polymers are generally stronger and tougher than thermoplastics, with higher dimensional stability. The majority of crosslinked and network polymers are thermosetting, including vulcanised rubbers, epoxies, phenolics, and some polyester resins.
Key Takeaway:
- Polymers are classed as thermoplastic or thermosetting depending on their behaviour at high temperatures.
- Thermoplastic polymers are made up of linear and branching structures that soften when heated.
- When heated, it becomes brittle and hardens when cooled.
- Thermosetting polymers, on the other hand, will not soften when heated once they have hardened because their structures are crosslinked and networked.
The rubberlike flexibility of elastomeric materials is one of their most interesting features. That is, they can be deformed to extremely massive deformations and then elastically return to their original shape. This is due to crosslinks in the polymer providing a force to return the chains to their original state. Natural rubber was perhaps the first to exhibit elastomeric behaviour; but, in recent years, a vast number of elastomers with a wide range of properties have been synthesised.
An elastomer is amorphous and consists of crosslinked molecular chains that are strongly twisted, kinked, and coiled in an unstressed state. When a tensile load is applied, elastic deformation is simply partial uncoiling, untwisting, and straightening of the chains, with the subsequent elongation of the chains in the stress direction. The chains spring back to their prestressed conformations when the stress is released, and the macroscopic component recovers to its original shape. A thermodynamic characteristic termed entropy, which is a measure of the degree of disorder inside a system and increases with increasing disorder, is part of the driving force for elastic deformation.
The system gets more organised as an elastomer is stretched and the chains straighten and align. If the chains return to their original kinked and coiled shapes from this state, the entropy increases. This entropic effect causes two fascinating events. First, an elastomer's temperature rises when stretched; second, the modulus of elasticity increases with increasing temperature, which is the opposite of what other materials do.
To be elastomeric, a polymer must meet a number of requirements: (1) It must be difficult to crystallise; elastomeric materials are amorphous, with molecular chains that are spontaneously coiled and kinked when not in use. (2) For the coiled chains to respond quickly to an applied force, chain bond rotations must be relatively free. (3) The commencement of plastic deformation must be delayed for elastomers to experience reasonably high elastic deformations.
Crosslinking accomplishes this goal by limiting the motion of chains past one another. The role of crosslinks in the deformation process is that they act as anchor points between the chains, preventing chain slippage. The process of vulcanization is used to crosslink numerous types of elastomers (4) Finally, the temperature of the elastomer must be higher than its glass transition temperature. For many typical elastomers, the lowest temperature at which rubberlike behaviour endures is between 50 and 90C (60 and 130F). An elastomer becomes brittle below its glass transition temperature, causing its stress–strain behaviour to change.
Vulcanization
In elastomers, the crosslinking process is known as vulcanization, and it is accomplished through a non-reversible chemical reaction that is usually carried out at a high temperature. Sulphur compounds are added to the heated elastomer in most vulcanizing reactions; sulphur atom chains bond with adjacent polymer backbone chains and crosslink them.
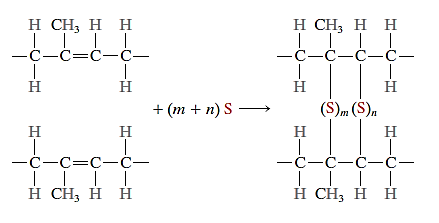
Unvulcanised rubber, which has minimal crosslinks, is soft and sticky, and has a low abrasion resistance. Vulcanization improves modulus of elasticity, tensile strength, and resistance to oxidation deterioration. The density of crosslinks is directly related to the amount of the modulus of elasticity.
Application:
Natural rubber is still widely utilised because it possesses an exceptional combination of desired qualities. The most important synthetic elastomer, however, is SBR, which is mostly used in vehicle tyres and is reinforced with carbon black. Another common synthetic elastomer is NBR, which is highly resistant to deterioration and swelling. Even vulcanised rubbers' mechanical qualities in terms of tensile strength, abrasion and tear resistance, and stiffness are insufficient for many applications (e.g., automotive tyres). Additives like carbon black may help to increase these qualities even more.
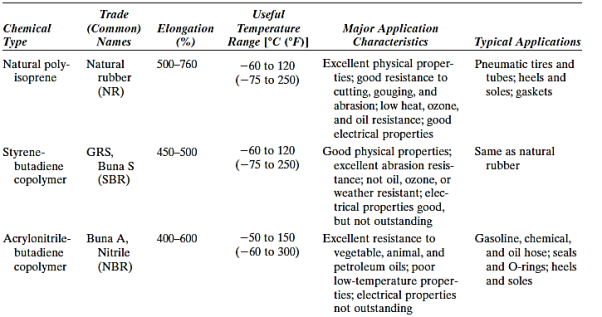
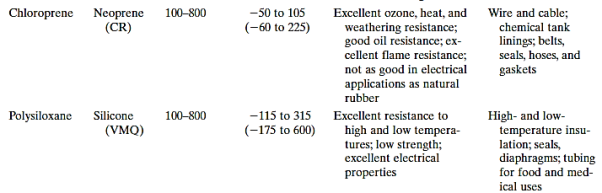
Key Takeaway:
- Large elastic extensions are feasible with amorphous and mildly crosslinked elastomeric materials.
- Deformation refers to the uncoiling and unkinking of chains as a result of a tensile tension.
- Many elastomers are copolymers, whereas silicone elastomers are really inorganic materials.
- Crosslinking is commonly achieved during the vulcanization process; higher crosslinking improves the elastomer's modulus of elasticity and tensile strength.
References:
- Material Science and Engineering by V. Raghavan
- Material Science and Engineering by William D. Callister
- Material Science by Prof. Satish V. Kailas (Associate Professor, Dept. Of Mechanical Engineering, Indian Institute of Science, Bangalore – 560012) NPTEL