Unit - 6
Composite materials
Materials with unique qualities are required for a wide range of high-tech applications, including those in the aircraft, undersea, biotechnology, and transportation industries. For example, aircraft designers are increasingly looking for structural materials that are low in density, strong, rigid, and abrasion and impact resistant, as well as corrosion resistant. This is a powerful combo of qualities. Strong materials are relatively dense among monolithic materials; increasing strength or stiffness often results in a decrease in toughness.
The development of composite materials has expanded material property combinations and ranges, and it continues to do so. In general, any multiphase material that exhibits a considerable fraction of the properties of both component phases, resulting in a better combination of properties, is deemed a composite. Better property combinations are fashioned by the appropriate combining of two or more separate elements, according to this principle of combined action. Many composites have property trade-offs as well.
The ferrite phase is ductile and soft, whereas the cementite phase is hard and brittle. The pearlite's combined mechanical properties (fairly high ductility and strength) outperform those of either of the constituent phases. A variety of composites can also be found in nature. Wood, for example, is made up of strong and flexible cellulose fibres that are surrounded and kept together by lignin, a stiffer substance. Bone is also made up of the hard, brittle mineral apatite and the strong yet soft protein collagen.
In this application, a composite is a multiphase substance that is created artificially rather than occurring or forming spontaneously. Furthermore, the constituent phases must differ chemically and be separated by a different interface.
Many composite materials are made up of only two phases: the matrix and the scattered phase. The matrix is a continuous phase that surrounds the dispersed phase. The qualities of composites are determined by the constituent phases' properties, their relative amounts, and the dispersion phase's shape. In this context, dispersed phase geometry refers to the shape of the particles as well as their size, dispersion, and orientation.
Key Takeaway:
- Composites are multiphase materials that have been synthesised artificially and have desirable combinations of the constituent phases' best qualities.
- One phase (the matrix) is usually continuous and entirely encircles the other (the dispersed phase).
The most important composites in terms of technology are those in which the dispersed phase is in the shape of a fibre. High strength and/or stiffness on a weight basis are frequently design goals for fibre-reinforced composites. Specific strength and specific modulus parameters are used to express these properties, which correspond to the ratios of tensile strength to specific gravity and modulus of elasticity to specific gravity, respectively. Low-density fibre and matrix materials have been used to create fibre-reinforced composites with extremely high specific strengths and moduli.
Fibre length is used to classify fibre-reinforced composites. The fibres of short fibre are too short to provide a significant increase in strength.
Influence of fibre length:
The mechanical properties of a fibre-reinforced composite are determined not only by the fibre qualities, but also by the degree to which the matrix phase transmits an applied load to the fibres. The magnitude of the interfacial connection between the fibre and matrix phases is critical to the load transmittance.
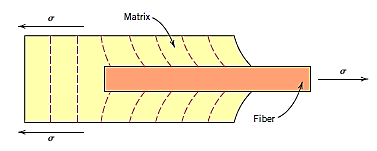





This critical length is on the order of 1 mm for a variety of glass and carbon fibre–matrix combinations, ranging from 20 to 150 times the fibre diameter.
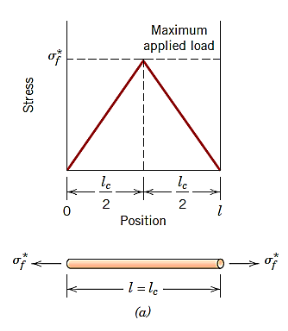
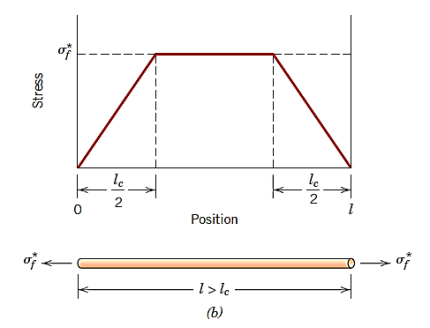
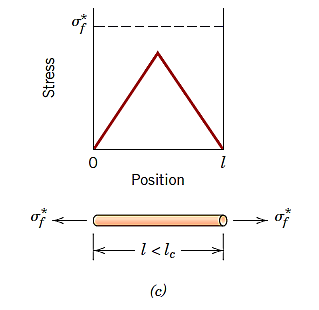
Influence of fibre orientation and concentration:
The strength and other properties of fiber-reinforced composites are influenced by the arrangement or orientation of the fibres relative to one another, the fibre concentration, and the fibre distribution. There are two conceivable orientations: (1) a single-direction parallel alignment of the longitudinal axis of the fibres, and (2) a completely random alignment.
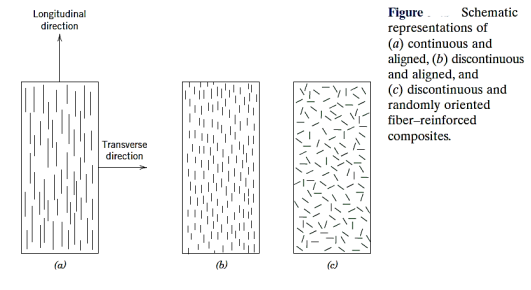
Key Takeaway:
- Fiber-reinforced composites have the highest potential for reinforcing efficiency among the various composite kinds.
- In fiber-reinforced composites, an applied load is communicated to and distributed among the fibres through the matrix phase, which is usually at least moderately ductile; significant reinforcing is only achievable if the matrix–fiber link is strong.
- Reinforcement efficiency is dependent on fibre length because reinforcement discontinues at the fibre extremities.
- There is a critical length (lc) for each fiber–matrix combination, which is determined by fibre diameter and strength, as well as fiber–matrix binding strength.
- Continuous fibres have a length that far surpasses this crucial limit (i.e., 15lc), whereas shorter fibres are discontinuous.
- Three main forms of fiber-reinforced composites are feasible based on fibre length and orientation:
1) Mechanical properties are highly anisotropic and are continuous and aligned. Reinforcement and strength are at their highest in the alignment direction and at their lowest perpendicular to it.
2) Discontinuous and aligned — large longitudinal strengths and stiffnesses are achievable.
3) Discontinuous and randomly oriented properties are isotropic, notwithstanding certain limitations in reinforcement efficiency.
Metal-matrix composites (MMCs) have a ductile metal matrix, as the name implies. These materials can withstand higher service temperatures than their basemetal counterparts, and the reinforcement can improve specific stiffness. Specific strength, abrasion resistance, creep resistance, thermal conductivity, and dimensional stability are all advantages of using these materials. Higher working temperatures, nonflammability, and improved resistance to degradation by organic fluids are some of the advantages of these materials over polymermatrix composites.
Metal-matrix composites are far more expensive than PMCs, hence their use is limited. As matrix materials, superalloys, as well as aluminium, magnesium, titanium, and copper alloys, are used. The reinforcement can take the shape of particles, continuous and discontinuous fibres, and whiskers, with concentrations ranging from 10% to 60% by volume.
Carbon, silicon carbide, boron, aluminium oxide, and refractory metals are examples of continuous-fiber materials. Discontinuous reinforcements, on the other hand, are mostly silicon carbide whiskers, chopped aluminium oxide and carbon fib
At high temperatures, some matrix–reinforcement combinations are particularly reactive. As a result, high-temperature processing or exposing the MMC to high temperatures during service may induce composite breakdown. This problem is usually remedied by covering the reinforcement with a protective surface coating or changing the matrix alloy composition.res, and silicon carbide and aluminium oxide particles.
Consolidation or synthesis (i.e., the insertion of reinforcement into the matrix) is usually followed by a shaping operation in the processing of MMCs. There are a variety of consolidation procedures available, some of which are quite advanced; discontinuous fibre MMCs can be shaped using ordinary metal-forming operations (e.g., forging, extrusion, rolling).
MMCs have just lately become popular with automobile manufacturers. For example, engine components made of an aluminum-alloy matrix reinforced with aluminium oxide and carbon fibres have been produced; this MMC is lightweight and resistant to wear and thermal distortion. Driveshafts (with greater rotational speeds and lower vibrational noise levels), extruded stabiliser bars, and forged suspension and transmission components all use metal-matrix composites.
MMCs are also used in the aerospace sector. Advanced aluminum-alloy metal-matrix composites are used in structural applications; boron fibres are used as reinforcement for the space shuttle orbiter, while continuous graphite fibres are used for the Hubble Space Telescope.
Fiber reinforcing using refractory metals like tungsten can improve the high-temperature creep and rupture qualities of some superalloys (Ni- and Co-based alloys). Excellent oxidation resistance and impact strength are also maintained at high temperatures. Turbine engines that use these materials may operate at higher temperatures and have higher efficiency.
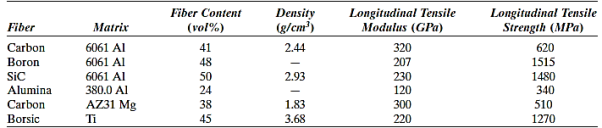
Key Takeaway:
- Although all three fundamental material categories are employed for matrices, polymers and metals are the most prevalent. In most cases, the matrix phase serves three purposes: It connects the fibres and transmits a load delivered externally to the fibres. It guards against surface damage to the individual fibres.
- Fibrous reinforced composites are sometimes classed by matrix type; within this scheme, there are three classifications: polymer-, metal-, and ceramic-matrix.
- Service temperatures are higher for metal-matrix composites than for polymermatrix composites. MMCs also use a variety of fiber and whisker types.
Ceramic materials are naturally resistant to oxidation and deterioration at high temperatures; if it weren't for their proclivity for brittle fracture, they would be ideal candidates for high-temperature and severe-stress applications, such as components in automobile and aircraft gas turbine engines.
The discovery of a new generation of ceramic-matrix composites (CMCs)—particulates, fibres, or whiskers of one ceramic material embedded in a matrix of another ceramic—has greatly enhanced the fracture toughness of ceramics. The fracture toughness of ceramic-matrix composite materials has been increased to between 6 and 20 MPa.
In essence, interactions between developing cracks and distributed phase particles cause this enhancement in fracture characteristics. The matrix phase usually initiates cracks, but the particles, fibres, or whiskers obstruct or restrict fracture growth.
For SiC whisker-reinforced alumina, increasing fibre content improves strength and fracture toughness in general. Furthermore, when compared to their unreinforced counterparts, whisker-reinforced ceramics have a significantly lower scatter of fracture strengths. Furthermore, these CMCs have better high-temperature creep behaviour and thermal shock resistance (i.e., failure resulting from sudden changes in temperature).
Hot pressing, hot isostatic pressing, and liquid-phase sintering processes can all be used to make ceramic-matrix composites. In terms of applications, SiC whisker-reinforced aluminas are employed as cutting-tool inserts for milling hard metal alloys; these materials have longer tool lifetimes than cemented carbides.
Key Takeaway:
- The purpose of ceramic-matrix composites is to increase fracture toughness. Interactions between developing cracks and distributed phase particles achieve this. One strategy for increasing KIc is transformation toughening.
Polymer-matrix composites (PMCs) are made up of a polymer resin matrix and fibres for reinforcing. Because of their room-temperature characteristics, ease of production, and low cost, these materials are employed in the widest range of composite applications and in the largest volumes.
Glass Fibre–Reinforced Polymer (GFRP) Composites:
Fiberglass is a composite made up of continuous or discontinuous glass fibres held together by a polymer matrix; it is the most common type of composite. Fibre diameters typically range from 3 to 20 um.
For numerous reasons, glass is widely used as a fibre reinforcing material:
1. From a molten condition, it is easily formed into high-strength fibres.
2. It is easily available and may be produced into a glass-reinforced plastic utilising a number of composite-manufacturing techniques at a reasonable cost.
3. It is a relatively strong fibre that generates a composite with a very high specific strength when inserted in a plastic matrix.
4. It has a chemical inertness when combined with the various plastics, making the composite usable in a variety of harsh conditions.
Glass fibre surface qualities are critical because even minor surface imperfections can have a negative impact on tensile properties. By rubbing or abrading the surface with another hard material, surface defects are easily introduced. Furthermore, glass surfaces that have been exposed to the normal atmosphere for even brief periods of time have a weaker surface layer that interferes with matrix bonding. During the drawing process, newly drawn fibres are usually coated with size, a thin layer of a substance that protects the fibre surface from damage and unwanted environmental interactions.
Prior to composite production, this size is usually removed and replaced with a coupling agent or finish that creates a chemical link between the fibre and the matrix.
This collection of items has a number of drawbacks. Despite their considerable strength, they are not very stiff and lack the stiffness required for various uses (for example, as structural elements for aeroplanes and bridges). Most fibreglass materials can only be used at temperatures below 200 degrees Celsius (400 degrees Fahrenheit); at higher temperatures, most polymers start to flow or deteriorate. Using high-purity fused silica fibres and high-temperature polymers like polyimide resins, service temperatures can be increased to around 300 C (575 F).
Automotive and marine bodies, plastic pipes, storage containers, and industrial floorings are all examples of fibreglass usage. In order to reduce vehicle weight and improve fuel efficiency, the transportation industry is increasingly employing glass fiber–reinforced polymers. The automotive sector is experimenting with or using a variety of novel applications.
Carbon Fibre–Reinforced Polymer (CFRP) Composites:
Carbon is a high-performance fibre that is the most often utilised reinforcement in advanced polymer-matrix composites (i.e., nonfiberglass). The following are the reasons for this:
1. Of all reinforcing fibre materials, carbon fibres have the highest specific modulus and specific strength.
2. They maintain their high tensile modulus and strength at high temperatures; nevertheless, high-temperature oxidation may be an issue.
3. Carbon fibres are unaffected by moisture or a wide range of solvents, acids, and bases at room temperature.
4. Because these fibres have a wide range of physical and mechanical properties, composites including them can have designed qualities.
5. Relatively low and cost-effective fibre and composite production technologies have been established.
Normally, carbon fibres are coated with a protective epoxy size that also promotes adherence to the polymer matrix. Carbon-reinforced polymer composites are now widely used in sports and recreational equipment (fishing rods, golf clubs), filament-wound rocket motor cases, pressure vessels, and aircraft structural components (e.g., wing, body, stabiliser, and rudder components)—both military and commercial, fixed-wing and helicopters.
Aramid Fiber–Reinforced Polymer Composites:
Aramid fibres have a high strength-to-modulus ratio. They are especially appealing because of their better strength-to-weight ratios compared to metals. Polymers are the chemical name for this class of materials (paraphenylene terephthalamide). There are several types of aramid fabrics; Kevlar and Nomex are two of the most common.
These fibres exhibit higher longitudinal tensile strengths and tensile moduli mechanically than other polymeric fibre materials, but they are weak in compression. Also known for its toughness, impact resistance, and resistance to creep and fatigue failure, this material has a lot to offer.
Despite the fact that aramids are thermoplastics, they are resistant to combustion and temperature stability; the temperature range over which they retain their high mechanical qualities is between 200 and 200 C. (-330 and 390 F). They can be degraded by strong acids and bases chemically, although they are largely inert in other solvents and chemicals.
In composites with polymer matrices, aramid fibres are most commonly used; common matrix materials are epoxies and polyesters. Most conventional textile procedures can be used to treat the fibres because they are relatively flexible and ductile. These aramid composites are commonly used in ballistic products (bulletproof vests and armour), sporting goods, tyres, ropes, missile cases, and pressure vessels, as well as in automotive brake and clutch linings and gaskets as a replacement for asbestos.
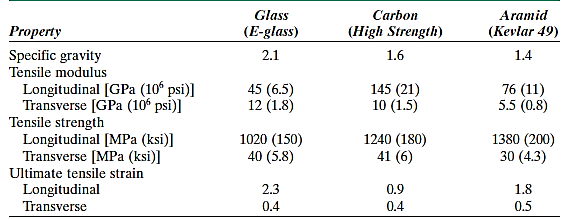
Key Takeaway:
- The most prevalent are polymer-matrix composites, which can be reinforced with glass, carbon, or aramid fibres.
References:
- Material Science and Engineering by V. Raghavan
- Material Science and Engineering by William D. Callister
- Material Science by Prof. Satish V. Kailas (Associate Professor, Dept. Of Mechanical Engineering, Indian Institute of Science, Bangalore – 560012) NPTEL