Unit - 4
Joining/Fastening Processes
The process of joining two similar or dissimilar materials is referred as joining process. The joining process is referred as fastening process, when there is the use of fasteners to joint them.
The term ‘joining’ is mainly used for welding, brazing, soldering, and adhesive bonding that form a permanent or a temporary joint between the parts. Permanent joint is referred to a joint that cannot easily be separated while temporary joint is the joint that can be easily separated when required.
The joining process can be divided into a liquid state joining or a solid-state joining process.
These processes are primarily used for the assembly of the machine to join various parts either permanently or temporarily.
Joining process generally contains the processes like welding, brazing, soldering, fastening, adhesive bonding, etc.
Welding process is the most widely used process for a permanent joint. While fastening process is most widely used process for temporary joint.
Fastening process can be divided into three types:
- Permanent mechanical fastening: When the joint required is permanent, then these fastening processes are used. It includes riveting, flanging, staking, stapling, crimping, seaming etc.
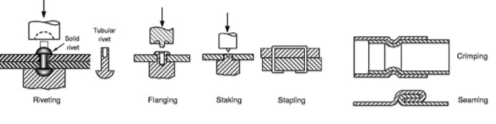
b. Semi-permanent fastening process: It includes snap fit, Blind rivet, press fit, etc.
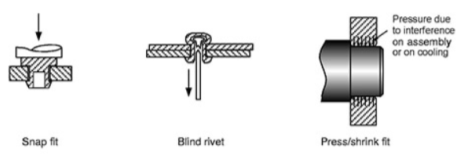
c. Non-permanent fastening process: When the joint required is temporary, then non-permanent fastening process is used. It includes Retaining, self-tapping, nut-bolt assembly, etc.
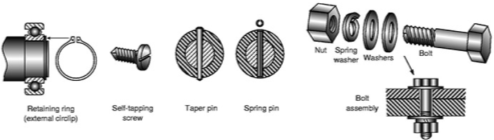
Welding is referred a material joining process where two or more parts are joined at their contacting surfaces through appropriate application of heat and pressure. Most of the welding processes are achieved via means of heat alone or with pressure alone. In few welding processes, filler material is introduced to facilitate bonding. The assemblage of elements which are joined by welding is known as weldment. Welding is most commonly related to metal parts, whereas the process is additionally used for joining plastics.
Advantages of welding:
- Welding provides a permanent joint and hence welded parts become a single entity.
- Welding is the most cost-efficient way to join components in terms of material utilization and fabrication costs.
- The welded joint may have more potential (simply may be stronger) compared to the parent materials if a filler metal is used which has strength properties that are superior to that of parents. For this proper welding techniques must be used.
- Welding is not limited to the factory environment and can be achieved in the field.
Limitations of welding:
- Many welding processes involve the use of high energy and hence are very dangerous.
- Since welding accomplishes a everlasting bond among the components, it does not permit for handy disassembly. If the product is to be disassembled (example, for repair or maintenance), then welding must not be used as the assembly approach.
- Many welding operations are performed manually and are expensive for labor cost. Many welding operations are considered ‘‘skilled trades,’’ and the labor to perform these operations may be less.
- The welded joint may suffer from specific quality defects that are hard to detect. These defects can reduce the strength of the joint.
Welding processes are divided into two major groups:
(1) fusion welding (liquid-state welding) and (2) solid-state welding.
Fusion Welding Process:
Fusion-welding processes make use of heat to melt the parent metals. In most of fusion welding operations, a filler metal is introduced to accelerate the process and offer strength to the welded joint. When there is no filler metal added, in a fusion-welding operation, is termed as an autogenous weld. The fusion category contains the most globally used welding processes that can be divided into the following types:
- Arc-welding: Arc welding is welding processes where heating of the metals is achieved by an electric arc. Few arc welding processes also apply pressure at the time of the process and most of them make use of a filler metal.
- Resistance welding: Resistance welding achieves bonding by using heat from electrical resistance to the flow of a current passing among the faying surfaces of two elements held collectively under pressure.
- Oxyfuel gas welding: These joining processes uses an oxyfuel gas, like a mixture of oxygen and acetylene, to create a hot flame for melting the parent metal and filler metal.
Solid State Welding Process:
Solid-state welding is a joining processes where joint results through application of pressure alone or by a mixture of heat and pressure. If heat is used for welding, the temperature in the operation is below the melting point of the metals that are being welded. There is no use of filler metal in solid state welding. Solid state welding is categorized into following types:
- Diffusion welding: When two surfaces are held together under pressure at an elevated temperature and the parts are joined then the welding process is termed by solid-state diffusion.
- Friction welding: Joint is achieved by the heat of friction between two surfaces.
- Ultrasonic welding: Moderate pressure is applied between the two parts and an oscillating motion at ultrasonic frequencies is used for welding. The direction of ultrasonic frequencies is parallel to the contacting surfaces. The combination of normal forces along with the vibratory forces leads to shear stresses which remove surface films and acquire atomic bonding of the surfaces.
Physics of Welding:
Many bonding mechanisms are available for welding, but fusion welding is the most widely used welding operation.
In order to achieve fusion, high density of heat energy source is applied on the saying surfaces. The leading temperatures are enough to cause local melting of the parent metals. The heat density should be sufficient enough to melt the filler material, if added.
Heat density can be referred as power transferred to the work per unit of the surface area.
Power density is given by,

Where,
P is the power entering the surface.
A is the surface area in which power is entering
The time required to melt the metal is inversely proportional to the power density. The minimum power density require to melt the metal in general welding processes is found to be 10 W/mm2
The approximate power densities required for different welding processes is given in the table below:
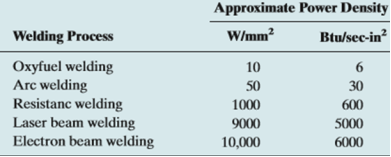
The quantity of heat needed to melt a given volume of metal is dependent on the following factors:
- The heat to increase the temperature to the melting point of the solid metal. This depends on the volumetric specific heat of the metal
- Metal’s melting point
- The heat to convert the metal at the melting point from solid to liquid phase. This depends on the heat of fusion of metal.
The unit energy for melting () is defined as the quantity of heat required to melt a unit volume of metal that starts from room temperature.
It is given by,

Where,
is the melting point of an metal in kelvin
K is the constant with value; K = 3.33 x 10-6
All this energy that is associated with heat source is not used to melt the metal. Some amount of heat is lost during the transfer of heat from source and to the workpiece, while some amount of heat is lost by dissipating heat into the work metal. This is shown in the figure below:
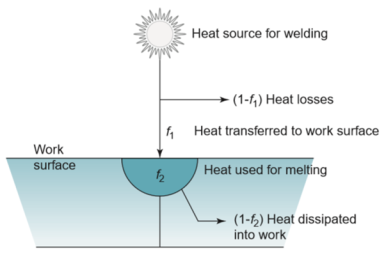
Heat transfer factor is defined as the ratio of the original heat received by the workpiece to the total heat generated at the source. It is denoted by .
Melting factor is defined as the heat used for welding to the heat received at the workpiece. It is denoted by .
Hence, heat available at welding is given by,

Where,
is the net heat available for welding process
H is total heat generated at the source of heat.
The balance equation which gives relation between energy input and energy required for welding is

Where, V is the volume of metal melted.
Brazing
Brazing is a joining process where a filler metal is melted and disbursed through a capillary action among the two surfaces of the metal parts to be joined. Here, the distance between two mating surfaces is very less. Melting of the base metals doesn’t occur in brazing. In brazing only the filler material is melted. In brazing the filler metal (also called the brazing metal), has a melting temperature that is above 450oC but below the melting point of the base metals to be joined. The brazed joint is much stronger compared to the filler metal from which it has been created upon solidification. This is because of the less part clearances used in brazing. The other reasons for stronger brazed bond is the metallurgical bonding that takes place among base and filler metals as well as the geometric constrictions which are imposed at the joint via base parts.
Advantages of Brazing
- Some brazing methods may be performed fastly and consistently, hence allowing high cycle rates and automated production
- Brazing can be used to join thin-walled parts which cant be welded
- Any metals may be joined, including dissimilar metals
- Problems with the heat-affected zone in the base metal near the joint are reduced.
- Some methods enable multiple joints to be brazed simultaneously;
- In general, less heat and power are required than in fusion welding
Limitation of Brazing:
- High service temperatures may weaken a brazed joint
- Although strength of a good brazed joint is greater than that of the filler metal, it is usually to be less compared to that of the base metals
- Joint strength is usually less compared to a welded joint
Soldering
Soldering is similar to brazing and can be defined as a joining process in which a filler metal, with melting point below 450oC, is melted and disbursed through capillary action among two surfaces of the metal parts to be joined. Similar to brazing, melting of the parent metals doesn’t occur but the filler metal is melted and it combines with the parent metal creating a metallurgical bond. Surfaces to be soldered should be pre-cleaned. This is done such that they are free of oxides, oils, etc. Proper flux should be applied to the soldering surfaces when the surfaces are heated. Filler metal, known as solder is added to the joint that disburses itself within the closely fitting parts of two materials. In industry, soldering is very closely connected to the electronics assembly.
Advantages of soldering:
- It requires low energy input relative to brazing and fusion welding
- Variety of heating methods are available
- It gives good electrical and thermal conductivity in the joint
- It has capability to make air-tight and liquid-tight seams for containers
- It is easy to repair and rework.
Limitations of soldering:
- Soldered joint has low joint strength unless reinforced by mechanically means.
- It can have possible weakening or melting of the joint in elevated temperature service.
Physics of Brazing and soldering:
The brazing and soldering processes are carried out by allowing a molten filler material to flow in the gap between the parent bodies.
To produce the perfect joint, the entire gap between the parent bodies must be filled by the filler material. This is achieved through the capillary action.
The theory of capillary flow tells us
- The liquid drop rises to a greater height with a reduced gap
- The rate of rise is slower with a reduced gap
In fact, the optimum gap maintained, between the parts to be joined is of 0.1 mm.
The strength of typically brazed joint varies with thickness of joint in the manner as show in figure below.
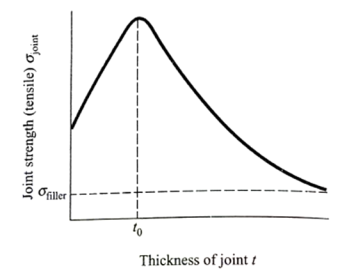
Fig. Variation of strength of brazed joint with joint thickness
From the figure it can be seen that optimum joint thickness exists at which the strength is maximum. For the very large thickness of joint the strength of joint approaches to that of brazing alloy
It can be seen that, maximum joint strength is higher than the filler material. This is because the yield strength of the filer material is lower than the parent material.
Consider the joint be subjected to a tensile load of . With increasing value of
the filler material tends to yield as shown in figure:
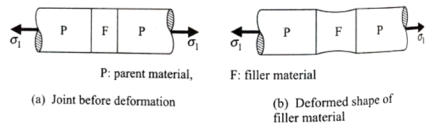
Fig. The resulting deformation is shown in fig b.
The yield strength of a filler alloy is determined by uniaxial test, when the deformed shape of rectangular specimen ABCD takes the shape A’B’C’D’ (shown in fig c). If AD and BC are considered as the P-F interfaces, then in the presence of the parent material, the deformed shape of the same specimen takes the shape A’’B’’C’’D’’.
The deformed shape A’’B’’C’’D’’ can be obtained from ABCD by simultaneous application of constant tensile stress on the faces AD and BC, together with the application of varying lateral tensile stress
on the faces AB and CD. The magnitude of lateral stress
is maximum at A and B with minimum of
occurring at the midpoint of AB.
Now, as is increased, the joint fails at the midpoint of AB. Using the maximum shear stress theory, we find the joint fails if

Or the strength of the joint

Above equation clearly shows that, is greater than
. As the joint thickness increases,
tends to zero and
approaches the value of
If an assembly is to be permanently welded, the following guidelines should be followed by designer
- Design for welding: The most primary guideline is that the product should be designed from the beginning as a welded assembly however no longer as a casting or forging or other formed shape.
- Minimum parts: Welded assemblies must include of the minimal quantity of parts possible. For example, it is generally more economical to carry out simple bending operations on a part instead to weld an assembly from flat plates and sheets.
The following design considerations apply to arc welding:
- Good fit-up of parts to be welded is very important to maintain dimensional control and minimize distortion. Machining is few times needed to achieve satisfactory fit-up.
- The assembly must have access room to allow the welding gun to reach the welding area
- Whenever possible, design of the assembly must enable flat welding to be performed, as this is the quickest and most feasible welding position. The possible welding positions are defined in Figure below. The overhead position is the most difficult.
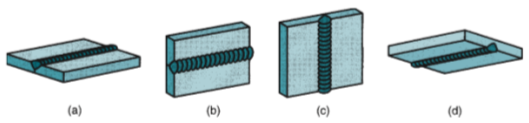
Figure. Welding positions (defined here for groove welds): (a) flat, (b) horizontal, (c) vertical, and (d) overhead.
The following design guidelines apply to resistance spot welding:
- Low-carbon sheet steel up to 3.2 mm is the ideal metal for resistance spot welding.
- Additional strength and stiffness may be received in large flat sheet metallic components by: (a) spot welding reinforcing parts into them, or (b) forming flanges and embossments into them.
- The spot-welded assembly need to offer access for the electrodes to attain the welding area.
- Sufficient overlap of the sheet-metal parts should be required for the electrode tip to make proper contact in spot welding.
Solid and liquid state joining process is referred to the joining process in which filler metal is melted or is in liquid state and is used for to create a bond between two solid metals.
Three different processes which are brazing, soldering and adhesive bonding are included in solid and liquid state joining process. The physical phenomenon associated with each of these processes is same but differ only in the metallurgical aspect. In these processes, the bulk material is not melted. A molten filler metal is used to provide a joint. The working temperature of these process is generally below the melting point of the base or parent metal.
Adhesive bonding is referred to a joining process where a filler material is used to hold two or more than two closely spaced parts together via means of a surface attachment. The filler material which helps in binding of these parts together is the referred to as adhesive. Adhesive is a nonmetallic substance, generally a polymer. Adherends are the parts that are being joined together.
A large number of commercially available adhesives are cured by various mechanisms and are suited to the bonding of various materials. Curing is defined as the process where the physical properties of adhesive are changed from a liquid to a solid, generally by chemical reaction, to achieve the surface attachment of the parts. The chemical reaction involves polymerization, condensation, or vulcanization. Curing is often motivated by heat or a catalyst, and pressure is sometimes applied between the two parts to activate the bonding process. If heat is required, the curing temperatures are relatively low, and so the materials being joined are usually unaffected. The curing or hardening of the adhesive requires time, called curing time or setting time. In some cases, setting time is generally significant.
Joint strength in adhesive bonding is determined by the strength of the adhesive itself and the strength of attachment between adhesive and each of the adherends.
Following are the conditions for adhesive bonding
- Surfaces of the adherend must be clean, which means that surfaces should be free of dirt, oil, and oxide films. These things may interfere with accomplishing close contact among adhesive and adherend. For this special preparation of the surfaces is often required.
- In the initial liquid form, the adhesive should achieve thorough wetting of the adherend surface.
- The surfaces must not be perfectly smooth. Slightly roughened surface maximizes the effective contact area and it promotes mechanical interlocking.
References:
1. Kalpakjian and Schmid, Manufacturing processes for engineering materials (5th Edition)- Pearson India, 2014.
2. Mikell P. Groover, Fundamentals of Modern Manufacturing: Materials, Processes, and Systems.
3. Manufacturing Technology by P.N. Rao., MCGRAW HILL INDIA.
4. Materials and Manufacturing by Paul Degarmo.
5. Manufacturing Processes by Kaushish, PHI.
Unit - 4
Joining/Fastening Processes
The process of joining two similar or dissimilar materials is referred as joining process. The joining process is referred as fastening process, when there is the use of fasteners to joint them.
The term ‘joining’ is mainly used for welding, brazing, soldering, and adhesive bonding that form a permanent or a temporary joint between the parts. Permanent joint is referred to a joint that cannot easily be separated while temporary joint is the joint that can be easily separated when required.
The joining process can be divided into a liquid state joining or a solid-state joining process.
These processes are primarily used for the assembly of the machine to join various parts either permanently or temporarily.
Joining process generally contains the processes like welding, brazing, soldering, fastening, adhesive bonding, etc.
Welding process is the most widely used process for a permanent joint. While fastening process is most widely used process for temporary joint.
Fastening process can be divided into three types:
- Permanent mechanical fastening: When the joint required is permanent, then these fastening processes are used. It includes riveting, flanging, staking, stapling, crimping, seaming etc.
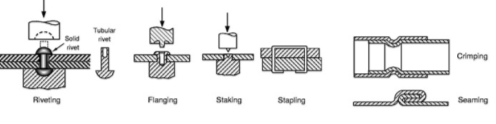
b. Semi-permanent fastening process: It includes snap fit, Blind rivet, press fit, etc.
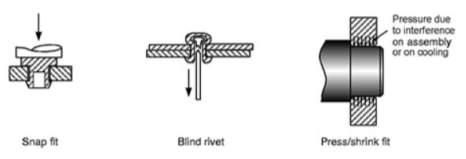
c. Non-permanent fastening process: When the joint required is temporary, then non-permanent fastening process is used. It includes Retaining, self-tapping, nut-bolt assembly, etc.
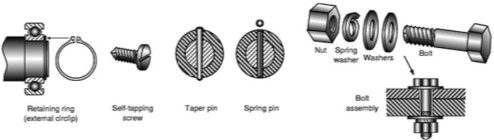
Welding is referred a material joining process where two or more parts are joined at their contacting surfaces through appropriate application of heat and pressure. Most of the welding processes are achieved via means of heat alone or with pressure alone. In few welding processes, filler material is introduced to facilitate bonding. The assemblage of elements which are joined by welding is known as weldment. Welding is most commonly related to metal parts, whereas the process is additionally used for joining plastics.
Advantages of welding:
- Welding provides a permanent joint and hence welded parts become a single entity.
- Welding is the most cost-efficient way to join components in terms of material utilization and fabrication costs.
- The welded joint may have more potential (simply may be stronger) compared to the parent materials if a filler metal is used which has strength properties that are superior to that of parents. For this proper welding techniques must be used.
- Welding is not limited to the factory environment and can be achieved in the field.
Limitations of welding:
- Many welding processes involve the use of high energy and hence are very dangerous.
- Since welding accomplishes a everlasting bond among the components, it does not permit for handy disassembly. If the product is to be disassembled (example, for repair or maintenance), then welding must not be used as the assembly approach.
- Many welding operations are performed manually and are expensive for labor cost. Many welding operations are considered ‘‘skilled trades,’’ and the labor to perform these operations may be less.
- The welded joint may suffer from specific quality defects that are hard to detect. These defects can reduce the strength of the joint.
Welding processes are divided into two major groups:
(1) fusion welding (liquid-state welding) and (2) solid-state welding.
Fusion Welding Process:
Fusion-welding processes make use of heat to melt the parent metals. In most of fusion welding operations, a filler metal is introduced to accelerate the process and offer strength to the welded joint. When there is no filler metal added, in a fusion-welding operation, is termed as an autogenous weld. The fusion category contains the most globally used welding processes that can be divided into the following types:
- Arc-welding: Arc welding is welding processes where heating of the metals is achieved by an electric arc. Few arc welding processes also apply pressure at the time of the process and most of them make use of a filler metal.
- Resistance welding: Resistance welding achieves bonding by using heat from electrical resistance to the flow of a current passing among the faying surfaces of two elements held collectively under pressure.
- Oxyfuel gas welding: These joining processes uses an oxyfuel gas, like a mixture of oxygen and acetylene, to create a hot flame for melting the parent metal and filler metal.
Solid State Welding Process:
Solid-state welding is a joining processes where joint results through application of pressure alone or by a mixture of heat and pressure. If heat is used for welding, the temperature in the operation is below the melting point of the metals that are being welded. There is no use of filler metal in solid state welding. Solid state welding is categorized into following types:
- Diffusion welding: When two surfaces are held together under pressure at an elevated temperature and the parts are joined then the welding process is termed by solid-state diffusion.
- Friction welding: Joint is achieved by the heat of friction between two surfaces.
- Ultrasonic welding: Moderate pressure is applied between the two parts and an oscillating motion at ultrasonic frequencies is used for welding. The direction of ultrasonic frequencies is parallel to the contacting surfaces. The combination of normal forces along with the vibratory forces leads to shear stresses which remove surface films and acquire atomic bonding of the surfaces.
Physics of Welding:
Many bonding mechanisms are available for welding, but fusion welding is the most widely used welding operation.
In order to achieve fusion, high density of heat energy source is applied on the saying surfaces. The leading temperatures are enough to cause local melting of the parent metals. The heat density should be sufficient enough to melt the filler material, if added.
Heat density can be referred as power transferred to the work per unit of the surface area.
Power density is given by,

Where,
P is the power entering the surface.
A is the surface area in which power is entering
The time required to melt the metal is inversely proportional to the power density. The minimum power density require to melt the metal in general welding processes is found to be 10 W/mm2
The approximate power densities required for different welding processes is given in the table below:
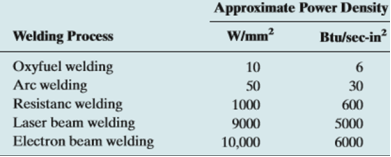
The quantity of heat needed to melt a given volume of metal is dependent on the following factors:
- The heat to increase the temperature to the melting point of the solid metal. This depends on the volumetric specific heat of the metal
- Metal’s melting point
- The heat to convert the metal at the melting point from solid to liquid phase. This depends on the heat of fusion of metal.
The unit energy for melting () is defined as the quantity of heat required to melt a unit volume of metal that starts from room temperature.
It is given by,

Where,
is the melting point of an metal in kelvin
K is the constant with value; K = 3.33 x 10-6
All this energy that is associated with heat source is not used to melt the metal. Some amount of heat is lost during the transfer of heat from source and to the workpiece, while some amount of heat is lost by dissipating heat into the work metal. This is shown in the figure below:
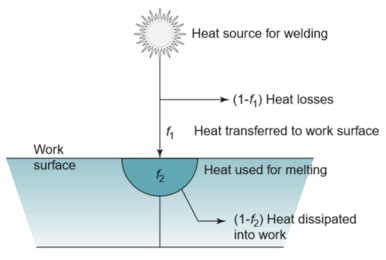
Heat transfer factor is defined as the ratio of the original heat received by the workpiece to the total heat generated at the source. It is denoted by .
Melting factor is defined as the heat used for welding to the heat received at the workpiece. It is denoted by .
Hence, heat available at welding is given by,

Where,
is the net heat available for welding process
H is total heat generated at the source of heat.
The balance equation which gives relation between energy input and energy required for welding is

Where, V is the volume of metal melted.
Brazing
Brazing is a joining process where a filler metal is melted and disbursed through a capillary action among the two surfaces of the metal parts to be joined. Here, the distance between two mating surfaces is very less. Melting of the base metals doesn’t occur in brazing. In brazing only the filler material is melted. In brazing the filler metal (also called the brazing metal), has a melting temperature that is above 450oC but below the melting point of the base metals to be joined. The brazed joint is much stronger compared to the filler metal from which it has been created upon solidification. This is because of the less part clearances used in brazing. The other reasons for stronger brazed bond is the metallurgical bonding that takes place among base and filler metals as well as the geometric constrictions which are imposed at the joint via base parts.
Advantages of Brazing
- Some brazing methods may be performed fastly and consistently, hence allowing high cycle rates and automated production
- Brazing can be used to join thin-walled parts which cant be welded
- Any metals may be joined, including dissimilar metals
- Problems with the heat-affected zone in the base metal near the joint are reduced.
- Some methods enable multiple joints to be brazed simultaneously;
- In general, less heat and power are required than in fusion welding
Limitation of Brazing:
- High service temperatures may weaken a brazed joint
- Although strength of a good brazed joint is greater than that of the filler metal, it is usually to be less compared to that of the base metals
- Joint strength is usually less compared to a welded joint
Soldering
Soldering is similar to brazing and can be defined as a joining process in which a filler metal, with melting point below 450oC, is melted and disbursed through capillary action among two surfaces of the metal parts to be joined. Similar to brazing, melting of the parent metals doesn’t occur but the filler metal is melted and it combines with the parent metal creating a metallurgical bond. Surfaces to be soldered should be pre-cleaned. This is done such that they are free of oxides, oils, etc. Proper flux should be applied to the soldering surfaces when the surfaces are heated. Filler metal, known as solder is added to the joint that disburses itself within the closely fitting parts of two materials. In industry, soldering is very closely connected to the electronics assembly.
Advantages of soldering:
- It requires low energy input relative to brazing and fusion welding
- Variety of heating methods are available
- It gives good electrical and thermal conductivity in the joint
- It has capability to make air-tight and liquid-tight seams for containers
- It is easy to repair and rework.
Limitations of soldering:
- Soldered joint has low joint strength unless reinforced by mechanically means.
- It can have possible weakening or melting of the joint in elevated temperature service.
Physics of Brazing and soldering:
The brazing and soldering processes are carried out by allowing a molten filler material to flow in the gap between the parent bodies.
To produce the perfect joint, the entire gap between the parent bodies must be filled by the filler material. This is achieved through the capillary action.
The theory of capillary flow tells us
- The liquid drop rises to a greater height with a reduced gap
- The rate of rise is slower with a reduced gap
In fact, the optimum gap maintained, between the parts to be joined is of 0.1 mm.
The strength of typically brazed joint varies with thickness of joint in the manner as show in figure below.
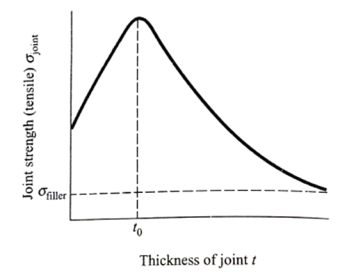
Fig. Variation of strength of brazed joint with joint thickness
From the figure it can be seen that optimum joint thickness exists at which the strength is maximum. For the very large thickness of joint the strength of joint approaches to that of brazing alloy
It can be seen that, maximum joint strength is higher than the filler material. This is because the yield strength of the filer material is lower than the parent material.
Consider the joint be subjected to a tensile load of . With increasing value of
the filler material tends to yield as shown in figure:

Fig. The resulting deformation is shown in fig b.
The yield strength of a filler alloy is determined by uniaxial test, when the deformed shape of rectangular specimen ABCD takes the shape A’B’C’D’ (shown in fig c). If AD and BC are considered as the P-F interfaces, then in the presence of the parent material, the deformed shape of the same specimen takes the shape A’’B’’C’’D’’.
The deformed shape A’’B’’C’’D’’ can be obtained from ABCD by simultaneous application of constant tensile stress on the faces AD and BC, together with the application of varying lateral tensile stress
on the faces AB and CD. The magnitude of lateral stress
is maximum at A and B with minimum of
occurring at the midpoint of AB.
Now, as is increased, the joint fails at the midpoint of AB. Using the maximum shear stress theory, we find the joint fails if

Or the strength of the joint

Above equation clearly shows that, is greater than
. As the joint thickness increases,
tends to zero and
approaches the value of
If an assembly is to be permanently welded, the following guidelines should be followed by designer
- Design for welding: The most primary guideline is that the product should be designed from the beginning as a welded assembly however no longer as a casting or forging or other formed shape.
- Minimum parts: Welded assemblies must include of the minimal quantity of parts possible. For example, it is generally more economical to carry out simple bending operations on a part instead to weld an assembly from flat plates and sheets.
The following design considerations apply to arc welding:
- Good fit-up of parts to be welded is very important to maintain dimensional control and minimize distortion. Machining is few times needed to achieve satisfactory fit-up.
- The assembly must have access room to allow the welding gun to reach the welding area
- Whenever possible, design of the assembly must enable flat welding to be performed, as this is the quickest and most feasible welding position. The possible welding positions are defined in Figure below. The overhead position is the most difficult.
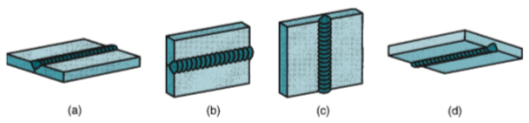
Figure. Welding positions (defined here for groove welds): (a) flat, (b) horizontal, (c) vertical, and (d) overhead.
The following design guidelines apply to resistance spot welding:
- Low-carbon sheet steel up to 3.2 mm is the ideal metal for resistance spot welding.
- Additional strength and stiffness may be received in large flat sheet metallic components by: (a) spot welding reinforcing parts into them, or (b) forming flanges and embossments into them.
- The spot-welded assembly need to offer access for the electrodes to attain the welding area.
- Sufficient overlap of the sheet-metal parts should be required for the electrode tip to make proper contact in spot welding.
Solid and liquid state joining process is referred to the joining process in which filler metal is melted or is in liquid state and is used for to create a bond between two solid metals.
Three different processes which are brazing, soldering and adhesive bonding are included in solid and liquid state joining process. The physical phenomenon associated with each of these processes is same but differ only in the metallurgical aspect. In these processes, the bulk material is not melted. A molten filler metal is used to provide a joint. The working temperature of these process is generally below the melting point of the base or parent metal.
Adhesive bonding is referred to a joining process where a filler material is used to hold two or more than two closely spaced parts together via means of a surface attachment. The filler material which helps in binding of these parts together is the referred to as adhesive. Adhesive is a nonmetallic substance, generally a polymer. Adherends are the parts that are being joined together.
A large number of commercially available adhesives are cured by various mechanisms and are suited to the bonding of various materials. Curing is defined as the process where the physical properties of adhesive are changed from a liquid to a solid, generally by chemical reaction, to achieve the surface attachment of the parts. The chemical reaction involves polymerization, condensation, or vulcanization. Curing is often motivated by heat or a catalyst, and pressure is sometimes applied between the two parts to activate the bonding process. If heat is required, the curing temperatures are relatively low, and so the materials being joined are usually unaffected. The curing or hardening of the adhesive requires time, called curing time or setting time. In some cases, setting time is generally significant.
Joint strength in adhesive bonding is determined by the strength of the adhesive itself and the strength of attachment between adhesive and each of the adherends.
Following are the conditions for adhesive bonding
- Surfaces of the adherend must be clean, which means that surfaces should be free of dirt, oil, and oxide films. These things may interfere with accomplishing close contact among adhesive and adherend. For this special preparation of the surfaces is often required.
- In the initial liquid form, the adhesive should achieve thorough wetting of the adherend surface.
- The surfaces must not be perfectly smooth. Slightly roughened surface maximizes the effective contact area and it promotes mechanical interlocking.
References:
1. Kalpakjian and Schmid, Manufacturing processes for engineering materials (5th Edition)- Pearson India, 2014.
2. Mikell P. Groover, Fundamentals of Modern Manufacturing: Materials, Processes, and Systems.
3. Manufacturing Technology by P.N. Rao., MCGRAW HILL INDIA.
4. Materials and Manufacturing by Paul Degarmo.
5. Manufacturing Processes by Kaushish, PHI.
Unit - 4
Joining/Fastening Processes
Unit - 4
Joining/Fastening Processes
The process of joining two similar or dissimilar materials is referred as joining process. The joining process is referred as fastening process, when there is the use of fasteners to joint them.
The term ‘joining’ is mainly used for welding, brazing, soldering, and adhesive bonding that form a permanent or a temporary joint between the parts. Permanent joint is referred to a joint that cannot easily be separated while temporary joint is the joint that can be easily separated when required.
The joining process can be divided into a liquid state joining or a solid-state joining process.
These processes are primarily used for the assembly of the machine to join various parts either permanently or temporarily.
Joining process generally contains the processes like welding, brazing, soldering, fastening, adhesive bonding, etc.
Welding process is the most widely used process for a permanent joint. While fastening process is most widely used process for temporary joint.
Fastening process can be divided into three types:
- Permanent mechanical fastening: When the joint required is permanent, then these fastening processes are used. It includes riveting, flanging, staking, stapling, crimping, seaming etc.
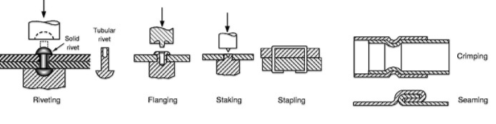
b. Semi-permanent fastening process: It includes snap fit, Blind rivet, press fit, etc.
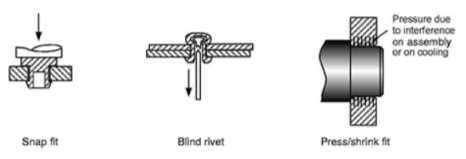
c. Non-permanent fastening process: When the joint required is temporary, then non-permanent fastening process is used. It includes Retaining, self-tapping, nut-bolt assembly, etc.
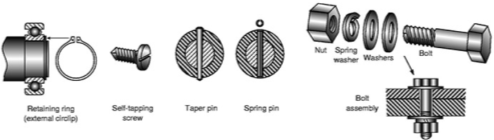
Welding is referred a material joining process where two or more parts are joined at their contacting surfaces through appropriate application of heat and pressure. Most of the welding processes are achieved via means of heat alone or with pressure alone. In few welding processes, filler material is introduced to facilitate bonding. The assemblage of elements which are joined by welding is known as weldment. Welding is most commonly related to metal parts, whereas the process is additionally used for joining plastics.
Advantages of welding:
- Welding provides a permanent joint and hence welded parts become a single entity.
- Welding is the most cost-efficient way to join components in terms of material utilization and fabrication costs.
- The welded joint may have more potential (simply may be stronger) compared to the parent materials if a filler metal is used which has strength properties that are superior to that of parents. For this proper welding techniques must be used.
- Welding is not limited to the factory environment and can be achieved in the field.
Limitations of welding:
- Many welding processes involve the use of high energy and hence are very dangerous.
- Since welding accomplishes a everlasting bond among the components, it does not permit for handy disassembly. If the product is to be disassembled (example, for repair or maintenance), then welding must not be used as the assembly approach.
- Many welding operations are performed manually and are expensive for labor cost. Many welding operations are considered ‘‘skilled trades,’’ and the labor to perform these operations may be less.
- The welded joint may suffer from specific quality defects that are hard to detect. These defects can reduce the strength of the joint.
Welding processes are divided into two major groups:
(1) fusion welding (liquid-state welding) and (2) solid-state welding.
Fusion Welding Process:
Fusion-welding processes make use of heat to melt the parent metals. In most of fusion welding operations, a filler metal is introduced to accelerate the process and offer strength to the welded joint. When there is no filler metal added, in a fusion-welding operation, is termed as an autogenous weld. The fusion category contains the most globally used welding processes that can be divided into the following types:
- Arc-welding: Arc welding is welding processes where heating of the metals is achieved by an electric arc. Few arc welding processes also apply pressure at the time of the process and most of them make use of a filler metal.
- Resistance welding: Resistance welding achieves bonding by using heat from electrical resistance to the flow of a current passing among the faying surfaces of two elements held collectively under pressure.
- Oxyfuel gas welding: These joining processes uses an oxyfuel gas, like a mixture of oxygen and acetylene, to create a hot flame for melting the parent metal and filler metal.
Solid State Welding Process:
Solid-state welding is a joining processes where joint results through application of pressure alone or by a mixture of heat and pressure. If heat is used for welding, the temperature in the operation is below the melting point of the metals that are being welded. There is no use of filler metal in solid state welding. Solid state welding is categorized into following types:
- Diffusion welding: When two surfaces are held together under pressure at an elevated temperature and the parts are joined then the welding process is termed by solid-state diffusion.
- Friction welding: Joint is achieved by the heat of friction between two surfaces.
- Ultrasonic welding: Moderate pressure is applied between the two parts and an oscillating motion at ultrasonic frequencies is used for welding. The direction of ultrasonic frequencies is parallel to the contacting surfaces. The combination of normal forces along with the vibratory forces leads to shear stresses which remove surface films and acquire atomic bonding of the surfaces.
Physics of Welding:
Many bonding mechanisms are available for welding, but fusion welding is the most widely used welding operation.
In order to achieve fusion, high density of heat energy source is applied on the saying surfaces. The leading temperatures are enough to cause local melting of the parent metals. The heat density should be sufficient enough to melt the filler material, if added.
Heat density can be referred as power transferred to the work per unit of the surface area.
Power density is given by,

Where,
P is the power entering the surface.
A is the surface area in which power is entering
The time required to melt the metal is inversely proportional to the power density. The minimum power density require to melt the metal in general welding processes is found to be 10 W/mm2
The approximate power densities required for different welding processes is given in the table below:
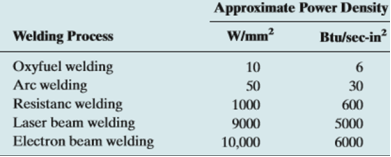
The quantity of heat needed to melt a given volume of metal is dependent on the following factors:
- The heat to increase the temperature to the melting point of the solid metal. This depends on the volumetric specific heat of the metal
- Metal’s melting point
- The heat to convert the metal at the melting point from solid to liquid phase. This depends on the heat of fusion of metal.
The unit energy for melting () is defined as the quantity of heat required to melt a unit volume of metal that starts from room temperature.
It is given by,

Where,
is the melting point of an metal in kelvin
K is the constant with value; K = 3.33 x 10-6
All this energy that is associated with heat source is not used to melt the metal. Some amount of heat is lost during the transfer of heat from source and to the workpiece, while some amount of heat is lost by dissipating heat into the work metal. This is shown in the figure below:
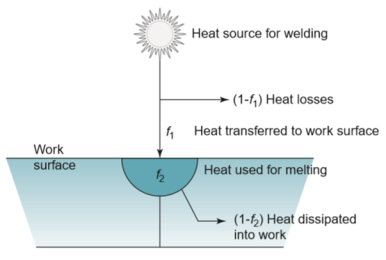
Heat transfer factor is defined as the ratio of the original heat received by the workpiece to the total heat generated at the source. It is denoted by .
Melting factor is defined as the heat used for welding to the heat received at the workpiece. It is denoted by .
Hence, heat available at welding is given by,

Where,
is the net heat available for welding process
H is total heat generated at the source of heat.
The balance equation which gives relation between energy input and energy required for welding is

Where, V is the volume of metal melted.
Unit - 4
Joining/Fastening Processes
The process of joining two similar or dissimilar materials is referred as joining process. The joining process is referred as fastening process, when there is the use of fasteners to joint them.
The term ‘joining’ is mainly used for welding, brazing, soldering, and adhesive bonding that form a permanent or a temporary joint between the parts. Permanent joint is referred to a joint that cannot easily be separated while temporary joint is the joint that can be easily separated when required.
The joining process can be divided into a liquid state joining or a solid-state joining process.
These processes are primarily used for the assembly of the machine to join various parts either permanently or temporarily.
Joining process generally contains the processes like welding, brazing, soldering, fastening, adhesive bonding, etc.
Welding process is the most widely used process for a permanent joint. While fastening process is most widely used process for temporary joint.
Fastening process can be divided into three types:
- Permanent mechanical fastening: When the joint required is permanent, then these fastening processes are used. It includes riveting, flanging, staking, stapling, crimping, seaming etc.
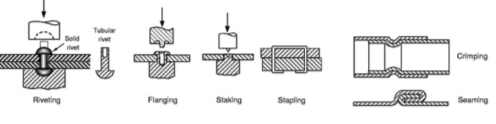
b. Semi-permanent fastening process: It includes snap fit, Blind rivet, press fit, etc.
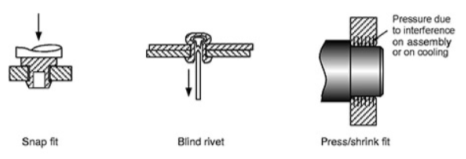
c. Non-permanent fastening process: When the joint required is temporary, then non-permanent fastening process is used. It includes Retaining, self-tapping, nut-bolt assembly, etc.
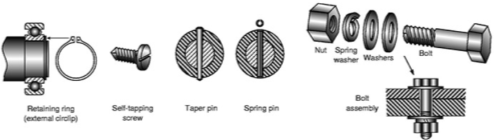
Welding is referred a material joining process where two or more parts are joined at their contacting surfaces through appropriate application of heat and pressure. Most of the welding processes are achieved via means of heat alone or with pressure alone. In few welding processes, filler material is introduced to facilitate bonding. The assemblage of elements which are joined by welding is known as weldment. Welding is most commonly related to metal parts, whereas the process is additionally used for joining plastics.
Advantages of welding:
- Welding provides a permanent joint and hence welded parts become a single entity.
- Welding is the most cost-efficient way to join components in terms of material utilization and fabrication costs.
- The welded joint may have more potential (simply may be stronger) compared to the parent materials if a filler metal is used which has strength properties that are superior to that of parents. For this proper welding techniques must be used.
- Welding is not limited to the factory environment and can be achieved in the field.
Limitations of welding:
- Many welding processes involve the use of high energy and hence are very dangerous.
- Since welding accomplishes a everlasting bond among the components, it does not permit for handy disassembly. If the product is to be disassembled (example, for repair or maintenance), then welding must not be used as the assembly approach.
- Many welding operations are performed manually and are expensive for labor cost. Many welding operations are considered ‘‘skilled trades,’’ and the labor to perform these operations may be less.
- The welded joint may suffer from specific quality defects that are hard to detect. These defects can reduce the strength of the joint.
Welding processes are divided into two major groups:
(1) fusion welding (liquid-state welding) and (2) solid-state welding.
Fusion Welding Process:
Fusion-welding processes make use of heat to melt the parent metals. In most of fusion welding operations, a filler metal is introduced to accelerate the process and offer strength to the welded joint. When there is no filler metal added, in a fusion-welding operation, is termed as an autogenous weld. The fusion category contains the most globally used welding processes that can be divided into the following types:
- Arc-welding: Arc welding is welding processes where heating of the metals is achieved by an electric arc. Few arc welding processes also apply pressure at the time of the process and most of them make use of a filler metal.
- Resistance welding: Resistance welding achieves bonding by using heat from electrical resistance to the flow of a current passing among the faying surfaces of two elements held collectively under pressure.
- Oxyfuel gas welding: These joining processes uses an oxyfuel gas, like a mixture of oxygen and acetylene, to create a hot flame for melting the parent metal and filler metal.
Solid State Welding Process:
Solid-state welding is a joining processes where joint results through application of pressure alone or by a mixture of heat and pressure. If heat is used for welding, the temperature in the operation is below the melting point of the metals that are being welded. There is no use of filler metal in solid state welding. Solid state welding is categorized into following types:
- Diffusion welding: When two surfaces are held together under pressure at an elevated temperature and the parts are joined then the welding process is termed by solid-state diffusion.
- Friction welding: Joint is achieved by the heat of friction between two surfaces.
- Ultrasonic welding: Moderate pressure is applied between the two parts and an oscillating motion at ultrasonic frequencies is used for welding. The direction of ultrasonic frequencies is parallel to the contacting surfaces. The combination of normal forces along with the vibratory forces leads to shear stresses which remove surface films and acquire atomic bonding of the surfaces.
Physics of Welding:
Many bonding mechanisms are available for welding, but fusion welding is the most widely used welding operation.
In order to achieve fusion, high density of heat energy source is applied on the saying surfaces. The leading temperatures are enough to cause local melting of the parent metals. The heat density should be sufficient enough to melt the filler material, if added.
Heat density can be referred as power transferred to the work per unit of the surface area.
Power density is given by,

Where,
P is the power entering the surface.
A is the surface area in which power is entering
The time required to melt the metal is inversely proportional to the power density. The minimum power density require to melt the metal in general welding processes is found to be 10 W/mm2
The approximate power densities required for different welding processes is given in the table below:
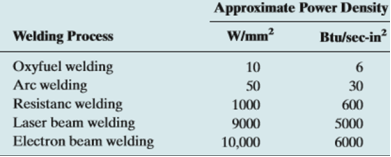
The quantity of heat needed to melt a given volume of metal is dependent on the following factors:
- The heat to increase the temperature to the melting point of the solid metal. This depends on the volumetric specific heat of the metal
- Metal’s melting point
- The heat to convert the metal at the melting point from solid to liquid phase. This depends on the heat of fusion of metal.
The unit energy for melting () is defined as the quantity of heat required to melt a unit volume of metal that starts from room temperature.
It is given by,

Where,
is the melting point of an metal in kelvin
K is the constant with value; K = 3.33 x 10-6
All this energy that is associated with heat source is not used to melt the metal. Some amount of heat is lost during the transfer of heat from source and to the workpiece, while some amount of heat is lost by dissipating heat into the work metal. This is shown in the figure below:
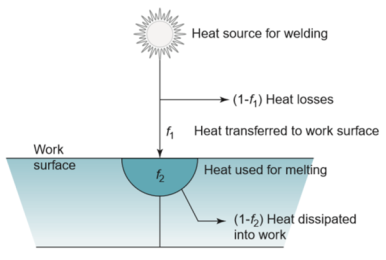
Heat transfer factor is defined as the ratio of the original heat received by the workpiece to the total heat generated at the source. It is denoted by .
Melting factor is defined as the heat used for welding to the heat received at the workpiece. It is denoted by .
Hence, heat available at welding is given by,

Where,
is the net heat available for welding process
H is total heat generated at the source of heat.
The balance equation which gives relation between energy input and energy required for welding is

Where, V is the volume of metal melted.
Brazing
Brazing is a joining process where a filler metal is melted and disbursed through a capillary action among the two surfaces of the metal parts to be joined. Here, the distance between two mating surfaces is very less. Melting of the base metals doesn’t occur in brazing. In brazing only the filler material is melted. In brazing the filler metal (also called the brazing metal), has a melting temperature that is above 450oC but below the melting point of the base metals to be joined. The brazed joint is much stronger compared to the filler metal from which it has been created upon solidification. This is because of the less part clearances used in brazing. The other reasons for stronger brazed bond is the metallurgical bonding that takes place among base and filler metals as well as the geometric constrictions which are imposed at the joint via base parts.
Advantages of Brazing
- Some brazing methods may be performed fastly and consistently, hence allowing high cycle rates and automated production
- Brazing can be used to join thin-walled parts which cant be welded
- Any metals may be joined, including dissimilar metals
- Problems with the heat-affected zone in the base metal near the joint are reduced.
- Some methods enable multiple joints to be brazed simultaneously;
- In general, less heat and power are required than in fusion welding
Limitation of Brazing:
- High service temperatures may weaken a brazed joint
- Although strength of a good brazed joint is greater than that of the filler metal, it is usually to be less compared to that of the base metals
- Joint strength is usually less compared to a welded joint
Soldering
Soldering is similar to brazing and can be defined as a joining process in which a filler metal, with melting point below 450oC, is melted and disbursed through capillary action among two surfaces of the metal parts to be joined. Similar to brazing, melting of the parent metals doesn’t occur but the filler metal is melted and it combines with the parent metal creating a metallurgical bond. Surfaces to be soldered should be pre-cleaned. This is done such that they are free of oxides, oils, etc. Proper flux should be applied to the soldering surfaces when the surfaces are heated. Filler metal, known as solder is added to the joint that disburses itself within the closely fitting parts of two materials. In industry, soldering is very closely connected to the electronics assembly.
Advantages of soldering:
- It requires low energy input relative to brazing and fusion welding
- Variety of heating methods are available
- It gives good electrical and thermal conductivity in the joint
- It has capability to make air-tight and liquid-tight seams for containers
- It is easy to repair and rework.
Limitations of soldering:
- Soldered joint has low joint strength unless reinforced by mechanically means.
- It can have possible weakening or melting of the joint in elevated temperature service.
Physics of Brazing and soldering:
The brazing and soldering processes are carried out by allowing a molten filler material to flow in the gap between the parent bodies.
To produce the perfect joint, the entire gap between the parent bodies must be filled by the filler material. This is achieved through the capillary action.
The theory of capillary flow tells us
- The liquid drop rises to a greater height with a reduced gap
- The rate of rise is slower with a reduced gap
In fact, the optimum gap maintained, between the parts to be joined is of 0.1 mm.
The strength of typically brazed joint varies with thickness of joint in the manner as show in figure below.
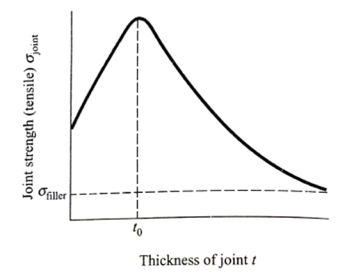
Fig. Variation of strength of brazed joint with joint thickness
From the figure it can be seen that optimum joint thickness exists at which the strength is maximum. For the very large thickness of joint the strength of joint approaches to that of brazing alloy
It can be seen that, maximum joint strength is higher than the filler material. This is because the yield strength of the filer material is lower than the parent material.
Consider the joint be subjected to a tensile load of . With increasing value of
the filler material tends to yield as shown in figure:
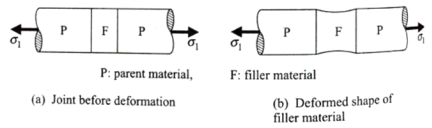
Fig. The resulting deformation is shown in fig b.
The yield strength of a filler alloy is determined by uniaxial test, when the deformed shape of rectangular specimen ABCD takes the shape A’B’C’D’ (shown in fig c). If AD and BC are considered as the P-F interfaces, then in the presence of the parent material, the deformed shape of the same specimen takes the shape A’’B’’C’’D’’.
The deformed shape A’’B’’C’’D’’ can be obtained from ABCD by simultaneous application of constant tensile stress on the faces AD and BC, together with the application of varying lateral tensile stress
on the faces AB and CD. The magnitude of lateral stress
is maximum at A and B with minimum of
occurring at the midpoint of AB.
Now, as is increased, the joint fails at the midpoint of AB. Using the maximum shear stress theory, we find the joint fails if

Or the strength of the joint

Above equation clearly shows that, is greater than
. As the joint thickness increases,
tends to zero and
approaches the value of
If an assembly is to be permanently welded, the following guidelines should be followed by designer
- Design for welding: The most primary guideline is that the product should be designed from the beginning as a welded assembly however no longer as a casting or forging or other formed shape.
- Minimum parts: Welded assemblies must include of the minimal quantity of parts possible. For example, it is generally more economical to carry out simple bending operations on a part instead to weld an assembly from flat plates and sheets.
The following design considerations apply to arc welding:
- Good fit-up of parts to be welded is very important to maintain dimensional control and minimize distortion. Machining is few times needed to achieve satisfactory fit-up.
- The assembly must have access room to allow the welding gun to reach the welding area
- Whenever possible, design of the assembly must enable flat welding to be performed, as this is the quickest and most feasible welding position. The possible welding positions are defined in Figure below. The overhead position is the most difficult.
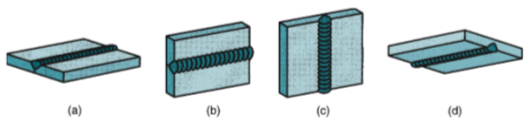
Figure. Welding positions (defined here for groove welds): (a) flat, (b) horizontal, (c) vertical, and (d) overhead.
The following design guidelines apply to resistance spot welding:
- Low-carbon sheet steel up to 3.2 mm is the ideal metal for resistance spot welding.
- Additional strength and stiffness may be received in large flat sheet metallic components by: (a) spot welding reinforcing parts into them, or (b) forming flanges and embossments into them.
- The spot-welded assembly need to offer access for the electrodes to attain the welding area.
- Sufficient overlap of the sheet-metal parts should be required for the electrode tip to make proper contact in spot welding.
Solid and liquid state joining process is referred to the joining process in which filler metal is melted or is in liquid state and is used for to create a bond between two solid metals.
Three different processes which are brazing, soldering and adhesive bonding are included in solid and liquid state joining process. The physical phenomenon associated with each of these processes is same but differ only in the metallurgical aspect. In these processes, the bulk material is not melted. A molten filler metal is used to provide a joint. The working temperature of these process is generally below the melting point of the base or parent metal.
Adhesive bonding is referred to a joining process where a filler material is used to hold two or more than two closely spaced parts together via means of a surface attachment. The filler material which helps in binding of these parts together is the referred to as adhesive. Adhesive is a nonmetallic substance, generally a polymer. Adherends are the parts that are being joined together.
A large number of commercially available adhesives are cured by various mechanisms and are suited to the bonding of various materials. Curing is defined as the process where the physical properties of adhesive are changed from a liquid to a solid, generally by chemical reaction, to achieve the surface attachment of the parts. The chemical reaction involves polymerization, condensation, or vulcanization. Curing is often motivated by heat or a catalyst, and pressure is sometimes applied between the two parts to activate the bonding process. If heat is required, the curing temperatures are relatively low, and so the materials being joined are usually unaffected. The curing or hardening of the adhesive requires time, called curing time or setting time. In some cases, setting time is generally significant.
Joint strength in adhesive bonding is determined by the strength of the adhesive itself and the strength of attachment between adhesive and each of the adherends.
Following are the conditions for adhesive bonding
- Surfaces of the adherend must be clean, which means that surfaces should be free of dirt, oil, and oxide films. These things may interfere with accomplishing close contact among adhesive and adherend. For this special preparation of the surfaces is often required.
- In the initial liquid form, the adhesive should achieve thorough wetting of the adherend surface.
- The surfaces must not be perfectly smooth. Slightly roughened surface maximizes the effective contact area and it promotes mechanical interlocking.
References:
1. Kalpakjian and Schmid, Manufacturing processes for engineering materials (5th Edition)- Pearson India, 2014.
2. Mikell P. Groover, Fundamentals of Modern Manufacturing: Materials, Processes, and Systems.
3. Manufacturing Technology by P.N. Rao., MCGRAW HILL INDIA.
4. Materials and Manufacturing by Paul Degarmo.
5. Manufacturing Processes by Kaushish, PHI.