Unit - 1
Introduction to steel structures
A steel structures is an assemblage of a group of members/elements expected to carry their applied forces and transform them safely to the ground the applied forces may be axial forces, bending or torsion or a combination of those and it depends on orientation of the member. Industrial buildings, some commercial buildings like warehouses, some public buildings like stadiums, transport terminals, bridges of railway lines, various towers are constructed with steel. Now day pre-engineered steel buildings are popular in all countries.
In a pre-engineered building, various components are manufactured in a factory and are erected at a site of construction by which building can be completed very quickly. These buildings are a combination of built-up sections, hot rolled sections and cold formed elements.
This concept provides a complete building envelop system which is air-tight, energy efficient and optimum in weight and cost. These can be used for various purposes such as factories, ware houses, supermarkets and offices.
The design steel structure, civil (structural) engineer plays important role. The design should suit the purpose, safety, economy and durability. Thus, safety is one of the paramount responsibilities of the designer.
However, it is difficult to access safety and economy due to uncertainty about the various factors like (i) uncertainty about loading (ii) uncertainty about material strength and (iii) uncertainty about structural dimensions and behavior. Hence standardization of all designs based on experience is required.
Most governments attempts to ensure structural safety through regulations and laws. Designers then attempts to achieve maximum economy within the range of designs that the regulations allow
Frequently the professions are allowed to regulate themselves; a 'Code of Practices'. IS 800-2007 Code for General Construction in Steel designed and introduced method of limit state design which overcome on working stress method (IS 800-1984).
Two fundamental changes have been made in the version of IS 800-2007 first, the switching over from allowable stress (working stress) design approach to limit state design approach and second, the convention of member axes; the axis along the member length is designated axes as x-x axis the major axis of the section as z-z axis, and the minor axis of the section as y-y axis. (Applicable for beam or I section) For angle section. y-y axis perpendicular to the smaller leg z-z axis parallel to smaller leg in angle section u-u major axis (when it does not coincide with z-z axis). v-v minor axis (when it does to coincide with the y-y axis)
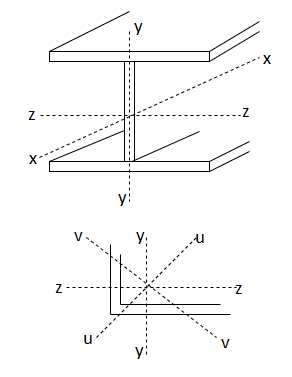
Key takeaways:
- This concept provides a complete building envelop system which is air-tight, energy efficient and optimum in weight and cost.
- These can be used for various purposes such as factories, ware houses, supermarkets and offices.
- The design steel structure, civil (structural) engineer plays important role.
- The design should suit the purpose, safety, economy and durability. Thus, safety is one of the paramount responsibilities of the designer.
1. Advantages:
1) High strength:
Steel members have high strength per unit weight. Therefore, a steel member of a small section can resist heavy loads. This property is applicable for the construction of long-span bridges, tall buildings and for buildings on soils where low bearing capacity of soil.
2) Ductility:
Steel being ductile material does not fail suddenly, but gives visible evidence of impending failure by large deflections.
3) Toughness:
Structural steels are enough tough, so that steel members subjected to large deformations during fabrication and erection will not fracture. Also, the steel may be bent, hammered, sheared or even the bolt holes may be punched without any damage.
4) Prefabrication:
As steel is light in weight, it can be manufactured at the factory and transported at site. This results in speedy construction saving in time and expense, ensuring better quality of finished structures.
5) Durability:
The properties of steel mostly do not change with time. This makes the steel most durable material for a structure.
6) Long life span:
If steel is properly maintained then steel structures have long life span.
7) Demount ability:
The steel structures can be disassembled and reused where ever required.
Recycling Steel is an ultimate recyclable material.
8) Retrofitting and strengthening:
Repairs retrofit and strengthening of steel member is much simple.
9) Addition and alteration:
Addition of any steel member and also alteration can be made easily to steel structures
2. Disadvantages:
1) Cost:
The cost of steel structures for any type of structures is more than the R.C.C structures.
2) Corrosion:
Steel structures are susceptible to corrosion when fully exposed to air and water. Therefore it requires periodic painting, cleaning etc.
3) Fire proof treatment:
Structural steel members are non-combustible but they lose their strength rapidly during fire. Therefore, steel structures require fire proof treatments which increase cost.
4) Fatigue:
Fatigue of steel involves reduction in the strength when steel is subjected to large number of stress reversals and even to a large number of variations of tensile stresses.
5) Aesthetic view:
Steel does not give pleasing appearance unless it is painted.
Key takeaways:
- Steel members have high strength per unit weight. Therefore, a steel member of a small section can resist heavy loads.
- Steel being ductile material does not fail suddenly, but gives visible evidence of impending failure by large deflections
- Structural steel members are non-combustible but they lose their strength rapidly during fire
Stress-Strain Diagram for mild steel (ductile material)
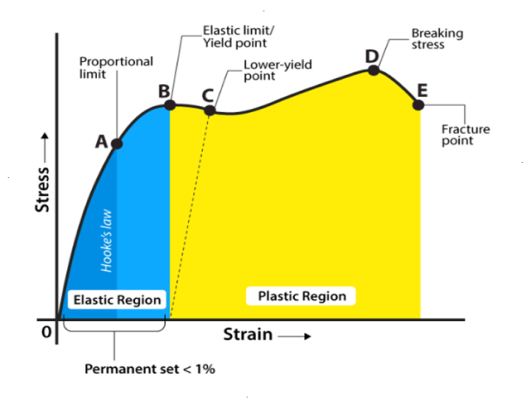
Explaining Stress-Strain Graph
The stress-strain graph has different points or regions as follows:
Proportional limit
Elastic limit
Yield point
Ultimate stress point
Fracture or breaking point
(i) Proportional Limit
It is the region in the stress-strain curve that obeys Hooke’s Law. In this limit, the ratio of stress with strain gives us proportionality constant known as young’s modulus. The point OA in the graph is called the proportional limit.
(ii) Elastic Limit
It is the point in the graph up to which the material returns to its original position when the load acting on it is completely removed. Beyond this limit, the material doesn’t return to its original position and a plastic deformation starts to appear in it.
(iii) Yield Point
The yield point is defined as the point at which the material starts to deform plastically. After the yield point is passed, permanent plastic deformation occurs. There are two yield points (i) upper yield point (ii) lower yield point.
(iv) Ultimate Stress Point
It is a point that represents the maximum stress that a material can endure before failure. Beyond this point, failure occurs.
(v) Fracture or Breaking Point
It is the point in the stress-strain curve at which the failure of the material takes place.
Key takeaways:
- It is the region in the stress-strain curve that obeys Hooke’s Law
- The yield point is defined as the point at which the material starts to deform plastically
- It is the point in the stress-strain curve at which the failure of the material takes place.
The main aim of structural designer is to select the appropriate cross section for individual members of the structure.
This selection is done using widely available standard rolled steel sections which are of any standard. Rolled steel sections manufactured are listed below with designation:
1. Rolled Steel I-section
2. Steel channel Sections
3. Rolled Steel Angle Sections
4. Rolled Steel Tee-sections
5. Steel Plates
6. Rolled Steel Strips
7. Rolled Steel Flats
8. Rolled Steel Bars
1. Rolled steel I section
Following series of rolled steel I sections are manufactured in India:
(a) Indian Standard Junior Beams - ISJB
(b) Indian Standard Light Beams - ISLB
(c) Indian Standard Medium Beams - ISMB
(d) Indian Standard Wide-flange Beams - ISWB
(e) Indian Standard Heavy Beams - ISHB
The above sections are designated by the series to which they belong followed by depth (in mm) and weight (in kg/m) per meter run e.g. ISMB 300@ 44.2 kg/m.
2. Rolled Steel Channel Sections
These sections are classified into the following series:
(a) Indian Standard Junior Channel - ISJC
(b) Indian Standard Light Channel - ISLC
(c) Indian Standard Medium Weight Channel - ISMC
(d) Indian Standard Special Channel - ISSC
Rolled steel channel sections are designated by the series to which they belong, followed by depth (in mm) and weight (in kg/m).
3. Rolled Steel Angle Sections:
These sections are classified into the following series:
(a) Indian Standard Equal Angle - ISA
(b) Indian Standard Unequal Angle - ISA
These sections are designated by series of names ISA followed by length thickness of leg.
4. Rolled steel Tee section:
These sections are classified into following series:
(a) Indian Standard Normal Tee Bars = ISNT
(b) Indian Standard Heavy Flanged Tee Bars = ISHT
(c) Indian Standard Special Legged Tee Bars = ISLT
(d) Indian Standard Light Legged Tee Bars = ISLT
(e) Indian Standard Junior Tee Bars = ISJT
These sections are designated by the series to which they belong, followed by depth (in mm) and weight per meter length (in kg/m) c.g. ISNT 60 @ 5.3 kg/m.
5. Rolled Steel Plates
These plates are classified into the following series.
Indian Standard Plate (ISPL) These plates are designated by ISPL, followed by dimension in mm i.e. length, width and thickness, e.g. ISPL 2000 x 1100 x 8. These are available for various thicknesses (mm) and widths (mm). Thicknesses of plates are more than 5 mm. (t>5 mm).
6. Rolled Steel Strips:
These strips are designated as Indian Standard Strip ISST, followed by width (mm) and thickness (mm) e.g. ISST 160 x 1.4.
Thickness of strips are less than 5 mm (t<5 mm).
7. Rolled Steel Flats:
They are designated by width, followed by Indian standard Flats ISF, and thickness e.g. 50 ISF 5. Flats have thickness more than 5 mm but width is limited (b< 250 mm).
8. Rolled Steel Bars
Rolled steel bars are classified in to following series:
(a) Indian Standard Round Bar (ISRO)
(b) Indian Standard square Bar (ISSQ)
These are designated by ISRO, followed by diameter in case of round bar and ISSQ followed by width e.g. ISRO-12, ISBQ-16.
Key takeaways:
- The main aim of structural designer is to select the appropriate cross section for individual members of the structure.
- This selection is done using widely available standard rolled steel sections which are of any standard.
- Thickness of strips are less than 5 mm (t<5 mm).
- Indian Standard Plate (ISPL) These plates are designated by ISPL, followed by dimension in mm i.e. length, width and thickness
The provisions in this section are applicable to the steels commonly used in steel construction, namely, structural mild steel and high tensile structural steel.
All the structural steel used in general construction, coming under the purview of this standard shall before fabrication conform to IS 2062.
Structural steel other than those specified may also be used provided that the permissible stresses and other design provisions are suitably modified and the steel is also suitable for the type of fabrication adopted.
Unless otherwise specified convention used for member axes is as follows (see Fig. 1):
a) x-x along the member.
b) y-y an axis of the cross-section.
1) Perpendicular to the flanges, and
2) Perpendicular to the smaller leg in an angle section.
c) 2-2 an axis of the cross-section
1) Axis parallel to flanges, and
2) Axis parallel to smaller leg in angle section.
d) u-u major axis (when it does not coincide with 2-2 axis).
e) v-v minor axis (when it does not coincide with y-y axis).
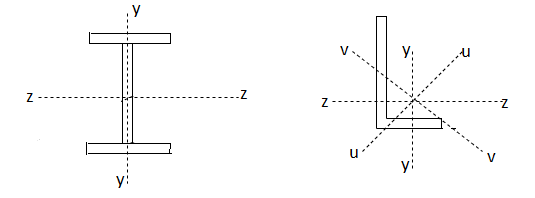
- Loads
For the purpose of designing any element, member or a structure, the following loads (actions) and their effects shall be taken into account, where applicable, with partial safety factors and combinations
a) Dead loads:
b) Imposed loads (live load, crane load, snow load, dust load, wave load, earth pressures, etc);
c) Wind loads;
d) Earthquake loads;
e) Erection loads;
f) Accidental loads such as those due to blast, impact of vehicles, etc; and
g) Secondary effects due to contraction or expansion resulting from temperature changes, differential settlements of the structure as a whole or of its components, eccentric connections, rigidity of joints differing from design assumptions.
Various loads are expected to act on a structure may be classified as given below:
(a) Dead Loads (DL)
(b) Imposed Loads (IL)
(c) Wind Loads (WL)
(d) Earthquake Loads (EL)
(e) Erection Loads (ER)
(f) Accidental Loads (AL)
(g) Secondary effects.
Judicious combination of the loads is necessary to ensure the required safety and economy in the design keeping in view the probability of their,
(a) Acting together combination of various loads.
The various load combination are given as below:
1. DL
2. DL+ WL
3. DL+TL
4. DL+IL+EL
5. DLNL+TL
6. DL+IL+EL+TL
7. DL+IL+EL+TL.
Where TL-Temperature Loads
All type of loads and load combinations required for design are briefly explained at the time of design of respective steel members
2. Dead Load
Dead loads should be assumed in design as specified in IS 875 (Part 1).
The dead load consists of masses which might be especially regular over time, inclusive of the burden of the shape itself, and immovable furniture which include walls, plasterboard or carpet.
The roof is likewise a lifeless load. Dead masses also are called everlasting or static masses. Building substances aren't lifeless masses till built in everlasting position. IS 875(component 1)-1987 deliver unit weight of constructing substances, parts, components.
3. Live Loads
Imposed loads for different types of occupancy and function of structures shall be taken as recommended in IS 875 (Part 2). Imposed loads arising from equipment, such as cranes and machines should be assumed in design as per manufacturers/suppliers data Snow load shall be taken as per IS 875 (Part 4).
Wind loads on structures shall be taken as per the recommendations of IS 875 (Part 3).
Earthquake loads shall be assumed as per the recommendations of IS 1893 (Part 1).
Live loads, or imposed loads, are temporary, of quick duration, or a transferring load. These dynamic loads might also additionally contain issues including impact, momentum, vibration, slosh dynamics of fluids and fabric fatigue. Live loads, from time to time additionally known as probabilistic loads, consist of all of the forces which can be variable inside the object's everyday operation cycle now no longer inclusive of production or environmental hundreds.
Roof and ground stay loads are produced throughout protection with the aid of using workers, gadget and materials, and throughout the existence of the shape with the aid of using movable objects, including planters and people. Bridge live loads are produced with the aid of using motors visiting over the deck of the bridge.
4. Environmental Loads
Environmental loads are structural loads because of herbal forces including wind, rain, snow, earthquake or intense temperatures.
- Wind loads
- Rain and ice loads
- Seismic loads
- Hydrostatic hundreds or loads
- Temperature adjustments main to thermal enlargement motive thermal hundreds or loads
- Ponding hundreds or loads
- Frost heaving Lateral strain of soil
- Groundwater or bulk materials Loads from fluids or floods Permafrost melting Dust hundreds/loads
5. Seismic Forces
Seismic forces are inertia forces. When any object, along with a building, reviews acceleration, inertia pressure is generated while its mass resists the acceleration.
M, the mass of an object, is decided via way of means of dividing its weight via way of means of the acceleration because of gravity, at the same time as a is the acceleration
6. Snow and Rain Loads
During its lifetime, a constructing roof is subjected to some of special structural masses – roof useless masses and roof stay masses (mainly snow, wind, and rain). Depending upon the location, the sort of may be the controlling roof stay load.
For a constructing in northern Vermont, snow is in all likelihood the controlling roof stay load; in northern Mississippi, it is able to be rain. For places which include northern Vermont wherein the snow load is typically large than the rain or wind masses, one expects greater snow-associated structural troubles. Similarly, one expects few snow-associated structural troubles in northern Mississippi wherein the snow load is small in contrast to wind or rain masses. That is, one expects greater snow-associated collapses in locations wherein the snow load is relatively massive and less in locations wherein the snow load is relatively small.
The comparisons beneath display that constructing losses pronounced with the aid of using FM Global for snow and wind dangers are steady with the above expectation; for a particular danger at places wherein the value of the danger is massive, greater losses are generated. However, surprisingly, this expectation does now no longer keep proper for the rain load danger.
7. Erection Loads
The erection loads and temperature effects shall be considered as specified in 3.3 and 3.4 respectively.
All loads required to be carried by the structure or any part of it due to storage or positioning of construction material and erection equipment, including all loads due to operation of such equipment shall be considered as erection loads. Proper provision shall be made.
Including temporary bracings, to take care of all stresses developed during erection.
Dead load, wind load and also such parts of the live load as would be imposed on the structure during the period of erection shall be taken as acting together with the erection loads.
The structure as a whole and all parts of the structure in conjunction with the temporary bracings shall be capable of sustaining these loads during erection.
Key takeaways
Various loads are expected to act on a structure may be classified as given below:
(a) Dead Loads (DL)
(b) Imposed Loads (IL)
(c) Wind Loads (WL)
(d) Earthquake Loads (EL)
(e) Erection Loads (ER)
(f) Accidental Loads (AL)
(g) Secondary effects.
Basis of Design (BOD) The Basis of Design (BOD) files the principles, assumptions, rationale, criteria, and considerations used for calculations and selections required all through layout. The BOD is evolved via way of means of the Designer and builds upon the PC and OPR. The BOD describes the technical method deliberate for the venture and is included into the venture technical specifications. The BOD is used as the idea for layout calculations and different layout selections.
It consists of catalog cuts and producer’s records used to set the minimal tiers of excellent or overall performance set via way of means of the layout. It additionally consists of a story to describe the layout method and evolves right into a greater targeted report that may be used later via way of means of renovation and operations employees for constructing operation, decommissioning, and renovation. BOD is submitted on the Schematic Design (SD) section and is always up to date thru the Design Development (DD) and Construction Document section (CD).
Criteria indexed consist of:
1) Manufacturer, make, and version quantity of the equipment, cloth or device
2) Listing of the specification necessities for compliance and an “equivalent” alternative
3) Highlighted reduce sheets and/or datasheets outlining necessities Topics blanketed within side the BOD report encompass however aren't confined to the following:
• Equipment, Systems and Materials o Owner’s Preferences and Specifications o A/E tips primarily based totally on Basis of Design Selections o DFM Facility Design Standard exceptions if any
• Life Cycle Analysis Synopsis Summary o Options Considered o Options Analyzed o LCCA Option Recommended o LCCA decided on via way of means of Owner
• Discipline Work Criteria and Assumptions Architectural:
1. General Information - Building and Design Codes - Design Conditions and Assumptions - Building Description
2. Thermal Insulation - Windows - Window mild shades
A structural layout project may also be divided into three phases, i.e. making plans, layout and construction.
Planning: This section includes consideration of the various necessities and factors affecting the well known layout and dimensions of the shape and results in the choice of one or perhaps several opportunity types of shape, which provide the satisfactory well known solution. The primary consideration is the function of the shape. Secondary issues which include aesthetics, sociology, law, economics and the surroundings might also be taken into account. In addition there are structural and constructional necessities and limitations, which may also have an effect on the form of shape to be designed.
Design: This section includes an in depth consideration of the opportunity answers described within side the making plans section and results in the determination of the most appropriate proportions, dimensions and details of the structural factors and connections for building each opportunity structural association being taken into consideration.
Construction: This section includes mobilization of personnel; procurement of substances and equipment, including their transportation to the web page, and actual on-web web page erection. During this section, a few redesign may also be required if unforeseen difficulties occur, such as unavailability of specified substances or foundation problems.
Philosophy of designing: The structural layout of any shape first includes establishing the loading and other layout conditions, which have to be supported via way of means of the shape and therefore have to be taken into consideration in its layout. This is accompanied via way of means of the analysis and computation of internal gross forces, (i.e. thrust, shear, bending moments and twisting moments), in addition to pressure intensities, strain, deflection and reactions produced via way of means of loads, changes in temperature, shrinkage, creep and other layout conditions.
Finally comes the proportioning and choice of substances for the contributors and connections to reply properly to the outcomes produced via way of means of the layout conditions. The standards used to choose whether or not specific proportions will result in the desired behavior reflect collected information primarily based totally on subject and version tests, and practical experience. Intuition and judgment are additionally critical to this process. The conventional foundation of layout known as elastic layout is primarily based totally on allowable pressure intensities which are chosen in accordance with the concept that pressure or strain corresponds to the yield factor of the cloth and should now no longer be exceeded at the most highly stressed points of the shape, the choice of failure due to fatigue, buckling or brittle fracture or via way of means of consideration of the permissible deflection of the shape.
The allowable – pressure technique has the critical drawback in that it does now no longer offer a uniform overload capability for all components and all sorts of structures. The more modern technique of layout is known as the strength layout in strengthened concrete literature and plastic layout in steel-layout literature. The predicted carrier loading is first elevated via way of means of a appropriate load issue, the magnitude of which depends upon uncertainty of the loading, the opportunity of it converting for the duration of the lifestyles of the shape and for a mixture of loadings, the likelihood, frequency, and period of the specific mixture.
In this technique for strengthened-concrete layout, theoretical capability of a structural detail is decreased via way of means of a capability- discount issue to offer for small detrimental variations in cloth strengths, workmanship and dimensions. The shape is then proportioned so that depending on the governing conditions, the increased load reason fatigue or buckling or a brittle-facture or just produce yielding at one internal section or sections or reason elastic-plastic displacement of the shape or reason the whole shape to be on the brink of collapse.
Key takeaways:
- Planning: This section includes consideration of the various necessities and factors affecting the well known layout and dimensions of the shape and results in the choice of one or perhaps several opportunity types of shape, which provide the satisfactory well known solution.
- Design: This section includes an in depth consideration of the opportunity answers described within side the making plans section and results in the determination of the most appropriate proportions, dimensions and details of the structural factors and connections for building each opportunity structural association being taken into consideration.
To decide the size, shapes and connection details of the members, the following design philosophies listed below are used in the order of their evolution and they are briefly explained.
1. Working Stress Method (WSM)
2. Ultimate Load Design (ULD)
3. Limit State Method (LSM)
1. Working Stress Method (Allowable Stress Design)
It is one of the oldest methods of design suitable for all structures. Through IS-800-2007 insists for the limit state design, permits use of this method wherever LSM cannot be conveniently adopted.
With the development of linear elastic theory in the 19th century, the stress-strain behavior of material is considered as linear till the yield stress. To take care of uncertainties in the design, permissible or Allowable stress is kept action of yield stress by the ratio known as factor of safety. So that the members designed are to keep the stresses within the permissible value.
Allowable or permissible stress = Yield stress/Factor of safety
Working stress due Permissible or to working loads
(a) For beams FOS = 1.67 Allowable stress
(b) For long column FOS = 1.92
(c) For short column FOS = 1.67
(d) For connections FOS = 2.5-3
A set of load combinations is given below, which are unlikely to act on the structure. (Stress due to DL + WL+LL) < 1.33 (Stress due to DL+LL) Allowable stress (Stress due to DL + WL) S Allowable stress
Advantages:
1) This method is simple.
2) This is reasonably reliable.
3) As the working stresses are low, the serviceability requirements are satisfied automatically.
Limitations:
1) Assumption of linear elastic behavior and the stresses under working loads can kept within the permissible stresses are not found to be realistic.
2) Many factors like the effect of stress concentrations, creep, shrinkage, residual stresses and other secondary effect are not considered.
3) This method does not consider material non linearity and non-linearity of structural members.
4) This method does not provide a realistic measure of the actual factor of safety for the design.
5) It gives uneconomical sections.
2. Ultimate Load Method (Load Factor Method) (ULM)
Ultimate limitation of the working stress method to determine actual load carrying capacity, made researchers to develop ultimate load method, which is also known as plastic design method.
In this method, a section is said to have formed a plastic hinge when all fibers yield. But the structure continues to resists load until sufficient number of plastic hinges are formed to transfer the structure in to a collapse mechanism. At this state the load is known as ultimate load. Safety measures are introduced by using load factor, which is defined as the ratio of design load to working load. This lo factors as per IS 800-1984 are given in table.
Thus, E (Working load + Load factor (LF)) Ultimate load
Sr. No. | Working load | Maximum load factor |
1 | DL | 1.7 |
2 | DL+IL | 1.7 |
3 | DL+WL or EL | 1.7 |
4 | DL+IL+WL or EL | 1.3 |
Advantages:
- Due to plastic hinge concept, redistribution internal forces are accounted.
- It allows varied selection of load factors.
Limitations:
- Limitation on deflection and also it does not guarantee other serviceability limits like instability and fatigue.
- This method is more comprehensive method to take care of strength.
- It does not guarantee of serviceability performance.
3. Limit State Method of Design (LSM)
IS 800-2007, a code of practice, applicable to the structural use of hot-rolled steel is largely based on limit state method of design. However, it still retains the working stress method where LSM cannot be adopted. The limit state method of design developed to take account of all uncertainties limitations of WSM and ULM] that can make the structure unfit for use by considering actual behavior of material and structure.
In the Limit State Method (LSM), basically statistical methods have been used for determination of loads and material properties with a probability of structure reaching the limit state of strength and serviceability. However, it is not yet possible to adopt a complete probability basis for design and therefore the method adopted partial factors of safety which are introduced to take account of all the uncertainties.
Advantages of Limit state method over working stress method:
- In this method, possibility of material non linearity, structural non-linearity, calculation error is considered.
- Factor of safety are called partial safety factors determined by statistical analysis.
- This method provides a realistic measure of the actual factor of safety.
- This method designs any structural element for strength as well as serviceability criteria.
- This method considered reserve strength of material beyond elastic limit of stress-strain curve.
Key takeaways:
- Allowable or permissible stress = Yield stress/Factor of safety
- In this method, possibility of material non linearity, structural non-linearity, calculation error is considered.
- This method designs any structural element for strength as well as serviceability criteria.
- This method considered reserve strength of material beyond elastic limit of stress-strain curve.
As a uniform axial compression is introduced to the member, the preliminary failure mode is neighborhood buckling of the plate factors as proven within side the image. As each plates have the identical b/t ratio, they each buckled on the identical time
The move sections of metal shapes generally tend to include a meeting of skinny plates.
When the move phase of a metal form is subjected to huge compressive stresses, the skinny plates that make up the move phase can also additionally buckle earlier than the entire energy of the member is attained if the skinny plates are too slender.
When a move sectional detail fails in buckling, then the member capability is reached. Consequently, nearby buckling turns into a restrict kingdom for the energy of metal shapes subjected to compressive stress.
Members with plates having b/t ratios among zero and lp are stated to be "compact" and may be predicted to now no longer showcase any buckling behavior. Their compressive energy is restriction via way of means of the fabric compressive energy as visible.
Members with plates having b/t ratios among lp and lr are stated to be "non-compact" and showcase each plastic and elastic buckling behavior. Their compressive energy is restricted via way of means of inelastic buckling.
Members with plates having b/t ratios more than lr are stated to be "slender" and showcase elastic buckling behavior. Their compressive energy is restriction via way of means of elastic buckling.
Local buckling is a very essential side of bloodless fashioned steel sections on account of the fact that the very thin elements used will invariably buckle earlier than yielding. Thinner the plate, the decrease could be the weight at which the buckles will form.
Elastic buckling of skinny plates It has been proven within side the bankruptcy on “Introduction to Plate Buckling” that a flat plate virtually supported on all edges and loaded in compression (as proven will buckle at an elastic important pressure given by
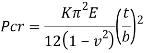
Key takeaways:
- As a uniform axial compression is introduced to the member, the preliminary failure mode is neighborhood buckling of the plate factors as proven within side the image.
- As each plates have the identical b/t ratio, they each buckled on the identical time
- The move sections of metal shapes generally tend to include a meeting of skinny plates.
The Working Stress Method assumes that all cloth used within side the layout behaves in a linear elastic way and calculations are primarily based totally on carrier situations. The predicted running hundred sat the shape are triggered as stresses at the shape for the duration of the layout and those are restricted (to be under the permissible stresses) to make certain ok protection. The thing of protection is the ratio of the power of the cloth to the permissible pressure. However, as running hundreds can't be stored in the permissible stresses this technique isn't always continually viable.
The assumption within side the Ultimate Load Method is that the cloth isn't always linear-elastic which means that extraordinary hundreds can have extraordinary protection elements. Calculations are primarily based totally on closing load situations and the pressure situations on the web page of failure or approaching crumble is analyzed. This effect in extra slender (consequently extra economic!) sections
However, this technique can bring about cracks and deflections which can be excessive because of the serviceability home snow no longer being met.
In the Limit State Method (aka as Limit State Design), the layout of the shape is taken into consideration for each the serviceability and closing load kingdom. This is consequently the higher layout philosophy to employ. The extraordinary restrict states is the Ultimate Limit State (ULS) and the Serviceability Limit State (SLS), for which distinction are made within side the code SANS10160: five.1.3... These states every have their own minimal degree of reliability - that's colloquially called the Safety Index.
The extraordinary restrict states of Limit State Design:
Ultimate Limit State offers with states simply earlier than the shape collapses. This pertains to the protection of human beings and the protection of the shape (power, fatigue, bucking, sliding and overturning). It has a protection index of β= 3.
Serviceability Limit State offers with functioning of the shape, acceptability of protection and look of the shape (deflections, crack width, malfunction and lack of durability). This has a protection index β= 1. Five.
Calculations regarding the impact of a carried-out load and the power or resistance of the shape have to fall in the Safety Index. This is executed throughway Partial Safety Factors. Partial protection elements have emerged inside restricting Dom layout as a method of adjusting parameters to account for versions in order that the best values are used for layout purposes. Partial protection elements are derived from thinking about a frequency distribution statistical evaluation of movements on a shape. Nominal hundreds, observed on symmetric bell curves, have an opportunity of being handed through five%. The overlap of nominal loading of imply load and imply power curves describes the failure condition. This suggests the need of getting a cloth/resistance partial protection thing.
For every layout technique and restricting Dom, an extraordinary set of layout parameters are used. In the Ultimate Load Method for strengthened concrete layout, partial protection elements of 1. five for concrete and 1.15 for metal are used. While within side the Working Stress Method, the protection thing is regularly known as being the ratio of the power of the cloth to the permissible pressure. However, within side the Ultimate Limit State: protection elements of 1.2 instances the use less hundreds, 1.6 instances the stay hundreds and 1.3 instances the wind hundreds are implemented.
This philosophy is a development over the conventional layout philosophies. It considers the protection on the closing load and serviceability on the running load, form of extension of the WSM and ULM.
“Limit kingdom is the kingdom of approaching failure, past which a shape ceases to carry out its meant characteristic satisfactorily, in phrases of both protection and serviceability.”
Key takeaways:
- In this method, possibility of material non linearity, structural non-linearity, calculation error is considered.
- Factor of safety are called partial safety factors determined by statistical analysis.
- This method provides a realistic measure of the actual factor of safety.
- Ultimate Limit State of strength:
It considers power, overturning, fatigue, sliding etc.
2. Serviceability Limit State:
It considers crack width, deflection, vibration etc.
It makes use of more than one protection elements for the desired protection and serviceability on the closing load and running load respectively through thinking about all restrict states. These are called “partial protection elements”.
Partial protection thing for materials:
The power of concrete in real shape is taken as (0. Sixty-seven *function power), i.e.,0. Sixty-seven fck.
The partial protection thing (for closing restrict kingdom) for concrete is 1. Five and that for metal is 1.15. The fee is better for concrete as its miles predicted to have extra variability as compared to metal. The partial protection thing (for serviceability restrict kingdom) for concrete and that for metal is taken as 1.0. This is taken as solidarity as we're interested by estimating the real deflections are crack width for the duration of carrier hundreds.
Partial protection thing for hundreds:
Various load combinations are laid out in IS 456 are
For Ultimate limit states or strength of limit state
- UL = 1.5(DL+LL)
- UL = 1.5(DL+QL) OR 0.9DL+1.5QL
- UL = 1.2(DL+LL+QL)
The load factor of 1.2 is considered for the combination of three because the probability of the three loads reaching its peak together is less.
For serviceability limit states
- SL = 1.0 (DL+LL)
- SL = 1.0 (DL+QL)
- SL = 1.0DL+ 0.8LL+ 0.8 QL
The load factor is taken as 0.8 in the third case as the probability of wind load or earthquake load acting with the peak of live load is less. For all cases the safety factor is taken as 1.0 as we are considering the serviceability of structure here.
Where DL is dead load, LL is live load and QL is earthquake/wind load.
The actions to be considered in the design include direct actions (loads) experienced by the structure due to self weight, external actions and imposed deformations such as those due to temperature and
Classification of Actions and Design Actions/Loads
Actions are classified by their variation with time as given below:
(1) Permanent Actions (Q): Actions due to self weight of structural and non structural components, fittings and fixed equipments.
(2) Variable actions (Q.): Actions due to construction and service stage loads such as Imposed (live) Loads (IL), Snow Loads (SL).Crane Load (CL), Wind Loads (WL) and Earthquake Loads (EL) etc.
(3) Accidental Actions (Q): Actions expected due to explosion and impact of vehicles etc.
The design actions Q, is expressed as
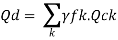
Where, Qck= Characteristic load
Partial safety factor for different loads give in Table 4 IS 800-2007 account for
Key takeaways:
- Ultimate Limit State of strength: It considers power, overturning, fatigue, sliding etc.
- Serviceability Limit State: It considers crack width, deflection, vibration etc.
- The load factor is taken as 0.8 in the third case as the probability of wind load or earthquake load acting with the peak of live load is less
References:
- Design of Steel Structures by N. Subramanian, Oxford University Press
- Limit State Design of Steel Structures by S. K. Duggal, Tata McGraw Hill.
- Design of Steel Structures by K S Sairam, Pearson Education
- Design of Steel Structures by S Ramamurtham, DhanpatRai Publishing Company.
- Steel Structures by Robert Englekirk. Hohn Wiley & sons inc.
- Structural Steel Design by Lambert tall (Ronald Press Comp. Newyork.
- Design of steel structures by Willam T Segui, CENGAGE Learning
- Structural Steel Design By D MacLaughlin, CENGAGE Learning