Unit - 7
Torsion
1. Theory of torsion:
- A member which subjected to couple which produce rotation about its longitudinal axis is known as Twisting moment or Torsion.
- Due to Torque applied on shaft, the shaft produces shear stress and shear strain in the material.
- In practice, torque is produced in shaft of motors or power equipment’s e.g., Fans, axles of vehicles, pumps, etc.
- Shaft are circular in section only; hollow shaft is preferable for design.
2. Derivation of Torsion Equation:
Consider a shaft of radius R and length L is subjected to torque T on the free end and other end is fixed.
Initially the line of the shaft is horizontal AB before twisting and after twisting it takes position AB’ as shown in fig.
Shear strain <BAB’ = and Angle of twist <BOB’ =
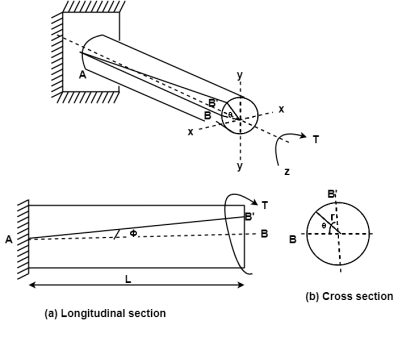
Fig:1
For longitudinal section,
Tan =
tan
=
BB’=L ………………...(i)
From cross-section,
Length of arc = Radius Angle tan
BB’=r ……………. (ii)
From equation I and ii
L = r
…………. (iii)
By definition shear modulus,
G==
……. (iv)
Equation for (iii) and (iv),
=
……………. (v)
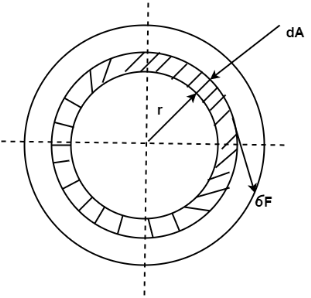
Fig:2
Maximum shear stress occurs at radius R.
=
Now consider elemental ring of area dA at radius r from center O.
Shear force on elemental ring = Stress Area
DF =
dA
Torsional moment on ring,
DT = dF r =
rdA)
DT = dA
Now torsional moment on whole sectional,
=
dA
But we know, dA = polar moment of inertia = J
T =
J
=
……………...(vii)
From equation (vi) and (vii), we get,
=
=
3. Assumptions:
- The shaft should be perfectly straight and uniform in cross-section.
- Material of shaft is homogeneous and isotropic.
- Circular shaft remains circular after twisting.
- Plane section of shaft remains plane before and after twisting.
- Twist is uniform along the length of shaft.
- Maximum shear stress induced in shaft does not exceed elastic limit.
- Torque applied on the shaft in the plane perpendicular to the axis of shaft.
Key takeaway:
- A member which subjected to couple which produce rotation about its longitudinal axis is known as Twisting moment or Torsion.
- Due to Torque applied on shaft, the shaft produces shear stress and shear strain in the material.
- Twist is uniform along the length of shaft.
- Maximum shear stress induced in shaft does not exceed elastic limit
1. A metal bar 15mm diameter subjected to pull of 40KN elongated by 0.5 mm over a gauge length of 500 mm. In a torsion test on the same material, maximum shear stress of 45Mpa was measured on a bar of 50mm diameter and an angle of twist over a length of 300 mm was measured 0.4 degree. Determine Poisson’s ratio for the material.
Ans:
Given:
Tensile test: D = 15mm P = 40KN
= 0.5 mm L = 500 mm
= 45Mpa D = 50 mm
= 0.4
L = 300mm
To find:
(i) Modulus of elasticity from tension test.
E = =
= 226.35
Mpa
(ii) Shear modulus from torsion test:
G = = 77.35
Mpa
(iii) Possions ratio
E = 2G (1+)

= 1.463-1 = 0.463
2. A hollow circular of 200mm external diameter, thickness of metal 20mm is rotating at 180rpm. The angle of twist of 3m length was found to be 0.7. Calculate the power transmitted and maximum shear stress induced in the material. Take G = 80
Mpa.
Ans:
Given
D = 200 mm
t = 20 mm
N = 180 rpm
L = 3m = 3000 mm
= 0.01222 radian

Internal diameter d= D – 2t = 200 - 220 = 160 mm
=
T = 30.2208
N.M
Power p = = 569.65 KW
Torsion rigidity K in the product of modulus of rigidity G and polar moment of inertia J. SI unit is N.m2
K= GJ
Cases stand up along with in propeller shafts of ships wherein a shaft is subjected to direct thrust similarly to bending second and torsion. In such instances the direct stresses because of bending second and the axial thrust should be combined right into a single resultant.
- Direct stress:

Where,
P= axial thrust
A= Area of cross section
2. Bending stress

Where,
M= Bending moment
I = Moment of inertia
3. Torsion Stress

Where,
T= Torque
R= Radius of shaft
J= polar moment of inertia
Combined Stresses:
Under combination of these stresses,
- Principle Stress

2. Maximum shear stress

Equivalent Moment and Torque
Equivalent bending second can be defined because the bending second with the intention to produce the identical direct pressure as produced by the bending second and torque appearing separately. Similarly, the equivalent torque can be defined because the torque which will produce the identical most shear pressure as produced by the bending second and torque appearing separately.
For a circular shaft of diameter, d = 2r
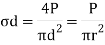
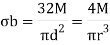

Power transmitted by a shaft
Torque= power (P) x 60 /2n
Where power is measured in watts and n is the speed in rpm
Consider a shaft subjected to the bending moment M and twisting moments T bending moment by using bending formula


Bending stress

Twisting moment by torsion formula



If is the normal stress and
is the shear stress the principal stresses are given by
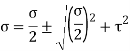
Substituting the value from equation
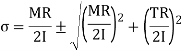
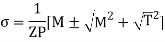
Where Zp is polar sectional modulus, Zp = 1/R
Equivalent bending moment

Numericals:
Q.The oil rig at A has just started to drill for oil on the ocean floor at a depth of 1500 m. Knowing that the top of the 200 mm diameter steel drill pipe rotates through two complete revolutions before the drill bit at B starts to operate. Determine the maximum shear stress caused in the pipe by torsion. Take G= 77GPa.
Given:
L=1500 m=1500×10^3 mm
d = 200mm
=4
G=77GPa=77×10^3 MPa
Polar Moment of inertia:
J =d4 =
(200)4=157.08×10^6 mm4
Using Torsional formula
=
=
T = 101.33×10^6 N-mm=101.33 KN.m
Shear stress
=
×100 =64.5 N/mm^2
Q.Calculate the diameter of shaft required to transmit 60 KW at 160 r.p.m. If the maximum torque is likely to exceed the mean by 30% for maximum permissible shear stress of 55 MPa. Calculate also the angle of twist for length of 1.5m,G=80GPa
Given:
P=60 KW
N=160 rpm
Tmax=1.3 Tmean
=55 MPa
G=80 GPa
L = 1.5 m =1500 mm
Torque by power formula
P=
60×10^3 =
∴Tmean =3.581×10^3 N.m=3.581×10^6N.mm
Tmax=1.3Tmean= 1.3×3.581×10^6 = 4.655×10^6 N.mm
Using Torsional formula
=
∴Zp= Tmax/ =
=84.64×10^3 mm^3
=84.64 ×10^3
d=75.54 mm
Polar sectional modulus J=d^4=π/32(75.54)^4=3.197×10^6 mm4
Permissible angle of twist =
=
=0.0273 radian=1.564 degree
Q.The internal diameter of a steel shaft is 70% of external diameter. The shaft is to transmit3500 kW at 200 rpm. If the maximum allowable stress in the shaft is 50 MPa, Calculate the diameter of the shaft. Also find the maximum twist when it is stressed to maximum permissible value. The length of the shaft is 4 m.
Soln.:
Let D = External diameter & d = internal diameter of the shaf
Given: d = 0.7 D
P = 3500 kW = 3500 × 103 W
N = 200 rpm
max = 50 MPa
= 4000 mm
D, d and
Torque P =
T =
=
= 167112.69 N-m
T = 167.112 × 106 Nmm
T = Zp
Zp = =
= 3342.25 × 103
= 3.342 × 106
= 3.342 × 106
D3 = = 22.398 × 106
D = 281.88 mm 282 mm …Ans.
D = 197.3 mm … Ans
Maximum twist
=
=
=
Assume G = 80 GPa
= 0.0177 rad = 1.016
…Ans.
Q.A steel shaft of 950 mm diameter is required to transmit 220 kW power at 225 rpm and maximum torque is 40 % greater than the mean torque. Find the maximum allowable shear stress in the shaft material.
Soln.:
Given: Diameter d = 950 mm, Power P = 220 kW = 220 103 W
Speed N = 225 rpm, Tmax = 1.4 Tmean
To find :
Mean torque by Power Formula
P =
220 103 =
Tmean = 9337.09 Nm
Maximum Torque
Tmax = 1.4 Tmean = 1.4 9337.09 = 13071.93 Nm
= 13.072 106 Nmm
Polar moment of Inertia J = =
= 7.996
1010 mm4
Torsional formula =
=
= 0.07765 N/mm2 …Ans.
Q.A hollow cylindrical shaft is 1.5 m long. It has an inner and outer diameter respectively equal to 40 and 60 mm. What is the largest torque that can be applied to the shaft if the shearing stress is not to exceed 120 Mpa? What is the corresponding minimum value of shearing stress in the shaft?
Given:
L=1.5m
D=60mm
d =40mm
τ = not > 120 MPa
Polar moment of inertia
J =(D4-d4) =
(604-404)
=1.021×10^6mm4
Maximum shear stress occur at R=D/2=60/2=30 mm
=
=
T= 4.084×10^6 N.mm
Minimum shear stress occur at inner face.
r =40/2=20 mm
=
=
= 80 N/mm2
Q.A hollow circular steel shaft has external and internal diameters as 75 mm and 30 mm respectively. While the shaft rotates at 120 rpm, its twist is observed as 2 degree in 4 m length. Using G= 77 GPa determine the power being transmitted.
Given:
D=75 mm
N=120 rpm
d =30 mm
=2 degree=0.0349 rad
L= 4m =4000 mm
G=77GPa=77×10^3 MPa
Polar moment of inertia J=(D4-d4) =
(754-304)=3.027×10^6 mm4
Using torsional formula
=
=
T=2.034×10^6N.mm=2.034×10^3N.m
Power transmitted by shaft
P==
=22.56×10^3 Watt=25.56KW
Q.A hollow shaft with ratio of internal diameter to external diameter 3/5 is required to transmit 450KW at 120 rpm with a uniform twisting moment.The shearing stress in the shaft must not exceed 60N/mm2 and the twist in the length of 2.5 m must not exceed 1 degree. Taking G=8×10^4 N/mm2, determine the minimum external diameter of the shaft satisfying above two conditions.
Given:
d = 3/5D =0.6D
P=450 KW
N=120 rpm
not > 60N/mm2
not> 1 degree =0.0175rad
L=2.5m
G=8×10^4 N/mm2
Minimum external diameter=?
Torque by power formula P=
450×10^3=
T=35.8×10^6 N.mm
Polar moment of inertia J=(D4-d4)=
(D4-(0.6D4)=0.0855D^4
1)Diameter based on shear stress
=
=
D3=3.49×106
D=157.67 mm
2)Diameter based on angle of twist
=
=
D4=747.7×10^6 mm
D=165.4mm
∴Minimum safe diameter will be the maximum value to satisfy both condition is
D=165.4mm
Closed Coiled Helical Springs: Designed to withstand stretching and twisting, these springs also are referred to as tension/extension springs.
These springs function a watch or a hook on the stop for attachment. These springs can undergo strain because of excessive torsion or bending
Spring is a vital element in nearly every machinery. These springs perform specific features in specific applications.
These take in shocks in vehicles jogging on choppy roads.
These shop power in toys and circuit breakers.
These deliver cushion impact in sofas and cars.
Springs are of various sorts particularly close and open coiled helical springs, laminated and spiral springs.
This spring is subjected to both axial load and axial couple.
The parameters to be studied in springs are stress, stiffness, deflection and resilience.
Key takeaway:
- These take in shocks in vehicles jogging on choppy roads.
- These shop power in toys and circuit breakers.
- These deliver cushion impact in sofas and cars.
References:
- Timoshenko, S. And Young, D. H., “Elements of Strength of Materials”, DVNC, New York USA.
- Kazmi, S. M. A., “Solid Mechanics” TMH, Delhi, India.
- Hibbeler, R. C. Mechanics of Materials. 6th ed. East Rutherford, NJ: Pearson Prentice Hall, 2004
- Crandall, S. H., N. C. Dahl, and T. J. Lardner. An Introduction to the Mechanics of Solids 2nd ed. New York, NY: McGraw Hill, 1979
- Laboratory Manual of Testing Materials - William Kendrick Hall
- Mechanics of Materials - Ferdinand P. Beer, E. Russel Johnston Jr., John T. DE wolf – TMH 2002.