Unit-3
Design of one way slab
Slab:
Slabs are plate element as the depth of member is much smaller than its other dimension hence it is called as two-dimensional member.
Slabs are very commonly used as a floors and roofs of building.
It is subjected to transverse loads which are transfer to the walls or beam to support the slab.
Slab transfer the load due to bending action in one or two direction, steel is .provided accordingly.
Classification of Slabs
Slabs are mainly classified into following types:
(A) Based on shape.
(a) Rectangular.
(b) Square.
(c) Circular.
(B) Based on supporting condition.
(a) Simply supported slab.
(b) Continuous slab.
(c) Cantilever slab.
(d) Flat slab supported directly on column without beams.
(C) Based on spanning direction.
(a) One way slab.
(b) Two way slab.
One Way Slab
The slab which is supported on two opposite support is called as one way slab.
When the aspect ratio ( ly / lx ) is greater than 2, the slab is called as one way slab.
Aspect ratio =ly /LX > 2
Where, lx = length of shorter span
Ly= length of longer span
It bends in one direction only.
Main reinforcement is provided to the shorter span only.
Distribution steel is provided is along the transverse direction to hold the main steel in position and take care of shrinkage and temperature stresses.
General Specifications for Slabs in I S 456: 2000
1) Effective Span:
The effective span of a slab depends upon the boundary condition as per IS456: 2000: clause No. 222 page No. 34.
Simply supported slab or beam which is not built integrally with its support
l = Clear span + effective depth
l = Clear span + width of support, …….. Whichever is less
Cantilever slab.
Effective span = length to the face of support + effective depth
Le = L + d/2
2) Modification Factor (M.F):
Span to effective depth ratio: (Ref. IS456: 2000: clause page No, 37)
Basic value of span to effective depth ratio for spa 10 m.
b) For spans above 10 m. The value in (a) may be multiple by 10/span is meters, except for cantilever.
c) Depending on the area and the stress of steel for tension reinforcement, the value in (a) and (b) shall be modified by multiple with modification factor
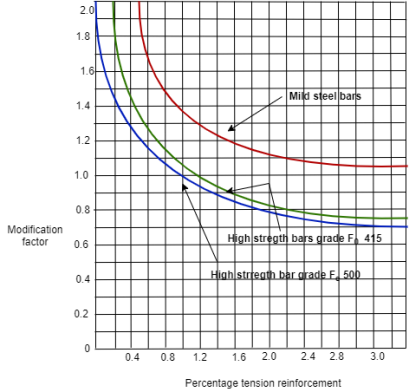
Fig no 1Percentage tensile reinforcement
d = …….. For simply supported slab ( one way)
d = …….. For cantilever slab
Reinforcement requirements for slab
1. Minimum reinforcement
2. Maximum diameter of reinforcing bar
3. Maximum distance between bar in tension (spacing)
4. Control of deflection
1) Minimum reinforcement:
As per clause 26.5.2.1, page no. 48 of IS456: 2000, reinforcement in each direction should not exceed as given below,
Type of reinforcement | Percentage steel |
Mild steel | 0.15% of total cross section area |
Hysd | 0.12% of total cross section area |
2) Maximum diameter of reinforcing bar (clause 26.5.2.2):
Diameter of bar <
3) Maximum distance between bar in tension (spacing)
As per clause 26.3.3(b), page no. 46 of IS456: 2000, spacing of reinforcement in each direction should not exceed as given below
Main reinforcement < 3 x effective depth of slab or 300 mm whichever is less.
Steel for shrinkage and temperature (distribution steel) < 5 x effective depth of slab or 450 mm whichever is less.
4) Control of deflection:
As per clause 23.2(b), page no. 37 of IS456: 2000, deflection of slab should not exceed span /350 or 20 mm whichever is less.
Design steps of Simply Supported One-way Slab
One-way slab is designed as a rectangular beam of one metre width in cross-section; as a balanced section to satisfy the requirements of limit state of collapse in flexure.
Step 1: Type of slab
(i) Aspect ratio =l y /lx> 2, it is one way slab
(ii) According to support condition, it may be simply supported, cantilever or continuous slab.
Step 2: Depth of slab based on deflection criteria (cl. 23.2, page No. 37).
Sr no | Type of slab | Basic value |
1 | Cantilever | 7 |
2 | Simply support | 20 |
3 | Continuous | 26 |
Assume percentage of steel find out modifications Factor for given of steel.
Grade of steel | Design stress | Percentage steel |
Fe 250 | 145 | 0.7% to 1% |
Fe 415 | 240 | 0.25% to 0.45% |
Fe 500 | 290 | 0.2% to 0.35% |
Depending on the area and the stress of steel for tension reinforcement, the values in (a) and (b) shall be modified by multiplying with modification factor obtained as per below figure.
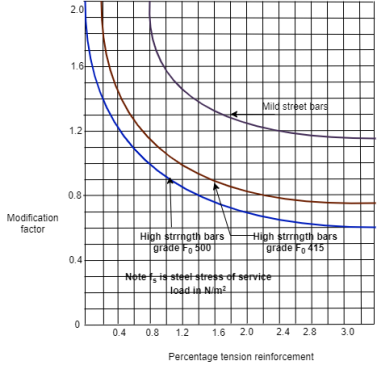
Fig no 2 Percentage tension reinforcement
Depending on the area of compression reinforcement the value of span to depth ratio be further modified by multiplying with the modification factor obtained as per below figure.
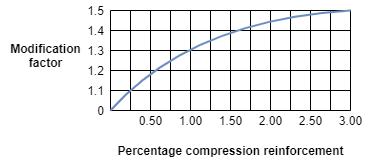
Fig no 3 Percentage compression reinforcement
d = …….. For simply supported slab (one way)
d = …….. For cantilever slab
Step 3: Find the effective span of the slab (Clause 22.2 of IS456: 2000 page 34)
The effective span of a member that is not built integrally with its supports shall be taken as clear span plus the effective depth of slab or to centre of supports whichever is less.
Leff= clear span + effective depth
OR
Leff= centre to centre of supports. ..........whichever is less.
Step 4: Load calculation
1) Dead load: refer IS875: 1984 (Part 1)
The self weight of slab may be found by considering unit area of slab and thickness of slab.
Self weight of slab = unit weight of concrete x depth of slab
Live load: refer IS875 : 1984 (Part 2)
Total load to be supported by slab per unit length along the short span is obtained.
3) Floor Finish (FF)
In addition to this also consider the weight of floor finish i.e. 0.6 to 1 kN/m2
Total load w = (DL + LL+ FF)
Factored load wu = Load factor x Total load
= 1.5 w
Step 5: Design factored moment
For cantilever slab,
Mu = 0.87 fyAst(d – 0.42xu)
For simply supported slab,
Mu =
Step 6: check for depth of slab
Grade of steel | Mu limiting |
Fe 250 | 0.148 f CK b d2 |
Fe 415 | 0.138 f CK b d2 |
Fe 500 | 0.133 f CK b d2 |
(OR) using relation Mu = 0.36fck• xu • b (d - 0.42 xu) where xu = xulim
Equate factored bending moment of Mu lim
If drequired<dassumed safe for flexure.
Overall depth = depth + clear cover
Step 7: Main reinforcement
Ast = 0.5 fck/ fy (1- √ 1- ((4.6 Mu)/(f CK b d 2)) b d
Or
Ast is calculated from the equation.
Mu = 0.87 fyAst(d – 0.42xu)
Step 7.1: check for minimum reinforcement
Type of reinforcement | Percentage steel | Ast min per meter |
Mild steel | 0.15% of total cross sectional area = 0.15 % bD | 1.5 D |
HYSD | 0.12 % of total cross section area = 0.12% b D | 1.2 D |
Where D = overall depth of slab
Step 7.2: Maximum diameter
Ref. Clause 26.5.2.2 of IS456: 2000, page number 48
d should not be less than
Assume diameter of bar 8 mm or 10 mm or 12
Step 7.3: Spacing of main reinforcement
Spacing, s = 1000 ast/Ast
Where, ast = Area of one bar.
Check or maximum spacing for main reinforcement
Spacing, s = 3d Or 300 mm ………………..whichever is smaller
Step 8: Check for serviceability
Calculate actual percentage of steel provided.
Pt = x 100
Find actual modification factor corresponding to given grade of steel and point actul
Depth required (for deflection) =
Depth required must be less than d provided. If not then the effective depth must be increased.
Step 9: Distribution steel
Minimum area of steel in tension is provided as distribution steel.
Assume diameter of bar 6 mm for Mild steel or 8 mm for HYSD bar.
Spacing = 1000 ast/Ast
Check spacing < 5d or 450 mm whichever is less.
Step 10: Check for development length
Provided development length Ld and value of from cl.26.2.1, page No. 42 of IS456.
Ld= Lo + d/2
Where, d = diameter of bar
The value of bdis increased by 60 % for deformed bar.
Permissible development length:
L d ≤ 1.3 + Lo
Reinforcement should be extend from the face of support by length equal to.( Ref. Cl. 26.2.3.3a).
M1 = Moment of resistance of remaining bar at support
= Tu1 x z = 0.87 fy Ast1 (d - 0.42 xu)
Ast= area of bar at supports (half of the area at the centre).
Vu = Shear force at centre of support.
Provided development should not exceed with limited development
Step 11: Check for shear
Calculate,v =
From Table 19 of IS456: 2000 page 73 find the design shear strength of concrete considering grade of concrete and percentage of steel.
Further multiply this design shear strength by k (clause 40.2.1.1 page 72 of IS456: 2000) to get exact design shear strength. This should not be less than 𝜏v calculated above.
Note:
The shear force in slab is very small and there is no need to provide shear reinforcement in slab.
Step 12: Details of reinforcement
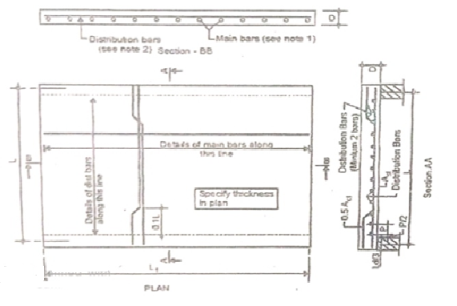
Fig no 4 Reinforcement
Note:
Diameter 8 mm for deformed bars 10 mm for plain bars: spacing not more than 3d or 300 mm
Diameter 6 mm spacing not more than 5d or 450 mm ( Typical details of a slab spanning in one direction i.e. one way slab)
Key take ways
Design steps for one way slabs
Step 1: Type of slab
Step 2: Depth of slab based on deflection criteria (cl. 23.2, page No. 37).
Step 3: Find the effective span of the slab (Clause 22.2 of IS456: 2000 page 34)
Step 4: Load calculation
Step 5: Design factored moment
Step 6: check for depth of slab
Step 7: Main reinforcement
Step 8: Check for serviceability
Step 9: Distribution steel
Step 10: Check for development length
Step 11: Check for shear
Step 12: Details of reinforcement
ONE WAY CONTINUOUS SLAB
One way slab, which is supported by beams on the two opposite sides to carry the load along one direction. The ratio of longer span (l) to shorter span (b) is equal or greater than 2, this slab will bend in one direction i.e in the direction along its shorter span.
Design steps
NUMERICAL
Design of simply supported slab one way slab:
Design a simply supported slab for a room with clear inner size 3 mx 7 m. The slab is supported by beams of width 230 mm along all the edges. The slab is subjected to floor finish of 1 kN/m2and live load 4 kN/m2.Use concrete of grade M20 and Fe 500 reinforcement. Draw details of reinforcement. Check for shear is not required. (Use LSM).
Ans:
Step 1: Aspect ratio = ly/LX = 2.33 > 2 ……….It is a one way slab
Step 2: Trial depth of the slab
For shorter span 3m > 3.5m, Ref. Clause 23.2.1 of IS 456:2000
Assume percentage steel 0.3 %, modification factor is 1.25 For Fe500
Dreq = 120 mm
Assuming cover 15 mm and diameter of bar 10 mm
D = d + c + d/2
= 120 + 15 + 10/2
= 140 mm
Step 3: Calculate efficiency span leff
leff= L + d
= 3 + 0.12 = 3.12 m
Leff= L + b
= 3 + 0.23 = 3.23 m
Leff= 3.12 m …………whichever is less
Step 4: Load calculation:
Self weight = 0.14 x 1 x 25 = 3.5 KN/m
F.F = 1 KN/m
L.L = 4 KN/m
Total = 8.5 KN/m
Factored load = 1.5 x 8.5 = 12.75 KN/m
Step 5: Factored moment:
Mu = 15.51 KN m
Factored shear force
Vu = 19.89 KN
Step 6: Determine required depth of bendng:
For Fe500
Mu.lim = 0.133fckbd2
15.51 x 106= 0.133x 20 x 1000d2
d = 76.35 mm < 120 mm
If drequired<dassumed …………….. safe for flexure.
Step 7: Determine main steel:
Ast = 0.5fck/fy(1-√1-((4.6Mu)/(fCKbd2))bd
Ast = 318.39 mm2
Spacing of 10 mm diameter of bar
Spacing , s = 1000 ast/Ast
s = 246.67 = 240 mm c/c
Check , s < 3d
240 < 300 ………………..ok
Provided main reinforcement of 10 mm diameter of bar @ 240 mm c/c
Pt actual = 0.26 % >0.12 %
Step 8: Determination of distribution steel:
Assuming 6 mm diameter bar is used for distribution steel
Ast d = 0.12 % of A gross = 0.12 % bD
Ast d = 0.12 x 1000 x 140
= 168 mm2
Spacing of distribution steel
Spacing, s = 1000 ast/Ast
s = 168.299 = 160 mm c/c
Check for max spacing
S < 5d = 5 x 120 = 600 mm
S = 160 mm ……………. Ok
Provided distribution reinforcement of 6 mm diameter of bar @ 160 mm c/c
Step 9: Check for deflection
F s = 0.58 fy
Ast req = 318.39 mm2
Ast provided = 327.08 mm2
Fs = 0.58 x 500 x
= 282. 29 mm2
Actual modification factor for pt = 0.26 % and for Fe500 is 1.2 ( as per fig 0f modification factor of tension reinforcement)
Depth required (for deflection) = span/20 MF
Depth required (for deflection) = 125 mm
As D req for deflection < D req
125 mm< 140 mm ……………..ok
2) Design a corridor slab over a passage of size 15.70m x 3.20m at an entrance of a public building. The slab is simply supported by 300mm wide beams and carries live load 3.00 kN/m2 and floor finish of 1 kN/m2 . Use M20 grade of concrete and Fe415 grade of steel. Assume mild exposure condition. Also show details of reinforcement. ( Feb – 2016)
Answer:
Longer span ly = 15.70 m,
Shorter span 1x = 3.20 m
Support beam bs = 300 mm,
Live load LL = 3 KN/m2
FF = 1 kN/m2
Use M20 fck = 20 N/mm2
Fe 415 fy = 415 N/mm2
Exposure = mild
Step 1: Aspect ratio = 4.9> 2 ……….It is a one way slab
Step 2: Trial depth of the slab
Assume percentage steel 0.3 %, modification factor is 1.45 for Fe415
Dreq = 110.34 mm
Assuming cover 15 mm and diameter of bar 8 mm
D = d + c + d/2
= 110.34 + 15 + 8/2
= 129.24 mm = 140mm
Effective depth d = D – c – d/2
= 140 – 15 – 8/2
= 121 mm
Step 3: Calculate efficiency span leff
L eff= L + d
= 3 + 0. 121 = 3.321 m
Leff= L + b
= 3 + 0.3 = 3.5 m
Leff= 3.321 m …………whichever is less
Step 4: Load calculation:
Self weight = 0.14 x 1 x 25 = 3.5 KN/m
F.F = 1 KN/m
L.L = 3 KN/m
Total = 7.5 KN/m
Factored load = 1.5 x 7.5 = 11.25 KN/m
Step 5: Factored moment:
Mu = 15.51 KN.m
Factored shear force
Vu = 19.89 KN
Step 6: Determine required depth of bending:
For Fe415
Mu.lim = 0.138fckbd2
15.51 x 106= 0.138x 20 x 1000d2
d = 74.96 mm < 121 mm
If drequired<dassumed …………….. safe for flexure.
Step 7: Determine main steel:
Ast = 318 mm2
Ast d = 0.12 % of A gross = 0.12 % bD
Ast d = 0.12 x 1000 x 140
A s t d= A s t min = 168 mm2
Spacing of 8 mm diameter of bar
Spacing,
s = 132.27 = 125 mm c/c
Provided main reinforcement of 8 mm diameter of bar @ 125 mm c/c
Check, s < 3d
125< 300 ………………..ok
Provided main reinforcement of 8 mm diameter of bar @ 125 mm c/c
Step 8: Determination of distribution steel:
Assuming 6 mm diameter bar is used for distribution steel
Ast d = 0.12 % of A gross = 0.12 % bD
Ast d = 0.12 x 1000 x 140
= 168 mm2
Spacing of distribution steel
Spacing, s = 1000 ast/ Ast
s = 168.299 = 160 mm c/c
Check for max spacing
S < 5d
S = 160 mm ……………. Ok
Provided distribution reinforcement of 6 mm diameter of bar @ 160 mm c/c
Step 9: Check for deflection
F s = 0.58 fy A s t required/ A s t provided
Ast req = 318mm2
Ast provided = 402 mm2
Fs= 0.58 x 415 x 318/ 402
= 227.5 mm2
Pt actual = 0.33% > 0.12 %
Actual modification factor for pt = 0.33% and for Fe415 is 1.5( as per fig 0f modification factor of tension reinforcement)
Depth required ( for deflection) = 110.7 mm
As D req for deflection < D req
110.7 mm< 121 mm ……………..ok
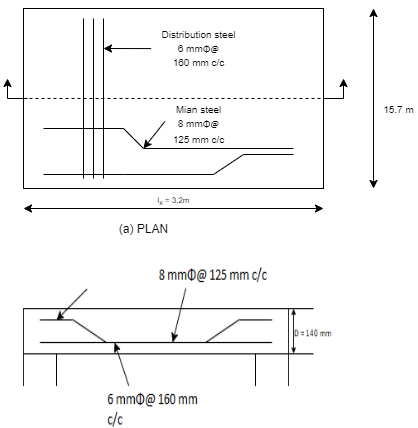
Fig no 5 Detailing of reinforcement
ONE WAY CONTINUOUS AND CANTILEVER SOLID SLABS BY LIMIT STATE DESIGN METHODS
CANTILEVER SOLIDS SLABS
Design steps
Step 1: Trial depth of slab 'D'
Step 2: Load calculation:
Step 3: Factored moment:
Step 4: Determine required depth of bendng:
Step 5: Determine main steel:
Step 6: Determination of distribution steel:
Step 7: Check for deflection
Step 8: Check for development Ld
Design of cantilever slab:
1) Design a cantilever chajja slab projecting 1.5 m, from the support using M-20 grade concrete and Fe415 steel. Take L.L as 2kN/m2. And F.F is 2 kN/m2
Ans:
Step 1: Trial depth of slab 'D'
Assuming M.F. = 1.5
Dreq =142.8 mm
Assuming cover 15 mm and diameter of bar 8 mm
D = d + c + d/2
= 142.8 + 15 + 8/2
= 161.85 mm = 170 mm
Effective depth d = D – c – d/2
= 170 – 15 – 8/2
= 151 mm
Step 2: Load calculation:
Self weight = 0.17 x 1 x 25 = 4.25 KN/m
F.F = 2 KN/m
L.L = 2 KN/m
Total = 8.25 KN/m
Factored load = 1.5 x 8.25 = 12.375 KN/m
Step 3: Factored moment:
Mu = 13.92KN.m
Step 4: Determine required depth of bending:
For Fe415
Mu.lim = 0.138fckbd2
13.92 x 106= 0.138x 20 x 1000d2
d = 71mm < 151 mm
If drequired<dassumed …………….. safe for flexure.
Step 5: Determine main steel:
Ast = 265.11 mm2
A s t d = 0.15 % of A gross = 0.15 % bD
Ast d =0.15 x 1000 x 170
A s t d= A s t min = 255 mm2
Spacing of 8 mm diameter of bar
Spacing, s = 1000 a s t/ A s t
s = 189.35 = 180 mm c/c
Provided main reinforcement of 8 mm diameter of bar @ 180 mm c/c
Check , s < 3d
180 < 453 ………………..ok
Provided main reinforcement of 8 mm diameter of bar @ 180 mm c/c
Step 6: Determination of distribution steel:
Assuming 6 mm diameter bar is used for distribution steel
Ast d = 0.15 % of A gross = 0.15 % bD
Ast d = 0.15x 1000 x 170
= 255 mm2
Spacing of distribution steel
Spacing, s = 1000 ast /Ast
s = 110.8 = 150 mm c/c
Check for max spacing
S < 5d
S = 150 mm ……………. Ok
Provided distribution reinforcement of 6 mm diameter of bar @ 150 mm c/c
Step 7: Check for deflection
F s = 0.58 fy A s t required/A s t provided
Astreq = 265.11 mm2
Astprovided = 278.88 mm2
F s = 0.58 x 415 x 265.11/278.88
= 228.8 mm2
Pt actual = 0.186 % > 0.12 %
Actual modification factor for pt = 0.185% and for Fe415 is 1.8( as per fig 0f modification factor of tension reinforcement)
Depth required ( for deflection) = 119 mm
As D req for deflection < D req
119 mm< 151 mm ……………..ok
Step 8: check for development Ld
Ld= 1.92 N/mm2for M20 concrete
Ld= 376 mm
Ld = 1.3 + Lo
Providing 90° bend and clear cover of 25 mm at side end
Assume support width = 300mm
Lo = – side cover – 3 x diameter of bar
= – 25 – 3 x 8
= 149 mm
Md = 13.92 x 106 N.mm
Vd = Wu x L
= 12.375 x 1.5 = 18.56 KN
Ld = 1.3 + Lo
Ld = 1.3 + 149
Ld = 1779.5 mm
Ld ≤ 1.3 + Lo
376 ≤ 1779.5 mm …………….ok
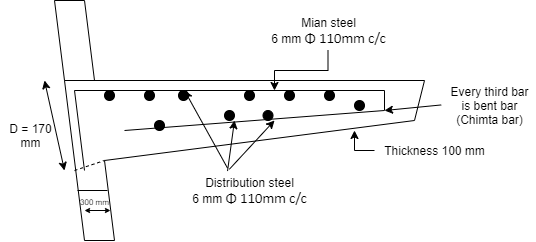
Fig no 6 Detailing
2) The centre line plan of a typical floor of residential building is as shown in Fig. Design the cantilever slab panel S3 only for flexure by L.S. M.
Draw neat sketches showing details of reinforcement.
(a) Take live load = 4 kN/m2
(b) Floor finish = 1.5 kN/m2
(c) Materials : M25 and Fe415 ( ( May – 2017 , May – 2016 , Dec – 2015)
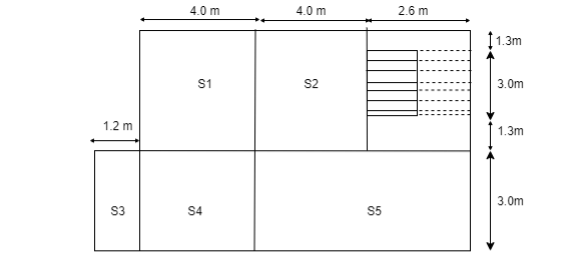
Fig no 7
Answer:
Given:
Le = 1.2 m
Fck = 25 mpa
Fy = 415 mpa
Step 1: Depth of slab based on serviceability
Assuming M.F. = 1.5
D required = 114.28 mm
Assuming cover 15 mm and diameter of bar 8 mm
D = d + c + d/2
= 114.28 + 15 + 8/2
= 133.28 mm = 140 mm
Effective depth d = D – c – d/2
= 140 – 15 – 8/2
= 121 mm
Step 2: Load calculation:
Self weight = 0.121 x 1 x 25 = 3.025 KN/m
F.F = 1.5 KN/m
L.L = 4 KN/m
Total = 8.525 KN/m
Factored load = 1.5 x 8.525 = 12.785 KN/m
Step 3: Factored moment:
Mu = 10.81 KN.m
Step 4: Determine required depth of bending:
For Fe415
Mu.lim = 0.138fckbd2
10.81 x 106= 0.138x 25 x 1000d2
d = 55.98 mm < 121 mm
If d required<d assumed …………….. Safe for flexure.
Step 5: Determine main steel:
Ast = 256.6 mm2
Ast d = 0.15 % of A gross = 0.15 % bD
A s t d= A s t min = 210 mm2
Spacing of 8 mm diameter of bar
Spacing ,
s = 195.9 = 190 mm c/c
Provided main reinforcement of 8 mm diameter of bar @ 190 mm c/c
Check , s < 3d
190 < 353 ………………..ok
Provided main reinforcement of 8 mm diameter of bar @ 190 mm c/c
Step 6: Determination of distribution steel:
Assuming 6 mm diameter bar is used for distribution steel
Ast d = 0.15 % of A gross = 0.15 % bD
Ast d = 0.15 x 1000 x 140
= 210 mm2
Spacing of distribution steel
Spacing ,
s = 134.45 = 130 mm c/c
Check for max spacing
S < 5d
S = 130 mm ……………. Ok
Provided distribution reinforcement of 6 mm diameter of bar @ 130 mm c/c
Step 7: Check for deflection
Fs = 0.58 fy A s t required/ A s t provided
Astreq = 256.6 mm2
Astprovided = 264.6 mm2
Fs = 0.58 x 415 × 256.6/264.6
= 223.4 mm2
Ptactual= 223.4 × 10^-3 x 100
Pt actual = 0.22 % > 0.12 %
Actual modification factor for pt = 0.22% and for Fe415 is 1.6( as per fig 0f modification factor of tension reinforcement)
Depth required ( for deflection) = 107mm
As D req for deflection < D req
107 mm< 121 mm ……………..ok
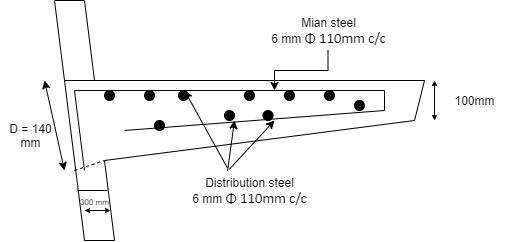
Fig no 8 Detailing
ONE WAY CONTINUOUS SLAB
One way slab, which is supported by beams on the two opposite sides to carry the load along one direction. The ratio of longer span (l) to shorter span (b) is equal or greater than 2, this slab will bend in one direction i.e in the direction along its shorter span.
Design Step for Continuous Slab
Continuous slab are design by using moment and shear coefficients given in table 12 and 13 page no.36 of IS456:2000.
Step 1: Effective span
As per clause 22.2., Page no. 34 and 35 of IS456: 2000
When bw<
Effective span L = Clear span + effective depth
L = Clear span + width of support …………. Whichever is less
When bw>or 600 mm whichever is less, effective 12 span for end span with one end fixed and the other end is continuous or for intermediate spans shall be taken as
Effective span = Clear span between supports
Step 2: Load calculation
Wd = Factored dead load
= 1.5 (Dead load + floor finish)
WL = Factored live load
= 1.5 LL
Step 3: Factored bending moment
Clause 22.5.1, Table 12 Page No. 36 of IS456: 2000
Note:
For obtaining the bending moment, the coefficient shall be multiplied by the load design load and effective span.
(A) Span moment:
1) B. M. Near middle of end span M1
M1 = wd Le2 + wL Le2
2) B. M. At middle of interior span M2
M2 = w d Le2 + wL Le2
(B) Support moment:
B. M. At support next to end support
M3 = - wd Le2 - wL Le2
B. M. At other interior support
M4 = - wd Le2 – wL Le2
Step 4: Check for required depth
Equating maximum B.M. To Mu lim
Step 5: Main Reinforcements
Ast= 0.5fck/fy(1-√1-((4.6Mu)/(fCKbd2))bd
Step 6: Distribution Reinforcements
Type of reinforcement
Mild steel = 0.15 % of total cross sectional area = 0.15 % bD
HYSD = 0.12 % of total cross sectional area = 0.12 % bD
Step 7: Check for deflection:
Ptactual=FS x 100
Fs = 0.58 fy Ast required/ Ast provided
Based on percentage steel and design stress from Fig. 4 page no.38, of IS456: 2000, Actual Modification factor is calculated.
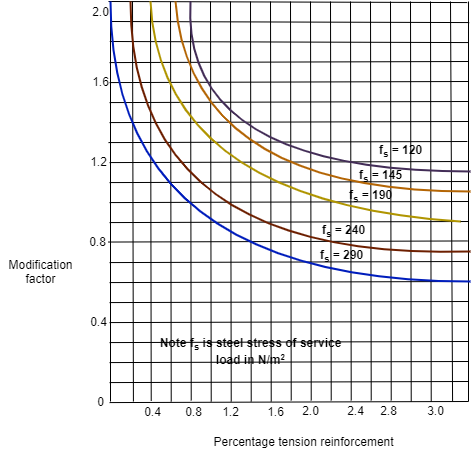
Fig no 9 Percentage tension reinforcement
Depth required (for deflection) = As D req for deflection < D req
Step 8: check the shear:
Note:
For obtaining the shear force the coefficient shall be multiplied by the total design load.
Shear force at end:
Vu = 0.4 wd Le + 0.45 WL L e
2) Shear force at support next to the end support:
a) Outer side
Vu = 0.6wd Le + 0.6 WL L e
b) Inner side
Vu = 0.55wd Le + 0.6 WL L e
3)Shear force at all interior supports:
Vu = 0.5 wd Le + 0.6 WL L e
Select the maximum shear force calculated
Nominal shear stressv =
From Table 19 of IS456: 2000 page 73 find the design shear strength of concrete considering grade of concrete and percentage of steel.
Further multiply this design shear strength by k (clause 40.2.1.1 page 72 of IS456 : 2000) to get exact design shear strength. This should not be less than 𝜏vcalculated above.
NUMERICAL
Design of continuous slab
Design a continuous slab to cover a hall 8 m x 17.5 m. The live load on a slab is 3.5 kN/m2 floor finish 0.8 kN/m2. Use M20 concrete and Fe415 steel. The slab is monolithically construction with beams & spaced at 3.5 m centre to centre.( May – 2004)
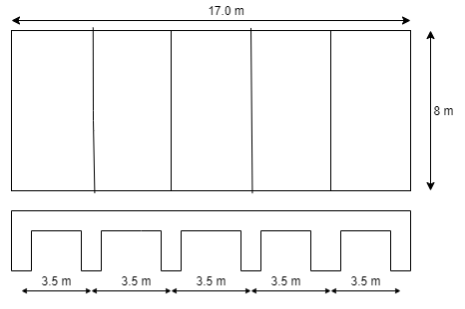
Fig no 10
Given figure
Ans:
Step 1: Aspect ratio = 2.29> 2 ……….It is a one way slab
Step 2: Trial depth of the slab
Assume percentage steel 0.35%, modification factor is 1.4 For continuous slab
Dreq = 96.15 mm
Assuming cover 15 mm and diameter of bar 10 mm
D = d + c + d/2
= 96.15+ 15 + 10/2
= 120 mm
D = 120 – 20 = 100mm
Step 3: Effective span:
Assume support width is 300mm
= 250mm <bw>
L = Clear span + width of support
L = 3500 – 300
= 3200 mm
Step 4: Load calculation:
Consider load per unit width
D.L = 25D = 25 x 0.12 = 3 KN/m
F.F = 0.8 KN/m
DL + imposed fixed load = 3.8 KN/m
Factored load wd = 1.5 x 3.8 = 5.7 KN/m
LL (imposed ls not fixed ) = 3.5 KN/m
Factored load wL = 1.5 x 3.5= 5.25 KN/m
Step 5: Factored bending moment:
(A) Span moment:
1) B. M. Near middle of end span M1
M1 = wd Le2 + wL Le2
M1 = 5.71 x 3.32 + 5.25 x 3.22
M1 = 10.25 KN.m
2) B. M. At middle of interior span M2
M2 = wd Le2 + wL Le2
M2 = 5.71 x 3.32 + 5.25 x 3.22
M2 = 8.13 KN.m
(B) Support moment:
B. M. At support next to end support
M3 = - wd Le2 – wL Le2
M3 = - 5.71 x 3.32 - 5.25 x 3.22
M3 = 11.81 KN.m
B. M. At other interior support
M4 = - wd Le2 - wL Le2
M4 = - x 5.71 x 3.32 - 5.25 x 3.22
M4 = 10.84 KN.m
Maximum B.M , BM max = 11.31 x 106 N.mm
Step 6: Check depth:
For Fe415
Mu.lim = 0.138fckbd2
11.81 x 106= 0.138x 20 x 1000d2
d = 65.4 mm < d prov ……………ok
Step 7: steel reinforcement:
Xulim= 0.48d = 0.48 x 100 = 48 mm
Mulim = 0.36 fckxulim .b ( d – 0.42 xulim)
= 0.36 x 20 x 48 x 1000 ( 100 – 0.42 x 48)
= 27.6 x 106 > 11.81 x 106
Hence design slab as singly reinforced under reinforced
Ast d = 0.12 % of A gross = 0.12% bD
Ast d = 0.12 x 1000 x 120
= 144mm2
Ast for mid of end span for M1
Ast1 = 302.78 mm2
Spacing of 8 mm diameter of bar
Spacing ,
s = 166 = 160 mm c/c < (3d or 300mm) ………ok
A s tprovided = 314.3 mm2
Ast for middle of interior span for M2
Ast2= 236.94 mm2
Spacing of 8 mm diameter of bar
Spacing ,s = 1000 Ast/ Ast
s = 212 = 210 mm c/c <( 3d or 300mm) ………ok
Astprovided = 239 mm2
As t for at support next to end support for M3
Ast3 = 353 mm2
The alternate bar for mid span will bent up at 0.25 L
= 0.25 x 3500 = 875 mm from centre of support
Extended for length = 0.3L = 0.3 x 3500 = 1050 mm from face of support
Area of bent up bar =
Area of steel available bent up bar = 276.5 mm2
Required Ast = Ast 3 = Ast available = 353 – 276.5 = 76.5 mm2
Spacing of 8 mm diameter of bar
Spacing ,
s = 657 = 600 mm c/c <( 3d or 300mm) ………ok
Ast for interior support for M4
Ast3 = 322mm2
Steel available due to alternate bent up bar
Area of bent up bar =
Area of steel available bent up bar = 239 mm2
Required Ast = Ast 3 = Ast available = 322 – 239 = 83mm2
Spacing of 8 mm diameter of bar
Spacing ,
s = 605.5 = 600 mm c/c <( 3d or 300mm) ………ok
Provided 8 mm diameter extra bar at 600 mm c/c for length pf 0.3 L = 0.3 x 3500 = 1050 mm from the face on both sides of support
Step 8: Determination of distribution steel:
Assuming 6 mm diameter bar is used for distribution steel
Ast d = 0.12 % of A gross = 0.12 % bD
Ast d = 0.12 x 1000 x 120
= 144 mm2
Spacing of distribution steel
Spacing , s= 1000 ast/ Ast
s = 196.3 mm = 190 mm c/c
Check for max spacing
S < 5d
S = 190 mm ……………. Ok
Provided distribution reinforcement of 6 mm diameter of bar @ 190 mm c/c
Step 9: Check for serviceability:
Actual modification factor for pt = 0.3% and for Fe415 is 1.3 (as per fig 0f modification factor of tension reinforcement)
Depth required ( for deflection) = 94.32 mm
As D req for deflection < D req
94.32 mm< 100 mm ……………..ok
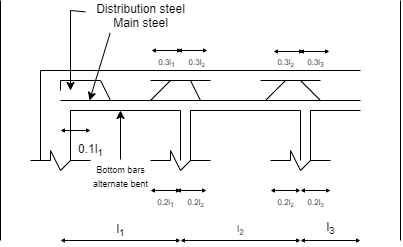
Fig no 11 Detailing reinforcement
Key takeaways:
CANTILEVER SOLIDS SLABS
Design steps
Step 1: Trial depth of slab 'D'
Step 2: Load calculation:
Step 3: Factored moment:
Step 4: Determine required depth of bending:
Step 5: Determine main steel:
Step 6: Determination of distribution steel:
Step 7: Check for deflection
Step 8: check for development L d
ONE WAY CONTINOUS SLAB
Design steps
Step 1: Effective span
Step 2: Load calculation
Step 3: Factored bending moment
Step 4: Check for required depth
Step 5: Main Reinforcements
Step 6: Distribution Reinforcement
Step 7: Check for deflection:
Step 8: check the shear:
1. General requirement for a staircase:
Location: It should be do located that sufficient light and ventilation should be ensure stairway
Width of stair: for public building= 1.5 to 2.5m, residential building= 0.9 to 1.5m
Pitch of staircase: The slope of stair should not be greater than 40 degree and should not be less than 25 degree.
Headroom: The vertical distance from a line connecting the nosing of all treads and the soffit above. The head room measured vertically above any step or below the mid landing shall not be less than 2.1 m.
Tread: Horizontal upper portion of a step where the foot is rests is known as tread. For residential building (T) 220mm to 250mm and for public building 250mm to 300mm.
Rise: Vertical distance between two consecutive treads. Rise is depends on type of building and the value varies 200mm to 300mm.
Flight: A series of steps provided between two landings.
2. Design steps:
Step 1) Preliminary depth of slab (waist slab and landing slab)
- As per limiting stiffness criteria
D Eff. Or D Req. = L Eff.
(l0/d)basic x α
Assuming α = 1.25
D = d eff. + Nominal cover + ɸ/2
2. Effective span calculation:
a. When top and bottom riser with landing is supported but beam the effective span is c/c distance of beam.
b. When spanning on the edge of landing and below the top riser effective span.
Going + each end either half the landing one m whichever < and small
c. In case of open well staircase L eff. Is taken into c/c dist. Of beam.
Step 2) Load calculation
- Load on waist slab
- Self wt. Of slab = 25D
- When due to finishing of soffit = unit wt. Of plaster x thickness of plaster
- Self wt. Of step = Area x length x unit wt. Of concrete x steps along 1m length
Self wt. Of steps = ½ X R X T X 1 X 25 X (1/ T)
Self wt. Of steps= 12.5 R
4. Wt. Due to finishing of steps= unit wt of plaster X thickness
5. Live load= For residential building ( 2 to 3 KN/M2) and for important building ( 4 to 5 KN/M2)
B. Load on landing slab:
- Self wt. Of slab = 25D
- Floor Finishing
- Live load
Step 3) Calculation for design moment
- Design of flight one
- Design moment: calculate maximum BM and maximum SF from the loading dia. Of flight no. 1
Check for depth: d req. = BM max.m
Ru .b
d req. < d prov. (Hence O.K)
c. Amount of Ast. And Sv
- Main steel
Ast min. = 0.12% X b X d
S.P. Max. = 3d or 300mm<
Ast= 0.5 Fck 1- 1- 4.6 mu x b x d
Fy Fck x b x d2
Sv = 1000 ast
Ast
2. Distribution steel
Ast min.m = 0.15 x b x d
S.P. Max = 5d or 450mm <
Sv = 1000 ast
Ast
3. Design of flight second
- Design moment
Calculate BM and SF maximum from loading Dia. Of flight no. 2
b. Check for depth
c. Amount of steel and spacing
Step 4) Check for deflection
Step 5) Check for shear
Step 6) Development length
Step 7) Reinforcement detailing
3. Reinforcement detailing of stairs
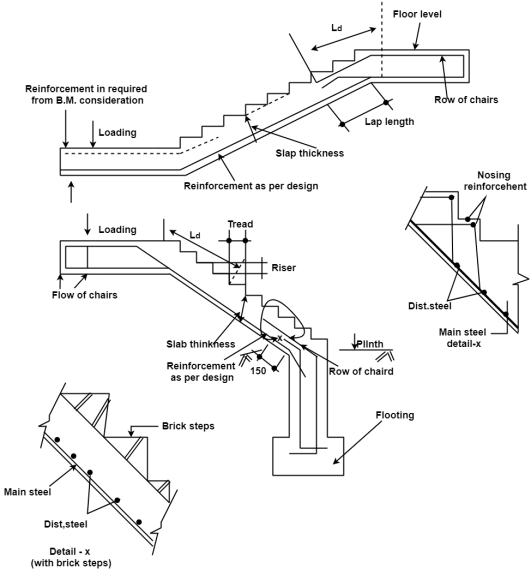
Fig. Stairs supported at ends of landing- showing position of main
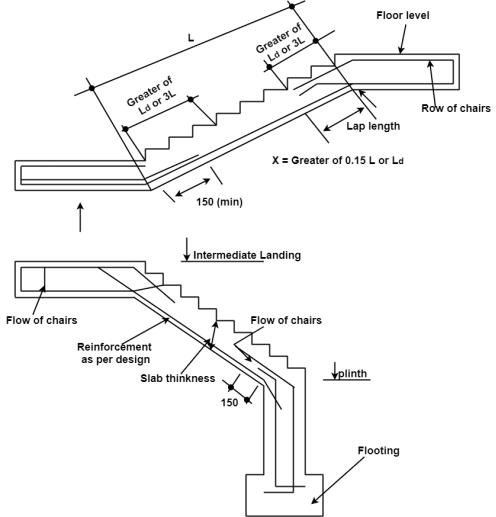
Fig. Stairs supported at ends of flight- showing main reinforcement
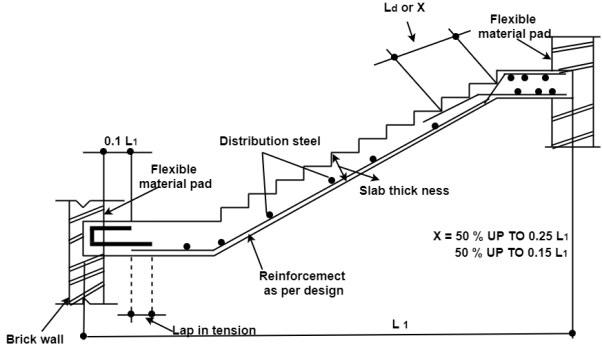
Fig. Cross section details of a single span straight flight supported on brick wall
Example 1) Design of dog-legged staircase first flight as shown in fig. For following details.
Floor to floor height = 2.88 m
Riser = 160 mm
Tread = 250 mm
Material M20 and Fe 415
At plinth level beam is provided below first step where as at mid landing level; and first floor level beam is provided at the outer face of landing show detailed load calculation and reinforcement details in sectional elevation.
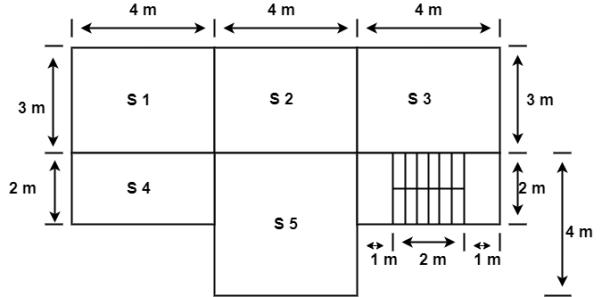
Solution:
R= 160mm, T= 250mm, Fck = 20 N/mm2 , Fy = 415 N/mm2
Number of tread = 2000/250 = 8
Step 1) Effective span
For flight I, L1 = 3m
Design of first flight
Step 2) Depth by serviceability criteria
Refer clause 23.2.1, page no. 37 of IS 456-2000
Ratio span to effective depth = 20 X MF
(L/d) = 20 X MF
Assume percentage of steel = 0.45% from fig. 4 IS 456-2000
Modification factor is 1.25 for Fe 415
d = L
20 MF
d = 3000/ (20 X 1.25)
d = 120mm
Assume diameter of longitudinal steel = 10 mm and cover 15mm
Overall depth of slab
D = d + ɸ/2 + c
= 120 + (10/2) + 15
= 140 mm
Step 3) Load calculation:
a. Dead load of waist slab on horizontal span
DLws = γ D X R2 + T2
T
= 25 X 0.14 X (0.16 + 0.25)
0.25
= 4.16 KN/m2
Floor finish load = 0.75 KN/m2
Live load = 3 KN/m2
Total udl on portion landing = (DLw + FF + LL)
= (4.16+ 0.75 + 3)
= 7.19 KN/m2
Factored load per meter Wu1 = 1.5 (7.91)
= 11.87 KN/m
Dead load of step = R/2 x γ
Total udl on step portion = (DLw + FF + LL) + DLstep
= (7.19 + 2)
= 9.91 KN/m2
Factored udl on step portion = 1.5 (9.91)= 15 KN/m
Step 4) Bending moment calculation
ΣMB =0
RA X 3 – 15 X 2 (2/2+1) – 12 X ½ = 0
RA = 22 KN
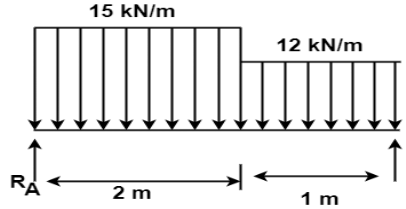
Maximum bending moments occurs where shear force is zero
Σ Sf = 0
RA – 15X = 0
22 = 15 X
X = 22/15 = 1.47 m
Maximum bending moment
Mmax.m = 22 X- 15X2/2
=16.06 KN.M
Step 5) Required depth for bending
Mu lim For Fe415
Mu, lim = 0.136 fckbd2
= 0.136 X 20 X 1000d2
= 2710d2
Equating bending moment to limiting moment
d = 78.4mm
d provided < d req.
Safe in bending
Step 6) Longitudinal reinforcement
Minimum Ast = 0.12/100 X b X d
= 0.12/ 100 X 1000 X 140
= 168 mm2
Ast = 0.5 Fck 1- 1- 4.6 mu x b x d
Fy Fck x b x d2
= 416 mm2> Ast.min. O.K.
Spacing for 10 mm dia.bar
A ɸ = π/4 X (10)2
= 78.54
Spacing = 1000 X A ɸ
416
= 188 mm
= 175 mm
Provide 10mm ɸ about 175mm c/c
Step 7) Distribution steel
Ast = Ast minimum = 168mm2
Spacing for 8 mm ɸ
A ɸ= π/4 X (8)2
Spacing = 1000X A ɸ
Ast
= 1000 X 50.27
168
= 299mm
= 275mm
Provide distribution steel 6mm ɸ @ 275mm
Step 8) Development length
Ld = 0.87 fy ɸ
1.6 (4Tbd)
= 0.87 X 415 X 10
1.6 X 1.92
= 470 mm
Step 9) Reinforcement detailing
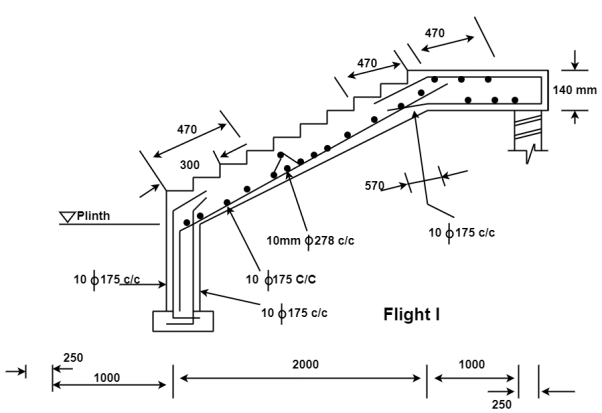
Key take ways
Step 1) Preliminary depth of slab (waist slab and landing slab)
- As per limiting stiffness criteria
D Eff. Or D Req. = L Eff.
(l0/d)basic x α
Assuming α = 1.25
D = d eff. + Nominal cover + ɸ/2
2. Effective span calculation:
- When top and bottom riser with landing is supported but beam the effective span is c/c distance of beam.
- When spanning on the edge of landing and below the top riser effective span.
Going + each end either half the landing one m whichever < and small
c. In case of open well staircase L eff. Is taken into c/c dist. Of beam.
Step 2) Load calculation
- Load on waist slab
- Self wt. Of slab = 25D
- When due to finishing of soffit = unit wt. Of plaster x thickness of plaster
- Self wt. Of step = Area x length x unit wt. Of concrete x steps along 1m length
Self wt. Of steps = ½ X R X T X 1 X 25 X (1/ T)
Self wt. Of steps= 12.5 R
d. Wt. Due to finishing of steps= unit wt of plaster X thickness
e. Live load= For residential building ( 2 to 3 KN/M2) and for important building ( 4 to 5 KN/M2)
2. Load on landing slab:
- Self wt. Of slab = 25D
- Floor Finishing
- Live load
Step 3) Calculation for design moment
- Design of flight one
- Design moment: calculate maximum BM and maximum SF from the loading dia. Of flight no. 1
Check for depth: d req. = BM max.m
Ru .b
d req. < d prov. (Hence O.K)
c. Amount of Ast. And Sv
- Main steel
Ast min. = 0.12% X b X d
S.P. Max. = 3d or 300mm<
Ast= 0.5 Fck 1- 1- 4.6 mu x b x d
Fy Fck x b x d2
2. Spacing
Sv = 1000 ast
Ast
3. Distribution steel
Ast min.m = 0.15 x b x d
S.P. Max = 5d or 450mm <
Sv = 1000 ast
Ast
2. Design of flight second
- Design moment
Calculate BM and SF maximum from loading Dia. Of flight no. 2
b. Check for depth
c. Amount of steel and spacing
Step 4) Check for deflection
Step 5) Check for shear
Step 6) Development length
Step 7) Reinforcement detailing
When the aspect ratio (ly / lx) is less than 2, the slab is called as two way slab.
Aspect ratio = ≤ 2, ……………it is two way slab
When the slab is supported along its all four edges and bends in two orthogonal direction, main reinforcement is provided in such slabs in two directions.3.2 Restrained Slab
Restrained slabs are corners are prevented from lifting due to effects of torsional moments.
Restrained slabs are divided into two types of strips in each direction:
One middle strip of width equal to three-quarters of the respective length of span ineither directions,
Two edge strips, each of width equal to one-eighth of the respective length of span in either directions.
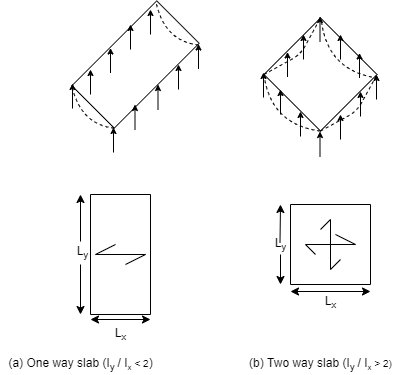
Fig no 13 One way and two-way slab
In restrained slab, the effect of torsion is taken into account and the bending moment coefficient with provision of torsion at corners are given in table 26, clause D-1.1 of IS456 : 2000.
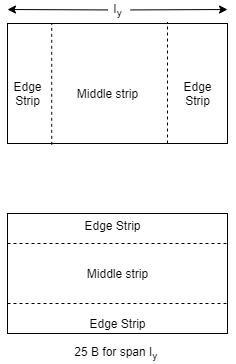
Fig no 14 Simply Supported Two Way Slab
Simply supported slabs are supported along the four edges with corners held down and loaded uniformly.
IS456: 2000 has given a simple method for designing simply supported slabs which do not have adequate provision to resist torsion at corners and to prevent the corner from lifting.
In this method the maximum bending moment is calculated by adopting bending moment coefficient specify in Table no. 27, clause D-2.1 of IS456 : 2000.
Bending Moment in Two Way Slab
In two slab, bending moment in both direction is predominant and hence provided main reinforcement in both directions.
Bending moment in each direction is calculated by
Mx = αxw L2x
My = αy w L2x
Where ,
Mx, My = Moment per unit width spanning 1x and Iy respectively
αx, αy= Coefficients given in Table 26 Annex D Page No. 91 of IS456 : 2000.
The moment developed is depends upon edge conditions.
Following are the various moment constrained (boundary conditions)
- All four edges continuous (interior panels)
- One short edge discontinuous
- One long edge discontinuous
- Two adjacent edges discontinuous
- Two short edge discontinuous
- Two long edge discontinuous
- Three edge discontinuous and one long edge continuous
- Three edge discontinuous and one short edge continuous
- Four edges discontinuous but corners held down by providing torsion reinforcement
- Simply supported slab without torsion reinforcements.
- Type of panel with boundary condition.
Bending moment coefficients for rectangular panels supported on four sides with provision for torsion at corers (Clauses D- 1.1, Table 26 and 24.4.1) as a below table.
Type of panel and moments considered
Short span coefficient ( value of Lx / Ly)
Long span coefficient ( value of Lx / Ly)
When corner of slab do not prevented from lifting are moment coefficient is given in Table 27, Page No. 91, of IS456: 2000.
Bending moment coefficients for slabs spanning in two directions at right angles, simply supported on four sides as the below table.
Problem:
1) Design a RC slab for a store room having clear dimensions as 4.77m x 3.77 m. The slab is to be casted monolithically over the 230mm wide beam with corners of slab held down. The slab carries live load of 3 kN/m2 and floor finish of 1 kN/m2Use M20 grade of concrete and Fe415 grade of steel. Also show details of reinforcement.
Answer:
Given:
Longer span ly = 4.77 m.
Support beam width bs = 230 mm.
Shorter beam lx = 3.77 m.
Condition : corners of slab held down
Live load LL = 3 kN/m2,
M20 Fe 415.
Floor finish FF = 1 kN/m2
Fck = 20 N/mm2
Fy = 415 N/mm2
Solution
Step 1: Aspect ratio: =ly /LX = 1.265 < 2 ……….It is a two way slab
Step 2: Trial depth of the slab
For shorter span 3.77> 3.5m, Ref. Clause 23.2.1 of fig – 4, of IS 456:2000 so that lx/d ratio given in clause 24.1 is not applicable.
Assume percentage steel 0.3 %, modification factor is 1.45 For Fe500
Fs = 9.58 fy = 0.58 x 415 = 240 mpa
Dreq = span /20 MF
Dreq = 130 mm
Assuming cover 15 mm and diameter of bar 8 mm
D = d + c + d/2
= 130 + 15 + 8/2
= 149 mm
d = D – c – d/2 = 150 – 15 – 8/2 = 131mm
Step 3: Calculate efficiency span leff
L effective = Lx + d
= 3.77 + 0.131= 3.901 m
L effective = Lx + b
= 3.77 + 0.23 = 4 m
Leff= 3.9 m …………whichever is less
Step 4: Load calculation:
Self weight = 0.15 x 1 x 25 = 3.75 KN/m
F.F = 1 KN/m
L.L = 3 KN/m
Total = 7.75 KN/m
Factored load = 1.5 x 7.75 = 11.625 KN/m
Step 5: Factored moment:
Mx = α x w L2x
My = αy w L2x
Since the slab is monolithically casted with corners of slab held down ( Ref : IS 456 – 2000 , table 26 , case 9 )
Four edges discontinuous
Ly/ lx | ![]() | ![]() |
1.2 | 0.072 | 0.056 |
1.3 | 0.079 | 0.056 |
x= 0.072 +((0.079- 0.072)/(1.3- 1.2)) ( 1.265 – 1.2 ) = 0.076
αy = 0.056
Mux = 0.076 x 11.625 x (3.9)2= 13.54 KN m
Mu y = 0.056 x 11.625 x (3.9)2= 9.89 KN m
Mumax = 13.54 KN.m
Step 6: Determine required depth of bending:
For Fe415
Mu.lim = 0.138fckbd2
13.54 x 106= 0.138x 20 x 1000d2
d = 70 mm < 131mm
If drequired<dassumed …………….. safe for flexure.
Step 7: Determine main steel:
Shorter span:
Astx = 0.5 fck/ fy (1- √ 1- ((4.6 Mu)/(f CK b d 2)) b d
Astx = 300 mm2
Longerspan :
d = ( 131 – 8) = 123 mm
Asty= 0.5fck/fy(1-√1-((4.6Mu)/(fCKbd2))bd
Asty = 232 mm2
Minimum area of steel in tension for HYSD
Ast min = 0.12 % of A gross = 0.12 % bD
Ast min = x 1000 x 150
= 180 mm2
BothAstx and Asty>Ast min ………….….ok
Step 8: Spacing:
Spacing required for A s tx
Spacing of 8 mm diameter of bar
Spacing , s = 1000 ast / Ast
s = 167.6 = 160 mm c/c
Check , s < 3d or 300mm
160 <393 ………………..ok
Provided main reinforcement of 8 mm diameter of bar @ 160 mm c/c
Spacing required for Asty
Spacing of 8 mm diameter of bar
Spacing , s = 1000 ast / Ast
s = 216.6 = 210 mm c/c
Check , s < 3d 04 300mm
210 < 393 ………………..ok
Provided main reinforcement of 8 mm diameter of bar @ 210 mm c/c
Step 9: Torsion steel:
Clause D – 1.8 page no. 90. IS 456 : 2000
As the corner of the slab held down ( i.e. torsional restrained at corner ), corner reinforcement has to provided in form meshes at top and bottom at each corner.
Side of mesh = LX / 5=3900/5 = 780 mm
Area of steel in each layer = 3/7 Astx= 3/7 x 300 = 225 mm2
Spacing , s = 1000 ast /Ast
s = 125 mm c/c
Provided 4 – 8 mm diameter bar both at top and bottom at each corner.
Step 10: Check for deflection
F s = 0.58 fy area of steel required/ area of steel provided
Astreq = 300mm2
Astprovided = 1000 ast / S required
Astprovided = 314.16 mm2
Fs = 0.58 x 415 x (300/314.16)
= 230 mm2
Ptactual= x 100
Pt actual = Ast /BD x 100
Pt actual = 0.24% > 0.12 %
Actual modification factor for pt = 0.24% and for Fe415 is 1.65 ( as per fig 0f modification factor of tension reinforcement)
Depth required (for deflection) = span /20 MF
Depth required (for deflection) = 118.2 mm
As D req for deflection < D req
118.2 mm< 131 mm ……………..ok
Slab is safe in deflection
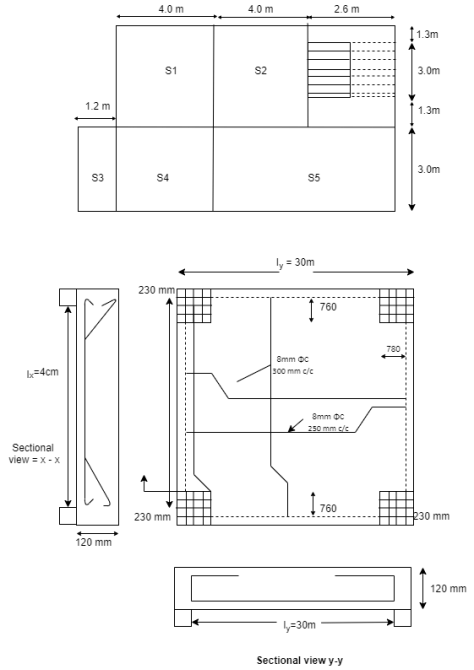
Fig no 15 Reinforced detailing
2) Design slab panel S4 shown in Fig. Only for flexure. Use take live load = 4 kN/m2. Floor Finish = 1.5 kN/m2. Draw neat sketches showing details of reinforcement. Use LSM. Material M25 and Fe415.( May – 2016)
Answer:
Given:
Longer span ly = 4 m.
Shorter beam lx = 3 m.
Live load LL = 4kN/m2,
M25 , Fe 415.
Floor finish FF = 1.5kN/m2
Fck = 25 N/mm2
Fy = 415 N/mm2
Solution:
Step 1: Aspect ratio: =l y/ lx= 1.333 < 2 ……….It is a two way slab
Step 2: Trial depth of the slab
For shorter span 3 < 3.5m, Ref. Clause 23.2.1 of fig – 4, of IS 456:2000
Assume modification factor is 1.5 ,For Fe415
Dreq = span/ 20 MF
Dreq = 100 mm
Assuming cover 15 mm and diameter of bar 8 mm
D = d + c + d/2
= 100 + 15 + 8/2
= 120 mm
d = D – c – d/2 = 120 – 15 – 8/2 = 101mm
Step 3: Calculate efficiency span leff
L effective = Lx + d
= 3 + 0.101= 3.101 m
L eff= 3.101 m
Step 4: Load calculation:
Self weight = 0.101 x 1 x 25 = 2.525 KN/m
F.F = 1.5 KN/m
L.L = 4 KN/m
Total = 8.025 KN/m
Factored load = 1.5 x 8.025 = 12.03 KN/m
Step 5: Factored moment:
Mx = αx w L2x
My = αy w L2x
( Ref : IS 456 – 2000 , table 26 , case 3 )
One long edges discontinuous
Ly /Lx | Alpha X 1.3 | 1.4 | Alpha y |
Negative moment at continuous edge | 0.057 | 0.063 | 0.037 |
Positive moment at mid span | 0.044 | 0.047 | 0.028 |
Negative moment at continuous edge :
αx= 0.057 + ((0.063 - 0.057)/(1.4-1.3))( 1.333– 1.3 ) = 0.059
αy = 0.037
Positive moment at mid - span:
αx= 0.044 + ((0.047-0.044)/(1.4-1.3)) ( 1.333– 1.3 ) = 0.045
αy = 0.028
Negative moment at continuous edge:
Mux = 0.059 x 12.03 x ( 3.101)2= 6.828KN.m
Muy = 0.037 x 12.03 x ( 3.101)2= 4.283 KN.m
Positive moment at mid – span :
Mux = 0.045 x 12.03 x ( 3.101)2= 5.208KN.m
Muy = 0.028 x 12.03 x (3.101)2= 3.241 KN m
Mu max = 6.828KN.m
Step 6: Determine required depth of bending:
For Fe415
Mu.lim = 0.138fckbd2
6.828 x 106= 0.138x 25 x 1000d2
d = 44.81 mm < 101mm
If drequired<dassumed …………….. safe for flexure.
Step 7: Determine main steel:
Astx = 0.5 fck/ fy (1- √ 1- ((4.6 Mu)/(f CK b d 2)) b d
Astx 1 = 193.50 mm2
A s tx = 0.5fck/fy(1-√1-((4.6Mu)/(fCKbd2))bd
Astx 2 = 164.4 mm2
d = (101 – 8) = 93 mm
Asty =0.5fck/fy(1-√1-((4.6Mu)/(fCKbd2))bd
Asty 3 = 130.67 mm2
A s ty = 0.5fck/fy(1-√1-((4.6Mu)/(fCKbd2))bd
Asty 4 = 98.29 mm2
Minimum area of steel in tension for HYSD
Ast min = 0.12 % of A gross = 0.12 % bD
Ast min = 0.12 x 1000 x 120
= 144 mm2
Step 8: Spacing:
Spacing required for Astx 1
Spacing of 8 mm diameter of bar
Spacing , s = 1000 ast /Ast
s = 259.8 = 250 mm c/c
Check , s < 3d or 300mm
250 <363 ………………..ok
Provided main reinforcement of 8 mm diameter of bar @ 250 mm c/c
Spacing required for Ast 2
Spacing of 8 mm diameter of bar
Spacing , s = 1000 ast /Ast
s = 343mm c/c
Check , s < 3d or 300mm
343 < 393
343 > 300mm
Take , s = 300mm…….
Provided main reinforcement of 8 mm diameter of bar @ 300 mm c/c
Step 9: Check for deflection
F s = 0.58 f y A s t required/A s t provided
Astreq = 193.5 mm2
Astprovided = 1000 Ad /S required
Astprovided = 167.55 mm2
Fs = 0.58 x 415 x 193.5/167.55
= 230 mm2
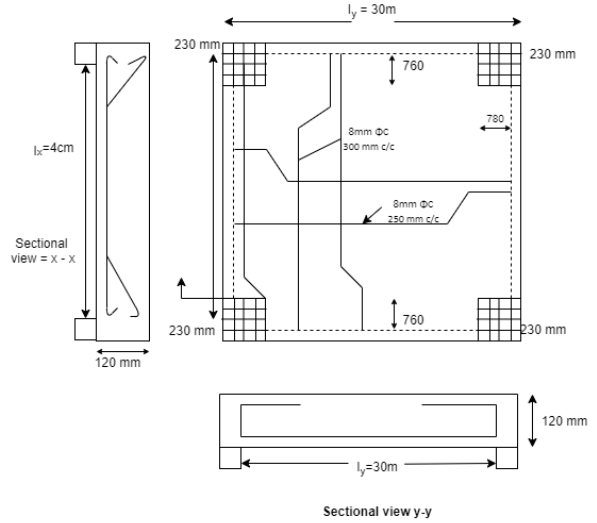
Fig no 16 Reinforced detailing
Pt actual= A s t /bd x 100
Pt actual = 0.19% > 0.12 %
Actual modification factor forpt = 0.19% and for Fe415 is 1.7( as per fig 0f modification factor of tension reinforcement)
Depth required ( for deflection) = span / 20 MF
Depth required ( for deflection) = 91.20 mm
As D req for deflection < D req
91.20 mm< 101 mm ……………..ok
Slab is safe in deflection
3) Design a simply supported two way slab over a room 4.8 m x 4 m effective with corners are free to lift carrying L.L of 4 kN/m2 and F.F of 1.5 kN/m2.use M20 and Fe 500. Draw details of reinforcement LSM is recommended.
Answer:
Given:
L y = 4.8 m
L x = 4m
F.F = 1.5 kN/m2
LL = 4 kN/m2
Solution:
Step 1: Aspect ratio: =ly /LX = 1.2 < 2 ……….It is a two way slab
Step 2: Trial depth of the slab
Assume percentage steel 0.3 %, modification factor is 1.4 For Fe500
Dreq = span/ 20 MF
Dreq = 142.86 mm = 143 mm
Assuming cover 15 mm and diameter of bar 8 mm
D = d + c + d/2
= 143+ 15 + 8/2
= 161.85 mm = 170 mm
d = D – c – d/2 = 170 – 15 – 8/2 = 151mm
Step 3: Calculate efficiency span leff
L effective = Lx + d
= 4 + 0.151= 4.151 m
Leff= Lx + b
= 4 + 0.23 = 4.23 m
L effective = 4.151 m …………whichever is less
Step 4: Load calculation:
Self weight = 0.17 x 1 x 25 = 4.25 KN/m
F.F = 1.5 KN/m
L.L = 4 KN/m
Total = 9.75 KN/m
Factored load = 1.5 x 9.75 = 14.625 KN/m
Step 5: Factored moment:
Mx = α x w L2x
My = αy w L2x
For , = 1.2 so that , αx = 0.084 , αy = 0.059
Mux = 0.084 x 14.625 x (4.15)2= 21.18KN.m
Muy = 0.059 x 14.625 x (4.15)2= 14.86KN.m
Mumax = 21.18KN.m
Step 6: Determine required depth of bending:
For Fe500
Mu.lim = 0.133fckbd2
21.18 x 106= 0.133x 20 x 1000d2
d = 87.6 mm < 151mm
If drequired<dassumed …………….. safe for flexure.
Step 7: Determine main steel:
Shorter span:
Astx = 0.5fck/fy(1-√1-((4.6Mu)/(fCKbd2))bd
Astx = 341.97 mm2
Longerspan :
d = ( 151 – 8) = 142 mm
Asty = 0.5fck/fy(1-√1-((4.6Mu)/(fCKbd2))bd
Asty = 251.86 mm2
Minimum area of steel in tension for HYSD
Ast min = 0.12 % of A gross = 0.12 % bD
Ast min = x 1000 x 170
= 204 mm2
BothAstx and Asty>Ast min ………….….ok
Step 8: Spacing:
Spacing required for Astx
Spacing of 8 mm diameter of bar
Spacing , s = 1000 ast /Ast
s = 147 = 140 mm c/c
Check , s < 3d or 300mm
140 <453 ………………..ok
Provided main reinforcement of 8 mm diameter of bar @ 140 mm c/c
Spacing required for Asty
Spacing of 8 mm diameter of bar
Spacing , s = 1000 ast /Ast
s = 199.71 = 190 mm c/c
Check , s < 3d 0r 300mm
190 < 453 ………………..ok
Provided main reinforcement of 8 mm diameter of bar @ 190 mm c/c
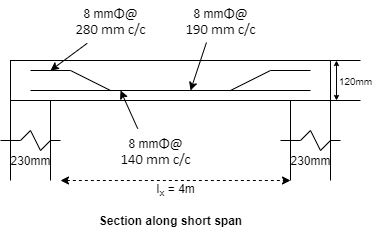
Fig no 17 Reinforcement
Key takeaways:
Design steps of two way slab
Step 1: Aspect ratio
Step 2: Trial depth of the slab
Step 3: Calculate efficiency span l effective
Step 4: Load calculation:
Step 5: Factored moment:
Step 6: Determine required depth of bending:
Step 7: Determine main steel:
Step 8: Spacing:
Serviceability limit states square measure verified in keeping with the chapter seven of nut 1992-1-1. Analysis of usableness limit states checks the desired service needs for a structure or support throughout its operating life.
Cross-sections square measure assumed to be cracked for any tensile stress throughout the analysis of usableness limit states. The user outlined setting is in a position to think about cross-sections with tensile stress up to the average of axial lastingness fctm as uncracked.
Working to accomplish the work required by their service life. For example, think of a reinforced concrete water tank, do you want the tank to break?! Of course not! Because water will leak out. This is a simple example of the value of a building that will work.
One of the useful features is a deficiency in flexible materials such as beams and slabs. Being within the permissible limits of deviation is important, even if the member is structurally safe, because people will not be comfortable when the upper floor is shaky and, of course, money would be charged for renovations.
In this article, additional steps are being taken to control the reduction of reinforced concrete beams and slides.
1- Increase Element Size
This includes increasing the thickness of the slabs and increasing the width and / or depth of the beams. Profits from growing sizes can be disclosed if we mentioned the separation of the standard beam that is not allowed to be cracked or slipped.
Where I in the previous figure is inertia. In the rectangular section,
Therefore, increasing b or d will result in a reduced amount of deviation. However, it is important to note that the effect of increase d is more important than the increase b.
2- The use of reinforcement reinforcement
Typically, slabs and beams have main reinforcing bars on the side of the tension only and the bars on the pressure side are used as suspensions for the beams or to control the shrinkage and penetration of slabs.
However, if these second bars are used to withstand the force of compression, it may help to reduce the amount of deviation.
Recognize that adding barriers to congestion will not affect the immediate decline but will also affect the long-term escape rate.
This method is less commonly used and has a greater impact on deeper beams than on shallow beams or slabs.
3- Use of Pre-stressing
Simply put, pre-pressure is the use of an external load that creates a moment that works against time from dead and live loads. The result will be a reduced deviation
CRACKING
1. Decreased plastic cracking of the plastic
When the concrete is in its plastic state (before hardening), it is filled with water. When that fluid finally leaves the sieve, it leaves behind large gaps between the solid particles. These blank spaces make the concrete fragile and more prone to cracking. This type of cracking occurs more frequently and is called "plastic shrinkage cracking".
While sloping plastic cracks can occur anywhere on the slab or wall, they almost always occur in intersecting corners (corners pointing to the slab) or with circular objects between slides (pipes, plumbing fixtures, drains and holes). Since the concrete will not sink into the corner, the pressure will cause the concrete to crack from the location of that corner cracks in plastic shrinkage
Decreased plastic cracks are usually very small in width and invisible. While it is almost invisible, it is important to remember that cracks in plastic shrinkage not only affect the surface, they extend to the entire size of the lab.
Excessive wet mixing is a contributing factor to the reduction of concrete. While water is an important ingredient in any concrete mix, there is such a thing as too much water. When the mixture contains too much water, the slab will shrink beyond the use of the right amount of water. The hot weather is another major cause of cracks in plastic decay.
Control joints can be inserted into the slide to prevent shrinkage cracking. The joints will open as the concrete lump becomes smaller.
2. Expansion of concrete cracks
Expansion cracks
Like a balloon, heat causes the concrete to expand. As the concrete expands, it presses on anything in its path (a brick wall or a nearby slab). When there is no flexibility, growing strength may be enough to cause concrete.
Extension joints are used as a point of separation (or separation), among other fixed areas. Often made of compact materials such as asphalt, rubber, or wood, the expansion joints must act as shock absorbers to relieve stress extensions that include concrete and prevent cracks.
3. Reduction of concrete cracks
Cracks burst
When the soil is cold, you can sometimes lift several inches before melting and sitting down. The movement of the earth brought about by the cycle of freezing and thawing is a major factor in the cracking of concrete. If the slab does not have freedom of movement, the slab will crack.
The roots of large trees can have a similar effect on a slide. If the tree is too close to the slab, the growing roots can lift and crack the concrete. Always keep this in mind when you put the label on.
4. Repairing concrete cracks
To repair cracks
On the other hand, sitting on a concrete slide can also cause cracks.
Fixing cracks occurs in cases where a gap is created in the soil beneath the concrete. Imagine when a large tree is removed near the roots begin to rot or when the company used to dig a trench for their ropes, pipes, etc. repairing cracks is possible.
5. Crack of concrete caused by overcrowding of the slide
Overloading cracks
Although concrete is a very durable material, it has its limitations. Putting too much weight on a concrete slide can cause cracks. If you feel the concrete mix is stronger than 2000, 3000, 4000, or 5000 + PSI, it refers to the kilograms per square inch that can take to crush that concrete slab.
When it comes to concrete tabs that reside, real overload slides are not all that. Instead, it is likely to occur in excess of the ground under the slide.
After heavy rain or snow when the ground below is soft and wet, excess weight in the container can compress the concrete on the ground and lead to cracking. Homeowners who live there who park their luxury cars or garbage dumps on their driveways often see this kind of cracking.
6. Concrete cracks are caused by premature drying
Cracks for premature drying
There are two common types of cracks caused by premature drying.
Cracking cracks are very good, more cracks like spider webs or cracked glass. When the surface of the concrete slide loses moisture very quickly, cracks may form. While unsightly, sector fragmentation is not a construction concern.
Splitting cracks occur during the concrete installation process, which is a way to add texture or pattern to concrete areas. On hot or windy days when the top of the slide dries faster than the bottom, the top of the concrete surface can bend. When the stamp is embedded, it pulls the surface farther away from the sealed joints and creates small cracks around the outer edges of the “stones”. And, although they may not look good, splitting spears is not a structural problem to consider.
It is often difficult to pinpoint exactly what caused an explosion. Proper site preparation, quality mixing, and good concrete finishing practices can go a long way in reducing the appearance of cracks and producing a more enjoyable concrete project.
We cannot stress the importance of quality design in concrete control. Read the Concrete Checklist: Find the Best Mix for Your Project, which will show you and your concrete provider how to create the right mix for your integration project.
VIBRATION
- The durability, softness, and natural frequency are the parameters required in the vibration analysis of any reinforced concrete floor plan. The following recommendations and standardized procedures can be used in the first stage of design to quickly identify the types of high-quality systems that are suitable to satisfy the required vibration conditions.
- Strength. Stabilization of the stage system has a direct impact on the natural frequency: it increases the density of the floor, greatly increases the natural frequency, which translates into a possible decrease in the negative effects of vibration.
- In standard concrete floor systems at standard measurements, a large part of the system decline is due to flexibility. Therefore, only the dynamic dynamics of the lower EcIe need to be considered. Ec abundance is a form of concrete reinforcement. Because concrete plates are smaller when placed in heavy loading, it is advisable to use a value of 20 to 30 percent larger than the specified code value. The word Ie is an active term for inertia. It is recommended to include the effects of cracks when first determining the durability of a non-compressed subcutaneous system as the natural frequency can be overestimated if left unchecked. A clearer analysis of the analysis can always be done later, if desired.
- Relief. Damping is a measure of how fast vibration will eventually subside and eventually stop. It relies heavily on non-grounded building materials, such as people, pieces, file cabinets, bookshelves, and furniture, to name a few.
- The amount of dumping is often expressed as a percentage to reduce the critical figure and is often referred to as a water drain rate. A water level of 0.02 is recommended for floors with a few non-structural elements (such as electric offices), while a 0.05 ratio can be used where complete separation exists between floors (ATC 1999). A value of 0.03 is often used for office spaces with a partial height division. Further details on how to choose a waste minimization measure can be found in Hewitt and Murray, 2004.
- Natural frequency. The natural frequency is a measure of how the floor system will respond to sources that may cause vibration, and is related to how passengers will perceive that vibration. Many resources and methods are available to determine this area. It is usually easy to find this and other vibrating features from a commercial computer program. As with all software, it is very important to understand the methods used to calculate this parameter.
- The statistics in the table provide approximate values of the natural frequency of various reinforced concrete systems. They are made using basic energy principles. Further details on their use, including examples of the design used for the reinforced concrete floor systems, can be found in the Vibrations of Vibrations of Reinforced Concrete Floor Systems
Key takeaways:
Cracking
1. Decreased plastic cracking of the plastic
2. Expansion of concrete cracks
3. Reduction of concrete cracks
4. Repairing concrete cracks
5. Crack of concrete caused by overcrowding of the slide
6. Concrete cracks are caused by premature drying
Vibration
The durability, softness, and natural frequency are the parameters required in the vibration analysis of any reinforced concrete floor plan. The following recommendations and standardized procedures can be used in the first stage of design to quickly identify the types of high-quality systems that are suitable to satisfy the required vibration conditions.
References
- IS 456 2000
- Reinforced concrete design by M .L. Gambhir
- Reinforced concrete design by S.U.Pillai