UNIT– 6
Reciprocating Compressors
6.1. Reciprocating compressor
Principles on which compressors work:
A compressor is a mechanical device that increases the pressure of a gas by reducing its volume. (The fluid here is generally air since liquids are theoretically incompressible).
Classification of compressor:
There are mainly two types of Compressors-
2. Rotary compressor
Reciprocating compressor:
In a reciprocating compressor, a volume of gas is drawn into a cylinder, it is trapped, and compressed by piston and then discharged into the discharge line. The cylinder valves control the flow of gas through the cylinder and these valves act as check valves.
Reciprocating compressors can be Single acting or double acting.
Reciprocating compressor types:
Compression is done in single stage or by single cylinder only and it is used for generation of low-pressure air.
2. Double–stage Reciprocating Compressor:
It is a compressor that produces highly pressurized air and mostly it is used nowadays in heavy duty mechanical devices.
Different parts of reciprocating compressor:
Figure1: Reciprocating compressor
Principle of Operation:
Figure 2: Operation of Reciprocating compressor
Key takeaway:
6.2. Staging of reciprocating compressor:
Single Stage Reciprocating Air Compressor
Working Principle:
• Here, pressure is increased by means of variation in the volume of cylinder obtained by a moving piston.
Construction:
• Single stage single acting air compressor consists of a piston, which reciprocates inside a cylinder having connecting rod and crank mechanism.
• There are inlet and delivery valves mounted in the head of cylinder.
• The inlet and delivery valves are of pressure differential type i.e.; they operate as a result of pressure difference across the valves.
Working:
Working of single stage reciprocating air compressor is completed in two strokes.
a). Suction Stroke:
b). Compression Stroke:
Two stage reciprocating compressor:
Key takeaway:
6.3. Optimal stage pressure ratio:
The optimal stage pressure ratio for a multi stage compression is calculated with well-known formula that assigns an equal ratio for all stages based on the hypotheses that all isentropic efficiencies are also equal.
For minimum power consumption in industrial applications, gases should ideally be cooled at the same time they are being compressed, maintaining their initial temperature as constant during the whole process. The increase in power consumption caused by compressing a gas that is progressively getting hotter, with large mass flows and long operating hours can be economically unstable.
It is given by,
r =
Key Takeaways:
Important formula for optimal stage compression ratio is given as-
r =
6.4. Effect of Intercooling:
An intercooler is any mechanical device used to cool a fluid, including liquids or gases, between stages of a multi-stage heating process, typically a heat exchanger that removes waste heat in a gas compressor. They are used in many applications, including compressors, air conditioners, refrigerators, and gas turbines.
Effects of intercooling on Brayton cycle:
Figure 3: Intercooling on Brayton cycle
For ideal cycle with intercooling
Wc = C p (T 2a -T 1) + (T 2 -T 2b)
Heat supplied
Qs = C p (T 3 -T 2)
Work by turbine: W t =C p (T 3 -T 4)
Thermal efficiency of gas turbine cycle with intercooling:
Key takeaway:
6.5. Minimum work for multistage compressor:
Maximum work is saved in a two-stage reciprocating air compressor with perfect intercooling. Work required to be done by a two-stage reciprocating air-compressor with complete intercooling is given by-
If the intake pressure and delivery pressure are constant, then the least value of the intermediate or intercooler pressure may be obtained by differentiating the above equation with respect to intercooler pressure. At this value of intercooler pressure, the work required to drive the compressor is minimum.
Now considering (a constant)
This is the condition of minimum work required for a two stage reciprocating air-compressor,
Now Substituting in equation (1)
In, general for compressor having q number of stages,
Condition for minimum work required,
And minimum work required for compression,
Key takeaway:
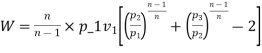
3. Minimum power required for compression is given by-
References:
1) Engineering thermodynamics P.K nag
2) I.C engineering =m.l mathur