Unit - 2
Helical, Bevel, Worm and Worm Wheel


The normal pitch may also be defined as the circular pitch in the normal plane which is a plane perpendicular to the teeth. Mathematically, normal pitch,
Pressure angle in the plane of rotation, ϕ =15° to 25°
Helix angle α = 20° to 45°
Addendum=0.8m
Dedendum= 1m
Minimum total depth= 1.8m
Minimum clearance=0.2m
Thickness of tooth=1.5708m
Let =total normal force
=tangential force
=axial force
=radial force
=normal force in the plane of
=Pressure angle
=Normal pressure angle
=Helix angle
Then
force applied tangentially on the driver,
=resisting force acting tangentially on the driven.
axial or end thrust on the driver
=axial or end thrust on the driven
= normal reaction at the point of contact,
= Angle of friction
R= resultant reaction at the point of contact
From triangle OPQ,
Work input to the driver
From triangle OST,
The work output of the driven
The efficiency of spiral gears,
………… 1
t pitch circle diameter of gear 1,
And pitch circle diameter of Gear 2
……………. 2
We know that ……………. 3
Multiplying equation 2 and 3 we get
Substituting this value in equation 1 we get
…….. 4
………… 5
Since the angles are constants, therefore the efficiency will be maximum, when.
) Is maximum.
or
Since , therefore
Similarly,
Similarly, in the equation we get

Where a and b are semi-major and semi-minor axis respectively.
Where, T= actual number of teeth on a helical gear, and
=Helix angle

5. Addendum angle:- It is the angle subtended by the addendum of the tooth at the cone center. It is denoted by Mathematically, addendum angle,
a= Addendum and OP=Cone distance
6. Dedendum angle:- It is the angle subtended by the dedendum of the tooth at the cone center. It is denoted by mathematically, dedendum angle,
d= Dedendum and OP=Cone distance
7. Face angle:- It is the angle subtended by the face of the tooth at the cone center. It is denoted by . The face angle is equal to the pitch angle plus addendum angle.
8. Root angle:- It is the angle subtended by the root of the tooth at the cone center. It is denoted by . It is equal to the pitch angle minus the dedendum angle.
9. Back cone:- It is an imaginary cone, perpendicular to the pitch cone at the end of the tooth.
10. Back cone distance:- It is the length of the back cone. It is denoted by It is also called a back cone radius.
11. Backing:- It is the distance of the pitch. From the back of the boss, parallel to the pitch point of the gear. It is denoted by B.
12. Crown height:- It is the distance of the crown point from the cone center, parallel to the axis of the gear. It is denoted by
13. Mounting height:- It is the distance of the back of the Boss from the cone center. It is denoted by
14. Pitch diameter:- It is the diameter of the largest pitch Circle.
15. Outside or addendum cone diameter:- It is the maximum diameter of the teeth of the gear. It is equal to the diameter of the blank from which the gear can be cut. Mathematically, outside diameter,
Pitch circle diameter
a= addendum and
=Pitch angle
16. Inside or dedendum cone diameter:-the inside of the dedendum cone diameter is given by
=Inside diameter, and
d= dedendum
The proportions for the bevel gears may be taken as follows:-
Where m is the module.
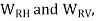
And the radial force acting on the pinion shaft,
2. Lead:- It is the linear distance through which a point on a thread moves ahead in one revolution of the worm. For single start thread lead is equal to the axial pitch, but for multiple start threads, lead is equal to the product of pitch and number of stars. Mathematically,
= axial pitch; n=number of starts.
3. Lead angle:- It is the angle between the tangent to the thread helix on the pitch cylinder and the plane normal to the axis of the worm. It is denoted by .
m =module, and
=pitch circle diameter of the worm.
4. Tooth pressure angle:- It is measured in a plane containing the axis of the warm and is equal to one half of the thread profile angle as shown in the figure.
5. Normal pitch:- It is the distance measured along the normal to the threads between two corresponding points on two adjacent threads of the worm. Mathematically,
Normal pitch,
6. Helix angle:- It is the angle between the tangent to the thread helix on the pitch cylinder and the axis of the worm. It is denoted by.
7. Velocity ratio:- It is the ratio of the speed of worm in r.p.m. to the speed of the worm gear in the r.p.m. mathematically velocity ratio.
Let. l= lead of the worm, and
= pitch circle diameter of the worm gear.
Proportions for the worm
Sr No. | Particulars | Single and double threaded worms | Triple and quadruple threaded worms |
1 | Normal-pressure angle | 14.5° | 20° |
2 | Pitch circle diameter for worms integral with the shaft | ||
3 | Pitch circle diameter for worm’s board to fit over the shaft | 2.4 | |
4 | Maximum bore for shaft | ||
5 | Hub diameter | ||
6 | Face length | ||
7 | Depth of tooth | ||
8 | Addendum |
Proportions for worm gear
Sr No. | Particulars | Single and double threads | Triple and quadruple threads |
1 | Normal-pressure angle | 20 | |
2 | Outside diameter | ||
3 | Throat diameter | ||
4 | Face width | ||
5 | The radius of gear face | ||
6 | The radius of gear rim |
= Axial force or thrust on the worm gear.
The tangential force on the worm produces a twisting moment of magnitude x
and bands the worm in the horizontal plane.
2. The axial force of thrust on the worm
=tangential force on the worm gear.
The axial force on the worm tends to move the worm axially, includes an axial load on the bearings and bends the worm in a vertical plane with a bending moment of magnitude x
.
3. Radial or separating force on the worm
Radial or separating force on the worm gear.
The radial or separating force tends to force the worm and worm gear out of the match. This force also bends the worm in the vertical plane.
Numerical :
1. The center distance between two matching spiral gears is 260 mm and the angle between the shafts is 65°. The normal circular pitch is 14mm and the gear ratio is 2.5. The driven gear has a helix angle of 35°. Find the
G =2.5 C =260mm
Let the gear with a smaller number of teeth be the driver.
Or
Take
Then
=262.4mm
=0.883
2. Two start worm rotating at 800 rpm drives a 26-tooth worm gear. The worm has a pitch diameter of 54 mm and a pitch of 18 mm. If the coefficient of friction is 0.06 find the
Solution
(i) Unwrap one thread of the worm,
Helix angle
(ii) The pitch of wheel =Axial pitch of the worm
=18mm
(iii)
(iv) For maximum efficiency
=43.29
(v)
=0.77
(vi)
3. A drive is made up of two spiral gear wheels of the same hand, the same diameter and of the normal pitch of 14mm. The center distance between the ages of the shafts is approximately 150mm. The speed ratio is 1.6 and the angle between the shafts is 75°. Assuming of friction angle of 6° determine the
Solution
(i) Let be the spiral angle of the wheel 1.
Then the spiral angle of the wheel 2,
Now velocity ratio, VR=
(ii) The center distance
say 20
=152.4mm
(iii) Efficiency
=
(iv) Maximum efficiency
= 0.872
4. A pair of spiral gears are required to connect two shafts 175 mm apart, the shaft angle being 70°. The velocity ratio is to be 1.5 to 1, the faster wheel having 80 teeth, and a pitch circle diameter of 100mm. Find the spiral angles for each wheel. If the torque on the faster wheel is 75N-m. Find the axial thrust on each shaft, neglecting friction.
Solution:- Given L=175mm=0.175m;
Spiral angles for each wheel
Let &
We know that velocity ratio,
No. of teeth on the slower wheel
We also know that the center distance between shafts (L)
……… i
We know that
Substituting the value of in equation (i)
Axial thrust on each shaft
Torque=tangential force × pitch Circle radius
Tangential force at the faster wheel,
And normal reaction at the point of contact,
We know that axial thrust on the shaft of the slower wheel,
And axial thrust on the shaft of the faster wheel,
1) Theory of machines – Khurmi & Gupta
2) Machine design – Khurmi & Gupta
3) Theory of machines – S.S. Rattan
4) Design of machine elements – V. B. Bhandari
5) Ghosh Malik, Theory of Mechanism and Machines, East-West Pvt. Ltd.
6) Hannah and Stephans, Mechanics of Machines, Edward Arnolde Publication.
7) R L Norton, Kinematics and Dynamics of Machinery, First Edition, McGraw Hill Education (India) P Ltd. New Delhi
8) Sadhu Singh, Theory of Machines, Pearson
9) D.K. Pal, S.K. Basu, Design of Machine Tools, Oxford & Ibh Publishing Co Pvt. Ltd.
10) Dr. V. P. Singh, Theory of Machine, Dhanpatrai, and sons.
11) C. S. Sharma & Kamlesh Purohit, “Theory of Machine and Mechanism”, PHI.