UNIT III
Unit Costing
Costing is an accounting method that records and analyses all costs associated with the execution of a process, project, or product. Such analysis helps management make strategic decisions.
Costing uses a variety of techniques to make your organization cost-effective. Everything you need to know about the different costing methods. The term "costing method" can be used to refer to the various processes or procedures used to determine and display costs.
There are different costing methods in different industries, depending on the nature of the job. Costing methods can be studied under the head below. -1. Method based on the principle of job costing 2. Method based on the principle of process costing.
Costing methods can be studied under the head below. -1. Method based on the principle of job costing 2. Method based on the principle of process costing.
Some of the methods based on the principles of process costing are: -
1. Process costing
2. Operating costing
3. Department costing
4. Single or unit or output costing
5. Operation or operation or work or service costing
6. Multiple or combined costing.
In addition, some other costing methods are: -
1. Uniform costing
2. Multiple or combined costing
3. Department costing
4. Cost plus method
5. Target costing method 6. Farm costing
7. Activity-based costing.
Different types of costing methods: job costing, contract costing, batch costing, process costing, and operating costing
Different methods of costing – individual costing, contract costing, batch costing, process costing, unit costing, operating costing, operating costing, and multiple costing
The costing method refers to the cost confirmation and costing system. Industries differ in their nature, the products they produce, and the services they provide. Therefore, different costing methods are used in different industries. For example, the costing method used by building contractors is different from that of shipping companies.
Job costing and process costing are two basic methods of costing. Job costing is suitable for industries that manufacture or perform work according to customer specifications. Process costing is suitable for industries where production is continuous and the units of production are the same. All other methods are a combination, extension, or improvement of these basic methods.
Let's take a closer look at how to calculate costs.
Method # 1 Job costing:
This is also known as specific order costing. There is no standard product and each job or work order is adopted in a different industry. The work is done strictly according to the customer's specifications, and the work is usually completed in a short time. The purpose of job costing is to see the cost of each job individually. Job costing is used in printing presses, motor repair shops, car garages, movie studios, the engineering industry, and more.
Method # 2 Contract Costing:
This is also known as terminal costing. Basically, this method is similar to job costing. However, it is used when the work is large and it takes a long time. The work will be done according to the customer's specifications.
The purpose of contract costing is to see the costs incurred in each contract individually. Therefore, a separate account is provided for each contract. This method is used by companies engaged in the construction of ships, buildings, bridges, dams and roads.
Method # 3 Batch Costing:
This is an extension of job costing. A batch is a group of identical products. All units in a particular batch are uniform in nature and size. Therefore, each batch is treated as a cost unit and is costed separately. The total cost of the batch is checked and divided by the number of units in the batch to determine the cost per unit. Batch costing is adopted by manufacturers of biscuits, ready-made garments, spare parts medicines and more.
Method # 4 Process Costing:
This is called continuous costing. In certain industries, raw materials go through various processes before they take the form of final products. In other words, the finished product of one process becomes the raw material for the next process. Process costing is used in these industries.
A separate account is opened for each process to see the total cost and cost per unit at the end of each process. Process costing applies to continuous process industries such as chemicals, textiles, paper, soaps and foam.
Method # 5-unit costing:
This method is also known as single costing or output costing. It is suitable for industries with continuous production and the same unit. The purpose of this method is to see the total cost and the cost per unit. Create a cost sheet considering material costs, labor costs, and overhead costs. Unit costing applies to mines, oil rig units, cement factories, brick factories and unit manufacturing cycles, radios, washing machines, etc.
Method # 6 Operating cost:
This method is followed by the industry that provides the service. To determine the cost of such services, use composite units such as passenger kilometres and tone kilometres to determine the cost. For example, for a bus company, operating costs represent the cost of carrying passengers per kilometre. Operating costs are used in air railways, road transport companies (commodities and passengers) hotels, movie theatres, power plants, etc.
Method # 7 Operating cost:
This is a more detailed application of process costing. It includes costing by all operations. This method is used when there is a repetitive mass production with many operations. The main purpose of this method is to see the cost of each operation.
For example, manufacturing a bicycle handlebar involves many operations such as cutting a steel plate into appropriate strips, forming, machining, and finally polishing. The cost of these operations can be viewed individually. Operating costs provide a detailed analysis of costs to achieve accuracy and apply to industries such as spare parts, toy manufacturing, and engineering.
Method # 8 Multiple Costing:
Also known as compound costing. This refers to a combination of two or more of the above costing methods. It is used in the industry where multiple parts are manufactured separately and assembled into a single product.
Different methods of costing – single costing, job costing, contract costing, batch costing, process costing, operating costing, operating costing, and a few others
The term "costing method" can be used to refer to the various processes or procedures used to determine and display costs. There are different costing methods in different industries, depending on the nature of the job. For example, the chemical industry follows a continuous production process in which raw materials are processed at various stages. There are other industries that undertake different types of work. For example, motor workshops accept a variety of jobs.
In industries such as transportation, banking and insurance, the entire activity is centred on a particular service operation. Similarly, many other industries may produce only one product. The nature of the manufacturing process and the way it works varies from industry to industry, making it essential to use different costing methods.
Preparation of cost sheet & production account
Cost sheet and production account
Cost statements may be displayed in the form of ledger accounts called "production accounts." Production accounts analytically present production cost information according to double-entry bookkeeping. Production costs and profits can be calculated in this ledger. The cost sheet and production account are as follows:
PARTICULARS | AMOUNT |
Direct material Direct wages Direct Expenses |
|
Prime Cost |
|
Add: Factory Overheads |
|
Factory Cost |
|
Add: Administration Overheads |
|
Cost of Production |
|
Add: Selling and Distribution Overheads |
|
Total Cost /Cost of sales |
|
Cost sheet
A cost sheet is a device used to determine and display costs in unit costing. This is a statement of costs incurred at each level of manufacturing a product or service. The cost sheet takes into account all the factors of cost. This includes prime costs, factory / manufacturing costs, manufacturing costs, selling costs, profits / losses, and more.
According to C.I.M.A, London
Cost schedule or document that provides a detailed cost assembly estimated for a cost centre or cost unit."
Items excluded from the cost sheet:
1. Pure financial costs such as capital interest, interest on loans, discounts on corporate bonds, loss on sale of allowance for doubtful accounts, amortization of bad debts, copyrights and reserves.
2. Pure financial income such as interest received, gain on sale of investment, dividend received, rent received, commission received, discount received.
In addition to the above, the budget limit does not include the budget limit.
Key takeaways:
- Costing is an accounting method that records and analyses all costs associated.
- Cost statements may be displayed in the form of ledger accounts called "production accounts
Production account
Meaning:
A production account is a statement in a ledger account format cost or cost sheet that shows the output for a particular period, the total and unit costs incurred during that period, and its components, and the profits or losses for that period.
According to Glover and Williams, "The term manufacturing account is used to describe a particular type of manufacturing account created in combination with a financial account to indicate the actual manufacturing cost of goods manufactured during the review period. Used. These accounts may be created at short intervals. Monthly.
The production account is created in the format in which the transaction account is created. There are usually two parts. The first part shows the total cost and the cost per unit. The second part shows the cost of goods sold and the cost of goods sold.
When the details of a cost table or production statement are displayed in the form of a ledger account, it is called a production account. In addition to manufacturing costs, selling and distribution costs are also included. It is created in three parts. The first part shows the manufacturing cost, the second part shows the cost of goods sold, and the third part shows the cost of goods sold or total cost for that period. Here is a sample production account:
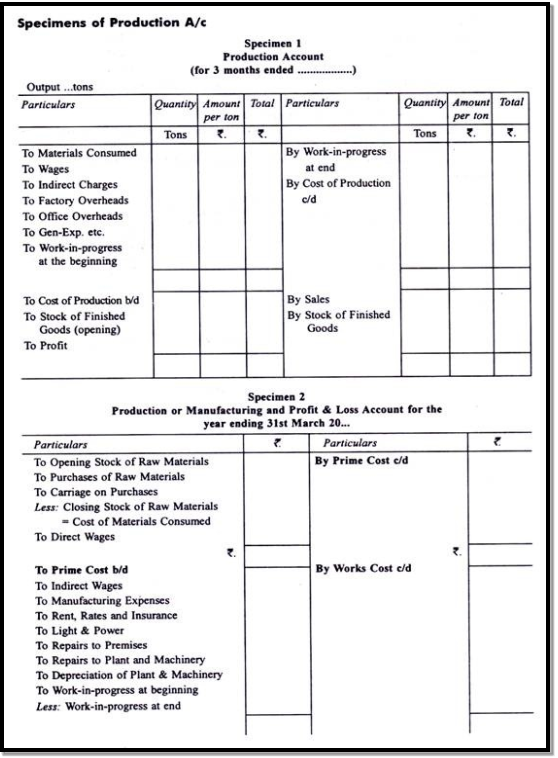
All companies are required to present the price of their products and services to their customers. There are several ways to do this.
- Many companies, such as beauty salons, use standardized price lists, which remain the same for all customers. Other companies, such as painters and decorators, need to offer prices tailored to the specific products and services that their customers want to buy. This is usually done with an estimate or an estimate. Large and complex projects are often priced based on detailed tender documents created by the customer.
This guide provides an overview of how to present prices to customers. Learn how to create a price list, the difference between a quote and a quote, how to create a quote and a quote, and how to price a contract bid.
- Create a price list
- The difference between a quote and a quote
- Create a quote
- Create a quote
- Prepare the price of the bid
- Win a contract at the right price
Prepare a price list
Most companies need to create a price list at a certain stage. If you sell a fixed range of products, this may be the only form of pricing you need. This type of standard price table can also be used as a basis for pricing non-standard orders.
It is recommended to date the price list. Especially if the customer is likely to hold it for a long time. It is necessary to clarify when the special offer will expire. It is also helpful to include a clause at the end of the price list that indicates that the price may change.We need to clarify whether shipping, packing and shipping are included in the price. In addition, it is not necessary to indicate discounts on bulk purchases in the price list, but they can attract more business.
You might be able to create complex price lists using software packages such as Sage Simply Accounting.
The difference between quotation and an estimate
- It is impossible for a few companies to supply standard prices for goods and services. This may be because the talents, time, and materials required for every job depend upon your needs.This situation is more common in some trades than in others. For example, decorators and builders rarely do the precise same job 2 times. If you cannot work from a typical list , you ought to submit a quote or quote instead.
- The quotation may be a fixed price offer and can't be changed after the customer accepts it.This is true albeit you would like to perform far more work than expected.
- .You can also specify exactly what you cover within the quote. Other variations are subject to a further charge.
- Estimates are guesses supported knowledge about the value of labor , but they're not binding. To take under consideration possible unexpected deployments, we'd like to supply some estimates supported different circumstances, including worst-case scenarios. This will prevent customers from being surprised by the value .
- To make an estimate or estimate, you would like to understand the fixed and variable costs. These include the value per 1 hour of manual labour and therefore the cost of the required materials. Then the estimate or estimate is calculated consistent with what seems to be relevant to the work.
- All estimates and estimates should be provided in writing and include an in-depth breakdown. This will avoid controversy about the work included within the overall price.
- You can also set an expiration date.After this era , the quote or quote will become invalid.
Create a quote
- When drawing up an estimate, it's recommended to supply the customer with a written copy, including an entire breakdown of the value .
- The estimate should include:
Overall price
List breakdown, price components
- Schedule, details of when work are going to be done and when products are going to be delivered
- Terms and conditions
- How long the estimate is valid
- Payment terms or schedule
- You should include your full business contact details in your quote.If you've got a letterhead, we recommend that you simply put a quote during thisGST / QST components for the worth should even be provided if applicable.
- It is an honest idea to sign and approve the quote and confirm the customer is obvious about the agreement.
- Please include a disclaimer that clearly indicates that the worth of the quote is subject to vary .You agree beforehand about the value of the variation.These can occur if the client changes the wants or if the work seems to be more complex than expected.
- If you think that that price complications are likely to occur, we recommend that you simply provide some estimates supported different scenarios.This will help to avoid disputes with the client because the work progresses.
- When starting work or supply, it's necessary to properly record the surplus of costs, alongside how and why they occur.
- The software package helps to spot the prices related to the work of providing an estimate.Many accounting and spreadsheet packages are often used for this purpose.
How to Calculate Tender Price or Quotations?
Very often, manufacturers or producers are asked to submit bids or cost estimates for the supply of future products. The estimated price for future production is called the estimated price or bid price. This price is confirmed on the basis of the previous cost sheet or production account. When you know future expected costs, consider the fields of past cost elements, taking into account future expected changes. Increase the estimated cost by the desired profit to check the bid price or estimate.
Bidding for similar types of goods:
When calculating the cost of goods of the same type and quality, the cost per unit of each element of the cost is usually used. If there are expected changes to these elements, the changes are adjusted accordingly. The following example illustrates the technique
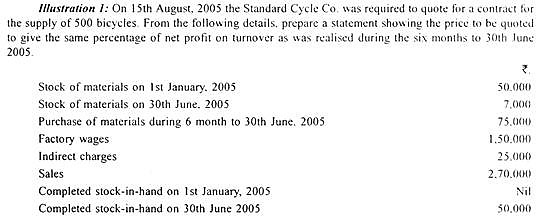
The number of bikes manufactured in 6 months was 2.000, including those sold and stock at the end of the year. The estimated bicycle should be uniform in size and quality, similar to the one manufactured in 2005-6.30 to 6 months. Since 8/1, the labor cost of the factory has increased by 10%, and the cost of materials has increased by 15%.
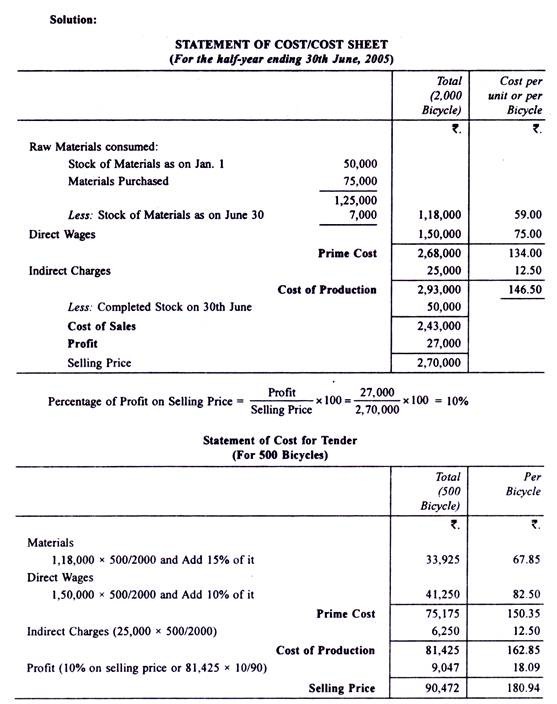
Bidding for different products:
If you want to check the bid or quote price for another product, estimate the direct material costs, direct labor costs, and other direct costs. These sums will be Prime costs. Work overhead, office overhead, and sales overhead are added Based on the absorption rate. Expenses are usually charged or absorbed based on the percentage of expenses relative to wages. Therefore, the percentage is calculated based on historical records.

Alternatively, you may be charged based on machine time rate or working hour’s rate. Office overhead may be absorbed based on the work cost or the percentage of office overhead relative to the work overhead

The sum of the prime cost and the absorbed work overhead and office overhead will be the production cost. Based on the absorption rate, sales overhead may be added. This can be the cost of production or sales, or a percentage of sales overhead per unit by adding the desired profit. You can see the bid or quote price.
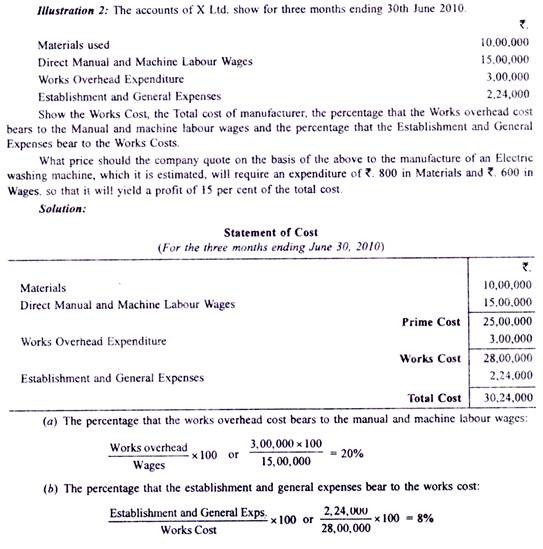
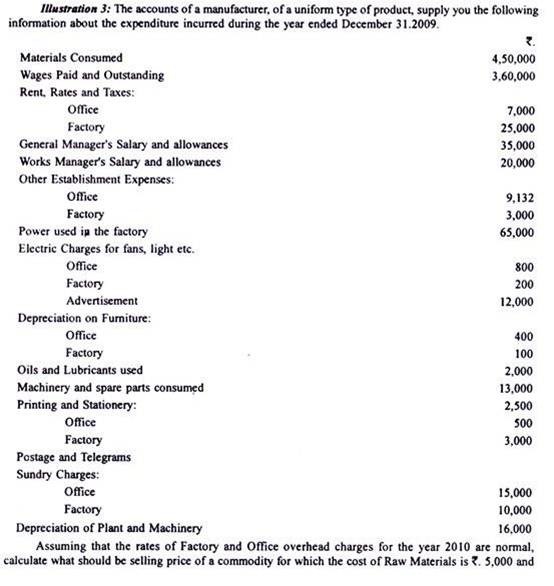
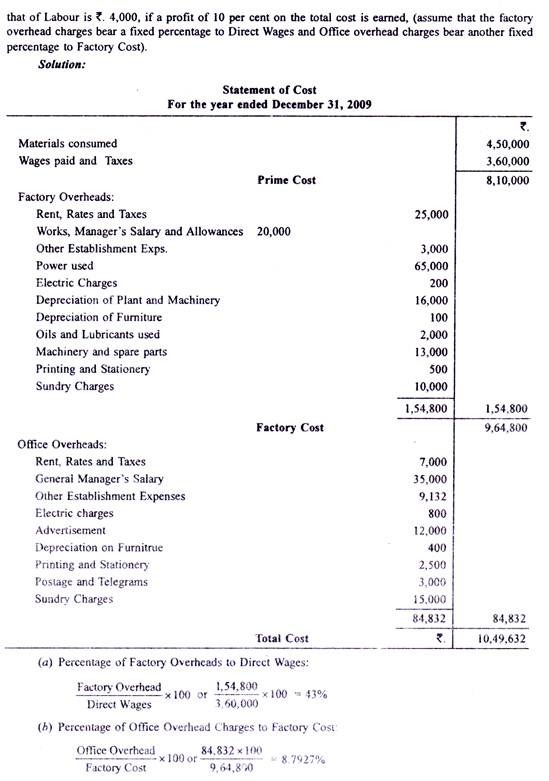
Key takeaways:
- All companies are required to present the price of their products and services to their customers
- Preparation of Price list.
- Calculation of Tender Price or Quotations.
- Illustrations