UNIT IV
Process Costing
Costing is an accounting method that records and analyses all costs associated with the execution of a process, project, or product. Such analysis helps management make strategic decisions.
Costing uses a variety of techniques to make your organization cost-effective. Everything you need to know about the different costing methods. The term "costing method" can be used to refer to the various processes or procedures used to determine and display costs.
There are different costing methods in different industries, depending on the nature of the job. Costing methods can be studied under the head below. -1. Method based on the principle of job costing 2. Method based on the principle of process costing.
Costing methods can be studied under the head below. -1. Method based on the principle of job costing 2. Method based on the principle of process costing.
Some of the methods based on the principles of process costing are: -
1. Process costing
2. Operating costing
3. Department costing
4. Single or unit or output costing
5. Operation or operation or work or service costing
6. Multiple or combined costing.
In addition, some other costing methods are: -
1. Uniform costing
2. Multiple or combined costing
3. Department costing
4. Cost plus method
5. Target costing method 6. Farm costing
7. Activity-based costing.
Different types of costing methods: job costing, contract costing, batch costing, process costing, and operating costing
Different methods of costing – individual costing, contract costing, batch costing, process costing, unit costing, operating costing, operating costing, and multiple costing
The costing method refers to the cost confirmation and costing system. Industries differ in their nature, the products they produce, and the services they provide. Therefore, different costing methods are used in different industries. For example, the costing method used by building contractors is different from that of shipping companies.
Job costing and process costing are two basic methods of costing. Job costing is suitable for industries that manufacture or perform work according to customer specifications. Process costing is suitable for industries where production is continuous and the units of production are the same. All other methods are a combination, extension, or improvement of these basic methods.
Let's take a closer look at how to calculate costs.
Method # 1 Job costing:
This is also known as specific order costing. There is no standard product and each job or work order is adopted in a different industry. The work is done strictly according to the customer's specifications, and the work is usually completed in a short time. The purpose of job costing is to see the cost of each job individually. Job costing is used in printing presses, motor repair shops, car garages, movie studios, the engineering industry, and more.
Method # 2 Contract Costing:
This is also known as terminal costing. Basically, this method is similar to job costing. However, it is used when the work is large and it takes a long time. The work will be done according to the customer's specifications.
The purpose of contract costing is to see the costs incurred in each contract individually. Therefore, a separate account is provided for each contract. This method is used by companies engaged in the construction of ships, buildings, bridges, dams and roads.
Method # 3 Batch Costing:
This is an extension of job costing. A batch is a group of identical products. All units in a particular batch are uniform in nature and size. Therefore, each batch is treated as a cost unit and is costed separately. The total cost of the batch is checked and divided by the number of units in the batch to determine the cost per unit. Batch costing is adopted by manufacturers of biscuits, ready-made garments, spare parts medicines and more.
Method # 4 Process Costing:
This is called continuous costing. In certain industries, raw materials go through various processes before they take the form of final products. In other words, the finished product of one process becomes the raw material for the next process. Process costing is used in these industries.
A separate account is opened for each process to see the total cost and cost per unit at the end of each process. Process costing applies to continuous process industries such as chemicals, textiles, paper, soaps and foam.
Method # 5 unit costing:
This method is also known as single costing or output costing. It is suitable for industries with continuous production and the same unit. The purpose of this method is to see the total cost and the cost per unit. Create a cost sheet considering material costs, labor costs, and overhead costs. Unit costing applies to mines, oil rig units, cement factories, brick factories and unit manufacturing cycles, radios, washing machines, etc.
Method # 6 Operating cost:
This method is followed by the industry that provides the service. To determine the cost of such services, use composite units such as passenger kilometres and tone kilometres to determine the cost. For example, for a bus company, operating costs represent the cost of carrying passengers per kilometre. Operating costs are used in air railways, road transport companies (commodities and passengers) hotels, movie theatres, power plants, etc.
Method # 7 Operating cost:
This is a more detailed application of process costing. It includes costing by all operations. This method is used when there is a repetitive mass production with many operations. The main purpose of this method is to see the cost of each
Operation.
For example, manufacturing a bicycle handlebar involves many operations such as cutting a steel plate into appropriate strips, forming, machining, and finally polishing. The cost of these operations can be viewed individually. Operating costs provide a detailed analysis of costs to achieve accuracy and apply to industries such as spare parts, toy manufacturing, and engineering.
Method # 8 Multiple Costing:
Also known as compound costing. This refers to a combination of two or more of the above costing methods. It is used in the industry where multiple parts are manufactured separately and assembled into a single product.
Different methods of costing – single costing, job costing, contract costing, batch costing, process costing, operating costing, operating costing, and a few others
The term "costing method" can be used to refer to the various processes or procedures used to determine and display costs. There are different costing methods in different industries, depending on the nature of the job. For example, the chemical industry follows a continuous production process in which raw materials are processed at various stages. There are other industries that undertake different types of work. For example, motor workshops accept a variety of jobs.
In industries such as transportation, banking and insurance, the entire activity is centred on a particular service operation. Similarly, many other industries may produce only one product. The nature of the manufacturing process and the way it works varies from industry to industry, making it essential to use different costing method
Preparation of cost sheet & production account
Cost sheet and production account
Cost statements may be displayed in the form of ledger accounts called "production accounts." Production accounts analytically present production cost information according to double-entry bookkeeping. Production costs and profits can be calculated in this ledger. The cost sheet and production account are as follows:
Cost sheet
PARTICULARS | AMOUNT |
Direct material Direct wages Direct Expenses |
|
Prime Cost |
|
Add: Factory Overheads |
|
Factory Cost |
|
Add: Administration Overheads |
|
Cost of Production |
|
Add: Selling and Distribution Overheads |
|
Total Cost /Cost of sales |
|
A cost sheet is a device used to determine and display costs in unit costing. This is a statement of costs incurred at each level of manufacturing a product or service. The cost sheet takes into account all the factors of cost. This includes prime costs, factory / manufacturing costs, manufacturing costs, selling costs, profits / losses, and more.
According to C.I.M.A, London
Cost schedule or document that provides a detailed cost assembly estimated for a cost center or cost unit."
Items excluded from the cost sheet:
1. Pure financial costs such as capital interest, interest on loans, discounts on corporate bonds, loss on sale of allowance for doubtful accounts, amortization of bad debts, copyrights and reserves.
2. Pure financial income such as interest received, gain on sale of investment, dividend received, rent received, commission received, discount received.
In addition to the above, the budget limit does not include the budget limit.
Form of a Cost Sheet: Cost sheet for the period ending
Production account
Meaning:
A production account is a statement in a ledger account format cost or cost sheet that shows the output for a particular period, the total and unit costs incurred during that period, and its components, and the profits or losses for that period.
According to Glover and Williams, "The term manufacturing account is used to describe a particular type of manufacturing account created in combination with a financial account to indicate the actual manufacturing cost of goods manufactured during the review period. Used. These accounts may be created at short intervals. Monthly.
The production account is created in the format in which the transaction account is created. There are usually two parts. The first part shows the total cost and the cost per unit. The second part shows the cost of goods sold and the cost of goods sold.
When the details of a cost table or production statement are displayed in the form of a ledger account, it is called a production account. In addition to manufacturing costs, selling and distribution costs are also included. It is created in three parts. The first part shows the manufacturing cost, the second part shows the cost of goods sold, and the third part shows the cost of goods sold or total cost for that period. Here is a sample production account:
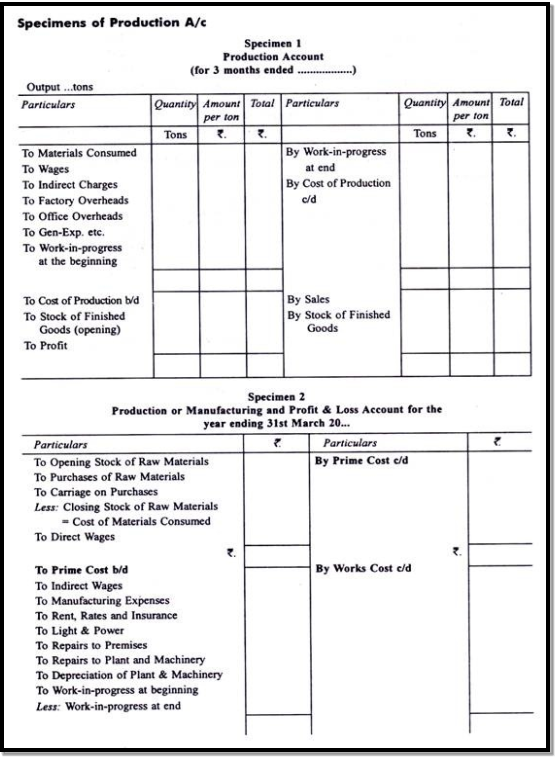
Key takeaways:
- Costing is an accounting method that records and analyses all costs associated.
- Cost statements may be displayed in the form of ledger accounts called "production accounts.
- A production account is a statement in a ledger account format cost.
Process costing is a method of costing under which all costs are accumulated for each stage of production or process, and the cost per unit of product is ascertained at each stage of production by dividing the cost of each process by the normal output of that process.
Definition:
CIMA London defines process costing as “that form of operation costing which applies where standardize goods are produced”
Features of Process Costing:
(a) The production is continuous
(b) The product is homogeneous
(c) The process is standardized
(d) Output of one process become raw material of another process
(e) The output of the last process is transferred to finished stock
(f) Costs are collected process-wise
(g) Both direct and indirect costs are accumulated in each process
(h) If the revise stock of semi-finished goods, it is expressed in terms of equal units
(i) The total cost of each process is divided by the normal output of that process to find out cost per unit of that process.
Advantages of process costing:
- Costs are be computed periodically at the end of a particular period
- It is simple and involves less clerical work that job costing
- It is easy to allocate the expenses to processes in order to have accurate costs.
- Use of standard costing systems in very effective in process costing situations.
- Process costing helps in preparation of tender, quotations
- Since cost data is available for each process, operation and department, good managerial control impossible.
Limitations:
- Cost obtained at each process is only historical cost and are not very useful for effective control.
- Process costing is based on average cost method, which is not that suitable for performance analysis, evaluation and managerial control.
- Work-in-progress is generally done on estimated basis which leads to inaccuracy in total cost calculations.
- The computation of average cost is more difficult in those cases where more than one type of products is manufactured and a division of the cost element is necessary.
- Where different products arise in the same process and common costs are prorated to various costs units. Such individual products costs may be taken as only approximation and hence not reliable.
For each process an individual process account is prepared. Each process of production is treated as a distinct cost center.
Items on the Debit side of Process A/c.
Each process account is debited with
a) Cost of materials used in that process.
b) Cost of labor incurred in that process.
c) Direct expenses incurred in that process.
d) Overheads charged to that process on some pre-determined.
e) Cost of ratification of normal defectives.
f) Cost of abnormal gain (if any arises in that process)
Items on the Credit side:
Each process account is credited with
a) Scrap value of Normal Loss (if any) occurs in that process.
b) Cost of Abnormal Loss (if any occurs in that process)
Cost of Process:
The cost of the output of the process (Total Cost less Sales value of scrap) is transferred to the next process. The cost of each process is thus made up to cost brought forward from the previous process and net cost of material, labor and overhead added in that process after reducing the sales value of scrap. The net cost of the finished process is transferred to the finished goods account. The net cost is divided by the number of units produced to determine the average cost per unit in that process. Specimen of Process Account when there are normal loss and abnormal losses
Dr. Process A/c. Cr.
Particulars | Units | Rs. | Particulars | Units | Rs. |
To Basic Material | Xxx | Xx | By Normal Loss | Xx | Xx |
To Direct Material |
| Xx | By Abnormal Loss | Xx | Xx |
To Direct Wages |
| Xx | By Process II A/c. | Xx | Xx |
To Direct Expenses |
| Xx | (output transferred to |
|
|
To Production Overheads |
| Xx | Next process) |
|
|
To Cost of Rectification of Normal Defects |
| Xx | By Process I Stock A/c. | Xx | Xx |
|
|
|
|
|
|
To Abnormal Gains |
| Xx |
|
|
|
| Xx | Xxx |
| Xx | Xx |
Wastage
Waste is the portion of basic raw material that is lost in processing, with no recoverable value. Residues can be produced due to evaporation, bulk breakage, loading and unloading, leaks, inefficient handling, fire, etc. It can be visible or invisible, for example gases, dust and smoke and non-salable waste. The effect of waste is to increase the unit cost of production, since the total cost is spread over a smaller number of good units. Accounting treatment: The accounting treatment of waste depends on whether the waste is normal or abnormal.
For normal waste arising from breakage, evaporation, deterioration, contraction in production, the total cost incurred is distributed over the good output. The treatment is based on the principle that normal losses must be borne by good performance. Abnormal material waste arising due to abnormal reasons i.e. theft, fire, careless handling, etc., is not added to the cost. Of production, but is transferred to the cost profit and loss account. This is necessary to avoid any fluctuation in the cost of production. Waste Control: To control waste in manufacturing industries, a waste report is prepared at regular intervals. The actual percentage of waste is compared to the standard percentage and corrective action is taken to eliminate any abnormal waste.
Key takeaways:
- Process costing is a method of costing under which all costs are accumulated for each stage of production or process.
- The cost of the output of the process (Total Cost less Sales value of scrap) is transferred to the next process.
- Waste is the portion of basic raw material that is lost in processing, with no recoverable value.
Co-costs are costs that benefit multiple products, and by-products are minor consequences of the manufacturing process and are low-selling products. Joint costing or by-product costing is used when there is a production process in which the final product is split at a later stage in production. The point at which a company can determine the final product is called the split point. There may be some dividing points. Each can clearly identify another product, is physically separated from the manufacturing process, and in some cases is further refined into a finished product. If manufacturing costs are incurred before the split point, you need to specify how these costs are distributed to the final product. If an entity bears any costs after the split point, those costs are likely to be related to a particular product and can be more easily allocated to them.
In addition to the dividing points, there may be one or more by-products. Given the importance of by-product revenue and cost, by-product accounting tends to be a minor issue.
If a company bears costs before the split point, it must be assigned to the product under the direction of both generally accepted accounting principles and International Financial Reporting Standards. If you do not assign these costs to a product, you will have to treat them as period costs and will charge them as costs for the current period. This can be a mishandling of costs, as if the related product is not sold until some point in the future, it will charge a portion of the product cost as an expense before the offset sale transaction is realized.
Co-cost allocations are not administratively useful, as the resulting information is essentially based on arbitrary allocations. Therefore, the best allocation method does not have to be particularly accurate, but it should be easy to calculate and easy to defend if reviewed by the auditor.
How to allocate joint costs
There are two common ways to allocate joint costs. The calculation method is as follows.
Allocate based on sales. Sum all manufacturing costs up to the split point, determine the sales value of all joint products at the same split point, and assign costs based on the sales price. If there are by-products, do not allocate costs to them. Instead, you charge the cost of goods sold as revenue from the sale. This is the simpler of the two methods.
Allocate based on gross profit. Sum the costs of all processing costs incurred by each joint product after the split point and deduct this amount from the total revenue each product ultimately earns. This approach requires additional cost accumulation work, but may be the only viable alternative if the selling price of each product at the point of split cannot be determined (of the calculation method described above).
Pricing for joint products and by-products
The costs allocated to joint products and by-products should not be related to the pricing of these products, as they are not related to the value of the items sold. Prior to the split point, all costs incurred are sunk costs and do not affect future decisions such as product prices.
The situation is quite different when it comes to costs incurred after the split point. Do not set the product price below the total cost incurred after the split point, as these costs can be attributed to a particular product.
If the lower limit of the price of a product is only the total cost incurred after the split point, this may result in a lower price than the total cost incurred (including the cost incurred before the split point). A strange scenario occurs. .. Obviously, charging such a low price is not a viable alternative in the long run, as companies will continue to suffer losses. This offers two alternative prices.
Short-term price. If market prices cannot be raised to sustainable levels in the long run, it may be necessary to allow very low product prices in the short run, even if they are close to the sum of costs incurred after the split point.
Long-term price. In the long run, companies need to set prices to achieve revenue levels that exceed total production costs. Otherwise, there is a risk of bankruptcy.
That is, if the individual product price can not be set high enough than to offset the production cost, and the customer does not want to accept the higher price, then the different co-products can be set.
An important point to remember about cost allocation related to joint products and by-products is that the allocation is simply an expression, not related to the value of the product to which the cost is allocated. The only reason to use these allocations is to achieve valid sales costs and inventory valuations under the requirements of various accounting standards.
Key takeaways:
- The point at which a company can determine the final product is called the split point.
- How to allocate joint costs.
- Pricing for joint products and by-products.