UNIT II
Elements of Cost
Composition of elements of cost:
The manufacturing organization converts raw materials into finished products. To that end, it employs labour and provides other facilities. It is necessary to check the amount spent on all this, while aggregating the cost of production. For this purpose, the cost is mainly classified into various factors. This classification is necessary for accounting and management.
The cost elements are
(i) Direct material
(II) Direct labour
(iii) Direct expenses and
(iv) Overhead.
The following chart shows the wide heading of the cost and these acts as the basis for preparing the cost sheet.
Elements of cost
Materials Labour Other Expenses
Direct Indirect Direct Indirect Direct Indirect
Overheads

Factory Administrative Selling & Distribution
Break up of cost sheet
Classification of Cost
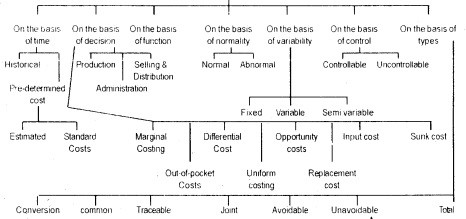
Prime cost:
The sum of direct material costs, direct labor and direct costs is called Prime costs. The direct cost is traceable to the product or job.
Direct material
This includes the costs of materials consumed in the production process that can be assigned directly to the cost centre. Direct materials can be identified and filled into
For example、:
- Materials purchased specifically for a particular job or process.
- Materials passing from one process to another.
- Consumption of materials or parts manufactured in the same factory.
- Primary packing material.
- Freight, insurance and other transportation costs, import duties, ochry duties, inward transportation, storage and handling costs are treated as the direct cost of the material consumed.
In some cases, direct materials are used in small quantities, and it is impossible to check and directly allocate their costs. For example, nails used in the manufacture of chairs and tables, glue used in the manufacture of toys. In such cases, the cost of the total quantity consumed during the period is treated as an indirect cost.
Direct labour
This includes the amount of wages that can be easily identified and billed directly to the product. These are the costs for converting raw materials into finished products. Wages paid to workers to operate lathe machines, drilling machines etc. In the tool room is a direct pay.
Direct expenses
This includes costs other than materials and labour that can be easily identified in a particular product or process. For example: the cost of excise duty. Overhead costs cannot be easily identified in a particular product or process.
Indirect materials
Materials that cannot be traced as part of a finished product are known as indirect materials.
For example、:
- Consumable stores such as lubricants, cotton waste, tools etc.
- For direct charging, such as nails (for making chairs) glue (for making toys), non-important materials that are not worth checking the cost separately. Allocate with these materials. Or absorb any in cost centres or cost units.
Indirect labor:
Indirect labor is a cost that cannot be invoiced or identified directly on the finished product. Indirect labor is assigned to or appropriately absorbed by the cost centre or cost unit.
For example、:
- Salary to store-keeper
- Wages to timekeepers
Overhead:
These are general costs that are not incurred for a particular product or service and cannot be billed directly to the product.
For example、:
- Factory rent, rates and insurance
- Power, lighting, heating, repair, telephone costs, printing and stationery.
Overhead can be subdivided into the following main groups.
Factory or work overhead: Also known as manufacturing or production overhead it consists of all the costs of indirect materials, indirect labor and other overhead incurred in the factory.
Example: Factory rent and insurance. Depreciation of factory buildings and machinery.
Office or management overhead: All indirect costs incurred by the office for the management and management of the enterprise.
Examples: Rent, fees, taxes and insurance for office buildings, audit fees, director fees.
Sales and distribution overhead: These are overhead related to marketing and sales.
Examples: Advertising of distributors, salaries and fees, travel expenses of salesmen.

A material is a substance (physical term) that is part of a finished product or is composed of a finished product. In other words, a material is a product that is supplied to a business for the purpose of consuming it in the process of manufacturing or providing services, or for the purpose of converting it into a product. The term "store" is often used as a synonym for material, but store has a broader meaning, not only the raw materials consumed or used in production, but also miscellaneous goods, maintenance stores, processed parts, components. Also includes items such as tools. Jigs, other items, consumables, lubricants, etc. Finished and partially finished products are also often included in the term "store". Materials are also called inventory. The term material / inventory include not only raw materials, but also components; work in process, finished products, and scrap.
Material costs are an important component of the total cost of a product. It accounts for 40% to 80% of the total cost. Percentages may vary from industry to industry. But for the manufacturing sector, material costs are paramount. Inventory is also an important component of working capital. Therefore, it is treated the same as cash. Therefore, analysis and control of material costs is very important.
Purpose of material management system
Material management: The ability to ensure sufficient inventory of goods to meet all requirements without carrying unnecessarily large amounts of inventory.
The purpose of the material management system is to:
2. Make the material available continuously so that the flow of material for production is uninterrupted. Production cannot be postponed due to lack of materials.
2. Purchase the required amount of materials to avoid working capital locks and minimize the risk of surplus or obsolete stores.
3. Make competitive and wise purchases at the most economical prices so that you can reduce material costs.
4. Purchase the right quality material to minimize the waste of material.
5. Acts as an information centre for material knowledge about prices, suppliers, lead times, quality and specifications.
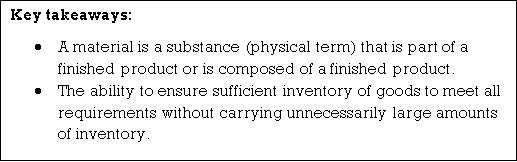
Introduction to purchasing materials:
For manufacturing concerns, there is another purchasing department under the control of the purchasing person. The main function of the purchasing department is to purchase the required amount of materials in time so that the store can provide the production department with a continuous supply of materials and purchase higher quality materials at a reasonable price.
Buyers need to play an important role as they can save or lose a lot of money. He requires good technical knowledge of the industry and some management skills. He also needs to be aware of management policies and sources of concern.
He also needs to be aware of market conditions and have knowledge of suppliers, trusted suppliers, prices and purchasing procedures.
He must keep up with government policies on import and export restrictions and various tariffs and taxes on goods. He must have practical knowledge of the law relating to contracts and the sale of goods so that he can negotiate and enter into contracts on behalf of his employer.
Centralized and Decentralized purchases:
Centralized purchase:
Centralized purchase means the purchase of materials by one specialized department. The purchasing department has personnel with expertise in all aspects of the material. The purchasing department has the authority to make purchases for the entire organization.
In this system, the requirements of the entire organization are confirmed through the creation of purchasing budget, the purchasing department makes purchases according to the accepted principle, and the materials are distributed to each production department according to the requirements.
In most cases, the purchasing department purchases materials based on the requisition form issued by the store. The supplier delivers the material to the Material Receipt section. Individual departments are not allowed to purchase their own materials when centralized purchases are made.
Decentralized purchase:
Decentralized purchases mean that each department can purchase materials according to their needs. Therefore, the authority to make purchases rests with the individual departments.
(A) Advantages of local purchase: If the production unit is far from the body, it is beneficial to have the unit available for purchase locally. You can enjoy the benefits of basic low price and seasonal price, and reduce the cost.
(B) Reduction of transportation costs: By supplying materials locally, transportation costs will be significantly reduced.
(C) Quick resolution of the problem: Disputes caused by refusals, shortages and returns can be resolved easily and quickly.
Advantages of centralized purchase:
From a centralized purchase, you can derive the following benefits:
a) Benefits of bulk purchase: Because materials are purchased in bulk, trade discount rates are high, credit lines are improved, bargaining power, quantity, and discounts are increased, so materials can be purchased at much lower prices.
(B) Maintaining quality: All purchases are made by the purchasing department, which has expertise in product quality, which helps maintain the quality of the materials and ultimately leads to the production of better quality finished products. Improving product quality ensures that your business is more credible, resulting in higher sales and higher profits.
(C) Reduction of transportation costs: This system purchases materials in bulk, significantly reducing shipping costs. This has a positive impact on the total cost or unit cost of the material. This makes your organization more competitive.
(D) Advantages of specialization: The Purchasing Department has dedicated purchasing personnel to ensure the right purchases from the right type of supplier. This, guarantees both quality and price.
(E) You can avoid duplication: All purchases are made by one person, avoiding duplicate purchases.
(F) Planned purchases: You can systematically eliminate the purchase and holding of surplus stores, which enables better space management and easily avoids unnecessary blocks of working capital.
Restriction:
The restrictions on centralized purchases are as follows:
(A) Expensive
The management costs of the purchasing department can be very high, resulting in a solid increase in total costs and defeating the very purpose of costs to reduce costs.
(B) It functions as an obstacle to smooth functioning.
If a production department does not have the materials it needs, it must wait for the purchasing department to purchase it. This delay leads to production outages, which in turn leads to increased costs.
Purchasing routine:
In general, the following routine is used to purchase materials.
(I) Request for purchase. The request is made by the store officer.
(Ii) Offering bids and quotations for the supply of the required amount of material.
(Iii) Place an order with a supplier after considering bids and quotations submitted by different suppliers.
(Iv) Receipt of material after proper inspection.
(V) Confirm and pass the supplier's payment invoice.
Purchase requisition:
The decision to purchase the material is made by the purchasing department after receiving the purchase request from the authorized department. A Purchase request is made from an approved department to the purchasing department in a prescribed form called a purchase request.
Requisitions provide three basic pieces of information that help buyers perform their purchasing functions efficiently.
The information is as follows:
- What materials to buy (purchasing the right quality).
- When to buy (appropriate time).
- Amount to purchase (appropriate quantity).
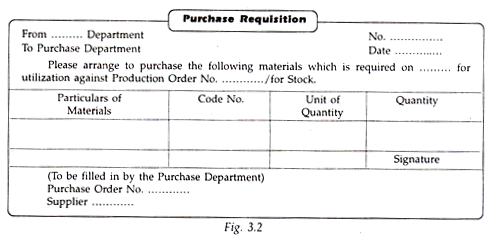
Purchase requisitions are received by the purchaser from:
(I) Shopkeepers of all standard materials.
(II) Production control department of non-standard materials required for production.
(III) Plant and maintenance engineers for special maintenance and capital investment.
(IV) Head of special items such as office supplies.
The requisition is created three times. Two copies will be sent to the purchasing department, one copy will be retained as proof of approval and the other copy will be returned to the inventor after quoting the order details. Purchasing department. A third copy is kept by the store for office records and future references.
Material specifications or bill of materials:
The requisition contains details and specifications of the materials to purchase. Material specifications are known as bills of material. This starts in the production control department or the plant and maintenance engineer department. The BUI of Material is a complete schedule of materials or parts required for a particular job or work order created by a drafting office.
A bill of materials is created for every job and a copy is sent to the storekeeper.
BOM Benefits:
The following benefits can be obtained in different departments of the BOM.
(I) upon receiving the bill of materials, the purchasing department can place an order with the supplier of choice. Therefore, the bill of materials serves the purpose of the purchase requisition.
(Ii) The bill of materials allows the store to publish materials.
(Iii) The bill of materials contains details of the materials used in the job or work order, so the supervisor does not need to prepare detailed material requirements. This saves time and makes it easier to pull out the material.
Purchase time:
Requisitions indicate the date on which the use of the material is required. The storekeeper makes a request to the purchaser as soon as the material reaches the reorder level. Upon receiving the purchase requisition, the purchaser places an order with the supplier with a delivery date.
Delivery times are fixed taking into account the material consumption rate and the minimum level fixed to it.
Purchases are also made when market conditions are good, despite the fact that there is no immediate need for materials for production. In an inflationary economy, we buy materials in bulk in the hope that prices will rise further.
For raw materials such as jute, cotton and sugar cane, quantity, quality and price are used to make bulk purchases during the season. To prevent future price increases, long-term contracts may be entered into with suppliers to purchase materials for a specified period of time and at a specified rate.
However, in doing so, the purchaser must take into account the following factors:
(I) A storage facility for storing quantities.
(Ii) Financial resources of concern. And
(Iii) Transportation costs, capital costs, storage costs, etc.
Purchase quantity:
Before placing an order with a supplier, the purchaser must ensure that only the right quantity of stores is purchased. The following factors should be taken into account when determining the purchase quantity:
(I) Material inventory levels must be maintained to meet the requirements of the production sector.
(Ii) Production is not hindered by a shortage of raw materials.
(Iii) There should be no excess inventory or material shortage inventory to unnecessarily block working capital. And
(IV) Availability of funds
Purchase order:
Definition:
A purchase order is an agreement between a material buyer and a supplier. It is a requirement from the purchaser to the supplier to supply goods of a specific quantity and quality in accordance with the terms set forth in the contract. It also means the buyer's commitment to deliver and pay for the goods according to the terms and conditions stated on the purchase order.
After carefully determining the purchase quantity, the purchasing department should place an order with the supplier of choice. You need to choose a supplier that can deliver the products you need at a competitive price and at the right time. We are looking for a quote from our supplier.
Quotations received from different suppliers are compared and an acceptable supplier is selected. After completing the above procedure, a purchase order will be issued to the supplier to supply the required quantity of goods at the specified time.
Purchase order i is issued in the prescribed format, produced in quadruples (4 copies), and sent to the next department for reference and coordination.
(I) the first copy will be sent to the supplier.
(Ii) One copy will be sent to the department that sent the purchase requisition.
(Iii) One copy will be sent to the store or the internal department of the product.
(Iv) One copy will be kept in the purchasing department as a permanent record.
(V) A copy will be sent to your account department.
Purchase procedure:
Purchasing departments need to follow specific steps for efficient purchasing. The purchasing procedure includes the following steps:
(2) Purchase request:
Receive purchase requisitions that you might receive from your store, production control department, or department manager. The amount of material you purchase should be carefully determined.
(2) Supplier search:
Purchasing departments need to find potential suppliers. Care must be taken when choosing the right supplier. Once the supplier has been identified, you will be asked to submit a quote or bid. You need to start bidding and select a supplier considering the conditions stated in the bid.
(3) Purchase order:
Once a supplier is selected, you need to pass the purchase order to the selected supplier. A copy of the purchase order should be sent to the original department, the accounting department, and one copy to the costing department.
(4) Receipt of materials:
The materials you receive must be entered in the receipt note and sent to the inspection department for inspection. After receiving the inspection report, the material is sent to the store and shipped to the manufacturing department.
To better understand the chart in this regard, it is shown below.
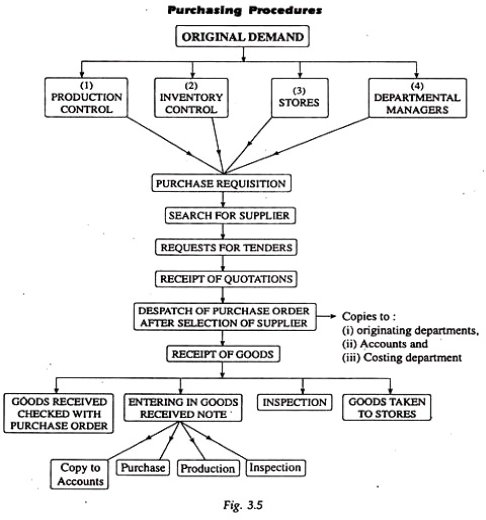
Receipt of goods:
The following chart shows the procedure for receiving and inspecting materials.
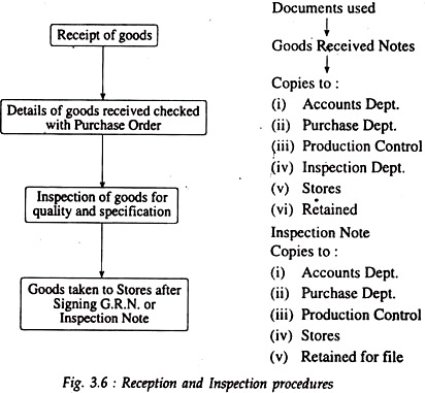
The warehousing department is usually located at the entrance of the factory. All carriers of goods are to report to this department. After receiving the delivery note or shipping advice from the supplier, the receiving department must arrange the unloading of the goods.
The receiving office must receive the goods after comparing the quantity, quality, and other details that should have been included in the purchase order. When you receive the item, you should check it by weighing, counting, or inspection.
If there is any damage or missing, you should state that fact on the carrier's copy or Challan. After being satisfied in all respects, the recipient of the goods must sign a copy of the carrier Challan. Next, you need to enter the item details on the receipt (below). The receipt memo is an important document and is required to confirm the supplier's invoice and pass it to payment.
The goods receipt note is prepared with an additional copy distributed as follows:
(I) to the purchasing department to update the purchase record.
(Ii) To the department that sent the purchase request.
(Iii) To the accounting and inventory management department.
(Iv) To the shop owner. And
(V) Stored in the receiving department for records and future reference.
Goods receipt note (GRN):
This is a testimony of the goods received according to the purchase order. Otherwise, the supplier will be notified by formal contact. When making adjustments for damaged or defective items, it is customary to send a debit note to the supplier with the value of the damaged or rejected item and the shipping costs for the return.
Confirmation of purchase invoice:
Along with the goods, the supplier sends an invoice containing details of the materials supplied and their price.
The purchaser who receives the material should refer to the following document to verify the accuracy of the details.
(I) Order form.
(Ii) Receipt notes.
(Iii) Inspection report.
(IV) Debit notes (if any).
If the invoice is determined to be correct, it will be stamped with a rubber stamp by the responsible authority of the purchasing department and passed to the accounting department for payment. Invoices are now checked by an authorized person in the accounting department to ensure that the calculations are correct.
The invoice will be entered in the purchase diary that will be credited to the supplier's account. Periodically, the purchase journal totals are debited to the general ledger purchase account.
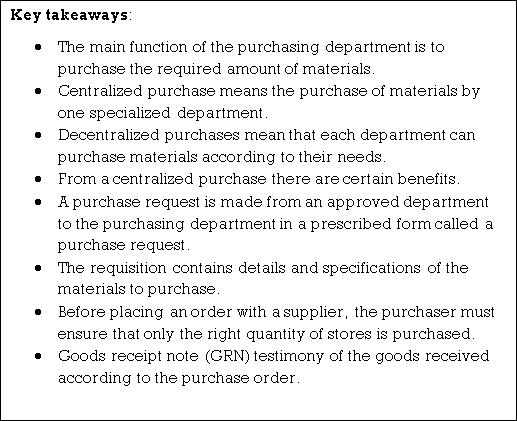
Storage of materials should not pose a danger. Make sure that the material stored in the tier is blocked. Interlocked and height limited, so drop, slide, or Collapse. Store all ingredients on pallets immediately to prevent rodent invasion. Clean up spills and leaks that create a rodent habitat. When lifting the bag using a sling Materials, wood, brick, masonry blocks, and similar loosely stacked materials. The sling is inspected before use and the material and load are completely fixed against drops by straps, sideboards, nets, or other suitable devices. See reclamation Health and Safety Standards (RSHS) Section 28, sling and rigging hardware, and for additional information on rigging and rigging, see Section 29, Hoists and Pile Driving Equipment Winding operation.
Once you receive the material, it is the responsibility of the store in charge to ensure that it is only done for documents that allow the material to enter or leave the store. The store in charge is responsible for making good use of storage space, better managing the materials in the store, and properly protecting the materials from all losses such as theft, theft, fire and misappropriation.
Shopkeeper duty:
The duties of the shopkeeper are as follows.
a. Overall control of all activities in the store department.
b. To ensure the safe storage of materials.
c. To maintain a proper record.
d. Whenever the inventory level of an item in the store reaches the minimum level, we initiate a requisition to replace the inventory of all regular materials.
e. When the inventory level approaches the maximum level, it will take action to stop further purchases.
f. Issue only the required amount of material for the approved request document.
g. We will review and receive the purchased materials transferred from the receiving department and arrange to store them in the appropriate place.
Stores of various classes-
Roughly speaking, there are three classes of stores
a. Central store
b. Decentralized store
c. Sub store (impressed store)
Centralized store:
The usual practice of most concerns is to have a central store. Individual stores to meet the requirements of each production department are not popular due to the high cost. For centralized stores, materials are received and published by a single store department. All materials are stored in one central store. The advantages and disadvantages of this type of store are:
Advantages of a centralized store:
a. All stores are housed in one department, so you can manage your stores better. You can minimize the risk of store obsolescence.
b. Staff Economy-Experts, or office work, floor space, records and stationery are available.
c. Better supervision is certainly possible.
d. Obsolescence of store items can be placed under close scrutiny and control.
e. You can operate a centralized material handling system, further saving space, personnel and equipment.
f. You can minimize your investment in stocks.
Disadvantages of a centralized store:
a. Due to the centralized storage, the distance travelled by the store can be long, which can increase the cost of transporting materials.
b. If the user departments are far from the store, they may delay the receipt of the store.
c. The collapse of the inter-departmental transportation system can hinder the entire process, as well as labor issues in centralized stores can stop overall concern.
d. There is an increased risk of loss due to fire, robbery, or other unfortunate incident.
e. It may not be safe to put some dangerous elements together in a central store.
Decentralized store:
This type of store has independent stores in different departments. Stores are handled by the owners of each department. Departments that need stores can withdraw stores from their respective stores in their respective departments. If you have a decentralized store, you can eliminate the disadvantages of a centralized store. However, these types of stores are unusual due to their high cost.
Central store with sub stores:
In large organizations, factories / workshops may be located in different locations far from the central store. Therefore, sub stores should be located near the factory to minimize shipping and handling costs. The quantity is determined for each item and must be kept in stock at the beginning of the period. At the end of the period, the storekeeper of each sub store requests the quantity of material consumed to bring the inventory to a given quantity from the central store. In short, this type of store operates in the same way as a retail cash system, so this store system is also known as a store management impressed system.
Advantage:
a. It ensures the prompt issuance of the store.
b. While limiting the benefits of a centralized store to sub stores, it does not sacrifice centralized control.
c. Reduce material handling costs.
d. It avoids maintaining elaborate inventory records.
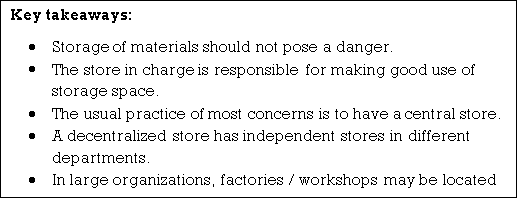
Store organisation
Importance of storage:
Material costs are one of the biggest factors in cost. Proper storage of materials is very important to prevent loss due to damage, theft or quality deterioration of the materials. Therefore, the store must be properly organized and equipped to handle raw materials.
Ideal inventory levels should be maintained for all raw material items so that the production department can obtain the required amount of material in time. Also, excess working capital is not unnecessarily trapped in excess inventory. In addition, excess inventory increases production costs. However, the store department must be under the control of a technically qualified store representative.
2. Shopkeeper function:
The store owner is responsible and needs to manage the store from all perspectives, so it should be placed higher in the management hierarchy. He is expected to assist the cost department for its effective functioning.
His duties and responsibilities are as follows:
(I) Receive materials from the receiving department.
(Ii) Maintaining proper store records.
(Iii) Arrange for proper storage of materials and finished products.
(Iv) To issue materials to the production department, contrary to appropriate and approved requirements.
(V) Monitor various inventory levels and issue requisitions to purchasing departments in time.
(Vi) Report waste, scrap, and obsolete inventories.
(Vii) To prevent unauthorized persons from entering the store.
(Viii) Regularly compare physical inventory and book numbers and adjust for any
Discrepancies.
(Ix) To keep the store clean.
(X) Make appropriate arrangements for the maintenance and storage of materials in storage.
(Xi) To recover surplus materials returned from the department or store.
The above features of the storekeeper show that storekeeping is an important factor and can greatly contribute to the efficient operation of business units.
Storage includes the following activities:
(I) Efficient and prompt issuance of materials and tools to the production sector, which is absolutely necessary to increase production.
(Ii) Receipt of materials from the warehousing and production departments.
(Iii) Organize storage in a logical order so that all items can be identified accurately and storage space is used economically and effectively
(iv) Organize inventory checks on an ongoing or regular basis so that we can provide accurate inventory quantities as needed
(V) Protect the material from damage and deterioration.
(Vi) Protect your store from theft, theft and fire.
3. Store composition:
In large organizations, management faces the problem of adopting the type of store organization.
Store type:
(A) Central store.
(B) Central store with sub stores.
(C) Independent stores in various departments.
The central store shows the centralized purchase and processing of the store.
Store benefits:
(A) It is economical because the floor area, office expenses, stationery, etc. are economical.
(B) The expertise and experience of store staff is available to ensure better management and supervision.
(C) A better layout is possible.
(D) Facilitates inventory checks.
(E) The amount of capital invested in stocks is minimized.
(F) All stores are located in one place, which is convenient for more effective management of physical inventory balance.
(G) You can regularly create brief reports on scrap and obsolete inventories.
(H) You can make better security arrangements.
However, centralized stores have some drawbacks.
Cons: Disadvantages:
(A) If the store is some distance from many departments, it will take time to deliver the materials to the production department. This causes inconvenience and delay.
(B) All types of substances are concentrated in one place, increasing the risk of fire loss.
(C) Shipping costs will increase.
(D) Due to a transportation failure at the central store, production may be stopped and costs may increase.
(E) Management is too complicated in very large stores.
4. Store layout:
As we saw in previous discussions, stores play an important role in the efficient and effective management of factories. The layout of the store should be carefully and carefully planned to ensure maximum efficiency.
The store department should receive the material from the supplier and place it in a convenient location so that it can be issued to the production department without delay. All parts of the factory should be easily accessible to minimize costs. Therefore, it is desirable that the store be centrally located in order to fulfil its responsibilities efficiently.
In a large factory with many departments, the store cannot be placed in a convenient location for delivery of materials, and at the same time the location must be close to the receiving department. Therefore, you should place your sub stores in a convenient location to serve specific parts of your organization.
Careful consideration is required for the layout of the store department. Racks, bins, shelves, etc. should be placed for easy access. There must be sufficient preparation for the open space for the truck to pass through. Special arrangements are required for the storage of materials that are affected by atmospheric conditions.
Heavy and bulky items that cannot be stored in racks or bottles should be stored on the floor. In that case, the area of the floor where these materials are stored should be marked with a white line indicating the area reserved for storing these materials.
5. Centralized store:
Large factories may choose to have a subsidiary within the production department. This facilitates the voluntary supply of materials needed by the manufacturing department. Deciding whether to have a subsidiary in a factory or a centralized store is very difficult. Before making a decision, you need to take into account the benefits of a centralized store.
Advantages of a centralized store:
I. Purchase orders can be placed according to the company's total requirements, and the more orders you have, the more costs you can save.
Ii. With a lot of small inventories, the total buffer inventories are much higher and are:
(A) There is little capital investment in stocks.
(B) The occupied space is small.
(C) Less risk of obsolescence and deterioration. And
(D) The time required to check the inventory balance is shortened.
Iii. Better supervision is possible by using specialized skills and equipment.
Iv. There are fewer administrative costs associated with inventory records.
v. Better layout of the store is possible and inventory management is more efficient.
Vi. The staff are familiar with different types of stores, so the absence of workers will not affect your work.
Vii. You can make better security arrangements.
Disadvantages of a centralized store:
Centralized storage of materials has the following drawbacks:
I. It involves increased shipping costs.
Ii. The production department needs to get the supply from remote stores, which causes inconvenience and delay in the supply of materials.
Iii. Moving small amounts of material more often increases costs and can lead to production control issues.
Iv. There is an increased risk of loss due to fire.
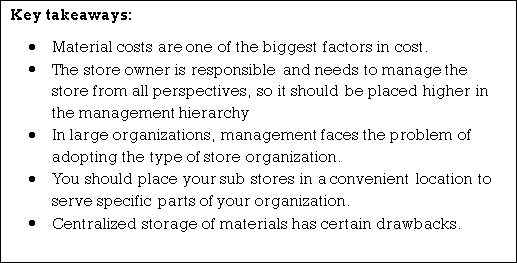
The important methods to follow in pricing material issuance are: -
2. Actual cost method
2. First-in first-out (FIFO) method
3. Last-in first-out (LIFO) method
4. Maximum first-in first-out method (HIFO) method
5. Simple average cost method
6. Weighted average cost method
7. Periodic average cost method
8. Standard Cost method
9. Exchange cost method
20. Last-in first-out (NIFO) method
22. Base stock method.
2. Actual cost method:
If you purchase a material specifically for a particular job, the actual cost of the material will be charged to that job. Such materials are usually kept separately and published only for that particular job.
2. First-in first-out (FIFO) method:
CIMA defines FIFO as "a method of setting the price of material issuance using the purchase price of the oldest unit in stock." With this method, the materials are issued out of stock in the order in which they were first stocked. It is assumed that the material that opens first is the material that is used first.
Advantage:
(A) Easy to understand and easy to price in question.
(B) It is a good store management practice to ensure that raw materials leave stores in chronological order based on age.
(C) This is an easy method with less administrative costs than other pricing methods.
(D) This inventory valuation method is accepted under standard accounting practices.
(E) Consistent and realistic practices in inventory and finished product valuation.
(F) Inventory is valued at the latest market price, close to the value based on replacement costs.
Cons: Disadvantages:
(A) If confused with other materials purchased at a different price at a later date, it is uncertain whether the material with the longest stock will be used.
(B) If the price of the purchased material fluctuates significantly, there will be more clerical work and errors may occur.
(C) Manufacturing costs are modest in situations where prices are rising.
(D) Inflationary markets tend to lower prices for key issues. The deflationary market tends to set higher prices for these issues.
(E) Generally, it is necessary to adopt multiple prices for the publication of a single document.
(F) This method makes it difficult to compare costs for different jobs when billed for the same material at different prices.
3. Last in first out (LIFO) method:
With this method, the latest purchase is issued first. Issues are priced on the latest batch you receive and will continue to be billed until the new batch you receive arrives in stock. This is a way to set the issue price of a material using the purchase price of the latest unit in stock.
Advantage:
(A) Shares issued at more recent prices represent the current market value based on exchange costs.
(B) Easy to understand and apply.
(C) Product costs tend to be more realistic as material costs are billed at more recent prices.
(D) When the price is rising, the issue pricing will be the more recent current market price.
(E) It tends to show modest profit figures by minimizing unrealized inventory gains and valuing inventory at its pre-price value, providing a hedge against inflation.
Cons: Disadvantages:
(A) Valuation of inventory in this way is not accepted in the creation of financial accounting.
(B) This is an assumption of a cash flow pattern and is not intended to represent the actual physical flow of material from the store.
(C) It may be necessary to adopt multiple prices for one problem.
(D) It becomes difficult to compare costs between jobs.
(E) It involves more clerical work and sometimes the evaluation may go wrong.
(F) During inflation, the valuation of inventory in this way does not represent the current market price.
4. Highest in first out (HIFO) method:
With this method, the most expensive material is published first, regardless of the date of purchase. The basic assumption is that in a fluctuating inflation market, material costs are quickly absorbed into product costs, hedging the risk of inflation. This method is used when the material is in short supply and when you are running a contract with costs. This method is uncommon and is not accepted by standard accounting practices.
5. Simple average cost method:
In this way, all the materials received are merged into the inventory of existing materials and their identities are lost. The simple average price is calculated regardless of the quantity involved. The simple average cost is obtained by dividing the number of batches and adding the various prices paid during the period to the batches purchased. For example, three batches of material received in Rs. 20, rupees 22 and Rs. 24 per unit each.
The simple average price is calculated as follows:
Rs. 20+ rupees 22+ rupees 24/3 batch = Rs. 36/3 batch = 22 rupees per unit
This method takes into account the prices of different batches, but is not common because it does not take into account the quantity purchased in different batches. Use this method when the price is less volatile and the stock price is small.
6. Weighted average cost method:
This is a permanent weighted averaging system in which the issue price is recalculated each time after each receipt, taking into account both the total quantity and the total cost when calculating the weighted average price. For example, three batches of material received in a quantity of 2,000 units @ Rs. 25, 2,300 units @ Rupee 26 and 800 units @ Rs. 24.24.
The weighted average price is calculated as follows:
(2,000 units x Rs .25) + (2,300 units x Rs .26) + (800 units x Rs .24) / 2,000 units + 2,300 units + 800 units
= Rs. 25,000+ rupees 20,800 + rupees 22,200 / 3,200 units = rupees 47,000 / 3,200 units = 25.26 per rupee unit
This method tends to smooth out price fluctuations and reduce the number of calculations because each issue is billed at the same price until you receive a new batch of material.
This method is easier than FIFO and LIFO because you do not have to identify each batch individually. However, this method adds more clerical work in calculating the new average price each time you receive a new batch. The calculated issue price rarely represents the actual purchase price.
7. Periodic average cost method:
With this method, instead of recalculating the simple or weighted average cost each time you have a receipt, the average for the entire accounting period is calculated.
The average price of all materials published during the period is calculated as follows:
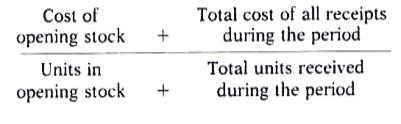
8. Standard cost method:
In this way, important issues are priced at a given standard issue price. The difference between the actual purchase price and the standard issue price is amortized on the income statement. The standard cost is a predetermined cost set by management before the actual material cost is known, and the standard issue price is used for all issuance to production and valuation of final stock.
Careful setting of standard prices first significantly reduces all clerical work and errors and simplifies inventory recording procedures. Eliminating cost fluctuations due to material price fluctuations makes it easier to compare realistic manufacturing costs. This method is not suitable in situations where prices fluctuate.
9. Exchange fee method:
The replacement cost is the cost of replacing the same material by purchasing it on the pricing date of the material issue. It is different from the actual cost on the purchase date. The exchange price is the exchange price of the material at the time the material is issued or on the valuation date of the end-of-term inventory.
This method is unacceptable to standard accounting practices as it reflects costs that are not actually paid. If the shares are held at exchange costs and are purchased at a lower price for balance sheet purposes, an element of profit that has not yet been realized will be included in the income statement.
This method is advocated by charging the job or process for the market price of the material, making it easier to determine the profitability of the job or process. This method is especially suitable for inflationary trends in material market prices. Without the exact market for a particular material, it is difficult to ascertain the replacement price for a material problem.
20. Next Inn First Out (NIFO) Method:
This method is a variant of the exchange cost method. In this way, the price quoted in the latest purchase order or contract is used for all issuance until a new order is placed.
22. Basic stock method:
With this method, the specified quantity of material is always kept in stock and priced as a buffer or base stock at its original cost. In addition, issuance of materials that exceed the basic stock quantity is priced using one of the above methods.
This method shows how prices fluctuate over time. However, this method is uncommon and makes stock valuation completely unrealistic and is not accepted by standard accounting practices.
Issue of Stores and Preparation of Store Ledger
Bin cards and store ledgers are two important store records that are commonly held to create records for various items.
Bin card:
A bin card is a quantitative record of receipts, issuance, and closing balances of store items. A separate bin card is maintained for each item and placed on a shelf or bin. This card is debited with the quantity of the store received, the quantity of the issued store is credited, and the balance of the quantity of the store is taken each time it is received or issued. You can easily find out the balance of an item at any time. To keep the store up-to-date balance, the principle is that you must touch the bin card before you can touch the item. For each item in the store, the material code, minimum quantity, maximum quantity, order quantity, and balance quantity are printed on the bin card. Bin cards are also known as "bin tags" or "stock cards."
Ledger storage.
BIN CARD OF A LTD | |||||||
Material Code: |
|
|
| Maximum Level: |
| ||
Mat. Description: |
|
|
| Minimum Level: |
| ||
Location: |
|
|
| Re-ordering level: |
| ||
Unit of Measurement: | |||||||
Date | Doc No. | Received from / Issued to | Receipts | Issue | Balance | Verification with Stores Ledger Date & Verified by | |
|
|
|
|
|
|
|
|
Stores Ledger is managed by the costing department (and possibly the unit price) to record the issuance of materials, including all receipts, quantities, and values. Ledger is similar to a bin card, except that receipts, issues, and balances are displayed along with the amount. The ledger contains accounts for receipts, issues, and all items in the store whose balances are recorded in both quantity and amount.
Matching store ledger with bin card:
Stores Ledger of Krishna Engineering Ltd. | |||||||||||
Material Code: | Minimum Qty: | ||||||||||
Bin No: | Maximum Qty: | ||||||||||
Material Description: | Ordering Qty: | ||||||||||
Location: |
| ||||||||||
|
| ||||||||||
Date | Receipts | Issues | Balance | ||||||||
| GR No | Qty | Rate | Amount | SR No | Qty | Rate | Amount | Qty | Rate | Amount |
|
|
|
|
|
|
|
|
|
|
|
|
Generally, there is no difference between the quantity displayed on the bin card and the store ledger. However, in reality, the difference is mainly due to the following reasons.
a. Arithmetic error when calculating balance.
b. If the document wasn't posted to either your bin card or your store ledger, it could be because the document wasn't received.
c. Post to the wrong bin card or the wrong sheet (code) in your store ledger.
d. Posting of the receipt being issued and vice versa.
e. Materials issued or received for loan or approval may be entered on the bin card, but not on the store's ledger.
The difference between a store ledger and a bin card invalidates the purpose of maintaining two separate sets and invalidates the physical inventory because the correct book balance is not available for comparison with the physical balance. I will. Therefore, various methods are used to control or reduce discrepancies between the store's ledger and bin card and maintain the correct balance of the books.
Difference between Bin Card and Stores Ledger: -
Bin Card | Stores Ledger |
(a) The shopkeeper manages it | (a) It is managed by the cost accounting department. |
(b) It contains only quantitative details of the materials received, issued, and returned to the store. | (b)Contains both quantity and value information |
(c) Input is made when the transaction is made | (c) Always posted after the transaction |
(d) Each transaction is posted individually. | (d) The transaction is summarized and then posted. |
(E) Transfers between departments are not displayed on the bin card. | (e) Material transfers from one job to another are recorded for costing purposes. |
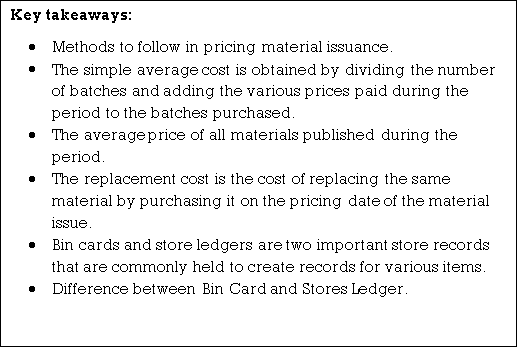
References:
1. Https://accountantskills.com/difference-between-bin-card-and-store-ledger/
2. Https://www.accountingnotes.net/term-papers/stores-ledger/term-paper-on-stores-ledger-stock-cost-accounting/24723
3. Http://www.unishivaji.ac.in/uploads/distedu/B.%20Com.%20Part-III282222.pdf
4. Https://www.yourarticlelibrary.com/cost-accounting/material-control/techniques-of-material-cost-control-22-techniques/55434
5. Https://ca-intermediate.in/wp-content/uploads/2028/08/Chapter-2-Material-Cost.pdf
6. Https://smallbusiness.chron.com/element-cost-management-accounting-67262.html
7. Https://www.economicsdiscussion.net/cost/elements-of-cost-in-cost-accounting/32700