UNIT III
Labour cost
Preface
Labor is an important element of production. It is a human resource and participates in the process of production. Wages paid for labor are an important cost item. Labor costs need to distinguish between direct and indirect labor. Direct labor costs can be directly identified and billed by product or job, but overhead costs are less identifiable and are included in overhead costs that may be assigned to different products or departments on appropriate criteria. Labor costing has three main purposes.
1. Determining labor costs in terms of product or service costs
2. Report labor costs for planning and management
3. Report labor costs for decision making.
Labor management
Labor costs are an important part of total production costs. Therefore, labor costs and labor costs need to be managed effectively. Various departments contribute to the efficient use of the workforce and the proper management of costs. The HR department needs to provide an efficient workforce. The engineering department maintains control over the working conditions and production methods of each job and department or process by creating plans and specifications. The time management department keeps an accurate record of the time each employee spends. Payroll preparation from the clock card, job or time ticker, or timesheet is done by the payroll department. The costing department is responsible for accumulating and classifying all data for which labor costs are one of the most important items.
Personnel costs represent human contribution. Labor costs are inherently sensitive. The reason is that labor costs are entirely based on human behaviour, labor behaviour. To manage labor costs, it is necessary to manage labor behaviour. Therefore, managers need to study human behaviour, labor performance, time and movement studies, labor turnover, and labor approaches to manage labor costs.
The workforce cannot be saved for future reference. It is very similar to the perishable nature of the material. Some materials are of poor quality and may not be used for manufacturing purposes. Such materials are wasted. Similarly, once the workforce is lost, it cannot be recovered and cannot be used effectively in the next few days.
If the work is kept idle, management will have to pay compensation or wages for such idle time. Therefore, management suffered two losses. They are lost working hours and lost money. Therefore, management is very enthusiastic about managing labor costs.
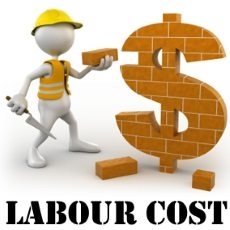
Classification of labor costs
Labor costs can be categorized as follows.
1. Direct labor costs
Direct labor costs are part of salary or wages and can be identified and billed by a single unit price of production.
Characteristics of direct labor costs:
Direct labor costs have the following characteristics.
- It has a direct relationship to the product, process, or cost unit.
- It can be measured quantitatively.
- A sufficient amount of material.
2. Indirect labor costs
Even if it occurs directly, it cannot be identified in the production of goods or services. These costs are incurred at the production site. Some cost centers may serve production departments or production activities. These cost centers are responsible for purchasing, engineering, and time management.
3. Manageable labor costs
Labor costs can be managed by managers during production and even when there is no production. Standard hours and hourly rates are fixed and workers can be required to complete a job or order within such time. That way, labor costs can be reduced to some extent.
4. Uncontrollable labor costs
Labor costs that management cannot easily control. Jobs and orders can be completed by a group of workers. The efficiency of such labor groups is inherently different. Workers can maximize their efficiency according to the general environment of the product location. If so, costs cannot be controlled by management.
Information required for labor cost management
To effectively manage labor costs, you need the following information:
3. Worker recruitment costs.
2. Worker training costs.
3. Worker turnover rate.
4. Idle time.
5. Over time.
6. Shift work.
7. Labor efficiency.
8. Number of workers.
9. Useless.
30. Corruption.
33. Payment of wages.
Personnel cost management method or method
To effectively manage labor costs, management can do the following:
3. Appropriate production planning.
2. Standard time correction.
3. Fixed clear wage structure.
4. Agreement with workers.
5. Preparation of labor budget, that is, labor cost budget and working time budget.
6. Labor performance report.
7. Modification of specific incentive payments
Computation of Labour cost
How to Calculate Labour Cost: Per Hour, Per Unit, Techniques and Formula
Techniques for managing labor costs can be effectively used by coordinating the activities of various labor-related departments.
(A) Human Resources Department
(B) Engineering and Operations Research Division
(C) Timekeeping department
(D) Payroll department and
(E) Cost accounting department.
The capabilities of these departments in reviewing and managing labor costs are described in detail below.
(A) Human Resources Department:
The Board of Directors has policies regarding recruitment, training, placement, transfer and promotion of employees. The Human Resources Manager of the Human Resources Department must implement these policies. The main functions of this department are recruitment, training, and placement of workers in the right jobs.
The Human Resources department recruits, workers when it receives employee placement requests from various departments.
(I) Employee placement request:
This is a document initiated by a department that needs employees. Upon receipt of the job, the Human Resources Department will take action to appoint a worker by receiving the application, scrutinizing the application, interviewing the applicant, and finally selecting the appropriate candidate.
The proforma for employee placement requests is:
All workers are appointed according to the labor budget. The budget specifies the number of workers appointed and the skills required. It is the task of the Human Resources Department to comply with the budget and appoint additional workers only if approved by the competent authority.
At the time of appointment, each worker is assigned a number, which is quoted in all communications relating to the worker. This makes it easy to identify EDP workers and systematically maintain information about them.
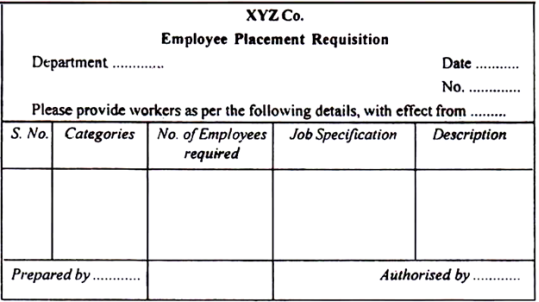
(II) Employee history card:
The Human Resources department maintains full details of the workers employed. Details for each employee are kept on the employee's history card. The card contains all relevant information such as (a) name and address, (b) number, (c) department, (d) date of employment, (e) category, (f) education qualification (g) experience (h), etc. It contains. Former employer's name and reason for retirement (i) Salary scale (j) Skills (k) Promotion (l) Reason for retirement. These details help management evaluate employees, especially the last column to help management prevent turnover.
Managing worker recruitment is essential to optimizing the right number of workers.
The following measures will help you manage the recruitment of workers.
(1) Hiring goes through the Human Resources Department.
(2) Hiring is done according to the labor budget.
(3) Hiring will be done only when you receive a job offer.
(4) In addition to budget labor, additional workers must be hired only if sanctions are imposed by the appropriate authorities.
(5) Recruitment of temporary workers should be properly approved.
(6) Introduce mechanization as much as possible.
(7) Labor utilization reports from all relevant departments so that management can make decisions on hiring surplus workers, hiring temporary workers, using surplus labor, reducing labor, reducing labor turnover, etc. Request.
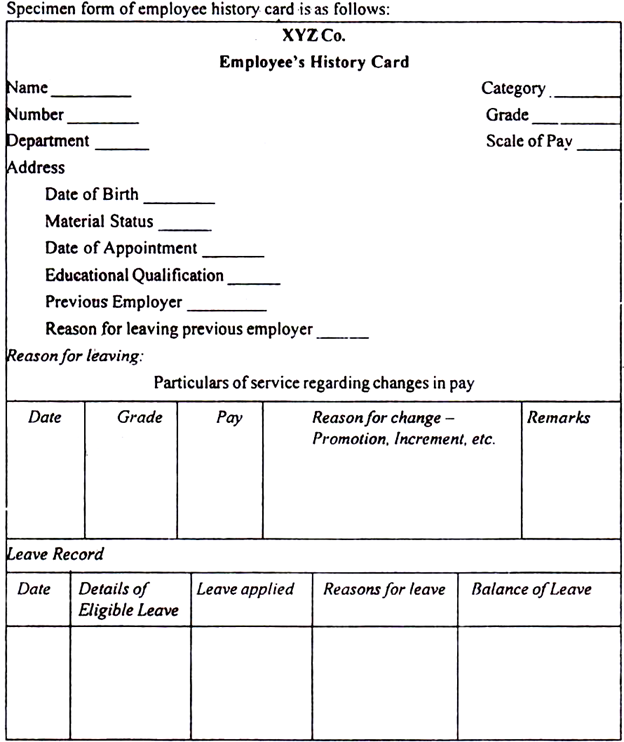
B) Engineering and Operations Research Division:
Preface:
This department is working to improve working conditions by carrying out the following activities.
(1) Conduct work studies such as method study, exercise study, and time study for each operation.
(2) Maintain the necessary safety standards.
(3) Perform job analysis and job evaluation.
(4) Prepare the specifications and time schedule for each job.
(5) Devise an appropriate wage system and
(6) Implementation of research and experimental work.
The engineering department is basically responsible for work content, standard time, work performance, and so on. These are achieved by performing detailed work studies, including method studies, motion studies, and time studies.
Work study:
Work study is the study of the technical aspects of production. This includes detailed investigation of processes, operations, job evaluation and analysis, and work measurements. Therefore, work studies include method studies, exercise studies, and time studies.
(I) Method study:
It is a procedure to analyse the work, remove unnecessary work and practices, systematically organize the remaining work, and standardize the work method. Motion studies only follow after deciding on the best way to do the work-
II) Motion study:
This is an important part of work study that divides the work into several key elements. Each of these elements is analysed in detail individually and in relation to each other. When the timing of these elements is set. Motion studies eliminate unnecessary and inefficient motion, "minimizing waste."
The main purpose of motion research is to standardize work practices by saving effort, reducing fatigue and improving efficiency. Motion studies take into account the human elements of work, plants and machines, tools and materials used. Once the motion study is complete, you need to perform a "time study".
(III) Time study:
Fixing the standard time for each operation is called a "time study". Also called workload measurement. Standard time is fixed for each operation. This is a fictitious time to measure the amount of work done in an hour. This helps management evaluate labor requirements, fix wage rates, and implement incentive schemes. Systematic method studies, along with exercise and time studies, help standardize work, equipment and methods. It is also useful for cost control, output and wage control.
Job analysis:
Job analysis is the process of determining the list of qualifications a worker has to do the job effectively.
The US Department of Labor defines job analysis as follows: “The process of making decisions by observing, investigating and reporting relevant information related to the nature of the job. It constitutes the skills, knowledge, abilities and responsibilities required of workers for work and successful performance. And it's a task decision that differentiates your work from everything else.
Therefore, job analysis is a study of work, identifying obligations and responsibilities, conditions of performance, nature of work, qualifications to own, opportunities and privileges related to the performance of the work.
Job analysis elements:
Job-related information can be analysed in the following two subheadings:
1. Analysis of work-related information:
This analysis analyses the requirements of the job. The requirement is known as a job description.
2. Employer-related analysis:
This analysis analyses the qualities that an employee should have. The qualities that a job holder should have are called job specifications.
Benefits of job analysis:
1. Fixed appropriate wage rate:
Fees are fixed according to the nature of each job, so fixed fees are reasonable and fair.
2. Elimination of personal prejudice:
Disputes over wage inequality are avoided because fees are fixed based on the nature of the job, not the value of individual workers.
3. Effective recruitment:
Job analysis guarantees the right job or the right person's policy of "no square pegs in round holes" because the job description and job specifications are key elements of job analysis.
4. Effective training:
Job analyses procedures help identify the qualifications and skills required for each job. Therefore, workers can be trained in the skills required for a particular job.
Job evaluation:
(1) Meaning and purpose:
Job valuation is the process of investigating and assessing the relative value of jobs within the industry and confirming their comparative value.
In addition to showing relative wage values, job valuation serves a variety of purposes:
(A) Helps to know if workers have the job that best suits them and if it benefits the employer.
(B) Help the HR department hire workers by demonstrating job responsibilities, requirements, conditions, and the qualities required for each job.
(C) Job evaluation forms the basis of a training plan.
Benefits of job evaluation:
(I) to employers:
(A) The hired employees are suitable for the job because the qualities required for the job are specified.
(B) The wage fund is fairly distributed because the labor value is confirmed by job evaluation.
(C) Job evaluation helps to minimize turnover.
(II) To employees:
(A) Jobs are best suited to employees because they are appointed based on the required qualities, skills and experience.
(B) Job evaluation reveals the comparative value of a job and the prospects it has for its employees.
(C) Workers will be happier because their total wages will be distributed fairly to them.
(3) Job evaluation procedure:
(A) Detailed work study
(B) Job description
(C) Job analysis
(D) Arranging work in progress and
(F) Determining the wage value of a job.
(4) Job evaluation method:
There are four ways to evaluate a job, as explained below.
(A) Ranking method:
In this way, jobs are rated from highest to lowest according to relative responsibility and complexity, not wage rates. Wage rates are assigned to jobs based on the prevailing rate in the area. This method is simple and suitable for small factories. The effect is limited because it does not accurately measure the work.
(B) Rating or classification method:
This method defines the basis of evaluation and divides the work into different grades. For example, grades can be categorized as skilled, unskilled, supervisory, executive, and administrative. Once your grades are confirmed, your work will be reviewed and your grades will be appropriate. Jobs in each grade are ranked as more sophisticated.
(C) Factor point scoring:
Evaluation of work in this way is done by comparing and analyzing the work against common factors. Points are assigned to each element according to their relative importance.
The most commonly recognized factors are:
(A) Education
(B) Experience and skills
(C) Job complexity
(D) Responsibility
(E) Effort and
(F) Working conditions.
Once jobs are analysed and points are assigned based on a common i-factor, the available wages are distributed among the jobs in proportion to the total points for each job.
The main advantage of this method is that it is easy to operate and the results are accurate.
The main drawbacks are:
(1) The points are not clearly defined.
(2) Points for each element are not scientifically assigned.
(3) Jobs that require extraordinary expectations cannot be analyzed with fixed factors.
(D) Factor comparison method:
This is similar to how factor points are scored. Jobs are analyzed, compared, and ranked under five factors:
(A) Mental requirements
(B) Skill requirements
(C) Physical requirements
(D) Responsibility and
(E) Working conditions.
These factors are evaluated by allocating existing wage rates to each. Jobs are compared by size and factor of "major jobs". The sum of the values of all the elements is the cache rate for each job.
(E) Merit evaluation:
Merit evaluation is intended to evaluate the performance of workers. The main purpose of merit assessment is to reward employees based on efficiency and merit. Merit evaluation brings out the comparative value of workers. The characteristics that are commonly considered to determine a worker's benefits and values are:
(1) Educational qualifications and knowledge
(2) Skills and experience
(3) Attitude toward work
(4) Quality of work done
(5) Efficiency
(6) Regularity
(7) Honesty
(8) Reliability
(9) Qualities such as leadership, initiative, self-confidence, and judgment
(10) Discipline and
(11) Cooperation.
Points are assigned to the above traits, and the total points scored for all traits determine the value of the worker. Employees are evaluated individually for each score and grouped based on a common score.
Importance of merit evaluation:
Merit assessment is a valuable tool that is considered important for measuring human resources.
The merit evaluation has the following advantages.
(1) It is useful to know the value and characteristics of individual workers. This helps supervisors assign tasks that workers are familiar with.
(2) It points out the characteristics that workers are not skilled. Workers have the opportunity to improve with proper training.
(3) Helps increase wages and opportunities for promotion.
(4) Recognizing the benefits and values of workers helps to stimulate their confidence.
Merit evaluation restrictions:
(1) Workers may be valued based on a single characteristic. The evaluator may ignore other features that the worker may not be good at.
(2) Disagreements among members of the Merit Evaluation Committee can lead to inadequate evaluation.
(3) Rating men are affected by personal discomfort with certain workers, which can lead to inadequate ratings.
(C) Time management department:
This department is concerned with maintaining worker attendance and working hours. Attendance time is recorded for wage calculation, and job time or time reservations are spent on each department, job, operation, and process to calculate labor costs for each department, job, and each process and operation. It will be considered to calculate the time taken.
Purpose of time management:
(1) Ensuring employee regularity
(2) Strengthen discipline among the labor force.
(3) Meets safety requirements
(4) Helps prepare for payroll.
(5) Track normality! Time, late, early leave.
(6) Used to absorb overhead costs based on working hours.
Depending on the size of your organization, there may be another time office at the factory gate. If your company is small, a gate office representative may be responsible for recording the time. Accurate time recording is essential because wage payments are based on the time spent by workers.
The point of a good time management system:
(1) A good time management system prevents "proxy" between workers.
(2) Even piecework workers must manage their time in order to maintain uniformity, regularity and continuous flow of production.
(3) Both arrivals and departures of workers should be recorded so that the total time spent by workers can be used for wage calculation.
(4) Mechanized time management methods should be used to avoid conflicts.
(5) Late arrival times and early departure times should be recorded to maintain discipline.
(6) Time recording should be simple, quick and smooth.
(7) Time records are supervised by the responsible person to eliminate irregularities.
Time management method:
There are two ways to manage time.
(1) Manual method.
(2) Mechanical method.
(1) The manual timing method is as follows.
(A) Attendance registration method.
(B) Metal disc method.
(A) Attendance registration method:
This is one of the traditional methods of time management. Attendance records are kept for workers in the time office or department adjacent to the factory gate. The register contains details about the worker's name, worker's number, the department in which he is employed, arrival time, departure time, normal time, passage of time, and more. Arrival and departure times may be recorded by the timekeeper.
This method is cheap and easy. Suitable for small organizations. In this way, workers and timekeepers are colluding, which can lead to fraudulent practices.
(B) Metal disc method:
In this way, the worker is assigned a disk or token with a hole containing the worker's identification number. The disc or token is hung on the board with pegs. The board of directors may be maintained individually for each department. Workers take out tokens and put them in the designated boxes when they enter the factory.
The box is deleted after the scheduled time. Late workers need to remove the token and hand it over to a timekeeper who records the exact arrival time. If tokens remain, they indicate an absent worker. The timekeeper then records attendance at a register called the "Daily Master Role" that the payroll department uses to create wage invoices and wage slips.
This method is simple and straightforward. If you have employees who are illiterate, you can follow them. You can easily identify the token. It can also be used by large companies with a large number of workers.
However, it has certain drawbacks-
(A) Employees may delete the companion token to mark attendance even when the companion is absent.
(B) The timekeeper can make mistakes, which can lead to disputes regarding the arrival time of workers.
(C) The master role may be a timekeeper with a dummy or ghost worker.
2. Mechanical method:
Time clocks are used to maintain accuracy and reliability.
There are two types of such devices.
(A) Time clock.
(B) Record dial time.
(A) Time clock:
Time cards are assigned to each worker for a week. Time cards are stored in the gate tray with a serial number. Workers remove the card from the tray and enter it into a time clock that records the exact time of arrival in the allocated space. This can also be done over time, departures, lunch breaks, and over time.
The time card may also contain details about hourly wages, total wages, deductions, and net wages. Wages are calculated based on the time recorded.
Below is a sample card that combines time and payroll.
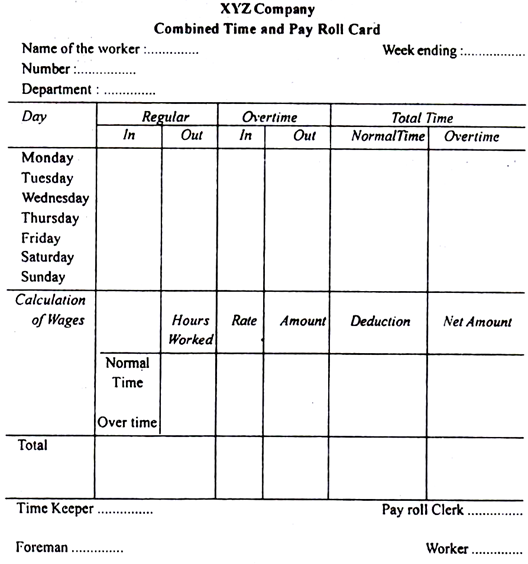
(B) Dial time recorder:
This machine has a 24-hour dial. There are about 150 holes on the dial, and each hole has a number corresponding to the worker's identification number. There is a radial arm in the center of the dial. The worker needs to place the radial arm in the hole of his number and his time is automatically recorded on the roll for the worker's number.
The worker's time is transferred by the machine to the wage table. The machine also calculates the wages of the workers. It provides excellent accuracy and saves time. The only limitation of dial time clocks is their high installation cost and their availability to a limited number of workers.
Time reservation:
The amount of time a worker spends on a variety of jobs and tasks is called a time reservation. This is a worker's productive time.
The purpose of time booking is to:
(1) We guarantee that the time paid according to time management will be used properly for work and orders.
(2) The cost department can check the labor cost of each job or work order.
(3) Helps distribute and distribute wages between different departments on which the working hour rate method is used.
(4) Useful for calculating idle time.
(5) By clarifying the time spent by workers on various jobs, it is useful when the incentive system is operated in the factory.
(6) Time reservations also help measure worker efficiency by comparing standard work hours with actual hours.
The documents used for time reservation are as follows.
(A) Daily timesheet.
(B) Weekly timesheet.
(C) Job ticket or job card.
(A) Daily timesheet:
A daily timesheet is issued to each worker who records the time spent on various tasks of the day. These sheets are used by small businesses with a small number of workers. The daily timesheet is verified and signed by Foreman at the end of each day.
Below is a sample daily timesheet.
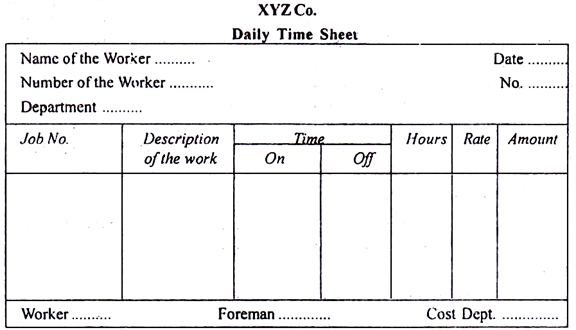
(B) Weekly timesheet:
This is an improvement over the daily timesheet because the daily timesheet increases the number of documents and the amount of work. Weekly timesheets are filled out by workers, verified by supervisors and counter-signed. In some cases, it is filled by department clerks to avoid incorrect input by workers. In addition, the foreman's precious time is not wasted to confirm the worker's input.
Below is a sample form of the weekly timesheet.
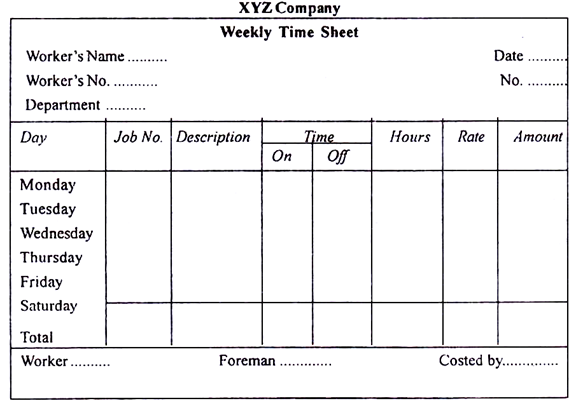
(C) Job card:
Job cards are used to accurately reach the time spent on each job.
There are four types of job cards used:
(I) Job card for each worker
(II) Job card for each job
(III) Combination of time and job card, and
(IV) Piece work.
(I) Job card for each worker:
Job cards are issued to each worker for a week or a day. The start and completion of each job is recorded. This serves the dual purpose of checking the time spent on each job and the total time the worker worked during the week or day.
(Ii) Job card for each job:
A card will be issued for each job. This is essential if the job needs to go through a large number of workers to complete. You can check the total number of working hours and total labor cost from the card.
The sample job card is as follows.
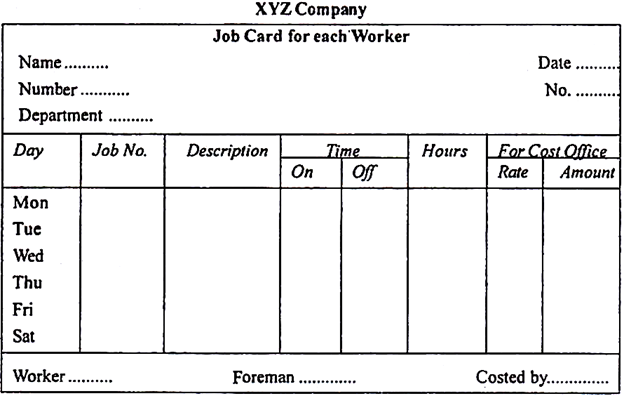
(III) Combination of time and job card:
It serves two purposes: time management and time booking. The card shows attendance and working hours. Cards can only be used when the number of workers is small.
A sample card is shown below.
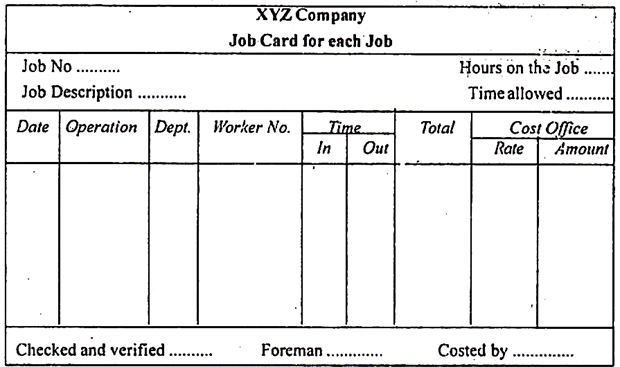
(Iv) Piece work:
This card is maintained by companies that use piece work to pay their wages. When payments are made on a results basis, production is taken into account, but time spent by workers is not. However, time must also be recorded to maintain the flow of production and discipline among workers. The piece work card shows the production volume, the refusal if any, and the piece work.
A sample piece work is shown below.
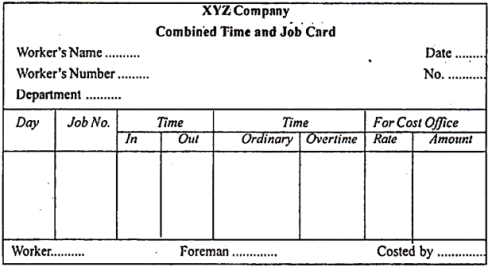
Time management and time reservation coordination:
(I) Idle time:
Attendance time must match work time. In general, it doesn't happen for many reasons. Examples-Time required to walk from the factory gate to the department, materials, tools, time lost to wait for instructions, loss due to machine failure, power outages, etc. This wasted time is called idle time. The idle time card is provided to check the idle time. The idle time card shows the reason for the idle time, so you can take action to prevent avoidable idle time.
A sample idle time card is shown below.
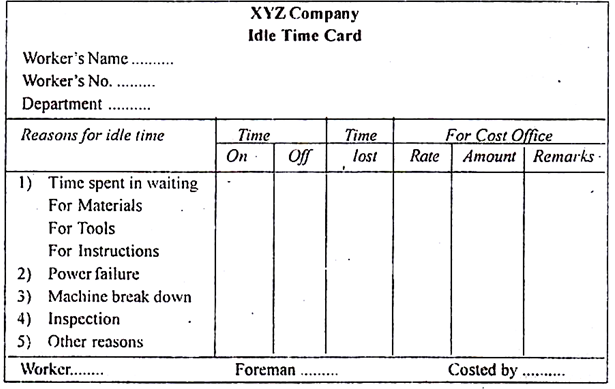
Idle time type:
Idle time can be divided into two categories based on the cause or reason for its occurrence.
(A) Normal idle time.
(B) Abnormal idle time.
(A) Normal idle time:
This is unique to all types of employment and cannot be avoided. The cost of this time is borne by each job or product or department.
An example of normal idle time is shown below.
(1) The time it takes for a worker to walk from the gate to the department.
(2) Time required to receive tools, change clothes, and receive work instructions.
(3) The time it takes to change from one job to another.
(4) Personal needs and time required for tea.
(5) Wait time for the machine to be ready for production work (called setup time).
Normal idle time processing:
There are two ways to charge your production environment during normal idle time:
(1) Normal idle time costs will be factory costs and will be collected as indirect costs.
(2) Normal idle time costs are charged directly to production as direct wages.
(B) Abnormal idle time:
Abnormal idle time is the avoidable idle time caused by preventable conditions.
The reasons why the idle time is abnormal are as follows.
(1) Time lost due to machine failure,
(2) Time lost due to a power outage.
(3) Loss of time due to lack of materials.
(4) Wasted time because there is no instruction. And
(5) Time lost due to strikes and lockouts.
Handling of abnormal idle time:
The basic principle of costing is to eliminate the impact of all anomalous losses and profits on a job or process or operation by transferring all anomalous costs and profits to the income statement. They should not form part of the production cost. Wages paid for abnormal idle time are charged to the costing profit and loss account.
Idle time control:
It is necessary to analyse the reasons for idle time and take measures to prepare for all contingencies, such as preventive maintenance of machines, proper arrangements to provide sufficient materials, preparation of work instructions in advance, and avoidance of strikes. There is. Even normal idle time can be controlled by efficient management planning and supervision.
(II) Overtime:
Employees are expected to work on a fixed schedule of day or week. If they work beyond it-overtime is called overtime. In other words, work that is done beyond normal time is called overtime.
The Indian Factory Act provides for overtime pay twice as much as usual. If a worker works more than 9 hours a day or more than 48 hours a week, he or she will be treated as overtime and will be paid twice as much as usual. Wages are calculated at the normal rate of up to 9 hours and at twice the normal rate of working more than 9 hours a day, or at a single rate of up to 48 hours and over 48 hours It is calculated at twice the normal rate.
The additional amount paid to a worker for overtime work is called overtime premium.
Overtime is not recommended as it increases production costs for the following reasons:
(1) Overtime is paid twice as much as usual.
(2) Overtime is done after normal hours at midnight, when fatigue may occur and workers' efficiency may not reach the required level.
(3) In order to work enough for overtime, workers may not be able to reach their full potential during normal hours.
(4) It is necessary to bear additional expenses for overtime work such as electricity bill, plant maintenance, wear and tear, and supervision.
Each of the above pushes costs up, so unless there is a demand for output that revenue justifies additional costs, it is not desirable over time.
Overtime treatment:
Regular wages form part of labor costs directly, but there is controversy over the treatment of overtime pay. Work done during normal hours has to bear a single rate, and work done over time is twice as expensive, creating "unfairness". To eliminate this, regular wages will be raised to include overtime pay, and regular hours or overtime work will bear the same costs.
However, if overtime is done under pressure from a particular customer, that customer will be charged for overtime. If overtime is due to an unusual reason, such as a machine failure or power outage, overtime will be charged directly to the income statement as an extraordinary cost.
Overtime management:
Overtime has many disadvantages and should be avoided and maximized control.
The following measures have been proposed.
(1) All normal work must be completed in normal time so that there is little room for overtime.
(2) Long-term justification should be supported by substantive interests, and long-term justification should be approved by the competent authority.
(3) The upper limit of time must be fixed for each worker.
(4) Frequent and regular reports should be prepared and forwarded to management regarding overtime hours and their costs. This allows management to take corrective action.
(D) Salary department:
Purpose:
This department creates payment invoices for the entire organization.
The purpose of the payroll department is to:
(1) Keep records of each worker's work, department and wage rate to reach each worker's total income, deductions and net income.
(2) Check the wages of various cost centers.
(3) Summarize the total deduction amount and post it to the relevant account.
(4) Check the total time of each cost center and calculate the labor cost and the hourly rate for management purposes.
(5) Confirmation of overtime pay and idle hourly wage.
(6) Provide an internal check system for wage payments.
Payroll Preparation:
A department salary or wage table is created based on the time card. A full-fledged payroll shows total wages, various deductions, and net wages. Payroll is the basis for checking wages and posting entries to various management accounts. Payroll details depend on your organization's requirements.
Below is a sample payroll.
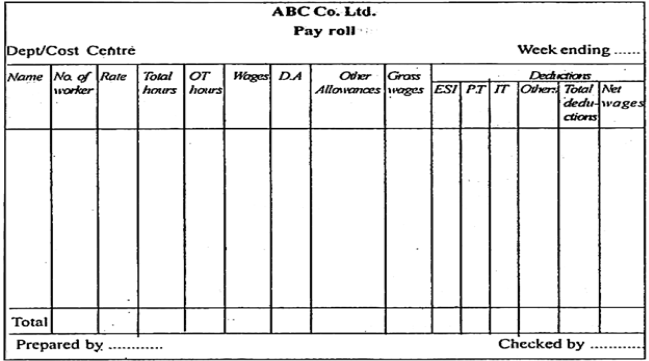
There are two aspects to payroll preparation. One is to reach total wages paid in the form of wages, including premiums and allowances over time. The second aspect of payroll is to calculate deductions in the form of ESI, PF, income tax, mortgage and prepayment related collections. Nowadays, most companies use computers to prepare for this.
Notes on paying wages:
Various types of fraud can occur in connection with wage payments. Unless the right systems are designed to prevent these frauds, repeated losses can occur and reduce the profitability of the enterprise. Effective internal checks and specific precautions can help reduce and prevent fraud in wage payments.
Here are the detailed steps for time management, time booking, payroll preparation, and finally wage payments to reduce wage payment fraud.
(1) Time management should be performed mechanically as much as possible, and appropriate and efficient supervision is essential to avoid time management fraud.
(2) How to calculate wages, various allowances, incentives and deductions should be simple and clear so that no doubt arises.
(3) If piece work is widespread, inspect the product quickly to maintain the quality of the product and pay only for the good product.
(4) If the incentive system is operated on a time basis, a record of actual working hours and saved hours will be maintained.
(5) Overtime should be approved by the appropriate sanctions of the competent authority. We will compare actual overtime with approved overtime to identify unapproved overtime and take appropriate measures to prevent it.
(6) Introduce effective internal checks when creating wage tables. The work done by the clerk needs to be verified by another clerk to ensure accuracy and perform internal checks to prevent fraud.
(7) The cashier must not have a role when creating the wage table. Similarly, the clerk involved in creating a wage table should not be involved in creating a wage envelope.
(8) The wage table is verified by a personnel officer to detect fraudulently included dummy workers.
(9) It can be seen that the workers have been identified before the wages are handed over to each person.
(10) Payment of wages shall be made simultaneously in all departments so that workers are not present in two places.
(11) Wages for absentees due to illness shall be paid only on the basis of an appropriate approval letter.
(12) Unpaid wages are entered in a separate record kept for that purpose. Attention should be paid while paying these wages.
(E) Cost accounting department:
Preface:
The department is responsible for ensuring the correct production costs.
Cost verification includes classification, collection, and calculation of output labor costs. In most organizations, cost department representatives
Posted to the manufacturing department to accumulate and categorize costs. The cost calculator oversees the work of the representative and uses the information contained in the timecard and payroll to find the labor costs of manufacturing by manufacturing department, operations, manufacturing instructions, and so on.
The costing department also analyses labor costs in the form of idle time and overtime. A labor cost report is also submitted to management to show the effectiveness of labor use.
Wage Accounting Documents:
(1) Clock card, job card, idle time card:
These are the basic documents for calculating labor costs for jobs, departments, operations, and jobs. Adjusting the clock card and job card is essential to reveal the idle time.
(2) Ratio of wage table and deduction chart:
These documents will help you prepare for payroll.
(3) Wage analysis or wage summary:
This is a salary analysis for various control accounts. This is a summary of the wages paid per job and the wages paid during idle hours. These totals must match the total wages paid.
Wage analysis:
The wages charged for various jobs are shown on an analysis sheet called the Wage Analysis Sheet. This is suitable if your company is small and the number of jobs running is small.
If you have a lot of work, as in a large company, the timesheet will pre-list the total labor costs and agree with a payroll overview.
The wage summary decisions are as follows:
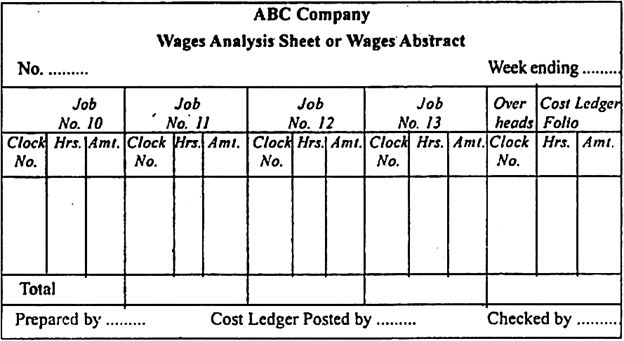
The analysis sheet shows the labor costs for various jobs and the overhead costs charged as overhead costs.
(4) Journals and ledgers:
Posting of various transactions related to labor costs is done from payroll. Various transactions are posted to the control account in the general ledger. Various sub ledgers in the form of work in process ledgers, factory overhead ledgers, etc. are posted along with the relevant labor cost items.
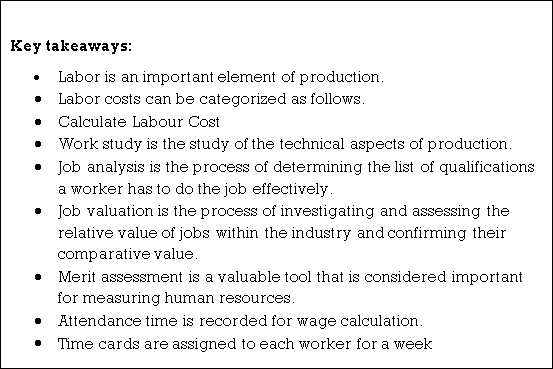
There are the following types of incentive wage systems:
1. Halsey Premium Plan
2. Rowan Premium Plan
3. Taylor Differential Peace Rate System
4. Gantt Bonus Plan
5. Emerson Efficiency Plan
6. Bedo Point Premium
7. Merrick Differential Wage Multi-Piece Rate Plan
8. 100% bonus plan.
Halsey Premium Plan:
This plan was introduced in 1891 by American engineer F. A. Halsey. Recognize your personal efficiency and pay bonuses based on the lime saved. In this way, workers are paid at the rate of the hours they actually worked and are also paid a bonus if they can complete the work in less time than the time allotted to do the work.
Bonuses are paid at a fixed percentage of the time saved, usually 50% (although the percentage varies from 30% to 70% of the time saved). The remaining 50% of the time saved will be shared by the employer.
Therefore,
Total revenue = T.T. × H.R. + 50% (T.S. × H.R.)
Here, T.T. = Time required
H.R. = hourly wage
T.S. = Time saved
The main advantages of this method are:
(I) the method is simple to operate and easy to understand.
(II) Late workers are not punished because hourly wages are guaranteed.
(III) Provide incentives for more efficient workers.
(IV) Worker efficiency means reducing costs per unit.
(V) The benefits of time savings are shared equally between employers and employees.
The main drawbacks of this method are:
(I) many employee organizations do not like to share the benefits of time savings equally.
(II) Attracting bonuses reduces the quality of work.
(III) Poor quality means more waste, potential for corruption, defects and failures, and more oversight costs.
(IV) Not as attractive as peace rate payments.
(V) There are few incentives for workers compared to other incentive plans.
(VI) This can lead to higher bonuses if the time rate is not fixed properly.
Halsey-Weir Premium Scheme:
This scheme was introduced by Weir Ltd. In Glasgow around 1900. This scheme is similar to the Halsey scheme, except that employees get 33⅓% (often 30%) of the time saved as a bonus and the remaining 66⅔% is paid to the employer.
Therefore:
Total revenue = T.T. × H.R. + 33⅓% (T.S. × H.R.)
Here, T.T. = Time required
H.R. = hourly wage
T.S. = Time saved
Rowan plan:
Grames Rowan first introduced this plan in Glasgow in 1898. In this scheme, like the Halsey scheme, workers receive a guaranteed hourly wage for actual working hours. However, premiums are calculated differently here.
If a worker can complete a job in less time than allowed, his bonus is to his hourly wage for that percentage of the time saved to endure the allowed time. Will be equal.
Therefore, the bonus is calculated as follows:
And total revenue = T.T x H.R. + (T.T. × H.R.) × T.S. / T.A.
Here, T.T. = Time required
H.R. = hourly wage
T.S. = Time saved
T.A. = Allowable time
The main advantages of this scheme are:
(I) It provides incentives for learners and slow workers.
(II) Premiums are proportional to the time saved, so employers are protected if they are not properly fixed.
(III) From the employer's point of view, the Rowan scheme is safer than the Halsey scheme.
(IV) With up to 50% of the time saved, the bonus for this scheme will be higher than the bonus for the Halsey scheme.
(V) As the bonus increases at a rate of decrease. Employees are not in a hurry to complete their work quickly, reducing the possibility of waste.
(VI) Due to the high output, the fixed overhead per unit is low.
The main drawbacks are:
(I) the method is complicated.
(II) Incentives are low at high production levels.
(III) Employees are willing to share their time savings with their employer.
Comparison of Halsey and Rowan schemes:
(1) With savings of up to 50%, premiums will be the same for the two schemes.
(2) In the Rowan scheme, the bonus rises faster than in the Halcy scheme until the job runs in half the standard time.
(3) However, if the work takes less than half the standard time, both the Halsey system premium and the total income will be higher than the Rowan system premium.
(4) On the other hand, if the work time exceeds half of the standard time, both the bonus and total income of the Rowan scheme will be larger than that of the Halsey scheme.
(5) The Halsey scheme provides more incentives to speed up production, but after certain stages there is an automatic check under the Rowan scheme.
(6) The Halsey scheme turns out to be costly if more than half the time is saved, while the Rowan scheme is costly if less than half the standard time is saved.
Taylor's Differential Peace Rate System:
This system was first introduced by F.W. Taylor, the father of scientific management. This system does not provide a minimum guaranteed hourly wage.
However, in this system, the two piece rates are fixed.
(A) Workers are paid a low peace rate for substandard production
(B) Higher fees are paid to workers who produce above the standard. Therefore, this system penalizes inefficient workers and rewards efficient workers.
Worker efficiency can be determined as one of the following percentages:
(I) from the time allowed for the job to the time actually taken, or
(II) From the actual output within the specified time to the standard output.
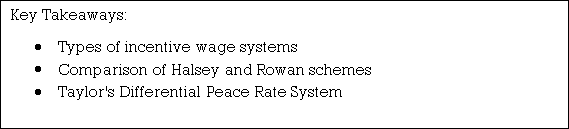
Overview of overhead
All overhead costs are collectively referred to as overhead costs. This is the sum of all indirect materials, indirect labor, and indirect expenses. They make up a key component of the total cost of a product, job, or process. Overhead is not directly measurable and is observed in relation to a particular activity or unit of production, but must be incurred in production. Examples: Factory building and machine depreciation, rent, taxes, insurance, maintenance, etc.
Classification of expenses
The process of grouping overheads according to common characteristics is known as overhead classification. It provides managers with information that allows them to effectively manage their business. Overhead can be categorized as follows:
a. Elements: indirect materials, labor costs;
b. Function: Expenses for production, management, sales and distribution.
c. Behaviour: Fixed, variable, and semi-variable overhead.
1. Fixed overhead remains fixed and is not affected by changes in production levels. For example, rent, fees, salaries, statutory expenses, etc.
2. Variable overhead costs change in direct proportion to changes in production, such as indirect materials, fuel, electricity, stationery, and sales staff commissions.
3. Semi-variable overhead costs are partially fixed and partially variable costs. They remain fixed to production volume and change when production exceeds a certain volume. For example, telephone charges include machine depreciation, repair and maintenance, and supervision costs.
Collection of expenses and codification
Overhead is collected and systematized under the appropriate head. Similar overhead items should be grouped. Overhead grouping is done by a technique called "Codification". This is a way to identify and describe various expenses with numbers, letters, or a combination of both, making it easy to collect cost data. The coding of the entire item is done through a proper coding system. Expenses are collected through store requests, financial accounting, wage tables, registries, and report sources.
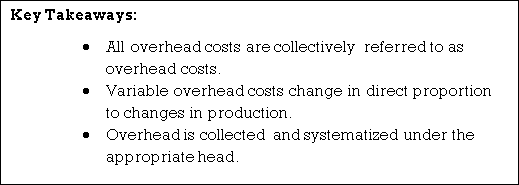
Overhead allocation is the allocation of all items of costs to cost centers or costs to units. This refers to the billing of overhead costs to the cost center. This means that overhead was incurred due to the existence of that cost center. If a company offers multiple products, factory overhead is allocated to different production departments or cost centers. Appropriate overhead allocation is very important because incorrect allocations can distort income decisions, asset valuations, and performance valuations. The overhead allocation process is as follows:
I. Accumulate overhead costs based on department or product.
Ii. Identify cost targets for assigned costs
Iii. Choose how to associate such accumulated costs with cost goals.

References
1. Https://accountlearning.com/what-is-overhead-meaning-importance-classification/
2. Https://www.investopedia.com/terms/c/cost-of-labor.asp
3. Cost Accounting Study Material
4. Author(s): CBSE Research and Development Unit
5. Cost Accounting Course Material
6. University Of Calicut