Unit – 1
Building Materials & Construction
STONES
TYPES
Type of Stones
Stones used for civil engineering works may be classified in the following three ways:
1. Geological
2. Physical
3. Chemical
4. Geological Classification
Based on their origin of formation stones are classified into three main groups—Igneous, sedimentary and metamorphic rocks.
(i) Igneous Rocks: These rocks are formed by cooling and solidifying of the rock masses from their molten magmatic condition of the material of the earth. Generally igneous rocks are strong and durable. Granite, trap and basalt are the rocks belonging to this category, Granites are formed by slow cooling of the lava under thick cover on the top. Hence they have crystalline surface. The cooling of lava at the top surface of earth results into non-crystalline and glassy texture. Trap and basalt belong to this category.
(ii) Sedimentary Rocks: Due to weathering action of water, wind and frost existing rocks disintegrates. The disintegrated material is carried by wind and water; the water being most powerful medium. Flowing water deposits its suspended materials at some points of obstacles to its flow. These deposited layers of materials get consolidated under pressure and by heat. Chemical agents also contribute to the cementing of the deposits. The rocks thus formed are more uniform, fine grained and compact in their nature. They represent a bedded or stratified structure in general. Sand stones, lime stones, mud stones etc. belong to this class of rock.
(iii) Metamorphic Rocks: Previously formed igneous and sedimentary rocks undergo changes due to metamorphic action of pressure and internal heat. For example due to metamorphic action granite becomes greisses, trap and basalt change to schist and laterite, lime stone changes to marble, sand stone becomes quartzite and mud stone becomes slate.
Physical Classification
Based on the structure, the rocks may be classified as:
Stratified rocks
Unstratified rocks
(i) Stratified Rocks: These rocks are having layered structure. They possess planes of Stratification or cleavage. They can be easily split along these planes. Sand stones, lime stones, slate etc. are the examples of this class of stones.
(ii) Unstratified Rocks: These rocks are not stratified. They possess crystalline and compact grains. They cannot be split in to thin slab. Granite, trap, marble etc. are the examples of this type of rocks.
USES OF STONES
- Stone masonry is used for the construction of foundations, walls, columns and arches.
- Stones are used for flooring.
- Stone slabs are used as damp proof courses, lintels and even as roofing materials.
- Stones with good appearance are used for the face works of buildings. Polished marbles and granite are commonly used for face works.
- Stones are used for paving of roads, footpaths and open spaces round the buildings.
- Stones are also used in the constructions of piers and abutments of bridges, dams and retaining walls.
- Crushed stones with graved are used to provide base course for roads. When mixed with tar they form finishing coat.
Crushed stones are used in the following works also:
- As a basic inert material in concrete.
- For making artificial stones and building blocks.
- As railway ballast.
TESTS ON STONES
- Acid Test: Acid test is used to investigate how much atmospheric action can be resisted by stone. In this test 100 grams of stones in chipped form are kept in a 5% solution of hydrochloric acid or sulphuric acid. After 3 days stones in chipped form are taken out and dried. If the edges of stones are sharp as earlier, it indicates that stone can resist weathering actions.
- Smith's Test: This test is used for finding out the presence of soluble matter in stones. In this test few sample of stones are place in a glass or test-tube filled with clean water. Stones are kept in water for 1 hour. After this the glass or test-tube is vigorously shaken. Due to presence of earthy material and clay impurities water is converted to dirty water. Slightly cloudiness of water will prove that the stones are good and durable. If water becomes too dirty, it indicates that stone contains too much soluble impurities and it is not suitable for construction.
- Crushing Strength: Crushing test is used to investigate the compressive strength of stone. In this test stone is cut into cubes of dimension 40mm. Sides of cube are finely dressed and finished. Cubes of stones are then kept in water for 72 hours. Then 5mm thick layer of plywood or plaster of paris is applied on the load bearing surface. Load is applied axially on load bearing surface using universal testing machine or crushing testing machine until cracks appear on the stone or stone starts crushing.
- Water Absorption Test: In this test, 50 grams of stones in chipped form are places in an oven at 105 degree Celsius for 3 hours then cooled at room temperature. Weight of stones is then taken (W1). Then stones are places in distilled water for 3 days. After 3 days weight of stones is taken (W2). (Percentage '%' of water absorption should not exceed 15%, otherwise stone is not suitable for construction.)

- Crystallization Test: 4 cubes of stone with dimension 40mm are taken. Stones are dried for 3 days and weighed. Then stones are immersed in 14% solution of Sodium Sulfate (Na2SO4) for 2 hours. After this stones are dried at 100 degree Centigrade and weighed. Difference in weight is noted .Process of drying, weighing, immersion and reweighing is repeated at least 5 times. Each time, change in weight is noted and it is expressed as a percentage of original weight. (percentage of wear should not exceed 2% for good stone).
- Hardness Test: This test is carried out to determine the hardness of stone. First weight of specimen is taken (W1). The specimen is filled in a test cylinder of diameter 25 mm and height 25 mm. Then cylinder is placed in Dorry's testing machine and force of 12.50 N is applied. The disc of testing machine is rotated at 28 revolutions per minute. During the rotation of the disc, coarse sand of standard specification is sprinkled on the top of disc. After 1000 revolutions specimen is weighed (W2).
- Impact Test: This test is carried out to determine the toughness of stone. This test requires an 'Impact Testing Machine'. In this test stones are filled in test cylinder of diameter 25 mm and height 25 mm. The cylinder is placed on machine and steel hammer of weight 20 N is allowed to fall on the specimen in cylinder. The height of first fall is 1 cm, height of second fall is 2 cm and so on. The height at which specimen breaks is recorded. If specimen breaks at 'n cm' then 'n' is the toughness index of stone.
- Microscopic Test: In this test specimen of stones is placed under microscope and various properties are studied such as grain size, texture of stone, pores, veins, shakes etc.
- Attrition Test: This test is carried out to test the resistance to abrasion (ability to withstand grinding action) of stone. This test is carried out in 'Attrition Test Machine'. In this test specimen of stone is weighed (W1). Then stones are transferred to drum and drum is inclined to 30 degree to the horizontal. Then stones are revolved ate 2000 revolution per hour for 5 hours. After this stones are sieved on a 2 mm sieve. Stones retained on sieve are weighed (W2) and loss in weight percentage gives the percentage of wear.
ENGINEERING PROPERTIES OF STONES
1. STRUCTURE
The structure of the stone may be stratified (layered) or unstratified. Structured stones should be easily dressed and suitable for super structure. Unstratified stones are hard and difficult to dress. They are preferred for the foundation works.
2. TEXTURE
Fine grained stones with homogeneous distribution look attractive and hence they are used for carving. Such stones are usually strong and durable.
3. DENSITY
Denser stones are stronger. Light weight stones are weak. Hence stones with specific gravity less than 2.4 are considered unsuitable for buildings.
4. APPEARANCE
A stone with uniform and attractive colour is durable, if grains are compact. Marble and granite get very good appearance, when polished. Hence they are used for face works in buildings.
5. STRENGTH
Strength is an important property to be looked into before selecting stone as building block. Indian standard code recommends, a minimum crushing strength of 3.5 N/mm2 for any building block
6. HARDNESS
It is an important property to be considered when stone is used for flooring and pavement. Coefficient of hardness is to be found by conducting test on standard specimen in Dory’s testing machine. For road works coefficient of hardness should be at least 17. For building works stones with coefficient of hardness less than 14 should not be used.
7. PERCENTAGE WEAR
It is measured by attrition test. It is an important property to be considered in selecting aggregate for road works and railway ballast. A good stone should not show wear of more than 2%.
8. POROSITY AND ABSORPTION
All stones have pores and hence absorb water. The reaction of water with stone causes disintegration. Absorption test is specified as percentage of water absorbed by the stone when it is immersed under water for 24 hours. For a good stone it should be as small as possible and in no case more than 5.
9. WEATHERING
Rain and wind cause loss of good appearance of stones. Hence stones with good weather resistance should be used for face works.
10. TOUGHNESS
The resistance to impact is called toughness. It is determined by impact test. Stones with toughness index more than 19 are preferred for road works. Toughness index 13 to 19 is considered as medium tough and stones with toughness index less than 13 are poor stones.
11. RESISTANCE TO FIRE
Sand stones resist fire better. Argillaceous materials, though poor in strength, are good in resisting fire.
12. EASE IN DRESSING
Cost of dressing contributes to cost of stone masonry to a great extent. Dressing is easy in stones with lesser strength. Hence an engineer should look into sufficient strength rather than high strength while selecting stones for building works.
13. SEASONING
The stones obtained from quarry contain moisture in the pores. The strength of the stone improves if this moisture is removed before using the stone. The process of removing moisture from pores is called seasoning. The best way of seasoning is to allow it to the action of nature for 6 to 12 months. This is very much required in the case of laterite stones.
BRICKS
Constituents of good brick earth: Bricks are the most commonly used construction material. Bricks are prepared by moulding clay in rectangular blocks of uniform size and then drying and burning these blocks. In order to get a good quality brick, the brick earth should contain the following constituents.
- Silica
- Alumina
- Lime
- Iron oxide
- Magnesia
Brick plays very important role in the field of civil engineering construction. Bricks are used as an alternative of stones in construction purpose.
USES OF BRICKS
- Construction of walls of any size
- Construction of floors
- Construction of arches and cornices
- Construction of brick retaining wall
- Making Khoa (Broken bricks of required size) to use as an aggregate in concrete
- Manufacture of surki (powdered bricks) to be used in lime plaster and lime concrete
CLASSIFICATION OF BRICKS AS PER CONSTITUENT MATERIALS
There are various types of bricks used in masonry
- Common Burnt Clay Bricks
- Sand Lime Bricks (Calcium Silicate Bricks)
- Engineering Bricks
- Concrete Bricks
- Fly ash Clay Bricks
Common Burnt Clay Bricks
Common burnt clay bricks are formed by pressing in moulds. Then these bricks are dried and fired in a kiln. Common burnt clay bricks are used in general work with no special attractive appearances. When these bricks are used in walls, they require plastering or rendering.
Sand Lime Bricks
Sand lime bricks are made by mixing sand, fly ash and lime followed by a chemical process during wet mixing. The mix is then moulded under pressure forming the brick. These bricks can offer advantages over clay bricks such as: their colour appearance is grey instead of the regular reddish colour. Their shape is uniform and presents a smoother finish that doesn’t require plastering. These bricks offer excellent strength as a load-bearing member.
Engineering Bricks
Engineering bricks are bricks manufactured at extremely high temperatures, forming a dense and strong brick, allowing the brick to limit strength and water absorption. Engineering bricks offer excellent load bearing capacity damp-proof characteristics and chemical resisting properties. Concrete Bricks Concrete bricks are made from solid concrete. Concrete bricks are usually placed in facades, fences, and provide an excellent aesthetic presence. These bricks can be manufactured to provide different colours as pigmented during its production.
Fly Ash Clay Bricks
Fly ash clay bricks are manufactured with clay and fly ash, at about 1,000 degrees C. Some studies have shown that these bricks tend to fail poor produce pop-outs, when bricks come into contact with moisture and water, causing the bricks to expand.
- ENGINEERING PROPERTIES OF CEMENT
To know the quality of bricks following 7 tests can be performed. In these tests some are performed in laboratory and the rest are on field.
- Compressive strength test
- Water Absorption test
- Efflorescence test
- Hardness test
- Size, Shape and Colour test
- Soundness test
TESTS ON BRICKS
Structure test Compressive strength test
This test is done to know the compressive strength of brick. It is also called crushing strength of brick. Generally 5 specimens of bricks are taken to laboratory for testing and tested one by one. In this test a brick specimen is put on crushing machine and applied pressure till it breaks. The ultimate pressure at which brick is crushed is taken into account. All five brick specimens are tested one by one and average result is taken as brick’s compressive/crushing strength.
Water Absorption test In this test bricks are weighed in dry condition and let them immersed in fresh water for 24 hours. After 24 hours of immersion those are taken out from water and wipe out with cloth. Then brick is weighed in wet condition. The difference between weights is the water absorbed by brick. The percentage of water absorption is then calculated. The less water absorbed by brick the greater its quality. Good quality brick doesn’t absorb more than 20% water of its own weight.
Efflorescence test The presence of alkalies in bricks is harmful and they form a grey or white layer on brick surface by absorbing moisture. To find out the presence of alkalis in bricks this test is performed. In this test a brick is immersed in fresh water for 24 hours and then it’s taken out from water and allowed to dry in shade. If the whitish layer is not visible on surface it proofs that absence of alkalis in brick. If the whitish layer visible about 10% of brick surface then the presence of alkalis is inacceptable range. If that is about 50% of surface then it is moderate. If the alkalies’ presence is over 50% then the brick is severely affected by alkalies.
Hardness test
In this test a scratch is made on brick surface with a hard thing. If that doesn’t left any impression on brick then that is good quality brick.
Size, shape and colour test
In this test randomly collected 20 bricks are staked along lengthwise, width wise and height wise and then those are measured to know the variation of sizes as per standard. Bricks are closely viewed to check if its edges are sharp and straight and uniform in shape. A good quality brick should have bright and uniform colour throughout.
Soundness test
In this test two bricks are held by both hands and struck with one another. If the bricks give clear metallic ringing sound and don’t break then those are good quality bricks.
Structure test In this test a brick is broken or a broken brick is collected and closely observed. If there are any flows, cracks or holes present on that broken face then that isn’t good quality brick.
TIMBER
TIMBER is the oldest material used by humans for construction after stone. Despite its complex chemical nature, wood has excellent properties which lend themselves to human use. It is readily and economically available; easily machinable ; amenable to fabrication into an infinite variety of sizes and shapes using simple on-site building techniques;
- Exceptionally strong relative to its weight
- A good heat and electrical insulator
- It is a renewable and biodegradable resource
A tree basically consists of three parts namely, trunk, crown and roots. The function of the trunk is to support the crown and to supply water and nutrients from the roots to the leaves through branches and from the leaves back to the roots .The roots are meant to implant the trees in the soil ,to absorb moisture and the mineral substances it contains and to supply them to the trunk.
ENGINEERING PROPERTIES OF TIMBER
The quality of timber must be ensured before using it for a purpose. The quality can be ensured by investigating the properties of timber. Here we have discussed both physical and mechanical properties of timber which affects timber quality.
Followings are the physical and mechanical properties of Timber
- Colour
- Appearance
- Hardness
- Specific Gravity
- Moisture Content
- Grain
- Shrinkage and Swelling
- Strength
- Density
- Toughness
- Elasticity
- Warping
- Durability
- Defectless
- Workability
- Soundness
- Free of abrasion
Colour
Color is a uniform property by which most trees are characterized as they show variation from tree to tree. Light color indicates weak timber. For example, freshly cut teak, Deodar, and Walnut have a golden yellow, whitish and dark brown shades respectively.
Appearance
Smell is a good property as timbers for few plants as they can be identified by their characteristic aroma. Fresh cut timbers have a good smell. For example resinous smell from pine.
Hardness
For the resistance of any kind of damage, hardness is an obvious property.
Specific Gravity
Variation of timber in specific gravity (0.3-0.9) is found. It depends on pores present inside timber. The specific gravity of this light material is less than that of water (<1). But in case of compact wood where pores are almost absent and become heavier, their specific gravity increases up to 1.5.
Moisture Content
Timbers are hygroscopic and gain water from nature (atmosphere). The absorption of water or dehydration depends on atmospheric humidity. If timbers moisture content is high that means the timber quality is low. Water content is the risk of fungal attack.
Grain
Several types of grain arrangement found. On the grain structure quality of timber varies. Grains remain closely related.
- Straight grain: Arrangement of vascular tissue (xylem and phloem) is important which grow parallel to the length of the timber that is termed as straight grain.
- Coarse grain: vascular tissue and fibre arranged broadly and widely.
- Interlocked grain: Instead of parallel arrangement twisted, a spiral arrangement may be found.
Shrinkage and Swelling
The percentage of shrinkage and swelling varies from plant to plant. Some give higher percentage after drying. Shrinkage starts when cell walls of timber start to release water. In moisture atmosphere timber swells when cell walls absorb water. Good quality timbers swell less. Timbers having thicker wall swell more than a thinner one.
Strength
Best quality timbers have the highest strength. Strength means capable to bear loads. Anisotropic material like timber has different structure at the different portion. So, the strength of timber is different at different points. Grain structure determines the strength of the timber. Some types of strength are
- Compressive strength: 500 kg/cm2 to 700 kg/cm2 load is enough to test timbers strength.
- Tensile strength: When timber is enough strong to the tensile force. If perpendicular force is made then timber is weaker. 500-2000 kg/cm2 is the range of tensile strength load.
- Transverse strength: Enough bending strength indicates good quality timber.
Density
Timber having higher density have a thicker wall. An important property that quality of timber. Moisture content: Presence of defects: There may be some of the natural and artificial defects in timber such as cross-grain, knots, and shakes, etc. All of them cause a decrease in the strength of the timber.
Toughness
Timber has to have the capability to bear shocks, jerk. Anti-bending and ant splitting characteristic is needed. Old timbers have annual rings which indicate their age is a good indicator.
Elasticity
Another property elasticity means timber should attain its own shape after use. Because of this quality, it is used in sports bat.
Warping
Environmental change with season can’t effect good quality timber.
Durability
A good quality timber has the property to resist the attack the infection of fungus or other insects. This resistance quality makes timber better.
Defectless
This property is gained if the timber is from a sound tree. A defectless tree is free from sap, shakes, and dead knots.
Workability
A good timber is always easy to work on it. Easy to drag using saw on good timber. The finishing can be done well.
Soundness
A good quality timber gives good sound.
Texture
The texture of good timber is fine and even.
Free of Abrasion
Timber should not be damaged by the external environment. It has to gain the ability to protect its skin.
USES OF TIMBER
Wood is a plant part having multipurpose uses those are impossible to deny and difficult to note all in our daily life. From the ancient time wood is used by human and this continuation still remains in the modern civilization. A few of many uses of wood are mentioned below:
1. Construction and Fencing
- Home Construction:
During the early periods, use of wood in domestic construction was a common scene and this is still followed in this twenty-first century. In different parts of the world in the making of houses, wood is used commonly like the flooring, frames of doors and windows for its strength and internment quality. e.g. Deodar, walnut wood is used in Pakistan widely, teak in South Asia and all over the world, Chir pine etc. In Bangladesh during construction of buildings woods from mango,bur flower tree are used for casting and piling.
- Fencing and Decorating Gardens:
In modern decoration system woods are also used for building the fencing and simple decoration for artificial gardening inside a home or on roofs.
e.g. Cedar, redwood, Shorea sp, Acacia sp.
2. Household Uses
- Utensils:
Utensils made up of wood instead of plastic and steel are a symbol of elegance which increases the charm and loveliness of the home corners.
e.g. Black walnut wood is used in the west for home utensils.
- Hand Tools:
The handles of most common hand tools made of wood help as heat resistant when they are kitchenware used in an oven and closes the chance to shock while used on electricity.
3. Art Industry
- Artworks:
For artworks such as statues, sculptures, carvings and making decorative objects woods are widely used. The frames of art board, colour plate are also made from wood in many cases. e.g. Pine, maple, cherry wood for framing work.
- Musical instrument:
The musical instruments such as Piano, violin, cello, drums, flute, guitar, double bass and a number of other music instruments material requires wood for making a perfect tune. e.g. Mahogany , maple, ash wood for guitars.
4. Sports Equipment
- Wooden Toys:
These are preferred to plastic towards the health conscious people which were supposed as a fashion before. Plastic is nothing but the combination of chemicals which is hazardous to children's health. Cricket, hockey, billiard, table tennis etc. Toys and sports equipment have long made use of wood for handles and main parts. e.g. Willow wood for cricket, tennis bat; Mulberry wood for hockey sticks.
5. Commercial Uses
- Furniture:
At present, the market for wooden furniture is very profitable. No one can deny the demand for wooden furniture as it is a sign of aristocracy since ancient time.
e.g. Teak wood is the best for making furniture. Some other woods from Mahogany , Shimul , Sundari, Jackfruit, Mango trees are used in south Asia for making different types of furniture.
- Ship building
Ships and rural fishing boats were made from wood. For constructing boats and ships wood is one of the most important construction material. Hardwood and softwood were used in the past for ship industry.
e.g. Teak, shal , mango, Arjun were frequently used in the past. Now Cypress ,redwood ,white, oak are water resistant and used for shipbuilding and boat building. Woods like kauri is used for making the frames of ships.
- Fuel
Wood is an age-old source of energy all over the world. Before the exploration of gas, fuel was the main source we can also define as only one source of energy that people used by burning as woods were available in the forest easily. Generally, sticks, pellets, sawdust, and charcoal are used as an energy source from wood. Usually, woods from cheap plants are used in this sector.
- Stationary
Some stationeries like paper pencil are made of wood. Wood pulp is used for making paper. Wood is used for making pencils too.
e.g. In the past Cyper papyrus trees were used to make paper.
CEMENT
Cement is a commonly used binding material in the construction. The cement is obtained by burning a mixture of calcarious (calcium) and argillaceous (clay) material at a very high temperature and then grinding the clinker so produced to a fine powder.
Types of Cement
In addition to ordinary portland cement there are many varieties of cement. Important varieties are
Briefly explained below:
- White Cement: The cement when made free from colouring oxides of iron, manganese and chromium results into white cement. In the manufacture of this cement, the oil fuel is used instead of coal for burning. White cement is used for the floor finishes, plastering, ornamental works etc. In swimming pools white cement is used to replace glazed tiles. It is used for fixing marbles and glazed tiles.
- Coloured Cement: The cements of desired colours are produced by intimately mixing pigments with ordinary cement. The chlorium oxide gives green colour. Cobalt produce blue colour. Iron oxide with different proportion produce brown, red or yellow colour. Addition of manganese dioxide gives black or brown coloured cement. These cements are used for giving finishing touches to floors, walls, window sills, roofs etc.
- Quick Setting Cement: Quick setting cement is produced by reducing the percentage of gypsum and adding a small amount of aluminium sulphate during the manufacture of cement. Finer grinding also adds to quick setting property. This cement starts setting within 5 minutes after adding water and becomes hard mass within 30 minutes. This cement is used to lay concrete under static or slowly running water.
- Rapid Hardening Cement: This cement can be produced by increasing lime content and burning at high temperature while manufacturing cement. Grinding to very fine is also necessary. Though the initial and final setting time of this cement is the same as that of portland cement, it gains strength in early days. This property helps in earlier removal of form works and speed in construction activity.
- Low Heat Cement: In mass concrete works like construction of dams, heat produced due to hydration of cement will not get dispersed easily. This may give rise to cracks. Hence in such constructions it is preferable to use low heat cement. This cement contains low percentage (5%) of tricalcium aluminate (C3A) and higher percentage (46%) of dicalcium silicate (C2S).
- Pozzolana Cement: Pozzolana is a volcanic power found in Italy. It can be processed from shales and certain types of clay also. In this cement pozzolana material is 10 to 30 per cent. It can resist action of sulphate. It releases less heat during setting. It imparts higher degree of water tightness. Its tensile strength is high but compressive strength is low. It is used for mass concrete works. It is also used in sewage line works.
- Expanding Cement: This cement expands as it sets. This property is achieved by adding expanding medium like sulpho aluminate and a stabilizing agent to ordinary cement. This is used for filling the cracks in concrete structures.
- High Alumina Cement: It is manufactured by calcining a mixture of lime and bauxite. It is more resistant to sulphate and acid attack. It develops almost full strength within 24 hours of adding water. It is used for under water works.
- Blast Furnace Cement: In the manufacture of pig iron, slag comes out as a waste product. By grinding clinkers of cement with about 60 to 65 per cent of slag, this cement is produced. The properties of this cement are more or less same as ordinary cement, but it is cheap, since it utilise waste product. This cement is durable but it gains the strength slowly and hence needs longer period of curing.
- Acid Resistant Cement: This cement is produced by adding acid resistant aggregated such as quartz, quartzite, sodium silicate or soluble glass. This cement has good resistance to action of acid and water. It is commonly used in the construction of chemical factories.
- Sulphate Resistant Cement: By keeping the percentage of tricalcium aluminate C3A below five per cent in ordinary cement this cement is produced. It is used in the construction of structures which are likely to be damaged by alkaline conditions. Examples of such structures are canals, culverts etc.
- Fly Ash Blended Cement: Fly ash is a byproduct in thermal stations. The particles of fly ash are very minute and they fly in the air, creating air pollution problems. Thermal power stations have to spend lot of money to arrest fly ash and dispose safely. It is found that one of the best way to dispose fly ash is to mix it with cement in controlled condition and derive some of the beneficiary effects on cement. Now-a-days cement factories produce the fly ash in their own thermal stations or borrow it from other thermal stations and further process it to make it suitable to blend with cement. 20 to 30% fly ash is used for blending.
- Fly ash blended cements have superior quality of resistance to weathering action. The ultimate strength gained is the same as that with ordinary portland cement. However strength gained in the initial stage is slow. Birla plus, Birla star, A.C.C. Suraksha are some of the brand mame of blended cement.
Uses of Cement
- Cement is used widely for the construction of various structures. Some of them are listed below:
- Cement slurry is used for filling cracks in concrete structures.
- Cement mortar is used for masonry work, plastering and pointing.
- Cement concrete is used for the construction of various structures like buildings, bridges.
- Water tanks, tunnels, docks, harhours etc.
- Cement is used to manufacture lamp posts, telephone posts, railway sleepers, piles etc.
- For manufacturing cement pipes, garden seats, dust bins, flower pots etc. cement is commonly used.
- It is useful for the construction of roads, footpaths, courts for various sports etc.
PROPETIES
(i) Chemical properties: Portland cement consists of the following chemical compounds:
(a) Tricalcium silicate 3 CaO.SiO2 (C3S) 40%
(b) Dicalcium silicate 2CaO.SiO2 (C2S) 30%
(c) Tricalcium aluminate 3CaO.Al2O3 (C3A) 11%
(d) Tetracalcium aluminate 4CaO.Al2O3.Fe2O3 (C3AF) 11%
There may be small quantities of impurifies present such as calcium oxide (CaO) and magnesium oxide (MgO). When water is added to cement, C3A is the first to react and cause initial set. It generates great amount of heat. C3S hydrates early and develops strength in the first 28 days. It also generates heat. C2S is the next to hydrate. It hydrates slowly and is responsible for increase in ultimate strength. C4AF is comparatively inactive compound.
(ii) Physical properties: The following physical properties should be checked before selecting a portland cement for the civil engineering works. IS 269–1967 specifies the method of testing and prescribes the limits:
(a) Fineness
(b) Setting time
(c) Soundness
(d) Crushing strength.
Fineness: It is measured in terms of percentage of weight retained after sieving the cement through 90 micron sieve or by surface area of cement in square centimetres per gramme of cement. According to IS code specification weight retained on the sieve should not be more than 10 per cent. In terms of specific surface should not be less than 2250 cm2/gm.
Setting time: A period of 30 minutes as minimum setting time for initial setting and a maximum period of 600 minutes as maximum setting time is specified by IS code, provided the tests are conducted as per the procedure prescribed by IS 269-1967.
Soundness: Once the concrete has hardened it is necessary to ensure that no volumetric changes takes place. The cement is said to be unsound, if it exhibits volumetric instability after hardening. IS code recommends test with Le Chatelier mould for testing this property. At the end of the test, the indicator of Le Chatelier mould should not expand by more than 10 mm.
Crushing strength: For this mortar cubes are made with standard sand and tested in compression testing machine as per the specification of IS code. The minimum strength specified is 16 N/mm2 after 3 days and 22 N/mm2 after 7 days of curing.
TESTS
Soundness Test: It is conducted by sieve analysis. 100 gms of cement is taken and sieved
through IS sieve No. 9 for fifteen minutes. Residue on the sieve is weighed. This should not exceed 10
per cent by weight of sample taken.
Setting Time: Initial setting time and final setting time are the two important physical properties of cement. Initial setting time is the time taken by the cement from adding of water to the starting of losing its plasticity. Final setting time is the time lapsed from adding of the water to complete loss of plasticity. Vicat apparatus is used for finding the setting times [Fig. 1.5]. Vicat apparatus consists of a movable rod to which any one of the three needles shown in figure can be attached. An indicator is attached to the movable rod. A vicat mould is associated with this apparatus which is in the form of split cylinder.
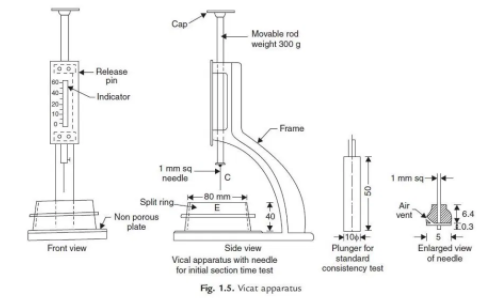
Before finding initial and final setting time it is necessary to determine water to be added to get standard consistency. For this 300 gms of cement is mixed with about 30% water and cement paste prepared is filled in the mould which rests on non porous plate. The plunger is attached to the movable rod of vicat apparatus and gently lowered to touch the paste in the mould. Then the plunger is allowed to move freely. If the penetration is 5 mm to 7 mm from the bottom of the mould, then cement is having standard consistency. If not, experiment is repeated with different proportion of water fill water required for standard consistency is found. Then the tests for initial and final setting times can be carried out as explained below:
Initial Setting Time: 300 gms of cement is thoroughly mixed with 0.85 times the water for standard consistency and vicat mould is completely filled and top surface is levelled. 1 mm square needle is fixed to the rod and gently placed over the paste. Then it is freely allowed to penetrate. In the beginning the needle penetrates the paste completely. As time lapses the paste start losing its plasticity and offers resistance to penetration. When needle can penetrate up to 5 to 7 mm above bottom of the paste experiment is stopped and time lapsed between the addition of water and end if the experiment is noted as initial setting time.
Final Setting Time. The square needle is replaced with annular collar. Experiment is continued by allowing this needle to freely move after gently touching the surface of the paste. Time lapsed between the addition of water and the mark of needle but not of annular ring is found on the paste. This time is noted as final setting time.
Soundness Test: This test is conducted to find free lime in cement, which is not desirable. Le Chatelier apparatus shown in Fig. 1.6 is used for conducting this test. It consists of a split brass mould of diameter 30 mm and height 30 mm. On either side of the split, there are two indicators, with pointed ends. The ends of indicators are 165 mm from the centre of the mould.
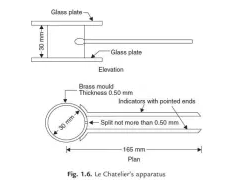
Properly oiled Le Chatelier mould is placed on a glass plate and is filled completely with a cement paste having 0.78 times the water required for standard consistency. It is then covered with another glass plate and a small weight is placed over it. Then the whole assembly is kept under water for 24 hours. The temperature of water should be between 24°C and 50°C. Note the distance between the indicator. Then place the mould again in the water and heat the assembly such that water reaches the boiling point in 30 minutes. Boil the water for one hour. The mould is removed from water and allowed to cool. The distance between the two pointers is measured. The difference between the two readings indicate the expansion of the cement due to the presence of unburnt lime. This value should not exceed 10 mm.
Crushing Strength Test: For this 200 gm of cement is mixed with 600 gm of standard sand confirming to IS 650–1966. After mixing thoroughly in dry condition for a minute distilled potable water (P/4)+ 3 percentage is added where P is the water required for the standard consistency. They are mixed with trowel for 3 to 4 minutes to get uniform mixture. The mix is placed in a cube mould of 70.6 mm size (Area 5000 mm2) kept on a steel plate and prodded with 25 mm standard steel rod 20 times within 8 seconds. Then the mould is placed on a standard vibrating table that vibrates at a speed of 12000 ± 400 vibration per minute. A hopper is secured at the top and the remaining mortar is filled. The mould is vibrated for two minutes and hopper removed. The top is finished with a knife or with a trowel and levelled. After 24 ± 1 hour mould is removed and cube is placed under clean water for curing. After specified period cubes are tested in compression testing machine, keeping the specimen on its level edges. Average of three cubes is reported as crushing strength. The compressive strength at the end of 3 days should not be less than 11.5 N/mm2 and that at the end of 7 days not less than 17.5 N/mm2.
LIME
It is an important binding material used in building construction. Lime has been used as the material of construction from ancient time. When it is mixed with sand it provides lime mortar and when mixed with sand and coarse aggregate, it forms lime concrete.
Types
The limes are classified as fat lime, hydraulic lime and poor lime:
1. Fat lime: It is composed of 95 percentage of calcium oxide. When water is added, it slakes vigorously and its volume increases to 2 to 2.5 times. It is white in colour. Its properties are:
(a) hardens slowly
(b) has high degree of plasticity
(c) sets slowly in the presence of air
(d) white in colour
(e) slakes vigorously
2. Hydraulic lime: It contains clay and ferrous oxide. Depending upon the percentage of clay present, the hydraulic lime is divided into the following three types:
(a) Feebly hydraulic lime (5 to 10% clay content)
(b) Moderately hydraulic lime (11 to 20% clay content)
(c) Eminently hydraulic lime (21 to 30% clay content)
The properties of hydraulic limes are:
• Sets under water
• Colour is not perfectly white
• Forms a thin paste with water and do not dissolve in water.
• Its binding property improves if its fine powder is mixed with sand and kept in the form of heap for a week, before using.
3. Poor lime: It contains more than 30% clay. Its colour is muddy. It has poor binding property. The mortar made with such lime is used for inferior works. IS 712-1973 classifies lime as class A, B, C, D and E.
Class A Lime: It is predominently hydraulic lime. It is normally supplied as hydrated lime and is commonly used for structural works.
Class B Lime: It contains both hydraulic lime and fat lime. It is supplied as hydrated lime or as quick lime. It is used for making mortar for masonry works.
Class C Lime: It is predominently fat lime, supplied both as quick lime and fat lime. It is used for finishing coat in plastering and for white washing.
Class D Lime: This lime contains large quantity of magnesium oxide and is similar to fat lime. This is also commonly used for white washing and for finishing coat in plastering.
Class E Lime: It is an impure lime stone, known as kankar. It is available in modular and block form. It is supplied as hydrated lime. It is commonly used for masonry mortar.
Tests on Lime stones
The following practical tests are made on lime stones to determine their suitability:
(i) Physical tests
(ii) Heat test
(iii) Chemical test
(iv) Ball test.
Physical Test: Pure limestone is white in colour. Hydraulic lime stones are bluish grey, brown or are having dark colours. The hydraulic lime gives out earthy smell. They are having clayey taste. The presence of lumps give indication of quick lime and un burnt lime stones.
Heat Test: A piece of dry stone weighing W1 is heated in an open fire for few hours. If weight of sample after cooling is W2, the loss of weight is W2 – W1. The loss of weight indicates the amount of carbon dioxide. From this the amount of calcium carbonate in limestone can be worked out.
Chemical Test: A teaspoon full of lime is placed in a test tube and dilute hydrochloric acid is poured in it. The content is stirred and the test tube is kept in the stand for 24 hours. Vigourous effervescence and less residue indicates pure limestone. If effervescence is less and residue is more it indicates impure limestone. If thick gel is formed and after test tube is held upside down it is possible to identify class of lime as indicated below:
• Class A lime, if gel do not flow.
• Class B lime, if gel tends to flow down.
• Class C lime, if there is no gel formation.
(iv) Ball Test: This test is conducted to identify whether the lime belongs to class C or to class B. By adding sufficient water about 40 mm size lime balls are made and they are left undisturbed for six hours. Then the balls are placed in a basin of water. If within minutes slow expansion and slow disintegration starts it indicates class C lime. If there is little or no expansion, but only cracks appear it belongs to class B lime.
Uses of Lime
The following are the uses of lime in civil works:
(i) For white washing.
(ii) For making mortar for masonry works and plastering.
(iii) To produce lime sand bricks.
(iv) For soil stabilization.
(v) As a refractory material for lining open hearth furnaces.
(vi) For making cement.
- Concrete is an artificial conglomerate stone made essentially of Portland cement, water, and aggregates.
- Portland cement is produced by mixing ground limestone, clay or shale, sand and iron ore.
- This mixture is heated in a rotary kiln to temperatures as high as 1 600 degrees Celsius high as 1,600 degrees Celsius. The heating process causes the materials to break down and recombine into new compounds that can react with water in a crystallization process called hydration.
- The raw ingredients of Portland cement are iron ore, lime, alumina and silica. These are ground up and fired in a kiln to produce a clinker. After cooling, the clinker is very finery ground.
- When first mixed the water and cement constitute a paste which surrounds all the individual pieces of aggregate to make a plastic mixture.
- A chemical reaction called hydration takes place between the water and cement, and concrete normally changes from a plastic to a solid state in about 2 hours.
- Concrete continues to gain strength as it cures. Heat of hydration - is the heat given off during the chemical reaction as the cement hydrates.
Workability that property of freshly mixed concrete that determines its working characteristics, i.e. the ease with which it can be mixed, placed, compacted and finished.
Factors effecting workability:
- Method and duration of transportation
- Quantity and characteristics of cementing materials
- Concrete consistency (slump)
- Aggregate grading, shape & surface texture
- % entrained air
- Water content
- Concrete & ambient air temperature Admixtures
Nominal Proportion Of Concrete Preparation Of Concrete, Compaction and Curing
Nominal Proportion Of Concrete Preparation Of Concrete
Concrete is a commonly used construction material, which is the mixture of cement, sand, aggregate, and admixtures blended with water. Concrete gets hardened with time and gains the strength, and for the best results in a construction of your dream home, mixing of concrete is said to be the most important process. All the ingredients are to be mixed in proper proportion because the properties of concrete like workability, strength, surface finish, and durability of concrete etc. are ensured by the right and proportionate blending.
In the nominal mix concrete, all the ingredients and their proportions are prescribed in the standard specifications. These proportions are specified in the ratio of cement to aggregates for certain strength achievement.
The mix proportions like 1:1.5:3, 1:2:4, 1:3:6 etc. are adopted in nominal mix of concrete without any scientific base, only on the basis on past empirical studies. Thus, it is adopted for ordinary concrete or you can say, the nominal mix is preferred for simpler, relatively unimportant and small concrete works.
As per the ‘Indian Standard- IS 456:2000’, nominal mix concrete may be used for concrete of M20 grade or lower grade such as M5, M7.5, M10, M15.
M 20 is identified as the concrete grade in which, M denotes the Mix and 20 denotes the compressive strength of concrete cube after 28 days of curing in N/mm2. There are various grades of concrete that can be used like M10, M15, M20, M25, M30, etc.
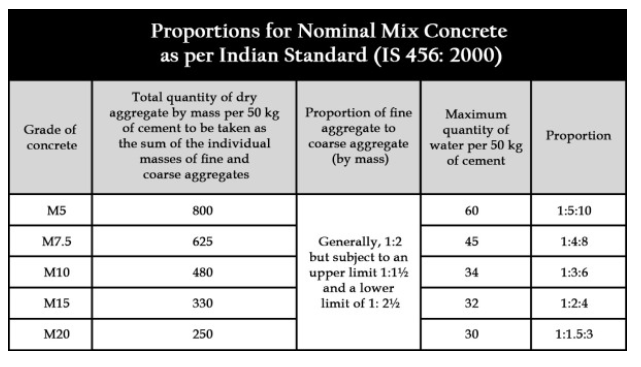
Compaction and Curing
Compaction of concrete and curing process of concrete
1) Compaction of concrete
- Concrete should be thoroughly compacted and fully work around the reinforcement and into the corners of the formworks
- Concrete shall be compacted using mechanical vibrators
- Whenever vibration has been applied externally the design of formwork and the deposition of vibrators should receive special consideration to ensure efficient compaction and to avoid sir face blemishes
2) Curing process of concrete
- Curing of concrete is defined as the process of maintaining the moisture and temperature condition of concrete for hydration reaction to the normally so that the concrete develops hardened and properties over time
- The main components which need to be taken care of your heat and time during curing process
- Curing is the process of preventing the loss of moisture from the concrete which maintaining a satisfactory temperature effect
- If the cement has high rate of strain development and if the concrete contains granulated blast furnace and flue Ash then,
- The curing should also prevent the development of high temperature gradients within the concrete
a) Moist curing
- Surface of the concrete shall be kept continuously in Dam or wet condition by covering with the layers of materials like checking Canvas etc.
- It should be kept continuously wet for at least 7 days from the date of placing concrete.
- In case of ordinary Portland cement at least 10 days. Where mineral admixture or blended cement are used.
- The period of curing shall not be less than 10 days for concrete exposed to the dry and hot weather condition.
- In case of concrete where mineral admixture or blended cement are used it is recommended that above minimum period may be extended 14 days.
b) Membrane curing
- Approved curing compounds may be used in place of moist curing with the permission of engineer in charge.
- Search compound shall be applied to all exposed surfaces of the concrete as soon as possible after the concrete has set.
- Impermeable membrane such as polyethylene sheeting covering closely the concrete surface may also be used to provide effective barriers against evaporation.
- For the concrete containing Portland pozzolana cement, Portland slag cement or mineral admixture period of curing may be increased.
Elements of Building Construction
The following are the basic elements of a building:
1. Foundation
2. Plinth
3. Walls and columns
4. Sills, lintels and chejjas
5. Doors and windows
6. Floors
7. Roofs
8. Steps, stairs and lifts
9. Finishing work
10. Building services.
Foundation
The lowest part of a structure which transmits the weight of the structure together with live loads, seismic and wind pressure to the ground surface on which the structure rests, ensuring its safe bearing capacity, is called foundation. To increase the stability of the structure, foundations are generally placed below the ground level.
The selection of the foundation type for a particular site depends on the following considerations:
1. Nature of subsoil.
2. Nature and extent of difficulties
3. Availability of expertise and equipment
Depending upon their nature and depth, foundations have been categorized as follows
- Open foundations or shallow foundations
- Deep foundations
Superstructure
Superstructure is the portion of a building parts which is constructed above the ground level and it serves the purposes of structure intended use . Such as column, beam, floor, wall and roof etc .
Materials used- timber, steel and concrete.
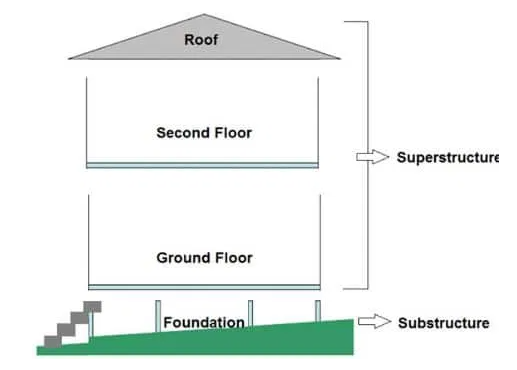
Functions of Foundation
- Reduction of load intensity
Foundations distribute the loads of the super-structure, to a larger area so that the intensity of the load at its base (i.e. total load divided by the total area) does not exceed the safe bearing capacity of the sub-soil. In the case of deep foundations, it transmits the super-imposed loads to the sub-soil both through side friction as well as through end bearing.
2. Even distribution of load
Foundations distribute the non uniform load of the super-structure evenly to be sub-soil. For example, two columns carrying unequal loads can have a combined footing which may transmit the load to sub-soil evenly with uniform soil pressure. Due lo this, unequal or differential settlements are minimised.
3. Provision of level surface
Foundations provide levelled and hard surface over which the super-structure can be built.
4. Lateral stability
It anchors the super-structure to the ground, thus imparting lateral stability to the super-structure. The stability of the building, against sliding and overturning, due to horizontal forces (such as wind, earthquake etc.) is increased due to foundations.
5. Safety against undermining
It provides the structural safety against undermining or scouring due to burrowing animals and flood water.
6. Protection against soil movements
Special foundation measures prevents or minimises the distress (or cracks) in the super-structure, due to expansion or contraction of the sub-soil because of moisture movement .
Types of Shallow and Deep Foundations
Depending upon their nature and depth, foundations have been categorized as follows
(i) Open foundations or shallow foundations
(ii) Deep foundations
SHALLOW FOUNDATIONS
This is the most common type of foundation and can be laid using open excavation by allowing natural slopes on both sides. This type of foundation is practicable for a depth up to 5m and is normally convenient above the water table. The base of the structure is enlarged or spread to provide individual support. Since spread foundations are constructed in open excavations, therefore they are termed as open foundations.
The various types of spread footings are:
1.Wall footings
2.Isolated footings
3.Combined footings
4.Inverted arch footings
5.Continuous footings
6.Cantilever footing
7.Grillage footing
1. Wall Footings:
These footings can either be simple or stepped. The base course of these footings can be concrete or of entirely one material. They have only one projection beyond the width of the wall on either side. The width of the concrete base should be at least equal to twice the width of the wall. The depth of the concrete bed is at least equal to the projection. Generally the projection provided in the footing is 15cm, on either side and the concrete mix comprises of cement, sand and aggregate in proportion of 1:3:6 or 1:4:8.
2. Isolated or Column Footings:
They are used to support individual columns. In case of heavy loaded columns, steel reinforcements is provided. Generally, 15cm offset is provided on all sides of concrete bed. The footing of concrete columns may be slab, stepped or sloped type.
3. Combined Footings:
A combined footing supports two or more columns in a row. The combined footing can be rectangular in shape if both the columns carry equal loads or can be trapezoidal if both the loads are unequal. Generally they are constructed of reinforced concrete. The location of the center of the gravity of the column loads and centroid of the footing should coincide.
4. Inverted arch footing:
This type of footing is used on soft soils to reduce the depth of the foundation. Loads above an opening are transmitted from supporting walls through inverted arches to the soil. In this type of footings the end columns must be stable enough to resist the outward pressure caused by the arch action.
5. Continuous footings:
In this type of footing a single continuous R.C. Slab is provided as foundation of two or three or more columns in a row. This type of footing is suitable at locations liable to earthquake activities. This also prevents differential settlements in structures.
6. Strap or cantilever footings:
Strap footing consists of two or more individual footings connected by a beam called strap. This type of footing is used where the distance between the columns is so great that the trapezoidal footing becomes quite narrow with bending moments.
7. Grillage footings:
This type of footings is used to transmit heavy loads from steel columns to the soils having low bearing power. This type of arrangements prevents deep excavations and provides necessary area at base to reduce the intensity of the pressure.
DEEP FOUNDATIONST
Hese foundations carry loads from a structure through weak incompressible soils or fills on to the stronger and less compressible soils or rocks at depth. These foundations are in general used as basements, buoyancy rafts, caissons, cylinders, shaft and piles
- Basements
They are constructed in place in an open excavations. They are hollow substructures designed to provide working space below ground level.
2. Buoyancy Rafts
They are hollow substructures designed to provide a buoyant substructure beneath which reduce net loadings on the soil to the desired low density.
3.Caissons
They are hollow s8ubstructures designed to be constructed on or near the surface and then sunk as single units to their required level.
4.Cylinders
They are single small cell caissons.
5.Shaft Foundations
They are constructed within deep excavation supported by lining constructed in place and subsequently filled with concrete.
6.Pile Foundations
The pile foundation is a construction supported on piles. A pile is an element of construction composed of timber, concrete or steel or a combination of them. The piles may be placed separately or they may be placed in form of a cluster throughout the structure.
Plinth
A plinth is a base or platform that supports a plinth, column, or structure. Structurally, the plinth distributes weight and pressure down evenly across a column across a wider space.
The height of the plinth is between 300 – 450 mm from the ground level. It is recommended that a minimum baseboard height of 150 mm be adopted from a natural level.
The minimum depth of the plinth beam is 20 cm, while its width must match the width of the final stroke of the foundation.
The plinth beam is a reinforced concrete beam built between the wall and its foundation. The plinth beam is provided to prevent the extension or cracking of the foundation cracks in the wall above when the foundation suffers from laying.
Walls
Wall is a structure defining an exact area and providing safety & shelter. There are various types of walls used in the construction of buildings given below.
- Load Bearing Walls
- Precast Concrete Wall
- Retaining Wall
- Masonry Wall
- Pre Panelized Load Bearing Metal Stud Walls
- Engineering Brick Wall
- Stone Wall
- Non-Load Bearing Wall
- Hollow Concrete Block
- Facade Bricks
- Hollow Bricks
- Brick Walls
- Cavity Walls
- Shear Walls
- Partition Walls
- Panel Walls
- Veneered Walls
- Faced Walls
1. Load Bearing Walls
Load bearing wall is a structural element. It carries the weight of a house from the roof and upper floors, all the way to the foundation. It supports structural members like beams (sturdy pieces of wood or metal), slab and walls on above floors above. A wall directly above the beam is called load bearing wall. It is designed to carry the vertical load. In another way, if a wall doesn’t have any walls, posts or other supports directly above it, it is more likely to be a load-bearing wall. Load bearing walls also carry their own weight. This wall is typically over one another on each floor. Load bearing walls can be used as interior or exterior wall. This kind of wall will often be perpendicular to floor joists or ridge. Concrete is an ideal material to support these loads. The beams go directly into the concrete foundation. Load bearing walls inside the house tend to run the same direction as the ridge.
2. Non-Load Bearing Walls
A wall which doesn’t help the structure to stand up and holds up only itself is known as a non-load bearing wall. It doesn’t support floor roof loads above. It is a framed structure. Most of the time, They are interior walls whose purpose is to divide the structure into rooms. They are built lighter. One can remove any non-load bearing walls without endangering the safety of the building. Non-load bearing walls can be identified by the joists and rafters. They are not responsible for gravitational support for the property. It is cost effective. This wall is referred to as “curtain wall”.
3. Cavity Walls
The cavity wall consists of two separate wythes. The wythes are made of masonry. Those two walls are known as internal leaf and external leaf. This wall is also known as a hollow wall. They reduce their weights on the foundation. They act as good as sound insulation. Cavity wall gives better thermal insulation than any other solid wall because space is full of air and reduces heat transmission. They have a heat flow rate that is 50 percent that of a solid wall. It is economically cheaper than other solid walls. It is fire resistant. Cavity wall helps to keep out from noise.
4. Hear Walls
It is a framed wall. It is designed to resist lateral forces. This lateral force comes from exterior walls, floor, and roofs to ground foundation. The usage of the shear wall is important, especially in large and high-rise buildings. It is typically constructed from materials like concrete or masonry. It has an excellent structural system to resist earthquakes. It provides stiffness in the direction. The construction and implementation are easy in shear walls. It is located symmetrically to reduce the ill effects of a twist. The shear wall doesn’t exhibit any stability problem.
5. Partition Walls
It is used in separating spaces from buildings. It can be solid, constructed from brick or stone. It is a framed construction. The partition wall is secured to the floor, ceiling, and walls. It is enough strong to carry its own load. It resists impact. It is stable and strong to support wall fixtures. The partition wall works as a sound barrier and it is fire resistant.
6. Panel Walls
It is a non-bearing wall between columns or pillars that are supported. The panel is installed with both nails and adhesive. The paneling design choices include rustic, boards, frame. Paneling can be from hardwoods or inexpensive pine. One should paint the space before installing panel walls.
7. Veneered Walls
With a veneered wall, we are holding up the material. It can be made of brick or stone. The most famous veneered wall is made of brick. The wall is only one wythe thick. It became the norm when building codes began to require insulation in the interior walls. It is light weighted. The construction takes less time to complete in veneered walls.
8. Faced Walls
It is a wall that masonry facing and backing are so bonded as to exert common action under load. It creates a streamlined look. The faced wall is easy to install.
Lintels
A lintel is defined as a horizontal structural member which is placed across the opening. Hence, the structure remains in the position by the resistance from the support.
Classification of lintel
Lintels are classified into the following types, according to the materials of their construction:
- Timber lintels
- Stone lintels
- Brick lintels
- Reinforced Brick lintels
- Steel lintels
- Reinforced cement concrete lintels
Timber lintels
- Easily available in hilly area.
- Relatively costly, structurally weak and vulnerable to fire.
- Easily decay, if not properly taken care.
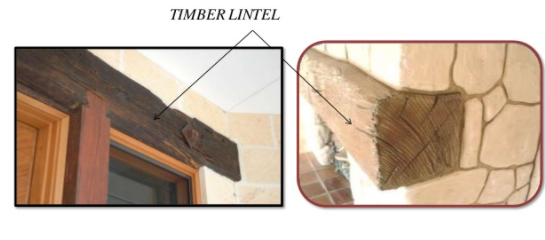
Stone lintels
- Used , where stones are easily available.
- Consists of a simple stone slab of greater thickness.
- Due to high cost and its inability to with stand the transverse stress load it is not commonly used.
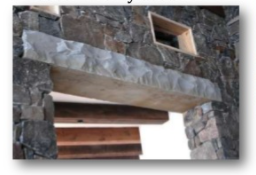
Brick lintels
- The brick are hard, well burnt , first class bricks .
- Suitable for small span.
- The bricks having frogs are more suitable.
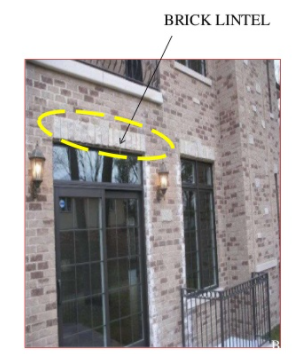
Reinforced Brick lintels
- For large spans and heavy loads .
- They are reinforced with mild steel bars.
- Very common due to durability, strength and fire resisting properties.
- Joints are filled with cement concrete.
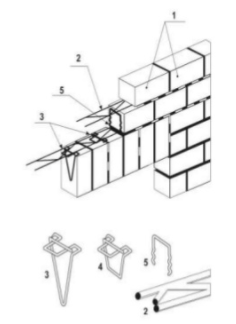
Steel lintels
- Provided at large opening and where the super-imposed loads are heavy.
- It consists of rolled steel joists .
- Either used singly or in combination of two or three units.
- Joint with Bolts.
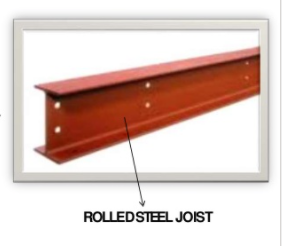
Reinforced Cement Concrete Lintel
- Common in used
- They may be pre-cast
- For smaller span, the pre- cast concrete lintels are used
- Depth of lintel depend on span
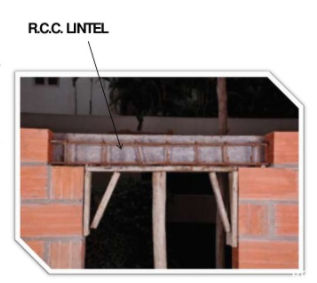
Beams
Horizontal member of a structure. It Carries transverse loads
It is classified into-
- SIMPLY SUPPORTED BEAM
- OVERHANGING BEAM
- CANTILEVER BEAM
- FIXED BEAM
- PROPPED
- CONTINUOUS BEAM
Columns
Column is a vertical structural member. It transmits the load from ceiling/roof slab and beam, including its self-weight to the foundation.
This is classified into three types-
- Long Column/ Slender
- Short Column
- Intermediate Column
Slabs
- It is a flat horizontal surface
- It is supported by beam and column
- It transfers load to the beam
This is classified into-
- GRANAIT
- MARBEL
- CONCRETE
- ONE WAY
- TWO WAY
- FLAT
- BEAM
4. RIBBED WOODEN
Roofs
It may be defined as the uppermost part of the building, provided as a structural covering, to protect the building from weather. Structurally, a roof is constructed in the same way as an upper floor, though the shape of its upper surface may be different. Roof consists of structural elements which support roof is roof covering. The roof coverings may be A.C. Sheets, G.I. Sheets, wooden shingles, tiles, slab itself.
TYPES OF ROOF
- Pitched or Sloping Roofs
- Flat Roofs or terraced Roofs
- Curved Roof
Staircases
The means of communication between various floors is offered by various structures such as stairs, lifts, ramps, ladders, escalators.
STAIR: A stair is a series of steps arranged in a manner as to connect different floors of a building. Stairs are designed to provide an easy and quick access to different floors.
- A staircase is an enclosure which contains the complete stairway.
- In a residential house stairs may be provided near the entrance.
- In a public building, stairs must be from main entrance and located centrally.
STAIRCASE: Room of a building where stair is located.
STAIRWAY: Space occupied by the stair.
Requirement Of Good Staircase
Stairs should be so located that it is easily accessible from the different rooms of a building.
It should have adequate light and proper ventilation.
It should have sufficient stair width to accommodate no. Of persons in peak hour/emergency.
Generally for interior stairs, clear width may be
- At least 50cm in one/two family dwellings
- At least 90cm in hotels, motels, apartment and industrial building
- At least 1.1m for other types like hospitals, temples etc.
No. Of steps in a flight should be restricted to a maximum of 12, minimum of 3.
Ample head room should be provided for tall people to give feeling of spaciousness. It should be minimum of 2.15m.
Risers and treads sizes should be provided from common point view.
TYPES OF STAIRS
- Straight stair
- Turning stairs
- Circular stair
- Spiral stairs
- Curved stair
- Geometric stair
- Bifurcated stair
Classification Of Stairs Based On Materials Of Construction
- Wooden
- Stone
- Brick
- Metals/steel
- Plane concrete
- RCC
Floors
A floor is the bottom surface of a room or vehicle. Flooring is the general term for a permanent covering of a floor, or for the work of installing such a floor covering. A lot of variety exists in flooring and there are different types of floors due to the fact that it is the first thing that catches your eye when you walk into a house, as it spans across the length and breadth of the house. It is also the surface that goes through the most wear and tear, and that's why choosing the right material is of utmost importance.
Types of Floors
1. MUD FLOOR:
Earthen Flooring also commonly known as Adobe flooring is made up of dirt, raw earth or other unworked ground materials. In modern times, it is usually constructed with mixture of sand, clay and finely chopped straw.
Mud flooring is commonly constructed in villages where by using stabilizers the properties of the soil are enhanced by manipulating its composition by adding suitable stabilizers. The tensile and shear strength of the soil is increased and shrinkage is reduced.
2. BRICK FLOOR:
Brick flooring is one of the types of floors whose topping is of brick. These are easy to construct and repair but the surface resulting from these is not smooth and is rough, hence, easily absorbs and retains moisture which may cause dampness in the building.
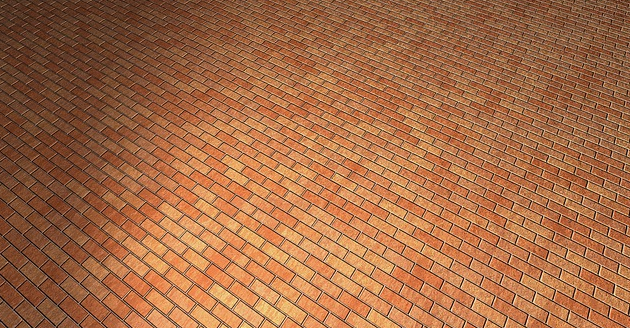
3. TILE FLOOR:
The floor whose topping is of tiles is called tile floor. The tiles used may be of any desired quality, color, shape or thickness.
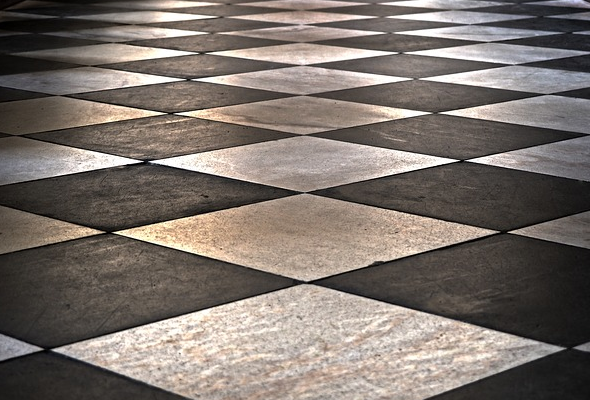
4. FLAGSTONE FLOOR:
The floors whose topping consists of stone slabs is called flagstone floor. The stone slabs used here may not be of the same size but should not be more than 75 cm length and not less than 35 cm in width and 3.8 cm in thickness.
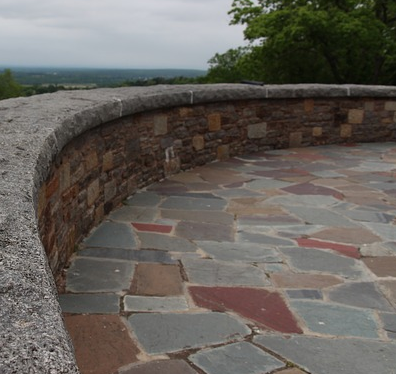
5. CEMENT CONCRETE FLOOR:
The types of floors whose topping consists of cement concrete is called cement concrete floor or conglomerate floor. These floors consists of 2.5 cm to 5cm thick concrete layer laid over 10 cm thick base concrete and 10 cm thick clean sand over ground whose compaction and consolidation is done. These floors are commonly used these days.
6.TERRAZZO FLOOR:
Terrazzo is a composite material, poured in place or precast, which is used for floor and wall treatments. It consists of chips of marble, quartz, granite, glass, or other suitable material, poured with a cementations binder (for chemical binding), polymeric (for physical binding), or a combination of both.

Doors
A door is a movable barrier provided in the opening of a wall, to provide access to various spaces of a building. A door is a frame work of wood, steel etc. secured in the wall opening for the purpose of providing access to the users of the building.
Types of Doors
- Type of doors based on material
- Types of doors based on placing of components
- Types of doors based on working functional
Type of doors based on material
WOODEN DOOR
- Wooden doors are classic choice for many Indians.
- This door material does not go out of fashion even if by passing long generations.
- They are like first preference of home owners without any hesitation.
- There are certain reasons due to which wooden doors are quite famous.
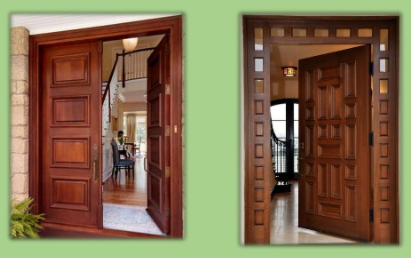
GLASS DOORS
- Glass doors makes an excellent choice for business houses as well as home owners.
- For the doors open towards outwards will provide great natural view .
- Glass doors provide great aesthetic look to business houses , hospitals.
- Easy to clean with liquid detergent available in market.
Glass doors are not damaged by any insects , termites , or rain or sun.
STEEL DOORS
- Steel doors are mostly preferred outside or main doors of the house. They are not preferred for interior door of the house.
- Even though steel doors are used for institutional purposes ,but it can be used for residential purposes.
- Steel doors are mainly used for garages, Storage rooms and for commercial and institutional buildings.
- But still many home owners use it for residential homes.
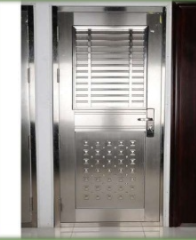
PVC DOORS
- PVC doors are appreciated for their benefits as an affordable and durable material.
- Vinyl doors have superior durability and not damaged by termites.
- They are self extinguishing making the house fire resistant.
They are very good insulators.
FIBER GLASS DOORS
- Wooden doors require a lot of maintenance. • If not maintained properly they can wrap, rot or corroded.
- But there are other materials available which door is more better. Fiber glass doors is one of them.
- They have a very good range of designs .
- Fiber glass doors are fairly modern providing great benefits.
- Fiber glass doors are very durable as they are moisture resistant, whether resistant.
- They provide good security as they are heavy in nature.
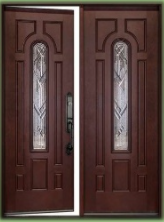
ALUMINIUM DOORS
- Aluminium doors are widely used in commercial building.
- But now people are also using it in residential buildings for modernizing purpose.
- They are very durable and have high strength .
- Aluminium resist rust , therefore they are good for coastal areas.
- They are having high cost.
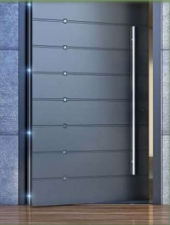
Types of Doors based on Placing of Components:
BATTENED AND LEDGED DOORS
- These doors are wooden or timber doors in which battens are vertical wood slabs joined together horizontally with the help of wooden ledges.
- To make more durable doors wooden strips are joined diagonally which are called braces.
- For simple battened and ledged doors framework is provided through 2 vertical slabs.
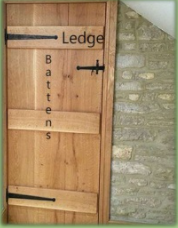
BATTENED, LEDGED AND BRACED DOORS
To make more durable doors wooden strips are joined diagonally which are called braces.
BATTENED, LEDGED AND FRAMED DOORS
- For simple battened and ledged doors framework is provided through 2 vertical slabs.
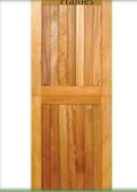
FRAMED AND PANELLED DOORS
- These doors look very elegant and are most preferred Indian doors. They are widely used.
- In this doors frame is prepared in which the timbers are grooved along with inner edges of frame and the jointed together.
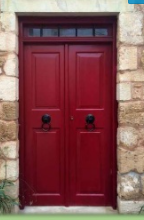
GLAZED DOORS
- Glazed doors are generally transparent.
- They are mostly preferred in Institutional buildings.

FLUSHED DOORS
- Flushed doors have two parts.
- Inner part is made with either hard strips of timber or hollow cardboard materials.
Then outer side is glued with plywood sheet or veneer finish under high pressure.
Types of doors based on working functions:
REVOLVING DOORS
- Revolving doors are one of the fascinating doors.
- They are mainly used in institutional buildings like hospitals, hotels, museums, offices.
- Revolving doors revolves in 360 degree angle.
- Only limited people can enter at a single time.
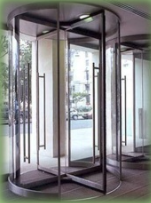
SLIDING DOOR
- Sliding door is one of the most essential requirement of modern buildings now a days.
- Due to lack of space and easy functionality they are most preferred.
- Also for natural view glass sliding doors are mostly preferred.
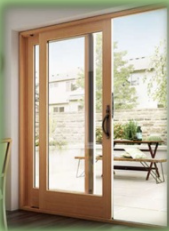
SWING DOORS
- Swing doors swings in 180 degree angle.
- Swing door is the style which is mostly used in Indian homes.
- They are the oldest form of doors.
- Due to it’s look, strength and security purpose it is used mostly.
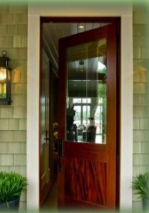
COLLAPSIBLE STEEL DOOR
- They are mainly used for outside door of home . Then can collapse horizontally saving space.
- They are very strong.
- Very long lasting
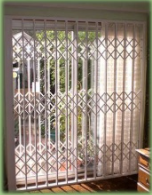
SHUTTER DOORS
These doors are mainly used for garage purposes. But many people are using for security purpose on front doors.
Windows
A window may be defined as an opening made in the wall for the purpose of providing day light, vision and ventilation. Windows are also made of frame work of wood, steel, aluminium etc., provided with shutters.
TYPES OF WINDOWS
Depending upon the manner of fixing, materials used for construction, nature of the operational movements of shutters , etc.,
The common varieties of windows used in the building can be grouped as follows:
1. Casement windows
2. Sliding windows
3. Metal windows
4. Corner windows
5. Gable windows bay windows
6. Lantern or lantern lights
7. Skylights
CASEMENT WINDOWS:
These are the windows, the shutters of which open like doors. The construction of a casement window is similar to the door construction.
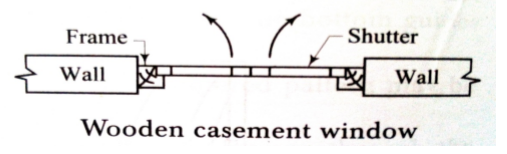
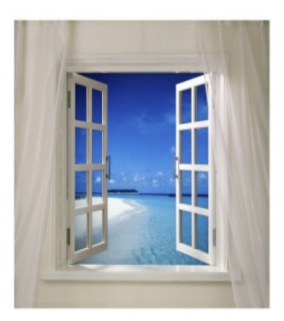
SLIDING WINDOWS:
These windows are similar to the sliding doors and the shutters moves on the roller bearings, either horizontally or vertically. Such windows are provided in trains, buses, bank counter, shops etc.
METAL WINDOWS:
These are now a days widely used, especially for public building. The metal used in construction may be mild steel, bronze, or other alloys. The metal frame may be fixed direct to the wall or it may be fixed on a wooden frame.
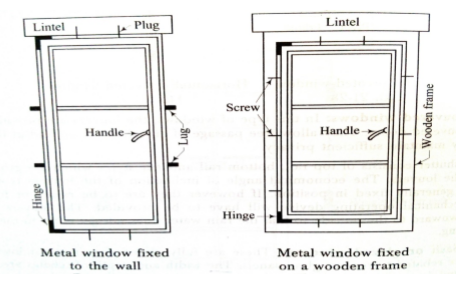
CORNER WINDOWS:
These windows are provided at the corner of a room .They are placed at the corner of the room and thus they have two faces in two perpendicular direction. Due to such situation, there is entry of light and air from two direction and in many cases , the elevation of building is also improved.
GABLE WINDOWS:
These are the windows which are provided in the gable ends of a roof.
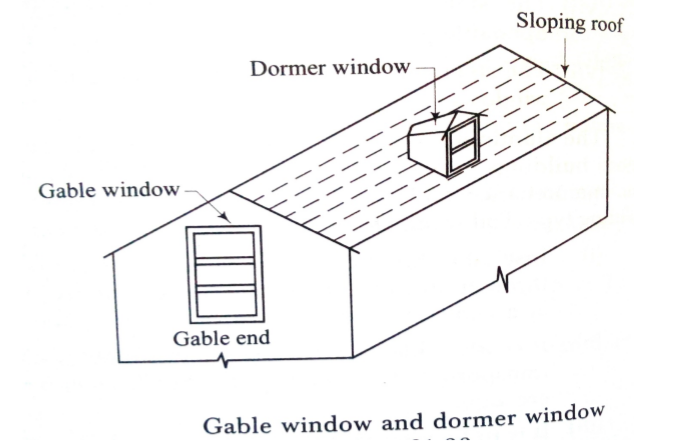
BAY WINDOWS:
These windows project outside the external wall of a room. They maybe square , splayed, circular, polygonal or of any shape. The projection of bay windows may start from floor level or sill level. These windows admit more lights, increase opening area , provide ventilation and improve the appearance of building.
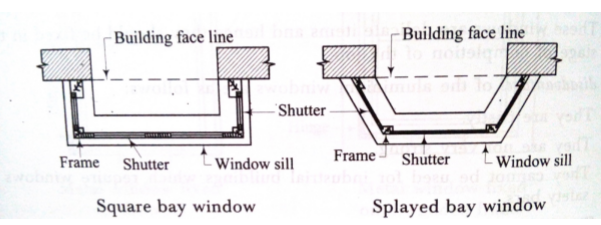
LANTERNS:
These are the windows which are fixed on flat roofs to provide light to the inner portion of building where light coming from external windows are insufficient. They maybe square or rectangular or curved.
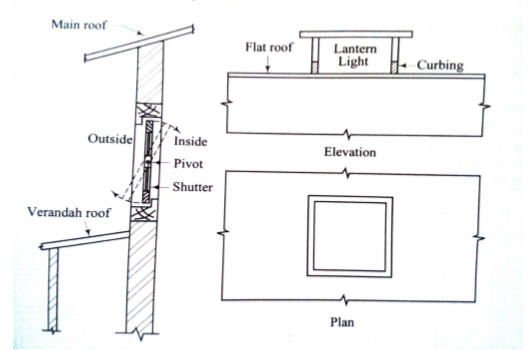
SKYLIGHTS:
These are the windows which are provided on the sloping surface of a pitched roof. The common rafter are suitably trimmed and the skylight is erected on a curb frame. As skylight are mainly meant for light, they are usually provided with the fixed glass panel.
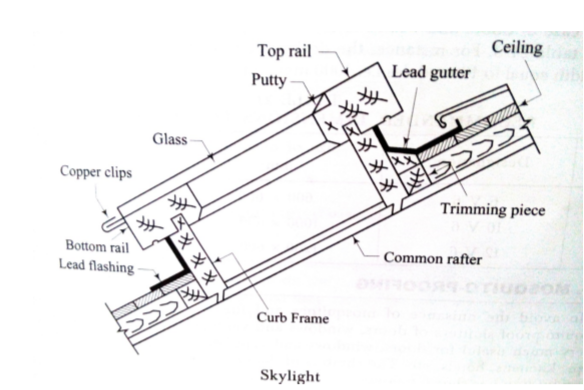
Reference Books
- A Text Book of Building Materials, by C.J. Kulkarrni
- Building Materials, by P. C. Varghese
- Building Construction, by P. C. Varghese