Unit 03
Lubricants and Lubrication
3.1 Introduction:
Lubricants are the fluid, solid or plastic substance that is helpful in the control of friction by the introduction of friction-reducing film between moving surfaces in contact. There are many different forms of the substance which is helpful in lubrications. The most common substances that are used is oil and grease. Grease is composed of oil and a thickening agent to obtain its consistency, while the oil helpful in lubrication. Oil can be a synthetic vegetable or mineral as well as a combination of these.
The application determines which oil, commonly referred to as the base oil and should be used. In extreme conditions, synthetic oils can be beneficial. Where the environment is of concern, vegetable base oils may be utilized. Lubricants containing oil have additives that enhance, add or suppress properties within the base oil. The amount of additives depends on the type of oil and the application for which it will be used. For instance, engine oil might have a dispersant added. A dispersant keeps insoluble matter conglomerated together to be removed by the filter upon circulation. In environments that undergo extremes in temperature, from cold to hot, a viscosity index (VI) improver may be added. These additives are long organic molecules that stay bunched together in cold conditions and unravel in hotter environments. This process changes the oil’s viscosity and allows it to flow better in cold conditions while still maintaining its high-temperature properties. The only problem with additives is that they can be depleted, and in order to restore them back to sufficient levels, generally the oil volume must be replaced. The roles of lubricant are -
- Reduce friction
- Prevent wear
- Protect the equipment from corrosion
- Control temperature (dissipate heat)
- Control contamination (carry contaminants to a filter or sump)
- Transmit power (hydraulics)
- Provide a fluid seal
3.2 Mechanism of lubrication:
(i) Fluid Film or Hydrodynamic Lubrication:
The shaft rotating in a bearing is supported by a layer or wedge of oil so that the shaft is not in contact with the bearing material. It is carried out with the help of liquid lubricants. In this mechanism, two moving and sliding surfaces are separated by thick film of lubricant fluid of about 1000A°, applied to prevent direct surface to surface contact and consequently reduce wearing and tearing of metals. Therefore it is known as thick film or fluid film lubrication or hydrodynamic lubrication. In this case fluid is formed by mixing of hydrocarbon oils and anti-oxidants with long chain polymer so as to maintain viscosity. Fluid film lubrication is useful in delicate and light machines like watches, clocks, guns, scientific equipments.
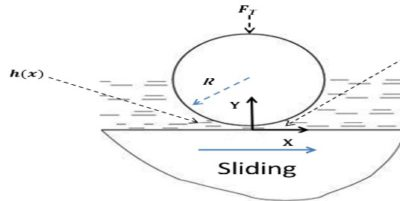
Lubrication film between the two contact surfaces is thick enough and two contact surfaces are separated completely by viscous oil film. At this time, frictional force of two contact surfaces are determined by viscous resistance of lubricant and it can take a very small value. Under this condition, when shaft also rotates due to the viscosity of the lubricant oil and generates oil pressure at the load area. This phenomenon is called wedge effect. The oil pressure P generated within lubricating oil film is affected by change of temperature and viscosity of lubricating oil, surface roughness, clearance and rotational speed of the shaft.
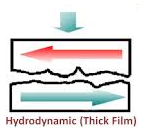
(ii) Thin Film or Boundary Lubrication:
It is carried out with grease and graphite & molybdenum disulphide lubricants. Boundary lubrication is a condition in which the lubricant film becomes too thin to provide total separation. In this type of lubrication a thin film of lubricant is adsorbed on the surface by weak Vander Waals forces. Thin film lubrication is operating at relatively low speed and high pressure. Lubricating oil film between the two contact surfaces is extremely thin and no viscous hydrodynamic oil film exists between the two contact areas, only film of absorbed oil molecules exists.
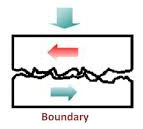
Absorptive oil film is arranged oil molecules that are adhered onto the solid surfaces and its shear resistance is greater than hydrodynamic oil film. Frictional force in this area is greater compare to hydrodynamic lubrication. In the frictional contact points, oil film is frequently broken. The lubrication condition that generates a frictional condition such as this is called boundary lubrication; in order to decrease the friction under this condition selection of self-lubricating bearing may be desirable.
3.3 Classification of lubricants:
Lubricants are classified on the basis of their physical state:
(i) Lubricating Oil
(ii) Semi-solid Lubricants (grease)
(iii) Solid lubricants
Lubricating Oil:
It plays the major role in reduction of friction between two moving metallic surfaces. The lubricating oil provides the fluid film in between the metallic surfaces those results in the friction reduction. Lubricants also act as the cooling medium, corrosion preventer.
Poroperties:
(i) They posses low pressure or high boiling point
(ii) Adequate viscosity for particular service condition
(iii) High oxidation resistance
(iv) They non-corrosive properties
They are further classified as-
Vegetable oils:
The petroleum industry existence took a several decades prior to its existence oil of the vegetable and animal origins were the most commonly used lubricants. They were very good for the use but due to their cost and the property of its to undergo oxidation easily tend to leave its presence. They were used as the blending agent with other lubricating oils to produce desired effects.
Mineral or petroleum oils: They are obtained by the petroleum distillation. The carbon chain varies from 12 to 50 carbon atom. They posses viscosity according to their chain length the shorter chain posses lower viscosity while vice versa for longer chain. This is one of the most widely used lubricants as because of its price and its availability. Crude liquid petroleum oils contain lot of impurities (like wax, asphalt, etc.) and consequently, they have to be thoroughly purified before being put to use.(i) The wax, if not removed, raises the pour-point and renders the lubricating oil unfit for use at low temperatures. (ii) Certain constituents get easily oxidized under working conditions and cause sludge formation. (iii) Some constituents mainly asphalt, undergo decomposition at higher temperatures, causing carbon deposition and sludge formation. A number of processes are used for removing these unwanted impurities by using Dew axing or acid refining or by solvent refining.
Semi-solid Lubricants (grease):
Lubricating grease is a semi - solid, consisting of a soap dispersed throughout liquid lubricating oil. The liquid lubricant may be petroleum oil or even synthetic oil and it may contain any of the additives for specific requirements. Greases are prepared by saponification of fat with alkali, followed by adding hot lubricating oil while under agitation. The total amount of mineral oil added determines the consistency of the finished grease. The structure of lubricating greases is that of a gel. Soaps are gelling agents, which give an interconnected structure containing the added oil. At high temperatures, the soap dissolves in the oil, whereupon the interconnected structures cease to exist and the grease liquefies. Consistency of greases may vary from a heavy viscous liquid to the of a stiff solid mass. To improve the heat-resistance of grease, inorganic solid thickening agents (like finely divided clay, bentonite, colloidal silica, carbon black, etc.) are added.
Greases have higher shear or frictional resistance than oils and, therefore, can support much heavier loads at lower speeds. They also do not require as much attention unlike the lubricating liquids. But greases have a tendency to separate into oils and soaps.
Grease is used:
(i) in situations where oil cannot remain in place, due to high load, low speed, intermittent operation, sudden jerks, etc. e.g. Rail axle boxes,
(ii) in bearing and gears that work at high temperatures
(iii) in situations where bearing needs to be sealed against entry of dust, dirt, grit or moisture, because greases are less liable to contamination by these
(iv) in situations where dripping or spurting of oil is undesirable, because unlike oils, greases if used do not splash or drip over articles being prepared by the machine. For example, in machines preparing paper, textiles, edible articles, etc.
Solid lubricants:
Solid lubricants are used at the place where liquid lubricant or grease cannot secured to be useful. The most usual solid lubricants used are graphite and molybdenum disulphide.
Graphite:
It is an allotropic form of the carbon atom (Allotropy form- When any element is formed in more than one form and in each form they posses different property). In graphite carbon are arranged in hexagonal ring form and each form is arranged upside down to form the layer and are attached together by weak Vander-wall’s forces. Graphite is the most stable form of the carbon. It is the good conductor of heat and electricity. The two major known form of graphite are alpha (Hexagonal) and Beta (Rhombohederal).
Structure:
The carbon atom is sp2 hybridized that means there is 4 valence electron in their outermost shell as in the diamond the all 4 valence electron are covalently bonded while in graphite the 3 electron makes a covalent bond while the remaining 1 electron are free. The interconnection of these carbon atoms forms the hexagonal structure. The C-C bond bond length is 1.42 Angstrom. This hexagonal layer attached toward each other by weak Vander Wall forces at a distance of 3.35 Angstrom. This is the reason why graphite is soft.
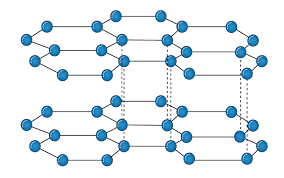
Properties:
Conducting Property: As the carbon of Graphite are sp2 hybridized that means the p orbital remain vacant of the carbon atom this tend to overlapping of the vacant P-orbital. This overlapping of the vacant orbital is responsible for the movement of electrons in parallel on their vacant orbital that is why Graphite shows the conducting property.
Lubricating Property: There is presence of weak Vander Wall forces between two layers due to these weak forces the two layers are flexible in nature which in result make the Graphite to be used for Lubricating purpose.
Applications:
1-Graphite can be used as the solid lubricant
2-Graphite can be used as conductor.
3-Graphite can be used as the electrodes.
3.4 Significance & determination of Viscosity and Viscosity Index:
Viscosity is used to measure the internal friction of a fluid. It is one of the most important properties of fluid. The viscosity of lubricant varies with temperature and pressure. “It is defined as the resistance offered by liquid to flow i.e.; some liquid can flow easily and some can’t. It exhibits the most of the property of liquid. This resistance to flow depends on other physical properties such as temperature, pressure etc.”
Significance:
1. Viscosity of lubricating oil determines its performance under operating conditions.
2. If the viscosity of liquid is too low, the fluid lubricant film cannot be maintained between the moving surfaces, as a result of which excessive wear may take place.
3. If the viscosity of the lubricating oil is too high, excessive friction may take place.
Viscosity Index: The rate at which viscosity of a lubricant changes with temperature is measured by any arbitrary scale is known as viscosity index. Viscosity of liquid is decreases with increasing temperature so that lubricating oil become thinner as the operating temperature is raised, and lubricant can be squeezed out from the subbing parts.
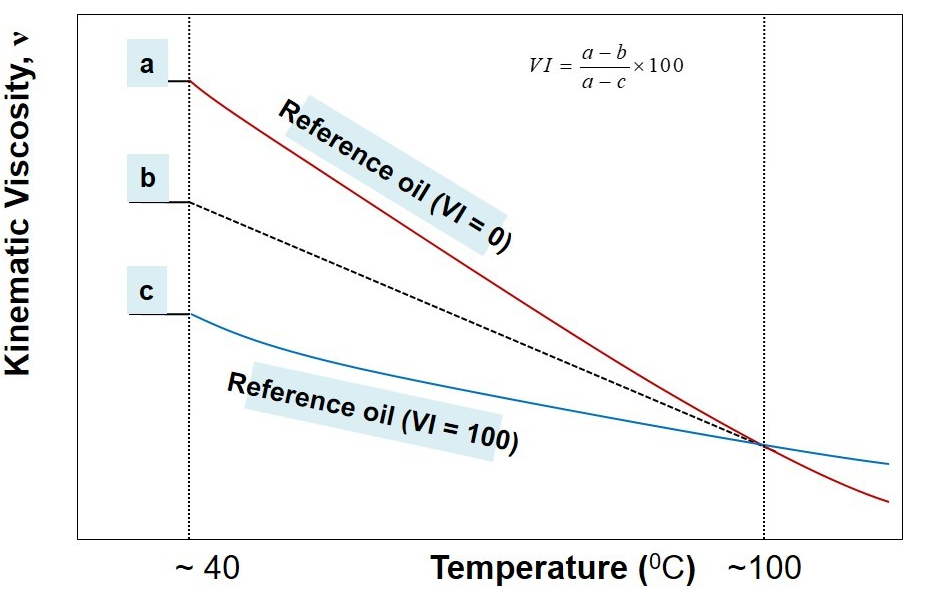
A stepwise procedure to estimate viscosity index, VI, may be outlined as below:
- Measure kinematic viscosity of the unknown oil at 40o C and 100oC.
- Identify two reference oils whose kinematic viscosity at 100oC coincides with the kinematic viscosity of the unknown oil (from the look-up chart of ASTM standard).
- Pick-up the kinematic viscosity of two identified reference oils at 40oC
- In reference to illustration above, now a, b, and c are known.
- Use the following formula to calculate viscosity index
VI=(a-b)/(a-c) *100
3.5 Flash & Fire Points:
The flashpoint for any volatile material is defined as the lowest temperature at which vapors of the material will ignite when ignited by a source. Similarly, the fire point is defined as the lowest temperature at which vapors of the material will catch fire and continue burning even after the ignition source is removed. The fire point is higher than the flash point because the vapors produced at the flash point are not sufficient enough to ignite the fuel. Flash and fire points depend upon the volatility of the biodiesel. Volatility is the tendency of the substance to vaporize, and it is directly related to the vapor pressure of the biodiesel at that particular temperature. The biodiesel exhibiting higher vapor pressure at a given temperature is said to be more volatile than the one exhibiting lower vapor pressure at the same temperature. Hence the lower the NBP (normal boiling point), the higher the volatility, which is in turn inversely proportional to its flash and fire point.
3.6 Cloud & Pour Points:
Cloud point is defined as the minimum temperature at which oil becomes hazy.
Pour point is defined as the minimum temperature at which oil stops pouring( or ceases to flow)
When oil is cooled , wax starts crystallizing , and the oil becomes hazy
Tiny wax crystals agglomerate and form bigger crystal lattice, at this stage the oil solidifies completely and does not pour out on tilting.
Both cloud and Pour points should be very less than the operating temperature
Cloud and pour points can be reduced by adding depressants
3.7 Aniline Point:
The minimum temperature at which oil is miscible with equal amount of aniline. It is the measure of aromatic content of the lubricating oil. The low aniline point have high aromatic content which attacks rubber seals. The higher the aniline point means the lower percentage of hydrocarbons. Thus Aniline point is used as an indication of possible deterioration of rubber sealing.
Determination of Aniline Point:
Aniline + Sample oil Homogenous Solution Cloudiness
3.8 Saponification Number:
The amount of KOH required to saponify the 1 gm of oil. Saponification is nothing just the hydrolysis of an easter with KOH to give alcohol and Na/K salt of acid. The saponification number pertains to all fatty acids present in the sample. To determine saponification number, the sample is completely saponified with an excess of alkali, which excess is then determined by titration (in mg KOH/g). The saponification number depends on the molecular weight and the percentage concentration of fatty acid components present in FAMEs of oil. The saponification number is effectively used to determine the average relative molecular mass of oils and fats. Lauric oils, with a higher percentage of ester bonds than longer chain oils, have a higher saponification number (240–250 mg KOH/g for CNO compared to 190–195 mg KOH/g for SBO). The distinction is quite relevant for biodiesel production in that oils with a high SV require more methanols, and produce more glycerol but less biodiesel than longer chain oils. Oils with high saponification number impart high foamability e.g. Palm kernel, coconut and babassu oils.
3.9 Steam Emulsification Number:
Steam emulsification number is the time (in seconds ) required for an emulsion of lubricating oil and water to separate into distinct layers at 900C.
Emulsification is the properly of oil to get mixed with water forming a dispersed phase of oil in water or water in oil, the emulsification property of oils is expressed in terms of stream emulsification number.
Determination of steam emulsification number
Steam of 1000C is bubbled through 20mL of lubricating oil till its temperature reaches 90 steams 0C When the oil temperature reaches 900C. The time required (in seconds) for water (formed due to condensation of steam) and oil to separate into two distinct layers is noted as steam emulsification number.
The significance of steam emulsification number
- Good lubricating oil has low steam emulsification number; so that when it comes in contact with water it does not form an emulsion.
- The emulsion has a tendency to collect dirt, dust etc which reduces the lubricating property emulsification number arrears vegetable oils have high stream emulsification number whereas vegetable oils have high steam oils have high steam emulsification number.
- Oil having high steam emulsification number is preferred for preparation of lubrication emulsification like cutting fluids