Unit 04
Polymer & polymerization
4.1 Introduction:
The process in which the simpler molecules combine together to form very large molecule having high molecular weight is known as polymerization. The molecule is known as polymer. The different ways of doing polymerization are –
By opening a double bond
Ex:
NCH2 = CH2 (CH2 – CH2)n
Ethane polythene
NCH2=CH (CH2 – CH)n
Cl Cl
Vinyl chloride polyvinyl chloride
4.2 Types of polymerization:
Types of polymerization:
Polymers can be synthesized by the following polymerization processes:
- Addition polymerization or chain polymerization
- Condensation or step or step growth polymerization
III. Copolymerisation
Addition polymerization:
The addition polymerization is the process in which the liniking together of monomer molecules by a chain reaction is observed. Polymer synthesized by addition polymerization has the same empirical formula as that of monomer. No molecule is evolved during polymerisation and the polymer is an exact multiple of the original monomeric molecule.
Condensation polymerization:
An intermolecular reaction involving two different bifunctional reactants with affinity for each other and taking place through repeated condensation reaction is known as condensation polymerization.
Copolymerisation:
Addition polymerisation involving a mixture of two or more suitable or compatible monomers gives a copolymer and the process is known as copolymerization. A reaction in which a mixture of two or more monomers is allowed to undergo polymerisation is known as copolymerization. The polymer is known as copolymer.
E.g.: Copolymerisation of styrene and methyl methacrylate
4.3 Classification, mechanism of polymerization (Free radical & Ionic polymerization):
Free Radical Polymerization: The formation of polymer from the successive addition of free-radical building blocks through the polymerization is called as the free radical polymerization. In order to obtain the wide variety of different polymers and material composites the free radical polymerization plays a major role in it. The relatively non-specific nature of free-radical chemical interaction make it one of the most versatile forms of polymerization which allows a facile reactions of polymeric free radical chain ends and other chemical or substrates. The monomers from which addition polymers are made are alkenes. The most common and thermodynamically favored chemical transformations of alkenes are addition reactions. Many of these addition reactions are known to proceed in a stepwise fashion by way of reactive intermediates, and this is the mechanism followed by most polymerization. The monomers are initiated by traces of oxygen, the pure compounds are stabilized by radical inhibitors.
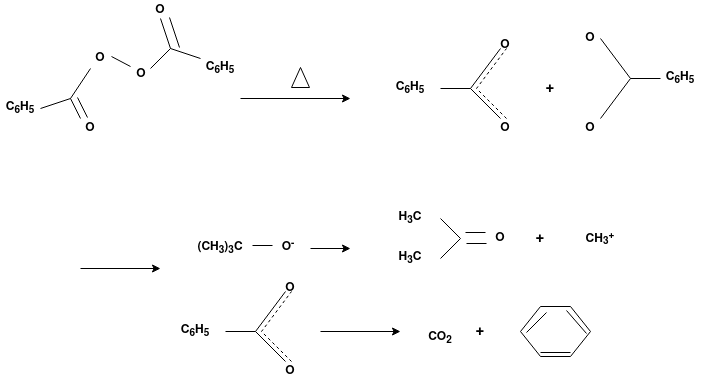
Radical Initiators
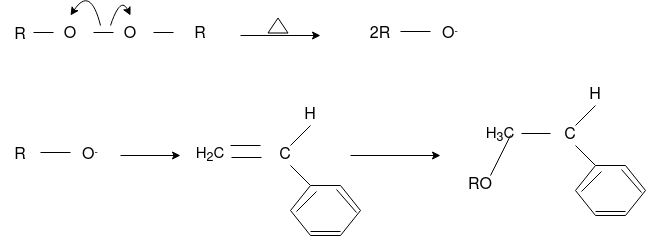
Chain Initiation
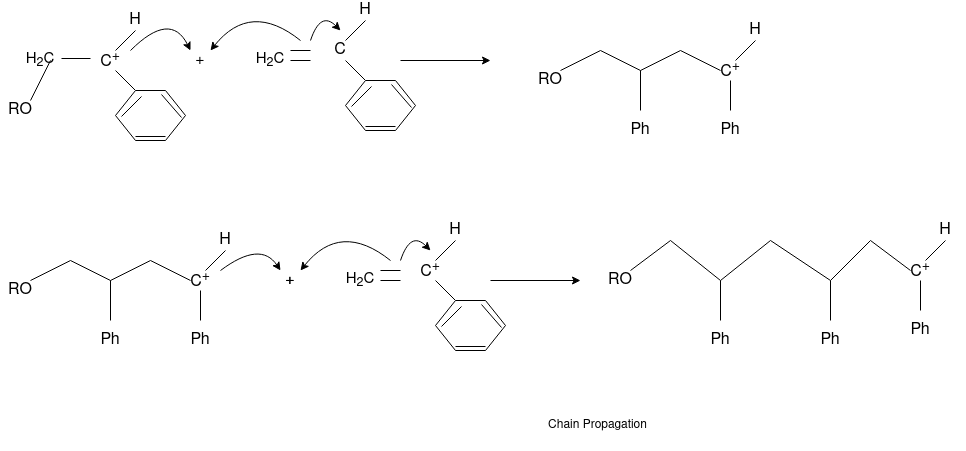
Chain Propagation
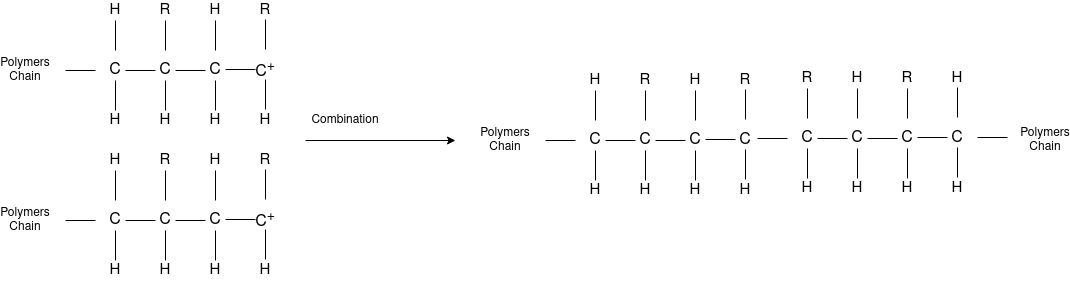
Chain Termination
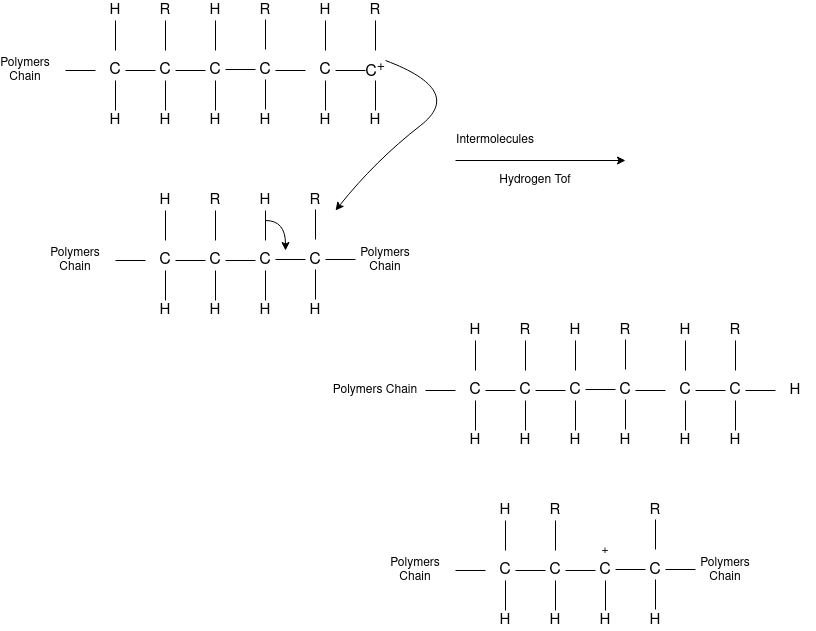
Chain Transfer Reaction
Ionic Polymerization: Alkenes can polymerize under the influence of both cationic and anionic initiators. As with free radical polymerizations, the ionic processes involve initiation, propagation and (sometimes) termination steps.
Cationic Polymerization: Cationic polymerizations are typically initiated by carbocations, generated by protonation of an alkene with a strong acid such as sulfuric or tri-fluoro methane sulfonic acid.
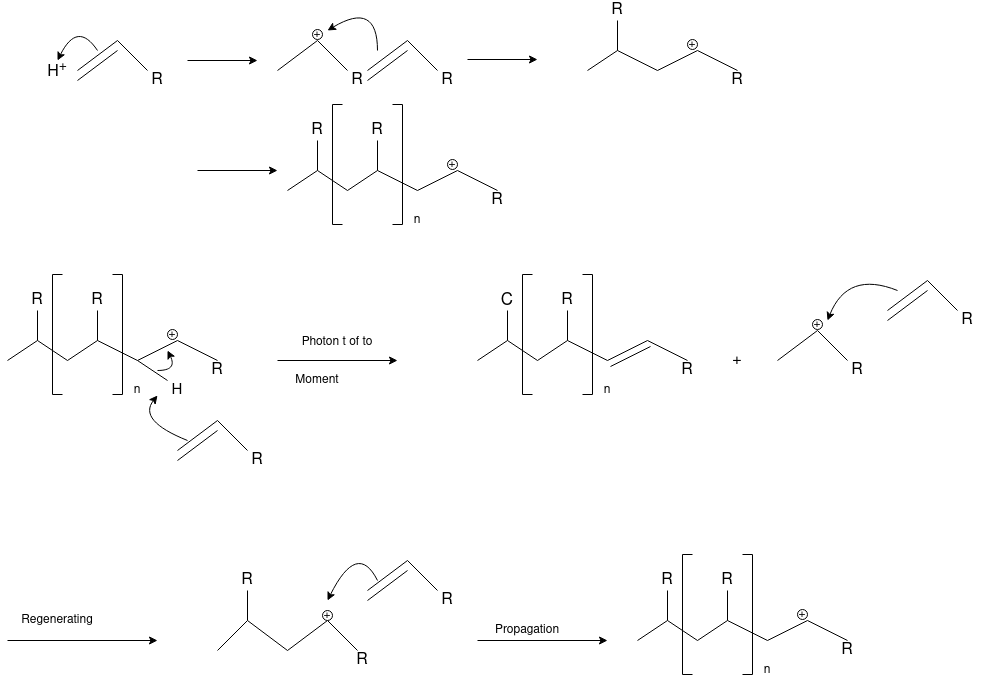
Anionic Polymerization: Anionic polymerizations are typically initiated by carbanions such as organolithium compounds.
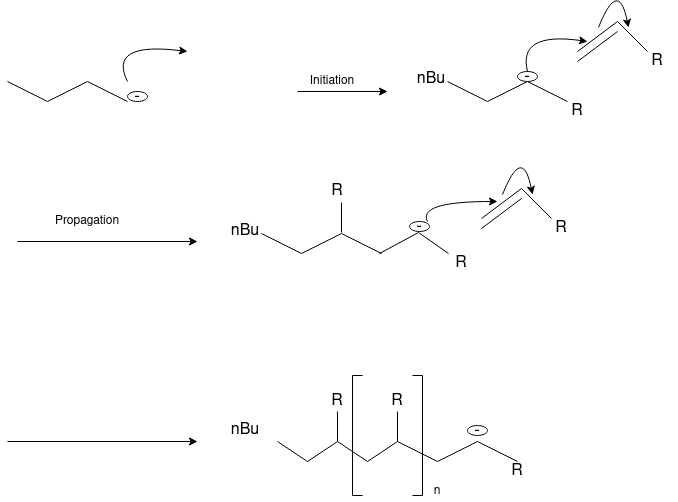
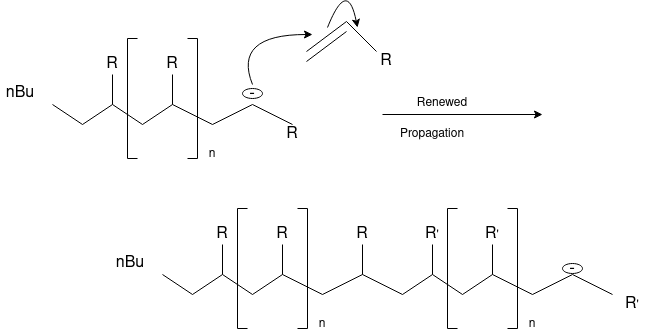
4.4 Thermoplastic &Thermosetting polymers:
Thermoplastic polymer: A thermoplastic is a resin that is solid at room temperature but becomes plastic and soft upon heating, flowing due to crystal melting or by virtue of crossing the glass transition temperature (Tg). Upon processing, usually via injection-molding or blow-molding-like processes, thermoplastics take the shape of the mould within which they are poured as melt, and cool to solidify into the desired shape. The significant aspect of thermoplastics is their reversibility, the ability to undergo reheating, melt again, and change shape. This allows for additional processing of the same material, even after being prepared as a solid. Processes such as extrusion, thermoforming, and injection molding rely on such resin behavior. Some common thermoplastic materials include polyethylene (PE), polycarbonate (PC), and polyvinyl chloride (PVC).
Thermosetting Polymer: A thermosetting resin, or thermosetting polymer, is generally a liquid material at room temperature which hardens irreversibly upon heating or chemical addition. When it is placed in a mould and heated, the most solidifies into the specified shape, but this solidification process includes the formation of certain bonds, called cross links, that hold the molecules in place and change the basic nature of the material, preventing it from melting. As a result, a there most, as opposed to a thermoplastic, cannot return to its initial phase, rendering the process irreversible. There most, upon heating, become set, fixed in a specific form. During overheating, there most tend to degrade without entering a fluid phase. Processes such as compression molding, resin transfer molding, pultrusion, hand lay-up, and filament winding depend on thermosetting polymer behavior. Some common there most include epoxy, polyimide, and phenolic, many of which are significant in composites.
Properties:
Property | Thermoplastics Polymer | Thermosetting Polymer |
Molecular Structure | Linear polymer: weak molecular bonds in a straight-chain formation | Network polymers: high level of crosslinking with strong chemical molecular bonds |
Melting point | Melting point lower than the degradation temperature | Melting point higher than the degradation temperature |
Mechanical | Flexible and elastic. High resistance to impact (10x more than thermosets). Strength comes from crystallinity | Inelastic and brittle. Strong and rigid. Strength comes from crosslinking. |
Polymerization | Addition polymerisation: repolymerised during manufacture (before processing) | Polycondensation polymerisation: polymerised during processing |
Microstructure | Comprised of hard crystalline and elastic amorphous regions in its solid state | Comprised of thermosetting resin and reinforcing fibre in its solid state |
Size | Size is expressed by molecular weight | Size is expressed by crosslink density |
Solubility | Can dissolve in organic solvents | Do not dissolve in organic solvents |
Service temperature | Lower continuous use temperature (CUT) than thermosets | Higher CUT than thermoplastics |
4.5 Elementary idea of Biodegradable polymers:
Biodegradation: -
It is a processes of converting polymer material into harmless simple gaseous products by the action on enzymes of microorganism and water.
A polymer which can be converted from harmless gaseous products by action of biological enzyme and water, is called as biodegradable polymers 3 components are important in the biodegradation of organic polymers.
A) Organisms: - like pseudomonas, bacillus, protozoa, acetobacter, various fungi, etc.
B) Environment: - suitable temp, moist condition, presence of salts, suitable ph.
C) Nature of polymer: -
- Polymer chain should contain bond which can be hydrolysed or oxidized by the enzyme action o, s.
- High aromatic they are tough for degradation
Hydrophilic chain backbone of polymer contains O,N,3. Atoms easily degrade.
3. Hydrophilic end groups
4. More amorphous nature of polymer
5. Small size of polymer material
Example: - PHBV
It is a co – polymer of hydroxy butyric acid and 3 hydroxyvaleric acid. It is produced by fermentation of glucose by acaligeneseutrophus species.

STRUTURE
Properties: -
- It is highly crystalline, soluble in chloroform
- It has melting point 180° c
- It is thermo softening polymer, soft, flexible.
Limitations: -
- Such polymers are very costly
- They cannot manufacture on a large scale
- Don’t possess high mechanical strength
Applications: -
- Used for moulded articles
- Used for films for packing and lamination
- It is used in medical field – for organs transplants, surgical, and orthopaedic, operations.
- It is used in agriculture field – for manufacturing fertilizers and pesticides.
The polymers have ability to conduct electricity are called as conducting polymers.
Structural requirements of polymer: -
- Polymer containing conjugation double bonds system
- Polymer with the higher crystallinity and high planarity
- Presence of aromatic rings in a polymer chain.
- Polymer has a linear structure.
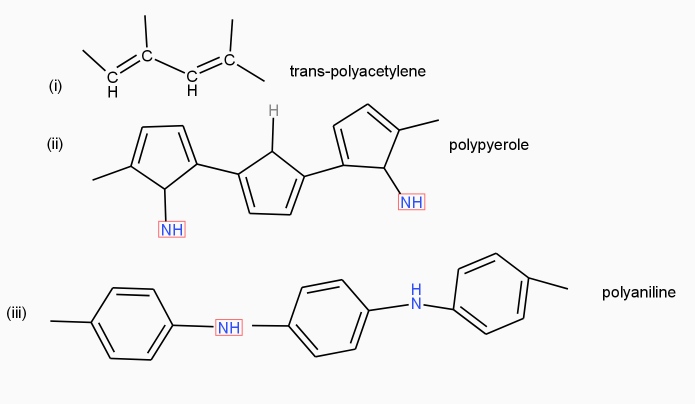
Poly acetylene: -
Structure: -
- The polymer consists of along chain carbon atoms with alternating single and double bonds between them. Each carbon possesses one hydrogen atom.it is obtained by Ziegler matter ayteslys.
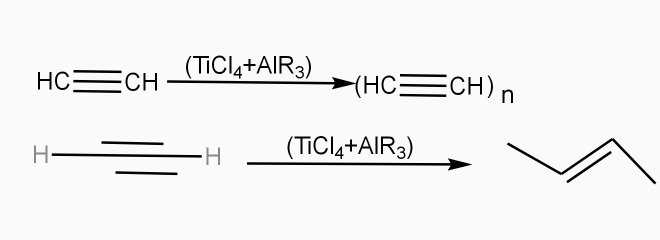
- Doping of polymer: - addition of impurities
- Intrinsic polymers: - the polymer which conduct electricity on their own is called as intrinsic polymers.
- Extrinsic polymers: - the polymers which conduct electricity by doping processes are called as extinct polymers.
In doping process, polymer is either oxidized or reduced.
There are two type of doping
a] oxidative / p type doping
- Includes ICPS with Lewis acid.
- Oxidizing reagents are used (e.g. Iodine vapours)
- Oxidation taking place
- +VE change develops on polymer chain.
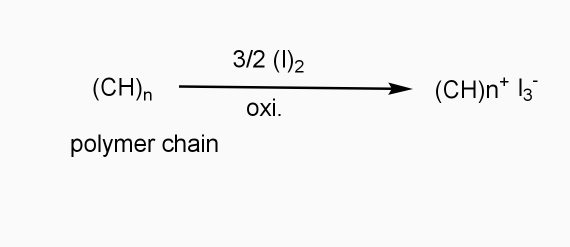
b] Reductive / n type doping
- Includes ICPS with Lewis bases
- Reducing reagents are used (e.g.Na,Li,etc.)
- Reduction taking place
- - ve charge develops on polymer chain
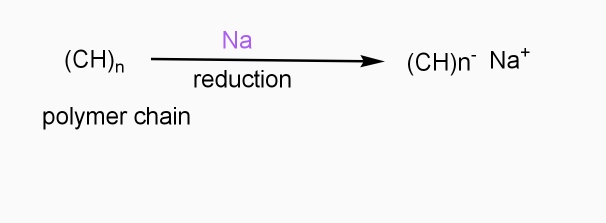
Applications: -
- For making rechargeable light weight batteries.
- In electronic devices, transistors, diodes.
- In optical display device.
- In solar cells.
- In telecommunication system.
4.6 Preparation, properties & uses of the following polymers- PVC,
PMMA, Teflon, Nylon 6, Nylon 6:6, Polyester phenol formaldehyde, Urea- Formaldehyde, Buna
N, Buna S
PMMA (Polymethyl Methacrylate):
Preparation:
This is an important thermoplastic resin. It is obtained by polymerization of methyl methacrylate which is an ester of methyl acrylic acid, CH2=C(CH3)COOH, in presence of acetyl peroxide or hydrogen peroxide. It is an acrylic polymer.
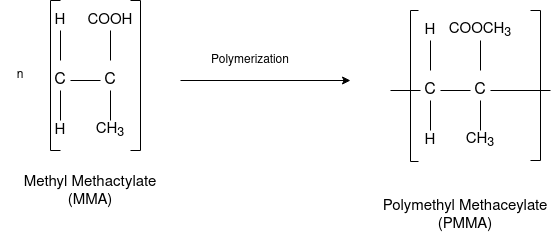
Properties:
(i) It is hard, fairly rigid material with a high softening point of about 130-14rfC.
(ii) It becomes rubber like at a temperature above 6oC.
(iii) It has outstanding shape-forming properties due to wide span of temperature from its rigid state to viscous.
(iv) It has high optical transparency.
(v) It has high resistance to sunlight and ability of transmission light accurately.
Uses:
They are used for making lenses, optical parts of instruments, air craft, light fixture, artificial eyes, wind screen, bone splints, decorative articles etc. PMMA is found in paint and used in window glasses.
Nylon-6:
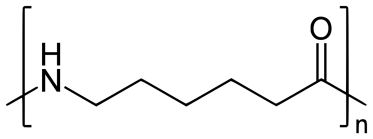
Nylon 6 is also called as the Polycaprolactam which is developed by Paul Schlack. They are semicrystalline polyamide.They have smooth surface and are featureless as a glass rods. Nylon 6 can be modified using comonomers or stabilizers during polymerization to introduce new chain end or functional groups, which changes the reactivity and chemical properties. It's often done to change its dyeability or flame retardance. Nylon 6 is synthesized by ring-opening polymerization of caprolactam. When caprolactam is heated at about 533 K in an inert atmosphere of nitrogen for about 4–5 hours, the ring breaks and undergoes polymerization. Then the molten mass is passed through spinnerets to form fibres of nylon 6.
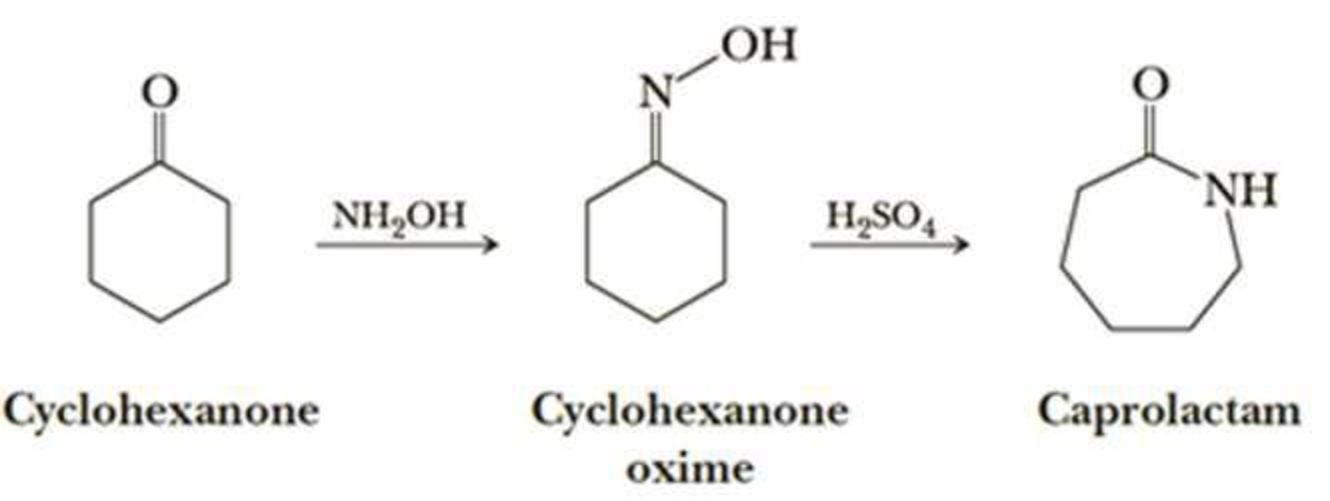
On further heating of Caprolactam at 533K with inert atmosphere of nitrogen for about 4-5 hours it gives
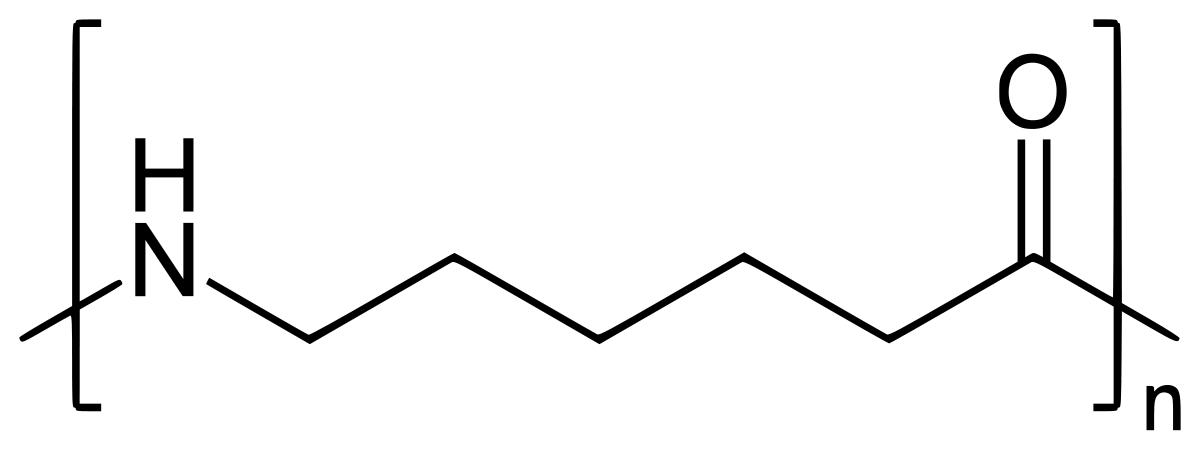
(Nylon-6)
Application:
(i) Nylon 6 is widely used for gears, fittings, bearings and automotive industry for various parts and as a material for power tools and housings.
(ii) It is used as threads in bristles for toothbrushes, surgical sutures and strings for acoustic and classical instruments.
(iii) It is used in production of large variety of ropes, filaments, nets as well as knitted garments.
(iv) It can also be used in gun frames, such as those used by Glock, which are made with composite of Nylon 6 and other polymers.
Nylon 6,6:
Nylon 6,6 is a polyamide made from adipic acid and hexamethylenediamine by polycondensation. The resulting polymer is extruded into a wide range of fiber types. The fiber are drawn and stretch in a process that increases their length and reorients the material molecules parallel to one another to produce a strong elastic filament. The thermo plasticity of nylon permits permanent cripping of the fibres and provides bulk and stretch properties. The Nylon 6,6 is prepared from Nylon salt i.e., prepared by reacting the hexamethylene diamine and adipic acid in boiling methanol. The comparatively insoluble salt precipitates out from methanol. A 60% of aqueous solution of salt is then run into a stainless steel autoclave together with a trace of acetic acid to limit the molecular weight. The vessel is sealed and purged with oxygen free nitrogen and the temperature raised to 220oC at about the pressure of 1-7 MPa is developed. After 1-2 hours the temperature is raised to 270-280oC and steam blend off to maintain the pressure.
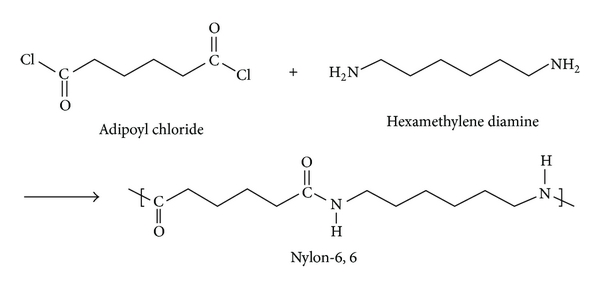
Buna-S:
Buna-S is also known as the styrene-butadiene. It is a copolymer of butadiene (75%) and styrene (24%). Buna is derived from the Bu-Butadiene while Na is Sodium or Natrium and S is Styrine. Buna-S is the replacement of natural rubber while styrene, 2 monomers and butadiene play a major role in its derivation where as these 2 monomers is polymerized by two basically different process i.e., from solution (S-SBR) or as an emulsion (E-SBR). It is prepared by the copolymerization of butadiene & styrene.
It is a random co-polymer formed by the emulsion polymerization of a mixture of 1:3 butadiene and styrene in the presence of peroxide as a catalyst at 5o C and this is the reason why the product is called as cold rubber. The obtained rubber is called as the Styrene Butadiene Rubber (SBR).
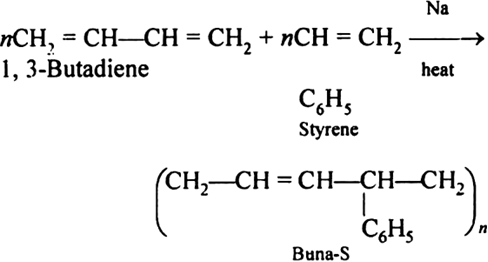
Applications:
(i) Buna-S is used as the natural rubber i.e., they are widely used in pneumatic tyres.
(ii) SBR is extensively used in coated papers.
(iii) They are highly used in building materials as a binding material.
(iv) SBR is also used as binder in lithium-ion battery electrodes.
Buna-N:
Buna-N are commonly used as elastomers. They are unsaturated synthetic co-polymer. They are obtained by the co-polymerisation of 1,3-butadiene and acrylonitrile in the presence of a peroxide catalyst. Nitrile rubber, NBR or Perbunan are another terms used for the Buna-N. They are synthetic rubber copolymer of acrylonitrile (ACN) and butadiene. Elastomers is natural or synthetic material which does not break when stretched and when released it return to its original length. The most important monomer used in preparing Buna-N is Acrylonitrile rubber which gives hardness, tensile strength, fuel and oil resistance. It usually contain 34% ACN. Grinding wheels can be made with nitrile rubber. When they are used for grinding smokes or fumes are emitted, which are known as acrid. The objectionable odor can be prevented if certain classes of diketones, which contain a conjugated system of two double bonds or unsaturated groups are added. Dibenzoylethylene, chloranil and anthraquinone help to prevent odor formation.

Buna-N are resistive to oil, fuel and other chemicals which means more Buna-N higher the resistance to oil but flexibility of the material is less. They are resistant to aliphatic hydrocarbons. They are non resistant to solvents but they may be attacked by ozone, ketones, esters and aldehydes.
Applications:
(i) They are used in the disposable non-latex rubbers, belts, gaskets.
They are used in preparation of adhesive and as a pigment binder.
4.7 Vulcanization of Rubber:
Vulcanization is a chemical process that converts natural rubber and other polydiene elastomers into cross-linked polymers. The most common vulcanization agent is sulfur. It forms bridges between individual polymer molecules when heated with rubber. Often a catalyst and initiator is added to accelerate the vulcanization process. The cross-linked elastomers have much improved mechanical properties. In fact, unvulcanized rubber has poor mechanical properties and is not very durable.
- Mixing of crude rubber with about 5-30% of sulfur (cross-linking agent) and other additives such as:
- Activator (commonly zinc oxide or stearic acid),
- Accelerator (guanidines, thiazoles, dithiocarbamates, xanthates, thiurams) ,
- Coagulants (acetic acid, calcium chloride),
- Anti-oxidants (amines, phenolics, phosphites),
- Color pigments,
- Surfacants,
- Softeners,
- Ant-foaming agents,
- Anti-tack agents (Rosin derivates, coumarone-indene resins, aliphatic petroleum resins, alkyl-modified phenol-formaldehyde resins).
Slow cross-linking starts at this stage. It is neccessary to avoid active vulcanization during mixing, which may cause cracks formation at the molding stage.
- Molding (shaping) the rubber mixture. The rubber must be shaped prior to heating stage since cross-linking makes shaping impossible.
- Heating the mixture to 250-400ºF (120-200ºC). Increased temperature speeds up the vulcanization process resulting in fast and complete cross-linking. C-S bonds replace C-H bonds linking chain polyisoprene molecules. Each link is formed by one to seven sulfur atoms.