UNIT1
Water Technology
Hardness can be defined as a soap consuming capacity of water sample. Soaps are sodium salts of fatty acids like oleic acid, palmetic acid and stearic acid. They dissolve readily .in water to form lather due to which it has cleansing property.
- But compounds of fatty acids with other metals done dissolve in water.
- If water contains other metal ions like calcium and magnesium ions they react with sodium salts of long chain fatty acids to form in soluble soap which we observe as curd.
2
(calcium stearate)
- If water contains other metal ions like calcium and magnesium ions they react with sodium salts of long chain fatty acids to form in soluble soap which we observe as curd
- These other metal ions are responsible for the hardness of water most important metal of ions which cause hardness to water are calcium and magnesium ions.
- The hardness of water along can be calculated from the amount of calcium and magnesium ions present in water along with bicarbonates, sulphates chlorides and nitrates.
TYPES OF WATER | HARDNESS |
Soft | 0 – 75 |
Moderately hard | 75 – 150 |
Hard | 150 – 300 |
Very hard | Above 300 |
Types of hardness: -
- Temporary hardness ( carbonate) :-
- When water containing calcium and magnesium bicarbonates is heated , bicarbonate decompose and from insoluble carbonate and form hydroxide.
- On filtering such water , soft water is obtained.
- The hardness which can be removed by more boiling is referred as ‘temporary hardness ’ or bicarbonate hardness.

Ca

Mg Mg
+ 2 CO
(Bicarbonates)
II. Permanent hardness :-
- The term permanent hardness ornon carbonate is the term applied to the hardness caused by dissolved chlorides , nitrates and sulphate of calcium and magnesium.
- This cannot be removed by boiling the water sample.
- Sum of temporary and permanent hardness is referred to as total hardness.
III. Alkaline or carbonate and non – alkaline or non – carbonate hardness :-
- Like all carbonate and bicarbonate, calcium and magnesium carbonate and bicarbonate are alkaline.
- Then hardness due to the carbonate and bicarbonate is called alkaline hardness or carbonate hardness.
- The alkalinity can be measures by titration with standard mineral acid using methyl orange and or phenol phthalein as an indicator.
4. As the sulphate and chloride are neutral salts , the hardness caused by presence of calcium and magnesium sulphate , chlorides and nitrates is termed as non-alkaline hardness or non-carbonate hardness.
IV. Total hardness :-
The hardness due to all hardness causing salts , known as total hardness.
Total hardness = temporary + permanent
Estimation of hardness :-
Hardness of weather can be determined by two methods.
1) Soap solution method :-
- Total hardness of water can be determined by titrating a fixed volume of water sample (100ml) against standard alcoholic soap solution.
- Appearance of stable lather which persists for two minutes is the end point of titration.
- In the beginning sodium soap will precipitate all the hardness causing metal ions in the form of their soap (card) and then it will form free lather.
- If same water sample is boiled for 30minutes and then titrated against same soap solution the titration reading corresponds to permanent hardness.
- The difference between two measurements corresponds to the temporary hardness of water.
The process by which impurities, quality of the water is treated in order to make it appropriate for specific end use. The end use is of versatile that may be used for drinking purpose or water supply irrigation whether in the industrial water supply. Water treatment removes contaminants and undesirable components, or reduces their concentration so that the water becomes fit for its desired end-use. For the human consumption that too without any short term or long term of any adverse health effect water need to be contaminated free. Faeces can be a source of pathogenic bacteria, viruses, protozoa or helminthes. Water supplied to domestic properties, for tap water or other uses, may be further treated before use, often using an in-line treatment process. Such treatments can include water softening or ion exchange. Many proprietary systems also claim to remove residual disinfectants and heavy metal ions.
Coagulation: Coagulation treatment chemicals are used in effluent waste water treatment process for solids removal, water clarification, lime softening, sludge thickening and solid dewatering. It is the process which can be used as preliminary steps between waste water treatment process like filtration and sedimentation. This can be affected by its dose, its pH and mass. Coagulation is usually accomplished in two stages i.e, rapid mixing and slow mixing. Rapid mixing serves to disperse the coagulants evenly throughout the water and to ensure complete reactions. Sometimes this is accomplished by adding the chemicals just before the pumps, allowing the pump impellers to do the mixing. Usually, though, a small flash-mix tank provides about one minute of detention time. After the flash mix, a longer period of gentle agitation is needed to promote particle collisions and enhance the growth of floc. This gentle agitation, or slow mixing, is called flocculation. It is accomplished in a tank that provides at least a half hour of detention time. The flocculation tank has wooden paddle-type mixers that slowly rotate on a horizontal motor-driven shaft. After flocculation the water flows into the sedimentation tanks. Some small water-treatment plants combine coagulation and sedimentation in a single prefabricated steel unit called a solids-contact tank.
Coagulant Dose Determination:
(i) Jar Test can be used for determining the coagulant dose.
(ii) Streaming Current Detector (SCD) is used for the determination of coagulant dose.
Sterilization using UV:
This method is one of the most effective methods for disinfecting bacteria from water. The ultraviolet rays penetrate in homes and destroy the harmful pathogens, illness causing microorganisms by attacking their genetic core i.e, DNA. These rays eliminate the ability of the microbes to reproduce. UV systems destroy 99.99% of harmful microorganisms without adding chemicals or changing your water’s taste or odor. UV water purification is usually used with other forms of filtration such as reverse osmosis systems or carbon block filters.
Principles:
UV radiation has three wavelength zones: UV-A, UV-B, UV-C and UV-C is the last region. A low-pressure mercury arc lamp resembling a fluorescent lamp produces the UV light in the range of 254 manometers (nm). These lamps contain elemental mercury and an inert gas, such as argon, in a UV-transmitting tube, usually quartz. Traditionally, most mercury arc UV lamps have been the so-called "low pressure" type, because they operate at relatively low partial pressure of mercury, low overall vapor pressure (about 2 mbar), low external temperature (50-100oC) and low power. These lamps emit nearly monochromatic UV radiation at a wavelength of 254 nm, which is in the optimum range for UV energy absorption by nucleic acids (about 240-280 nm).
In recent years medium pressure UV lamps that operate at much higher pressures, temperatures and power levels and emit a broad spectrum of higher UV energy between 200 and 320 nm have become commercially available. However, for UV disinfection of home drinking water at the household level, the low-pressure lamps and systems are entirely adequate and even preferred to medium pressure lamps and systems. This is because they operate at lower power, lower temperature, and lower cost while being highly effective in disinfecting more than enough water for daily household use. An essential requirement for UV disinfection with lamp systems is an available and reliable source of electricity. While the power requirements of low-pressure mercury UV lamp disinfection systems are modest, they are essential for lamp operation to disinfect water. Since most microorganisms are affected by radiation around 260 nm, UV radiation is in the appropriate range for germicidal activity. There are UV lamps that produce radiation in the range of 185 nm that are effective on microorganisms and will also reduce the total organic carbon content of the water. For typical UV system, approximately 95 percent of the radiation passes through a quartz glass sleeve and into the untreated water. The water is flowing as a thin film over the lamp. The glass sleeve is designed to keep the lamp at an ideal temperature of approximately 104 °F.
Working:
UV rays affect microorganisms by altering the DNA and prohibiting them to reproduce. A UV ray only inactivates the microbes from the water. The effectiveness of this process is related to exposure time and lamp intensity as well as general water quality parameters. Most manufacturers provide a lamp intensity of 30,000-50,000µwatt-sec/cm^2. Due to the regular use of lamp its intensity decreases with time hence that requires the replacement for the success of disinfection. A UV ray does not affect the taste, odor or clarity of water instead they are most effective disinfectant among all. The amount of microbes affected by the UV rays is directly depends on the intensity of the UV rays. The darker the material the most microbes get affected while in the transparent glass intensity of UV rays are reduced which left less impact over the microbes.
Ozone:
Ozone which consists 3 oxygen atom is an inorganic molecule. Ozone is a highly reactive gas. It is both a natural and a man-made product that occurs in the Earth's upper atmosphere (the stratosphere) and lower atmosphere (the troposphere). Depending on where it is in the atmosphere, ozone affects life on Earth in either good or bad ways. O3 is a allotrope of oxygen which is less stable than it’s diatomic allotrope of O2. Ozone is formed from dioxygen by the action of ultraviolet (UV) light and electrical discharges within the Earth's atmosphere. It is present in very low concentrations throughout the latter, with its highest concentration high in the ozone layer of the stratosphere, which absorbs most of the Sun's ultraviolet (UV) radiation. Ozone is a powerful oxidant (far more so than dioxygen) and has many industrial and consumer applications related to oxidation. This same high oxidizing potential, however, causes ozone to damage mucous and respiratory tissues in animals, and also tissues in plants, above concentrations of about 0.1 ppm. While this makes ozone a potent respiratory hazard and pollutant near ground level, a higher concentration in the ozone layer (from two to eight ppm) is beneficial, preventing damaging UV light from reaching the Earth's surface.
Structure:
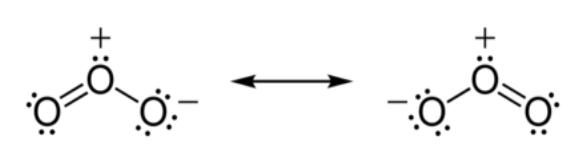
Properties:
(i) They are pale blue gas slightly soluble in water.
(ii) It formed dark blue liquid when condenses.
(iii) It forms violet-black solid at temperature below 80K.
Reactions:
With sulphur compounds: Ozone oxidizes sulphides to sulphates.
PbS + 4 O3 → PbSO4 + 4 O2
Sulphuric acid produced from ozone
S + H2O + O3 → H2SO4
3 SO2 + 3 H2O + O3 → 3 H2SO4
With metals: Ozone oxidizes metals to their higher oxidation states.
Cu + O3 → CuO + O2
Applications:
(i) Ozone can be used to remove iron and manganese from water.
(ii) Ozone will also oxidize dissolved hydrogen sulfide in water to sulfurous acid.
(iii) Ozone can completely decompose Urea.
(iv) Ozone can detoxify cyanides.
Chlorine:
Chlorine is an essential chemical building block, useful in making the products that contribute to public health and safety, advanced technology, nutrition etc. Majority of the products used in a day is directly or indirectly depend on the chlorine. Chlorine plays a major role in the field of manufacturing they are highly used in manufacturing the contact lenses, air conditioning refrigerators etc. Chlorine can be obtained from the ordinary salts. Elemental chlorine is commercially produced from brine by electrolysis, predominantly in the chlor-alkali process. The high oxidising potential of elemental chlorine led to the development of commercial bleaches and disinfectants, and a reagent for many processes in the chemical industry. Chlorine is used in the manufacture of a wide range of consumer products, about two-thirds of them organic chemicals such as polyvinyl chloride (PVC), many intermediates for the production of plastics, and other end products which do not contain the element. As a common disinfectant, elemental chlorine and chlorine-generating compounds are used more directly in swimming pools to keep them sanitary. Elemental chlorine at high concentration is extremely dangerous, and poisonous to most living organisms. As a chemical warfare agent, chlorine was first used in World War I as a poison gas weapon. The chlorine production process is extraordinarily efficient: hydrogen, a by-product of the production process, used in energy source in manufacturing facilities.
Uses & Benefits:
Water:
Chlorine plays a major role in the safety of swimming pools and drinking water. The number of death ratio was high before the use of chlorine for trating the water in cities.
Household Disinfectant:
Chlorine helps in manufacturing the household chlorine bleach, which whitens and disinfect the clothes. This is also used in kitchen and bathroom surfaces.
Building & Construction:
Chlorine is used in plastic foam insulation; increase the energy efficiency of home heating and air conditioning system, helps in reducing bills and conserving natural resources. Energy-efficient vinyl windows reduce heating and cooling costs and GHG emissions.
Break Point Chlorination:
Breakpoint chlorination is the stage at which the chlorine demand has been fulfilled with respect to the addition of water. The tipping point at which oxidation is complete and further addition of shock chlorine or other oxidizer is unnecessary and unfruitful. In other words, the chlorine has completely reacted with the bather pollutants leaving a zero chlorine residuals.
The following graph represents this condition clearly:
This graph shows the theory of continuous breakpoint chlorination. There is chlorine concentration on the left vertical axis which is zero at bottom while it increases with moving upward while the right vertical axis is ammonia-nitrogen concentration which changes on moving from bottom to upside. The bottom horizontal axis represents the ratio of chlorine to ammonia by weight which is zero on the left and increases to the right. The bottom horizontal axis also represents time and increases from left to right. Further the graph is distributed in three zones i.e, zone-1, zone-2 and zone-3.
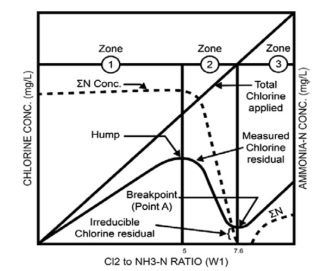
Zone-1: On moving form left side of the graph; there is a concentration of ammonia-nitrogen in the pool from bathers. Chlorine has been allowed to fall to zero and total applied chlorine and measured chlorine residual are both zero. Chlorine is then added at a constant rate. The principal reaction in zone 1 is the reaction between chlorine and the ammonium ion.
Zone 2: The phenomenon of breakpoint occurs in this zone, this zone is also known as the chloramines destruction zone. Due to the change in weight ratio from 5:1, some of the monochloramine starts reacting slowly with further addition of chlorine to form dichloramine that is about two times as germicidal as monochloramine. A pure dichloramine residual has a noticeable disagreeable taste and odor, while monochloramine does not. Total Chlorine Applied is still increasing and both the Concentration of ammonia-nitrogen and Measured Chlorine Residual decrease rapidly. This rapid decrease occurs because the dichloramine is reacting immediately with additional hypochlorous acid in a series of destruction reactions to form volatile compounds and other by-products such as nitrogen gas, nitrate and chloride. Therefore, ammonia and chlorine are consumed in the reactions and lost from the pool. Thus, additional chlorine is required to destroy ammonia and chloramines.
Zone 3:
This zone is very right in the graph. The total residual consists of the nuisance residuals plus free chlorine. If the formation of trichloramine took place then that would form in this zone only. Trichloramine formation is more likely to occur at a pH between 7 and 8. In practice it has been found the most pleasant water for bathing will occur if more than 85% of the total chlorine is free chlorine.
In reality, ammonia-nitrogen does not stay static but is continually added while the pool is open to the public. To achieve breakpoint chlorination, chlorination must continue after the pool has been closed to the public to ensure oxidation of the additional chloramines every night.
The shape of the breakpoint curve is affected by contact time, temperature, concentration of chlorine and ammonia, and pH. Higher concentrations of the chemicals increase the speed of the reactions.
The presence of high dissolved mineral contents of calcium magnesium ions leads to make the water hard. Hardness in water is defined as concentration of multivalent cations. Multivalent cations are cations (metal ions) with a charge greater than 1+, mainly 2+. These cations may be Ca2+ and Mg2+.
The mix ion water or hard water is not harmful to health but can pose serious plumbing problems in both residential and commercial applications. From the lack of suds formation in bathing and laundry applications to the costly breakdowns in boilers, cooling towers and other equipment that handle water, water hardness is a serious issue.
Methods:
(i) Lime-soda process: In this process the conversion of soluble calcium and magnesium salts took place into insoluble compounds by further addition of lime (Ca(OH)2) and soda (Na2CO3) while Calcium Carbonate and Magnesium Hydroxide are precipitated and are filtered
Of.
Cold lime-soda process: In this process the calculated quantity of chemical is mixed with water at room temperature. The formed precipitate at room temperature are divided in such a way that they do not settled down neither filtered easily.
NaAIO2 + 2H2O NaOH + AI(OH)3
AI2(SO4)3 + 3Ca(HCO3)2 2AI(OH)3 + 3CaSO4 + 6CO2
Hot lime-soda process: This process is operated at a temperature of boiling point, it involves in treating water with softening chemicals at 80 to 150oC.
(a) Speed of reaction increases.
(b) The softening process is also increases at several folds.
(c) No coagulants took place as the precipitate and formed sludge settled down rapidly.
(d) The most dissolved gases driven out of water.
(ii) Zeolite or pemutits process: Zeolite is hydrated sodium alumina silicate, capable of exchanging its sodium ions for hardness-producing ions in water. They are also known as the Permutits. Chemical structure of sodium zeolite:
Na2O.Al2O3.xSiO2.yH2O
Where, x=2-10 and y=2-6
The hard water is percolated at a specified rate through a bed of zeolite present in the cylinder. The hardness causing ions are retained by zeolite as CaZe and MgZe; while the outgoing water contains sodium salts.
Boiler: The closed vessels in which fluid is heated that result in vapour formation this vapour exist boiler in order to attain various process or heating applications. Eg. Water heating, central heating, boiler-based power generation, cooking, sanitation. The boiler consists of two principal parts: the furnace, which provides heat, usually by burning a fuel, and the boiler proper, a device in which the heat changes water into steam. The steam or hot fluid is then recirculated out of the boiler for use in various processes in heating applications.
The water circuit of a water boiler can be summarized by the following pictures:
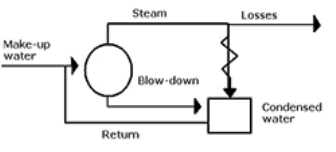
Sludge & Scale: The water evaporates continuously and the dissolved salts concentration increases progressively. When their concentrations reach at saturation point, they are thrown out of water in precipitate form which get stick in inner walls of boiler. If the precipitation takes place in the form of loose or slimy precipitate it is called sludge. While if the precipitated matter forms a hard-adhering coating on inner walls of boiler, then it is called as scale. Eg- MgCO3, MgCl2, MgSO4 etc.
Priming & Foaming: The duration at which boiler is producing steam rapidly, some particles of the condensed liquid are carried along with the steam. The process of wet steam formation is called priming. Priming is mainly caused by the presence of large amounts of dissolved solids, high steam velocities, sudden boiling etc. Whereas the continuous production of foam or bubbles in boilers which do not break easily are called as the foaming. This is caused due to the presence of substance like oils in water that reduce the surface tension in water.
Caustic Embrittelment: The use of high alkaline water in the boiler cause rust in the boiler which is called as Caustic Embrittelment. The presence of sodium carbonate plays a major role during the softening process.
Na2CO3 + H2O → NaOH + CO2
the caustic embrittelment is caused by using sodium phosphate as a softening agent instead of sodium carbonate.
Boiler Corrosion: The decay of the boiler material by attack of chemicals or electro-chemicals at its environment is called as boiler corrosion.
Reasons of boiler corrosion:
(i) Dissolved Oxygen
(ii) Dissolved Carbon di oxide
(iii) Acid from dissolved salts
Sludge, scale, priming and foaming, caustic embrittlement, boiler corrosion are collectively known as boiler troubles.
Processes :-
- When a boiler is steaming (i.e producing steam ) rapidly some particles of liquid water are carried along with the steam . This processes of wet stram formation is called priming.
- Priming is caused by :-
- The presence of large amount of dissolved solids
- High steam velocites
- Sudden boiling
- Improper boiler design
- Sudden increase in steam production rate
3. Foaming :-
- It is the production of persistent foam or bubbles in boilers which do not break easily.
- Foaming is due to presence of substance like oils ( which greatly reduce the surface tension of water )
4. Priming and foaming usually occur togther. They are objectionable because:-
- Dissolved salts in boiler water are carried by the wet steam to super – heater and turbine blades where they get deposit as water evaporates . This deposite reduce their efficiency.
- Dissolved salts may entire in the parts of other machinery where steam is being used there by decreasing the life of the machinery.
- Actual height of water column Cnnot be judge property there by making the maintance of boiler pressure becomes difficult.
Priming can be avoided by :-
- Fitting mechinical steam puritires
- Avoiding rapid change in steaming rate
- Maintaning low water levels in boilers
- Efficent softening and filteration of boiler – feed water
Foaming can be avoided by ;-
- Adding anti – foaming chemical like castor , oil or
- Removing oil from boilerr water by adding compounds like sodium aluminate.
Sludge formation , scale formation
- In boiler water evaporates continously and the concentration of salts left behind goes on increasing . After the saturation point they get precipitated.
- If the precipitate remains in boiler tube as loose and slimy matter is called sludge.
- If some of the precipitated matter adhers strongly and forms strong bad conducting layer on their inner side of boiler tube , then it is known as scale.
Sludge :-
( formation of sludge )
- The loose slimy mass of salts precipitated in boiler water is the sludge.
- They are generally formed at cooler portion of boiler and they loosely deposit in the parts of boiler tube where flow rate is slow e.g vlves bends
- Sludges are easy to remove by using brushes detergent solutions blow down opreation e.t.c .
Disadvanatages of sludges :-
- They tend to waste some portion of heat.
- Edcessive sludge formation distrub working of boiler and sometimes may choke up the pipe .
Prevention of sludges :-
- Use of water contaning very low quantity of total disolved solids.
- Frequently making blow down opreation i.e replacing salts concentrated water with fresh water.
Scales
A] formation of scales :-
Scale is the hard and strongly adhered coating to the inner surface of boiler and it is a bad conductor of heat. It is the main source of boiler trouble.
It is caused due to :-
- Decomposition of bicarbonates :-
At high temprature bicarbonates decompose into sticky water insolube material.
Ca ( HcO3)2 ----------------- CaCO3 + H2O + CO2
Mg ( HCo3)2 - - -------------- Mg (Oh)2 + 2CO2
2. Hydrolsis of magnesium salts :-
At higher temprature magnesium salts undergo hydrolysis.
MgCl2 + 2H2O ---------------------- mg ( OH)2 + 2HCl
3. Presence of silica :-
The source of ssilica is ( form) from sand and filter .silica may be in the form of colloidal particles. And it can be deposite as calcium silicate or magnesium silicate as firmly adhering materials.
4. Decreased solublity of CaSO4 :-
CaSo4 has lesser solublity at higher temprature hence at high temprature CaSo4 present in boiler feed water will precipitate as hard scale forming materials.
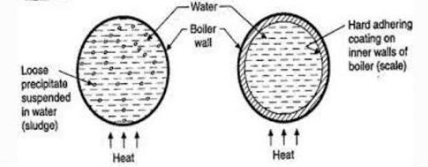
B] Disadvantages of scale :-
1. Waste of fuel :-
Scales are bad conductors of heat and resultes in the reduction of heat transfer to the boiler . Higher the thickness of scale greater than the wastage of fuel there by . It has been reported that 0.25 cm . Scale would increase fuel consuption by aboyut 2 to 3 percent.
Thickness of scale | 0.325 mm | 0.625mm | 1.25mm | 2.5 mm |
Wastage of fuel | 10 percent | 15 percent | 50 percent | 80 ercent |
3. over heating of boiler :-
Scale being pooe conducter of heat it reduces transfer of heat from boiler to boiler water . To keep the required steam pressure we need to overheat the boiler .
4. boiler saftey :-
Due to the scale formation the overheating of boiler is done in order to maintain constant stream supply with required pressure . This overheating makes boiler metal to become soft and weak . This cause distortation of boiler tube and becomes dangerous in morden high pressure boiler .
5. Danger of Explosion :-
When thick scale cracks due to uneven expansions the water come suddenly suddenly in contact with the overhead boiler metal. This cause large amount of steam formation suddenly and sudden high pressure is developed . Due to sudden high pressure is devloped . Due to sudden high pressure the softer boiler metal may burst with explosion.
C] Removal of scales :-
Scales are removeed from time by different ways.
- By use of suitable chemicals the scale can be dissolved and removed.
- Use of scraper or wire brush for thin scales to remove.
- Thick s ales may br removed by hammer and chisle.
- The thermal shocks technique is used to remove hard brittle scale . In this method empty boiler is heated and cooled by cold water suddenly . While sudden cooling the contracting boiler metal excerts pressure on scale to crack them.
- Blow down opreation used if scales are loosely adhering.
D] prevention of scales :-
It is better to minimize scales formation and reduce the problems in steam generation.
- Use of softened water.
- Adding sodium phosphate to the water
- Frequent blow down operations to remove the scales when they are thin.
- Adding sodium aluminate which can trap the scale forming particles.
- Adding organic chemicals like tannin which forms coating on the scale forming particles . This matter becomes easily removable by blow down operation.
DIFFRENCE BETWEEN SLUDGE AND SCALE
Sludge | Scale |
Sludge is loose deposite of slimy matter | Scale is hard coating |
Sludge is less adherent on boiler metal and can br removed by brushes detergents | Scale is strongly adhered to boiler metal and difficult to remove |
Heat transfer to boiler water is affected slightly | Being bad conductor heat transfer to boiler water is affected largely |
Sludge form at coller parts and flow rate is low | Scale is formed at hotter parts |
Sludge may lead to choking | Scale may lead to bluging of metal tube its bursting explosion |
Softening methods :-
Water used for industrial purpose ( such as for steam generation) should be sufficiently pure it should be therfore be freed from hardness producing salts before put to use the processes of removing hardness producing salts from water is known as softening water is known as softening of water . In industry main three methods employed for softening of water are
- Ion exchange or de ionisation
- Zeolite
- Lime soda processes
- Ion exchange or de ionization or de mineralization ion exchange resins are insoluble cross linked long chain organic polymers with a microporous structure and the functional group attached to the chains are responsible for the ion exchange properties resins contaning acidic function groups are capable of exchaning their anions with other anions which comes in their contact the ion exchange resins may be classified as :-
Cation exchange resins ( RH+) :-
They are mainly styrene divinly benzene co-polymers which on sulphonation or carbonoxylation become capable to exchange their hydrogen ions with the cations in the water.
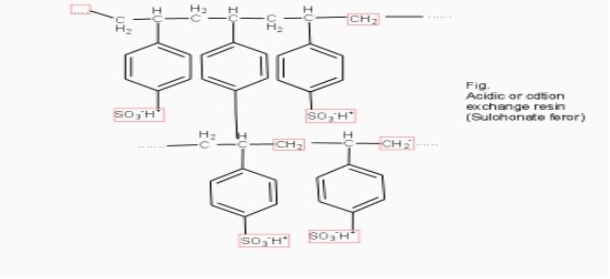
2. Anion exchange resins :-
They are styrene – divinly benzene or amine fermaldehyde which contain amino or quaternary ammonium or4 quaternary phosphonium or tertiary sulphonium group as an integral part of the resin matrix.these after treatment with dilute NaOH solution become capable to exchange their OH- anions with anions in water .
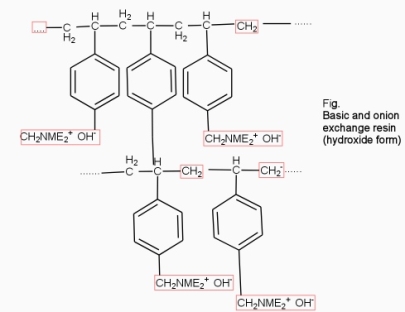
Processes :-
The hard water is passed first through cation exchange column which removes all the cations like Ca²+ , Mg² + e.t.c . From it and equivalent amount of H+ ions are released from this column Water
2RH+ + Ca².+ ---------------------- R2Ca2+ + 2H
2RH+ Mg2+ --------------------------- R2Mg2+ 2H+
After cation exchange column the hard water passed through anion like cl- . Present in the water and equivalent amount of OH- ions are released from this column to water,



H+ And OH – ions ( released from cation exchange and anion exchange columns respectively ) get combined to produce water molecule.
H+ + OH - -- ----------------- H2O
Thus,
The water coming out form the exchanger is free from cations as well as an ions . Ion free water is known as de mineralizes water.
Regeneration :-
When capacities of cation and anion exchangers to exchange H+ and OH- ions respectively . Are lost they are then said to be exhausted.
The exhausted cation exchange column is regenerated by passing a solution of dil.HclH2SO4. The regeneration can be represented as
------------------------
( washing )
The column is washed with deionized water and washing ( which contains Ca2+ and Cl2- ions ) is passed to sink or drain.
The exhausted anion exchange column is regenerated by passing a solution of dil. NaOH.
The column is washed with deionized water and washing ( which contains NA+ and ions ) is pass to sink or drain.
The regenerated ion exchange ion exchange resins are then used again.
Advantages :-
- The processes can be used to soften highly acidic or alkaline waters.
- It produces water of very low hardness ( say 2 ppm ) so it is very good for treating water for use in high pressure boilers.
Disadvantages :-
- The equipment is costly and more expensive chemicals are needed.
- If water contains turbidity, then the out- put of the processes is reduced .the turbidity must be below 10 ppm if it is more it has to be removed first by filtration.
Mixed – bed deionizer :-
Consist essentially of a single cylinder containing and intimate mixture of hydrogen exchanger and strongly basic an ion exchanges when water is passed through this bed it comes in contact a number of times with the two kinds of exchanger alternative consequently the net effect of mixed bed exchange is equivalent to passing water through a series of several cation and anion exchangers .the outgoing water from the mixed – bed contains even less than 1 ppm of dissolved salts.
Regeneration :-
When the resins are exhausted the mixed bed is back – washed ( by forcing water in the upward direction ) when the lighter anion exchanger get displaced to form an upper layer above the heavier cation exchanger ( shown in fig ) thereafter the anion exchanger is regenerated by passing caustic soda solution from the top and then rinsed the lower cation exchanger bed is then regenerated by the H2SO4 solution treatment and then mixed again by forcing compressed air . The bed is ready for use again.
- It is a type of corrison caused by high concentration of sodium hydroxide in boiler water sodium carbonate hydroxide in the boiler and extent of hydrolysis increases with temprature.
Na2CO3 + H2O ----------------- 2Na.OH + CO2
2. Sodium hydroxide reacts with metal ion to form ion to form iron oxide and hydrogen.
3. When metral oxide coating cracks, chemical attack continues into metal along grain boundaries . Through the cracks , water flows , wwhen it evaporates sodium hydroxide is left there.
4. This attack iron of boiler.
5. This type of corrision of boiler parts particularly at stress parts caused due to chemical of caustic soda ( NaOH) Is called as embrittlement.
6. During water softening by soda – limes , processes Na2CO3 is added to water as precipitant . Caustic embrittlement can be prevented by addition lignins or tannos which help in blocking of hair cracks.
Chemical structure of sodium zeolite may be represented as Na2O. AL2O3. XSIO2.Y.H2O where x=2-10 and Y=2-6 zeolite is hydrated sodium aluminum silicate capable of exchanging reversibility its sodium ions for hardness producing ions in water zeolites are known as zeolite. Zeolite are also known as permutits.
Zeolite are of two types
- Natural zeolites :- are non – porous for example natrolite Na2O3.
- Synthetic zeolites: - they are prepared by heating together china clay and soda ash. Such zeolite possesses higher exchange capacity per unit weight than natural zeolites.
Processes :-
For softening of water by zeolite processes hard water is percolated at a specified rate through a bed of zeolite kept in a cylinder (shown in fig.)
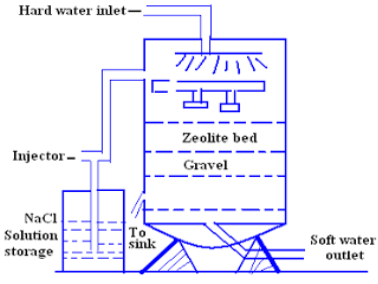
The hardness causing ion are retained by the zeolite as caze and MgZe while the out-going water contain sodium salts reaction take place during the softening processes are
Ca
Mg
Ca
M
Regeneration-
After some time, the zeolite is completely converted into calcium and magnesium zeolite and it ceases to soften water,i.e. it gets exhausted.
At this stage the supply of hard water is stopped and the exhausted zeolite is reclaimed by treating the bed with a concentrated ( 10 percent ) brine ( NaCl ) solution.
The washings ( containing CaCl2 and MgCl2 ) are led to drain and the regenerated zeolite bed thus obtained is used again for softening purpose.
Limitations of zeolite processes :-
- If the supply of water is turbid the suspended matter must be removed (by coagulation, factorization, etc.) before the water is admitted to the zeolite bed , otherwise the turbidity will clog the processes of zeolite bed there by anking it inactive.
- If water contains large quantities of colored ions such as Mn2+ they must be removed first because these ions produce manganese and iron zeolite which cannot be easily regenerated.
- Mineral acids if present in water destroy the zeolite bed and therefore they must be neutralized with soda before admitting the water to the zeolite softening plant.
Advantages of zeolite processes:-
- It removes the hardness almost completely and water of about 10 ppm hardness is produced
- The equipment used is compact occupying a small space
- No impurities are precipitated so there is no danger of sludge formation in the treated water at later stage
- The processes automatically adjust itself for variation in hardness of incoming water
- It is quite clean
- It requires less time for softening
- It requires less skill for maintenance as well as operation
Lime Soda Process:
Lime Soda process is majorly used in softening up of water. On adding up of lime [Ca(OH)2] and soda (Na2CO3) to hard water then present soluble calcium and magnesium in hard water are converted into insoluble compounds like CaCO3 which is precipitated by filtration.
To proceed with solving the lime soda numerical following steps must be taken in notice:
(i) The analysed impurities unit must be in ppm
(ii) On calculating lime and soda requirements the remaining substance that does not contribute in hardness must be ignored.
(iii) If the impurities are given as CaCO3 these should be considered to be due to Ca(HCO3)2 and it is only expressed in terms of CaCO3.
(iv) The amount expressed must be in CaCO3 form else other chemical can be converted in this form on multiplication with 100/84.
(v) Lime and Soda requirement can be calculated as:
Lime required for softening
=74/100*{Temporary calcium hardness + (2*Temporary magnesium hardness) + Permanent Mg hardness + CO2 + HCl + H2SO4 + HCO3 + salts of Fe2+}*Vol. Of water
Soda required for softening
=106/100*{Permanent calcium hardness + Permanent Mg Hardness + Salts of Fe2+, Al3+ + HCl + H2SO4}*vol. Of water.
Question:
Calculate the amount of lime and soda required for softening of 10000 litres of water, which on analysis gave the following results.
Mg2+ = 12 ppm, Ca2+ = 40 ppm, HCO3 = 164.7 ppm, CO2 = 30.8 ppm
Solution:
Constituent | Amount(ppm) | Multiplication factor | CaCO3 (ppm) |
Mg2+ | 12.0 | 100/24 | 12*100/24=50 |
Ca2+ | 40.0 | 100/40 | 40*100/40=100 |
HCO3 | 164.7 | 100/61 | 164.7*100/122=135 |
CO2 | 30.8 | 100/44 | 30.8*100/44=70 |
CaCO3 Calculations
Lime Requirement =74/100(Bicarbonate hardness + Mg2+ + CO2)
=74/100(135+50+70)
=74/100*255
=74*2.55 mg/lt.
1 Litre of water require 74*2.55 mg/lt
10000 lt of water =74*2.55*10000
=74*2.55*10000/1000*1000
=1.887 kg
Soda Requirement =106/100(Ca2+ + Mg2+)
=106/100(100+50)
=159 mg/lt
Soda required for 10000 lt. Of water
=159*10000
=159*10000/1000*1000 kg
=1.59 kg
Numerical based on Zeolite Process:
Question:
1000 litres of hard H2O is softened by zeolite process. The zeolite was regenerated by passing 20 litres of sodium chloride solution containing 1500 mg/lit. Of NaCl. Calculate hardness of H2O.
Solution:
20 litres of NaCl contain = 1.5 * 20 = 30 gm of NaCl
We have to convert it in terms of CaCO3 equivalent.
2 NaCl = CaCO3
2* 58.5 gm = 100 gm
58.5 = 50 gm
Thus, 30 gm of NaCl equivalent to 30*50/58.5 gm of CaCO3
10,00 litres of H2O contains 30*50/58.5 gm of NaCl as CaCO3
1 litre of H2O contains 30/1000*50/58.5 gm of NaCl as CaCO3
Thus, 1 litre water contains = 30/1000*50/58.5*1000 mg of NaCl as CaCO3
= 25.64 mg 1 litres
Desalination: The process of converting up of saline water into fresh water by removing of salts and minerals from the target source is called as the Desalination. Saltwater is desalinated to produce water suitable for human consumption or irrigation. The by-product of the desalination process is brine. Desalination is used on many seagoing ships and submarines. Most of the modern interest in desalination is focused on cost-effective provision of fresh water for human use. Along with recycled wastewater, it is one of the few rainfall-independent water sources.
Desalination using electro dialysis:
The passing up of direct current through the water in order to drive the ions through membranes to electrodes of opposite charge. The common techniques which applied the electro dialysis principle is electro dialysis reversal (EDR). This system uses ion transfer anion and cation membranes to separate the ions in source water. This membrane allows the unidirectional transfer of ions of given charge through them. E.g.- the cation transfer membranes allow only positive charge ions to pass.
Desalination using reverse osmosis:
Reverse osmosis is a process where the water is separated from the salts in the source water by pressure-driven transport through a membrane. This process uses semi-permeable membrane and applied pressure to preferentially induce water permeation through the membrane while rejecting salts. The RO plant uses less energy than thermal desalination process. This process uses thin-film composite membrane that too comprises of ultra thin aromatic polyamide thin film. The used polyamide film gives the transparent properties while the remaining part provides the mechanical supports. The polyamide films are very dense void free polymer with high surface area allowing for its high permeability. RO desalination plant include source water intake system, pretreatment facilities and high pressure feed pumps, RO membrane trains, energy recovery and desalinated water conditioning system. The intake system may be the open surface water intake or series of seawater beach wells. The pretreatment system may be the screening, chemical conditioning, sedimentation or filtration that totally depends on the used quality water further the filtered water is conveyed by transfer pump from filtrate water storage tank through cartridge filter and into the suction pipe of high pressure RO feed pumps. The cartridge filters are designed in such a manner that can retain 1 to 20 microns particles which remained in the source water after pretreatment. The high pressure feed pumps are designed to deliver the source water to the RO membranes at pressure required for membrane separation of the fresh water from the salts. The actual required feed pressure is site-specific and is mainly determined by the source water salinity and the configuration of the RO system.
Introduction:
The water discharged from houses, industries, institution etc are contaminated with chemicals and other substances are called as the waste water. The process of removing up of water contaminants from waste water or sewage in order to get the effluent water which can be returned into water cycle or can be used for various other purposes. This type of treatment took place in waste water treatment plant (WWTP) or sewage treatment plant. An average of 200 to 500 liters of wastewater is generated for every person connected to the system each day. The amount of flow handled by a treatment plant varies with the time of day and with the season of the year. Type of treatment plants:
(i) Industrial waste water Treatment Plant
(ii) Leachate Treatment Plant
(iii) Agricultural waste water treatment Plant
(iv) Sewage Treatments Plant
Industrial waste water treatment Plant:
The waste water released from industrial plant carry impurities with it, it become very difficult and very costly to dispose them. Most of the industries have their onsite facility to treat the water and convert into pure and usable forms. Constructed wetlands are used in an increasing number of cases as they provide high quality and productive on-site treatment.
Leachate Treatment Plant:
These plants are used to treat leachate from landfills. It includes biological treatment, mechanical treatment by ultra-filtration.
Agricultural waste water treatment Plant:
Agricultural waste water are highly contaminated, meaning they cannot be disposed directly without treatment. If they are disposed incorrectly, agricultural wastewaters run the risk of eutrophication of surface and ground waters and can impose significant trade waste charges. E.g Reedbed Technology which provides an ideal solution for all types of agricultural wastewaters, including those with high nutrient and contaminant loads.
Sewage Treatments Plant:
The waste water collected from municipal’s mainly consisting of sewage and industrial wastewater is highly contaminated. There are many different processes used to remove the contaminations that may be the physical, chemical or biological process to make safe and favorable to be released in environment. A by-product of sewage treatment is a semi-solid waste or slurry, called sewage sludge. The sludge has to undergo further treatment before being suitable for disposal or application to land.
Importance of waste water treatment:
Clean water is one of the most important natural resources present in the planet. Waste water contains much harmful substance in it therefore it cannot be released in the environment directly. This waste water contains many harmful microbes which is very harmful for direct use.
Restoring the water supply:
Look at a global drought map and you will see that many areas of the world simply do not have enough water. All communities, especially areas with water scarcity, need to ensure they have good water treatment processes in place so that treated water can either be reused or returned to the water cycle, but never wasted.
Protecting the Planet:
Waste water can include contaminants from both residential and commercial use. Untreated, the chemical compounds and pathogens in wastewater can harm the health of animals, plants and birds that live in or near the water. It can also contaminate crops and drinking water, affecting human health. Wastewater treatment is fundamental to protect the health of many different ecosystems.