UNIT 2
Corrosion Science
Corrosion: -
The destruction of metal by chemical or electrochemical attack of environment this process starting at the surface of metal known as corrosion. Corrosion is the two step process that requires three things i.e., a metallic surface, an electrolyte and oxygen. In the process of corrosion a metal atom at surface dissolve into an aqueous solution leaving the metal with excess negatively charged ions. These resultant ions are removed by a suitable electron acceptor. Corrosion can be thought of as the spontaneous return of metals to their ores through the process of oxidation.
Causes of Corrosion:
Corrosion is the electrochemical process that occurs in various forms such as chemical forms and atmospheric forms. On the contact of acid substance with iron it pretend to form rust. Rust is the result of corroding steel after the iron (Fe) particles have been exposed to oxygen and moisture. When steel is exposed to water, the iron particles are lost to the water’s acidic electrolytes. The iron particles then become oxidized, which results in the formation of Fe⁺⁺. When Fe⁺⁺ is formed, two electrons are released and flow through the steel to another area of the steel known as the cathodic area.
Oxygen causes these electrons to rise up and form hydroxyl ions (OH). The hydroxyl ions react with the Fe2+ to form hydrous iron oxide, better known as rust. Where the affected iron particles were, has now become a corrosion pit, and where they are now, is called the corrosion product (rust).
Consequences of corrosion:
Corrosion has many consequences on economic, health, safety, to our society.
Economic Effects: To determine the economic cost on the country’s economy there are several studies conducted by different country. Among all the most extensive study was carried out by United State in 1975 and gathered that it cost about $70 billion.
Health Effects: Recent years have seen an increasing use of metal prosthetic devices in the body, such as pins, plates, hip joints, pacemakers, and other implants. New alloys and better techniques of implantation have been developed, but corrosion continues to create problems. E.g.- inflammation caused by corrosion products in the tissue around implants, fracture of weight-bearing prosthetic devices.
Technological effects: Technology sector is also very badly affected by the corrosion. A great deal of the development of new technology is held back by corrosion problems because material is required to withstand in many cases simultaneously higher temperature, higher pressure. Corrosion problems that are less difficult to solve affect solar energy systems, which require alloys to withstand hot circulating heat transfer fluids for long periods of time, and geothermal systems, which require materials to withstand highly concentrated solutions of corrosive salts at high temperatures and pressures.
Electrochemical:
The deterioration of materials by chemical process is called as corrosion. In electrochemical corrosion M→M+ + e- is facilitated by the presence of suitable electron acceptor and some time it is also called as depolarizer. Corrosion can also be viewed as the spontaneous return of metals to their ores, the abandoned amount of energy used that were consumed in the mining, refining into useful objects is dissipated by variety of different routes.
Corrosion Cells and reactions:
The occurrence of oxidation and reduction steps in corrosion results in separation of metal’s location. This can be possible due to the conductive property of metal, so that electrons can flow through metal form anodic to cathodic regions. The water presence plays a major role on transportation.
Fe → Fe2+ + 2e-
The metal is under pressure or is isolated from the air. The metal ions dissolve in the moisture film and e- migrates to another location.
The anodic process is
Fe(s) → Fe2+ (aq) + 2e-
While cathodic steps involve the reduction of oxygen gas
O2 + 2H2O(aq) + 4e- → 4OH-
Or the proton reduction
H+ + e- → ½ H2(g)
Or the reduction of metal ion
M2+ + 2e- → M(s)
Since both the cathodic and anodic steps must take place for corrosion to occur, prevention of either one will stop corrosion. The most obvious strategy is to stop both processes by coating the object with a paint or other protective coating. Even if this is done, there are likely to be places where the coating is broken or does not penetrate, particularly if there are holes or screw threads. A more sophisticated approach is to apply a slight negative charge to the metal, thus making it more difficult for the reaction to take place:
M⟶M2++2e−.
Galvanic Series: Galvanic series relationships are useful as a guide for selecting metals to be joined, will help the selection of metals having minimal tendency to interact galvanically, or will indicate the need or degree of protection to be applied to lessen the expected potential interactions. In general, the further apart the materials are in the galvanic series, the higher the risk of galvanic corrosion, which should be prevented by design. Conversely, the farther one metal is from another, the greater the corrosion will be. However, the series does not provide any information on the rate of galvanic corrosion and thus serves as a basic qualitative guide only.
(i) Nature of metal
Position of metal in galvanic series.
If position is higher in galvanic series then it corrode faster
While for 2 metal the difference between them shows the corrosion ratio.
(ii) Potential Difference
If the difference at the electrode potential between two metal is high then the rate of corrosion would be also high while vice versa for lesser difference.
(iii) Purity of metal
Corrosion never took place in pure metals. While if metal itself has a impurity then galvanic cell set up easily which intend increases the rate of corrosion.
(iv) Relative areas of cathode and anode parts
Rate of corrosion is directly depends on the area of cathode and inversely depends on the area of anode. If the area of cathode is larger then there is more demand of electrons while in the smaller anode area the corrosion took place very fast.
(v) Nature of corrosion Product
Metal oxide film is formed on the surface of metal by corrosion due to oxygen. The formed film would be stable, unstable, volatile.
(vi) Temperature
At high temperature the rate of corrosion increases as because there is a consistent increase in the ionization and mobility difference rate while in some cases rate of corrosion decreases at high temperature as the solubility of O2 gas increases.
(vii) Presence of moisture
The rate of corrosion decreases in dry while increases in presence of moisture. Moisture act as the solvent for setting up of electrochemical corrosion.
(viii) Effect of pH
Rate of corrosion is high at acidic pH due to the evolution of H2 gas at cathode.
(ix) Concentration of electrolytes
This is also called as the Oxygen concentration cell. The rate of corrosion would be directly depend on the supply of oxygen on air.
(x) Over Voltage
The difference between the actual value and theoretical value of decomposition potential of electrode.
Chemical Corrosion: The reaction of metal with water vapour or gas at high temperature causes the metal to corrode chemically. This is the redox process in which the electron of the metal are passed directly to the substance in the environment. The metal corrodes generally in the metal which is in higher contact with water.
3Fe + 4H2O Fe3O4 + 4H2
3Fe + 2O2 Fe3O4
Electrochemical Corrosion: Corrosion occurs due to the electrochemical process of oxidation and reduction process. In the corroding solution electrons are released by the metal and that is gained by the elements in the corroding solution. The release of electron from metal is called as the oxidation while vice-versa that is gain of electron by elements is reduction. The regular electron flow in the corrosion reaction can be measured and controlled electronically. This is why controlled electrochemical experimental methods are used to characterize the corrosion properties of metal.
For example,
(i) a thin film of moisture on a metal surface forms the electrolyte for atmospheric corrosion.
(ii) when wet concrete is the electrolyte for reinforcing rod corrosion in bridges. Although most corrosion takes place in water, corrosion in non-aqueous systems is not unknown.
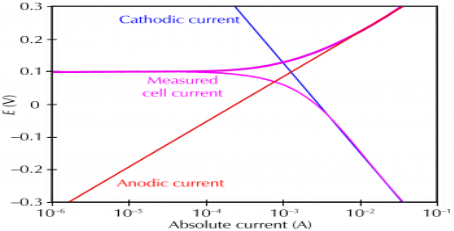
Corrosion process showing the anodic and cathodic component of current
Mechanism of dry corrosion due to o2 gas there are 4 types: -
- Absorption of oxygen molecules on the metal surface
- Dissociation of oxygen atom into metal atom
- Loss of e- by metal atom
- Formation of oxide layer on the metal surface.
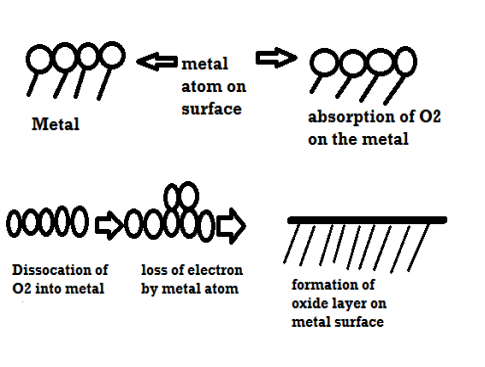
4 types of oxide layers: -
- Porous oxide layer (non – protective): -
- If the oxide layer is porous then through pores – penetration of o2 gas taking place and metal get corroded.
e.g.: - fe,Mg,Na,K,Ca, etc.
Reaction: - 2fe + o2 – 2feO
2Mg + o2 – 2MgO
2. Non – porous oxide layer (protective): -
- If the oxide layer is stable non – porous strong then further corrosion of metal will be stopped.
e.g.: - chromium, nickel, Sn (tin),lead, aluminium, zinc, bronze, various metal alloys .
Reaction: - 1. 2AL + O2 – AL2O3
3. Unstable oxide layer: -
- When oxide layer is unstable, and it decomposes back into metal and o2 gas then there is no corrosion of metal taking place.
e.g: -Ag,AU, Pt.
4. Volatile oxide layer: -
- If the oxide layer is volatile, then its evaporation taking place the under lying metal gets exposed for further attack of o2 gas and corrosion taking place.
- e.g: - MO2O3 (molybdenumoxide)
Dillingbedworth rule / ratio (PBR)
- This rule gives an idea about nature of oxide film, whether it is porous or nonporous.
- The rule states that,Metal ‘if the volume of oxide < volume of metal consumed
Then,
Oxide layer – porous
Else, oxide layer – nonporous
PBR =
If, PBR > 1 but PBR < 1.45
Metal oxide layer – nonporous(protective)
B] Mechanism of dry corrosion due to other gases: -
a) Dry corrosion due to chlorine: -
Reaction: - 1. 2Ag + Cl2 – 2AgCl
Agcl forms thin protective (non-porous) layer on the metal surface.
Non corrosion taking place
Sn + 2cl2 – SnCl4
SnCl4 forms thin, non-protective layer on the metal surface
Corrosion taking place
b) Due to So2: -
- Sulphur oxide is produced due to combustion of fossil fuels. When So2 attacks on metallic surface in the form of H2So4, corrosion of metal taking place.
Reaction: - SO2 + H2O – H2SO3
SO2 + H2O ½ O2 – H2SO4
c) Due to oxides of nitrogen: -
- Oxides of nitrogen are produced due to combustion of fuels it forms HNO3 which cause corrosion of metal.
Reaction: - NO2 + O3 – NO3 + O2
NO 2 + NO3 – N2O5
N2O5 + H2O – 2HNO3
d) Decarburisation: -
- The processes of removal of carbon of carbide from the metal by action of hydrogen at higher temperature is called as decarburisation.
e) H2 embrittlement: -
- Breaking of metal at the weekend region by hydrogen accumulation in metal called as H2 embrittlement.
f) Presence of co2: -
- Due to co2 formation of h2co3 taking place and it reacts with metal to occur corrosion.
H2O + co2 – H2CO3
Fe + CO2 – FeO + CO
EMF series and galvanic series
EMF series | Galvanic series |
|
|
|
|
|
|
|
|
|
|
|
|
|
|
2) wet corrosion: -
- The corrosion occurs due to aqueous conducting medium with the formation of anodic and cathodic areas.
2types: -
A) Galvanic cell wet corrosion
B) Conc. Cell wet corrosion / differential wet corrosion
Galvanic cell wet corrosion: -
- It occurs due to aqueous conducting medium with the formation of galvanic cell.
Conc. Cell wet corrosion: -
- It occurs due to aqueous conducting medium with the formation of conc. Cell due to variation of oxygen conc. Metal.
Possibilities: -
- Two dissimilar metal
- Stressed and unstressed part
- Presence of impurities in the metal
Possibilities: -
- Partial part of metal dipped in water.
- Partially buried part of metal in ground.
- Crevices
- Partially oxide layer on metal surface
The uneven supply of oxygen to the same metal component leads to the formation of oxygen concentration cells that is called as the differential aeration theory of corrosion. It is the type of electrochemical corrosion that affects the metals such as steel and iron. The less oxygenated part behaves anodic while the more oxygenated part cathodic. Since cathodic reactions involve consumption of oxygen, the more oxygenated part behaves cathodic and less oxygenated pan behaves anodic. The reaction occurs because oppositely charged electrons flow between the smaller anode and larger cathode. Positively charged cations meeting negatively charged anions forming corrosion product and a resulting pit in the metal, otherwise known as pitting corrosion. In a gutter, pipe, tank or similar the anode is just below the waterline. This is where the oxidation occurs, corrosion product forms and a pit develops weakening the metal.
There are several types of corrosion:
(i) Galvanic Corrosion: Galvanic corrosion is the most common corrosion which can be get in notice. This corrosion occurs when two different type of metals are in contact with each other in the presence of electrolyte. In this type of corrosion noble metal are safe while the active metals corrodes.
(ii) Pitting Corrosion: This type of corrosion occurs at certain conditions, there is a accelerated corrosion in some areas rather than the uniform corrosion over the substance. This condition includes low level of concentration of oxygen or high concentration of chlorides.
(iii) Microbial Corrosion: Microbial Corrosion is caused by micro-organisms. They commonly referred to as microbiologically influenced corrosion. It applies to both metallic and non-metallic materials with or without oxygen. In the presence of oxygen there are some bacteria that directly oxidize iron to iron oxides and hydroxides while in the absence of oxygen sulphate reducing bacteria are active and produce hydrogen sulphide causes sulphide stress cracking.
(iv) High Temperature Corrosion: The deterioration caused on the metal due to heating. This can cause when the metal is kept in hot atmosphere that too in the presence of oxygen, sulphur, or with any other compound which is capable of oxidizing the material.
(v) Crevice Corrosion: This occurs in confined spaces where access of fluid from the environment is limited such as gaps and contact areas between parts, under gaskets or seals, inside cracks and seams and spaces filled with deposits.
Corrosion prevention is the process which aimed at reducing the corrosion rate to a tolerable level. The preventing up of metal substance to get corrodes at its preferable atmosphere. There are many different ways used to retard the corrosion on the surface.
Surface Treatment: On the surface treatment method it requires cares a lot in order to ensure complete coverage, without gaps, cracks or pinhole defects. A minute defect can cause to penetrate the corrosion inside it that lead to the extensive damage to the material.
Controlled Permeability formwork: This is the method in which the corrosion can be controlled by naturally increasing the capability of material to enhance their durability.
Cathodic Protection: Cathodic protection (CP) is a technique to control the corrosion of a metal surface by making that surface the cathode of an electrochemical cell. Cathodic protection systems are most commonly used to protect steel pipelines and tanks; steel pier piles, ships, and offshore oil platforms.
Anodic Protection: It impresses the anodic current on the structure to be protected. It is appropriate for the metals which are suitably small passive current over a wide range of potentials. It is used in aggressive environment such as solution of sulphuric acid.
Material Selection: The selection of the corrosion-resistant alloy would be the best answer for corrosion problem. Cost dictates the selection of material. The most corrosion–resistant metal or alloy may not be always optimum choice because:
High Cost
Low abundance
Difficulty in manufacturing
Unsuitability to meet the engineering requirement
The material selection process is also influenced by whether the material to be used for New design or the modification of existing design.
The designing up of building in order to reduce the effect of corrosion. The following measures can be taken in that would help in trapping the moisture.
- Avoiding the creation of cavities in the structure.
- Grind flush weld on horizontal surfaces
- Avoid using channels with toes upward
- Arranging the angles with vertical leg below the horizontal.
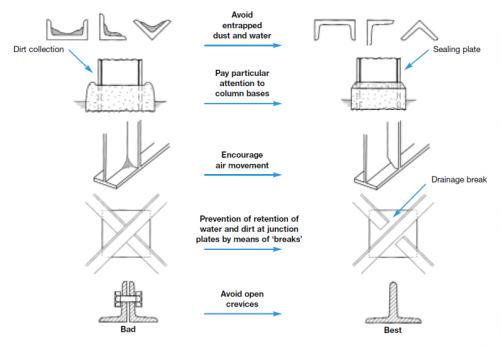
Principle: -
The metal to be protected is forced to behave as cathode.
2 types: -
A) By using sacrificial anode
Methods / processes: -
- The metallic structure to be protected from corrosion is connected to the anodic metal by insulated wire.
- Anodic metal is more reactive like Zn etc.
- Anodic metal corrosion itself but it protects the cathodic metal from corrosion .it is called as sacrificial metal.
- Anodic metal is kept in back fill (mixture of coal and Nacl) to increase electrical contact with surrounding soil.
- When anodic metal consumed completely then it is replaced with fresh piece of metal
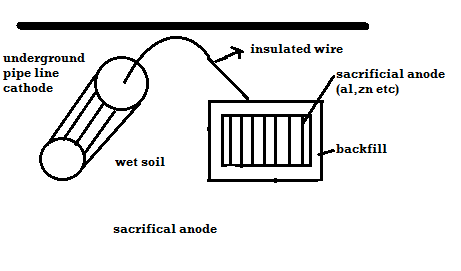
B) By using impressed current: -
Method: -
- In this method an impressed current is applied in opposite to nullify the corrosion current and convert the corroding metal from anode to the cathode.
- The impressed current Is derived from DC source and given to insoluble anode like graphite, stainless steel which buried in soil.
- The –ve terminal of DC source is connected to pipeline to be protected from corrosion.
- Anodic metal is kept in black fill to increase electrical contact with the surrounding soil.
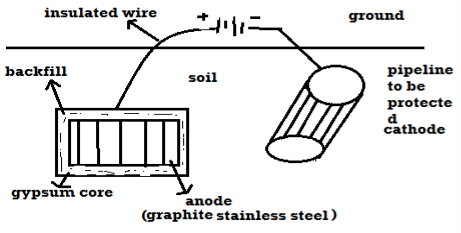
Limitations: -
- Highly investment and maintenance cost
- Special case needs to be taken to see the structure is not over protected otherwise H2 liberation maybe occur.
B] anodic protection: -
Principle: -
A metal or alloy having wider range of passivity vtg, is made anode and the vtg is passivity range is applied over it do control its corrosion even by strong corroding media.
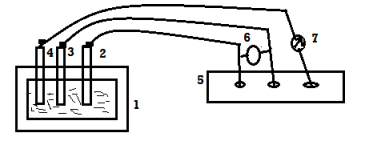
- The metallic installation (reactor,water,tank, water coolers, industrial condensers,etc.) is made anode by using reference electrode and axillary electrode.
- There is a potentiostatfor applying the desired ammeter to watch the corrosion current. The min or negligible current indicates that anodic protection take place successfully if the system goes out of corrosion control, then immediately remove all electrical connection.
Application: -
- Chemical reactors
- Industrial water coolers
- Complex metallic installations on ground or under sea water.
- Industrial metals condensers
- Pipelines for carrying corrosive liquids.
Advantages: -
- Low operating cost
- It is applicable for highly corrosive media
- Suitable to protect complex structures
- Protection current gives anidea about rate of corrosion.
Limitations: -
- High installation cost
- High starting current is req.
- In case system goes out of control then high is the rate of corrosion
It is applicable for only those metals which show active – passive behaviour.
Metallic coating: -
Cleaning methods: -
2 types: -
- Anodic coating
- Catholic coating
Anodic coating: -
Coating metal is higher placed than the base metal then it is called as anodic coatings.
e.g.: -galvanizing
Cathodic coatings: -
If coating metal is lower placed in galvanic series than base metal then it is called as tinning.
Methods of applying metallic coatings: -
- Hot dipping
- Electroplating
- Cementation’
- Metal cladding
Hot dippingprocesses: -
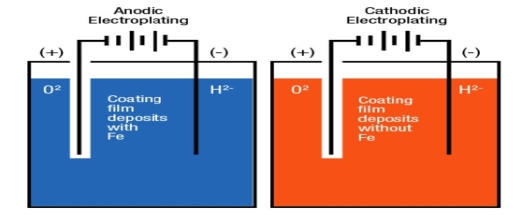