Unit - 2
Energy-II
Petrol is a volatile flammable liquid, that consists of a mixture of hydrocarbons namely heptane, hexane and octane. They are mainly obtained from petroleum and used as a solvent and fuel for internal combustion engines. Petrol also contains additives such as antiknock compounds and corrosion inhibitors.
Elemental Composition of Petroleum
Although there is considerable variation between the ratios of organic molecules, the elemental composition of petroleum is well-defined:
- Carbon - 83 to 87%
- Hydrogen - 10 to 14%
- Nitrogen - 0.1 to 2%
- Oxygen - 0.05 to 1.5%
- Sulphur - 0.05 to 6.0%
- Metals - < 0.1%
The most common metals are iron, nickel, copper, and vanadium.
Classification:
The hydrocarbons in crude oil can generally be divided into four categories:
- Paraffins: These have a carbon ratio of 1:2 and form up to 15 to 60% of crude, the ratio 1:2 means that they contain twice the amount as they do for carbon. They are compounds that are never circular they are either in straight or branched chains. The shorter the paraffins are, the lighter the crude is.
- Napthenes: They are also called as cyclic paraffins, they possess cyclic compounds and have the carbon and hydrogen ratio of 1:2. They form about 30-60% of crude. They are generally more viscous and higher in density than paraffins.
- Aromatics: Burning aromatics form soot hence they are undesirable and form around 3 to 30% of crude. They show much less hydrogen in comparison to carbons that are present in paraffins. They have a much less hydrogen in comparison to carbon than is found in paraffins. They are also more viscous. They may exist in a solid or semi-solid when an equivalent paraffin would be a viscous liquid under the same conditions.
- Asphaltic: The hydrogen carbon ratio is1:1 and form about 6% of the crude, they are dense in nature and undesirable, but their 'stickiness' makes them excellent for use in road construction.
Origin
- They are mainly formed the remains of dead plants and animals.
- When animals and plants usually die, they settle and sink on the seabed.
- Many millions of years ago this wildlife and vegetation decomposed and they mixed with silt and soil.
- Some specific Bacteria act on this decomposed organic matter and caused few chemical changes
- The matter could not be decomposed completely, s there is no sufficient oxygen present in the sea, however matter consisting of largely carbon and hydrogen was left behind.
- The decomposed matter remained on the sea bed and eventually was covered with multiple layers of sand and silt.
- After millions of years, due to high temperature and pressure finally the organic matter decomposed completely and formed oil
Refining of crude oil
In an oil refinery the crude oil is converted into valuable goods such as petroleum, naphtha, gasoline liquified gas, kerosine etc. Oil refineries are usually huge, vast industrial facilities with extensive pipelines running throughout, holding fluid streams in between.
- Many substances are present in petroleum as a mixture, they include lubricating oil, paraffin wax, diesel, gas, wax etc.
- Therefore, it becomes important to separate these substances and use them separately for different purposes, hence they are refined and the process of separation various constituents of petroleum is called petroleum refining.
- It involves a three-step process and usually performed in oil refineries.
- The first step is distillation process, that separates the crude oil from various components. The lighter constituents rise up as vapour or remain as a liquid while the heavier constituents remain at the bottom.
- In the next step the heavier constituents are converted into gas, gasoline and diesel.
- The last step is to remove the impurities in the constituents and obtain the products in pure form. The most common method of separating components into their constituents is by fractional distillation when due to boiling differences in temperature the crude oil heat up, spray and then condense the vapour.
- New methods, in a method called conversion, use Chemical processing on certain fractions to produce others. For example, chemical processing may split lengthier chains into shorter chains. This allows a refinery to convert diesel fuel into gasoline, depending on the gasoline demand.
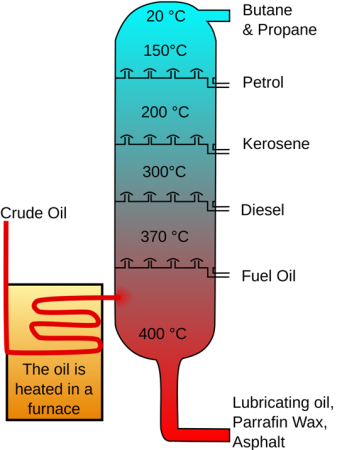
Crude Oil Distillation
Fig.1: Crude oil distillation
In industries, the process of refining is usually called the downstream sector, and the raw crude oil output is called the downstream sector the word downstream is synonymous with the idea of sending oil down the supply chain of a commodity to an oil refinery to be refined into petrol. The downstream also indicates the sale of petrol and its products to other companies and government and private sectors.
Internal combustion engines provide outstanding drivability and durability, with more than 250 million highway transportation vehicles in the United States relying on them. Along with gasoline or diesel, they can also utilize renewable or alternative fuels (e.g., natural gas, propane, biodiesel, or ethanol). They can also be combined with hybrid electric powertrains to increase fuel economy or plug-in hybrid electric systems to extend the range of hybrid electric vehicles.
Working:
Combustion, also known as burning, is the basic chemical process of releasing energy from a fuel and air mixture. In an internal combustion engine (ICE), the ignition and combustion of the fuel occurs within the engine itself. The engine then partially converts the energy from the combustion to work. The engine consists of a fixed cylinder and a moving piston. The expanding combustion gases push the piston, which in turn rotates the crankshaft. Ultimately, through a system of gears in the powertrain, this motion drives the vehicle’s wheels.
There are two kinds of internal combustion engines currently in production: the spark ignition gasoline engine and the compression ignition diesel engine. Most of these are four-stroke cycle engines, meaning four piston strokes are needed to complete a cycle. The cycle includes four distinct processes: intake, compression, combustion and power stroke, and exhaust.
Spark ignition gasoline and compression ignition diesel engines differ in how they supply and ignite the fuel. In a spark ignition engine, the fuel is mixed with air and then inducted into the cylinder during the intake process. After the piston compresses the fuel-air mixture, the spark ignites it, causing combustion. The expansion of the combustion gases pushes the piston during the power stroke. In a diesel engine, only air is inducted into the engine and then compressed. Diesel engines then spray the fuel into the hot compressed air at a suitable, measured rate, causing it to ignite.
Knocking, in an internal-combustion engine, sharp sounds caused by premature combustion of part of the compressed air-fuel mixture in the cylinder. In a properly functioning engine, the charge burns with the flame front progressing smoothly from the point of ignition across the combustion chamber.
Gasoline is a refined product of petroleum consisting of a mixture of hydrocarbons, additives, and blending agents. The composition of gasolines varies widely, depending on the crude oils used, the refinery processes available, the overall balance of product demand, and the product specifications. The typical composition of gasoline hydrocarbons (% volume) is as follows: 4-8% alkanes; 2-5% alkenes; 25-40% isoalkanes; 3-7% cycloalkanes; l-4% cycloalkenes; and 20-50% total aromatics (0.5-2.5% benzene) (IARC 1989). Additives and blending agents are added to the hydrocarbon mixture to improve the performance and stability of gasoline (IARC 1989; Lane 1980). These compounds include anti-knock agents, anti-oxidants, metal deactivators, lead scavengers, anti-rust agents, anti-icing agents, upper-cylinder lubricants, detergents, and dyes (IARC 1989; Lane 1980). At the end of the production process, finished gasoline typically contains more than 150 separate compounds although as many as 1,000 compounds have been identified in some blends.
Cetane number and octane number both are used to measure the tendency of the fuel ignition. The cetane number refers to the ease with which fuel ignites easily at a relatively low temperature. The Research Octane number and Motor Octane number used in determination of a single cylinder test engine in the laboratory while Road Octane Number measures the anti-knock performance in an actual vehicle under road driving conditions. Cetane rating indicates the cold starting ability of diesel fuel that are mostly recommended by the automakers of about 45. High cetane rating means the fuel will ignite easily from heat and pressure and burn quickly.
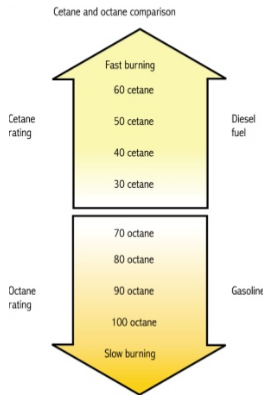
Fig.2 Cetane Rating
Fuel | Research Octane Number | Motor Octane Number | Cetane Number | Boiling Point (oC) |
Ethanol | 107 | 89 | 5 | 79 |
Methane (LPG) | 120 | 120 | 0 | -161.66 |
Diesel | -25 | - | 45-55 | 140-360 |
Gasoline | 92-98 | 80-90 | 0-5 | 37-205 |
Additives in petrol that increase the octane number of petrol by increasing anti-knocking property of petrol are known as known as dope or doping agents. The main function of doping agents in petrol is reduced the combustion rate of the air petrol mixture. The doping agents undergo thermal degradation to form free radicals which reduce combustion rate and increase octane number. Earlier tetraethyl lead (TEL) was predominantly used. Although as the deposit leads in the cylinder and on the spark plug is removed as lead bromide along with exhaust gases. Therefore, nowadays various organic compounds containing oxygen are used as anti-knocking agents to increase anti-knocking properties of the petrol and is known as unleaded petrol.
However, in case of diesel engine knocking is due to the slow combustion rate air diesel mixture initiated due to compression of air. In diesel oils, the doping agents like is amyl nitrate, ethyl nitrite, acetone peroxide etc are used. They provide nascent oxygen at a higher temperature to increase combustion rate and cetane number.
Liquid transportation hydrocarbon fuels and various other chemical products can be produced from syngas via the well-known and established catalytic chemical process called Fischer-Tropsch (FT) synthesis.
Figure 1 shows a simplified block flow diagram of a process incorporating FT synthesis. The gasification island consists of all the supporting process technologies of coal handling & feed preparation, heat recovery, syngas cleanup and conditioning, water-gas-shift, sulphur recovery, etc. The clean syngas leaving the gasification island is sent onto the FT synthesis island, where the clean shifted syngas is converted into primary products of wax, hydrocarbon condensate, tail gas, and reaction water. The wax is sent on to an upgrading unit for hydrocracking in the presence of hydrogen, where it is chemically split into smaller molecular weight hydrocarbon liquids. A hydrogen recovery unit is used to extract the required quantity of hydrogen from the tail gas as shown, or alternatively from the feed syngas stream. The reaction products, along with that from the upgrading section, are fractionated into the final products of diesel, naphtha, and other light ends, depending on the desired product mix. The production facility is supported by several utility plants, including the power train.
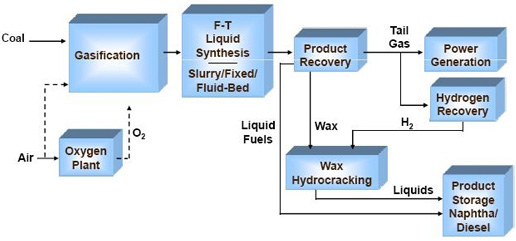
Fig.3: Fisher- Tropsch process
The Fischer-Tropsch process is a catalytic chemical reaction in which carbon monoxide (CO) and hydrogen (H2) in the syngas are converted into hydrocarbons of various molecular weights according to the following equation:
(2n+1) H2 + n CO → Cn H(2n+2) + n H2O
Where n is an integer. Thus, for n=1, the reaction represents the formation of methane, which in most CTL or GTL applications is considered an undesirable byproduct. The Fischer-Tropsch process conditions are usually chosen to maximize the formation of higher molecular weight hydrocarbon liquid fuels which are higher value products. There are other side reactions taking place in the process, among which the water-gas-shift reaction
CO + H2O → H2 + CO2
Is predominant. Depending on the catalyst, temperature, and type of process employed, hydrocarbons ranging from methane to higher molecular paraffins and olefins can be obtained. Small amounts of low molecular weight oxygenate (e.g., alcohol and organic acids) are also formed. The Fischer-Tropsch synthesis reaction, in theory, is a condensation polymerization reaction of CO. Its products obey a well-defined molecular weight distribution according to a relationship known as Shultz-Flory distribution.
Catalysts
Catalysts considered for Fischer-Tropsch synthesis are based on transition metals of iron, cobalt, nickel and ruthenium. FT catalyst development has largely been focused on the preference for high molecular weight linear alkanes and diesel fuels production. Among these catalysts, it is generally known that:
- Nickel (Ni) tends to promote methane formation, as in a methanation process; thus generally it is not desirable
- Iron (Fe) is relatively low cost and has a higher water-gas-shift activity, and is therefore more suitable for a lower hydrogen/carbon monoxide ratio (H2/CO) syngas such as those derived from coal gasification
- Cobalt (Co) is more active, and generally preferred over ruthenium (Ru) because of the prohibitively high cost of Ru
- In comparison to iron, Co has much less water-gas-shift activity, and is much more costly.
It is the process by which heavy hydrocarbon molecules are broken up into lighter molecules by means of heat and usually pressure and sometimes catalysts. Cracking is the most important process for the commercial production of gasoline and diesel fuel.
Crude oil in its raw form contains a blend of large and complex hydrocarbon molecules. Although the crude oil is valuable even in its raw form, its economic usefulness is relatively limited until it has been subject to additional refining processes.
In order to help render the crude oil into a form that can be more widely utilized, the first and foremost stage in the refining process is to break up, or "crack," the unprocessed hydrocarbon molecules into smaller components. This stage—commonly referred to as "cracking"—makes it possible to turn crude oil into a variety of marketable fuels, lubricants, and other products.
Although the basic concept is the same in all cases, the process of cracking can be implemented in a variety of ways. A common application is what is known as fluid catalytic cracking (FCC), which is used in the production of gasoline as well as various distillate fuels.
Types of Cracking
The different types of cracking are thermal cracking and catalytic cracking. Here is a brief elaboration on the two –
1. Thermal Cracking
The thermal method of cracking uses pressure and heat to break down large hydrocarbon molecules into lighter molecules. This process can be further categorised into –
a. Steam Cracking
This is an older process which uses the heat energy generated from steam. It is also referred to as Pyrolysis. Due to the presence of greater latent heat of energy in the steam, it is considered to be a useful technique for the production of alkenes.
The raw materials used in the process include propane-butane mixture, naptha (obtained from directly distilling crude, and gas oil (in rare instances).
b. Modern Thermal Cracking
Both high pressure and high temperature are used for this method. Homolytic fission takes place among carbon bonds of hydrocarbon compounds. This reaction gains industrial importance with the production of burner fuels.
By lowering the temperature, the delayed coking process takes place. It leads to the production of needle coke which is used for carbon electrodes.
2. Catalytic Cracking
As understood from the term, a catalytic cracking process is undertaken in presence of a catalyst. The large molecules are broken in such a manner that it leads to the maximisation of gasoline yield.
There are three sub-processes involved in this method –
- Reaction
- Regeneration
- Fractionation
Catalytic cracking can be further categorised into –
a. Hydrocracking
It involves a two-stage process that includes a combination of hydrogenation and catalytic cracking. In the presence of hydrogen, heavier feedstocks are being cracked to arrive at the desirable products.
This process needs high temperature, high pressure, hydrogen, and a catalyst. The process is also largely dependent on relative rates of the two reactions and the nature of the feedstock.
b. Fluid Catalytic Cracking
This process is a little distinct. The feedstock is subjected to moderate pressure and high temperature. It is subsequently brought into contact with powdered and hot catalysts. The long-chain molecules are broken down by such a catalyst into considerably shorter molecules.
Advantages:
- The supply of fractions is matched with the demand. Crude oil’s fractional distillation aids in the production of larger hydrocarbons as opposed to smaller hydrocarbons. Once cracking leads to conversion of smaller hydrocarbons from larger ones, fuels such as petrol are formed. The supply of fuel is improved.
- The production of alkenes is also undertaken with the help of cracking. Given that alkenes are more reactive as opposed to alkanes, the former acts as feedstock for the petrochemical industry.
Example:
- Compute the proximate analysis results 1.9 gms of a coal sample loses 0.285gm weight at 110°c.
- 1.5 gm of the same coal sample loses 0.36gm weight at 925°c.
- 2.15 gms of the coal sample leaves 0.26 gm ash.
Given data:
M=1.9 gm
(m – m1)= 0.285 gm (moisture loss)
Loss in weight due to moisture and VM = 0.36gm
Weight of coal = 2.15 gm
Weight of ash = 0.26gm
- Moisture % =
*100
= = 15 %
2. V.M %:
v.m = *10
= *100-15 = 24 – 15
= 9 %
3. Ash %:-
Therefore,
Ash =
=
= 12 %
Example:
- Calculate C , N , H , S from the following observation for a sample of coal.
- 2.05 gms of the coal is burnt in combustion tube. The increase in weight of any hydrous Cacl2 is 0.55 gm and increase in weight of KoH tube is 5.75gm.
- 0.75 of the coal is kjaldahl experiment released NH3 which is passed in 50ml 0.12 N NaoH to neutralize in back titration.
- Washings of the bomb pot when 1.8 gm.
Given data:
Increase in weight of any hydrous calcl2 = 0.55
Mass of coal = 0.75gms
Volume of 0.12 NHCL consumed by NH3 = 50 – 41
= 9 ml
Mass of coal = 1.8gms
Weight of Baso4 = 0.31 gm
- Weight of CO2 formed = increase in wt. Of KOH
Therefore,
C % = *
*100 = 76.5 %.
Increase in weight of any hydrous CaCl2
= weight of H2O formed
Mass of coal = 2.05gm
H % = *
*100
= 2.98 %
2. N % =
=
= 2.02 %
3. S % = *100
=
= 2.36 %
References:
1. A Text book of Engineering Chemistry: Shashi Chawla; Dhanpat Rai & sons, New Delhi
2. Chemistry in Engineering: Lloyd a. Munro, Prentice-hall, Inc Nj
3. Chemistry of Advanced Materials: CNR Rao, Rsc Pbl‟
4. Chemistry of Engineering Materials: Robert B Leighou Mc Graw – Hill Book Company, Inc New York
5. Engineering Materials: Kenneth G Budinski (Prentice – Hall of India)