Unit - 3
Lubrication
Lubricants are substances that are used to reduce the friction and wear of the surfaces of the bodies in relative motion. Lubricants can be in solid liquid and gaseous form, depending on its nature, they are used to eliminate heat, wear debris and supply additives, transmit power, protect and seal
Lubrication refers to the control of friction and wear by introducing a friction-reducing film between moving surfaces that are in contact, lubricant used for such purposes can be a fluid, solid, or plastic substance. Oil and grease are common substances used for lubricating a surface, oils actually help in lubrication while grease acts as a thickening agent to obtain consistency.
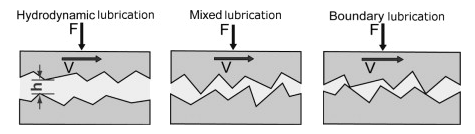
Fig.1: Hydrodynamic Lubrication
Hydrodynamic lubrication occurs when non-parallel rigid bearing surfaces lubricated by a film-fluid slide over each other, forming a converging wedge of fluid and forming a lifting pressure.
Hydrodynamic lubrication (HL) is also known as full film or thick film lubrication. By the beginning of the twentieth century, HL theory was well advanced, based on the work of Navier and Stokes. The Reynolds equation had been widely validated for continuous liquid films acting under restricted conditions (Reynolds, 1886). The fluid film is thick enough to prevent physical or direct contact between the friction-coupled elements. HL enables the coupled elements to function without any measurable wear over a long operating period.
Boundary lubrication occurs when the solid surfaces are so close together that the surface interactions between monomolecular or multi-molecular films of lubricants (liquids or gases) and the solid asperities dominate the contact. Failure in boundary lubrication is caused by adhesive and chemical (corrosive) wear. Boundary lubricants form an easily sheared film on the bearing surfaces, thereby minimising adhesive and chemical wear. The important physical properties of the films are their melting point, shear strength and hardness. Other properties are adhesion or tenacity, cohesion and rates of formation. The bulk flow properties of the lubricant (such as viscosity) play little part in the friction and wear behaviour.
In some lubricants with EP (Extreme Pressure) additives, or other additives to form metallic organic compounds, the metallic salt layer is formed on the steel surface under extreme pressure. The tiny wear particles generated from the metallic salt layer resemble rubbing wear particles under optical microscope. Strictly speaking, the particles from metallic salt layer do not belong to the rubbing wear particles.
Figure a shows the tiny metallic salt layer wear particles on a filtergram. The particles were from a rolling element bearing oil sample with the EP additives. On the filtergram, it is difficult to differentiate the metallic salt layer wear particles from the tiny varnish particles. However, on ferrogram the metallic salt wear particles forms strings (Figure b) whereas the varnish particles had almost washed away entirely.
Classification of Lubricants
Liquid Lubricants
The liquid lubricants are primarily used to support high speed friction and heat dissipation.
- Free-flowing of constant volume
- Amorphous and difficult to compress
- Easily conformable to shape of containers
Solids
Low speed, High load application regime
- They protect the surface against wear and corrosion damages
- Deformable of constant volume
- The solids are not conformed to the shape of the container
- It Resistant to changes in size and shape.
- Molybdenum disulphide and Graphite are common lubricants, the others include tungsten disulphite, boron nitride and polytetrafluorethylene.
Semi-fluid lubricants (greases)
They are mainly greases that are produced, by emulsification of oils, fats with metallic soap and water at 400-600oF, Vaseline is a typical oil base grease. The properties of grease are determined by the types of oil, type of soap, and additives.
Types of oils: mineral, synthetic, vegetable and animal fat.
Types of soap: lithium, sodium, calcium etc
Additives: antioxidation, corrosion protection and pressure.
Biodegradable lubricants possess molecular structures that have the ability to biologically degrade over time by processes like bacterial decomposition or by the enzyme biodegradation of other living microorganisms like yeast, fungi and protozoans. The bases of the biodegradable are mainly derived from vegetable oils, that includes castor oil, rapeseed oil, soybean oil, palm oil, corn oil, hemp oil or chemically synthesized esters.
Properties
- Bio lubricants have excellent lubricity
- These lubricants possess a high flash point and a high viscosity index.
- Compared to mineral based lubricants they are less toxic.
- The biodegradable lubricants degrade rapidly in the natural environment and can reach up to 90% in biodegradability levels.
- The lubricants are produced from renewable materials and are non-toxic in nature, that helps to overall use up the fossil fuels. Base oils used are vegetable and synthetic esters, which are 100% renewable bio-products.
- They show positive impact on the emissions caused by the reduction of carbon dioxide.
- They are designed specifically to show an increase in performance, efficiency and reliability.
Applications
- The biodegradable oils are used in two stroke outboard engine oils and also in Chain saw lubricants.
- They are used in concrete mould release lubricants and also in lubricant greases.
- The lubricants are useful in leakages in mobile hydraulic equipment
- They are economical in the water industry and are treated in sewage plants locks and turbines.
- Transporting plants (ropeways, sky lifts)
- Railways, tramways (wheel flange, tracks, swathes)
- Corrosion preventatives
- Open gears, metal working and lubrication of air tools
Advantages
- The bio-lubricants reduce the risk of skin irritation in contrast to mineral lubricants that produce oil mist that release volatile organic compounds into the air and cause skin irritation and other dermatitis.
- Biodegradable lubricants are found to improve lubricity.
- These lubricants increase customer satisfaction as customers are looking for natural based products than man made ones.
- They meet the requirements of sustainability and environmental protection set by the government.
- Vegetable oils have a higher flashpoint than the mineral oil, which helps substantially to reduce the risk of machine shop fires.
- The use of Bio-lubricant helps to reduce the dependency on imported petroleum products.
- The lubricants are made from vegetable oils, which are biodegradable and are less toxic, and better for the environment and renewable causing less damage.
- Bio-lubricants may be economically beneficial for domestic farmers. Greases and lubricants made from soybean oil can help stabilize prices of soybeans for farmers. This is because these products use surpluses of soybeans for production, stimulating demand for the product.
Disadvantages
- The vegetable oils in its natural form lack sufficient oxidative stability for lubricant use
- As the stability(oxidative) is low, the oil will oxidize quickly during use and if left untreated can become thick and polymerise to a plastic
- Any chemical modification in the vegetable oil to increase its efficiency like partial hydrogenation and fatty acid shifting can lead to cost increase
- Natural Vegetable oils cannot withstand temperatures above 80oC
- Biodegradable lubricants have a high pour point
- The presence of a minute amount of water leads to foaming and degradation problems.
Silicones are polymers that are also known by the name polysiloxanes. These are the polymers that involve any inert, synthetic compound made up of iterative units of siloxane. It is a chain of alternating oxygen and silicon atoms that are frequently combined with hydrogen and carbon.
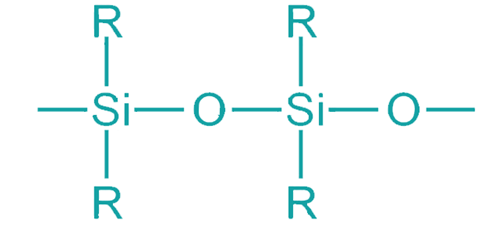
Silicons are the present time class of synthetic objects and contribute to thousands of applications that offer safety and wellbeing in everyday life. Silicones are further a diverse family of high-performance materials that include silicone fluids, silicone polymers and reactive silanes. These materials are widely used in a variety of industrial and consumer products and they provide essential benefits in various areas including personal care, health care, aerospace, transportation, electronics and construction.
Composition and Structure
The silicones are different from many industrial polymers where the chain of atoms that build the backbones of their molecules does not include carbon, being the characteristic member of organic compounds. The absence of carbon makes silicone a unique polymer, though maximum members of class II organic groups such as methyl (CH3), vinyl(CH2) are linked to every silicon atom. Alternatively called polymerized siloxanes or polysiloxanes, silicones have an inorganic silicon-oxygen backbone chain (⋯−Si−O−Si−O−Si−O−⋯) where two organic groups are attached to each silicon center.
The general formula of silicone is (R2SiO)x, where R belongs to any one of the organic groups.
Poly-dimethyl siloxane is the most silicone compound can which illustrates the primary characteristics of the organic class. The first substance is metallic silicon, obtained from silica sand. The silicon reacts with methyl chloride (Ch3Cl) and forms dimethyl dichloro silane ([CH3]2Si[Cl]2), over a copper catalyst. When this compound is made to react with water, the atoms of chlorine get replaced by hydroxyl groups(OH). The resulting compound, silanol ([CH3]2Si[OH]2) polymerizes in a condensation reaction. Every individual unit of molecules links together to form poly-dimethyl siloxane with associated loss of water.
Properties of Silicones
- Silicones have low thermal conductivity and chemical reactivity.
- Their toxicity is also low.
- It can repel water and form watertight seals.
- Has high resistance to oxygen, ozone, and ultraviolet (UV) light.
- Has both electrically insulative and conductive properties.
- High gas permeability and high thermal stability
- Superior solvents for organic compounds.
An emulsion is a two-phase system which consists of two immiscible liquid (such as oil and water), the one being dispersed in other. Out of two liquids, one which is broken into droplet is called as dispersed phase whereas the other liquid-liquid surrounding the internal phase is called dispersion medium or external phase; such a system of two immiscible liquids is very unstable and separates out into a different phase.
So, to increases the stability, the emulsifier is added. The emulsifier molecules like sodium palmitate shown polar character. It consists of hydrophilic and hydrophobic ends which are preferably wetted by water and oil respectively. Thus, emulsifier molecule is absorbed and places itself at the interface of two phases namely oil and water forming an intermediate layer in between two phases.
Conditions where lubricating emulsion are used
These are used in various jobs like milling, threading etc. The tool at the cutting edge experiences very high pressure and temperature. They may result in oxidation and deformation of metal under work. Hence to prevent overheating of metal and tools proper lubricating and cooling is done by lubricating emulsion. Oils are coolant but lubricant whereas water is good coolant but a poor lubricant.
Advantages of emulsion
- It increases the life of the machining tools.
- It reduces power requirement.
- It maintains higher machining speed.
- It increases the accuracy of machining of metals and reduces its cost.
The emulsion is further classified as-
Oil – in water: oil is the dispersed phase and water is dispersing medium. It is prepared by mixing oil and water along with 3 % to 20% of water-soluble emulsifiers like water-soluble soaps alkyl sulphate etc. Eg: cutting fluids
Water-in-oil: water is the dispersed by mixing water and oil along with 1% to 10 % of water insoluble emulsifiers like alkaline earth metal soaps etc: cooling liquids.
- The ability to form a film of lubricant which is not easily removed and which may be required to resist shock loading.
- The ability to form a large mass which will not be easily removed, thus making a seal which will prevent contamination by water, scale and dust.
- The ability to prevent corrosion.
- The ability to resist temperature rises without becoming softened unduly in the process.
- The ability to withstand shear without breakdown of the structure.
The dropping point of a grease is the temperature at which it passes from a semi-solid to a liquid state. The dropping point test determines the cohesiveness of the oil and thickener of a grease. Dropping point tests are used for quality control to verify that the soap structure has been formed correctly and will withstand high temperatures.
The test featured in this video is Dropping Point, also known as ASTM Method D-2265. The dropping point of a grease is the temperature at which it passes from a semi-solid to a liquid state. The dropping point test determines the cohesiveness of the oil and thickener of a grease. Dropping point tests are used for quality control to verify that the soap structure has been formed correctly and will withstand high temperatures.
The technician monitors the entire test apparatus as it is slowly heated in order to ensure that the heater block temperature and the sample temperature remain within 3°C of each other. As the temperature increases in the test apparatus, a drop of oil will fall from the cup to the bottom of the test tube at the temperature at which the thickener can no longer hold the oil. When this occurs, the technician will record both the sample and heater block temperatures on the thermometers to the nearest degree.
To calculate the dropping point of the grease, the recorded temperature of your sample is subtracted from the heater block temperature. And that value is added to the sample temperature to determine the Dropping Point.
A Dropping Point is most often performed on any soap-thickened grease. Soap thickened greases consist of simple and complex soaps. Soap-thickened greases are most often used in bearing applications in the automotive, industrial and aerospace industries.
A good lubricant generally possesses the following characteristics:
- A high boiling point and low freezing point (in order to stay liquid within a wide range of temperature)
- A high viscosity index.
- Thermal stability.
- Hydraulic stability.
- Demulsibility.
- Corrosion prevention.
- A high resistance to oxidation.
The acid value (AV) is a common parameter in the specification of fats and oils. It is defined as the weight of KOH in mg needed to neutralize the organic acids present in 1g of fat and it is a measure of the free fatty acids (FFA) present in the fat or oil. An increment in the amount of FFA in a sample of oil or fat indicates hydrolysis of triglycerides. Such reaction occurs by the action of lipase enzyme and it is an indicator of inadequate processing and storage conditions (i.e., high temperature and relative humidity, tissue damage). The source of the enzyme can be the tissue from which the oil or fat was extracted or it can be a contaminant from other cells including microorganisms. Besides FFA, hydrolysis of triglycerides produces glycerol.
Acid value (mg KOH/g fat) = Titre value x Normality of KOH x 56.1 Weight of sample (g)
Saponification is simply the process of making soaps. Soaps are just potassium or sodium salts of long-chain fatty acids. During saponification, ester reacts with an inorganic base to produce alcohol and soap.
Generally, it occurs when triglycerides are reacted with potassium or sodium hydroxide (lye) to produce glycerol and fatty acid salt, called ‘soap’.
Saponification value or saponification number refers to the amount of base that is required to saponify a fat sample. Generally, saponification values are listed in KOH and so, saponification value can also be defined as that value which represents the number of milligrams required to saponify 1 gram of fat under the specified conditions.
In case sodium hydroxide is used for the saponification process, the saponification value must be converted from potassium to sodium by dividing the KOH values by the ratio of the molecular weights of KOH and NaOH (i.e. 1.403).
The flashpoint for any volatile material is defined as the lowest temperature at which vapours of the material will ignite when ignited by a source. Similarly, the fire point is defined as the lowest temperature at which vapours of the material will catch fire and continue burning even after the ignition source is removed. The fire point is higher than the flashpoint because the vapours produced at the flashpoint are not sufficient enough to ignite the fuel. Flash and fire points depend upon the volatility of the biodiesel. Volatility is the tendency of the substance to vaporize, and it is directly related to the vapor pressure of the biodiesel at that particular temperature. The biodiesel exhibiting higher vapor pressure at a given temperature is said to be more volatile than the one exhibiting lower vapor pressure at the same temperature. Hence the lower the NBP (normal boiling point), the higher the volatility, which is in turn inversely proportional to its flash and fire point.
Key Takeaways:
1) The flashpoint for any volatile material is defined as the lowest temperature at which vapours of the material will ignite when ignited by a source.
2) Flash and fire points depend upon the volatility of the biodiesel.
3) The biodiesel exhibiting higher vapor pressure at a given temperature is said to be more volatile than the one exhibiting lower vapor pressure at the same temperature.
The rate at which viscosity of lubricant changes with temperature is measured by an arbitrary scale is known as viscosity index. The viscosity of the liquid decreases with increasing temperature so that lubricating oil becomes thinner as the operating temperature is raised, and lubricant can be squeezed out from the subbing parts.
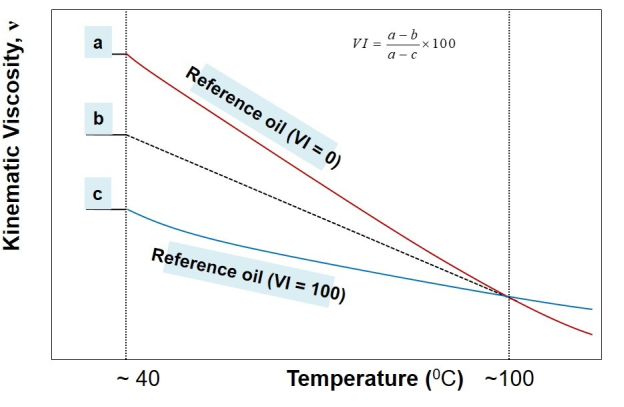
A stepwise procedure to estimate viscosity index, VI, may be outlined as below:
- Measure kinematic viscosity of the unknown oil at 40o C and 100oC.
- Identify two reference oils whose kinematic viscosity at 100oC coincides with the kinematic viscosity of the unknown oil (from the look-up chart of ASTM standard).
- Pick-up the kinematic viscosity of two identified reference oils at 40oC
- About the illustration above, now a, b, and c are known.
- Use the following formula to calculate the viscosity index
VI=(a-b)/(a-c) *100
Key Takeaways:
1) The rate at which viscosity of lubricant changes with temperature is measured by an arbitrary scale is known as viscosity index.
2) The viscosity of the liquid decreases with increasing temperature so that lubricating oil becomes thinner as the operating temperature is raised, and lubricant can be squeezed out from the subbing parts.
It is the measure of the aromatic content of the lubricating oil. The low aniline point has high aromatic content which attacks rubber seals. The higher the aniline point means the lower percentage of hydrocarbons. Thus Aniline point is used as an indication of possible deterioration of rubber sealing.
Determination of Aniline Point:
Aniline + Sample oil Homogenous Solution Cloudiness
Key Takeaways:
1) The acid value (AV) is a common parameter in the specification of fats and oils.
2) An increment in the amount of FFA in a sample of oil or fat indicates hydrolysis of triglycerides.
3) The higher the aniline point means the lower percentage of hydrocarbons.
The key difference between cloud point and pour point is that the cloud point refers to the temperature at which there is a presence of a wax cloud in the fuel whereas the pour point is the lowest temperature below which the fuel loses its flow characteristics.
Cloud point and pour point are important physical properties of any liquid fuel. Cloud point, as the name suggests is the temperature at which a cloud of wax crystals first appear in a liquid fuel when we cool it under special testing conditions. The cloud point of any petroleum product is an indicator of how well the fuel will perform under cold weather conditions. Pour point is just the opposite of cloud point as it refers to the lowest temperature at which we can observe the movement of oil and also we can pump the fuel easily. As such, there is only a slight difference in these two temperatures on the temperature scale, but the difference between cloud point and pour point is significant in the use of any fuel.
I.C Engines
The I.C engine burns fuel to convert the chemical energy into mechanical energy, in the combustion chamber chemical energy is released when fuel-air mixture is ignited by a spark. The gas thus produced in this reaction expands rapidly and forces the piston down the cylinder on the power stroke.
The advantages of lubrication in IC engine:
- The lubrication helps to reduce the wear and tear of the moving parts.
- It damps down the vibration of the engine.
- The moving parts are cleaned.
- The gas Piston is made tight.
Refrigeration Systems
In general, large refrigerant systems, especially those that use ammonia as a refrigerant, are provided with oil separators. In these kinds of systems, using a lubricant that is immiscible or has low miscible with the refrigerant fluid is advisable.
In most other refrigeration systems, the blending of the lubricant and the refrigerant fluid is unavoidable. Therefore, it becomes necessary to select a lubricant that has the right miscibility and solubility features. For example, with systems that do not have the oil-separation capability, the lubricant that moves from the compressor into the must be appropriately miscible with the refrigerant at the temperature of the evaporator, so that the refrigerant fluid–lubricant blend rests in one phase after expansion in the evaporator and at a sufficiently low viscosity to travel through to the compressor. Consequently, if the lubricant separates itself in the evaporator due to poor miscibility with the refrigerant fluid or the blend viscosity is more, fluid is likely to get trapped in the evaporator and adversely affect the system’s cooling capacity and efficiency.
Solubility is very important at the compressor portion of the refrigeration circuit. Another important aspect of proper lubricant selection is to ensure that the viscosity of the lubricant, after absorption of gaseous refrigerant at the high compressor temperature, is sufficient for effective lubrication of the compressor.
Gear
In order to choose the best lubricant for a gear set, the following criteria must be addressed:
- Viscosity – this is one of the important properties of lubricating oil. The viscosity of a gear lubricant is initially chosen so that they provide the desired thickness between the interacting surfaces for a given load and speed.
- Additives – the additive present in the lubricants will determine the general category and also perform key properties effectively. The gear lubricants are categorised into three parts the antiscuff, rust and oxidation and compounded, under operation condition, the best gear lubricant that fits the requirement is taken eventually.
- Base Oil Type – In most applications the mineral base oil of high quality is used. Sometimes the synthetic base oils are also preferred. The mineral base oils have higher pressure-viscosity coefficients than common synthetics that provide a greater thickness at given operating viscosities.
Transformer:
A transformer lubricant provide insulation for components of the electrical systems, thereby reducing the danger of overheating and breakdowns, every sector requires power systems, with a proper transformer oil lubricant that protect the transformer and keep the power flowing.
The oil needs to reduce the cleaning and repair maintenance. Lower costs and durability are the key factors the transformer oil is for insulation and cooling of the electric transformers and switchgears of extra high voltage conforming to the technical particulars. The oil should also be suitable for oil circuit breakers and other electrical equipment’s in which oil is used as insulating medium. The tests on transformer oil shall be conducted in accordance with the relevant methods.
Delicate Mechanical System
Hydrodynamic lubrication is said to exist when the moving surfaces are separated by the pressure of a continuous unbroken film or layer of lubrication. In this type of lubrication, the load is taken completely by the oil film.
The basis of hydrodynamic lubrication is the formation of an oil wedge. When the journal rotates, it creates an oil taper or wedge between the two surfaces, and the pressure build up with the oil film supports the load.
Hydrodynamic lubrication depends on the relative speed between the surfaces, oil viscosity, load, and clearance between the moving or sliding surfaces.
In hydrodynamic lubrication the lube oil film thickness is greater than outlet, pressure at the inlet increases quickly, remains fairly steady having a maximum value a little to the outside of the bearing centre line, and then decreases quickly to zero at the outlet.
Application of hydrodynamic lubrication
- Delicate instruments.
- Light machines like watches, clocks, guns, sewing machines.
- Scientific instruments.
- Large plain bearings like pedestal bearings, main bearing of diesel engines.
Hydrocarbon oils are considered to be satisfactory lubrication for fluid film lubrication. In order to maintain the viscosity of the oil in all seasons of the year, ordinary hydrocarbon lubricants are blended with selected long chain polymers.
Steam Turbines
The importance should be first given to the physical and chemical properties of turbines before the selection process.
Steam, gas and hydro turbines operate on a family of lubricating oils known as R&O oils (Rust & Oxidation inhibited oil). Compared to other lubricating oils like gasoline and diesel the turbine lubricating oil, its equipment, geometry, maintenance practises, operating temperatures and contamination system present a lot of demand.
The drive for a long-lasting lubricant oil lies in having a huge size of turbine sump capacities of size ranging from 1,000 to 20,000 gallons, and is also economical. Low turbine oils makeup rates also help to contribute the need for high quality and long-life lubricants. Without significant oil contamination issues, turbine oil life is primarily dictated by oxidation stability.
Heat and water, particulate contamination and aeration adversely affect oxidation stability the oil life is extended by adding rust inhibitors, antioxidants and demulsibility additives and a rich quality base stock Lube oil cooler, water removal systems and filters are installed in turbine lubrication systems for the same purpose.
Steam turbine oil is designed to shed water and allow the solid particles to settle, these are later removed through kidney loop filtration systems, sump drains. Formulated to shed water and allow solid particles to settle where they can be removed through sump drains or kidney loop filtration systems during operation. To help in contamination separation, high levels of detergents are not added. Turbine oils are not exposed to fuel or soot and therefore do not need to be drained and replaced on a frequent basis.
References:
1. A Text book of Engineering Chemistry: Shashi Chawla; Dhanpat Rai & sons, New Delhi
2. Chemistry in Engineering: Lloyd a. Munro, Prentice-hall, Inc Nj
3. Chemistry of Advanced Materials: CNR Rao, Rsc Pbl.
4. Chemistry of Engineering Materials: Robert B Leighou Mc Graw – Hill Book Company, Inc New York
5. Engineering Materials: Kenneth G Budinski (Prentice – Hall of India)