Unit - 6
Fluid Machinery
Q1) Define turbines.
A1)
TURBINES: Definition
Several bodily standards are hired through mills to acquire this power: Impulse mills alternate the course of waft of an excessive pace fluid or fuelling jet.
The ensuing impulse spins the turbine and leaves the fluid waft with faded kinetic power.
There isn't any strain alternate of the fluid or fuelling with inside the turbine blades (the transferring blades), as with inside the case of a steam or fuelling turbine, all of the strain drop takes vicinity with inside the desk bound blades (the nozzles). Before achieving the turbine, the fluid's strain head is modified to pace head through accelerating the fluid with a nozzle.
Pelton wheels and de Laval mills use this technique exclusively. Impulse mills do now no longer require a strain casement across the rotor for the reason that fluid jet is created through the nozzle previous to achieving the blades at the rotor. Newton's 2nd regulation describes the switch of power for impulse mills.
Impulse mills are maximum green to be used in instances in which the waft is low and the inlet strain is excessive. Reaction mills increase torque through reacting to the fuelling or fluid's strain or mass.
The strain of the fuelling or fluid modifications because it passes thru the turbine rotor blades. A strain casement is wanted to include the running fluid because it acts at the turbine stage(s) or the turbine have to be completely immersed with inside the fluid waft (along with wind mills).
The casing consists of and directs the running fluid and, for water mills, keeps the suction imparted through the draft tube. Francis mills and maximum steam mills use this concept.
For compressible running fluids, a couple of turbine ranges are typically used to harness the increasing fuelling efficiently. Newton's 1/3 regulation describes the switch of power for response mills.
Reaction mills are higher suitable to better waft velocities or packages in which the fluid head (upstream strain) is low. In the case of steam mills, along with might be used for marine packages or for land-primarily based totally strength generation, a Parsons-kind response turbine might require about double the wide variety of blade rows as a de Laval-kind impulse turbine, for the identical diploma of thermal power conversion.
Whilst this makes the Parsons Turbine lots longer and heavier, the general performance of a response turbine is barely better than the equal impulse turbine for the identical thermal power conversion.
In practice, present day turbine designs use each response and impulse standards to various stages on every occasion possible. Wind mills use an airfoil to generate a response carry from the transferring fluid and impart it to the rotor. Wind mills additionally advantage a few power from the impulse of the wind, through deflecting it at an angle.
Turbines with a couple of ranges can also additionally use both response and impulse blading at excessive strain. Steam mills have been historically extra impulse however hold to transport closer to response designs just like the ones utilized in fuelling mills.
At low strain the working fluid medium expands in extent for small discounts in strain. Under those conditions, blading will become strictly a response kind layout with the bottom of the blade completely impulse.
The motive is because of the impact of the rotation velocity for every blade. As the extent increases, the blade top increases, and the bottom of the blade spins at a slower velocity relative to the tip.
This alternate in velocity forces a fashion dressmaker to alternate from impulse at the bottom, to an excessive response-fashion tip.
Steam mills are used to pressure electric mills in thermal electricity plant life which use coal, gasoline oil or nuclear gasoline.
They have been as soon as used to without delay pressure mechanical gadgets which include ships' propellers (for instance the Turbine, the primary turbine-powered steam launch), however maximum such packages now use discount gears or an intermediate electric step, in which the turbine is used to generate electricity, which then powers an electric powered motor linked to the mechanical Turbo electric powered deliver equipment turned into in particular famous with inside the duration without delay earlier than and throughout World War II, in the main because of a loss of enough gear-slicing centers in US and UK shipyards. Aircraft fuelling turbine engines are now and again called turbine engines to differentiate among piston engines.
Q2) Explain gross and net heads.
A2)
Gross and net heads
Now we can consciousness right here to apprehend a few critical terminologies related to a hydraulic turbine together with Gross head, Net head and efficiencies of a hydraulic turbine with the assist of this post. Will you be fascinated nowadays to discover those critical terminologies related to a hydraulic turbine? So allow us to begin right here with the subsequent critical terminologies
Gross Head
Gross head is largely described because the distinction among the pinnacle race stage and tail race stage whilst water isn't always flowing. Gross head may be indicated with the aid of using Hg as displayed right here in following figure.
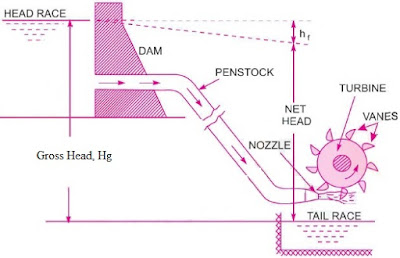
Net Head
Net head is largely described as the pinnacle to be had on the inlet of the turbine. Net head is likewise in reality referred to as powerful head.
When water will waft from head race to the turbine, there may be a few losses of head because of friction among water and penstock.
There may also be different losses of head together with lack of head because of bend, fitting, at front of penstock etc. We should observe it right here that those losses may be very much less and will be left out whilst we evaluate with head loss because of friction.
Net head to be had on the inlet of turbine will be written as referred to right here.
Net head, H = Gross head (Hg) – head loss because of friction (hf) Loss of head because of friction may be given with the aid of using Darcy-Weisbach equation and we are able to discover it right here.
Q3) Explain different efficiency.
A3)
Different efficiencies
There are following crucial efficiencies that we are able to speak right here on this post.
- Hydraulic performance
- Mechanical Efficiency
- Volumetric performance
- Overall Efficiency
Hydraulic performance
Hydraulic performance is largely described because the ratio of electricity given with the aid of using water to the runner of turbine to the electricity provided with the aid of using the water on the inlet of the turbine.
Hydraulic performance may be indicated with the aid of using ηh.
Runner is largely a rotating element of a turbine and buckets or vanes may be constant on the circumference of the runner. Vanes or buckets constant at the runner aren't easy and therefore there may be hydraulic losses whilst water will waft thru those vanes of the turbine.
Therefore, electricity given with the aid of using water to the runner of the turbine may be much less than the electricity provided with the aid of using the water on the inlet of the turbine. Hydraulic performance of a turbine will be written as referred to right here
Hydraulic performance (ηh) = Power added to the runner of turbine / Power provided on the inlet of turbine
Hydraulic performance (ηh) = R.P/ W.P R.P = Power added to the runner of turbine
W.P = Power provided on the inlet of turbine or water electricity
Mechanical Efficiency
Mechanical performance is largely described because the ratio of electricity to be had on the shaft of the turbine to the electricity added to the runner of the turbine. Mechanical performance may be indicated with the aid of using ηm.
Power given with the aid of using water to the runner of turbine may be transmitted to the shaft of the turbine. Power to be had on the shaft of the turbine may be much less than the electricity added to the runner of the turbine because of mechanical losses.
Mechanical performance of a turbine will be written as referred to right here
Mechanical performance (ηm) = Power to be had on the shaft of the turbine / Power added to the runner of the turbine
Mechanical performance (ηm) = S.P/ R.P S.P = Power to be had on the shaft of the turbine R.P = Power added to the runner of turbine
Volumetric Efficiency
The quantity of the water placing the runner of a turbine may be barely much less than the quantity of the water provided to the turbine as a few quantity of water may be discharged to the tail race without placing the runner of the turbine.
Volumetric performance is largely described because the ratio of the quantity of the water honestly placing the runner of the turbine to the quantity of water provided to the turbine.
Volumetric performance may be indicated with the aid of using ηv.
Volumetric performance of a turbine will be written as referred to right here
Volumetric performance (ηv) = Volume of the water honestly placing the runner of the turbine / Volume of water provided to the turbine
Overall Efficiency
Overall performance is largely described because the ratio of the electricity to be had on the shaft of the turbine to the electricity provided with the aid of using the water on the inlet of the turbine.
Overall performance may be indicated with the aid of using ηo.
Overall performance,
ηo = Power to be had on the shaft of the turbine / Power provided with the aid of using the water on the inlet of the turbine
Overall performance, ηo = S.P/W. P
Overall performance is likewise described because the manufactured from mechanical performance and hydraulic performance
Overall performance = Mechanical performance x Hydraulic performance ηo = ηm x ηh
Q4) Give classification of turbines.
A4)
Classification of turbines
Types of Turbines Based on Energy Exchange among the water and the Machine
Considering how the fluid float acts at the turbine blades reasons hydro generators to be categorized into categories: impulse and response.
Impulse Turbines
If the turbine wheel is pushed through the kinetic electricity of the fluid that moves the turbine blades via the nozzle or otherwise, the turbine is called an impulse turbine. In those forms of generators, a hard and fast of rotating equipment operates at atmospheric stress. Impulse generators are commonly appropriate for excessive head and coffee float quotes.
Pelton, Turgo, and Cross-float generators are 3 forms of impulse generators. The production of the Pelton and Turgo generators is similar. However, the Cross-float turbine is a changed sort of impulse generators this is categorized as an impulse turbine because of the rotation of the runner at atmospheric stress and now no longer as a submerged turbine.
Reaction Turbines
If the sum of ability electricity and kinetic electricity of water which can be because of the stress and velocity, respectively reason the turbine blades to rotate, the turbine is classed as a response turbine. In those forms of generators, the whole turbine is immersed in water and adjustments in water stress in conjunction with the kinetic electricity of the water reason energy exchange. Applications of response generators are commonly at decrease heads and better float quotes than impulse generators.
The water passage via the turbine divides those generators into the subsequent 4 categories:
Radial Flow Turbine
These generators are divided into types: Inward radial float and outward radial float.
Inward Radial Flow Turbines
In those generators, water enters the turbine casing via the Penstock, and travels via the constant manual vanes to the rotor, and exits from there. Therefore, the internal and outer diameters are as the opening and the inlet, respectively. The Following determine suggests the course of the water in an inward radial float turbine. Water enters from the casing with inside the middle of the constant manual vanes.
Axial Flow Turbines
In this sort of turbine, the fluid flows parallel to the turbine shaft (turbine axis). Kaplan is this type of generators.
Mixed Flow Turbines
A turbine wherein the float enters the turbine radially and leaves it axially is a blended float turbine, like cutting-edge Francis generators.
Types of generators primarily based totally at the hydraulic running variety accordingly, water generators are of 3 categories:
Low Head Turbines
Hydraulic generators running with inside the head variety of fewer than forty five meters are taken into consideration low-head generators. Kaplan turbine is this type of generators. If the pinnacle is much less than three meters, it's far taken into consideration an ultra-low head.
Medium Head Turbines
The running variety for heads of forty five to 250 meters is called medium heads. Francis generators normally perform in such conditions.
High Head Turbines
With heads better than 250 meters are called excessive-head generators, Like the Pelton Turbine. In the determine beneath, you could see the running variety of various generators primarily based totally at the adjustments in head and float rate. Types of Turbines
Based on Specific Speed
The precise velocity of a turbine (denoted through Ns) is described as the velocity of a turbine with a geometrical similarity that could generate a unit of energy beneath a head unit. Based in this parameter, water generators are categorized into 3 classes:
Low Specific Speed Turbine
The values among 1 and 10 are low precise speeds. Impulse generators perform on this variety. For example, the Pelton turbine commonly operates at a selected velocity of approximately
Medium Specific Speed Turbine
Turbines that perform with inside the precise velocity variety of 10 to one hundred, along with Francis, have a medium precise velocity.
High Specific Speed Turbine
Specific speeds above one hundred are taken into consideration excessive values. Kaplan turbine works at an excessive precise velocity.
Q5) Explain working principle of turbine.
A5)
Working Principle:
In those mills, the static stress in the runner is constant, and the turbine runner is at atmospheric stress.
The runner spins with inside the air, and the fluid is sprayed to the blades via the nozzle to change electricity with the turbine. A jet nozzle or a sequence of nozzles directs the excessive-velocity waft to the blades, which might be typically with inside the form of buckets or cups.
The software of the curved blades is to extrude the speed of the waft. This strike reasons a extrude in momentum and primarily based totally at the regulation of communique of electricity, a pressure is carried out to the turbine blades. .According to Newton’s 2nd regulation of movement, the pressure acquired via the movement of a fluid relies upon on factors: the mass of the fluid coming into the turbine and the adjustments in fluid speed among the turbine inlet and outlet.
Since no extrude in fluid mass occurs, most effective speed adjustments are taken under consideration in calculating the pressure carried out to the runner.
The saved water flows from a supply upstream via Penstock to be added to the nozzle. The capacity electricity of the water in the nozzle is transformed into kinetic electricity and injected into the blades or buckets; thus, the runner spins.
There is a mechanism to manipulate the waft of water injected into the runner. The spear typically performs a critical function on this procedure.
The generator connected to the shaft converts mechanical electricity into electric electricity. Impulse mills have the cap potential to take all of the kinetic electricity from the water for excessive efficiency.
Water is discharged into the environment from the lowest of the turbine housing after achieving the runner; therefore, there's no suction at the lowest of the turbine.
Here you may see schematically how an impulse turbine works with inside the procedure of extracting electricity from the kinetic electricity of water in addition to its additives.
Q6) Explain components of an impulse turbine.
A6)
Components of an Impulse Turbine
Impulse mills are composed of the subsequent additives.
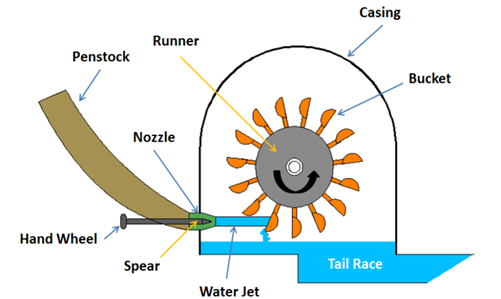
Runner
The runner includes a round disk to which some of curved blades are connected and a cylindrical shaft with inside the center. Shafts and runners are typically product of chrome steel. In instances wherein the waft head is less, the runner is product of solid iron.
Buckets
Buckets are a fixed of spoon-fashioned cups which are hooked up across the runner to change electricity among the fluid and the turbine. The fluid jet hits those buckets after leaving the nozzle, making the turbine to rotate and exiting the outer fringe of the bucket.
The extrude with inside the course of the fluid in the course of the go out as compared to the perspective of effect varies relying at the layout of the turbine. To get the biggest momentum, this perspective need to be a hundred and eighty levels.
However, this perspective is restrained to angles of approximately a hundred and seventy levels because of concerns which include that the go out waft from one bucket does now no longer collide with the following bucket and does now no longer reason it to brake.
Nozzle
The nozzle is set up to alter and jet the fluid waft to strike the buckets. As stated earlier, it's miles the most effective a part of the impulse turbine meeting that the stress adjustments and the waft head are transformed into kinetic electricity.
The extent of water jet achieving the buckets is adjusted through an aspect referred to as a spear, that is a conical needle that actions inside and out of the nozzle through a hand wheel or automatically. By shifting this needle backward, the water waft increases, and through shifting forward, it decreases. The nozzle is usually crafted from tungsten carbide, which could be very difficult and may resist erosive particles.
Casing
The casing for an impulse turbine is a defend over the turbine to save you the water from splashing and additionally to manual it to the spillway, which exists for the greater water to guard the structural integrity of the dam. Normally, Cast iron is used to fabricate the casing.
Penstock
Penstocks in hydropower flowers are pipes and channels that deliver water from dams and reservoirs to mills. In general, they're product of steel. Water flows in those ducts beneath excessive pressures.
The discern under indicates the special additives of impulse mills and their positions. In addition to the principle additives stated above, a mechanism is typically used to save you the turbine from rotating.
When the water jet is stopped, the runner keeps to rotate because of the results of inertia.
In those instances, to save you this rotation, a jet of water is injected into the again of the buckets, that is referred to as a breaking jet.
Here you may schematically see how an impulse turbine works with inside the procedure of extracting electricity from the kinetic electricity of water in addition to its additives.
Q7) Explain selection of turbines on the basis of head and specific speed.
A7)
Selection of turbines on the basis of head and specific speed
Initial turbine selection is usually based on the ratio of design variables known as the power specific speed. In U.S. Design practice this is given by
N = nP1/2 /H5/4
Wherein n is in revolutions in step with minute, P is the output in horsepower, and H is the pinnacle of water in ft. Turbine kinds may be categorized via way of means of their particular velocity, N, which usually applies on the factor of most performance.
If N stages from one to 20, similar to excessive heads and coffee rotational speeds, impulse mills are appropriate. For N among 10 and ninety, Francis-kind runners need to be selected, with slow-running, near-radial devices for the decrease N values and greater hastily rotating mixed-glide runners for better N values.
For N as much as 110, Deriaz mills can be suitable. If N stages from 70 to the most of 260, propeller or Kaplan mills are referred to as for. Using the particular velocity formula, a turbine designed to supply 100,000 horsepower (74, six hundred kilowatts) with a head of forty ft (12.2 meters) running at seventy two revolutions in step with minute could have a particular velocity of 226, suggesting a propeller or Kaplan turbine.
It also can be proven that the glide fee ought to be approximately 24,500 cubic ft in step with second (694 cubic meters in step with second) at a turbine performance of ninety percent.
The runner diameter can be approximately 33 ft (10 meters).
This illustrates the massive sizes required for excessive-power, low-head installations and the low rotational velocity at which those mills ought to function to live inside the permissible particular velocity range.
Before constructing massive-scale installations, the layout need to be looked at with turbine version tests, the usage of geometrically comparable fashions of small and intermediate size, all running on the identical particular velocity.
Allowances have to be made for the consequences of friction, decided via way of means of the Reynolds number (density × rotational velocity × runner diameter squared/viscosity) and for feasible adjustments in scaled roughness and clearance dimensions.
Friction consequences are much less essential for massive devices, which have a tendency to be greater green than smaller ones.
Q8) Explain reciprocating pump in detail.
A8)
RECIPROCATING PUMPS
Reciprocating pump is a tremendous displacement pump in which positive extent of liquid is accumulated in enclosed extent and is discharged the use of strain to the desired application.
Reciprocating pumps are extra appropriate for low volumes of waft at excessive pressures.
Components of Reciprocating Pump
The principal additives of reciprocating pump are as follows:
Suction Pipe
Suction pipe connects the supply of liquid to the cylinder of the reciprocating pump. The liquid is suck through this pipe from the supply to the cylinder.
Suction Valve
Suction valve is non-go back valve this means that simplest one directional waft is feasible on this kind of valve. This is located among suction pipe inlet and cylinder. During suction of liquid it's far opened and throughout discharge it's far closed.
Cylinder:
It is a whole cylinder fabricated from forged iron or metal alloy and it includes the association of piston and piston rod.
Piston and Piston rod:
For suction, the piston movements returned in the cylinder and for discharging of fluid, the piston movement’s with inside the ahead route. The Piston rod facilitates the piston to transport in a linear route i.e. both the ahead and the backward directions.
Crank and Connecting rod:
For rotation, the crank is attached to the strength supply like engine, motor, etc.
Delivery Pipe:
The characteristic of the transport pipe is to supply the water to the favored place from the cylinder.
Delivery valve:
Similar to the suction valve, a transport valve is likewise a Non-go back valve.
Q9) Explain working principle of reciprocating pump.
A9)
Working Principle of Reciprocating Pump:
When the strength deliver is given to the reciprocating pump, the crank rotates thru an electric powered motor. The attitude made with the aid of using the crank is answerable for the motion of the piston in the cylinder.
By regarding the above diagram, the piston movements closer to the intense left of the cylinder while the crank meets function A i.e. θ=zero.
Similarly, the piston movements closer to the intense proper of the cylinder while the crank meets the placement C i.e. θ=a hundred and eighty.
This is because of the presence of atmospheric stress at the sump liquid that is pretty much less than the stress in the cylinder. Therefore, because of the distinction in stress, the water enters into the cylinder thru a non-go back valve.
The water which remains with inside the extent of the cylinder must be dispatched to the release pipe thru discharge valve and this could be carried out while the crank is rotating from C to A i.e. (θ=a hundred and eighty to θ=360) which movements the piston with inside the ahead route.
Due to the motion of the piston in an ahead route, the stress will increase in the cylinder that is extra than the atmospheric stress. This consequences with inside the starting of the transport valve and last of the suction valve.
Once the water comes into the transport valve, it cannot flow returned to the cylinder due to the fact its miles a unidirectional valve or non-go back valve.
From there, it enters into the transport pipe in order that it could be dispatched to the specified function.
Therefore, on this way, the water is sucked and discharged from the sump to the favored place thru the piston in the cylinder.
Q10) What is single acting pump?
A10)
Single acting pumps:
A pump is a tool that makes use of to switch distinctive fluids from one area to another. Pumps have a couple of kinds in keeping with distinctive applications. A reciprocating pump is a fava form of pump from the class of superb displacement pumps. In this article, we can deeply talk numerous elements of the reciprocating pump.
A reciprocating pump is a mechanical tool that modifications the mechanical strength of the fluid into hydraulic strength (strain strength). It makes use of a piston or plunger for pumping the fluid from one area to another. Because a reciprocating pump makes use of a piston or plunger for pumping purposes, therefore, it's also called a piston pump. In this pump, the piston reciprocates in an upward and downward role in the pump cylinder. As the piston actions in the direction of BDC, it sucks fluid at the same time as it pressurizes the fluid whilst it actions in the direction of TDC.
A hand pump is a maximum not unusual place instance of a reciprocating pump. A bicycle pump and syringe pump also are the maximum typically used examples of reciprocating pumps.
Slip in reciprocating pump is essentially described because the distinction among the theoretical discharge and real discharge of the reciprocating pump.
Actual discharge of a reciprocating pump might be much less than the theoretical discharge of the pump because of leakage of water in the course of operation of pump.
The distinction of the theoretical discharge and real discharge might be known as slip of reciprocating pump. Mathematically, we are able to explicit the slip in reciprocating pump as stated below
Slip = Qth – Qact
Slip is usually expressed as percentage slip and it will be given by following expression.
Percentage slip = (Qth – Qact)/Qth 100 = ( 1 – Qact/Qth) 100
= (1 – Cd) 100
Where, Cd = Co-efficient of discharge
Q11) What is double acting pump?
A11)
Double acting pumps:
Water can be performing on each facet of the piston in case of double performing reciprocating pump as displayed right here in following figure.
Therefore, there can be suction and shipping pipes for double performing reciprocating pump as proven in following figure.
When there can be a suction stroke on one facet of the piston, identical time there can be a shipping stroke at the alternative facet of the piston.
Hence, in case of double performing reciprocating pump, there can be suction strokes and shipping strokes for one whole revolution of crank and water can be discharged via the shipping pipes at some stage in those shipping strokes.
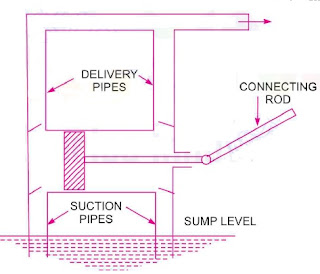
Let us consider the following terms as mentioned below
D = Diameter of the piston
d = Diameter of the piston rod
Area on one side of the piston, A = (π/4) x D2
Area on other side of the piston where piston rod is connected with piston, A1 = (π/4) x [D2 -d2]
Work done by double acting reciprocating pump
Work done per second = Weight of water delivered x total height
Work done per second = 2g ALN/60 (hs + hd)
Negative slip
As we've got mentioned above that slip in reciprocating pump is essentially the distinction among the theoretical discharge and real discharge of the reciprocating pump.
If real discharge is greater than the theoretical discharge, slip of the reciprocating pump might be poor and it is able to be concluded via way of means of thinking about the equation of slip of reciprocating pump.
Negative slip will arise while suction pipe is long, shipping pipe is brief and pump is jogging at excessive speed.
So, we've got visible in short describe the reciprocating pump and essentially we've got mentioned right here the slip and poor slip in reciprocating pump.
You need to additionally discover the diverse critical posts as noted under and those are pretty critical and beneficial and consequently you ought to see those posts.
Positive and poor outcomes of friction, classifications of friction, coulomb's regulation of dry friction, a few tips for fixing frictional problems, idea of rolling resistance or rolling friction, wedge friction and idea of self- locking and the minimal preventing distance for a vehicle.
This is normally because of beginning and remaining of suction and transport valves because of water inertia. Please refer beneath photograph at the same time as studying in addition explanation.
Imagine End of suction inventory. Liquid is transferring (rushing) in the cylinder as piston is transferring outward (right here on this photograph proper facet of photograph).
As piston cannot circulate in addition as it’s already on its severe position, water will hammer transport valve. If this water hammer has sufficient pressure to raise transport valve than a few quantity of liquid will move in transport line
Before transport inventory commence. Due to this phenomena, transport inventory will throw more extent of liquid than swept extent of pump.
Q12) What is air vessels?
A12)
Air vessels – Working principle and necessity
Air vessel is a robust closed vessel as proven in figure. The pinnacle 1/2 of consists of compressed air and the decrease element consists of water or the fluid being pumped.
Air and water are separated via way of means of a bendy diaphragm which can move up or down relying at the difference in strain between the fluids.
The air charged at close to total transport strain/suction strain from the pinnacle and sealed. The air vessel is attached to the pipe traces very close to the pump, at almost the pump level.
On the transport aspect, whilst at the start and as much as the center of the transport stroke the top equals hs + hf + ha, better than the static and friction heads.
At this time a part of the water from pump will circulate the air vessel and the last will glide thru the transport pipe.
This will growth the compressed air strain. At the center stroke role the top can be enough to simply reason glide.
The entire of the glide from pump will guide to the transport pipe. At the second one 1/2 of the stroke the top can be identical to hs + hf - ha. At the placement the top can be now no longer enough to reason glide.
The compressed air strain will act at the water and water charged in advance into the air vessel will now glide out. Similar scenario prevails at the suction aspect.
At the begin and as much as the center of the suction stroke the top on the pump is better than static suction head via way of means of the quantity of acceleration head. The glide can be greater and component will circulate the air vessel.
The 2d 1/2 of the stroke water will glide out of the air vessel. In this system the rate of water with inside the transport pipe past the air vessel is uniform, and decrease than the most speed if air vessel isn't always fitted.
Necessity:
To stable the non-stop waft of liquid with uniform price of waft
To shop the suction and discharge pipe
To shop the significant quantity of labor in overcoming the frictional resistance with inside the suction and transport pipes
To run the reciprocating pump at an excessive velocity without separation
Working Principle:
Air vessel acts at the equal precept on the premise of which hydraulic accumulator and flywheel work.
When liquid will waft in to the vessel, air containing on the pinnacle of the chamber of air vessel could be compressed and whilst liquid will waft out from the vessel, air containing on the pinnacle of the chamber of air vessel could be expanded.
At begin of suction stroke of reciprocating pump or at some stage in first 1/2 of suction stroke, acceleration head could be most and therefore extra water could be required via suction pipe at some stage in beginning of suction stroke.
At the quilt of suction stroke, there could be retardation and therefore much less water could be required via the suction pipe and therefore extra water will waft to the air vessel and air vessel will save the power in phrases of water with the aid of using compressing the air contained with inside the pinnacle.
This saved power of air vessel could be applied at some stage in the begin of subsequent suction stroke.
At begin of transport stroke of reciprocating pump or at some stage in first 1/2 of transport stroke, acceleration head could be most and therefore extra water could be discharged to transport pipe of reciprocating pump at some stage in beginning of transport stroke.
In that case, extra water will waft to the air vessel and air contained above the water with inside the pinnacle of chamber could be compressed or we will say that power could be saved with inside the air vessel.
At the quilt of transport stroke, there could be retardation and therefore much less water could be discharged via the transport pipe and therefore extra water could be given with the aid of using the air vessel and air vessel will launch the power in phrases of water with the aid of using increasing the air contained with inside the pinnacle of the chamber.
Therefore, we've got visible right here the simple precept of air vessel in reciprocating pump and we've got additionally visible right here that how air vessel enables to preserve the uniform discharge with inside the operation of reciprocating pump.
Q13) What do you mean by model testing of pump?
A13)
Model testing of pumps
In instances wherein technical or monetary factors (for instance length, rotational pace and material/fluid properties) make checking out on an item or system infeasible beneath authentic situations, measurements also can be made with the aid of version checking out.
Particularly with inside the case of hydraulic turbo machinery (centrifugal pumps, water turbines, hydraulic torque converters) version checking out may be conducted: on decreased scale models, and/or with decreased rotational pace, and the usage of a replacement fluid as appropriate.
The blessings of version checking out are: decreased dimensions of the check item and the check facility, decrease strength input/running charges for the duration of checking out, probably less complicated coping with of the fluid (e.g. Bloodless water in place of warm water or toxic, flammable fluids), more precision whilst shifting the consequences of particularly specific version checking out than whilst operating with measurements taken beneath authentic situations with inside the system.
When planning, appearing and comparing version assessments and shifting the consequences to the authentic-length gadget and/or the authentic running situations, the affinity legal guidelines should be located and applied. Key issues are:
Geometric similarity should be maintained, inclusive of clearance hole widths, and, wherein possible, floor roughness.
Changes in period because of elastic and thermal deformations should additionally be located.
Test consequences should be transformed on the idea of version legal guidelines.
Dynamic similarity cannot typically be fulfilled. If infringement is unavoidable, practice corrections to the transformed consequences, e.g. Performance scale-up in instances wherein the Reynolds range equivalence is comprised in version checking out and authentic situations. Cavitation version checking out: have a look at the fluid properties (germ count, fuel line content).
Q14) Explain pump head curves in detail.
A14)
Pump head curves
The performance curve indicates the η (performance) of the pump. Efficiency is measured in %. All pumps have a ‘quality point’ (ηmax), indicating in which the pump is operating maximum efficiently.
The performance of the pump relies upon at the pump length and the high-satisfactory of the construction/production. Small pumps generally have a decrease performance than big pumps.
The pump overall performance curve indicates the correlation among media flow (Q) and the strain differential or head (H) that the pump creates.
The gadgets for Q are generally [m3/h] or [l/s]
The unit for H is generally [m] H (head) may be recalculated top (strain) with the aid of using the usage of the subsequent equation:
p = ρ x g x H [pa] p = strain [pa] ρ = density [kg/m3] g = acceleration because of gravity [m/s2] H = head [m] Flow is generally given in m3/h or l/s.
For variable-velocity pumps, the overall performance curve is given at minimal and most RPM. When numerous pumps are linked, the very last overall performance curve is carried out with the aid of using combining the traits of the person pumps.
Parallel-linked pumps are delivered horizontally to growth Q. For equal pumps, the most Q will double, but most H might be the same. This precept is usually utilized in pump systems. Series-linked pumps are delivered vertically to growth H. For equal pumps, the most H will double.
Maximum Q will stay the same. This precept is usually utilized in multi-degree pumps. The overall performance curve is used collectively with the gadget traits whilst dimensioning and choosing pumps.
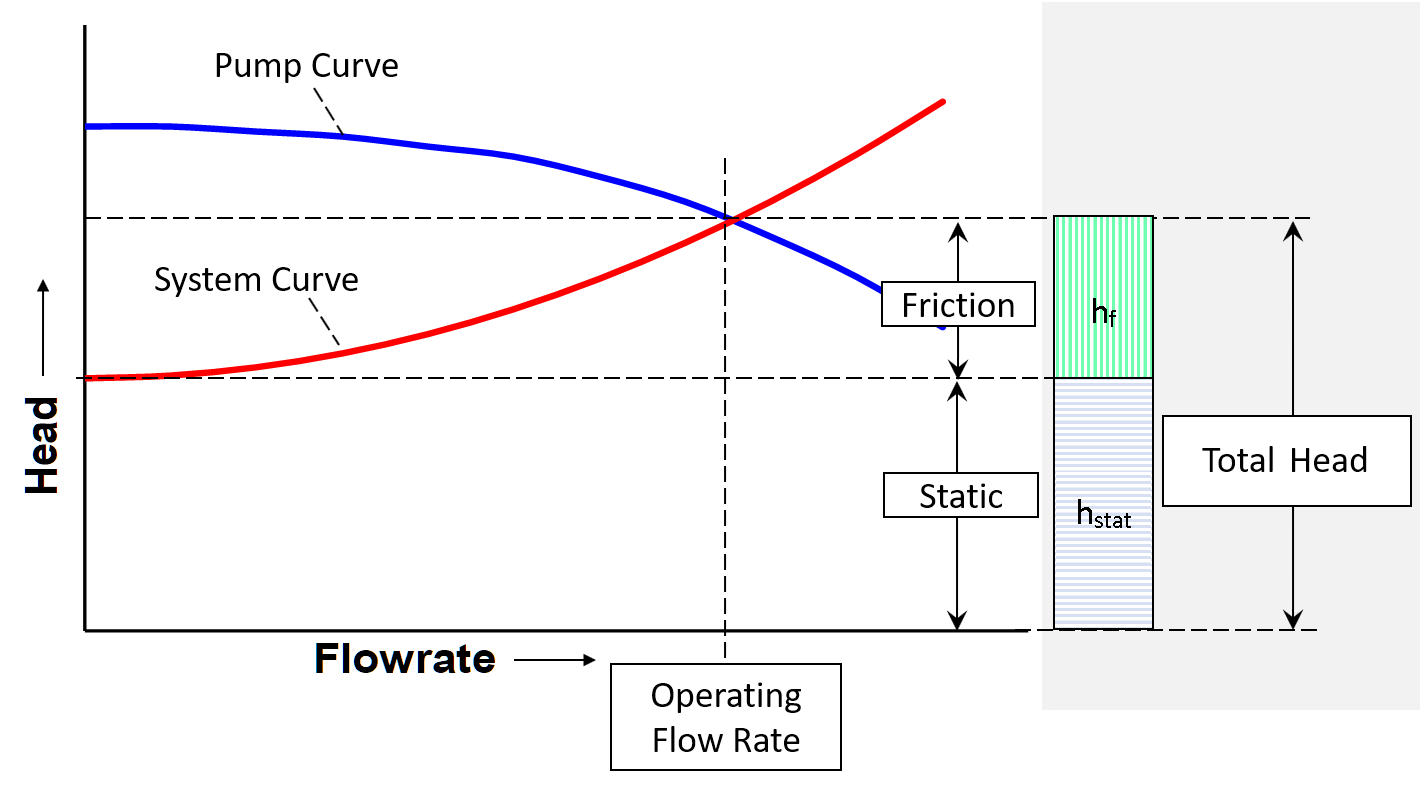
Fig: System and pump head curves
Q15) What do you mean by system head curves?
A15)
System head curves
It combines factors of the performance (H-Q) curve of the unique pump below attention with the mixed static, working, and frictional loss heads (the entire dynamic head or TDH) of the machine below layout.
The intersection factor of those curves is usually taken into consideration because the real working factor or the situation of service (COS) for the pump. System head curves may be a precious device for studying pumping structures with distinct pumps, a couple of or variable head situations, a couple of pump speeds, or numerous impeller trims at the identical sheet of paper.
They are adaptable for low or excessive head situations, a couple of float situations, or with one or extra pumping units. Formerly, machine head curves have been evolved with the aid of using the use of a tedious manner related to the plotting of numerous pump curve situations towards an alternating set of machine potential vs. Head situations.
Advancements in pc era now allow the identical kind of machine head plotting in a far shorter time and with advanced accuracy. A machine head curve is plotted in a comparable style as a pump curve, however the number one distinction entails the plotting of the machine situations.
Both curves usually observe the identical conference of plotting potential at the “x” axis towards head at the “y” axis. The unique nature of the 2 curves dictates the curve ascends, beginning with the static head, with growing head values alongside the “y” axis for the machine head curve, and descends, beginning with the pump’s shutoff head, alongside the identical axis for the pump curve.