Unit – 3
Construction Materials
Cement: Concrete is most widely used non-metallic material in construction of buildings, dams, bridges, etc. Cement act as a binder substance which is used to harden and help in binding the material together. It is used for binding material like bricks, stones, tile and also used for flooring and plastering purpose. Cement is used for construction work by mixing up of sand and crushed stones. It is a mixture of sand and water which is used in binding bricks together and for plastering purpose. On the basis of chemical composition cement can be classified into 4 different parts:
(i) Natural Cement
(ii) Puzzolona Cement
(iii) Slag Cement
(iv) Portland Cement
Portland cement: Portland cement used as the basic ingredient of the concrete worldwide. It is the most common type of cement in general use. It is the mixture of calcium silicates and calcium aluminates with small amount of gypsum in it. On mixing the powder of Portland cement with water it gives the hard, stone like mass which resembles like Portland rock this is the reason why it is named as the Portland cement.
Composition of Portland Cement: - Hydraulic cement produced by pulverizing clinkers that consists of calcium silicate, usually containing one or more of the forms of calcium sulfate as a inter ground station. A good sample of Portland cement consists of:
(i) Silica(SiO2) : - 20-24%
(ii) Calcium Oxide : - 60-70%
(iii) Alumina (Al2O3) : - 5-7%
(iv) Magnesia(MgO) : - 2-3%
(v) Ferric Oxide (Fe2O3) : - 1-2.5%
(vi) Sulphur trioxide (SO3) : - 1-1.5%
(vii) Sulphur Oxide : - 1%
(viii) Potassium Oxide (K2O) : - 1%
The raw material which are used for manufacturing of cement contains the following materials:
- Calcareous (chalk consist of limestone)
- Argillaceous (clay consist of silicates of alumina)
Wet Process manufacturing: On using the calcareous as a raw material then chalk must be crushed into minute particles and hence dispersed it in water in a wash mill. Wash mill used to break the solid materials into lumps/slurry. In similar wash mill clay is also broken up and mixed with water. Then this slurry is stored in the silo called as slurry silo where it is consistently stirred. The composition of raw material is checked again and if required corrected by adding clay or chalk materials as per requirement.
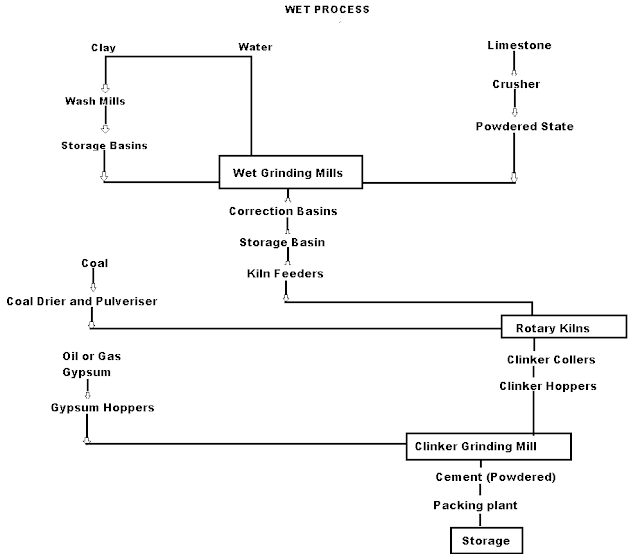
Cement Manufacturing Process Flow Chart
(i) Drying Zones : The raw material in slurry form is directly fed into the kiln which has more amount of water. It is the upper portion of the kiln. In this zone, water is evaporated at temperature 100-400°C.
(ii) Formations of modules: As the slurry gradually descends in the kiln, the carbon di oxide from slurry evaporates and small lumps formed which may be called as modules.
(iii) Burning Zone:- The modules enter in this zone where temperatures is kept about 1400-1500° C. The modules are converted into dark greenish balls and the product obtained in the kiln, known as clinker, is of varying size 5 to 20 mm. The clinkers are very hot when come out from this zone.
(iv) Cooling of Clinkers:- It is used for cool down the clinkers up to about 90°C.
Grinding: The cooled clinkers are finally ground in ball mills or tube mills.
Also, the gypsum is added during grinding about 2-4%. The gypsum acts as a retarder and so allows the cement to mix with sand or aggregate and to be placed in position. i.e. it increases the initial setting time of cement.
Storage and Packing: As cement comes out from grinding mills, it is collected in a hopper and taken in bucket elevator for storage in silos.
The cement from silos is packed by machines in bags. Each bag of cement contains 50 kg or 0.035 m3 of cement.
Dry Process manufacturing: This type of process for manufacturing the cement is available in the places where hard crystalline limestone and shales are available. The advantage of using this type of process is that fuel consumption is low.
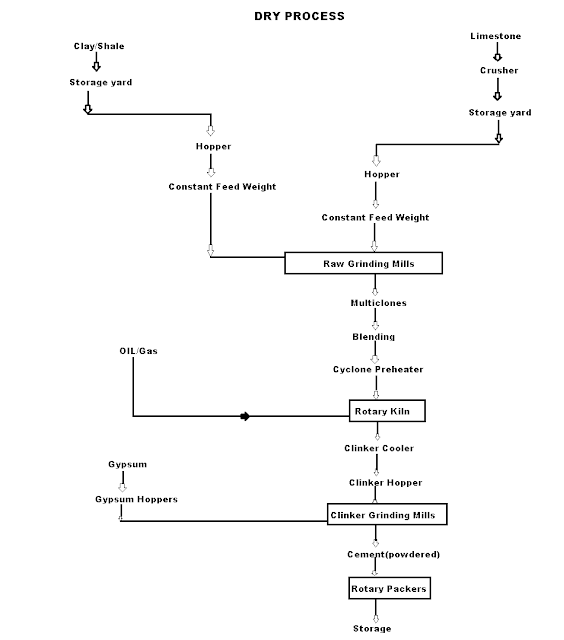
Mixing of Raw Materials: The used raw material undergo the following process:
- Crushing: The raw materials are broken in crushers to small fragments.
- Drying: The crushed materials are dried by heating at a sufficiently high temperature. It may be done in drying kilns.
- Reduction of size: The drying materials are then grind by using ball mills and tube mills to reduce the size of materials to find powder.
- Mixing in correct proportion: The finely dried materials are mixed in exact proportions. The mixing may be done either mechanically or by pneumatic methods.
Burning and Grinding: In this process, the raw materials mixed, fined and then fed into kiln whereas in the wet process, the raw materials are crushed separately and then directly mixed in correct proportion in the presence of water to make a fine thin paste known as Slurry.
The microscopic constituent and proportion of cements are:
a) Tricalcium Silicate (50%)
b) Dicalcium Silicate (25%)
c) Tricalcium Aluminate (10%)
d) Tetracalcium Aluminoferrite (10%)
e) Gypsum (5%)
Roles:
Tricalcium Silicate:
- It hardens rapidly and largely, and is responsible for initial set & early strength
- A bigger percentage of this compound will produces higher heat of hydration and accounts for faster gain in strength.
Dicalcium Silicate
- It hardens slowly
- This is responsible for long term strength
Tricalcium Aluminate
- It turns out higher heat of hydration and contributes to faster gain in strength.
- Cements with low Tricalcium Aluminate contents usually generate less heat, develop higher strengths and show greater resistance to sulfate attacks.
- It has high heat generation and reactive with soils and water containing moderate to high sulfate concentrations so it’s least desirable.
Tetracalcium Aluminoferrite
- Assist in the manufacture of Portland Cement by allowing lower clinkering temperature.
- Tetra calcium Aluminoferrite act as a filler
- Contributes very little strength of concrete even though it hydrates very rapidly.
- Also responsible for grey colour of Ordinary Portland Cement
The cement additives enhance the quality of concrete for application in construction with special requirements. Concrete admixtures is defined as the material other than water aggregates and hydraulic cement and additives like slag and fiber reinforcement, used as an ingredient of concrete or mortar and added to the batch immediately before mixing to modify the properties of concrete in the plastic or hardened state. Some of the important purposes for which additives are used are:
(i) To increase the workability without increasing water content
(ii) To retard or accelerate time of initial setting
(iii) To reduce or prevent settlement
(iv) To improve pumpability
(v) To reduce the rate of slump loss
On mixing up of cement with water to form plastic mass then it is called as cement paste. During hydration reaction, gel and crystalline products are formed. The inter-locking of the crystals binds the inert particles of the aggregates into a compact rock like material.
This process comprises of
(i) Setting
(ii) Hardening
Setting is defined as stiffening of the original plastic mass due to initial gel formation while hardening is development of strength, due to crystallization.
The hardening starts after setting as because of gradual progress of crystallization in the interior mass of cement. The strength developed by cement paste at any time depends upon the amount of gel formed and the extent of crystallization. The setting and hardening of cement is due to the formation of inter locking crystals reinforced by rigid gels formed by the hydration and hydrolysis of the constitutional compounds.
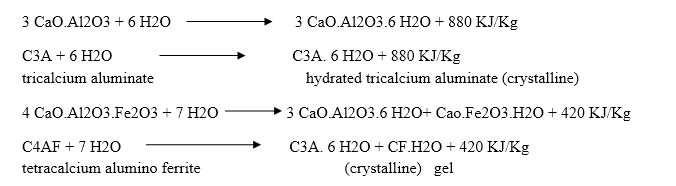
Dicalcium silicate also hydrolyses to tobermonite gel which contributes to initial setting.

Final setting and hardening of cement paste is due to the formation of tobermonite gel and crystallization of calcium hydroxide and hydrated tricalcium aluminate.

During setting and hardening of cement, some amount of heat is liberated due to hydration and hydrolysis reactions. The quantity of heat evolved during hydration of cement is 500 KJ/Kg.
Function of gypsum in cement :-
Tri calcium aluminate combines with water very rapidly.

After the initial setting, the paste becomes soft and the added gypsum retards the dissolution of tri calcium aluminate by forming insoluble calcium sulpho aluminate.
The heat generated at the time when the reaction took place between water and Portland cement. This is majorly influenced by the preparation of C3S and C3A in the cement instead it is also influenced by the cement water ratio. The heat of hydration changes according to these factors as each of these factors increased the heat of hydration increases. In large mass concrete structures such as gravity dams, hydration heat is produced significantly faster than it can be dissipated (especially in the center of large concrete masses), which can create high temperatures in the center of these large concrete masses that, in turn, may cause undesirable stresses as the concrete cools to ambient temperature.
Factors affecting the Heat of Hydration:
(i) According to the requirement the material selection should be done.
(ii) Cements with higher tricalcium silicate, tricalcium aluminate influence the rate of heat generation.
(iii) The cement content, water-cement ratio, placing and curing temperature.
(iv) The higher cement content generates more heat.
Characteristics of cements:
(i) The color of cement is grey with greenish shade. It gives an indication of excess lime or clay and the degree of burning.
(ii) It should feel smooth when touched or rubbed in between fingers.
(iii) It feels cool when the hands are inserted inside the cement bag
(iv) Cement should be free from any hard lumps
(v) Cement bag should not contain excess silica , lime, alumina or alkalies.
Applications of cement:
(i) Cements are used for wall making, plaster, pointing etc.
(ii) Concrete for laying floors, roof, beams etc
(iii) Construction of important engineering structures such as bridges, dams, tunnel etc
(iv) Construction of water tanks, well, courts, septic tanks etc
(v) Preparation of foundations, watertight floor, footpaths etc.
There are major thirteen types of cements:
(i) Ordinary Portland Cement
(ii) Portland Pozzolana Cement
(iii) Rapid hardening cement
(iv) Quick Setting Cement
(v) Low Heat Cement
(vi) Sulfates Resisting Cement
(vii) Blast Furnace Slag Cement
(viii) High Alumina Cement
(ix) White Cement
(x) Colored Cement
(xi) Air Entraining Cement
(xii) Expansive Cement
(xiii) Hydrographic Cement
Ordinary Portland Cement: Ordinary Portland Cement is the most widely used type of cement that is suitable for all general concrete construction with the annual global production of 3.8 million cubic meters.
Portland Pozzolana Cement: This cement is prepared by grinding pozzolanic clinker with Portland cement. It can also be produced by the mixing up of pozzolana with gypsum or calcium sulfate. It is used in marine structures, seawage works, laying underwater concrete etc.
Rapid Hardening Cement: This cement is used in concrete where formworks are removed at an early stage and are similar to ordinary Portland cement. This cement has increased lime content. The strength of rapid hardening cement at three days is similar to 7 days strength of OPC with the same water cement ratio. Hence, it increases the rate of construction with decreasing the cost of construction by saving formwork cost.
Quick Setting Cement: This type of cement gains the strength quickly. This type of cement can be used where the time period for the allotted work is very low.
Low Heat Cement: This type of cement can be produce by maintaining the percentage of tricalcium aluminate below 6% by increasing the proportion of C2S. The lesser quantity of tricalcium aluminate make the concrete to produce low heat of hydration. This cement has increased power against sulphates and is less reactive.
Sulfates Resisting Cement: This type of cement is used to reduce the risk of sulfate attack on concrete hence it is used in the construction of foundation where the sulfate content is high in the soil.
Blast Furnace Slag Cement: This can be obtained by grinding the clinkers with about 60% slag and resembles more or less in properties of Portland Cement.
High Alumina Cement: This type of cement can be obtained by the melting the mixture of bauxite and limeand grinding it with the clinker. The compressive strength of this cement is very high and more workable than ordinary Portland cement and is used in the work where concrete is subjected at high temperatures, frost and acidic action.
White Cement: These type of cements are generally prepared from the raw materials that is free from iron oxide. These cement are costlier and is majorly used for architectural purpose such as precast curtain wall and facing panel.
Colored cement: It is produced by mixing 5-10% mineral pigments with ordinary cement. These type of cement are widely used in decorating purpose.
Air Entraining Cement: This type of cement are produced by adding indigenous air-entraining agents as resins, glues etc. This cement can be used with the smaller water rat
Ready mix concrete is the concrete manufactured in the batch plant. This plant combines the precise amount of gravel, sand and water together by weight. The developed mixture is implemented on the construction site. The ready mix concrete is used generally in the large projects like high rise buildings and bridges. This concrete posses the long life span when compared to other material. It is the mixture of Portland cement, water and aggregates, sand, gravel or crushed stones.
Advantage of Ready Mix Concrete:
(i) Ready Mix Concrete (RMC) allows speedy construction through programmed delivery at site.
(ii) RMC reduces the labour cost and site supervising cost.
(iii) RMC comes with consistency in quality through accurate & computerized control of sand aggregates and water as per mix designs.
(iv) Production of RMC helps in minimizing cement wastage due to bulk handling.
(v) Production of RMC is relatively pollution free.
(vi) Reduced project time resulting in savings in all aspects.
(vii) Proper control and economy in use of raw material resulting in saving of natural resources.
Disadvantage of Ready Mix Concrete:
(i) The materials are batched at a central plant, and the mixing begins at that plant. So the travelling time from the plant to the site is critical over longer distances. Some sites are just too far away, which can risk that ready mix concrete may become unusable due to setting.
(ii) It will generate additional road traffic.
(iii) Concrete’s limited time span between mixing and curing means that ready-mix should be placed within 210 minutes of batching at the plant.
Fly Ash:
Fly ash is the byproduct of burning pulverized coal in electric generation power plants. Fly ash consists of aluminous and siliceous material that form the cement in the presence of water. On mixing up of fly ash with lime and water then it form the compound that is very similar to the Portland Cement. This makes the fly ash suitable as prime material in blended cement, mosaic tiles, and other building material. Fly ash improves the strength and segregation of the concrete and makes it easier to pump.
Advantages:
(i) These are cold weather resistance
(ii) Fly can be used as an admixture
(iii) Fly Ash are high strength gains, depending on use
(iv) They reduces crack problems, permeability and bleeding
Limitations:
(i) Increases need for air-entraining admixtures
(ii) Seasonal limitation
(iii) Slower strength gain
(iv) Increase of salt scaling produced by higher proportions of fly ash
Application:
(v) Fly Ash can be used as the prime material in many cement based products.
(vi) Fly Ash is most commonly used in Portland Cement Concrete Pavement.
(vii) Fly Ash usage is economically beneficial.
(viii) This is also used as embankment and mine fill.
Reference Books:
1. A Text book of Engineering Chemistry : Shashi Chawla; Dhanpat Rai & Sons, New Delhi.
2. A textbook of Polymer Science : Fred, Billmeyer Jr. ,Wiley India Third edition.
3. Applied Chemistry by N. Krishnamurthy:P. Vallinavagam. And K. Jeysubramanian TMH
4. Applied Chemistry for Engineers : T.S. Gyngell.
5. Chemistry of Advanced Materials : CNR Rao, Rsc Publication.
6. Chemistry of Engineering Materials: Robert B Leighou Mc Graw – Hill Book Company, Inc New York
7. Engineering Materials: Kenneth G Budinski (Prentice – Hall of India)
8. Fuels and Combustion by Amir Circar, Orient Longmans
9. Fundamentals of Engineering Chemistry (Theory and Practice) :S. K. Singh (New Age Materials
10. Materials Science and Engineering an Introduction, William D. Callister, (Jr. Wiley publisher).
11. Fundamentals of Corrosion : Michael Henthorne, Chemical Engineering.
12. Water Treatment : F. I. Bilane, Mir publisher