Unit – 1
Introduction to Civil Engineering Content
Civil Engineering is that field of engineering concerned with planning, design and construction for environmental Control, development of natural resources, buildings, transportation facilities and other structures required for health, welfare, safety, employment and pleasure of mankind"
The main scope of civil engineering or the task of civil engineering is planning, designing, estimating, supervising construction, managing construction, execution, and maintenance of structures like building, roads, bridges, dams, etc. ' One who designs and maintains works of public utility is known as civil engineer. Civil engineer should have qualities like scientific attitude, imaginative and intuitive approach, He should have good analysis and decision power. He should be able to solve engineering problems, by using mathematical modelling, scientific principles and laboratory techniques using computer and information technology. He should be able to use operation research techniques for solution of management problems.
A civil engineer has to conceive, plan, estimate, get approval, create and maintain all civil engineering activities.
Civil engineer has very important role in the development of the following infrastructure:
- Measure and map the earth’s surface.
- Plan new townships and extension of existing towns
- Build the suitable structures for the rural and urban areas for various utilities
- Build tanks and dams to exploit water resources.
- Build river navigation and flood control projects.
- Provide and maintain communication systems like roads, railways, harbours and airports
- Purify and supply water to the needy areas like houses, schools, offices etc.
- Build canals and distributaries to take water to agricultural fields
- Devise systems for control and efficient flow of traffic
- Provide and maintain solid and waste water disposal system
- Monitor land, water and air pollution and take measures to control them
Fast growing industrialization has put heavy responsibilities on civil engineers to preserve and protect environment.
Selection of site
Site selection indicates the practice of new facility location, both for business and government. Site selection involves measuring the needs of a new project against the merits of potential locations. The practice came of age during the 20th century, as governments and corporate operations expanded to new geographies on a national and international scale
Factors affecting selection of site
The site for a residential building should, present a peaceful environment , good landscape, sun for the most part of the day and uninterrupted flow of natural air. The following factors need to be studied in depth, while selecting the site for a residential building:
- Topography
- Nature of sub-soil
- Position of the ground water table
- Facilities
- Neighbourhood
- Undesirable things near the site
- Vegetation
- Shape of the site
- Availability of men and materials
- Proximity to sea-shore, river or lake or the place of natural beauty
Basic functions of buildings, types of buildings – Residential, Public, Commercial, and Industrial
A building structure is a man-made structure with a roof and walls standing more or less permanently in one place, such as a house or factory.
Buildings are classified into two categories.
- Based on the occupancy.
- Based on the type of construction
Buildings classified, based on the occupancy: Every building or portion of land shall be classified according to its use or the character of its occupancy as a building of Occupancy.
They are categorized into the following types
- Agricultural buildings
- Commercial buildings
- Residential buildings
- Educational buildings
- Government buildings
- Industrial buildings
- Military buildings
- Religious buildings
- Transport buildings
- Power plants
Residential buildings:
A Residential building is that, in which housing predominates, as opposed to industrial and commercial areas. Building may vary significantly between, single-family building, multi-family building, or mobile homes. Apartment Villa Bungalow Nursing home.
Industrial buildings
These buildings are designed to house industrial operations and provide the necessary conditions for workers, and for the operation of industrial equipment. Factory Water mill Foundry Power plant Wind mill Tide mill.
Commercial buildings
They are the buildings, which are used exclusively for commercial use. Automobile companies Ware house Bank Convention centers Gas stations
Importance of Planning, Scheduling, and Construction Management
Management is a social and scientific process of defining the objectives, planning, organizing, coordinating, motivating, controlling and harnessing the resources of an organization at the optimum level to achieve predetermined goal.
Principal of Planning
- Aspect
- Prospect
- Privacy
- Circulation
- Roominess
- Grouping
- Elegance
- Sanitation
- Flexibility
- Economy
- Practical consideration
Aspect
Placement of different rooms of house in accordance with our activities at different hours of day. Rooms should get enough sunlight and air, which gives, Great environment , Comfort etc . A room which receives light & air from particular direction is said to have ‘aspect’ of that direction.
Prospect
Prospect is the view from outside of a house. The house should have a proper prospect so that it can give a feeling of cheerfulness to the people living in it. It should create a good impression on a person who views it from outside. It must also possess good qualities like comfort, cheerfulness, security, labour saving and modern outlook. For e.g. Small Projections or bay window can have a good out-look as well as helps in providing breeze, light and sunlight to the room.
Privacy
It is an important principle while planning a residential building. Privacy can be maintained in ways: 1. External 2. Internal
- External Privacy
The privacy from sides can be secured by providing planned entrance and pathways. This can achieved by screening the front and rear entrance.
2. Internal Privacy
Privacy in internal rooms can be easily obtain by proper planning of diff. Areas and location of doors and windows. The shutter when opened should give the minimum view of room for an entering persons.
Circulation
Circulation is movement within the premises and includes both horizontal and vertical circulation. Horizontal circulation ( room to room) ,Passage , Corridors , Lobbies etc. Vertical circulation (floor to floor) - Stairs
Roominess
Roominess means getting maximum advantage from the minimum dimension of the room. The effect of roominess depend on the relative dimension of length, width and height of room. The shape and size of the room are also very important for roominess. A rectangular room has more roominess then square room in same area.
Grouping
Grouping means the arrangement of various rooms in the building for the convenience of user. It minimizes the circulation and at the same time improves the comfort. A dining room should be close to kitchen ,while sanitary be away from kitchen, but convenient to bed rooms.
Elegance
Elegance is grand appearance of a building attained mainly owing to the elevation which in turn depends on the plan. It depends upon proper positioning/selection of doors, windows, balcony, roofs, staircase etc. For better elegance . Selecting superior building material for facing as polished stone- granite, marble or mosaic. Providing projection like sunshades, balconies, porch with or without pergola opening. Providing bay window, corner window, etc.
Sanitation
It includes providing light ,ventilation, cleanliness, water supply and sanitary amenities. For residential building window area should not less then 1/10th of floor area. In school not less than 1/5th of the floor area.
Flexibility
Flexibility means that a room which is planned for one function be used for other, if required. Like study room may be planned for using guest room. Etc.
Economy
The building should have minimum floor area with maximum utility. It will reduce cost of the building .hence, it will be economical. Economy can achieved by: Providing simple elevation. Reducing the storey height. Dispensing of porches, lobbies and balconies.
Practical Consideration
After the all fundamental some practical points should be additionally considered: Provision for future extensions without dismantling should be made while planning. Strength, stability, convenience and comfort of occupants, should be the first consideration while planning. As far as possible sizes of rooms should be kept large. Large room can be shortened by providing movable partition but smaller room cannot be enlarge easily. The number of door and window should be minimum provisions for built in furniture at proper places are useful from point of view of utility.
Orientation of buildings
Orientation is the positioning of a building in relation to seasonal variations in the sun’s path as well as prevailing wind patterns. Good orientation can increase the energy efficiency of your home, making it more comfortable to live in and cheaper to run.
Principles of good orientation
Good orientation, combined with other energy efficiency features, can reduce or even eliminate the need for auxiliary heating and cooling, resulting in lower energy bills, reduced greenhouse gas emissions and improved comfort. It takes account of summer and winter variations in the sun’s path as well as the direction and type of winds, such as cooling breezes.
Good orientation can help reduce or even eliminate the need for auxiliary heating and cooling, resulting in lower energy bills, reduced greenhouse gas emissions and improved comfort.
Ideally, choose a site or home with good orientation for your climatic and regional conditions and build or renovate to maximize the site’s potential for passive heating and passive cooling, adjusting the focus on each to suit the climate. For those sites that are not ideally orientated, there are strategies for overcoming some of the challenges.
In hot humid climates and hot dry climates with no winter heating requirements, aim to exclude direct sun by using trees and adjoining buildings to shade every façade year round while capturing and funnelling cooling breezes.
Height of building
Building height means the average maximum vertical height of a building or structure measured at a minimum of three equidistant points from finished grade to the highest point on the building or structure along each building elevation. Architectural elements that do not add floor area to a building or structure, such as parapet walls, chimneys, vents, and roof equipment are not considered part of the height of a building or structure (See page 3 for special restrictions in the Central Business and Waterway Overlay zones).
Height of building according to width of street:
1. The maximum height of the building shall not exceed 1.5 times the width of road.
2. For building in vicinity of aerodromes, the maximum height of the building is fixed in consultation with civil aviation authorities.
The height shall not included if building is erected one-third of roof area, including:
1. Roof tank and its support
2. Ventilating, lift room
3. Roof structure other than pent-house
Open space requirement
Open air space for ventilation. Every room intended for human habitation should abut an interior or exterior opening air space of the width r dimensions specified below.
F.S.I.,
FSI stands for Floor Space Index also known as Floor Area Ratio (FAR). FSI means the ratio between the area of a covered floor (Built up Area) to the area of that plot (land) on which a building stands.
It is calculated by dividing the total covered built-up area on all floors of a building by the area of the plot it stands on. For instance, if you have 1,000 square feet of land on which you want to build a residential or commercial building and the FSI in your locality is 1.5, then you could build up to 1,500 sq.
Carpet area
Carpet area is the area that can be used to spread a carpet inside the house. It is the net usable area of the apartment. It includes the thickness of the internal wall but excludes balcony or terrace. Technically, the distance between inner walls is carpet area.
Built up area
Built up Area is the carpet area plus the thickness of outer walls and the balcony. Super Built Up Area is the built up area plus proportionate area of common areas such as the lobby, lifts shaft, stairs, etc. Sometimes it may also include the common areas such, swimming pool, garden, clubhouse, etc.
Setbacks
In land use, a setback is the minimum distance which a building or other structure must be set back from a street or road, a river or other stream, a shore or flood plain, or any other place which is deemed to need protection.
Ventilation
Ventilation moves outdoor air into a building or a room, and distributes the air within the building or room. The general purpose of ventilation in buildings is to provide healthy air for breathing by both diluting the pollutants originating in the building and removing the pollutants from it
Building ventilation has three basic elements:
- Ventilation rate — the amount of outdoor air that is provided into the space, and the quality of the outdoor air
- Airflow direction — the overall airflow direction in a building, which should be from clean zones to dirty zones; and
- Air distribution or airflow pattern — the external air should be delivered to each part of the space in an efficient manner and the airborne pollutants generated in each part of the space should also be removed in an efficient manner.
There are three methods that may be used to ventilate a building: natural, mechanical and hybrid (mixed-mode) ventilation.
INTRODUCTION
Simply, loads are some sort of force. Major types of loads:
- Dead loads. (red arrow) - Exerted by the weight of the element of the structure.
- Live loads. (rest arrow) - Exerted by any temporary force acting on the structure Loads in simple structure
DEAD LOADS
Dead Loads are those loads which are considered to act permanently; they are "dead," stationary, and unable to be removed. The self-weight of the structural members normally provides the largest portion of the dead load of a building. Exerted by the weight of the element of the structure
LIVE LOADS
Live Loads are not permanent and can change in magnitude.They include items found within a building LIVE LOADS All the arrows indicate the live loads unless the red one.
Wind load
The wind's relatively large projected areas can develop substantial forces in the structure.
Earthquake loads are another lateral live load.
They are very complex, uncertain, and potentially more damaging than wind loads. LIVE LOADS EARTHQUAKE LOADS: Mass tends to remain in its original position, deformation due to sudden ground moving take place at the base
POINT LOAD OR CONCENTRATED LOAD
The load concentrated at one point is called point load. Unit of point load is N or kN. e.g. 20kN,100N etc. W1 and W2 are point loads.
UNIFORMLY DISTRIBUTED LOAD
Load uniformly distributed on certain length of a beam is called uniformly distributed load. It is written as u.d.l. It is shown by w. Unit of u.d.l. Is kN/m or N/m.
UNIFORMLY VARYING LOAD
This type of load gradually increase or decrease on the length of the beam. It is also called triangular load.
Soils are divided into three major groups, coarse grained, fine grained and highly organic. The classification is based on classification test results namely grain size analysis and consistency test. The coarse grained soils shall be classified using Table Outlines of organic and inorganic soil separations are also provided in Table The fine grained soils shall be classified using the plasticity chart. In addition to these classifications, a soil shall be described by its colour, particle angularity (for coarse grained soils) and consistency. Further to the above classification soils exhibiting swelling or collapsing characteristic shall be recorded. For undisturbed soils information on stratification, degree of compactness, cementation, moisture conditions and drainage characteristics shall be included.
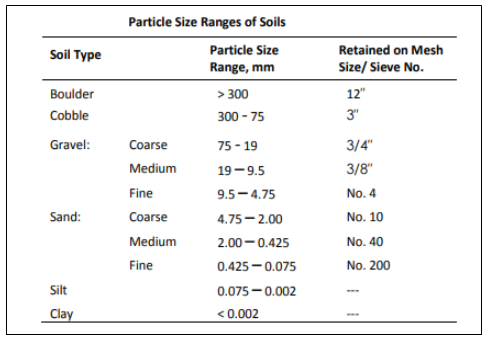
1. Sand
It is most extensively used construction material. It consists of particles of rock and hard minerals, such as silicon dioxide. They are the largest type of soil particles, where each particle is visible to naked eye. The large, relatively stable sand-particle size increases soil aeration, improves drainage in tight soils and creates plant-growth supporting qualities, or tilt.
Sand
The particle size of course sand ranges from 2 – 4.75mm, Medium sand ranges from 0.425 – 2 mm and fine sand ranges from 0.075 – 0.425 mm. The bigger particle size of the sand gives wet or dry sandy soil a grainy texture when you rub it between your fingers, and it makes the soil light and crumbly even when you try to stick it together in your hand. The particle shape is angular, sub angular, rounded, flat or elongated. The texture is rough, smooth, or polished.
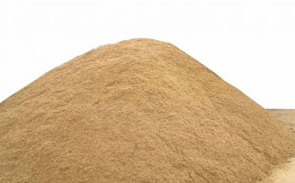
2. Silt
Silt is a sediment material with an intermediate size between sand and clay. Carried by water during flood it forms a fertile deposit on valleys floor. The particle size of silt ranges from 0.002 and 0.06 mm.
Silt in wet condition
Silt is a non-plastic or low plasticity material due to its fineness. Due to its fineness, when wet it becomes a smooth mud that you can form easily into balls or other shapes in your hand and when silt soil is very wet, it blends seamlessly with water to form fine, runny puddles of mud.

3. Clay
Clay particles are the finest of all the soil particles, measuring fewer than 0.002 mm in size. It consists of microscopic and sub-microscopic particles derived from the chemical decomposition of rocks. Clay is a fine grained cohesive soil. They stick together readily and form a sticky or gluey texture when they are wet or dry.
Clay when mixed with water
Clay is made of over 25 percent clay, and because of the spaces found between clay particles, clay soils hold a high amount of water. Clay expand when in contact with water and shrink when getting dry. Compared to sand particles, which are generally round, clay particles are thin, flat and covered with tiny plates. Organic clay is highly compressible and its strength is very high when dry, which is why it is used in construction as mud mortar.
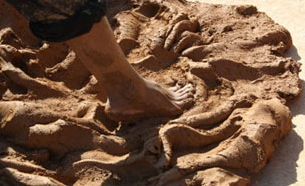
4. Loam
Loam is a mixture of clay, sand and silt and benefits from the qualities of these 3 different textures, favouring water retention, air circulation, drainage and fertility. These soils are fertile, easy to work with and provide good drainage. Depending on their predominant composition they can be either sandy or clay loam.
Loam
The way the other particles combine in the soil makes the loam. For instance, a soil that is 30 per cent clay, 50 per cent sand and 20 per cent silt is a sandy clay loam, with the soil types before “loam” listed in the order their particles are most dominant in the loam. The labels “clay loam,” “silt loam” and “sand loam” are used to refer to soils that are composed predominantly of those ingredients.
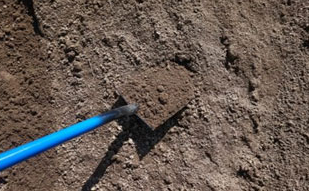
Concept of bearing capacity
In geotechnical engineering, bearing capacity is the capacity of soil to support the loads applied to the ground. The bearing capacity of soil is the maximum average contact pressure between the foundation and the soil which should not produce shear failure in the soil. Ultimate bearing capacity is the theoretical maximum pressure which can be supported without failure; allowable bearing capacity is the ultimate bearing capacity divided by a factor of safety. Sometimes, on soft soil sites, large settlements may occur under loaded foundations without actual shear failure occurring; in such cases, the allowable bearing capacity is based on the maximum allowable settlement.
There are three modes of failure that limit bearing capacity: general shear failure, local shear failure, and punching shear failure. It depends upon the shear strength of soil as well as shape, size, depth and type of foundation.
Types of foundation and their suitability
FOUNDATION:
Lower part of the structure which is in direct contact with the soil and transmits loads to the ground.
- DEEP FOUNDATION: A foundation unit that provides support for a structure transferring loads by end bearing and/or by shaft resistance at considerable depth below the ground. Generally, the depth is at least five times the least dimension of the foundation.
- SHALLOW FOUNDATION: A foundation unit that provides support for a structure transferring loads at a small depth below the ground. Generally, the depth is less than two times the least dimension of the foundation.
- FOUNDATION ENGINEER: A graduate Engineer with at least five years of experience in civil engineering particularly in foundation design or construction.
Load Bearing construction
Loadbearing walls in small buildingsin the case of a small building, brick walls will often have the abilityto also support other parts of the building (that is, to be loadbearing) without any particular modification. Masonry has traditionally been used as the principal loadbearing system for buildings, ranging from small single storey housing to fairly tall commercial and industrial buildings. In most cases, some thought will have to be given to theform and detailing of the walls to make sure they are suitable to carry these loads. In order to carry vertical loads, the wall has to be continuous from top to bottom. Ideally, openings should be rather narrow and in line vertically, rather than wide or haphazardly located on the elevation. Since walls rely on intersecting with each other to provide some oftheir stability, continuous vertical openings would turn the wall into aseries of isolated piers. This layout would only be efficient if thefloors each served to tie the separate piers together at each level. The Building Code of Australia requires lintels over openings inloadbearing walls to have the same Fire Resistance Level (FRL) as thewall itself, unless it falls within the scope of certain exemptions. The exemptions allow non fire rated lintels in single storey buildings, andin other buildings where the span does not exceed 1.8m and the wallor leaf is not more than 150mm thick. In practice, this is another reason for limiting the width of openings in load bearing walls. Layout of walls to support floor loads In order to use the walls to support floor loads, we first have toconsider a suitable span for the floor structure. Conventional timberjoist floors seldom span more than 4 or 5 metres. Domestic concreteslabs only improve on these spans a little, while commercial flatconcrete slabs commonly cover 6 to 8 metres between supports, and floors using steel or concrete beams can extend these limits a little. Slab systems can be continuously supported on walls, but beamsystems usually need thickened piers under the beams.
Frame Construction
Framed buildings are building structures formed by the framed elements usually in the form of columns and beams, as well as further strengthened as necessary by the introduction of rigid floor membranes and external walls.
Composite Construction
In structural engineering, composite construction exists when two different materials are bound together so strongly that they act together as a single unit from a structural point of view. When this occurs, it is called composite action. One common example involves steel beams supporting concrete floor slabs. If the beam is not connected firmly to the slab, then the slab transfers all of its weight to the beam and the slab contributes nothing to the load carrying capability of the beam. However, if the slab is connected positively to the beam with studs, then a portion of the slab can be assumed to act compositely with the beam. In effect, this composite creates a larger and stronger beam than would be provided by the steel beam alone. The structural engineer may calculate a transformed section as one step in analyzing the load carry capability of the composite beam.
Cement
Cement is a binder, a substance that sets and hardens and can bind other materials together. Cements used in construction can be characterized as being either hydraulic or non-hydraulic, depending upon the ability of the cement to be used in the presence of water. Non-hydraulic cement will not set in wet conditions or underwater, rather it sets as it dries and reacts with carbon dioxide in the air. It can be attacked by some aggressive chemicals after setting. Hydraulic cement is made by replacing some of the cement in a mix with activated aluminium silicates, pozzolanas, such as fly ash. The chemical reaction results in hydrates that are not very water-soluble and so are quite durable in water and safe from chemical attack. This allows setting in wet condition or underwater and further protects the hardened material from chemical attack (e.g., Portland cement).
Use
Cement mortar for Masonry work, plaster and pointing etc.
Concrete for laying floors, roofs and constructing lintels, beams, weather shed, stairs, pillars etc.
Construction for important engineering structures such as bridge, culverts, dams, tunnels, light house, clocks, etc.
Construction of water, wells, tennis courts, septic tanks, lamp posts, telephone cabins etc.
Making joint for joints, pipes, etc.
Manufacturing of precast pipes, garden seats, artistically designed wens, flower posts, etc.
Preparation of foundation, water tight floors, footpaths, etc.
Types of Cements
Many types of cements are available in markets with different compositions and for use in different environmental conditions and specialized applications. A list of some commonly used cement is described in this section:
Ordinary Portland cement
Ordinary Portland cement is the most common type of cement in general use around the world. This cement is made by heating limestone (calcium carbonate) with small quantities of other materials (such as clay) to 1450°C in a kiln, in a process known as calcination, whereby a molecule of carbon dioxide is liberated from the calcium carbonate to form calcium oxide, or quicklime, which is then blended with the other materials that have been included in the mix. The resulting hard substance, called 'clinker', is then ground with a small amount of gypsum into a powder to make 'Ordinary Portland Cement'(often referred to as OPC). Portland cement is a basic ingredient of concrete, mortar and most non-specialty grout. The most common use for Portland cement is in the production of concrete. Concrete is a composite material consisting of aggregate (gravel and sand), cement, and water. As a construction material, concrete can be cast in almost any shape desired, and once hardened, can become a structural (load bearing) element. Portland cement may be grey or white.
Rapid hardening Portland cement
- It is firmer than Ordinary Portland Cement
- It contains more C3S are less C2S than the ordinary Portland cement.
- Its 3 days strength is same as 7 days strength of ordinary Portland cement. Low heat Portland cement
- Heat generated in ordinary Portland cement at the end of 3days 80 cal/gm. While in low heat cement it is about 50cal/gm of cement.
- It has low percentage of C3A and relatively more C2S and less C3S than O.P. Cement.
- Reduce and delay the heat of hydration. British standard ( B S. 1370 : 1974 ) limit the heat of hydration of this cement.
Sulphate resisting Portland cement
- For this cement, the silage as obtained from blast furnace is used
- The clinkers of cement are ground with about 60 to 65 percent of slag.
- Its strength in early days is less and hence it required longer curing period. It proves to be economical as slag, which is a Waste product, is used in its manufactures.
Pozzolanic cement
- As per Indian standard, the proportions of Pozzolana may be 10 to 25 % by weight. e.2. Burnt clay, shale, Fly ash.
- This Cement has higher resistance to chemical agencies and to sea water because of absence of lime.
- It evolves less heat and initial strength is less but final strength is 28 days onward equal to ordinary Portland cement.
- It possesses less resistance to the erosion and weathering action.
- It imparts higher degree of water tightness and it is cheap.
White Portland cement
- Grey colour of O.P. Cement is due to presence of Iron Oxide. Hence in White Cement Fe, O, is limited to 1 %. Sodium Alumina Ferrite (Crinoline) NavAlF6 is added to act as flux in the absence of Iron-Oxide.
- It is quick drying, possesses high strength and has superior aesthetic values and it also cost lee than ordinary Cement because of specific requirements imposed upon the raw materials and the manufacturing process. White Cement are used in Swimming pools, for painting garden furniture, moulding sculptures and statues etc.
Coloured Portland Cement
- The Cement of desired colour may be obtained by mixing mineral pigments with ordinary Cement.
- The amount of colouring material may vary from 5 to 10 percent. If this percentage exceeds 10percent, the strength of cements is affected.
- The iron Oxide in different proportions gives brown, red or yellow colour. The coloured Cement are widely used for finishing of floors, window sill slabs, stair treads etc.
Expansive cement
- This type of cement is produced by adding an expanding medium like sulpho aluminate and a stabilising agent to the ordinary cement.
- The expanding cement is used for the construction of water retaining structures and for repairing the damaged concrete surfaces.
High alumina cement
- This cement is produced by grilling clinkers formed by calcining bauxite and lime. It can stand high temper lures.
- If evolves great heat during setting. It is therefore not affected by frost.
Bricks
Bricks are small rectangular blocks that can be used to form parts of buildings, typically walls. The use of bricks dates back to before 7,000 BC, when the earliest bricks were formed from hand-moulded mud and dried in the sun. During the Industrial Revolution, mass-produced bricks became a common alternative to stone, which could be more expensive, less predictable and more difficult to handle.
Bricks are still in common use today for the construction of walls and paving and for more complex features such as columns, arches, fireplaces and chimneys. They remain popular because they are relatively small and easy to handle, can be extremely strong in compression, are durable and low maintenance, they can be built up into complex shapes and can be visually attractive.
However, more recently, other materials have been developed that can be used as alternatives for building walls or for cladding facades and for some building types, particularly larger buildings, bricks can be seen as time consuming, expensive (although this is disputed by the Brick Development Association), structurally limiting, and requiring too much on-site labour. Some of these difficulties have been overcome by the introduction of reinforcement systems and by the development of pre-fabricated brick panels.
Constituents of good brick earth:
Bricks are the most commonly used construction material. Bricks are prepared by moulding clay in rectangular blocks of uniform size and then drying and burning these blocks. In order to get a good quality brick, the brick earth should contain the following constituents.
- Silica
- Alumina
- Lime
- Iron oxide
- Magnesia
STONES
The process of taking out stones from natural rock beds is known as the quarrying. The term quarry is used to indicate the exposed surface of natural rocks. The stones, thus obtained, are used for various engineering purposes. The difference a mine and quarry should be noted. In case of a mine, the operations are carried out under the ground at great depth. In case of quarry, the operations are carried out at ground level in an exposed condition.
SITE FOR QUARRY-The selection of site for a quarry of stones should be done after studying carefully the following aspects:
1. Availability of tools, power, materials and labour for the efficient working of quarry.
2. Easy availability of clean water in sufficient quantity all the year round.
3. Economy in quarrying.
4. Drainage of quarrying pit.
5. Facility of carrying and conveying stones from quarry.
6. Quality of stone available from quarry.
Aggregate
Construction aggregate, or simply aggregate, is a broad category of coarse- to medium-grained particulate material used in construction, including sand, gravel, crushed stone, slag, recycled concrete and geosynthetic aggregates. Aggregates are the most mined materials in the world. Aggregates are a component of composite materials such as concrete and asphalt concrete; the aggregate serves as reinforcement to add strength to the overall composite material. Due to the relatively high hydraulic conductivity value as compared to most soils, aggregates are widely used in drainage applications such as foundation and French drains, septic drain fields, retaining wall drains, and roadside edge drains. Aggregates are also used as base material under foundations, roads, and railroads. In other words, aggregates are used as a stable foundation or road/rail base with predictable, uniform properties (e.g. To help prevent differential settling under the road or building), or as a low-cost extender that binds with more expensive cement or asphalt to form concrete.
Reinforced concrete
Reinforced concrete (RC) (also called reinforced cement concrete or RCC) is a composite material in which concrete's relatively low tensile strength and ductility are counteracted by the inclusion of reinforcement having higher tensile strength or ductility. The reinforcement is usually, though not necessarily, steel reinforcing bars (rebar) and is usually embedded passively in the concrete before the concrete sets.
Glazing Structures
The act of installing glass in windows, doors or fixed openings. To glaze a unit would be the actual installation of a piece of glass within a frame or sash. The term is also referred to as all the glass within a structure. The glazing required within a structure would be described as all of the glass required to accommodate that structure. To glaze an opening is to install the glass within the frame or sash of that opening. The glazing for a project, would identify all of the glass required for that project and is now used as a noun as opposed to the verb. In addition to the standard glass on a project the glazing for a project would normally include all of the storefront glass, the skylights, the interior fixed lites, etc. required to complete the project.
TYPES OF GLASS:
(1) Soda-lime glass
(2) Potash-lime glass
(3) Potash-lead glass
(4) Common glass
STRUCTURAL STEEL CONSTRUCTION
Structural steel is a category of steel construction material that is produced with a particular cross section or shape, and some specified values of strength and chemical composition. Structural steel composition, strength, size, shape, strength, and storage are controlled in most advanced countries. The word structural steel includes a broad variety of low carbon and manganese steels that are used in great numbers for civil and marine engineering applications. Structural steels are manufactured in section and plate shapes and are normally used in bridges, buildings, ships, and pipelines.
PCC
Plain cement concrete is generally used for the foundation. However, its other uses are:
- As bed concrete below the wall footings, column footings and on walls below beams.
- As sill concrete to get a hard and even surface at window and ventilator sills.
- As to coping concrete over the parapet and compound walls.
- For flagging the area around the buildings.
- To make pavements.
- To make tennis courts, basketball courts etc.
- Plinth Protection
- Storm/ Sewer at drains, small retaining walls.
RCC
Its full name is reinforced cement concrete, or RCC. RCC is concrete that contains steel bars, called reinforcement bars, or rebars. This combination works very well, as concrete is very strong in compression, easy to produce at site, and inexpensive, and steel is very very strong in tension.
To make reinforced concrete, one first makes a mould, called formwork, that will contain the liquid concrete and give it the form and shape we need. Then one looks at the structural engineer's drawings and places in the steel reinforcement bars, and ties them in place using wire. The tied steel is called a reinforcement cage, because it is shaped like one. Once the steel is in place, one can start to prepare the concrete, by mixing cement, sand, stone chips in a range of sizes, and water in a cement mixer, and pouring in the liquid concrete into the formwork tilll exactly the right level is reached.
The concrete will become hard in a matter of hours, but takes a month to reach its full strength. Therefore it is usually propped up until that period. During this time the concrete must be cured, or supplied with water on its surface, which it needs for the chemical reactions within to proceed properly.
Pre-stressed
Prestressed concrete is a form of concrete used in construction. It is substantially "prestressed" (compressed) during production, in a manner that strengthens it against tensile forces which will exist when in service.
This compression is produced by the tensioning of high-strength "tendons" located within or adjacent to the concrete and is done to improve the performance of the concrete in service.[4] Tendons may consist of single wires, multi-wire strands or threaded bars that are most commonly made from high-tensile steels, carbon fiber or aramid fiber. The essence of pre stressed concrete is that once the initial compression has been applied, the resulting material has the characteristics of high-strength concrete when subject to any subsequent compression forces and of ductile high-strength steel when subject to tension forces. This can result in improved structural capacity and/or serviceability compared with conventionally reinforced concrete in many situations. In a prestressed concrete member, the internal stresses are introduced in a planned manner so that the stresses resulting from the superimposed loads are counteracted to the desired degree.
Prestressed concrete is used in a wide range of building and civil structures where its improved performance can allow for longer spans, reduced structural thicknesses, and material savings compared with simple reinforced concrete. Typical applications include high-rise buildings, residential slabs, foundation systems, bridge and dam structures, silos and tanks, industrial pavements and nuclear containment structures.
Precast
Precast concrete is a construction product produced by casting concrete in a reusable mold or "form" which is then cured in a controlled environment, transported to the construction site and lifted into place ("tilt up"). In contrast, standard concrete is poured into site-specific forms and cured on site. Precast stone is distinguished from precast concrete using a fine aggregate in the mixture, so the final product approaches the appearance of naturally occurring rock or stone. More recently expanded polystyrene is being used as the cores to precast wall panels. This is lightweight and has better thermal insulation.
Ready Mix Concrete
Ready-Mix Concrete is concrete that is manufactured in a batch plant, according to a set engineered mix design. Ready-mix concrete is normally delivered in two ways.
- First is the barrel truck or in–transit mixers. This type of truck delivers concrete in a plastic state to the site.
- Second is the volumetric concrete mixer. This delivers the ready mix in a dry state and then mixes the concrete on site.
Batch plants combine a precise amount of gravel, sand, water and cement together by weight (as per mix design formulation for grade of concrete recommended by the Structural consultant), allowing specialty concrete mixtures to be developed and implemented on construction sites. The first ready-mix factory was built in the 1930s, but the industry did not begin to expand significantly until the 1960s, and it has continued to grow since then.
Ready-mix concrete is often used over other materials due to the cost and wide range of uses in building, particularly in large projects like high rise buildings and bridges.[1] It has a long life span when compared to other products of a similar use, like road ways. It has an average life span of 30 years under high traffic areas compared to the 10 to 12 year life of asphalt concrete with the same traffic.
Ready-mix concrete, or RMC as it's also known, refers to concrete that is specifically batched or manufactured for customers' construction projects, and supplied to the customer on site as a single product. It is a mixture of Portland or other cements, water and aggregates: sand, gravel, or crushed stone. All aggregates should be of a washed type material with limited amounts of fines or dirt and clay. An admixture is also added to improve work-ability of the concrete and/or increase setting time of concrete (using retarders) to factor in the time required for the transit mixer to reach the site/ place of casting.
Ready-mixed concrete is used in construction projects where the construction site is not willing, or not able, to mix concrete on site. Using ready-mixed concrete means product is delivered finished, on demand, in the specific quantity required, to the specific mix design required. For a small to medium project, the cost and time of hiring mixing equipment, labour, plus purchase and storage for the ingredients of concrete, added to environmental concerns (cement dust is a particular airborne health hazard and nuisance)may simply be not worth it when compared to the linear cost model of ready-mixed concrete, where the customer pays for what they use, and lets someone else do the work up to that point. For a large project, outsourcing concrete production to ready-mixed concrete suppliers means delegating the quality control and testing, material logistics and supply chain issues, and mix design, to specialists who are already set up for those tasks, trading off against introducing another contracted external supplier who needs to make a profit, and losing the control and immediacy of on-site mixing.
Eco friendly Materials in Construction
We are discussing here the different types of eco friendly materials used in the construction projects.
Green Concrete
Green concrete is a technology that was invented to promote sustainability within the environment. It is made up of recycled and waste materials such as mining wastes, glass wastes, mud, sawdust, burnt clay, etc.
This eco friendly material is low-maintenance and long-lasting. It was designed while keeping in mind the entire construction life cycle including the structural design, parameters, production, and maintenance. There are no harmful emissions released while using green concrete and reduced emission of CO2 into the atmosphere. It is also thermal and fire-resistant and has a long-lasting life.
Plastic bricks – An Eco friendly Materials
With an ever-increasing challenge in the disposal of plastic, technology has found a way to tackle this problem. An innovative concept has been developed where plastic is being reused. It is mixed with cement aggregates and made into the shape of bricks. This has proven to be a spectacular solution for eradicating plastic waste. Plastic material has a high ratio of tensile strength and weight.
They are also lighter than traditional bricks and have superb noise and heat-insulating properties that are more than 5 times that of normal bricks. So far, it has been used for highways and railway infrastructure and can be used for buildings. This eco-friendly construction material promotes a sustainable environment and will reduce the amount of waste that is generated on land and in water bodies.
Bamboo
Bamboo has been used as a building material for centuries now. It is a comparable material to wood and, in recent times, has also been preferred more often due to the scarcity of the wood. Bamboo has rapid regenerative properties. Due to its hard-wearing nature and low cost, it is used in the construction industry. Bamboo mat corrugated sheets are often used as a substitute for plastic, asbestos and corrugated metal that is used for roofing purposes. Bamboo roofing sheets are eco-friendly material and have a high tolerance to extreme weathering conditions. They are also easy to install.
Rice husk Ash concrete
Rice husk ash is a product of burning rice husk. The burned remains are then mixed with concrete to increase the workability of the concrete. Rice husk ash concrete shows better bond strength when compared to Portland cement. The compressive strength, split tensile strength and flexural strength of the material is greater than ordinary concrete. It is resistant to corrosion and chemicals. Rice husk ash concrete is one of its kind a eco friendly materials. Its high-performance material can be used for both small and large scale applications as an insulator, on industrial floorings, in bathrooms and swimming pools, etc.
AAC blocks
AAC blocks also called Autoclaved Aerated Concrete blocks are prepared out of industrial waste materials. They can be made into any shape or size. This material is the perfect example of converting waste materials into usable construction materials. They are energy efficient, resistant to earthquakes, mould resistant, fire-resistant, cost-cutting and have a longer life. They are generally used in the construction of wall partitions, roofing panels, floor panels, etc.
Porotherm bricks -An Eco friendly Materials
Porotherm bricks are the next best eco-friendly building materials that everyone should be aware about! It is made up of clay mixed with other natural products like rice ash husk, sawdust, coal ash, etc. Porotherm hollow bricks are hollow from the inside which makes them lightweight. Even so, they are more durable than conventional bricks. Some of their features include light-weight, low water absorption, fire-proof and thermally insulated. Porotherm bricks have a life span that lasts more than 150 years. This building material allows for substantial savings as it is low-priced.
Fly ash bricks
Fly Ash bricks are made of waste products without releasing any harmful toxins into the environment. This green building material absorbs less heat and water, thereby making it more preferable over clay bricks. The composition of fly ash bricks is uniform and strong. Since they are lightweight, they reduce the dead load on buildings. The method of manufacturing these bricks is energy efficient. All in all, fly ash bricks promote sustainability and reduce the overall cost and wastage of building materials.
Reference Books
- A Text Book of Building Materials, by C.J. Kulkarrni
- Building Materials, by P. C. Varghese
- Building Construction, by P. C. Varghese