Unit - 1
Energy-I
Fuels:
A fuel is the substance which on combustion produces a large amount of heart.
Classification of chemical fuels:
Chemical fuels are classified on the basis of occurrence into:
- Primary (natural)
- Secondary (derived) types / manmade
The secondary fuels are obtained from primary fuel by processing or they are manmade. e.g.:- charcoal is obtained from wood by partial combustion of wood , ethyl alcohol is obtained by fermentation of carbohydrates .
Both the primary and secondary fuels are further classified on the basis of physical state into solid liquid and gaseous fuels.
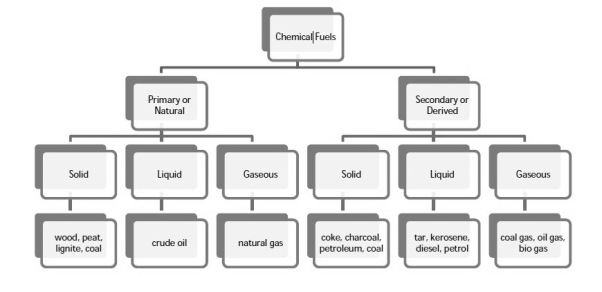
Extra definitions:
1] Fuels:
Fuels are defined as materials that create usable energy through chemical nuclear or electrochemical reaction.
2] Chemical fuel:
The fossil fuels, wood vegetal oils etc. which produce heat on burning are known as chemical fuels.
Calorific value- efficiency of combustible fuels can be measured in terms of their calorific value. It is the heat evolved on combustion of a unit quantity of fuel.
Definition of calorific value:
- It is defined as the amount of heat obtained on complete combustion of unit mass of a solid or liquid fuel or unit volume of a gaseous fuel at STP.
Gross calorific value (G.V.C):
- Usually fuel contains some hydrogen. The hydrogen atoms are bonded to carbon atoms in the fuel when the fuel is burnt, hydrogen forms water vapors. The water vapor if cooled, we get certain amount of heat as the water has high latent heat of 2450 joules / gm or 587 Cal / gm.
- Thus, during the study of calorific value of a fuel we get some heat directly by combustion of fuel and in addition we get certain amount of heat by cooling the products of combustion to 15-degree c.
Gross calorific value:
- Gross calorific value of a fuel can be defined as the total amount of heat obtained on complete combustion of unit mass of a solid or liquid fuel or unit volume of a gaseous fuel (S T P) and on cooling the products of combustion to 15 degree c . The gross calorific value is also called as higher calorific value.
- The G.V.C is of only theoretical importance because in actual practice we do not have any provision of cooling the products of combustion during combustion of fuel in an engine, furnace or any other fuel burning device.
Net calorific value:
- A fuel contain hydrogen produces water heat and actually less heat is available for heating.
- There is not any furnace, engine or device designed to collect the heat being taken away by the water vapors. Therefore, practically we get lower calorific value than the theoretical expected.
Net calorific value:
- Net calorific value is defined as the amount of heat obtained practically on complete combustion of unit mass of solid or liquid fuel or unit mass of solid or liquid fuel or unit volume of a gaseous fuel at step and the products of combustion are allowed to escape with some heat N.C.V is also called as lower calorific value.
The N.C.V and G.C.V are related as under
G.C.V = N.C.V + )
Where h is the percentage of hydrogen in the fuel.
It should be noted that the unit of latent heat of water and unit of G.V.C, N.C.V should be same .
Units of calorific value:
System | Solid or liquid fuel | Gaseous fuel |
CGS | Cal / gm | Cal / liter |
MKS | Kcal / kg | Kcal / ![]() |
S.I | Joules / kg | Joules / ![]() |
Higher Calorific Value (HCV)
Fuel consists of elements that produce energy on combustion.
But the total amount of heat produced by combustion of fuel is not completely available to perform external work.
Some of the heat is utilized to evaporate the moisture content present in the fuel itself.
HCV is the maximum amount of energy that is produced on complete combustion of fuel. It is also generally termed as gross calorific value or GCV.
Lower Calorific Value (LCV)
If the amount of heat or energy utilized in evaporation of moisture content is removed from the HCV, we get LCV for the fuel. It is generally termed as net calorific value or NCV.
Calorific value of fuel can be determined by Bomb calorimeter experiment.
The gross calorific value of solid fuels and liquid fuels can be determined by bomb calorimeter (if the liquid is volatile, then it is filled in a polythene capsule of negligible mass then used in experiment).
Construction: A bomb colorimeter consists of
- Bomb pot
- Calorie meter
- Water and air jackets
- Accessories
- Pellet press
- Oxygen cylinder
Bomb pot:
It is a cylindrical strong stainless-steel pot having a lid. The lid can be fitted air. Tight to bomb pot by screwing.
- There are two types of electrodes fitted through lid and there is an oxygen inlet valve as its center.
- One of these electrodes is provided with a ring to hold the crucible containing fuel. There is thin resistance wire tied to the electrodes in loop form and the loop touches the fuel.
- The weighed fuel is burnt in the bomb pot in the presence of high-pressure oxygen.
Calorimeter:
- There is a stainless steel or copper calorimeter in which the bomb pot is kept. It contains a known volume of water and the water is kept circulating around the bomb pot with the help of a stirrer.
- A Beckman thermometer or digital thermometer is kept in the water of calorimeter, which can record the rise in temperature of welter due to absorb in a heat generated.
- There are insulator stands between calorimeter and water jacket.
Accessories:
- There is a pellet press to convert the powder of solid fuel to pellet form for a liquid fuel a capsule of negligible weight can be used.
- There is an oxygen cylinder with pressure gauge to fill oxygen in the bomb pot at the pressure of nearly 25 kg / cm².
- There is also a D.C battery of a about 6 volts to start combustion of fuel.
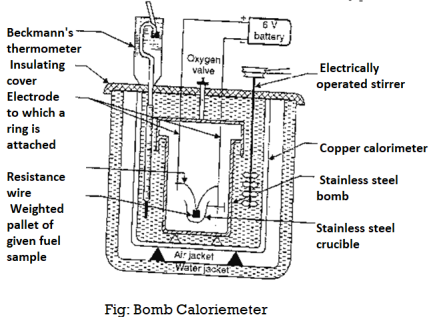
Fig: Bomb Calorimeter
Working:
- Weigh the pellet of solid fuel or liquid capsule and keep it in the crucible. Keep the crucible in the ring of the electrode. Keep the resistance wire touching to the fuel.
- Add about 10 ml of distilled water at the bottom of bomb pot and fix the lid tightly to bomb by screwing.
- Fill the bomb with oxygen at the pressure about 25 kg / cm².
- Place the bomb in calorimeter add known volume of water in the calorimeter so that the bomb gets immersed in the water.
- Place the calorimeter in the water jacket over the plastic studs keep the thermometer and stirrer in the water of calorimeter.
- Put the plastic cover on the and make electrical connections from battery to electrodes.
- Operate the stirrer for s minutes and note the initial temperature of water (t1° c ).
- Pass the current for about 5 – 10 seconds to heat the wire so that the fuel catches fire. If the fuel contains S and N elements, they get converted to SO3 and N2O5. These gases get dissolved in the distilled water in bomb to form H2SO4 and HNO3 (along with liberation little heat).
- Note the maximum temperature reached after that note the rate of fall of temperature per minute and the time taken for reaching to initial temp. Are noted.
- Open the bomb pot and wash the contents at its bottom into a beaker to find out the amount of H2SO4 and HNO3 formed.
Calculations:
Gross calorific value of fuel = l calories / gm
Rise in temperature of water = ( t2 – t1 )
Heat liberated by burning fuel = heat absorbed by water and calorimeter
Therefore,
XL = ( W+W) ( T2 – T1 )
G.CV = L = cal / gm
Note:
Water equivalent of calorimeter – set ( w ) is determined by burning fuel of known gross calorific value and using the above equation.
Standard gross calorific values of some pure fuels are,
Naphthalene = 9622 Cal / gm
Benzoic acid = 6325 Cal / gm
Camphor = 9292 Cal / gm
Salicylic acid = 5269 Cal /gm
NCV for the fuel is calculated as below
If H is percentage of hydrogen in the fuel, then the heat taken by water formed during combustion to convert it into steam is = 0.09h * 587 Cal / gm
And
NCV = GCV – 0.09h * 587 Cal / gm or kcal / kg.
Corrections:
To get more accurate results, the following corrections should be considered.
- Fuse wire correction (F)
- Acid correction (a)
- Cooling correction (tc)
- Fuse wire correction (f):
Out of the total obtained little heat is given out by fuse wire when the current is passed for s – 10 sec .to start the combustion. Hence it must be subtracted. Are exothermic and the heat measured includes a small share by these acid formation.
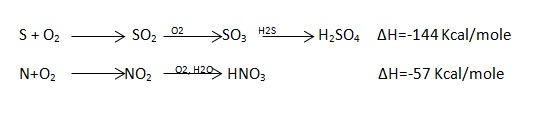
2. Cooling correction (te):
If the time taken for water in calorimeter to cool from maximum temperature attained to the room. Temperature is t minutes and average cooling rate is dt / min, then the cooling correction to be added to rise in temperature is t.dt .
The actual rise in temperature would have been (t23 – t1) had the heat liberated been absorbed by water and calorimeter rapidly and there would have no loss of heat from the set by radiation.
This calorimeter is used to measure calorific value of gaseous fuels and highly volatile fuels.
Principle:
The gaseous fuel is burnt at a known constant rate in the calorimeter under such conditions that entire amount of heat produced is absorbed by water.
- Gas burner
- Combustion chamber (chimney)
- Thermometers
- Insulating cover
2. Gas burner:
There is a gas burner in which a known volume of gas is burnt at a known pressure. The gas is burnt at the rate of 3 – 4 lit. Per minute.
3. Combustion chamber (chimney):
Around the burner there Is a combustion chamber which has a copper tubing coiled inside as well as outside of it water enters from top of the outer coils, moves to bottom of chimney and then goes up through the inner coil to the exit at top.
4. Thermometer:
There are two thermometer to measure temperatures of inlet water and outlet water.
5. Insulating cover:
The assembly is covered with by an insulator to detach combustion chamber from atmosphere. There are three holes for exhaust gas, water inlet and condensed steam.
Working:
- Start burning the gas at suitable pressure and adjust the rate of water flow such that the temperature of outgoing water remains constant.
- Burn the gas for 5 – 10 minutes to have the steady temperatures in and around the combustion chamber.
- After the steady (temperature in and around the combustion chamber) conditions of outgoing.
A) Volume of gas burnt at given temperature and pressure in certain time period.
B) Quantity of water passed through coil during this period.
C) Mass of water condensed from product gas during the period.
D) The steady rise in temperature of water ( t2 – t1 )
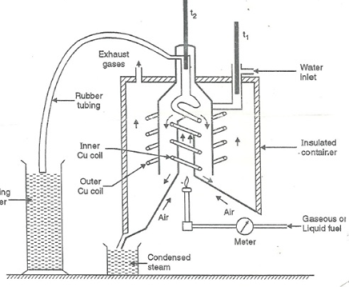
Fig: Boy’s gas calorimeter
Calculations:
- First convert the volume of gas burnt to volume of gas at STP .let this STP volume be V m3.
- Let W = mass of cooling water used in the period of observation in Kg
- Let m= mass of water condensate in kg
- L= G.C.V OF THE FUEL
Heat produced by combustion of fuel = heat absorbed by cooling water
(assuming no heat loss in the steady state conditions)
Vl = w ( t2 – t1 )
L = Kcal / m3
The mass of condensate water per m of gas will be m/v kg /m
If this water had left as steam in product gases it would have taken away heat.
= *587 kcal / m3
Therefore,
NCV = GCV - *587
NCV =
|
|
|
|
|
|
|
|
|
|
|
|
|
|
|
Suppose a fuel contains carbon, hydrogen, Nitrogen, Sulphur, Oxygen as 86.5%, 12%, 0.9%, 0.2%, 0.4% respectively,
To calculate GCV of fuel we use the formula as follows:
GCV of Fuel
= QC*(%C/100)+ QS*(%S/100) + QH*2*(%H/2) -[2*(%O/32)]/100
GCV of fuel
= 8137.5*(86.5/100)+ 2181*(0.2/100) + 28905*2*(12/2)- [2*(0.4/32)]/100
=7038.9 + 4.3 + 3454 = 10497.2 Kcal/Kg
NCV of Fuel = GCV – 584 [(9 * H2%+M%)/100]
=10430 – 584[(9*12+0)/100]
= 10497.2- 630.7 = 9866.5 Kcal/kg
Solid fuels: coal
Coal is highly carbeanous matter formed vegetable matter buried in geomorphic changes, under pressure, by action of aerobic and anaerobic bacteria for long time.
1. The time for transformation wood to coal depends upon the depth of the burial.
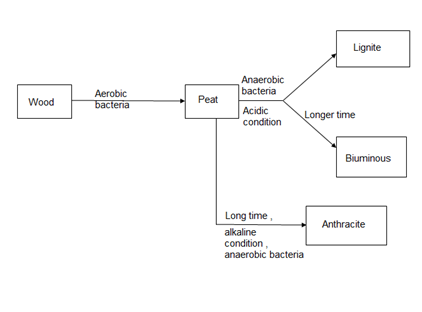
2. The processes of conversion of wood into coal is known as coalification.
3. In general coal contains mainly carbon atoms with mostly sp² hybridization. Atoms like O, H, S, N are covalently bonded to carbon atoms. Coal also contain water and mineral particles entrapped.
4. When coal start burning, some of the heat produced is utilized to evaporate water and minerals are left behind. As ash (metal oxidize, silica)
5. The volatile matter is the unburnt decomposed coal molecules fragments of colloidal size.
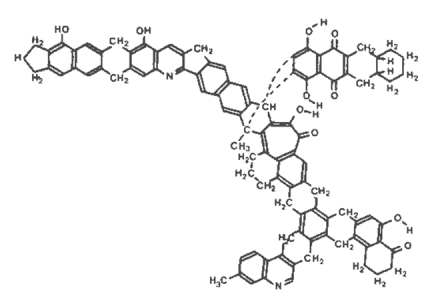
Classification of coal (types / grades):
The conversion of wood (plant matter) into coal takes place progressively. Depending upon the extent of transformation coals are divided into 4 types or grades or ranks.
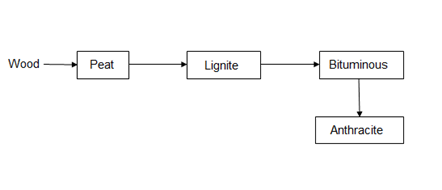
During the progressive conversion from peat to anthracite there is, Increase in carbon percentage calorific value, density luster, hardness, black color intensity decreases in – moisture, volatile, matter.
Peat:
- Peat is brown and fibrous in texture.
- Freshly mined out peat contains large quantity of water as it is found in waterlogged areas.
- Air dried peat contains 15 – 25 percent moisture and it crumbles into powder during air drying.
- Calorific value of peat is about 5400 Cal / gm.
- It has low density
- It contains 57 % C, 61 % C .
Uses:
- Peat type of coal gets powdered during combustion; therefore, it is used after briquetting as domestic and industrial fuel.it is used for soil conditioning
- On carbonization (heating in absence of air) at 5000° c it produces char oil light spirits.
- It can be used for steam raising, thermal insulation packing gas purification and sometimes for power generation.
Lignite:
- It is intermediate stage between peat and black coal.
- It is brownish black and more compact than peat.
- It contains 45 – 50 percent volatile matter and burns with log flame.
- Its C.V id about 6000- 6700 Cal / gm and c percent it is 65 – 70 %.
- It contains 5 % H20.
Uses:
- After briquetting it is used as domestic and industrial fuel.
Bituminous coal:
- This type of coal burn with smoky yellow flame and are dark – grey to black they contain 70 – 90 %C and therefore they are classified as
- Sub – bituminous coal:
- This coal has character’s between lignite and bituminous coal.
- It is harder and denser than lignite .it is grey black and has dull waxy lusture.
- Its C.V is about 7000 Cal / gm and 70 – 75-degree c. it contains large volatile matter 35 – 40-degree c.
- It crumbles into pieces on air drying and during transportation .it is non caking.
- This coal is used for domestic and insulation purpose.
2. Bituminous coal:
- This coal has banded or laminated structure with alternate bright and dull layers.
- It has cubical fracture.
- It is black dense and hard.
- It contains 75 – 85 percent c and has c.v 8000-8500 Cal / gm
- It is a caking coal and forms coke and coal gas on carbonization, as it contains 20 – 30 percent volatile matter.
3. Semi bituminous coal:
- It has characters between bituminous and anthracite coals.
- It has low volatile matter and caking property.
(caking – coal decomposing at about 400°c melting forming a plastic mass through which U.M blows out forming highly swollen open structured coal called as coke)
- Its c.v is about 8400 Cal / gm
Uses:
Making of coke, high temperature heating, coal gas for tar and chemicals.
4. Anthracite coal:
- This is highest rank or grade coal
- It has C.V about 8700 coal / gm and 92 – 98-degree c.
- It is highly lustrous black and hard coal.
- It burns with non – smoky short blue flame of high temperature.
Uses:
- Costly coal it is used for specific industrial purposes.
- It used as metallurgical fuel
- It is used for making electrodes
- It is used for high temp heating’s
Analysis of coal:
Coal is mainly composed of C, h, N, S moisture volatile matter.
The purpose for coal analysis is
- To decide price of coal
- To determine quality
- To specify use of coal for a particular purpose
- To calculate theoretical calorific values of coal
- To calculate air requirement for complete combustion of coal and design the furnace fire box suitably.
A sample of coal taken out from coal mine is analyzed in two ways.
- Proximate analysis
- Ultimate analysis
Proximate analysis:
This is an approximate analysis of fuel to find the basic composition of fuel. The results obtained are only approximate and proper values can be obtained by ultimate analysis.
Following are the important deductions of proximate analysis:
- It is important in finding the combustion properties of fuel. The factors that are determined by this method are: moisture content, ash, volatile matter and fixed carbon.
- Moisture increases weight of the fuel without increasing its calorific value. The evaporation of water reduces the calorific value of the fuel. Ash also increases weight without producing any heat during combustion.
- Volatile matter are all those contents in the fuel that are converted to gas during combustion.
- Fixed carbon is the carbon remaining on the surface of grates as soot. High proportion of fixed carbon reduces the combustibility of fuel.
Ultimate analysis:
This is an analysis of fuel which gives exact composition of fuel. Percentage of different components can be found by completely combusting the fuel in the furnace.
Following are the important deductions of ultimate analysis:
- It is useful for calculating mass balance for a chemical or thermal process.
- Ultimate analysis of fuel is carried out to determine the proportions of C, H, O, N and S.
- Presence of toxic metals like Cd, Cr, Hg, Ni, Pb, Sn and Zn in ash can be determined by ultimate analysis.
- Presence of other non-toxic metals in the fuel like Fe, Mn, Ca, Mg, Na and more can be determined by ultimate analysis.
Numerical:1
- Compute the proximate analysis results 1.9 gms of a coal sample loses 0.285gm weight at 110°c.
- 1.5 gm of the same coal sample loses 0.36gm weight at 925°c.
- 2.15 gms of the coal sample leaves 0.26 gm ash.
Given data:-
M=1.9 gm
( m – m1 )= 0.285 gm ( moisture loss )
Loss in weight due to moisture and VM = 0.36gm
Weight of coal = 2.15 gm
Weight of ash = 0.26gm
- Moisture (percent) =
*100
= = 15 percent
2. V.M (percent):
v.m = *10
= *100-15 = 24 – 15
= 9 percent
3. Ash (percent):
Therefore,
Ash =
=
= 12 (percent)
Numerical:2
- Calculate C , N , H , S from the following observation for a sample of coal.
- 2.05 gms of the coal is burnt in combustion tube. The increase in weight of any hydrous Cacl2 is 0.55 gm and increase in weight of KoH tube is 5.75gm.
- 0.75 of the coal is kjaldahl experiment released NH3 which is passed in 50ml 0.12 N NaoH to neutralize in back titration.
- Washings of the bomb pot when 1.8 gm.
Given data:-
Increase in weight of any hydrous calcl2 = 0.55
Mass of coal = 0.75gms
Volume of 0.12 NHCL consumed by NH3 = 50 – 41
= 9 ml
Mass of coal = 1.8gms
Weight of Baso4 = 0.31 gm
- Weight of CO 2 formed = increase in wt. OfKoH
Therefore,
C percent = *
*100 = 76.5 percent
Increase in weight of any hydrous Cacl2
= weight of H2O formed
Mass of coal = 2.05gm
H ( percent ) = *
*100
= 2.98 (percent)
2. N (percent) =
=
= 2.02 (percent)
3. S (percent) = *100
=
= 2.36 (percent)
The common plants used for biodiesel production is Soybean and oil palm. Microorganisms such as algae and bacteria also form sources of biodiesel, they seem promising but are economically difficult to develop Few species of algae have up to 40% lipids by weight that can be converted to synthetic petroleum or biodiesel.it is estimated that few algae and cyanobacteria yield between 10 and 100 times more fuel per unit area than plant-based biofuels.
Is a fuel where the chemical energy stored in the fuel is converted into mechanical energy, any internal combustion engine, where air is compressed to very high temperatures to ignite the diesel fuel injected into the cylinder. The piston is actuated by combustion and expansion, the mechanical energy can to use to drive freight expansion, The tractors and marine vessels. A limited number of automobiles also are diesel-powered, as are some electric-power generator sets.
Preparation
The preparation of the biodiesel is a transesterification reaction where the triglycerides are converted into simpler methyl esters of the fatty acids (the biodiesel). Biodiesel is produced from tallow, vegetable oil or animal fat, and waste oils. There are three stages of this transformation of oil and fats to biodiesel.
a) Transesterification of the oil in which it is base-catalysed.
b) The direct acid-catalysed transesterification
c) Finally, conversion of oil to fatty acid and then the formation of biodiesel.
The production of biodiesel involves a chemical reaction. This chemical reaction is known as transesterification.
Transesterification is the chemical process, which converts natural fats and oils into Fatty Acid Methyl Esters (FAME) or Biodiesel. Some of the major sources of suitable oil (to make biodiesel) come from crops like palm, soybean or rapeseed.
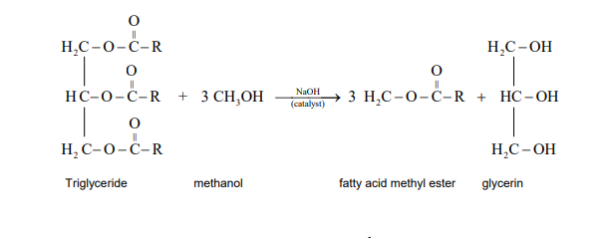
Advantages:
- As Biodiesel is a renewable energy source, they will not vanish away like many petroleum products, since they are made from vegetable oils they can be produced whenever necessary and they cause less pollution.
- One of the distinct advantages of using biodiesel is they can be used in existing diesel engines with no or very less modifications and can form the primary transport energy source.
- Usage of biodiesel helps to reduce, burning of fossil fuels as they cause pollution and global warming.
- The biofuel serves as an alternate form of fuel, thus reduce our dependence on foreign supplies of oil, as biofuels are produced from domestic energy crops.
- 305 fuel economy is achieved by vehicles that run on biodiesel than the one that use petrol-based engines, which means it makes fewer trips to gas stations and runs more miles per gallon.
Disadvantages:
- Biodiesels are produced from crops, most of the crops are treated with fertilizers that can affect the environment and cause pollution, excess use of fertilizers cause soil erosion.
- As they are produced from crops and animal fat, their demand may rise leading to a shortage of food crisis
- Biodiesel are not suitable in low temperatures, they form gel under low temperatures, which depends on the oil or fat used to make it
- The engine efficiency increases with the use of biodiesel, it can cause considerable damage to the rubber house of some engines.
Liquefied Petroleum Gas (LPG) is a blend of light hydrocarbon compounds. It mainly consists of butane (C4H10) or propane (C3H8) or a mixture of both. At room temperature, both gases are colourless and odourless. Propane has its boiling point at -42°C and butane at -0.5 °C. Under modest pressure or in cooler conditions, LPG transforms into a liquid state. LPG in domestic cylinders used for cooking generally comprises more butane than propane, because the fuel value per kilogram of butane is higher than propane and it liquefies under much lower pressure than propane and thus the handling is safer.
Liquefied Gas is heavier than air and can therefore accumulate above the ground. This may lead to LPG-'lakes'. It is common practice to add a foul-smelling odorant to the gas in order to detect leaks and reduce the risk of explosions.
LPG is non-toxic but highly flammable. Therefore, LPG has to be handled with care and all equipment and appliances used to store or transport the gas must comply with high safety standards. They have to be maintained and regularly inspected. Trading with LPG is normally subject to government safety regulations and corresponding enforcement do prevent fire and explosion accidents.
Liquefied gas is produced from three main sources:
- As a by-product from degasolining of natural gas,
- As a by-product from stabilization of petroleum in crude oil mining site,
- As a by-product from petroleum refining in a refinery.
LPG has a very wide variety of uses, mainly used for cylinders across many different markets as an efficient fuel container in the agricultural, recreation, hospitality, industrial, construction, sailing and fishing sectors. It can serve as fuel for cooking, central heating and to water heating and is a particularly cost-effective and efficient way to heat off-grid homes.
Advantages:
- Health-related: The use of LPG reduces the interior air pollution by 90% in comparison to traditional ways of burning biomass.
- Environmental impacts-related: CO2 emissions are relatively low. Greenhouse gases are reduced by 5-16 times per prepared meal compared to coal.
- LPG stoves quickly supply heat and work more efficient than stoves which burn biomass.
Disadvantages:
- Availability: A UNDP study found that 120 billion tons of LPG are necessary to supply 2 billion people with cooking energy.
- Costs: The LPG market is underdeveloped in most regions where LPG would be an addition to current cooking fuels. Significant sums would have to be invested to develop these markets.
Comparison of LPG with Petrol
Petrol | Liquefied Petroleum Gas |
Fuel consumption is less | Fuel consumption is more |
Petrol has odor | It is odorless |
Octane number is 81 | Octane number is 110 |
Engine running is not as smooth as LPG | Engine runs smooth on LPG fuel |
To increase octane number Lead is used in Petrol | It is Lead free |
Life of petrol engine is comparatively less than LPG engine | Life of engine is more than that on petrol |
Due to carbon deposit on spark plug its life decreases | No carbon deposit problem |
Natural Gas is a fossil fuel. It occurs naturally and approximately consists of 95% hydrocarbon methane, the other 5% consists of nitrogen, carbon dioxide, helium or hydrogen sulfide. It takes millions of years for it to form.
The gas is formed when layers of decaying plants and animals are buried under the earth’s surface and are exposed to intense heat and pressure for millions of years. Plants originally obtain energy from the sun and store in the form of chemical bonds in the gas. And thus, the formation of this gas occurs.
Properties:
- The state of matter of this gas is gaseous.
- It doesn’t have any color and is a tasteless gas.
- It is free of any kind of toxic, there is no smoke on burning and it has high calorific value.
- The gas is odourless. However, a chemical called mercaptan is added to it in small amounts to give it distinctive smell of eggs. This helps to find out any gas leaks.
- It is a combustible gas and a fossil fuel.
- Its a mixture of simple hydrocarbon compounds.
- It contains primarily methane, along with small amounts of ethane, butane, pentane, and propane.
- The by-products of this gas are water vapor and carbon dioxide.
- Air is 60% heavier than natural gas.
- It has a low flammability range and a high ignition temperature.
- Generally, it is transported through pipes.
- It occurs naturally in the rocks beneath the earth’s surface, in sedimentary rocks that are porous.
Applications
- It is used in vehicles in the form of CNG (Compressed Natural Gas).
- It is also used to manufacture a few chemicals and fertilizers.
- The gas is used as a source of energy for cooking, heating, and electricity generation.
- It is used as chemical feedstock for manufacturing plastic and other commercially important organic chemicals.
- The gas is also useful in the production of fabrics, glass, paint, plastic, steel, etc.
- Hydrogen can also be produced with the help of it.
- Protein-rich animal and fish feed is produced by feeding this gas on a commercial scale.
Hydrogen gas as a future fuel
The main purposes to produce green hydrogen is to add it to the natural gas system, because the natural gas system is seen as a seasonal and large energy storage and necessary for balancing the intermittent electricity production from renewable wind and solar. When hydrogen is mixed with natural gas, the hydrogen content can vary in a wide range. Gas engines have the capability to burn gases with a wide range of hydrogen content, but there are also some challenges with a potentially high fluctuation of the hydrogen content or fast rate of change.
The two technology areas, traffic decarbonisation and long-term energy storage, depend on H2. As H2 will be transported in pipelines, the need for flexible H2-tolerant gas engines will rise.
Power alcohol
Definition:
When ethyl alcohol is used as fuel internal combustion engine. It is called as power alcohol. Combustion engine it is called as power alcohol generally, ethyl alcohol is used as its 5 – 25 percent mixture with petrol.
- India has started mixing 5 percent ethyl alcohol in petrol from year 2003 but countries like brazil use 25 percent. Ethyl alcohol in petrol from 1970.
- Use of ethyl alcohol is petrol reduces our dependence for petrol on foreign reserves by about Rs 5000 annum. Further it gives boost to the indigenous manufactures of ethyl alcohol and farmers get better price of their grain produce.
- Ethyl alcohol is mainly manufactured by fermentation of molasses stretch. Carbohydrates on a large scale and cheaply. It can also be obtained from synthesis of gas (co, H2).
Reactions:
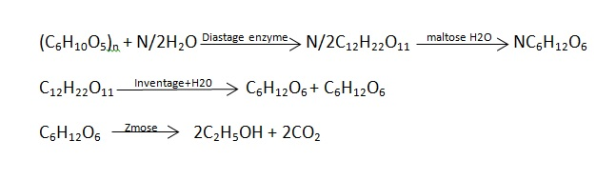
4. The starch or sucrose in molasses is converted into ethyl alcohol by fermentation as in above reactions the ethyl alcohol obtained contains 95.5 percent alcohol is separated by use of suitable dehydration agent or by distilling it along with benzene.
Advantages of power alcohol:
- Ethyl alcohol has very good anti knocking property and its octane number is go, while the octane number of petrol is about 65 (percent).
Therefore, addition of ethyl alcohol to petrol increases its octane number.
2. Alcohol has property of absorbing any traces of water if present in petrol.
3. If a specially designed engine with higher compression ratio is used, then the disadvantage of lower c.v of ethyl alcohol can be overcome.
4. Ethyl alcohol contains O atoms which help for complete combustion of power alcohol and the polluting emissions of co, hydrocarbon is reduced largely.
5. Use of ethyl alcohol in petrol reduces our dependence on foreign countries for petrol and saves foreign currency considerably.
6. Power alcohol is cheaper than petrol.
Disadvantages:
- Ethyl alcohol has c.v 7000cal /gm use of power alcohol reduces power output up to 35 (percent)
- Ethyl alcohol has high surface tension and its atomization especially at lower temperature is difficult causing starting trouble.
- Ethyl alcohol may undergo oxidation to form acetic acid which corrodes engine parts.
4. Ethyl alcohol obtained by fermentation processes cannot be mixed with petrol, but it has to be dehydrated first.
5. Prepare sodium methoxide from sodium metal and methanol. Add the sodium methoxide about 2 percent by weight to vegetable oil or fat.
6. Add methanol about 20 percent by volume to the mixture.
7. Heat the mixture with stirring for 30 min
8. Cool and mix sufficient water stir well the glycerol and soap dissolve in water phase.
9. Separate the water insoluble phase from water phase
10. Add antioxidant to the biodiesel to avoid it to become gumany due to oxidation and polymerization.
Biodiesel
Biodiesel can be obtained from various vegetable oils like soya been oil, palm oil, groundnut oil, cottonseed oil, mustard oil, flower oil, etc. and also, from the animal fats.
The product is given name biodiesel on account of that it is obtained from biological product and it is biodegradable material.
Advantages of biodiesel:
Biodiesel can be used as a good fuel for diesel engine but generally it is used as its 20 percent mixture with diesel.
- Biodiesel is cheaper
- It has high c.v of about 40 kg / gm
- It is regenerative and environmentally friendly.
- It does not give out particulate and CO pollutants.
- It has certain extent of lubricity
- It uses provided good market to vegetable oils and reduces our dependence on biodiesel on foreign countries, saving currency.
- It is clean to use biodiesel in diesel engine.
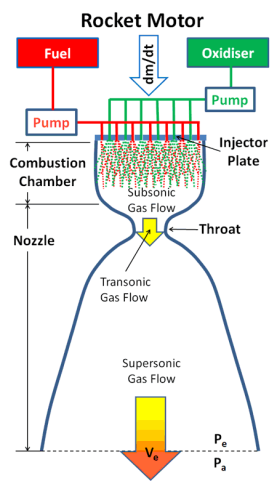
Fig.: Rocket
Rockets depend for their action on Newton's Third Law of Motion that: "For every action there is an equal and opposite reaction."
In a rocket motor, fuel and oxidiser, collectively called the propellants, are combined in a combustion chamber where they react chemically to form hot gases which expand rapidly and are then accelerated and ejected at high velocity through a nozzle, thereby imparting momentum to the motor in the opposite direction.
Construction:
The Propellant Pump(s)
An essential component of liquid fuelled rocket engines is the means of delivering the propellants (the fuel and the oxidiser) to the combustion chamber. The simplest method used in low thrust rockets is by pressurising the fuel and oxidiser tanks with compressed air or a gas such as nitrogen, but for most liquid fuelled rockets, the high propellant flow rates required are provided by on-board turbopumps.
The Injector Plate
The injector plate is a passive device which has three purposes. It breaks up the liquid propellants into tiny droplets to aid and speed up combustion, it enables homogeneous mixing of the fuel with the oxidiser and it ensures stable, controlled burning of the fuel, preventing the explosive combustion of the propellants.
The Nozzle
The purpose of the nozzle is to promote the isentropic (constant entropy) expansion of the exhaust gas. As the gas expands, its pressure drops, but since there is no change in total energy, its velocity (kinetic energy) increases to compensate for the reduction in pressure energy.
There are thus two factors contributing to the engine thrust, namely, the kinetic energy of the gas particles ejected with high velocity from the exhaust and the pressure difference between the exhaust gas pressure and the ambient pressure of the atmosphere acting across the area of the nozzle exit. The relationship is shown in the following equation.
Engine Thrust F = dm/dt. Ve + Ae(Pe - Pa)
Where
Dm/dt = Propellant Mass Flow Rate per Second
Ve = Gas (Exhaust) Velocity at Nozzle Exit
Ae = Area of Nozzle Exit
Pe = Gas Pressure at Nozzle Exit
Pa = Ambient Pressure of the Atmosphere
The first term is known as the momentum thrust and the second term the pressure thrust.
Considering the pressure thrust alone, since the ambient pressure decreases with altitude, in the vacuum of free space where the pressure is zero, the rocket thrust will increase to a maximum of 15% to 20% more than the thrust at sea level.
(By contrast, the thrust of a jet engine decreases with altitude to zero in free space since it depends for its thrust on air as the oxidiser for the fuel. The rocket on the other hand carries its oxidiser with it.)
The momentum of the exhaust gas is however much more effective in creating thrust than the pressure difference at the exhaust exit, so that the more the pressure energy is converted into kinetic energy in the nozzle, the more efficient the nozzle will be. So paradoxically the maximum thrust occurs when the exhaust pressure is equal to the ambient pressure.
The effective exhaust velocity Ve is a function of the nozzle geometry such as the nozzle expansion ratio Ae/At
Where At = Area of Nozzle Throat
Equation of motion:
A rocket can be considered as a large body carrying small units of propellant and travelling with a velocity V.
The reaction due to expelling the propellant from the rocket exhaust causes the velocity of the rocket to increase.
Assuming no change in ambient pressure, the Conservation of Momentum for the rocket and the expelled propellant gives:
(M+dm)V = M(V+dv) + dm(V - Ve)
Where
M = The total remaining mass of the rocket and its fuel
Dm = The mass ejected rearwards through the exhaust nozzle or the change in mass during a given period.
V = The initial absolute forward velocity of the rocket just before the ejection of the propellant
Dv = The increase in forward velocity of the rocket due to the ejection of the exhaust gases
Ve = The exhaust velocity, relative to the rocket, of the propellant leaving the rocket motor.
Simplifying we can derive the following:
Dm.Ve = M.dv
Dividing by dt to get the instantaneous rates and substituting Newton's Laws
a = dv/dt The acceleration of the rocket
F = M.a The force or thrust acting on the rocket
This gives
Dm/dt. Ve = M.dv/dt = M.a = F = The Force or Thrust
Where
Dm/dt = The mass flow rate of the burning fuel mass ejected.
Thus the instantaneous thrust on the rocket is directly proportional to the fuel mass flow or burn rate.
For the change in velocity over a longer period we must take into account the reduction dM in the total mass of the rocket as its fuel is consumed and integrate the velocity over time for the duration of the period.
From the above:
The mass expelled = The reduction in mass of the rocket and its propellant load
Or
Dm = - dM
And
∫dv = Ve ∫dm / M
So that
∫dv = - Ve ∫dM / M
Thus
Vf - Vi = - Ve(ln M)if
= - Ve (lnMf - lnMi)
= V e ln (Mi / Mf)
Where
Vi = The initial velocity of the rocket
Vf = The final velocity of the rocket
Ln = The natural logarithmic function
Mi = The initial mass of the rocket including its payload all its propellant
Mf = The final mass of the rocket and its payload including its remaining propellant
Mi / Mf is known as the rocket's Mass Ratio
This is known as Tsiolkovsky's Equation
Note that although a greater initial mass (of propellant) which increases the Mass Ratio, will create a greater increase in velocity, the relationship is not linear and the increase in velocity due to the increased available fuel becomes proportionally less as the initial mass Mi increases. This is because some of the extra propellant must be used to accelerate the mass of the extra fuel itself.
Types:
There are three main types of propellants: solid, liquid, and hybrid.
Solid propellants
The earliest rockets were created hundreds of years ago by the Chinese, and were used primarily for fireworks displays and as weapons. They were fueled with black powder, a type of gunpowder consisting of a mixture of charcoal, sulfur and potassium nitrate (saltpeter). Rocket propellant technology did not advance until the end of the nineteenth century, by which time smokeless powder had been developed, originally for use in firearms and artillery pieces. Smokeless powders and related compounds have seen use as double-base propellants.
Solid propellants (and almost all rocket propellants) consist of an oxidizer and a fuel. In the case of gunpowder, the fuel is charcoal, the oxidizer is potassium nitrate, and sulfur serves as a catalyst. (Note: Sulfur is not a true catalyst in gunpowder as it is consumed to a great extent into a variety of reaction products such as K2S. The sulfur acts mainly as a sensitizer lowering threshold of ignition.) During the 1950s and 60s researchers in the United States developed what is now the standard high-energy solid rocket fuel. The mixture is primarily ammonium perchlorate powder (an oxidizer), combined with fine aluminum powder (a fuel), held together in a base of PBAN or HTPB (rubber-like fuels). The mixture is formed as a liquid, and then cast into the correct shape and cured into a rubbery solid.
Liquid propellants
Liquid-fueled rockets have better specific impulse than solid rockets and are capable of being throttled, shut down, and restarted. Only the combustion chamber of a liquid-fueled rocket needs to withstand combustion pressures and temperatures. On vehicles employing turbopumps, the fuel tanks carry very much less pressure and thus can be built far more lightly, permitting a larger mass ratio. For these reasons, most orbital launch vehicles and all first- and second-generation ICBMs use liquid fuels for most of their velocity gain.
The primary performance advantage of liquid propellants is the oxidizer. Several practical liquid oxidizers (liquid oxygen, nitrogen tetroxide, and hydrogen peroxide) are available which have much better specific impulse than ammonium perchlorate when paired with comparable fuels.
Gas propellants
A gas propellant usually involves some sort of compressed gas. However, due to the low density and high weight of the pressure vessel, gases are seldom used at present.
Hybrid propellants
A hybrid rocket usually has a solid fuel and a liquid or gas oxidizer. The fluid oxidizer can make it possible to throttle and restart the motor just like a liquid-fueled rocket. Hybrid rockets are also cleaner than solid rockets because practical high-performance solid-phase oxidizers all contain chlorine, versus the more benign liquid oxygen or nitrous oxide used in hybrids. Because just one propellant is a fluid, hybrids are simpler than liquid rockets.
References:
1. A Text book of Engineering Chemistry: Shashi Chawla; Dhanpat Rai & sons, New Delhi
2. Chemistry in Engineering: Lloyd a. Munro, Prentice-hall, Inc Nj
3. Chemistry of Advanced Materials: CNR Rao, Rsc Pbl‟
4. Chemistry of Engineering Materials: Robert B Leighou Mc Graw – Hill Book Company, Inc New York
5. Engineering Materials: Kenneth G Budinski (Prentice – Hall of India)