Unit - 6
Pavement Construction and Modern Trends in Highway Materials, Construction & Maintenance
Difference between WBM & WMM
Water Bound Macadam (WBM) | Wet Mix Macadam (WMM) |
Old technology in which the pavement base course is made of crushed or broken aggregates, mechanically interlocked by rolling followed by screening using water as a binder material. | New Technology having greater durability as compared to WBM. All components are pre-mixed in plants. |
40-90 mm coarse aggregates for sub-base course, 53-63 mm for base course. Hand broken aggregates can be used. For screenings, gravel or moorum retained on 75 µ sieve is used. | For thickness of layer > 100 mm, use 53 mm size of coarse aggregates, passing through 75 µ sieve. For thickness of layer < 100 mm, use 26.5 mm size of coarse aggregates passing through 75 µ sieve. |
Construction Procedure of WBM Road
- Preparation of Sub-grade
First of all, the site is cleaned and cleared. Proper camber is provided and trenches are cut in the sub-grade soil so as to prevent the spread of aggregates beyond the carriageway. Brick bunds are constructed to provide confinement to the loose aggregate on the clayey sub-grade. The sub-grade should be stable and well-drained.
2. Spreading of Aggregates
Coarse aggregate is spread on the sub-grade surface prepared in Step 1 in uniform layers of thickness 75 mm each. The surface is checked at regular intervals of time so as to ensure proper camber and grade.
3. Dry-Rolling
This is done to compact the coarse aggregates thoroughly using power rollers weighing 6 to 10 tons. Generally rolling is started from the edges towards the center by backward & forward movement of roller.
4. Application of Screening
Screening is done to fill about 50% of the total voids in the above prepared surface of coarse aggregates and the remaining 50% of the voids are filled using filler materials like sand.
5. Wet Rolling
The surface is now sprinkled with water and rolled again, till the slurry fills all the voids. The size of aggregates, nature of aggregates, the type of surface desired etc are the deciding factors for the quantity of water to be applied.
6. Application of Fillers
Once the slurry has filled all the voids, rolling is done with power roller weighing 6 to 10 tons so as to wash down the binding material from the wheels of the roller when water is poured on them.
7. Surface Finishing
The prepared section is allowed to dry overnight. Next day, a thin layer of sand or earth (about 0.6 cm thick) is spread over the surface. Water is sprinkled and rolling is done again.
8. Shoulders
Shoulders are made having the same cross slope as that of pavement. Finally, after proper drying and setting of the WBM, the road is opened to traffic.
Construction Procedure of WBM Road
- WMM is prepared in a batching plant having moisture content slightly higher than optimum moisture content (OMC) in order to account for evaporation losses during transit of material. OMC shall be determined in accordance with IS: 2720 (Part-8).
- Mix is spread with the help of self-propelled paver finisher and motor graders.
- Rolling is the carried out using rollers having minimum weight of about 80-100 KN.
- The pavement is then left to dry and set for 24 hours.
Mix Design of Granular Sub-base (GSB)
GSB is the layer in pavements just above the compacted soil layer or the sub-grade layer.
GSB is prepared using well-graded granular soil having suitable moisture content and in layers not less than 150 mm thick.
It provides strength & support to the layers above it and also permits efficient drainage.
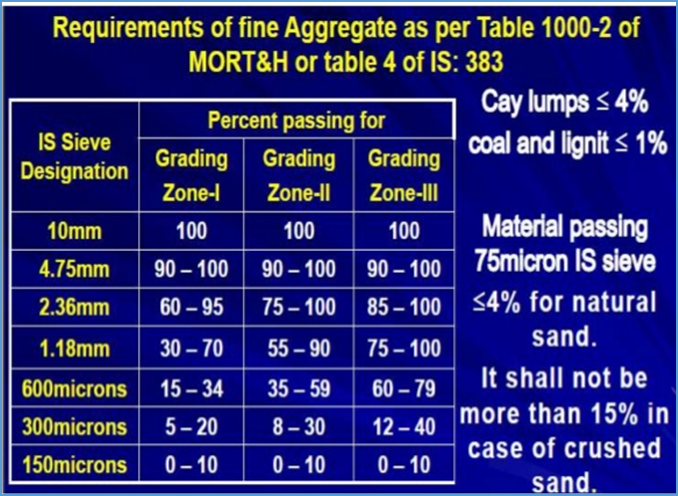
Cemented Base or Cement-treated base (CTB) is a mixture of granular soils and aggregate materials combined with measured quantities of water and port land cement. The material hardens after curing and compaction to form a durable paving material.
In order to provide finishing to a pavement, a wearing course made up of bituminous/ port land cement concrete is placed on the CTB. This kind of structure is widely used for highway roads, parking areas, airports, and materials handling and storage areas.
Factors affecting the quality of CTB are:
- Cement Content
- Moisture Content
- Proper Mixing
- Compaction of Surface
- Curing of Concrete
The thickness of cemented base is much less than that required for granular base, both carrying the same traffic load as CTB distributes the load over a large area. It has both slab-like characteristics and beam like strength. CTB is hard, rigid and impervious. It can resist all-weather damages.
The material continues gaining its strength with age even under traffic.
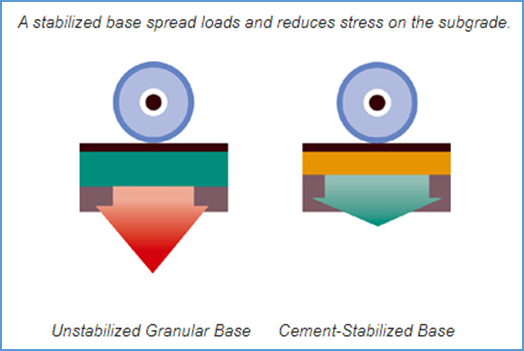
a) Prime Coat: A prime coat is used to protect the bottom layers in pavement construction before adding additional layers on the top. The prime coat can also be used as a binder with secondary and tertiary compounds, thereby ensuring adhesion between the layers. Generally, asphalt is used for coating purposes. Some important things to remember before installing a prime coat are:
- It imparts temporary waterproofing to the bottom layer
- The asphalt coat must completely penetrate the sub-surface in order to be most effective.
- A prime coat must completely cure before incorporating an additional layer.
- Weather conditions play a major role during the application of asphalt prime coat. For example, in wet weather conditions, the coat may runoff and flow into the water supply.
b) Tack Coat: The tack coat is applied right after the prime coat, so as to impart an adhesive bond between the tack coat and the layer above it. The tack coat acts as a permanent, long-term sealant to protect sub-surface from bacteria attack and also prevents slippage. Some important points to remember about installing a tack coat are:
- It is required that the prime coat is cleaned and dried before applying the tack coat.
- Higher viscosity of the tack layer imparts more shear strength to the overall structure.
- Diluted emulsions with large setting times are generally used as tack coat.
c) Seal Coat: A prime coat is defined as the final coating of a bituminous material such as bituminous macadam or concrete used for sealing the surface of the pavement. It is a protective coating that increases the life of the pavements.
d) Built-up Spray Grout (BSG): It is a composite two-layer course of coarse aggregates. Each layer is compacted with the help of a bituminous binder, to be used as base or binder course only.
e) Asphaltic Concrete (AC): It is used for construction of parking lots, core of dams, airport surfaces etc.
f) Bituminous Concrete (BC): It is used for construction of heavy traffic roads.
g) Bituminous Macadam (BM): It is used for base course or is applied as a sealant on an old base.
h) Dense Bituminous Macadam (DBM): It is used for binder coarse and has only 5-10% voids; used for construction of roads carrying higher number of commercial vehicles.
i) Premix Carpet: It is used as an overlay in urban roads and as the top base on rural roads; highly porous in nature and requires a sealant surface on top.
j) Dry lean Concrete (DLC): It is a type of concrete consisting of a large proportion of aggregates with respect to cement in comparison to conventional concrete. It is generally used as hard paving in base or sub-base course because of its high resistance to deformation and ease of use in all weather conditions.
k) Pavement Quality Concrete (PQC): It is the top layer in pavements and highways having a thickness of about 300 mm and made up of minimum M40 grade of concrete and 32mm size of aggregates. It has a high load bearing capacity and does not deform easily even under heavy loads.
Stone Mastic Asphalt (SMA), also known as Stone Matrix Asphalt/ Split Mastic Asphalt, was developed in the 1960s in Germany by a large construction company, Strabag, before spreading to Europe & other parts of the world in 1980s.
SMA provides a durable pavement, resistant to wearing & tearing due to rutting action under heavy traffic.
SMA is characterised by its high stone content with voids filled with highly viscous bituminous mastic. Stiffness of the mastic is achieved by the addition of crushed sand. The materials used in the preparation of SMA are aggregates (coarse & fine), bitumen, fibre and filler.
Advantages of SMA
- 20-30% increase in design life of pavements is achieved.
- Good interlocking of aggregates is obtained.
- Low permeability of pavements with high durability and resistance to wearing is an important feature.
- SMA can be used to used to carry heavy traffic loads at intersections, at gradients and at traffic lights.
Disadvantages of SMA
- SMA requires high mixing temperature.
- High cost of material and continuous monitoring is a major disadvantage.
- White fines are obtained on the surface.
- Stripping of asphalt layers below SMA is a common phenomenon.
When asphalt is applied to pavement surfaces without any heating for application, the process is known as Cold Mix Asphalt (CMA) Technology.
CMA is used for patching & repair purposes in case of pavement cracks and potholes when the surrounding temperature is too low.
Advantages of CMA
- Affordable technology as compared to Warm/ Hot Mix Asphalt Technology
- Can be easily used in cold weather and cold regions
Disadvantages of CMA
- Strength is lesser as compared to Hot Mix Asphalt
- Can only be used for temporary repair works and not for mass construction purposes
Asphalt is heated to a high temperature before application on pavement surfaces. This is known as Hot/ Warm Mix Asphalt (HMA) Technology.
It is used for mass construction and paving purposes like roads, driveways, parking areas etc.
Advantages of HMA
- Highly weather resistant
- Cools down very quickly
- Has high strength
- Highly flexible
Disadvantages of HMA
- Highly expensive
- Must be used only when surrounding temperature is greater than 40ᵒC
According to the book titled ‘MS-2 Asphalt Mix Design Methods’ published by the Asphalt Institute in USA, Reclaimed or recycled asphalt pavement (RAP) is obtained from good quality, properly screened, crushed, and well-graded aggregates coated by asphalt cement. These materials are used for reconstruction and resurfacing.
Asphalt pavement is not only economical to use because of its ability to be re-used but also has environmental benefits as it reduces the depletion of non-renewable materials like aggregates and asphalt binder. Excess asphalt concrete is disposed of by use in landfills or in the construction of the right of way.
Most of the RAP is produced from milling. RAP is also produced from any existing asphalt pavement by processing it to an appropriate size to be used as a component of a new asphalt mixture.
Superpave Mix design Method is considered as an improved method over Marshall Mix Design and Hveem Mix design to produce a good performing asphalt paving mix.
This technique was developed by the Strategic Highway Research Program (SHRP) in 1987. It is an improvised system used to specify asphalt binders and mineral aggregates, design asphalt mixtures, and predict the pavement performance keeping in mind the traffic characteristics, the surrounding environment and associated risk/ reliability of the structure rather than empirical parameters only.
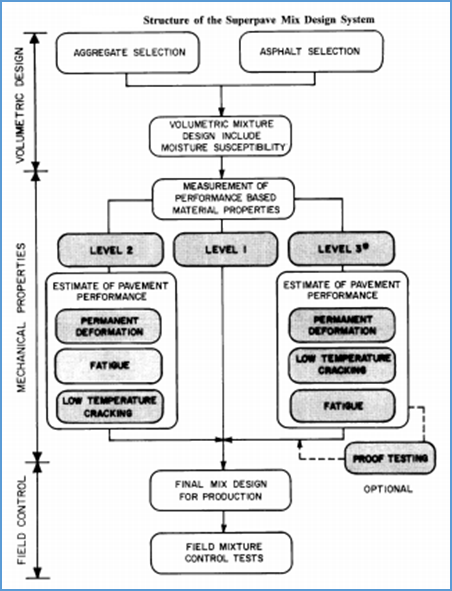
The Superpave mixture design involves three rigorous degrees of testing:
- Careful material selection and volumetric proportioning
- Intermediate mix testing and analyses in order to optimize the asphalt mixes based on estimate of pavement performance (for critical, high traffic volume projects)
- Advanced (complete) mix testing and analyses in order to get better optimization of the asphalt mixes through sophisticated estimate of pavement performance (for more critical, higher traffic volume projects).
Non-Destructive Testing is done on finished pavements to test their quality, durability, strength and load bearing capacity without hampering the structure. Some of the tests involved in NDT are as the Benkelman Beam Test, Le Croix Deflectograph, Falling Weight Deflectograph, Dynaflect etc.
Falling Weight Deflectometer (FWD)
FWD is an impulse loading device in which a transient load is applied to the pavement structure and the deflected shape of the pavement is evaluated.
The structural evaluation of the pavement involves applying a standard load to the pavement and measuring the resultant stress, strain and deflection in the pavement.
Principle of FWD: A heavy weight is dropped from a pre-determined height on to a series of springs placed on top of a loading plate. This causes vertical surface deflections at different locations, which are then measured.
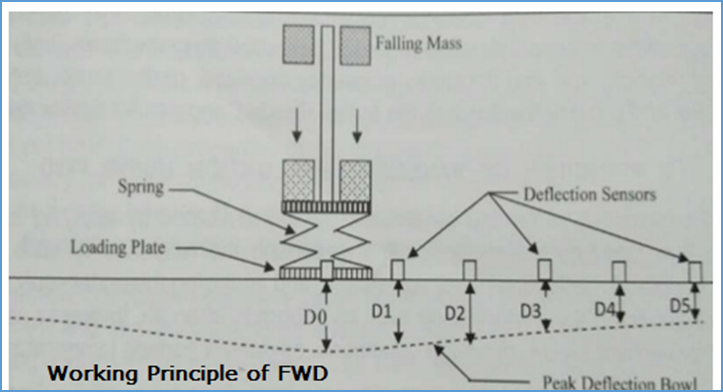
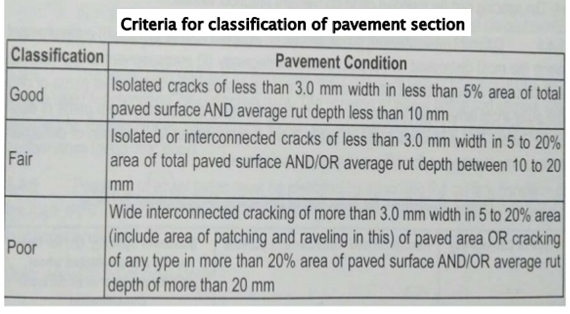
Steps:
- Mark the test points on the pavement.
- Raise the mass to a pre-determined height so as to produce a target load of 40 KN.
- Drop the mass and record the deflection data through data acquisition system.
- Record the pressure and temperature of the surrounding air at regular intervals.
- Measure the pavement temperature by drilling holes of 40mm depth into the pavement.
- Deflection measurements should not be carried out when pavement temperature > 45ᵒC.
Reference Books:
- S.K. Khanna and C.E.G. Justo - Highway Engineering - 10th Edition, Nem Chand and Bros. Roorkee
- L.R. Kadiyali - Traffic Engineering and Transport Planning - Khanna Publishers