Unit - 1
Design Philosophy and Tension Members
1. Tower:
Towers may be self-supporting or cable-stayed. Towers are made of steel angles or tubes, bolted at site. Towers are of different types such as telephone tower, windmill tower, observation towers, lighting towers, power transmission towers etc. The function of tower is to provide support.
2. Roof truss:
A truss is a framed structure consisting of different members like tie, principal rafter, strut and slings; forming triangles i.e., a perfect frame. The steel roof trusses are used when
(1) Span is very large and the beam construction is not economical
(2) The building is in area of heavy rainfall.
Various types of trusses are
(i) Howe truss
(ii) Simple fink truss
(iii)Compound French truss
(vi) Simple tan truss
(v) Pratt truss
(vi) Compound fink truss
(vii) North-light truss etc.
3. Water tank:
They may be circular, rectangular or spherical. They may rest on the ground or be elevated. The function of water tank is to contain material.
4. Bridges:
The truss and plate-girder bridges are commonly used for small to moderate spans, cable-stayed and suspension bridges for long spans. Sometimes arch bridge and cantilever bridge are also used. Foot Bridge is very common in a railway station. The function of bridge is to provide runway.
5. Gantry girder:
The travelling overhead cranes are commonly used in workshops and factories. The function and gantry girder is to lift and move the heavy materials and machinery from one place to other.
6. Column:
These are the members that resist compressive components of loads in a truss, and bridge piers. In building structure loads and moments are transmitted to column through beams. Generally, a compound column is used consisting of channels placed face to face or back-to-back. The two components must be tied together with the help of lacing or battening. The function of column is to give support.
Key takeaways:
- Towers may be self-supporting or cable-stayed. Towers are made of steel angles or tubes, bolted at site.
- These are the members that resist compressive components of loads in a truss, and bridge piers.
- They may be circular, rectangular or spherical. They may rest on the ground or be elevated. The function of water tank is to contain material.
Types of steel | Designation | IS Codes | C (Max) | Mn (Max) | S (max) | P (Max) | Si (Max) | Carbon equivalent |
Standard | Fe 410 A | 2062 | 0.23 | 1.5 | 0.050 | 0.050 | 0.4 | SK 0.42 |
Structure | Fe 410 B | 2062 | 0.22 | 1.5 | 0.045 | 0.045 | 0.4 | SK 0.41 |
Steel (IS 2062) | Fe 410 C | 2062 | 0.20 | 1.5 | 0.040 | 0.040 | 0.4 | K 0.39 |
Micro alloyed medium high strength steel | Fe 440 | 8500 | 0.20 | 1.5 | 0.050 | 0.050 | 0.45 | 0.40 |
Fe540 | 8500 | 0.20 | 1.5 | 0.045 | 0.045 | 0.45 | 0.44 | |
Fe 590 | 8500 | 0.20 | 1.5 | 0.045 | 0.045 | 0.45 | 0.48 |
Where,
Fe Stands for steel and the number after Fe is the tensile strength in N/mm^2 or MPa
K: killed steel
SK: Semi killed steel
C= Carbon
Mn = Manganese
S= Sulphur
P= phosphorus
Si= silicon
Structural Steel has been classified based on its ultimate or yield strength
e.g., Fe 410 Steel means minimum tensile strength of 410 N/mm^2. The mechanical properties of steel largely depend on its chemical composition given below
Types of steel | Designation | UTS | Yield strength (MPa) Thickness (mm)/ (<20 20-40>40) | Min. Percentage elongation gauge length = 5.65(A0) ^2 | Charpy V notch impact energy (min) | ||
Standard | Fe 410 A | 410 | 250 | 240 | 230 | 23 | - |
Structure | Fe 410 B | 410 | 250 | 240 | 230 | 23 | 27 |
Steel (IS2062) | Fe 410 c | 410 | 250 | 240 | 230 | 23 | 27 |
Micro alloyed | Fe 440 B | 440 | 300 | 290 | 280 | 22 | 30 |
Medium/High | Fe 540 B | 540 | 410 | 390 | 380 | 20 | 25 |
Standard Steel | Fe 490 B | 490 | 350 | 330 | 320 | 22 | 25
|
The main aim of structural designer is to select the appropriate cross section for individual members of the structure.
This selection is done using widely available standard rolled steel sections which are of any standard. Rolled steel sections manufactured are listed below with designation:
1. Rolled Steel I-section
2. Steel channel Sections
3. Rolled Steel Angle Sections
4. Rolled Steel Tee-sections
5. Steel Plates
6. Rolled Steel Strips
7. Rolled Steel Flats
8. Rolled Steel Bars
1. Rolled steel I section
Following series of rolled steel I sections are manufactured in India:
(a) Indian Standard Junior Beams - ISJB
(b) Indian Standard Light Beams - ISLB
(c) Indian Standard Medium Beams - ISMB
(d) Indian Standard Wide-flange Beams - ISWB
(e) Indian Standard Heavy Beams - ISHB
The above sections are designated by the series to which they belong followed by depth (in mm) and weight (in kg/m) per meter run e.g., ISMB 300@ 44.2 kg/m.
2. Rolled Steel Channel Sections
These sections are classified into the following series:
(a) Indian Standard Junior Channel - ISJC
(b) Indian Standard Light Channel - ISLC
(c) Indian Standard Medium Weight Channel - ISMC
(d) Indian Standard Special Channel - ISSC
Rolled steel channel sections are designated by the series to which they belong, followed by depth (in mm) and weight (in kg/m).
3. Rolled Steel Angle Sections:
These sections are classified into the following series:
(a) Indian Standard Equal Angle - ISA
(b) Indian Standard Unequal Angle - ISA
These sections are designated by series of names ISA followed by length thickness of leg.
4. Rolled steel Tee section:
These sections are classified into following series:
(a) Indian Standard Normal Tee Bars = ISNT
(b) Indian Standard Heavy Flanged Tee Bars = ISHT
(c) Indian Standard Special Legged Tee Bars = ISLT
(d) Indian Standard Light Legged Tee Bars = ISLT
(e) Indian Standard Junior Tee Bars = ISJT
These sections are designated by the series to which they belong, followed by depth (in mm) and weight per meter length (in kg/m) c.g. ISNT 60 @ 5.3 kg/m.
5. Rolled Steel Plates
These plates are classified into the following series.
Indian Standard Plate (ISPL) These plates are designated by ISPL, followed by dimension in mm i.e., length, width and thickness, e.g., ISPL 2000 x 1100 x 8. These are available for various thicknesses (mm) and widths (mm). Thicknesses of plates are more than 5 mm. (t>5 mm).
6. Rolled Steel Strips:
These strips are designated as Indian Standard Strip ISST, followed by width (mm) and thickness (mm) e.g., ISST 160 x 1.4.
Thickness of strips are less than 5 mm (t<5 mm).
7. Rolled Steel Flats:
They are designated by width, followed by Indian standard Flats ISF, and thickness e.g., 50 ISF 5. Flats have thickness more than 5 mm but width is limited (b< 250 mm).
8. Rolled Steel Bars
Rolled steel bars are classified in to following series:
(a) Indian Standard Round Bar (ISRO)
(b) Indian Standard square Bar (ISSQ)
These are designated by ISRO, followed by diameter in case of round bar and ISSQ followed by width e.g., ISRO-12, ISBQ-16.
Key takeaways:
- The main aim of structural designer is to select the appropriate cross section for individual members of the structure.
- This selection is done using widely available standard rolled steel sections which are of any standard.
- Thickness of strips are less than 5 mm (t<5 mm).
- Indian Standard Plate (ISPL) These plates are designated by ISPL, followed by dimension in mm i.e., length, width and thickness
To decide the size, shapes and connection details of the members, the following design philosophies listed below are used in the order of their evolution and they are briefly explained.
1. Working Stress Method (WSM)
2. Ultimate Load Design (ULD)
3. Limit State Method (LSM)
1. Working Stress Method (Allowable Stress Design)
It is one of the oldest methods of design suitable for all structures. Through IS-800-2007 insists for the limit state design, permits use of this method wherever LSM cannot be conveniently adopted.
With the development of linear elastic theory in the 19th century, the stress-strain behavior of material is considered as linear till the yield stress. To take care of uncertainties in the design, permissible or Allowable stress is kept action of yield stress by the ratio known as factor of safety. So that the members designed are to keep the stresses within the permissible value.
Allowable or permissible stress = Yield stress/Factor of safety
Working stress due Permissible or to working loads
(a) For beams FOS = 1.67 Allowable stress
(b) For long column FOS = 1.92
(c) For short column FOS = 1.67
(d) For connections FOS = 2.5-3
A set of load combinations is given below, which are unlikely to act on the structure. (Stress due to DL + WL+LL) < 1.33 (Stress due to DL+LL) Allowable stress (Stress due to DL + WL) S Allowable stress
Advantages:
1) This method is simple.
2) This is reasonably reliable.
3) As the working stresses are low, the serviceability requirements are satisfied automatically.
Limitations:
1) Assumption of linear elastic behavior and the stresses under working loads can kept within the permissible stresses are not found to be realistic.
2) Many factors like the effect of stress concentrations, creep, shrinkage, residual stresses and other secondary effect are not considered.
3) This method does not consider material non linearity and non-linearity of structural members.
4) This method does not provide a realistic measure of the actual factor of safety for the design.
5) It gives uneconomical sections.
2. Ultimate Load Method (Load Factor Method) (ULM)
Ultimate limitation of the working stress method to determine actual load carrying capacity, made researchers to develop ultimate load method, which is also known as plastic design method.
In this method, a section is said to have formed a plastic hinge when all fibres yield. But the structure continues to resists load until sufficient number of plastic hinges are formed to transfer the structure in to a collapse mechanism. At this state the load is known as ultimate load. Safety measures are introduced by using load factor, which is defined as the ratio of design load to working load. This lo factors as per IS 800-1984 are given in table.
Thus, E (Working load + Load factor (LF)) Ultimate load
Sr. No. | Working load | Maximum load factor |
1 | DL | 1.7 |
2 | DL+IL | 1.7 |
3 | DL+WL or EL | 1.7 |
4 | DL+IL+WL or EL | 1.3 |
Advantages:
- Due to plastic hinge concept, redistribution internal forces are accounted.
- It allows varied selection of load factors.
Limitations:
- Limitation on deflection and also it does not guarantee other serviceability limits like instability and fatigue.
- This method is more comprehensive method to take care of strength.
- It does not guarantee of serviceability performance.
3. Limit State Method of Design (LSM)
IS 800-2007, a code of practice, applicable to the structural use of hot-rolled steel is largely based on limit state method of design. However, it still retains the working stress method where LSM cannot be adopted. The limit state method of design developed to take account of all uncertainties limitations of WSM and ULM] that can make the structure unfit for use by considering actual behavior of material and structure.
In the Limit State Method (LSM), basically statistical methods have been used for determination of loads and material properties with a probability of structure reaching the limit state of strength and serviceability. However, it is not yet possible to adopt a complete probability basis for design and therefore the method adopted partial factors of safety which are introduced to take account of all the uncertainties.
Advantages of Limit state method over working stress method:
- In this method, possibility of material non linearity, structural non-linearity, calculation error is considered.
- Factor of safety are called partial safety factors determined by statistical analysis.
- This method provides a realistic measure of the actual factor of safety.
- This method designs any structural element for strength as well as serviceability criteria.
- This method considered reserve strength of material beyond elastic limit of stress-strain curve.
Key takeaways:
- Allowable or permissible stress = Yield stress/Factor of safety
- In this method, possibility of material non linearity, structural non-linearity, calculation error is considered.
- This method designs any structural element for strength as well as serviceability criteria.
- This method considered reserve strength of material beyond elastic limit of stress-strain curve.
The Working Stress Method assumes that all cloth used within side the layout behaves in a linear elastic way and calculations are primarily based totally on carrier situations. The predicted running hundred sat the shape are triggered as stresses at the shape for the duration of the layout and those are restricted (to be under the permissible stresses) to make certain ok protection. The thing of protection is the ratio of the power of the cloth to the permissible pressure. However, as running hundreds can't be stored in the permissible stresses this technique isn't always continually viable.
The assumption within side the Ultimate Load Method is that the cloth isn't always linear-elastic which means that extraordinary hundreds can have extraordinary protection elements. Calculations are primarily based totally on closing load situations and the pressure situations on the web page of failure or approaching crumble is analyzed. This effect in extra slender (consequently extra economic!) sections
However, this technique can bring about cracks and deflections which can be excessive because of the serviceability home snow no longer being met.
In the Limit State Method (aka as Limit State Design), the layout of the shape is taken into consideration for each the serviceability and closing load kingdom. This is consequently the higher layout philosophy to employ. The extraordinary restrict states is the Ultimate Limit State (ULS) and the Serviceability Limit State (SLS), for which distinction are made within side the code SANS10160: five.1.3... These states every have their own minimal degree of reliability - that's colloquially called the Safety Index.
- Ultimate Limit State of strength:
It considers power, overturning, fatigue, sliding etc.
2. Serviceability Limit State:
It considers crack width, deflection, vibration etc.
It makes use of more than one protection elements for the desired protection and serviceability on the closing load and running load respectively through thinking about all restrict states. These are called “partial protection elements”.
Partial protection thing for materials:
The power of concrete in real shape is taken as (0. Sixty-seven *function power), i.e.,0. Sixty-seven fck. The partial protection thing (for closing restrict kingdom) for concrete is 1. Five and that for metal is 1.15. The fee is better for concrete as its miles predicted to have extra variability as compared to metal. The partial protection thing (for serviceability restrict kingdom) for concrete and that for metal is taken as 1.0. This is taken as solidarity as we're interested by estimating the real deflections are crack width for the duration of carrier hundreds.
Partial protection thing for hundreds:
Various load combinations are laid out in IS 456 are
For Ultimate limit states or strength of limit state
- UL = 1.5(DL+LL)
- UL = 1.5(DL+QL) OR 0.9DL+1.5QL
- UL = 1.2(DL+LL+QL)
The load factor of 1.2 is considered for the combination of three because the probability of the three loads reaching its peak together is less.
For serviceability limit states
- SL = 1.0 (DL+LL)
- SL = 1.0 (DL+QL)
- SL = 1.0DL+ 0.8LL+ 0.8 QL
The load factor is taken as 0.8 in the third case as the probability of wind load or earthquake load acting with the peak of live load is less. For all cases the safety factor is taken as 1.0 as we are considering the serviceability of structure here.
Where DL is dead load, LL is live load and QL is earthquake/wind load.
Key takeaways:
- Ultimate Limit State of strength: It considers power, overturning, fatigue, sliding etc.
- Serviceability Limit State: It considers crack width, deflection, vibration etc.
- The load factor is taken as 0.8 in the third case as the probability of wind load or earthquake load acting with the peak of live load is less
1.The partial safety factor for load
It accounts for
- Possibility of unfavorable deviation of the load from the characteristics value
- Possibility of inaccurate assessment of the load
- Uncertainty in the assessment of effect of the load
- Uncertainty in the assessment of the limit states being considered
The loads or loads effects shall be multiplied by the relevant factor given in table 1.10.1 to get design loads or factored load
Combination | Limit state of strength | Limit state of serviceability | |||||||
| DL | LL | WL/EL | AL | DL |
| LL | WL/EL | |
|
| Leading | Accompanying |
| Leading | Accompanying |
| ||
DL+LL+CL | 1.5 | 1.5 | 1.05 | - | - | 1.0 | 1.0 | 1.0 | - |
DL+LL+CL+WL/EL | 1.22 1.2 | 1.2 1.2 | 1.05 0.53 | 0.6 1.2 | - | 1.0 | 0.8 | 0.8 | 0.8 |
DL+WL/EL | 1.5(0.9) | - | - | 1.5 | - | 1.0 | - | - | 1.0 |
DL+ER | 1.2(0.9) | 1.2 | - | - | - | - | - | - | - |
DL+LL+Al | 1.0 | 0.35 | 0.35 | - | 1.0 | - | - | - | - |
2.The partial safety factor for resistance
It accounts for
- Possibility of unfavorable deviation of material strength from the characteristics value.
- Possibility of unfavorable variation of member sizes
- Possibility of unfavorable reduction in member in strength due to fabrication and tolerances
- Uncertainty to the calculation of strength of member
Sr. No | Definition | Partial safety factor | |
1 | Resistance governed by yielding ![]() | 1.10 | |
2 | Resistance of member to buckling ![]() | 1.10 | |
3 | Resistance governed by ultimate stress ![]() | 1.25 | |
4 | Resistance of connection ![]()
| Shop fabrication | Field fabrication |
1.25
1.25
1.25 1.25 | 1.25
1.25
1.25 1,50 |
Various loads are expected to act on a structure may be classified as given below:
(a) Dead Loads (DL)
(b) Imposed Loads (IL)
(c) Wind Loads (WL)
(d) Earthquake Loads (EL)
(e) Erection Loads (ER)
(f) Accidental Loads (AL)
(g) Secondary effects.
Judicious combination of the loads is necessary to ensure the required safety and economy in the design keeping in view the probability of their,
(a) Acting together combination of various loads.
The various load combination are given as below:
1. DL
2. DL+ WL
3. DL+TL
4. DL+IL+EL
5. DLNL+TL
6. DL+IL+EL+TL
7. DL+IL+EL+TL.
Where TL-Temperature Loads
All type of loads and load combinations required for design are briefly explained at the time of design of respective steel members
Tension member
When an anxiety member is subjected to axial tensile pressure, then the distribution of strain over the pass-segment is uniform.
The complete internet place of a member is efficaciously used on the most permissible uniform strain.
Therefore, a tensile member subjected to axial tensile pressure is used to be green and not pricey member.
The method of the layout of an anxiety member is defined under with assist of instance problems.
Tension members are structural elements which are subjected to axial tensile forces. Examples of anxiety members are bracing for homes and bridges, truss members, and cables in suspended roof systems.
In an axially loaded anxiety member, the strain is given by:
F = P/A
Where in P is the importance of the burden and A is the pass-sectional place.
The strain given by this equation is exact, understanding that the pass segment isn't adjoining to the factor of utility of the burden nor having holes for bolts or other discontinuities.
For instance, given an eight x 11 five plate this is used as an anxiety member (segment a-a) and is hooked up to a gusset plate with 7/eight-inch-diameter bolts (segment b-b):
- Gross section yielding:
Steel member (plates, angle) without bolt holes can sustain loads up to the ultimate load without failure. However, the member will elongate considerably (10 to 15 % of its original length) at this load and hence make the structure unserviceable.

Where,
Fy = yield strength of the materials in MPa
Ag = gross area of cross section in mm2
2. Net section rupture:
This occurs where tension member connected to the main or other member by bolts or weld. The holes made in members for bolts will reduce the cross section, and hence net area will govern the failure in this case.
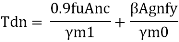

Where

w = outstanding lag effect
Bs = shear lag width
For preliminary sizing the rupture strength of net section may be approximately taken as

3. Block shear failure:
Block shear failure considered as a potential failure made at the ends of an axially loaded tension member. In this failure mode, the failure of the member occurs along a path involving tension on one plane and shear on a perpendicular plane along the fasteners.
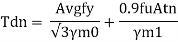
Where,
Avg= minimum gross and net area
Fu and fu = ultimate and yield stress due to the materials resp.
Key takeaways:
- Steel member (plates, angle) without bolt holes can sustain loads up to the ultimate load without failure.
- Block shear failure considered as a potential failure made at the ends of an axially loaded tension member
- This occurs where tension member connected to the main or other member by bolts or weld.
Examples:
Q.1 Design bolted connection for single angle ISA 90 x 90x 6 mm @ 8.2 kg/m carrying factored axial tension 115 KN with 8 mm thick gusset plate. Use M16 bolt of property class 4.6
Solution:
Given
- Properties of cross section
ISA 90x90x6 mm @ 8.2 kg/m
Ultimate strength of bolt fub= 400 MPa
Ultimate strength of steel fu= 410 MPa


d = 16mm
d0= 18 mm
2. Design of bolted connection
- Shear strength of bolt




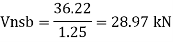
b. Bearing strength of bolt
a)
b)



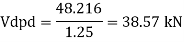
Bolt value = least of V dsb and V dpb= 28.97 kN
Number of bolts required = 115/28.97 = 3.96 = 4 bolts
Q.2 A tie member of a truss 2ISA 65x65x6 @ 5.8 kg/m back-to-back on either side is welded to gusset plate. Design a weld to transmit a load equal to the full strength of the member.
Solution:
- Design tensile strength due to yielding of gross cross section

2. Design of welded connection
From table 21 IS 800-2007
Assume size of weld= 6 mm
By equating,



But

Taking moment about C.G


By using equation


Case Study
Steel Structure:
Firstly, its useful to recognize what structural metal absolutely is and the way its miles formed. Structural metal shapes are comprised of this type of metal, that is formatted from a specific move section. Yet, on the identical time it follows exact requirements for mechanical homes and chemical composition. Structural metal is available in numerous shapes like L-beam, Z shape, HSS shape, L shape (angle), structural channel (C-beam, move section), T shaped, rail profile, bar, rod, plate and an open joist of internet metal.
Standard structural metallic varies in one-of-a-kind international locations with numerous specifications. For example, European I-beam is Euro norm 19-57, while structural metallic within side the USA is available in carbon, low alloy, corrosion resistant excessive power low alloy, quenched and tempered alloy metallic etc. Structural metallic is versatile, sturdy and durable, so it is infrequently sudden that it is able to be morphed into nearly any form primarily based totally on the development task at hand; it is able to be built nearly straight away the instant its miles obtained at the constructing site. Structural metallic is hearth place-resistant in itself however hearth place safety strategies must be installed vicinity in case there may be an opportunity of it getting heated up to some extent wherein it begins off evolved to lose its sturdiness and power.
Corrosion must be avoided in terms of structural metallic, however tall homes are regarded to have withstood diverse types of adversities while constructed the usage of structural metallic. Steel creation is growing in reputation everywhere in the world, with each area benefitting from metallic for the duration of the years. Many of the quality architectural wonders were built thru the usage of metallic, be it structural, carbon or rebar, together with The Empire State Building and the Sydney Harbor Bridge. More importantly, using metallic is useful in phrases of eco friendliness than different modes of creation, and because of this aspect alone, it's far given extra preference. Taking into attention the charge of marvelous constructions, metallic has proved favorable. With using metallic growing within side, the creation industry, there may be absolute confidence that it's going to take over the whole creation discipline quickly within side the future.
Tension Members:
Tension participants are structural factors which might be subjected to natural tensile forces. The choice in their go phase is one of the handiest and maximum truthful troubles encountered in metal layout. Since balance is of teen situation with anxiety participants, the hassle is decreased to choosing a phase with enough place to hold the layout load without exceeding the allowable tensile stress, as decided via way of means of the element of safety. A structural member is taken into consideration a compression member if it's far below a compressive load, both on my own or with different loadings. Columns, beam-columns, plates, element elements of frames, and the compression flange of beams or plate girders will be protected on this category.
The fundamental variations among anxiety and compression participants are: • Tension participants are held instantly by way of tensile masses, whilst in compression participants, the compressive masses generally tend to bend the member out of the aircraft of loading. • For riveted and bolted connections, the internet region will govern the power of an anxiety member, whilst for compression participants the rivets and holes are assumed to fill the holes. For anxiety participants, balance phenomena aren't standards within side the design, however they may be required to save you sagging for anxiety participants if they may be too lengthy or applied to assist vibrating equipment. In this case, the slenderness ratio (λ=kL/r), in which L is the anxiety member duration and r is the radius of gyration, need to be now no longer better than three hundred and the buckling duration component is identical to 1.0.
References:
- Design of Steel Structure, N Subramanian, Oxford University Press, New Delhi
- Limit State Design in Structural Steel, M. R. Shiyekar, PHI, Delhi
- Fundamentals of structural steel design, M L Gambhir, Tata McGraw Hill Education Private limited, New Delhi.
- Limit State Design of Steel Structure, Ramchandra & Gehlot, Scientific Publishers, Pune
- Analysis and Design: Practice of Steel Structures, Karuna Ghosh, PHI Learning Pvt. Ltd. Delhi
- Structural Design in Steel, Sarwar Alam Raz, New Age International Publisher
- Limit State Design of Steel Structure, V L Shah & Gore, Structures Publication, Pune
- IS Codes :- IS 800-2007: Code of practice for general construction in steel, Bureau of Indian Standards, New Delh