Unit 2
DC Motor Drives
Here, a braking resistor Rb is connected across the armature as soon as the DC motor is disconnected from the supply mains. The motor now works as a generator, producing the braking torque. The motor is connected in two ways.
It is connected either as a separately excited generator, where the flux is kept constant.
The second way is that it can be connected to a self-excited shunt generator, with the field winding in parallel with the armature.
The diagram of separately excited DC motor is shown below. When the machine works in the motoring mode.
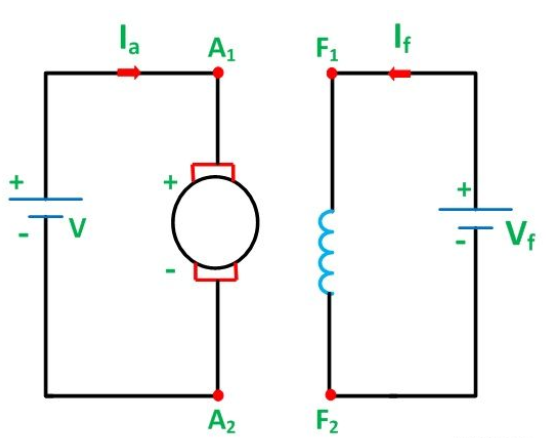
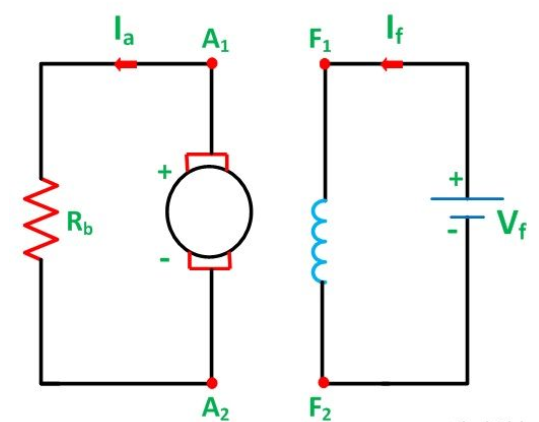
This method is also known as Rheostatic Braking because an external braking resistance Rb is connected across the armature terminals for electric braking.
Plugging Braking
Here, the armature terminals or the supply polarity of a separately excited or shunt motor when running are reversed. Therefore, in this the supply voltage V and the induced voltage Eb which is also called back EMF will act in the same direction.
Thus, during plugging the effective voltage across the armature will be (V + Eb) which is almost twice the supply voltage. The armature current is reversed, and a high braking torque is produced.
An external current limiting resistor is connected in series with the armature to limit the armature current. The connection diagram of DC separately excited motor and its characteristics is shown below.
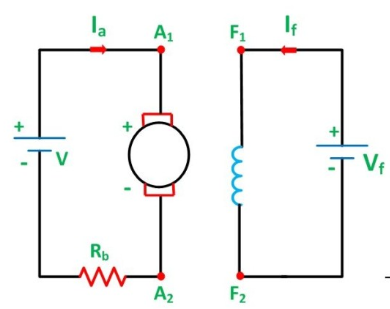
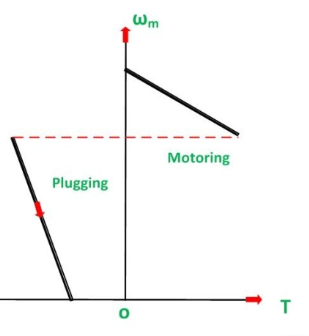
Where,
V is the supply voltage
Rb is the external resistance
Ia is the armature current
If is the field current.
Similarly, the connection diagram and the characteristic of the series motor in plugging mode is shown below.
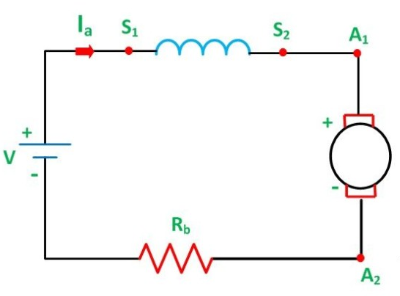
Regenerative Braking
Here, the power or energy of the driven machinery which is in kinetic form is returned back to the power supply mains. This type of braking is possible when the driven load or machinery forces the motor to run at a speed higher than no load speed with a constant excitation.
Under this condition, the back emf Eb of the motor is greater than the supply voltage V, which reverses the direction of motor armature current. The machine now begins to operate as a generator and the energy generated is supplied to the source.
It can also be performed at very low speeds if the motor is connected as a separately excited generator. The excitation of the motor is increased as the speed is reduced so that the two equations given below are satisfied.

The motor does not enter into saturation on increasing excitation.
Regenerative braking is possible with shunt and separately excited motors. In compound motors, braking is possible only with weak series compounding.
In closed loop system, the output of the system is feedback to the input. The closed loop system controls the electrical drive, and the system is self-adjusted. Feedback loops in an electrical drive may be provided to satisfy the following requirements.
Enhancement of speed of torque
To improve steady-state accuracy.
Protection
Current Limit Control
This scheme is used to limit the converter and motor current below a safe limit during the transient operation. The system has a current feedback loop with a threshold logic circuit.

The logic circuit protects the system from a maximum current. If the current is raised above maximum set value due to a transient operation, the feedback circuit becomes active and force the current to remains below the maximum value. When the current become normal, the feedback loop remains inactive.
Torque control
Such types of loop are used in battery powered vehicles, rails, and electric trains. The reference torque T* is set through the accelerator, and this T* follows by the loop controller and the motor. The speed of the drive is controlled by putting pressure on the accelerator.
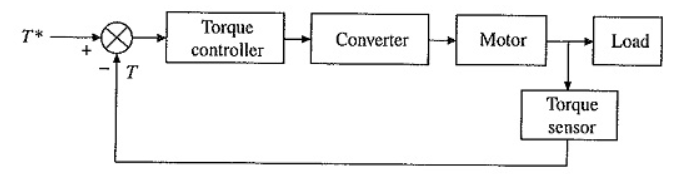
Speed control
The block diagram of the closed loop speed control system is shown in the figure below. This system used an inner control loop within an outer speed loop. The inner control loop controls the motor current and motor torque below a safe limit.
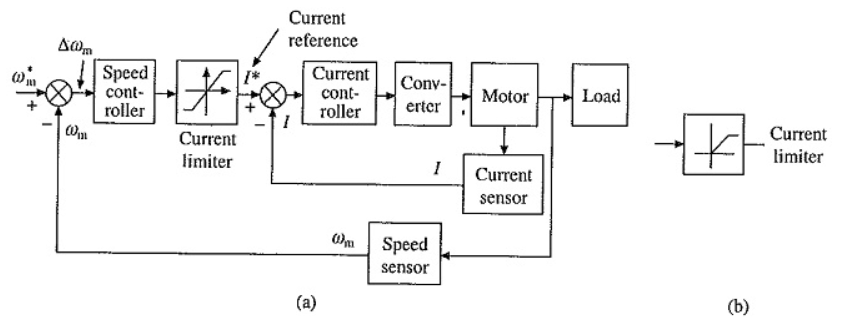
Single phase and three phase fully controlled converter drives
Here AC supply is fed to the phase controlled rectifier circuit.AC supply may be single phase or three phase. Phase controlled rectifier converts fixed AC voltage into variable DC voltage . Here the circuit consists of SCR’s. By varying the SCR firing angle the output voltage can be controlled. This variable output voltage is fed to the DC motor. By varying the motor input voltage, the motor speed can be controlled.

Figure shows block diagram of single phase controlled rectifier fed separately excited DC motor. The armature voltage is controlled by means of a half wave controlled or half controlled or full convener. l¢ AC supply is fed to the single phase controlled rectifier. This controlled rectifier converts fixed AC voltage into variable DC voltage. By varying the firing angle of this converter, we can get variable DC voltage. The field winding is fed from the AC supply through a diode bridge rectifier.
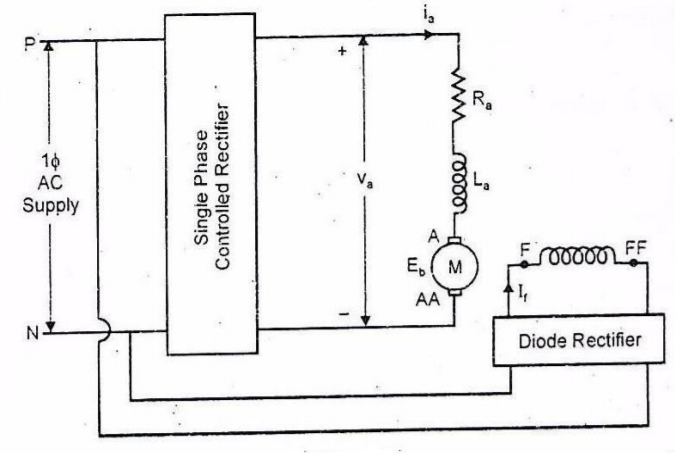
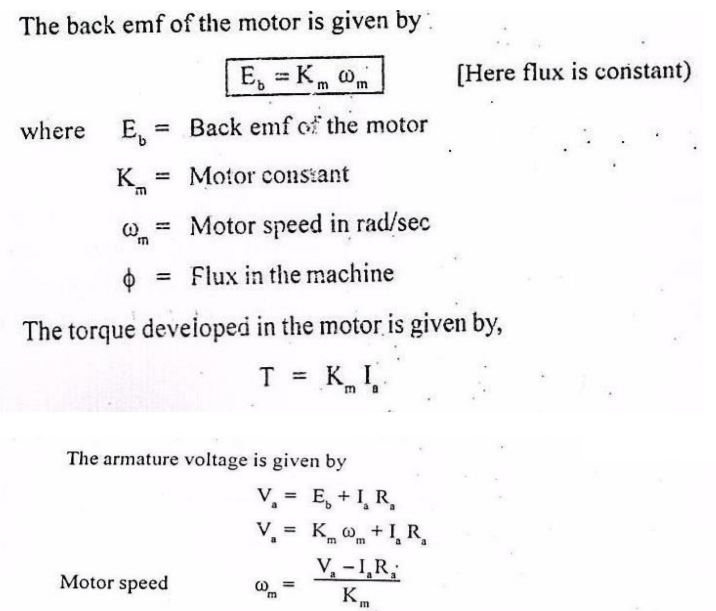
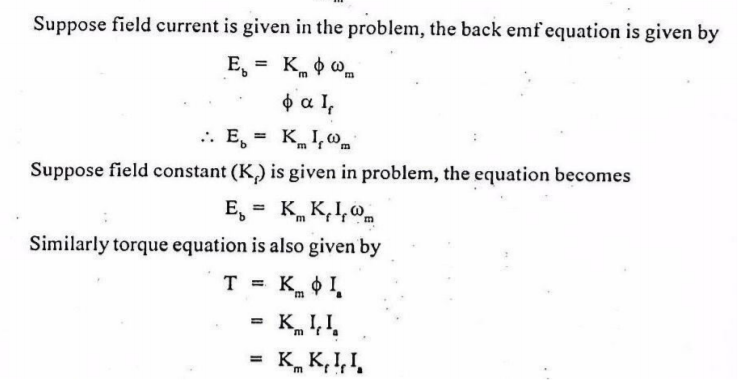
Three phase fully controlled converter drives
Three phase-full converters are used industrial applications upto 1500 kW drives. It is a two quadrant convener i.e., the average output voltage is either positive or negative but average output current is always positive.
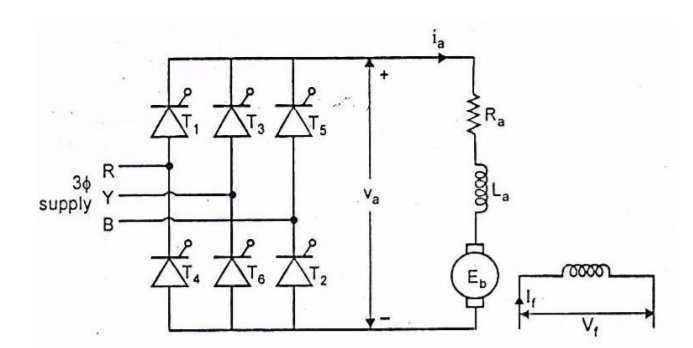
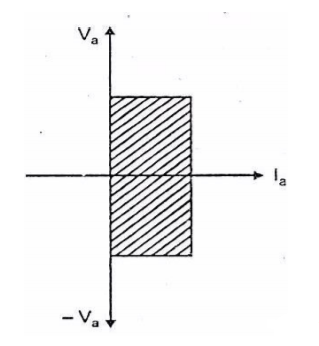
The circuit consists of six thyristors.
There are two groups of thyristors, one is positive group Tl, T3, T5 and another one is negative T4, T6, T2 group.
The positive group thyristors are tumed on when the supply voltages are positive and vice versa.
For α = 60°,
T1 is turned on at П/3+ 60 =120°,
T2 at ωt = l80°,
T3 at ωt = 240°
And so on.
When T1 is turned on at ωt = l20°, T5 is turned off. T6 is already conducting. As T1 and T6 are connected to R and Y respectively, load voltage must be very as shown in fig.
When T2 is turned on, T6 is commutated. As T1 and T2 are now conducting, the load voltage is vrb, figure. In this way, load voltage waveform can be drawn with thyristors in sequence.
For α = 120°,
T1 is triggered at ωt = l80°,
T2 is triggered at ωt = 240°
And so on,
The output voltage waveform is shown in figure. From this waveform, the average output voltage is negative. This means that dc source is delivering power to ac source. This operation is called line commutated inverter operation. For α 0 to 90°, this converter operates rectification mode (power flows from source to load) and 90° to 180 it operates an inversion mode (power flows from load to source). It can work in the inverter mode only if the load has a direct emf E. It is a regenerative braking mode.
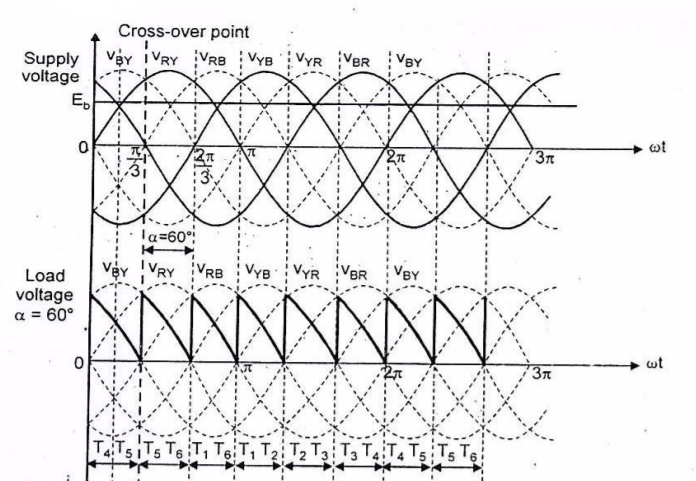
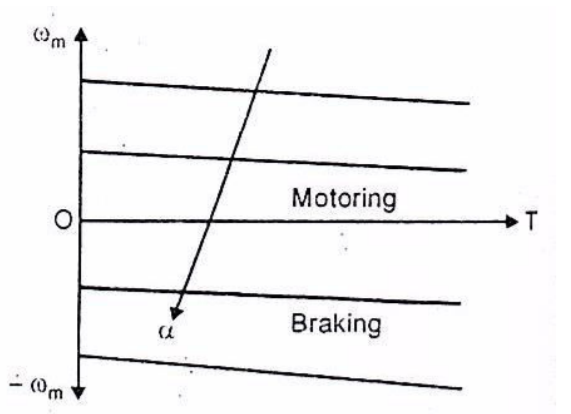
Fig: Speed Torque characteristics

Fixed DC voltage is fed to the Dc chopper circuit. DC chopper converts fixed DC into Variable DC voltage. This variable DC voltage is fed to the motor. By varying the DC voltage, the motor speed can be controlled.
Separately excited DC Motor operations
A transistor chopper controlled separately excited motor drive is shown in fig
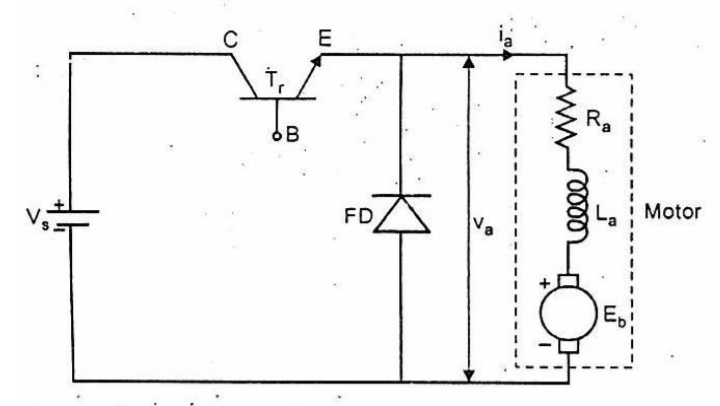
Current limit control is used in chopper.
In current limit control, the load current is allowed to vary between two given (upper and lower) limits.
The ON and OFF times of the chopper adjust automatically, when the current increases beyond the upper limit the chopper is turned off, the load current freewheels and starts to decrease.
When it falls below the lower limit the chopper is turned ON. The current starts increasing in the load. The load current ‘ia’ and voltage ‘va’ waveform are shown in figure .
By assuming proper limits of current, the amplitude of the ripple can be controlled, The lower the ripple current, the higher the chopper frequency. By this switching losses get increase. Discontinuous conduction avoid in this case,
The current limit control is superior one. During ON-period of chopper (i.e.) duty interval,0≤t≤TON, motor terminal voltage Va is a source voltage Vs and armature current increases from ia1 to ia2
The operation is described by,

Chopper is turned off at t = t0N. During off-period of chopper (i.e.) free wheeling interval, Ton≤ t ≤ T , motor current freewheels through diode FD and motor terminal voltage Va is zero.
This is described by,

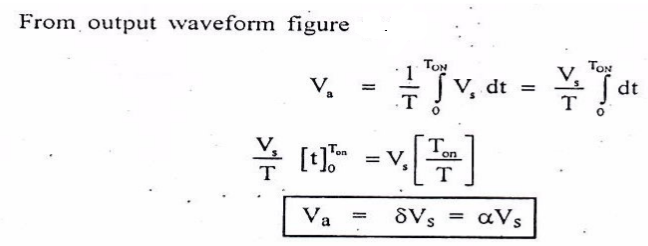
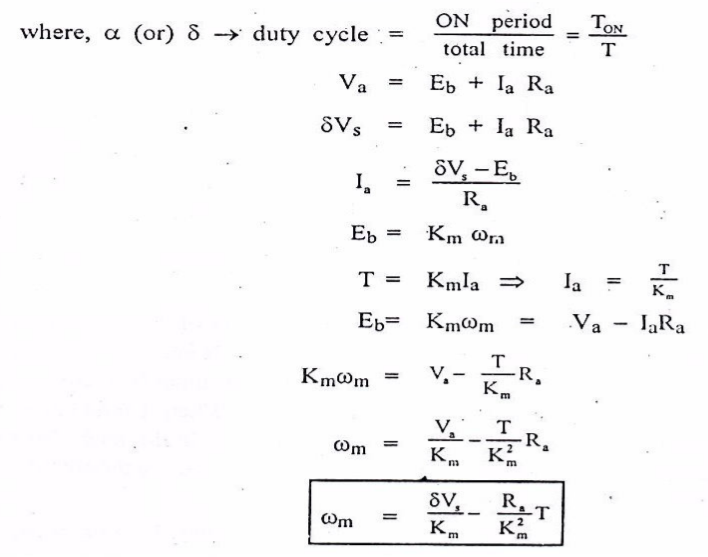
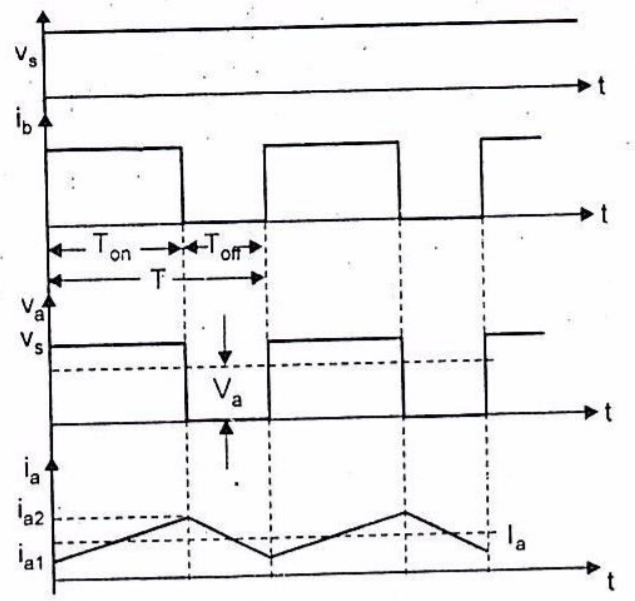
Example 1
A 25 Hp separately excited motor is operating at a speed of 250 rpm. It is supplied from a 120 V supply and draws 5.6 A. The total armature circuit resistance is .473 ohms. Find the torque constant for the machine.
Solution:

Eb = 120 – 5.6 x 0.473 = 117.35V
Pe = Eb x Ia = 117.35 x 5.6 = 657.17W
Now, Pem = Pe
Power = w x Torque
Converting rpm to rad/sec : (2π/60) x 250 = 26.16 rad/sec
Torque =Pem/w
T = 657.17/26.16 = 25.1 Nm
Now, T/Ia = BpKG
Here, Bp is constant for constant field current.
BpKG = KT is motor torque constant
Hence 25.1/5.6 = 4.485 Nm/A
KT is numerically equal to Ke when using SI units. In this case Ke = 4.485 V-sec/rad
Example 2
A 15 Hp separately excited motor is operating at its rated speed of 1200 rpm Determine the rated torque of the motor in ft-lbs
Solution:
Rated mechanical power output =15Hp
Pshaft = 15Hp
Rated speed n = 1200 RPM
Pshaft = Trated x n/5252
Or = Trated = Pshaft x 5252/ n
Trated = 65.65 lb. Ft
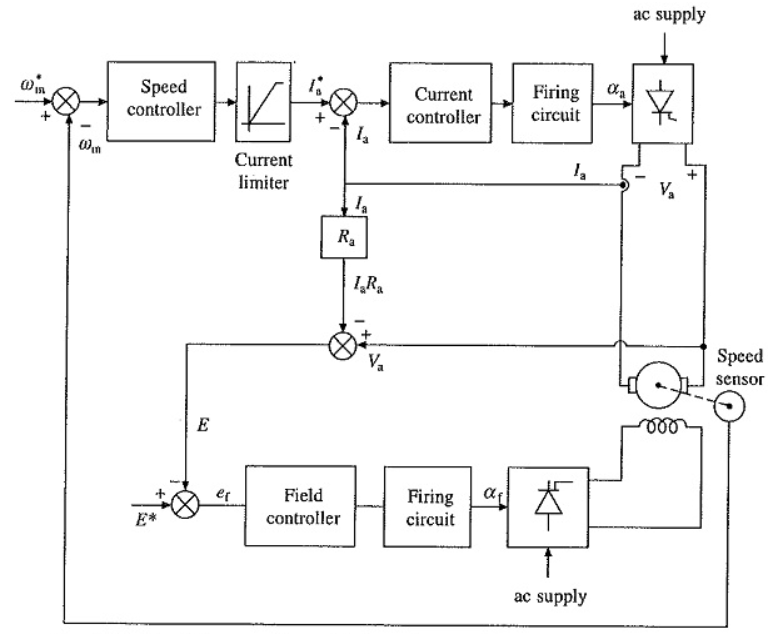
Fig: Closed loop speed control of DC motor below and above base speed.
The drive employs inner current control loop and outer speed loop. Such a drive will operate at a constant field current and variable armature voltage below the base speed, and at a constant armature voltage and variable field current above the base speed.
Both armature and field, are therefore, fed from fully-controlled rectifiers. Since, the armature is fed from a fully-controlled rectifier, forward braking is not possible; the drive will decelerate due to load torque only.
Because of inner current control with current limiter, the acceleration will take place at the maximum permissible current and torque. In semiconductor converter fed drives PI (proportional and integral) controller is often used because it filters out noise which can otherwise become a problem. PI controller also gives good steady-state accuracy.
Operation below the base speed
- In the field control loop, the back emf E is compared with a reference voltage E* which is chosen to be between 0.85 to 0.95 of the rated armature voltage.
- The higher value is used for motors with low armature circuit resistance.
- For speeds below base speed, the field controller saturates due to large value of error ef.
- The firing angle of field rectifier αf is maintained at zero, applying rated voltage to the field. This ensures rated field current for motor operation below base speed (ωmb).
- When speed reference is increased from ω*m1 to ω*m2 (ω*m2 <ωm1) due to large speed error, the current limiter saturates and sets the current reference at the maximum permissible value.
- The drive accelerates at the maximum available current and torque. When speed reaches close to ω*m2, the current limiter saturates and the drive settles at speed ωm2 and at the current which gives motor torque equal to the load torque.
- If speed reference is reduced back to ω*m1, the current reference is set at zero and the drive decelerates due to load torque.
- When ωm becomes slightly less than ω*m1 motor current flows again and finally drive settles at speed ωm1 and current for which motor torque balances the load torque.
- For negative speed error, I*a is set at zero because negative I*a is of no use. It will however charge PI controller.
- When reference speed is increased again, making speed error positive, the charged PI controller takes longer time to respond, making the transience response slower.
Operation above base speed
- When close to base speed, the field controller comes out of saturation. Now if the reference speed is set for a speed above base speed, the current reference is set at the maximum permissible value.
- The firing angle of the armature rectifier αa is reduced to initially increase Va. The motor accelerates, E increases, ef decreases, reducing the field current.
- Thus the motor speed continues to increase and field current continues to decrease until the motor speed becomes equal to the reference speed.
- Since, the speed error will now be small, Va will return to a value close to original value. Thus, the speed control above base speed is obtained by field control with the armature voltage maintained near the rated value.
- In the field control region (above base speed), the drive responds very slowly due to large value of the field time constant.
Reference Books
[R1] B. K. Bose, “Modern Power Electronics and AC Drives”, Pearson Education
[R2] Malcolm Barnes, “Practical Variable Speed Drives and Power Electronics”, Elsevier
Newnes Publications
[R3] V. Subrahmanyam, “Electric Drives: Concepts and Application”, Tata Mc-Graw Hill
(An imprint of Elsevier)
[R4] M.D. Singh and Khanchandani “Power Electronics”, Tata Mc-Graw Hill
[R5] Austin Huges, “Electrical motor and drives: Fundamental, types and applications”,
Heinemann Newnes, London
[R6] Tyagi MATLAB for engineers oxford (Indian Edition)