Unit 4
Induction Motor Drives II
The basic conceptual implementation of vector control is shown in the figure below.
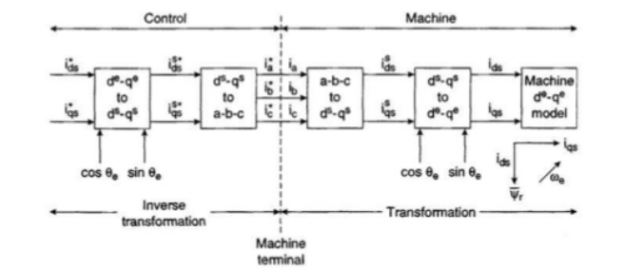
Figure 1. Vector control implementation principle with machine d e – q e model.
The motor phase currents ia, ib and ic are converted to ids s and I qss in the stationary reference frame.
These are converted to synchronously rotating reference frame d-q currents ids and iqs.
•Assume that the position of the rotor flux linkages phasor λ r is known.
• Let θ f be referred to as field angle, and λ r be at θ f from a stationary reference.
• The transformation in the synchronous frame

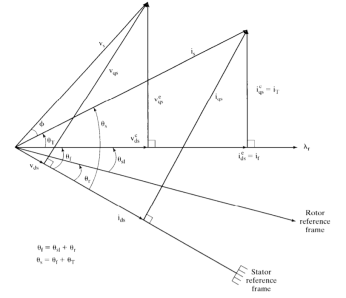
Figure 2. Phasor diagram of vector controller
Steps:
(i) Obtain the field angle
(ii) Calculate i f*, for the required λ r *
(iii) From λ r* and the required T e*, calculate the stator current i T*.
(iv) Calculate the stator-current phasor magnitude, is i s*, from the vector sum of i T* and i f*.
(v) Calculate torque angle
T = tan -1iT/i*f
(vi) Add θT and θf to obtain θs.
(vii) Through the dqo transformation to abc variables:
i* as = is * sin s
i*bs = i*s sin(s - 2π/3)
i*cs = i*s sin (s + 2π/3
(viii) Synthesize these currents by using an inverter.
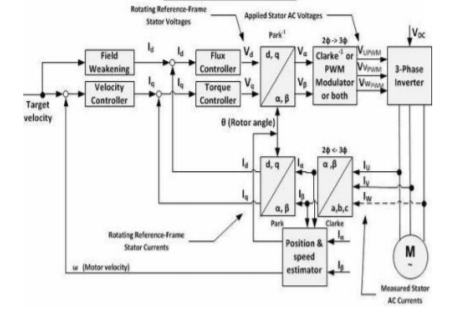
Figure 3. Vector control of induction motor
Vector control Block Diagram of separately excited DC motor which means the AC motor behaves like a DC motor in which the field flux linkage and armature flux linkage are created by the respective field and armature (or torque component) currents are orthogonally aligned such that, when torque is controlled, the field flux linkage is not affected, hence enabling dynamic torque response. Vector control accordingly generates a three-phase PWM motor Fig-3 displays the vector controlling results.
The three-phase stator current input through projections or rotations, back and forth between the three-phase speed and time dependent system . These vectors’ are rotating reference-frame two-coordinate time invariant system. Such complex stator current space vector can be defined in a (D-Q) coordinate system with orthogonal components along d (direct) and q (quadrature) axes such that field flux linkage component of current is aligned along the d-axis and torque component of current is aligned along the q-axis. The induction motor’s (D -Q) coordinate system can be superimposed to the motor’s instantaneous (a,b,c) three-phase sinusoidal system Components of the (D-Q) system current vector, allow conventional control such as proportional and integral, or PI control, as with a DC motor.
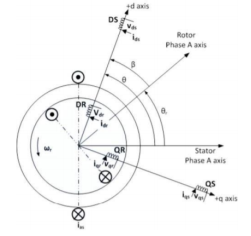
Figure 4. Co-ordinated system of three phase induction motor.
- Servo means controlling mechanical position or derivatives of position like velocity and acceleration.
- It’s an automatic device that uses the error sensing negative feedback for correction of the performance mechanism.
- Servo control mechanism uses negative feedback to control the mechanical position.
- Position control servo mechanism is used in pneumatic and hydraulic machines to control position.
- It is used in automatic machine tools, satellite tracking antenna, aircraft system and navigation system.
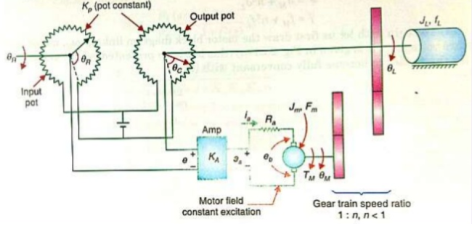
Figure 5.Position control servo mechanism.
The components of the system are :
Drive motor dc armature controlled .
Load is driven through a reduction gearing to amplify torque for moving load.
Load angular position is sensed by circular potentiometer.
Angle reference input sensed by an identical potentiometer.
Position error is fed to the amplifier to feed the motor armature at voltage Ea.
For control system the load reflected to motor shaft is giving the effective inertia and friction at motor shaft as
J = JM + n 2 JL.
f = fM + n 2 fL
To begin with the block diagram of linking wM motor speed, armature voltage ea.
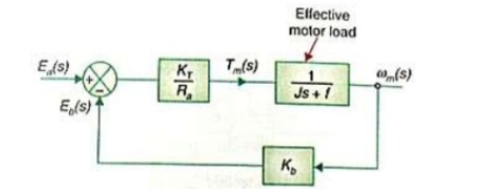
Figure 6. Linking motor speed and armature control.
Reducing block diagram
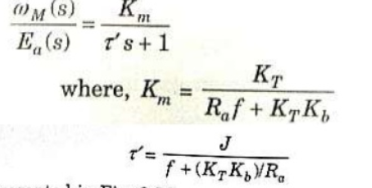
This can be represented as
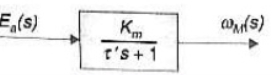
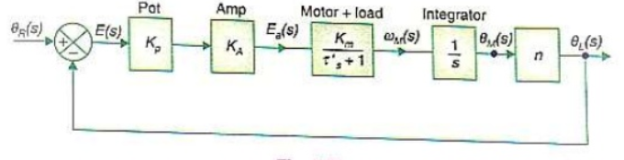
Figure 7. Complete block diagram.
The effective motor time constant including friction f and equivalent friction effect by motor back emf (Kb KT )/Ra
Symbol r is reversed for motor’s mechanical time constant t = J/f.
When an electric motor and drive operate, there is a generation of heat inside the motor. The amount of heat generated inside the motor should be known accurately. Therefore, thermal modeling of motor is necessary.
The material of the motors and the shapes and size of the motors are not unique. Therefore, the generation of heat does not alter very much depending on these characteristics.
So, a simple thermal model of any motor can be obtained by assuming it to be a homogeneous body. The main aim of this modeling is to choose the appropriate rating of a motor so that the electric motor does not exceed its safe limit during operation.
At time ‘t’, let the motor has following parameters
p1 = Heat developed, Joules/sec or watts
p2 = Heat dissipated to the cooling medium, watts –
W = Weight of the active parts of the machine.
h = Specific heat, Joules per Kg per oC.
A = Cooling Surface, m2
d = Co-efficient of heat transfer, Joules/Sec/m2/oC
θ = Mean temperature rise oC
Now, if time dt, let the temperature rise of the machine be dθ,
Therefore, heat absorbed in the machine = (Heat generated inside the machine – Heat dissipated to the surrounding cooling medicine)
Where, dθ = p1dt – p2dt…………….(i)
Since, p2 = θdA…………….(ii)
Substituting (ii) in (i), we get
Here, C is called the thermal capacity of the machine in watts/oC and D is the heat dissipation constant in watts/oC.
When we acquire the first order differential equation of the equation –
We obtain the value of K by putting t = 0 in equation (iii) and get the solution as
From the above equation we find the rise in temperature inside a working machine, which is very near to being accurate and if we plot a graph for the variation of temperature risk with time during heating and cooling and thus the thermal model of the motor gets completed.
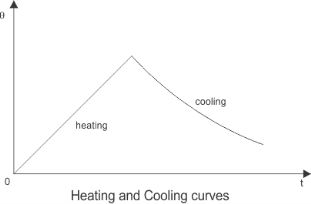
Figure 8. Heating and cooling curves.
In almost all applications electric motors are used, and to control them electrical drives are employed. But the operating time for all motors are not the same. Some of the motors runs all the time, and some of the motor’s run time is shorter than the rest period.
Depending on this, concept of motor duty class is introduced and based on this duty cycles the motor can be divided in eight categories such as
Continuous duty
Short time duty
Intermittent periodic duty
Intermittent periodic duty with starting
Intermittent periodic duty with starting and braking
Continuous duty with intermittent periodic loading
Continuous duty with starting and braking
Continuous duty with periodic speed changes
Continuous Duty
This duty denotes that motor is running long enough AND the electric motor temperature reaches the steady state value. These motors are used in paper mill drives, compressors, conveyers etc.
Figure 9. Continuous Duty.
Short Time Duty
In these motors, the time of operation is extremely low, and the heating time is much lower than the cooling time. So, the motor cooks off to ambient temperature before operating again. These motors are used in crane drives, drives for house- hold appliances, valve drives etc.
Figure 10. Short time duty.
Intermittent Periodic Duty
The motor operates for some time and then there is rest period. In both cases, the time is insufficient to raise the temperature to steady state value or cool it off to ambient temperature. This is seen at press and drilling machine drives.
Figure 11. Intermittent Periodic Duty
Intermittent Period Duty with Starting
In this type of duty, there is a period of starting, which cannot be ignored and there is a heat loss at that time. After that there is running period and rest period which are not adequate to attain the steady state temperatures. This motor duty class is widely used in metal cutting and drilling tool drives, mine hoist etc.
Figure 12.Intermittent Periodic Duty
Intermittent Periodic Duty with Starting and Braking
In this type of drives, heat loss during starting and braking cannot be ignored. So, the corresponding periods are starting period, operating period, braking period and resting period, but all the periods are too short to attain the respective steady state temperatures, these techniques are used in billet mill drive, manipulator drive, mine hoist etc.
Figure 13. Intermittent Periodic Duty with Starting and Braking
Continuous Duty with Intermittent Periodic Loading
In this type of motor duty, everything is same as the periodic duty but here a no load running period occurs instead of the rest period. Pressing, cutting are the examples of this system.
Continuous Duty with Starting and Braking
It is also a period of starting, running and braking and there is no resting period. The main drive of a blooming mill is an example.
Continuous Duty with Periodic Speed Changes
In this type of motor duty, there are different running periods at different loads and speeds. But there is no rest period and all the periods are too short to attain the steady state temperatures.
A motor enclosure not only holds the motors components together, it also protects the internal components frommoisture and contaminants. The degree of protection depends on the enclosure type. In addition, the type of enclosure affects the motor’s cooling.There are two categories of enclosures: open and totally enclosed.
Open Drip Proof (ODP) Enclosure
- Open enclosures permit cooling air to flow through the motor. One type of open enclosure is the open drip proof (ODP) enclosure. This enclosure has vents that allow for air flow. Fan blades attached to the rotor move air through the motor when the rotor is turning.
- The vents are positioned so that liquids and solids falling from above at angles up to 15° from vertical cannot enter the interior of the motor when the motor is mounted on a horizontal surface.
- When the motor is mounted on a vertical surface, such as a wall or panel, a special cover may be needed. ODP enclosures should be used in environments free from contaminates.
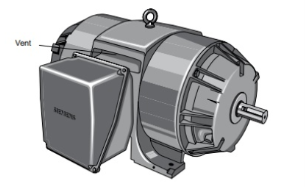
Figure 14. Open Drip Proof Enclosure.
Totally Enclosed Non-Ventilated (TENV) Enclosure
In some applications, the air surrounding the motor contains corrosive or harmful elements which can damage the internal parts of a motor. A totally enclosed non-ventilated (TENV) motor enclosure limits the flow of air into the motor but is not airtight. However, a seal at the point where the shaft passes through the housing prevents water, dust, and other foreign matter from entering the motor along the shaft.
Most TENV motors are fractional horsepower. However, integral horsepower TENV motors are used for special applications. The absence of ventilating openings means that all the heat from inside the motor must dissipate through the enclosure by conduction. These larger horsepower TENV motors have an enclosure that is heavily ribbed to help dissipate heat more quickly.TENV motors can be used indoors or outdoors.
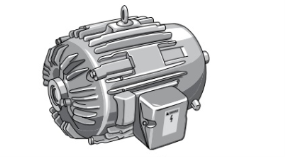
Figure 15. TENV Enclosure
Totally Enclosed Fan Cooled (TEFC) Enclosure
A totally enclosed fan cooled (TEFC) motor is similar to a TENV motor, but has an external fan mounted opposite the
drive end of the motor.The fan blows air over the motor’s exterior for additional cooling. The fan is covered by a shroud to prevent anyone from touching it.TEFC motors can be used in dirty, moist, or mildly corrosive environments.
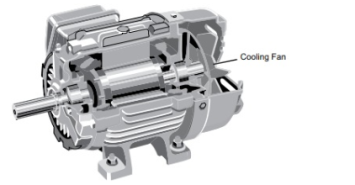
Figure 16. TEFC enclosure
Explosion Proof (XP)
Hazardous duty applications are commonly found in chemical processing, mining, foundry, pulp and paper,waste management, and petrochemical industries. In these applications, motors must comply with the strictestsafety standards for the protection of life, machines and the environment. This often requires use of explosion proof (XP) motors.
Reference Books
[R1] B. K. Bose, “Modern Power Electronics and AC Drives”, Pearson Education
[R2] Malcolm Barnes, “Practical Variable Speed Drives and Power Electronics”, Elsevier
Newnes Publications
[R3] V. Subrahmanyam, “Electric Drives: Concepts and Application”, Tata Mc-Graw Hill
(An imprint of Elsevier)
[R4] M.D. Singh and Khanchandani “Power Electronics”, Tata Mc-Graw Hill
[R5] Austin Huges, “Electrical motor and drives: Fundamental, types and applications”,
Heinemann Newnes, London
[R6] Tyagi MATLAB for engineers oxford (Indian Edition)