Unit 6
Industrial application
Specific requirement and choice of drives for following applications
Choice of Electrical Drives depends on several factors. Some of the important factors are:
- Steady state operation requirements: Nature of speed torque characteristics, speed regulation, speed range, efficiency, duty cycle, quadrants of operation, speed fluctuations and ratings.
- Transient operation requirements: Values of acceleration and deceleration, starting, braking and reversing performance.
- Requirements related to the source: Type of source, and its capacity, magnitude of voltage, voltage fluctuations, power factor, harmonics and their effect on other loads, ability to accept regenerated power.
- Capital and running cost, maintenance needs, life.
- Space and weight restrictions if any.
- Environment and location.
- Reliability.
Machine tool, any stationary power-driven machine that is used to shape or form parts made of metal or other materials. The shaping is accomplished in four general ways:
(1) by cutting excess material in the form of chips from the part.
(2) by shearing the material.
(3) by squeezing metallic parts to the desired shape; and
(4) by applying electricity, ultrasound, or corrosive chemicals to the material.
Machine tools that form parts by removing metal chips from a workpiece include lathes, shapers and planers, drilling machines, milling machines, grinders, and power saws.
The cold forming of metal parts, such as cooking utensils, automobile bodies, and similar items, is done on punch presses, while the hot forming of white-hot blanks into appropriately shaped dies is done on forging presses.
- A textile mill is a manufacturing facility where different types of fibres such as yarn or fabric are produced and processed into usable products. This could be apparel, sheets, towels, textile bags, and many more.
- Textile mills employ a multi-step process for taking raw materials and turning them into usable products.
- A typical production cycle looks something like this:
1. Fibres, whether natural or synthetic, are arranged in various way to create a desired texture, appearance, strength or durability.
2. Fibres are spun into yarn.
3. Yarn is transformed through fabric production techniques such as weaving or knitting.
4. Pre-treatment processes are carried out on the fabrics to prepare them to accept dyes and necessary chemicals.
5. Dyeing and printing using pigments and prints is performed on the textiles.
6. Finishing treatments are added to the fabric to create special technical properties or a desired aesthetic appeal. This might include antibacterial properties, water resistance, or fashion applications.
7. Textiles are given needed additional properties such as buttons or zippers before being finalized for sale and distribution.
The rolling process is the most common industrial process, used for making large length cross section like sheets and plates of steel and aluminum for structures. Rolling mills are used for completing the rolling process.
These are available with various steel roll manufacturers in a variety of shapes and sizes as per requirement of the process. The number of the rolling mill depends on the demand of the process.
Roll forming is a process in which a sheet of metal usually steel is passed through regular rolls until the required cross-section profile is achieved. The sheet is plastically deformed along a linear axis on room temperature environment. The process is used for creating parts with more length, and useful in manufacturing of large quantities of a shape.
Every roll in the process has a specific function in the making of the piece. At every stage, there are minor changes in the configuration of the metal. The size of the roll depends on the metal type, thickness, and formability. Hence, a roll forming process utilizes the following material.
Sugar mills in the past have burned bagasse, the fibrous by-product of the processing of sugarcane, using special boilers to produce the steam needed to break down the sugar cane.
As the cost of powering this equipment by burning fossil fuels has steadily risen, the use of biofuel cogeneration as a source of power production has become more prevalent. Many sugar mills have updated their bagasse-fired boilers and linked them to generators that produce electricity used to power the mill’s operations and to be sold to the local power grid.
Optimizing combustion efficiency and achieving cleaner burning throughout the process will generate more electricity and steam, and reduce harmful emissions. These results can be achieved if the equipment used in the cogeneration process is frequently tested using a portable emissions analyzer.
Combustion Efficiency & Safety
Measuring the levels of O2 (oxygen), CO (carbon monoxide), and CxHy (hydrocarbons) being emitted from bagasse-fired boilers will inform the mill’s operators if their equipment is burning the biomass cleanly and efficiently. Achieving higher efficiency will allow them to be minimizing the amount of auxiliary fossil fuel being used to help power the system.
Environmental Emissions
Monitoring the CO2, SO2, and NOx emissions from the system is necessary to ensure compliance with current environmental regulations and to minimize environmental and health hazards. Emissions measurements should also be taken before and after the flue gas cleaning system to ensure the efficient elimination of any corrosive components present in the system.
The locomotion in which the driving force is obtained from electric motor is called electric traction drive.
Traction motor refers to an electric motor providing primary rotational torque of a machine for conversion to linear motion.
There are various system of electric traction existing such as electric train, trolley buses, diesel electric vehicles and gas turbine electric vehicles.
Traction drive:
- High starting tractive effort in order to have fast acceleration.
- The wear on the trach is minimum
- Equipment capable of withstanding large temporary overloads for short periods
- Speed control should be easy.
- Pollution free
- Low initial and maintenance cost.
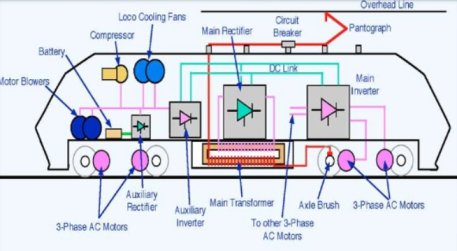
Figure 1. Locomotive.
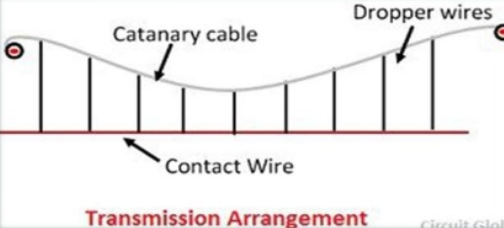
Figure 2. Transmission arrangement.
This is overhead wire of special cross section which is used to maintain good contact between current collector and contact wire.
The Requirements of the Cranes and Hoist Drives are
- The motion of the crane hook is in all three dimensions.
- In crane drives, the acceleration and retardation must be uniform. This is more important than the speed control.
- For exact positioning of the load creep speeds must be possible.
- When the motion is in the horizontal direction braking is not a problem. This is a problem if the load overhauls the motor in vertical motion. In the case of vertical motion the movement of the empty cage has to be carefully The speed must be constant while lowering the loads. The steady braking of the motor against cnierhauling must be possible.
- The drive must have high speeds in both the directions. The motor must have high speeds at light loads.
- Mechanical braking must be available under emergency conditions.
- Power lowering may be used when an empty cage or light hooks are
The duty cycle of cranes depends upon some requirements. These are:
- It must be able to perform strenuous duty
- It must withstand high ambient temperature
- It must be able to work in a dusty atmosphere
- It must provide trouble free operation
- It should have rigid safety measures.
DC Systems for Cranes and Hoist Drives
Among the dc motors, series motors are extremely suitable for crane operation. They have the following features:
- They have exceptionally good starting torque, high torque capability at low speeds and light torques at high speeds.
- Power demand under highly loaded conditions decreases due to, fall in
- Electrical braking is possible even at low speeds due to low critical speeds.
- Light conditions are not possible. Suitable changes may be made in the circuitry to make it to run at low speeds and light load conditions.
- The lowering speeds increase with the load. Regenerative braking is not possible to limit this speed. The speed of the empty cage can be limited by limiting the current to full load value.
However, the speed-torque characteristics of dc series motors may be modified to suit all the phases of crane control and are depicted in Fig. 7.6.
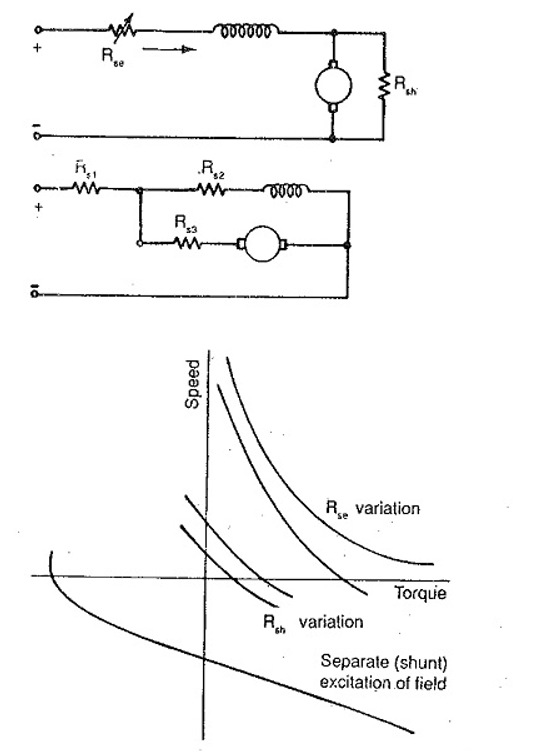
Figure 3. Connection of series motor
AC Systems for Cranes
Among ac motors, squirrel cage motors are normally used. They have the following features:
- No speed control is required. However with the development of variable frequency converters which solve the problems of speed control of induction motor, inverter fed motors are used in situations requiring wide range of speed control.
- They have fast acceleration and a fixed sequence of operation.
- Regenerative braking is not a problem. This occurs automatically when the load overhauls or the empty cage is being raised.
- The Motor is simple and robust
These are not suitable when a large number of starlings and brakings are required. A starting torque up to 250% of full load torque may be obtained. In cases of very high starting torque these are not suitable. Non-uniform sequence of operation cannot be handled and conventional methods of speed control are not suitable if precise speed control is necessary.
Slip ring induction motors for cranes and hoists have the following features:
1. The speed-torque curve can be modified by suitably altering the rotor resistance. The starting torque can also be varied to the required value.
Regeneration is possible. Reverse current braking can be employed limiting the current to the desired value by rotor resistance. DC dynamic braking may also be employed. While selecting a motor for crane duty the following points require consideration:
1. Breakdown torque must be greater than 250% (in the range of 275-300)
2. The inertia must be small.
3. It must withstand large frequency of starts.
4. The motor must have sufficient running torque, starting torque and ther-mal capability for the given duty cycle.
5. The duty cycle must be specified.
The solar energy can be converted into useful electrical energy using photovoltaic technology. The attractive feature of PV technology is that the installed power can be increased by adding panels. Among the applications is the pumping system. In PV pump storage system, the solar energy is stored when sunlight is available as potential energy in water reservoir and consumed according to demand. The main disadvantage is that they suffer from maintenance problems due to the presence of commutator and brushes. Hence pumping system based on induction motor provides a reliable and maintenance free operations with less cost. The operation of induction motor is based on converter-inverter system fed to induction motor. But these converter systems are limited to low power hence push-pull converters are used to produce high power throughout. The induction motor are Ac motors and hence from converter an inverter is required to obtain AC voltage. This inverter is chosen based on its advantages and fed to induction motor.
The vehicles that get powered through a self-controlled battery for converting fuel into electricity, such type of vehicles is called battery powered vehicles or electrical vehicles. The lead acid battery is mostly used for powering the vehicles because of their low cost. The various types of DC and induction motors are used in battery powered vehicles.
Advantages:
It causes less pollution.
It reduces noise pollution.
The battery powered vehicles required less maintenance because it has no water-cooling system to maintain, no filters, belts, or hoses to replace, or no oil to change.
It is more reliable because of the presence of fuel injectors, compressors, pumps and valve.
Reference Books
[R1] B. K. Bose, “Modern Power Electronics and AC Drives”, Pearson Education
[R2] Malcolm Barnes, “Practical Variable Speed Drives and Power Electronics”, Elsevier
Newnes Publications
[R3] V. Subrahmanyam, “Electric Drives: Concepts and Application”, Tata Mc-Graw Hill
(An imprint of Elsevier)
[R4] M.D. Singh and Khanchandani “Power Electronics”, Tata Mc-Graw Hill
[R5] Austin Huges, “Electrical motor and drives: Fundamental, types and applications”,
Heinemann Newnes, London
[R6] Tyagi MATLAB for engineers oxford (Indian Edition)