Unit IV
Measurement of Energy
The meter which is used for measuring the energy utilizes by the electric load is known as the energy meter. The energy is the total power consumed and utilized by the load at a particular interval of time. It is used in domestic and industrial AC circuit for measuring the power consumption. The meter is less expensive and accurate.
Construction
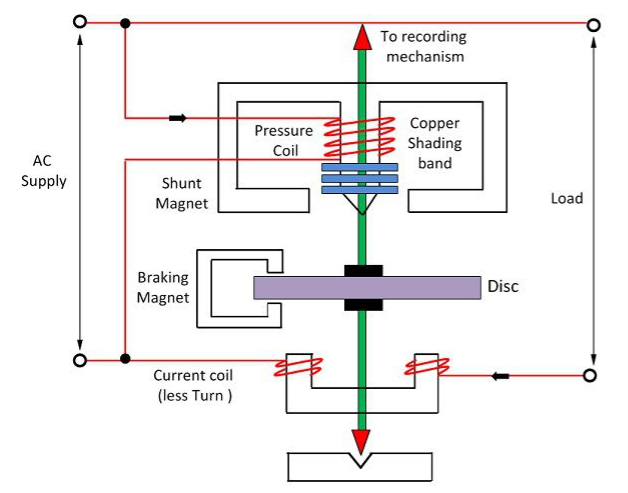
The energy meter has four parts;
Driving System: The electromagnet is the main component of the driving system. It is the temporary magnet which is excited by the current flow through their coil. The core of the electromagnet is made up of silicon steel lamination. The driving system has two electromagnets. The upper one is called the shunt electromagnet, and the lower one is called series electromagnet. The series electromagnet is excited by the load current flow through the current coil. The coil of the shunt electromagnet is directly connected with the supply and hence carries the current proportional to the shunt voltage. This coil is called the pressure coil. The centre limb of the magnet has the copper band. These bands are adjustable. The main function of the copper band is to align the flux produced by the shunt magnet in such a way that it is exactly perpendicular to the supplied voltage.
Moving System: The moving system is the aluminum disc mounted on the shaft of the alloy. The disc is placed in the air gap of the two electromagnets. The eddy current is induced in the disc because of the change of the magnetic field. This eddy current is cut by the magnetic flux. The interaction of the flux and the disc induces the deflecting torque. When the devices consume power, the aluminum disc starts rotating, and after some number of rotations, the disc displays the unit used by the load. The number of rotations of the disc is counted at particular interval of time. The disc measured the power consumption in kilowatt hours.
Braking System: The permanent magnet is used for reducing the rotation of the aluminum disc. The aluminum disc induces the eddy current because of their rotation. The eddy current cut the magnetic flux of the permanent magnet and hence produces the braking torque. This braking torque opposes the movement of the disc, thus reduces their speed. The permanent magnet is adjustable due to which the braking torque is also adjusted by shifting the magnet to the other radial position.
Registration (Counting): The main function of the registration or counting mechanism is to record the number of rotations of the aluminium disc. Their rotation is directly proportional to the energy consumed by the loads in the kilowatt hour. The rotation of the disc is transmitted to the pointers of the different dial for recording the different readings. The reading in kWh is obtained by multiply the number of rotations of the disc with the meter constant. The figure of the dial is shown below.
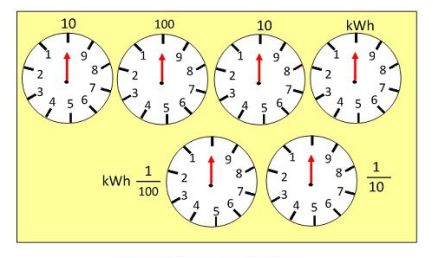
Working of Energy Meter
The energy meter has the aluminum disc whose rotation determines the power consumption of the load. The disc is placed between the air gap of the series and shunt electromagnet. The shunt magnet has the pressure coil, and the series magnet has the current coil. The pressure coil creates the magnetic field because of the supply voltage, and the current coil produces it because of the current.
The field induces by the voltage coil is lagging by 90º on the magnetic field of the current coil because of which eddy current induced in the disc. The interaction of the eddy current and the magnetic field causes torque, which exerts a force on the disc. Thus, the disc starts rotating.
The force on the disc is proportional to the current and voltage of the coil. The permanent magnet controls their rotation. The permanent magnet opposes the movement of the disc and equalizes it on the power consumption. The cyclometer counts the rotation of the disc.
The pressure coil has the number of turns which makes it more inductive. The reluctance path of their magnetic circuit is very less because of the small length air gap. The current Ip flows through the pressure coil because of the supply voltage, and it lags by 90º.
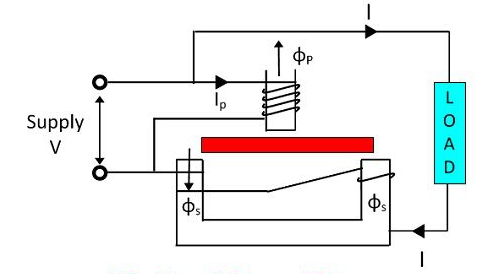
The Ip produces the two Φp which is again divided into Φp1 and Φp2. The major portion of the flux Φp1 passes through the side gap because of low reluctance. The flux Φp2 goes through the disc and induces the driving torque which rotates the aluminium disc.
The flux Φp is proportional to the applied voltage, and it is lagged by an angle of 90º. The flux is alternating and hence induces an eddy current Iep in the disc.
The load current passes through the current coil induces the flux Φs. This flux causes the eddy current Ies on the disc. The eddy current Ies interacts with the flux Φp, and the eddy current Iep interacts with Φs to produce the another torque. These torques are opposite in direction, and the net torque is the difference between these two.
The phasor diagram of the energy meter is shown in the figure below.
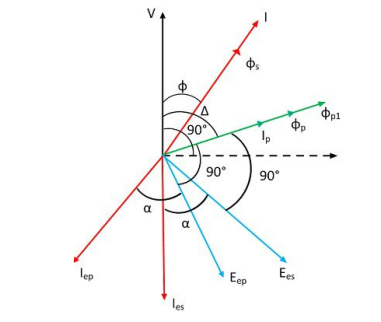
Let
V – applied voltage
I – load current
∅ – the phase angle of load current
Ip – pressure angle of load
Δ – the phase angle between supply voltage and pressure coil flux
f – frequency
Z – impedance of eddy current
∝ – the phase angle of eddy current paths
Eep – eddy current induced by flux
Iep – eddy current due to flux
Eev – eddy current due to flux
Ies – eddy current due to flux
The net driving torque of the disc is expressed as
Where,
K1 = Constant
= phase angle between fluxes
= phase angle between
= (
)
Driving Torque,

As we know
Therefore,

If f, Z and are constants then,

If N is steady speed, braking torque,
At steady state, the speed of the driving torque is equal to braking torqueIf
Speed; The speed of rotation is directly proportional to the power
Total number of revolution =
If
Total number of revolutions =
The meter which is used for measuring the power of three phase supply is known as the three phase energy meter. The three phase meter is constructed by connecting the two single phase meter through the shaft. The total energy is the sum of the reading of both the elements.
Working Principle
The torque of both the elements is added mechanically, and the total rotation of the shaft is proportional to the three phase energy consumption.
Construction
The three phase energy meter has two discs mounted on the common shaft. Both the disc has its braking magnet, copper ring, shading band and the compensator for getting the correct reading. The two elements are used for measuring the three phase power. The construction of the three phase meter is shown in the figure below.
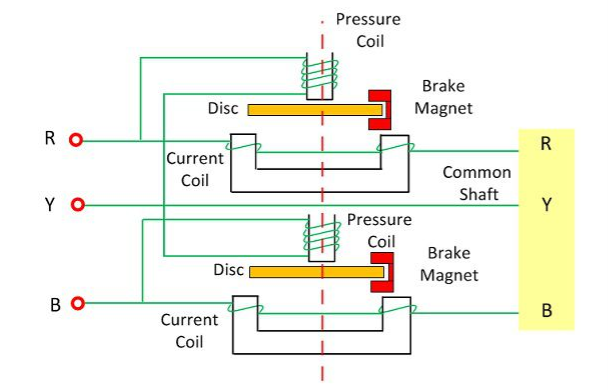
For three phase meter, the driving torque of both the elements is equal. This can be done by adjusting the torque. The torque is adjusted by connecting the current coils of both the elements in the series and their potential coils in parallel. The full load current is passed through the coil due to which the two opposite torque is set up in the coil.
The strength of both the torques are equal, and hence they do not allow the disc to rotate. If the torque becomes unequal and the disc rotates then the magnetic shunt is adjusted. The balance torque is obtained before testing the meter. The position of the compensator and the braking magnet are separately adjusted to each of the element for obtaining the balance torque.
Time of Day metering (ToD), also known as Time of Usage (ToU), metering involves dividing the day into tariff slots with higher rates at peak load periods and low tariff rates at off-peak load periods. While this can be used to automatically control usage on the part of the customer (resulting in automatic load control), it is often simply the customer’s responsibility to control his own usage, or pay accordingly (voluntary load control). This also allows the utilities to plan their transmission infrastructure appropriately.TOD metering normally splits rates into an arrangement of multiple segments including on-peak, off-peak, mid-peak and critical peak. A typical arrangement is a peak occurring during the day, such as from 5 pm to 11 pm. By Implementing the Automated Meter Data Acquisition System coupled with GIS the utility will not only be able to find out the accurate Technical Losses occurring from Feeder to DT to HT but also find out the reason of such losses. Their can be losses due to sub standard asset quality, pilferage or any other reason but the same can be pin pointed with the MDAS application Accountability and Transparency in the system will increase as exact ownership of the Loss can be identified. In case of dealing with any fault we would be able to pinpoint the exact location where there is a fault and contact the relevant teams who would repair the same By using the Network Analysis tool the Utility would be able to find out which feeders or transformers are being over used and which are underutilized. This would be useful to them for Capacity Planning and Enhancement purposes as they would know where exactly there is excess capacity which can be diverted and wherever there is a need for Capacity Enhancement There would be minimal human interference in the entire metering process thereby reducing chances of mischief. All this would definitely lead to Increased Customer Satisfaction. Moreover, even the customer would be able to use many services online such as New Connection or Disconnection Request, Fault Logging and tracking, Bill Payments etc.
References
1) R.K. Rajput -“Electrical Measurements and Measuring Instruments” – S. Chand Limited, 2009
2) J.B. Gupta - “ Electrical Measurements and Measuring Instruments ” – S.K. Kataria & Sons
3) E.W. Golding - “ Electrical Measurements and Measuring Instruments ”