Unit 6
Three Phase Induction Motor
The transfer of energy from stator to rotor of an induction motor is entirely inductive, with help of mutual flux between them. Hence, induction motor is essentially a transformer with stator forming the primary and rotor forming the secondary. The vector is shown below
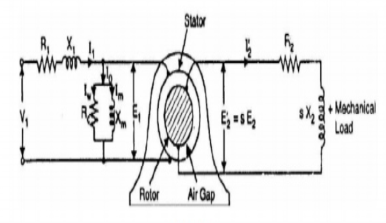
Fig. 1: Induction motor
V1 is the applied voltage/stator phase, R1 and X1 are stator resistance and leakage reactance/phase. The applied voltage V1 produces a magnetic flux which links the primary and secondary producing self-induced emf E1 in primary and mutually induced emf in secondary Er (=sE2). The whole emf Er is used to circulate the rotor current so no secondary terminal voltage V2.
V1= E1+ I1R1+jI1X1
Er=I2Z2=I2(R2+jsX2)
Key takeaway
From vector diagram:
i) I0 is the no load primary current. It has two components Iw and I.
Ii) Iw supplies no-load motor losses. The component I sets up magnetic flux in core and air gap.

Iii) In vector diagram is equivalent load current in primary and is equal to KI2. Total primary current is vector sum of
and
.
Iv) R0=E1/ Iw and X0=E1/ I
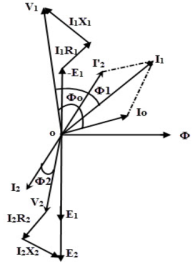
Fig. 2: Phasor Diagram
The case is quite similar to that of transformer. Here also the secondary values can be transferred to the primary and vice versa. The equivalent circuits are shown below
Fig. 3: Equivalent circuit of induction motor referred to primary
,
,
=KI2,
=
(1-s/s)
Whenever we shift impedance or resistance from secondary to primary, we divide it by K2. The approximate equivalent circuit is shown below.
R01=R1+
X02=X1+
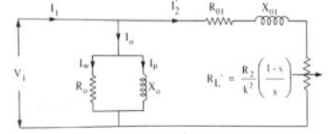
Fig. 4: Approximate circuit of induction motor
Key takeaway
When referred from primary
R01=R1+
X02=X1+
No-load test: The no load test is carried out with different values of applied voltage, below and above the value of normal voltage range. The input power is measured by two wattmeters. I0 by ammeter and V by voltmeter. As motor is running on light load, p.f is low. The total power input will be the difference of reading of W1 and W2.
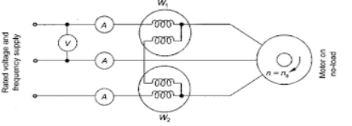
Fig. 5: No load test
The total power input W0 =VLI0cosφ0
Cosφ0=
Where VL= Line voltage.
W0= no load stator input.
Stator winding loss = 3Io2R1
I0 = No load input current
R1 = Resistance of the motor
Core loss = 3GoV2
Blocked Rotor Test:
A blocked rotor test is normally performed on an induction motor to find out the leakage impedance. In the blocked rotor test, the applied voltage on the stator terminals should be low otherwise normal voltage could damage the winding of the stator. In block rotor test, the low voltage is applied so that the rotor does not rotate and its speed becomes zero and full load current passes through the stator winding.
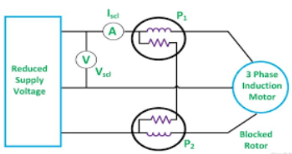
Fig. 6: Blocked rotor test
The slip is unity related to zero speed of rotor hence the load resistance becomes zero. Now, when the voltage is increased slowly in the stator winding so that current reaches to its rated value. At this point, take readings of the voltmeter, wattmeter and ammeter to know the values of voltage, power and current. The test can be repeated at different stator voltages for the accurate value.
Resistance and Leakage Reactance Values
The copper loss is given Wcu.
Therefore,
Where, Wc = core loss
Wcu=3I2R01
Where, R01 = Motor winding of stator and rotor as per phase referred to stator.
R01=
Thus,
Let
Is = short circuit current
Vs = short circuit voltage
Z0 = short circuit impedance as referred to stator
Z01==
Therefore,
X01 = Motor leakage reactance per phase referred to stator will be
X01=
Stator reactance X1 and rotor reactance per phase referred to stator X2 are normally equal.
Hence,
X1=X2=
Similarly, stator resistance per phase R1 and rotor resistance per phase referred to stator R2 can be calculated as follows:
First some suitable tests are done on stator windings to find the value of R1 and then to find R2 subtract the R1 from R01
R2=R01-R1
Short Circuit Current for Normal Supply Voltage
To calculate short circuit current Isc at normal voltage V of the stator, we must note short-circuit current Is and low voltage Vs applied to the stator winding.

Key takeaway
No-load test
W0 =VLI0cosφ0
Core loss = 3GoV2
Blocked Rotor Test:
Z01==
X1=X2=
X01=
Que: A 110V, 3-phase star connected induction motor takes 25A at a line voltage of 30V with rotor locked. With this line voltage power input to motor is 400W and core loss is 30 W. The dc resistance between the pair of stator terminals is 0.1 ohm. If ratio of ac to dc resistance is 1.6. Find equivalent leakage reactance per phase and stator and rotor resistance per phase?
Sol: S.C voltage/phase= 30/=17.3V
Is=25A/phase
Z01=17.3/25=0.7ohm/phase
Stator and cu loss=400-30=370W
3 x 252xR01=370
R01=0.197ohm
Leakage reactance/phase X01==
=0.67ohm
Dc resistance/phase stator=0.1/2=0.05ohm
Ac resistance/phase R1=0.05x1.6=0.08ohm
Effective resistance/phase rotor referred to stator =0.197-0.08=0.117ohm
Que) In a no load test an induction motor took 8A and 440W with a line voltage of 110V. If the stator resistance/phase is 0.05ohm and frictional and windage losses are 135W. Calculate the exciting conductance and susceptance/phase?
Sol: Stator cu loss=3R1=3x82x0.05=9.6W
Stator core loss=440-135-9.6=295.4W
Voltage/phase v=110/V
Core loss=3G0V2
295.4=3 G0(110/)2
G0=0.024siemens/phase
Y0=I0/V = (8///110=0.042siemens/phase
B0==0.034siemens/phase
6.5.1 Plotting of circle diagrams
For drawing circle diagram, we need to find the per phase values of no load current I0, short circuit current ISC and the corresponding phase angles Ф0 and ФSC. We also find short circuit current ISN corresponding to normal supply voltage. These all values are found through No load test and blocked rotor test on the induction motor with this data, the circle diagram can be drawn as follows
1.First of all we consider a suitable scale and then we draw vector OA with length corresponding to I0 at an angle Ф0 from the vertical axis. Then we draw a horizontal line AB.
2.Then we draw OS equal to ISN at an angle ФSC and join AS.
3. Then we draw perpendicular bisector to AS to meet the horizontal line AB at C.
4.With C as centre, we draw a portion of circle passing through A and S. This forms the circle diagram which is the locus of the input current.
5. From point S, draw a vertical line SL to meet the line AB.
6.Then divide SL at point K so that SK: KL = rotor resistance: stator resistance.
7. For a given operating point P, draw a vertical line PEFGD as shown. Then PE = output power, EF = rotor copper loss, FG = stator copper loss, GD = constant loss (iron loss + mechanical loss)
8.To find the operating points corresponding to maximum power and maximum torque, we need to draw tangents to the circle diagram parallel to the output line and torque line respectively. The points at which these tangents touch the circle are respectively the maximum power point and maximum torque point.
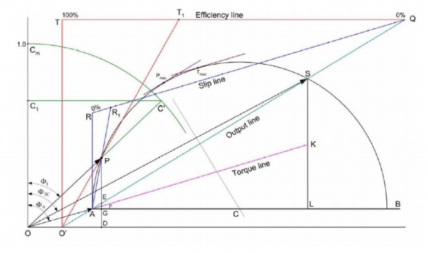
Fig. 7: Construction of circle diagram
The efficiency line can be drawn through following steps
1.The output line AS is extended backwards to meet the X-axis at O′.
2.From any convenient point on the extended output line, we draw a horizontal line QT so as to meet the vertical from O′. Then the line QT into 100 equal parts.
3.To find the efficiency corresponding to any operating point P, draw a line from O′ to the efficiency line through P to meet the efficiency line at T1. Now QT1 is the efficiency.
The Slip Line can be constructed by following steps:
1.Draw line QR parallel to the torque line, meeting the vertical through A at R. Divide RQ into 100 equal parts.
2.To find the slip corresponding to any operating point P, we need draw a line from A to the slip line through P to meet the slip line at R1. Now RR1 is the slip
6.5.2 Computation of Performance Characteristics from Equivalent Circuit and Circle Diagram
The performance characteristics of IM depends on the efficiency, power factor, starting torque, maximum torque.
i) Speed Torque characteristics:
There is no direct relation in the speed and torque. At, full load the motor runs at a speed N. When mechanical load increases motor speed decreases till the motor torque again becomes equal to the load torque. As long as two torques are equal the motor runs at constant speed. When the supply frequency increases the speed increases and reduces the maximum torque of motor. So,
i) F increases, N increases, Tmax decreases.
Ii) V increases, Tmax increases.
Fig. 8(a): Speed Torque Characteristics
If the above two features are combined, we see that speed increases and torque kept same. If frequency is increased up to certain level and keeping voltage constant the motor speed increases and torque decreases. But when supply frequency is kept same and voltage is increased, then the motor characteristics in this case are stretched and the value of Tmax increases.
Ii) Effect of Rotor resistance on Speed Torque characteristics
It is conventional method, performed by adding a variable rheostat in series with the motor winding. It has many drawbacks which are listed in this section. The torque equation for 3 phase induction motor is
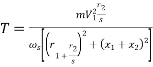
Normally r2/s>>r1, x1 so,

From above equation slip is directly proportional to rotor resistance. Hence speed decreases. This method is applicable to wound rotor induction motor.
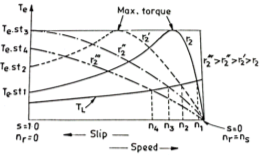
Fig. 8(b): Torque speed characteristics
At the normal operating condition, the slip increases with increasing torque so there is curve is linear. For a fixed load curve, the speed is downward from n1 to n4. From this figure we can also obtain the maximum torque at the starting of the resistance r2”. So, this method has an advantage of achieving maximum torque at the starting period.
But the maximum torque is independent of the rotor resistance as per the equation,
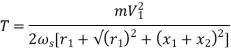
Iii) Operating point stable and unstable region
The system consisting of motor and load will operate where two characteristics meet. So, we need to find theses operating points. The characteristics are never the same they change with time. TO calculate this, we consider a small band in the curve where the actual points of the characteristics lie. The difference of the torque at the two points if positive will accelerate the machine. If for some reason the developed torque is smaller than speed would drop and the effect becomes cumulative. Hence, this point will be the unstable point. At stable point there will not be any runaway effect seen.
Key takeaway
The Power Factor Curve is drawn as follows:
1.Draw a quadrant of a circle with O as centre and any convenient radius. Divide OCm into 100 equal parts.
2.To find power factor corresponding to P, we just need to extend the line OP to meet the power factor curve at C′. Draw a horizontal line C′C1 to meet the vertical axis at C1. Now OC1 represents power factor.
This is discussed in detail in section 6.5. Kindly refer.
A starter is needed for a three-phase induction motor because at the time of starting, if induction motor is started directly, it will draw a huge amount of current which can cause damage to adjoining equipment. A starter is required in an induction motor for following reasons:
In a 3-phase induction motor, the magnitude of an induced emf in the rotor circuit depends on the slip of the induction motor. Thus, induced emf effectively decides the magnitude of the rotor current. The rotor current in the running condition is given by:
I2r = s E’2 / (R22 + sX22)
- At starting time, the speed of the motor is zero and slip is at its maximum i.e. unity. So, magnitude of rotor induced emf is very large at start. As rotor conductors are short-circuited, the large induced emf circulates very high current through rotor at start.
- The condition is exact similar to a transformer with short-circuited secondary. Such a transformer when excited by a rated voltage, circulates a very high current through short-circuited secondary. As secondary current is large the Primary current also draws very large current from the supply line.
- Similarly, in a 3-phase induction motor, when rotor current is high, the stator draws a very high current from the supply line. Due to this increase in line current the Voltage starts rising resulting in collapse of the system.
Key takeaway
A starter is needed for a three-phase induction motor because at the time of starting, if induction motor is started directly, it will draw a huge amount of current which can cause damage to adjoining equipment
Starting of slip-ring induction motor
Below shown is a 3-phase slip ring induction motor with a starter. Full supply voltage is connected across the starter. As starting resistances are connected the supply current to the stator reduces. The rotor begins to rotate and the rotor resistance decreases as the speed of motor gradually increases. When motor is running at its full speed, the starting resistances are cut out and slip rings are short circuited.

Fig. 9: Slip-ring induction motor
Cage Rotor Induction Motor
The starting current in induction motor is proportional to the input voltage per phase (Vs) to the motor (stator) I1 α Es, if the stator impedance is neglected then Vs= Es. This has been shown earlier. So, in a (squirrel) cage induction motor, the starter is used only to decrease the input voltage, so that the input current cab be decreased.
There are three methods for starting of cage induction motor
6.8.1 Direct On Line starter (Full voltage starting method)
In this induction motor is directly connected to the 3-phase supply. The DOL starter applies full line voltage to the motor terminals.
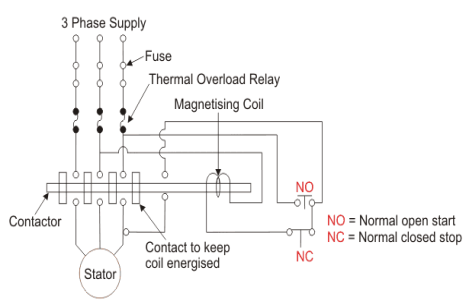
Fig. 10: D.O.L Starter
If the high input current does not cause any excess voltage drop in circuit than only this starter can be used. The value of armature current in motor is given as
Ia=
The expression for starting torque is given as
Ts starting torque
Tf Full load torque
If per phase rotor current at full load
Is per phase rotor current at starting
sf full load slip
ss starting slip
R2 rotor resistance
Ws synchronous speed of motor
In induction motor torque is given as
T=
The ratio of starting torque to full load torque is given as
x sf
The wiring diagram for a DOL starter is shown above. The working principle of a DOL starter begins with the connection to the 3-phase main with the motor. The control circuit is connected to any two phases and energized from them only. When we press the start button, the current flows through magnetizing coil and control circuit also.
The current energises the contactor coil and leads to close the contacts, and hence 3-phase supply becomes available to the motor. When we stop it, the current discontinues. As the supply to motor breaks the machine stops. The contactor coil (Magnetizing Coil) gets supply even though we release start button because when we release start button, it will get supply from the primary contacts as illustrated in the diagram of the Direct Online Starter.
Key takeaway
- Simple and most economical starter.
- More comfortable to design, operate and control.
- Provides nearly full starting torque at starting.
- Easy to understand and troubleshoot.
- DOL starter connects the supply to the delta winding of the motor.
The reduced voltage starting methods are:
6.8.2 Star delta starter
The set up for star delta starter is shown below
Fig. 11: Star delta starter
The starter phases are connected to star by TPDT (triple pole double throw switch). Initially the TPDT switch is at position 1 and when motor attains steady state switch is thrown to position 2. In position 1 terminals are short circuited and at position 2 a, b and c are connected to B, C and A. The expression for starting torque is given as
Ts starting torque
Tf Full load torque
If per phase rotor current at full load
Is per phase rotor current at starting
sf full load slip
ss starting slip
R2 rotor resistance
Ws synchronous speed of motor
In induction motor torque is given as
T=
The ratio of starting torque to full load torque is given as
x sf
Let V1 line voltage
Iss per phase starting current
Iss=
Starting current in stator when connected in delta position
Isd=
Isd= Iss
Then the torque ratio equation will be
x sf
Key takeaway
This shows that the reduced voltage method has an advantage of reducing the starting current but the disadvantage is that all these methods of reduced voltage causes the objectionable reduction in the starting torque.
6.8.3 Auto Transformer Starter
The Auto transformer is used in both the type of the connections, i.e., either star connected or delta connected. The auto transformer is used to limit the starting current of the induction motor. The auto transformer used is a step down, so it reduces the voltage V1 to xV1. This leads to reduction in current from I1 to xI1. After the motor reaches to its normal operating speed, the auto transformer is disconnected and then full line voltage is applied. The starting torque in terms of full load will be
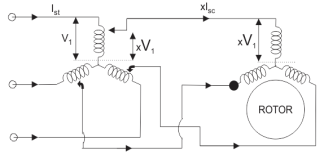
Fig. 12: Starting of Auto transformer
In induction motor torque is given as
T=
The ratio of starting torque to full load torque is given as
x sf
Let rotor resistance be constant for this case. As step down transformer is used, the voltage and current decreases as mentioned above. So, the ratio of torque equation changes as
x sf
x sf x
2
This shows the variation of the starting torque with the value of k.
Que) Find the percentage tapping required on an autotransformer required for a squirrel cage motor to start the motor against 1/5 of full load torque. The SC current on normal voltage is 4 times the full load current and the full load slip 3%?
Sol: =
=4
sf=0.03
k2
)2sf
1/5=k2x4x4x0.03
K=0.645=64.5%
Que) A full load slip of 440V, 3 phase cage induction motor is 3.5% and with locked rotor, full load current is circulated when 80volt is applied between lines. Find necessary tapping on an autotransformer to limit the starting current to twice the full load current of the motor. Determine starting torque in terms of full load torque?
Sol: Isc = (440/80)If=5.5If
Supply line current Ist=2If
Ist=k2Isc
K=60.3%
k2
)2sf=0.385
Tst=38.5% of full load torque
6.8.4 Stator Resistance Starting Method
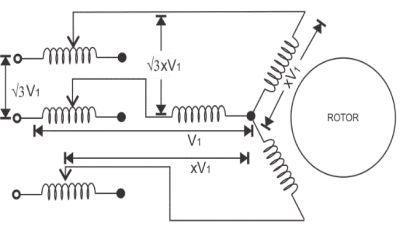
Fig. 13: Stator resistance starting
Here as see from above figure resistor or reactor is added in each phase. Thus, by adding resistor we can control the supply voltage. Only a fraction of the voltage (x) of the supply voltage is applied at the time of starting of the induction motor. The value of x is always less than one. Due to the drop in the voltage the starting torque also decreases. We will derive the expression for the starting torque in terms of the voltage fraction x in order to show the variation of the starting torque with the value of x. As the motor speeds up the reactor or resistor is cut out from the circuit and finally the resistors are short circuited when the motor reaches to its operating speed. Now let us derive the expression for starting torque in terms of full load torque for the stator resistor starting method:
In induction motor torque is given as
T=
The ratio of starting torque to full load torque is given as
x sf
x sf
x sf x
2
Now there are some considerations regarding this method.
Key takeaway
If we add series resistor then the energy losses are increased so it’s better to use series reactor in place of resistor because it is more effective in reducing the voltage however series reactor is more costly than the series resistance.
6.6.5 Star Delta Starter and Rotor Resistance Starter
Star delta starter is discussed in section 6.6.2
Rotor resistance starter
It is conventional method, performed by adding a variable rheostat in series with the motor winding. It has many drawbacks which are listed in this section. The torque equation for 3 phase induction motor is
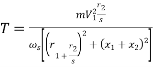
Normally r2/s>>r1, x1 so,

From above equation slip is directly proportional to rotor resistance. Hence speed decreases. This method is applicable to wound rotor induction motor.
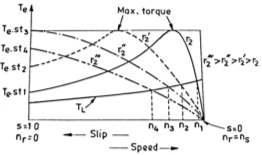
Fig. 14: Torque speed characteristics
At the normal operating condition, the slip increases with increasing torque so there is curve is linear. For a fixed load curve, the speed is downward from n1 to n4. From this figure we can also obtain the maximum torque at the starting of the resistance r2”. So, this method has an advantage of achieving maximum torque at the starting period.
But the maximum torque is independent of the rotor resistance as per the equation,
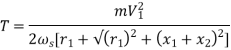
It has some drawbacks
- The rheostat used to vary the resistance per phase causes unbalancing in rotor.
- The resistances generate huge losses and generate heat in the system.
- In case of a large machine the size of the rheostat will be large and, in such cases, it is not easily portable.
- It requires more maintenance, hence the cost associated with it is more.
Key takeaway
This method cannot be used for industrial automation purpose since we have to change manually the value of the resistance.
Que) Determine approximately the starting torque of an induction motor in terms of full load torque when started by means of a star delta switch. The SC current of the motor at normal is 6 times the full load current and the full load slip is 4%.
Sol: x sf = (1/3) x 62 x 0.04=0.48
Tst=0.48Tf
Que) The full load efficiency and power factor of a 12kW, 400V, 3-phase induction motor is 85% and 0.8lag respectively. The blocked rotor line current is 40A at 220V. Calculate the ratio of starting to full load current, if the motor is provided with a star-delta starter.
Sol: Blocked rotor current with full voltage applied
Isc=40x400/220=72.73A
x400xIfx0.8=12000/0.85
If=25.47A
In star delta starter
Ist=Isc/72.73/
=41.99A
Ist/If=41.99/25.47=1.65
6.8.6 D.O.L. Starter and Soft Starting with Torque and Current Relations
For DOL starter refer section 6.6.1
Soft starting: A soft starter is a device that is included in the motor circuit in order to reduce the load and torque in the power train. A soft starter slowly increases the voltage in motor. This helps in smooth acceleration of power, instead of sudden rise in power, which can even damage the machine. This is achieved by limiting the value of torque in the motor. This in turn allows the soft starter to reduce the voltage and allows it to gradually stop reducing the voltage to allow for a smooth progression of current. Some soft starters use solid state devices.
Key takeaway
Advantages of soft starter: They reduce the risk of overheating, improve the operating efficiency. There is low risk of power surge. They also reduce energy use.
Starter type | Percentage line voltage | Starting current | Starting Torque | ||
|
| DOL current | Full load current | DOL torque | Full load torque |
DOL | 100% | Both are equal | Is=6I | Ts=Tdol | Tg=6T |
Auto transformer Starter | 80% or 60% | Ig=(0.8)2Idol Ig=(0.6)2Idol | Is=3.84I Is=2.16I | Tg=(0.8)2Tdol Tg=(0.6)2Tdol | Tg=1.28T Tg=0.72T |
Star delta starter | 57.7% | Ig=(1/ ![]() | Is=2I | Ts(1/ ![]() | Tg=2/3T |
Resistance starter | 64% | Ig=(0.64)2Idol | Is=2.5I | Tg=(0.45)2Tdol | Tg=0.35T |
References
[1] Edward Hughes “Electrical Technology”, ELBS, Pearson Education.
[2] Ashfaq Husain, “Electrical Machines”, Dhanpat Rai& Sons.
[3] S. K. Bhattacharya, “Electrical Machine”, Tata McGraw Hill publishing Co. Ltd, 2nd Edition.
[4] Nagrath & Kothari, “Electrical Machines”, Tata McGraw Hill.
[5] Bhag S Guru, Husein R. Hiziroglu, “Electrical Machines”, Oxford University Press.
[6] K Krishna Reddy, “Electrical Machines- I and II”, SCITECH Publications (India) Pvt. Ltd. Chennai.