Unit 3
Transducers
LVDT is an acronym for Linear Variable Differential Transformer.
- It is a common type of electromechanical transducer that can convert the rectilinear motion of an object to which it is coupled mechanically into a corresponding electrical signal.
- LVDT linear position sensors are readily available that can measure movements as small as a few millionths of an inch up to several inches, but are also capable of measuring positions up to ±30 inches (±0.762 meter). Figure shows the components of a typical LVDT.
- The transformer's internal structure consists of a primary winding centered between a pair of identically wound secondary windings, symmetrically spaced about the primary.
- The coils are wound on a one-piece hollow form of thermally stable glass reinforced polymer, encapsulated against moisture, wrapped in a high permeability magnetic shield, and then secured in a cylindrical stainless steel housing.
- This coil assembly is usually the stationary element of the position sensor.
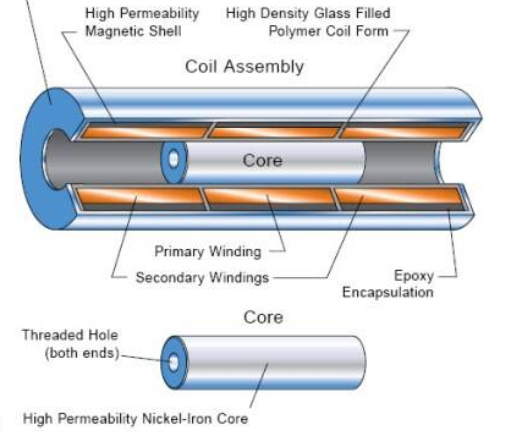
Figure illustrates what happens when the LVDT's core is in different axial positions.
The LVDT's primary winding, P, is energized by a constant amplitude AC source.
The magnetic flux thus developed is coupled by the core to the adjacent secondary windings, S1 and S2.
If the core is located midway between S1 and S2, equal flux is coupled to each secondary so the voltages, E1 and E2, induced in windings S1 and S2 respectively, are equal.
At this reference midway core position, known as the null point, the differential voltage output, (E1 - E2), is essentially zero.
As shown in Figure , if the core is moved closer to S1 than to S2, more flux is coupled to S1 and less to S2, so the induced voltage E1 is increased while E2 is decreased, resulting in the differential voltage (E1 - E2).
Conversely, if the core is moved closer to S2, more flux is coupled to S2 and less to S1, so E2 is increased as E1 is decreased, resulting in the differential voltage (E2 - E1).
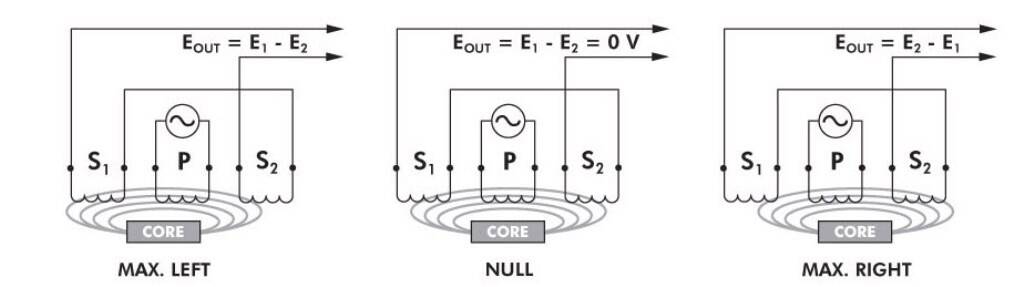
Figure Illustrates what happens when the LVDT's core is in different axial positions.
Figure shows how the magnitude of the differential output voltage, EOUT, varies with core position.
The value of EOUT at maximum core displacement from null depends upon the amplitude of the primary excitation voltage and the sensitivity factor of the particular LVDT, but is typically several volts RMS.
The phase angle of this AC output voltage, EOUT, referenced to the primary excitation voltage, stays constant until the center of the core passes the null point, where the phase angle changes abruptly by 180 degrees, as shown graphically in Figure b. This 180 degree phase shift can be used to determine the direction of the core from the null point by means of appropriate circuitry.
This is shown in Figure C, where the polarity of the output signal represents the core's positional relationship to the null point. The figure shows also that the output of an LVDT is very linear over its specified range of core motion, but that the sensor can be used over an extended range with some reduction in output linearity.
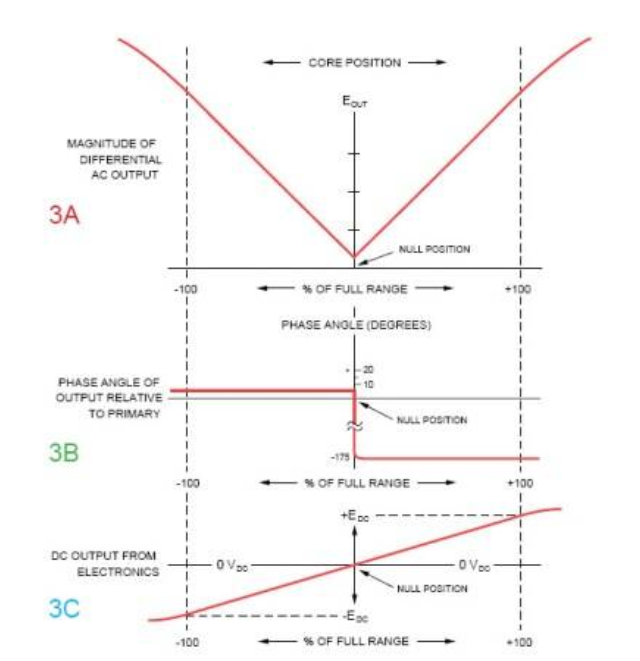
- An RTD is a temperature sensor which measures temperature using the principle that the resistance of a metal changes with temperature. In practice, an electrical current is transmitted through a piece of metal (the RTD element or resistor) located in proximity to the area where temperature is to be measured.
- The resistance value of the RTD element is then measured by an instrument. This resistance value is then correlated to temperature based upon the known resistance characteristics of the RTD element.
RTDs work on a basic correlation between metals and temperature. As the temperature of a metal increases, the metal's resistance to the flow of electricity increases. - Similarly, as the temperature of the RTD resistance element increases, the electrical resistance, measured in ohms (Ω), increases. RTD elements are commonly specified according to their resistance in ohms at zero degrees Celsius (0C).
The most common RTD specification is 100 Ω, which means that at 0C the RTD element should demonstrate 100 Ω of resistance.
Platinum is the most commonly used metal for RTD elements due to a number of factors, including its
(1) Chemical inertness
(2) Linear temperature versus resistance relationship
(3) Temperature coefficient of resistance that is large enough to give readily measurable resistance changes with temperature and
(4) Stability
Other metals that are less frequently used as the resistor elements in an RTD include nickel, copper and Balco.
RTD elements are typically in one of three configurations:
(1) a platinum or metal glass slurry film deposited or screened onto a small flat ceramic substrate known as "thin film" RTD elements, and
(2) platinum or metal wire wound on a glass or ceramic bobbin and sealed with a coating of molten glass known as "wire wound" RTD elements.
(3) A partially supported wound element which is a small coil of wire inserted into a hole in a ceramic insulator and attached along one side of that hole. Of the three RTD elements, the thin film is most rugged and has become increasingly more accurate over time.
- A Strain gauge (sometimes refered to as a Strain gage) is a sensor whose resistance varies with applied force; It converts force, pressure, tension, weight, etc., into a change in electrical resistance which can then be measured.
- When external forces are applied to a stationary object, stress and strain are the result. Stress is defined as the object's internal resisting forces, and strain is defined as the displacement and deformation that occur.
The strain gauge is one of the most important sensor of the electrical measurement technique applied to the measurement of mechanical quantities. - As their name indicates, they are used for the measurement of strain. As a technical term "strain" consists of tensile and compressive strain, distinguished by a positive or negative sign. Thus, strain gauges can be used to pick up expansion as well as contraction.
Shaft encoders are optical devices that provide two logical outputs called A and B. Conceptually, the shaft is attached to two discs. Each disc has alternating transparent and opaque segments, 256 in all. There is a light source on one side of the disc and a light detector on the other side.
When a transparent segment of the disc lies between the source and detector the corresponding output is 1, and when an opaque sector lies between the source and detector the corresponding output is 0. Thus the output alternates between 1 and 0 as the shaft is turned.
The sectors of the two discs are not lined up. Instead, one is shifted by half a segment angle with respect to the other. Because of the relationship between the two discs, the output signals are shifted with respect to one another:
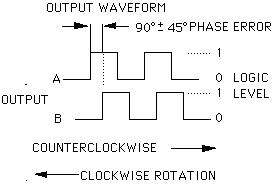
Assume that the shaft is positioned so that the signals are those at the midpoint of this diagram, where both A and B are 0.
If the shaft is turned counter-clockwise from this position, first A and then B will become 1.
If the shaft were turned clockwise from the midpoint of the diagram then B would become 1 before A did. This means that by observing the order of the changes, a program can determine which way the shaft is turning. The sequence of values is known as a Gray code. By counting the changes, the program can determine how far the shaft has been turned.
The sequence of 2-bit values maybe accessed by reading a byte from location $700001. The bits of interest are in bits 0 and 1. Also, the byte, and the 2-bit values are in negative logic. A "00" value is represented by a 1111 1111, while a "11" value is read as 1111 1100.
A single shaft can be used to control any number of quantities by providing some mechanism for mode switching'': telling the computer that from this point forward, motions of the shaft have a different effect.
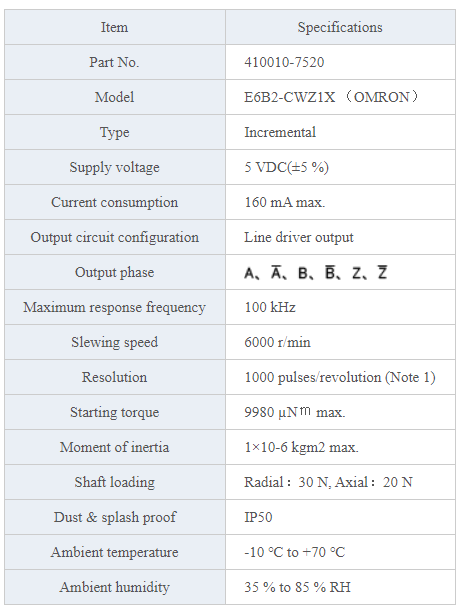
Range :
The range encoder is an entropy coder similar to the arithmetic coder or huffman coder. Compared to an arithmetic coder the files are minimally larger (less than 0.01% in most cases) but the operation speed is nearly twice as fast.
Limitations:
The biggest limitations of encoders are that they can be fairly complex and contain some delicate parts. This makes them less tolerant of mechanical abuse and restricts their allowable temperature. One would be hard pressed to find an optical encoder that will survive beyond 120ºC.
Appliances:
A digital thermometer is used to verify a smart temperature transmitter under flowing conditions and a successful calibration of the smart temperature transmitter. Portable electronic thermometers (PETs) are designed to measure temperature in a RTD-type thermowell using a thermistor or RTD probe. The thermometer should be approved for use in hazardous locations, Class 1, Groups C and D. The thermometer should be furnished with suitably coated probe cables at least 6 inches long. The digital display should be easily read in direct sunlight and equipped with a backlight (optional) for night operations. The display shall have a resolution to at least XX. XX°F.
A simple digital thermometer is a combination of a thermocouple, a battery-powered, dual-slope digital voltmeter to measure the thermocouple output, and an electronic display. This provides a low noise, digital output that can resolve temperature differences as small as 0.1°C. The accuracy achieved is dependent on the accuracy of the thermocouple element, but reduction of measurement inaccuracy to ±0.5% is achievable.
A weighing scale (or weighing balance) is a device to measure weight or mass. These are also known as mass scales, weight scales, mass balance, weight balance, or simply scale, balance, or balance scale.
The traditional scale consists of two plates or bowls suspended at equal distances from a fulcrum. One plate holds an object of unknown mass (or weight), while known masses are added to the other plate until static equilibrium is achieved and the plates level off, which happens when the masses on the two plates are equal.
A spring scale will make use of a spring of known stiffness to determine mass (or weight). Suspending a certain mass will extend the spring by a certain amount depending on the spring's stiffness (or spring constant).
The heavier the object, the more the spring stretches, as described in Hooke's law. Other types of scale making use of different physical principles also exist.
Some scales can be calibrated to read in units of force (weight) such as newtons instead of units of mass such as kilograms. Scales and balances are widely used in commerce, as many products are sold and packaged by mass.
Washing machine is the machine used to wash the various types of clothes without applying any physical efforts. With washing machine you don’t have to rub the clothes with hand or squeeze them to remove the water from them. The washing machine is also called as clothes washer or simply the washer. The washing machine enables you to wash your clothes automatically without having to supervise its operation. All you have to do is put the clothes in the machine and select the wash mode. The washing machine automatically takes in the amount of water and detergent required and it also automatically sets the timer for washing, rinsing and drying as per the selected mode and the amount of clothes.
Microwave oven, also called electronic oven, appliance that cooks food by means of high-frequency electromagnetic waves called microwaves. A microwave oven is a relatively small, boxlike oven that raises the temperature of food by subjecting it to a high-frequency electromagnetic field The microwaves are absorbed by water, fats, sugars, and certain other molecules, whose consequent vibrations produce heat. The heating thus occurs inside the food, without warming the surrounding air; this greatly reduces cooking - time, and baking and other cooking tasks that require hours in a conventional oven can be completed in minutes in a microwave oven. Microwave ovens generate radiation at a frequency of about 2,450 megahertz by means of a magnetron, which is a kind of electron tube.
Tachometer
Tachometer, device for indicating the angular (rotary) speed of a rotating shaft. The term is usually restricted to mechanical or electrical instruments that indicate instantaneous values of speed in revolutions per minute, rather than devices that count the number of revolutions in a measured time interval and indicate only average values for the interval.
References:
- Basic Electrical Engineering” by C L Wadhwa.
- “ Basic Electrical Engineering” by Mehta V K and Mehta Rohit.
- “ Basic Electrical Engineering” by Nagrath, I and Kothari.