UNIT 1
Engineering Properties and use Materials
Requirements of good building stone
The following are the requirements of good building stones:
(i) Strength:
- The stone should be able to resist the load coming on it. Ordinarilly this is not of primary concern since all stones are having good strength.
- However in case of large structure, it may be necessary to check the strength.
(ii) Durability:
- Stones selected should be capable of resisting adverse effects of natural forces like wind, rain and heat.
(iii) Hardness:
- The stone used in floors and pavements should be able to resist abrasive forces caused by movement of men and materials over them.
(iv) Toughness:
- Building stones should be tough enough to sustain stresses developed due to vibrations.
- The vibrations may be due to the machinery mounted over them or due to the loads moving over them. The stone aggregates used in the road constructions should be tough.
(v) Specific Gravity:
- Heavier variety of stones should be used for the construction of dams,retaining walls,docks and harbours.
- The specific gravity of good building stone is between 2.4 and 2.8.
(vi) Porosity and Absorption:
- Building stone should not be porous. If it is porous rain waterenters into the pour and reacts with stone and crumbles it.
- In higher altitudes, the freezing of water inpores takes place and it results into the disintegration of the stone.
(vii) Dressing:
- Giving required shape to the stone is called dressing. It should be easy to dress so that the cost of dressing is reduced.
- However the care should be taken so that, this is not be at the cost of the required strength and the durability.
(viii) Appearance:
- In case of the stones to be used for face works, where appearance is a primary requirement, its color and ability to receive polish is an important factor.
(ix) Seasoning:
- Good stones should be free from the quarry sap. Laterite stones should not beused for 6 to 12 months after quarrying.
- They are allowed to get rid of quarry sap by the action of nature. This process of removing quarry sap is called seasoning.
(x) Cost:
- Cost is an important consideration in selecting a building material. Proximity of the quarry to building site brings down the cost of transportation and hence the cost of stones comes down.
- However it may be noted that not a single stone can satisfy all the requirements of a good building stones, since one requirement may contradict another.
- For example, strength and durability requirement contradicts ease of dressing requirement. Hence it is necessary that site engineer looks intothe properties required for the intended work and selects the stone.
USES OF BUILDING STONES-
- Sandstone is a popular stone with sculptors.
- Good and durable construction material.
- Thresholds and steps in manor houses.
- War memorials in the 19th and 20th centuries.
- Limestone for burning lime and also for manufacture of cement.
- Limestone as a flux in blast furnaces.
- Insulators in electrical appliances.
- Broken stones and chips are used for foundation, roofs, and floors of the building and as road metal and railway ballast.
- Stones blocks are mainly used in walls, foundation, and ornamental facial work.
- Quartzite is used for rubble masonry, road metalling and also as aggregate for concrete.
- Limestone slabs are used for flooring, paving, and roofing.
- Slates are used as roofing and flooring material.
- Granite is used for important works like bridge abutments, pipers etc.
- Marble is extremely suitable for the ornamental and superior type of building work.
- Crushed stone is used as an alternative substitute for artificial sand.
Manufacturing-
Manufacturing of bricks consists of the following 4 operations or steps.
- Preparation of brick clay or brick earth
- Moulding of bricks
- Air drying of bricks
- Burning of bricks
(1) Preparation of brick Clay:
The clay for bricks is prepared in the following order:
(i) Un-soiling
(ii) Digging
(iii) Cleaning
(iv) Weathering
(v) Blending
(vi) Tempering
(i) Un-Soiling:
- The top layer of soil, about 200 mm in depth, is taken out and thrown away.
- The clay in top soil is full of impurities and hence it is to be rejected for the purpose of preparing bricks.
(ii) Digging:
- The clay is then dug out from the ground. It is spread on the levelled ground, just a little deeper than the general level of ground.
- The height of heaps of clay is about 600 mm to 1200 mm.
(iii) Cleaning:
- The clay, as obtained in the process of digging, should be cleaned of stones, pebbles, vegetable matter, etc.
- If these particles are in excess, the clay is to be washed and screened. Such a process naturally will prove to be troublesome and expensive.
- The lumps of clay should be converted into powder form in the earth crushing roller.
(iv) Weathering:
- The clay is then exposed to atmosphere for softening or mellowing. The period of exposure varies from few weeks to full season.
- For a large project, the clay is dug out just before the monsoon and it is allowed to weather throughout the monsoon.
(v) Blending:
- The clay is made loose and any ingredient to be added to it is spread out at its top. The blending indicates intimate or harmonious mixing.
- It is carried out by taking small portion of clay every time and by turning it up and down in vertical direction.
- The blending makes clay fit for the next stage of tempering.
(vi) Tempering:
- In the process of tempering, the clay is brought to a proper degree of hardness and it is made fit for the next operation of moulding.
- The water in required quantity is added to clay and the whole mass is kneaded or pressed under the feet of men or cattle.
- The tempering should be done exhaustively to obtain homogeneous mass of clay of uniform character.
- For manufacturing good bricks on a large scale, the tempering is usually done in a pug mill. A typical pug mill capable of tempering sufficient earth for a daily output of about 15000 to 20000 bricks is shown in fig. 4-1.
- The process of grinding clay with water and making it plastic is known as the pugging.
- A pug mill consists of a conical iron tub with cover at its top. It is fixed on a timber base which is made by fixing two wooden planks at right angles to each other.
- The bottom of tub is covered except for the hole to take out pugged earth. The diameter of pug mill at bottom is about 800 mm and that at top is about one meter.
- The provision is made in top cover to place clay inside the pug mill. A vertical shaft with horizontal arms is provided at the centre of iron tub. The small wedge-shaped knives of steel are fixed on horizontal arms.
- The long arms are fixed at the top of vertical shaft to attach a pair of bullocks. The ramp is provided to collect the pugged clay. The height of pug mill is about 2 m. Its depth below ground is about 600 mm to 800 mm to lessen the rise of the barrow run and to throw out the tempered clay conveniently.
- In the beginning, the hole for pugged clay is closed and clay with water is placed in pug mill from the top. When the vertical shaft is rotated or turned by a pair of bullocks, the clay is thoroughly mixed up by the actions of horizontal arms and knives and a homogeneous mass is formed.
- The rotation of vertical shaft can also be achieved by using steam, diesel or electric power. When clay has been sufficiently pugged, the hole at the bottom of tub is opened out and the pugged earth is taken out from ramp by barrow i.e., a small cart with two wheels for the next operation of moulding.
- The pug mill is then kept moving and feeding of clay from top and taking out of pugged clay from bottom are done simultaneously.
- If tempering is properly carried out, the good brick earth can then be rolled without breaking in small threads of 3 mm diameter.
(2) Moulding of bricks:
- Bricks are made in metric sizes called modular bricks, as prescribed by the Bureau of Indian Standards. Nominal size of the bricks is 20cm X 10cm X 10cm, which include the thickness of the mortar and the actual size of modular brick is 19cm X 9cm X 9cm.
- A brick mould is a rectangular box of steel or wood, which is open at the top and bottom of the box and inside dimensions of the mould are 20cm X 10cm X 10cm.
- Moulding of bricks can be done using either hand or machine.
Hand Moulding
- There are two types in hand moulding, i.e. ground moulding and table moulding. In this type, bricks are moulded manually and preferred where only a small quantity of bricks is needed.
Ground Moulding:
- The process of moulding bricks on the ground manually by labour is called ground moulding. On an average, a moulder can mould about 750 bricks per day.
- When the bricks have dried sufficiently, they are moved to the drying shed and placed in an orderly manner.
Table Moulding:
- This moulding is done on a table of size 2m X 1m X 0.7m instead of on the ground. This table moulding process is almost similar to ground moulding expect for some minor changes.
Machine Moulding
- Moulding machines are used when a large scale of bricks are to be manufactured in less time.
- These types of bricks are heavier and stronger than the hand moulded ones and possess a sharp regular shape, a smoother surface and sharp edges. There are two types in machine moulding
- Plastic Method:
- In this method, pugged earth is used, which is placed in the machine that contains a rectangular shape of size equal to the length and width of the brick.
- A beam of the moulded earth comes out of it and is cut into strips by wires fixed in the frames. These bricks are also called wire-cut bricks.
II. Dry Method:
- In this method, the machine first converts the hard earth into a powder form and a small quantity of water is added to the powder to make it a stiff plastic paste.
- This paste is placed in the mould and pressed by the machine to form hard and correct-shaped bricks.
- These bricks are known as pressed bricks, which do not require any drying and can be sent directly to the burning section.
(3) Air drying of bricks
- The damp bricks, if burnt, are likely to be cracked and distorted. Hence the moulded bricks are dried before they are taken for the next operation of burning.
- For drying, the bricks are laid longitudinally in stacks of width equal to two bricks. A stack consists of eight or ten tiers.
- The bricks are laid along and across the stock in alternate layers. All bricks are placed on edge. The bricks should be allowed to dry till they become leather hard or bone-dry with moisture content of about 2 per cent or so.
The important facts to be remembered in connection with the drying of bricks are as follows:
(i) Artificial Drying:
- The bricks are generally dried by natural process. But when bricks are to be rapidly dried on a large scale, the artificial drying may be adopted. In such a case, the moulded bricks are allowed to pass through special dryers which are in the form of tunnels or hot channels or floors.
- Such dryers are heated with the help of special furnaces or by hot flue gases. The tunnel dryers are more economical than hot floor dryers and they may be either periodic or continuous.
- In the former case, the bricks are filled, dried and emptied in rotation. In the latter case, the loading of bricks is done at one end and they are taken out at the other end.
- The temperature is usually less than 120°C and the process of drying of bricks takes about 1 to 3 days depending upon the temperature maintained in the dryer, quality of clay product, etc.
(ii) Circulation of Air:
- The bricks in stacks should be arranged in such a way that sufficient air space is left between them for free circulation of air.
(iii) Drying Yard:
- For the drying purpose, special drying yards should be prepared. It should be slightly on a higher level and it is desirable to cover it with sand.
- Such an arrangement would prevent the accumulation of rain water.
(iv) Period for Drying:
- The time required by moulded bricks to dry depends on prevailing weather conditions. Usually it takes about 3 to 10 days for bricks to become dry.
(v) Screens:
- It is to be seen that bricks are not directly exposed to the wind or sun for drying. Suitable screens, if necessary, may be provided to avoid such situations.
(4) Burning of bricks
- In the process of burning, the dried bricks are burned either in clamps (small scale) or kilns (large scale) up to certain degree temperature. In this stage, the bricks will gain hardness and strength so it is important stage in manufacturing of bricks.
- The temperature required for burning is about 1100oC. If they burnt beyond this limit they will be brittle and easy to break. If they burnt under this limit, they will not gain full strength and there is a chance to absorb moisture from the atmosphere.
- Hence burning should be done properly to meet the requirements of good brick.
TYPES OF BRICKS-
(1)Burnt Clay Bricks
- Burnt clay bricks are the oldest and most widely used construction material. These are superior quality bricks and are used in the construction of many vital structural members like walls, columns, foundation, etc.
- Burnt bricks are classified into 4 different types, these are:
(A) First-Class Bricks
- This category of burnt clay bricks complies with all the quality of good bricks. These are table molded and are burnt in kilns.
- These bricks hold standard shape, smooth surfaces, and sharp edges and are more durable and have more strength.
(B) Second-Class Bricks –
- These bricks are of moderate quality. These are ground-molded and then burnt in brick kilns. The shape of these bricks is irregular, and the surface isn’t smooth but rough.
- In addition to this, these bricks can have hair cracks. This class of bricks is used in places where the brickwork is covered with a coat of plaster.
(C) Third-Class Bricks –
- As the name suggests, these are poor quality bricks which are normally used for structures that are temporarily constructed. Note, these are not suitable for areas that receive a lot of rain.
- Third Class bricks are molded on the ground and are further burnt in clamps. The surface of this category of bricks are rough and these have edges that are unfair.
(D) Fourth-Class Bricks –
- These are over-burnt, irregular shaped and dark in colour. This class of bricks is used as the aggregate for concrete in foundations, roads, floors, etc.
- Owing to its compact structure, these bricks are sometimes found to be stronger than the first-class bricks.
(2) Fly Ash Bricks
- Fly ash brick is a building material that is specifically used in masonry units. It contains class C or class F fly ash (a byproduct of coal burning) and water that is fired at around 1,000 degree Celsius.
- Due to the high concentration of calcium oxide in class C fly ash, this type of bricks is every so often described as “self-cementing”.
- Typical uses for fly ash clay brick are in structural walls, pillars, and foundations.
(3)Cellular Light Weight Concrete Bricks
- Cellular Light Weight Concrete Bricks/ Blocks (CLC) is also called as Foam Concrete Blocks.
- Advantages:
- Light in Weight :
CLC blocks are very lightweight with density ranging from 300 to 1800 Kg/m3. Three times less weight then clay or fly ash brocks.
Ii. Eco friendly :
- CLC blocks are Environment-friendly. Foam concrete is eco- friendly material as fly ash and other industrial waste material are used in part of manufacturing blocks to protect the environment.
- The production process of CLC or its use does not release any harmful effluents to ground, water or air. CLC, due to its low weight is ideal for making partitions.
- The use of CLC for this purpose will reduce the need for plywood partitions. This consequently will result in reduction in deforestation and will benefit environment.
Iii. Sound Insulation :
- CLC Blocks are excellent for Sound insulation which keeps the house cool in Summer and warm in Winter saving energy/electricity for cooling and heating.
- It is possible to achieve even higher values depending upon the thickness of block.
Iv. Thermal Insulation :
- Thermal insulations as a 100mm thick CLC wall, the equivalent thickness of dense concrete wall would have to be more than 5 times thicker and ten times heavier.
v. Lower Water Absorption :
- The water absorption of this material is relatively lower than any other materials.
Properties Of Bricks-
1.It should have a rectangular shape, regular surface and red colored appearance.
2. It should confirm in size to the specified dimensions (19 x 9 x 9 cm).
3. It should be properly burnt. This can be ascertained by holding two bricks freely, one in each hand, and striking them.
4. A sharp metallic sound indicates good burning whereas a dull thud would indicate incomplete burning.
5. A good building brick should not absorb water more than 20 percent of its dry weight. Absorption should not exceed 25 percent in any case.
6. A good building brick should possess requisite compressive strength, which in no case should be less than 35 kg/cm2 .
7. A rough test for the strength of the brick is to let it fall freely from a height of about one meter on to a hard floor. It should not break.
8. Brick should be hard enough so that it is not scratched by a finger nail.
- Artificial wood
- Artificial wood may be any of a variety of man-made products used in the building industry.
- Sometimes referred to as composite or synthetic, artificial wood products are widely accepted as a durable alternative to natural wood.
- Inspired by contemporary innovation, artificial wood products may contain wood byproducts or consist entirely of plastic, vinyl or aluminum.
Artificial Wood Properties
- Artificial wood is insect resistant. It's virtually maintenance-free and can be washed off with a hose.
- Mold and mildew are not prone to inhabit artificial wood; if either does occur, it washes off with soap and water.
- Artificial wood products never need to be sanded, scraped, refinished or stained -- but stain is an option to change the color of composite wood.
- The maintenance-free, durable quality of artificial wood makes it a viable option to natural wood even though the initial investment for artificial wood is higher.
- Most artificial wood products are designed for exterior use, with built-in UV protection against fading.
Applications-
- Artificial wood is heavy; the density is part of the appeal. It's solid and resists splitting, cracking or warping. Synthetic or artificial wood cuts and mills using common woodworking tools.
- The uniform, consistent quality of artificial wood expedites projects. With standard lengths exceeding 16 feet, decks, fences and exterior projects go up faster.
- Natural boards exceeding 16 feet in length can be hard to find without variations such as warps, twists or knots. Drawbacks to artificial wood may include requirements for larger screws, brackets, fasteners and other hardware needed to support the extra weight.
- Artificial wood may appear industrial; it doesn't have the natural patterns, beauty and appeal of real wood.
Standard structural section-
- Angle sections
- Channel sections
- T- sections
- I-sections
- Round bars
- Square bars
- Flat bars
- Corrugated sheets
- Expanded metal
- Plates
- Ribbed bars (HYSD)
- Ribbed bars (mild steel)
- Thermo-mechanically treated bars
- Welded wire fabrics
1. Rolled Angle Sections
- Angle sections are manufactured in “L” shape. It contains two legs. Some angle sections contains legs with similar dimensions are called as equal angle sections and some contains different legs are called as unequal angle sections.
- Angle sections are widely used for roof truss constructions and for filler joist floors.
- Equal angle sections are available from 20 mm x 20 mm x 3 mm to 200 mm x 200mm x 25 mm with their corresponding weights as 9 N and 736 N per meter length respectively.
- Unequal angle sections are available from 30 mm x 20 mm x 3 mm to 200mm x 150mm x 18mm with 11 and 469 N per meter length weight respectively.
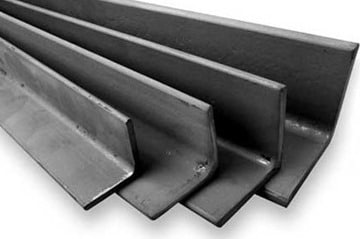
2. Rolled Channel Sections
- The channel section or C- section consists two equal flanges connected to web at both ends. Channel sections are extensively used in steel framed structures.
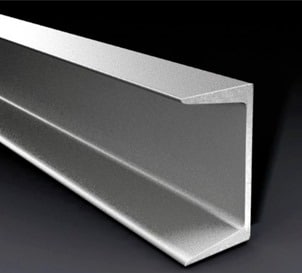
- They are available in various sizes ranging from 100 mm x 45 mm to 400mm x 100 mm. Corresponding unit weights are 58 N and 494 N per meter length respectively.
3. Rolled T- Sections
- T section consists of flange and web arranged in “T” shape. They are used in steel roof trusses to form built up sections.
- Two angle sections can also be joined to get T section.
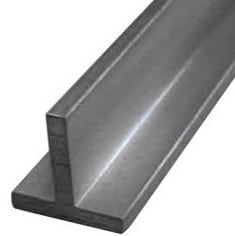
- Rolled T sections size varies from 20 mm x 20 mm x 3 mm to 150 mm x 150mm x 10 mm with 9 N and 228 N as their corresponding weights per meter length.
4. Rolled I – Sections
- I sections which are also called as steel beams or rolled steel joist are extensively used as beams, lintels, columns etc. It consists two flanges and a web connected as shown in figure.
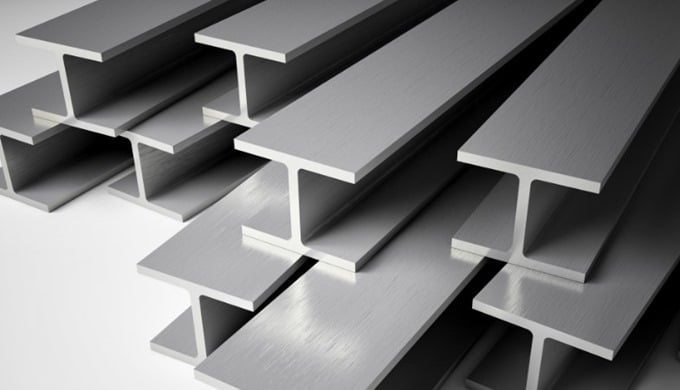
- These are available in various sizes ranges from 75 mm x 50 mm at 61 N per meter length to 600 mm x 210 mm at 995 N per meter length.
5. Rolled Round Bars
- Round bars contain circular cross sections and these are used as reinforcement in concrete and steel grill work etc.
- Round bars are available in various diameters varies from 5 mm to 250 mm.
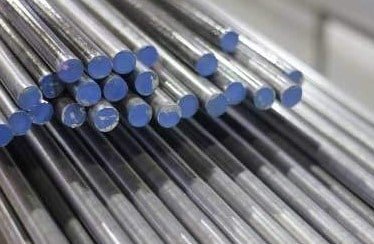
6. Rolled Square Bars
- Square bars contain square cross sections and these are widely used for gates, windows, grill works etc. the sides of square cross section ranges from 5 mm to 250 mm.
7. Rolled Flat Bars
- Flat bars are also used for gates, windows, grill works etc. Flat bars are designated with width of the bar which varies from 10 mm to 400 mm. Thickness of flat bars will be from 3 mm to 40 mm.
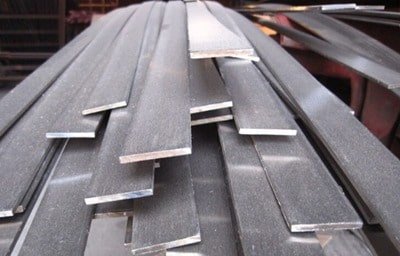
8. Corrugated Sheets
- Plain steel sheets are passed through machines which produce bends by pressing them called corrugations. These sheets are used for roof coverings.
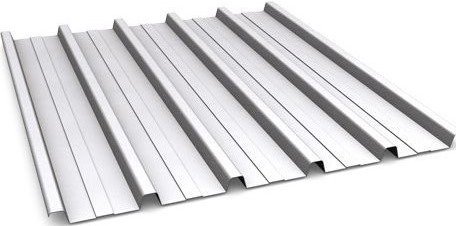
9. Expanded Metal
- Expanded metal sheets are made from mild steel sheets. Which are cut through machine and expanded. Generally, Diamond shaped mesh is appeared in this type of sheets.
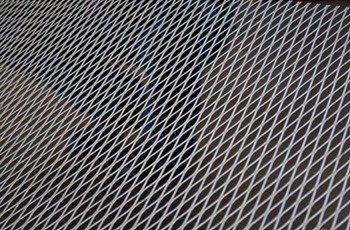
10. Rolled Steel Plates
- Steel plates are well used items in steel structures.
- They are used for connecting steel beams, tensional member in roof truss etc. They are designated with their thickness which is varying from 5 mm to 50 mm.
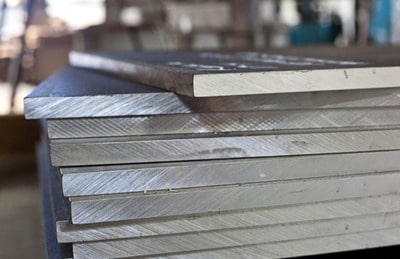
11. Ribbed Bars (HYSD)
- Ribbed HYSD bars are made of high yield strength steel.
- Ribs are nothing but projections produced on bars by cold twisting of bar in hot rolled condition. The twist is made according the standard requirements.
- HYSD bars are important innovation of steel and they are extensively used as main reinforcement materials in all concrete works like bridges, buildings, precast concrete works, foundations, roads etc..
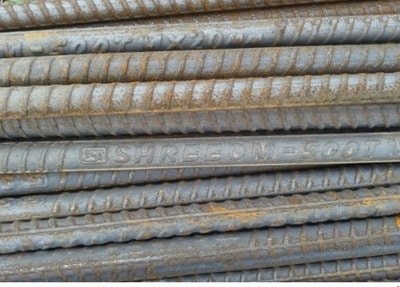
- They are available in many sizes varying from 6 mm to 50 mm diameter. The reason why these are more famous than any other bars is because of following advantages:
- HYSD bars can be bend up to 180o without any cracks.
- High strength and durable.
- 30 to 40% of cost reduced when compared to other round bars.
- Suitable for any type of concrete work.
- Excellent bonding properties with concrete.
- HYSD bars can be welded using electronic flash butt welding or arc welding.
12. Ribbed Bars (Mild Steel)
- Ribbed bars can also be produced from mild steel. These are look-alike HYSD ribbed bars but these bars are not recommended by any code and they also have very less strength compared to HYSD bars.
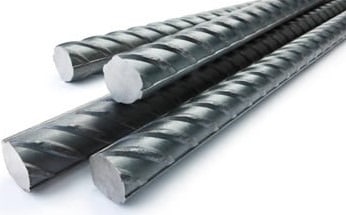
13. Rolled Thermo-Mechanically Treated (TMT) Bars
- Thermo-mechanically treated bars or TMT bars are manufactured by a special technique in which the red-hot steel bars are suddenly quenched by spraying water on it.
- So, surface of bar gets cooled down and inner side or core of the bar still in hot condition.
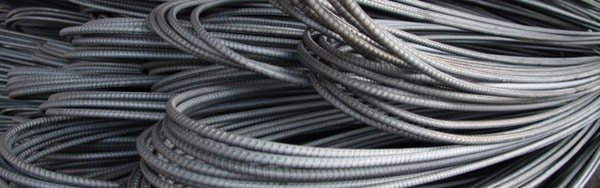
- The core helps the outer surface to be tempered. By this combination of different temperature, the bar gains more yield strength and exhibits good elongation at ultimate failure.
- Copper, phosphorus and chromium etc. are added in manufacturing process of TMT bars which improves its corrosion resistance.
14. Welded Wire Fabrics
- Welded wire fabrics are nothing but a series of mild steel bars which are arranged perpendicular to each other and welded at all intersection.
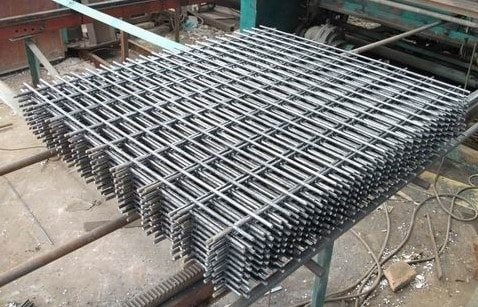
- These are used as reinforcement for floor slabs, small canal linings, pavement’s etc.
STEEL AS A REINFORCEMENT-
- Steel used as a reinforcement because, the two materials bond together very well with no slippage and thus act together as one unit in resisting the applied loads, apart from few other important properties of steel. The tensile strength of steel is approximately equal to 100 – 140 times the tensile strength of plain concrete mix.
- We can reinforce steel as-
- Weld stiffener plates to the bottom of the beam. By adding mass to the bottom of the beam, deflection is minimized and carrying capacity is increased.
- The plates can be any size, but the most efficient reinforcement occurs when the plates are the same width as the beam, and run the entire length of the beam.
- Generally there are two types of steel bars ("Sariya" in hindi) available in the market. Mild steel bars are used for tensile stress of RCC (Reinforced cement concrete) slab beams etc. in reinforced cement concrete work. These steel bars are plain in surface and are round sections of diameter from 6 to 50 mm.
- Ceramic Tiles-
Ceramic tiles are used for-
- Ceramic tiles is one of the key components used in the construction industry for building interior and exterior floors, footpaths, swimming pools, walls, partitions, and roofs.
- Ceramic tiles are highly durable. They offer protection from abrasion and stains and they require less maintenance.
Disadvantages-
- Because ceramic tile is hard and brittle, it is prone to cracking and chipping from impacts.
- Replacing a damaged tile without doing harm to adjacent tiles is a difficult undertaking.
- On countertops, the grout between tiles can become dirty and discolored. Grout is hard to clean.
- Vitrified tiles-
- Vitrified tiles are made by fusing 60% silica and 40% clay. They are also a type of ceramic tile made by warming the blend or setting it under high temperatures.
- They gain a glass-like texture in the process. Longevity, low porosity, scratch resistance, and low maintenance are some characteristics of vitrified tiles.
Major differences between ceramic tiles and vitrified tiles:
- As mentioned before, the composition varies. Ceramics are made using earthen clay while vitrified tiles contain a mixture of silica and clay.
- Ceramic tiles have a coarser texture than vitrified tiles, which are known for their glossy look. However, ceramic tiles have a more natural and earthy look than vitrified tiles, whose glassy appearance gives an artificial touch.
- The process of vitrification makes vitrified tiles stronger than ceramic tiles. Since they are composed of a mixture of various materials like silica, quartz, and feldspar along with clay, baking at high temperatures fuses them together to make them more durable and resistant.
- Due to their low porosity, vitrified tiles absorb very little water when compared to ceramic tiles. This makes vitrified tiles a good choice for flooring.
- Vitrified tiles are more scratch and stain resistant than ceramic tiles.
- Ceramic tiles are easier to install.
- Ultimately, due to the obvious advantages of vitrified tiles, they cost more than ceramic tiles.
NATURAL STONE –
- The term "natural stone" refers to a variety of mountain-born mineral substances that stand in contrast to any synthetic or manufactured stone products.
- Common natural stone flooring includes slate, marble, limestone, travertine, granite, and sandstone—each of which has slightly different properties. Marble, limestone, travertine, granite, and sandstone—each of which has slightly different properties.
BEST OPTIONS OF NATURAL STONES-
- Marble.-
As the king of natural-stone flooring, marble is the best choice for homeowners who want to make a classic and elegant statement.
2. Granite
3. Sandstone
4. Flagstone
5. Limestone
- Paving Blocks–
- Block paving also known as brick paving is a commonly used decorative method of creating a pavement or hard standing.
- This allows for remedial work to be carried out under the surface of the paving without leaving a lasting mark once the paving bricks have been replaced.
Paving materials
- Porcelain. A contemporary material that requires little maintenance.
- Natural granite. Celebrated for its strength, granite is incredibly resilient making it a great option for heavy traffic areas.
- Natural limestone. Make a real statement with your paving thanks to limestone.
- Natural slate.
- Natural sandstone.
(1) Aluminium-
- Aluminum is widely used in building because of its intrinsic properties of lightness and corrosion resistance.
- Aluminum is used in external facades, roofs and walls, in windows and doors, in staircases, railings, shelves, and other several applications.
- There are many benefits that aluminum offers to the construction industry:
- Alloys
Pure aluminum is a low-strength metal and consequently not suitable for building applications but thanks to the addition of alloying elements such as copper, manganese, magnesium, zinc etc. and thanks to specific production processes, it changes its physical and mechanical properties to meet requirements of a large number of applications.
2. Durability
- Aluminum alloys for Building are resistant to water, corrosion and immune to the harmful effects of UV rays, thus ensuring a lasting endurance
3. Low maintenance costs
- Aluminum does not require any special kind of maintenance, whether it is raw or lacquered aluminum
4. Finishes
- Aluminum can be anodized or lacquered in any color, so it’s possible to get the most varied effects and thus meet the designer’s decorative needs. Aluminum treatments can increase the durability of the material and its corrosion resistance
5. Reflective properties
- Aluminum is widely used for light management: its reflective properties help to reduce energy consumption for lighting and heating.
- For example, it’s possible to reduce the use of air conditioning in summer season by using aluminum shielding devices.
6. Aluminum is not combustible
- Aluminum does not burn and is therefore it’s classified as non-combustible material (A1 fire reaction class).
- Nevertheless, aluminum alloys melt at about 650 ° C, but without releasing any harmful gases. And so, more and more often, the outer covers and external surfaces of industrial structures (and not) are made with thin aluminum panel finishes which are destined to merge only in case of fierce fire, thus allowing heat and smoke to escape and reducing damage Caused by the fire.
7. Aluminum is eco-friendly
GLASS-
- There are various types of glasses used in construction and the use of these glasses depends on the purpose. Various purposes of glass can be for use in natural lighting, doors, windows, balconies etc.
- Silica is the main constituent of glass. But it is to be added with sodium potassium carbonate to bring down melting point. To make it durable lime or lead oxide is also added. Manganese oxide is added to nullify the adverse effects of unwanted iron present in the impure silica.
- The raw materials are ground and sieved. They are mixed in specific proportion and melted in furnace. Then glass items are manufactured by blowing, flat drawing, rolling and pressing.
Important Properties of Glass
- It absorbs, refracts or transmits light. It can be made transparent or translucent.
- It can take excellent polish.
- It is an excellent electrical insulator.
- It is strong and brittle.
- It can be blown, drawn or pressed.
- It is not affected by atmosphere.
- It has excellent resistance to chemicals.
- It is available in various beautiful colors.
- With the advancement in technology, it is possible to make glass lighter than cork or stronger than steel.
- Glass panes can be cleaned easily.
Types of Glass in Construction
The glass may be broadly classified as:
- Soda-lime glass
- Potash lime glass
- Potash lead glass
- Common glass and
- Special glasses.
1. Soda Lime Glass
It is mainly a mixture of sodium silicate and calcium silicate. It is fusible at low temperature. In the fusion condition it can be blown or welded easily. It is colorless. It is used as window panes and for the laboratory tubes and apparatus.
2. Potash Lime Glass
It is mainly a mixture of potassium silicate and calcium silicate. It is also known as hard glass. It fuses at high temperature. It is used in the manufacture of glass articles which have to withstand high temperatures.
3. Potash Lead Glass
It is mainly a mixture of potassium silicate and lead silicate. It possesses bright lustre and great refractive power. It is used in the manufacture of artificial gems, electric bulbs, lenses, prisms etc.
4. Common Glass
It is mainly a mixture of sodium silicate, calcium silicate and iron silicate. It is brown, green or yellow in color. It is mainly used in the manufacture of medicine bottles.
5. Special Glasses
Properties of glasses can be suitably altered by changing basic ingredients and adding few more ingredients. It has now emerged as versatile material to meet many special requirements in engineering. The following is the list of some of the special glasses:
- Fiberglass
- Foam glass
- Bullet proof glass
- Structural glass
- Glass black
- Wired glass
- Ultraviolet ray glass
- Perforated glass.
(2) PLASTIC-
Properties of Plastics as a Construction Material
Each plastic material has its own peculiar properties to suit its particular uses. The success of plastic as an engineering material will depends up on the selection of variety of plastic. Following are the general properties of plastic.
- Appearance
- Chemical resistance
- Dimensional stability
- Ductility
- Durability
- Electric insulation
- Finishing
- Fire resistance
- Fixing
- Humidity
- Maintenance
- Melting point
- Optical property
- Recycling
- Sound absorption
- Strength
- Thermal property
- Weather resistance
- Weight
1. Appearance of Plastics
- In the market there are so many types of models of plastics are available such as transparent, colored etc. suitable pigments are added in the process of manufacturing of plastic material to get these different properties. So, these will give good appearance to the structure and makes it attractive.
2.Chemical Resistance of Plastics
- Plastics offer great resistance against chemicals and solvents. Chemical composition of plastics during manufacturing will decide the degree of chemical resistance.
- Most of the plastics available in the market offer great corrosion resistance. So, corrosive metals are replaced by plastic in the case of water carrying pipes, etc.
3. Dimensional Stability
- Thermo-plastic types of plastics can be easily reshaped and reused. But in the case of thermo-setting type plastics, it is not possible to reshape or remold the material.
4. Ductility of Plastics
- Ductile nature of plastic is very low. When tensile stress are acting on plastic member they may fail without any prior indication.
5. Durability of Plastics
- Plastics with sufficient surface hardness are having good durability. Sometimes, plastics may affected by termites and rodents especially in the case of thermo-plastic types, however it is not a serious problem because of no nutrition values in plastic.
6. Electric Insulation
- Plastics are good electric insulators. So they are used as linings for electric cables and for electronics tools.
7. Finishing
- Any type of finishing treatment van be given to the plastics. Mass production of plastic particles with uniformity of surface finish is done by having technical control during manufacturing.
8. Fire Resistance
- The resistance to temperature or fire for varieties of plastics considerably varies depending upon the structure. Plastics made of cellulose acetate are burnt slowly. PVC made plastics do not catch fire easily. Plastics made of phenol formaldehyde and urea formaldehyde are fire proof materials.
9. Fixing
- Fixing of plastic materials is so easy. We can bolt, drill or glued to fix plastic material position.
10. Humidity
- The plastics made up of cellulosic materials are affected by the presence of moisture. The plastics made of poly vinyl chloride (PVC pipes) offers great resistance against moisture.
11. Maintenance
- Maintaining of plastics are so simple. Because they do not need any surface finishing coats or paints etc.
12. Melting Point
- Generally plastics have very low melting point. Some plastics may melt at just 50oC. So, they cannot be used in the positions of high temperature.
- Thermo setting type of plastics are having high melting point than thermo plastic type plastics. However, thermo setting types are cannot used for recycling. To improve the heat resistance of the plastics, glass fiber reinforcement is provided in its structure.
13. Optical Property
- There are so many types of plastics. Some plastics are transparent which allows light in its original direction and some are translucent nothing but semi-transparent which allows light but changes light rays direction.
14. Recycling of Plastics
- Disposal of plastics in the environment causes severe pollution. But it is not a serious problem because of its recycling property. We can use plastic waste disposal conveniently to produce drainage pipes, fencing, hand rails, carpets, benches etc.
15. Sound Absorption
- By the saturation of phenolic resins we can produce acoustic boards. These acoustic boards are sound absorbents and provide sound insulation. Generally for theatres, seminar halls this type of acoustic ceilings are used.
16. Strength
- Practically we can say that plastic is strong material but ideal section of plastic which is useful for structural component is not designed yet. Generally by reinforcing fibrous material into plastic improves its strength.
- If the strength to weight ratio of plastic is same as metals, then also we cannot give preference to plastics because of various reasons like, heavy cost, creep failure may occur, poor stiffness and sensitive against temperature.
17. Thermal Property
- The thermal conductivity of plastics is very low and is similar to wood. So, foamed and expanded plastics are used as thermal insulators.
18.Weather Resistance
- Most of the plastics except some limited varieties are capable of resistance against weathering. But, major problem is plastics when the plastics are exposed to sunlight, they are seriously affected by ultra violet rays and gets brittle.
- To prevent this, plastics are incorporated by fillers and pigments which helps to absorb or reflect the UV rays to surface.
19. Weight of Plastics
- The Plastics have low specific gravity generally ranges from 1.3 to 1.4. So they are light in weight and easily transportable to any place in a large quantity.
Reference Books
1. A to Z of Practical Building Construction and Its Management- Sandeep Mantri Satya Prakashan, New Delhi.
2. Handbook of Building Construction- M. M. Goyal ( Amrindra Consultancy).