UNIT 6
Roof
The roof is the covering of the uppermost part of a building. A roof protects the building and its contents from the effects of weather. Structures that require roofs range from a letterbox to a cathedral or stadium, dwellings being the most numerous. In most countries, a roof protects primarily against rain.
Terms used –
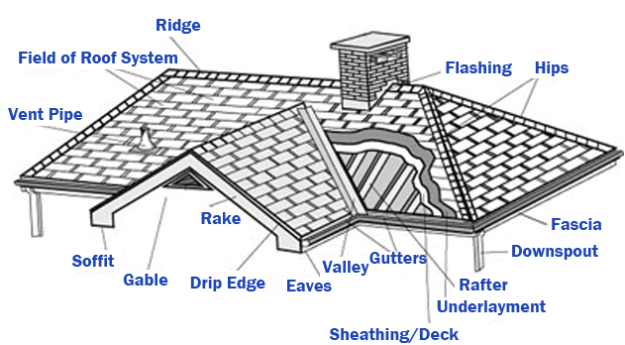
- Span:
It is the clear distance between the supports of an arch beam or roof truss.
2. Rise:
It is the vertical distance between the top of the ridge and the wall plate.
3. Pitch:
It is the inclination of the sides of a roof to the horizontal plane. It is expressed either in terms of degrees (angles) or a ratio of rising to span.
4. Ridge:
It is defined as the apex line of the sloping roof. It is thus the apex of the angle formed by the termination of the inclined surfaces at the top of a slope.
5. Eaves:
The lower edge of the inclined roof surface is called eaves. From the lower edge (eaves), the rainwater from the roof surface drops down
6. Hip:
It is the ridge formed by the intersection of two sloping surfaces, where the exterior angle is greater than 180 degree
7. Valley:
It is a reverse of a hip. It is formed by the intersection of two roof surfaces, making an external angle less than 180 degrees.
8. Hipped end:
It is the sloped triangular surface formed at the end of a roof.
9. Verge:
The edge of a gable, running between the eaves and ridge is known as a verge.
10. Ridge piece, ridge beam, or ridge board:
It is the horizontal wooden member, in the form of a beam or board, which is provided at the apex of a roof truss. It supports the common rafters fixed to it.
11. Purlins:
These are horizontal wooden or steel members, used to support common rafters of a roof when the span is large. Purlins are supported on trusses or walls.
12. Hip rafters:
These are sloping rafters that form the hip of a sloped roof. They run diagonally from the ridge to the corners of the walls to support roof coverings. They receive the purlins and ends of jack rafters.
13. Valley rafters:
These are sloping rafters that run diagonally from the ridge to the eaves for supporting valley gutters. They receive the ends of the purlins and the ends of jack rafters on both sides.
14. Jack rafters:
These are the rafters shorter in length, which run from the hip or valley to the eaves.
15. Eaves board or facia board:
It is a wooden plank or board fixed to the feet of the common rafters at the eaves. It is usually 25 mm wide. The ends of the lowermost roof covering material rest upon it. The eaves gutter, if any, can also be secured against it.
16. Barge boards:
It is a timber board used to hold the common rafter forming verge.
17. Truss:
A roof truss is a framework, usually of triangles, designed to support the roof covering or ceiling over rooms.
Factors depend on the selection of Roof Materials-
An outermost exterior covering part of a building is known as the roof. The roof is supported by the beneath a layer of structure, Roofing materials commonly provide shelter from natural resources like sun heat and light, air, rain, animals, etc. When choosing roofing materials, there are some important things we need to consider. They are as follows,
- Duration and ability of roofing material to withstand
- Properties of the material such as weight, thickness, durability, slope, and shape
- Whether the material eco-friendly or not / recyclable or not
- Cost of the material.
TYPE OF ROOFING MATERIALS-
- CLAY & CONCRETE TILES
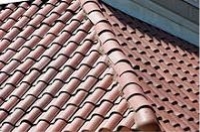
Clay tiles are very heavy, requiring additional roof framing, but they are non-combustible and extremely durable. Clay roofing tiles can come in lighter colors, which adhere to the cool roof standards and can reflect well over 50% of the sun’s solar energy. Concrete roofing tiles offer elegant, enduring aesthetics for your home’s design and added value. Concrete tiles are very versatile and provide greater protection to the homeowner. These flexible tiles come in so many different hues, shapes, textures, and styles that they don’t even look like tiles at all. Shingle, shake, and slate are just some of the varieties of tile.
2. PVC ROOFING MATERIAL
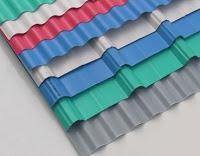
Polyvinyl chloride (PVC) roofing material exists as leading roofing material at present. Comparatively PVC roofing material is a better one, for its quality, durability, resistance to UV rays, availability of different colors, flexibility, a good heat stabilizer, and also for its cost. A German company produced the PVC roofing material for the first time in 1966. It is a single ply, thermoplastic roofing material which popularized in a short period.
3. ASPHALT ROOFING MATERIAL
A mixture of aggregates, binder, and filler are used to form the Asphalt. Asphalt is used as asphalt shingles and asphalt roll in roof construction works.
3.1 ASPHALT SHINGLES
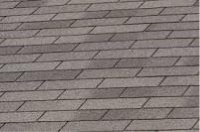
The asphalt shingles roofing material is commonly used roofing material which is a good waterproofing material. Strip asphalt roofing shingles, dimensional asphalt roofing shingles, and premium asphalt roofing shingles are the three main asphalt shingles roofing material available.
3.2 ASPHALT ROLL ROOFING
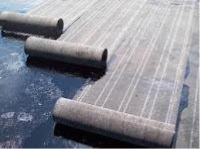
The easiest way of roofing is by using roll roofing material. The same materials used in the production of asphalt roll roofing as in asphalt shingles. An easiest and cheap way of roofing but not suitable for high slope roofing construction.
4. METAL ROOFING (STEEL, ALUMINIUM )
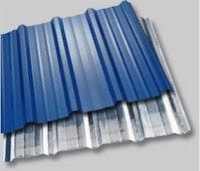
Metal roofs are some of the coolest roofs around, both in temperature and style for new homes. Metal roofs are available in copper, aluminum, and stainless steel, and often have a high percentage of recycled content. They offer high insulation solar reflectance, and durability, often lasting twice as long as wood or asphalt. Metal shingles typically simulate traditional roof coverings, such as wood shakes, shingles, slate, and tile. Aside from its longevity, metal shingles are much lighter than most materials and very resistant to adverse weather.
5. ECO ROOFING OR GREEN ROOFING MATERIAL
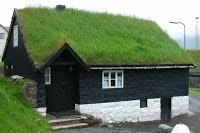
The best way to reduce global warming is eco roofing. A layer of plants grown above the primary cement layer of a building with necessary barriers and medium ( Root barrier, waterproof layer, and soil) is known as eco roofing. Large trees and plants or light plants like mosses are the materials of eco roofing. A good way to reduce heat within the building and provides natural, fresh air. Low cost and environmentally friendly way of roofing material.
Pitched roofs and their types-
A pitched roof is a roof comprising a sloping surface or surfaces with an angle of usually over 20 degrees. It is a bi-fold, bi-planer roof with a ridge at its highest point. To be more specific – a pitched roof requires a pitch of more than 10 degrees or a roof with two slopes that meet at a central ridge.
Pitched roofs offer a more classical appearance. They remain the most common and efficient solution in wet and cold weather to ensure maximum protection.
Parts of Pitched Roof
The followings are the major parts of pitched roofs.
- Eaves
- Gable
- Flashing
- Hip
- Ridge
- Purlines
- Fascia
- Rafter
- Battens
- Joist
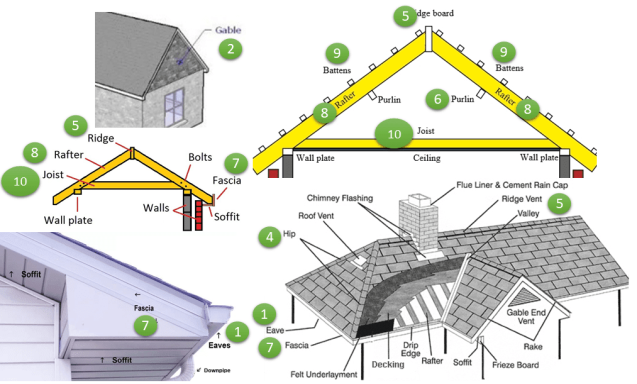
The description of these parts of pitched roofs is given below.
Eaves
In the roof, the lower portion of the inclined roof is projecting beyond the outer face of the wall. The main function of eaves is to rainwater to pour from the roof directly on the exterior wall. I also give protection from sunlight. Sometimes eaves are highly decorated to increase architectural beauty.
Gable
The Triangular upper part of the wall at the end of a ridge roof.
Flashing
A strip of impervious material, usually metal used to exclude water from the junction between a roof covering and another part of the structure.
Flashings are provided to prevent moisture from entering the wall and roof through joints in copings, parapet walls, and other penetrations through the roof plane.
Hip
The outer angle (more than 180 degrees) formed by the inclined ridge between two intersecting roof slopes.
Ridge
The horizontal intersection at the apex of the two rising roof surfaces inclined in opposite directions.
Purlins
These are horizontal members laid on principal rafters on wall-to-wall to support common rafter of a roof when the span is large. Purlins are made from wood or steel.
The top surfaces of the purlins shall be uniform and plane. They shall be painted before fixing them on top.
Fascia
This is a wooden board fixed to the feet of the common rafter at eaves. The ends of the lower-most roof covering material rest upon it.
Rafter
Rafter is a structural component of a pitched roof. Typically it starts from roof support (column or wall) to ridge or hip. Multiple rafters are used side by side with equal spacing to support the purlin. In typical home construction, wooden rafters are used. For large industrial of commercial sheds, steel rafters are used.
Battens
These are thin strips of wood which are fixed on the common rafters or on the top of ceiling boards to support the roofing materials such as tiles, sheets, etc. Batten could be also made of metal or plastic.
Types of Pitched Roof
Followings are the type of pitched roof
- Mono Pitch Roof
- Couple Roof
- Closed Couple Roof
- Collar Roof
- Purlin Roof
- Trussed Rafter
Brief descriptions of these pitched roof types are given below.
Mono Pitch Roof
- Slopes from one side or part of a building to another commonly used to form extensions.
- Comprises a series of rafters fixed to plates at the top of a wall and the rafter feet are nailed to a wall plate, which distributes the load evenly across the supporting wall.
- Joists are fitted to form level ceilings and could be raised to give more height.
- Joists are commonly supported by struts, which precludes rafters from sagging.
Couple Roof
- The simplest form of the pitched roof, the couple roof comprises two lengths of rafters leaning against each other, tied where they meet at the top.
- A very limited span of approximately 3.5 m.
- The downside of this roof is that the weight of it creates natural deflection in the supporting walls by pushing those outwards at the top. Walls could be reinforced but this would require extra brickwork and unnecessary expense.
Closed Couple Roof
- Ceiling joists are added, a length of timber running horizontally in-between the rafter feet, making the structure much more secure. The joist acts as a tie that prevents the outward deflection of the wall and increases the potential roof-span to approximately 5 m.
- Joists are secured to the rafter feet rather than the wall Plate to negate any potential deflection. A secure connection between the rafter and ceiling joist is therefore critical.
- The benefit of this form of roof is by using struts, much of the roof space could be utilized for storage and allowed the space to be used for accommodation if needed.
Collar Roof
- The height of the ceiling joists is raised, such that the roof allowed any upper rooms to be constructed in the roof space, thus the height of the external walls is slightly reduced.
- The drawback of this method is that lifting the ceiling joist reduces its restraining force, increasing the instability of the supporting walls and decreasing the span to approximately 4 m.
- For maintaining stability, the height of the ceiling joist could be lifted to a maximum of 1/3 of the height of the roof.
Purlin Roof
- By introducing purlins roof spans could be increased without compromising wall stability, increasing the size of rafters, or attracting extra costs. Purlins allow rafters to get extra support and become lighter and thinner, allowing a potential span of 8 m.
- The benefit of this form of roof was that by using struts, much of the roof space could be utilized for storage and ultimately allowed the space to be used for accommodation
Trussed Rafter
- The fink or 'w' truss is the most common form of the trussed rafter in modern house construction. This consists of a rafter comprising W shaped tension and compression members. This trussed rafter is capable of spans up to 12 m and can be designed to accommodate many different pitch angles.
- The most significant advantage is the off-site assembly of the trussed rafter which speeds up the whole construction process.
- The addition of diagonal bracing from eaves to ridge on the underside of the rafters binds the whole structure into one unit rather than a series of individual trusses, protecting from possible collapse due to wind forces.
- The only real disadvantage of the trussed rafter is that it requires careful design where a change of direction occurs in the roof.
STEEL TRUSSES-
For different constructions, different types of steel trusses are used. Some of these types are mentioned below.
(1)Pratt Truss
The most common and economical truss found in constructions is the Pratt truss. In this type, the members placed vertically are for compression whereas diagonal ones respond to the tension. This truss is ideal to use in buildings that have a span of around 20 to 100 meters. Pratt trusses are basically of two types:
- Pratt truss with secondary members
- Duo-pitch Pratt truss
(2)Warren Truss
In Warren truss, the diagonal members are placed alternatively to create a shape of ‘W.’ They have equal compression and tension and hence, require fewer members compared to Pratt truss. They can be used for buildings or constructions that have around 20 to 100-meter of the span.
(3)Fink Truss
Most commonly used for a roof, fink truss has shorter members and chords. The arrangement for compression and tension depends on the construction it will be used for. This type is useful in places with shorter span. Also, due to the short size, these trusses are very economical to use.
(4)King Post Truss
One of the simplest truss to fabricate, king post truss has two-angle support members. They are used for a short span of around 8 meters and so, they are ideal for small houses.
(5)Queen Post Truss
Like king post truss, queen post truss is also simple to fabricate but is very versatile in use. This type can be used to make cover bridges, roofs, etc. It can be used for a short span of 10 meters. The two horizontal members have a beam in the center for support.
(6)Howe Truss
Howe truss is a combination of wood and steel. The use of steel provides extra support and reliability to the construction. Also, they have a wide span which can cover around 6 to 30 meters. Due to its versatility, this type is used in the construction of bridges.
(7)North-Light Truss
One of the oldest and resistant trusses is the North-Light truss. This is because of the proper ventilation it provides, and the spread has a 20 to 30-meter span. Due to its durability and versatility, North-Light Truss is used in large spaces and allows maximum light to reach the space.
Different types of roofing materials-
1. Solar tiles
Advanced solar collectors integrate seamlessly into existing shingles, generating up to 1 kilowatt of energy per 100 square feet. They’re particularly good for sunny roofs in homeowners’ associations that forbid typical solar panels. While they may help offset energy costs with solar power, they also cost more than traditional solar options.
2. Asphalt shingles
Asphalt shingles are the most common roofing materials in America because they’re effective in all environmental conditions. Quality varies widely, so ask whether they pass the ASTM D3161, Class F (110 mph) or ASTM D7158, Class H (150 mph) wind tests, and the AC438 durability test. Upfront costs are low, but you should expect to replace the shingles after about 20 years. If you live in a hail prone area, consider impact-resistant shingles that have a UL 2218 Class 4 rating. Impact-resistant shingles may qualify for a discount on your homeowner’s premium.
3. Metal roofing
Metal roofing comes in vertical panels or shingles resembling slate, tile, and shake – and lasts about 60 years. Metal excels at sloughing off heavy snow and rain, won’t burn, and resists high winds. It is lightweight and can be installed over existing roofs. However, metal can be noisy during rainstorms and may dent from hail. Average costs range between $5 and $12 per square foot, depending on type and style of metal – which is more than asphalt but less than concrete tiles. Corrosion also varies by material.
4. Stone-coated steel
Interlocking panels mimic slate, clay, or shingles and resist damage caused by heavy rains (up to 8.8 inches per hour), winds of 120 miles per hour, uplifting, hail, and freeze-thaw cycles. Consequently, they’re an economical, effective choice for wet, windy regions or areas prone to wildfires. Some stone-coated steel roofs are warranted for the lifetime of the house.
5. Slate
Slate roofing lasts more than 100 years. It won’t burn, is waterproof and resists mold and fungus. Slate is effective in wet climates but is expensive, heavy, and may be easily broken when stepped on. Keep this in mind if you live in an area that experiences hail.
6. Rubber slate
Rubber slate looks natural and can be cut with a knife to fit intricate roofs like those found in Victorian homes. Rubber slate roofs can last 100 years but can be damaged by satellite dishes and walking – so may also be susceptible to damage by hail, similar to slate. Roofing professionals that are trained to install rubber slate may be hard to find.
7. Clay and concrete tiles
Clay and concrete roof tiles can withstand damage from tornadoes, hurricanes, or winds up to 125 miles per hour and even earthquakes, according to "A Summary of Experimental Studies on Seismic Performance of Concrete and Clay Roofing Tiles" by the University of Southern California for the Tile Roofing Institute. They are good in warm, dry climates. They may require extra support to bear their weight, and they are likely to break when walked on.
8. Green roofs
Green roofs are covered with plants and can improve air quality, reduce water runoff and insulate homes to reduce urban heat islands. However, they need extra structural support, a vapor barrier, thermal insulation, waterproofing, drainage, water filtration, soil, compost, and plants. Their estimated lifespan is 40 years.
9. Built-up roofing
This heavy roofing consists of layers of asphalt, tar, or adhesive topped with aggregate and is only for flat roofs. Tar and gravel roofs, also for flat roofs, are best for roof-top decks with heavy foot traffic. These roofs may become sticky in summer, and it is harder to shovel snow off of these roofs when compared to smooth surfaces. They can last 20 to 25 years.
The best type of roof for you depends on your climate, budget, and house. To see what’s best in your area, talk with licensed roofing contractors, and look at some of the newer developments nearby to get ideas on what type of roofing material to use.
Regardless of what type of roof you go with, there is always a chance it can be damaged. Roofing can be expensive, so you want to make sure you’re covered when the unexpected happens. Find out how Better Roof Replacement from Nationwide can help protect your home.
- Mangalore tiles-
Mangalore tiles (also Mangalorean tiles) are a type of tile native to the city of Mangalore, India. Typically considered to be a part of Spanish and Italian architectural styles, the tiles were first introduced to India in 1860 by a German missionary. Since that time, the industry has flourished in India with these red tiles, prepared from hard laterite clay, in great demand throughout the country. They are exported to Myanmar, Sri Lanka, and the Far East and even as far as East Africa, the Middle East, Europe, and Australia These were the only tiles recommended for government buildings in India under the British Raj.
- A.C.and G. I.sheets
- G.I. SHEETS-
The term is derived from the name of Italian scientist Luigi Galvani. Galvanized iron (GI) sheets are steel sheets which are coated with zinc and include a range of hot-dip galvanized and electro-galvanized steel sheets. To retain the steel intact with its full initial strength
- A.C. SHEETS-
Asbestos cement, genericized as fibro or fibrolite - short for "fibrous (or fiber) cement sheet" - and AC sheet, is a building material in which asbestos fibers are used to reinforce thin rigid cement sheets.
- Concept of Proflex-
Proflex is the pioneer of Self Supported Steel Roofing in India that introduced the concept in the year 2001. This unique technology does not use any nuts or bolts and the panels are joined together by the mechanical seaming process, ensuring leakproof roofing.
- Concrete Flooring
Concrete floor slab construction process includes the erection of formwork, placement of reinforcement, pouring, compacting and finishing concrete, and lastly removal of formwork and curing of a concrete slab.
Concrete Floor Slab Construction Process
- Assemble and Erect Formwork
- Prepare and Place Reinforcement
- Pour, Compact and Finish Concrete
- Curing Concrete and Remove Formwork
1. Assemble and Erect Formwork for Slab
The formwork shall be designed to withstand construction loads such as fresh concrete pressure and weight of workers and operators and their machines. Guide to Formwork for Concrete ACI 347-04 shall be followed for the design of formworks.
Moreover, various construction aspects need to be considered during the erection of formworks. For example, it should be positioned correctly, lined and leveled, joints sealed adequately, and prevent protruding of nails into the concrete, etc…
Furthermore, different materials such as wood, steel, and aluminum can be used for the formworks of the concrete floor slab.
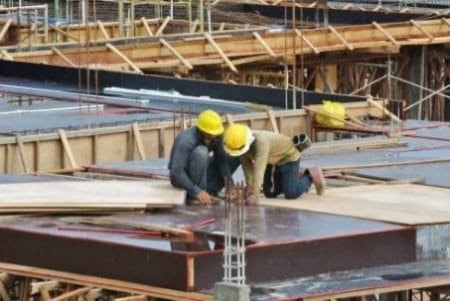
2. Prepare and Place Reinforcement for Slab
Before the placement of reinforcement for concrete floor slab construction, inspect and check forms to confirm that the dimensions and the location of the concrete members conform to the structural plans.
Added to that, the forms shall be properly cleaned and oiled but not in such amount as to run onto bars or concrete construction joints.
Design drawings provide necessary reinforcement details, so it only needs the understanding to use designated bar size, cutting required length, and make necessary hooks and bents.
After preparation is completed, steel bars are placed into their positions with the provision of specified spacings and concrete cover.
The concrete cover and spacing for floor slabs can be maintained by introducing spacers and bars, supporters. Wires are used to tie main reinforcement and shrinkage and temperature reinforcement (distribution reinforcement).
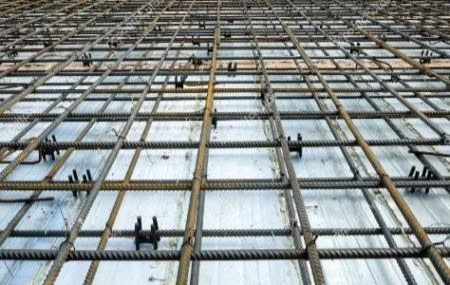
Fig. 2: wires used to tie reinforcement and supporters used to maintain concrete cover
It should be known that incorrect reinforcing steel placement can lead to serious concrete structural failures. Improper concrete cover exposes reinforcement bars to danger and jeopardizes concrete-steel bond.
Finally, after all, requirements of reinforcement placements (positions, concrete cover, spacing, and correct bars size; length; hooks; and bending) are finalized, then the site engineer can order concreting.
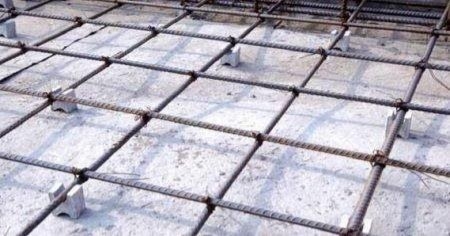
Fig. 3: Provision of concrete cover for reinforcement bars in slab
3. Pour, Compact and Finishing Concrete Floor Slab
Mixing, transporting, and handling of concrete shall be properly coordinated with placing and finishing works. In-floor slab, begin concrete placing along the perimeter at one end of the work with each batch placed against previously dispatched concrete.
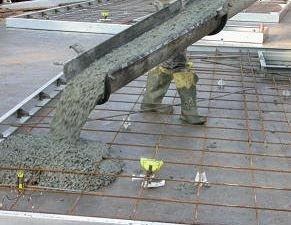
Fig. 4: Concrete placement started from one end of the slab
4. Curing Concrete and Remove Formwork
After finishing the ended, a suitable technique shall be used to cure the concrete adequately. Slab curing methods such as water cure; concrete is flooded; ponded, or mist sprayed.
In addition to water retaining method in which coverings such as sand; canvas; burlap; or straw used to kept slab surface wet continuously, chemical Membranes, and waterproof paper or plastic film seal.
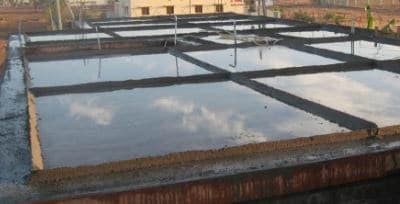
2. R.C.C. SLABS-
- A Reinforced Concrete Slab is one of the most important components in a building. It is a structural element of modern buildings. Slabs are supported on Columns and Beams.
- RCC Slabs whose thickness ranges from 10 to 50 centimeters are most often used for the construction of floors and ceilings.
- Thin concrete slabs are also used for the exterior paving purpose.
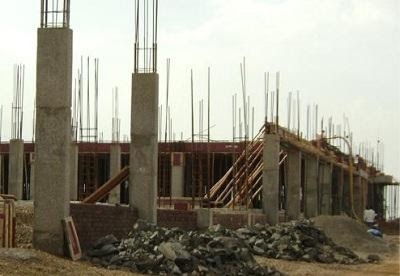
- In many domestic and industrial buildings a thick concrete slab, supported on foundations or directly on the subsoil, is used to construct the ground floor of a building.
- In high rises buildings and skyscrapers, thinner, pre-cast concrete slabs are slung between the steel frames to form the floors and ceilings on each level.
- While making structural drawings of the reinforced concrete slab, the slabs are abbreviated to “r.c.slab” or simply “r.c.”.
3. R.C.C. Beams and slab
- RCC roof slab with the beam is called a flat beam slab or flat slab beam. In the normal course, the beam project outside the slab, but in the case of monolithic construction where height consideration is there, flat slab beam design is adopted for construction.
- RCC roof slab with the beam is a monolithically casted structure in which the beam and slab are cast together.
- This reduced forming, pouring, and finishing time.
- An RCC ( Reinforced Cement Concrete) slab along with the RCC beam is a monolithically cast structural system which distributes the dead load and lives load of the building on to the columns, which in turn disperses the load into the earth through the foundation system.
- It is a part of the superstructure of any RCC building. There are different types of slabs which may or may not require beams conventionally. For example, a flat slab will have capitals at column and slab junction or a coffered slab which is also used for large column-free spaces.
4. Flat slab floor
- Flat slab is a reinforced concrete slab supported directly by concrete columns without the use of beams. Flat slab is defined as a one-sided or two-sided support system with the sheer load of the slab being concentrated on the supporting columns and a square slab called ‘drop panels’.
- Drop panels play a significant role here as they augment the overall capacity and sturdiness of the flooring system beneath the vertical loads thereby boosting the cost-effectiveness of the construction. Usually, the height of drop panels is about two times the height of the slab.
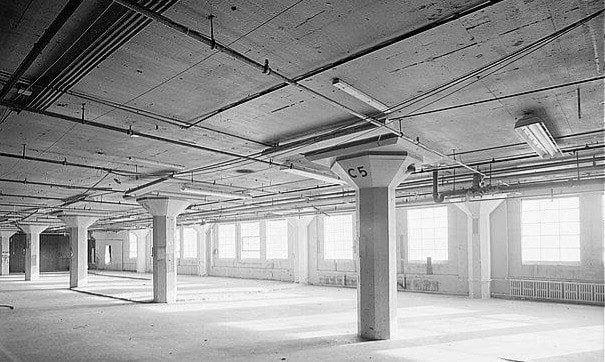
Types of Flat Slab Construction
Following are the types of flab slab construction
- Simple flat slab
- Flat slab with drop panels
- Flat slab with column heads
- Flat slab with both drop panels and column heads
Benefits of Using Flat Slab Construction Method
- Flexibility in room layout
- Saving in building height
- Shorter construction time
- Ease of installation of M&E services
- Use of prefabricated welded mesh
- Buildable score
Construction of floors: Precoated sheets
- Waterproofing is the process of making an object or structure waterproof or water-resistant so that it remains relatively unaffected by water or resisting the ingress of water under specified conditions. Such items may be used in wet environments or underwater to specified depths.
- There are many types of waterproofing materials. Some of the best and most common include; Polyurethane, Cementitious Coating, EPDM Rubber, Rubberized Asphalt, Thermoplastic, Bituminous Membrane, and PVC Waterproofing Membrane, etc.
- Polyurethane-
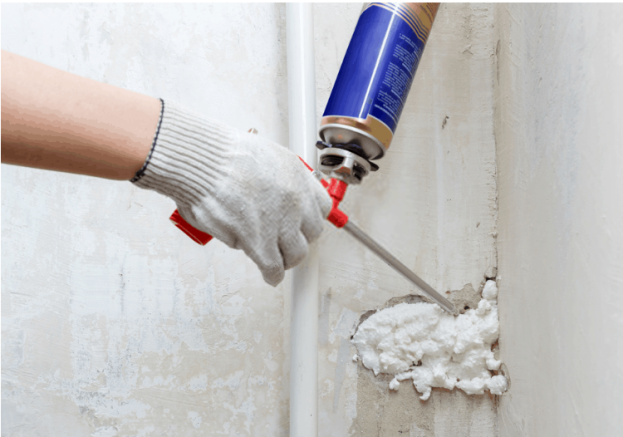
While there are many types of waterproofing materials, not all of them are equal. For many people, polyurethane will be the best option. It offers numerous benefits and many of them are not available with the alternatives. Therefore, you should learn as much as you can about this type of waterproofing material before investing your time or money. Doing so will ensure that you’re able to find the best material for your specific needs. This material is going to offer a seamless waterproofing membrane. This can make a big difference. On top of that, this waterproofing material will fill all capillary cracks. It can decrease the concrete’s water absorbency. Another thing to note is that this material will harden the concrete’s uppermost surface.
2. Cementitious Coating
Cementitious coating is a powder that consists of sand, organic and inorganic chemicals, and silica-based substances. When the active ingredients are combined with lime, it causes a hydration reaction, creating a waterproof seal. Many experts prefer working with this type of coating because it is so easy to utilize.
As mentioned above cementitious waterproof coating is extremely easy to utilize. Most brands recommend mixing the coating with a specific amount of tap water before applying. Some experts utilize an acrylic additive to create a more durable, solid coating.
3. EPDM Rubber
EPDM Rubber is a very effective material for waterproofing your roof. It’s a synthetic rubber material that can be used for an abundance of situations. It is a class M rugged that is made using ethylene and propylene. While it is commonly associated with silicone, the two materials are extremely different. EPDM rubber is primarily used to provide a waterproof coating to roofs. It works great for this purpose. It is also used in vehicles. In this type of environment, the rubber is used to seal windows, trunks, and even woods.
4. Rubberized Asphalt
Another waterproofing material is rubberized asphalt. This material works great for keeping your home protected from the elements. However, it is primarily found on roofs for commercial businesses. 790-11 hot rubberized asphalt is best for two specific applications. If you’re dealing with extensive vegetative assemblies or intensive roofing assemblies, you’ll want to go with this material. It will prevent problems and provide you with the best results. This material is sometimes utilized to provide a waterproofing cover to RVs and campers. There’s a lot to like about rubberized asphalt. For instance, it is very tough.
5. Thermoplastic
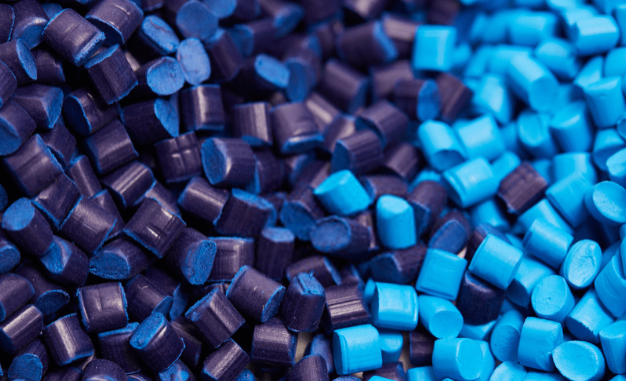
Another very popular waterproofing material is thermoplastic. This material might not be the cheapest out there, but it offers a wealth of benefits. For instance, it is one of the strongest waterproofing materials on the market. On average, it can provide you with 50 years or more of waterproofing durability. This makes it longer lasting than many of the alternatives. When heated correctly, the material will transform from solid to semi-solid. This allows a professional to seal the sheets or panels together. In return, this makes thermoplastic waterproofing more effective for the intended purpose. The material also features elastomers.
Waterproofing Methods
- Cementitious Waterproofing
- Liquid Waterproofing Membrane
- Bituminous Membrane
- Bituminous Coating
- Polyurethane Liquid Membrane
1. Cementitious Waterproofing
- Cementitious waterproofing is the easiest method of waterproofing in construction. The materials for cementitious waterproofing are readily available from suppliers of masonry products. And they are easy to mix and apply.
- The applications of the cementitious waterproofing technique are in the internal wet areas, such as toilets. That is why it does not go through the contract and expansion process.
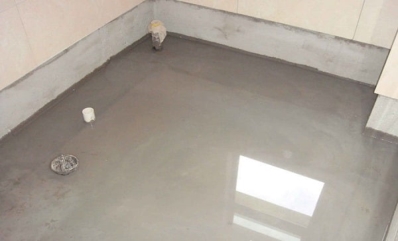
Fig. : Cementitious Waterproofing
2. Liquid Waterproofing Membrane
- The liquid membrane consists of a primer coat and two topcoats. The application of the coatings is by spray, roller, or trowel. The liquid layer is thin and offers more flexibility than the cementitious types of waterproofing.
- Liquid waterproofing membrane can be of a spray-applied liquid layer composed of polymer-modified asphalt. Polyurethane liquid membranes in separate grades for trowel, roller, or spray are also available from various manufacturers.
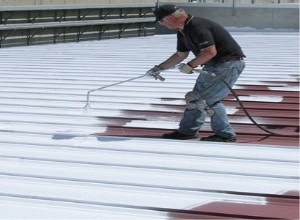
Fig. : Liquid Waterproofing Membrane
3. Bituminous Coating Waterproofing
- Bituminous coating (asphalt coating) is made of bitumen based materials. It is a flexible protective coat based on its formulation and polymerization grade. The flexibility and protection against water can be influenced by the polymer grade and reinforcement of fiber.
- The most common applications of bituminous coatings include areas that are beneath screed wet. It is an excellent protective coating and waterproofing agent, especially on surfaces such as concrete foundations.
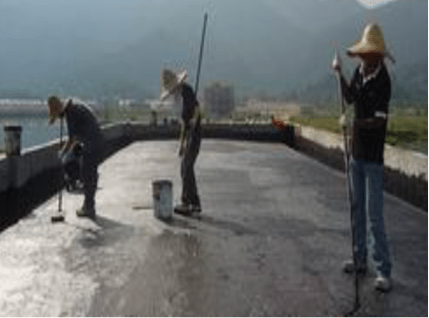
Fig. : Bituminous Waterproof Coating
4. Bituminous Membrane Waterproofing
Bituminous membrane waterproofing is a popular method used for low-sloped roofs due to their proven performance. The bituminous waterproofing membrane has a torch on the layer and self-adhesive membrane.
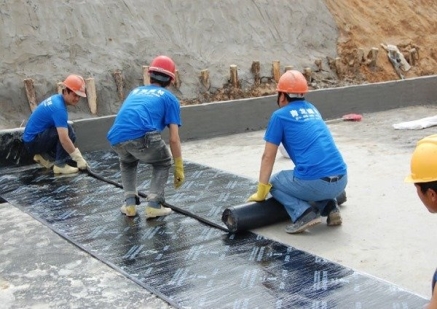
Fig. : Bituminous Membrane Waterproofing
5. Polyurethane Liquid Membrane Waterproofing
Polyurethane liquid membrane method of waterproofing is used for the flat roof area and exposed to weathering. This waterproofing method is expensive.
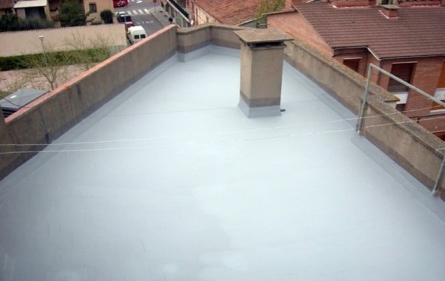
Fig. : Polyurethane Liquid Membrane Waterproofing